压裂车液压系统存在问题及改进措施(新编版)
液压系统常见故障及消除方法

液压系统常见故障及消除方法液压系统在工程和机械设备中广泛应用,但随着时间的推移,常见的故障也会发生。
本文将介绍一些常见的液压系统故障,并提供相应的消除方法。
1.油温过高油温过高是液压系统中常见的故障之一、通常,油温过高可能是由以下几个原因引起的:-油液过载:液压系统过载会导致油液温度升高。
解决方法是检查负载并适当调整液压流量。
-耗能装置故障:若消耗部分的散热器、散热器或油冷却器出现故障,则可能导致油温过高。
解决方法是修复或更换受损的零件。
-油液质量不合格:悬浮物、杂质或水分可能导致油液质量下降,进而使油温升高。
解决方法是更换油液并定期检查。
2.液压泄漏液压系统中的泄漏是另一个常见的故障。
泄漏可能会导致系统性能下降,并可能损坏关键部件。
常见的泄漏原因及解决方法如下:-密封件老化或损坏:通过检查系统的密封件并及时更换来解决问题。
-过高的应力或压力:检查系统的压力和应力水平,确保它们在设计范围内。
-错误安装或组装:重新检查系统的安装和组装过程,并纠正可能的错误。
3.液压缸无力或无法移动如果液压缸无法提供足够的动力或无法进行平稳的运动,可能有以下几个原因:-漏气或气体混入:检查气体混入的可能性,并排除气体。
-油液供应不足:检查液压泵、压力阀以及供油管路,确保它们正常工作并供油充足。
-液压缸密封失效:检查液压缸密封件并及时更换。
4.液压系统噪音大液压系统噪音大可能会影响设备的工作效率和舒适性。
-油液泵的进气或压力阀噪音:检查泵的进气管道,排除可能的泄漏或振动源。
检查压力阀并清洁和润滑。
-操作元件过度磨损:检查和更换磨损的操作元件(如阀、泵)。
-油液中的悬浮物:检查和更换油液,并确保油液质量合格。
总之,液压系统常见的故障包括油温过高、液压泄漏、液压缸无力或无法移动以及系统噪音大。
根据具体情况,可以采取相应的解决方法来消除故障。
定期维护和保养液压系统,确保其正常运行,也是预防故障的重要措施。
压裂作业过程中常见的问题及应对措施

247压裂作业过程中常应各种因素造成压裂效果不理想,常见的问题有地层不入液压不开、压窜层、卡压裂管柱、沉砂等。
遇到该类问题如果不能采取正确的方式处理,不仅延迟了作业工期,还有可能造成工程事故,影响开采效果,增加了投入成本,造成巨大的经济损失,本文针对以上常见问题的产生及处理进行分析:1 目的层不吸液,压不开的原因及相应措施该类问题表现为当针对目的层实施压裂作业时,压裂车辆刚起泵施工,其泵注压力迅速升高至设计限制最高压力,目的层没有液量吸入,降排量时压力依然没有下降的趋势。
造成该问题的的主要因素如下:一是改造目的层的构造问题,地层物性差、孔隙度低、连通性极差,造成地层吸液困难;还有可能目的层含有大量的水敏性黏土矿物,遇压裂液会膨胀堵塞孔隙,导致地层不能吸入液体;还有可能是开采层结蜡或钻井过程中造成进井污染,导致连通性降低。
二是管柱及井下工具问题,目的层改造位置吐砂,造成喷砂器被砂埋,造成液体不流通,不能实施改造;还有可能管柱长度测量有误或是作业人员疏忽导致喷砂器未能下至指定层位,造成地层不吸液;管柱或油套环形空间存在油污或是其他杂物,在泵注过程中冲洗掉落造成堵塞;射孔质量不合格也会导致目的层未打开,导致改造层堵塞。
对于目的层存在的问题可以采取通过打前置酸,软化近井地层,实现目的层孔隙的清洗,去除近井污染,然后再进行常规压裂作业,通常可以解决该类问题。
对于管柱及井下工具问题则需要首先要对欲施工井进行通井,然后充分的循环和洗井,并对管柱长度进行认真测量并按设计配置好相应的短接,防止位置出现问题,还可采用瞬间起泵停泵,进行憋压和缓冲,或将管柱快速提放,来处理卡钻问题。
2 压窜地层问题压裂过程中出现窜层现象也较为常见,通常可通过压裂快速下降或先后两层破裂压裂几近相同两种情况进行判断,通常引起窜层现象的因素主要有如下几点:一是封隔器方面,当胶筒不能正常膨胀或在下钻过程中出现刮坏等现象无法在目的层形成有效的封隔效果,导致形成套喷,造成层位压窜,或是下钻位置不准确,导致封隔层位出现偏差也会出现层位压窜现象。
液压系统故障的检查与排除范本

液压系统故障的检查与排除范本液压系统故障的检查与排除是维修液压设备的重要环节。
本文将分享一个液压系统故障的检查与排除的范本,旨在帮助读者更好地理解和解决液压系统故障。
一、液压系统压力不足液压系统压力不足是一种常见的故障现象,可以通过以下步骤进行检查和排除:1. 检查液压泵的工作状态。
检查液压泵是否正常运转,是否有异常噪声或震动。
如果存在异常情况,需要对液压泵进行检修或更换。
2. 检查液压泵的进油口和出油口。
确保进油口没有堵塞物,并且出油口没有泄漏。
如果有堵塞物或泄漏现象,需要进行清洁和修复。
3. 检查液压系统的油液质量和油液量。
确保油液质量符合要求,不含杂质和水分。
同时,检查油液量是否足够。
如有必要,需要更换油液或添加新的油液。
二、液压系统漏油液压系统漏油是另一种常见的故障现象,可以通过以下步骤进行检查和排除:1. 检查液压系统的密封件。
检查液压系统中的密封圈、密封垫等密封件是否完好无损。
如有磨损或老化现象,需要进行更换。
2. 检查液压系统的管路连接。
确保液压系统的管路连接牢固,没有松动现象。
如有松动,需要进行紧固。
3. 检查液压系统的油箱和油管。
检查油箱和油管是否有破损或渗漏的情况。
如有破损或渗漏,需要进行修复或更换。
三、液压系统工作不稳定液压系统工作不稳定是另一种常见的故障现象,可以通过以下步骤进行检查和排除:1. 检查液压系统的油液温度。
检查油液温度是否超过允许范围。
如超过范围,需要采取降温措施。
2. 检查液压系统的油液粘度。
检查油液粘度是否符合要求。
如不符合要求,需要更换合适的油液。
3. 检查液压系统的阀门和元件。
检查阀门和元件是否正常工作,是否存在卡滞或老化的情况。
如有必要,需要进行清洁或更换。
四、液压系统噪声过大液压系统噪声过大是一种常见的故障现象,可以通过以下步骤进行检查和排除:1. 检查液压泵和液压缸的工作状态。
检查液压泵和液压缸是否存在异常噪声或震动。
如存在异常情况,需要对相关部件进行检修或更换。
液压系统常见故障原因及解决方法.docx

1、零油压液压系统没有压力的原因:油泵旋转方向反了或油泵没有输出液:电液比例装置上的溢流陶阀芯卡死,阻尼孔堵塞;油泵吸油口不通畅,吸油过滤器堵塞:压力阀内有脏物,锥阀关不住。
处理方法:纠正泵的旋转方向,排除油泵故障;把溢流阀拆开清洗,要求做到阀芯在阀体内运动灵活,用压缩空气把阻尼孔吹通;清洗过滤器滤芯,并检查吸油管路是否堵塞:拆开压力阀,把锥阀芯取下来清洗。
2、油压值不能保证原因是液压系统内有空气吸入,油箱内的油有好多泡沫,或者是溢流阀、电磁换向阀内泄漏大。
处理方法:检查液压站吸油口是否泄漏油:泵吸油处管接头是否拧紧;检查吸油过滤器到油泵吸油口处的管路是否漏气:检查油泵端盖螺钉是否拧紧:清洗溢流阀阀芯,如果溢流网阀芯在阀体内运动不灵活,可以用手拿住阀芯在体内来回研磨:清洗电磁换向阀阀芯,要求阀芯在阀体内运动灵活,保证工作时阀芯到位。
3、漏油即油压不稳长期使用后,安全制动装置中的各集油路之间,以及同与集油路间大量泄漏,且油压下降导致松不开阀,原因是它们之间的螺钉松动,将螺钉拧紧即可消除故障:液压站油压不稳原因是液压系统中混入空气,应排除空气,或是电液调压装置线圈的电流滤波不好,线圈上下振动,造成油压不稔,加装电解电容器加强滤波即可。
4、残压过大残压过大会使制动器失去作用,其主要原因是:电液调压装置的控制杆上的档板里喷嘴距离太小:溢流同节流孔太大。
处理方法:将控制杆上档板调整或更换;将溢流阀节流孔更换宜径小一点的节流孔。
5、二级制动油压假保压性能故障产生二级制动油压保压性能故障的原因有:液压站油路块上的大溢流网内有赃物卡住使阀芯关不严;单向节流截止网开口太大,油大量泄出:电磁换向阀内有赃物,内泄漏太大。
针对这一类故障可先取下阀芯清洗,去掉脏物,使阀芯到位,然后调整单向节流截止阀,使其开口尽量开的小,起到节流补油的作用液压油缸。
液压传动系统常见故障及解决措施分析

液压传动系统常见故障及解决措施分析液压传动系统是现代机械设备中使用最广泛的一种传动方式,它具有传动力大、响应迅速、控制方便等特点。
但在使用过程中,由于设计、制造、维护的问题,会出现一些常见故障,本文对此进行分析,并提出相应的解决措施。
一、液压系统压力不够或泄漏原因分析:可能是油路系统内部漏油或压力不足导致。
或者是与外界的连接件(如油管、卡箍、垫片等)损坏或破损,导致压力泄漏。
解决方法:首先静下心分析原因,寻找出泄漏的位置和原因。
如果是与外部连接的零部件问题,可以对其进行检查和维修或更换。
如果是油路内部的问题,需要对油路进行检查,并更换损坏的部件。
如果是由于压力不足,可以调整液压系统的工作压力或更换大功率的泵。
二、液压系统噪声大原因分析:液压系统的噪声主要是由于流体在高速运动时所产生的振动和冲击声。
此外,如果配合间隙过大或发动机系统设备部件过于磨损,也会引起噪音。
解决方法:可以加装隔声罩、减震装置或增加噪声吸收材料,减轻噪声。
如果配合间隙过大或设备磨损严重,需要进行设备维修或更换,从而达到减少噪声的效果。
三、液压泵振动或声音异常原因分析:油的污秽堆积或传动链条过紧,会导致液压泵振动,发出异常的声音。
解决方法:首先需要清理油路中的污垢和积碳,调整泵的链条松散度,在正确的链条松散度下运行。
此外,可以使用地脚螺栓或加重平衡机构,增加液压泵的稳定性。
四、液压油温过高或过低原因分析:液压油的温度过高可能是由于液压油过度泄漏、液压系统运行时间过长、液压泵运动过程中受热过度等原因,导致液压油温度升高。
液压油温度过低可能是由于冷却系统设备故障、流体通过电磁阀时泄漏等。
解决方法:如果液压油过热,可以适当降低液压油系统的压力、增加系统散热条件,或降低油温测定点的温度。
如果液压油温过低,可以检查设备冷却系统,及时维护更换。
此外,也可以增加降温器和加热器等设备,从而控制液压油的温度。
五、液压缸运动不稳定且速度不一致原因分析:可能是电磁阀内部元件损坏、蒸汽阀门松动、油缸较大的压力建议过大等原因,导致液压缸的运动不稳定,速度不一致。
液压系统常见故障及消除方法

液压系统常见故障的诊断及消除方法1 常见故障的诊断方法1.1 简易故障诊断法目前采用最普遍的方法,凭个人的经验,具体做法如下:1)询问设备操作者,了解设备运行状况。
其中包括:液压系统工作是否正常;液压泵有无异常现象;液压油检测清洁度的时间及结果;滤芯清洗和更换情况;发生故障前是否对液压元件进行了调节;是否更换过密封元件;故障前后液压系统出现过哪些不正常现象;过去该系统出现过什么故障,是如何排除的等,逐一进行了解。
2)看液压系统压力、速度、油液、泄漏、振动等是否存在问题。
3)听液压系统声音:冲击声;泵的噪声及异常声;判断液压系统工作是否正常。
4)摸温升、振动、爬行及联接处的松紧程度判定运动部件工作状态是否正常。
1.2 液压系统原理图分析法根据液压系统原理图分析液压传动系统出现的故障,找出故障产生的部位及原因,并提出排除故障的方法。
结合动作循环表对照分析、判断故障就很容易了。
1.3 其它分析法液压系统发生故障时根据液压系统原理进行逻辑分析或采用因果分析等方法逐一排除,最后找出发生故障的部位,这就是用逻辑分析的方法查找出故障。
为了便于应用,故障诊断专家设计了逻辑流程图或其它图表对故障进行逻辑判断,为故障诊断提供了方便。
7.4 压力阀常见故障及处理7.6 方向阀常见故障及处理7.6.2 多路换向阀常见故障及处理7.7 液压控制系统的安装、调试和故障处理要点7.7.1 液压控制系统的安装、调试液压控制系统与液压传动系统的区别在于前者要求其液压执行机构的运动能够高精度地跟踪随机的控制信号的变化。
液压控制系统多为闭环控制系统,因而就有系统稳定性、响应和精度的需要。
为此,需要有机械-液压-电气一体化的电液伺服阀、伺服放大器、传感器,高清洁度的油源和相应的管路布置。
液压控制系统的安装、调试要点如下:1)油箱内壁材料或涂料不应成为油液的污染源,液压控制系统的油箱材料最好采用不锈钢。
2)采用高精度的过滤器,根据电液伺服阀对过滤精度的要求,一般为5~10μm。
液压系统存在的各种问题和解决办法分析

液压系统存在的问题和解决办法分析一.液压系统普遍存在的问题1.可靠性问题(寿命和稳定性)(1)国产元件质量差,不稳定;(2)设计水平低,系统不完善。
2.振动与噪音(1)系统中存在气体,没有排净。
(2)吸油管密封不好,吸进空气。
(3)系统压力高。
(4)管子管卡固定不合理。
(5)选用液压元件规格不合理,如小流量选用大通径的阀,产生低频振荡;系统压力在某一段产生共振。
3.效率问题液压系统的效率一般较低,只有80%左右或更低。
系统效率低的原因主要由于发热、漏油、回油背压大造成。
4.发热问题系统发热的原因主要由于节流调速、溢流阀溢流、系统中存在气体、回油背压大引起。
5.漏油问题(1)元件质量(包括液压件、密封件、管接头)不好,漏油。
(2)密封件形式是否合理,如单向密封、双向密封。
(3)管路的制作是否合理,管子憋劲。
(4)不正常振动引起管接头松动。
(5)液压元件连接螺钉的刚度不够,如国内叠加阀漏油。
(6)油路块、管接头加工精度不够,如密封槽尺寸不正确,光洁度、形位公差要求不合理,漏油。
6.维修问题维修难,主要原因:(1)设计考虑不周到,维修空间小,维修不便。
(2)要求维修工人技术水平高。
液压系统技术含量较高,要求工人技术水平高,出现故障,需要判断准确,不仅减少工作量,而且节约维修成本,因为液压系统充满了液压油,拆卸一次,必定要流出一些油,而这些油是不允许再加入系统中使用。
另外,拆卸过程有可能将脏东西带入系统,埋下事故隐患。
因此要求工人提高技术水平,判断正确非常必要。
7.液压系统的价格问题液压系统相对机械产品,元件制造精度高,因此成本高。
二.如何保证液压系统正常使用液压系统正常工作,需要满足以下条件:1.系统干净系统出现故障,70%都是由于系统中有脏东西如铁屑、焊渣、铁锈、漆皮等引起。
例如,这类污染物,如果堵住溢流阀中的小孔(0。
2mm)就建立不了压力;如果卡在方向阀阀芯,就导致不能换向,功能不对;如果堵住柱塞泵滑靴的小孔,就产生干摩擦,损坏泵。
液压传动系统常见故障及解决措施分析

液压传动系统常见故障及解决措施分析液压传动系统是目前工程机械中广泛应用的动力传输装置。
然而,由于系统中存在的复杂性和工作环境等诸多因素,液压传动系统往往会出现一些故障。
本文将从常见的故障入手,分析液压传动系统的故障原因及解决措施。
一、液压系统渗漏液压系统的渗漏是最常见的问题之一,容易导致系统压力下降和操作手柄变重,甚至危及机器的安全性。
渗漏问题通常分为以下两种:1.内部渗漏:内部渗漏是指在系统中流体的漏失量,如泵、阀、密封等部件中的漏油。
一般情况下,导致内部渗漏的原因有以下几点:(1)油液粘度不合适导致泄漏。
如果油液粘度过低,会导致泄漏增加;反之,过高则会增加系统的阻力,影响机器的运行效率。
(2)密封体老化、磨损导致泄漏。
密封体老化、磨损也是导致内部泄漏的主要原因之一。
(3)安装不当导致泄漏。
如接头紧固不当、密封圈装反等,这些安装错误都会导致泄漏。
(1)管路接头不严密。
管路连接不严密也是外部渗漏的主要原因之一,一般情况下可以用扳手或扳手梭紧固接头来解决。
(2)油箱鼓包导致泄漏。
油箱鼓包会导致油箱的密封性下降,因此需要及时更换或修理,以减少泄漏。
二、液压系统压力不足液压系统压力不足通常是由于液压泵无法输出合适的压力引起的。
导致系统压力不足的原因有以下几点:(1)油泵损坏。
油泵损坏致使输出的压力低于要求,它的原因主要为零件磨损、泵轴非正轴、泵内漏等。
(2)回油管路阻塞。
回油管路阻塞会导致油无法流回油箱,压力在系统中逐渐增加。
(3)压力调节阀故障。
压力调节阀故障也是导致系统压力不足的主要原因之一。
液压系统过载常常会导致系统崩溃、机器停工等严重后果。
液压系统过载的原因有以下几点:(1)或操作负荷变重。
当机器运行时,操作负荷突然变得很重,导致压力大幅度上升,从而导致压力过载。
(2)负载不平衡。
当机器在施工现场运行时,由于工况不同,某些部位的负载可能会突然增加,导致压力突然上升。
(3)泵能力不足。
泵的输出量小于要求时,也会导致系统过载。
液压系统常见故障分析及维修方法
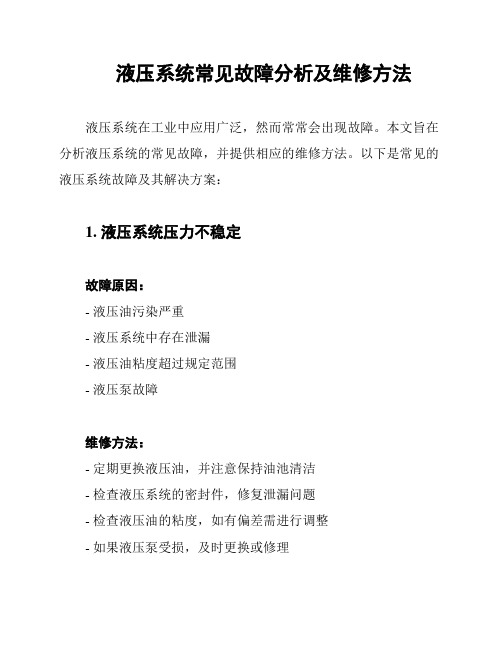
液压系统常见故障分析及维修方法液压系统在工业中应用广泛,然而常常会出现故障。
本文旨在分析液压系统的常见故障,并提供相应的维修方法。
以下是常见的液压系统故障及其解决方案:1. 液压系统压力不稳定故障原因:- 液压油污染严重- 液压系统中存在泄漏- 液压油粘度超过规定范围- 液压泵故障维修方法:- 定期更换液压油,并注意保持油池清洁- 检查液压系统的密封件,修复泄漏问题- 检查液压油的粘度,如有偏差需进行调整- 如果液压泵受损,及时更换或修理2. 液压系统工作缓慢故障原因:- 液压油温度过高- 液压泵进油口堵塞- 液压泵内部磨损维修方法:- 定期检查液压油的温度,如超过标准范围,考虑增加散热装置或更换液压油- 检查液压泵进油口,如有堵塞需要清除- 如果液压泵内部磨损严重,需要修理或更换泵体或泵内部零件3. 液压油泄漏故障原因:- 液压系统密封件老化或损坏- 系统安装不当- 油管松动或磨损维修方法:- 检查液压系统密封件,如有老化或损坏,及时更换- 检查液压系统的安装,确保无渗漏或松动- 检查油管连接,如有松动或磨损,及时进行修复或更换4. 液压执行机构动作不准确故障原因:- 液压执行机构内部存在异物或堵塞- 液压执行机构密封件老化或损坏维修方法:- 检查液压执行机构内部,清除可能存在的异物或堵塞- 检查液压执行机构的密封件,如有老化或损坏,及时更换5. 液压系统噪音大故障原因:- 液压油中存在气体- 液压泵内部损坏维修方法:- 检查液压油,如存在气体,需进行排气处理- 检查液压泵,如有损坏,及时修理或更换泵体或泵内部零件以上是液压系统常见故障的分析与维修方法,希望对您有所帮助。
在实际操作中,请运用这些方法进行故障排除,并定期维护液压系统,以确保其正常运行。
压裂整改措施

压裂整改措施引言压裂技术是一种在钻井和油藏开采过程中常用的方法,它通过将高压液体注入井下,以分裂地层岩石,增加原油或天然气的采取效率。
然而,压裂操作也存在一些环境和安全风险,需要进行整改措施来确保操作的安全可靠性。
本文将介绍压裂操作中常见的问题,对这些问题提出整改措施和建议。
这些措施旨在降低压裂操作的环境影响、提高操作安全性,并促进能源行业的可持续发展。
压裂操作中存在的问题在压裂操作中,可能存在以下问题:1.水资源消耗过量:压裂过程需要大量的水用于注入地下,这可能导致水资源的过度消耗。
2.化学品使用和泄漏:压裂作业中使用各种化学品,如果未妥善管理,可能会对环境造成污染,并对工作人员的健康造成危害。
3.地震活动:压裂作业可能引起地下地震活动,这可能导致地下水源变得不稳定,甚至可能引发地震。
4.噪音和振动:压裂作业会产生噪音和振动,对附近的居民和野生动物造成干扰和困扰。
压裂整改措施和建议为了解决上述问题,以下是一些建议的整改措施:1. 水资源管理•研究并采用节水技术:研发和采用节水技术,降低压裂过程中对水资源的需求量。
•水资源回收和再利用:开发水资源回收和再利用技术,将回收的水用于后续的压裂操作,减少对淡水资源的依赖。
•推广使用替代水源:开展研究,鼓励和支持使用替代水源,如海水、废水等,来替代淡水用于压裂操作。
2. 化学品管理•使用环境友好型化学品:选用对环境影响较小的化学品,减少对地下水和土壤的污染风险。
•健康与安全培训:提供必要的培训和教育,确保工作人员对化学品的正确使用和处理有充分的了解。
•定期检查和维护设备:确保设备的正常运行和泄漏的及时修复,防止化学品的泄漏和外溢。
3. 地震风险管理•地质勘探和评估:在进行压裂操作之前,进行充分的地质勘探和评估,以了解地下地质情况和潜在的地震风险。
•控制注入压力:对注入的压力进行严格控制,以减少引发地震的可能性。
•监测地震活动:建立地震监测网络,及时监测地下地震活动的变化,对异常情况进行及时预警和处理。
液压系统的异常现象分析及预防措施
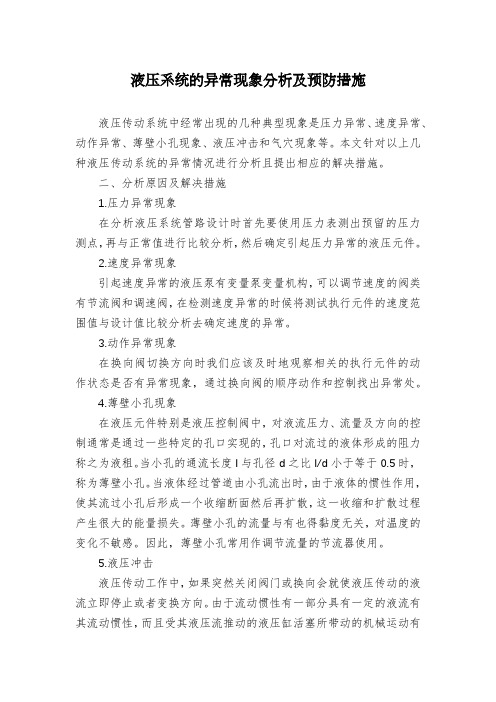
液压系统的异常现象分析及预防措施液压传动系统中经常出现的几种典型现象是压力异常、速度异常、动作异常、薄壁小孔现象、液压冲击和气穴现象等。
本文针对以上几种液压传动系统的异常情况进行分析且提出相应的解决措施。
二、分析原因及解决措施1.压力异常现象在分析液压系统管路设计时首先要使用压力表测出预留的压力测点,再与正常值进行比较分析,然后确定引起压力异常的液压元件。
2.速度异常现象引起速度异常的液压泵有变量泵变量机构,可以调节速度的阀类有节流阀和调速阀,在检测速度异常的时候将测试执行元件的速度范围值与设计值比较分析去确定速度的异常。
3.动作异常现象在换向阀切换方向时我们应该及时地观察相关的执行元件的动作状态是否有异常现象,通过换向阀的顺序动作和控制找出异常处。
4.薄壁小孔现象在液压元件特别是液压控制阀中,对液流压力、流量及方向的控制通常是通过一些特定的孔口实现的,孔口对流过的液体形成的阻力称之为液租。
当小孔的通流长度l与孔径d之比l/d小于等于0.5时,称为薄壁小孔。
当液体经过管道由小孔流出时,由于液体的惯性作用,使其流过小孔后形成一个收缩断面然后再扩散,这一收缩和扩散过程产生很大的能量损失。
薄壁小孔的流量与有也得黏度无关,对温度的变化不敏感。
因此,薄壁小孔常用作调节流量的节流器使用。
5.液压冲击液压传动工作中,如果突然关闭阀门或换向会就使液压传动的液流立即停止或者变换方向。
由于流动惯性有一部分具有一定的液流有其流动惯性,而且受其液压流推动的液压缸活塞所带动的机械运动有一定的惯性,两种惯性的作用造成液压系统中局部内压力突然急速变化,瞬间使内部压力急剧增加,行成一股液流压力冲击。
这种液流冲击作用在输油管管壁上会产生很大的冲击声,严重时有可能造成输油管破裂或者损坏液压系统零部件。
这种突发现象,通常被称为水锤现象。
液压冲击现象的预防与排除方法:(1)在容易发生液压冲击的地方,安装有蓄能器。
安装蓄能器的主要作用是吸收冲击压力。
液压传动系统常见故障及解决措施分析

液压传动系统常见故障及解决措施分析液压传动系统在工程机械、航空航天、冶金、石油化工等领域得到广泛应用,它具有传动效率高、传动动力大、反应速度快、可靠性高等优点。
液压传动系统也存在着一些常见的故障问题,今天我们就来分析一下液压传动系统常见故障及解决措施。
1. 液压系统泄漏故障液压系统泄漏是液压系统中最为常见的问题之一,如果液压系统存在泄漏,将会导致液压油压力下降,使得系统无法正常工作。
液压系统泄漏的原因可能是液压管路接头处密封不良、密封圈老化磨损、液压油箱内部密封件损坏等。
解决措施:(1)对于液压管路接头处密封不良的情况,可以重新拧紧螺母,或者更换密封垫片。
(2)对于密封圈的老化磨损,需要及时更换密封圈,保证密封效果。
(3)液压油箱内部密封件损坏时,需要清洗油箱,并更换密封件。
2. 液压系统压力过高或过低故障液压系统的工作压力是由泵站输出的压力决定的,如果液压系统的压力过高或者过低都会导致液压系统无法正常工作。
这种故障可能是由于液压泵的失效、阀门堵塞、泄漏等原因引起的。
解决措施:(1)对于液压泵的失效,需要及时更换液压泵。
(2)对于阀门的堵塞,需要清洗或更换阀门。
(3)对于泄漏的情况,需要按照前面提到的方法进行处理。
液压系统在工作过程中如果出现异常振动或噪音,说明液压系统可能存在问题。
液压系统振动或噪音的原因可能是由于液压泵失调、阀门不稳定、油液污染等引起的。
液压传动系统常见故障及解决措施可以通过定期的检查维护来避免和解决。
只有及时发现问题,采取正确的解决措施,才能保证液压传动系统的正常工作,延长设备的使用寿命。
希望大家在使用液压传动系统的能够加强对其维护及检查,确保其安全可靠的工作。
机械设备液压系统常见故障原因分析和应对措施

机械设备液压系统常见故障原因分析和应对措施机械设备液压系统是一种常见的动力传递系统,常见于工程机械、农业机械、航空航天设备以及其他需要大功率输出的设备中。
由于液压系统是一个复杂的系统,它容易受到各种因素影响而出现故障。
本文将分析液压系统常见的故障原因,并提出相应的应对措施,以帮助读者更加深入地了解和掌握液压系统的维护和维修知识。
一、液压系统常见故障原因分析1. 液压系统漏油故障液压系统漏油是液压系统常见的故障,主要原因有:(1)密封件老化:液压系统中的密封件随着使用时间的增长会出现老化、硬化,从而导致液压系统漏油。
(2)密封件破损:密封件在使用过程中会受到各种因素的影响,如高温、高压等,从而导致密封件破损。
(3)安装不当:液压系统的密封件在安装时如果操作不当,如未正确安装密封圈、密封面粗糙等,也会导致液压系统漏油。
液压系统压力不稳主要原因有:(1)油液污染:液压系统油液污染严重会导致油液中的杂质在液压系统中积聚,从而导致油液的黏度增大,影响系统的工作压力。
(2)液压泵损坏:液压泵是液压系统的核心组件,如果泵的油封、叶轮损坏,会影响液压系统的工作压力。
(3)调压阀故障:液压系统中的调压阀如果出现故障,也会导致液压系统的工作压力不稳。
液压系统噪音大的原因有:(1)液压泵损坏:液压泵在工作时如果叶片磨损严重或轴承损坏,会导致液压系统噪音大。
(2)阀体损坏:液压系统中的阀体如果损坏,也会产生噪音。
(3)管路磨损:液压系统中的管路如果磨损严重,也会产生噪音。
2. 液压系统压力不稳故障的应对措施(1)定期更换液压系统油液:定期更换液压系统中的油液,避免油液污染严重导致油液黏度增大。
(2)定期检查液压泵:定期检查液压泵的油封、叶轮等零部件,及时发现并处理液压泵的故障。
(3)定期检查调压阀:定期检查液压系统中的调压阀,及时发现并处理调压阀的故障。
压裂施工过程中常见问题及应对措施

压裂施工过程中常见问题及应对措施摘要:压裂为油水井增产增注的重要措施,越来越多的应用到油层的改造上来,本文通过分析在压裂施工过程中遇到的问题,并提出相应的解决办法,为压裂施工的成功实施提供经验。
关键词:压裂常见问题应对措施压裂施工的成功与否涉及到方方面面,包括地下、井筒及地面等,在多年的压裂施工监督中,总结了以下5种压裂施工中常见的问题及解决办法。
1 配错或下错管柱(1)单层压裂:单层压裂施工一般是用一级封隔器来保护压裂层上部套管,或用两级封隔器来隔离目的层与其它油层。
如果压裂管柱下错,使封隔器卡在射孔炮眼上,压裂时压裂液就会通过封隔器上面的炮眼进入套管形成套喷。
处理措施:正确丈量计算下井管柱。
(2)多层压裂时管柱配错,对压裂施工是极其危险的,出现的情况也很复杂,包括:压不开、套喷、油管打洞、损坏封隔器、卡管柱等一系列严重问题,一旦发现有套喷现象,要立即终止施工,核对井场管柱记录或上磁测查找原因。
2 压裂砂堵发生砂堵的原因主要有:(1)前置液少,动态缝宽不够,容易形成砂堵。
(2)加砂过程中,由于设备损坏、仪器故障停车更换或修理,中途停泵时间长,造成沉砂堵。
这些故障有多种情况:压裂车抽空、混砂车零部件故障、计算机系统失灵、井口设备破裂。
(3)压裂液滤失严重砂比提升过快,造成砂堵。
解决办法:若出现砂堵,应立即放喷或反循环洗井,压力正常后,泵入前置液,如果压力稳定可恢复压裂施工。
3 压裂封隔器出现问题Y531型压裂封隔器自1997年投入使用以来,经过多次改型,其工艺技术已经成熟。
失效原因除部分受到井内温度(高温)等恶劣环境影响外,大部分是因为工具质量不稳定造成的。
主要表现为:(1)封隔器胶筒耐温耐压不达标,工作时胶筒破裂失去密封;水力锚锚定机构选材和装配缺陷,造成管柱在高压下窜动,封隔器失去密封;出现问题的井有D6-4井(封隔器失效)、E55-X9(封隔器失效)。
(2)水力锚爪回复机构故障,导致压裂放喷压井后,起管柱遇卡,这种情况较多,E72-斜2井、E 7-斜17井、D80-斜91井等6口。
液压系统常见故障及解决方法

液压系统常见故障及解决方法液压系统作为工程机械和工业设备中常见的动力传输系统,其稳定运行对设备的正常工作至关重要。
然而,在使用过程中,液压系统也会出现一些常见的故障,给设备的正常运行带来困扰。
本文将对液压系统常见故障及解决方法进行介绍,希望能够帮助大家更好地了解和维护液压系统。
1. 液压系统漏油。
液压系统漏油是液压系统中常见的故障之一。
漏油可能会导致液压系统压力下降,甚至无法正常工作。
漏油的原因可能是密封件老化、损坏或安装不当,管路连接松动等。
解决方法包括及时更换密封件、加强管路连接处的紧固,确保液压系统的密封性。
2. 液压系统压力不稳定。
液压系统压力不稳定会导致设备运行不稳定,甚至影响设备的正常工作。
这可能是由于液压泵内部损坏、油液污染、液压阀故障等原因造成的。
解决方法包括检修或更换液压泵、清洗油液、更换液压阀等。
3. 液压系统温升过高。
液压系统温升过高会导致液压油的氧化加剧,降低了液压油的使用寿命,甚至会引发其他故障。
温升过高的原因可能是液压油油温过高、冷却系统故障等。
解决方法包括检查冷却系统是否正常工作、更换液压油等。
4. 液压系统噪音过大。
液压系统噪音过大可能是由于液压泵内部损坏、液压阀不稳定、管路连接松动等原因引起的。
解决方法包括检修或更换液压泵、调整液压阀、加强管路连接处的紧固等。
5. 液压缸漏油。
液压缸漏油会导致液压缸无法正常工作,影响设备的使用。
漏油的原因可能是密封件老化、损坏或安装不当等。
解决方法包括及时更换液压缸密封件、检查液压缸安装是否合理等。
综上所述,液压系统常见故障的解决方法主要包括及时更换密封件、加强管路连接处的紧固、检修或更换液压泵、清洗油液、更换液压阀、检查冷却系统是否正常工作等。
在日常使用中,定期对液压系统进行检查和维护,及时发现并解决问题,是保证液压系统正常运行的关键。
希望本文所介绍的内容能够对大家有所帮助,让液压系统能够更加稳定、高效地运行。
压裂施工过程中常见问题及应对措施

压裂施工过程中常见问题及应对措施摘要:压裂为油水井增产增注的重要措施,越来越多的应用到油层的改造上来,本文通过分析在压裂施工过程中遇到的问题,并提出相应的解决办法,为压裂施工的成功实施提供经验。
关键词:压裂常见问题应对措施压裂施工的成功与否涉及到方方面面,包括地下、井筒及地面等,在多年的压裂施工监督中,总结了以下5种压裂施工中常见的问题及解决办法。
1 配错或下错管柱(1)单层压裂:单层压裂施工一般是用一级封隔器来保护压裂层上部套管,或用两级封隔器来隔离目的层与其它油层。
如果压裂管柱下错,使封隔器卡在射孔炮眼上,压裂时压裂液就会通过封隔器上面的炮眼进入套管形成套喷。
处理措施:正确丈量计算下井管柱。
(2)多层压裂时管柱配错,对压裂施工是极其危险的,出现的情况也很复杂,包括:压不开、套喷、油管打洞、损坏封隔器、卡管柱等一系列严重问题,一旦发现有套喷现象,要立即终止施工,核对井场管柱记录或上磁测查找原因。
2 压裂砂堵发生砂堵的原因主要有:(1)前置液少,动态缝宽不够,容易形成砂堵。
(2)加砂过程中,由于设备损坏、仪器故障停车更换或修理,中途停泵时间长,造成沉砂堵。
这些故障有多种情况:压裂车抽空、混砂车零部件故障、计算机系统失灵、井口设备破裂。
(3)压裂液滤失严重砂比提升过快,造成砂堵。
解决办法:若出现砂堵,应立即放喷或反循环洗井,压力正常后,泵入前置液,如果压力稳定可恢复压裂施工。
3 压裂封隔器出现问题Y531型压裂封隔器自1997年投入使用以来,经过多次改型,其工艺技术已经成熟。
失效原因除部分受到井内温度(高温)等恶劣环境影响外,大部分是因为工具质量不稳定造成的。
主要表现为:(1)封隔器胶筒耐温耐压不达标,工作时胶筒破裂失去密封;水力锚锚定机构选材和装配缺陷,造成管柱在高压下窜动,封隔器失去密封;出现问题的井有D6-4井(封隔器失效)、E55-X9(封隔器失效)。
(2)水力锚爪回复机构故障,导致压裂放喷压井后,起管柱遇卡,这种情况较多,E72-斜2井、E 7-斜17井、D80-斜91井等6口。
液压站使用过程出现的问题以及解决措施

液压站使用过程出现的问题以及解决措施液压系统使用过程为了防止提升机发生过速、过卷等意外事故,采用了不少保护设备。
将保护设备有机地联系在一起,形成了电控装置中的重要控制回路:安全回路。
现以多绳摩擦提升机采用安全回路为例,分析安全回路的保护作用。
安全回路中串有很多保护设备的触头,提升机工作不正常时,相应触头断开,安全接触器线圈AC失电。
1)油压上升较慢,造成松闸滞后现象的检查和处理。
①油管和液压缸内有空气,应放掉空气。
②安全阀进油量小,应检查滑阀和阀体尺寸以及安全阀电磁铁T 作行程是否为llmm,电磁铁是否下到底。
2)液压站有时出现失压现象的检查和处理①电液调压装置的动线圈引出线焊接不牢,突然断掉,有的焊接处虚焊,对辊式破碎机厂家造成断续失压现象,应重新焊牢。
②油脏造成调压装置的节流孔被堵,应立即清洗并更换制动油。
③有的矿井加油注入速度过快时,造成油箱沉淀物向上浮动,堵住节流孔及油中混入空气等造成失压,故加油时应缓慢加入,另一方面要注意保持使用中压力油的清洁。
④电液调节装置上的十字弹簧必须如图10 -8所示,用M3 x6的螺钉紧固,十字弹簧调整后上下螺母必须拧紧,以免十字弹簧位移和松动造成失压和油压失调现象。
3)有少量液压站在使用中发现油压振溢现象的检查和处理。
①电液调压装置上的可动线圈输入的直流电,如滤波不净夹有交流成份,将能引起磁力方向的变化,造成油压振动,应检查整流和滤波质量,如二极管和电容已坏,应设法更换,以提高滤波质量。
②油压系统中贮有空气易引起油压振动,必须利用盘形制动器上的放气孔,排除系统中的气体。
③喷嘴孔与溢流阀中的节流孔比例失调,容易引起振动现象,可分别试换成直径φ0.8、φ0.9、φ1、φ1.1、φ1.2mm的节流孔,以选配其中一个不振溢的节流孔。
④油泵系统中的管子安装时必须设法固定,否则反击破碎机价格容易引起油压振动现象。
4)油压不稳定,有时压力会突然自动下降,然后又慢慢恢复到最大值,也就是所谓的压力波动,其原因主要是加油或将油搅动时混入空气,并将沉淀杂质搅起所致。
油田压裂设备管理存在的问题与措施
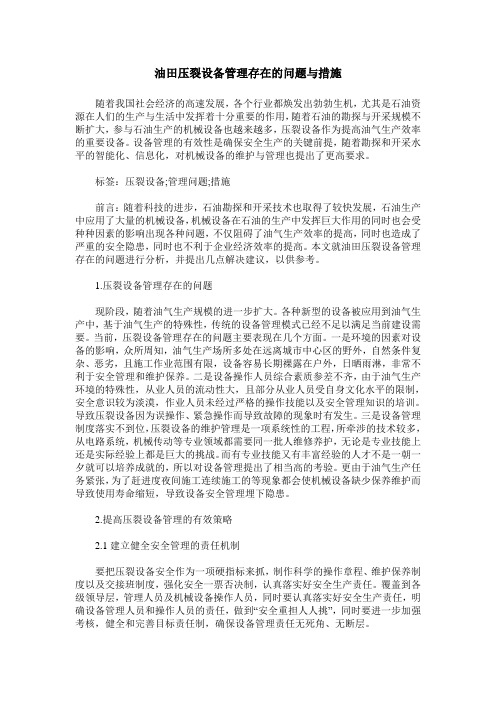
油田压裂设备管理存在的问题与措施随着我国社会经济的高速发展,各个行业都焕发出勃勃生机,尤其是石油资源在人们的生产与生活中发挥着十分重要的作用,随着石油的勘探与开采规模不断扩大,参与石油生产的机械设备也越来越多,压裂设备作为提高油气生产效率的重要设备。
设备管理的有效性是确保安全生产的关键前提,随着勘探和开采水平的智能化、信息化,对机械设备的维护与管理也提出了更高要求。
标签:压裂设备;管理问题;措施前言:随着科技的进步,石油勘探和开采技术也取得了较快发展,石油生产中应用了大量的机械设备,机械设备在石油的生产中发挥巨大作用的同时也会受种种因素的影响出现各种问题,不仅阻碍了油气生产效率的提高,同时也造成了严重的安全隐患,同时也不利于企业经济效率的提高。
本文就油田压裂设备管理存在的问题进行分析,并提出几点解决建议,以供参考。
1.压裂设备管理存在的问题现阶段,随着油气生产规模的进一步扩大。
各种新型的设备被应用到油气生产中,基于油气生产的特殊性,传统的设备管理模式已经不足以满足当前建设需要。
当前,压裂设备管理存在的问题主要表现在几个方面。
一是环境的因素对设备的影响,众所周知,油气生产场所多处在远离城市中心区的野外,自然条件复杂、恶劣,且施工作业范围有限,设备容易长期裸露在户外,日晒雨淋,非常不利于安全管理和维护保养。
二是设备操作人员综合素质参差不齐,由于油气生产环境的特殊性,从业人员的流动性大,且部分从业人员受自身文化水平的限制,安全意识较为淡漠,作业人员未经过严格的操作技能以及安全管理知识的培训。
导致压裂设备因为误操作、紧急操作而导致故障的现象时有发生。
三是设备管理制度落实不到位,压裂设备的维护管理是一项系统性的工程,所牵涉的技术较多,从电路系统,机械传动等专业领域都需要同一批人维修养护,无论是专业技能上还是实际经验上都是巨大的挑战。
而有专业技能又有丰富经验的人才不是一朝一夕就可以培养成就的,所以对设备管理提出了相当高的考验。
- 1、下载文档前请自行甄别文档内容的完整性,平台不提供额外的编辑、内容补充、找答案等附加服务。
- 2、"仅部分预览"的文档,不可在线预览部分如存在完整性等问题,可反馈申请退款(可完整预览的文档不适用该条件!)。
- 3、如文档侵犯您的权益,请联系客服反馈,我们会尽快为您处理(人工客服工作时间:9:00-18:30)。
( 安全管理 )
单位:_________________________
姓名:_________________________
日期:_________________________
精品文档 / Word文档 / 文字可改
压裂车液压系统存在问题及改
进措施(新编版)
Safety management is an important part of production management. Safety and production are in
the implementation process
压裂车液压系统存在问题及改进措施(新
编版)
压裂泵车是油田实施压裂酸化作业的关键设备,压裂泵车中的液压系统是保证其正常工作的关键系统,而在现场施工中,经常会遇到液力变矩器油液变质而使润滑系统不能正常工作的问题,严重影响着酸化压裂施工的连续性,同时油液的变质也使得液力变矩器寿命缩短。
基于此,本文以四机厂生产的TYL105型酸化压裂泵车为例,在充分的现场调研分析的基础上,对其液压系统提出了改进措施,以期改善其运行状态。
压裂泵车是油田实施压裂酸化作业的关键设备,其主要作用是利用压裂泵车将携带有支撑剂的压裂液打入储层,在储层中撑开人工裂缝而形成原有通道,从而提高油井产量。
在压裂泵车中液压系统是保证其正常工作的关键系统,在施工作业时,台上柴油机通过
液力变矩器和万向轴驱动减速器,将动力传递给柱塞,同时从液力变矩器取力而驱动液力端和动力端润滑油泵,实现对系统的润滑。
而在现场施工中,经常会遇到液力变矩器油液变质而导致润滑系统难以正常工作的问题,使压裂作业被迫中断,严重影响了酸化施工的连续性,而且一旦油液变质就需要进行重新更换,这将大大增加设备使用成本,同时会缩短液力变矩器的使用寿命。
为此本文以四机厂生产的TYL105型压裂泵车为例,在充分调研和分析的基础上,提出了对液力变矩器上的取力结构进行优化改造的措施。
液力变矩器结构及其润滑方式
从液力变矩器结构上分析,影响油液变质的结构方面的原因主要集中在液力变矩器的动力端和液力端。
1.1.动力端
压裂泵车的动力端主要由传动轴、连杆、曲轴、十字头滑块、导板和壳体等部分构成,其主要作用是将传动轴过来的旋转动力转换为柱塞的往复运动动力,其中传动轴、曲轴及导板分别安装在壳体的固定支撑部位上,而十字头滑块则通过其内部的螺纹与液力端
的柱塞相连接。
传动轴和曲轴都采用合金钢热锻而成,两轴之间通过人字齿轮实现动力传递。
曲轴上均匀的分布着相互夹角为120°的三个曲柄轴颈,曲柄轴颈和主轴颈的偏心距为120mm。
连杆的两端是滑块轴承,在曲轴轴颈部位安装有一个剖分式双金属轴瓦,而在十字头滑块部位则是一个铜套。
这里的剖分式双金属片轴瓦的内表面因其使用条件不同而有所不同,其中连杆上的轴瓦内表面上浇铸了一层锡锑合金,以使其达能够承受高压冲击;而连杆下轴瓦内表面则设置了一条环形槽,作为手机曲轴轴颈上面的油通道,以保证油液不流出曲轴,并通过轴瓦下面的连杆上制的环形槽将油池与润滑管连通。
这两种轴承的位置是不可调整的,当轴瓦间隙大于0.30mm,铜套间隙大于0.25mm时,其磨损程度就已达到其使用极限,这是就需要对这些零部件进行更换。
另外,在十字头滑块配有青铜滑板在钢制导板经过热处理的工作表面上滑动,十字头滑块和导板之间的间隙超过1.2mm时,就已达到其许用极限,需要对其进行调整,这是可以通过更换位于导板和泵壳之间的垫片或更换已磨损的滑板来使其达到使用要求,而不需要再使用在导板表面上镀层的方法来调
整。
动力端所采用的润滑方式为:以柱塞泵的泵壳作为动力端的润滑油池,润滑油被齿轮泵从润滑油池中吸出,并通过滤清器和分配管,分别流向曲柄两端的油孔,达到对主轴轴颈和连杆轴颈的润滑,同时喷射到两端和中间两个轴承上,流到十字轴销轴,齿轮则为飞溅润滑。
1.2.液力端
压裂泵车液力变矩器的液力端主要由泵头体、凡尔总成、凡尔座、柱塞、缸套、密封组件等部分构成。
泵头体由分体式合金钢锻造而成,并通过M39螺栓和盘根盒连接在一起,吸入和排出凡尔总成都采用了相同的材质和结构,其结构上由凡尔体、凡尔和凡尔盖等部件组成,其中凡尔座和凡尔体的配合锥角为55°,凡尔与泵头体的配合锥度为16度,凡尔座的通孔半径为40mm。
柱塞首先用特殊的螺母和拉杆固定,然后拉杆直接被固定在十字头滑块上,柱塞规格为100mm。
并用缸套压帽将缸套固定在泵头体上。
其润滑方式为,齿轮泵动盘根盒中吸取润滑油,并通过管线将其输送至柱塞出实现
润滑。
油液变质原因分析
液力变矩器液力端、液力端的机油泵都被安装与液力变矩器的侧面,并通过取力器在液力变矩器上取力而得到动力。
经过上文对液力变矩器动力端和液力端及其润滑方式的分析,不难看出引起液力变矩器油液变质的原因主要两个方面:一是动力端机油泵密封件失效。
当柱塞盘根的弹性头密封圈失效后酸液就会沿着管线进入大泵的驱动箱中,而对大泵中的齿轮油造成污染,使其变质;然后通过大泵的额润滑驱动管道进入齿轮泵,并对齿轮泵的油封造成破坏,从而使酸液持续不断地进入液力变矩器内部,导致液力变矩器内的油液增多,大泵油液减少。
这时候设备操作人员仅仅通过观察液面的方法很难及时发现问题;二是液力端机油泵密封件失效。
当动力端缸套密封圈、盘根的密封性能劣化或丧失后,油、酸液的混合物就会沿着润滑管线进入盘根盒内部,导致盘根盒内的机油变质;三是当润滑柱塞的机油泵的密封件失效后,油、酸的混合液将沿着机油泵和液力变矩器相连接的管道进入液力变速器内部,使液力变矩
器内油面上升,大泵油面下降。
同样,操作手仅靠观察液面来判断是不科学的。
一般而言,液力变速器的油液没工作1000h时需要进行更换,然而由于出现以上原因,会使液力变矩器的油液迅速劣化,需要平均每工作100~120h就需要更换,而更换一次需要95L左右的油液,造成了大量的浪费,且给压裂作业埋下了安全隐患。
液压系统改进措施
当齿轮泵的油封失效后,润滑油和酸液就会通过取力器两端机油泵进入液力变矩器内,为了防止液力变矩器油劣化变质,有必要采取措施阻止杂质进入液力变矩器内部,通过现场调研、查阅资料,并对改进的可行性进行分析,最终提出如下个改进措施。
3.1.保证齿轮泵油封及盘根等密封件的质量过关
齿轮泵油封和盘根劣化失效时导致润滑油窜入液力变矩器内的重要原因,因此在更换油封时严把质量关,从源头上杜绝劣质密封件,从而防止大泵油、盘根盒内润滑油不变质,以此来保证液力变矩器的良好运行,延长其使用寿命。
3.2.改造取力器两端的润滑油泵
齿轮泵的动力是有取力器从液力变矩器上取得的,取力器是连接液力变矩器和齿轮泵的重要部件,因此在压裂车工作时要密切监测取力器两端油泵的工作状态,这样才能有效的防范大泵及盘根盒内润滑油窜入到液力变矩器内。
具体的改进措施有两个方面:一是在取力器上装设报警信号等,具体方法是首先在取力器通道上打一直径10mm的小孔,然后在小孔内安装一个螺钉式的液体传感器,并在操作台上安装以声光报警器,将传感器输出端与报警器相连,并将接入24V电源,这样一旦油封失效而酸液通过油封进入通道槽内时,就会触动传感器,而使声光报警器点亮并发出报警声,以引起操作人员注意,及时查找原因并整改;二是在取力器通道底部安装一条回油管线。
方法是首先在取力器通道底部开一个小孔,并安装一个放油阀,阀另一端接回油管线至盘根盒。
这样在作业中,如果齿轮泵油窜入到取力器通道槽内,声光报警器触发,操作人员可以立即停泵并打开放油阀门,窜入到取力器通道槽内的油液通过回油管循环至盘根盒内,这是可以继续施工,待施工完毕后对其进行整改处理。
这样既避免了变质的润滑油进入液力变矩器内,同时又保
证了施工的连续性。
经过上述改进,大大的延长了液力变矩器润滑油使用时间,改进前需要每隔70~100h更换一次,而改进后延长至700~800h。
而且经过改进提高了液力变矩器的运行性能,保证了施工的延续性,提高了酸化施工的成功率和保证了施工质量。
可以说,该项改造不经给压裂施工单位创造了可观的经济效益,节约了大量的人力和物力,具有广阔的推广应用价值。
云博创意设计
MzYunBo Creative Design Co., Ltd.。