锂电池活化阶段对电池性能的影响
电池循环性能影响
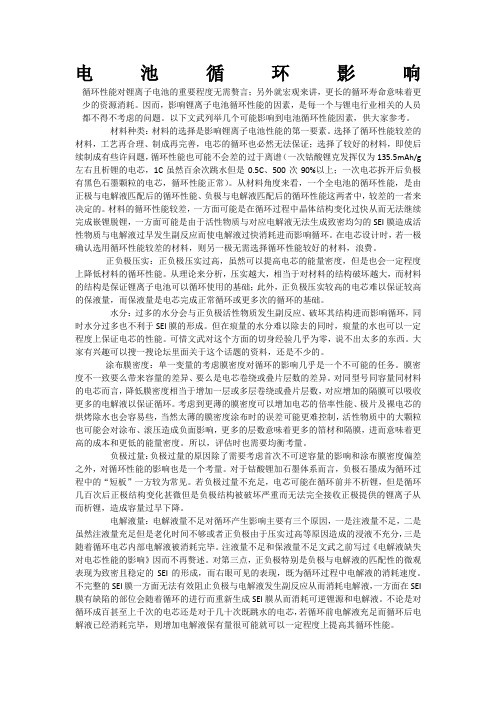
电池循环影响循环性能对锂离子电池的重要程度无需赘言;另外就宏观来讲,更长的循环寿命意味着更少的资源消耗。
因而,影响锂离子电池循环性能的因素,是每一个与锂电行业相关的人员都不得不考虑的问题。
以下文武列举几个可能影响到电池循环性能因素,供大家参考。
材料种类:材料的选择是影响锂离子电池性能的第一要素。
选择了循环性能较差的材料,工艺再合理、制成再完善,电芯的循环也必然无法保证;选择了较好的材料,即使后续制成有些许问题,循环性能也可能不会差的过于离谱(一次钴酸锂克发挥仅为135.5mAh/g 左右且析锂的电芯,1C虽然百余次跳水但是0.5C、500次90%以上;一次电芯拆开后负极有黑色石墨颗粒的电芯,循环性能正常)。
从材料角度来看,一个全电池的循环性能,是由正极与电解液匹配后的循环性能、负极与电解液匹配后的循环性能这两者中,较差的一者来决定的。
材料的循环性能较差,一方面可能是在循环过程中晶体结构变化过快从而无法继续完成嵌锂脱锂,一方面可能是由于活性物质与对应电解液无法生成致密均匀的SEI膜造成活性物质与电解液过早发生副反应而使电解液过快消耗进而影响循环。
在电芯设计时,若一极确认选用循环性能较差的材料,则另一极无需选择循环性能较好的材料,浪费。
正负极压实:正负极压实过高,虽然可以提高电芯的能量密度,但是也会一定程度上降低材料的循环性能。
从理论来分析,压实越大,相当于对材料的结构破坏越大,而材料的结构是保证锂离子电池可以循环使用的基础;此外,正负极压实较高的电芯难以保证较高的保液量,而保液量是电芯完成正常循环或更多次的循环的基础。
水分:过多的水分会与正负极活性物质发生副反应、破坏其结构进而影响循环,同时水分过多也不利于SEI膜的形成。
但在痕量的水分难以除去的同时,痕量的水也可以一定程度上保证电芯的性能。
可惜文武对这个方面的切身经验几乎为零,说不出太多的东西。
大家有兴趣可以搜一搜论坛里面关于这个话题的资料,还是不少的。
化成工艺对磷酸铁锂锂离子电池性能的影响

化成工艺对磷酸铁锂锂离子电池性能的影响闻人红雁;毛松科;田德祥【摘要】采用磷酸铁锂-石墨作为正负极材料制备超大容量叠片式单体电池(200Ah),分析两种不同化成工艺对锂离子电池性能的影响.分析了不同化成工艺后对应的电池负极的表面情况、电池内阻大小以及单体电池放电容量和循环性能等.结果显示,适当降低充电电压,有利于负极表面SEI膜的形成,并且形成的负极极片表面光滑,制备的电池具有更好的化成性能和循环性能.【期刊名称】《材料科学与工程学报》【年(卷),期】2016(034)003【总页数】4页(P372-374,426)【关键词】磷酸铁锂大容量电池;化成工艺;循环寿命【作者】闻人红雁;毛松科;田德祥【作者单位】浙江佳贝思绿色能源有限公司,浙江余姚315400;浙江佳贝思绿色能源有限公司,浙江余姚315400;浙江佳贝思绿色能源有限公司,浙江余姚315400【正文语种】中文【中图分类】TB34随着石油资源的枯竭和价格高涨以及环境污染问题的日益突出,电动汽车包括纯电动、混合动力汽车受到世界各国的广泛重视,而高性能的动力电池是电动汽车的核心技术之一。
锂离子电池具有高比能量、无记忆效应、绿色环保等特点,作为电动汽车用动力电池具有其它二次电池无法比拟的优势[1-3],特别是以橄榄石结构LiFePO4为正极材料的锂离子电池,以其资源丰富、环境友好、价格低廉、循环性能好以及过充电安全性高等优点,成为目前车用动力电池的首选之一[4-6]。
在锂离子电池制备过程中,化成是一道重要的工序,化成即对注液搁置后的电池进行首次充电,形成固体电解质界面膜(SEI)的过程[4-5]。
不同的化成工艺形成的SEI膜则有所不同,SEI膜的形态直接影响单体电池的综合性能,特别是对电池的循环性能影响巨大[7-9]。
传统的小电流预充方式有助于稳定的SEI膜形成,然而长时间的小电流或高截止电压充电会导致形成的SEI膜阻抗增大,从而影响电池的循环性能、倍率性能等。
锂电池化成前高温静置的作用

锂电池化成前高温静置的作用全文共四篇示例,供读者参考第一篇示例:锂电池是一种常用的电池类型,具有高能量密度和长寿命的特点,因此被广泛应用于手机、笔记本电脑、无人机等电子设备中。
在锂电池制造过程中,经常会遇到需要将电池在高温下静置一段时间的情况,这个过程被称为化成前高温静置。
那么,化成前高温静置对锂电池有什么作用呢?本文将就此问题进行探讨。
化成前高温静置可以提高锂电池的性能和稳定性。
锂电池在制造完成后需要经过一系列的充放电循环来激活电池,使其达到最佳性能。
而在高温下静置可以促使电池内部的材料更均匀地充分混合,同时还可以加速活化锂离子导电层,提高电池的导电性能,从而提高电池的性能和稳定性。
化成前高温静置可以帮助检测电池的质量。
在高温下静置的过程中,可以观察电池是否有发生异常现象,如漏液、电解液浸润等情况,如果有异常现象出现,就可以及时修复或淘汰该电池,确保生产出的电池质量达标。
化成前高温静置也是锂电池生产过程中质量控制的一个重要环节。
化成前高温静置还可以减少锂电池制造过程中可能产生的安全隐患。
在锂电池生产过程中,由于涉及到高温、高压等因素,极易发生电解液泄露、短路等安全问题。
通过在高温下静置可以将这些潜在的安全隐患暴露出来,使生产厂家及时发现并处理,从而提高生产过程中的安全性。
值得注意的是,虽然化成前高温静置对锂电池有很多好处,但也需要注意控制好静置的时间和温度。
如果静置时间过长或温度过高,可能会导致电解液的不稳定性增加,从而对电池产生负面影响。
在进行化成前高温静置时,应遵循生产厂家提供的具体操作规范,确保静置的时间和温度在合适范围内。
化成前高温静置是锂电池制造过程中的重要环节,它可以提高电池的性能和稳定性,帮助检测电池的质量,减少生产过程中的安全隐患。
锂电池生产厂家应该重视化成前高温静置这一环节,在生产过程中严格执行相关要求,以确保生产出高质量、安全可靠的锂电池产品。
【2000字】第二篇示例:锂电池作为现代电子产品中广泛使用的电池之一,具有高能量密度、轻量化等优点,因此在手机、平板电脑、电动汽车等领域得到了广泛应用。
锂电池baking工序
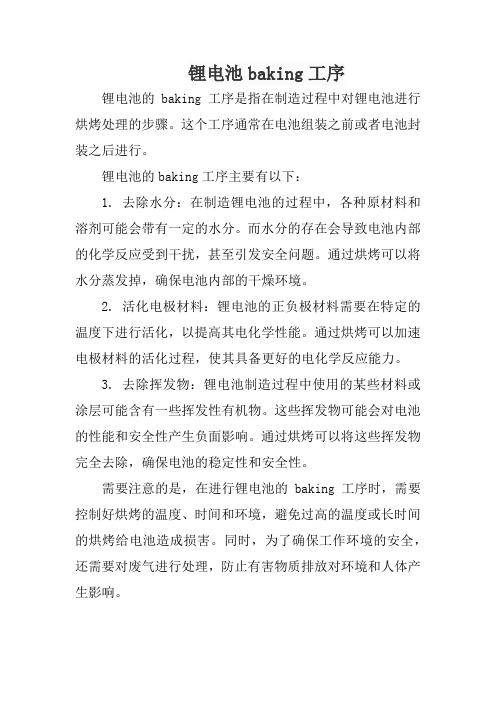
锂电池baking工序
锂电池的baking工序是指在制造过程中对锂电池进行烘烤处理的步骤。
这个工序通常在电池组装之前或者电池封装之后进行。
锂电池的baking工序主要有以下:
1. 去除水分:在制造锂电池的过程中,各种原材料和溶剂可能会带有一定的水分。
而水分的存在会导致电池内部的化学反应受到干扰,甚至引发安全问题。
通过烘烤可以将水分蒸发掉,确保电池内部的干燥环境。
2. 活化电极材料:锂电池的正负极材料需要在特定的温度下进行活化,以提高其电化学性能。
通过烘烤可以加速电极材料的活化过程,使其具备更好的电化学反应能力。
3. 去除挥发物:锂电池制造过程中使用的某些材料或涂层可能含有一些挥发性有机物。
这些挥发物可能会对电池的性能和安全性产生负面影响。
通过烘烤可以将这些挥发物完全去除,确保电池的稳定性和安全性。
需要注意的是,在进行锂电池的baking工序时,需要控制好烘烤的温度、时间和环境,避免过高的温度或长时间的烘烤给电池造成损害。
同时,为了确保工作环境的安全,还需要对废气进行处理,防止有害物质排放对环境和人体产生影响。
总而言之,锂电池的baking工序是为了去除水分、活化电极材料和去除挥发物等目的而进行的烘烤处理步骤,以提高电池的性能和安全性。
电池制成工序(修正)
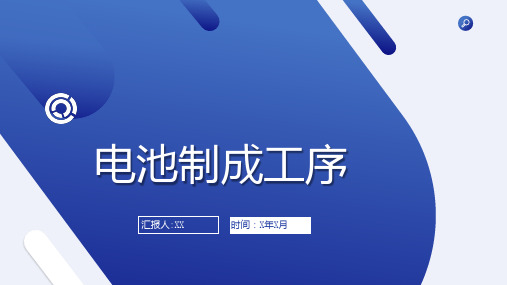
一、检测车间工艺流程(以2、3厂为例)
<6>胶钉上料,入导 向套:胶钉在震动盘作 用下进入轨道,并有序 进入导入套,是塞钉前 的准备工作,导向套清
洁超过1天
<7>负压塞钉:通过 抽取电芯腔体的空气, 然后将塞钉塞入,以保
证电池的密封性
胶钉(4.6*9.15mm)
<8>人工全检:检查 负压塞钉效果,
<9>后称重:后称重 数据与前称重数据相减, 确定二次注液量是否在 范围内(90-100g)后称 重,与前称盘、每次班
开班前校准2kg砝码 (2000±05g).
<10>线体归码组盘: 将电芯妇码并与托盘绑
定约1分钟清 洗完毕;;送至换盘机 等待时间间隔大约1分
一、检测车间工艺流程(以2、3厂为例)
OCV3: 3.27503.2950(管控在15mv
极差内)
上限为Xxbar+K3.726
K值为自放电不同SOC 月损失(≤3%)的电压
下降
x
x
x
x
x
常温自放电同盘极差 :同盘排异规则,去 除乎异常值计算xbar
和,
-0.5~2.8mv xr+K3.726(上限取两者较
电池制成工序
汇报人:XX
时间:X年X月
-
一、检测车间工艺流 程(以2、3厂为例)
目录
电池制成工序
电池检测工序介绍
1
一、检测车间工艺流程 (以2、3厂为例)
一、检测车间工艺流程(以2、3厂为例)
1、大概流程
高温浸润→化成→二次注液→充电→高温 老化→降温→分容→三次注液→封口→自 放电→机械分选→人工分选→人工返修
一、检测车间工艺流程(以2、3厂为例)
01
技术丨锂离子电池老化机理与工艺过程

技术丨锂离子电池老化机理与工艺过程导读:对于不同的电池体系,三元正极/石墨负极锂电池、磷酸铁锂正极/石墨负极锂电池抑或是钛酸锂负极电池,需要根据材料特性及锂电池特性进行针对性试验。
锂电池的生产工艺可以分为前道极片制造、中道电芯封装、后道电池活化三个阶段,电池活化阶段的目的是让电池中的活物质和电解液经过充分活化以达到电化学性能稳定。
活化阶段包括预充电、化成、老化、定容等阶段。
预充电和化成的目的是为了让正负极材料进行最初几次的充放电来激活材料,使材料处于最佳的使用状态。
老化的目的主要有几个:一是让电解液的浸润更加良好,有利于电池性能的稳定;二是正负极材料中的活性物质经过老化后,可以促使一些副作用的加快进行,例如产气、电解液分解等,让锂电池的电化学性能快速达到稳定;三是通过老化一段时间后进行锂电池一致性筛选。
化成之后电芯的电压不稳定,其测量值会偏离实际值,老化后的电芯电压、内阻更为稳定,便于筛选一致性高的电池。
老化制度对锂电池性能的影响因素主要有两个,即老化温度和老化时间。
除此之外,还有老化时电池处于封口还是开口的状态也比较重要。
对于开口化成来说,如果厂房可以控制好湿度可以老化后再封口。
如果采用高温老化,封口后老化比较好。
对于不同的电池体系,三元正极/石墨负极锂电池、磷酸铁锂正极/石墨负极锂电池抑或是钛酸锂负极电池,需要根据材料特性及锂电池特性进行针对性试验。
在试验设计中,可以通过锂电池的容量差别、内阻差别、压降特点来确定最佳的老化制度。
一、三元或磷酸铁锂正极/石墨负极锂电池对于三元作为正极材料,石墨作为负极材料的锂电池来说,锂离子电池的预充化成阶段会在石墨负极的表面形成一层固态电解质膜(SEI),此种膜的形成电位约在0.8V左右,SEI允许离子穿透而不允许电子通过,由此在形成一定厚度后会抑制电解液的进一步分解,可以起到防止电解液分解引起的电池性能下降。
但是化成后形成的SEI膜结构紧密且孔隙小,将电池再进行老化,将有助于SEI结构重组,形成宽松多孔的膜,以此提高锂电池的性能。
电池性能的影响因素

电池性能的影响因素锂电池内部复杂的电化学过程,理解起来有一定难度,这里先说结论。
锂电池容量的衰减来自于电极材料的损失和电解质的分解;而电池阻抗的增加来自于电荷传导过程中阻力的上升;电池结构的破坏则会导致容量损失。
锂电池寿命可以分为两种概念,一种是日历寿命,另一种是循环寿命。
锂电池还有一种情况,就是在操作不当,事故等情况下造成电池寿命在短时间内快速衰减。
先从电池内部开始,讨论一些影响电池寿命的因素,再结合温度,电压,充放电深度,电流说明。
目前的锂电池,不论是三元,锰酸锂还是磷酸铁锂等各种正极材料,配备的负极基本都是石墨材质。
石墨材质的负极不能与电解质稳定相融,在两者刚接触的时候会形成一层固体电解质界面即SEI膜(solid electrolyte interface)关于SEI的具体内容会在另一篇文章里呈现。
SEI膜上的空隙允许锂离子进出,又可以将电解液与石墨隔离开,同时,相对于电子导电,它又是绝缘体,不允许电子通过。
这种性质对于锂电池来说非常的好,SEI是维持锂电池稳定的重要结构之一。
在日历寿命以及循环寿命中,SEI并非静止,正常情况下SEI会慢慢增长厚度且有一定程度的破损,而破损的部分也会因为石墨与电解液的再次接触而形成新的SEI膜,在形成以及修复的过程中,需要消耗锂离子,但高质量的SEI膜也是锂电池长循环寿命的必备条件。
而电池由于外因(受力、湿度、温度场变化等)而变形时,在物体内各部分之间产生相互作用的内力,也就是应力作用,会使SEI的孔洞发生变形,使得离子通道不再通畅。
这些微观上的变化,使得电池对外表现出内阻增加,容量下降,充电能力变差等寿命衰退的现象。
析锂现象应该都听过,可以说是锂电池的第一大难题,目前对于这种现象的研究不是特别透彻,没有太好的解决办法,但是多数人认可的原因是,由于负极嵌锂空间不足,锂离子迁移阻力过大,锂离子过快从正极脱出但无法等量嵌入负极等异常引起的无法嵌入负极的锂离子只能在负极表面得到电子,从而形成银白色的锂单质的现象。
锂离子电池针刺实验影响因素的研究

锂离子电池针刺实验影响因素的研究王磊【期刊名称】《《信息记录材料》》【年(卷),期】2019(020)009【总页数】4页(P4-7)【关键词】锂离子电池; 针刺; 短路【作者】王磊【作者单位】乐凯胶片股份有限公司研究所河北保定 071054【正文语种】中文【中图分类】TQ551 引言在传统化石燃料逐渐枯竭和国家排放法规巨大压力的背景下,锂离子电池逐渐成为研究的热点问题[1]。
在锂电产业快速发展的同时,其安全问题也日益凸显,相关产品和设备起火燃烧的案例屡见不鲜[2]。
在新能源汽车大行其道的今天,车用动力锂电池的安全性显得至关重要。
尤其是2019年4月上海地下车库MODELS起火燃烧以及最近几个月以来蔚来ES8的多起自燃事件,再次把锂电池的安全问题推上了舆论风头。
热失控是锂离子电池产生安全性问题的主要体现方式,其中短路是产生热失控的最常见因素。
造成电池发生安全事故的情形有两种:一是使用过程中的人为短路,二是电池在制造或者使用中发生的内部短路[3]。
对于第一种短路情况,隔膜被外界物体刺穿,造成了正负极接触,产生大量的热,存在热失控的危险。
第二种内部短路情况,是在锂离子电池的生产过程中,极易产生毛刺,包括铜箔、铝箔切割处和极耳焊接过程中产生的毛刺。
在电池充放电过程中,这些毛刺刺穿隔膜造成正负极短接。
为了评估锂离子电池在发生短路情况下的实际表现,目前主要通过针刺测试来模拟和评估短路发生时电池的安全耐用性[4]。
针刺测试是将一枚钢针以规定的速度垂直刺穿锂离子电池,人为强制造成内部短路。
在进行针刺测试时,除了观察电池有无冒烟起火等恶劣现象,同时也对电池表面的温度变化情况进行监测[5]。
通过观察电池的温升状况,以及是否发生起火、爆炸,就可以方便地评价锂离子电池的内部短路情况。
本文根据针刺测试结果,对影响锂离子电池针刺测试结果的因素,包括测试环境温度、注液量波动性、活化时间、电池容量以及电压波动性等实验变量做出了相应评价。
金属锂的活化能

金属锂的活化能全文共四篇示例,供读者参考第一篇示例:金属锂是一种重要的金属材料,常被用作锂电池等高性能电池的主要材料。
在应用中,金属锂的活化能是一个重要的参数,它直接影响金属锂的电化学性能和循环寿命。
本文将介绍金属锂的活化能的概念和意义,并探讨影响金属锂活化能的因素及其调控方法。
一、金属锂的活化能概念在电池中,金属锂的电化学性能取决于其在电极材料中的离子扩散速度。
而金属锂在电解液中的溶解、沉积和扩散过程均需要克服一定的能量障碍,即所谓的活化能。
活化能越小,金属锂在电极材料中的扩散速度越快,电池的充放电性能也就越好。
1. 温度:金属锂的活化能与温度密切相关,通常情况下,温度越高,活化能越小。
但过高的温度也会降低金属锂的电化学稳定性,影响电池的循环寿命。
2. 结晶缺陷:金属锂的结晶缺陷会增加其活化能,影响其在电极材料中的扩散速度。
对金属锂进行精密的合成和处理可以降低其活化能。
3. 晶体结构:金属锂的晶体结构也会影响其活化能。
一些特殊晶体结构的金属锂可能具有更低的活化能,有利于提高电池的性能。
4. 表面涂层:在一些情况下,对金属锂进行表面涂层处理能够降低其活化能,提高其在电极材料中的扩散速度。
1. 温度控制:在设计电池的工作温度范围时,需考虑金属锂的活化能和电池的循环寿命之间的平衡。
2. 材料设计:设计新型金属锂材料和电极材料,优化晶体结构和缺陷密度,从而降低金属锂的活化能。
3. 表面处理:对金属锂进行表面涂层处理,如氧化、硫化、碳包覆等,可以有效降低其活化能。
4. 循环寿命测试:通过对金属锂电池的长期循环寿命测试,可以评估活化能对电池性能和寿命的影响,为电池设计和优化提供参考。
金属锂的活化能是影响电池性能和循环寿命的重要参数,其调控方法包括温度控制、材料设计、表面处理和循环寿命测试等。
通过深入研究金属锂的活化能和相关调控方法,可以进一步提高金属锂电池的性能和稳定性,推动电池技术的发展和应用。
第二篇示例:金属锂是一种非常重要的金属元素,被广泛应用于锂电池等领域。
锂电池化成和分容工艺要点

篇十六锂电池之化成十六部分化成1、锂电池封装完毕后,最后工序化成(也是影响电池性能最重要工序之一)。
所谓化成指给一定的电流,使得锂电池正负极活性物质被激发,最后使电池具有放电能力的电化学过程。
影响化成的因素条件有化成电流、SOC、老化时间及温度,还需要考虑电池材料体系和产能要求。
化成不是仅简单的充放电,而是衡量对电池性能的影响。
需要做大量的研究和验证,与电池进行匹配。
2、化成对电池哪些电性能产生影响?1)首效,次放电容量/预充容量之和=首效%2)放电容量,充电恒流比,放电平台时间3)倍率性能4)循环性能5)自放电性能6)交流内阻值……例如动力类LFP(磷酸亚铁锂)的化成工艺研究如下表3、化成小结1)≥65℃老化时间过长对后期电性能负相关2)预充SOC对首次充放电效率有一定影响,首效与放电容量正相关3)大电流影响倍率和循环性能……4、化成过程异常有哪些?异常数据需要10ms~100ms级的采样测试系统,数据结合工艺、配方进行分析1)恒流充电阶段:U不升反降,变化斜率较大,内部可能存在微短路;恒压充电阶段:I不降反升,变化斜率较大,内部可能存在微短路。
2)化成也会出现充不进电?化成高压?化成低压?内阻异常?十七部分分容分容即对化成完的电池进行充放电,统计电池的容量、充电恒流比、放电平台电压、内阻进行区分,以便分档配组。
1)容量:指放电的容量,一般会循环3~5次取中间某次放电容量为额定容量。
一般三元类电池充放电流为0.5C,磷酸亚铁锂为0.5C~1C,钛酸锂电池为1C,钴酸锂电池为0.2C~0.5C等2)充电恒流比:充电过程中,恒流充入容量/(恒流+恒压充入容量之和)*100% 3)放电平台时间:指在电池在≈标称电压放电持续时间。
化成工艺对锂离子电池性能的影响
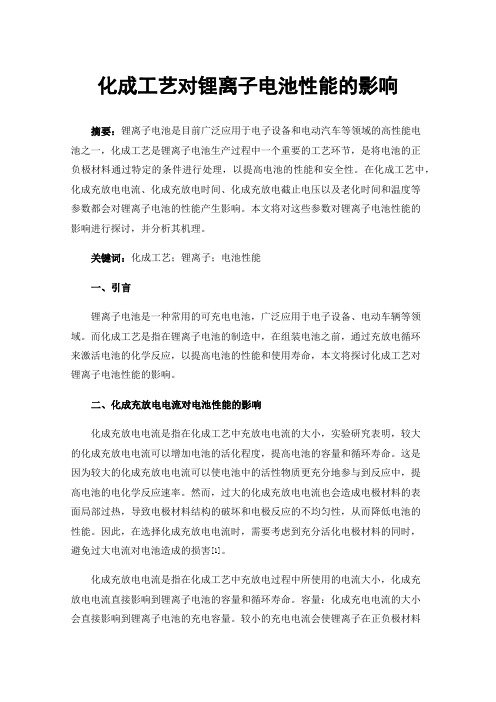
化成工艺对锂离子电池性能的影响摘要:锂离子电池是目前广泛应用于电子设备和电动汽车等领域的高性能电池之一,化成工艺是锂离子电池生产过程中一个重要的工艺环节,是将电池的正负极材料通过特定的条件进行处理,以提高电池的性能和安全性。
在化成工艺中,化成充放电电流、化成充放电时间、化成充放电截止电压以及老化时间和温度等参数都会对锂离子电池的性能产生影响。
本文将对这些参数对锂离子电池性能的影响进行探讨,并分析其机理。
关键词:化成工艺;锂离子;电池性能一、引言锂离子电池是一种常用的可充电电池,广泛应用于电子设备、电动车辆等领域。
而化成工艺是指在锂离子电池的制造中,在组装电池之前,通过充放电循环来激活电池的化学反应,以提高电池的性能和使用寿命,本文将探讨化成工艺对锂离子电池性能的影响。
二、化成充放电电流对电池性能的影响化成充放电电流是指在化成工艺中充放电电流的大小,实验研究表明,较大的化成充放电电流可以增加电池的活化程度,提高电池的容量和循环寿命。
这是因为较大的化成充放电电流可以使电池中的活性物质更充分地参与到反应中,提高电池的电化学反应速率。
然而,过大的化成充放电电流也会造成电极材料的表面局部过热,导致电极材料结构的破坏和电极反应的不均匀性,从而降低电池的性能。
因此,在选择化成充放电电流时,需要考虑到充分活化电极材料的同时,避免过大电流对电池造成的损害[1]。
化成充放电电流是指在化成工艺中充放电过程中所使用的电流大小,化成充放电电流直接影响到锂离子电池的容量和循环寿命。
容量:化成充电电流的大小会直接影响到锂离子电池的充电容量。
较小的充电电流会使锂离子在正负极材料中嵌入的速率较慢,导致嵌入锂离子数目较少,充电容量也相应减少。
而较大的充电电流会使锂离子嵌入速率加快,增加了嵌入锂离子的数量,从而提高了充电容量。
因此,在化成工艺中选择适当的充电电流,可以使得锂离子电池具有更高的充电容量。
循环寿命:充放电电流还会影响锂离子电池的循环寿命。
活化工艺对锂离子电池容量的影响
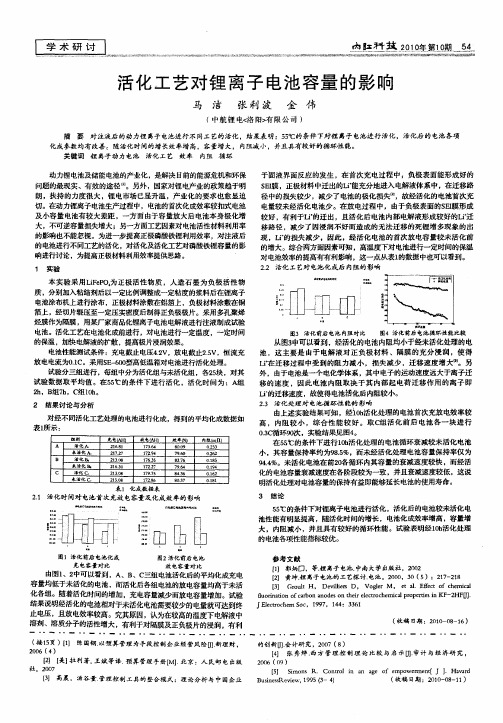
【] G o l H, De i es D, V ge M , e 1 f c o h m cl 3 ru t vl r l i o l r ta .E et f c e ia
化各组 。随着活化时间的增加 ,充电容量减少而放 电容量增加 。试验 吉 果说明经活化的电池相对于 未活化 电池需要较少的 电量就可达到终 止电压 , 且放 电效率较 高。究 其原 因,认为在较高的温度下电解液中
5'的条件下对锂离子 电池进行活化 , 52 t 活化后 的电池较未活化电 池性能有 明显提高 ,随活化时 间的增长 ,电池化成效率增高 ,容量增 大 ,内阻减小 ,并且具 有较 好的循 环性 能 。试验表 明经 1h 0 活化 处理
的电池各项性能指标较优 。
图1活化前后 电池化成 充 电容 量 对 比 图2活化前后 电池 放 电 容 量 对 比
,
的创 新Ⅱ 会 计研 究 ,2 0 8 】 0 7( )
20 4 0 6( )
.
。
[ 张 秀 烨 . 方 管理 控 制 理 论 比 较 与 启 示 【. 计 与 经 济研 究 , 4 】 西 】审 ]
20 0 ) 0 6( 9
【 【 拉 利 著 . 斌 等译 . 算 管 理 手册 [ 北 京 :人 民邮 电 出版 2 美】 】 王 预 M】
9. 4 %。未 活化电池在前2各循环 内其容量 的衰 减速 度较 快 ,而经活 4 O 化的 电池容量衰减速度在各阶段较 为一致 ,并且衰 减速度 较低 ,这说 明活化处理对 电池容量 的保持有益即能够延长电池的使用寿 命。
3 结 论
耒活化
C 活 化 C,
2 63 1 o
2 30 1 8
由图1 中0  ̄看到 ,A 、2 - 3 " 、B 三组电池活化 后的平均化成充 电 、c 容量均 低于未活化的 电池 ,而活化后各组电池的放 电容量均高于未活
锂电池极片设计基础、常见缺陷和对电池性能的影响

锂电池极⽚设计基础、常见缺陷和对电池性能的影响⼀、极⽚设计基础篇锂电池电极是⼀种颗粒组成的涂层,均匀的涂敷在⾦属集流体上。
锂离⼦电池极⽚涂层可看成⼀种复合材料,主要由三部分组成:(1)活性物质颗粒;(2)导电剂和黏结剂相互混合的组成相(碳胶相);(3)孔隙,填满电解液。
各相的体积关系表⽰为:孔隙率 + 活物质体积分数 + 碳胶相体积分数=1锂电池极⽚的设计是⾮常重要的,现针对锂电池极⽚设计基础知识进⾏简单介绍。
(1)电极材料的理论容量电极材料理论容量,即假定材料中锂离⼦全部参与电化学反应所能够提供的容量,其值通过下式计算:例如,LiFePO4摩尔质量157.756 g/mol,其理论容量为:这计算值只是理论的克容量,为保证材料结构可逆,实际锂离⼦脱嵌系数⼩于1,实际的材料的克容量为:材料实际克容量=锂离⼦脱嵌系数 × 理论容量(2)电池设计容量与极⽚⾯密度电池设计容量可以通过下式计算: 极⽚涂层⾯积 电池设计容量=涂层⾯密度×活物质⽐例×活物质克容量×极⽚涂层⾯积其中,涂层的⾯密度是⼀个关键的设计参数,压实密度不变时,涂层⾯密度增加意味着极⽚厚度增加,电⼦传输距离增⼤,电⼦电阻增加,但是增加程度有限。
厚极⽚中,锂离⼦在电解液中的迁移阻抗增加是影响倍率特性的主要原因,考虑到孔隙率和孔隙的曲折连同,离⼦在孔隙内的迁移距离⽐极⽚厚度多出很多倍。
(3)负极-正极容量⽐N/P负极容量与正极容量的⽐值定义为:N/P要⼤于1.0,⼀般1.04~1.20,这主要是处于安全设计,防⽌负极侧锂离⼦⽆接受源⽽析出,设计时要考虑⼯序能⼒,如涂布偏差。
但是,N/P过⼤时,电池不可逆容量损失,导致电池容量偏低,电池能量密度也会降低。
⽽对于钛酸锂负极,采⽤正极过量设计,电池容量由钛酸锂负极的容量确定。
正极过量设计有利于提升电池的⾼温性能:⾼温⽓体主要来源于负极,在正极过量设计时,负极电位较低,更易于在钛酸锂表⾯形成SEI膜。
- 1、下载文档前请自行甄别文档内容的完整性,平台不提供额外的编辑、内容补充、找答案等附加服务。
- 2、"仅部分预览"的文档,不可在线预览部分如存在完整性等问题,可反馈申请退款(可完整预览的文档不适用该条件!)。
- 3、如文档侵犯您的权益,请联系客服反馈,我们会尽快为您处理(人工客服工作时间:9:00-18:30)。
锂电池活化阶段对电池性能的影响
锂电池的生产工艺可以分为前道极片制造、中道电芯封装、后道电池活化三个阶段,电池活化阶段的目的是让电池中的活物质和电解液经过充分活化以达到电化学性能稳定。
活化阶段包括预充电、化成、老化、定容等阶段。
预充电和化成的目的是为了让正负极材料进行最初几次的充放电来激活材料,使材料处于最佳的使用状态。
老化的目的主要有几个:
➤一是让电解液的浸润更加良好,有利于电池性能的稳定;
➤二是正负极材料中的活性物质经过老化后,可以促使一些副作用的加快进行,例如产气、电解液分解等,让锂电池的电化学性能快速达到稳定;
➤三是通过老化一段时间后进行锂电池一致性筛选。
化成之后电芯的电压不稳定,其测量值会偏离实际值,老化后的电芯电压、内阻更为稳定,便于。