2019超声波焊接的塑件设计规范.
CBT3559-2019CCS无损检测超声波标准
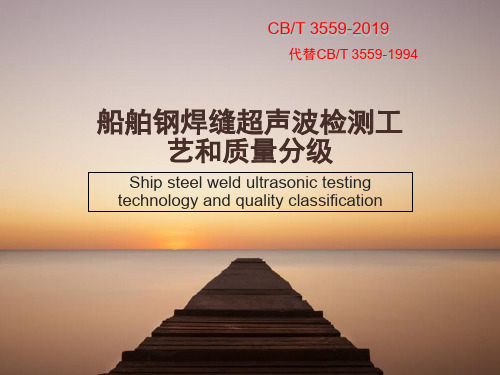
13 时基线调节
13.1 用标准试块上圆弧面的反射波和其他等效试块的反射波进行时基线调节 13.2 最大检测声程处回波至少调节到示波屏满刻度的3/4以上 13.3 当检测面曲率半径不大于W²/4时,探头楔块应磨成与工件面相吻合,在 6.6规定 的对比试块上作时基线调整
PS:时基线:A 型显示荧光屏中表示时间或距离的水平扫描线。
图1
图2
10 探头频率与斜探头折射角的选择
10.1 探测频率按下表进行选择
10.2 探头折射角的选择应能使主声束覆盖整个焊缝检测区,具体要求如下: a)平板对接焊缝探伤折射角的选择
10 探头频率与斜探头折射角的选择
b)条件允许时,T型接头焊缝检测应分别使用直探头和斜探头扫查,斜探头按下表选 择
10 探头频率与斜探头折射角的选择
14.7 检测横向缺陷时,应将各线灵敏度分别提高6dB 14.8 T型接头焊缝直探头检测按附录D的规定
15 补偿
15.1 补偿包括耦合补偿和衰减补偿等 15.2 耦合补偿和衰减补偿统称为传输补偿,传输补偿的测定和修正要求按附 录E的方法进行 15.3 当检测面曲率半径不大于W²/4时,曲面补偿应采用曲率半径与工件相同 的试块,通过对比试验进行实际测量 15.4 工件与试块表面有差异时,应进行补偿,补偿值计入DAC曲线。
14 距离-波幅曲线
14.1 DAC曲线应以实际检测用的仪器和探头,根据在对比试块上实际的数据绘制而 成。(绘制方法略) 14.2 绘制DAC曲线是应不少于3点,且最大深度应满足检测要求 14.3 在检测范围内的DAC曲线不应低于示波屏刻度的20% 14.4和14.5 见下图
14 距离-波幅曲线
10.3 选择检测面和探头时应考虑到焊缝中产生各类缺陷的可能性, 并尽可能是主声束垂直于焊缝中的危害性缺陷。
超声波塑件结构设计理论

超声焊接结构
阶梯型
Step Joint
0.40
0.03
( 0.30 ) 0.17 0.20
Join Design①
肉厚達 1.5 mm 程度時
1.5 0.05 (0.5) 0.5 R型 到ED為10mm 以下 0.5
60 °
Join Design②
肉厚 1.0 mm 程度時
(0.03)
(0.5 ) 0.3 0.4 R型很重要
(Range) 0.008” to 0.012”
(0.2 to 0.3mm) 0.012” to 0.016”
(18-35mm) Greater than 1.50”
(35mm)
(0.3 to 0.4mm) 0.016” to 0.020”
(0.4 to 0.5mm)
剪切设计例子
剪切设计例子
剪切设计的长处
Share Join②
0.8 以上
<0.05
0.3 2.0
W
Shear Joint
0.8 W 0.03 0
Shear Joint
0.5 0.25
0.5
0.25
0.1
0.1
Shear Joint Interference
Maximum Part Dimension Less than 0.75” (18mm) 0.75” to 1.50” Interference per Side Part Dimension Tolerance + 0.001” (+ 0.025mm) + 0.002” (+ 0.050mm) + 0.003” (+ 0.075mm)
45°~ 60° 1.0
焊接件通用技术条件(2019)

焊接件通用技术条件1 范围本标准适用于公司所有产品中采用手工电弧焊、钨极氩弧焊、富氩气体保护焊及自动焊焊接的零部件。
本标准适用于产品图样或技术文件中无特殊要求的焊接件。
2 引用标准下列文件中的条款通过本标准的引用而成为本标准的条款。
凡是注日期的引用文件,其随后所有的修改单(不包括勘误的内容)或修订版均不适用于本标准,然而,鼓励根据本标准达成协议的各方研究是否可使用这些文件的最新版本。
凡是不注日期的引用文件,其最新版本适用于本标准。
GB/T 985 气焊、手工电弧焊及气体保护焊焊缝坡口的基本形式和尺寸GB/T 986 埋弧焊焊缝坡口的基本形式和尺寸GB/T 2649 焊接接头机械性能试验取样方法GB/T 2650 焊接接头冲击试验方法GB/T 2651 焊接接头拉伸试验方法GB/T 2652 焊缝及熔敷金属拉伸试验方法GB/T 2653 焊接接头弯曲及压扁实验方法GB/T 3323 钢熔化焊对接接头射线照相和质量分等GB/T 5117 碳钢焊条GB/T 5118 低合金钢焊条GB/T 8110 气体保护焊丝用碳钢、低合金钢焊丝JG/T 5082.1 建筑机械与设备焊接件通用技术条件3 一般要求3.1焊接结构件的制造应符合设计、工艺文件和本标准的规定。
3.2焊接生产过程对环境温度的规定:3.2.1零件和成品矫正时,不应低于下列温度:3.2.1.1低碳钢材质:-20℃;3.2.1.2低合金结构钢材质:-15℃。
3.2.2一般焊接件允许施焊温度应符合表1的规定。
3.2.3焊接件在低温条件下(如表1所列)焊接时,钢材表面应进行预热,必须保证预热区宽度大于被焊板材厚度的4倍,且每侧预热宽度不得小于100mm,必须保证加热到100~200℃后才能施焊。
如果用火焰预热时,焰芯距板面距离应大于50mm。
3.2.4在常温条件下,对刚性大、可焊性差的焊接件,也应焊前预热(预热温度在100~200℃范围内),焊后需进行保温或回火消除焊接应力。
超声波焊接技术大全

超声波焊接塑料件的设计塑料件的设计代注塑方式能有效提供比较完美的焊接用塑胶件。
光我们决定用超声波焊接技术完成熔合时,塑料件的结构设计必须首先考虑如下几点:1 焊缝的大小(即要考虑所需强度)2是否需要水密、气密3 是否需要完美的外观4 避免塑料熔化或合成物的溢出5 是否适合焊头加工要求焊接质量可能通过下几点的控制来获得:1材质2塑料件的结构3 焊接线的位置和设计4 焊接面的大小5 上下表面的位置和松紧度6 焊头与塑料件的妆触面7顺畅的焊接路径8 底模的支持为了获得完美的、可重复的熔焊方式,必须遵循三个主要设计方向:1 最初接触的两个表面必须小,以便将所需能量集中,并尽量减少所需要的总能量(即焊接时间)来完成熔接。
2 找到适合的固定和对齐的方法,如塑料件的接插孔、台阶或企口之类。
3围绕着连接界面的焊接面必须是统一而且相联系互紧密接触的。
如果可能的话,接触面尽量在同一个平面上,这样可使能量转换时保持一致。
下面就对塑料件设计中的要点进行分类举例说明:整体塑料件的结构1.1塑料件的结构塑料件必须有一定的刚性及足够的壁厚,太薄的壁厚有一定的危险性,超声波焊接时是需要加压的,一般气压为2-6kgf/cm2。
所以塑料件必须保证在加压情况下基本不变形。
1.2罐状或箱形塑料等,在其接触焊头的表面会引起共振而形成一些集中的能量聚集点,从而产生烧伤、穿孔的情况(如图1所示),在设计时可以罐状顶部做如下考虑○1 加厚塑料件○2增加加强筋○3 焊头中间位置避空1.3尖角如果一个注塑出来的零件出现应力非常集中的情况,比如尖角位,在超声波的作用下会产生折裂、融化。
这种情况可考虑在尖角位加R角。
如图2所示。
1.4塑料件的附属物注塑件内部或外部表面附带的突出或细小件会因超声波振动产生影响而断裂或脱落,例如固定梢等(如图3所示)。
通过以下设计可尽可能减小或消除这种问题:○1 在附属物与主体相交的地方加一个大的R角,或加加强筋。
○2增加附属物的厚度或直径。
超声波焊接塑胶件的设计
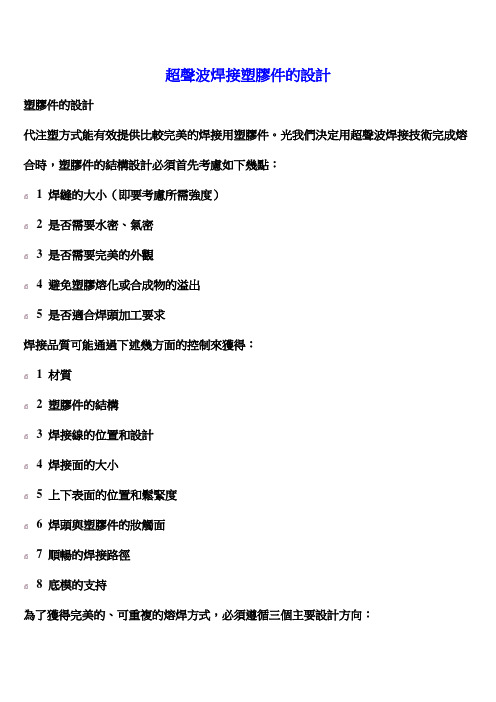
超聲波焊接塑膠件的設計塑膠件的設計代注塑方式能有效提供比較完美的焊接用塑膠件。
光我們決定用超聲波焊接技術完成熔合時,塑膠件的結構設計必須首先考慮如下幾點:1 焊縫的大小(即要考慮所需強度)2 是否需要水密、氣密3 是否需要完美的外觀4 避免塑膠熔化或合成物的溢出5 是否適合焊頭加工要求焊接品質可能通過下述幾方面的控制來獲得:1 材質2 塑膠件的結構3 焊接線的位置和設計4 焊接面的大小5 上下表面的位置和鬆緊度6 焊頭與塑膠件的妝觸面7 順暢的焊接路徑8 底模的支持為了獲得完美的、可重複的熔焊方式,必須遵循三個主要設計方向:1 最初接觸的兩個表面必須小,以便將所需能量集中,並儘量減少所需要的總能量(即焊接時間)來完成熔接。
2 找到適合的固定和對齊的方法,如塑膠件的接插孔、臺階或企口之類。
3 圍繞著連接介面的焊接面必須是統一而且相聯繫互緊密接觸的。
如果可能的話,接觸面儘量在同一個平面上,這樣可使能量轉換時保持一致。
下面就對塑膠件設計中的要點進行分類舉例說明:整體塑膠件的結構1.1塑膠件的結構塑膠件必須有一定的剛性及足夠的壁厚,太薄的壁厚有一定的危險性,超聲波焊接時是需要加壓的,一般氣壓為2-6kgf/cm2 。
所以塑膠件必須保證在加壓情況下基本不變形。
1.2罐狀或箱形塑膠等,在其接觸焊頭的表面會引起共振而形成一些集中的能量聚集點,從而產生燒傷、穿孔的情況(如圖1所示),在設計時可以罐狀頂部做如下考慮○1 加厚塑膠件○2 增加加強筋○3 焊頭中間位置避空1.3尖角如果一個注塑出來的零件出現應力非常集中的情況,比如尖角位元,在超聲波的作用下會產生折裂、融化。
這種情況可考慮在尖角位加R角。
如圖2所示。
1.4塑膠件的附屬物注塑件內部或外部表面附帶的突出或細小件會因超聲波振動產生影響而斷裂或脫落,例如固定梢等(如圖3所示)。
通過以下設計可盡可能減小或消除這種問題:○1 在附屬物與主體相交的地方加一個大的R角,或加加強筋。
超声波焊接塑料件的设计

超声波焊接塑料件的设计代注塑方式能有效提供比较完美的焊接用塑胶件。
光我们决定用超声波焊接技术完成熔合时,塑料件的结构设计必须首先考虑如下几点:1 焊缝的大小(即要考虑所需强度)2 是否需要水密、气密3 是否需要完美的外观4 避免塑料熔化或合成物的溢出5 是否适合焊头加工要求焊接质量可能通过下几点的控制来获得:1 材质2 塑料件的结构3 焊接线的位置和设计4 焊接面的大小5 上下表面的位置和松紧度6 焊头与塑料件的妆触面7 顺畅的焊接路径8 底模的支持为了获得完美的、可重复的熔焊方式,必须遵循三个主要设计方向:1 最初接触的两个表面必须小,以便将所需能量集中,并尽量减少所需要的总能量(即焊接时间)来完成熔接。
2 找到适合的固定和对齐的方法,如塑料件的接插孔、台阶或齿口之类。
3 围绕着连接界面的焊接面必须是统一而且相联系互紧密接触的。
如果可能的话,接触面尽量在同一个平面上,这样可使能量转换时保持一致。
下面就对塑料件设计中的要点进行分类举例说明:整体塑料件的结构1.1塑料件的结构塑料件必须有一定的刚性及足够的壁厚,太薄的壁厚有一定的危险性,超声波焊接时是需要加压的,一般气压为2-6kgf/cm2 。
所以塑料件必须保证在加压情况下基本不变形。
1.2罐状或箱形塑料等,在其接触焊头的表面会引起共振而形成一些集中的能量聚集点,从而产生烧伤、穿孔的情况(如图1所示),在设计时可以罐状顶部做如下考虑○1 加厚塑料件○2 增加加强筋○3 焊头中间位置避空1.3尖角如果一个注塑出来的零件出现应力非常集中的情况,比如尖角位,在超声波的作用下会产生折裂、融化。
这种情况可考虑在尖角位加R角。
如图2所示。
1.4塑料件的附属物注塑件内部或外部表面附带的突出或细小件会因超声波振动产生影响而断裂或脱落,例如固定梢等(如图3所示)。
通过以下设计可尽可能减小或消除这种问题:○1 在附属物与主体相交的地方加一个大的R角,或加加强筋。
○2 增加附属物的厚度或直径。
超声波焊接技术规范

何谓超声波焊接在进行超声波振动的同时施加压力,使要结合的塑料产品的一部分因摩擦产生热量软化,焊接在一起的方法。
接合部的接合形状案例(1)斜面接合该接合是利用斜面以达到完全的面接合。
由于可获得均一的热能及较大的焊接面积,故焊接强度高,气密性好。
设计时的注意事项•接合部的倾斜角度越大则焊接面积也就越大,但由于结合面不易产生滑动,故需要较大的能源。
另一方面,当倾斜角为锐角时,在焊接时会形成压入状态,并因打开接合部而引起变形、降低了融化密合性等,有可能引起不良问题的发生。
在设计是我们必须考虑到成型品的厚度,一般成品厚度应设定在30~60的范围内。
•将要进行焊接的二个成型品在组合时,确定纵向与横向的焊接深度是尤为重要的。
虽然所设定的尺寸会因使用塑料的等级与性能要求而异,但纵向与横向的设定标准则为0.4~0.7mm左右。
•为了确保焊接时嵌接状态的稳定性,尽可能地将接合部设计的大一点。
实际上成型品的间隙设计的大则不会发生晃荡,且不能有压入。
单侧设定为0.05mm左右为最佳。
•为了达到焊接后的制品尺寸(进入量)的稳定,必须设有浇口塞。
设定位置为可软化焊接的位置。
•若想防止在焊接时发生融化飞边时,最好能设有飞边滞留。
•以下为最具代表性的斜面接合设计案例,以及该接合形状的焊接强度例。
(2)逐次接合属于剪切焊接,由振动方向的面接触结合部获得均一的热量,其气密性、焊接强度都十分良好。
但是,焊接后所产生的飞边会滞留在表面,特别是不允许有飞边产生时,一定要注意。
设计时的注意事项•接合部倾斜角度的考虑方法斜面接合一样。
同时也要考虑到成型品的厚度,我们希望设定在40~50的范围内。
•焊接深度含倾斜部分的设定一般为纵向1.0~1.2mm,横向0.3~0.5mm左右。
当纵向的焊接深度发生变化时其焊接强度也会发生变化,焊接量过大的话在焊接时容易产生飞边,由此引发出破裂、气密不良等问题。
此外,横向的焊接深度以适当为佳。
•间隙的设定斜面接合一样,单侧设定为0.05mm左右。
塑胶制品超声波线设计手册
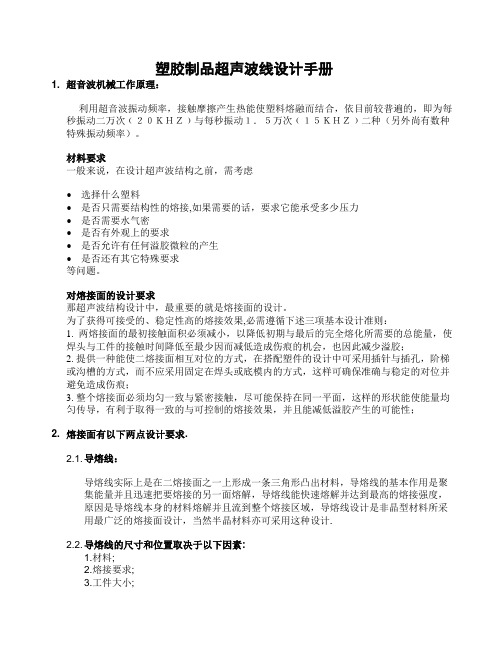
塑胶制品超声波线设计手册1. 超音波机械工作原理:利用超音波振动频率,接触摩擦产生热能使塑料熔融而结合,依目前较普遍的,即为每秒振动二万次﹙20KHZ﹚与每秒振动1.5万次﹙15KHZ﹚二种(另外尚有数种特殊振动频率)。
材料要求一般来说,在设计超声波结构之前,需考虑•选择什么塑料•是否只需要结构性的熔接,如果需要的话,要求它能承受多少压力•是否需要水气密•是否有外观上的要求•是否允许有任何溢胶微粒的产生•是否还有其它特殊要求等问题。
对熔接面的设计要求那超声波结构设计中,最重要的就是熔接面的设计。
为了获得可接受的、稳定性高的熔接效果,必需遵循下述三项基本设计准则:1. 两熔接面的最初接触面积必须减小,以降低初期与最后的完全熔化所需要的总能量,使焊头与工件的接触时间降低至最少因而减低造成伤痕的机会,也因此减少溢胶;2. 提供一种能使二熔接面相互对位的方式,在搭配塑件的设计中可采用插针与插孔,阶梯或沟槽的方式,而不应采用固定在焊头或底模内的方式,这样可确保准确与稳定的对位并避免造成伤痕;3. 整个熔接面必须均匀一致与紧密接触,尽可能保持在同一平面,这样的形状能使能量均匀传导,有利于取得一致的与可控制的熔接效果,并且能减低溢胶产生的可能性;2. 熔接面有以下两点设计要求.2.1. 导熔线:导熔线实际上是在二熔接面之一上形成一条三角形凸出材料,导熔线的基本作用是聚集能量并且迅速把要熔接的另一面熔解,导熔线能快速熔解并达到最高的熔接强度,原因是导熔线本身的材料熔解并且流到整个熔接区域,导熔线设计是非晶型材料所采用最广泛的熔接面设计,当然半晶材料亦可采用这种设计.2.2. 导熔线的尺寸和位置取决于以下因素:1.材料;2.熔接要求;3.工件大小;导熔线必须愈尖愈好,圆顶或扁平的导熔线将减低熔胶流动的效率,当熔接相对容易熔接的塑料(如高硬度和低熔解温度的PS),建议导熔线的高度不可低于0.25㎜,若熔接半晶型或高熔解温度之非晶型塑料(如PC),导熔线高度不可低于0.5㎜;对于采用导熔线设计的半晶型塑料(如PA),熔接强度是来自导熔线三角型的底线之宽度.顶角随壁厚而改变;原则上导熔线设置在哪一边的塑件的熔接面上是没有任何分别的.但在熔接两种不同材料的特殊情况下,一般上是将导熔线设置在熔解温度和硬度较高的那一边的工件的熔接面上;导熔线的设计要有能相互对位的功能如插针与插孔,肋状对位片,沟槽设计,或需要良好的支撑.熔接区域不可放置顶针;2.3. 下面是几种比较典型的导熔线的结构设计:2.3.1. 阶梯熔接面一阶梯熔接面设计主要用于需要精确对位与完全不可接受过熔或溢胶出现在外露表面的高质量要求上;设计注意(图1.)围绕整个工件接口之额外0.25至0.64㎜的空隙,这新增的“影线(美工线)”设计特性使熔接完毕后接口四周将出现0.25至0.64㎜之空隙.如此会产生美观的效应,因为工件与工件之间的变形不易被发觉.如果完全密合,很可能会在某些位置出现溢胶,在别的位置却出现微隙;美工线的设置使微小的变形不易被察觉.这款导熔线设计采用与平头加导熔线设计一样的基本概念(就是:材料、熔接要求、工件大小).注意这款设计的壁厚要求最小尺寸为2㎜图片附件: 1.gif (2007-4-30 14:41, 10.02 K)2.3.2. 沟槽式之熔接面设计—这种设计的主要优点是能从裹外二面防止溢胶,并且可提供对位功能.由于熔胶被封,因此提高达到水气密的机会.也由于沟槽的设计需要一定的公差配合,因此也增加成型的困难度.同时,由于熔接面积的减少,往往造成它的熔接强度比不上平头接面设计,这款导熔线设计采用与平头加导熔线设计一样的基本概念(就是:材料、熔接加工要求、工件大小).注意这款设计的壁厚要求最小尺吋为2㎜图片附件: 2.gif (2007-4-30 14:49, 13.02 K)2.3.3. 咬花面设计--此设计是专为配合导熔线设计使用,熔接面有咬花形状可改善整体熔接质量和强度,原因在于粗糙面能增进摩擦与控制熔解(图3.).通常咬花深度0.076至0.152㎜,其变化视导熔线高度而定.往往得到的优点包括强度的增进、溢胶或微粒的减少、熔接时间的减短以及振幅的减低;图片附件: 3.gif (2007-4-30 14:54, 10.42 K)2.3.4. 十字交叉熔接面设计—在塑件的二熔接面上都设计导熔线并且使它们互呈垂直交叉,使初接触面减至最低并使大量的塑料熔接以增加熔接强度(图4).这种导熔线的每一段尺寸可采取标准导熔线尺寸的60%左右.若欲取得水气密的熔接效果,建议一方的导熔线设计采用如图5.所示之连续钩齿状.同时建议导熔线的顶角角度为600而非标准型的900,同时还建议把比钩齿状设计之导熔线设置在与焊头接触边的塑件上.应注意的是,此款设计将产生大量的溢胶,因此必须考虑溢胶的问题或采用有溢料槽设计的熔接面如沟槽式的熔接面设计图片附件: 4.gif (2007-4-30 15:04, 6.42 K)图片附件: 5.gif (2007-4-30 15:04, 8.72 K)2.3.5. 垂直于墙壁的导熔线设计—用于增加抗撕裂与减少溢胶(图6),这种设计仅适用于只需要结构性的熔接而已;2.3.6. 间断的导熔线设计—可减少熔接面积因此降低能量或所需的功率层级,这种设计只能用于非水气密的结构性熔接而已(图7);图片附件: 6.gif (2007-4-30 15:12, 6.7 K)图片附件: 7.gif (2007-4-30 15:12, 7.22 K)2.3.7. 凿子型导熔线—为壁厚不及1.524㎜之工件所采用(图10.)如果在此等薄壁厚之塑件上使用标准导熔线,熔接强度将会减弱.尖刀处可采0.381至0.508㎜之高度并且采用450角.由于熔接强度取决于导熔线之宽度,当采用此款导熔线设计时必须配合使用咬花面;2.3.8. 凿子型导熔线—为壁厚不及1.524㎜之工件所采用(图8)如果在此等薄壁厚之塑件上使用标准导熔线,熔接强度将会减弱.尖刀处可采0.381至0.508㎜之高度并且采用450角.由于熔接强度取决于导熔线之宽度,当采用此款导熔线设计时必须配合使用咬花面;图片附件: 8.gif (2007-4-30 15:16, 11.17 K)2.3.9. 特殊熔接面设计—为了使较难熔接的塑料或外型不规则之塑件达到水气密熔接,可能需要使用弹性油封与旋绕道以阻隔熔胶之流动.图9.显示一种配合“O”型环的熔接面设计.有一要点应注意“O”型环在熔接完毕后只压缩10%至15%而已.柱状塑件与插孔(大头柱子熔接)亦可成功的配合“O”型环以达到水气密;图片附件: 9.gif (2007-4-30 15:22, 4.29 K)2.4. 剪切的设计注意点:2.4.1. 剪切式熔接面设计—在熔接尼龙、乙缩醛、聚乙烯、聚丙烯和热塑性聚酯这类半晶型塑料时,采用导熔线设计有时是不能达到预期效果的.这是因为这类半晶型塑料在相对很狭窄的温度变化范围内迅速从固态再变回固态.导熔线熔化时还未来得及与对面塑件熔合即开始固化,因此熔接强度只赖由三角形之宽度所提供.因此当熔接以上塑料,如果外型许可的话的建议采用剪切式熔接面设计,可达到理想的熔接效果.剪切式熔接面的熔接过程是,首先熔化开始接触的小面积材料,然后沿着壁面继续垂直向下而有控制的导引入下工件裹头去(请观看图10).这种熔接方式绝对不会让四周的空气接触到熔解区域,因此可获得高强度的结构性或水气密的熔接.由于上述原因,剪切式熔接设计特别适用于半晶型塑料材料;熔接强度与熔接面垂直向下的熔接面积有直接关系.强度可由改变熔接深度去达到个别应用的熔接要求.注意:若熔接强要求超过墙壁的接强,建议熔接深度为壁厚之1.25倍;剪切式熔接需要有坚固的侧边墙壁支撑以避免熔接时变形.下工件的四周墙壁高度必须高至接口位置,内壁必须与工件外部型体完全吻合.上工件的整体结构也应十分坚固以防止内倾变形.对于熔接部位在墙壁中央位置,可采用图11.所示的变体沟槽设计.这种设计也适用于大型塑件的熔接.建议采用单边干涉如图12.所示图片附件: 10.gif (2007-4-30 15:35, 9.95 K)图片附件: 11.gif (2007-4-30 15:35, 3.69 K)图片附件: 12.gif (2007-4-30 15:35, 5.94 K)应当注意的是如果工件最大尺吋在89㎜或更大并且复杂或者有直角的转角就不宜采用剪切式熔接设计,因为这会给上下工件之间所必须保持的成型公差带来困扰.也就是难于保持稳定的熔接效果.在这种情况下只能建议采用导熔线设计.当只需要结构性熔接而已.(即不要求强度与水气密),可采用图13.所示的间断性的垂直导熔线设计.如此可减少整个熔接面积,也因此减少所需的能量或功率.伤痕出现的机会亦可大大的减少图14提供干涉尺吋与工件尺吋公差对应于最大之工件外形尺吋图片附件: 13.gif (2007-4-30 15:40, 7.3 K)图片附件: 14.gif (2007-4-30 15:43, 4.35 K)2.5. 熔接面设计的其它考虑:1.直角转角会聚集应力.如果塑件上面有若干应力聚集点,在经过超音波机械振动后,塑件的高应力区域如转角、边沿与交界处可能出现断裂或其它的伤痕.补救的措施是尽量增加转角之圆弧度(0.508㎜).请参阅图152.塑件上的孔位或缺口像气孔类的开口会阻断焊头传送出来的超音波能量(图16).它对熔接的影响取决于塑件材料种类(尤其是半晶型塑料)和开口的大小,在缺口的正下方几乎没有办法熔接.当塑件上有缺口或有转弯形状,塑料将会阻碍能量的传导,使能量更难到达熔接面,尤其是剪切式熔接.在塑件设计过程当中应特别注意避免此类问题的发生.由于钢模设计不当造成塑件内出现气孔,这种情况也会使能量传导受阻或使塑件穿孔;3.近场与远场熔接之对比一近场熔接指的是熔接面距离焊头接触位置在6.35㎜以内;大于6.35㎜的距离则为远场熔接(图17),如上所述,因为半晶型分子结构塑料会阻碍振动能量的传导,所以难以对它们作远场熔接.至于非晶型塑料,由于分子随意排列,振动能量容易在其间传导并且衰减也很小.在低硬度塑料裹头也会发生振动能量的衰减现象.因此在设计塑料产品过程当中应考虑到是否有足够的能量传达熔接面;图片附件: 15.gif (2007-4-30 15:52, 6.02 K)图片附件: 16.gif (2007-4-30 15:52, 9.93 K)图片附件: 17.gif (2007-4-30 15:52, 13.72 K)4.塑件的分肢,柄,或其它细节—机械振动会影响塑件内外表面上的各种突出物,可能造成断裂(图18.)下列各种措施能减低或消除这种影响:․将突出物与主体连接处设计成最大的圆弧状.․利用外加手段削减连接处的扭折.․增加材料的厚度.․评估采用其它频率的超音波5.薄膜效应—一种能量聚集效应造成塑件出现烧穿现象.在平的圆形的、壁厚较薄的位置最为常见,通过采取下列一个或结合数个措施可以克服这种现象(图19)․减少熔接时间․改变振幅․采用振幅剖析․在焊头上设计节点活塞․增加壁厚․使用内部支撑肋骨․评估其它频率6.焊头接触与放置位置在塑件熔接时可扮演举足轻重的角色.一般而言,焊头的尺寸应该大到足以遮盖整个工作,因此从顶直接施压在熔接区域上,(图20.)这有利于机械振动能量的传导并可避免接触面留下伤痕.焊头或塑件的表面也可以在熔接区域凸起以增进接触的效能;如此将改善熔接效果的稳定度,注意:焊头与工件的接触面必须大于熔接区域的总面积,否则将有可能导至表面伤痕.图片附件: 18.gif (2007-4-30 16:08, 7.8 K) 图片附件: 19.gif (2007-4-30 16:08, 4.76 K) 图片附件: 20.gif (2007-4-30 16:08, 12.5 K)另:1.相同熔点的塑料材质熔接强度愈强。
超声波焊接设计要求

超声波焊接设计要求导言:超声波焊接是一种常用的金属焊接方法,它利用超声波振动来产生热量,从而实现材料的焊接。
在超声波焊接的设计过程中,需要考虑一系列的要求和指导原则,以确保焊接质量和工艺稳定性。
本文将就超声波焊接设计的要求进行详细阐述。
一、焊接部件的设计要求1. 材料选择:焊接部件的材料选择应根据焊接的要求来确定。
常见的焊接材料包括金属、塑料、陶瓷等。
在选择材料时,应考虑其导热性、熔点、熔化温度范围等因素。
2. 接头设计:焊接接头的设计应符合力学原理,确保焊接强度和密封性。
接头的形状和尺寸应适当选择,以确保焊接过程中的振动传递和能量转化。
3. 表面处理:焊接部件的表面处理对焊接质量有重要影响。
在进行超声波焊接前,应确保焊接部件的表面清洁、平整,以避免焊接时出现气泡、脱离等问题。
二、焊接设备的设计要求1. 超声波振动系统:焊接设备中的超声波振动系统是实现焊接的核心部分。
其设计应考虑频率、功率、振幅等参数的选择,以及振动传递的稳定性和可靠性。
2. 压力系统:焊接设备中的压力系统用于施加焊接压力。
压力的大小应根据焊接材料和接头的要求来确定,并确保其稳定、均匀施加在焊接部件上。
3. 控制系统:焊接设备的控制系统用于控制焊接过程中的参数,如振动频率、压力大小、焊接时间等。
控制系统的设计应可靠、灵活,以满足不同焊接要求。
三、焊接过程的设计要求1. 焊接参数的选择:焊接过程中的参数选择对焊接质量和工艺稳定性至关重要。
应根据焊接材料、接头形状和尺寸等因素,合理选择振动频率、压力大小、焊接时间等参数。
2. 焊接速度的控制:焊接速度的控制直接影响焊接质量。
过快的焊接速度容易导致焊接不充分,而过慢的焊接速度则容易造成热损伤。
应根据焊接部件的要求,控制焊接速度在适当范围内。
3. 焊接过程的监测:焊接过程中的监测对于及时发现焊接缺陷和调整焊接参数至关重要。
可以利用传感器监测焊接过程中的温度、压力等参数,并通过控制系统进行实时监测和调整。
2019超声波焊接的塑件设计规范.
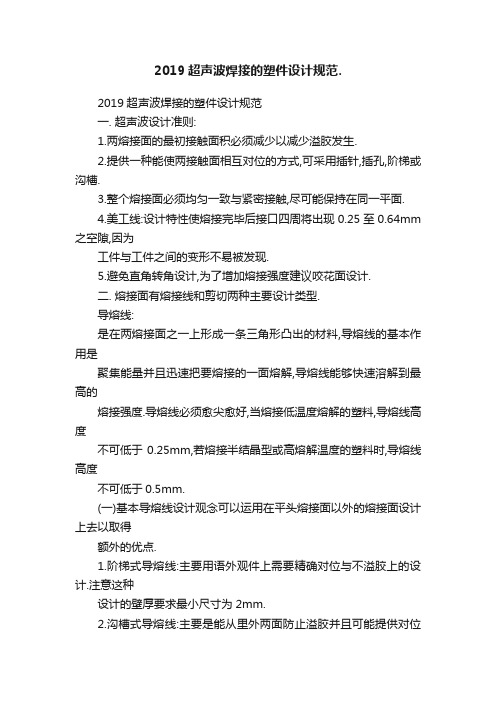
2019超声波焊接的塑件设计规范.2019超声波焊接的塑件设计规范一. 超声波设计准则:1.两熔接面的最初接触面积必须减少以减少溢胶发生.2.提供一种能使两接触面相互对位的方式,可采用插针,插孔,阶梯或沟槽.3.整个熔接面必须均匀一致与紧密接触,尽可能保持在同一平面.4.美工线:设计特性使熔接完毕后接口四周将出现0.25至0.64mm 之空隙,因为工件与工件之间的变形不易被发现.5.避免直角转角设计,为了增加熔接强度建议咬花面设计.二. 熔接面有熔接线和剪切两种主要设计类型.导熔线:是在两熔接面之一上形成一条三角形凸出的材料,导熔线的基本作用是聚集能量并且迅速把要熔接的一面熔解,导熔线能够快速溶解到最高的熔接强度.导熔线必须愈尖愈好,当熔接低温度熔解的塑料,导熔线高度不可低于0.25mm,若熔接半结晶型或高熔解温度的塑料时,导熔线高度不可低于0.5mm.(一)基本导熔线设计观念可以运用在平头熔接面以外的熔接面设计上去以取得额外的优点.1.阶梯式导熔线:主要用语外观件上需要精确对位与不溢胶上的设计.注意这种设计的壁厚要求最小尺寸为2mm.2.沟槽式导熔线:主要是能从里外两面防止溢胶并且可能提供对位功能,提升高度的熔合使熔接面积增加而提升熔接强度的设计,注意这况设计的壁厚要求最小尺寸为2mm.3.十字交叉式导熔线:是一导熔线使它们相互呈垂直交叉,能缩短熔接时间及降低熔接时所消耗的功率,且并不影响熔接强度,但是会产生高低断差以及溢胶.4.连续沟齿状导熔线:若取得完全密合的熔接效果,建议一方的导熔线设计采用连续沟齿状.此款设计将产生大量的溢胶.5.垂直与墙壁式导熔线:适用于增加抗撕裂与减少溢胶,这种设计仅适用于只需要结构性的熔接而已.6.间断的导熔线:可以减少熔接面积因此降低能量或所需的功率层级,这种设计只能用非要求高强度的结构性熔接而已.7.凿子型导熔线:壁厚不到1.524mm时可以采用,适用于薄壁以及小的工件的塑件上使用,但是熔接强度将会减弱.8.特殊熔接面设计:使用于以防水为优先考虑的设计上,使较难熔接的塑料或外型不规则之塑件达到紧密接合,借用弹性油封来帮助防水的功能.(二) 剪切式熔接面设计:剪切式熔接面的熔接过程是,首先熔化开始接触的小面积材料,然后沿着壁面继续垂直向下而有控制的引入下工件里头去.塑料在相对很狭窄的温度变化范围内迅速从固态变为液态再变回固态.下工件的四周壁的高度必须高至接口位置,内壁必须与工件外部型体完全吻合.1.形状复杂或者有直角的转角的就不宜采用剪切式的熔接设计.2.适合高强度的结构性或水气密的熔接.3.熔接需要有坚固的侧边壁支持以避免熔接时的变形.注意:若熔接深度要求超过壁的接触壁,建议熔接深度为壁厚的 1.25倍.三近场与远场熔接的对比:近场熔接指的是熔接面积距离焊头接触位置在6.356mm以内;大于6.356mm的距离则为远场熔接.因此在设计塑胶产品的过程当中应考虑到是否有足够的能量传导熔接面.四薄膜效应:在平的圆形的,壁较薄的位置最为常出现塑件烧穿现象,通过采取以下的措施可以克服这种现象.1.减少熔接时间.2.改变振幅.3.采用振幅剖析.4.在焊头上设计调节活塞.5.增加壁厚.6.塑件在其部位使用内部支撑筋.7.使用其他频率.五.焊头接触与放置位置:焊头或塑件的表面也可以在熔接区域凸起以增进接触的效能.注意:焊头与工件的接触面必须大于熔接区域的总面积,否则将有可能导致表面伤痕.。
塑胶件的超声波焊接工艺下

焊头
焊头
夹具
近场焊接
远场焊接
ห้องสมุดไป่ตู้
A 超声波焊接—近场焊接与远场焊接
有资料规定:在20KHz系统中,将焊头/上焊件 界面到焊接界面之间的距离小于6mm的称为近场焊 接;大于6mm的称为远场焊接。 当声波频率是20KHz时,由于聚合物结构差异, 声波在聚合物中的波长约为6cm~13cm。
(2)超声波焊口设计一般分为(端面式)和(剪切式)。
(3)在20KHz系统中,将焊头/上焊件界面到焊接界面之间的 距离小于6mm的称为(近场)焊接;大于6mm的称为(远场) 焊接。
2.判断题 (1)所有焊接尽量使用近场焊接。(正确) (2)聚合物的熔点越高,其焊接所需的超音波能量越 少 (。3)(半错结误晶)聚合物焊接不建议使用远场。(正确)
A 超声波焊接—近场焊接与远场焊接
近场焊接:
20kHz操作系统中,焊头与焊接面距离远小于 波长。焊接面与焊头表面的振幅几乎相等。 此类焊接质量易于控制。
远场焊接:
焊头距离焊接面距离近于或大于波长,焊接面 的振幅取决于声波在聚合物中的传输性质。 较近场焊接:耗能大、焊件伤害大。 此类焊接质量更加难以控制。
A 超声波焊接--焊接构件设计应注意的问题
设计中常见的几种现象说明
焊接终止定位:一般不建议使用结构定位 导向、定位:设计中常出现缺失 焊接方式选择:端面、剪切、端面+剪切 焊接缺陷:
假焊:材料、结构、工艺、工装 焊伤:结构、焊口设计、焊头接触面位置及面积、
工装、功率
1.填空 (1).非结晶聚合物分子排列无序,能有效传输(超音速)振 动,实现良好焊接的压力,振幅范围宽。
面质量要求较高
导融线
超声波焊接的塑件设计规范

超声波焊接的塑件设计规范集团标准化小组:[VVOPPT-JOPP28-JPPTL98-LOPPNN]超声波焊接的塑件设计规范一. 超声波设计准则:1.两熔接面的最初接触面积必须减少以减少溢胶发生.2.提供一种能使两接触面相互对位的方式,可采用插针,插孔,阶梯或沟槽.3.整个熔接面必须均匀一致与紧密接触,尽可能保持在同一平面.4.美工线:设计特性使熔接完毕后接口四周将出现0.25至0.64mm之空隙,因为工件与工件之间的变形不易被发现.5.避免直角转角设计,为了增加熔接强度建议咬花面设计.二. 熔接面有熔接线和剪切两种主要设计类型.导熔线:是在两熔接面之一上形成一条三角形凸出的材料,导熔线的基本作用是聚集能量并且迅速把要熔接的一面熔解,导熔线能够快速溶解到最高的熔接强度.导熔线必须愈尖愈好,当熔接低温度熔解的塑料,导熔线高度不可低于0.25mm,若熔接半结晶型或高熔解温度的塑料时,导熔线高度不可低于0.5mm.(一)基本导熔线设计观念可以运用在平头熔接面以外的熔接面设计上去以取得额外的优点.1.阶梯式导熔线:主要用语外观件上需要精确对位与不溢胶上的设计.注意这种设计的壁厚要求最小尺寸为2mm.2.沟槽式导熔线:主要是能从里外两面防止溢胶并且可能提供对位功能,提升高度的熔合使熔接面积增加而提升熔接强度的设计,注意这况设计的壁厚要求最小尺寸为2mm.3.十字交叉式导熔线:是一导熔线使它们相互呈垂直交叉,能缩短熔接时间及降低熔接时所消耗的功率,且并不影响熔接强度,但是会产生高低断差以及溢胶.4.连续沟齿状导熔线:若取得完全密合的熔接效果,建议一方的导熔线设计采用连续沟齿状.此款设计将产生大量的溢胶.5.垂直与墙壁式导熔线:适用于增加抗撕裂与减少溢胶,这种设计仅适用于只需要结构性的熔接而已.6.间断的导熔线:可以减少熔接面积因此降低能量或所需的功率层级,这种设计只能用非要求高强度的结构性熔接而已.7.凿子型导熔线:壁厚不到1.524mm时可以采用,适用于薄壁以及小的工件的塑件上使用,但是熔接强度将会减弱.8.特殊熔接面设计:使用于以防水为优先考虑的设计上,使较难熔接的塑料或外型不规则之塑件达到紧密接合,借用弹性油封来帮助防水的功能.(二)剪切式熔接面设计:剪切式熔接面的熔接过程是,首先熔化开始接触的小面积材料,然后沿着壁面继续垂直向下而有控制的引入下工件里头去.塑料在相对很狭窄的温度变化范围内迅速从固态变为液态再变回固态.下工件的四周壁的高度必须高至接口位置,内壁必须与工件外部型体完全吻合.1.形状复杂或者有直角的转角的就不宜采用剪切式的熔接设计.2.适合高强度的结构性或水气密的熔接.3.熔接需要有坚固的侧边壁支持以避免熔接时的变形.注意:若熔接深度要求超过壁的接触壁,建议熔接深度为壁厚的1.25倍.三近场与远场熔接的对比:近场熔接指的是熔接面积距离焊头接触位置在6.356mm以内;大于6.356mm的距离则为远场熔接.因此在设计塑胶产品的过程当中应考虑到是否有足够的能量传导熔接面.四薄膜效应:在平的圆形的,壁较薄的位置最为常出现塑件烧穿现象,通过采取以下的措施可以克服这种现象.1.减少熔接时间.2.改变振幅.3.采用振幅剖析.4.在焊头上设计调节活塞.5.增加壁厚.6.塑件在其部位使用内部支撑筋.7.使用其他频率.五.焊头接触与放置位置:焊头或塑件的表面也可以在熔接区域凸起以增进接触的效能.注意:焊头与工件的接触面必须大于熔接区域的总面积,否则将有可能导致表面伤痕.。
超声波塑料件的结构设计

超声波塑料件的结构设计公司标准化编码 [QQX96QT-XQQB89Q8-NQQJ6Q8-MQM9N]塑料件必须有一定的刚性及足够的壁厚,太薄的壁厚有一定的危险性,超声波焊接时是需要加压的,一般气压为2-6kgf/cm2 。
所以塑料件必须保证在加压情况下基本不变形。
罐状或箱形塑料等,在其接触焊头的表面会引起共振而形成一些集中的能量聚集点,从而产生烧伤、穿孔的情况(如图1所示),在设计时可以罐状顶部做如下考虑○1 加厚塑料件○2 增加加强筋○3 焊头中间位置避空尖角如果一个注塑出来的零件出现应力非常集中的情况,比如尖角位,在超声波的作用下会产生折裂、融化。
这种情况可考虑在尖角位加R角。
如图2所示。
塑料件的附属物注塑件内部或外部表面附带的突出或细小件会因超声波振动产生影响而断裂或脱落,例如固定梢等(如图3所示)。
通过以下设计可尽可能减小或消除这种问题:○1 在附属物与主体相交的地方加一个大的R角,或加加强筋。
○2 增加附属物的厚度或直径。
如被焊头接触的零件有孔或其它开口,则在超声波传递过程中会产生干扰和衰减(如图4所示),根据材料类型(尤其是半晶体材料)和孔大小,在开口的下端会直接出现少量焊接或完全熔不到的情况,因此要尽量预以避免。
塑料件中薄而弯曲的传递结构被焊头接触的塑件的形状中,如果有薄而弯曲的结构,而且需要用来传达室递超声波能量的时候,特别对于半晶体材料,超声波震动很难传递到加工面(如图5所示),对这种设计应尽量避免。
近距离和远距离焊接近距离焊接指被焊接位距离焊头接触位在6mm以内,远距离焊接则大于6mm,超声波焊接中的能量在塑料件传递时会被衰减地传递。
衰减在低硬底塑料里也较厉害,因此,设计时要特别注意要让足够的能量传到加工区域。
远距离焊接,对硬胶(如PS,ABS,AS,PMMA)等比较适合,一些半晶体塑料(如POM,PETP,PBTB,PA)通过合适的形状设计也可用于远距离焊接。
塑料件焊头接触面的设计注塑件可以设计成任何形状,但是超声波焊头并不能随意制作。
超声波焊接技术大全
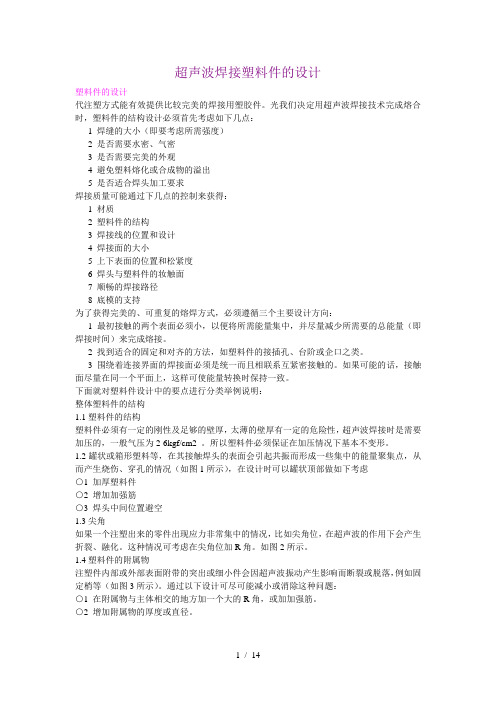
超声波焊接塑料件的设计塑料件的设计代注塑方式能有效提供比较完美的焊接用塑胶件。
光我们决定用超声波焊接技术完成熔合时,塑料件的结构设计必须首先考虑如下几点:1 焊缝的大小(即要考虑所需强度)2 是否需要水密、气密3 是否需要完美的外观4 避免塑料熔化或合成物的溢出5 是否适合焊头加工要求焊接质量可能通过下几点的控制来获得:1 材质2 塑料件的结构3 焊接线的位置和设计4 焊接面的大小5 上下表面的位置和松紧度6 焊头与塑料件的妆触面7 顺畅的焊接路径8 底模的支持为了获得完美的、可重复的熔焊方式,必须遵循三个主要设计方向:1 最初接触的两个表面必须小,以便将所需能量集中,并尽量减少所需要的总能量(即焊接时间)来完成熔接。
2 找到适合的固定和对齐的方法,如塑料件的接插孔、台阶或企口之类。
3 围绕着连接界面的焊接面必须是统一而且相联系互紧密接触的。
如果可能的话,接触面尽量在同一个平面上,这样可使能量转换时保持一致。
下面就对塑料件设计中的要点进行分类举例说明:整体塑料件的结构1.1塑料件的结构塑料件必须有一定的刚性及足够的壁厚,太薄的壁厚有一定的危险性,超声波焊接时是需要加压的,一般气压为2-6kgf/cm2 。
所以塑料件必须保证在加压情况下基本不变形。
1.2罐状或箱形塑料等,在其接触焊头的表面会引起共振而形成一些集中的能量聚集点,从而产生烧伤、穿孔的情况(如图1所示),在设计时可以罐状顶部做如下考虑○1 加厚塑料件○2 增加加强筋○3 焊头中间位置避空1.3尖角如果一个注塑出来的零件出现应力非常集中的情况,比如尖角位,在超声波的作用下会产生折裂、融化。
这种情况可考虑在尖角位加R角。
如图2所示。
1.4塑料件的附属物注塑件内部或外部表面附带的突出或细小件会因超声波振动产生影响而断裂或脱落,例如固定梢等(如图3所示)。
通过以下设计可尽可能减小或消除这种问题:○1 在附属物与主体相交的地方加一个大的R角,或加加强筋。
NBT47013.32015标准2019超声Ⅲ级班

恢复了超声测厚并增加了不锈钢堆焊层的超声测厚, 扩大了适用范围,更多地采用了欧标,体现了与国际接 轨的发展方向。
路漫漫其修远兮, 吾将上下而求索
NBT47013.32015标准 2019超声Ⅲ级班
路漫漫其修远兮, 吾将上下而求索
2020年4月12日星期日
NB/T47013.3标准的发展
1、JB4730-94 第三篇 超声检测 包括钢板、锻件、复合钢板、无缝钢管、高压螺栓件
、奥氏体钢锻件、钢焊缝、不锈钢堆焊层、铝焊缝、超 声测厚等; 2、 JB/T4730.3-2005
路漫漫其设备焊接接头工件厚度的适用范围从8mm~ 400mm扩大到了6~500mm;
12、重新设计了CSK-IIA和CSK-IVA试块上人工反射体 的位置和数量。这样既保证检测区域覆盖,又适用于 直探头检测焊接接头基准灵敏度的调节。新CSK-IIA试 块适用工件厚度范围为6mm~200mm,该试块主要参考 欧盟(EN)和日本(JIS)标准,人工反射体直径仍为 φ2mm ;新CSK-IVA试块适用工件厚度大于200mm~ 500mm。CSK-IVA试块主要在参考美国ASME规范的基础 上进行了改进,人工反射体直径统一为φ6mm;
13、细化了不同类型焊接接头超声检测要求。涉及内 容包括平板对接接头、T型焊接接头、插入式接管角接 接头、L型焊接接头、安放式接管与筒体(或封头)角 接接头、十字焊接接头、嵌入式接管与筒体(或封头 )对接接头等;
路漫漫其修远兮, 吾将上下而求索
14、重新设计了GS试块。增加了圆弧反射面等。主要有利 于弧面探头的时基线调整;
- 1、下载文档前请自行甄别文档内容的完整性,平台不提供额外的编辑、内容补充、找答案等附加服务。
- 2、"仅部分预览"的文档,不可在线预览部分如存在完整性等问题,可反馈申请退款(可完整预览的文档不适用该条件!)。
- 3、如文档侵犯您的权益,请联系客服反馈,我们会尽快为您处理(人工客服工作时间:9:00-18:30)。
2019超声波焊接的塑件设计规范
一. 超声波设计准则:
1.两熔接面的最初接触面积必须减少以减少溢胶发生.
2.提供一种能使两接触面相互对位的方式,可采用插针,插孔,阶梯或沟槽.
3.整个熔接面必须均匀一致与紧密接触,尽可能保持在同一平面.
4.美工线:设计特性使熔接完毕后接口四周将出现0.25至0.64mm之空隙,因为
工件与工件之间的变形不易被发现.
5.避免直角转角设计,为了增加熔接强度建议咬花面设计.
二. 熔接面有熔接线和剪切两种主要设计类型.
导熔线:
是在两熔接面之一上形成一条三角形凸出的材料,导熔线的基本作用是
聚集能量并且迅速把要熔接的一面熔解,导熔线能够快速溶解到最高的
熔接强度.导熔线必须愈尖愈好,当熔接低温度熔解的塑料,导熔线高度
不可低于0.25mm,若熔接半结晶型或高熔解温度的塑料时,导熔线高度
不可低于0.5mm.
(一)基本导熔线设计观念可以运用在平头熔接面以外的熔接面设计上去以取得
额外的优点.
1.阶梯式导熔线:主要用语外观件上需要精确对位与不溢胶上的设计.注意这种
设计的壁厚要求最小尺寸为2mm.
2.沟槽式导熔线:主要是能从里外两面防止溢胶并且可能提供对位功能,提升高
度的熔合使熔接面积增加而提升熔接强度的设计,注意这况设计的壁厚要求最小尺寸为2mm.
3.十字交叉式导熔线:是一导熔线使它们相互呈垂直交叉,能缩短熔接时间及降
低熔接时所消耗的功率,且并不影响熔接强度,但是会产生高低断差以及溢胶.
4.连续沟齿状导熔线:若取得完全密合的熔接效果,建议一方的导熔线设计采用
连续沟齿状.此款设计将产生大量的溢胶.
5.垂直与墙壁式导熔线:适用于增加抗撕裂与减少溢胶,这种设计仅适用于只需
要结构性的熔接而已.
6.间断的导熔线:可以减少熔接面积因此降低能量或所需的功率层级,这种设计
只能用非要求高强度
的结构性熔接而已.
7.凿子型导熔线:壁厚不到 1.524mm时可以采用,适用于薄壁以及小的工件的塑
件上使用,但是熔接强度将会减弱.
8.特殊熔接面设计:使用于以防水为优先考虑的设计上,使较难熔接的塑料或外
型不规则之塑件达到紧密接合,借用弹性油封来帮助防水的功能.
(二) 剪切式熔接面设计:剪切式熔接面的熔接过程是,首先熔化开始接触的小面积材料,然后沿着壁面继续垂直向下而有控制的引入下工件里头去.塑料在相对很狭窄的温度变化范围内迅速从固态变为液态再变回固态.下工件的四周壁的高度必须高至接口位置,内壁必须与工件外部型体完全吻合.
1.形状复杂或者有直角的转角的就不宜采用剪切式的熔接设计.
2.适合高强度的结构性或水气密的熔接.
3.熔接需要有坚固的侧边壁支持以避免熔接时的变形.
注意:若熔接深度要求超过壁的接触壁,建议熔接深度为壁厚的 1.25倍.
三近场与远场熔接的对比:近场熔接指的是熔接面积距离焊头接触位置在
6.356mm以内;大于6.356mm的距离则为远场熔接.因此在设计塑胶产品的过程当中应考虑到是否有足够的能量传导熔接面.
四薄膜效应:在平的圆形的,壁较薄的位置最为常出现塑件烧穿现象,通过采取以下的措施可以克服这种现象.
1.减少熔接时间.
2.改变振幅.
3.采用振幅剖析.
4.在焊头上设计调节活塞.
5.增加壁厚.
6.塑件在其部位使用内部支撑筋.
7.使用其他频率.
五.焊头接触与放置位置:焊头或塑件的表面也可以在熔接区域凸起以增进接触的效能.
注意:焊头与工件的接触面必须大于熔接区域的总面积,否则将有可能导致表面伤痕.。