尿素合成、制造工艺
尿素 生产工艺

尿素生产工艺
尿素是一种最常用的氮肥,也是农田中使用最广泛的肥料之一。
它是在压缩空气和氨的存在下制造的。
下面是尿素生产的工艺流程。
首先,通过空气分离装置将空气中的氮气和氧气分离出来。
这样纯净的氮气就可以用作后续的制氨过程。
然后,在制氨装置中,将氮气与纯氢气经过高温高压条件下的反应,生成氨气。
这个反应通常使用铁-钼催化剂来加速反应
速度。
制氨反应可以分为低温反应和高温反应两个阶段,低温反应通常在200-300°C下进行,生成的氨气含量在15-20%;
而高温反应则在高温下进行,将氮气和未反应的氢气继续反应,使氨气的含量达到25-35%。
接下来,通过氨合成器将制得的氨气与二氧化碳反应,生成尿素。
氨合成器中采用铁-钼催化剂,条件为200-220°C,压力为150-200 atm。
尿素反应生成的热量通过蒸汽汽化剂来排出。
尿素的反应方程式为:
2NH3 + CO2 → NH2CONH2 + H2O
尿素生成之后,需要通过冷却、脱水和干燥的过程来提高尿素的纯度。
这些过程通常通过旋转蒸发器、冷却器和离心机来完成。
最后,尿素需要进行粉碎和筛分处理,以获得所需的颗粒大小
和均匀度。
粉碎过程通常使用球磨机或者研磨机来完成,而筛分则使用振动筛或者离心筛来分离不同颗粒大小的尿素。
总的来说,尿素的生产过程包括氨的制备、尿素的合成、尿素的精制和颗粒的粉碎筛分等步骤。
这些步骤通过控制温度、压力和催化剂的选择来实现高效的生产。
尿素的工艺流程不仅提高了氮肥的产量,而且还减少了对环境的污染。
尿素的生产方法
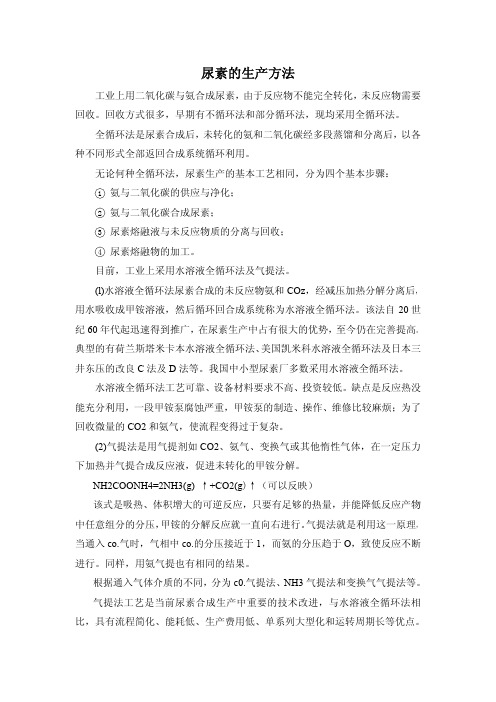
尿素的生产方法工业上用二氧化碳与氨合成尿素,由于反应物不能完全转化,未反应物需要回收。
回收方式很多,早期有不循环法和部分循环法,现均采用全循环法。
全循环法是尿素合成后,未转化的氨和二氧化碳经多段蒸馏和分离后,以各种不同形式全部返回合成系统循环利用。
无论何种全循环法,尿素生产的基本工艺相同,分为四个基本步骤:1氨与二氧化碳的供应与净化;2氨与二氧化碳合成尿素;3尿素熔融液与未反应物质的分离与回收;4尿素熔融物的加工。
目前,工业上采用水溶液全循环法及气提法。
(l)水溶液全循环法尿素合成的未反应物氨和COz,经减压加热分解分离后,用水吸收成甲铵溶液,然后循环回合成系统称为水溶液全循环法。
该法自20世纪60年代起迅速得到推广,在尿素生产中占有很大的优势,至今仍在完善提高。
典型的有荷兰斯塔米卡本水溶液全循环法、美国凯米科水溶液全循环法及日本三井东压的改良C法及D法等。
我国中小型尿素厂多数采用水溶液全循环法。
水溶液全循环法工艺可靠、设备材料要求不高、投资较低。
缺点是反应热没能充分利用,一段甲铵泵腐蚀严重,甲铵泵的制造、操作、维修比较麻烦;为了回收微量的CO2和氨气,使流程变得过于复杂。
(2)气提法是用气提剂如CO2、氨气、变换气或其他惰性气体,在一定压力下加热并气提合成反应液,促进未转化的甲铵分解。
NH2COONH4=2NH3(g)↑+CO2(g)↑(可以反映)该式是吸热、体积增大的可逆反应,只要有足够的热量,并能降低反应产物中任意组分的分压,甲铵的分解反应就一直向右进行。
气提法就是利用这一原理,当通入co.气时,气相中co.的分压接近于1,而氨的分压趋于O,致使反应不断进行。
同样,用氨气提也有相同的结果。
根据通入气体介质的不同,分为c0.气提法、NH3气提法和变换气气提法等。
气提法工艺是当前尿素合成生产中重要的技术改进,与水溶液全循环法相比,具有流程简化、能耗低、生产费用低、单系列大型化和运转周期长等优点。
浅析尿素合成工艺及流程的选择

浅析尿素合成工艺及流程的选择【摘要】尿素作为一种重要的化学肥料和工业原料,在世界范围内广泛使用。
自从1922年尿素开始工业化生产以来,许多国家都致力于尿素生产系统的研究,在合成机理、热力学性质和工艺流程方面都有创新和进展。
本文从尿素生产系统热力学模型的研究入手,对尿素生产工艺流程进行研究,在此基础上开发尿素生产工艺计算与优化软件,以帮助指导尿素工业生产。
【关键词】尿素;生产;工艺;优化1 尿素合成的基本原理用氨合成尿素的反应,通常认为是按以下两个步骤,在合成塔内连续进行:第一步:氨作用生成氨基甲酸铵2NH3+CO2=NH4COONH2+Q1第二步:氨基甲酸铵脱水生成尿素NH4COONH2=CO(NH2)2+H2O-Q2这两个反应都是可逆反应,反应(1)是放热反应,在常温下实际上可以进行到底,150℃时,反应进行的很快、很完全,为瞬时反应,而反应(2)是吸热反应,进行的比较缓慢,且不完全,这就使其成为合成尿素的控制反应。
尿素的生产过程要求在液相中进行,即氨基甲酸铵必须呈液态存在。
温度要高于熔点145-155℃,因此,决定了尿素的合成要在高温下进行。
2 尿素合成工艺条件的选择2.1 过剩氨过剩氨是比较氨与二氧化碳的比化学反应量所多的氨,常以百分率表示,或氨比二氧化碳表示。
过剩氨可以使反应的平衡趋向生成尿素的一方,使产率提高。
过剩氨也可以合成速度加快,提高尿素产率,过剩氨的存在,可与系统中的水结合,从而降低了水的浓度,抑制了副反应的发生。
NH4COONH2+H2O→(NH4)2CO2(NH4)2CO→NH4HCO3+NH2NH4HCO→NH4+CO2+H2O过剩氨的增加过大,二氧化碳转化率增加率也逐渐增加,并且提高了合成塔内反应系的平衡压力;过剩氨的增加,会破坏反应物的自然平衡,为维持合成塔内顶定温度,就必须提高浓氨预热温度;过剩氨的增加,会是反应混合物的比重下降,所需反应釜的容积加大,处理未生成尿素的反应物的设备也更大,动力消耗增加。
无机化工工艺学-尿素
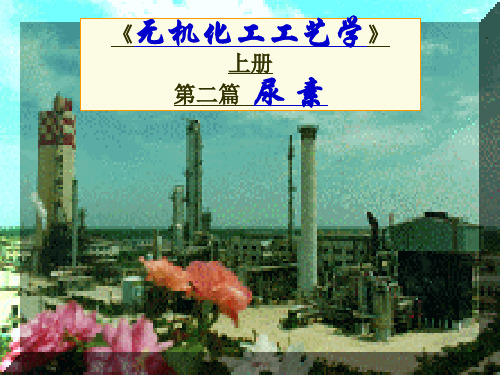
半循环法:将一部 分或大部分未反应的 NH3和CO2返回合成塔 使用,这类循环氨的 利用率为42-73%。
1-二氧化碳压缩机;2-液氨泵;3-尿素合成塔; 4-预分离器;5-高压加热分离器;6-低压加热分 解器;7-高压吸收器;8-氨冷凝器
全循环法(流程附后1.4):将未转化成尿素的NH3和CO2经减压加热 或气提分离后,全部返回合成系统循环利用,构成密闭的循环系统 ,原料的利用最充分,氨利用率高达98%以上。
④气提法 利用一种气体介质在与合成等压的条件下分解甲铵并将分解物返
回系统。 依气提介质的不同分为CO2气提法、NH3气提法、变换气气提法。
优点:热量回收完全,低压NH3和CO2处理量较少,技术经济指标先 进,是尿素发展的方向。
20世纪60年代初期, 斯塔米卡邦与DSM的研究中心一起开发了新的 尿素工艺———二氧化碳气提法,并于1967 年建成工厂投入生产,使尿 素生产的能耗大为降低。
意大利的SnamProgetti 也于1966 年建成了第一个以NH3作为气提 气的氨气提法尿素工厂(日产70 t) ,其设备采用框架式立体布置,而且 NH3直接加入气提塔底部,为第一代氨气提法。70 年代中期SNAM改进 了设计,设备改为平面布置,而且也不直接向气提塔加入气氨,即所谓的 自气提工艺或称为第二代氨气提法工艺。
由于添加的水量不同,又可分为两类:
添加水量较多,分子比近于1,称为碳酸铵盐水溶液全循环法。 添加水量较少,基本上以甲铵溶液返回系统,称为氨基甲酸铵溶
液全循环法。
难度—气液分离的温度不可太高,以免使生成的尿素分解;液体吸收 气体的温度不可太低,以防出现固体结晶;返回系统的水量必须控制 在最少,否则由于有水进入反应器,一次通过的尿素合成率太低,造 成大量溶液循环。
尿素利用条件和原理

尿素利用条件和原理尿素(化学式:CO(NH2)2),是一种由碳、氮、氧和氢组成的有机化合物,拥有多种用途。
作为一种重要的化工原料,尿素的利用条件和原理主要取决于其生产和应用方面。
尿素的制备条件主要包括原料和工艺条件两个方面。
从工艺条件的角度来看,尿素的制备需要一定的温度和压力条件。
一般来说,尿素的生产需要高温高压的条件,一般在高温(约180-210°C)和高压(约150-200 bar)下进行。
尿素的合成原理主要是:1.反应方程式:2NH3+CO2→CO(NH2)2+H2O尿素的合成反应为氨和二氧化碳的催化气相反应,产生尿素和水。
反应通常在一个反应器中进行,反应器内用催化剂催化,常用的催化剂有铁、钴、镍等。
反应速度较慢,需要一定时间来完成反应。
2.反应机理:尿素合成反应的机理复杂,主要有三个步骤:氨酉(NH3)的催化酸化、尿酸和尿素的生成以及尿素和尿酸的降解。
其中,催化酸化这个步骤是尿素合成反应的速控步骤,通常利用催化剂促进反应速率。
尿素的主要应用条件和原理如下:1.农业应用:尿素是一种重要的氮肥,可以提供植物所需的氮元素。
尿素通常以颗粒或结晶形式出现,并通过喷施、撒施等方式施用于土壤中。
在农业应用中,需考虑土壤的养分含量、水分状况以及植物对氮肥的需求,合理施用尿素以保证植物的生长发育。
2.工业应用:尿素在工业中广泛应用于制造塑料、树脂、粘合剂等材料。
尿素可以与甲醛反应形成脲醛树脂,该树脂具有优良的物理和化学性质,可用于制造胶合板、木材粘合剂等。
此外,尿素还可以用于涂料、染料、医药等行业。
总结起来,尿素的利用条件主要包括原料和工艺两个方面,其中氨气、二氧化碳和纯净水是尿素制备的重要原料。
尿素的制备需要高温高压的条件,较为复杂。
尿素的原理是氨和二氧化碳的催化气相反应。
尿素的应用条件主要根据具体领域的需求,例如在农业中需要考虑土壤养分、水分状况和植物需求的情况,而在工业中则需根据具体产品制造的需求。
尿素制造工艺

尿素制造工艺
嘿,咱今天就来讲讲尿素制造工艺,这可是个很有意思的事儿呢!
你想想看,尿素就像是农业的小魔法,能让庄稼长得壮壮的。
那它是怎么来的呢?这就得从那些复杂又神奇的工艺说起啦。
先来说说原料吧,就好像做菜得有食材一样,尿素制造也得有它的“食材”呀,一般就是氨气和二氧化碳。
这俩家伙凑到一块儿,就能开始一场奇妙的变化之旅啦。
然后呢,它们会进入一个叫做合成塔的地方,这合成塔就像是一个魔法盒子,氨气和二氧化碳在里面经过一系列反应,慢慢就变成尿素啦。
这过程是不是很神奇?就好像变魔术一样!
接着呀,生成的尿素溶液可不能就这么直接用哦,还得经过一些处理呢。
就像你做好了一道菜,还得装盘摆个漂亮的造型一样。
这些处理步骤就是为了让尿素更纯、更好用。
你说这尿素制造工艺像不像一场大冒险?各种设备和反应就像是冒险路上的关卡和挑战,只有顺利通过了,才能得到我们想要的尿素。
咱再想想啊,如果没有这个尿素制造工艺,那农民伯伯们种庄稼可就没那么容易啦。
没有足够的肥料,庄稼怎么能长得好呢?所以说呀,这尿素制造工艺可真是太重要啦!
而且哦,随着科技的不断进步,尿素制造工艺也在不断改进呢。
就像我们的手机一样,一代比一代厉害。
以后说不定会有更高效、更环保的方法来制造尿素,那可就太棒啦!
你看,这就是尿素制造工艺,一个看似普通却又无比重要的存在。
它就像一个默默奉献的小英雄,为我们的农业发展贡献着自己的力量。
咱可得好好珍惜这个工艺呀,让它为我们创造更多的价值!怎么样,是不是对尿素制造工艺有了更深的了解呢?。
产万吨尿素工艺设计方案
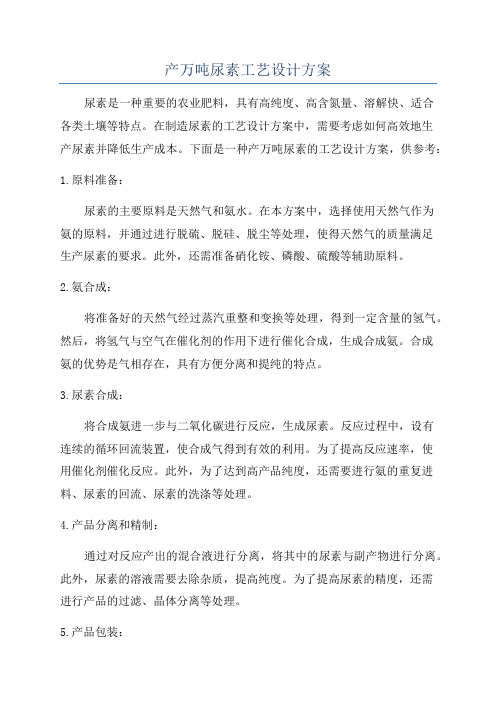
产万吨尿素工艺设计方案尿素是一种重要的农业肥料,具有高纯度、高含氮量、溶解快、适合各类土壤等特点。
在制造尿素的工艺设计方案中,需要考虑如何高效地生产尿素并降低生产成本。
下面是一种产万吨尿素的工艺设计方案,供参考:1.原料准备:尿素的主要原料是天然气和氨水。
在本方案中,选择使用天然气作为氨的原料,并通过进行脱硫、脱硅、脱尘等处理,使得天然气的质量满足生产尿素的要求。
此外,还需准备硝化铵、磷酸、硫酸等辅助原料。
2.氨合成:将准备好的天然气经过蒸汽重整和变换等处理,得到一定含量的氢气。
然后,将氢气与空气在催化剂的作用下进行催化合成,生成合成氨。
合成氨的优势是气相存在,具有方便分离和提纯的特点。
3.尿素合成:将合成氨进一步与二氧化碳进行反应,生成尿素。
反应过程中,设有连续的循环回流装置,使合成气得到有效的利用。
为了提高反应速率,使用催化剂催化反应。
此外,为了达到高产品纯度,还需要进行氨的重复进料、尿素的回流、尿素的洗涤等处理。
4.产品分离和精制:通过对反应产出的混合液进行分离,将其中的尿素与副产物进行分离。
此外,尿素的溶液需要去除杂质,提高纯度。
为了提高尿素的精度,还需进行产品的过滤、晶体分离等处理。
5.产品包装:将去除杂质和经过精制的尿素进行包装,方便运输和储存。
包装过程中需要控制产品的湿度和粒度,确保产品的质量符合标准。
总结:以上是一种产万吨尿素的工艺设计方案,可以实现高效的尿素生产。
在实际操作中,还需考虑生产设备的选型、工艺参数的优化、废水处理和资源利用等问题。
此外,需要优化工艺流程,提高产品的质量和产量,确保安全、环保和经济可行。
尿素工艺流程 PPT课件

尿素生产流程有多种,最早实现工业化的方法是不循环法 和部分循环法,后来被水溶液全循环法代替,又出现各种 气提法流程。虽然方法、其实现的工艺流程和工艺条件不 同,但生产原理是相同的。主要介绍尿素生产的工艺流程、 主要设备和操作条件。
一、不循环法和部分循环法
尿素生产工业化早期实现的是不循环和部分循环流程,两 种方法在生产尿素时必定伴有大量副产物生成,此种流 程已不再采用。
5
(二)溶液全循环改良C法
1.工艺流程(见296-297页图)
日本三井东压/东洋工程全循环改良C法,是传统水溶液全 循环法的改进,生产低缩二脲含量尿素产品,也生产常规 尿素产品。
2.主要设备(尿素合成塔)
尿素合成塔操作条件:压力23-25MPa、温度190-200℃, 氨碳比4,水碳比0.37,转化率约72%,外壳应用保温材料 改良C法的尿素合成塔采用高径比为18的空塔,用钛作衬 里,耐高温腐蚀。
❖ 2.P:P降低使甲铵分解,对过量氨蒸出及吸收有利,气 ❖ 提效率提高,但为节省能耗,常选用P气提=P合成。 ❖ 3.液气比:即进入气提塔尿素液与CO2的重量比。它由
合成反应本身的加料组成确定,不可任意改变。生产中为保 证每根管子内的正常流量,防止管子造成严重腐蚀,一 般 气提塔内液气比控制在4左右。 ❖ 4.停留时间:生产上以接近1min为宜。
二、水溶液全循环法
❖(一)传统水溶液全循环法
❖(二)溶液全循环改良C法
1
(一)传统水溶液全循环法
1.工艺流程(见294页图)
2.主要设备(尿素合成塔)
合成塔工艺操作条件:压力20-22MPa、温度190-200℃,氨碳 比4-4.5,水碳比0.6-0.7,转化率约62-64%,应符合高压 容器要求,外壳应用保温材料 大中型尿素工厂采用衬里式合成塔 合成塔外筒为多层卷焊受压容器,内部衬有一层耐腐蚀的 不锈钢板,隔离尿素甲铵腐蚀介质,外壳保温,防止热量 外散。 优点:容积利用率高,耐腐蚀材料用量少,操作方便。 最早采用空塔,不设置内件,塔高径比较大。后采用高径 比小的塔,常设置混合器或筛板等内件,减少返混的影响。
尿素生产工艺
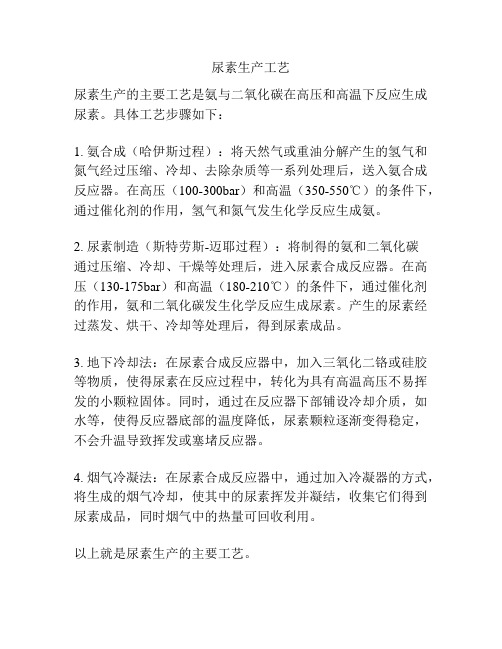
尿素生产工艺
尿素生产的主要工艺是氨与二氧化碳在高压和高温下反应生成尿素。
具体工艺步骤如下:
1. 氨合成(哈伊斯过程):将天然气或重油分解产生的氢气和氮气经过压缩、冷却、去除杂质等一系列处理后,送入氨合成反应器。
在高压(100-300bar)和高温(350-550℃)的条件下,通过催化剂的作用,氢气和氮气发生化学反应生成氨。
2. 尿素制造(斯特劳斯-迈耶过程):将制得的氨和二氧化碳
通过压缩、冷却、干燥等处理后,进入尿素合成反应器。
在高压(130-175bar)和高温(180-210℃)的条件下,通过催化剂的作用,氨和二氧化碳发生化学反应生成尿素。
产生的尿素经过蒸发、烘干、冷却等处理后,得到尿素成品。
3. 地下冷却法:在尿素合成反应器中,加入三氧化二铬或硅胶等物质,使得尿素在反应过程中,转化为具有高温高压不易挥发的小颗粒固体。
同时,通过在反应器下部铺设冷却介质,如水等,使得反应器底部的温度降低,尿素颗粒逐渐变得稳定,不会升温导致挥发或塞堵反应器。
4. 烟气冷凝法:在尿素合成反应器中,通过加入冷凝器的方式,将生成的烟气冷却,使其中的尿素挥发并凝结,收集它们得到尿素成品,同时烟气中的热量可回收利用。
以上就是尿素生产的主要工艺。
尿素合成塔主要零部件的制造工艺流程设计_图文(精)
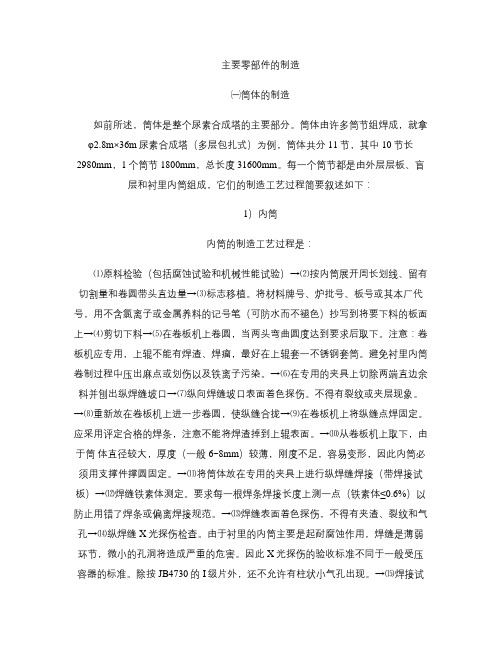
主要零部件的制造㈠筒体的制造如前所述,筒体是整个尿素合成塔的主要部分。
筒体由许多筒节组焊成,就拿φ2.8m×36m尿素合成塔(多层包扎式)为例,筒体共分11节,其中10节长2980mm,1个筒节1800mm,总长度31600mm。
每一个筒节都是由外层层板、盲层和衬里内筒组成,它们的制造工艺过程简要叙述如下:1)内筒内筒的制造工艺过程是:⑴原料检验(包括腐蚀试验和机械性能试验)→⑵按内筒展开周长划线、留有切割量和卷圆带头直边量→⑶标志移植。
将材料牌号、炉批号、板号或其本厂代号,用不含氯离子或金属养料的记号笔(可防水而不褪色)抄写到将要下料的板面上→⑷剪切下料→⑸在卷板机上卷圆,当两头弯曲圆度达到要求后取下。
注意:卷板机应专用,上辊不能有焊渣、焊瘤,最好在上辊套一不锈钢套筒。
避免衬里内筒卷制过程中压出麻点或划伤以及铁离子污染。
→⑹在专用的夹具上切除两端直边余料并刨出纵焊缝坡口→⑺纵向焊缝坡口表面着色探伤。
不得有裂纹或夹层现象。
→⑻重新放在卷板机上进一步卷圆,使纵缝合拢→⑼在卷板机上将纵缝点焊固定。
应采用评定合格的焊条,注意不能将焊渣掉到上辊表面。
→⑽从卷板机上取下,由于筒体直径较大,厚度(一般6~8mm)较薄,刚度不足,容易变形,因此内筒必须用支撑件撑圆固定。
→⑾将筒体放在专用的夹具上进行纵焊缝焊接(带焊接试板)→⑿焊缝铁素体测定。
要求每一根焊条焊接长度上测一点(铁素体≤0.6%)以防止用错了焊条或偏离焊接规范。
→⒀焊缝表面着色探伤,不得有夹渣、裂纹和气孔→⒁纵焊缝X光探伤检查。
由于衬里的内筒主要是起耐腐蚀作用,焊缝是薄弱环节,微小的孔洞将造成严重的危害。
因此X光探伤的验收标准不同于一般受压容器的标准。
除按JB4730的I级片外,还不允许有柱状小气孔出现。
→⒂焊接试板的晶间腐蚀倾向试验和选择性腐蚀检查及金相检查。
其方法按HG/T3172和HG/T3173、HG/T3174验收标准按GB9842或工程标准的规定。
尿素生产技术

改良C法(日本)
改良C法,是传统水溶液全循环法的改进,生产低缩二 脲含量尿素产品,也生产常规尿素产品。
改良C法--操作条件
合成塔: 温度:190-200℃,压力:23-25MPa,氨碳比:4,水碳比: 0.37,转化率:72%。 合成塔为高径比18的空塔,用钛衬里,耐高温腐蚀。
分解塔:
高压分解(1.7-1.9MPa,165℃:其热量由塔外的热虹吸式
尿素合成塔内, NH 3/CO2的摩尔比和H2O/ CO2的摩尔比控制在一定的范围内进行反应。
合成后的气液混合物进入预分离器,一段分解, 进行气液分离,将分离气相后的尿液送入二段 分解,进一步将混合物中的气相除去。
净化后的尿液依次进入闪蒸器、一段蒸发、二 段蒸发浓缩,最后得到尿素熔融物,用泵输送 到尿素造粒塔喷洒器,经在空气中沉降冷却固 化成粒状尿素,并通过尿素塔底刮料机用运输 皮带送往储存包装车间。
流程:合成塔出口液进预分 离器自然减压进行气液预分 离,它的液相进一段分解塔7。 气体送入一段蒸发器19下部。
主要设备--预分离器6
一段分解塔出口气体也引入预分离器。 预分离器有改造为预精馏塔的,内装填料,
气液逆流接触,可降低出口气体的温度和水 分。 气体送入一段蒸发器19下部,充分利用了预 分离器出口气体的冷凝热,部分气体冷凝并 放出热量,供尿液蒸发用。
第三章 尿素生产技术
(1)不循环法;
(2)半循环法(部分循环法、高效半循环) ;
(3)全循环法
热气全循环法
全循环法
矿物油全循环法 尾气分离全循环法
水溶液全循环法 发展:改良C、D法,二氧化碳汽提法,氨汽提法及联尿法等。
水溶液全循环法的流程图
惰气洗涤
尿素工艺流程简述
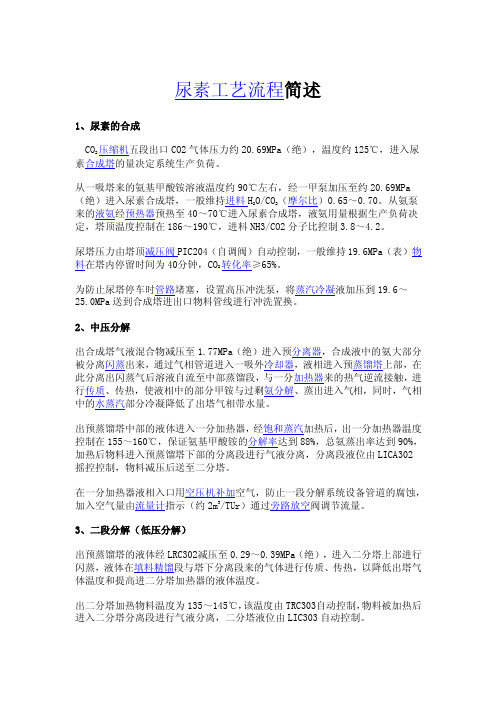
尿素工艺流程简述1、尿素的合成CO2压缩机五段出口CO2气体压力约20.69MPa(绝),温度约125℃,进入尿素合成塔的量决定系统生产负荷。
从一吸塔来的氨基甲酸铵溶液温度约90℃左右,经一甲泵加压至约20.69MPa(绝)进入尿素合成塔,一般维持进料H2O/CO2(摩尔比)0.65~0.70。
从氨泵来的液氨经预热器预热至40~70℃进入尿素合成塔,液氨用量根据生产负荷决定,塔顶温度控制在186~190℃,进料NH3/CO2分子比控制3.8~4.2。
尿塔压力由塔顶减压阀PIC204(自调阀)自动控制,一般维持19.6MPa(表)物料在塔内停留时间为40分钟,CO2转化率≥65%。
为防止尿塔停车时管路堵塞,设置高压冲洗泵,将蒸汽冷凝液加压到19.6~25.0MPa送到合成塔进出口物料管线进行冲洗置换。
2、中压分解出合成塔气液混合物减压至1.77MPa(绝)进入预分离器,合成液中的氨大部分被分离闪蒸出来,通过气相管道进入一吸外冷却器,液相进入预蒸馏塔上部,在此分离出闪蒸气后溶液自流至中部蒸馏段,与一分加热器来的热气逆流接触,进行传质、传热,使液相中的部分甲铵与过剩氨分解、蒸出进入气相,同时,气相中的水蒸汽部分冷凝降低了出塔气相带水量。
出预蒸馏塔中部的液体进入一分加热器,经饱和蒸汽加热后,出一分加热器温度控制在155~160℃,保证氨基甲酸铵的分解率达到88%,总氨蒸出率达到90%,加热后物料进入预蒸馏塔下部的分离段进行气液分离,分离段液位由LICA302摇控控制,物料减压后送至二分塔。
在一分加热器液相入口用空压机补加空气,防止一段分解系统设备管道的腐蚀,加入空气量由流量计指示(约2m3/TUr)通过旁路放空阀调节流量。
3、二段分解(低压分解)出预蒸馏塔的液体经LR C302减压至0.29~0.39MPa(绝),进入二分塔上部进行闪蒸,液体在填料精馏段与塔下分离段来的气体进行传质、传热,以降低出塔气体温度和提高进二分塔加热器的液体温度。
尿素合成、制造工艺
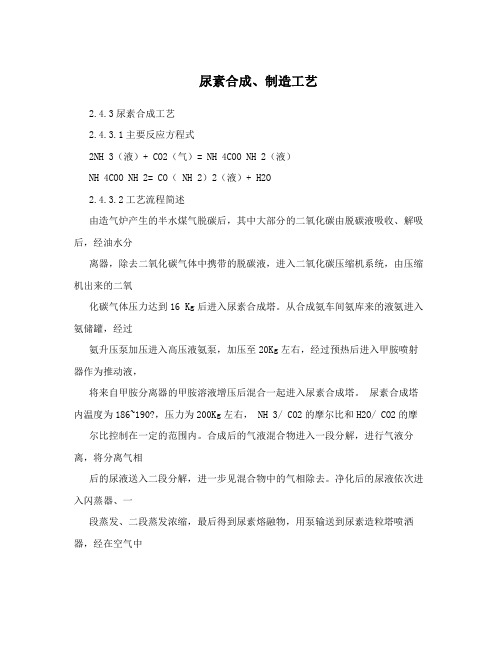
尿素合成、制造工艺2.4.3尿素合成工艺2.4.3.1主要反应方程式2NH 3(液)+ CO2(气)= NH 4COO NH 2(液)NH 4COO NH 2= CO( NH 2)2(液)+ H2O2.4.3.2工艺流程简述由造气炉产生的半水煤气脱碳后,其中大部分的二氧化碳由脱碳液吸收、解吸后,经油水分离器,除去二氧化碳气体中携带的脱碳液,进入二氧化碳压缩机系统,由压缩机出来的二氧化碳气体压力达到16 Kg后进入尿素合成塔。
从合成氨车间氨库来的液氨进入氨储罐,经过氨升压泵加压进入高压液氨泵,加压至20Kg左右,经过预热后进入甲胺喷射器作为推动液,将来自甲胺分离器的甲胺溶液增压后混合一起进入尿素合成塔。
尿素合成塔内温度为186~190?,压力为200Kg左右, NH 3/ CO2的摩尔比和H2O/ CO2的摩尔比控制在一定的范围内。
合成后的气液混合物进入一段分解,进行气液分离,将分离气相后的尿液送入二段分解,进一步见混合物中的气相除去。
净化后的尿液依次进入闪蒸器、一段蒸发、二段蒸发浓缩,最后得到尿素熔融物,用泵输送到尿素造粒塔喷洒器,经在空气中沉降冷却固化成粒状尿素,并通过尿素塔底刮料机用运输皮带送往储存包装车间。
从一段分解、二段分解出来的气相含有未反应的氨和二氧化碳,分别进入一段吸收和二段吸收,氨和二氧化碳被后面闪蒸、一段蒸发、二段蒸发工段冷凝下来的冷凝水吸收混合形成水溶液,用泵送入尿素合成塔;一段吸收后剩余的气体进入惰洗器稀释后,与二段吸收的残余气体混合进入尾气吸收塔,与一段蒸发、二段蒸发工段气相冷凝除去水后残余的气体混合后放空。
尿素制造工艺尿素, 工艺, 制造-(1)全循环法将氨与二氧化碳作用生成氨基甲酸铵,然后脱水生成尿素。
未反应的氨和二氧化碳用水吸收生成甲铵或碳酸铵水溶液返回合成系统循环利用。
合成压力约19.61 MPa,温度185~190 oc,约62%co,转化为尿素。
反应液经两段分解及真空蒸发浓缩至造粒。
尿素生产工艺(一)

尿素生产工艺(一)前言在化学和工业领域,尿素是一种重要的化学物质。
尿素从20世纪初就已被广泛应用于肥料、塑料、溶剂和各种化学工艺中。
本文将介绍尿素的生产工艺。
尿素的基础知识尿素是一种有机化合物,化学式为CO(NH2)2。
它的特点是白色晶体状或结晶体。
尿素是一种氮肥,可以对农作物提供稳定的氮源,帮助植物生长。
尿素还是一种重要的化学原料,可以制造塑料、溶剂等各种产品。
尿素的生产工艺尿素的生产工艺被称为“尿素合成”,它是通过高压和高温下的化学反应完成的。
下面是尿素的生产工艺的流程:1.氨气制备首先,需要制备氨气。
氨气可以通过以下两种基本工艺制备:•湿法生产氨气•干法生产氨气2.氨与二氧化碳的反应氨气和二氧化碳在高温高压下反应,产生尿素和水:CO2 + 2NH3 → CO(NH2)2 + H2O3.尿素的结晶产生的尿素溶液经过结晶过程,形成尿素结晶体。
尿素生产工艺的优点尿素的生产工艺具有以下优点:1.高效性尿素的生产工艺是一种高效的化学反应过程。
可以产生大量的尿素。
2.低成本尿素生产工艺使用的原料是氨和二氧化碳,这些原料很容易得到。
因此,这种生产工艺的成本相对较低。
3.环保尿素合成过程中的废品和非官能化物质量非常小,所以这个过程非常环保。
结论尿素生产工艺已被广泛应用于农业和工业领域。
它可以为农作物提供肥料,同时还可以制造塑料、溶剂等各种产品。
这种生产工艺的优点是效率高,成本低,而且非常环保。
尿素生产工艺的局限尽管尿素生产工艺具有许多优势,但它仍然存在着一些局限性:1.能耗高尿素生产的主要能耗来自制氨和反应器,使得尿素的生产成本较高。
2.环境污染由于尿素生产工艺需要高温高压,废水中含有氨、硝酸等物质。
如果不加处理就会对环境造成污染。
3.工艺改进难度大由于尿素生产工艺的反应条件十分苛刻,任何一处的变化都可能影响到反应效果,因此改进这种生产工艺的不同方面是非常困难的。
结尾尿素生产工艺是化工领域中的一个重要的生产过程。
尿素工艺流程

尿素工艺流程尿素是一种重要的氮肥和工业原料,在生产过程中通常使用尿素工艺流程进行制造。
下面是一篇关于尿素工艺流程的700字文章。
尿素工艺流程是将天然气和空气作为原料,经过多个步骤反应合成尿素的过程。
一般来说,尿素工艺流程包括合成氨、尿素合成、尿素结晶和尿素精制等部分。
尿素的工艺流程起始于合成氨。
合成氨是尿素合成的重要中间体,可以通过多种方法制备,其中最常用的是哈柏过程。
哈柏过程使用天然气和空气为原料,在高温和高压下经过氧化、还原和吸收等反应,生成含有高浓度氨的合成氨。
合成氨生成后,需要进一步进行尿素合成。
尿素合成是一种反应性强且环境条件苛刻的反应。
在尿素合成过程中,合成氨与二氧化碳发生反应,生成尿素和水。
这一反应需要在高温和高压下进行,在合适的催化剂作用下才能达到最佳效果。
尿素合成完成后,经过进一步处理可以得到尿素溶液。
尿素溶液需要经过结晶和干燥等步骤,最终得到固体尿素产品。
尿素结晶是将尿素溶液经过蒸发浓缩,使其过饱和,然后通过降温结晶的过程得到尿素晶体。
尿素晶体经过离心和干燥等步骤,得到尿素颗粒或颗粒状产品。
尿素精制是尿素工艺流程中的最后一步。
尿素精制主要是通过蒸馏和干燥等操作进一步提纯尿素,并达到所需的产品质量指标。
蒸馏是将尿素加热至沸点,使其汽化,然后通过冷凝器冷却,收集纯净的尿素液体。
尿素液体再经过干燥处理,得到干燥的尿素产品。
总体来说,尿素工艺流程是一个复杂而精细的过程,需要高温、高压以及适当的催化剂和反应条件。
通过合成氨、尿素合成、尿素结晶和尿素精制等步骤,最终能够得到高纯度的尿素产品。
尿素作为一种重要的肥料和工业原料,在农业和化工领域有着广泛的应用,尿素工艺流程的改进和优化也对提高生产效率和产品质量有着重要意义。
车用尿素的制作过程

车用尿素的制作过程
车用尿素的制作过程主要包括尿素合成和尿素精制两个步骤。
尿素合成的步骤如下:
1. 合成氨的制备:通过空气氧化铵或者在选择性催化剂的催化下,用天然气、煤气、石油气等碳氢化合物作为原料,利用高温高压合成氨法合成氨。
2. 尿素合成反应:将制备好的氨气与二氧化碳在催化剂的作用下进行反应,生成尿素。
反应过程中需控制温度、压力和催化剂的选择,以提高反应的效率和选择性。
尿素合成反应产生的尿素溶液含有杂质,需要进行精制处理。
尿素精制的步骤如下:
1. 酸处理:将尿素溶液加入适量的硫酸、磷酸等强酸中进行反应,使尿素转化为尿素酸盐。
2. 脱色:将酸处理后的尿素酸盐进行脱色处理,常用活性炭吸附法或者氧化脱色法。
3. 水洗:脱色后的尿素酸盐用清水进行洗涤,去除残留的酸和杂质。
4. 结晶:将水洗后的尿素酸盐溶液进行蒸发浓缩,然后降温结晶,得到纯净的尿素晶体。
5. 干燥:将尿素晶体进行干燥处理,得到车用尿素。
制造尿素的工艺有众多,具体的流程和条件可能存在差异。
上述只是一种常见的
尿素制备方法的主要步骤。
川化尿素生产工艺

川化尿素生产工艺
川化尿素生产工艺是一种制造尿素的化学工艺。
具体工艺流程如下:
1. 原料准备:将天然气、空气和水经过预处理分别得到氢气、氮气和蒸汽,为后续的反应提供原料。
2. 氨合成:将氢气和氮气通过合成器反应生成氨气。
这个反应是一个放热反应,通常在高压和高温下进行,以提高反应速率和氨气的产量。
3. 尿素合成:将氨气通过尿素合成装置与二氧化碳反应生成尿素。
尿素合成是一个放热反应,需要在压力和温度适中的条件下进行。
4. 结晶和干燥:将反应生成的尿素溶液冷却并结晶,得到尿素结晶体。
然后将尿素结晶体进行干燥,去除其中的水分,得到干燥的尿素。
5. 精制和包装:将干燥的尿素进行精制处理,去除其中的杂质和不纯物质。
然后将精制的尿素进行包装,以便储存和运输。
川化尿素生产工艺的优点包括能够充分利用天然气资源、尿素产量高、产品纯度高等。
然而,川化尿素生产工艺也存在一些挑战,如对高温、高压和强酸碱环境的需求较高、能耗较大等。
为了改进川化尿素生产工艺,可以采取一些措施,如优化反应
条件,提高反应速率和产量;改进装置结构,提高尿素的纯度和产品质量;优化能源利用,减少能源消耗和环境污染等。
另外,还可以引入先进的控制技术和自动化设备,提高生产效率和操作安全性。
总之,川化尿素生产工艺是一种成熟而高效的尿素生产工艺,通过不断优化和改进,可以进一步提高生产效率和产品质量,降低成本和环境污染,促进尿素工业的可持续发展。
尿素工艺流程简述(副本)

尿素工艺流程简述1、尿素的合成CO2压缩机五段出口CO2气体压力约20.69MPa(绝),温度约125℃,进入尿素合成塔的量决定系统生产负荷。
从一吸塔来的氨基甲酸铵溶液温度约90℃左右,经一甲泵加压至约20.69MPa(绝)进入尿素合成塔,一般维持进料H2O/CO2(摩尔比)0.65~0.70。
从氨泵来的液氨经预热器预热至40~70℃进入尿素合成塔,液氨用量根据生产负荷决定,塔顶温度控制在186~190℃,进料NH3/CO2分子比控制3.8~4.2。
尿塔压力由塔顶减压阀PIC204(自调阀)自动控制,一般维持19.6MPa(表)物料在塔内停留时间为40分钟,CO2转化率≥65%。
为防止尿塔停车时管路堵塞,设置高压冲洗泵,将蒸汽冷凝液加压到19.6~25.0MPa送到合成塔进出口物料管线进行冲洗置换。
2、中压分解出合成塔气液混合物减压至1.77MPa(绝)进入预分离器,合成液中的氨大部分被分离闪蒸出来,通过气相管道进入一吸外冷却器,液相进入预蒸馏塔上部,在此分离出闪蒸气后溶液自流至中部蒸馏段,与一分加热器来的热气逆流接触,进行传质、传热,使液相中的部分甲铵与过剩氨分解、蒸出进入气相,同时,气相中的水蒸汽部分冷凝降低了出塔气相带水量。
出预蒸馏塔中部的液体进入一分加热器,经饱和蒸汽加热后,出一分加热器温度控制在155~160℃,保证氨基甲酸铵的分解率达到88%,总氨蒸出率达到90%,加热后物料进入预蒸馏塔下部的分离段进行气液分离,分离段液位由LICA302摇控控制,物料减压后送至二分塔。
在一分加热器液相入口用空压机补加空气,防止一段分解系统设备管道的腐蚀,加入空气量由流量计指示(约2m3/TUr)通过旁路放空阀调节流量。
3、二段分解(低压分解)出预蒸馏塔的液体经LRC302减压至0.29~0.39MPa(绝),进入二分塔上部进行闪蒸,液体在填料精馏段与塔下分离段来的气体进行传质、传热,以降低出塔气体温度和提高进二分塔加热器的液体温度。
尿素工艺流程和结论

化肥厂尿素生产工艺流程(co2汽提法)•第一步由氨与二氧化碳生成中间产物甲铵,其反应式为:2NH3(液)+CO2(气) NH2COONH4(液)+ 119.2KJ/molA•第二步由甲铵脱水生成尿素,其反应式为(合成尿素过程中的控制反应):NH2COONH4(液) CO(NH2)2(液)+H2O(液)- 15.5KJ/mol B•总的反应方程式:•2NH3(液)+CO2(气) CO(NH2)2(液)+H2O(液)+103.7KJ/mol•从气提塔201C底部出来的液体经减压进入精馏塔顶部,均匀地喷洒在精馏塔的填料层上,然后自上而下和上升的135℃分解气逆流接触,温度上升至120℃左右,尿液从301E底部送到底部和中部、顶部循环加热器,在此分别用高调水和0.6MPa蒸汽将其温度提高到约140℃,使甲铵再次发生分解。
•用精馏塔出口调节阀TIC301来调节进入顶部循环加热器的蒸汽压力,在循环分离段中气液相发生分离,气体通过精馏塔填料段进行热质交换后,从精馏塔301E塔顶出口管进入低甲冷,冷凝吸收。
•离开精馏塔分离段的尿液位液位调节阀LV301送至闪蒸槽,闪蒸槽301F真空度由HV701控制,闪蒸使尿液中部分氨、CO2、H2O挥发,尿液由135℃降至90~95℃,浓度增加到约72~74%,流入尿液小槽,闪蒸气相去闪蒸冷凝器冷凝。
•精馏气回流泵来回流液及工艺液在低甲冷进行浸没式冷凝吸收,为了移走冷凝热,低甲冷用低调水进行冷却,现低调水是由化水送来的脱盐水与系统换热后热脱盐水混合后温度控制在50~55℃,一部分热脱盐水送至电厂,出301C的汽液混合物进入低压液位槽进行气液分离,气相及回流冷气相同时进入鼓泡塔,经吸收塔给料泵打来的解吸液吸收后再进入常压吸收塔,液相返回氨水槽,气体至放空总管,循环气相管前设有吹扫蒸汽,以防此管线结晶。
循环系统甲铵液经甲铵泵加压至15MPa送至高压洗涤器作吸收剂。
.精馏塔的精馏过程•高压圈合成的合成液,经气提塔气提后,由气提塔出料调节阀压力由14.6MPa减压至0.25~0.3MPa,使气提液中的部分甲铵分解成为氨和二氧化碳气体。
尿素的合成工艺

第四步尿素溶液加工,实际上是尿素溶液浓缩 结晶造粒生产尿素颗粒成品或液态尿素的过程。 造粒塔排放的粉尘和NH3会对大气环境造成污染, 但对水环境不会有很大的影响。
尿素合成塔结构和流程
尿素合成塔是氨和 二氧化碳反应生成尿素 的场所,是整个尿素装 置的核心设备。尿素合 成塔的结构是圆柱形的 塔体,内设若干块阻止 物料返混的塔板。可以 看成是由若干个串联的 、混合的小室组成。虽 每个小室接近理想混合 型,但就整个塔来说, 其流动状况却接近理想 置换型。
铵处于在高温情况下容易分解为氨,二 氧化碳,因而使尿素的转化率下降,所 以尿素在合成过程中操作压力一般应大 于其它的平衡压力。平衡压力值是不固 定的,它随着物料组分不同,NH3/CO2、 H2O/CO2及温度不同,平衡压力也不同。
(3)氨碳比
用过量氨的过量率及氨碳比(NH3/CO2) 两种形式表示。根据平衡移动原理可知,增加反应物 NH3的浓度,反应有利于向生成物方向进行,必然能够 提高二氧化碳的转化率。过量氨的优点: 过量氨的优点: a、 增加反应物的浓度,必然增加尿素的转化率。 b、 可以与反应生成的水作用,降低水的活度,使平衡向 生成尿素和方向进行。 c、 过量氨可以控制合成塔自然和维持最合适的反应温度 d、 系统内过量氨还可抑制其他副反应,并能降低腐蚀作 用。
(1)水溶液全循环法
水溶液全循环法是将未反应的氨和二氧化碳用 水吸收生成甲铵或碳酸铵水溶液返回合成系统的 生产方法。 未转化物需两段分解,三段吸收。流程较长 且分解压力不高,分解气的冷凝热除小部分被利 用外,其余须用冷却水移走,能耗较高。此外, 循环甲铵液量大,甲铵泵易腐蚀,且发生结晶堵 塞时,操作维修麻烦。
(1)温度 是吸热较弱,速度较慢。随
着温度上升,甲铵脱水反应平衡常数增 大;甲铵脱水反应速度 也加快。因此, 提高温度对尿素的反应有利。但是必须 指出,温度不能随意的升高,在测定温 度与转化率关系中表明,在某一温度下 转化率有极大值。当超过此温度后平衡 转化率反而下降。
- 1、下载文档前请自行甄别文档内容的完整性,平台不提供额外的编辑、内容补充、找答案等附加服务。
- 2、"仅部分预览"的文档,不可在线预览部分如存在完整性等问题,可反馈申请退款(可完整预览的文档不适用该条件!)。
- 3、如文档侵犯您的权益,请联系客服反馈,我们会尽快为您处理(人工客服工作时间:9:00-18:30)。
2.4.3尿素合成工艺2.4.3.1主要反应方程式2NH 3(液)+ CO2(气)= NH 4COO NH 2(液)NH 4COO NH 2= CO( NH 2)2(液)+ H2O2.4.3.2工艺流程简述由造气炉产生的半水煤气脱碳后,其中大部分的二氧化碳由脱碳液吸收、解吸后,经油水分离器,除去二氧化碳气体中携带的脱碳液,进气体混合进入尾气吸收塔,与一段蒸发、二段蒸发工段气相冷凝除去水后残余的气体混合后放空。
尿素制造工艺尿素, 工艺, 制造-(1)全循环法将氨与二氧化碳作用生成氨基甲酸铵,然后脱水生成尿素。
未反应的氨和二氧化碳用水吸收生成甲铵或碳酸铵水溶液返回合成系统循环利用。
合成压力约19.61 MPa,温度185~190 oc,约62%co,转化为尿素。
反应液经两段分解及真空蒸发浓缩至造粒。
其反应式如下:2NH3+COz—NHzCOONH。
NHzCOONH4——CO(NH2)2+H20(2)二氧化碳气提法合成压力13.73 MPa,温度180~185℃,转化率57~58%,用二氧化碳作为气提剂,使未转化的甲铵分解成二氧化碳及氨蒸出。
气提效率80~83%,气提塔出气在高压冷凝器内冷凝生成甲铵溶液回合成塔。
气提塔出液经进一步分解,蒸发,送造粒。
(3)氨气提法合成压力14.71 MPa,温度185~190℃,转化率60%左右。
未转化甲铵在气提塔中用氨气提而分解,出气提塔尿液经两段分解使残余甲铵进一步分解,游离氨馏出,以水溶液形式回收,过剩氨经冷凝成液氨返回系统。
4、等压双气提法合成压力17.65~19.61 MPa。
温度185~190。
C,氨/二氧化碳4~5,转化率70~75%。
出塔尿液依次经过两个串联的气提塔,分别以氨气、二氧化碳气提分解未转化的甲铵并蒸出部分过量氨。
由于循环法生产尿素存在动力消耗大,一次通过的尿素合成率低等诸多缺点,目前大多厂家采用汽提法生产尿素。
汽提法是水溶液全循环法的一项重要改进类型。
其实质是在与合成反应相等压力的条件下,利用一种气体通过反应物系(同时伴有加热),使未反应的氨和二氧化碳通过气提法合成。
二种气提法简易流程如下:二氧化碳气提法是将液氨和二氧化碳经高压泵和压缩机加压后送人高压合成系统生成尿素及甲铵,经低压分解,将未生成尿素的氨和二氧化碳分解出并加以回收,出低压的尿液进入蒸发器浓缩至99.8%,送造粒塔进行尿素颗粒造粒。
与全循环工艺的不同点在于用氨、二氧化碳或其他气体作为气提剂,在高压下(或与合成等压)促使甲铵分解。
具有代表性的二氧化碳气提工艺流程(见附图2[ 二氧化碳气提法尿素生产流程])是:从合成塔出来的溶液依靠重力流入气提塔,气提塔的结构为列管式的降膜塔,温度保持在180~190℃,溶液在列管内壁成膜从塔顶流向塔底;二氧化碳原料气从塔底进入,向上流动。
从气提塔出来的氨和二氧化碳流入高压甲铵冷凝器的顶部,同时还送入稀甲铵循环溶液和一部分由合成塔引出的溶液,保证有足够的溶剂,使甲铵不致析出。
从高压甲铵冷凝器底部流出的溶液再返回合成塔,形成循环。
从气提塔出来的溶液通过阀降压,然后进入低压分解系统(包括精馏塔、加热器和闪蒸罐)。
分离出来的氨和二氧化碳再凝缩成稀甲铵溶液,返回高压系统。
合成塔操作条件;压力约13.8MPa温度180~185℃、氨与二氧化碳的摩尔比约 2.8。
设备采用含钼的低碳不锈钢(气提塔用高镍铬不锈钢)。
气提法工艺还有多种类型,如意大利斯纳姆公司的氨气气提工艺、意大利蒙特爱迪生集团公司的氨与二氧化碳双气提工艺、日本东洋工程公司的节能型二氧化碳气提工艺、中国上海化工研究院等开发的变换气气提与合成氨脱除二氧化碳联合生产的工艺等。
气提技术的采用,使甲铵的分解与回收可以在较高压力下进行,相应地可以回收压力0.4~0.5MPa的蒸汽供本系统自用,使每吨尿素蒸汽耗量降至1t以下。
由于二氧化碳原料气中约含有低于 1%的氢气等可燃气体,它与为防腐蚀而加入的氧气混合在一起,在一定条件下有可能产生爆炸。
特别是作为尿素生产尾气排放时,正处于爆炸极限内(可加入蒸汽缩小其爆炸极限)。
为此,斯塔米卡本公司提出采用铂(钯)催化剂(见),在高温下脱除二氧化碳中的氢气,这样可保证尿素安全生产,但增加了投资费用及生产成本。
本项目尿素装置工艺选择为二氧化碳气提法。
2.1.3 工艺流程液氨经离心泵抽出并加压至 2.1MPa,部分送至中压吸收塔,余下的由泵压缩至21MPa,经来自低压分解塔的排放气预热后,进人喷射器,将来自甲胺分离器的甲胺液加压至合成压力后一同进人合成塔,与进行反应。
离开合成塔的产物进入降膜式氨气提塔,混合物经过降膜管时被加热,通过自气提作用,溶液中的含量降低。
由氨气提塔顶出来的气体与来自中压吸收塔并经高压甲按泵加压的流体一同进人高压甲按冷凝器。
在此除少量惰性组分外,全部混合物被冷凝并产生0.45MPa蒸汽。
经分离后液体流至甲按喷射器。
由甲胺分离器顶部出来的未冷凝气体 (含有少量的 )被送往中压分解塔处理。
含有少量的溶液离开氨气提塔底部去中压分解工序。
下面就做以分析详见图12.1.3.1 二氧化碳压缩和脱氢从合成氨装置来的气体,经过液滴分离器与来自空压站的工艺空气混合(空气量为二氧化碳体积4%),进入二氧化碳压缩机。
二氧化碳出压缩机三段进脱硫、脱氢反应器,脱氢反应器内装铂系[wiki]催化剂[/wiki],操作温度:入口≥150℃,出口≤200℃。
脱氢的目的是防止高压洗涤器可燃气体积聚发生爆炸。
在脱氢反应器中H2被氧化为H2O,脱氢后二氧化碳含氢及其它可燃气体小于50ppm,经脱硫、脱氢后,进入压缩机四段、五段压缩,最终压缩到14.7MPa(绝)进入汽提塔。
二氧化碳压缩机设有中间冷凝器和分离器,二氧化碳压缩机压缩气体设有三个回路,以适应尿素生产负荷的变化,多余的二氧化碳由放空管放空。
2.1.3.2 液氨升压液氨来自合成氨装置氨库,压力为2.3MPa(绝),温度为20℃,进入液氨过滤器,经过滤后进入高压氨泵的入口,液氨流量在一定的范围内可以自调,并设有副线以备开停车及倒泵用.主管上装有流量计.液氨经高压氨泵加压18.34MPa(绝),高压液氨泵是电动往复式柱塞泵,并带变频调速器,可在20—110%的范围内变化,在总控室有流量记录,从这个记录来判断进入系统的氨量,以维持正常生产时的原料N/C(摩尔比)为2.05:1。
高压液氨送到高压喷射器,作为喷射物料,将高压洗涤器来的甲铵带入高压冷凝器,高压液氨泵前后管线均设有安全阀,以保证装置设备安全。
2.1.3.3 合成和汽提生产原理:合成塔、气提塔、高压甲铵冷凝器和高压洗涤器四个设备组成高压圈,这是本工艺的核心部分,这四个设备的操作条件是统一考虑的,以期达到尿素的最大产率和最大限度的热量回收。
从高压冷凝器底部导出的液体甲铵和少量的未冷凝的氨和二氧化碳,分别用两条管线送入合成塔底,液相加气相物料N/C(摩尔比)为2.9—3.2,温度为165--172℃。
合成塔内设有11块塔板,形成类似几个串联的反应器,塔板的作用是防止物料在塔内返混。
物料从塔底至塔顶,设计停留时间1小时,二氧化碳转化率可达58%,相当于平衡转化率90%以上。
尿素合成反应液从塔内上升到正常液位,温度上升到180--185℃,经过溢流管从塔下出口排出,经过合成塔出液阀(HPV2201)汽提塔上部,再经塔内液体分配器均匀地分配到每根气提管中,沿管壁成液膜下降,分配器液位高低,起着自动调节各管内流量的作用,尿液在气提管均匀分配并在内壁形成液膜下降,内壁液膜是非常重要的,否则气提管将遭到腐蚀,由塔下部导入的二氧化碳气体,在管内与合成反应液逆流相遇,气提管外以蒸汽加热,合成反应液中过剩氨及未转化的甲铵将被气提气蒸出和分解,从塔顶排出,尿液及少量未分解的甲铵从塔底排出,气提塔出液温度控制在165--174℃之间。
塔底液位控制在40--80%左右,以防止二氧化碳气体随着液体流至低压分解工段造成低压设备超压。
从气提塔顶排出185--189℃的气体,与新鲜氨及高压洗涤器来的甲胺液在14.22MPa(绝)下混合一起进入高压冷凝器顶部。
高压冷凝器是一个管壳式换热器,物料走管内,管间走水用以副产蒸汽,根据副产蒸汽压力高低,可以调节氨和二氧化碳的冷凝程度。
但要保留一部分气体在合成塔内冷凝以便补偿在合成塔内甲铵转化为尿素所需热量,而达到自热平衡。
所以把控制副产蒸汽压力作为控制合成塔温度、压力的条件之一。
生成的甲胺,已冷凝的和未冷凝的氨和二氧化碳被导入到合成塔的底部,在这里,发生了甲胺转化为尿素、氨和二氧化碳反应生成氨基甲酸胺两个最主要的反应,转化和加热合成塔中的溶液所需的热量由附加的氨和二氧化碳的冷凝热来提供。
从合成塔顶排出的气体,温度约为180--185℃,进入高压洗涤器,在这里将气体中的氨和二氧化碳用加压后的低压吸收段的甲铵液冷凝吸收,然后经高压冷凝器再返回合成塔,不冷凝的惰性气体和一定数量的氨气,自高压洗涤器排出高压系统,进入低压吸收塔吸收后,直接放空。
甲铵吸收冷凝的热量被管间的调温冷却水带走,调温水从110℃升到125℃,并由高压洗涤器循环水冷却器调节到110--120℃,经高压洗涤器循环水泵循环使用。
从合成塔至高压洗涤器的管道,除设有安全阀外,还装有分析取样阀,通过对气相的分析,测得气相中氨、二氧化碳和惰性气体含量,从而可以判断合成塔的操作是否正常。
2.1.3.4 循环来自气提塔底部的尿素—甲铵溶液,经过气提塔的液位控制阀LPV—2202,减压到0.25—0.35MPa(绝),溶液中41.5%的二氧化碳和69%的氨得到闪蒸,并使溶液温度从175℃降到107℃,气液混和物喷到精馏塔顶,精馏塔上部为填料塔,起着气体精馏作用,下部为分离器,经过填料段下落的尿素—甲铵液流入循环加热器。
循环加热器用高压冷凝器副产的0.4MPa(绝)蒸汽加热。
温度升高到135--138℃,甲铵进一步分解,而后进入精馏塔下部的分离器分离。
液体经液位控制阀LIC2301流入闪蒸槽,气体上升到精馏塔填料段,精馏后的气体导出精馏塔与部分回流液、解吸液和液氨混合送到浸没式低压甲铵冷凝器。
在此,两相并流上升进行吸收,吸收时产生的热量,被冷凝器中冷却水带走,冷却水温从55℃升到65℃。
此冷却水经低压甲铵冷凝器循环水泵送低压甲铵冷凝器循环冷却器冷却后循环使用。
气液混合物从浸没式低压甲铵冷凝器上部溢流到低压甲铵冷凝器液位槽,液体从液位槽底导出,经高压甲铵泵升压到16.0MPa(绝),送入高压洗涤器顶部,高压甲铵泵是往复泵,采用变频调节甲铵流量。
液位槽分离出的气体,经低甲冷液位槽气相阀TPV2302阀进入常压吸收塔,经填料段,被来自低压吸收塔和常压吸收塔循环泵经循环冷却器冷却后的氨水喷淋吸收,未能被吸收的惰性气体,经吸收塔放空筒放空。