高分子材料成形工艺 橡胶制品成形
橡胶高分子材料直接循环利用的工艺流程
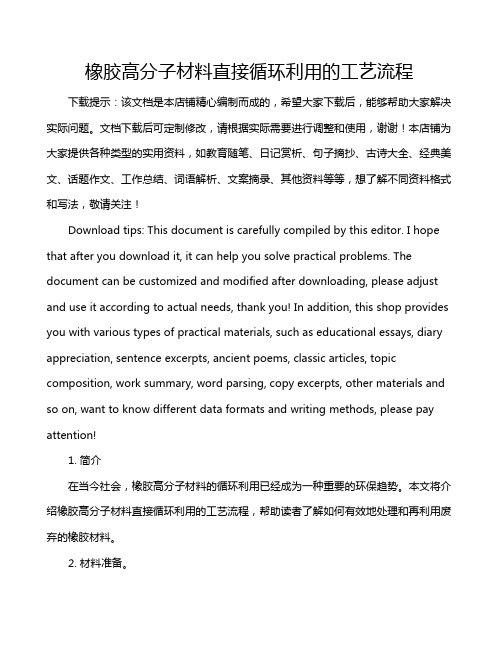
橡胶高分子材料直接循环利用的工艺流程下载提示:该文档是本店铺精心编制而成的,希望大家下载后,能够帮助大家解决实际问题。
文档下载后可定制修改,请根据实际需要进行调整和使用,谢谢!本店铺为大家提供各种类型的实用资料,如教育随笔、日记赏析、句子摘抄、古诗大全、经典美文、话题作文、工作总结、词语解析、文案摘录、其他资料等等,想了解不同资料格式和写法,敬请关注!Download tips: This document is carefully compiled by this editor. I hope that after you download it, it can help you solve practical problems. The document can be customized and modified after downloading, please adjust and use it according to actual needs, thank you! In addition, this shop provides you with various types of practical materials, such as educational essays, diary appreciation, sentence excerpts, ancient poems, classic articles, topic composition, work summary, word parsing, copy excerpts, other materials and so on, want to know different data formats and writing methods, please pay attention!1. 简介在当今社会,橡胶高分子材料的循环利用已经成为一种重要的环保趋势。
高分子材料成型加工

高分子材料成型加工简介高分子材料成型加工是指通过加热、挤压、拉伸等工艺将高分子材料转变成所需形状和尺寸的过程。
高分子材料广泛应用于各个领域,如塑料制品、橡胶制品、纤维材料等。
本文将介绍高分子材料成型加工的基本原理、常用的加工方法以及在实际应用中的注意事项。
基本原理高分子材料成型加工是利用高分子材料的可塑性进行加工的过程。
高分子材料的可塑性是指在一定的温度和压力下,可以被加工成各种形状的性质。
其基本原理可以归纳为以下几点:1.熔融:高分子材料在一定的温度范围内可以被熔化成流体状态,使得材料更易于流动和变形。
2.成型:将熔融的高分子材料注入到模具中,通过模具的形状和尺寸限制,使得熔融材料在冷却后得到所需的形状和尺寸。
3.冷却固化:熔融材料在模具中冷却后逐渐固化成固体,成为最终的成型品。
常用的加工方法注塑成型注塑成型是一种常用的高分子材料成型加工方法,适用于制造各种塑料制品。
其基本流程包括:1.材料准备:选择合适的塑料颗粒作为原料,将其加入注塑机的进料口中。
2.加热熔融:注塑机将原料加热、熔融,并将熔融的塑料材料注入到模具中。
3.冷却固化:模具中的熔融塑料材料在冷却后逐渐固化成固体,形成最终的成型品。
4.取出成品:将固化的成型品从模具中取出,并进行后续加工,如修整边缘、打磨表面等。
挤出成型挤出成型是另一种常用的高分子材料成型加工方法,适用于制造各种管材、板材等长型产品。
其基本流程包括:1.材料准备:将高分子材料以颗粒形式加入到挤出机的料斗中。
2.加热熔融:挤出机将颗粒状的高分子材料加热、熔融,并通过螺杆将熔融的材料挤出。
3.模具成型:挤出的熔融材料通过模具的形状和尺寸限制,被冷却成所需的形状和尺寸。
4.冷却固化:在模具中冷却后,熔融材料逐渐固化成固体,形成最终的成型品。
5.切割成品:挤出机会根据需要将成型品切割成所需的长度,以便后续使用。
除了注塑成型和挤出成型,还有许多其他的高分子材料成型加工方法,如压延成型、注射拉伸成型等,根据材料和产品的需求选择合适的加工方法。
橡胶成型工艺及模具设计

挤出机由螺杆、机身、机头(包括口型和芯型)、 机架和传动装置等部件组成。
一、螺杆
螺杆种类: 按螺纹分:单头、双头、 三头 按螺距分:等距收敛式和 复合螺纹等 按螺杆外形分:圆柱形、
圆锥形
二、机身(机筒)
机筒为中空圆筒,为了及时散发
和提供热量,机筒备有夹套,可通入
冷却水和蒸汽。
三、机头与口型
1.机头 ①直向形机头 如圆筒形、喇叭形 ②T形、Y形
5. 必须进行硫化才能使用,热塑性弹性体除外。
6. 必须加入配合剂。
其它如比重小、硬度低、柔软性好、气密性好等 特点,都属于橡胶的宝贵性能。
橡胶基本加工工艺
无论什么橡胶制品,都要经过混炼和硫化这两个 过程。橡胶基本加工工艺主要包括塑炼、混炼、 压延、压出、成型和硫化等。另外,对于一些特 殊产品还包括注压、浇注和黏合。
聚合单体:氯丁二烯 ★一般工作温度:-35~120℃
★特性:耐候性、耐臭氧性、阻燃、耐热性及耐化学 药品性均好 ★用途:轮胎内衬层、低压电线电缆、输送带、减震 橡胶、窗户密封条、胶粘剂、胶布、涂料 ★参考价格:3.0~3.5万元/吨
硅胶 (Q )
聚合单体:主链由硅原子和氧原子交替组成 ★一般工作温度:-93~250℃ ★性能:使用温度范围最广,毒性最低、具生理惰性、 透气性好、电绝缘性好,物理机械性能较差 ★用途:胶管、胶带、胶辊、电绝缘制品、人造皮肤、 器官等. ★参考价格:7.0~8.0万元/吨
三元乙丙胶 ( EPDM )
聚合单体: 乙烯\丙烯\第三单体 ★一般工作温度:-50~150℃ ★性能:耐老化耐臭氧性、耐极性液体、耐水及 过热水、水蒸气好、耐电性能好 ★用途:电线电缆绝缘层、汽车玻璃除水条、窗户密 封条、 蒸汽胶管、输送带等 ★参考价格:2.8~3.3万元/吨
四大高分子材料加工方法
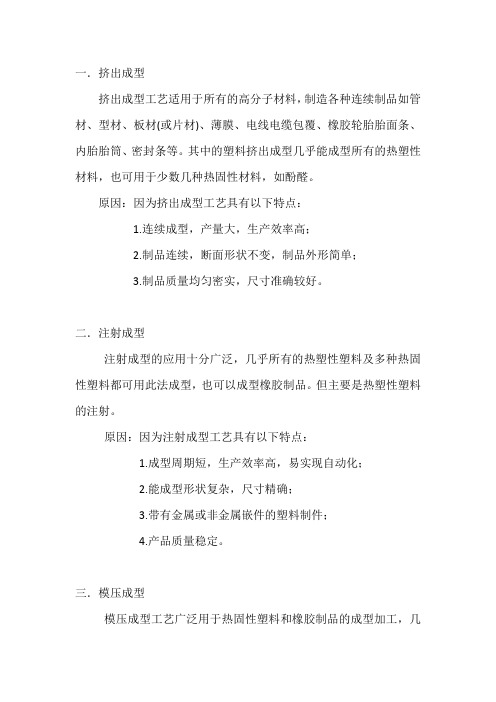
一.挤出成型挤出成型工艺适用于所有的高分子材料,制造各种连续制品如管材、型材、板材(或片材)、薄膜、电线电缆包覆、橡胶轮胎胎面条、内胎胎筒、密封条等。
其中的塑料挤出成型几乎能成型所有的热塑性材料,也可用于少数几种热固性材料,如酚醛。
原因:因为挤出成型工艺具有以下特点:1.连续成型,产量大,生产效率高;2.制品连续,断面形状不变,制品外形简单;3.制品质量均匀密实,尺寸准确较好。
二.注射成型注射成型的应用十分广泛,几乎所有的热塑性塑料及多种热固性塑料都可用此法成型,也可以成型橡胶制品。
但主要是热塑性塑料的注射。
原因:因为注射成型工艺具有以下特点:1.成型周期短,生产效率高,易实现自动化;2.能成型形状复杂,尺寸精确;3.带有金属或非金属嵌件的塑料制件;4.产品质量稳定。
三.模压成型模压成型工艺广泛用于热固性塑料和橡胶制品的成型加工,几乎所用的高分子材料都可用此方法来成型制品。
目前主要用于:热固性塑料的成型;橡胶制品的成型;复合材料的成型。
原因:因为模压成型工艺具有以下特点:1.与挤出和注射等成型工艺相比,模压成型工艺所需设备结构简单、制造精度不髙、制造费用低,所以投资少、见效快,为发展多品种、小批量的生产提供了有利条件;2.在模压成型过程中,由于塑料的流动距离很短,受填料的定向影响小,所以塑件的尺寸变动小,不易变形,尺寸稳定性好,机械性能稳定;3.相同吨位的压机可以成型较大平面的制品;4.模压成型工艺成熟,生产过程易于控制;5.模压成型中没有浇注系统,原材料浪费相对较少。
对于不能重复利用的热固性材料来讲,节约原料尤为重要;6.模压成型基本上适合于加工各种塑料,尤其像氨基树脂、环氧树脂和聚酰亚胺等材料,用注射成型既困难又会影响制品外观质量;对于用石棉或玻璃纤维等增强的塑料,在注射和挤出成型中,纤维易在浇口部分断裂,使制品的机械强度特别是冲击强度降低,失去增强的意义;聚酯团状和片状模塑料若采用注射成型,则需特殊的强迫加料装置,导致设备费用昂贵。
高分子材料成型加工(注射成型)详解

作用:将注射油缸的压力传给塑料,并使熔体注射 入模具 (4)分流梭
将物料流变成薄层,使塑料产生分流和收敛流动 加快热传递,缩短传热过程,避免物料过热分解 熔体在分流梭表面流速↑,剪切速度↑,产生较大的 摩擦热,使料温↑,有利于塑料的混合与塑化,有效 提高产量和质量
顿流体,通过圆形截面或平板狭缝形浇口。
ηa= Kγn-1 (n<1) 浇口的截面积↑ ,熔体体积流量↑
高分子材料成型加工
4. 熔体在模腔的流动:
4.1 熔体在典型模腔内的流动方式
4.2 熔体在模腔内的流动类型
高分子材料成型加工
三. 增密与保压过程: 1. 增密过程(压实过程) 2. 保压过程
4. 注射模具 成型零部件
凸模、凹模、型芯、 成型杆、镶块、动模、定模
浇注系统
主流道、分流道、浇口、 冷料阱、导向零件、分型 抽芯机构、顶出、加热、冷却、 排气
二. 注射机的工作过程
高分子材料成型加工
高分子材料成型加工
第二节 注射过程原理
一. 塑化过程 对塑料塑化的要求:塑料熔体进入模腔之前要 充分塑化,达到规定的成型温度。 塑化料各处的温度要均匀一致。 热分解物的含量达最小值。
高分子材料成型加工
2. 按注射机外形特征分类
高分子材料成型加工
高分子材料成型加工
3. 按注射机加工能力分类
注射量:注射机在注射螺杆(柱塞)作一次最大注射 行程时,注射装置所能达到的最大注射量
锁模力:注射机合模机构所能产生的最大模具闭紧力
4. 按注射机用途分类
高分子材料成型加工
二.注射机的基本结构
高分子材料成型工艺

高分子材料成型工艺高分子材料是一类具有高分子量、由大量重复单元结构组成的聚合物材料,具有良好的物理性能和化学稳定性,广泛应用于塑料、橡胶、纤维等领域。
高分子材料的成型工艺是指将高分子材料加工成所需形状和尺寸的工艺过程,包括塑料成型、橡胶成型和纤维成型等多个方面。
本文将重点介绍高分子材料成型工艺的相关内容。
首先,塑料成型是高分子材料成型工艺中的重要部分。
塑料成型工艺通常包括热塑性塑料和热固性塑料两种类型。
热塑性塑料成型工艺主要包括挤出成型、注塑成型、吹塑成型和压延成型等方法,通过加热塑料原料使其熔化,然后通过模具成型成所需的产品。
而热固性塑料成型工艺则是通过将热固性树脂与填料、助剂等混合后,经过加热固化成型。
塑料成型工艺的选择应根据塑料材料的性质、成型产品的要求和生产效率等因素进行综合考虑。
其次,橡胶成型是另一个重要的高分子材料成型工艺。
橡胶成型工艺通常包括挤出成型、压延成型、模压成型和注射成型等方法。
橡胶材料具有良好的弹性和耐磨性,广泛应用于汽车轮胎、密封件、橡胶垫等领域。
橡胶成型工艺的关键是控制橡胶材料的流动性和硫化反应,以确保成型产品的质量和性能。
最后,纤维成型是高分子材料成型工艺中的另一个重要领域。
纤维成型工艺通常包括纺丝、织造、非织造和纺粘等方法。
纤维材料具有良好的拉伸性和柔韧性,广泛应用于纺织品、复合材料、过滤材料等领域。
纤维成型工艺的关键是控制纤维材料的拉伸和取向,以确保成型产品的强度和外观。
总之,高分子材料成型工艺是高分子材料加工的关键环节,直接影响产品的质量和性能。
通过选择合适的成型工艺和优化工艺参数,可以实现高效、稳定地生产高质量的高分子材料制品,满足不同领域的需求。
希望本文对高分子材料成型工艺有所帮助,谢谢阅读。
高分子材料成型工艺

高分子材料成型工艺高分子材料是一种具有高分子量、由许多重复单元组成的材料,如塑料、橡胶和纤维等。
高分子材料的成型工艺是指将原料经过一系列加工工艺,使其具备特定形状和性能的过程。
本文将就高分子材料的成型工艺进行探讨,包括热塑性塑料和热固性塑料的成型工艺、注塑成型、挤出成型、吹塑成型、压延成型等内容进行详细介绍。
首先,热塑性塑料的成型工艺是指在一定温度范围内具有可塑性的塑料。
在加热软化后,通过模具加压成型,冷却后即可得到所需形状的制品。
而热固性塑料的成型工艺则是在一定温度范围内,通过热固化反应形成三维网络结构,使其成型后不再软化。
这两种成型工艺在实际生产中有着各自的特点和应用领域,需要根据具体情况选择合适的工艺。
其次,注塑成型是一种常见的高分子材料成型工艺,它是将熔融状态的塑料通过注射机注入模具中,经过一定的压力和温度条件下,塑料在模具中冷却凝固,最终得到所需的制品。
挤出成型是将塑料颗粒或粉末加热至熔融状态后,通过挤出机的螺杆推动,使塑料通过模具的特定截面形成连续的断面,冷却后得到所需的制品。
吹塑成型是将热塑性塑料加热软化后,通过气压吹塑成型。
压延成型是将热塑性塑料加热软化后,通过压延机的辊轧压成型。
这些成型工艺在高分子材料加工中起着至关重要的作用,不同的工艺适用于不同的产品类型和生产要求。
总的来说,高分子材料成型工艺是高分子材料加工中至关重要的一环,它直接影响着制品的质量和性能。
因此,在实际生产中,需要根据具体的材料特性、产品要求和生产条件选择合适的成型工艺,以确保生产出符合要求的制品。
同时,随着科技的不断进步和工艺的不断创新,高分子材料成型工艺也在不断发展和完善,为高分子材料的应用提供了更广阔的空间。
在实际生产中,需要根据具体的材料特性、产品要求和生产条件选择合适的成型工艺,以确保生产出符合要求的制品。
同时,随着科技的不断进步和工艺的不断创新,高分子材料成型工艺也在不断发展和完善,为高分子材料的应用提供了更广阔的空间。
橡胶制品工艺

橡胶制品工艺橡胶制品工艺是一门传统的制造技术,其定义为在一定条件下,通过在橡胶中添加各种助剂,使其具有可塑性、可加工性和定型性等物理和化学性能,以达到特定的制品要求。
橡胶制品工艺已经广泛应用于工业、医疗、交通、建筑、家庭等领域。
本文将详细介绍橡胶制品工艺的基本概念、加工流程、生产设备和制品质量控制等方面的知识。
一、橡胶制品工艺的基本概念1. 橡胶的种类和特性橡胶是一种高分子复合材料,通常由天然橡胶和合成橡胶两种组成。
天然橡胶可以从橡胶树的树液中提取,而合成橡胶是由石油和天然气等化石能源中提取的烃类化合物制成。
橡胶具有优异的物理和化学性能,例如良好的可塑性、弹性和抗拉性能,特别适用于制造运动器材、消费品、药品和医疗器械等各种产品。
2. 橡胶制品的工艺流程橡胶制品的加工流程通常包括以下几个步骤:混炼、成型、硫化和切割等。
混炼是将橡胶材料和各种助剂混合成形的过程,其目的是使橡胶具有可塑性、可加工性和定型性等特性。
成型是将混炼好的橡胶材料加工成各种形状和尺寸的制品,例如胶管、胶带和气囊等。
硫化是通过加热和添加硫化剂等方法,使橡胶中的分子间化学键形成交联结构,从而提高橡胶的硬度、强度和耐磨性。
切割是将硫化后的橡胶制品按照规定的尺寸和形状进行切割加工,以使其符合生产要求。
3. 橡胶制品的助剂种类和作用橡胶制品制造中需要添加各种助剂,以调节橡胶的性质和加工过程。
常见的助剂种类包括增塑剂、填料、加工油、抗氧化剂和硫化剂等。
增塑剂可以使橡胶具有更好的可塑性和可加工性。
填料可以提高橡胶制品的硬度和强度,减少成品的成本。
加工油可以降低混炼温度,延长橡胶的流动性。
抗氧化剂可以增加橡胶的耐热性和耐老化性。
硫化剂可以通过交联橡胶中的分子间化学键,提高橡胶的强度和硬度,同时增加其耐腐蚀性和弹性。
二、橡胶制品加工流程橡胶制品的加工流程通常由混炼、成型、硫化和切割等几个步骤组成。
1. 混炼混炼是橡胶制品加工的首要步骤,可以将各种橡胶和助剂混合成形。
橡胶加工工艺—橡胶压延工艺(高分子成型课件)
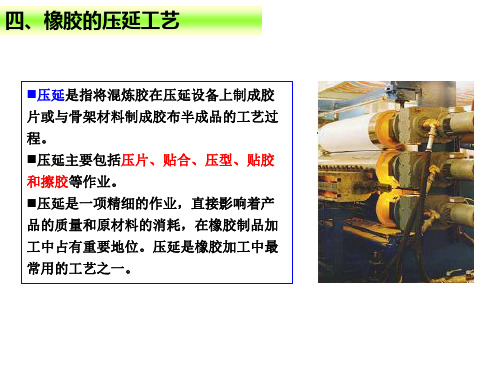
a,b-两辊压型(v1=v2); c-三辊压型(v1v2=v3); d-四辊压型(v2=v3=v4v1)
三、橡胶的压延工艺
(二)压延工艺方法 3 胶片贴合
胶片贴合:通过压延机将两层或多层薄胶片贴合在一起的工艺过程。
通常用于制造较厚、质量要求较高 的胶片和两种不同胶料组成的胶片、 夹布层胶片等。 贴合方法有二辊压延机贴合法、三 辊压延机贴合法、四辊压延机贴合法。 四辊压延机可一次同时完成两个新 鲜胶片的压延与贴合。贴合效率高、 质量好、精度高,但压延效应大。
三、橡胶的压延工艺
(二)压延工艺方法 1 压片
压片:利用压延机等速辊筒将胶料制成具有规定断面厚度和宽度的表面 光滑的胶片。胶片应表面光滑,无绉缩,内部密实,无孔穴、气泡或海绵; 断面厚度均匀,精度,各部分收缩变形一致。 设备:压片压延机一般为三辊或四辊压延机,但多采用三辊压延机
压片工艺分类: ①积胶压延法片材表 面光滑,密实,减少气泡,但会增大压 延效应,适于丁苯橡胶。②普通挤胶法 适于NR。
三、橡胶的压延工艺
(三)压延制品厚度的控制
1 沿辊筒轴线方向上厚度
三高两低现象
(1)辊筒的弹性弯曲变形(横压力) 辊筒弹性弯曲变形(横压力)使压延制品中间厚两边薄 克服方法: a 中高度补偿法 ; b 轴交叉法 ; c 预应力法 (2)辊筒表面温度 轴承润滑油带走部分热量,辊筒温度中间高两边低使压延制品两边 较中间厚。 克服方法: a 中间鼓风冷却; b 两边红外加热
厚擦法:T上>T下>T中; 薄擦法: T上>T中> T下
三、橡胶的压延工艺
(二)压延工艺方法 5 纺织物挂胶的工艺影响因素
(1)胶料的可塑度 为了保证胶料对布孔的充分渗透,胶料要有较高的可塑 度(比压片胶料大)。天然橡胶的贴胶可塑度为0.4-0.5、 擦胶可塑度为0.5-0.6较为合适。 (2)辊温 辊温控制比压片时高,以增大胶料的流动性及胶料与纺织 物间的附着力。但辊温过高易产生焦烧。
高分子材料加工技术--压制成型

1.2工艺过程
高分子材料成型加工
高分子材料成型加工
2.片状模塑料模压成型
(Sheet Molding Compound. SMC)
2.1 配比:
不饱和聚酯 约20~30%
增稠剂
约 5%
无机填料 40~50%
引发剂
2~3%
脱模剂
0.5~1%
短切玻璃纤维或毡片 适量
2.2 工艺过程
高分子材料成型加工
高分子材料成型加工
三. 模型硫化工艺及硫化条件
工艺过程
混炼胶和橡胶半成品→ 计量→ 加料→ 闭 模→排气 →保压(硫化)→ 脱模→ 制品
这一过程基本上与热固性塑料的模压成型 相同,硫化工艺条件是硫化压力、硫化温 度和硫化时间。
高分子材料成型加工
1.硫化压力 大多数的橡胶制品的硫化是在一定压力下 进行的 一般模压制品的硫化压力为2~4 MPa 胶料流动性差,制品形状复杂,制品表面 花纹细致,结构复杂,厚制品,硫化温度 高,则硫化压力高一些。 太高的硫化压力会加速橡胶分子链的热降 解
高分子材料成型加工
一. 热固性模塑料的成型工艺性能:
1.流动性:热固性模塑料的流动性是指其在受热和受 压情况下充满整个模具型腔的能力。 影响流动性的因素:
压模塑料的性能和组成(分子量、颗粒形状、小分 子物质)
模具与成型条件(光洁度、流道形状、预热)
流动性要适中:
太大:溢出模外,塑料在型腔内填塞不紧,或树脂 与填料分头聚集。
高分子材料成型加工
根据实践经验,在选择模压成型的工艺条 件时,可以从模压压力、温度和时间三者 中先固定一个条件,如按经验选定成型压 力,然后再变化成型的温度和时间,从实 验中找出合理的条件来。
(完整版)高分子材料成型加工四种成型加工方法优缺点

1.压制成型:应用于热固塑料和橡胶制品的成型加工压制成型方法对于热固性塑料、橡胶制品和增强复合材料而言,都是将原料加入模具加压得到制品,成型过程都是一个物理—化学变化过程。
不同的是橡胶制品的成型中要对原料进行硫化。
橡胶通过硫化获得了必需的物理机械性能和化学性能。
而在复合材料压制成型过程中,还用到了层压成型(在压力和温度的作用下将多层相同或不同材料的片状物通过树脂的粘结和熔合,压制成层压塑料的成型方法)和手糊成型(以玻璃纤维布作为增强材料,均匀涂布作为黏合剂的不饱和聚酯树脂或环氧树脂的复合材料)。
2.挤出成型:适用于所有高分子材料,广泛用于制造轮胎胎面、内胎、胎管及各种断面形状复杂或空心、实心的半成品,也用于包胶操作。
挤出成型挤出成型对于高分子三大合成材料所用的设备和加工原理基本上是相同的。
有区别的是橡胶挤出是在压出机中对混炼胶加热与塑化,通过螺杆的旋转,使胶料在螺杆和料筒筒壁之间受到强大的挤压作用,不断向前推进,并借助于口型(口模)压出具有一定断面形状的橡胶半成品。
而合成纤维的挤出纺丝过程,采用三种基本方法:熔融纺丝、干法纺丝、湿法纺丝。
一般采用熔融纺丝(在熔融纺丝机中将高聚物加热熔融制成溶体,通过纺丝泵打入喷丝头,并由喷丝头喷成细流,再经冷凝而成纤维)。
3.注射成型:应用十分广泛,几乎所有的热塑性塑料及多种热固性塑料都可用此法成型,也可以成型橡胶制品。
注射成型高分子三大合成材料的注射成型过程中所用设备和工艺原理比较相似,但是从基本过程和要求看热固性塑料注射和热塑性塑料注射有很多不同之处。
热固性塑料的注射成型要求成型物料首先在温度相对较低的料筒内预塑化到半熔融状态,然后在随后的注射充模过程中进一步塑化,避免其因发生化学反应而使黏度升高,甚至交联硬化为固体。
塑料注射成型原料是粒状或粉状的塑料,而橡胶注射成型原料则是条状或块粒状的混炼胶,且混炼胶在注压入模后须停留在加热的模具中一段时间,使橡胶进行硫化反应。
高分子材料成型加工四种成型加工方法优缺点

1.压制成型:应用于热固塑料和橡胶制品的成型加工压制成型方法对于热固性塑料、橡胶制品和增强复合材料而言,都是将原料加入模具加压得到制品,成型过程都是一个物理—化学变化过程。
不同的是橡胶制品的成型中要对原料进行硫化。
橡胶通过硫化获得了必需的物理机械性能和化学性能。
而在复合材料压制成型过程中,还用到了层压成型(在压力和温度的作用下将多层相同或不同材料的片状物通过树脂的粘结和熔合,压制成层压塑料的成型方法)和手糊成型(以玻璃纤维布作为增强材料,均匀涂布作为黏合剂的不饱和聚酯树脂或环氧树脂的复合材料)。
2.挤出成型:适用于所有高分子材料,广泛用于制造轮胎胎面、内胎、胎管及各种断面形状复杂或空心、实心的半成品,也用于包胶操作。
挤出成型对于高分子三大合成材料所用的设备和加工原理基本上是相同的。
有区别的是橡胶挤出是在压出机中对混炼胶加热与塑化,通过螺杆的旋转,使胶料在螺杆和料筒筒壁之间受到强大的挤压作用,不断向前推进,并借助于口型(口模)压出具有一定断面形状的橡胶半成品。
而合成纤维的挤出纺丝过程,采用三种基本方法:熔融纺丝、干法纺丝、湿法纺丝。
一般采用熔融纺丝(在熔融纺丝机中将高聚物加热熔融制成溶体,通过纺丝泵打入喷丝头,并由喷丝头喷成细流,再经冷凝而成纤维)。
3.注射成型:应用十分广泛,几乎所有的热塑性塑料及多种热固性塑料都可用此法成型,也可以成型橡胶制品。
注射成型高分子三大合成材料的注射成型过程中所用设备和工艺原理比较相似,但是从基本过程和要求看热固性塑料注射和热塑性塑料注射有很多不同之处。
热固性塑料的注射成型要求成型物料首先在温度相对较低的料筒内预塑化到半熔融状态,然后在随后的注射充模过程中进一步塑化,避免其因发生化学反应而使黏度升高,甚至交联硬化为固体。
塑料注射成型原料是粒状或粉状的塑料,而橡胶注射成型原料则是条状或块粒状的混炼胶,且混炼胶在注压入模后须停留在加热的模具中一段时间,使橡胶进行硫化反应。
高分子材料成型加工中的热转印成型工艺

高分子材料成型加工中的热转印成型工艺
高分子材料成型加工是制造行业中的重要工艺之一,其中热转印成
型工艺作为一种高效、环保的成型方法,逐渐受到关注和应用。
本文
将从热转印成型工艺的原理、优势以及应用领域等方面进行探讨。
一、热转印成型工艺的原理
热转印成型工艺是一种将热塑性高分子材料通过热压成型的过程。
其原理为首先将高分子材料制品与转印膜放置在加热板上,经过高温
和高压的作用,使得转印膜上的图案或文字转移到高分子材料表面,
完成产品的装饰或烫印。
二、热转印成型工艺的优势
1. 成型速度快:热转印成型工艺在制作产品时,只需简单地将热塑
性高分子材料与转印膜进行热压,无需等待时间,成型速度快。
2. 成型精度高:热转印成型工艺可以实现对产品表面的图案、色彩
等细节要求,确保产品的装饰效果和品质。
3. 环保健康:热转印成型工艺采用的转印膜和颜料都是环保无害的
材料,不会对人体造成伤害,符合环保要求。
4. 适用性广:热转印成型工艺适用于各种形状、材质的高分子制品,如塑料制品、橡胶制品等,具有很强的适用性。
三、热转印成型工艺的应用领域
热转印成型工艺广泛应用于日常生活用品、工艺品、电子产品外壳等领域。
比如塑料杯子、手机壳、玩具等制品的表面图案和花纹都可以通过热转印成型工艺进行装饰,使得产品更加美观、个性化。
总的来说,热转印成型工艺作为一种低成本、高效率的加工方法,在高分子材料成型加工中发挥了重要的作用。
通过不断的技术改进和创新,相信热转印成型工艺将在未来得到更广泛的应用和推广。
高分子材料成型

高分子材料成型高分子材料是一类分子量较大的有机化合物,由许多重复单元组成,具有较高的分子量和较大的分子量分布范围。
高分子材料广泛应用于各个领域,如塑料制品、橡胶制品、纤维材料等。
在高分子材料的生产过程中,成型是一个非常重要的环节,成型工艺的优劣直接影响着最终产品的质量和性能。
高分子材料的成型工艺主要包括挤出成型、注塑成型、吹塑成型、压延成型、模压成型等。
其中,挤出成型是一种常见的成型工艺,通过将高分子材料加热至熔融状态,然后通过挤出机将熔融物料挤出成型,最终得到所需形状的制品。
注塑成型则是将高分子材料加热至熔融状态,然后将熔融物料注入模具中,经冷却凝固后得到制品。
吹塑成型则是将高分子材料加热至熔融状态,然后通过气压将熔融物料吹塑成型,最终得到空心制品。
压延成型是将高分子材料加热至熔融状态,然后通过辊压将熔融物料压延成型,最终得到薄膜或片材。
模压成型则是将高分子材料加热至熔融状态,然后将熔融物料放入模具中,经加压冷却后得到制品。
在高分子材料的成型过程中,需要考虑原料的选择、加工工艺、成型温度、成型压力等因素。
首先,原料的选择对成型工艺具有重要影响,不同的高分子材料适用于不同的成型工艺,需要根据具体情况进行选择。
其次,加工工艺对成型质量和效率有着直接影响,需要根据产品的要求进行合理的工艺设计。
再者,成型温度和成型压力也是影响成型质量的重要因素,需要根据具体材料和产品要求进行合理的控制。
在实际生产中,需要根据具体产品的要求和工艺条件选择合适的成型工艺,合理控制成型温度和成型压力,确保最终产品的质量和性能。
同时,还需要加强对成型设备的维护和保养,确保设备的正常运转和稳定性。
此外,还需要不断改进和优化成型工艺,提高生产效率和产品质量,满足市场需求。
总之,高分子材料的成型是一个复杂而重要的工艺环节,需要综合考虑原料选择、加工工艺、成型温度、成型压力等因素,确保最终产品的质量和性能。
只有不断优化和改进成型工艺,才能适应市场需求,提高生产效率,实现可持续发展。
高分子材料加工技术

高分子材料加工技术高分子材料加工技术是一门涉及高分子材料的物理、化学和工程技术的综合学科。
高分子材料是一种由大量重复连接而成的大分子化合物,具有独特的化学和物理特性,因此在各个领域都有广泛的应用。
高分子材料加工技术则是将这些材料加工成各种形状和结构的技术过程,包括塑料成型、橡胶加工、纤维制造等。
高分子材料加工技术的发展离不开先进的加工设备和技术手段。
在塑料成型方面,注塑成型是常用的方法之一。
它通过将高分子材料加热至熔化状态,然后通过高压注射进入模具中,经过冷却凝固成型。
注塑成型具有成本低、生产效率高、产品质量稳定等优点,广泛应用于制造日用品、汽车零部件、电子产品外壳等领域。
另一种常用的塑料成型方法是挤出成型。
挤出成型是利用高温和高压将塑料材料从模具中挤压出来,形成连续的薄膜、板材、管材等产品。
这种方法适用于大批量生产,常用于制造塑料膜、塑料板材等领域。
除了塑料成型,高分子材料的加工还包括橡胶加工和纤维制造。
橡胶加工主要是通过将橡胶材料热塑或硫化,然后进行压延、压制等工艺,制造橡胶制品。
橡胶制品广泛应用于汽车轮胎、密封件、管道等领域。
纤维制造是将高分子材料加工成纤维状态,主要有纺丝、纺纱、纺织等工艺。
纤维制品在纺织、服装、家居用品等领域有着广泛的应用。
高分子材料加工技术在现代工业中发挥着重要的作用。
它不仅满足了人们对材料性能和外观要求的不断提高,还提高了生产效率,降低了生产成本。
随着科技的不断进步和人们对材料性能要求的不断提高,新型的高分子材料加工技术也在不断涌现。
例如,纳米材料技术是近年来兴起的一种高分子材料加工技术。
纳米材料是指颗粒尺寸在1到100纳米之间的材料,在纳米尺度下具有独特的物理、化学和生物学特性。
纳米材料技术通过操纵和控制纳米级颗粒的组装和结构,实现对材料性能的精确调控和改善。
纳米材料技术在医学、能源、环境等领域有着广泛的应用前景。
除了纳米材料技术,生物降解材料也是近年来受到关注的一种高分子材料加工技术。
浅谈高分子材料成型加工技术以及应用前景

浅谈高分子材料成型加工技术以及应用前景高分子材料是一类具有高分子结构的材料,常见的有塑料、橡胶、纤维等。
高分子材料成型加工技术是将高分子材料通过加热、压力等工艺加工成形的过程。
这项技术在工业生产中有着广泛的应用,因为高分子材料具有优良的性能,能够满足各种需求。
高分子材料成型加工技术主要包括注塑、挤出、吹塑、压延、模压等多种加工方法。
注塑是最常用的一种方法,通过将高分子材料加热融化后注入模具中,经过冷却凝固后取出得到所需产品。
这种方法适用于制作各种复杂形状的产品,如塑料盒、汽车配件等。
挤出是将高分子材料加热融化后通过挤出机挤出成形的方法,适用于制作长条状产品,如塑料管道、板材等。
吹塑是将高分子材料加热融化后通过喷嘴喷吹成形的方法,适用于制作中空产品,如瓶子、容器等。
压延是将高分子材料加热融化后通过辊压机进行连续压制成形的方法,适用于制作薄膜、薄板等产品。
模压是将高分子材料加热融化后注入模具中,经过冷却凝固后取出得到所需产品,适用于制作各种复杂形状的产品,如手机壳、电器壳等。
高分子材料成型加工技术的应用前景非常广阔。
高分子材料成型加工技术可以应用于各个领域的制造业中。
如汽车行业,高分子材料可以制作汽车配件,如悬挂件、内饰件等,具有降低重量、提高强度、降低噪音等优点;电子电器行业,高分子材料可以制作各种电子产品外壳、连接器等,具有绝缘、耐高温等优点;航空航天行业,高分子材料可以制作航空器的结构件、隔热材料等,具有轻质、耐高温等优点;医疗器械行业,高分子材料可以制作各种医疗器械、器皿等,具有生物相容性等优点。
高分子材料成型加工技术还可以应用于环保领域。
高分子材料可以通过成型加工技术制作可降解的塑料制品,如餐具、袋子等,可以减少传统塑料制品对环境的污染。
高分子材料还可以应用于再生资源利用,通过回收利用废旧高分子制品,再经过适当的加工处理,可以得到具有一定性能的再生材料,用于制造新的高分子制品。
高分子材料成型加工技术还可以应用于新材料研究领域。
高分子材料成形工艺橡胶制品成形

•图15.3 倾斜式加料口结 构
PPT文档演模板
高分子材料成形工艺橡胶制品成形
二、机筒
v 橡胶挤出温度在30~140℃间,通常100℃以下,所以 橡胶挤出机通常采用螺旋夹套供加热冷却用
Ø 长径比较大的挤出机在塑化段和挤出段有时采用 轴向钻孔机筒以强化冷却效果,加热一般用蒸汽, 冷却常用水
Ø 冷喂料机螺杆(较热喂料机复杂)常分三段设计, 多采用主副螺纹形(即分离型),销钉型机筒挤 出机是新型冷喂料挤出机,销钉可使混合均化作 用强化,但温升均匀且不会过高
PPT文档演模板
高分子材料成形工艺橡胶制品成形
橡胶挤出机与塑料挤出机螺杆的差异:
①橡胶挤出机螺杆长径比较小 Ø 因为橡胶黏度很高,缩短挤出机长度可防止胶 料过热和焦烧(热喂料机L/D一般很短,4~5, 而冷喂料机在8~16,冷喂料排气机则16~22)
PPT文档演模板
高分子材料成形工艺橡胶制品成形
②橡胶挤出机螺杆螺槽深度通常相当大
高分子材料成形工艺橡胶制品成形
v 挤出实心或圆形中空半成品的口型尺寸一般约为螺杆 直径0.3~0.75 Ø 口型过大,机头内压力不足,排胶不均匀,半成 品形状不规整 Ø 口型过小,压力太大,剪切作用太强,增加焦烧 的危险性
v 对于扁平形半成品,挤出宽度可为螺杆直径的 2.5~3.5倍
PPT文档演模板
PPT文档演模板
高分子材料成形工艺橡胶制品成形
PPT文档演模板
•图15.4销钉机筒
高分子材料成形工艺橡胶制品成形
三、螺杆
v 螺杆螺纹有单头、双头和复合型三种形式 Ø 单头多用于滤胶;双头可使出料均匀,多用于挤 出成形;为利于加料和保证出料均匀性,可采用 加料段为单头、出料段为双头的复合型螺纹 Ø 螺杆主要是利用等距不等深实现压缩比
高分子材料成形工艺橡胶制品成形共97页

60、生活的道路一旦选定,就要勇敢地 走到底 ,决不 回头。 ——左
高分子材料成形工艺橡胶制品成形
1、合法而稳定的权力在使用得当时很 少遇到 抵抗。 ——塞 ·约翰 逊 2、权力会使人渐渐失去温厚善良的美 德。— —伯克
3、最大限度地行使权力总是令人反感 ;权力 不易确 定之处 始终存 在着危 险。— —塞·约翰逊 4、权力会奴化一切。——塔西佗
5、虽然权力是一头固执的熊,可是金 子可以 拉着它在、过 去和未 来文化 生活的 源泉。 ——库 法耶夫 57、生命不可能有两次,但许多人连一 次也不 善于度 过。— —吕凯 特 58、问渠哪得清如许,为有源头活水来 。—— 朱熹 59、我的努力求学没有得到别的好处, 只不过 是愈来 愈发觉 自己的 无知。 ——笛 卡儿
- 1、下载文档前请自行甄别文档内容的完整性,平台不提供额外的编辑、内容补充、找答案等附加服务。
- 2、"仅部分预览"的文档,不可在线预览部分如存在完整性等问题,可反馈申请退款(可完整预览的文档不适用该条件!)。
- 3、如文档侵犯您的权益,请联系客服反馈,我们会尽快为您处理(人工客服工作时间:9:00-18:30)。
均匀、致密,容易变换规格,设备占地面积小,结构简单,
操作连续,生产率高
(按加入胶料温度)橡胶挤出工艺:热喂料和冷喂料两种 热喂料挤出的喂料是经过热炼工序的较高温度胶条 冷喂料挤出的喂料是室温状态的较硬胶条和块状料
15.1.1 橡胶挤出机
生产,胶料高热历程短而不易发生焦烧,挤出胶料均匀 性好,制的质量改善
应用:天然橡胶及合成橡胶的挤出,电线、电缆、胶管
等小规格制品方面逐渐取代热喂料挤出
冷喂料挤出各部位常用温度:螺杆<35℃,加料段
35~50℃,塑化段40~60℃,挤出段50~70℃,机头和口型 80~100℃
冷喂料挤出还常采用冷喂料排气挤出机:可用于胎面胶
第十五章 橡胶制品成形
1
15.1 挤出成形 15.2 压延成形 15.3 注射成形 15.4 橡胶复合制品实例――充气
外胎的成形
2
(按制造过程特征)橡胶制品:非模型制品和模型制品
大多数橡胶制品都属模型制品,特征是成形过程
与硫化过程同时进行,成形工艺主要有模压成形
和注射成形两种
非模型制品(胶布、胶管、压延胶片、氧气袋、
层以增加织物与压延胶层的结合强度
浸胶:将纺织物浸入胶乳中使纺织物附着一定胶量的工艺
浸胶工艺有单独浸胶和与压延机联动浸胶两种,生产以
单独浸胶工艺为主
浸胶工艺包括浸胶、挤压、扩布、干燥、卷取等工序,
工艺因素有浸胶液组成及浓度、浸渍时间、布张力、挤
压辊压力和干燥条件等
图15.6 浸胶工艺过程示意图 1-布卷 2-调节装置 3-浸渍槽 4-压辊 5-干燥室 6-卷取
用量过大易引起焦烧)
添加适量软化剂可提高挤出速度且挤出物表面质量改善 胶料中掺入适量再生胶,挤出速度可增大且挤出物收缩率
相应降低
(2)挤出机温度
挤出机一般以口型处温度最高,机头次之,机筒最低
温度控制可根据情况调节:如胶料含生胶量较大,
可塑性较小,则应采用较高的温度
表15.1部分常用橡胶挤出时各部位温 度的控制范围
延机、挂胶压延机、通用压延机和钢丝压延机等
15.2.1 压延前准备
压延前准备:包括胶料热炼及供胶和纺织物预加工
一、胶料热炼及供胶
1.胶料热炼
一般采用开炼机,开炼机热炼分为一步热炼法和两步热炼法 一步热炼法:把胶料在开炼机上一次完成,热炼温度
60~70℃,辊距5~6mm,时间5~10min
两步热炼法:分粗炼和细炼两步完成,粗炼采用低温薄通
采用三辊压延机
(1)压片工艺
压片:方法有两种,一是中下辊不积胶方式,下辊仅
起冷却作用;二是中下辊间积胶方式,适量的积胶有 利于胶片光滑,减少气泡和提高胶片致密性
要求:胶片表面光滑、不皱缩、无气泡且厚度均匀
影响因素:主要有胶料组成及配方、可塑度、辊温、
辊速及辊速比等
图 15.7 压片工艺示意图 (a)中下辊不积胶 (b)四辊压延机压片 (c)中下辊间有积胶
37
3.热伸张
锦纶和聚酯帘布有受热收缩的特性,压延前必须进行热伸
张处理以保证尺寸稳定性
热伸张处理工艺通常分三步进行:①热伸张区,即在帘线
软化点以上的温度对帘布施加张力使取向度和结晶度提高; ②热定形区,对热伸张的帘布进行热定形,温度与热伸张 区相同或低5~10℃,张力作用略低;③冷定形区,保持帘 布张力不变,使帘布冷到玻璃化温度以下的常温范围
片等)
T型和Y型分别用于胶料挤出方向与螺杆成90°和60°
角的场合,如电线电缆包胶、钢丝和胶管的包胶等
还有剪切机头等特殊机头和各种复合挤出机头
五、口型
机头前安装口型,口型一般分两种: 用于挤出实心和片状半成品的口型是带有与半成
品形状相应开孔的钢板
用于挤出中空半成品的口型由外口型、芯型及支
贴合鞋等)特征是成形过程和硫化过程分开进行, 成形工艺主要有挤出成形和压延成形两种
15.1 挤出成形
15.1.1 橡胶挤出机 15.1.2 挤出工艺
4
橡胶挤出(或称压出):应用很广,如轮胎胎面、内胎、
胶管、胶带、电线电缆外套和异形橡胶制品,胶料的过滤、 造粒、塑炼、混炼以及上下工序的联动(如密炼机下的补 充混炼下片,热炼后对压延机的供胶等)
断面有很大差异,因此必须根据挤出变形特征合理设
计口型
首先需要考虑胶料的挤出膨胀率,其次考虑挤出
膨胀的各向差异特征(板式口型挤出胶料的断面 变形通常是中间大边缘小)
图15.5 各种实心制品挤出断面的变形图 (上面为口型形状,下面为对应的挤出物断面形状)
19
15.1.2 挤出工艺
一、热喂料挤出工艺
因为橡胶黏度很高,缩短挤出机长度可防止胶
料过热和焦烧(热喂料机L/D一般很短,4~5, 而冷喂料机在8~16,冷喂料排气机则16~22)
②橡胶挤出机螺杆螺槽深度通常相当大
螺槽较深是为减少黏性生热,深度增加可提高产
量但太深会影响胶料机械强度,深度过浅则易过 热和焦烧
螺纹深度一般为螺杆外径18%~23%,冷喂料机
橡胶挤出机通常采用螺旋夹套供加热冷却用
长径比较大的挤出机在塑化段和挤出段有时采用
轴向钻孔机筒以强化冷却效果,加热一般用蒸汽,
冷却常用水 多采用主副螺纹形(即分离型),销钉型机筒挤 出机是新型冷喂料挤出机,销钉可使混合均化作
冷喂料机螺杆(较热喂料机复杂)常分三段设计,
用强化,但温升均匀且不会过高
橡胶挤出机基本结构和主要参数名称与塑料挤出机
相同,但结构特征及参数数据有所差别
(根据加入胶料的温度不同)橡胶挤出机:热喂料
挤出机和冷喂料挤出机两大类,两者的差异主要在 于挤出系统
图15.1 橡胶螺杆挤出机(热喂料)的结构示意图 1-螺杆 2-机头 3-机筒 4-分配装置 5-加料口 6-螺杆尾部 7-变速装置 8-螺杆供水装置 9-电机
图15.4销钉机筒
11
三、螺杆
螺杆螺纹有单头、双头和复合型三种形式
单头多用于滤胶;双头可使出料均匀,多用于挤
出成形;为利于加料和保证出料均匀性,可采用
加料段为单头、出料段为双头的复合型螺纹
螺杆主要是利用等距不等深实现压缩比
橡胶挤出机与塑料挤出机螺杆的差异:
①橡胶挤出机螺杆长径比较小
却,然后再降至20~30℃,以免冷却程度过强导致冷却
变形不规则
为防止半成品相互黏结,可以在冷却水槽中加入滑石粉形
成悬浮隔离液或者使挤出物先通过滑石粉槽然后空气冷却
挤出空心半成品则应通过芯型上的喷射孔喷射隔离剂(多
采用液体隔离剂,如皂片水溶液)以免半成品内壁黏连
二、冷喂料挤出工艺
冷喂料挤出:省去热炼设备,易于实现机械化、自动化
螺纹槽偏浅些 ③橡胶挤出机螺杆压缩比相对较小
热喂料机压缩比一般1.3~1.4,冷喂料机一般
1.6~1.8,而滤胶机不需要压缩,一般为1,是等 距等深螺杆
四、机头
机头结构:主要有圆筒型、扁平型、T型和Y型四类 圆筒型用于挤出圆形或小型半成品(如胶管、内胎、
密封条等)
扁平型用于挤出宽断面扁平半成品(如外胎胎面、胶
26
(3)挤出速度
机台塑化性能好则可用较高的速度挤出 胶料中生胶含量低或挤出性能较好时挤出速度可选取
较高的范围
挤出温度高则挤出速度可以提高 丁苯、丁腈和丁基橡胶的挤出膨胀收缩大,挤出较困
难,挤出速度宜低些
(4)挤出物的冷却
生产上常用水喷淋或水槽冷却两种方法 挤出大型半成品(如胎面)一般须经预缩处理后
1.挤出工艺流程
热喂料挤出工艺:包括胶料热炼及供胶、挤出、冷
却、裁断和接取等
(1)胶料热炼及供胶
冷胶料送入挤出机之前必须进行充分热炼以提高胶
料均匀性及热塑性
热炼:可采用开炼机和密炼机,一般采用开炼机,通
常分粗炼和细炼两步进行
粗 炼 采 用 低 温 薄 通 法 , 温 度 4 5 ℃ 左 右 , 辊 距
架组成,芯型上有喷射隔离剂的孔
挤出实心或圆形中空半成品的口型尺寸一般约为螺杆
直径0.3~0.75
口型过大,机头内压力不足,排胶不均匀,半成
品形状不规整
口型过小,压力太大,剪切作用太强,增加焦烧
的危险性
对于扁平形半成品,挤出宽度可为螺杆直径的
2.5~3.5倍
橡胶挤出膨胀变形比较严重,半成品几何形状与口型
才进入冷却水槽,预缩率可5%~12%,预缩方法是 使半成品经过一组倾斜导辊或一组由大到小圆辊 使沿长度方向预缩
冷却水温通常宜控制在15~25℃之间,挤出物要冷到
25~35℃
冷却水流动方向与挤出方向相反以免挤出物骤冷(骤冷
会引起局部收缩而导致挤出物的畸形或引起硫黄析出)
较厚或厚度相差较大的挤出物通常采用40℃左右温水冷
法,温度45℃左右,辊距1~2mm;细炼是把粗炼胶料在另 一台开炼机进一步较高温度热炼,胶温略低于压延最高辊
筒温度5~15℃
2.向压延机供胶
向压延机供胶有连续和间断两种方法 间断供胶:把热炼胶料打成胶卷或制成胶条再往
压延机上供胶,胶卷停放时间不能过长,一般不 超过30min
连续供胶:有两种方式,一是采用圆盘式或平板
7
一、加料口
加料以条状或块状胶料为主,加料口上方一般不设加
料斗
加料口一般与螺杆成33°~45°倾角以利胶料沿螺杆
底部卷入机筒内
为满足自动连续供料的需要螺杆旁可加旁压辊或在加
料口上方设有导辊
图15.2 橡胶挤出机的4种加料口形式
图15.3 倾斜式加料口结构
9
二、机筒