固定床流化床设计计算
精选固定床反应器的工艺设计
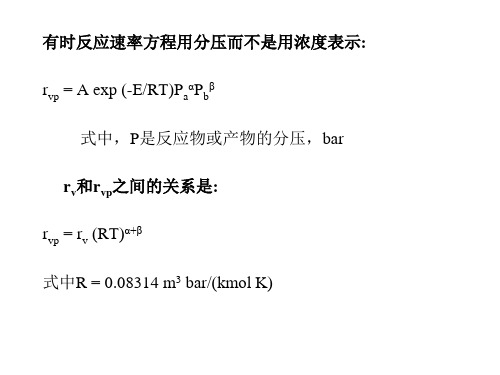
CA = PFyo(1-x)/(RG*T(6.5555Fyo+ 急冷量)) CB = P(Fyo(5-x)+0.9急冷量)/(RG*T (6.5555Fyo+急冷量))若把这些CA和CB项代入式(6-32),则: rv = - dCA/dθ = kCACB0.5 = Aexp(-E/RGT) (P/(RG*T(6.5555Fyo+ 急冷量)))1.5 Fyo(1-x) (Fyo(5-x)+0.9急冷量)0.5将上式与(6-8)合并:dx/dz = AcAexp(-E/RGT)(P/RG*T(6.5555Fyo+急冷量))1.5(1-x) (Fyo(5-x)+0.9急冷量)0.5
压降方程
开始可计算出∆P/z值,而后在每一步进行适当的压力校正。
实例,恒温反应器设计
H2C=CH2十H2 → CH3一CH3 (6-9)这是一个放热反应,但它可在很小的恒温反应器中进行。铜—氧化镁为催化剂,把这些催化剂装在一个内径为9.35mm、长为280mm带水夹套的黄铜制的反应器管中。由于把37.85 l/min的水循环通过夹套,因而可得到大于5.67kJ/(m2 S K)的水膜传热系数和恒定的管壁温度。在此反应器内,9—79℃范围内的各种恒定温度下进行的许多试验证明,对氢气来说,式(6-9)表示的反应是一级的。通过给定下列条件可写出反应速率方程:rv = kCH (6-10)该系统中, η = 1
有时反应速率方程用分压而不是用浓度表示:rvp = A exp (-E/RT)PaαPbβ 式中,P是反应物或产物的分压,bar rv和rvp之间的关系是:rvp = rv (RT)α+β 式中R = 0.08314 m3 bar/(kmol K)
第六章 固定床

水力半径
• 湿周---在总流的有效截面上,流体与固体壁面的接 触长度称为湿周,用字母L表示。
• 水力半径---总流的有效截面积A和湿周L之比。用字
母RH表示
RH = A / L
44
• 对于圆形截面的管道,其几何直径用水力半径表示 时可表示为
• A=(1/4)×πd2 • L=πd • 则 R=A/L=(1/4)×d → d = 4 R
当ReM>1000 湍流, 局部阻力损失为主, f≈1.75 , 略去第一项
结论: 对ΔP影响最大的是ε和u
49
Pf L
'(duSm 2 )(1B3B)
f ' 1501.75 ReM
一般床压不宜超过床内压力的15%,所以颗粒不 能太细,应做成圆球状。
50
➢ 压降的计算 ΔP=ΔP1+ ΔP2
= 15fu 0 OG L 0(1)21.75fuO 2 G L 0(1)
dS 2
3
dS
3
Pa
式中混合物的粘度
1
yi
fi M
2 i
f
1
yiM
2 i
kg/m.s
51
6.3 固定床中的传热
传热包括: 粒内传热,颗粒与流体间的传热,床层与器壁的传热
给热系数 αP 给热系数αW ,λer 总给热系数α t
当单纯作为换热装置时,以床层的平均温度tm与 管壁温差为推动力-----总给热系数αt
n
算术平均直径: d xWidi i1
调和平均直径:
1 n xWi
d
d i1 i
几何平均直径:
di
didi
30
6.2.3 床层空隙率及分布
生物接触氧化法固定床与流化床比较

生物接触氧化法固定床与流化床比较
1、固定床一般用弹性填料,半软性填料,比表面积只有100-180m3/m2;流化床用立体柱状空心填料,比表面积可达到1000 m3/m2。
2、固定床填料更换麻烦,需更换支架,要固定安装;流化床填料更换简单,只需从柱修孔加入即可。
3、固定床填料寿命一般只有2-3年;流化床立体柱状空心填料寿命在10年以上。
4、固定床填料生物相单一,水力停留时间长;流化床填料集硝化与反硝化于一体,生物相集中,处理效率高,水力停留时间短。
5、固定床设备体积大,占地多,投资高;流化床设备体积小,占地少,投资省。
6、陶粒每二年增加10%,生物炭每二年增加5%。
7、系统剩余污泥一般为3-6个月抽吸一次,具体时间根据实际定。
江苏鹏鹞集团有限公司
吴彩莉
2002年1月31日
北京西二旗创业者家园污水排放标准
江苏鹏鹞集团有限公司
吴彩莉
2002年1月31日。
化工基础实验 固定床和流化床实验

• 防止指示液冲出,如流量过猛或过大也易造成指示液冲 出。
13
五、实验结果整理
• 定流速与压降和高度的关系,并仔细观察实验现象,将 数据和现象详细记录。下表可供记录参考:
流体流量计
这种床层称为流化床,如图(c)、(d)所示。
• 流化床阶段,每一个空塔速度对应一个相应的床层空隙 率,流体的流速增加,空隙率也增大,但流体的实际流 速总是保持颗粒的沉降速度μt不变,且原则上流化床有 一个明显的上界面。
C、颗粒输送阶段
• 当立体在床层中的实际流速超过颗粒的沉降速度μt时, 流化床的上界面消失,颗粒将虚浮在流体中并被带出器
固定床和流化床实验
2021/7/22
1
预习复习系统
• 实验目的 • 实验原理 • 实验装置图 • 注意事项 • 实验结果整理 • 实验报告内容 • 思考题
2
一、实验目的
•
观察固定床与流化床的总体性状;
•
观察固定床向流化床转变的过程及流化现象;
•
观察液固系统与气固系统流态化的差异;
•
测定两系统的流化关系曲线即(∆P~w曲线);
外,如图(e)所示。
6
此时,实现了固体颗粒的气力或液力输送,相应的床 层称为相输送床层。
2、两种不同流化形式 A、散式流化 • 散式流化状态的特点:固体颗粒均匀的分散在流化介
质中,故称均匀流化。当流速增大时,床层逐渐膨胀 而没有气泡产生,颗粒彼此分开,颗粒间的平均距离 或床层中各处的空隙率均匀增大,床层高度上升,并 有一稳定的上界面。通常两相密度差小的系统趋向散 式流化,故大多数液—固流化属于“散式流化”。
化工基础实验 固定床和流化床实验

流化床压力与气速的关系
log
固定床
流化床
带出开始
C
B
A
D
A 起始流化速度
带出速度
logu
图 3-28 流化床压力降与气速关系
三、实验装置图
图2 气固系统流程图 1.鼓风机 2.孔板流量计 3.孔板压差计 4. 压差计 5.床身 6.接收管 7.旋风分离器 8.按钮开关
图2 液固系统流程图 1. 旋液分离器 2. 接收器 3.床身 4. 压差计 5. 孔板压差计 6.水槽 7.水泵 8. 孔板流量计 9. 按钮开关
ቤተ መጻሕፍቲ ባይዱ
B、 聚式流化
对于密度差较大的系统,则趋向于另一种流化 形式——聚式流化。例如,在密度差较大的 气—固系统的流化床中,超过流化所需最小气 量的那部分气体以气泡形式通过颗粒层,上升 至床层上界面时即行破裂。在这些气泡内可能 夹带有少量固体颗粒。这时床层内分为两相, 一相是空隙小而固体浓度大的气固均匀混合物 构成的连续相,称为乳化相;另一相则是夹带 有少量固体颗粒而以气泡形式通过床层的不连 续相,称为气泡相。由于气泡在上界面处破裂, 所以上界面是以某种频率上下波动的不稳定界 面,床层压强降也随之作相应的波动。
实验装置
四、注意事项
在全部的操作中,流量调节是关键,要求流量调节要缓 慢,由其是在临界流化点附近要更加缓慢,做出流化曲 线的全部过程,至少要做15—20个点左右,点并均匀分 布。
由于实验完毕后,床层颗粒的孔隙率增大,为了使下一 次实验数据准确性好些,用手轻轻拍一下床体,使固体 的孔隙率减小,床层高度为实验前原有的高度。
本实验室装置为二维床。便于观察现象。但固体颗粒回 收到床内,并不十分方便。所以操作中注意流量调节不 要过猛,防止颗粒带出。
流化床反应器的操作与控制—流化床反应器的工艺计算

A组分总消失量 dCAb dt
dl dt
dCAb dl
ub
dCAb dl
流化床反应器内的传热
流化床反应器具有温度分布均匀和传热速率高的特点,特别适于产生大量反 应热的化学反应,同时换热器的传热面积可以减小,结构更紧凑。
传热的三种基本形式:
• 固体颗粒与固体颗粒之间的传热 • 固体颗粒与流体间的传热 • 床层与器壁或换热器表面的传热
这三种传热的基本形式中,前两种传热速度比后一种要大得多,所以要提 高整个流化床的传热速度,关键就在于提高后一种传热速度。
1.844 102 C 1
Re0.23
Pr 0.43
CP P
CP
0.8
P
0.66
0.43
• 注意: 是有单位的,其单位为[s.cm-2]
• 床层与横放的换热器器壁之间传热时,给热系数计
算式为
Nu
0.66 Re0.44
Pr 0.3
P
1
0.44
流化床传热小结
• 水平管的给热系数比垂直管低5-15%,因此倾向 于使用垂直管。
• u:气流的空塔流速[m.s-1]
可见,流化床的内径取决于气流的空塔气速,而流化床的空塔气速应介
于初始流化速度(也称临界流化速度)与逸出速度之间。即维持流化状态的最 低气速与最高气速之间。
例8-1 计算萘氧化制苯酐的微球硅胶钒催化剂的起始流化 速度和逸出速度
已知催化剂粒度分布如下:
目 >1 100 80- 60 40 < 数 20 - 10 - - 4
d p gumf
2
反应器选型与设计
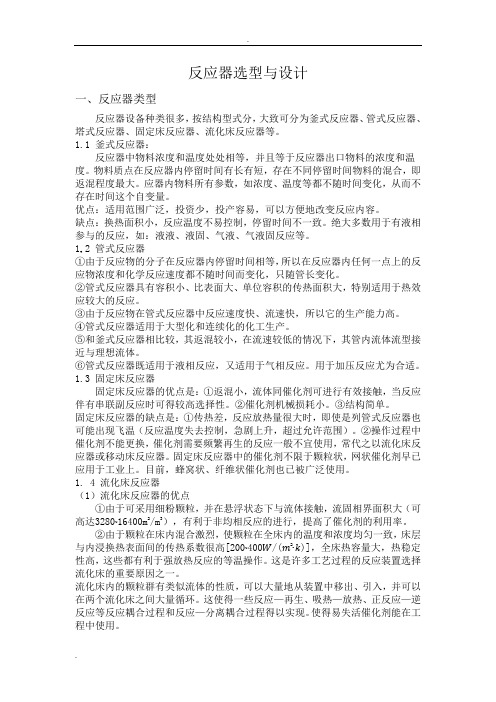
反应器选型与设计一、反应器类型反应器设备种类很多,按结构型式分,大致可分为釜式反应器、管式反应器、塔式反应器、固定床反应器、流化床反应器等。
1.1釜式反应器:反应器中物料浓度和温度处处相等,并且等于反应器出口物料的浓度和温度。
物料质点在反应器内停留时间有长有短,存在不同停留时间物料的混合,即返混程度最大。
应器内物料所有参数,如浓度、温度等都不随时间变化,从而不存在时间这个自变量。
优点:适用范围广泛,投资少,投产容易,可以方便地改变反应内容。
缺点:换热面积小,反应温度不易控制,停留时间不一致。
绝大多数用于有液相参与的反应,如:液液、液固、气液、气液固反应等。
1.2 管式反应器①由于反应物的分子在反应器内停留时间相等,所以在反应器内任何一点上的反应物浓度和化学反应速度都不随时间而变化,只随管长变化。
②管式反应器具有容积小、比表面大、单位容积的传热面积大,特别适用于热效应较大的反应。
③由于反应物在管式反应器中反应速度快、流速快,所以它的生产能力高。
④管式反应器适用于大型化和连续化的化工生产。
⑤和釜式反应器相比较,其返混较小,在流速较低的情况下,其管内流体流型接近与理想流体。
⑥管式反应器既适用于液相反应,又适用于气相反应。
用于加压反应尤为合适。
1.3 固定床反应器固定床反应器的优点是:①返混小,流体同催化剂可进行有效接触,当反应伴有串联副反应时可得较高选择性。
②催化剂机械损耗小。
③结构简单。
固定床反应器的缺点是:①传热差,反应放热量很大时,即使是列管式反应器也可能出现飞温(反应温度失去控制,急剧上升,超过允许范围)。
②操作过程中催化剂不能更换,催化剂需要频繁再生的反应一般不宜使用,常代之以流化床反应器或移动床反应器。
固定床反应器中的催化剂不限于颗粒状,网状催化剂早已应用于工业上。
目前,蜂窝状、纤维状催化剂也已被广泛使用。
1. 4 流化床反应器(1)流化床反应器的优点①由于可采用细粉颗粒,并在悬浮状态下与流体接触,流固相界面积大(可16400m2/m3),有利于非均相反应的进行,提高了催化剂的利用率。
应用化工技术专业《流化床反应器结构尺寸及反应器压力降的计算》
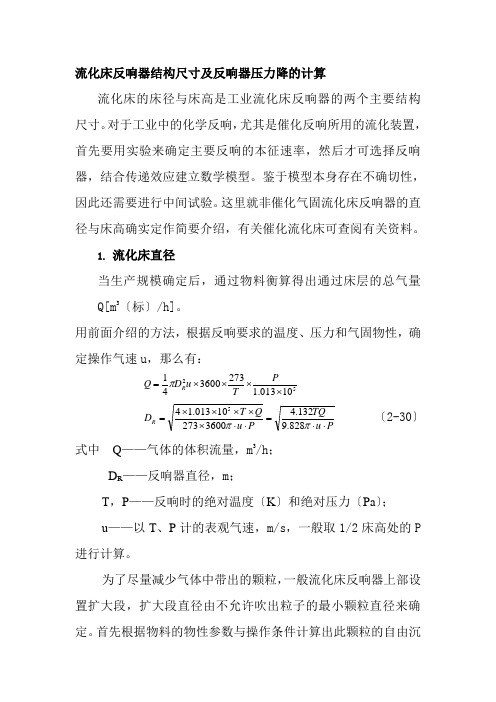
流化床反响器结构尺寸及反响器压力降的计算流化床的床径与床高是工业流化床反响器的两个主要结构尺寸。
对于工业中的化学反响,尤其是催化反响所用的流化装置,首先要用实验来确定主要反响的本征速率,然后才可选择反响器,结合传递效应建立数学模型。
鉴于模型本身存在不确切性,因此还需要进行中间试验。
这里就非催化气固流化床反响器的直径与床高确实定作简要介绍,有关催化流化床可查阅有关资料。
1. 流化床直径当生产规模确定后,通过物料衡算得出通过床层的总气量Q[m 3〔标〕/h]。
用前面介绍的方法,根据反响要求的温度、压力和气固物性,确定操作气速u ,那么有:5210013.1273360041⨯⨯⨯⨯=P T u D Q R π P u TQ P u Q T D R ⋅⋅=⋅⋅⨯⨯⨯⨯⨯=ππ828.9132.4360027310013.145 〔2-30〕式中 Q ——气体的体积流量,m 3/h ;D R ——反响器直径,m ;T ,P ——反响时的绝对温度〔K 〕和绝对压力〔Pa 〕; u ——以T 、P 计的表观气速,m/s ,一般取1/2床高处的P 进行计算。
为了尽量减少气体中带出的颗粒,一般流化床反响器上部设置扩大段,扩大段直径由不允许吹出粒子的最小颗粒直径来确定。
首先根据物料的物性参数与操作条件计算出此颗粒的自由沉降速度,然后按下式计算出扩大段直径L D 。
013.12733600412P T u D Q t L ⋅⋅⋅⋅=π P u TQD t L ⨯⨯⨯=π828.9013.14〔2-31〕2.流化床床高一台完整的流化床反响器高度包括流化床高度、扩大段高度和别离高度。
而流化床高又包括临界流化床高mf L ,流化床高f L 与别离段高度D L 。
临界流化床高mf L ,也称静止床高D L 。
对于一定的流化床直径和操作气速,必须有一定的静止床高。
对于生产过程,可根据产量要求算出固体颗粒的进料量W P 〔kg/h 〕,然后根据要求的接触时间τ〔h 〕,求出固体物料在反响器内的装载量M 〔kg 〕,继而求出临界流化床时的床高mf L 。
- 1、下载文档前请自行甄别文档内容的完整性,平台不提供额外的编辑、内容补充、找答案等附加服务。
- 2、"仅部分预览"的文档,不可在线预览部分如存在完整性等问题,可反馈申请退款(可完整预览的文档不适用该条件!)。
- 3、如文档侵犯您的权益,请联系客服反馈,我们会尽快为您处理(人工客服工作时间:9:00-18:30)。
碳四馏分选择性加氢反应器一般采用绝热固定床反应器。在工程上要确定反
应器的几何尺寸,首先得确定出一定生产能力下所需的催化剂容积,再根据高
径比确定反应器几何尺寸。
反应器的设计主要依据试验结果和技术要求确定的参数, 催化剂床层和液体分布板等进行计算和设计。
1.设计参数
反应器进口温度:20C
进口压力:O.IMPa
进料量(含氢气进料组分)
体积流量:197.8m3/h
质量流量:3951kg/h
液相体积空速:400h-1
2.催化剂床层设计计算
正常状态下反应器总进料量为2040nVh液体体积空速400h-1
则催化剂用量VRV总/SV2040/4005.1m3
催化剂堆密度b850kg/m3
催化剂质量mBBVR8505.1kg 4335kg
因此,圆整可得反应器内径可以选择1200mm
此时’床层高度L0翠3.1采4-512m
反应器选型
表4-1和表4-2为反应器类型。
表4-1固定床反应器类型比较
反应器
优点
缺点
备注
绝热固定床
反应器结构简单,
反应过程中温
主要用于热效应
反应器单位体积内 催化剂量大,生产 能力大。
度变化大。
不大的反应。
自热式固定
求取最适宜的反应器直径D:
设不同D时,其中高径比一般取2-10,设计反应器时,为了尽可能避免径向的 影响,取反应器的长径比5,则算出反应器的直径和高度为:按正常进料量2040m3/ h
及液体空速400h-1,计算反应器的诸参数:
取床层高度L=5m则截面积SVr/L5.1/51.02m2
床层直径D, 4S~.4一1.02/3.14 1.140m
Hale Waihona Puke 度分布合理,能是 反应接近最佳温度 曲线进行,产能大,
转化率咼。
总结
比较三种固定床的优缺点以及结合本工艺特点选用绝
热固定床反应器。
、流化床反应器设计
1.1
(1)具有适宜的流体力学条件,流动性能好,有利于热量传递和质量传递;
(2)合理的结构,能有效的加速反应和水的脱除;
(3)保证压力和温度符合操作条件;
以原料气作为冷却
反应器结构复
主要用于热效应
床
剂来冷却床层,易
杂造价高,只
不咼的咼压反应
维持床层在一定的
温度分布。
适合用于放热
反应。
过程。
多段绝热式固定
床层之间设置气体
传热较差。
适合各种宽热效
床
的冷却装置,有效 的减小了床内的温 度变化,有较咼的 反应速率。反应器 结构简单,能容纳 较多的催化剂,温
应反应。
4.2.2.1操作气速
(1) 起始流化速度Umf的确定
流化床出口流量:V129667 m3/h
4.2.2工艺计算
当流体流过颗粒床层的阻力等于床层颗粒重量时,床层中的颗粒开始流动起来,此时流
体的流速称为起始流化速度,记作Umf。起始流化速度仅与流体和颗粒的物性有关,其计
算公式如下式所示:
pl I I
对于Repp mf1000的大颗粒
由于C4裂解反应需要较长的接触时间,故流化床的操作线速不必太高
炔烃液相选择加氢固定床床反应器设计计算
由于固定床反应器具有结构简单、操作方便、操作弹性大、建设投资低等优点,而
广泛应用于各类油品催化加氢裂化及精制、低碳烃类选择加氢精制等领域。将碳四馏分 液相加氢新工艺就是采用单台固定床绝热反应器进行催化选择加氢脱除碳四馏分中的乙 基乙炔和乙烯基乙炔等。在工业装置中,由于实际所采用的流速足够高,流体与催化剂 颗粒间的温差和浓差,除少数强放热反应外,都可忽略。对于固定床反应器来讲最重要 的是处理好床层中的传热和催化剂粒子内扩散传质的影响。
1.3
1.基本参数:
催化剂颗粒密度:P1500kg/m3
催化剂堆密度:b700kg/m3
催化剂平均粒径:dp0.12m 1.2104m(属于B区粒子)
混合气体粘度:2.0 10-5Pa.s
反应温度:T=550°C
反应压力:P= 0.2MPa
C4处理流量:m°30584m/h
混合气体密度:m0/V030584/175051.75 kg/m3
(4)操作稳定,调节方便,能适应各种操作条件的变化。
1.2
以Superflex工艺为依托,以C4为原料,以ZSM-5分子筛为催化剂活性组分,通过流 化床反应器,将C4转换为乙烯、丙烯产品。其特点是在2个独立的流化床反应器(区)中分别进行(乙烯和丁烯歧化反应)过程,产物汇总后进入分离系统,乙烯、丙烯产品出装 置,C4及C4以上组分循环返回反应器继续转化G及以上组分两股物流在返回烯烃转化反应 区之前有少量驰放,以免惰性组分积累。催化剂顺次通过反应器,经汽提后进入再生器烧 焦,再生催化剂连续返回反应器以实现连续反应-再生。