快速反应程序qsb
QSB+快速反应流程
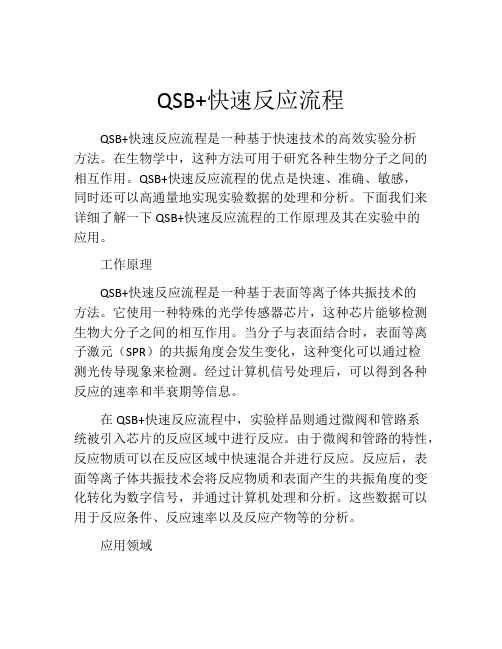
QSB+快速反应流程QSB+快速反应流程是一种基于快速技术的高效实验分析方法。
在生物学中,这种方法可用于研究各种生物分子之间的相互作用。
QSB+快速反应流程的优点是快速、准确、敏感,同时还可以高通量地实现实验数据的处理和分析。
下面我们来详细了解一下QSB+快速反应流程的工作原理及其在实验中的应用。
工作原理QSB+快速反应流程是一种基于表面等离子体共振技术的方法。
它使用一种特殊的光学传感器芯片,这种芯片能够检测生物大分子之间的相互作用。
当分子与表面结合时,表面等离子激元(SPR)的共振角度会发生变化,这种变化可以通过检测光传导现象来检测。
经过计算机信号处理后,可以得到各种反应的速率和半衰期等信息。
在QSB+快速反应流程中,实验样品则通过微阀和管路系统被引入芯片的反应区域中进行反应。
由于微阀和管路的特性,反应物质可以在反应区域中快速混合并进行反应。
反应后,表面等离子体共振技术会将反应物质和表面产生的共振角度的变化转化为数字信号,并通过计算机处理和分析。
这些数据可以用于反应条件、反应速率以及反应产物等的分析。
应用领域QSB+快速反应流程在生物学研究中发挥着重要的作用。
它不仅可以用于研究蛋白质和核酸之间的相互作用,也可以研究生物膜、细胞和受体之间的交互作用等。
具体应用领域包括:蛋白质-蛋白质相互作用研究。
QSB+快速反应流程可以用于研究蛋白质间的相互作用,包括蛋白质复合物的结构和稳定性以及相互作用动力学等。
蛋白质-核酸反应研究。
QSB+快速反应流程可以用于研究蛋白质和核酸之间的相互作用,包括RNA合成和修复等。
受体激活研究。
QSB+快速反应流程可以用于研究受体激活过程中,受体和配体之间的相互作用,以及反应动力学及其与下游信号转导通路之间的关系。
分子诊断和药物筛选。
QSB+快速反应流程可以用于鉴定和筛选与慢性疾病相关的受体,以及对这些受体进行高通量的药物筛选。
总结QSB+快速反应流程是一种基于表面等离子体共振技术的高效实验分析方法。
快速反应程序:解决质量问题的反应模式

(Example)
OPERATION:
STEP NO.
Standardized Operations Worksheet And Layout标准化操作工作表和布局
WORK ELEMENT
FROM:___________________________
QUANTITY PER SHIFT:______________
TO: _____________________________
SHIFT:________
ELEMENT TIME
HAND WORK MACHINE WALK
STANDARD INPROCESS STOCK
Q
QUALITY
CHECK
CUSTOMER CYCLE TIME:________________
•用目视管理方法建立统一的识别程序
• (Example) 用明亮色彩作为首选的识别方法
✓ ✓✓✓-
红色=废品 黄色=可疑品 绿色=合格品
废品
可疑品或待处 理品
标签内容
标签内容
IN THIS SECTION IN THIS SECTION
IS AT LOCAL
IS AT LOCAL
DISCRETION
DISCRETION
PLT001
红标签表示废品。
PLT002
黄色标签表示可疑产品或待 处理的材料,需要返工的材 料或需要进一步检查的材料
半成品或合格 品
标签内容 IN THIS SECTION
IS AT LOCAL DISCRETION
PLT003
绿色或其他颜色的标签表示产品是可 接受的 (红色和黄色除外). .
TOTAL
QSB 快速反应程序

November 2006 Revision 2006年11月版 年 月版
This presentation was developed by General Motors Corporation Worldwide Purchasing. All rights reserved. No part of this material may be reproduced in any form, or by any method, for any purpose, without written permission of General Motors Worldwide Purchasing.
Contam
SCM
QSB WORKSHOP REV. 111406
10
General Motors Corporation. All rights reserved.
问 题 解 决
什么是"问题" 什么是"问题"?
所谓问题,就是当前状态和客户满意之间的差距
FR&PS
NCM
VS
LPA
EPV
WPO
SWI (SOS)
(例)
PFMEA / 控制计划更新 标准化作业指导书 标准化作业指导书/ 操作员指导书
根本原因分析
验证纠正措施
序号
1 2
问题描述
Material Contam inated Burrs Parts m islocated on assem bly Mixed Parts
开始日 期
1/10/2005 2/15/2005
成长
FR&PS NCM VS LPA EPV WPO SWI (SOS) OI (JES) SOT(JIT) Risk Reduct Contam SCM
QSB快速反应流程

QSB快速反应流程快速反应流程(QSB,Quick Service Bulletin)是一种用于迅速处理问题和将解决方案迅速传达给相关人员的流程。
它旨在确保问题能够得到及时解决,以最小程度地对组织的正常运营造成干扰。
以下是一个包含超过1200字的QSB的标准流程:第一步:问题识别(Identification)快速反应流程的第一步是识别问题。
这可以通过多种方式进行,例如通过客户反馈、内部质量监控和检查、日常操作的异常情况等等。
一旦问题被发现,相关人员应该立即报告给负责的团队或部门。
第二步:问题分析(Analysis)第三步:解决方案开发(Solution Development)一旦问题的根本原因得到确认,团队需要制定相应的解决方案。
这通常涉及到制定一系列具体的步骤和行动计划,以修复问题并防止类似问题的再次发生。
解决方案应该是可操作和具体的,以便相关人员能够迅速理解并采取相应行动。
第四步:解决方案验证(Solution Validation)在制定解决方案之后,团队需要进行验证,以确保问题解决方案的有效性。
这可能包括验证方案的实施、测试解决方案的可行性,并确保它真正解决了问题。
如果验证过程中发现问题或需要进行进一步的调整,团队将返回前面的步骤进行修正。
第五步:解决方案发布(Solution Release)在解决方案被验证通过之后,团队需要将其传达给相关人员。
这可能包含编制发布公告、更新相关文件或培训相关人员。
目标是确保解决方案被传达给那些需要知道并实施它的人员。
第六步:问题解决(Problem Resolution)解决方案发布之后,团队需要跟踪问题是否得到解决。
这可以通过定期的监控和检查来实现。
如果发现问题仍未解决或出现新的问题,团队需要立即采取行动进行纠正。
第七步:总结和反馈(Summary and Feedback)在问题解决之后,团队应该进行总结和反馈。
这包括评估问题解决的效果、提取教训和经验,并在需要的情况下更新标准操作程序和其他相关文件。
QSB+检查表标准
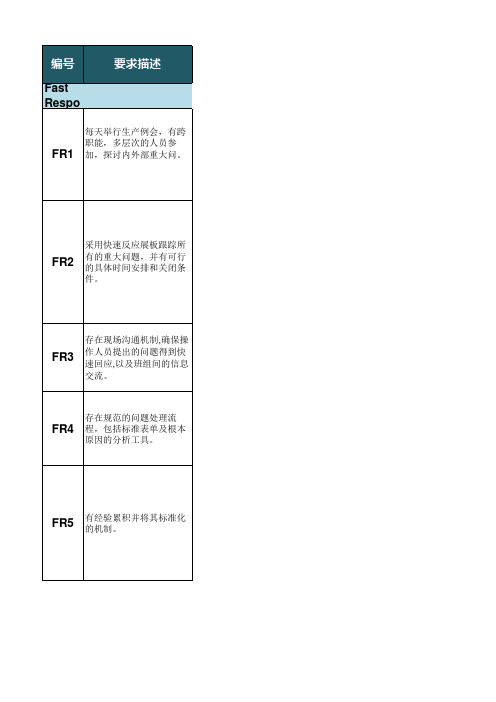
MC2
针对所有的产品/过程更改 实施风险分析。
MC3
有生产试运行(PTR)管 控流程。
MC4
建立实施库存规划策略/流 程,保证不断货。并考虑 到零件或材料的储藏期限 的限制。
定义并管应急工艺备案。
MC5 有相关的程序批准应急工
艺备案。
建立指标并跟踪,以确保
MCE 变更不会对客户造成影响
。
Maint enanc e 设备 维护
编号
Fast Respo
要求描述
每天举行生产例会,有跨 职能,多层次的人员参
FR1 加,探讨内外部重大问。
FR2
采用快速反应展板跟踪所 有的重大问题,并有可行 的具体时间安排和关闭条 件。
FR3
存在现场沟通机制,确保操 作人员提出的问题得到快 速回应,以及班组间的信息 交流。
存在规范的问题处理流
FR4 程,包括标准表单及根本
Layer ed Proce ss Audit 过程分 层审核
LPA1
建立普遍的分层审核机制 。
LPA2
分层审核覆盖所有的生产 领域,由生产部门实行。
与分层审核相关的行动计
LPA3
划得到实施和跟踪。偏差 得到处理。
持续监控分层审核的有效
LPAE
性。并通过分层审核的结 果分析,跟踪监控流程和
工艺文件的遵守。
MMFM1
有完整的体系来制定生产 计划,并对其进行定期评
审。
MMFM2
工厂制定详尽的日生产计 划并进行跟踪。
MMFM3
制约工艺得到识别及特殊 的跟踪管理。
生产包装材料(成品,在制
MMFM4
品和来料)的在库量和储存 条件得到跟踪管理,以确
QSB【快速反应】 介绍

风险降低 (RPN)
主动式风险降低
跨部门团队应该: • 执行定期PFMEA审查
• 在完成审查之后,建立最高(RPN)风险降低机会列表
• 制定一个行动计划(或类似计划)来跟踪降低RPN级别的 进展情况
Why RPN? Risk and Prioritization
It is important to give fair and spread-apart ratings
确定组织内合格的培训人员
合格的培训人员: • 利用标准化培训记录和培训柔性图表来指导操作员 • 监控新操作员的行为,并在必要时对其进行重新培训,以遵 守确保标准化操作 • 将潜在故障告诉下游操作部门
受训操作员跟踪表
确定哪些受训人员需要被追踪: • 操作名称 • 受训人员和培训完成日期 • 培训最新版本
7– LAYER PROCESS AUDITS 分层审核
8– RPN REDUCTION 风险降低
降低各类缺陷的风险
工艺更改 质量指示
程序流程
PFMEA
控制计划
作业指导
对作业人员 提供指导
降低 RPN
风险降低(RPN)
主动式和被动式策略以利用PFMEA减低质量风险 PFMEA
Quality Systems Basics 质量系统基础
Key Strategies 关键战略
质量系统基础
质量系统基础是通过10个关键策略以达到改进质 量的目的
10个关键策略的实施
• • • • •
利用系统化方式即刻大幅度降低运营成本 将组织由被动模式快速转变成主动模式 通过分层审核保持制造/装配的完整性 促进沟通 改进你的ISO/TS 16949 (QS-9000)质量体系
QSB
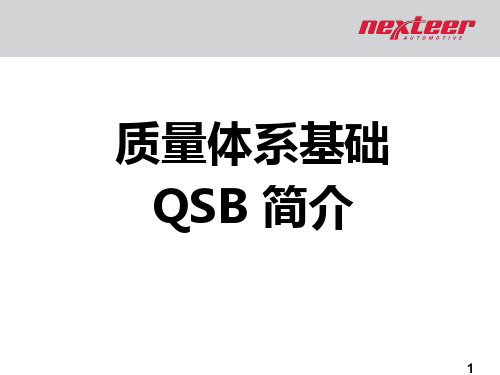
12
标准化作业的益处?
Without 没 有 Standardisation 标准作业 With 采 Standardisation 用标准作业
提供一个安全的工作环境
保持高质量水平 容易看到问到人力和设备的高利用率
13
标准化作业的三大模块
详细的动作步骤,怎样做, 为什么这样操 作。 操作主要步骤,每一步 骤所花时间 (平衡生产) 整洁、有序的工作 环境
29
10.0 供应链的管理
3级 供应商
2级 供应商
1级 供应商
Nexteer
OEM
客户热情
原材料 供应商
外协加工 服务
部件采购
供应链管理的目的:
提供一个管理整个供应链中各级供应商的标准化的程序。
您对供应商的期望是什么?
30
供应链管理要求
使用各种工具对其战略性分供方的特殊要求进行识别和 跟踪 开发一个衡量其所有分供方业绩的系统。包括对供应链各 级的评审 – QSB 审核,过程控制计划审核, PSA (潜在 供应商评审)等. 符合 ISO9001:2000 是达到目标的第一 步. 在供应链中交流 Nexteer 的期望和要求。使用管理工具, 如:对问题的反馈,业绩指标,供应活动的评审, 和问 题解决工具。 通过应用共同的原则,方法和系统来支持持续改善质量水 平, 降低PPM以及零件的故障产生的费用
维护保养的目的是什么?
目的: 保持各类设备在正常的工作条件下运行 提高设备的总运行效率 推动相关活动的风险管理 管理各种类型的维护保养 备品备件的管理
范围: 装配区域, 制造生产线, 维护区域, 所有生产区域
职责: 主管:设备维修经理 生产经理
QSB+评价标准及要求
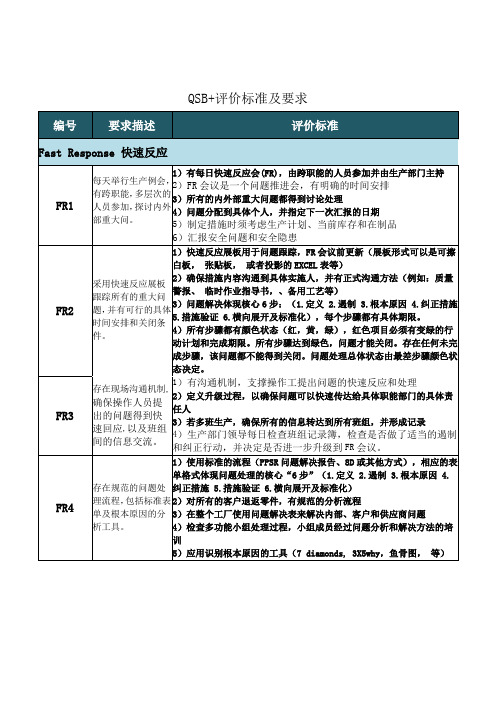
1)有工作场所的布局标准,包括内部存储和必要的缓冲区。
2)工作场所的组织合适,以确保FIFO,包括倒包装操作。
3)有管理工作场所组织(例如5S)的系统的方法并维护。
4)车间实施可视化管理
5)在工作场所的组织上,实施持续改进和优化/消除浪费
SW3
QSB+评价标准及要求
Fast Response快速反应
FR1
每天举行生产例会,有跨职能,多层次的人员参加,探讨内外部重大问。
1)有每日快速反应会(FR),由跨职能的人员参加并由生产部门主持
2)FR会议是一个问题推进会,有明确的时间安排
3)所有的内外部重大问题都得到讨论处理
4)问题分配到具体个人,并指定下一次汇报的日期
-满足客户需求的生产节奏和实际生产节拍
-在制品储存数量规定
-有安全防护要求,必须按要求配备个人安全防护装备
-尽量用图片、简图、照片描述
-产品/过程/控制标准的编号
5)对于每个操作文件,指南描述:
- 主要步骤(什么)
- 关键点(如何)
- 原因(为什么)
6)SWI张贴在操作工位上或附近
SW4
生产启动的流程是否得到定义和实施。
5)制定停止遏制行动的条件。
CNC5
返工或返修须标准化,只有获得批准后才能重新上线。
1)明确定义禁止和批准的返修操作。返工返修操作必须是零件/过程认可的一部分。待返修的零件必须视作可疑零件处理。
2)有关返工返修的失效模式须包含在PFMEA中,并在工艺流程中识别。零件重返生产线时要在移出工位或之前。
3)返工返修零件须得到识别,返回产线后须实施下游所有的检查,以确保完全实施控制计划中所有的检查&试验。
QSB-快速响应-070816

D7
在整个组织内进行教育 和形成制度
D8
总结表扬& 正式解散 团队
SDE Module 2007.08
SGM Confidential
19
7 颗钻石法
问题已被定义
开始调查
QSB-快速响应
负责人
用来判断生产是否严格 按照设计内容在运行。
是否需要开发支持?
负责人
生产部门 1
过程 是否正确? 是 工具/刀具 是否正确 是 零件 是否正确 是
SGM Confidential
11
QSB管理层必须通过目视的方式来展示质量状态 快速响应
可使用任何形式的目视方法: 如日历, 图表, 等
每日质量状态图
月份
年度
1月
2004
31 29 28 30
22 21 13 12 2 1 3 14 4 5 23 15
24 25 17 16 6 7
26 27 19 18 8 9 20 10 11
QSB-快速响应
是一个交流会,不是 一个问题解决会议, 可以是一个10-20分钟 的站立会议,在生产 现场或生产部门的会 议室召开
时间
形式
责任
是一个制造评审会议 ,由制造部门负责召 开,由质量、工程等 支持
6
SDE Module 2007.08
SGM Confidential
快速响应会议
在快速响应会议上,领导应该: - 指定每一个问题的责任人 - 确定责任人下次汇报的时间
QSB-快速响应
解
污 染 物
供 应 链
控 制
管 理
经
验
教
SDE Module 2007.08
SGM Confidential
QSB普及知识点

QSB普及知识点1、5W2HWhat(做什么)Why(为什么做)Who(谁)When(什么时候)Where(在哪里)How to do(什么程度)How many(How much)(多少钱)2、GP12和岗位验证的区别相同的都是100%全检。
区别GP12是永久的岗位验证是临时的只判别好坏具有报警功能月底统计立即响应持续改进问题解决每日审核零缺陷为目的前馈后馈看板目视化一、快速反应会议3、生产部的操作工是内部最大的顾客,因为他们是直接为有效产出服务的。
4、生产计划是内部最重要的流程5、提升公司整体的有效产出是最高目标6、日计划是最易把握的,昨/今日计划是最重要的计划7、生产计划做的是否好取决于6M。
人、机、料、法、环、测。
8、快速反应会议是沟通的会议,不是解决问题的会议,是站立的会议,不是坐着的会议,接近一线现场。
总目标是提升有效产出,以昨/今日生产计划为载体,是每日例会;时长30分钟,对着看板、目视化、会前展示信息状态,带好笔记本、报告、证据、样件、方法等。
由生产部老大主持。
由技术部、采购部、销售部、质量部、物流部、人力资源部、公司总经理等相关部门的一把手参加。
9、生产计划应包含返工返修生产计划;样件生产计划;量产件生产计划。
10、以生产计划完成的目标来区分优先等级。
11、根据优先等级又分短期问题和中长期问题。
12、快反会议场所应有生产计划看板;中场期问题看板和短期问题看板;Q图1+12月图;安全十字图;时钟;审核台;捐款箱;签到表;样件;报告;证据;数据;照片;投影;挂历;音响;有签名的会议规则。
13、问题的快速有效解决是快反会议的根本。
14、快反会议包含快反会议;有效问题解决;经验教训总结。
二、不合格品控制1、不合格品指的是不满足顾客要求的产品和材料。
2、顾客指的是法律法规;外部顾客;下道工序。
3、不合格品的4中表现形式:1、尺寸、性能、装配、标识、包装等不良。
2、可疑品(无标识、多标识、标识不清、新旧标识混用、标识破损、落地品)3、变质品(生锈、老化、氧化、变质)4、退回品3、不合格品的处置方法:报废;让步;返工返修;降级;退回;召回。
汽车行业QSB快速反应程序

快速反应程序1.术语:快速反应:通过每日例会加强沟通和管理,采用目视管理方法展示重要信息,使应对重大的内、外部质量问题的反应标准化。
问题解决:一个系统化的用来识别、分析和消除现状和现行标准或期望之间的差距,并预防根本原因再次发生的过程。
经验总结:利用成功经验,防止错误重复出现。
2.职责:(1)制造部负责快速反应会议,质量部,技术部,设备部等给予支持。
(2)问题负责人负责采用8D等方法、运用相应工具解决问题。
(3)各负责部门负责其相应经验教训活动,总经办负责文件归档和发布。
3.快速反应会议:3.1开会时间:每天一次,每次10~15分钟,会上只对质量问题进行沟通。
3.2开会地点:生产现场看板前或生产现场办公室。
3.3参会人员:所有部门(财务部外)的第一责任人,因故不在候补出席。
3.4会议主题:应对每天的具体重大质量问题。
3.5会议准备:每天质量部每天找出过去24小时发生的重大质量问题,开会前详细描述在白板上。
具体问题包括:(1)客户关注的问题;(2)供应商关注的问题;(3)停线(内部或外部);(4)重复发生的质量问题;(5)除调车废品以外班废品率超过综合废品率目标;(6)验证岗位中发现的问题;(7)分层审核中发现的问题;(8)其它内部质量问题。
3.6会议内容:(1)会议主席协调各方意见,确定新问题的责任人和关闭日期。
(2)旧问题负责人提交相关报告,报告具体进度,紧抓问题退出标准,由与会人员确认关闭。
(3)会议主席根据当天情况,标明具体问题和日Q图的状态。
3.7会后工作:问题负责人运用8D等方法、相关工具解决问题,总结形成报告。
3.8其他定期工作:快速反应跟踪表应记录所有产生的问题。
每月汇总公布问题发生数趋势图。
4解决问题:4.1采用8D问题解决流程:(1)D1选择团队:建立跨部门、跨学科的问题解决团队。
团队成员应具备有效解决问题所需的专业技能和权限。
(2)D2定义问题:描述具体问题与相关标准的差距和现状及持续的时限。
QSB+01快速反应

12
12
13
快速反应
快速反应跟踪板示例
看板可以是可擦白板, 张贴板, 或者投影的EXCEL表等
板可以不同但内容必须相符
14
快速反应
快速反应跟踪板
为优化目视化管理,看板形式运用于会议区(例,4’x 8’可擦白板,张贴板等)
回顾要点:责任归属、关闭条件、 总体状态、下次报告日期
ABC公司-质量快速反应跟踪板
s2
Contain The Problem 遏制问题
s4
Implement Permanent Corrective Actions 永久实施纠正措施
s5 s3
Identify The Cause 明确原因
Verify Effectiveness Of Actions 检查措施效果
s6
Institutionalize Throughout The Organization 组织内展开及标准化
4
快速反应
快速反应会查什么?
ITEM 要求 评价标准
FR1
1)有每日快速反应会 (FR),由跨职能的人员参加并由生产部 门主持 每天举行生产例会, 2)FR会议是一个问题推进会,有明确的时间安排 有跨职能,多层次 3)所有的内外部重大问题都得到讨论处理 的人员参加,探讨 4)问题分配到具体个人,并指定下一次汇报的日期 内外部重大问题 5)制定措施时须考虑生产计划、当前库存和在制品 6)汇报安全问题和安全隐患
35 D
Standard Work Operator Instructions
N/A
Forecasted Closed date
Customer Closed Date
Issue Description
1、QSB快速反应-A

FR
PS
NCP
VS
WPO
SWI (SOS)
OI(JES)
SOT(JIT)
EPV
LPA
Risk
Contam
SCM
MC
WS
5
快速反应 目录
1.0) 导言,目的 ,范围, 职责 1.1) 益处 1.2) 快速反应 • 问题识别,问题源 • 会议模式 • 职责 • 设计,模板,退出标准,状态 • 绩效指标 1.3) 问题解决 • 描述, 基本原则 • 问题解决的6个核心步骤 1.4) 经验教训 1.5) 总结,必须
现场管理 – 7种浪费 标准化作业指导书 – SOS 操作员指导书 – JES 检具标准化 (新增)
5. 6. 7. 8. 9. 10. 11.
标准化的操作员培训 – JIT 防错(装置)验证 分层审核 RPN 风险降低(增加逆向 PFMEA) 异物控制 供应链管理 变更管理 (新增战略)
Y G
N/A
快速反应会议签到表 白板两面的结构: 8 ½ x 11 2) 4’ x 8’ x ¾” 木板. 2) 48” 图表区 2) 4’ x 8’ x ¼” 有机玻璃 Quality Systems Basics rev March 2009
Global Purchasing and Supply Chain
FR
PS
NCP
VS
WPO
SWI (SOS)
OI(JES)
SOT(JIT)
EPV
LPA
Risk
Contam
SCM
MC
WS
14
快速反应跟踪板
(例)
为优化目视管理,将这个表格尽可能大的显示在会议区域( 如: 4’ x 8’ 可擦写 的白板 ) 推出标准
QSB+快速反应流程

1.目的为了及时的对内/外部顾客抱怨进行处理,及时对内部质量缺陷进行解决及总结经验,提升企业生产效率并最终达成提升企业有效产出之目的。
2.范围本程序适用于企业生产运作过程中所有表露出的内/外部问题。
3.术语和定义3.1快速反应会议是一个接近生产现场的、基于数据和目视化看板的沟通会议。
以生产计划(昨/今日)为关注节点,由生产部主管或更高级别管理人员进行主导、各部门主管及核心工程师参加的会议。
会议全程站立进行、保持在30分钟内。
3.2是以生产计划为主线并以提高组织有效产出为目标的会议。
3.3对过去24小时内发生的重大质量问题或事件进行检查,定义中长期问题和短期问题、应根据快速反应短期、中长期看板登入标准进行目视化管理。
3.4目的是提高信息共享、快速沟通决策并加以跟踪,从而提高团队沟通的有效性。
该会议的有效召开是基于问题的有效解决和经验总结的应用(横向展开等)避免后期问题重复发生。
3.5对分层审核、岗位验证发生的重大事件必须在会议上进行评审和跟踪。
3.6规定解决质量问题和时间的负责人、完成时间、汇报日期、跟踪方式等,建立快速反应系统。
3.7对分层审核、岗位验证发生的重大事件必须在会议上进行评审和跟踪。
3.8规定解决质量问题和事件的负责人、完成时间、回报日期、跟踪方式等,完善快速反应系统。
4.职责和要求4.1质量部负责快速反应流程开发、培训、维护、问题解决之验证等。
4.2公司级快速反应会议主持人一般由生产部部长或质量部部长担任,负责组织每日质量例会;必要时可做适当调整。
4.3与会人员需按时参加、不得迟到、早退、缺席;由会议主持人于会议上明确指定问题解决负责人、相关部门作为小组成员为其提供团队支持。
4.4参会部门及参会人员详见《快反会议参会人员名单》,快反会议规定应由各部门部长亲自参加。
如遇出差或其它客观原因不能按时出席时,应及时向会议主持者请假并委派其他人员代替参加,参会人员需每日会前五分钟进行《快反会议签到表》登记。
- 1、下载文档前请自行甄别文档内容的完整性,平台不提供额外的编辑、内容补充、找答案等附加服务。
- 2、"仅部分预览"的文档,不可在线预览部分如存在完整性等问题,可反馈申请退款(可完整预览的文档不适用该条件!)。
- 3、如文档侵犯您的权益,请联系客服反馈,我们会尽快为您处理(人工客服工作时间:9:00-18:30)。
通过每日的快速反应会议能促进沟通和知识分享,使用显示重要信息的目视化方法促进关闭,对重大的内、外部问题的反应标准化,从客户向上游传递问题鉴定,尽快解决内部问题。
2范围
公司级快速反应会设在底楼会议室,由质量部主持。
3引用文件
4术语
4.1快速反应:通过每日例会促进沟通和知识分享,使用显示重要信息的目视化方法促进关闭,对重大的内、外部质量问题的反应标准化,从客户向上游传递问题鉴定,尽快解决内部问题。
5快速反应会议在装配车间、油漆车间、注塑车间由生产车间主任牵头;在质量审核区由质量主管牵头。
5.1开会时间:每天一次,每次 10~20分钟,会上只对质量和安全问题进行沟通。
5.2开会地点:生产现场看板前和质量部产品审核区。
5.3支持部门:由质量、工程、维护部门和支持人员。
5.4会议主题:应对产生的具体重大质量问题和跟踪未关问题的处理沟通。
5.5会议准备:每天各车间和质量部找出过去 24 小时发生的重大质量问题,开会前详细描述在看板上。
具体问题包括:
(1)客户关注的问题;
(2)健康与安全问题(所有安全相关事件,如事故、侥幸末发生的事故);
(3)停线(导致内部停线达 30 分以上的或外部);
(4)重复发生的质量问题和防错装置故障;(生产班次连续或累计发现同一缺陷达 3 个以上的)
( 5)生产问题(生产计划和实际产量,如班废品率超过废品率目标;影响向用
户发送)
(6)验证岗位中发现的问题;(进货、过程、产品审核发现的问题)
(7)分层审核中发现的体系问题;
(8)其它内部质量问题(出货审核、遏制行动)。
6解决问题:
6.1 采用 8D 问题解决流程:
(1) D1选择团队:建立跨部门、跨学科的问题解决团队。
团队成员应具备有效解决问题所需的专业技能和权限。
(2)D2 定义问题:描述具体问题与相关标准的差距和现状及持续的时限。
同时,描述工程师或专家的意见。
(3)D3遏制:制定临时措施以防止问题在客户端发生.
(4)D4 识别根本原因:列出所有导致问题发生的事件,使用系统性的方法来识别和验证其中的根本原因。
(5)D5长期纠正措施:制定并实施长期的纠正措施以彻底解决冋题。
(6) D6验证措施是否有效:从4个方面验证:根本原因,临时措施,长期措施,问题的预防。
(7) D7预防问题的重复发生:防止那些导致问题发生的变化出现,即零件,过程和系统的变化。
(8) D8团队庆祝:应认可和表扬团队及团队每位成员的努力和贡献。
6.2 分析解决问题的工具和方法:
(1) 7钻法
1~4 钻:通过检查过程、工具、零件是否正确,零件质量是否符合要求等,来评定过程的稳定性。
5~6 钻:评定设计的合理性;此时解决问题通常需要考虑工艺更改,甚至产品更
改。
通常对于GM产品而言,要和GM的质量工程师或产品工程师联系。
7钻:对于极端复杂的问题,必须采用统计工程才能解决。
(2)柏拉图(又称:排列图、ABC图、主次因素排列图)
基于“关键的少数,次要的多数”的柏拉法则,采用ABC3类分析方
法,累计在 80%左右的问题和因素,即为主要问题或影响质量的主要因素
(3)鱼骨图(又称:因果图,特性要因图)定义:一种能一目了然的表示结果(特性)与(影响特性的要因)原因之影响情形或两者间关系之图形。
目的:通过图形的绘制来展开影响结果的各种原因,并以此为基础寻求主要原因。
适应范围:品质纠正、预防和改善过程中均适应。
展开类型:可按五大要素、工序项
目、原因罗列进行展开。
(4)直方图(又称:频数分布图)定义:用横坐标标注质量特性的测量值的分组值,纵坐标标注频数值,各组的频数用直方柱的高度表示,这样就作出了直方图。
目的:显示数据的波动状态;直观地传达有关过程情况的信息;决定在何处集中力量进行改进。
适应范围:一般用于数据整理,调查工序能力,研究质量分布。
(5)运行图(又称:推移图,趋势图,分析用控制图)
定义:一种随着时间的移动,将设定工作推动的项目,结合设定的指标而将实绩在成果绘制在图上,以观察实际的成果与设定指标的差距,以便采取调整措施的一种图表。
目的:改变了一般报表在文字上的体现,并且也弥补了一般报表不容易查觉到随时间的变动所呈现结果的变化起伏状况。
适应范围:日常管理工作;研究质量数据可控制幅度。
(6)离散图(又称:散布图,相关图,相关分析图)定义:一种通过采集两个变量相关一组原始数据后,在坐标系描出点,并从点的分布趋势中进行线性分析的图表。
目的:通过相关分析能找到两个变量的相互关系,为分析品质问题提供便利,从而查出问题的本质之所在。
适应范围:计量型数据分析。
7 经验总结经验教训适用于所有的岗位,公司每个人都应参与经验教训总结的过程。
通过下列内容
相关的活动展开经验总结(括号内为负责部门):
(1)每月的质量Q图(质量部)
(2)分层审核(制造部)
(3)防错装置验证(设计部、工艺部)
(4)内外部质量问题(质量部)
(5)验证岗位(质量部)
(6)顾客满意度总结与评估(质量部)
(7)A PQP程序执行(项目部)
(8)持续改进小组活动(质量部)
(9)(顾客抱怨,风险降低)问题解决和报告(质量部、工艺部)
(10)合理化建议项目(行政人事部)
以上活动的负责部门应建立一个经验教训档案,每月更新公布经验教训清单。
8会议流程
9记录
骨口,
序号 名称
编号
1 《快速响应跟踪表》
2 《每日质量状态图》
2 《8D 报告》
3 《遏制表》
4 《分层审核报告》
5 1
《FMEA'CP
6
《冋题分析报告》
10流程图
公司级指标」
关闭
二级供应商管理襖
关闭
关;可的标;企
按严重瓷和舐童分类
*巧程婕、就誉、壽&灶冋題,
问题的分级
快逢商应—r
问题的通报
*问题分析工具
逼制
不合格品握:制模块
分*斤74皆迄反蟻“
实施
实施
防端和工艺欖块
正卤位模块
客户反镭.停线
问题的分解
标准化操作。