基于CAE的书立注塑模设计及成型工艺优化
基于cae分析的塑件产品注射成型浇注系统优化设计
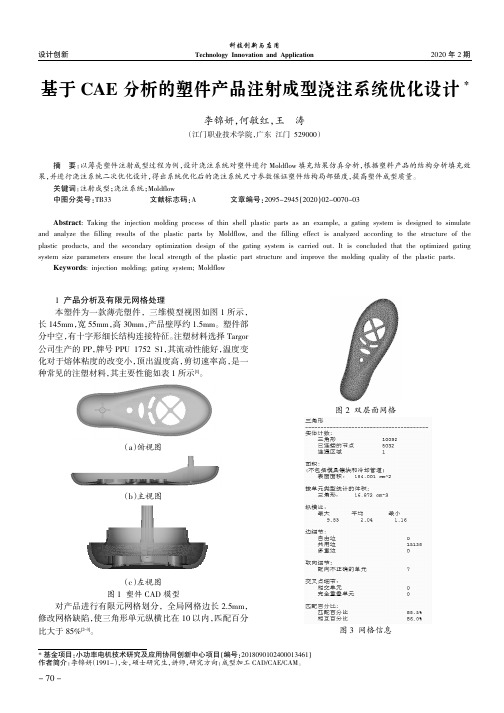
2020年2期设计创新科技创新与应用Technology Innovation andApplication基于CAE 分析的塑件产品注射成型浇注系统优化设计*李锦妍,何敏红,王涛(江门职业技术学院,广东江门529000)1产品分析及有限元网格处理本塑件为一款薄壳塑件,三维模型视图如图1所示,长145mm ,宽55mm ,高30mm ,产品壁厚约1.5mm 。
塑件部分中空,有十字形细长结构连接特征。
注塑材料选择Targor 公司生产的PP ,牌号PPU 1752S1,其流动性能好,温度变化对于熔体粘度的改变小,顶出温度高,剪切速率高,是一种常见的注塑材料,其主要性能如表1所示[1]。
(a )俯视图(b )主视图(c )左视图图1塑件CAD 模型对产品进行有限元网格划分,全局网格边长2.5mm ,修改网格缺陷,使三角形单元纵横比在10以内,匹配百分比大于85%[2-3]。
图2双层面网格图3网格信息摘要:以薄壳塑件注射成型过程为例,设计浇注系统对塑件进行Moldflow 填充结果仿真分析,根据塑料产品的结构分析填充效果,并进行浇注系统二次优化设计,得出系统优化后的浇注系统尺寸参数保证塑件结构局部强度,提高塑件成型质量。
关键词:注射成型;浇注系统;Moldflow中图分类号:TB33文献标志码:A文章编号:2095-2945(2020)02-0070-03Abstract :Taking the injection molding process of thin shell plastic parts as an example,a gating system is designed to simulateand analyze the filling results of the plastic parts by Moldflow,and the filling effect is analyzed according to the structure of the plastic products,and the secondary optimization design of the gating system is carried out.It is concluded that the optimized gating system size parameters ensure the local strength of the plastic part structure and improve the molding quality of the plastic parts.Keywords :injection molding;gating system;Moldflow*基金项目:小功率电机技术研究及应用协同创新中心项目(编号:2018090102400013461)作者简介:李锦妍(1991-),女,硕士研究生,讲师,研究方向:成型加工CAD/CAE/CAM。
基于cae的pp塑料件注射成型工艺参数的影响及优化
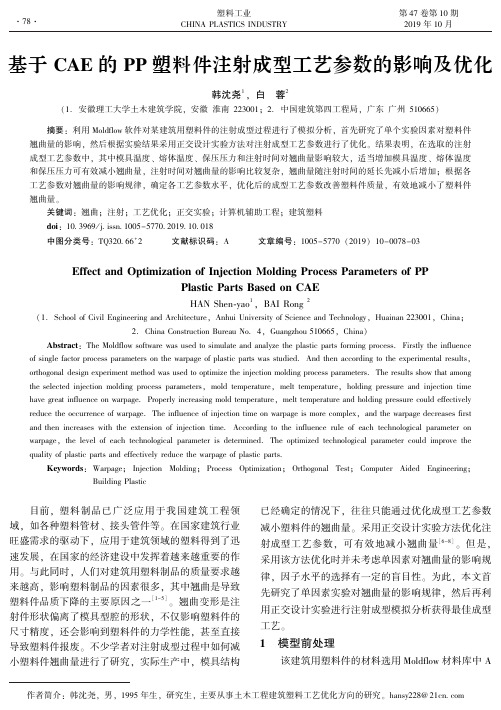
翘曲量的影响ꎬ 然后根据实验结果采用正交设计实验方法对注射成型工艺参数进行了优化ꎮ 结果表明ꎬ 在选取的注射
成型工艺参数中ꎬ 其中模具温度、 熔体温度、 保压压力和注射时间对翘曲量影响较大ꎬ 适当增加模具温度、 熔体温度
Plastic Parts Based on CAE
HAN Shen ̄yao1 ꎬ BAI Rong
2
(1. School of Civil Engineering and Architectureꎬ Anhui University of Science and Technologyꎬ Huainan 223001ꎬ Chinaꎻ
第 47 卷第 10 期
2019 年 10 月
塑料工业
CHINA PLASTICS INDUSTRY
78
基于 CAE 的 PP 塑料件注射成型工艺参数的影响及优化
韩沈尧1 ꎬ 白 蓉2
(1. 安徽理工大学土木建筑学院ꎬ 安徽 淮南 223001ꎻ 2. 中国建筑第四工程局ꎬ 广东 广州 510665)
域ꎬ 如各种塑料பைடு நூலகம்材、 接头管件等ꎮ 在国家建筑行业
减小塑料件的翘曲量ꎮ 采用正交设计实验方法优化注
旺盛需求的驱动下ꎬ 应用于建筑领域的塑料得到了迅
射成型工艺参数ꎬ 可有效地减小翘曲量 [6-8] ꎮ 但是ꎬ
速发展ꎬ 在国家的经济建设中发挥着越来越重要的作
用ꎮ 与此同时ꎬ 人们对建筑用塑料制品的质量要求越
the selected injection molding process parametersꎬ mold temperatureꎬ melt temperatureꎬ holding pressure and injection time
基于CAE技术的注塑模具高效率设计方法

基于CAE技术的注塑模具高效率设计方法newmakerCAE系统的核心思想是结构的离散化,即将实际结构离散为有限数目的规则单元组合体。
实际结构的物理性能可以通过对离散体进行分析,得出满足工程精度的近似结果来替代对实际结构的分析,这样可以解决很多实际工程需要解决而理论分析又无法解决的复杂问题。
把CAE理论应用于塑料模具的设计,预测模具结构及注射工艺参数对制品外现和性能的影响,有目的地修正设计方案和工艺条件,克服因为经验少而造成的不良后果,进而优化注塑模具结构设计。
实践证明此项研究明显的缩短了设计周期,提高了设计效率,保证了产品质量,降低了模具的设计成本,因此此项研究具有广阔的研究前景和开发空间。
1 传统注塑模具设计流程传统注塑模具设计流程是典型的串行路线,在正式生产前,由设计人员凭经验与直觉设计模具,模具装配完毕后,需要通过试模才能发现问题。
发现问题后从概念设计、产品设计、模具设计、模具制造到试模进行调整,之后才能进行模具生产。
设计、调整及模具质量很大程度取决于设计人员的经验。
此方案设计周期长,模具质量不稳定,产品质量难以保证。
2 基于CAE技术的塑料模具设计流程基于CAE技术的塑料模具设计流程如图2所示,和传统的模具设计流程不同,这种设计生产流程是典型的并行路线。
基于CAE技术模具设计流程利用CAE分析软件,可以在模具制造之前,先在计算机上对整个注塑成型过程进行模拟分析,准确预测熔体的填充、保压、冷却以及制品中的应力分布、分子和纤维取向分布、制品的收缩和翘曲变形等情况,从而使设计者能够模拟调整工艺参数,优化工艺规程,尽早发现并解决绝大教问题,及时修改制品和模具结构设计,而不是等到试模以后再返修模具,在设计阶段以最小的花费、最短的时间优化设计,缩短开发周期,提高设计效率、保证模具设计质量。
3 注塑模具CAE基本结构及设计过程3.1 注塑模具CAE基本结构基本过程是将一个形状复杂的连续体的求解区域分解为有限的形状简单的子区域,即将一个连续体简化为由有限个单元组合的等效组合体:通过将连续体离散化,把求解连续体的场变量(应力、位移、压力和温度等)问题简化为求解有限的单元节点上的场变量值此时得到的基本方程是一个代数方程组,而不是原来描述真实连续体场变量的微分方程组。
基于CAE分析注射模具结构的优化设计
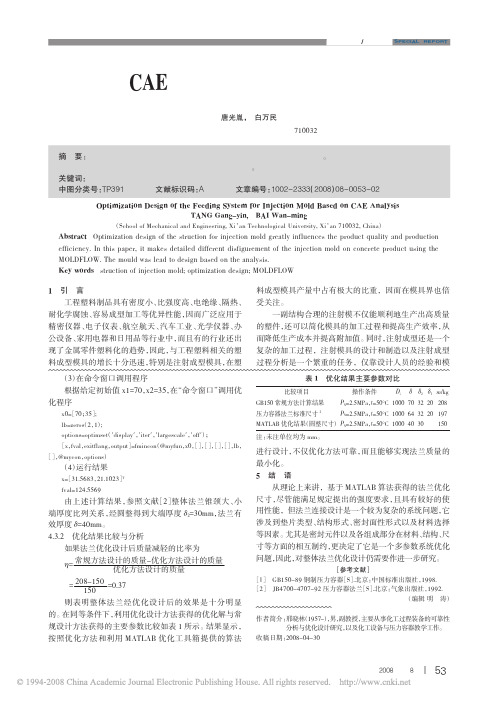
!!!!!!!!!!!!!!!!!!!!!!!!!!!!!!!!!!!!!!!!!!!!!!!!!!!!!!!!!!!!!!!!!!!注:未注单位均为mm 。
表1优化结果主要参数对比比较项目GB150常规方法计算结果压力容器法兰标准尺寸[2]MATLAB 优化结果(圆整尺寸)操作条件P N =2.5MPa ,t =50°C P N =2.5MPa ,t =50°C P N =2.5MPa ,t =50°C D i 100010001000δ706440δ2323230δ12020m /kg208197150(3)在命令窗口调用程序根据给定初始值x1=70,x2=35,在“命令窗口”调用优化程序x0=[70;35];lb=zeros (2,1);options=optimset(′display ′,′iter ′,′largescale ′,′off ′);[x ,fval ,exitflang ,output ]=fmincon (@myfun ,x0,[],[],[],[],lb ,[],@mycon ,options )(4)运行结果x=[31.5683,21.1023]T fval=124.5569由上述计算结果,参照文献[2]整体法兰锥颈大、小端厚度比列关系,经圆整得到大端厚度δ2=30mm ,法兰有效厚度δ=40mm 。
4.3.2优化结果比较与分析如果法兰优化设计后质量减轻的比率为浊=常规方法设计的质量-优化方法设计的质量=208-150150=0.37则表明整体法兰经优化设计后的效果是十分明显的。
在同等条件下,利用优化设计方法获得的优化解与常规设计方法获得的主要参数比较如表1所示。
结果显示,按照优化方法和利用MATLAB 优化工具箱提供的算法进行设计,不仅优化方法可靠,而且能够实现法兰质量的最小化。
5结语从理论上来讲,基于MATLAB 算法获得的法兰优化尺寸,尽管能满足规定提出的强度要求,且具有较好的使用性能,但法兰连接设计是一个较为复杂的系统问题,它涉及到垫片类型、结构形式、密封面性形式以及材料选择等因素。
基于CAE技术的注塑模具设计

基于CAE技术的注塑模具设计Moldflow 软件可以模拟整个注塑过程,指导模具设计,并可优化塑料制品结构设计。
Moldflow软件技术可以提供基本的热塑性注塑成型分析功能外,以及许多新的注塑成型工艺分析。
近年来,Moldflow 软件在家电、汽车、电子通信、化工及日用品等领域都等到了广泛的应用。
下面我们以Moldflow 为例,来介绍注塑成型 CAE 软件的主要应用分析功能模块。
(一)进行产品优化产品优化顾问是快速检查塑料零件设计的生产能力的理想工具。
用户可以获得有关修改壁厚、浇口位置、材料或几何体的快速反溃分析结果和详细的设计建议可以用于最合理的零件壁厚和浇口位置,并可用于识别和消除装饰等问题,如熔接痕、气穴和缩水。
(二)进行产品的填充和保压分析填充和保压分析是所有 CAE 软件中最基本的分析功能,可以模拟注塑成型工程的填充和保压阶段。
它的分析输出结果包括填充时间、温度、压力、锁模力、剪切速率/应力、气穴和熔接痕等,有助于选择浇口位置、确定浇口数量和优化浇注系统,并可预测熔接位置、最终填充位置/排气位置,以及填充时间、压力和温度分布,确定和潜在的塑料制品质量缺陷。
(三)进行产品的曲俏分析翘曲变形分析是在设计阶段完成制品尺寸的预测,并可预测制品的使用性能,验证模具结构和注塑工艺参数是否合理。
它的主要分析输出结果包括变形量和应力等,可帮助用户找出翘曲变形成因,提高制品的尺寸精度,为用户提供有用的参考数据,并优化制品的结构参数。
二、利用CAE技术进行模具注塑的应用现状利用CAE进行模具注塑,在国外已经有着非常悠久的应用历史,在上个世纪50年代,美国研究学者通过数值计算的方法。
将聚合物不断的优化和设计,改善了注塑工艺。
到了上个世纪80年代,CAE注塑技术已经比较成熟,由于有限元法和边界元法的出现,使得CAE在注塑模具领域有着非常广泛的应用。
澳大利亚,美国以及德国分别研发了相应的软件,进行CAE的注塑工作。
基于CAE的轿车零件注射模具优化设计

第39卷第1期2011年1月塑料工业C H I N AP L A S T I C S I ND U S T R Y作者简介:钱应平,男,工学博士,副教授,湖北工业大学机械学院,专长:模具C A D /C A E /C A M ,快速制造。
q i a n y p 98@163.c o m 。
基于C A E 的轿车零件注射模具优化设计钱应平1,黄菊华2,周细枝1,者凌秋1(1.湖北工业大学机械工程学院,湖北武汉430068;2.湖北工业大学土木与建筑工程学院,湖北武汉430068) 摘要:以汽车零件为研究对象,利用C A E 技术及注塑模具C A D 技术,借助M o l d f l o w 和P R O /E 软件,建立了产品的三维实体模型,在产品的结构工艺性和成型性分析的基础上,进行了产品成型过程的模拟分析,获得了优化的成型方案和参数,并利用P R O E /E 模块E M X 进行了模具结构的三维优化设计。
关键词:计算机辅助工程;注塑模具;优化设计中图分类号:T Q 320.66+2 文献标识码:B 文章编号:1005-5770(2011)01-0065-04O p t i m i z a t i o nD e s i g n o f I n j e c t i o nMo u l d o f C a r P a r t s B a s e do n C A EQ I A NY i n g -p i n g 1,H U A N GJ u -h u a 2,Z H O UX i -z h i 1,Z H EL i n g -q i u1(1.S c h o o l o f M e c h a n i c a l E n g i n e e r i n g ,H u b e i U n i v e r s i t y o f T e c h n o l o g y ,W u h a n 430068,C h i n a ;2.S c h o o l o f C i v i l a n d A r c h i t e c t u r a l E n g i n e e r i n g ,H u b e i U n i v e r s i t y o f T e c h n o l o g y ,Wu h a n 430068,C h i n a )A b s t r a c t :I n t h i s p a p e r ,t h e c a r p a r t w a s u s e d a s s t u d y o b j e c t ,t h e C A Ea n d i n j e c t i o n m o l d C A Dt e c h -n o l o g y w e r e u s e d ,a n d t h e t h r e e d i m e n s i o nm o d e l o f p r o d u c t w a s e s t a b l i s h e d b y t h e M o l d f l o wa n dP R O /E .T h e o p t i m i z e d m o l d i n g m e t h o d s a n d p a r a m e t e r s w e r e o b t a i n e db a s e d o n t h e a n a l y s i s o f s t r u c t u r e p r o c e s s a n dm o l d i n g c h a r a c t e r i s t i c s a n d t h e t h r e e d i m e n s i o n o p t i m i z i n g d e s i g n o f m o u l d s t r u c t u r e w a s f i n i s h e d b y u s i n g t h e E M Xm o d u l e i n P R O /E .K e y w o r d s :C A E ;I n j e c t i o n M o l d ;O p t i m i z a t i o n D e s i g n1 塑料件的结构及工艺分析1.1 塑件结构分析轿车零件的示意图如图1。
基于CAE和DOE技术的注射成型工艺优化

基于C AE和DOE技术的注射成型工艺优化黄松王喜顺(华南理工大学机械与汽车工程学院,广州510640)摘要以打印机上盖为例,以体积收缩率、翘曲量和沉降斑指数为考察指标,结合CAE和DOE技术研究了模具温度、熔体温度、注射时间、保压压力和保压时间五个工艺参数对考察指标的影响,用DOE软件回归拟合得到体积收缩率、翘曲和沉降斑指数的预测模型,并运用该模型求解最佳的工艺参数,通过试验验证了该方法的可行性。
关键词注射成型CAE DOE工艺参数优化随着塑料工业的飞速发展,许多企业使用C AE 技术对注射成型过程进行模拟分析并预测潜在的问题,以提高一次试模率,达到降低生产成本、缩短生产周期的目的。
成型工艺参数的优化设置在一定范围内能克服成型缺陷,提高制品质量。
但影响制品质量的工艺参数比较多,而且各参数之间存在非线性和强耦合特性,设计师往往需要花费大量的时间进行C AE模拟才能获得合适的参数组合。
为了获得最佳的工艺参数组合,众多学者对此进行了研究, G.H.Choi等[1]应用ANN技术建立工艺参数和制品质量指标之间的神经网络关系模型,并采用自适应优化算法优化工艺参数。
郑晓培等[2]结合CAE和Taguch i技术研究了工艺参数对(丙烯晴/丁二烯/苯乙烯)共聚物、高密度聚乙烯和聚丙烯注塑制品沉降斑的影响,并对工艺参数进行了优化。
H.Okte m 等[3]基于田口试验方法、信噪比及均方差分析等方法,利用三水平的L27和L9等正交试验表,以最大翘曲量和最大体积收缩率为目标,对薄壳塑料制品的注射成型参数进行了优化设计。
钟浩东等[4]提出一个利用注射成型软件Mol d fl o w与遗传算法结合对熔接痕长度和位置进行优化的方法,经过多代搜索,最终获得对应于熔接痕长度与位置最佳的注射时间、熔体温度、模具温度、浇口位置等工艺参数。
D OE技术是一种研究试验数据的获得和科学地分析处理试验数据与结果的方法。
回归分析是其常用的数据分析方法,回归分析的主要内容为:¹从一组数据出发确定某些变量之间的定量关系式,即建立数学模型并估计其中的未知参数。
利用CAE技术进行注塑制品模拟分析及工艺优化
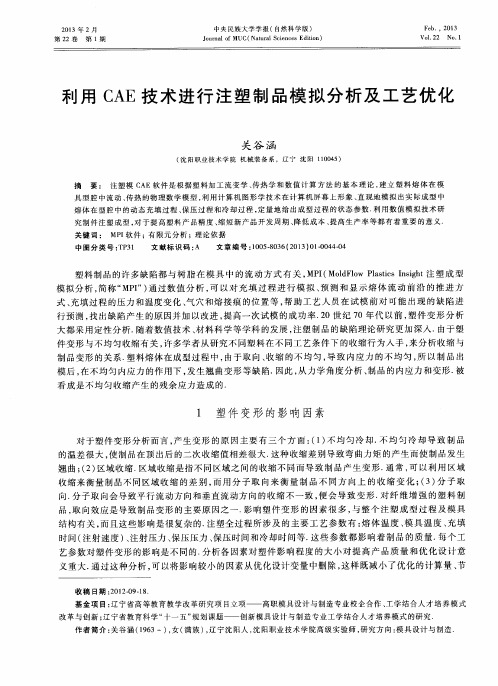
具型腔中流动、 传 热 的物 理 数 学 模 型 , 利 用 计 算 机 图形 学 技 术 在 计 算 机 屏 幕 上 形 象 、 直 观地 模 拟 出实 际成 型 中
熔 体 在 型 腔 中的 动 态 充 填 过 程 、 保压过程和冷却过程 , 定 量 地 给 出成 型 过 程 的状 态 参 数 . 利 用数 值 模 拟技 术 研 究制件注塑成型 , 对 于提 高 塑 料 产 品精 度 、 缩 短 新 产 品 开 发周 期 、 降低成本 、 提 高 生 产 率 等 都 有 着 重 要 的意 义 .
时间( 注 射速 度 ) 、 注 射压 力 、 保 压压力 、 保 压时 间和冷 却时 间等 . 这些 参 数都 影 响着 制 品 的质量 . 每 个 工 艺 参数对 塑件 变形 的影 响是不 同的. 分析 各 因素对 塑件 影 响程 度 的大小 对 提 高产 品 质量 和 优化 设 计 意 义 重大 . 通过 这种分 析 , 可 以将影 响较小 的 因素从优 化设 计变量 中删 除 , 这 样既 减小 了优化 的计 算量 、 节
2 0 1 3年 2月
中央 民族 大 学 学 报 (自然 科 学 版 )
J o u r n a l o f MU C( N a t u r a l S c i e n c e s E d i t i o n )
F e b. ,2 01 3
V0 I _ 2 2 NO . 1
关键词 : MP I 软件 ; 有限元分析 ; 理 论 依 据 中 图分 类 号 : T P 3 1 文献标识码 : A 文章 编 号 : 1 0 0 5 — 8 0 3 6 ( 2 0 1 3 ) 0 1 - 0 0 4 4 - 0 4
塑料制 品 的许多 缺陷都 与 树脂 在 模 具 中的 流 动方 式 有 关 , MP I ( Mo l d F l o w P l a s t i c s I n s i g h t 注 塑成 型 模拟 分析 , 简称 “ MP I ” ) 通 过数 值 分 析 , 可 以对 充 填 过程 进 行 模 拟 、 预 测 和显 示 熔 体 流 动前 沿 的 推 进方 式、 充填 过程 的压力 和温 度变化 、 气 穴和熔 接痕 的位 置等 , 帮 助工 艺人 员 在试 模 前对 可能 出现 的缺 陷进 行 预测 , 找 出缺 陷产 生 的原 因并 加 以改进 , 提高 一次试 模 的成 功率 . 2 0世纪 7 0年代 以前 , 塑件 变形 分 析 大 都采 用定性 分 析. 随着 数值技 术 、 材料科 学 等学科 的发展 , 注 塑制 品的缺 陷理 论研究 更加 深入 . 由于塑 件 变形 与不 均匀 收缩有关 , 许 多学 者从研 究不 同塑 料在 不 同工 艺条 件下 的收缩 行为 人手 , 来分 析收 缩与 制 品变 形 的关系 . 塑料熔 体 在成型 过程 中 , 由于取 向 、 收缩 的不 均 匀 , 导 致 内应 力 的不 均匀 , 所 以制 品 出 模后 , 在不 均匀 内应力 的作 用下 , 发生翘 曲变 形等 缺陷 . 因此 , 从力 学角 度分析 、 制 品 的内应力 和变 形. 被 看成 是不 均匀 收缩产 生 的残余应 力造 成 的.
浅谈基于CAE的注塑模具结构优化设计

浅谈基于CAE的注塑模具结构优化设计摘要:为进一步缩短模具研发周期,管控模具成本,切实提升模具的实用性,使其满足经济发展与社会生活的需求。
相关企业在研发以及生产环节,逐步转换思路,投入大量资源,进行技术升级,以技术优化模具产业的优化。
文章以CAE技术作为研究框架,从多个角度出发,探讨注塑模具结构优化的基本方法,旨在为后续相关实践活动的开展提供方向性引导。
关键词:注塑模具;CAE技术;结构优化;技术方案前言作为技术密集型产业,模具工业在日常研发、设计、生产以及评估过程中,需要CAD技术、CAE技术以及CAM技术的深度参与,在相关专业技术的支持下,降低模具研发以及生产难度,缩短模具研发与优化周期,减少了成本投入,对于模具产业的发展产生了深远影响。
CAE技术在模具工业中的应用,改变了传统了模具研发体系以及优化方式,促进了模具工业的现代化、可视化与智能化。
为进一步发挥CAE技术在注塑模具中的作用,实现模具结构的合理优化,文章在对CAE技术进行整体性分析的基础上,结合过往有益经验,系统梳理CAE技术框架下注塑模具结构优化的基本方法,着眼于相关案例,进行技术规律的总结,以期为CAE技术应用以及注塑模具结构优化活动的进行创造条件。
1.CAE技术概述对CAE技术的整体性梳理,有助于技术人员对该项技术的机理、重要性形成正确的认知,并在这一过程中,逐步明确CAE技术相关应用要求,在很大程度上,确保了CAE技术在注塑模具结构优化中科学高效应用。
CAE技术作为一种高效的分析方法,其在计算机平台之上,快速完成对复杂工业产品结构强度、产品刚度、稳定性、动力响应以及热传导性等相关参数的科学计算以及整体分析,是现阶段较为成熟的分析机制[1]。
随着技术的发展,CAE技术日益成熟,现阶段CAE技术大致上可以划分为两类,一类为专用CAE技术软件,主要针对于特定类型的建筑工程或者工业产品,用于分析、预测以及优化性能;另一类为通用CAE技术软件,主要服务于一般类型建筑工程以及工业产品,对其进行分析、预测以及优化。
基于cae注射成型工艺参数的优化
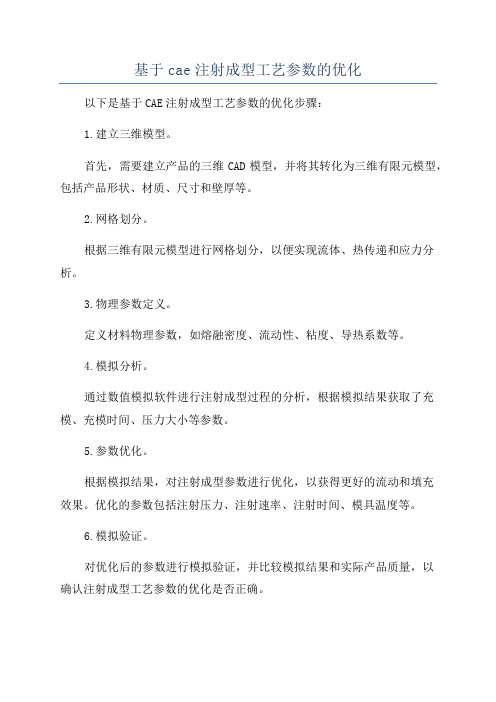
基于cae注射成型工艺参数的优化
以下是基于CAE注射成型工艺参数的优化步骤:
1.建立三维模型。
首先,需要建立产品的三维CAD模型,并将其转化为三维有限元模型,包括产品形状、材质、尺寸和壁厚等。
2.网格划分。
根据三维有限元模型进行网格划分,以便实现流体、热传递和应力分析。
3.物理参数定义。
定义材料物理参数,如熔融密度、流动性、粘度、导热系数等。
4.模拟分析。
通过数值模拟软件进行注射成型过程的分析,根据模拟结果获取了充模、充模时间、压力大小等参数。
5.参数优化。
根据模拟结果,对注射成型参数进行优化,以获得更好的流动和填充
效果。
优化的参数包括注射压力、注射速率、注射时间、模具温度等。
6.模拟验证。
对优化后的参数进行模拟验证,并比较模拟结果和实际产品质量,以
确认注射成型工艺参数的优化是否正确。
通过以上步骤,基于CAE注射成型工艺参数的优化可以显著提高产品的质量,并降低成本和制造周期。
基于CAE技术注射模冷却系统的优化设计
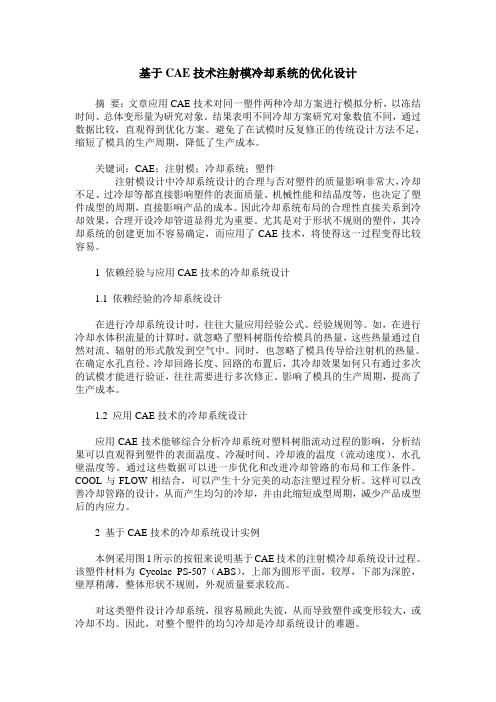
基于CAE技术注射模冷却系统的优化设计摘要:文章应用CAE技术对同一塑件两种冷却方案进行模拟分析,以冻结时间、总体变形量为研究对象。
结果表明不同冷却方案研究对象数值不同,通过数据比较,直观得到优化方案。
避免了在试模时反复修正的传统设计方法不足,缩短了模具的生产周期,降低了生产成本。
关键词:CAE;注射模;冷却系统;塑件注射模设计中冷却系统设计的合理与否对塑件的质量影响非常大,冷却不足、过冷却等都直接影响塑件的表面质量、机械性能和结晶度等,也决定了塑件成型的周期,直接影响产品的成本。
因此冷却系统布局的合理性直接关系到冷却效果,合理开设冷却管道显得尤为重要。
尤其是对于形状不规则的塑件,其冷却系统的创建更加不容易确定,而应用了CAE技术,将使得这一过程变得比较容易。
1 依赖经验与应用CAE技术的冷却系统设计1.1 依赖经验的冷却系统设计在进行冷却系统设计时,往往大量应用经验公式、经验规则等。
如,在进行冷却水体积流量的计算时,就忽略了塑料树脂传给模具的热量,这些热量通过自然对流、辐射的形式散发到空气中。
同时,也忽略了模具传导给注射机的热量。
在确定水孔直径、冷却回路长度、回路的布置后,其冷却效果如何只有通过多次的试模才能进行验证,往往需要进行多次修正。
影响了模具的生产周期,提高了生产成本。
1.2 应用CAE技术的冷却系统设计应用CAE技术能够综合分析冷却系统对塑料树脂流动过程的影响,分析结果可以直观得到塑件的表面温度、冷凝时间、冷却液的温度(流动速度)、水孔壁温度等。
通过这些数据可以进一步优化和改进冷却管路的布局和工作条件。
COOL与FLOW相结合,可以产生十分完美的动态注塑过程分析。
这样可以改善冷却管路的设计,从而产生均匀的冷却,并由此缩短成型周期,减少产品成型后的内应力。
2 基于CAE技术的冷却系统设计实例本例采用图1所示的按钮来说明基于CAE技术的注射模冷却系统设计过程。
该塑件材料为Cycolac PS-507(ABS),上部为圆形平面,较厚,下部为深腔,壁厚稍薄,整体形状不规则,外观质量要求较高。
基于注塑模具CAE技术的浇注系统和冷却系统优化方案设计
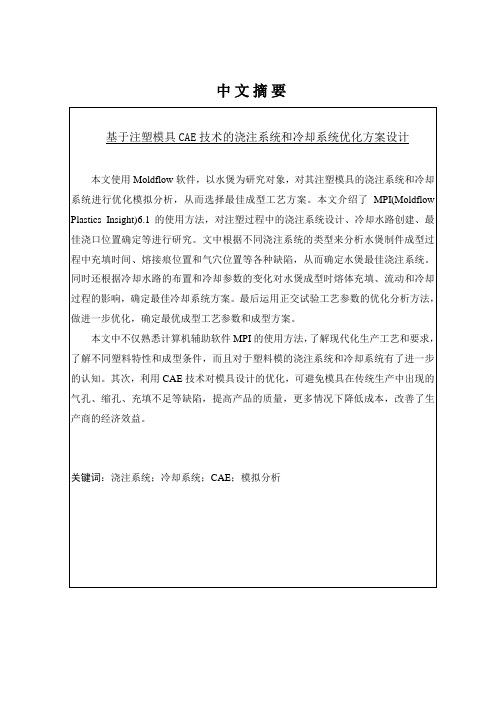
中文摘要基于注塑模具CAE技术的浇注系统和冷却系统优化方案设计本文使用Moldflow软件,以水煲为研究对象,对其注塑模具的浇注系统和冷却系统进行优化模拟分析,从而选择最佳成型工艺方案。
本文介绍了MPI(Moldflow Plastics Insight)6.1的使用方法,对注塑过程中的浇注系统设计、冷却水路创建、最佳浇口位置确定等进行研究。
文中根据不同浇注系统的类型来分析水煲制件成型过程中充填时间、熔接痕位置和气穴位置等各种缺陷,从而确定水煲最佳浇注系统。
同时还根据冷却水路的布置和冷却参数的变化对水煲成型时熔体充填、流动和冷却过程的影响,确定最佳冷却系统方案。
最后运用正交试验工艺参数的优化分析方法,做进一步优化,确定最优成型工艺参数和成型方案。
本文中不仅熟悉计算机辅助软件MPI的使用方法,了解现代化生产工艺和要求,了解不同塑料特性和成型条件,而且对于塑料模的浇注系统和冷却系统有了进一步的认知。
其次,利用CAE技术对模具设计的优化,可避免模具在传统生产中出现的气孔、缩孔、充填不足等缺陷,提高产品的质量,更多情况下降低成本,改善了生产商的经济效益。
关键词:浇注系统;冷却系统;CAE;模拟分析毕业设计说明书(论文)外文摘要Title Design Of Gating System And The Cooling System Based OnThe Technology Of Injection Mold CAEAbstract:This paper use Moldflow software to research the gating system of injection mould and cooling system optimization and simulation analysis for select the best molding process.This paper introduces the use of the MPI (Moldflow Plastics Insight) 6.1, the gating system of injection molding process design, cooling water to create, and the optimal gate location, etc.In this paper, according to different types of gating system to analysis the fill time in the process of stamping shape water boil, various defects such as weld mark and acupuncture point location, the best gating system to determine the water pot.Also according to the change of the arrangement of the cooling water and cooling parameters of molding melt filling water boil, the effect of flow and cooling process, determine the optimal cooling system solutions.Finally USES the method of orthogonal test process to produce several optimization analysis, further optimization, optimal molding process parameters and forming scheme.Keywords: Gating System; The Cooling System.CAE;Simulation Analysis目录前言 (1)第一章绪论 (2)1.1 注塑成型技术简介 (2)1.2 注塑模CAE技术 (2)1.2.1 CAE技术发展水平 (2)1.2.2 注塑模CAE技术发展趋势 (3)1.3 本文研究的目的和内容 (3)1.3.1 研究目的 (3)1.3.2 研究内容 (4)第二章注塑成型工艺方案设计 (5)2.1 浇注系统设计 (5)2.1.1 普通浇注系统的组成和设计 (5)2.1.2 主流道设计 (6)2.1.3 分流道设计 (6)2.1.4 浇口的设计 (7)2.1.5 水煲浇注系统设计 (9)2.2 冷却系统设计 (11)2.2.1 冷却水路布置 (11)2.2.2 常见冷却系统的结构 (11)2.2.3 水煲冷却水路的方案设计 (12)第三章基于MPI的注塑工艺CAE模拟仿真过程 (15)3.1 Moldflow软件简介 (15)3.2 水煲CAE仿真模拟分析 (15)3.2.1 产品模型导入 (15)3.2.2 网格的划分及修复 (16)3.2.3 最佳浇口位置的确定 (21)3.2.4 浇注系统创建 (22)I3.2.5 冷却系统创建 (24)3.2.6 分析序列选择 (26)3.2.7 注塑原料选择 (27)3.2.8 工艺参数设置 (27)3.2.9 分析计算 (28)第四章注塑成型模拟结果分析 (29)4.1 模拟结果分析 (29)4.2 水煲模拟分析结果比较 (30)4.2.1 浇注系统的分析比较 (30)4.2.2 冷却系统的分析比较 (33)4.3 水煲成型方案确定 (36)第五章基于正交试验工艺参数优化分析 (37)5.1 正交试验简述 (37)5.1.1 概述 (37)5.1.2 水煲的试验指标和因子 (37)5.2 数值模拟与正交试验方法结合的多工艺参数优化 (39)5.2.1 基于正交试验的多工艺参数优 (39)5.2.2 单个因素影响的试验 (42)第六章结论 (47)参考文献 (48)致谢 (49)附录 (50)II前言塑料成型在现代制造业中占有重要的地位,塑料制品随现代生活的变化而变的样式各异、绚丽多彩,因而对于成型塑料件的模具要求越来越高。
基于CAE的注塑模开发技术研究
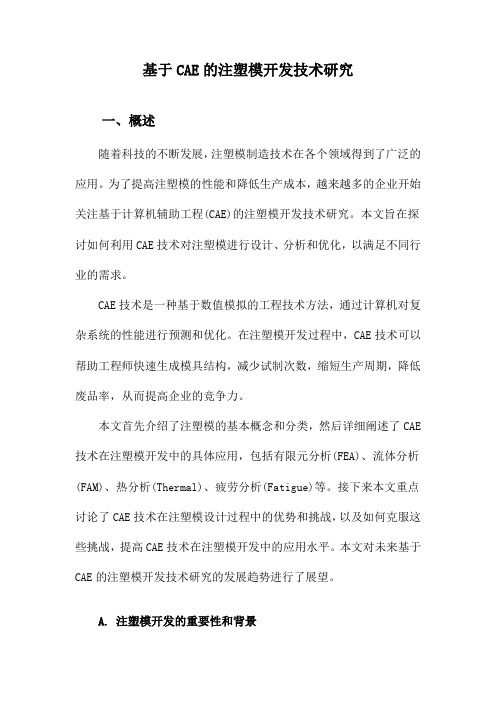
基于CAE的注塑模开发技术研究一、概述随着科技的不断发展,注塑模制造技术在各个领域得到了广泛的应用。
为了提高注塑模的性能和降低生产成本,越来越多的企业开始关注基于计算机辅助工程(CAE)的注塑模开发技术研究。
本文旨在探讨如何利用CAE技术对注塑模进行设计、分析和优化,以满足不同行业的需求。
CAE技术是一种基于数值模拟的工程技术方法,通过计算机对复杂系统的性能进行预测和优化。
在注塑模开发过程中,CAE技术可以帮助工程师快速生成模具结构,减少试制次数,缩短生产周期,降低废品率,从而提高企业的竞争力。
本文首先介绍了注塑模的基本概念和分类,然后详细阐述了CAE 技术在注塑模开发中的具体应用,包括有限元分析(FEA)、流体分析(FAM)、热分析(Thermal)、疲劳分析(Fatigue)等。
接下来本文重点讨论了CAE技术在注塑模设计过程中的优势和挑战,以及如何克服这些挑战,提高CAE技术在注塑模开发中的应用水平。
本文对未来基于CAE的注塑模开发技术研究的发展趋势进行了展望。
A. 注塑模开发的重要性和背景随着科技的不断发展,塑料制品在各个领域的应用越来越广泛,尤其是在汽车、电子、家电等行业。
塑料制品的需求量逐年增长,使得注塑模开发技术成为了这些行业中至关重要的一环。
注塑模是一种用于制造塑料制品的模具,其质量直接影响到制品的质量、生产效率以及成本。
因此注塑模的开发技术对于降低生产成本、提高产品质量具有重要意义。
近年来随着全球经济一体化的发展,国际市场竞争日益激烈,企业为了在竞争中立于不败之地,纷纷加大研发投入,提高产品的技术含量和附加值。
在这个过程中,注塑模开发技术的研究和应用显得尤为重要。
通过引入先进的CAE(计算机辅助工程)技术,可以实现对注塑模设计的全过程模拟和优化,从而提高注塑模的开发效率和质量,降低生产成本,为企业创造更大的经济效益。
此外随着环保意识的不断提高,企业在生产过程中对环境的保护要求也越来越高。
CAE优化分析在大型注塑模设计中的应用
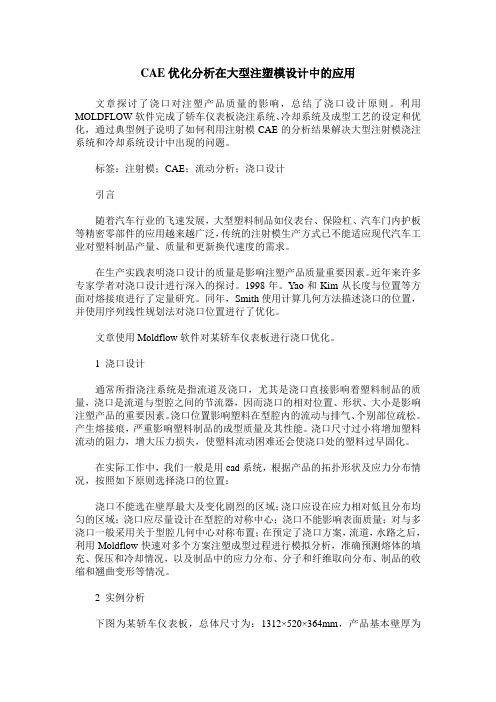
CAE优化分析在大型注塑模设计中的应用文章探讨了浇口对注塑产品质量的影响,总结了浇口设计原则。
利用MOLDFLOW软件完成了轿车仪表板浇注系统、冷却系统及成型工艺的设定和优化,通过典型例子说明了如何利用注射模CAE的分析结果解决大型注射模浇注系统和冷却系统设计中出现的问题。
标签:注射模;CAE;流动分析;浇口设计引言随着汽车行业的飞速发展,大型塑料制品如仪表台、保险杠、汽车门内护板等精密零部件的应用越来越广泛,传统的注射模生产方式已不能适应现代汽车工业对塑料制品产量、质量和更新换代速度的需求。
在生产实践表明浇口设计的质量是影响注塑产品质量重要因素。
近年来许多专家学者对浇口设计进行深入的探讨。
1998年。
Yao和Kim从长度与位置等方面对熔接痕进行了定量研究。
同年,Smith使用计算几何方法描述浇口的位置,并使用序列线性规划法对浇口位置进行了优化。
文章使用Moldflow软件对某轿车仪表板进行浇口优化。
1 浇口设计通常所指浇注系统是指流道及浇口,尤其是浇口直接影响着塑料制品的质量,浇口是流道与型腔之间的节流器,因而浇口的相对位置、形状、大小是影响注塑产品的重要因素。
浇口位置影响塑料在型腔内的流动与排气、个别部位疏松。
产生熔接痕,严重影响塑料制品的成型质量及其性能。
浇口尺寸过小将增加塑料流动的阻力,增大压力损失,使塑料流动困难还会使浇口处的塑料过早固化。
在实际工作中,我们一般是用cad系统,根据产品的拓扑形状及应力分布情况,按照如下原则选择浇口的位置:浇口不能选在壁厚最大及变化剧烈的区域;浇口应设在应力相对低且分布均匀的区域;浇口应尽量设计在型腔的对称中心;浇口不能影响表面质量;对与多浇口一般采用关于型腔几何中心对称布置;在预定了浇口方案,流道,水路之后,利用Moldflow快速对多个方案注塑成型过程进行模拟分析,准确预测熔体的填充、保压和冷却情况,以及制品中的应力分布、分子和纤维取向分布、制品的收缩和翘曲变形等情况。
基于CAE模流分析的注塑成型方案优化应用
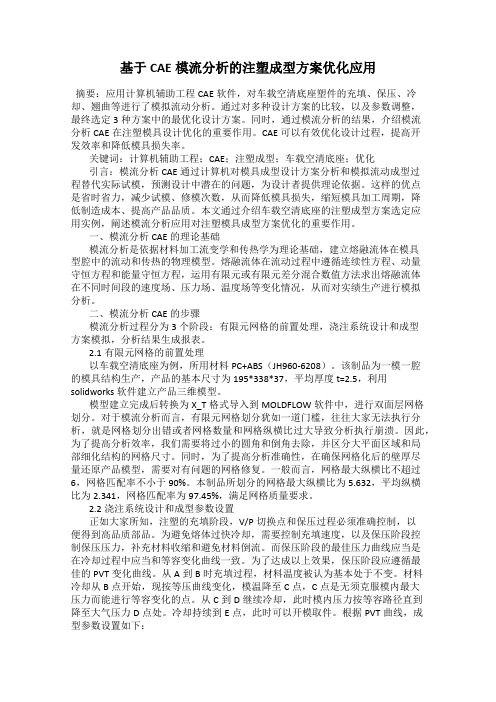
基于CAE模流分析的注塑成型方案优化应用摘要:应用计算机辅助工程CAE软件,对车载空清底座塑件的充填、保压、冷却、翘曲等进行了模拟流动分析。
通过对多种设计方案的比较,以及参数调整,最终选定3种方案中的最优化设计方案。
同时,通过模流分析的结果,介绍模流分析CAE在注塑模具设计优化的重要作用。
CAE可以有效优化设计过程,提高开发效率和降低模具损失率。
关键词:计算机辅助工程;CAE;注塑成型;车载空清底座;优化引言:模流分析CAE通过计算机对模具成型设计方案分析和模拟流动成型过程替代实际试模,预测设计中潜在的问题,为设计者提供理论依据。
这样的优点是省时省力,减少试模、修模次数,从而降低模具损失,缩短模具加工周期,降低制造成本、提高产品品质。
本文通过介绍车载空清底座的注塑成型方案选定应用实例,阐述模流分析应用对注塑模具成型方案优化的重要作用。
一、模流分析CAE的理论基础模流分析是依据材料加工流变学和传热学为理论基础,建立熔融流体在模具型腔中的流动和传热的物理模型。
熔融流体在流动过程中遵循连续性方程、动量守恒方程和能量守恒方程,运用有限元或有限元差分混合数值方法求出熔融流体在不同时间段的速度场、压力场、温度场等变化情况,从而对实绩生产进行模拟分析。
二、模流分析CAE的步骤模流分析过程分为3个阶段:有限元网格的前置处理,浇注系统设计和成型方案模拟,分析结果生成报表。
2.1有限元网格的前置处理以车载空清底座为例,所用材料PC+ABS(JH960-6208)。
该制品为一模一腔的模具结构生产,产品的基本尺寸为195*338*37,平均厚度t=2.5,利用solidworks软件建立产品三维模型。
模型建立完成后转换为X_T格式导入到MOLDFLOW软件中,进行双面层网格划分。
对于模流分析而言,有限元网格划分犹如一道门槛,往往大家无法执行分析,就是网格划分出错或者网格数量和网格纵横比过大导致分析执行崩溃。
因此,为了提高分析效率,我们需要将过小的圆角和倒角去除,并区分大平面区域和局部细化结构的网格尺寸。
基于CAE技术的汽车前面板注塑成型工艺优化
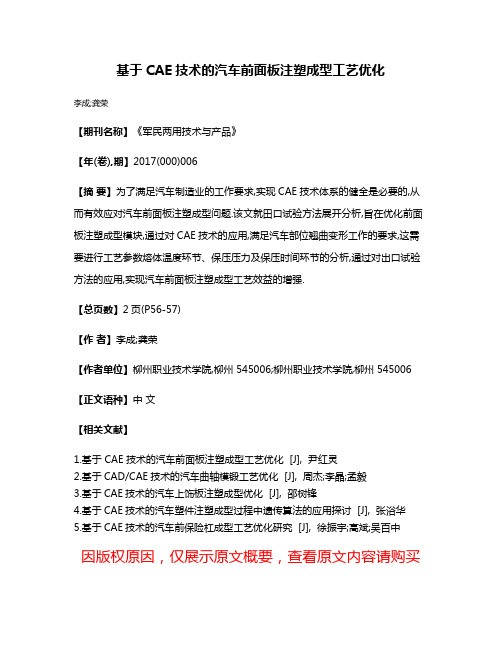
基于CAE技术的汽车前面板注塑成型工艺优化
李成;龚荣
【期刊名称】《军民两用技术与产品》
【年(卷),期】2017(000)006
【摘要】为了满足汽车制造业的工作要求,实现CAE技术体系的健全是必要的,从而有效应对汽车前面板注塑成型问题.该文就田口试验方法展开分析,旨在优化前面板注塑成型模块,通过对CAE技术的应用,满足汽车部位翘曲变形工作的要求,这需要进行工艺参数熔体温度环节、保压压力及保压时间环节的分析,通过对出口试验方法的应用,实现汽车前面板注塑成型工艺效益的增强.
【总页数】2页(P56-57)
【作者】李成;龚荣
【作者单位】柳州职业技术学院,柳州 545006;柳州职业技术学院,柳州 545006【正文语种】中文
【相关文献】
1.基于 CAE 技术的汽车前面板注塑成型工艺优化 [J], 尹红灵
2.基于CAD/CAE技术的汽车曲轴模锻工艺优化 [J], 周杰;李晶;孟毅
3.基于CAE技术的汽车上饰板注塑成型优化 [J], 邵树锋
4.基于CAE技术的汽车塑件注塑成型过程中遗传算法的应用探讨 [J], 张浴华
5.基于CAE技术的汽车前保险杠成型工艺优化研究 [J], 徐振宇;高斌;吴百中
因版权原因,仅展示原文概要,查看原文内容请购买。
基于CAE技术注塑模冷却系统优化设计

基于CAE技术注塑模冷却系统优化设计陈冲【摘要】The design proposal for a cooling system is critical for molding quality, molding cycle and production efficiency of products in the course of plastic injection molding. Based on theory of cooling in injection molding, deficiencies of the design of the cooling system are obtained by analyzing numerical simulation of molding injection molded plastic part of automobile wheel hub cap by CAE technology, with temperature distribution of a mould, part temperature at ejection, ejection time and warping deformation of parts during plastic injection molding as indices of cooling performances, while the cooling systems are compared, improved and optimized. Practices prove that the product quality conforms to requirements, and the optimization method for a cooling system is reliable and effective, which has certain referential value for structural design of plastic injection moulds.%在塑料注塑成型过程中,冷却系统的方案设计对产品的成型质量、成型周期以及生产效率起到了关键性作用。
基于CAE技术下双色显示器前壳注射模具的优化设计
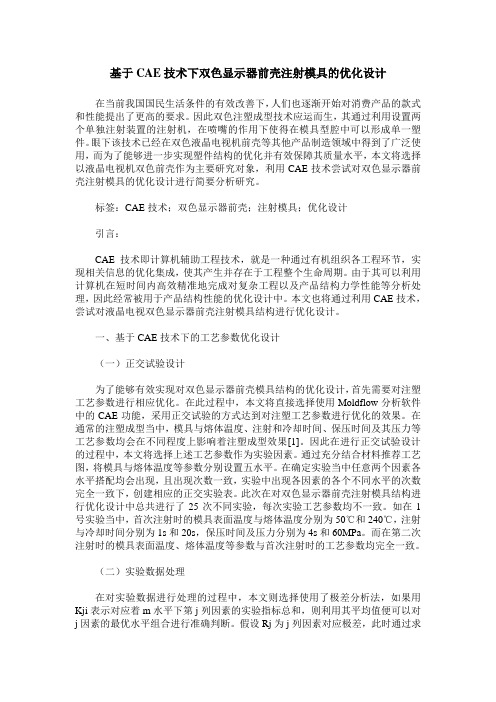
基于CAE技术下双色显示器前壳注射模具的优化设计在当前我国国民生活条件的有效改善下,人们也逐渐开始对消费产品的款式和性能提出了更高的要求。
因此双色注塑成型技术应运而生,其通过利用设置两个单独注射装置的注射机,在喷嘴的作用下使得在模具型腔中可以形成单一塑件。
眼下该技术已经在双色液晶电视机前壳等其他产品制造领域中得到了广泛使用,而为了能够进一步实现塑件结构的优化并有效保障其质量水平,本文将选择以液晶电视机双色前壳作为主要研究对象,利用CAE技术尝试对双色显示器前壳注射模具的优化设计进行简要分析研究。
标签:CAE技术;双色显示器前壳;注射模具;优化设计引言:CAE技术即计算机辅助工程技术,就是一种通过有机组织各工程环节,实现相关信息的优化集成,使其产生并存在于工程整个生命周期。
由于其可以利用计算机在短时间内高效精准地完成对复杂工程以及产品结构力学性能等分析处理,因此经常被用于产品结构性能的优化设计中。
本文也将通过利用CAE技术,尝试对液晶电视双色显示器前壳注射模具结构进行优化设计。
一、基于CAE技术下的工艺参数优化设计(一)正交试验设计为了能够有效实现对双色显示器前壳模具结构的优化设计,首先需要对注塑工艺参数进行相应优化。
在此过程中,本文将直接选择使用Moldflow分析软件中的CAE功能,采用正交试验的方式达到对注塑工艺参数进行优化的效果。
在通常的注塑成型当中,模具与熔体温度、注射和冷却时间、保压时间及其压力等工艺参数均会在不同程度上影响着注塑成型效果[1]。
因此在进行正交试验设计的过程中,本文将选择上述工艺参数作为实验因素。
通过充分结合材料推荐工艺图,将模具与熔体温度等参数分别设置五水平。
在确定实验当中任意两个因素各水平搭配均会出现,且出现次数一致,实验中出现各因素的各个不同水平的次数完全一致下,创建相应的正交实验表。
此次在对双色显示器前壳注射模具结构进行优化设计中总共进行了25次不同实验,每次实验工艺参数均不一致。
- 1、下载文档前请自行甄别文档内容的完整性,平台不提供额外的编辑、内容补充、找答案等附加服务。
- 2、"仅部分预览"的文档,不可在线预览部分如存在完整性等问题,可反馈申请退款(可完整预览的文档不适用该条件!)。
- 3、如文档侵犯您的权益,请联系客服反馈,我们会尽快为您处理(人工客服工作时间:9:00-18:30)。
文 献 标 识 码 :A
文 章 编 号 :1 0 0 5— 5 7 7 0( 2 0 1 3 )0 5— 0 0 5 5— 0 4
Abs t r a c t : Th e a r t i c l e a n a l y z e d t h e s t r u c t u r e a n d mo l d i n g pr o c e s s o f a p l a s t i c b o o k e n d. Th e g a t e l o c a t i o n, f il l i n g a n a l y s i s a n d c o o l i n g a n a l y s i s i n Mo l d lo f w ,wa s u s e d t o i f ni s h t he mo l d d e s i g n. Th e o p t i ma l mo l d i n g p r o c e s s p a r a me t e r c o mb i n a t i o n s f o r r e d u c i n g t h e wa r pa g e o f t h e p l a s t i c p a t r wa s f o un d i n t h e t e s t r a n g e t h r o u g h t h e CAE s i mu l a t i o n o f t he p r o c e s s p a r a me t e r s us i n g o th r o g o n a l t e s t me t h o d . Th e r e s u l t s i n d i c a t e d t h a t :t h e a pp l i c a t i o n o f CAE t e c h n o l o g y c a n s h o te r n t h e mo l d d e v e l o p me n t c y c l e a n d i mp r o v e t h e q u a l i t y o f mo l d d e s i g n. Ke y wor ds : CAE; Mo l d lo f w An a l y s i s; Mo l d; Pr o c e s s P a r a me t e r s Op t i mi z a t i o n; W a r p a g e
I n j e c t i o n Mo l d D e s i g n o f B o o k E n d s a n d Op t i mi z a t i o n o f F o r mi n g
Pr o c e s s Ba s e d o n CAE
第4 l 卷 第 5期 2 0 1 3年 5月
塑 料 工 业
CH I NA PLAS TI CS I NDUS TRY ・5 5・
基于 C A E的书 立 注 塑 模 设 计及 成 型工 艺 优 化 术
谈 建豪 ,陈 燕 ,向和 平 ,徐 东风
( 1 .华 南农 业大学工程学 院,广东 广州 5 1 0 6 4 2 ;2 .华南农业大学信息学 院,广东 广州 5 1 0 6 4 2 )
T AN J i a n — h a o , CHE N Y a n , XI ANG He — p i n g , XU Do n g 。 f e n g ( 1 .C o l l e g e o f E n g i n e e r i n g ,S o u t h C h i n a A g i r c u l t u r a l U n i v e r s i t y ,G u a n g z h o u 5 1 0 6 4 2 ,C h i n a ; 2 .C o l l e g e o f I n f o r ma t i e s ,S o u t h C h i n a A g r i c u l t u r a l U n i v e r s i t y ,G u a n g z h o u 5 1 0 42 6 ,C h i n a )
模具 C A E技 术通 过 在计 算 机 上 模 拟 塑 件 的 成 型
的长度 与厚 度之 比过小 ,脱模 表 面 的脱 模斜 度不 宜过
过程 ,预测模 具 设计 和成 型过 程 中存在 的问题 ,指 导 模 具 的优化 设计 和合 理 工艺参 数 获取 ,不 但可 提高 模
具 的设 计质 量 ,同时可减 少试 模 时 间 ,缩 短产 品开 发 周 期 ,降低 产 品开 发 成 本 。 因此 ,模 具 C A E技 术 在 模具 行 业 中得 到广泛 的应 用 - 6 1 。
摘要 :通过对塑料 书立 的结 构和工艺性分析 ,并参考 Mo l d f l o w对浇 口位置选 择 、填充 和冷却分析的结果进行 了模 具设 计 ;以减少塑件翘 曲变形 为 目标 ,采 用正交试 验方 法 ,对工艺 参数 进行 了 C A E仿 真试验 ,在试 验范 围 内得 到了 最优成型工艺参数组合 。结 果表明 ,应用 C A E技术可缩短模具开发周期 ,提高模具设计 质量 。 关键词 :C A E;模流分析 ;模具 ;工艺参数优化 ;翘 曲