面层制壳工艺研究
对熔模铸造现行制壳工艺

对熔模铸造现行制壳工艺的改进和讨论黄炳荣1,景宗梁2(1. 无锡鹰普精密铸造有限公司,江苏无锡 214028;2. 郑州大禹化工产品有限公司,江苏无锡 214035)摘要:中温模料硅溶胶制壳工艺是目前国内、国外的主流工艺,用于生产精密铸件。
然而,面临制壳生产周期长、因面层型壳缺陷导致铸件缺陷的困扰。
提出面层浆料加入防裂剂、面层大风力干燥、面层采用大粒径硅溶胶、取消涂二层前预湿、取消涂面层前沾硅溶胶的工艺举措,从而提高面层型壳的强度,减少面层型壳的缺陷,缩短涂层干燥时间,提高铸件一次性合格率。
关键词:防裂剂;干燥时间;预湿;胶粒径•The current system of investment casting shell process of thinking and discussHUANG Bing-rong1, JING Zong-liang2(1. Wuxi Impro Precision Casting Co., Ltd., Wuxi 214028, Jiangsu,China; 2. Zhengzhou Dayu Chemical Products Co., Ltd., Wuxi 214035,Jiangsu, China)Abstract:WenMo silicon sol material in the shell is the current domestic and foreign technology process for the production of the mainstream, precision castings. However, faced with the shell long production period, because the surface defects casting mold shell to defect problems. Put forward the surface crack size to join agent, facing big wind dry, facing the large particle size silicon sol, cancel besmear before the second floor surface coating, prewettingcancelled before the process with silicon sol measures, so as toimprove the strength of the road surface mold shell, reduce thesurface defects, shorten the mold shell coating drying time, improve casting one-time qualified.Key words:Guards against the crack agent; Drying time; The wet;Glue size熔模铸造中温蜡全硅溶胶结壳工艺适合生产表面粗糙度值小、尺寸精度高的精密件,已经成为主流工艺被广泛应用。
水玻璃精密铸造制壳工艺新型配方与传统配方比较

水玻璃精密铸造制壳工艺新型配方与传统配方比较一:大幅度提高表面质量..传统配方下;特别是在生产单件二十公斤以上的铸件;表面质量难以保证;表面毛刺、粘砂、表面癞蛤蟆皮、桔子皮及分层引起的缺陷难以避免..在生产厚大件时;表面几乎都要靠打磨才能满足要求..新型配方则完全解决了上述问题;几乎所有材质除了含锰大于4%的材质外的铸件达到甚至超过了复合型型壳的水平..二:大幅度提高内在质量..采用传统配方;由于表面层强度低;在型壳焙烧后;用手在型壳内壁上摸;经常会发现掉白灰的情况;还有采用传统配方;表面层制壳工艺复杂;影响因素很多;导致表面型壳质量很不稳定;型壳分层时有发生;这些因素导致传统的水玻璃型壳的铸件内部质量得不到保证;特别是在要求高的加工面上;时常因为加工出砂孔等缺陷导致铸件报废;这其中有相当部分是型壳质量差造成的;而新型配方很好的解决了这一难题;使铸件内在质量得到大幅度的提升..三:提高成品率;特别是大幅度提高优良品率..采用传统的配方;由于表面和内在质量得不到可靠的控制;废品率比较高;采用新型配方;由于表面质量和内在质量得到大幅度的提高;成品率也相应的提高;特别是不需要修补和打磨优良品率大幅度提高..四:大幅度降低后处理的工作量..采用传统配方;由于表面质量差;后处理工作量相当大;在劳动力日趋紧缺的今天;工作环境很差的后处理招工越来越难;采用新型配方后;后处理的工作量大幅度降低;特别是厚大件;后处理的工作量可以降低80%以上..五:大幅度改善制壳车间的工作环境..传统配方;大多数面层和过渡层采用氯化铵硬化;硬化过程中会产生氨气;氨气严重污染环境的同时;还腐蚀设备..新型配方在制壳过程中没有氨气产生;很好的解决了这一问题..六:降低生产成本..实践表明;采用新型配方比传统配方在制壳成本上每吨铸件高出30——80元;但是;大幅度降低了后处理成本..七:大大提高了传统水玻璃型壳生产大件的能力..对于传统水玻璃型壳;越大的件;出问题越多;生产难度越大..采用新型配方;许多问题迎刃而解;大大提高了传统水玻璃型壳生产大件甚至超大件的能力..总之;新型配方相比传统配方而言;是革命性的进步..谁先使用;谁将引领潮流..本人还有一篇文章免硬化水玻璃精密铸造制壳面层、过渡层划时代的技术革新;在百度文库里同样可以下载;如需要的;请直接下载..如有对新工艺感兴趣的业内专家或者同行需要进一步了解新配方和新工艺的使用情况;请联系我们;谢谢联系方式:。
精密铸造4种制壳工艺特点分析及改进方向探讨
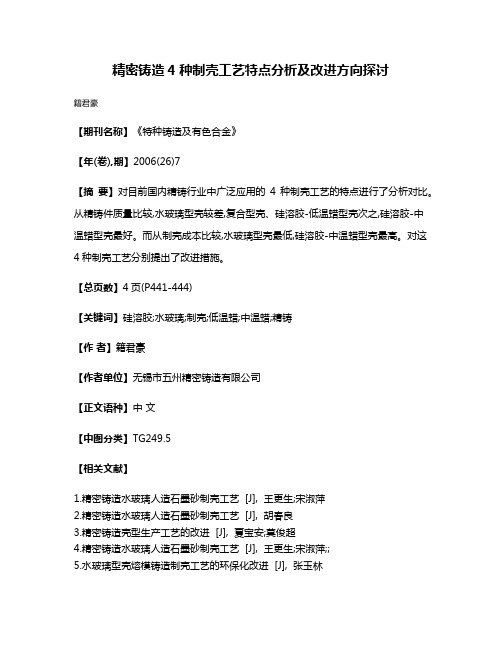
精密铸造4种制壳工艺特点分析及改进方向探讨
籍君豪
【期刊名称】《特种铸造及有色合金》
【年(卷),期】2006(26)7
【摘要】对目前国内精铸行业中广泛应用的4种制壳工艺的特点进行了分析对比。
从精铸件质量比较,水玻璃型壳较差,复合型壳、硅溶胶-低温蜡型壳次之,硅溶胶-中温蜡型壳最好。
而从制壳成本比较,水玻璃型壳最低,硅溶胶-中温蜡型壳最高。
对这4种制壳工艺分别提出了改进措施。
【总页数】4页(P441-444)
【关键词】硅溶胶;水玻璃;制壳;低温蜡;中温蜡;精铸
【作者】籍君豪
【作者单位】无锡市五州精密铸造有限公司
【正文语种】中文
【中图分类】TG249.5
【相关文献】
1.精密铸造水玻璃人造石墨砂制壳工艺 [J], 王更生;宋淑萍
2.精密铸造水玻璃人造石墨砂制壳工艺 [J], 胡春良
3.精密铸造壳型生产工艺的改进 [J], 夏宝安;莫俊超
4.精密铸造水玻璃人造石墨砂制壳工艺 [J], 王更生;宋淑萍;;
5.水玻璃型壳熔模铸造制壳工艺的环保化改进 [J], 张玉林
因版权原因,仅展示原文概要,查看原文内容请购买。
水玻璃面层型壳制备.
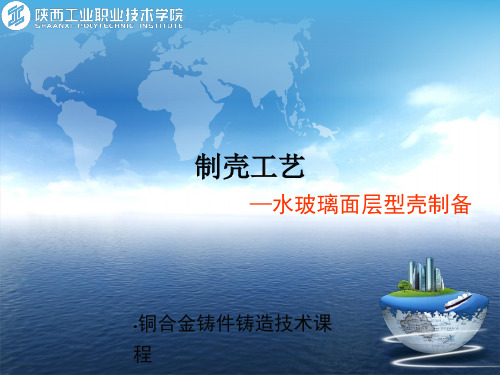
使用工具、设备
水玻璃、搅拌器、石英粉、涂料桶
面层型壳制备
水玻璃石英粉面层涂料、蜡模组、撒砂床、硅砂、挂棒架
铜合金铸件铸造技术 课程
面层涂料配制
(1)耐火涂料配制 涂料所需的原材料有耐火粉料(石英粉)、水玻璃(密度和模数符合要求:密 度1.27~1.34g/cm3,模数3.0~3.4)、表面活性剂(静止时间大于2h。
铜合金铸件铸造技术 课程
模组清洗 水玻璃涂料的涂挂性远高于水玻璃涂料和硅
溶胶涂料。
清洗目的:洗净蜡模表面粘附的油污及蜡屑,
进一步提高蜡模表面和涂料之间的涂挂性。
方法:JFC或肥皂水洗涤后清水冲净。
铜合金铸件铸造技术 课程 干燥、硬化
每涂、撒好一层型壳后,就要对这一层进行干燥和硬化,
制壳工艺
—水玻璃面层型壳制备
•
铜合金铸件铸造技术课
程
铜合金铸件铸造技术 课程
面层型壳制备
任务布置 生产准备 型壳制备
1
1 2
3
4
型壳检查
铜合金铸件铸造技术 课程
一、任务布置
根据制定的工作计划,
完成吊锤铸件熔模铸造型
壳制备。
铜合金铸件铸造技术 课程
二、生产准备
吊锤铸件水玻璃型壳熔模铸造面层型壳制备工艺 步骤
5.考虑到制壳工艺时间的要求,本次课每 次半个班倒班进行。
铜合金铸件铸造技术 课程
四、型壳检验
项目 1 2 3 4 5 6 总分 序 小组 涂挂涂料质 撒砂是否均匀, 型壳是否有裂 脱蜡后型 操作规 文明生 号 量 是否有掉砂 纹和砂眼 壳质量 程 产 20 1 2 3 20 20 10 10 100
制壳工艺原理

制壳工艺原理制壳工艺原理是指通过一系列的加工和处理工艺,将物体表面包覆上一层外壳的工艺过程。
这种工艺广泛应用于各个行业,如电子产品、汽车零部件、家具等。
制壳工艺的目的是保护物体表面不受损坏、腐蚀或污染,同时也能提高产品的外观质量和使用寿命。
制壳工艺主要包括以下几个步骤:1. 表面处理:在进行制壳之前,需要对物体表面进行处理,以确保壳体能够牢固地附着在物体表面上。
表面处理的方法包括机械处理、化学处理和电化学处理等。
机械处理主要是利用刷洗、研磨等方法去除物体表面的杂质和氧化层;化学处理主要是利用酸、碱等溶液对物体表面进行腐蚀或溶解,以清洁表面;电化学处理是利用电解液和电流的作用,使物体表面发生化学反应,形成均匀的氧化膜或金属保护层。
2. 壳体制作:壳体是制壳工艺的核心部分,它需要根据物体的形状和尺寸来设计和制作。
壳体的材料可以是金属、塑料、陶瓷等,根据不同的要求选择合适的材料。
制作壳体的方法有很多种,如注塑成型、压铸、冲压等。
其中,注塑成型是一种常用的方法,它通过将熔化的塑料注入到模具中,然后冷却固化成型。
3. 壳体装配:在制作好壳体之后,需要将其与物体进行装配。
装配的方法有很多种,如螺纹连接、焊接、粘接等。
螺纹连接是一种常用的方法,它通过螺纹的互相咬合,实现壳体和物体的连接。
焊接是将壳体和物体的接触面加热至熔化状态,然后冷却固化,使其形成一体化。
粘接是利用胶水或粘合剂将壳体和物体黏合在一起。
4. 表面处理:装配完成后,还需要对壳体表面进行处理,以提高其外观质量和耐用性。
常见的表面处理方法有喷涂、电镀、喷砂等。
喷涂是将涂料喷洒在壳体表面,形成一层均匀的涂层;电镀是利用电解液和电流的作用,将金属沉积在壳体表面,形成一层金属保护层;喷砂是利用高速喷射的砂粒对壳体表面进行冲击,使其表面变得粗糙。
通过以上的步骤,制壳工艺可以为物体提供良好的保护和装饰效果。
它能够有效地防止物体表面受到损坏和腐蚀,延长物体的使用寿命。
精铸硅溶胶型壳工艺的改进电子教案

5.由表十一,十二及十三实验结果得出以下结论:
⑴.在表面层涂料中加入少量“分散剂”能改变硅溶胶涂料的流变特性,增
加涂料的屈服值从而可提高涂挂性和覆盖性(涂层平均厚度)3可提高15-25%。同时由于
“分散剂”作用能使粉料“分散”不易“结团”。使平均粒径减小因而3增加。虽然粉液比
n略有下降,但致密性k%仍在要求范围之内(表七)。涂料的均匀性,悬浮性,涂挂性和流 平性均有提高。“板结”“老化”时间延长(稳定性提高)。
1.美国在2006年前面层涂料的典型工艺是在锆英粉中掺加5-10%(质量)的熔融石英粉。
其主要目的是:降低成本,提高铸件尺寸精度和改善脱壳性、透气性。国外重点工艺改进方 向是:充分利用熔融石英纯度高,杂质少,密度和热膨胀系数小,加上高温“析晶”,低温
“相变”的特点,使型壳在高温时保持高强度而在低温时因相变产生剧烈收缩(-3.7%)致
精铸硅溶胶型壳工艺的改进
前言:
众所周知,全球精铸界通用的硅溶胶型壳工艺存在三大缺点:
1.成本高。2.制壳周期长。3.铸件脱壳性差(型壳残留强度高)。
据统计,表面层型壳通用的耐火料锆英石砂、粉占型壳原辅材料成本的48%占总生产成本
的10%(平均值)[1]。优质锆英石资源稀缺,因而寻找它的代用品或减少其消耗量是当今 国内外精铸界共同关心,重点研究的课题之一。
2.混合涂料用粉料粒度要求应符合表五规定。
注:1•采用GSL-101BI型“激光颗粒度测定仪” 测定(丹东市辽宁仪器仪表研究所生产)
2.粒度判定以DV90, DV50及Wo三项指标为主要依据。DV98 DV84为参考指标。
3.无粒度检测条件时,可将待测粉料与“标准”硅溶胶配制成“标准”涂料来判定
免硬化解决分层水玻璃精密铸造制壳面层、过渡层新工艺

划时代的水玻璃精密铸造制壳工艺面层、过渡层新型工艺和配方各位精密铸造行业的专家、企业家们,衷心的请您耐心认真的了解本文介绍的内容,相信您一定可以感受到即将到来的呼之欲出的精铸工艺革命!我国传统的水玻璃精密铸造工艺,面层、过渡层以水玻璃为粘结剂,辅以石英粉,适当添加消泡剂、渗透剂配浆以后,将蜡模模组进行蘸浆、洒砂、风干,然后用氯化铵、或者氯化铝、氯化铝氯化镁混合作为硬化剂,浸泡,待水玻璃和氯化铵反应以后,起到硬化的作用,硬化以后仍需等待模组干燥,然后再进入到下一层的操作。
多年来,我国一直用氯化铵作水玻璃型壳的硬化剂。
以后又逐步发展为用氯化铝:氯化镁作硬化剂。
无论用何种硬化剂,都免不了需要硬化,都有其不可克服的缺点。
氯化铵虽能在较短时间内硬化型壳,但焙烧后型壳强度差,作高强度型壳的硬化,显然不行,加之硬化时有氨气逸出,散发出刺鼻的气味,故工作环境条件差,导致招工难,留人难。
用氯化铝,还是氯化铝和氯化镁混合溶剂硬化,又有铸件表面质量差,清砂困难等缺点。
为客服上述传统工艺的各种缺陷,我公司技术人员经过多年的生产实践和摸索,经历了无数次的试验失败和不断尝试,研究出一种新型工艺和配方(该工艺和配方已经进入了国家实用型专利的申请流程),利用量身定做的配浆设备、配浆配方、脱蜡装置等重要工艺因素,让水玻璃精密铸造工艺取得飞跃的进步。
本文介绍的新工艺,主要是体现在型壳的面层、过渡层制作彻底告别硬化时代,使铸件的表面质量得到很大的提高,其光洁度甚至可以与硅溶胶精铸工艺生产出来的铸件媲美。
避免了传统的制壳工艺带来的表面分层、表面粘砂,橘子皮等缺陷。
同时,由于没有了氯化铵挥发出来的氨味,工作环境得到明显的改善,同时工艺参数要求、操作要求没有传统的硬化工艺那么复杂和严格,操作简单,一般工人均可上手,减少了由于熟练工流失,新工人上岗时的废品损失,稳定了工厂的正常生产效率。
成本方面,制壳材料成本比传统硬化工艺非但没有增加,而且明显减少了铸件后处理的焊补打磨抛丸处理,大大降低了生产成本,提高了良品率,缩短了生产周期,提升了利润空间的同时,大大提升了客户满意度。
面层制壳工艺研究

涂料干燥工艺:自干1.5~2h;风干1.5~2h;氨干0.5 h,氨气流量:表面层10~15 L/min; 加固层10~20 L/min。
采用中国标准杯体积测定粘度。
再将电熔刚玉的主要成分及杂质与锆英砂作一个比较,见表2:
电熔刚玉 Al2O3≥98.5 Fe2O3≤0.10 1级锆砂 ZrO2≥65 Fe2O3≤0.30 2级锆砂 ZrO2≥63 Fe2O3≤0.70 3级锆砂 ZrO2≥60 Fe2O3≤1.00 表2 电熔刚玉与锆英砂成分比较表
2.1 锆英粉-熔融石英粉混合浆-撒锆英砂
面层配浆工艺如下:
锆英粉:熔融石英粉 = 85%:15%
粉液比: 1:3.2
粘度值(詹氏4#):42~45s
润湿剂:10kg面层硅溶胶加30ml
消泡剂:10kg面层硅溶胶加22ml
面层撒砂:100~120目锆英砂
面层干燥时间:6~7h
环境条件:温度22~25℃;湿度22~25%
该工艺适用于生产汽车零件和精密机械零件,面层制壳成本比全锆英粉降低约25%左右。
图3A左 锆英粉+熔融石英粉混合浆,撒锆英砂
Fig.3 Left Zircon-powder + Melting Quartz Powder Admixture pulp,Caesar Zircon-Sand
1.2莫来砂做面层撒砂材料
锆英石与高岭石这两种耐火材料有着良好的兼容性和复合性,所以,面层砂采用以莫来砂替代锆英砂。
面层配浆工艺如下:
粉液比(325目锆英粉): 1:3.3~3.4
粘度值(詹氏4#):42~45s
润湿剂:10kg面层硅溶胶加28ml
制壳工艺操作规程及注意事项

制壳工艺操作规程及注意事项一.工艺要求:面层:室温:24±2℃湿度:50-70% 风速:6-8m/s硬化时间:8-10分钟,干燥时间:≥3h且干透手工撒砂:40-70目石英砂过度层:室温:24±2℃湿度:40-60% 风速:6-8m/s硬化时间:11-15分钟,干燥时间:≥4h且干透手工撒砂:20-40目石英砂加固层:室温24±2℃湿度:40-60% 风速:6-8m/s硬化时间:20-35分钟,干燥时间:≥0.5h第一层撒砂:12-20目石英砂,第二、三、四层撒砂8-12目石英砂封浆(半层)干燥时间: ≥12h二.操作程序:1.面层涂挂前,检查清洗后的模组是否有掉件的情况,并检查是否彻底干燥。
2.检查涂料粘度和设备转速是否符合要求,如不正常应加以调整(涂料粘度用4#詹氏杯测检,32±2秒)3.从运送小车上取下模组,以30度左右角度将模组较慢的浸入面层涂料浆中稍做旋转,注意使蜡模沟槽和尖角处泡在涂料中的空气减到最少,有铸字或凹槽的要用毛刷涂刷或压缩空气吹除气泡。
预先喷涂涂料。
4.以稍快的速度取出模组,使多余涂料滴除,用压缩空气吹破包在蜡模孔洞和尖角内的气泡,以不同角度不停的转动模组,模组上形成完整均匀涂层,若不能获得均匀完整涂层需重新沾浆。
5.将敷有均匀涂层的模组伸入淋砂机翻转,让全部表面均匀敷上一层砂。
6.取出模组吊挂在运送小车上,等整车挂满后,推到适当位置,让面层型壳干燥到技术规定时间。
7.将面层型壳已干燥的模组运送到过渡层制壳车间。
8.取下模组检查型壳内角,孔内是否彻底干燥,若有涂层堆积皱纹或开裂等的情况,应立即另做处理。
9.取下模组轻轻震落多余浮砂。
10.把模组浸入硅溶胶中,不超过2秒钟取出后滴约5秒钟。
11.把不再滴预湿剂的模组以30度左右角度缓慢浸入过渡层涂料中稍做旋转3-4秒,以稍快速度取出模组不停转动,滴除多余涂料形成均匀涂层,如孔洞等处有涂料闭塞和堆积可使用压缩空气或毛刷弄开。
精密铸造制壳工艺特点及改进方向探讨
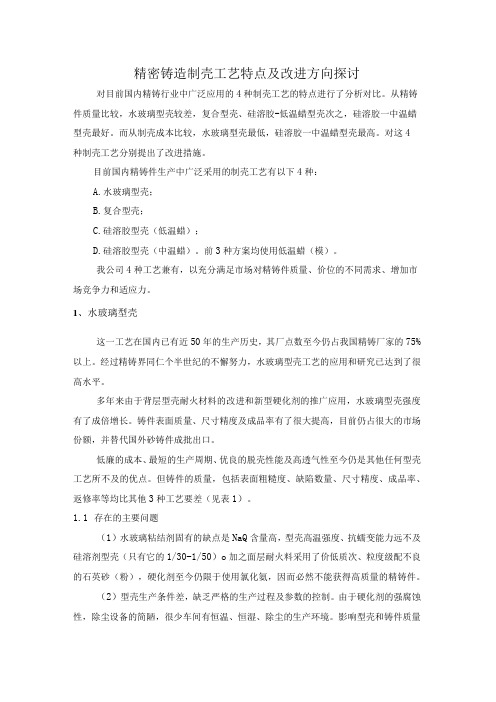
精密铸造制壳工艺特点及改进方向探讨对目前国内精铸行业中广泛应用的4种制壳工艺的特点进行了分析对比。
从精铸件质量比较,水玻璃型壳较差,复合型壳、硅溶胶-低温蜡型壳次之,硅溶胶一中温蜡型壳最好。
而从制壳成本比较,水玻璃型壳最低,硅溶胶一中温蜡型壳最高。
对这4种制壳工艺分别提出了改进措施。
目前国内精铸件生产中广泛采用的制壳工艺有以下4种:A.水玻璃型壳;B.复合型壳;C.硅溶胶型壳(低温蜡);D.硅溶胶型壳(中温蜡)。
前3种方案均使用低温蜡(模)。
我公司4种工艺兼有,以充分满足市场对精铸件质量、价位的不同需求、增加市场竞争力和适应力。
1、水玻璃型壳这一工艺在国内已有近50年的生产历史,其厂点数至今仍占我国精铸厂家的75%以上。
经过精铸界同仁个半世纪的不懈努力,水玻璃型壳工艺的应用和研究已达到了很高水平。
多年来由于背层型壳耐火材料的改进和新型硬化剂的推广应用,水玻璃型壳强度有了成倍增长。
铸件表面质量、尺寸精度及成品率有了很大提高,目前仍占很大的市场份额,并替代国外砂铸件成批出口。
低廉的成本、最短的生产周期、优良的脱壳性能及高透气性至今仍是其他任何型壳工艺所不及的优点。
但铸件的质量,包括表面粗糙度、缺陷数量、尺寸精度、成品率、返修率等均比其他3种工艺要差(见表1)。
1.1存在的主要问题(1)水玻璃粘结剂固有的缺点是NaQ含量高,型壳高温强度、抗蠕变能力远不及硅溶剂型壳(只有它的1/30-1/50)o加之面层耐火料采用了价低质次、粒度级配不良的石英砂(粉),硬化剂至今仍限于使用氯化氨,因而必然不能获得高质量的精铸件。
(2)型壳生产条件差,缺乏严格的生产过程及参数的控制。
由于硬化剂的强腐蚀性,除尘设备的简陋,很少车间有恒温、恒湿、除尘的生产环境。
影响型壳和铸件质量的涂料配制、硬化、风干、脱蜡等工序,极少按行业规定的操作规范严格控制。
如定期检测涂料粘度、涂片重、硬化剂浓度、PH值等。
型壳风干处的温度、湿度、风速等更是不加控制,故常在高、低温或梅雨季节发生批量报废的质量事故。
制壳工艺操作规程及注意事项

4.应经常清除涂料表面的蜡屑等杂物。
5要确保背层干燥期间,模组之间的空气流动,除湿机能处于最佳状态。
16.取出模组让多余涂料滴落,连续操作时可挂在沾浆机上方架上。让涂料滴回浆桶,然后取下模组,不停转动使各处涂层均匀,要注意浇口杯缘处涂层不要太薄。
17.将模组伸入浮砂桶内敷砂,当浇口杯缘已达砂中时,缓慢抽出模组震落多余砂粒,把模组吊挂回小车上,推到干燥区进行规定时间的充分干燥。
18.重复以上步骤进行背层第二、三层涂挂敷砂,充分干燥后再封浆。注意封浆干燥时间通常情况下时间相对延长。
12.将模组伸入浮砂桶内敷砂,当浇口杯缘已有砂时,即可缓慢抽出模组,震落多余的砂粒,目视应无任何区域尚未被砂敷住,如有无覆盖处,可用手辅助敷砂,直到均匀。
13.把模组吊挂到运送小车上,整车挂满后,推到干燥区干燥8小时以上。
14.将小车推到背层涂料处,取下模组轻摇,去除型壳上松散的浮砂。
15.小心将模组浸入背层涂料桶中,轻轻转动最少10秒钟。
7.将面层型壳已干燥的模组运送到过渡层制壳车间。
8.取下模组检查型壳内角,孔内是否彻底干燥,若有涂层堆积皱纹或开裂等的情况,应立即另做处理。
9.取下模组轻轻震落多余浮砂。
10.把模组浸入硅溶胶中,不超过2秒钟取出后滴约5秒钟。
11.把不再滴预湿剂的模组以30度左右角度缓慢浸入过渡层涂,如孔洞等处有涂料闭塞和堆积可使用压缩空气或毛刷弄开。
19.各层涂挂完毕,及时清理现场,清扫设备等保养。
三.注意事项:
1.严格控制制壳车间湿度、温度、风速及涂料粘度。
2.要特别认真制好面层,确保深孔和尖角处涂料与蜡模间无气泡,无涂料堆积,糊住孔等现象,面层型壳刚制完不得置于风扇前后,注意面层和过滤层干燥速度不宜过快,干燥时间不应过长,以防出现龟裂缺陷。
中国铸造协会组团赴法、日对外交流通知

于清砂脱壳 ,使得 制壳成本 大幅度 的下降 。
参 考 文献 :
[] 山屋洋树 . 密铸 造实用技 术革新 [ . 1 精 M]许去祥 ,译. 合肥 :中国 科学技术 大学 ,2 0 . 02
用61 .所述 工艺生 产 的铸 件更 为光 洁 、细腻 ,达 到硅溶 胶一 水玻璃 复合工艺 的水 平 ,尺寸精 度高 。 63 水 玻璃— 硅 微粉 浆—撒 精 铸 专用砂 .
【】 聂小 武 . 模铸 件 在制 壳 工序 产 生缺 陷 的消 除 []金属 加 工 , 8 熔 J.
2 1 ():6 — 1 00 1 97 .
[】 邵抗振 , 3 李桐 ,赵竞 翔, 喷嘴的熔模铸造生产 工艺研 究 【 . J 铸造 , 】
2 0 ,5 ( ) 3 2 . 0 8 7 1 :2 — 4
璃复合工艺 的水平 。
( 编辑 :刘冬 梅 ,lm@ fu dy ol. r) a o n rw r cn do
( 接第 8 2页 ) 上 0
[】 袁有录 ,曾大新 ,董艺 ,等. 2 r 复杂铸钢件熔模精铸过程数 5 4 C Mo 值模拟及试验研究 []铸造 ,2 0 ,5 () 7 — 7 . J. 0 8 7 5 :4 3 4 6
面层浆料 配制 工艺参 数 同61 述工艺 参数 ,面 层 . 所
撒8 — 0 目精 铸专用 砂 ,第 三层及 之后 的工艺参 数 同 0 10 61 .。大量 生产 实践 表 明 ,应 用此 工艺 宜 生产 1- 5k 0 1 g
[ 中国机械工程学会铸造分会. 2 】 熔模铸造手册 [ . 京 : 械工业 M】 北 机
精 度高 。
的材料 组合 ,有 针对性 地 选择 和配 合使用 面层用 粉 和
硅溶胶制壳面层浆料配比

硅溶胶制壳面层浆料配比说到硅溶胶制壳面层浆料配比,嘿,咱们得先捋一捋这玩意儿是个啥。
你想啊,硅溶胶就像是那个万能胶,能把各种材料粘在一起,啥都不怕。
而壳呢,就是咱们在制作一些特殊的物品时用到的外壳。
比如说,铸造一些精密的零件,外面得有个硬壳把它包起来。
听起来挺简单的,但其实里面的学问可大了去了。
好啦,咱们先从配比说起。
面层浆料的配比就像是做饭,得有主料和配料。
首先是硅溶胶,得有个合适的比例。
你看,硅溶胶的好处在于它的流动性很好,能均匀地涂抹在表面。
记住,比例可不能瞎来,一不小心多了,成品可就变得跟大象屁股似的,厚得离谱;少了,又不够结实,像纸糊的房子,随便一吹就倒。
然后就是水,水也是很关键的角色。
水多了,浆料就稀得跟水煮白菜一样;水少了,那浆料就干得像老干妈,涂不上去。
所以说,这水啊,得掌握个度,不能让它太贪心,也不能让它太小气。
要想把这个比例搞得刚刚好,得多试几次。
嘿,这就像调味料,得慢慢尝,慢慢找感觉。
再来呢,咱们还得考虑其他添加剂。
这些可不是随便加的,得根据实际需求来选。
有些添加剂能提高浆料的强度,有些则能改善流动性。
就好比你做菜,放点盐能提鲜,但放多了可就变成咸菜了。
所以,添加剂的选择和用量,得时刻保持警惕,确保每一步都稳妥。
别想着一蹴而就,这可是个细活儿。
搅拌也是个关键环节。
把所有材料都放在一起,就像一锅大杂烩,得搅拌得均匀,不然你一口吃下去,可能咬到一块硬的东西,尴尬得很。
搅拌的时候可别太大力,轻轻地,慢慢地,像是在呵护一个小宝宝。
要知道,搅拌得好,浆料才能呈现出最佳状态。
这样一来,涂在壳上的浆料,才能如丝般顺滑。
说完这些,得提醒大家,制壳的环境也不能忽视。
温度、湿度这些都对浆料的性能有影响。
太热了,浆料会干得快,根本来不及用;太潮湿了,浆料反而不容易干,搞得一团糟。
所以,得在合适的环境下工作,就像开车,路况好,车才开得快,安全。
在实际操作中,得准备好一些工具,比如涂刷的工具、测量的工具。
制壳总结报告

总结报告尊敬的各位领导、同事们你们好:首先,自我介绍一下:我是制壳车间的一名沾浆工,我叫XXX。
今天非常荣幸的能够站到这里和大家见面,我感到十分激动。
在这里我要感谢公司及车间主任对我的信任与栽培、同时也要感谢同事们对我的支持,我才会有今天的成绩。
谢谢!2011年已经成为历史,在这期间我们的公司、车间发生了很大的变化。
新员工的增加、老员工技术经验的提高;公司新产品的增多、以及公司的面貌发生了很大的变化,这都是在公司领导的英明领导下才能够有今天的成绩。
在这一年里,作为在基层工作的我感觉到自身的素质提高了、工作的技能、经验提高了、为人处事的能力也提高了,下面我就把我的工作向大家汇报一下。
目前为止我来到公司已有3年的时间了,我从事于制壳的面层工序,我能够做到不迟到、不早退,对于领导交代的工作能够不折不扣的执行,在团结同事方面我能够做到团结合作、互帮互助,对待每一种产品我能够做到认真的操作,精心的操作,能够做到提前预防,为达到“零”缺陷的目标我能够以百倍的努力来实现。
制壳车间的质量缺陷有:漏壳、凸起、脊状、鼓包、夹砂等缺陷,环境温湿度、材料、特别是人员的操作是影响缺陷形成的主要因素。
每周质量情况主任都会开会告诉大家本周的质量情况,漏壳的比例、夹砂的比例、突起的比例等等,同时组织大家一起来分析问题产生的原因以及解决的办法。
对于我从事的面层主要的缺陷问题就是突起、夹砂,对于凸起来讲造成缺陷产生的主要原因是:由于我们在操作面层时沾浆速度快,有气泡没有吹破;锆砂中有颗粒没有及时筛干净、浆液中有气泡没有调好浆液所造成都会引起突起的产生,浇注后铸件就会形成小钢豆,对后工序修件造成增加工作量,特别是一些凹坑件如BPE1#,尖角处如HDLE 856、FPQ962等尖角处有钢豆严重的就没办法修理,会直接造成废品,还有一些产品在字块处产生钢豆,字块会由于钢豆不清晰,甚至造成废品。
对于夹砂来讲:形成的原因主要是有几个方面:1、蜡树有焊缝、模头有孔洞、有气泡在沾面层浆时,浆液就会进到焊缝及孔洞中去,最终形成夹砂。
精铸硅溶胶型壳工艺的改进
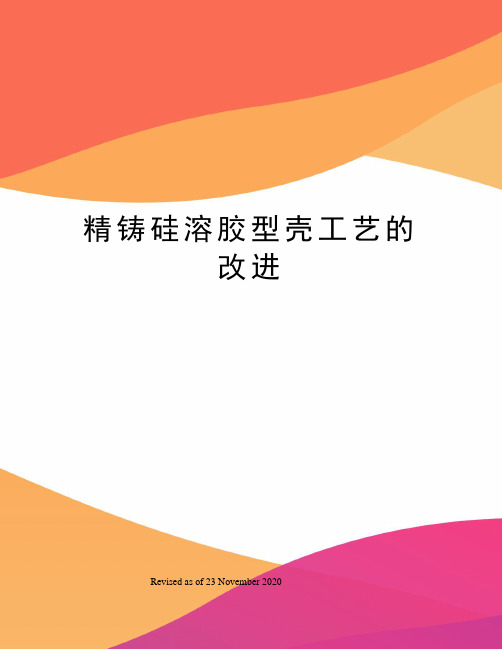
精铸硅溶胶型壳工艺的改进Revised as of 23 November 2020一.前言:众所周知,全球精铸界通用的硅溶胶型壳工艺存在三大缺点:1.成本高。
2.制壳周期长。
3.铸件脱壳性差(型壳残留强度高)。
据统计,表面层型壳通用的耐火料锆英石砂、粉占型壳原辅材料成本的4 8%,占总生产成本的10%(平均值)[1] 。
优质锆英石资源稀缺,因而寻找它的代用品或减少其消耗量是当今国内外精铸界共同关心,重点研究的课题之一。
“快干”硅溶胶的推广应用和真空干燥设备的逐步完善,缓解了制壳周期长的缺点。
由于硅溶胶型壳高温强度高(是水玻璃型壳的倍),其相应的残留强度也高(是水玻璃型壳的倍),因而铸件的脱壳性能比水玻璃差得多。
加之大部分生产的精铸件是结构复杂的中小件,型壳残留强度高会严重影响后处理工序生产效率和增加材料工时成本、降低铸件表面质量,延误交货期。
我们通过学习国内外同行的先进经验,经过多年的努力研究和实践,在降低硅溶胶型壳生产成本和改善脱壳性方面取得了一定成效,特向精铸界同仁作一介绍,以期达到抛砖引玉的目的。
二.表面层制壳工艺的改进:〈一〉. 锆英石粉料的代用—长期以来锆英石是全球精铸业首选的型壳表面层耐火料。
正如2007年美国精铸学会(ICI)第54届年会论文所言:“锆英石与多种合金反应低、密度高、热化学性能好,要寻找替代用品是困难的”。
[2]1.美国在2006年前面层涂料的典型工艺是在锆英粉中掺加5-10%(质量)的熔融石英粉。
其主要目的是:降低成本,提高铸件尺寸精度和改善脱壳性、透气性。
国外重点工艺改进方向是:充分利用熔融石英纯度高,杂质少,密度和热膨胀系数小,加上高温“析晶”,低温“相变”的特点,使型壳在高温时保持高强度而在低温时因相变产生剧烈收缩(%)致使型壳残留强度大大降低,从而使铸件脱壳性、透气性、尺寸精度提高。
自2007年起,通过技术改进美国已有80%的精铸企业表面层涂料中的熔融石英粉掺入量已提高至50%(按体积比为%)。
- 1、下载文档前请自行甄别文档内容的完整性,平台不提供额外的编辑、内容补充、找答案等附加服务。
- 2、"仅部分预览"的文档,不可在线预览部分如存在完整性等问题,可反馈申请退款(可完整预览的文档不适用该条件!)。
- 3、如文档侵犯您的权益,请联系客服反馈,我们会尽快为您处理(人工客服工作时间:9:00-18:30)。
46.10 46.09 表 1 锆英粉与锆英粉+熔融石英粉混合浆尺寸精度对比
图 3A 左 锆英粉+熔融石英粉混合浆,撒锆英砂 Fig.3 Left Zircon-powder + Melting Quartz Powder Admixture pulp,Caesar Zircon-Sand
图 3A 右 锆英粉浆,撒锆英砂 Fig.3A Right Zircon-powder pulp, Caesar Zircon-Sand
3 电熔刚玉耐火材料应用于面层 电熔刚玉(俗称白刚玉)是工业氧化铝,经高温熔融,冷却结晶成三氧
化二铝,应用于熔模铸造的à-Al2O3 属于三方晶系,是氧化铝变体中最稳 定的一种。电熔刚玉的熔点高,密度大,导热性好,热膨胀系数小,结构 致密,铝、锰、锡、钴、铁、铬、镍、硅等元素都不与它发生反应,有良 好的化学稳定性。所以,早在硅溶胶-锆英粉面层制壳工艺引进之前,硅 酸乙酯水解液-刚玉粉、砂制壳工艺已经广泛应于军工生产、航空工业, 高温合金真空浇注增压器叶轮,见图 7,就是此
图 3 B 吊角铸件照片 材质 316 Fig.3B Lifting of Angle Casting Photos Materials 316
2.2 锆英粉-熔融石英粉浆-撒熔融石英砂 此工艺的浆料配制、干燥时间等工艺参数同 2.1,面层撒 100~120
目熔融石英砂,第二层及以后,同全硅溶胶结壳工艺参数。 生产实践效果,该浆料的粉液比不要不太高,流动性与全锆英粉相似,制 壳可操作性好,干燥时间比 2.1 还可以短些,尺寸精度好,不粘砂,质量 稳定,溃散性优于锆英粉锆英砂,铸件表面质量和尺寸精度达到 2.1 的水 准。见图 4 所示
图 5 能谱分析报告单 着重提及,美国对熔模铸造用锆砂的化学成分要求十分苛求,将二氧 化硅列为杂质,其限量为 33.02%;三氧化二铁的限量为 0.03%。可见, 对于锆英砂这种天然矿物材料,必须经过后续深加工、严格去除杂质,才 能保证良好的铸造品质。 应用于熔模铸造的电熔刚玉之基体物质是三氧化二铝,是稳定的同质 变体à-Al2O3 晶相,杂质三氧化二铁≤0.10%、氧化钠≤0.60%,有理由 相信,目前许多精铸厂家“弃锆英,择刚玉”的缘故不仅仅是因为价格的 因素。 硅溶胶-白刚玉粉浆-撒白刚玉砂
寸精度高,不粘砂,溃散性同于全锆英粉浆料。 该混合面层浆料,适用于较大、壁厚较厚的铸件,例如泵类、阀类铸件 上应用。大多数采用低温模料,浇注 300 系列奥氏体不锈钢铸件表面粗糙 度粗糙度可达 Ra ≤6.3,尺寸精度可达到 CT4 级,浇注碳钢、低合金钢 更理想,见图 1 所示。制壳成本比全锆英粉浆料降低 60-70%。 1.2 莫来砂做面层撒砂材料 锆英石与高岭石这两种耐火材料有着良好的兼容性和复合性,所以, 面层砂采用以莫来砂替代锆英砂。 面层配浆工艺如下: 粉液比(325 目锆英粉): 1:3.3~3.4 粘度值(詹氏 4#):42~45s 润湿剂:10kg 面层硅溶胶加 28ml
目棕刚玉砂;第六层只粘浆,不撒砂。 环境控制:温度 18~27℃;湿度 60%~80%。 涂料干燥工艺:自干 1.5~2h;风干 1.5~2h;氨干 0.5 h,氨气流量:表面 层 10~15 L/min; 加固层 10~20 L/min。 采用中国标准杯体积测定粘度。
再将电熔刚玉的主要成分及杂质与锆英砂作一个比较,见表 2: 电熔刚玉 Al2O3≥98.5 Fe2O3≤0.10 1 级锆砂 ZrO2≥65 Fe2O3≤0.30 2 级锆砂 ZrO2≥63 Fe2O3≤0.70 3 级锆砂 ZrO2≥60 Fe2O3≤1.00 表 2 电熔刚玉与锆英砂成分比较表
图 2 阀芯 粗抛后铸件表面粗糙度 材质 1.4408 该工艺适用于机械件、水暖管件等壁厚不是很厚的铸件上应用,低、 中温模料的蜡模均可使用。浇注 300 系列奥氏体不锈钢、沉淀不锈钢,铸 件表面粗糙度比撒锆英砂逊色不了多少,若浇注碳钢、低合金钢,铸件表 面粗糙度与撒锆英砂达到同等水准。制壳成本比撒锆英砂降低 80 %。
2 熔融石英作面层材料 近年来,国外先进的工业国家,用于制壳的耐火材料发生明显的变化,
锆英石使用得最少,熔融石英大幅上升,这与国内的情况绝然不同。熔融 石英的热膨胀系数在所有耐火材料中堪称最小,型壳在脱蜡和焙烧过程中 的开裂、变形倾向最小,型壳高温抗蠕变性能优秀,使得铸件尺寸稳定,
故尔,将熔融石英引入面层材料有理论、实践依据。 2.1 锆英粉-熔融石英粉混合浆-撒锆英砂 面层配浆工艺如下: 锆英粉:熔融石英粉 = 85%:15% 粉液比: 1:3.2 粘度值(詹氏 4#):42~45s 润湿剂:10kg 面层硅溶胶加 30ml 消泡剂:10kg 面层硅溶胶加 22ml 面层撒砂:100~120 目锆英砂 面层干燥时间:6~7h 环境条件:温度 22~25℃;湿度 22~25% 第二层及以后,相同于全硅溶胶结壳工艺,具体的工艺参数相同于全硅溶 胶结壳工艺。 通过较长时间的生产应用,这种混合浆料与锆英砂的粘结力良好,浆料流 淌均匀,沾浆、撒砂的可操作性优于全锆英粉浆料,采用中温蜡,则铸件 表面粗糙度为 Ra 6.3~3.2,见图 3 所示,
面层配浆工艺如下: 粉液比: 1:3.4~3.45(白刚玉) 粘度值(詹氏 4#):40~45s 润湿剂:10kg 面层硅溶胶加 27ml 消泡剂:10kg 面层硅溶胶加 19ml
面层撒砂:小件 100 目白刚玉砂 大件 70 目白刚玉砂 面层干燥时间:8~10h 环境条件:温度 22~25℃;湿度 22~25% 第三层及以后,水玻璃结壳工艺。
图 4 三通 未经抛丸的铸件表面粗糙度 材质 35CrMo 该工艺适用于汽车零件和一般机械零件,低、中温模料的蜡模均可使用,
笔者推荐浇注碳钢、低合金钢产品。制壳成本比锆英粉锆英砂降低 40 % 左右。
面层结壳材料 专用粉+熔融石英浆 撒专用砂 图纸尺寸 尺寸名称 (mm)
面层结壳材料
锆英粉浆料 撒锆英砂
尺寸精度 CT 3~5,见表 1。加入熔融石英粉的 质量分数一般是 15%,若超过 15%,铸件表面会产生毛剌,笔者所用的熔 融石英是国内产品,其二氧化硅的纯度以及熔融后冷却转变为非晶型的工
艺与国外产品相比存在一定的差异,所以,该浆料的粉液比不宜太高,流 动性与全锆英粉相似,干燥时间适当可以短一点,溃散性优于全锆英粉浆 料。 该工艺适用于生产汽车零件和精密机械零件,面层制壳成本比全锆英粉降 低约 25%左右。
面层制壳工艺研究
熔模铸造表面层制壳工艺的研究 景宗梁 车顺强 (郑州大禹化工产品有限公司) 摘 要 近年来,熔模铸造硅溶胶工艺表面层制壳工艺呈现新的改进,例 如熔融石英粉、莫来粉、砂、精铸专用粉、砂等应用于面层,使面层耐火 材料从单一品种发展为多品化,充分发挥出不同材料之间铸造性能上的互 补性,显示出多种耐火材料特性的优化组合,形成了多档次的面层结壳工 艺,使铸件表面质量持续保持优秀,尺寸精度稳定,从而,制壳生产成本 大幅度下降。另外,水玻璃工艺面层引入新材料,成为水玻璃制壳工艺的 新亮点。
关键词 表面涂层;混合浆料;耐火材料的优化组合
全硅溶胶结壳工艺的面层结壳耐火材料一直采用价格昂贵的锆英粉 和锆英砂,据统计,制壳材料成本占精铸成本的 30%左右,耐火材料占制壳 材料成本的 80%左右,而面层的材料成本占整个制壳材料成本的五分之三, 所以,必须突破传统工艺的束搏,改进面层材料的应用,创新面层结壳工 艺,降低面层制壳的生产成本。
环境条件:温度 22~25℃;湿度 22~25 第二层及以后,采用莫来粉浆、 撒莫来砂,工艺参数仍然是全硅溶胶结壳工艺,脱蜡及焙烧工艺也相同于 全硅溶胶结壳工艺。
图 1 前盖 脱壳后未经抛丸铸件的表面粗糙度 材质 304 生产实践效果,此混合浆料的涂挂性好,易于操作,有助于面层强度和耐火 度的提高,铸件表面粗糙度接近于全锆英粉浆料,尺
奥氏体不锈钢铸件,表面产生“麻点”和“黑点”的概率相当高,为了弄 清楚“麻点”和“黑点”究竟是什么物质,探究产生“麻点”和“黑点” 的原由,笔者采用进口能谱仪对表面缺陷(黑点)部位进行微区成分检测, 见图 5。
报告显示二氧化硅(质量分数,%)高达 18.90,接着,质控部再检 验近期进的锆英粉和锆英砂的铁含量,三氧化二铁达到 0.82%,“析硅” 现象得到求证,说明:锆英石材料中的三氧化二铁含量超标是产生“麻点” 和“黑点”的主要原因。
消泡剂:10kg 面层硅溶胶加 20ml 面层撒砂:100 目莫来砂 面层干燥时间:第二层及以后,采用莫来粉浆、撒莫来砂,具体的工艺参数相同于全硅溶 胶结壳工艺。
生产实践结果,面层浆料的粉液比及粘度值要相应适当提高,砂与浆 层的结合力好,若采用浮砂机撒砂,则效果更佳,干燥时间略长。铸件表 面粗糙度可达 Ra 6.3,尺寸精度达到 CT4 级,质量稳定,不粘砂,溃散 性同于锆英粉锆英砂。见图 2 所示。
1.1 莫来粉作面层粉料 将莫来粉加入到锆英粉中,从理论组成分析:硅酸锆中的三分之一是
二氧化硅,铝-硅系材料中的二分之一强是二氧化硅,锆粉与莫来粉混合, 二者中的二氧化硅应该是相似相溶,不发生排斥,仅增加了氧化铝组分, 氧化铝与氧化锆这两种氧化物互不干扰,独立存在,形成三元组合混物 ZrO2-Al2O3-SiO2,兼容性良好,晶相组织理论分析可行。 面层配浆工艺如下: 粉液比: 1:3.4~3.5 锆英粉:莫来粉 320 目(熟料) = 1:1 粘度值(詹氏 4#):34±1s 润湿剂:10kg 面层硅溶胶加 30ml 消泡剂:10kg 面层硅溶胶加 22ml 面层撒砂:90~120 目锆英砂 面层干燥时间:7~8h
生产效果,电熔刚玉的密度较大(3.99~4.0g/cm3),该浆料的粉液 比可以配得比较高,浆料流动性与锆英粉相差无几,粘浆、撒砂的可操作 性好,干燥时间适当可以短一点,质量稳定,表面粗糙度 Ra 6.3,尺寸精 度只有 CT 5~7 级。缺点是:铸件的深孔、狭槽处有轻度的粘砂,此部位 的溃散性也稍差。该工艺采用低温模料,十分适宜做各种阀门、阀体类大 件,浇注材质 300 系列奥氏体不锈钢和 316 Ti,见图 6。