降低整机生产不良率QCC
QCC降低生产不良圈名及口号

QCC降低生产不良圈名及口号1. 生产质量标语口号个人比较推崇的一句:做质量没有任何借口下面是网上找的:最佳答案市场是海,质量是船,品牌是帆。
今日的质量,明日的市场。
筑质量长城,兴中华经济。
ISO9000—效率、效益之源。
构造“质量、环境、安全”——一体化的管理体系。
建有质量文化的质量体系,创造有魅力、有灵魂的质量。
未来的成功属于质量领先者的世纪。
21 世纪——质量领先者的世纪。
铸造辉煌,唯有质量。
品质的优劣比成本更重要。
以质量求生存,以质量求发展,向质量要效益。
以质量求生存,以改革求发展。
品质合格是尽社会的义务,品质卓越是对社会的贡献。
质量是成功的伙伴,贯标是质量的保障。
和传统的昨天告别,向规范的未来迈进。
只有步入国际标准的轨道,才有无限延伸的空间。
用户是企业发展的源泉。
正视危机、增强信心、艰苦奋斗、再创辉煌。
增强紧迫感、加强责任心、全力抢市场、打好翻身仗。
能上能下,能进能出,唯才是举,唯能是用。
转变观念,转变作风,创新机制,创新局面。
把生命注入到产品中去,产品就会在市场上活起来。
制造须靠低成本,竞争依赖高品质。
用心血融铸经营理念,让企业文化生生不息。
树立核心价值观,而且要善于学习,更要善于创造。
质量是企业的生命。
]品质—企业致胜的关键。
雄关漫道真如铁,而今迈步从头越。
立足新起点,开创新局面。
百尽竿头,更进一步。
今天的付出,明天的回报。
筑质量大堤,迎世纪挑战。
让高质量的产品乘着环宇风帆,冲出亚洲、走向世界。
让环宇风帆载着优质的产品,跨越21 世纪。
跨越今日的视野、扩展21 世纪的眼光。
春种一粒粟、秋收万颗籽。
走进质量天地,带来无限商机。
质量存在于人类生存的一切地方。
质量—带给你看得见的未来,说不出的精彩。
跨过ISO9000 的门廊,进入21 世纪的殿堂。
贯标九千,飞越二千。
时代精神演绎民族灵魂,优质精神构筑时代精神。
效益来源于服务社会的回报。
质量是企业的生命,为了保护您的生命,请为您的企业建立质量保证体系。
降低整机生产不良率QCC

降低整机生产不良率QCC1. 引言在整机生产过程中,不良率是一个重要的指标,直接影响产品质量和生产效率。
因此,采取一系列的质量控制措施是至关重要的。
本文将介绍一种质量控制方法,即QCC(Quality Control Circle),旨在帮助企业降低整机生产不良率。
2. QCC概述QCC是一种以小组为单位的员工参与的质量管理方法。
通过成立质量控制小组,通过小组成员的参与和协作,发现并解决生产过程中的问题,从而降低产品不良率。
QCC的核心思想是追求持续改进和全员参与,提高整体生产质量。
3. QCC的实施步骤3.1 小组成立首先,需要成立一个质量控制小组。
小组成员应涵盖生产线上的各个关键环节,包括工人、质检员、技术人员等,并确保小组成员具备相应的培训和技能。
3.2 问题识别与数据收集小组成员应该定期收集和分析整机生产过程中出现的问题和缺陷。
通过数据分析,找出生产过程中存在的主要问题和症结所在。
3.3 问题分析和改进方案制定小组成员应对收集到的问题进行分析,并制定相应的改进方案。
在制定改进方案时,应充分考虑实际操作情况、工艺流程和设备条件等因素。
3.4 实施改进方案小组成员应积极实施制定的改进方案,并跟踪记录改进效果。
在实施改进方案时,需要保持团队合作和沟通,确保改进措施得到有效执行。
3.5 持续改进QCC是一个连续的过程,小组成员应定期评估改进效果,并根据评估结果进行调整和改进。
通过持续改进,不断提高整机生产的质量水平。
4. QCC的优势4.1 全员参与QCC鼓励全员参与,通过集思广益,充分发挥员工的智慧和创造力,能够更全面地发现和解决问题。
此外,全员参与还能增强员工的责任感和归属感,提高整体生产效率。
4.2 快速改进QCC的小组成员具有多种技能和经验,能够快速分析问题并制定相应的改进方案。
由于小组成员紧密合作,能够及时进行实施和跟踪,实现快速改进。
4.3 持续改进QCC强调持续改进的理念,小组成员不断评估和调整改进方案,通过不断地优化和改进,提高整体生产质量。
QCC降低设备故障率

目的和意义
目的
通过实施QCC活动,降低设备故障率,提高生产效率和产品质量,实现企业可 持续发展。
意义
降低设备故障率有助于提高企业的生产效益和竞争力,同时能够减少维修和停 机时间,降低生产成本。此外,QCC活动还有助于培养员工的团队协作和持续 改进意识,促进企业文化的建设。
02 QCC(质量控制圈)介绍
01
QCC成员对设备进行定期检查,及时发现潜在的故障或问题,
确保设备正常运行。
故障诊断与修复
02
QCC成员具备一定程度的设备维修技能,能够快速诊断和修复设备故障,减少停机来自间。预防性维护03
通过分析设备运行数据和故障模式,QCC制定相应的维护计划,
降低设备故障率。
QCC的运作方式
制定计划
制定详细的实施计划,包括目 标、时间安排、人员分工等。
安全事故风险增加
设备故障可能引发安全事 故,给企业员工和财产带 来威胁。
04 QCC降低设备故障率的实 施方案
确定问题并提出解决方案
确定设备故障率高的原因
通过数据收集和分析,确定导致设备故障的主要原因,如设 备老化、操作不规范、维护不足等。
提出解决方案
针对确定的问题,制定相应的解决方案,如更新设备、规范 操作流程、加强维护保养等。
设备故障率定义及影响
设备故障率定义
设备故障率是指设备在运行过程中出现故障的概率,通常以设备故障次数与设备 运行总时间的比值来计算。
设备故障率影响
设备故障率高会增加企业的维修成本、影响生产效率和产品质量,甚至可能引发 安全事故,给企业带来重大损失。
设备故障率高的原因分析
设备老化
设备长时间运行,缺乏必要的维护和保养,导致设备性能下降, 容易发生故障。
品质保证圈QCC汇报稿

品质保证圈QCC汇报稿1. 概述本文档是品质保证圈QCC(Quality Control Circle)的汇报稿,旨在总结和分享我们团队的活动和成果。
2. 活动描述我们的品质保证圈团队致力于提升产品质量和工作效率。
在过去的一段时间里,我们进行了一系列的活动,包括但不限于:- 定期召开QCC会议,讨论产品质量问题和解决方案;- 实施质量报告分析,发现潜在的问题和改进机会;- 进行QCC培训和知识分享,提升团队成员的技能和意识。
3. 活动成果我们的活动取得了一些显著的成果,包括:- 降低产品不良率:通过QCC团队成员的努力,我们成功减少了产品的不良率,提高了产品的质量水平;- 提高工作效率:通过改进工作流程和引入新的方法和工具,我们成功提高了工作效率,减少了工作中的浪费;- 强化团队协作:QCC活动促进了团队成员之间的沟通和协作,加强了团队的凝聚力和效能。
4. 经验与展望在过去的活动中,我们积累了一些宝贵的经验和教训,例如:- 重视团队成员的参与和反馈:每个团队成员的经验和意见都是宝贵的资源,应该积极倾听和尊重;- 持续改进:品质保证是一个持续的过程,我们应该不断改进和优化流程和方法,以追求更高的质量和效率;- 推广经验和成果:我们应该积极向其他团队和部门分享我们的经验和成果,以帮助整个组织提升品质管理水平。
展望未来,我们将继续努力,不断探索和创新,为公司的持续发展贡献更大的努力。
5. 结语品质保证圈QCC的活动已经成为我们团队不可或缺的一部分,我们将继续秉持着持续改进的原则,为提升产品质量和工作效率而努力。
感谢所有团队成员的辛勤付出和支持!谢谢。
QCC_降低设备故障率

确定 课题
降低故障率
三、活动计划
为了开展好活动,我们制定了详细的活动计划。
计划与实施进度 项目
计划
完成
采用 手法
三 月
四 月
五 月
六 月
七 月
八 月
九 月
十 月
十一 月
地 点
负责人
可行性分 析 目标确定
调查表 柱状图 排列图 鱼骨图 图 表 车 间
周宁华 吴利祥
P
原因分析 主因确定 制定对策
周宁华 汤静怡
十二、目标值检查
故障率6.5%
故障率5% 故障
故障 运 行
故障率4.9%
故障
运
行 运
行
活动前
目标值 活动后
经济效益
效益测算:通过QC维修小组成员的共同努力,实现故障率降至5%
以下的目标,即提高了有效的生产时间,从而提高产量,稳定质量: 1、年提高产量计算:2、社会效益:减少了随机停机概率,保证订单及 时完成,保障公司信誉。 3、其他:稳定、提高了产品质量,为车间开发多种高附加值产品提供 了坚实的设备保障;保障了设备的安全稳定运行。
检修 保养
1.分解落实 1.极大减少因缺少备件造成的 1.明确包机责任人对所包机设备备件的 统计责任;2.严格对包机人所包设备因 备件计划责 停机故障。 缺少备件造成长时间停机的考核。 任
对因排查不到位造成的设备故障严格考 2.使包机责任人加强设备巡查, 核 及时发现隐患部位
1.对备件型号的正确性把关
二、计划检修、保养不及时
系统相对较为复杂,润滑点众多,液压装备运用广泛,电气、机械系统 运行精度较高,因此检修计划不周全,润滑保养不到位、定期更换不及 时均造成不确定性停机现象频繁出现。
QCC_降低设备故障率

车 间 现 场
吴利祥 周宁华
周宁华 吴利祥
汤静怡
根据确定的两个要因,小组成员讨论研究,制定出可实施性对策表
十一、对策实施
要 因 一
备件计划不周,全缺少备件
对策实施
分解落实备件计划责任 2.严格备品备件审批制度
2、由材料 员定期调查 仓库库存 技术员调查 备件部位的 实际状况
1.明确包 机责任人 对所包机 设备备件 的统计责 任;
■确认方法: 现场调查
■标准和内容 to add Text : 设备配置满足生
to add Text 产需求
• Click to add Text
结论
结论
结论
• Click to add Text
技能考试: 95%符合
■负责人:周宁华
工作考评: 99%符合
■负责人:汤静怡
• Click to add Text 现场调查: 公 • Click to add Text 司加大了对部分老 现场调查: 设备的改,基本满 99%符合 足生产需求
目标值切实 可行
素质 具备
主观 意愿
由和 众多技术骨干组成的小组成员具备较高的理论知识和实 践经验。
设备主管技术部门对目标制定充分肯定;全体 QC小组成员和班组成员、技术骨干充满信心。
七、故障率高原因分析
利用排列图法查找故障率高的末端原因
故障率 系统名称 故障时间 故障率高的因素 循环水 系统 压缩 空气 系统 传动系统
建立、完善各设备机组备件档案
2.对照备件库存情况,调整购 由材料员定期调查仓库库存 技术员调查备件部位的实际状况 买计划,避免重复采购
1.严格执行备用设备倒替运行制度;2.备 机故障立即修复。
QCC案例提高总装下线一次合格率QC小组

现 场
9月
李/
3
现 场
9月
胡/
4
调整模具动程及相 关联的定位。
现 场
10 月
孙/
八、对策实施:
1.安装尺寸存在偏差
(11.91~11.92)
(15.34~16.6)
0 16 -0.1
(4.62~4.63) 5
31.5 (31.1~31.14)
一、实施: 1.经过现场测试,侧板多处尺寸存在偏差(上图括号内数据为实 际测量偏差值); 2.根据图纸要求,重新整改模具底部,使其达到标准。 二、效果检验: 整改之后,由此引起的尺寸偏差现象彻底根治了。
十一、 今后打算:
通过本次活动,大 家增强了分析问题、解 决问题的能力,今后我 们将把提高相关机种的 工艺问题作为下一个 FDAR循环解决。
谢谢 Thanks
验证: 1、侧板与后背板安装出现 侧板外倾。 2、侧板外倾角度偏差的主要 原因是第二道模具动程偏小.
非要因
2、对二道成型模具动程调整 后,现场安装验证已消除角 度倾斜。
六、要因验证:
6、成型模具动模动程较小
验证:
1、 成型作业,动模对定 模进行冲压成型后,制品 起翘,成型后角度测量为 98°38′,标准要求为 90°±2 ° ,角度超标。
制表人:/ 时 间:2004.6
活动概况
课题 小组名称 成立日期 迅雷QC小组 2002.08 攻关型 1020040602 2004.6—2005.2 活动32次
提 高总 装一 次下 线合 格率
课题类型 注册编号
本次活动时间 活动次数
制表人:/ 时 间:2004.6
二、选题理由:
实际与指标差异2%
不良率降低改进方案,品质管理改善办法,提升产品质量
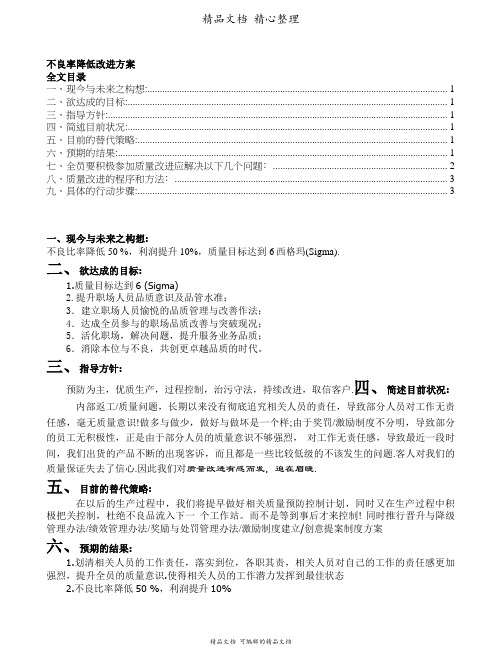
不良率降低改进方案全文目录一、现今与未来之构想: (1)二、欲达成的目标: (1)三、指导方针: (1)四、简述目前状况: (1)五、目前的替代策略: (1)六、预期的结果: (1)七、全员要积极参加质量改进应解决以下几个问题﹕ (2)八、质量改进的程序和方法﹕ (3)九、具体的行动步骤: (3)一、现今与未来之构想:不良比率降低50 %,利润提升10%,质量目标达到6西格玛(Sigma).二、欲达成的目标:1.质量目标达到6 (Sigma)2.提升职场人员品质意识及品管水准;3.建立职场人员愉悦的品质管理与改善作法;4.达成全员参与的职场品质改善与突破现况;5.活化职场,解决问题,提升服务业务品质;6.消除本位与不良,共创更卓越品质的时代。
三、指导方针:预防为主,优质生产,过程控制,治污守法,持续改进,取信客户.四、简述目前状况:内部返工/质量问题,长期以来没有彻底追究相关人员的责任,导致部分人员对工作无责任感,毫无质量意识!做多与做少,做好与做坏是一个样;由于奖罚/激励制度不分明,导致部分的员工无积极性,正是由于部分人员的质量意识不够强烈,对工作无责任感,导致最近一段时间,我们出货的产品不断的出现客诉,而且都是一些比较低级的不该发生的问题.客人对我们的质量保证失去了信心.因此我们对质量改进有感而发,迫在眉睫.五、目前的替代策略:在以后的生产过程中,我们将提早做好相关质量预防控制计划,同时又在生产过程中积极把关控制,杜绝不良品流入下一个工作站。
而不是等到事后才来控制! 同时推行晋升与降级管理办法/绩效管理办法/奖励与处罚管理办法/激励制度建立/创意提案制度方案六、预期的结果:1.划清相关人员的工作责任,落实到位,各职其责,相关人员对自己的工作的责任感更加强烈,提升全员的质量意识.使得相关人员的工作潜力发挥到最佳状态2.不良比率降低50 %,利润提升10%3.引导员工本着自动自发精神,运用各种改善手法,启发个人潜能,透过团队力量,结合群体智慧,群策群力,持续地从事各种问题的改善;而能使每一位成员有参与感、满足感、成七、全员要积极参加质量改进应解决以下几个问题﹕1﹒增强质量意识﹐决心改革。
40页生产工厂制造企业品管圈QCC之降低MYFRDC砂芯不良率

根据主题,制定详细的品管圈活动计划,包 括活动目标、实施步骤、时间安排等。
品管圈的活动计划
数据收集
收集MYFRDC砂芯不良率的相关数据 ,进行统计分析,找出问题所在。
制定改进措施
针对分析出的问题,制定相应的改进 措施,包括优化生产工艺、改善设备
性能、加强原材料检测等。
原因分析
分析砂芯不良率高的原因,从原材料 、生产工艺、设备、环境等方面进行 深入探讨。
02 现状分析
砂芯不良率的现状
01
当前砂芯不良率:20%
02
历史砂芯不良率:最高达到30%
03
存在的问题:高不良率导致生产效率降低、成本增 加、客户满意度下降
砂芯不良率的原因分析
原材料问题
砂子质量不稳定,导致砂芯强度不足。
设备老化
部分生产设备老化,无法保证砂芯的精度和 表面质量。
工人操作不规范
部分工人未严格按照操作规程进行生产,导 致砂芯出现裂纹、气孔等问题。
生产环境不佳
车间温度、湿度控制不当,影响砂芯的成型 和固化。
砂芯不良率的影响分析
01
生产成本增加
高不良率导致需要大量返工和重制 ,增加了生产成本。
客户满意度下降
不良品可能导致产品性能下降,影 响客户的使用体验和满意度。
03
02
交货期延误
标准化与推广
将本次QCC活动中成功的措施和方法 标准化,并在企业内推广应用,以提 高整个企业的生产质量和效率。
05 成果展示与总结
成果展示
MYFRDC砂芯不良率下降
通过品管圈活动,MYFRDC砂芯的不良率从活动前的20%降低到了活动后的5%,实现 了显著的改善。
改进措施实施情况
降低整机生产不良率QCC

改善前
改善后 FOR Weekly Chart
持续改善
0.60%
Jun09
Jul
Aug w936 w937 w938 w939 w940 w941 w942 w943 w944 w945 w946 w947
FOR 1.68% 1.70% 1.62% 1.51% 1.55% 1.49% 1.43% 1.41% 1.37% 1.38% 1.32% 1.28% 1.23% 1.25% 1.21% Target 1.50% 1.50% 1.50% 1.45% 1.45% 1.45% 1.45% 1.30% 1.30% 1.30% 1.30% 1.30% 1.20% 1.20% 1.20% 1.20%
肖 兵 8.17--8.27
6 机芯检焊不良
王贤文 8.17--8.27
7 机心操作不良
何文志 8.17--8.27
我们首先通过Pareto确定部品不良中的主要缺陷:
部品不良Pareto分析图
40 37
35
34 33
37.2%
39.0%
40.8%
45.0% 42.7%
40.0%
35.1%
35.0%
我们的目标是将FOR下降30%,即目标设定为由目前的1.70% 降低为1.20%;
2.00%
1.70%
目标设定
目标这么严 格,我们能 达到吗?
1.50%
设定目标
1.00%
1.45% 1.30% 1.20%
0.50%
0.00% 现状
一期目标(Sep) 二期目标(Oct)三期目标(Nov)
整机操作不良 5%
本单位存在的问题是
选定课题
我得想个好办法降低质 量管理成本
- 1、下载文档前请自行甄别文档内容的完整性,平台不提供额外的编辑、内容补充、找答案等附加服务。
- 2、"仅部分预览"的文档,不可在线预览部分如存在完整性等问题,可反馈申请退款(可完整预览的文档不适用该条件!)。
- 3、如文档侵犯您的权益,请联系客服反馈,我们会尽快为您处理(人工客服工作时间:9:00-18:30)。
FOR
Target
w948
LETTER OF APPRECIATION
Plan
效果检查确认、巩固措 施及总结等计划12月份完成.
选择矩阵
56 工程
20.0%
26 设计
25
0.0% 整机操作
2.对故故障类型按照饼型图做进一步的分析:
工厂内部可 控制的不
良,且预计改 善所需时间及 效果会比较显 著
整机操作不良 5%
其他不良 8%
部品不良 31%
涵盖的种类多且 大多符合质量协 议要求,因此我 们只关注批量性 问题
机芯相关不良 31%
部品不良
700 647
600 500 400 300
81.8% 517
69.3%
55.2% 299 264
87.8%
91.5%
94.2%
根据质量改善 的二八原则, 这应该是我们
改善的重点
96.8%
98.1%
99.2%100.0% 80.0% 60.0% 40.0%
200
30.7%
100
126 77 57
0 部品 CRT不良 机芯手插 机芯操作 机芯检焊 整机装配 副板
本单位存在的问题是
选定课题
我得想个好办法降低质 量管理成本
1.目前生产不良率与既定的目标存在差距, 造成生产效率降低,生产成本增加; 2.主要客户对目前的质量水平有一定程度的 ,期望提升我司质量控制水平;
降低整机生产不良率—FOR
--选取产量占总整机产量70%的A产品
2.20% 1.80% 1.40% 1.00%
对策实施(五) :增加剪钳管理流程/制定修理作业指引 对策实施(六) :规范员工取板方法
对策实施(七) :改善设计缺陷(CN801由单体更改为连体)
更改前
对策实施(八) :提高ICT测试覆盖率
更改后
测试率大 幅提高
对策实施(九) :减少员工插件数量等 改改 善善 前后
改改 善善 前后
2.00% 1.80% 1.60% 1.40% 1.20% 1.00% 0.80%
其他不良 8%
部品不良 31%
改进估算
项目 占总 实际 目标 备注 说明 不良 FOR%
1 CRT 25% 0.42% 0.30% •技术相当成熟 彩管
2 •机芯 31% 0.55% 0.25% •出货SKD线不良0.25%
3 部品 31% 0.52% 0.42% 降低0.1%是非常有希 望达到的;
是
否合格
C1 D1
是是
是是
E1 F1 G1 H1 J1
是
是是
是是
是
是是
是是
结论:员工操作不良不是主要原因。
要因确认二:检查工装夹具是否规范:
因为IC对ESD防护要求很高,我们重点检查生产线静电敏感工位及生产线 ESD防护是否符合要求;
线体传输带及调试、 检测工位静电胶皮 效果良好
静电敏感工位、 线体ESD防护、 员工静电防护 符合要求
标
存
软件与CRT匹配存在缺陷
在
机芯手插不良 主要不良 漏插、插反/插错、飞脚
差
距
机芯相关不良
机芯检焊不良 主要不良
虚焊、连焊
仔细分析 认真对待
员工操作不良 主要不良 铜断、断脚、板面异物
1.首先排除小组成员不能改变的供应商来料不良. 2.针对剩下的7条末端因素制定了要因确认计划表,分工负责进行逐一确认.
30
33.0%
26 29.8%
25
30.0%
23.9% 20
25.0%
20.0%
15
16.3%
10 8.5%
IC及晶1振4 、 15.0%
声表不良是
9
9
重点
8
8
8
10.0%
5
5.0%
0 IC201
IC101
SAW101
X801
IC402
C239
L102
C211
C308
C424
0.0%
要因确认一:检查员工操作:
NG
结论:工装夹具不规范是主要原因。
要因确认三:检查QC检验员是否熟练掌握标准:
• 对标准把握不清,容易造成误判
2) 供应商也曾反馈部分QC判定有疑问
对此我们进行试验确认: 6名QC检验员
检验中较难判断的(A)聚焦 及(B)线性不良
检验人员进行判定是否合格,结果如下:
姓名
AA
KK
RR
DD
判断的准确率 100% 87.5% 100% 100%
确定主因计划表
No 项目
确认内容
确认方法
判别标准
负责人 日期
1 员工不良操作 检查操作的规范性 导致
1.作业者是否有相关 1.是否符合公司要求。 谭 强
的资格证明。
2.考核合格
2.进行现场考核。
8.17--8.19
2 工装夹具不规 包装或运输生产物料 现场测量调查
范导致
时工装是否符合要求
是否符合工装规格 张繁荣 8.17--8.20 及要求
我们的目标是将FOR下降30%,即目标设定为由目前的1.70% 降低为1.20%;
2.00%
1.70%
目标设定
目标这么严 格,我们能 达到吗?
1.50%
设定目标
1.00%
1.45% 1.30% 1.20%
0.50%
0.00% 现状
一期目标(Sep) 二期目标(Oct)三期目标(Nov)
整机操作不良 5%
肖 兵 8.17--8.27
6 机芯检焊不良
王贤文 8.17--8.27
7 机心操作不良
何文志 8.17--8.27
我们首先通过Pareto确定部品不良中的主要缺陷:
部品不良Pareto分析图
40 37
35
34 33
37.2%
39.0%
40.8%
45.0% 42.7%
40.0%
35.1%
35.0%
Dec 1.76% 2.00%
Jan-09 1.85% 1.50%
Feb 1.81% 1.50%
Mar 1.86% 1.50%
Apr 1.74% 1.50%
May 1.71% 1.50%
Jun 1.68% 1.50%
Jul 1.70% 1.50%
Aug 1.50%
目前FOR 水平为1.70%左右,与既定的目标存在差距;
SS 87.5%
GG 100%
结论:QC检验人员误判不是主要原因。
要因确认四:软件与CRT匹配存在缺陷;
白平偏色 2% C2%RT defect classification
飞色2% 3%
色纯不良 3%
会聚不良 4%
漏气 5%
脱粉 23%
供应商、设计师及SQM 共 同会议讨论,确认关机彩 斑不良的50%都是由于软 件与CRT匹配缺陷造成的
改善前
改善后 FOR Weekly Chart
持续改善
0.60%
Jun09
Jul
Aug w936 w937 w938 w939 w940 w941 w942 w943 w944 w945 w946 w947
FOR 1.68% 1.70% 1.62% 1.51% 1.55% 1.49% 1.43% 1.41% 1.37% 1.38% 1.32% 1.28% 1.23% 1.25% 1.21% Target 1.50% 1.50% 1.50% 1.45% 1.45% 1.45% 1.45% 1.30% 1.30% 1.30% 1.30% 1.30% 1.20% 1.20% 1.20% 1.20%
137
128
120
116
73.9%
79.0%
81.9%
84.5%
86.6%
88.7% 90.0% 80.0% 70.0%
65.6% 100
60.0%
55.3%
80 71
50.0%
60
38.5%
40 19.9%
20
将前三项 57
40.0%
做为改善 的重点
30.0%
35
20.0%
20
18
15
14
10.0%
达到 == --目标
1.20% 1.70%减去 (-12%)+(0.3%)+(0.1%) =1.18%
机芯相关不良 31%
CRT不良 25%
故障类型 饼型图
部品不良 CRT我们取09年5月到7月份质量日报按照故障类型制定Pareto,以确认改善方向:
故障类型Pareto
CRT不良 机芯相关不良
其他不良
CRT不良 25%
整机操作不良
改善周期长,主 要通过供应商
方面进行改善
3.采用系统图对FOR不良前三项做进一步的分析:
FOR
部品不良
不
良
率
供应商来料不良 员工不良操作导致 工装夹具不规范导致 供应商来料不良
9条末端因素
不可控制因素
与
目
CRT不良
QC检验员工误判所致
可控制因素
课题名称
制造总部海外分厂
小 组 名: 雄 鹰 参与部门:质量工程/生产/SQM
小组简介
1、小组名称:啄木鸟小组 2、所属单位:制造总部海外分厂 3、课题类型:现场型
4、活动时间:09.07.01—09.12.31 5、活动次数:15次 6、出席率 :85%
小组成员
组长:王杰
顾问 客 服 部 总 监:张 总 质量工程部经理:莫小荣