陶瓷的烧结
陶瓷烧结

目前,微波烧结技术已经被广泛用于多种陶瓷复合 材料的试验研究材料直接耦合导致整体加热。
(2)微波烧结升温速度快,烧结时间短。 (3)安全无污染。 (4)能实现空间选择性烧结。
材料与微波场的作用类型
材料与微波的作用方式示意图
微波烧结系统
5 )反应烧结
反应烧结(reaction-bonded sintering)是让原料混合 物发生固相反应或原料混合物与外加气(液)体发生 围—气(液)反应,以合成材料,或者对反应后的反应 体施加其它处理工艺以加工成所需材料的一种技术 。
是将粉末压坯或装入包套的粉料装入高压容器中,使粉 料经受高温和均衡压力的作用,被烧结成致密件。
其基本原理是:以气体作为压力介质,使材料(粉 料、坯体或烧结体)在加热过程中经受各向均衡的压力, 借助高温和高压的共同作用促进材料的致密化。 目前,热等静压技术的主要应用有:金属和陶瓷的 固结,金刚石刀具的烧结,铸件质量的修复和改善,高 性能磁性材料及靶材的致密化。
(2)具备快熔快冷性,有利于保持粉末的优异特性;
(3)可以使 Si3N4,SiC 等非热熔性陶瓷在无需添加
烧结助剂的情况下 发生烧结。
间接法爆炸烧结装置(a.单面飞片; b.单活塞;c.双活塞)
直接法爆炸烧结装置
谢谢大家!
1)热压烧结
热压烧结(hot pressing)是在烧结过程中同时对
坯料施加压力,加速了致密化的过程。所以热压 烧结的温度更低,烧结时间更短。
热压技术已有70年历史,最早用于碳化钨和钨粉致密件的 制备。现在已广泛应用于陶瓷、粉末冶金和复合材料的生 产。
热压烧结的优点
(1)所需的成型压力仅为冷压法的1/10
烧结装置
烧结系统大致由 四个部分组成:真空 烧结腔(图中6), 加压系统(图中3), 测温系统(图中7) 和控制反馈系统。图 中1示意石墨模具,2 代表用于电流传导的 石墨板,4是石墨模 具中的压头,5是烧 结样品。
陶瓷烧结PPT课件

未来研究方向与展望
新材料与新工艺的开发
跨学科合作与技术融合
智能化与数字化技术的 应用
未来,研究者们将继续探索新型陶瓷 材料,研究新的烧结工艺和技术,以 满足各种应用需求。同时,如何实现 陶瓷材料的绿色生产和降低成本也是 未来的重要研究方向。
陶瓷烧结技术涉及到材料科学、物理 学、化学等多个学科领域,未来的研 究将更加注重跨学科的合作和技术融 合,以推动陶瓷材料的发展和应用。
还原气氛
可以还原杂质,提高陶瓷的纯度。
压力的影响
常压烧结
是最常见的烧结方式,适用于大多数 陶瓷材料。
加压烧结
在加压条件下,可以促进陶瓷的致密 化,提高其性能。
05
陶瓷烧结的质量控制与检测
质量控制方法
原料质量控制
对原料的化学成分、粒度、含水 率等指标进行严格检测和控制,
确保原料质量稳定。
工艺参数控制
在烧结过程中,对温度、压力、气 氛等工艺参数进行精确控制,以获 得最佳的烧结效果。
设备维护与校准
定期对烧结设备进行维护和校准, 确保设备运行稳定,提高产品的重 复性和可靠性。
性能检测与评价
物理性能检测
检测产品的密度、气孔率、热膨 胀系数等物理性能指标,确保产
品性能符合要求。
力学性能检测
通过抗弯强度、抗压强度等力学 性能试验,评估产品的机械性能
和可靠性。
耐腐蚀性能检测
对产品的耐酸、耐碱、耐热等性 能进行检测,以适应不同环境下
的使用要求。
缺陷分析与改进
缺陷识别
通过外观检查、无损检测等方法,识别产品中的 缺陷和问题。
原因分析
对缺陷产生的原因进行深入分析,找出根本原因 并制定相应的改进措施。
陶瓷烧结方法
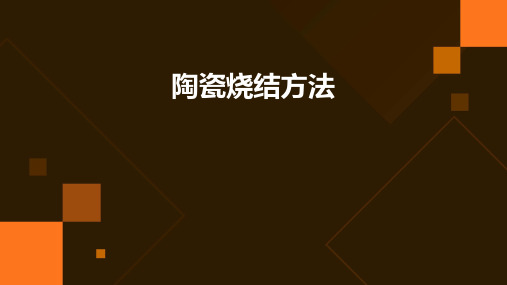
马弗炉是一种传统的陶瓷烧成设备,具有结构简单、操作方便、加 热速度快等优点。
应用范围
适用于各种陶瓷材料的烧成、烧结和熔融等工艺过程,特别适合于 大规模生产。
使用注意事项
使用马弗炉时应注意安全,避免烫伤和火灾事故;同时应注意炉温的 控制和炉内气氛的调节,以保证烧成效果。
真空炉
特点
真空炉是在真空环境下进行加热的设备,具有高温、高真 空的特点,可以有效地去除材料中的气体和杂质,提高产 品的纯度和性能。
02
烧结方法的分类
固相烧结
01
02
03
定义
固相烧结是陶瓷材料在完 全或部分熔融状态下获得 致密化的过程。
特点
固相烧结过程中不出现液 相,致密化主要依靠颗粒 重排、扩散传质和颗粒表 面能的驱动。
应用
适用于制备高熔点、低导 热系数、低塑性的陶瓷材 料,如氧化铝、氮化硅等。
液相烧结
定义
01
液相烧结是通过添加可熔性组分(如金属、玻璃或其它陶瓷材
在复合材料中的应用
树脂基复合材料
通过烧结方法制备树脂基复合材料,提高材料的强度、刚度和耐 腐蚀性。
碳纤维复合材料
通过烧结方法制备碳纤维复合材料,实现材料的轻量化和高性能 化。
玻璃纤维复合材料
通过烧结方法制备玻璃纤维复合材料,提高材料的强度和耐热性。
感谢您的观看
THANKS
瓷材料的致密度和力学性能。
应用
适用于制备形状复杂、细孔结构的陶 瓷制品,如蜂窝陶瓷、多层陶瓷电容
器等。
03
烧结工艺参数
温度
低温烧结
低温烧结通常在1000℃以下进行,适用于对热敏感的材料,如某些玻璃或陶瓷。低温烧结可以减少材料内部的热应力, 降低烧结温度对材料性能的影响。
《陶瓷材料的烧结》课件

对废弃的陶瓷材料进行回收和再利用,实现资源的循环利用,降 低对自然资源的依赖。
THANKS。
致密度、均匀性和性能。
烧结设备的改进
03
随着技术的进步,烧结设备的性能和效率也将得到提升,为陶
瓷材料的制备提供更好的设备支持。
环保和可持续发展在陶瓷烧结领域的应用
环保材料的研发
为了降低陶瓷产业对环境的影响,未来将大力研发环保型的陶瓷 材料,如低毒陶瓷、可降解陶瓷等。
节能减排技术的应用
通过采用新型的节能技术,降低陶瓷烧结过程中的能耗和排放, 实现低碳、环保的生产。
04
陶瓷材料的烧结性能
烧结密度和孔隙率
烧结密度
烧结后的陶瓷材料密度,影响材料的 机械性能和热学性能。
孔隙率
陶瓷材料内部孔隙的多少,与材料的 强度、热导率和绝缘性能有关。
烧结陶瓷的力学性能
01
硬度
烧结陶瓷的硬度取决于其成分和 显微结构,硬度高的陶瓷耐磨、 耐划痕。
02
03
抗弯强度
韧性
陶瓷抵抗弯曲应力的能力,与材 料的成分、显微结构和制备工艺 有关。
航天器结构材料
陶瓷材料具有轻质、高强度和耐高温的特性,适用于航天器结构材料,如卫星天线骨架、太阳能电池板支架等。
06
未来展望
新型陶瓷材料的开发
高性能陶瓷
随着科技的发展,对陶瓷材料性能的要求越来越高,未来 将开发出具有更高强度、硬度、耐磨性、耐高温等高性能 的新型陶瓷材料。
多功能陶瓷
除了传统的结构陶瓷外,未来还将开发出具有多种功能如 导电、导热、压电、磁性等功能的新型陶瓷材料。
05
陶瓷材料的烧结应用
在电子行业的应用
电子封装
陶瓷材料的烧结与晶粒生长
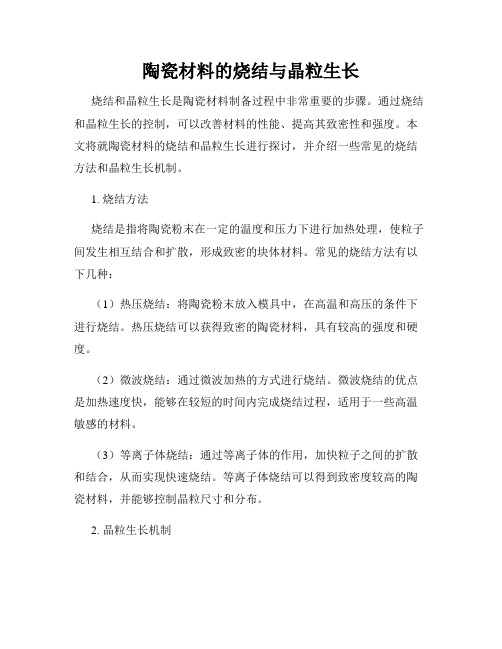
陶瓷材料的烧结与晶粒生长烧结和晶粒生长是陶瓷材料制备过程中非常重要的步骤。
通过烧结和晶粒生长的控制,可以改善材料的性能、提高其致密性和强度。
本文将就陶瓷材料的烧结和晶粒生长进行探讨,并介绍一些常见的烧结方法和晶粒生长机制。
1. 烧结方法烧结是指将陶瓷粉末在一定的温度和压力下进行加热处理,使粒子间发生相互结合和扩散,形成致密的块体材料。
常见的烧结方法有以下几种:(1)热压烧结:将陶瓷粉末放入模具中,在高温和高压的条件下进行烧结。
热压烧结可以获得致密的陶瓷材料,具有较高的强度和硬度。
(2)微波烧结:通过微波加热的方式进行烧结。
微波烧结的优点是加热速度快,能够在较短的时间内完成烧结过程,适用于一些高温敏感的材料。
(3)等离子体烧结:通过等离子体的作用,加快粒子之间的扩散和结合,从而实现快速烧结。
等离子体烧结可以得到致密度较高的陶瓷材料,并能够控制晶粒尺寸和分布。
2. 晶粒生长机制晶粒生长是指陶瓷材料在烧结过程中晶粒尺寸的增大。
晶粒尺寸的大小和分布对陶瓷材料的性能有着重要的影响。
常见的晶粒生长机制包括以下几种:(1)一维生长:晶粒沿着某个方向生长,呈现出棒状或柱状的形态。
一维生长机制适用于一些具有纤维状结构的陶瓷材料。
(2)表面扩散:晶粒表面发生扩散,并与周围的颗粒结合。
表面扩散是晶粒生长的主要机制之一,通过控制晶粒表面的扩散速率,可以调控晶粒尺寸和形态。
(3)体内扩散:晶粒内部的原子通过扩散运动,使晶粒尺寸增大。
体内扩散主要取决于材料的化学成分和温度条件。
3. 影响烧结和晶粒生长的因素烧结和晶粒生长受到多种因素的影响,下面介绍其中几个重要的因素:(1)温度:温度是烧结和晶粒生长的关键因素之一。
适当的温度可以促进晶粒的结合和生长,但过高的温度可能引起过烧,导致晶粒长大过快。
(2)压力:压力可以提高粒子的结合程度和致密性,对烧结效果有重要影响。
不同材料和形状的陶瓷,适宜的压力范围也有所不同。
(3)时间:烧结时间影响烧结程度和晶粒生长的速率。
陶瓷的特种烧结方法

陶瓷的特种烧结方法陶瓷烧结是将陶瓷粉末转变为坚硬、致密和均质的陶瓷体的过程。
在传统烧结方法上,高温烧结严重影响了陶瓷晶体的生长和致密化程度,同时易出现微裂纹及材料不均匀等问题。
为了解决这些问题,并提高陶瓷材料的性能及成纤网络形态,一些特种烧结方法被发展出来。
1. 微波烧结法微波烧结利用微波辐射,刺激陶瓷颗粒内部产生电磁波吸收现象,从而使物料内部产生局部加热,加速物料烧结过程,达到陶瓷晶体快速成长和致密化的效果。
同时,微波烧结可以实现快速均一化和高效化,提高了材料的成型和烧结速度,避免了材料的因温度差异引起的变形和启口。
2. 等离子烧结法等离子烧结是在真空或气氛中,通过引入高压等离子体激发陶瓷粉体表面覆盖的气体分子形成碘原子或硝基自由基等等离子体与材料反应,进而形成坚硬、致密和均质的陶瓷体。
这种方法可以避免烧结过程中存在的微孔和烧结反应不充分情况,具有优异的形成特性和微观结构调控能力。
3. 热等静压法热等静压法是将原始陶瓷粉末制成绿坯,用模具加压热压成形,然后加热进一步烧结而成的一种方法。
绿坯制备通过脱模后即可以直接进行热加压,克服了冷压而在烧结阶段固体化程度较低的缺点,可提高陶瓷材料的致密度和性能,同时可以实现复杂形状烧结。
快速烧结法在短时间内,快速加热陶瓷样品到一定温度,并控制在一定时间后,快速冷却而达到致密化和晶体生长的效果。
这种方法可以提高烧结的速度,降低了烧结过程中的氧化作用和烧结后的裂纹等问题,可以克服传统烧结方法中的很多缺陷,同时可以实现高温烧结。
总之,特种烧结方法的发展极大地提高了陶瓷材料的性能和应用,创新技术不断涌现,如等离子烧结、微波烧结、热等静压法和快速烧结法等,在实际应用中具有广泛的前景和市场需求。
陶瓷烧结过程中的物理化学变化

陶瓷烧结过程中的物理化学变化陶瓷烧结过程和物理变化:随着温度升高,陶瓷坯体中具有比表面大,表面能较高的粉粒,力图回向降低表面能答的方向变化,不断进行物质迁移,晶界随之移动,气孔逐步排除,产生收缩,使坯体成为具有一定强度的致密的瓷体。
烧结的推动力为表面能。
烧结可分为有液相参加的烧结和纯固相烧结两类。
烧结过程对陶瓷生产具有很重要的意义。
为降低烧结温度,扩大烧成范围,通常加入一些添加物作助熔剂,形成少量液相,促进烧结。
如添加少量二氧化硅促进钛酸钡陶瓷烧结;又如添加少量氧化镁、氧化钙、二氧化硅促进氧化铝陶瓷烧结。
陶瓷烧结过程和化学变化:陶瓷的主要成分的化学式是SiO2 在高温下,陶瓷生坯固体颗粒的相互键联,晶粒长大,空隙(气孔)和晶界渐趋减少,通过物质的传递,其总体积收缩,密度增加,最后成为具有某种显微结构的致密多晶烧结体,这种现象称为烧结。
这个过程中包含有物理变化和化学变化瓷是由粘土、石英及长石等天然矿物原料按不同配方配制,经加工、成型及烧成而得,其化学组成取决于所用天然原料及配方,不同地区不同窑口的古陶瓷由于所用原料的不同,配方的不同以及烧制工艺的不同,其胎釉化学组成、显微结构及物理性能就会有各自的特点。
如果收集不同窑口发掘时有可靠地层年代的陶瓷标本进行系统地研究,把积累的数据资料如化学组成数据(包括主次量元素含量以及微量元素含量)建立数据库,并用适当的处理方法,譬如多元统计分析等方法对数据进行处理,找出具有特征意义的规律。
对要鉴定的陶瓷的化学组成、显微结构、物理性能以及烧制工艺等方面进行研究,并将其化学组成数据与已知窑口和年代的古陶瓷的化学组成数据进行比较处理,再综合显微结构、物理性能以及烧制工艺等方面的信息就可能对陶瓷作出鉴定。
陶瓷是混合物,成分特别多而复杂,而且根据陶瓷的产地不同成分也不同。
其主要成分是二氧化硅和硅酸盐(硅酸铝,硅酸钙等)。
陶瓷烧结四个过程

陶瓷烧结四个过程陶瓷烧结是一种重要的陶瓷加工方法,通过高温下的压制和烧结将陶瓷原料转变为致密的陶瓷制品。
它主要包括四个过程:原料制备、成型、烧结和后处理。
一、原料制备陶瓷烧结的第一个过程是原料制备。
通常,陶瓷烧结所用的原料主要包括粉末、添加剂和溶剂。
粉末是陶瓷的主要成分,可以是氧化物、硝酸盐、碳酸盐等,根据不同的陶瓷材料选择合适的粉末。
添加剂用于改善陶瓷的性能,如增加强度、改善导电性等。
溶剂用于调节陶瓷糊料的流动性和粘度。
二、成型成型是陶瓷烧结的第二个过程,它将原料制备好的糊料通过成型工艺转变为成型体。
常见的成型方法有压制、注塑、挤出等。
其中,压制是最常用的方法之一,通过将糊料放入模具中,施加一定的压力使其成型。
注塑则是将糊料注入模具中,通过模具的空腔形状使其成型。
挤出则是将糊料通过挤出机挤出成型。
三、烧结烧结是陶瓷烧结的核心过程,通过高温下的加热和压制使成型体中的颗粒结合成致密的陶瓷制品。
烧结过程中需要控制温度、时间和压力等参数,以确保陶瓷制品的质量。
烧结温度一般高于原料的熔点,但低于熔融温度,使得陶瓷颗粒能够粘结在一起。
烧结压力可以提高陶瓷的致密度和强度,但过高的压力会导致产品变形或开裂。
四、后处理烧结后的陶瓷制品还需要进行后处理,以提高其性能和外观质量。
后处理的方法包括抛光、研磨、清洗等。
抛光和研磨可以去除陶瓷制品表面的粗糙度,使其更加光滑。
清洗则是去除烧结过程中产生的灰尘和残留物,以保证产品的纯净度。
陶瓷烧结的四个过程分别是原料制备、成型、烧结和后处理。
每个过程都起着重要的作用,相互关联,缺一不可。
只有在严格控制每个过程的参数和工艺条件下,才能生产出优质的陶瓷制品。
陶瓷烧结技术的不断发展和改进,使得陶瓷制品在各个领域得到了广泛的应用,如电子、化工、航空等。
先进陶瓷的6种新型快速烧结技术
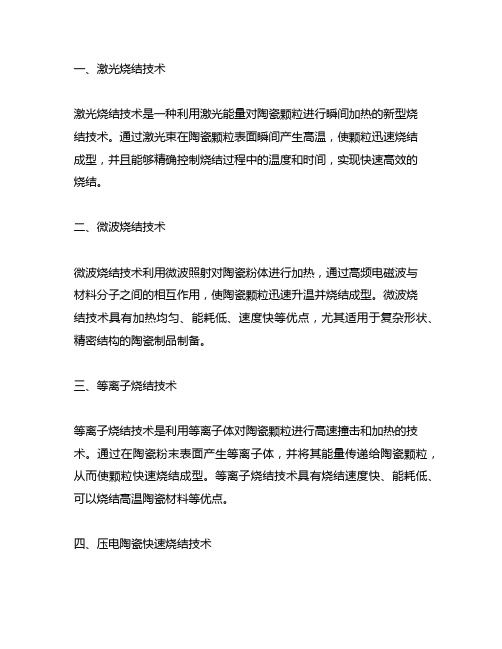
一、激光烧结技术激光烧结技术是一种利用激光能量对陶瓷颗粒进行瞬间加热的新型烧结技术。
通过激光束在陶瓷颗粒表面瞬间产生高温,使颗粒迅速烧结成型,并且能够精确控制烧结过程中的温度和时间,实现快速高效的烧结。
二、微波烧结技术微波烧结技术利用微波照射对陶瓷粉体进行加热,通过高频电磁波与材料分子之间的相互作用,使陶瓷颗粒迅速升温并烧结成型。
微波烧结技术具有加热均匀、能耗低、速度快等优点,尤其适用于复杂形状、精密结构的陶瓷制品制备。
三、等离子烧结技术等离子烧结技术是利用等离子体对陶瓷颗粒进行高速撞击和加热的技术。
通过在陶瓷粉末表面产生等离子体,并将其能量传递给陶瓷颗粒,从而使颗粒快速烧结成型。
等离子烧结技术具有烧结速度快、能耗低、可以烧结高温陶瓷材料等优点。
四、压电陶瓷快速烧结技术压电陶瓷快速烧结技术是一种利用压电作用对陶瓷颗粒进行紧致烧结的技术。
通过施加外加电场,使陶瓷颗粒表面发生压电效应,从而实现颗粒的紧致烧结,烧结速度大大提高,同时制备出的陶瓷制品密度高、性能卓越。
五、等离子喷涂技术等离子喷涂技术是一种利用等离子体对陶瓷粉末进行快速烧结成型的技术。
通过等离子喷涂装置将陶瓷粉末与等离子体混合后,在高温高速气流的作用下迅速烧结成型。
等离子喷涂技术不仅可以实现陶瓷材料的快速烧结,还能够制备出具有优异性能的陶瓷涂层。
六、电磁场烧结技术电磁场烧结技术是一种利用电磁场对陶瓷颗粒进行加热和烧结的技术。
通过在陶瓷颗粒周围建立强磁场或者强电场,使颗粒表面迅速加热并烧结成型。
电磁场烧结技术具有能耗低、烧结速度快、制品性能优异等特点,尤其适用于纳米陶瓷材料的制备。
先进陶瓷的快速烧结技术主要包括激光烧结、微波烧结、等离子烧结、压电陶瓷快速烧结、等离子喷涂和电磁场烧结等多种技术。
这些新型烧结技术都具有烧结速度快、能耗低、制品性能优异等特点,对于提高陶瓷制品的生产效率、降低生产成本、改善产品性能具有重要意义。
随着科技的不断发展和进步,相信这些先进陶瓷的新型快速烧结技术在未来会得到更广泛的应用,为陶瓷制造业带来新的发展机遇。
陶瓷烧结炉工艺原理及烧结方式
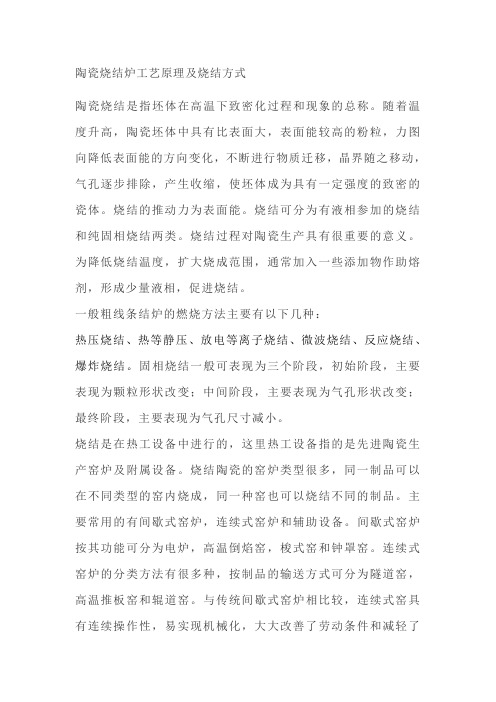
陶瓷烧结炉工艺原理及烧结方式陶瓷烧结是指坯体在高温下致密化过程和现象的总称。
随着温度升高,陶瓷坯体中具有比表面大,表面能较高的粉粒,力图向降低表面能的方向变化,不断进行物质迁移,晶界随之移动,气孔逐步排除,产生收缩,使坯体成为具有一定强度的致密的瓷体。
烧结的推动力为表面能。
烧结可分为有液相参加的烧结和纯固相烧结两类。
烧结过程对陶瓷生产具有很重要的意义。
为降低烧结温度,扩大烧成范围,通常加入一些添加物作助熔剂,形成少量液相,促进烧结。
一般粗线条结炉的燃烧方法主要有以下几种:热压烧结、热等静压、放电等离子烧结、微波烧结、反应烧结、爆炸烧结。
固相烧结一般可表现为三个阶段,初始阶段,主要表现为颗粒形状改变;中间阶段,主要表现为气孔形状改变;最终阶段,主要表现为气孔尺寸减小。
烧结是在热工设备中进行的,这里热工设备指的是先进陶瓷生产窑炉及附属设备。
烧结陶瓷的窑炉类型很多,同一制品可以在不同类型的窑内烧成,同一种窑也可以烧结不同的制品。
主要常用的有间歇式窑炉,连续式窑炉和辅助设备。
间歇式窑炉按其功能可分为电炉,高温倒焰窑,梭式窑和钟罩窑。
连续式窑炉的分类方法有很多种,按制品的输送方式可分为隧道窑,高温推板窑和辊道窑。
与传统间歇式窑炉相比较,连续式窑具有连续操作性,易实现机械化,大大改善了劳动条件和减轻了劳动强度,降低了能耗等优点。
温度制度的确定,包括升温速度,烧成温度,保温时间和冷却速度等参数。
通过飞行坯料在烧成过程中性状变化,初步得出坯体在各温度或时间阶段可以允许的升、降温速度(相图,差热-失重、热膨胀、高温相分析、已有烧结曲线等)。
升温速度:低温阶段,氧化分解阶段,高温阶段。
烧成温度与保温时间:相互制约,可在一定程度上相互补偿,以一次晶粒发展成熟,晶界明显、没有显著的二次晶粒长大,收缩均匀,致密而又耗能少为目的。
冷却速度,随炉冷却,快速冷却。
压力制度的确定,压力制度起着保证温度和气氛制度的作用。
全窑的压力分布根据窑内结构,燃烧种类,制品特性,烧成气氛和装窑密度等因素来确定。
5-4_陶瓷材料的烧结

可广泛用于磁性材料、梯度功能材料、纳米陶瓷、纤维增强陶瓷和金 属间化合物等系列新型材料的烧结。
一、放电等离子体烧结的优点 ①烧结温度低(比HP和HIP低200-300℃)、烧结时间短(只需3-10min, 而HP和HIP需要120-300min)、单件能耗低; ②烧结机理特殊,赋予材料新的结构与性能;
2.2 烧结驱动力
烧结的驱动力就是总界面能的减少。粉末坯体的总界面能表示为 γA, 其中γ为界面能;A为总的比表面积。那么总界面能的减少为:
A A A
其中,界面能的变化(Δγ)是因为样品的致密化,比表面积的变化 是由于晶粒的长大。对于固相烧结,Δγ主要是固/固界面取代固/气界面。
(2)保温时间对产品性能的影响 在烧成的最高温度保持一定的时间,一方面使物理化学变化更趋完全,使 坯体具有足够液相量和适当的晶粒尺寸,另一方面组织结构亦趋均一。但保温 时间过长,则晶粒溶解,不利于在坯中形成坚强骨架,而降低机械性能。 (3)烧成气氛对产品性能的影响 ① 气氛对陶瓷坯体过烧膨胀的影响 ② 气氛对坯体的收缩和烧结的影响 ③ 气氛对坯的颜色和透光度以及釉层质量的影响 (4)升温与降温速度对产品性能的影响
(pore drag)和晶粒生长驱动力之间力的平衡作用。
研究表明,较小的颗粒尺寸分布范围是获取高烧结密度的必要条件。
二、影响陶瓷材料烧结的工艺参数 (1)烧成温度对产品性能的影响 烧成温度是指陶瓷坯体烧成时获得最优性质时的相应温度,即操作时的 止火温度。 烧成温度的高低直接影响晶粒尺寸和数量。对固相扩散或液相重结晶来 说,提高烧成温度是有益的。然而过高的烧成温度对特瓷来说,会因总体晶 粒过大或少数晶粒猛增,破坏组织结构的均匀性,因而产品的机电性能变差。
4.3 晶粒生长和粗化
陶瓷烧结原理
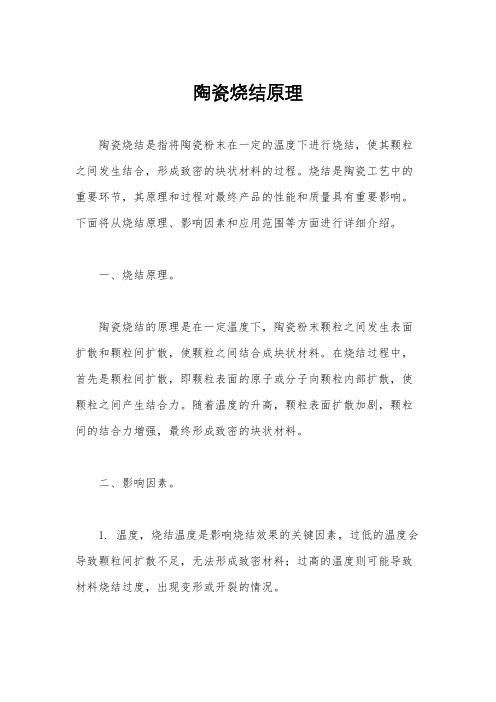
陶瓷烧结原理陶瓷烧结是指将陶瓷粉末在一定的温度下进行烧结,使其颗粒之间发生结合,形成致密的块状材料的过程。
烧结是陶瓷工艺中的重要环节,其原理和过程对最终产品的性能和质量具有重要影响。
下面将从烧结原理、影响因素和应用范围等方面进行详细介绍。
一、烧结原理。
陶瓷烧结的原理是在一定温度下,陶瓷粉末颗粒之间发生表面扩散和颗粒间扩散,使颗粒之间结合成块状材料。
在烧结过程中,首先是颗粒间扩散,即颗粒表面的原子或分子向颗粒内部扩散,使颗粒之间产生结合力。
随着温度的升高,颗粒表面扩散加剧,颗粒间的结合力增强,最终形成致密的块状材料。
二、影响因素。
1. 温度,烧结温度是影响烧结效果的关键因素,过低的温度会导致颗粒间扩散不足,无法形成致密材料;过高的温度则可能导致材料烧结过度,出现变形或开裂的情况。
2. 时间,烧结时间也是影响烧结效果的重要因素,过短的时间会导致烧结不完全,材料性能不达标;过长的时间则可能造成能耗浪费和生产效率低下。
3. 压力,在烧结过程中施加一定的压力可以促进颗粒间的结合,提高烧结效率和材料密度。
4. 添加剂,适量的添加剂可以改善陶瓷粉末的流动性和烧结性能,提高最终产品的质量。
三、应用范围。
陶瓷烧结广泛应用于陶瓷制品的生产过程中,如陶瓷砖、陶瓷器皿、陶瓷瓷砖等。
通过烧结工艺,可以使陶瓷制品具有较高的强度、硬度和耐磨性,满足不同领域的需求。
总结,陶瓷烧结是一项重要的陶瓷加工工艺,其原理是在一定温度下实现颗粒间的结合,影响因素包括温度、时间、压力和添加剂等,应用范围广泛,可用于生产各种陶瓷制品。
掌握烧结原理和技术,对于提高陶瓷制品的质量和性能具有重要意义。
陶瓷烧成机理

1、概述 2、烧结定义 3、烧结的驱动力 4、烧结的机理 5、烧结的过程 6、陶瓷烧结方法
1、概述
烧结过程是一门古老的工艺。现在,烧 结过程在许多工业部门得到广泛应用,如 陶瓷、耐火材料、粉末冶金、超高温材料 等生产过程中都含有烧结过程。烧结的目 的是把粉状材料转变为致密体。 研究物质在烧结过程中的各种物理化学 变化。对指导生产、控制产品质量,研制 新型材料显得特别重要。
4.2.3蒸发-冷凝
由于颗粒表面各处的曲率不同,按开尔文公式: (8) 式中d为液体密度,M为摩尔质量,R为气体常数。 可知,各处相应的蒸气压大小也不同。故质点容易从高 能阶的凸处(如表面)蒸发,然后通过气相传递到低能 阶的凹处(如颈部)凝结,使颗粒的接触面增大,颗粒 和空隙形状改变而使成型体变成具有一定几何形状和性 能的烧结体。这一过程也称气相传质。
6、陶瓷烧结方法
陶瓷烧结方法很多,必须根据对材料烧结 的要求以及具体的实验条件和成本等来进行选 择,以下介绍其中的几种烧结方法。 6.1热压烧结法
将粉体置于压模中,加高温并单轴加压(10~50Mpa), 通过模具热辐射和加压形成塑性变形进行烧结。此法可 以得到高强度和低空隙率的产品,如切削工具等。但是 由于单轴向加压,因此难以进行形状复杂的陶瓷产品的 烧结。
烧结中期晶粒间的界面增大,晶粒开始长大,烧 结温度一般大于0.25Tm(Tm为熔点)。颈的生长以 扩散为主,此时气孔在表面和界面张力作用下达到平 衡并相互连通成连续网络,而颗粒间的界面互相孤立, 未形成连续网络。烧结中期占了整个烧结过程的大部 分时间,通常以烧结体的密度达到理论密度的90%时 标志烧结中期结束。
图1
因此,粘附作用是烧结初始阶段,导致粉体 颗粒间产生键合、靠拢和重排,并开始形成接触 区的一个原因。
陶瓷烧结过程【共23张PPT】

– 钟罩窑、梭式窑 室温就高吸收:CaCO3、Fe2O3、Cr2O3、SiC等
以高压气体作为压力介质作用于陶瓷材料(包封的粉体和素坯,或烧结体),使其在高温环境下受到等静压而达到高致密化 氧化锆,(<2000C)
• 连续式: 氮化硅无熔点、高温分解(1900C)
硅钼棒,MoSi2(<1700C)
• 整体均匀加热 低温吸收小,高于某温度急剧增加:Al2O3、MgO、ZrO2、Si3N4等
利用微波与材料的相互作用,其介电损耗导致陶瓷坯体自身发热而烧结
• 无热惯性,烧成周期短 埋粉(Si3N4:BN:MgO=5:4:1)抑制氮化硅分解
管式气氛炉:电热丝、硅碳、硅钼 为了抑制氮化物分解,在N2气压力1-10MPa高压下烧成。
Al2O3-SiO2)
• 采用α氮化硅为原料,1420C相变为β相,有利烧结, 且该β相为柱状晶,力学性能好。
• 埋粉(Si3N4:BN:MgO=5:4:1)抑制氮化硅分解
氮化硅的气压烧结 (Gas Pressure Sintering GPS)
• 为了抑制氮化物分解,在N2气压力110MPa高压下烧成。
• 对于氮化硅常压烧成温度要低于1800C, 而气压烧结温度可提高到2100-2390C。
热压烧结(Hot Pressing, HP)
• 加热的同时施加机械压力 ,增加烧结驱动力,促进 烧结
– 粘性流动 – 塑性变形 – 晶界滑移 – 颗粒重排
• 一般采用石墨模具,表面 涂覆氮化硼,防止反应
热等静压 (Hot Isostatic Pressing, HIP)
陶瓷烧结过程
烧结的驱动力
• 粉体表面能与界面能的差 • 传质过程
陶瓷烧结工艺

陶瓷烧结工艺
陶瓷烧结是一种将陶瓷粉末通过高温加热,使其颗粒之间发生结合并形成固体陶瓷体的工艺。
烧结的目的是消除粉末之间的孔隙,提高陶瓷的密实度、硬度、强度和耐磨性。
陶瓷烧结工艺主要包括以下几个步骤:
1. 制备陶瓷粉末:选择合适的原料,经过研磨、筛分等处理,将原料粉末制备成所需的颗粒大小和形状。
2. 造型成型:将陶瓷粉末与所需的添加剂混合均匀,然后使用成型方法将混合物制备成所需形状的陶瓷坯体。
常用的成型方法包括注塑成型、压制成型、挤出成型等。
3. 烧结过程:将陶瓷坯体放入烧结炉中,通过高温加热使其逐渐烧结成固体陶瓷。
烧结温度和时间根据陶瓷材料的性质和要求进行调控。
在烧结过程中,陶瓷粉末颗粒之间发生结合,形成致密的陶瓷体,同时消除孔隙。
4. 冷却处理:烧结完成后,将烧结好的陶瓷体从炉中取出,并进行冷却处理。
冷却过程需要慢慢降温,以免陶瓷材料因快速冷却引起应力过大而破裂。
5. 后续处理:根据需要,可以对已烧结的陶瓷体进行后续处理,如磨削、抛光、涂层等,以改善陶瓷产品的表面光洁度、功能特性等。
陶瓷烧结工艺的选择和优化对于陶瓷制品的品质和性能至关重要。
通过合理的烧结工艺,可以获得具有优异力学性能、耐热性、耐腐蚀性和电性能等特点的陶瓷制品。
陶瓷材料的烧结与原理

陶瓷材料的烧结与原理烧结是陶瓷材料加工的重要工艺之一,通过烧结可以使陶瓷材料的颗粒结合成坚实的整体,提高其物理和化学性能。
烧结的原理主要包括粒间结合、扩散和晶粒长大三个方面。
首先是粒间结合。
烧结陶瓷材料的第一步是颗粒的接触,在高温下颗粒接触面出现局部融化,形成粒间结合区。
当局部融化发生时,一些颗粒间的空隙被完全填满,使得颗粒间距变小。
局部熔融的液相材料充当粘结剂,促使颗粒互相结合,形成更加坚固的结构。
其次是扩散。
在烧结过程中,颗粒间的物质会发生扩散,使得局部结合区域的颗粒之间更加牢固地结合。
扩散过程受温度、时间和颗粒之间的距离等因素的影响。
一般来说,扩散速率随着温度的上升而增加,扩散距离也会增加,从而促进了材料的结合。
最后是晶粒长大。
在烧结过程中,由于颗粒间的扩散,晶粒之间的材料也发生了重排和扩散。
在高温下,晶粒会长大,晶界会消失或减少,从而提高陶瓷材料的致密性和力学性能。
晶粒长大的速率受到烧结温度、时间和材料颗粒的尺寸等因素的影响。
除了上述原理外,烧结还受到其他因素的影响,例如:1.烧结温度:烧结温度决定了材料的烧结速率和晶粒长大速率。
温度过高可能导致结构破坏或晶粒过大,温度过低则会导致烧结不完全。
2.烧结时间:烧结时间决定了物质的扩散程度和晶粒的长大程度。
时间过短会导致烧结不完全,时间过长则会导致结构破坏。
3.烧结气氛:烧结过程中的气氛对于陶瓷材料的烧结也有一定影响,不同的气氛可以影响材料的结构和性能。
4.材料的物理和化学性质:材料的物理和化学性质直接影响烧结的过程和结果。
例如,不同成分的材料具有不同的烧结性质。
总之,烧结是陶瓷材料加工过程中不可或缺的一环,通过粒间结合、扩散和晶粒长大等原理,可以实现颗粒间的结合,提高陶瓷材料的致密性和力学性能。
同时,烧结过程中的温度、时间、气氛等因素,以及材料的物理和化学性质,也对烧结的效果产生一定的影响。
以上就是关于陶瓷材料烧结与原理的简要介绍。
陶瓷的特种烧结方法

陶瓷的特种烧结方法
烧结是陶瓷制品生产过程中非常重要的一个环节,直接影响到产品的质量和性能。
为了满足不同行业的需求,人们研发出了多种特种烧结方法,下面介绍几种常用的方法。
1. 高温烧结法
高温烧结法是指将陶瓷制品置于高温下进行烧结,一般温度在1200℃以上。
这种方法可以加快烧结速度,提高产品的硬度和密度,适用于制作高强度、高硬度的陶瓷制品,如切削工具、轴承等。
2. 低温烧结法
低温烧结法是指将陶瓷制品置于较低温度下进行烧结,一般在1100℃以下。
这种方法可以减少能耗,降低成本,适用于制作一些需求较低强度和硬度的陶瓷制品,如餐具、瓷砖等。
3. 微波烧结法
微波烧结法是指将陶瓷制品置于微波辐射下进行烧结。
这种方法可以缩短烧结时间,提高产品的均匀性和致密性,适用于制作高精度的陶瓷制品,如电子器件、光学器件等。
4. 热等静压烧结法
热等静压烧结法是指将陶瓷粉末在高温下进行压缩,再进行烧结。
这种方法可以提高产品的致密性和强度,适用于制作高要求的陶瓷制品,如氧化铝陶瓷刀片、高温炉具等。
总之,不同的烧结方法适用于不同的陶瓷制品,生产者可以根据产品的要求选择合适的烧结方法,以达到最佳的生产效果。
陶瓷烧制中常见烧结问题及解决方法
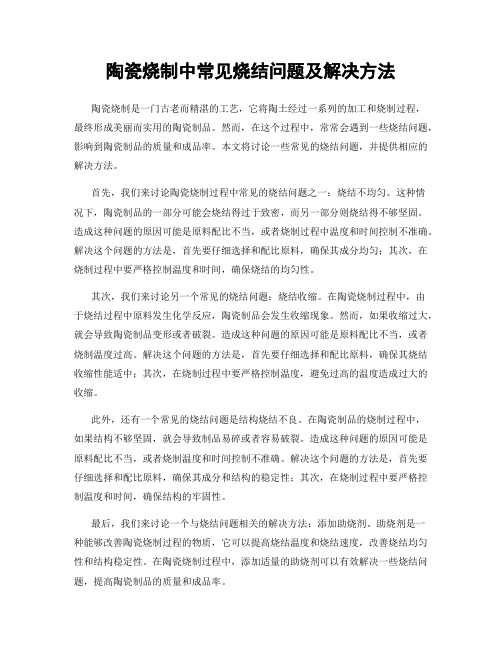
陶瓷烧制中常见烧结问题及解决方法陶瓷烧制是一门古老而精湛的工艺,它将陶土经过一系列的加工和烧制过程,最终形成美丽而实用的陶瓷制品。
然而,在这个过程中,常常会遇到一些烧结问题,影响到陶瓷制品的质量和成品率。
本文将讨论一些常见的烧结问题,并提供相应的解决方法。
首先,我们来讨论陶瓷烧制过程中常见的烧结问题之一:烧结不均匀。
这种情况下,陶瓷制品的一部分可能会烧结得过于致密,而另一部分则烧结得不够坚固。
造成这种问题的原因可能是原料配比不当,或者烧制过程中温度和时间控制不准确。
解决这个问题的方法是,首先要仔细选择和配比原料,确保其成分均匀;其次,在烧制过程中要严格控制温度和时间,确保烧结的均匀性。
其次,我们来讨论另一个常见的烧结问题:烧结收缩。
在陶瓷烧制过程中,由于烧结过程中原料发生化学反应,陶瓷制品会发生收缩现象。
然而,如果收缩过大,就会导致陶瓷制品变形或者破裂。
造成这种问题的原因可能是原料配比不当,或者烧制温度过高。
解决这个问题的方法是,首先要仔细选择和配比原料,确保其烧结收缩性能适中;其次,在烧制过程中要严格控制温度,避免过高的温度造成过大的收缩。
此外,还有一个常见的烧结问题是结构烧结不良。
在陶瓷制品的烧制过程中,如果结构不够坚固,就会导致制品易碎或者容易破裂。
造成这种问题的原因可能是原料配比不当,或者烧制温度和时间控制不准确。
解决这个问题的方法是,首先要仔细选择和配比原料,确保其成分和结构的稳定性;其次,在烧制过程中要严格控制温度和时间,确保结构的牢固性。
最后,我们来讨论一个与烧结问题相关的解决方法:添加助烧剂。
助烧剂是一种能够改善陶瓷烧制过程的物质,它可以提高烧结温度和烧结速度,改善烧结均匀性和结构稳定性。
在陶瓷烧制过程中,添加适量的助烧剂可以有效解决一些烧结问题,提高陶瓷制品的质量和成品率。
综上所述,陶瓷烧制中常见的烧结问题包括烧结不均匀、烧结收缩和结构烧结不良。
这些问题的解决方法包括仔细选择和配比原料、严格控制烧制温度和时间,以及添加适量的助烧剂。
陶瓷真空烧结注意事项
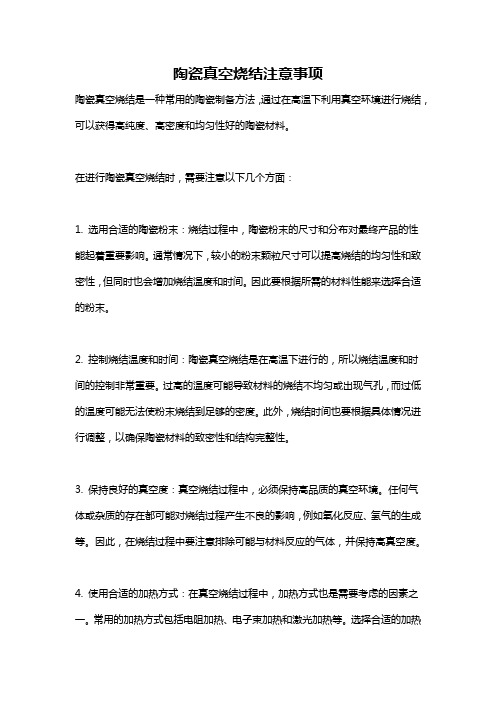
陶瓷真空烧结注意事项陶瓷真空烧结是一种常用的陶瓷制备方法,通过在高温下利用真空环境进行烧结,可以获得高纯度、高密度和均匀性好的陶瓷材料。
在进行陶瓷真空烧结时,需要注意以下几个方面:1. 选用合适的陶瓷粉末:烧结过程中,陶瓷粉末的尺寸和分布对最终产品的性能起着重要影响。
通常情况下,较小的粉末颗粒尺寸可以提高烧结的均匀性和致密性,但同时也会增加烧结温度和时间。
因此要根据所需的材料性能来选择合适的粉末。
2. 控制烧结温度和时间:陶瓷真空烧结是在高温下进行的,所以烧结温度和时间的控制非常重要。
过高的温度可能导致材料的烧结不均匀或出现气孔,而过低的温度可能无法使粉末烧结到足够的密度。
此外,烧结时间也要根据具体情况进行调整,以确保陶瓷材料的致密性和结构完整性。
3. 保持良好的真空度:真空烧结过程中,必须保持高品质的真空环境。
任何气体或杂质的存在都可能对烧结过程产生不良的影响,例如氧化反应、氢气的生成等。
因此,在烧结过程中要注意排除可能与材料反应的气体,并保持高真空度。
4. 使用合适的加热方式:在真空烧结过程中,加热方式也是需要考虑的因素之一。
常用的加热方式包括电阻加热、电子束加热和激光加热等。
选择合适的加热方式可以提高陶瓷材料的烧结效率和质量。
5. 选择适当的脱气程序:在进行陶瓷真空烧结前,通常需要进行脱气处理,以排除粉末和烧结前体中的气体。
脱气程序可以根据不同的陶瓷材料进行调整,包括预热、低温脱气和高温脱气等。
6. 避免二次污染:为了确保陶瓷材料的纯度和质量,需要避免杂质的二次污染。
在操作过程中,要注意使用干净的工具、容器和材料,并严格控制环境中的杂质。
总之,陶瓷真空烧结是一项复杂的工艺,在进行过程中需要注意控制烧结温度和时间、保持良好的真空度、选用合适的陶瓷粉末、使用适当的加热方式、选择合适的脱气程序,并避免二次污染。
通过合理操作,可以获得高质量的陶瓷材料。
- 1、下载文档前请自行甄别文档内容的完整性,平台不提供额外的编辑、内容补充、找答案等附加服务。
- 2、"仅部分预览"的文档,不可在线预览部分如存在完整性等问题,可反馈申请退款(可完整预览的文档不适用该条件!)。
- 3、如文档侵犯您的权益,请联系客服反馈,我们会尽快为您处理(人工客服工作时间:9:00-18:30)。