最新中厚板控制冷却技术的发展
中厚板生产线冷却控制系统改造与实现
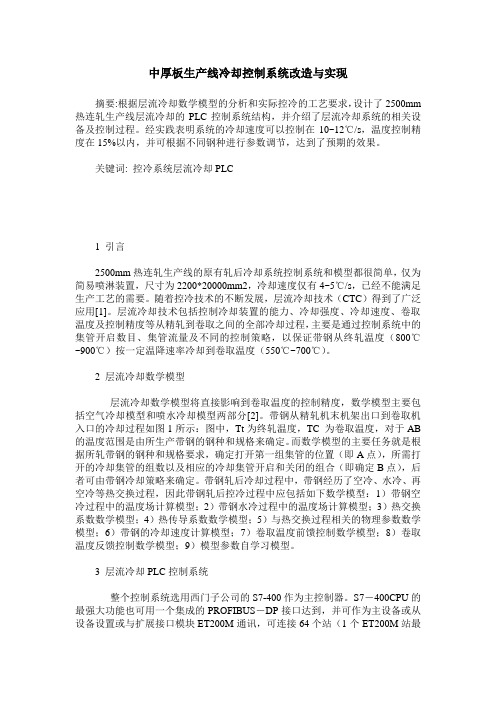
中厚板生产线冷却控制系统改造与实现摘要:根据层流冷却数学模型的分析和实际控冷的工艺要求,设计了2500mm 热连轧生产线层流冷却的PLC控制系统结构,并介绍了层流冷却系统的相关设备及控制过程。
经实践表明系统的冷却速度可以控制在10~12℃/s,温度控制精度在15%以内,并可根据不同钢种进行参数调节,达到了预期的效果。
关键词: 控冷系统层流冷却PLC1 引言2500mm热连轧生产线的原有轧后冷却系统控制系统和模型都很简单,仅为简易喷淋装置,尺寸为2200*20000mm2,冷却速度仅有4~5℃/s,已经不能满足生产工艺的需要。
随着控冷技术的不断发展,层流冷却技术(CTC)得到了广泛应用[1]。
层流冷却技术包括控制冷却装置的能力、冷却强度、冷却速度、卷取温度及控制精度等从精轧到卷取之间的全部冷却过程,主要是通过控制系统中的集管开启数目、集管流量及不同的控制策略,以保证带钢从终轧温度(800℃~900℃)按一定温降速率冷却到卷取温度(550℃~700℃)。
2 层流冷却数学模型层流冷却数学模型将直接影响到卷取温度的控制精度,数学模型主要包括空气冷却模型和喷水冷却模型两部分[2]。
带钢从精轧机末机架出口到卷取机入口的冷却过程如图1所示:图中,Tt为终轧温度,TC 为卷取温度,对于AB 的温度范围是由所生产带钢的钢种和规格来确定。
而数学模型的主要任务就是根据所轧带钢的钢种和规格要求,确定打开第一组集管的位置(即A点),所需打开的冷却集管的组数以及相应的冷却集管开启和关闭的组合(即确定B点),后者可由带钢冷却策略来确定。
带钢轧后冷却过程中,带钢经历了空冷、水冷、再空冷等热交换过程,因此带钢轧后控冷过程中应包括如下数学模型:1)带钢空冷过程中的温度场计算模型;2)带钢水冷过程中的温度场计算模型;3)热交换系数数学模型;4)热传导系数数学模型;5)与热交换过程相关的物理参数数学模型;6)带钢的冷却速度计算模型;7)卷取温度前馈控制数学模型;8)卷取温度反馈控制数学模型;9)模型参数自学习模型。
中厚板正火控制冷却系统的设计与应用

中厚板正火控制冷却系统的设计与应用摘要:中厚板正火控制冷却系统是钢板加热过程中至关重要的一个环节。
本文介绍了该系统的设计和应用,包括液压系统、传动系统、控制系统和冷却系统。
在操作过程中,通过控制液压系统调整钢板的进出速度,以及配置不同的传动系统和冷却系统,可以提高钢板的成品率和质量。
具体实验结果表明,采用中厚板正火控制冷却系统可以使钢板达到更加均匀的温度分布和良好的表面质量。
关键词:中厚板、正火、控制、冷却系统、成品率、质量正文:一、引言中厚板的加热处理中,正火是一个十分重要的工艺环节。
而中厚板正火控制冷却系统则是决定正火工艺质量的关键因素之一。
在钢板加热过程中,采用合理的控制冷却系统可以使钢板达到更加均匀的温度分布和良好的表面质量,从而提高钢板的成品率和质量。
二、设计和应用1.设计原理中厚板正火控制冷却系统是由液压系统、传动系统、控制系统和冷却系统组成的。
在操作过程中,通过控制液压系统的启停和调整,调整钢板的进出速度,以及配置不同的传动系统和冷却系统,使钢板可以达到最优的正火工艺质量。
2.液压系统液压系统是整个控制系统中最重要的部分之一,主要用于钢板的进出速度、合模压力和上下模板移动控制。
通过液压油泵的输出,产生高压油流,驱动静压缸和冷却卷筒,使中厚板在正火过程中保持平稳和平衡。
3.传动系统传动系统是决定中厚板正火控制冷却系统公差的重要因素,主要分为同步传动系统和不同步传动系统,通过不同的传动系统结构来解决钢板进出系统中的同步问题。
4.控制系统控制系统是中厚板正火控制冷却系统的核心部分,主要处理中厚板的各个加热环节,通过不同的控制方式,可以实现钢板的进出控制、温度控制、压力控制和冷却控制等。
5.冷却系统冷却系统是中厚板正火控制冷却系统中最后一步的控制环节,通过钢板温度传感器收集钢板的温度信息,然后通过冷却卷筒将钢板整体冷却到合理的温度范围内,从而达到最优的正火工艺质量。
三、实验结果通过对中厚板正火控制冷却系统的设计和应用分析,实验结果表明,采用中厚板正火控制冷却系统可以使钢板达到更加均匀的温度分布和良好的表面质量,并且可以提高钢板的成品率和质量。
中厚板轧后冷却系统的研究与改进
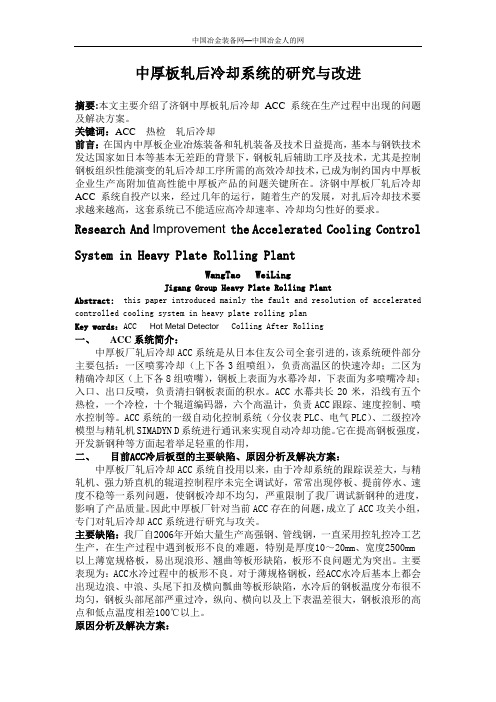
中厚板轧后冷却系统的研究与改进摘要:本文主要介绍了济钢中厚板轧后冷却ACC系统在生产过程中出现的问题及解决方案。
关键词:ACC 热检轧后冷却前言:在国内中厚板企业冶炼装备和轧机装备及技术日益提高,基本与钢铁技术发达国家如日本等基本无差距的背景下,钢板轧后辅助工序及技术,尤其是控制钢板组织性能演变的轧后冷却工序所需的高效冷却技术,已成为制约国内中厚板企业生产高附加值高性能中厚板产品的问题关键所在。
济钢中厚板厂轧后冷却ACC系统自投产以来,经过几年的运行,随着生产的发展,对扎后冷却技术要求越来越高,这套系统已不能适应高冷却速率、冷却均匀性好的要求。
Research And Improvement the Accelerated Cooling Control System in Heavy Plate Rolling PlantWangTao WeiLingJigang Group Heavy Plate Rolling PlantAbstract: this paper introduced mainly the fault and resolution of accelerated controlled cooling system in heavy plate rolling planKey words:ACC Hot Metal Detector Colling After Rolling一、ACC系统简介:中厚板厂轧后冷却ACC系统是从日本住友公司全套引进的,该系统硬件部分主要包括:一区喷雾冷却(上下各3组喷组),负责高温区的快速冷却;二区为精确冷却区(上下各8组喷嘴),钢板上表面为水幕冷却,下表面为多喷嘴冷却;入口、出口反喷,负责清扫钢板表面的积水。
ACC水幕共长20米,沿线有五个热检,一个冷检,十个辊道编码器,六个高温计,负责ACC跟踪、速度控制、喷水控制等。
ACC系统的一级自动化控制系统(分仪表PLC、电气PLC)、二级控冷模型与精轧机SIMADYN D系统进行通讯来实现自动冷却功能。
中厚板轧后冷却技术交流

沸腾强制对流区(区域Ⅲ),
稳温
热量传递须穿过热阻较大的汽
定度 性偏
差
膜导热,换热强度低。
沸腾曲线示意图
气雾冷喷却射冷传却 统加速Su冷pe却r-方OLAC 式
层流冷却
差大 小
小
温度不均匀
大
性能不均匀
大
RAL
中厚板DQ的问题
作为控制冷却的极限结果,DQ的作用早已为人们所认识。 但是,其潜在的能力一直未得到发挥,原因在于直接淬 火条件下冷却均匀性的问题一直没有的到解决,DQ情况 下板形控制一直困扰人们。 国内:宝钢5mDQ、酒钢ADCO DQ采用的技术: 日本厚板厂DQ采用的冷却技术:
•••
出炉,建立微跟踪数据区 预设定计算
•••
控冷区前,微跟踪区域修正设 定计算
末道次,微跟踪触发 修正设定计算
冷却后,模型自学习
RAL
控制系统组成
• 第2级过程控制级:通过数学模型进行设定计算,板坯跟踪, 数据采集,模型自学习,打印报表,人机接口,历史数据存 储,报警等;
• 第1级基础自动化级:顺序控制,设备控制和质量控制,执行 过程机的设定,保证板坯头部、尾部、边部与中间部分的温 度一致。通过控制,使产品冷却速度及全长的温度达到要求 的精度;
膜沸腾,低热交换 核沸腾,高热交换
RAL 3 均匀、高效冷却的基本原理
• 倾斜喷射;压力;较近距离;消除膜态沸腾,实现核 态沸腾;2-5倍的冷却效率
RAL 中厚板加速冷却过程的换热分析
局部换热区域描述
1.射流冲击区
在水流下方和2~3倍水 流宽度的扩展区域内,形成 具有层流流动特性的单相强
表面形态 Ⅰ—单相强制对流 水柱 Ⅱ—核状/过渡沸腾区 Ⅲ—膜状沸腾区 Ⅳ—小液态聚集区 Ⅴ—向环境辐射和对流散热
中厚板轧后控制冷却技术的发展及现状

收稿日期 : 1999 - 03 - 22 作者简介 : 王笑波 (1964~) , 女 (汉族) , 辽宁人 , 讲师 , 博士后 。 国家自然科学基金项目 。
© 1994-2009 China Academic Journal Electronic Publishing House. All rights reserved.
钢板尺寸/ mm
冷却 上喷流 下喷流 方式 形式 形式
ACC、DO 12~80 × 连续式 柱状层流 喷射
4700 ×38000
ACC 10~40 × 同时式 柱状层流 喷射
4500 ×38000
ACC 10~40 ×5350 同时式 柱状层流 喷射
×38000 ,DO 10~150 ×
5300 ×50000
P IC 意大利治金 ACP - 塔兰托厂 奥 钢 联 -
林茨厂 伯利恒 - 伯 ADCO 恩斯港厂 酒钢中板厂 ADCO
劳塔鲁基 MA 厚板厂 ACC
台湾中钢 MD 厚板厂 ACC 俄勒冈 MD 厚板厂 ACC
设备尺寸/ m 418 ×1515 415 ×4410 ACC 5135 ×40100 DO 5135 ×43100 DAC 1417 ×2710 DAC 2417 ×1410 417 ×3911 510 ×1210 316 ×3010 417 ×3010 417 ×2610 410 ×1510 410 ×2219 218 ×1610 3610 ×3210 411 ×2415 316 ×2810
ACC 12~50 × 连续式 幕状层流 喷射
4500 ×50000 , DO 20~
100 ×4500 ×50000
中厚板控轧控冷技术

RAL 中厚板控制轧制与控制冷却技术讲座
为什么进行两相区轧制
RAL Ar3以下压下量与力学性能关系
实验室数据(): 0.17C-1.6Mn钢,
1150℃加热,Ar3为 730℃ 两相区轧制,利用铁素 体的位错亚结构强化
K2.7
RAL 两相区轧制对组织和性能的影响
200织构的 反射强度
K6-2
第三阶段变形量/%
设定要求 • 如果无板凸度调整手段,凸度无法保证,大压下
形同虚设
RAL
比例凸度放松的效果
P 力矩限制 轧制力限制
比例凸度恒定限制
h hn
RAL 板凸度控制手段-双锥度BUR
最大改善30mm
RAL 板凸度调整手段-液压弯辊
BURB WRB
RAL
CVC轧机的凸度调整
等效凸度
横移距离
RAL
PC轧机P的原理与特点
为什么要低温轧制
RAL 轧制温度对组织和力学性能的影响
0.18C-1.36Mn钢 各道次压下量20% 总计9道次轧制到20mm 轧制温度变化范围200℃
K2-3
RAL 热变形奥氏体的温度-压下量-再结晶图
压下量/%
C-Mn钢轧制后1s水冷
K2-13
压下量/%
含铌钢轧制后3s水冷
RAL 900℃以下变形量与韧脆转变温度的关系
* 水幕装置,管层流装置( 直管式, U型管式,气雾式) * 快速响应阀(气动薄膜阀) * 水处理系统 (大流量反冲洗过滤器)
RAL 中厚板控制轧制与控制冷却技术讲座
控轧控冷的基本原理
RAL 2 控轧控冷的基本原理
2.1 控轧控冷机理 2.2 控制轧制
- 轧制温度制度(加热、粗轧、精轧,待温) - 轧制压下制度(粗轧、精轧压下量,方向) - 液压弯辊等板凸度控制制度 2.3 控制冷却ACC - 冷却模式,冷却温度制度 2.4 直接淬火DQ - 淬火温度,回火制度(温度、时间)
9 中厚板的控制轧制与控制冷却

9中厚板的控制轧制与控制冷却9.1中厚板的主要性能指标中厚板轧制过程是钢坯在承受巨大外力作用下产生塑性变形的过程,在整个变形过程中不仅可使钢板获得所必须的尺寸和形状,而且也使之获得所必须的组织和性能。
借助装备水平和自动化程度的提高保证中厚板形状和尺寸精度的相关内容在本书的以上各章已有详细论述,本章将着重介绍在特定的设备条件下,如何通过钢板生产工艺参数的合理控制来获得理想的组织和性能。
中厚板的主要性能指标包括力学性能(屈服强度、抗拉强度、伸长率、冲击功等)、工艺性能(冷弯、冲压、焊接性能等)和理化性能(如耐蚀、耐火性能)等。
根据钢板用途的不同在相关标准中对所要求的各种性能指标都有明确的规定。
如GB/T 1591—94标准对Q345中厚板拉伸、冲击和冷弯性能的规定如表9-1所示。
本节仅就结构钢中厚板中常接触到的几种性能指标介绍如下。
9.1.1强度指标对于结构钢中厚板,在工程中常用的强度指标有:(1)比例极限ζP。
拉伸试样中的弹性变形阶段,应力和应变的关系符合虎克定律,当试样被拉至具有一定的应力时,应力.应变曲线偏离了直线关系。
当该曲线与应力轴夹角的正切值已较直线部分增加50%时,此应力即为该材料的比例极限。
(2)弹性极限ζe。
弹性极限是指完全卸载后不出现任何明显残余应变的最大应力。
弹性极限的高低除受材料本身性质、材料的加工条件和试验条件等各种因素的影响外,还取决于测量应变时所用仪器的灵敏度。
仪器越灵敏,越能在早期检测出塑性变形的出现,则弹性极限的数值就越低。
为了便于比较,技术上规定一个基准的应变量,弹性极限就是产生该基准永久应变量的应力值。
基准量的大小通常确定为10-2%。
为了更早期发现材料的弹性一塑性过渡,就要用更灵敏的测量仪器。
产生2×10-4%残余应变量的应力值称为“真弹性极限”。
这个应力值相当于驱使几百个位错运动的应力,很接近于“临界”的形变应力。
(3)屈服强度ζs。
有屈服效应的材料,在拉伸过程中负荷不增加或有所降低而试样能继续变形的最小负荷所对应的应力称为屈服应力。
【精品】专业论文文献--中厚板轧后控冷技术应用

中厚板轧后控冷技术应用中厚板轧后控冷技术应用摘要:叙述了控制冷却技术对钢材组织性能的影响、控制方式、主要设备、工艺、技术应用,并提出了应用控冷技术应注意的几个问题。
关键词:中厚板;控制冷却技术;应用中图分类号:TF713.2文献标识码:A文章编号:引言:生产中厚钢板的控制冷却技术(ACC)自20世纪80年代初在日本首次投入使用以来,由于它在控制产品的组织和性能,提高产品附加值方面发挥了很大的作用,因而很快在世界范围内被推广应用。
目前控制冷却技术已广泛应用于桥梁、建筑、结构、管道、压力容器用钢生产过程成为当代钢铁工业最重要的技术成就之一。
1.控制冷却技术对钢材性能的影响控制冷却技术是控制轧后钢板的冷却速度从而达到控制钢板组织性能的目的。
控制冷却技术之所以受到重视并得到广泛应用推广,是因为它比经过再加热后的等轴奥氏体加速冷却能产生更大的强化韧性效果,在进一步细化铁素体的同时使珠光体分布均匀,消除带状珠光体,并且有可能形成细贝氏体组织。
此外在控制冷却过程中阻止或延迟了碳化物过早析出,使其在铁素体中弥散,提高钢板强度而不损害脆性转化温度。
2.控制冷却的主要方式目前,中厚板控制冷却方式主要有压力喷射冷却、层流冷却、雾化冷却、喷淋冷却和直接淬火等。
2.1高压喷射冷却水以一定压力从喷嘴喷出,水流连续呈紊流状态喷射到钢板表面。
这种冷却方法穿透性好,一般在水汽膜比较厚的条件下采用。
但是,这种冷却方式用水量大、水花飞溅严重、冷却不均匀、水质要求高、喷嘴易被堵塞而且水的利用率较低。
2.2喷淋冷却将水加压,由喷嘴喷出的水的流速超过连续喷流,水流破断后形成的液滴冲击被冷却的钢板表面。
这种喷嘴冷却能力强,冷却较为均匀,但是需要很高的水压,冷却能力的调节范围较窄,而且对水质要求高。
2.3层流冷却水以较低压力从水口自然连续流出,形成平滑水流。
水流流到钢板表面后在一段距离内仍保持平滑层流状态,可获得很强的冷却能力,冷却均匀。
目前,钢板热轧后的层流冷却一般采用板层流(水幕冷却)和管层流(U形管层流)两种方式。
中厚板控制冷却技术简介

中厚板控制冷却技术简介1控制冷却系统的分类1.1冷却方式按冷却方式的不同,加速冷却可以归纳为三种类型。
(1)同时冷却方式。
即钢板进入冷却装置后,同时向钢板全长喷水使钢板达到规定的温度。
为了避免因辊道与钢板下表面的长时间接触造成冷却不均,冷却装置所在辊道具有摆动功能。
冷却装置的长度比最大的控冷轧件长度略长。
同时冷却方式可减少钢板头尾温差。
(2)连续冷却方式。
即钢板在通过控制冷却装置的过程中,边前进,边冷却,使之从头至尾渐次达到规定的终冷温度。
这是目前世界上采用最多的冷却方式。
(3)兼容冷却方式。
当钢板较厚较短时,可采用同时冷却方式;当钢板较长时,可采用连续冷却方式。
1.2冷却状态冷却状态是指钢板在控制冷却是否处于压力结束状态。
钢板在辊压状态下称为约束型冷却,反之,称为非约束型冷却。
约束型冷却装置主要用于直接淬火处理。
通过改善冷却均匀性,一些新建的控制冷却装置实现了在非约束型冷却方式下对钢板的直接淬火处理。
1.3喷水方式按喷水方式主要可以将冷却系统分为:层流、水幕、高压喷嘴、气水冷却等方式。
主要特点比较见表1。
表1 喷水方式的比较2影响冷却质量的主要因素(1)冷却速度。
为了使钢板获得均匀的组织和力学性能,冷却装置的冷却速度应随钢板厚度增加而降低。
如果厚钢板的冷却速度太高,钢板的表面和中部温差会过大。
对厚规格钢板而言,沿厚度方向的热传导系数是限制因素;对薄钢板而言,表面的热传递系数才是关键因素。
加速冷却应用的温度范围一般为800~500℃,处于稳定膜态沸腾区,因此热交换系数的稳定是控制冷却速度的关键因素。
典型直接淬火的温度范围为900~200℃,冷却过程通过部分膜态沸腾区,热交换系数对冷却效果不产生主要影响。
(2)钢板平直度。
如果进入冷却区的钢板平直度差,就会造成钢板冷却不均,并使板形更加恶化。
因此,坯料的均匀加热和轧机具有良好的平直度控制水平是取得良好板形的前提条件。
如果以生产薄规格钢板为主,75%以上的钢板厚度在20mm以下,可以考虑在冷却装置前设置预矫直机。
国内中厚板热处理工艺与设备发展现状及展望

国内中厚板热处理工艺与设备发展现状及展望目前在中厚钢板的生产中控轧控冷(TMCP)工艺已普遍应用,并在管线钢、高强度结构钢、海洋平台用钢、造船板等的生产中发挥了积极作用,大大提高了钢板的综合性能,节约了宝贵的合金元素。
但是,TMCP处理的钢板性能离散度较大,而且一些钢种要求很苛刻的临界轧制。
因此,对于生产厚规格、高性能钢板,尤其是要求性能均匀性比较高的锅炉压力容器钢板、桥梁钢板、高层建筑钢板、Z向钢板等,传统的离线热处理方式仍然是难以替代的。
因此一个定位于生产高性能品种钢为主的中厚板厂,建设一条现代化的中厚板热处理生产线,是在设计之初就必须考虑的问题。
建设热处理工序应统筹考虑的问题1 对炼钢、轧钢工序设备的要求中厚板轧后热处理炉是生产高技术含量、高附加值产品不可缺少的主要设备,因此应定位在生产“双高”产品,要求钢质纯净、有害元素和夹杂物含量低,板坯厚度要满足一定的压缩比,配备有控轧控冷设施等。
这就要求前面的炼钢和轧钢工序具备生产“双高”产品的条件,如炼钢工序要配备有铁水预处理设施、大吨位的顶底复吹转炉或高功率电炉、LF/VD/RH 等炉外精炼设施、直弧形大板坯连铸机等,轧钢工序要配备有高刚度强力轧机、ACC(DQ)、强力矫直机等。
2 对轧钢厂的场地要求在建设中厚板厂时,要考虑精整的能力足够大,也就是后面剪切、冷床等的能力要大于前面轧钢能力,以便于充分发挥轧机的潜能。
同样如果一个中厚板厂定位于生产高技术含量、高附加值产品时,就要考虑厂房后部工序要留有充分的火焰切割、探伤、热处理生产线的场地。
因为对于需要热处理的钢板来说,一般40mm以上的厚规格钢板受剪切能力限制,需要火焰切割,而且热处理的钢种很多要求逐张探伤。
因此,在厂房设计时要留有足够的场地,否则将严重制约生产能力的发挥。
探伤一般可安排在热处理之前,这样探伤不合可直接改判以节省热处理费用,但正火通过再结晶细化均匀组织,对于某些微小的探伤缺陷有改善作用,尤其是合金含量较高的钢种。
中厚板TMCP生产技术现状及发展
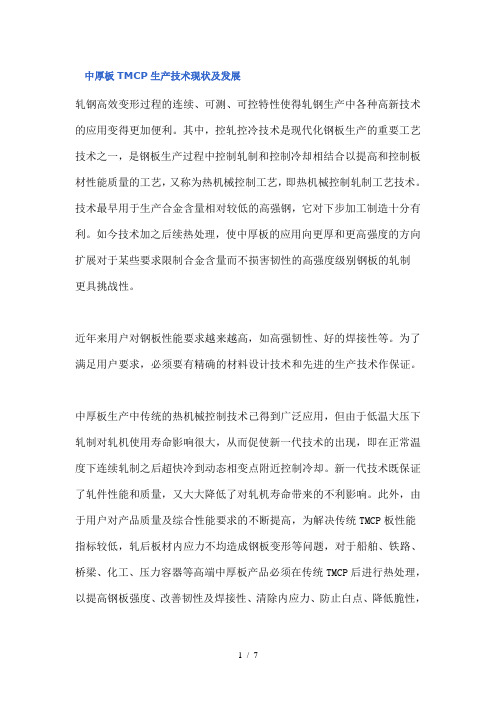
中厚板TMCP生产技术现状及发展轧钢高效变形过程的连续、可测、可控特性使得轧钢生产中各种高新技术的应用变得更加便利。
其中,控轧控冷技术是现代化钢板生产的重要工艺技术之一,是钢板生产过程中控制轧制和控制冷却相结合以提高和控制板材性能质量的工艺,又称为热机械控制工艺,即热机械控制轧制工艺技术。
技术最早用于生产合金含量相对较低的高强钢,它对下步加工制造十分有利。
如今技术加之后续热处理,使中厚板的应用向更厚和更高强度的方向扩展对于某些要求限制合金含量而不损害韧性的高强度级别钢板的轧制更具挑战性。
近年来用户对钢板性能要求越来越高,如高强韧性、好的焊接性等。
为了满足用户要求,必须要有精确的材料设计技术和先进的生产技术作保证。
中厚板生产中传统的热机械控制技术己得到广泛应用,但由于低温大压下轧制对轧机使用寿命影响很大,从而促使新一代技术的出现,即在正常温度下连续轧制之后超快冷到动态相变点附近控制冷却。
新一代技术既保证了轧件性能和质量,又大大降低了对轧机寿命带来的不利影响。
此外,由于用户对产品质量及综合性能要求的不断提高,为解决传统TMCP板性能指标较低,轧后板材内应力不均造成钢板变形等问题,对于船舶、铁路、桥梁、化工、压力容器等高端中厚板产品必须在传统TMCP后进行热处理,以提高钢板强度、改善韧性及焊接性、清除内应力、防止白点、降低脆性,及此同时热处理还可调整性能,挽救性能不合格所造成的损失。
本文将简要论述TMCP的现状和发展。
1.TMCP技术的现状及发展应用TMCP技术可生产出综合机械性能和焊接性能均优良的高强度焊接结构钢板,该工艺技术已成为近几年来中厚板生产领域最为核心的工艺技术。
TMCP技术已被各国所普遍认可。
1.1 TMCP技术现状传统TMCP技术见图是将钢坯加热到1150-1050℃温度,在再结晶区或未再结晶区给予大压下进行轧制,然后再根据轧件的不同,进行不同温度区段的冷却。
通常根据不同钢种,控制钢板950℃-600℃温度范围的变形量,达到奥氏体状态的控制和进一步由这种受控态奥氏体发生相变的控制。
中厚板轧后控制冷却技术的发展及现状

中厚板轧后控制冷却技术的发展及现状发布时间:2022-10-20T11:15:35.420Z 来源:《中国科技信息》2022年第12期作者:李渊[导读] 冷却技术控制是通过轧制材料过热进行热处理的技术。
李渊八一钢铁股份有限公司轧钢厂中厚板分厂摘要:冷却技术控制是通过轧制材料过热进行热处理的技术。
冷却控制设置在终轧机与精整机之间,通过改变热轧的冷却条件、奥氏体相态条件和改善碳化物析出行为,改善钢的结构和性能。
通过采用控制冷却技术,不仅提高了性能,还提高了钢板的强度,而不影响质量。
同时,钢板的不平整度和残余应力减少,钢板质量明显改善。
本文总结了中厚板轧后控制冷却技术的发展情况,并探讨了水冷及其控制的难点。
了解这些条件对于中厚板厂选择合适的冷却方法并对其进行配置以管理冷却系统非常重要。
关键词:中厚板;控制冷却;发展控制轧制和冷却是现代钢铁工业技术成就之一。
冷却控制和管理是通过控制冷却后的轧制温度。
控制轧辊冷却后钢的冷却速度,以提高钢的结构和性能。
由于热轧变形效应,奥氏体变形后的铁转变温度升高,反转后的铁晶体变得容易生长,机械性能下降。
采用可控冷却方法,优化铁晶粒,减小珠光体层间距,防止碳化物在高温下析出,采用控制冷却是增强了强化效果。
一、控制冷却方式控制冷却方法有许多优点和缺点。
不同的冷却方法因技术环境和条件而异。
1.压力喷射。
优点是,水可以连续流动,而不会中断钢板表面的流动,从而可以将冷却部件喷到钢板表面,同时顶部和底部的冷却差异可以在水汽膜环境中渗透到钢板中。
缺点,冷却性能少,冷却效率低,需水量高,用水量大,冷却不均匀,水质要求高,喷嘴堵塞,水利用率低。
2.层流。
优点是水保持高冷却状态,并提供稳定的冷却能力,自上而下和垂直均匀冷却。
缺点,冷却路径长,管道间距有限,横向分布不均匀,要求水质高,喷嘴堵塞,维护量及难度大。
3.水幕冷却。
优点是冷却功率最大,水流保持静层流止,冷却速度快,冷却区域距离小,需水量低,可维修性低,冷却速度一般为12-30℃s,有时可达80℃s。
新型中厚板快速冷却系统研发

新型中厚板快速冷却系统研发摘要:近年来,我国行业对高寿命、高强高韧性钢板的需求与日俱增,钢铁企业不断改进工艺技术和生产设备。
其中控制轧制和控制冷却技术在高性能钢铁材料的开发和生产中得到广泛应用和不断的创新,作为TMCP工艺主要组成部分的轧后冷却技术也取得了长足的发展;传统的管层流冷却技术由于冷却能力不足、冷却均匀性较差,已无法满足现阶段中厚板生产工艺和成材率等方面的要求,近几年我国钢铁企业或引进国外先进的轧后冷却工艺生产线,或对现有轧后冷却系统进行升级改造。
关键词:快速冷却,智能精准,温度1快速冷却装置本冷却系统结合了Super-OLAC和Mupic技术优势,设计出一套新型喷箱结构,该系统冷却能力强、冷却水压力和流量控制稳定、冷却水分布更加均匀,经有限元流体软件(FLUNT)仿真分析和优化,形成一套全新的中厚板在线冷却系统。
主要技术特征包括:(1)采用新型喷箱结构:结合缝隙式+高密喷嘴设计,水量大、冷却能力强、调节范围宽、流量控制稳定,是一种功能完善的在线强力冷却装置;(2)分段升降框架+喷箱分组控制模式:实现准确灵活的水量控制,冷却水分布均匀,冷效果均匀;(3)供水系统:满足不同冷却工艺要求、水压稳定、水质可控;(4)基础自动化系统:控制完善、易调节、跟踪和动作精准;(5)均匀板形综合控制技术:每组冷却单元之间设置顶喷,各组冷却水分布均匀,结合水凸度、边部遮蔽技术,保证钢板轧向与横向的冷却均匀性;(6)矫冷一体综合控制技术:保证不因轧制板形问题造成冷却水分布不均,结合高精度温度模型为基础的均匀板形综合控制技术,保证冷却均匀性。
2智能精准冷却控制系统本套系统综合了材料学、流体力学、传热学和自动化控制等多个学科,基于傅立叶导热微分方程和非稳态隐式差分方法,建立快速冷却控制系统的核心算法。
开发了高精度、高效率、高适用性的中厚板在线冷却控制系统,该系统功能先进和完善、计算准确、易调整;通过相关试验,测得典型钢种的热物性参数,并根据FLUNT,ANSYS等有限元仿真软件和生产实绩验证、优化模型的精度和功能。
中厚板控制冷却的板形控制与实践

中厚板控制冷却的板形控制与实践摘要:对控冷过程中,中厚板控制冷却原理分析,研究横向、纵向的板形控制方法,并阐述某轧板厂实际运用板形控制技术的情况。
关键词:中厚板;控制冷却;板形控轧控冷是现代轧钢过程中的两个重要环节,能有效改善钢板的强度和塑性等。
本文采用控制冷却技术的主要目的是改善钢板组织,提高钢板的力学性能 ;并要保证在同一块钢板上力学性能均匀 ,生产的同一批、同钢种的钢板力学性能波动小;同时 ,还要在控冷过程中保持钢板的板形平直。
为了满足控制冷却工艺的要求 ,需要在控制冷却机械设备设计、自动控制中考虑以下几个方面。
组织和性能控制。
保证冷却装置能提供足够的冷却能力和终冷温度的精确控制 ;平直度控制。
在冷却过程中做到钢板横向温度均匀、厚度方向温度对称,使钢板冷却之后的板形平直;性能均匀性控制。
做到钢板纵横向温度均匀、终冷温度控制精确 ,使钢板性能均匀一致。
一、控制冷却原理控制冷却的重要目的之一是在不降低钢板的韧性的前提下通过控制冷却能够进一步提高钢板的强度。
它能防止奥氏体晶粒长大,阻止减少网状碳化物的析出量和降低级别,保持其碳化物固溶状态,达到固溶强化的目的,同时减少珠光体球团尺寸,改善珠光体形貌和片层间距,从而改善钢板的性能。
以上控冷技术运用到中厚板厂并配合控制轧制进行。
根据轧制实际情况,采取轧制过程中和轧后控温的方式,实现控冷工艺。
在此主要研究轧后快速冷却,通过控制冷却温度和冷却速度,以及整个板面冷却的均匀性,保证钢板的性能和板形。
二、控制冷却中厚板板型控制方法1.横向温度均匀性控制。
控制钢板横向温度均匀性,目前采用最多的方法是:采用冷却器边部遮蔽技术;设计钢板上下表面冷却器合理的流量分布曲线。
边部遮蔽技术是在两侧设置喷水量可随板宽调节的边部遮蔽挡板(Edge Masking),使水流不直接冲击两侧,实现边部均匀冷却的技术。
采用边部遮蔽技术,减轻宽度方向滞留水对钢板传热的影响,使钢板上表面的横向传热均匀一致,克服钢板上表面的中部滞留水流造成的中间传热慢、边部传热快,传热系数差距大的不均匀冷却问题。