推行精益生产常见的七大困惑
精益生产之七大浪费

精益生产之七大浪费精益生产是一种以最小化浪费为目标,通过优化流程和提高效率来提高产品质量和客户满意度的管理方法。
在精益生产中,有七大浪费被认为是造成资源浪费和低效率的主要原因,它们是:过产、等待、运输、不合格、运动、库存和过程错误。
1. 过产(Overproduction):过产是指在没有实际需求的情况下进行生产活动,导致产品过度积压和资源浪费。
这不仅会给企业带来高成本,还会增加库存量和缩短产品寿命。
2. 等待(Waiting):等待是指生产过程中出现的不必要的停顿和延迟。
这可能是由于设备故障、物料不足、工人缺席等原因导致的。
等待会降低生产效率,增加生产周期,延迟产品交付。
3. 运输(Transportation):运输是指不必要的材料和产品的长距离运输。
这使得运输成为了一个独立的过程,需要额外的时间和资源。
这些额外的步骤可能会导致物料的损坏、遗失和延迟,进一步增加了生产成本。
4. 不合格(Defects):不合格是指生产中出现的错误、缺陷和质量问题。
不合格的产品需要进行修正、重新制造或报废,这增加了不必要的时间和资源。
这不仅会导致生产延误,还会降低产品质量和客户满意度。
5. 运动(Motion):运动是指工人在生产过程中进行不必要的移动和动作。
这可能是由于生产线布局不合理、工具和设备摆放不当等原因导致的。
这增加了工人的体力消耗,降低了生产效率,也增加了人为错误的可能性。
6. 库存(Inventory):库存是指未经加工的原材料和半成品的储存量。
过多的库存可能会导致资金占用、过期损失、储存空间浪费等问题。
此外,库存过多也会隐藏潜在的问题,如质量问题和需求变化的风险。
7. 过程错误(Processing):过程错误是指生产过程中出现的不必要的重复、增补和调整。
这可能是由于不合理的工艺流程、工具和设备的不良设计等原因导致的。
这会增加生产成本和时间,降低生产效率和产品质量。
有效管理和消除以上七大浪费是精益生产的关键。
精益生产管理的挑战与对策
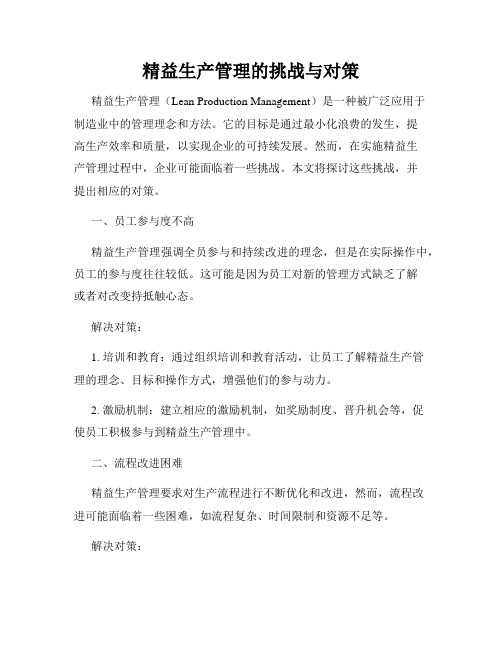
精益生产管理的挑战与对策精益生产管理(Lean Production Management)是一种被广泛应用于制造业中的管理理念和方法。
它的目标是通过最小化浪费的发生,提高生产效率和质量,以实现企业的可持续发展。
然而,在实施精益生产管理过程中,企业可能面临着一些挑战。
本文将探讨这些挑战,并提出相应的对策。
一、员工参与度不高精益生产管理强调全员参与和持续改进的理念,但是在实际操作中,员工的参与度往往较低。
这可能是因为员工对新的管理方式缺乏了解或者对改变持抵触心态。
解决对策:1. 培训和教育:通过组织培训和教育活动,让员工了解精益生产管理的理念、目标和操作方式,增强他们的参与动力。
2. 激励机制:建立相应的激励机制,如奖励制度、晋升机会等,促使员工积极参与到精益生产管理中。
二、流程改进困难精益生产管理要求对生产流程进行不断优化和改进,然而,流程改进可能面临着一些困难,如流程复杂、时间限制和资源不足等。
解决对策:1. 流程分析:对生产流程进行详细分析,找出不必要的环节和浪费,并提出相应的改进方案。
2. 资源优化:分配适当的资源用于流程改进,确保改进的有效实施。
3. 时间管理:合理安排时间,采取分阶段改进的方式,逐步推进流程的优化。
三、供应链管理挑战精益生产管理侧重于整个供应链的优化,而供应链的管理是一个复杂的过程,涉及到多个环节和合作伙伴。
解决对策:1. 合作伙伴选择:选择可靠的供应商和合作伙伴,建立长期稳定的合作关系,确保供应链的稳定性和效率。
2. 信息共享:建立信息共享平台,通过及时准确地共享信息,提高供应链的可见性和协同性。
3. 风险管理:制定相应的风险管理策略,应对供应链中的各种风险和不确定性。
四、文化转变困难精益生产管理涉及到企业文化的转变,这是一个长期而艰巨的过程,可能面临着一些困难和阻力。
解决对策:1. 领导力发展:培养和提升领导层的精益生产管理意识和技能,使他们成为文化变革的引领者和榜样。
精益生产在中小企业中的实施难点有哪些
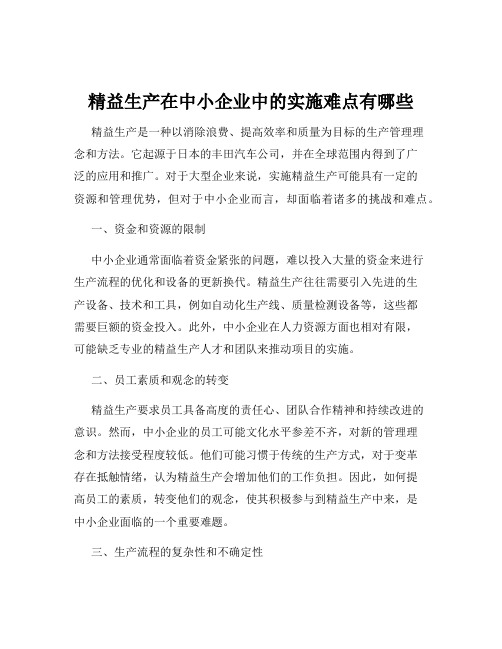
精益生产在中小企业中的实施难点有哪些精益生产是一种以消除浪费、提高效率和质量为目标的生产管理理念和方法。
它起源于日本的丰田汽车公司,并在全球范围内得到了广泛的应用和推广。
对于大型企业来说,实施精益生产可能具有一定的资源和管理优势,但对于中小企业而言,却面临着诸多的挑战和难点。
一、资金和资源的限制中小企业通常面临着资金紧张的问题,难以投入大量的资金来进行生产流程的优化和设备的更新换代。
精益生产往往需要引入先进的生产设备、技术和工具,例如自动化生产线、质量检测设备等,这些都需要巨额的资金投入。
此外,中小企业在人力资源方面也相对有限,可能缺乏专业的精益生产人才和团队来推动项目的实施。
二、员工素质和观念的转变精益生产要求员工具备高度的责任心、团队合作精神和持续改进的意识。
然而,中小企业的员工可能文化水平参差不齐,对新的管理理念和方法接受程度较低。
他们可能习惯于传统的生产方式,对于变革存在抵触情绪,认为精益生产会增加他们的工作负担。
因此,如何提高员工的素质,转变他们的观念,使其积极参与到精益生产中来,是中小企业面临的一个重要难题。
三、生产流程的复杂性和不确定性中小企业的生产规模相对较小,产品种类较多,生产流程往往不够标准化和规范化。
这使得精益生产中的流程优化和标准化工作变得更加困难。
同时,市场需求的不确定性也给中小企业的生产计划和调度带来了很大的挑战。
由于订单量不稳定,生产批量小,频繁的切换生产线会导致生产效率低下和成本增加,这与精益生产追求的连续流生产理念相冲突。
四、供应链管理的难度中小企业在供应链中的话语权相对较弱,与供应商的合作关系不够稳定。
供应商的交货期不准时、原材料质量不稳定等问题都会影响到企业的生产进度和产品质量。
在精益生产中,强调与供应商建立长期的合作伙伴关系,实现准时化供应,但中小企业往往难以做到这一点。
此外,中小企业自身的库存管理也存在问题,过高的库存会占用大量的资金,而过低的库存又可能导致缺货,影响客户满意度。
公司推进精益生产存在什么问题
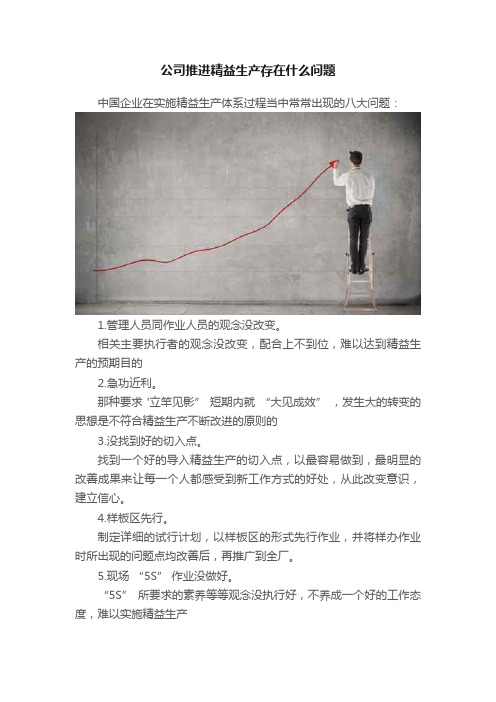
公司推进精益生产存在什么问题
中国企业在实施精益生产体系过程当中常常出现的八大问题:
1.管理人员同作业人员的观念没改变。
相关主要执行者的观念没改变,配合上不到位,难以达到精益生产的预期目的
2.急功近利。
那种要求 '立竿见影” 短期内就“大见成效” ,发生大的转变的思想是不符合精益生产不断改进的原则的
3.没找到好的切入点。
找到一个好的导入精益生产的切入点,以最容易做到,最明显的改善成果来让每一个人都感受到新工作方式的好处,从此改变意识,建立信心。
4.样板区先行。
制定详细的试行计划,以样板区的形式先行作业,并将样办作业时所出现的问题点均改善后,再推广到全厂。
5.现场“5S” 作业没做好。
“5S” 所要求的素养等等观念没执行好,不养成一个好的工作态度,难以实施精益生产
6.实施过程遇到困难就停滞不前。
“三个糗皮匠,胜过诸葛亮” 要集思广益,准备多个解决方案。
打开心胸,吸取不同意见,不要解释不能做的理由,要想出做下去的办法。
不要等到十全十美,有五分把握就可以动手
7.投入资金太多。
改善要以不花钱为原则,不要一碰到问题点就想到投入新设备、新技术,应该尽量避免投入大量资金,能在现有的设施或基础上给以改进也是最好的方案。
8.缺乏整体配合。
认为精益生产方式的实施只是IE工程师的责任,与其它的单位无关,例如:采购、物流、工程等单位不能充分协作的话,就算是有好的方案,但也只是“昙花一现”,无法持续发挥精益的效能。
精益生产中的七大浪费及改善方法
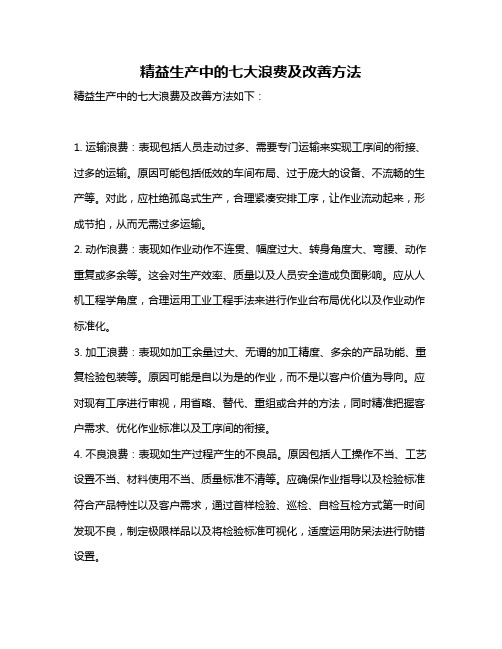
精益生产中的七大浪费及改善方法精益生产中的七大浪费及改善方法如下:1. 运输浪费:表现包括人员走动过多、需要专门运输来实现工序间的衔接、过多的运输。
原因可能包括低效的车间布局、过于庞大的设备、不流畅的生产等。
对此,应杜绝孤岛式生产,合理紧凑安排工序,让作业流动起来,形成节拍,从而无需过多运输。
2. 动作浪费:表现如作业动作不连贯、幅度过大、转身角度大、弯腰、动作重复或多余等。
这会对生产效率、质量以及人员安全造成负面影响。
应从人机工程学角度,合理运用工业工程手法来进行作业台布局优化以及作业动作标准化。
3. 加工浪费:表现如加工余量过大、无谓的加工精度、多余的产品功能、重复检验包装等。
原因可能是自以为是的作业,而不是以客户价值为导向。
应对现有工序进行审视,用省略、替代、重组或合并的方法,同时精准把握客户需求、优化作业标准以及工序间的衔接。
4. 不良浪费:表现如生产过程产生的不良品。
原因包括人工操作不当、工艺设置不当、材料使用不当、质量标准不清等。
应确保作业指导以及检验标准符合产品特性以及客户需求,通过首样检验、巡检、自检互检方式第一时间发现不良,制定极限样品以及将检验标准可视化,适度运用防呆法进行防错设置。
5. 等待浪费:表现如人员(以及设备)在等待,或者有时忙、有时闲的不均衡现象。
原因如生产线品种切换、工作量少、时常缺料、设备闲置等。
应实施生产均衡化,快速换模技术的运用,全员生产性防护,多技能工,消除不良浪费,提升供应商水准。
6. 过量生产:这是常被视为最大的浪费。
其结果导致库存、资金的占用以及潜在的报废风险。
应形成一个流、节拍化生产。
“一个流生产”是指从毛坯投入成品产出的整个制造加工过程,零件始终处于不停滞、不堆积、不超越的状态。
每道工序加工完一个制件后立即流到下一工序;工序间的在制品数量不超过前工序的装夹数量。
零件的运动不间断、不超越、不落地。
只有合格的产品才允许往下一道工序流。
节拍化生产要求是需求节拍与生产节拍平衡。
精益生产中涉及到需解决的问题汇总
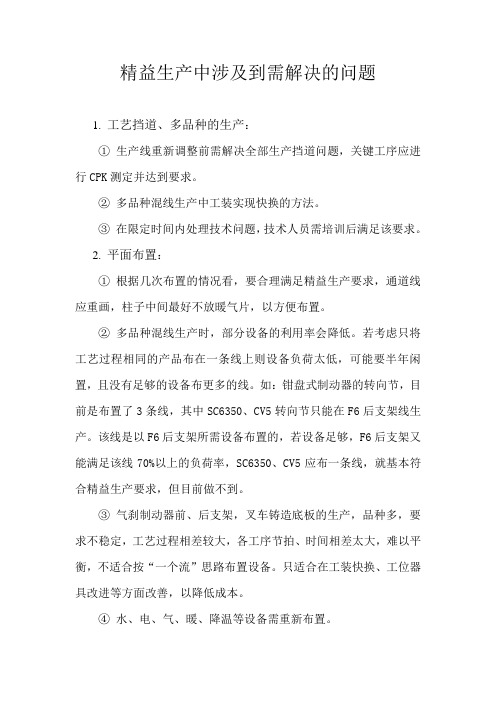
精益生产中涉及到需解决的问题1. 工艺挡道、多品种的生产:①生产线重新调整前需解决全部生产挡道问题,关键工序应进行CPK测定并达到要求。
②多品种混线生产中工装实现快换的方法。
③在限定时间内处理技术问题,技术人员需培训后满足该要求。
2. 平面布置:①根据几次布置的情况看,要合理满足精益生产要求,通道线应重画,柱子中间最好不放暖气片,以方便布置。
②多品种混线生产时,部分设备的利用率会降低。
若考虑只将工艺过程相同的产品布在一条线上则设备负荷太低,可能要半年闲置,且没有足够的设备布更多的线。
如:钳盘式制动器的转向节,目前是布置了3条线,其中SC6350、CV5转向节只能在F6后支架线生产。
该线是以F6后支架所需设备布置的,若设备足够,F6后支架又能满足该线70%以上的负荷率,SC6350、CV5应布一条线,就基本符合精益生产要求,但目前做不到。
③气刹制动器前、后支架,叉车铸造底板的生产,品种多,要求不稳定,工艺过程相差较大,各工序节拍、时间相差太大,难以平衡,不适合按“一个流”思路布置设备。
只适合在工装快换、工位器具改进等方面改善,以降低成本。
④水、电、气、暖、降温等设备需重新布置。
3. 设备很多设备损坏或长年不用,如:金一的日本立车、台湾立车、台中精机立加、双轴立车、多刀半自动,单柱立车等;金二的EQ153底板加工中心孔专机、制动蹄蹄片轴孔专机、制动蹄铆钉孔专机、制动蹄铆接孔数控专机等。
不足的原因很复杂,这些设备修好时间或做为闲置设备或做为报废设备处理不定,生产线无法合理布置。
4. 基础资料①各车间报的节拍时间不准确,由于某些产品没有生产,技术部门无法核实。
②市场预测中,各品种产品的需求量应认真推敲。
如以上两项与事实出入很大,将造成布线错误,给精益生产的组织带来很大困难,基本无法进行。
因为布几条线,每条线都哪些产品在该线生产都是依据以上两项。
5.应注意的问题:①精益生产前期有大量投入而短期内回报很少,甚至没有回报,公司的资金应能支撑,一旦推行将无法返回。
企业精益生产推行障碍与解决措施

企业精益生产推行障碍与解决措施引言近年来,精益生产在企业管理中逐渐流行起来。
企业精益生产的目标是通过减少浪费和提高生产效率,从而实现降低成本、提高质量和增加利润的目标。
然而,在推行精益生产的过程中,企业可能会遇到一些障碍。
本文将探讨企业推行精益生产时可能遇到的障碍,并提出相应的解决措施。
1. 缺乏顶层支持企业推行精益生产需要得到管理层的支持和认可。
然而,在一些企业中,管理层可能并不了解精益生产的价值和意义,或者对其持怀疑态度。
因此,缺乏顶层支持成为企业推行精益生产的一大障碍。
为了解决这个问题,企业可以采取以下措施:•教育和培训:向管理层介绍精益生产的原理和成功案例,帮助他们了解精益生产的价值,以获得他们的支持和认可。
•意识增强:通过内部宣传、分享会等形式,让员工了解并认同精益生产的重要性,进而推动管理层的变革。
2. 员工抵触情绪在推行精益生产的过程中,一些员工可能会抵触改变、担心自身利益受损、或者对新方式持怀疑态度。
这种抵触情绪可能会阻碍精益生产的推行。
为了解决这个问题,企业可以采取以下措施:•培训和教育:向员工解释精益生产的意义和好处,以便他们理解并接受新的工作方式。
•参与和激励:鼓励员工参与精益生产改进活动,给予他们合理的激励,以增强他们的积极性和支持度。
•沟通和反馈:及时与员工进行沟通,并给予他们反馈,让他们感受到自己的意见和贡献被重视,从而减轻抵触情绪。
3. 不适应的组织文化推行精益生产需要企业建立一种以改进和创新为核心的组织文化。
然而,一些企业可能存在保守、守旧的组织文化,不适应精益生产的要求。
为了解决这个问题,企业可以采取以下措施:•建立激励机制:通过建立与精益生产理念相符的奖惩制度,激励员工提出改进建议和创新点子,推动组织文化的转变。
•培训和教育:通过员工培训和教育,使员工逐渐接受和认同精益生产的理念和文化,并能够在实践中应用。
•建立沟通渠道:建立多种沟通渠道,使员工可以自由表达自己的意见和建议,从而促进组织文化的开放和变革。
精益生产缺点及改进措施
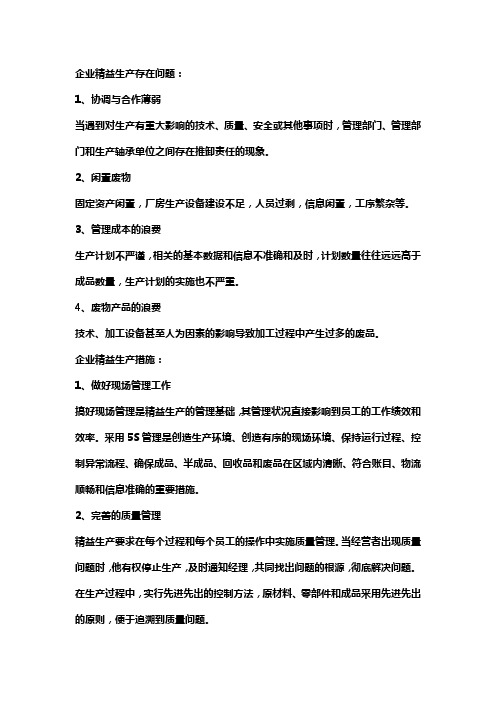
企业精益生产存在问题:
1、协调与合作薄弱
当遇到对生产有重大影响的技术、质量、安全或其他事项时,管理部门、管理部门和生产轴承单位之间存在推卸责任的现象。
2、闲置废物
固定资产闲置,厂房生产设备建设不足,人员过剩,信息闲置,工序繁杂等。
3、管理成本的浪费
生产计划不严谨,相关的基本数据和信息不准确和及时,计划数量往往远远高于成品数量,生产计划的实施也不严重。
4、废物产品的浪费
技术、加工设备甚至人为因素的影响导致加工过程中产生过多的废品。
企业精益生产措施:
1、做好现场管理工作
搞好现场管理是精益生产的管理基础,其管理状况直接影响到员工的工作绩效和效率。
采用5S管理是创造生产环境、创造有序的现场环境、保持运行过程、控制异常流程、确保成品、半成品、回收品和废品在区域内清晰、符合账目、物流顺畅和信息准确的重要措施。
2、完善的质量管理
精益生产要求在每个过程和每个员工的操作中实施质量管理。
当经营者出现质量问题时,他有权停止生产,及时通知经理,共同找出问题的根源,彻底解决问题。
在生产过程中,实行先进先出的控制方法,原材料、零部件和成品采用先进先出的原则,便于追溯到质量问题。
企业精益生产
3、科学的生产过程
以产品的交货期为Zui终时间节点,制定科学可行的生产流程,生产调度部门做好前期的组织协调工作,确保产品生产各环节的有序循环,不耽误每一步。
企业推行精益生产管理活动过程中会遇到哪些问题

企业推行精益生产管理活动过程中会遇到哪些问题在很多企业精益生产实际推动中,会碰到以下一些情况:一、退而居其次的情况有人可能会问,精益生产推动中,许多企业是达不到既定目标的或者说失败的,那么如果这样岂不是不如开始就不推动。
实际上,精益生产导入也分许多层级的,很多企业认为达到拉动式生产是很高的水平了,但是这也是把双刃剑,一些管理水平不错的公司也没有用拉动式生产。
即便实现不了拉动式生产,推动精益生产对企业也大有益处,至少5S、消除浪费、降低成本这些事天经地义到哪里都应该做好吧。
在精益生产中实现流线化生产可以起到巩固基础工作的程度,所以至少流线化生产还是要达到的,真达到了流线化生产,现在企业降低15%的成本是有希望的。
另外看板(Kanban)是可以和MRP系统共生的,MRP系统基于长期的复杂的系统的信息综合,资源调配,而看板方式对于短期的小范围的简单的信息反馈,资源调配是擅长的。
比如20分钟到2个小时的现场物料情况,半成品情况,还是看板方式较实用,但对于超过2天的计划还是MRP系统占优势。
所以说两者是可以共存的。
精益生产推动是没问题的。
二、本地化设计任何生产方式都要适应当地的实际情况,精益生产也是这样,推动精益生产切记不能生搬硬套,需要建立专业团队进行精益生产如何适合于本企业实际所属行业、实际人员特性及实际产品物料形态进行客制化设计及实际推行过程中的经验总结。
要建立一套符合自身经营模式与产品特性,结合工业工程的改善手法及借鉴六西格玛管理与解决问题方式的制造管理文化。
很多企业直接原版引用精益生产方式,忽视自身企业实际情况,并没有进行一些基础及前提条件的前期改造。
简单复制部分精益生产的做法,结果最后不能达到预期的设想,反倒将责任归咎于精益生产方式和精益生产,进而武断地认为精益生产根本不适用于自己的企业而宣告精益生产不宜导入或推行中断。
例如,某公司聘请外部顾问公司来推行精益生产,顾问公司一到生产线,直接要求所有的操作员要站立作业,因为很多精益企业都是这样做的,尽管顾问公司一再说这样可以提高作业幅度,提升作业的效率。
工厂实施精益生产改善常见的五大误区
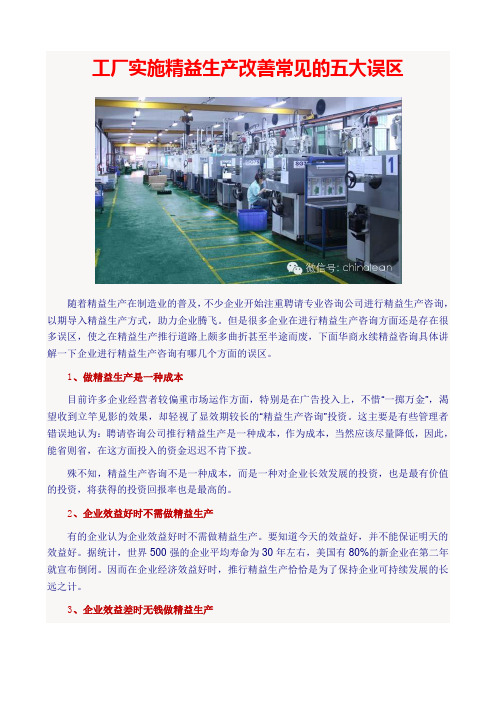
工厂实施精益生产改善常见的五大误区随着精益生产在制造业的普及,不少企业开始注重聘请专业咨询公司进行精益生产咨询,以期导入精益生产方式,助力企业腾飞。
但是很多企业在进行精益生产咨询方面还是存在很多误区,使之在精益生产推行道路上颇多曲折甚至半途而废,下面华商永续精益咨询具体讲解一下企业进行精益生产咨询有哪几个方面的误区。
1、做精益生产是一种成本目前许多企业经营者较偏重市场运作方面,特别是在广告投入上,不惜“一掷万金”,渴望收到立竿见影的效果,却轻视了显效期较长的“精益生产咨询”投资。
这主要是有些管理者错误地认为:聘请咨询公司推行精益生产是一种成本,作为成本,当然应该尽量降低,因此,能省则省,在这方面投入的资金迟迟不肯下拨。
殊不知,精益生产咨询不是一种成本,而是一种对企业长效发展的投资,也是最有价值的投资,将获得的投资回报率也是最高的。
2、企业效益好时不需做精益生产有的企业认为企业效益好时不需做精益生产。
要知道今天的效益好,并不能保证明天的效益好。
据统计,世界500强的企业平均寿命为30年左右,美国有80%的新企业在第二年就宣布倒闭。
因而在企业经济效益好时,推行精益生产恰恰是为了保持企业可持续发展的长远之计。
3、企业效益差时无钱做精益生产有的企业认为自己的经济效益不太好,因此对于精益生产的咨询费用“望而生畏”,自己在企业里搞一搞就放弃了。
殊不知这样会让自己的企业陷入这样一种恶性循环:不推行精益生产——经营不好——更不推行精益生产——经营更不好。
要打破这种恶性循环,企业要端正认识,长远打算,选择合适的精益生产咨询公司,为自己打造一条突围之路。
4、精益生产是灵丹妙药有的企业对与精益生产急功近利,希望立竿见影,恨不得一口气吃成个胖子。
事实上,精益生产的推行需要全面的考察,精确的评估,做出细致的方案,并且坚定有力地实施下去。
一切工作都是需要时间的,指望一两个月就能让企业大变样,做个简单的5S表面功夫或许有可能,想要让企业起死回生,焕发生机却是不可能的。
精益生产七大浪费

1.直接的财务问题。说明库存和在制品增加,资金周转率低,制造时间变长,资金和利息被占用, 会造成库存空间的浪费,这在现金流量表中是很明显的。
2.产生次要问题。搬运和堆积会产生废物;先进先出的工作造成困难;产品积压导致不良品的发生, 物流阻断过程时间变长,现场工作空间变小,存在滞留仓库的风险和不良品的风险。
1. 优化工艺流程,对生产流程进行全面分析,找出其中的瓶颈和不必要的环节,进行优化和改进。 采用更高效的加工方法和设备,减少加工时间和工序。 2. 减少调整时间,通过标准化作业、快速换模等技术手段,减少设备调整和准备时间,提高设备的 利用率。 3. 提高加工精度,采用先进的加工技术和设备,提高加工精度,减少废品和返工,降低加工成本。 4. 引入自动化和智能化,利用自动化设备和智能化系统,提高生产的自动化水平,减少人工干预, 降低加工误差和浪费。 5. 加强质量控制,建立严格的质量控制体系,对原材料、半成品和成品进行严格检测,确保产品质 量符合标准,减少因质量问题导致的加工浪费。 6. 培训员工,加强员工培训,提高员工的技能水平和质量意识,使他们能够熟练掌握加工工艺和操 作方法,减少因操作不当导致的浪费。 7. 持续改进,建立持续改进的机制,鼓励员工提出改进建议,不断优化加工过程,提高生产效率和
5.建立持续改进文化
建立持续改进文化是实现精益生产的关键之一。通过建立持续改进文化,可以使员工充分认识到 浪费的危害和价值,从而积极参与到消除浪费的行动中来。例如,可以定期组织员工进行交流和 分享经验,以提高员工对精益生产的认识和实践水平。
(三)不良品的浪费
(1)不良品浪费对企业生产经营产生了诸多不利影响: (2)成本增加:不良品的产生会增加原材料、人力、设备等资源的浪费,导致生产成本的 增加。 (3)产能降低:不良品的产生会导致生产线停机、返工时间增加,进而降低了企业的产能。 (4)产品质量下降:不良品的产生会影响产品的质量,降低了产品的市场竞争力。 (5)顾客满意度下降:不良品的产生会导致交货延迟、产品质量问题等,降低了顾客的满 意度。
如何处理精益生产过程中遇到的问题?

如何处理精益生产过程中遇到的问题?
精益生产是一种高效的生产管理方法,但在实施过程中,难免会遇到一些问题。
本文,深圳天行健精益管理咨询公司就如何处理精益生产过程中遇到的问题作出如下解析。
问题一:生产过程中出现浪费现象
问题二:员工对精益生产缺乏理解和支持
问题三:供应链环节存在瓶颈
问题四:产能不足导致生产进度延误
问题五:产品质量不稳定
针对问题一,我们可以通过持续改进来减少浪费。
通过价值流图的绘制和分析,找出生产过程中的非价值增加环节,并采取措施进行优化,以提高生产效率。
针对问题二,我们可以开展员工培训和意识提升活动,让员工了解精益生产的核心原理和优势,增强他们对精益生产的支持和参与度。
针对问题三,我们可以与供应商建立良好的合作关系,共同解决供应链环节中的瓶颈问题。
通过信息共享和协同创新,提高供应链的整体效率和灵活性。
针对问题四,我们可以进行产能规划和调整,确保生产能够按时完成。
通过优化生产流程、提高设备利用率和人员配备,最大程度地提高产能水平,以满足市场需求。
针对问题五,我们可以建立完善的质量管理体系,从源头控制产品质量。
通过制定严格的质量标准和流程,加强对关键环节的监控和检测,及时发现和解决质量问题,确保产品质量的稳定性。
总之,处理精益生产过程中遇到的问题需要采取有针对性的措施,从不同的角度进行分析和解决。
通过持续改进、培训和意识提升、合作共赢、规划调整和质量管理等方式,我们可以不断优化生产过程,提高生产效率和产品质量,实现企
业的可持续发展。
企业推行精益生产失败原因是什么

企业推行精益生产失败原因是什么引言精益生产作为一种管理理念,旨在通过优化流程、减少浪费和提高效率来提升企业的竞争力。
然而,实施精益生产并不总是成功的。
本文将探讨企业推行精益生产失败的一些常见原因,并提供一些解决方案以帮助企业避免这些问题。
1. 管理层缺乏明确的目标和愿景企业推行精益生产需要领导者具备明确的目标和愿景,并向组织中的所有成员清晰地传达这些目标和愿景。
如果管理层没有清楚地表达他们希望通过精益生产实现的结果,并没有明确的规划和战略,那么员工在执行过程中就会缺乏动力和方向。
解决方案:由管理层确立明确的目标和愿景,并定期与员工分享这些目标。
同时,将这些目标细化为可操作的指标和步骤,让员工更容易理解和实施。
2. 不合适的组织文化精益生产需要企业建立一种注重质量、效率和持续改进的组织文化。
如果企业已经存在一种以权威和传统为基础的文化,员工可能会对精益生产的改变持怀疑态度,并不愿意积极参与其中。
解决方案:建立一种鼓励创新、开放沟通和团队合作的文化。
提供培训和培养计划,帮助员工理解精益生产的价值,并鼓励他们参与到改进流程中。
3. 不合理的期望和时间压力推行精益生产需要时间和耐心。
然而,一些企业可能过于追求快速结果,期望短时间内就能看到显著的改善效果。
这种心态可能导致企业在实施阶段过于急于求成,忽视了问题的深层次根本原因,只是进行一些表面上的改动。
解决方案:明确向员工传达,推行精益生产是一个持续不断的过程,需要时间和努力。
制定合理的目标和时间计划,并坚持不懈地推动改进,逐步实现预期效果。
4. 培训和支持不足精益生产需要员工具备一定的知识和技能,才能有效地参与改进活动。
如果企业没有提供足够的培训和支持,那么员工可能会感到无所适从,无法应对改变。
解决方案:建立培训计划,为员工提供必要的培训和学习机会,帮助他们理解并掌握精益生产的概念和工具。
同时,建立一个持续学习和知识分享的机制,让员工能够相互学习和支持。
精益生产之七大浪费及5S管理
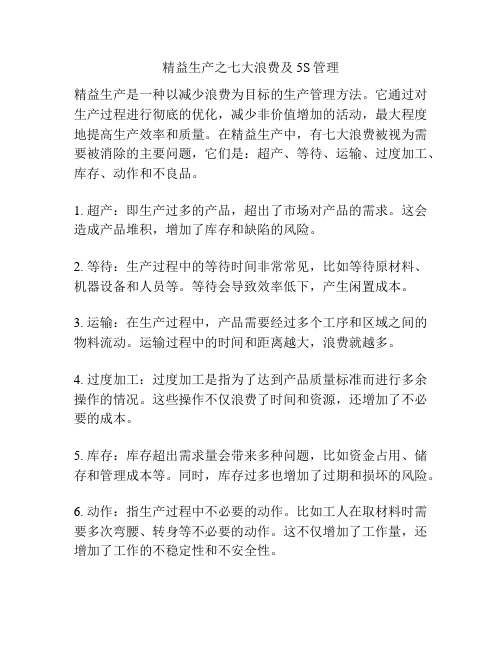
精益生产之七大浪费及5S管理精益生产是一种以减少浪费为目标的生产管理方法。
它通过对生产过程进行彻底的优化,减少非价值增加的活动,最大程度地提高生产效率和质量。
在精益生产中,有七大浪费被视为需要被消除的主要问题,它们是:超产、等待、运输、过度加工、库存、动作和不良品。
1. 超产:即生产过多的产品,超出了市场对产品的需求。
这会造成产品堆积,增加了库存和缺陷的风险。
2. 等待:生产过程中的等待时间非常常见,比如等待原材料、机器设备和人员等。
等待会导致效率低下,产生闲置成本。
3. 运输:在生产过程中,产品需要经过多个工序和区域之间的物料流动。
运输过程中的时间和距离越大,浪费就越多。
4. 过度加工:过度加工是指为了达到产品质量标准而进行多余操作的情况。
这些操作不仅浪费了时间和资源,还增加了不必要的成本。
5. 库存:库存超出需求量会带来多种问题,比如资金占用、储存和管理成本等。
同时,库存过多也增加了过期和损坏的风险。
6. 动作:指生产过程中不必要的动作。
比如工人在取材料时需要多次弯腰、转身等不必要的动作。
这不仅增加了工作量,还增加了工作的不稳定性和不安全性。
7. 不良品:生产出的不良产品无法被销售,这会导致浪费资源和劳动力。
为了减少这些浪费,精益生产倡导使用5S管理方法。
5S是指整理(Seiri)、整顿(Seiton)、清扫(Seiso)、清洁(Seiketsu)和素养(Shitsuke)。
- 整理:将工作场所中无用的东西清除出去,只保留必要的物品。
- 整顿:将工作场所中的物品有序地摆放,方便取用。
为每个物品设立明确的标识。
- 清扫:保持工作场所的清洁,清除尘土和垃圾。
维持一个良好的工作环境。
- 清洁:对设备、工具和工作区域进行定期的清洁和维护,确保其正常运行。
- 素养:让员工养成良好的工作习惯和态度,培养责任心和自我管理能力。
通过5S管理,可以降低生产过程中的浪费,提高工作效率和质量。
它强调提高工作环境和员工意识,促进生产过程的规范化、标准化和自律化。
- 1、下载文档前请自行甄别文档内容的完整性,平台不提供额外的编辑、内容补充、找答案等附加服务。
- 2、"仅部分预览"的文档,不可在线预览部分如存在完整性等问题,可反馈申请退款(可完整预览的文档不适用该条件!)。
- 3、如文档侵犯您的权益,请联系客服反馈,我们会尽快为您处理(人工客服工作时间:9:00-18:30)。
推行精益生产常见的七大困惑
困惑1:我们导入水蜘蛛时,物料员原来一天只发两次料,现在要每小时送到不同工位去,工作负荷增大了很多,抱怨比较大,怎么处理?
导师解答:华商永续精益生产管理咨询培训专家认为,如果改用水蜘蛛确实能提高生产率,需要把产生的效益中的部分做为工资或奖金补贴给增加了工作量的员工,这是精益改善中双赢的原则;另外,也要想办法帮助水蜘蛛改进送料路线,工具,料车等,减轻其非增值的劳动。
困惑2:水蜘蛛送料有什么注意事项吗?
导师解答:采用水蜘蛛的目的是减少操作工人拿取物料的浪费,但我们发现很多生产线水蜘蛛只把物料送到工位工人座位旁边或后面,工人还是要转身或弯腰拿取物料,或者要移动拿取物料,所以设计水蜘蛛的时候,要注意送料直接送到作业人员双臂可以触及的范围,尽量减少动作浪费。
困惑3:我们看到丰田生产线节奏相当快,当员工想上洗手间时怎么办?
导师解答::每天上午和下午我们都有10分钟的工间休息,中午也有午餐时间,员工一般利用这些时间上洗手间,在这时间之外员工有上洗手间的要求时,会拉绳,由班长暂时顶替他的工作。
困惑4:我们不敢实施拉动看板,因为刚一尝试就发生了生产停线,大家压力都太大了。
导师解答:拉动式生产有些先决条件是要先营造的,如果条件不具备而盲目拉动,就会因为问题的暴露而让整个生产现场一片混乱。
这些条件包括:品质的稳定,物料供应的稳定,设备故障低,快速转换到位,人员能力具备等。
所以,企业应该先花时间研究目前阻碍拉动的各种限制因素,分别采取措施来消除后,再实施拉动系统,这个过程一般要1-2年,不可急功近利。
困惑5:精益生产是不是比较适合流水线作业,或者说类同于流水线作业,目前我们公司生产各工序生产作业比较独立,经常会出现很多在制品,产品从投入到产出周期长。
导师解答:华商永续精益生产管理咨询培训专家认为,精益生产没有说适合流水作业的,精益是可以用在制造业,服务业的。
对于生产各工序生产作业比较独立,经常会出现很多在制品的情况,这是实施精益化可以改善的地方,价值流管理的方法一般能有效地联系各比较独立的工序。
困惑6 :如何确定顾客需求量是多少来决定生产量?
导师解答:一般工厂是先定预测,再定生产数量、每天的生产计划,再制造。
TPS最大的特征是顾客需要多少,生产多少,客人买多少生产多少。
前工程、后工程,后工程接近客户,客人拿走多少,生产多少。
客户需要多少自己来取,也就是后工程的客户自己来取。
需要一点库存,多余的是没有的。
华商永续精益生产管理咨询培训专家认为,TPS是超市、市场的方式,美国的24小时超市、便利店的方式,开发了这个生产方式。
每天客户购买,每天将客户购买出的数量来补货,这前、后工程相当于这个购买补货过程。
困惑7 :我们工厂是计时制,发现有些员工偷懒,所以想改成计件制,可否?
导师解答:员工偷懒,问题在管理者,通过计件也许会短期让员工紧张起来,但其中会有隐患:因为计件的工时标准本来是可以不断改善的,一旦计件后,这种改善就没有了空间。
例如,现在生产效率是30分钟一个产品,如果每天工作8小时,那么计件就是16个产品,计件后,工人可能可以做到17-18个,如果生产效率可以提高到20分钟一个产品的话,意味着工人每天能做24个,这种通过公司投入技术或资金带来的效率的改善利益,就难以体现到工厂财务收益上,会给成本降低带来问题。
华商永续精益生产管理咨询培训专家认为,给员工设定标准作业,按照计时工作,提高的效率部分的利益,用合理奖金发放给员工,而非工资的方式。