注塑工艺缺陷分析
注塑缺陷描述及解决方案

注塑缺陷描述及解决方案一、缺陷描述注塑是一种常见的塑料加工方法,广泛应用于各个行业。
然而,在注塑过程中,常常会出现一些缺陷,影响产品的质量和性能。
下面将描述一些常见的注塑缺陷。
1. 气泡缺陷:气泡是注塑过程中常见的缺陷之一。
它们通常出现在塑料制品的表面或内部,给产品的外观和强度带来不利影响。
气泡的形成可能是由于塑料材料中含有挥发性成分,或者注塑过程中存在过高的温度或压力。
2. 热流痕缺陷:热流痕是由于注塑过程中塑料材料的流动受到阻碍而形成的。
它们通常呈线状或条状,并且会降低产品的外观质量。
热流痕的形成可能是由于模具设计不合理、注塑温度过高或注塑速度过快等原因。
3. 毛刺缺陷:毛刺是指产品表面出现的细小突起,给产品的触感和外观带来不良影响。
毛刺的形成可能是由于模具表面粗糙、注塑温度过高或注塑压力过大等原因。
4. 缩孔缺陷:缩孔是指塑料制品内部出现的空洞或凹陷,降低了产品的强度和密封性能。
缩孔的形成可能是由于注塑过程中塑料材料的收缩不均匀或注塑温度不合适。
5. 热胀冷缩缺陷:热胀冷缩是指注塑制品在冷却过程中由于温度变化而引起的尺寸变化。
如果注塑制品的尺寸与设计要求不符,就会影响产品的装配和使用。
热胀冷缩的控制需要合理设计模具和控制注塑工艺参数。
二、解决方案针对上述注塑缺陷,以下是一些常见的解决方案,以帮助改善产品质量和性能。
1. 气泡缺陷解决方案:- 选择低挥发性的塑料材料,减少挥发性成分的含量。
- 调整注塑过程中的温度和压力,避免过高的温度或压力导致气泡的形成。
- 使用真空抽气装置,帮助排除塑料材料中的气泡。
2. 热流痕缺陷解决方案:- 优化模具设计,确保塑料材料的流动畅通无阻。
- 降低注塑温度,避免过高的温度导致热流痕的形成。
- 控制注塑速度,避免过快的注塑速度导致热流痕的产生。
3. 毛刺缺陷解决方案:- 改善模具表面的光洁度,减少毛刺的形成。
- 调整注塑温度和压力,避免过高的温度或压力导致毛刺的产生。
注塑缺陷原因分析与解决方案

注塑缺陷原因分析与解决方案注塑是一种常见的塑料加工方法,广泛应用于各个行业。
然而,在注塑过程中,可能会出现各种缺陷,如气泡、翘曲、短射等问题,影响产品的质量和性能。
为了解决这些问题,我们需要进行缺陷原因分析,并提出相应的解决方案。
一、缺陷原因分析1. 气泡缺陷气泡是注塑过程中常见的缺陷之一。
其主要原因可能包括以下几个方面:- 塑料材料中含有挥发性物质,如水分、溶剂等,这些物质在高温下蒸发产生气泡。
- 注塑机温度设置不当,过高的温度会使塑料材料中的气体膨胀形成气泡。
- 注塑模具设计不合理,存在气孔或死角,导致塑料充填不均匀,形成气泡。
2. 翘曲缺陷翘曲是注塑产品常见的缺陷之一,其主要原因可能包括以下几个方面:- 注塑机温度不均匀,导致塑料材料在冷却过程中收缩不均匀,引起产品翘曲。
- 注塑模具设计不合理,存在过于薄弱的部位,无法承受注塑过程中的压力,导致产品变形。
- 注塑过程中冷却时间不足,使得产品在脱模后还未完全固化,导致变形。
3. 短射缺陷短射是指注塑产品未能充填满模具而产生的缺陷,其主要原因可能包括以下几个方面:- 注塑机温度设置不当,导致塑料材料粘度过高,无法充填满模具。
- 注塑模具设计不合理,存在过于狭窄的充填道或浇口,导致塑料流动受阻,无法充填满模具。
- 注塑过程中注射速度过快,导致塑料材料无法充填满模具。
二、解决方案1. 气泡缺陷的解决方案- 检查塑料材料的质量,确保其含水量和挥发性物质含量符合要求。
- 调整注塑机的温度,确保塑料材料在注塑过程中不会过热。
- 优化注塑模具的设计,避免气孔和死角的存在,确保塑料充填均匀。
2. 翘曲缺陷的解决方案- 调整注塑机的温度分布,确保塑料材料在冷却过程中收缩均匀。
- 优化注塑模具的设计,增加产品的结构强度,避免过于薄弱的部位。
- 增加注塑过程中的冷却时间,确保产品完全固化后再进行脱模。
3. 短射缺陷的解决方案- 调整注塑机的温度,降低塑料材料的粘度,促进充填。
注塑缺陷原因分析与解决方案
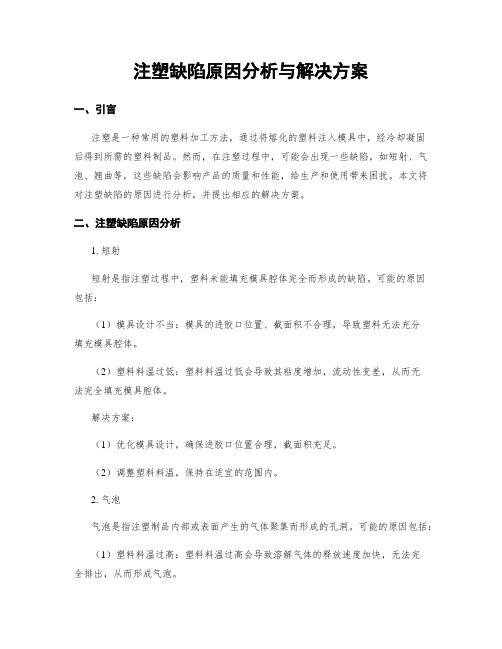
注塑缺陷原因分析与解决方案一、引言注塑是一种常用的塑料加工方法,通过将熔化的塑料注入模具中,经冷却凝固后得到所需的塑料制品。
然而,在注塑过程中,可能会出现一些缺陷,如短射、气泡、翘曲等,这些缺陷会影响产品的质量和性能,给生产和使用带来困扰。
本文将对注塑缺陷的原因进行分析,并提出相应的解决方案。
二、注塑缺陷原因分析1. 短射短射是指注塑过程中,塑料未能填充模具腔体完全而形成的缺陷。
可能的原因包括:(1)模具设计不当:模具的进胶口位置、截面积不合理,导致塑料无法充分填充模具腔体。
(2)塑料料温过低:塑料料温过低会导致其粘度增加,流动性变差,从而无法完全填充模具腔体。
解决方案:(1)优化模具设计,确保进胶口位置合理,截面积充足。
(2)调整塑料料温,保持在适宜的范围内。
2. 气泡气泡是指注塑制品内部或表面产生的气体聚集而形成的孔洞。
可能的原因包括:(1)塑料料温过高:塑料料温过高会导致溶解气体的释放速度加快,无法完全排出,从而形成气泡。
(2)模具排气不畅:模具腔体内的气体无法顺利排出,导致气泡的形成。
解决方案:(1)控制塑料料温,使其保持在适宜的范围内。
(2)优化模具结构,增加排气通道,确保气体能够顺利排出。
3. 翘曲翘曲是指注塑制品在冷却过程中,由于温度不均匀而导致的变形现象。
可能的原因包括:(1)模具温度不均匀:模具温度不均匀会导致注塑制品在冷却过程中收缩不均匀,从而产生翘曲。
(2)注塑压力不均匀:注塑过程中的压力分布不均匀,会导致塑料在模具中的填充不均匀,从而产生翘曲。
解决方案:(1)优化模具冷却系统,确保模具温度均匀。
(2)调整注塑过程中的压力分布,使之均匀。
三、结论注塑缺陷的原因多种多样,需要综合考虑多个因素。
在解决问题时,需要根据具体情况进行分析,并采取相应的解决方案。
通过优化模具设计、控制塑料料温、优化模具结构等手段,可以有效减少注塑缺陷的发生,提高产品质量和生产效率。
四、参考文献[1] 刘明, 张三. 注塑工艺缺陷原因分析及改进措施[J]. 塑料工业, 2018, 46(5): 12-15.[2] 王五, 李四. 注塑缺陷分析与解决方案研究[J]. 机械设计与制造, 2019, 37(2): 45-49.以上是对注塑缺陷原因分析与解决方案的详细描述,请参考。
注塑缺陷的分析ppt
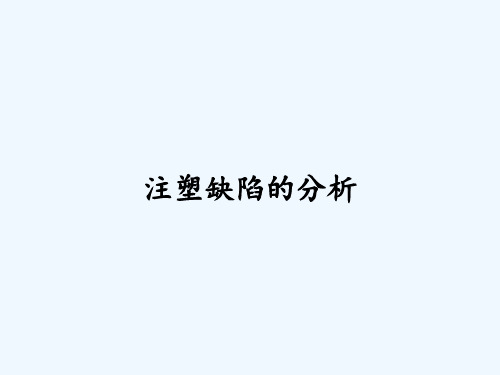
1、选择合理得浇口位置及 形式,将熔接线引导至不显
眼位置。
1、增加模温;2、加高熔体温度;3、优化注射速度 及注射压力。
六、湿气痕; 湿气痕由模壁上得冷凝水汽造成,就是顺着塑流得方向出现得灰白色喷射
线段,一些个案表现为表面气泡及粗糙。
故障件图片
成形原因:塑料粒子在存储或注塑过程中吸入了空气中得水分,当这种潮湿得 粒子在注塑熔化时,水分便变为水蒸气泡。由于熔料得模壁流动速度慢于中心 部位,这样这些水蒸气泡就被推向了塑件得表层,受压得气泡因为补偿压力而 爆破,随之被熔胶得流动波峰压至变形,并在模壁上固化。
度缺陷
1、选择合理得浇口位置(将熔接线放在不影响 产品处或将料流改为75°以上得汇流);2、模具 水路要合理,让有熔接线得模具对应处温度能调
得更高些;3、要有充分得排气。
1、加大保压;2、优化注射速度;3、增加熔胶温度 ;5、增加模具温度。
三、喷射纹; 喷射纹就是像蛇形般蜿蜒得粗糙得编织纹,出现在注塑件表面上, 极大得影响着零件得外观质量。 喷射纹一般均从浇口处开始,有时也可以从塑件得狭窄处开始。
1、选择合理得浇口大小及形式,需保证能 充分得补压;2、模具水路要合理,通过模 温得控制使其更好补压;3、要有充分得
排气。
1、料筒得储料行程就是否足够;2、保压及保压 时间就是否太小;3、注射速度就是否太小;4、增
加熔胶温度;5、增加模具温度。
二、熔接线; 熔接线一般均以线形方式显现。熔接线得出现会直接影响零件得 外观质量及零件强度。
得出现。
直接对着空腔得细小得浇 口最易形成喷射纹
优化后得浇口,料流通过上侧 壁模腔得阻挡,使前锋料与后 面得料流能很好得融合在一
注塑缺陷原因分析与解决方案
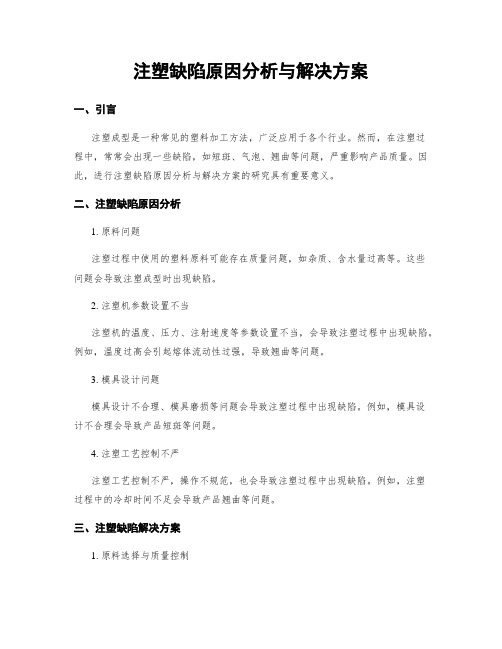
注塑缺陷原因分析与解决方案一、引言注塑成型是一种常见的塑料加工方法,广泛应用于各个行业。
然而,在注塑过程中,常常会出现一些缺陷,如短斑、气泡、翘曲等问题,严重影响产品质量。
因此,进行注塑缺陷原因分析与解决方案的研究具有重要意义。
二、注塑缺陷原因分析1. 原料问题注塑过程中使用的塑料原料可能存在质量问题,如杂质、含水量过高等。
这些问题会导致注塑成型时出现缺陷。
2. 注塑机参数设置不当注塑机的温度、压力、注射速度等参数设置不当,会导致注塑过程中出现缺陷。
例如,温度过高会引起熔体流动性过强,导致翘曲等问题。
3. 模具设计问题模具设计不合理、模具磨损等问题会导致注塑过程中出现缺陷。
例如,模具设计不合理会导致产品短斑等问题。
4. 注塑工艺控制不严注塑工艺控制不严,操作不规范,也会导致注塑过程中出现缺陷。
例如,注塑过程中的冷却时间不足会导致产品翘曲等问题。
三、注塑缺陷解决方案1. 原料选择与质量控制选择质量可靠的塑料原料供应商,并建立严格的原料质量控制流程。
对原料进行检测,确保无杂质、含水量符合要求。
2. 注塑机参数优化根据产品的特性和要求,合理设置注塑机的温度、压力、注射速度等参数。
通过试验和实践不断优化参数,提高注塑过程的稳定性和产品质量。
3. 模具设计与维护合理设计模具结构,避免出现短斑、翘曲等缺陷。
定期对模具进行维护和保养,及时更换磨损严重的部件,确保模具的稳定性和精度。
4. 注塑工艺控制与操作规范建立严格的注塑工艺控制流程,确保操作规范。
对注塑过程中的温度、压力、冷却时间等参数进行严格控制,避免出现缺陷。
5. 质量检测与反馈建立完善的质量检测体系,对注塑过程中的产品进行全面检测,及时发现和解决问题。
同时,建立反馈机制,将问题及时反馈给相关部门,进行改进和优化。
四、结论注塑缺陷是注塑成型过程中常见的问题,但通过对原因的分析和解决方案的实施,可以有效地提高产品质量,减少缺陷的发生。
因此,注塑缺陷原因分析与解决方案的研究具有重要的实际意义,并为注塑行业的发展提供了有益的参考。
注塑缺陷原因分析与解决方案
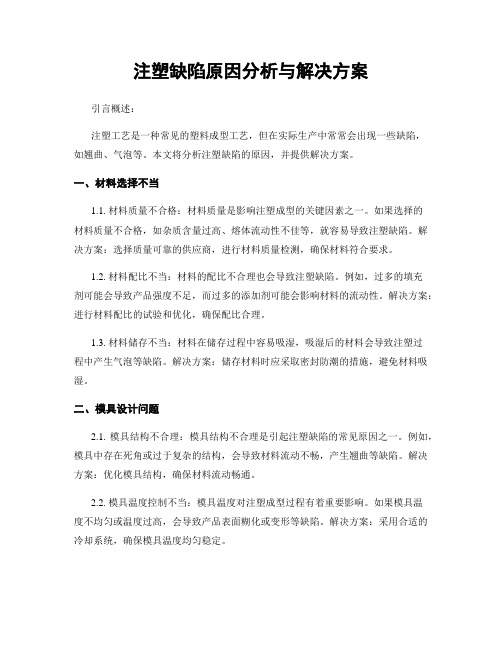
注塑缺陷原因分析与解决方案引言概述:注塑工艺是一种常见的塑料成型工艺,但在实际生产中常常会出现一些缺陷,如翘曲、气泡等。
本文将分析注塑缺陷的原因,并提供解决方案。
一、材料选择不当1.1. 材料质量不合格:材料质量是影响注塑成型的关键因素之一。
如果选择的材料质量不合格,如杂质含量过高、熔体流动性不佳等,就容易导致注塑缺陷。
解决方案:选择质量可靠的供应商,进行材料质量检测,确保材料符合要求。
1.2. 材料配比不当:材料的配比不合理也会导致注塑缺陷。
例如,过多的填充剂可能会导致产品强度不足,而过多的添加剂可能会影响材料的流动性。
解决方案:进行材料配比的试验和优化,确保配比合理。
1.3. 材料储存不当:材料在储存过程中容易吸湿,吸湿后的材料会导致注塑过程中产生气泡等缺陷。
解决方案:储存材料时应采取密封防潮的措施,避免材料吸湿。
二、模具设计问题2.1. 模具结构不合理:模具结构不合理是引起注塑缺陷的常见原因之一。
例如,模具中存在死角或过于复杂的结构,会导致材料流动不畅,产生翘曲等缺陷。
解决方案:优化模具结构,确保材料流动畅通。
2.2. 模具温度控制不当:模具温度对注塑成型过程有着重要影响。
如果模具温度不均匀或温度过高,会导致产品表面糊化或变形等缺陷。
解决方案:采用合适的冷却系统,确保模具温度均匀稳定。
2.3. 模具磨损严重:模具长时间使用后会出现磨损,磨损严重的模具会导致产品尺寸不准确或表面粗糙等缺陷。
解决方案:定期检查和维护模具,及时更换磨损严重的模具部件。
三、注塑工艺参数设置不当3.1. 注射压力过高或过低:注射压力是影响注塑成型的关键参数之一。
如果注射压力过高,会导致产品变形或开裂,而注射压力过低则会导致产品表面光洁度不高。
解决方案:根据产品要求和材料特性,合理设置注射压力。
3.2. 注射速度不合理:注射速度对产品的充填和冷却过程有着重要影响。
如果注射速度过快,会导致产品内部产生气泡或短射,而注射速度过慢则会导致产品表面瑕疵。
注塑缺陷原因分析与解决方案
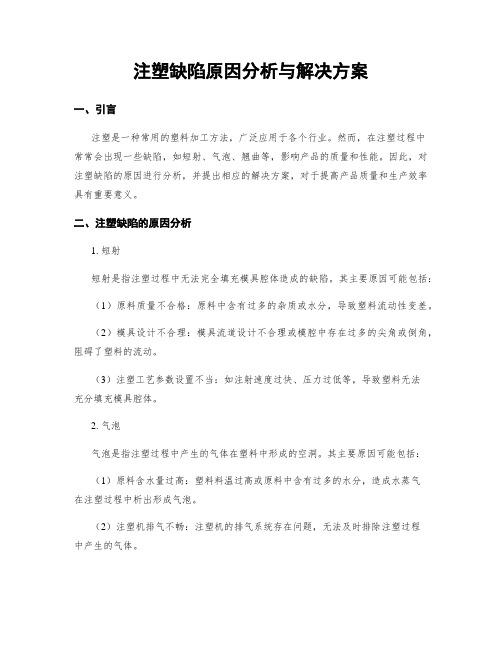
注塑缺陷原因分析与解决方案一、引言注塑是一种常用的塑料加工方法,广泛应用于各个行业。
然而,在注塑过程中常常会出现一些缺陷,如短射、气泡、翘曲等,影响产品的质量和性能。
因此,对注塑缺陷的原因进行分析,并提出相应的解决方案,对于提高产品质量和生产效率具有重要意义。
二、注塑缺陷的原因分析1. 短射短射是指注塑过程中无法完全填充模具腔体造成的缺陷。
其主要原因可能包括:(1)原料质量不合格:原料中含有过多的杂质或水分,导致塑料流动性变差。
(2)模具设计不合理:模具流道设计不合理或模腔中存在过多的尖角或倒角,阻碍了塑料的流动。
(3)注塑工艺参数设置不当:如注射速度过快、压力过低等,导致塑料无法充分填充模具腔体。
2. 气泡气泡是指注塑过程中产生的气体在塑料中形成的空洞。
其主要原因可能包括:(1)原料含水量过高:塑料料温过高或原料中含有过多的水分,造成水蒸气在注塑过程中析出形成气泡。
(2)注塑机排气不畅:注塑机的排气系统存在问题,无法及时排除注塑过程中产生的气体。
(3)注塑工艺参数设置不当:如注射速度过快、压力过高等,造成塑料内部气体无法顺利排出。
3. 翘曲翘曲是指注塑制品在冷却后出现变形的现象。
其主要原因可能包括:(1)模具温度不均匀:模具温度不均匀导致注塑制品冷却不均匀,从而引起翘曲。
(2)注塑过程中的应力积累:注塑过程中,塑料在注射后会受到冷却和收缩的影响,如果释放不及时,会导致应力积累引起翘曲。
(3)注塑工艺参数设置不当:如注射速度过快、冷却时间过短等,造成塑料冷却不充分,引起翘曲。
三、注塑缺陷的解决方案1. 短射的解决方案(1)优化原料质量:选择质量合格的原料,避免杂质和水分的存在。
(2)优化模具设计:合理设计模具流道,避免尖角和倒角的存在,保证塑料的顺畅流动。
(3)优化注塑工艺参数:合理设置注射速度和压力,确保塑料能够充分填充模具腔体。
2. 气泡的解决方案(1)控制原料含水量:确保塑料料温适宜,原料中的水分含量符合要求。
注塑成型各种缺陷分析总结
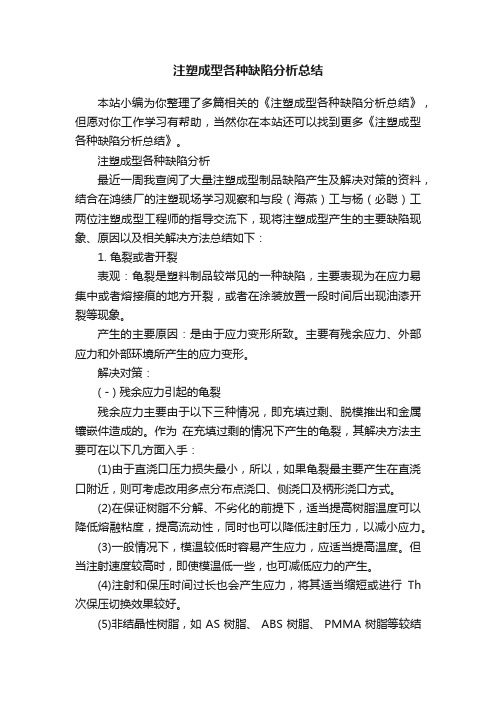
注塑成型各种缺陷分析总结本站小编为你整理了多篇相关的《注塑成型各种缺陷分析总结》,但愿对你工作学习有帮助,当然你在本站还可以找到更多《注塑成型各种缺陷分析总结》。
注塑成型各种缺陷分析最近一周我查阅了大量注塑成型制品缺陷产生及解决对策的资料,结合在鸿绩厂的注塑现场学习观察和与段(海燕)工与杨(必聪)工两位注塑成型工程师的指导交流下,现将注塑成型产生的主要缺陷现象、原因以及相关解决方法总结如下:1. 龟裂或者开裂表观:龟裂是塑料制品较常见的一种缺陷,主要表现为在应力易集中或者熔接痕的地方开裂,或者在涂装放置一段时间后出现油漆开裂等现象。
产生的主要原因:是由于应力变形所致。
主要有残余应力、外部应力和外部环境所产生的应力变形。
解决对策:(-) 残余应力引起的龟裂残余应力主要由于以下三种情况,即充填过剩、脱模推出和金属镶嵌件造成的。
作为在充填过剩的情况下产生的龟裂,其解决方法主要可在以下几方面入手:(1)由于直浇口压力损失最小,所以,如果龟裂最主要产生在直浇口附近,则可考虑改用多点分布点浇口、侧浇口及柄形浇口方式。
(2)在保证树脂不分解、不劣化的前提下,适当提高树脂温度可以降低熔融粘度,提高流动性,同时也可以降低注射压力,以减小应力。
(3)一般情况下,模温较低时容易产生应力,应适当提高温度。
但当注射速度较高时,即使模温低一些,也可减低应力的产生。
(4)注射和保压时间过长也会产生应力,将其适当缩短或进行Th 次保压切换效果较好。
(5)非结晶性树脂,如 AS 树脂、 ABS 树脂、 PMMA 树脂等较结晶性树脂如聚乙烯、聚甲醛等容易产生残余应力,应予以注意。
在注射成型的同时嵌入金属件时,最容易产生应力,而且容易在经过一段时间后才产生龟裂,危害极大。
这主要是由于金属和树脂的热膨胀系数相差悬殊产生应力,而且随着时间的推移,应力超过逐渐劣化的树脂材料的强度而产生裂纹。
(二) 外部应力引起的龟裂这里的外部应力,主要是因设计不合理而造成应力集中,特别是在尖角处更需注意。
注塑缺陷原因分析与解决方案

注塑缺陷原因分析与解决方案一、引言注塑是一种常用的塑料加工方法,广泛应用于各个行业。
然而,在注塑过程中,可能会浮现一些缺陷,例如短斑、气泡、翘曲等问题,这些缺陷会影响产品质量和使用寿命。
因此,对注塑缺陷的原因进行分析,并提出相应的解决方案,对于提高产品质量具有重要意义。
二、注塑缺陷原因分析1. 温度控制不当:注塑过程中,温度是一个关键因素。
如果温度过高或者过低,都会导致注塑缺陷。
例如,温度过高会导致熔融物流动性增加,易产生短斑;温度过低会导致熔融物流动性降低,易产生翘曲。
2. 压力控制不当:注塑过程中,压力也是一个重要因素。
如果压力过高或者过低,都会导致注塑缺陷。
例如,压力过高会导致短斑、气泡等缺陷;压力过低会导致产品密度不足,易产生翘曲。
3. 注塑模具设计问题:注塑模具的设计也会影响产品质量。
如果模具设计不合理,例如流道设计不良、冷却系统不完善等,都会导致注塑缺陷的产生。
4. 塑料材料选择不当:不同的塑料材料具有不同的熔点、流动性等特性。
如果选择的塑料材料与产品要求不匹配,也会导致注塑缺陷。
例如,选择的塑料材料熔点过高,容易产生短斑;选择的塑料材料流动性不足,容易产生翘曲。
5. 操作人员技术水平不高:注塑过程需要操作人员具备一定的技术水平。
如果操作人员技术水平不高,不了解注塑工艺的要点,也会导致注塑缺陷的产生。
三、注塑缺陷解决方案1. 温度控制方案:合理控制注塑过程中的温度,根据塑料材料的特性和产品要求,调整熔融温度和模具温度。
可以通过使用温度传感器和温度控制器来实时监测和调整温度,确保温度在合适的范围内。
2. 压力控制方案:合理控制注塑过程中的压力,根据塑料材料的特性和产品要求,调整注射压力和保压压力。
可以通过使用压力传感器和压力控制器来实时监测和调整压力,确保压力在合适的范围内。
3. 注塑模具设计方案:优化注塑模具的设计,确保流道设计合理、冷却系统完善。
可以通过使用CAD软件进行模具设计和摹拟分析,优化模具结构,减少缺陷的产生。
注塑缺陷原因分析与解决方案
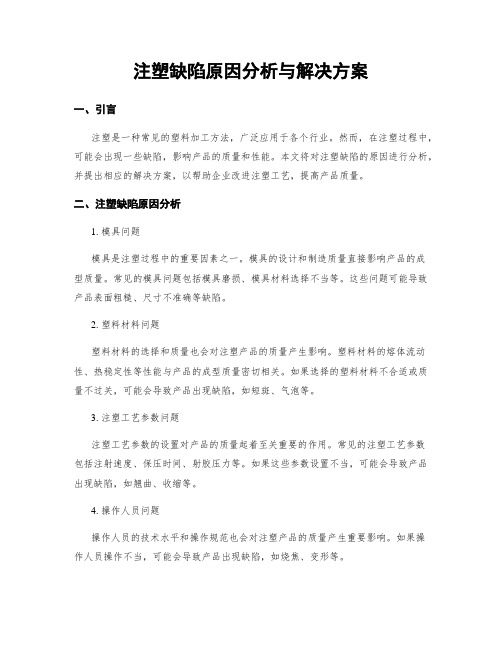
注塑缺陷原因分析与解决方案一、引言注塑是一种常见的塑料加工方法,广泛应用于各个行业。
然而,在注塑过程中,可能会出现一些缺陷,影响产品的质量和性能。
本文将对注塑缺陷的原因进行分析,并提出相应的解决方案,以帮助企业改进注塑工艺,提高产品质量。
二、注塑缺陷原因分析1. 模具问题模具是注塑过程中的重要因素之一。
模具的设计和制造质量直接影响产品的成型质量。
常见的模具问题包括模具磨损、模具材料选择不当等。
这些问题可能导致产品表面粗糙、尺寸不准确等缺陷。
2. 塑料材料问题塑料材料的选择和质量也会对注塑产品的质量产生影响。
塑料材料的熔体流动性、热稳定性等性能与产品的成型质量密切相关。
如果选择的塑料材料不合适或质量不过关,可能会导致产品出现缺陷,如短斑、气泡等。
3. 注塑工艺参数问题注塑工艺参数的设置对产品的质量起着至关重要的作用。
常见的注塑工艺参数包括注射速度、保压时间、射胶压力等。
如果这些参数设置不当,可能会导致产品出现缺陷,如翘曲、收缩等。
4. 操作人员问题操作人员的技术水平和操作规范也会对注塑产品的质量产生重要影响。
如果操作人员操作不当,可能会导致产品出现缺陷,如烧焦、变形等。
三、注塑缺陷解决方案1. 模具问题解决方案针对模具问题,可以采取以下解决方案:- 定期检查和维护模具,及时修复磨损部位,确保模具的精度和质量。
- 选择合适的模具材料,确保模具的耐磨性和使用寿命。
2. 塑料材料问题解决方案针对塑料材料问题,可以采取以下解决方案:- 选择合适的塑料材料,根据产品的要求选择具有良好流动性和热稳定性的材料。
- 严格控制塑料材料的质量,确保供应商提供的材料符合产品的要求。
3. 注塑工艺参数问题解决方案针对注塑工艺参数问题,可以采取以下解决方案:- 根据产品的要求和塑料材料的性能,合理设置注塑工艺参数,确保产品的成型质量。
- 进行工艺参数的优化和调整,通过试模和实验,找到最佳的注塑工艺参数。
4. 操作人员问题解决方案针对操作人员问题,可以采取以下解决方案:- 加强操作人员的培训和技术水平提升,确保操作人员具备良好的注塑操作技能和操作规范。
注塑产品常见的13种质量缺陷原因分析及解决办法
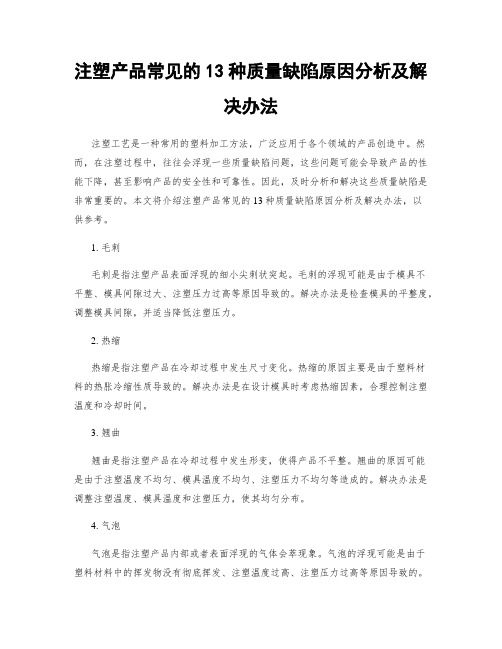
注塑产品常见的13种质量缺陷原因分析及解决办法注塑工艺是一种常用的塑料加工方法,广泛应用于各个领域的产品创造中。
然而,在注塑过程中,往往会浮现一些质量缺陷问题,这些问题可能会导致产品的性能下降,甚至影响产品的安全性和可靠性。
因此,及时分析和解决这些质量缺陷是非常重要的。
本文将介绍注塑产品常见的13种质量缺陷原因分析及解决办法,以供参考。
1. 毛刺毛刺是指注塑产品表面浮现的细小尖刺状突起。
毛刺的浮现可能是由于模具不平整、模具间隙过大、注塑压力过高等原因导致的。
解决办法是检查模具的平整度,调整模具间隙,并适当降低注塑压力。
2. 热缩热缩是指注塑产品在冷却过程中发生尺寸变化。
热缩的原因主要是由于塑料材料的热胀冷缩性质导致的。
解决办法是在设计模具时考虑热缩因素,合理控制注塑温度和冷却时间。
3. 翘曲翘曲是指注塑产品在冷却过程中发生形变,使得产品不平整。
翘曲的原因可能是由于注塑温度不均匀、模具温度不均匀、注塑压力不均匀等造成的。
解决办法是调整注塑温度、模具温度和注塑压力,使其均匀分布。
4. 气泡气泡是指注塑产品内部或者表面浮现的气体会萃现象。
气泡的浮现可能是由于塑料材料中的挥发物没有彻底挥发、注塑温度过高、注塑压力过高等原因导致的。
解决办法是控制注塑温度和压力,选择合适的塑料材料,并进行充分的挤出和干燥处理。
5. 缩孔缩孔是指注塑产品内部浮现的空洞状缺陷。
缩孔的原因可能是由于注塑温度过低、注塑压力不足、模具设计不合理等导致的。
解决办法是提高注塑温度、增加注塑压力,并优化模具设计。
6. 裂纹裂纹是指注塑产品表面或者内部浮现的裂纹状缺陷。
裂纹的浮现可能是由于注塑温度过高、注塑压力过大、冷却时间过短等原因导致的。
解决办法是降低注塑温度、减小注塑压力,并延长冷却时间。
7. 毛边毛边是指注塑产品边缘浮现的不平整现象。
毛边的原因可能是由于模具设计不合理、注塑压力过高、注塑速度过快等导致的。
解决办法是优化模具设计,降低注塑压力,并适当调整注塑速度。
注塑缺陷原因分析与解决方案
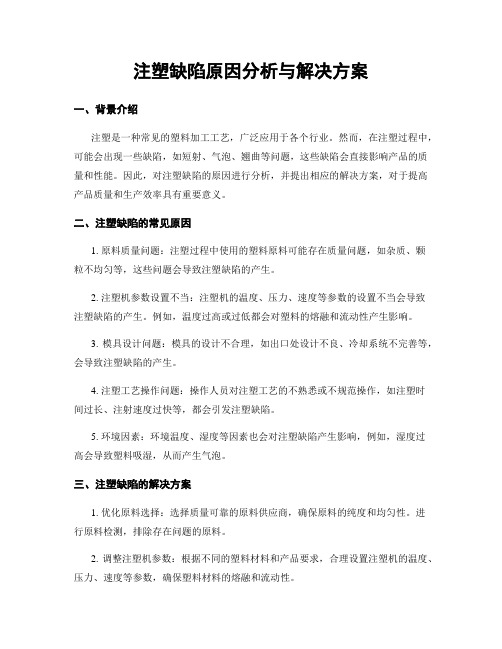
注塑缺陷原因分析与解决方案一、背景介绍注塑是一种常见的塑料加工工艺,广泛应用于各个行业。
然而,在注塑过程中,可能会出现一些缺陷,如短射、气泡、翘曲等问题,这些缺陷会直接影响产品的质量和性能。
因此,对注塑缺陷的原因进行分析,并提出相应的解决方案,对于提高产品质量和生产效率具有重要意义。
二、注塑缺陷的常见原因1. 原料质量问题:注塑过程中使用的塑料原料可能存在质量问题,如杂质、颗粒不均匀等,这些问题会导致注塑缺陷的产生。
2. 注塑机参数设置不当:注塑机的温度、压力、速度等参数的设置不当会导致注塑缺陷的产生。
例如,温度过高或过低都会对塑料的熔融和流动性产生影响。
3. 模具设计问题:模具的设计不合理,如出口处设计不良、冷却系统不完善等,会导致注塑缺陷的产生。
4. 注塑工艺操作问题:操作人员对注塑工艺的不熟悉或不规范操作,如注塑时间过长、注射速度过快等,都会引发注塑缺陷。
5. 环境因素:环境温度、湿度等因素也会对注塑缺陷产生影响,例如,湿度过高会导致塑料吸湿,从而产生气泡。
三、注塑缺陷的解决方案1. 优化原料选择:选择质量可靠的原料供应商,确保原料的纯度和均匀性。
进行原料检测,排除存在问题的原料。
2. 调整注塑机参数:根据不同的塑料材料和产品要求,合理设置注塑机的温度、压力、速度等参数,确保塑料材料的熔融和流动性。
3. 优化模具设计:对模具进行优化设计,确保出口处的设计合理,冷却系统完善,避免注塑缺陷的产生。
使用高质量的模具材料,提高模具的耐磨性和使用寿命。
4. 规范操作流程:对操作人员进行培训,提高其对注塑工艺的理解和操作技能。
建立规范的操作流程和记录,及时发现和解决问题。
5. 控制环境因素:保持注塑车间的适宜温湿度,避免环境因素对注塑缺陷的影响。
使用除湿设备,控制湿度在合理范围内。
四、注塑缺陷分析方法1. 观察法:通过对注塑产品外观的观察,发现缺陷的类型和位置,进而分析可能的原因。
2. 断面分析法:通过截取注塑产品的断面,观察其内部结构,分析缺陷产生的原因。
注塑缺陷原因分析与解决方案

注塑缺陷原因分析与解决方案引言概述:注塑是一种常见的制造工艺,用于生产各种塑料制品。
然而,在注塑过程中,常常会出现一些缺陷,如短射、气泡、翘曲等问题,影响产品的质量和性能。
本文将分析注塑缺陷的原因,并提出相应的解决方案,以帮助企业提高产品质量和生产效率。
正文内容:1. 原材料选择不当1.1. 塑料材料质量不稳定:不同批次的塑料材料可能存在成分差异,导致注塑过程中的缺陷。
1.2. 塑料材料含水量过高:过高的含水量会导致注塑过程中产生气泡、短射等缺陷。
2. 注塑工艺参数不合理2.1. 注射速度过快:过快的注射速度容易造成短射、气泡等缺陷。
2.2. 注射压力不足:不足的注射压力会导致产品翘曲、尺寸不准确等问题。
2.3. 注射温度不当:过高或过低的注射温度都会影响产品的质量,如翘曲、缩水等缺陷。
3. 模具设计问题3.1. 模具结构不合理:模具的结构设计不合理会导致产品的翘曲、尺寸不准确等缺陷。
3.2. 模具表面处理不当:模具表面的处理不当会导致产品出现划痕、气泡等问题。
4. 注塑机设备问题4.1. 注射机压力不稳定:注射机压力的不稳定会导致产品尺寸不准确、表面不光滑等缺陷。
4.2. 注射机温度控制不准确:温度控制不准确会导致产品翘曲、缩水等问题。
5. 操作人员技术不熟练5.1. 操作不规范:不规范的操作会导致产品尺寸不准确、表面不光滑等缺陷。
5.2. 操作技术不熟练:操作人员对注塑机设备和工艺参数不熟悉,无法及时调整,导致产品质量下降。
总结:通过分析注塑缺陷的原因,我们可以得出以下解决方案:首先,选择稳定的塑料材料,并控制好含水量。
其次,合理调整注塑工艺参数,控制注射速度、压力和温度。
再次,优化模具设计,确保结构合理,表面处理良好。
同时,保证注塑机设备良好的运行状态,调整好注射机压力和温度控制。
最后,加强操作人员的培训和技术水平,确保规范操作,熟练掌握注塑机设备和工艺参数的调整。
通过以上的分析和解决方案,企业可以有效地解决注塑过程中的缺陷问题,提高产品质量和生产效率。
注塑缺陷描述及解决方案
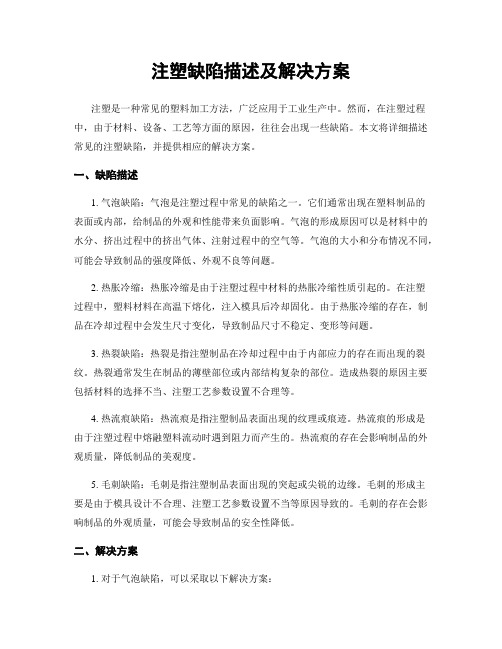
注塑缺陷描述及解决方案注塑是一种常见的塑料加工方法,广泛应用于工业生产中。
然而,在注塑过程中,由于材料、设备、工艺等方面的原因,往往会出现一些缺陷。
本文将详细描述常见的注塑缺陷,并提供相应的解决方案。
一、缺陷描述1. 气泡缺陷:气泡是注塑过程中常见的缺陷之一。
它们通常出现在塑料制品的表面或内部,给制品的外观和性能带来负面影响。
气泡的形成原因可以是材料中的水分、挤出过程中的挤出气体、注射过程中的空气等。
气泡的大小和分布情况不同,可能会导致制品的强度降低、外观不良等问题。
2. 热胀冷缩:热胀冷缩是由于注塑过程中材料的热胀冷缩性质引起的。
在注塑过程中,塑料材料在高温下熔化,注入模具后冷却固化。
由于热胀冷缩的存在,制品在冷却过程中会发生尺寸变化,导致制品尺寸不稳定、变形等问题。
3. 热裂缺陷:热裂是指注塑制品在冷却过程中由于内部应力的存在而出现的裂纹。
热裂通常发生在制品的薄壁部位或内部结构复杂的部位。
造成热裂的原因主要包括材料的选择不当、注塑工艺参数设置不合理等。
4. 热流痕缺陷:热流痕是指注塑制品表面出现的纹理或痕迹。
热流痕的形成是由于注塑过程中熔融塑料流动时遇到阻力而产生的。
热流痕的存在会影响制品的外观质量,降低制品的美观度。
5. 毛刺缺陷:毛刺是指注塑制品表面出现的突起或尖锐的边缘。
毛刺的形成主要是由于模具设计不合理、注塑工艺参数设置不当等原因导致的。
毛刺的存在会影响制品的外观质量,可能会导致制品的安全性降低。
二、解决方案1. 对于气泡缺陷,可以采取以下解决方案:a. 在材料加工前,对原料进行干燥处理,以减少材料中的水分含量。
b. 在注塑过程中,控制好挤出和注射过程中的温度和压力,避免产生气泡。
c. 优化模具设计,合理设置通气孔,以便将气泡排出。
2. 对于热胀冷缩问题,可以采取以下解决方案:a. 在模具设计中考虑材料的热胀冷缩性质,合理设置模具尺寸和结构,以减少尺寸变化。
b. 控制注塑过程中的温度和冷却时间,避免过快的冷却导致热胀冷缩问题。
注塑缺陷原因分析与解决方案
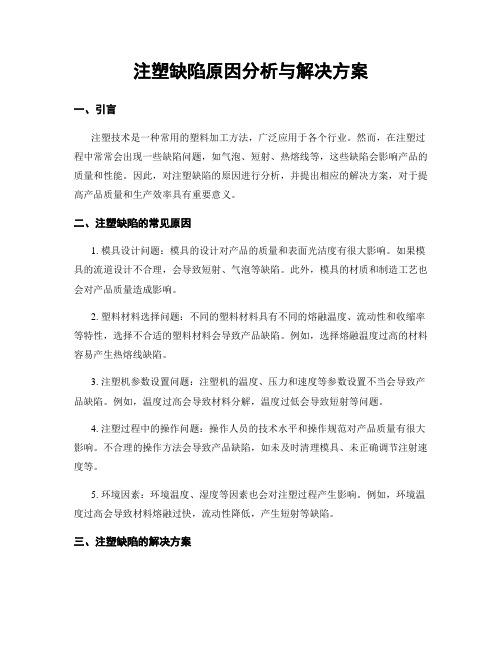
注塑缺陷原因分析与解决方案一、引言注塑技术是一种常用的塑料加工方法,广泛应用于各个行业。
然而,在注塑过程中常常会出现一些缺陷问题,如气泡、短射、热熔线等,这些缺陷会影响产品的质量和性能。
因此,对注塑缺陷的原因进行分析,并提出相应的解决方案,对于提高产品质量和生产效率具有重要意义。
二、注塑缺陷的常见原因1. 模具设计问题:模具的设计对产品的质量和表面光洁度有很大影响。
如果模具的流道设计不合理,会导致短射、气泡等缺陷。
此外,模具的材质和制造工艺也会对产品质量造成影响。
2. 塑料材料选择问题:不同的塑料材料具有不同的熔融温度、流动性和收缩率等特性,选择不合适的塑料材料会导致产品缺陷。
例如,选择熔融温度过高的材料容易产生热熔线缺陷。
3. 注塑机参数设置问题:注塑机的温度、压力和速度等参数设置不当会导致产品缺陷。
例如,温度过高会导致材料分解,温度过低会导致短射等问题。
4. 注塑过程中的操作问题:操作人员的技术水平和操作规范对产品质量有很大影响。
不合理的操作方法会导致产品缺陷,如未及时清理模具、未正确调节注射速度等。
5. 环境因素:环境温度、湿度等因素也会对注塑过程产生影响。
例如,环境温度过高会导致材料熔融过快,流动性降低,产生短射等缺陷。
三、注塑缺陷的解决方案1. 模具设计优化:通过优化模具的流道设计,增加冷却系统,改善模具表面光洁度等方式,减少短射、气泡等缺陷的发生。
此外,选择合适的模具材料和制造工艺也是提高产品质量的关键。
2. 塑料材料选择合理:根据产品要求选择合适的塑料材料,考虑其熔融温度、流动性和收缩率等特性。
通过调整材料的配方和添加剂,改善材料的流动性和熔融性,减少热熔线等缺陷的发生。
3. 注塑机参数优化:合理设置注塑机的温度、压力和速度等参数,确保材料能够充分熔融、流动和充实模腔。
通过调整注射速度、保压时间等参数,减少产品缺陷的发生。
4. 加强操作培训和规范:提高操作人员的技术水平,加强对注塑过程的培训和指导。
注塑缺陷原因分析与解决方案

注塑缺陷原因分析与解决方案一、引言注塑是一种常见的塑料加工方法,广泛应用于各个行业。
然而,在注塑过程中往往会浮现一些缺陷,如短射、气泡、热缩等。
本文将对注塑缺陷的原因进行分析,并提出相应的解决方案,以匡助企业提高产品质量和生产效率。
二、注塑缺陷原因分析1. 短射短射是指注塑过程中无法将塑料彻底填充模具腔体的现象。
短射的原因可能包括以下几点:- 模具设计不合理:模具的流道设计不合理或者过小,导致塑料无法充分流动。
- 注塑参数设置不当:注塑机的注射速度、压力等参数设置不当,影响了塑料的充填性能。
- 塑料材料选择不当:选择的塑料材料流动性差,导致无法充分填充模具腔体。
2. 气泡气泡是指注塑制品中浮现的气体会萃的现象。
气泡的原因可能包括以下几点:- 塑料材料含水量高:塑料材料含水量高会在注塑过程中产生蒸汽,形成气泡。
- 注塑机排气不畅:注塑机排气系统不畅,无法及时排出注塑过程中产生的气体。
- 模具设计不合理:模具中存在死角或者过小的通气孔,导致气体无法顺利排出。
3. 热缩热缩是指注塑制品在冷却后发生尺寸变化的现象。
热缩的原因可能包括以下几点:- 注塑温度过高:注塑温度过高会导致塑料在冷却后收缩过大。
- 模具温度不均匀:模具的温度分布不均匀,导致注塑制品冷却不均匀,进而引起热缩。
- 塑料材料热性能不稳定:选择的塑料材料热性能不稳定,导致注塑制品在冷却后发生尺寸变化。
三、注塑缺陷解决方案1. 短射解决方案- 模具设计合理化:优化模具的流道设计,增加流道的截面积,确保塑料能够充分流动。
- 注塑参数优化:根据塑料材料的特性,合理设置注塑机的注射速度、压力等参数,保证塑料充填模具腔体。
- 选择合适的塑料材料:根据产品的要求,选择流动性好的塑料材料,提高充填性能。
2. 气泡解决方案- 塑料材料干燥处理:在注塑过程前,对塑料材料进行干燥处理,降低含水量,减少气泡的产生。
- 注塑机排气系统改进:优化注塑机的排气系统,增加排气孔的数量和大小,提高排气效果。
注塑缺陷分析解决方案(3篇)

第1篇摘要:注塑成型是塑料制品生产中常用的加工方法,但由于各种原因,注塑过程中可能会出现各种缺陷,影响产品的质量和外观。
本文将对注塑缺陷进行分析,并提出相应的解决方案,以帮助生产者提高产品质量,降低生产成本。
一、引言注塑成型是将熔融塑料注入模具中,经过冷却、固化后得到所需形状和尺寸的塑料制品的过程。
注塑成型具有生产效率高、成本低、制品精度高等优点,因此在塑料工业中得到广泛应用。
然而,在注塑过程中,由于设备、工艺、材料等方面的原因,可能会出现各种缺陷,影响产品的质量和外观。
因此,对注塑缺陷进行分析,并提出有效的解决方案,对于提高产品质量和降低生产成本具有重要意义。
二、注塑缺陷分析1. 热变形热变形是指塑料制品在加热过程中,由于材料的热膨胀系数不同,导致制品尺寸发生变化的现象。
热变形缺陷的主要原因包括:(1)材料选择不当:不同塑料的热膨胀系数不同,若选择热膨胀系数大的材料,在加热过程中易发生热变形。
(2)模具设计不合理:模具冷却系统设计不合理,导致制品在冷却过程中温度分布不均匀,从而引起热变形。
(3)注塑温度过高:注塑温度过高,使塑料熔体在模具内流动速度加快,导致制品内部应力增大,从而引起热变形。
2. 熔接痕熔接痕是指塑料制品在注塑过程中,由于熔体流动速度不同,导致熔体在界面处发生不均匀冷却和固化,形成明显的接痕。
熔接痕缺陷的主要原因包括:(1)注塑速度过快:注塑速度过快,导致熔体在模具内流动速度不均匀,从而形成熔接痕。
(2)模具设计不合理:模具流道设计不合理,导致熔体在流动过程中发生偏移,形成熔接痕。
(3)材料流动性差:材料流动性差,导致熔体在流动过程中容易发生堆积,从而形成熔接痕。
3. 射痕射痕是指塑料制品在注塑过程中,由于塑料熔体在模具内流动时受到阻碍,导致熔体在界面处发生不均匀冷却和固化,形成明显的痕迹。
射痕缺陷的主要原因包括:(1)模具设计不合理:模具流道设计不合理,导致熔体在流动过程中受到阻碍,从而形成射痕。
注塑缺陷描述及解决方案

注塑缺陷描述及解决方案一、缺陷描述:注塑是一种常见的塑料加工工艺,用于制造各种塑料制品。
然而,在注塑过程中可能会出现一些缺陷,影响产品的质量和性能。
以下是常见的注塑缺陷描述:1. 气泡:在注塑制品中出现的气泡是一种常见的缺陷。
气泡可能是由于注塑材料中的气体未能完全排出,或者由于注塑过程中的温度和压力不合适导致的。
2. 热裂纹:热裂纹是指注塑制品在冷却过程中出现的裂纹。
这种缺陷通常是由于注塑材料的热收缩不均匀或注塑过程中的冷却速度不合适引起的。
3. 热变形:热变形是指注塑制品在使用过程中由于温度变化而发生的形状变化。
这种缺陷可能是由于注塑材料的热稳定性不好或注塑过程中的温度控制不当引起的。
4. 短射:短射是指注塑制品中出现的未充填完全的区域。
这种缺陷可能是由于注塑模具的设计不合理或注塑过程中的注塑速度不适当导致的。
5. 毛刺:毛刺是指注塑制品表面出现的不平整或多余的塑料。
这种缺陷通常是由于注塑模具的设计不良或注塑过程中的压力控制不当引起的。
二、解决方案:针对以上注塑缺陷,我们可以采取一些解决方案来提高产品的质量和性能。
1. 气泡解决方案:a. 优化注塑工艺参数,确保注塑过程中的温度和压力控制在合适的范围内。
b. 使用低气泡率的注塑材料,减少气泡的生成。
c. 加入适量的排气装置,帮助排除注塑材料中的气体。
2. 热裂纹解决方案:a. 优化注塑模具设计,确保注塑制品在冷却过程中受力均匀。
b. 控制注塑过程中的冷却速度,避免过快或过慢导致的热裂纹。
c. 选择具有良好热稳定性的注塑材料,减少热收缩不均匀引起的热裂纹。
3. 热变形解决方案:a. 选择具有良好热稳定性的注塑材料,降低热变形的风险。
b. 控制注塑过程中的温度,避免温度变化过大引起的热变形。
c. 优化产品结构设计,减少热变形对产品性能的影响。
4. 短射解决方案:a. 优化注塑模具设计,确保注塑材料能够充填完全。
b. 控制注塑过程中的注塑速度,避免过快或过慢导致的短射。
注塑缺陷原因分析与解决方案

注塑缺陷原因分析与解决方案一、引言注塑工艺是一种常用的塑料加工方法,广泛应用于各个领域。
然而,在注塑过程中,常常会出现一些缺陷,如气泡、翘曲、短射等问题,严重影响产品的质量和性能。
因此,对注塑缺陷的原因进行分析,并提出相应的解决方案,对于提高产品质量和生产效率具有重要意义。
二、注塑缺陷的原因分析1. 模具设计不合理:模具是注塑过程中的关键因素之一,模具的设计不合理会导致产品缺陷。
例如,模具中存在过于复杂的结构、不合理的冷却系统等,都可能引起产品的翘曲、短射等问题。
2. 塑料材料选择不当:不同的塑料材料具有不同的物理性能和熔融特性,选择不当会导致产品缺陷。
例如,选择的塑料材料熔点过高或过低,都会影响产品的成型效果。
3. 注塑工艺参数设置错误:注塑工艺参数的设置对于产品质量至关重要。
例如,注射压力、注射速度、保压时间等参数的设置不当,都会导致产品的缺陷,如气泡、短射等。
4. 模具磨损和老化:长时间使用的模具会出现磨损和老化现象,导致产品的尺寸精度下降。
此外,模具的使用寿命过长也会影响产品质量。
5. 注塑设备故障:注塑设备的故障也是导致产品缺陷的原因之一。
例如,注射机的温度控制不准确、压力控制不稳定等,都会对产品的成型效果产生影响。
三、注塑缺陷的解决方案1. 模具设计优化:通过对模具的结构进行优化设计,减少复杂结构的使用,合理设计冷却系统,可以有效降低产品缺陷的发生率。
2. 塑料材料选择合理:根据产品的要求和特性选择合适的塑料材料,确保其熔融特性和物理性能与产品的要求相匹配。
3. 注塑工艺参数优化:通过合理设置注塑工艺参数,如注射压力、注射速度、保压时间等,控制好温度和压力的变化,可以提高产品的成型效果。
4. 定期维护和更换模具:定期对模具进行维护,及时更换磨损和老化的部件,可以保证模具的精度和使用寿命,提高产品的质量。
5. 定期检查和维护注塑设备:定期检查注塑设备的温度控制、压力控制等系统,确保其正常工作,减少设备故障对产品质量的影响。
注塑缺陷原因分析与解决方案

注塑缺陷原因分析与解决方案引言概述:注塑工艺是一种常见的制造工艺,广泛应用于各个行业。
然而,在注塑过程中,常常会出现一些缺陷,如短射、气泡、翘曲等问题。
本文将从原因分析和解决方案两个方面,详细介绍注塑缺陷及其解决方法。
一、短射问题1.1 原因分析:短射是指注塑制品在充模过程中未能完全填充模腔,导致制品出现不完整或缺陷。
其主要原因包括:1.1.1 注射速度过快:过快的注射速度会导致熔融塑料在进入模腔之前已经开始凝固,从而无法完全填充模腔。
1.1.2 模具温度不合适:模具温度过低会导致塑料熔融不完全,无法充分填充模腔。
1.1.3 压力不足:注塑机的射胶压力不足会导致塑料无法充分填充模腔。
1.2 解决方案:针对短射问题,可以采取以下解决方案:1.2.1 调整注射速度:根据具体情况,适当调整注射速度,以确保塑料能够完全填充模腔。
1.2.2 控制模具温度:通过调整模具温度,确保塑料能够充分熔融,提高注塑质量。
1.2.3 增加射胶压力:适当增加注塑机的射胶压力,以保证塑料能够充分填充模腔。
二、气泡问题2.1 原因分析:气泡是注塑制品中常见的缺陷之一,其主要原因包括:2.1.1 塑料中含有气体:在塑料加工过程中,如果塑料中含有气体,会在注塑过程中形成气泡。
2.1.2 注射过程中的气体:注射过程中,如果注射速度过快,会产生气泡。
2.1.3 模具温度不稳定:模具温度不稳定会导致塑料熔融不均匀,从而产生气泡。
2.2 解决方案:针对气泡问题,可以采取以下解决方案:2.2.1 塑料预处理:在注塑前对塑料进行预处理,去除其中的气体,以减少气泡的产生。
2.2.2 控制注射速度:控制注射速度,避免过快注射导致气泡产生。
2.2.3 稳定模具温度:通过控制模具温度,确保塑料能够充分熔融,减少气泡的产生。
三、翘曲问题3.1 原因分析:翘曲是指注塑制品在冷却后出现变形或弯曲的现象,其主要原因包括:3.1.1 冷却不均匀:冷却不均匀会导致注塑制品不均匀收缩,从而产生翘曲。
- 1、下载文档前请自行甄别文档内容的完整性,平台不提供额外的编辑、内容补充、找答案等附加服务。
- 2、"仅部分预览"的文档,不可在线预览部分如存在完整性等问题,可反馈申请退款(可完整预览的文档不适用该条件!)。
- 3、如文档侵犯您的权益,请联系客服反馈,我们会尽快为您处理(人工客服工作时间:9:00-18:30)。
收缩率
收缩率
收缩率
保压时间
保压压力
模腔表面温度
收缩率
收缩率
收缩率
熔体温度
注射时间
如图: 各参数对材料收缩的影响
脱模温度
> 浇口冷凝太早: (1)浇口尺寸偏小 (2)模具温度太低
> 材料上: 材料本身收缩太大
注意: (1)转压点的合理设定 (2)模具温度过低 (3)止回阀的磨损
正确区分: 气泡”,和 空洞”
模具上:
· 增大浇口尺寸 · 增大主流道和分流道的直径 · 浇口应尽可能设在空洞产生部位(较厚部分)的附近 · 减小产品壁厚
> 加快表面固化
降低模具温度. 注意: 可能会诱发真空空洞.
模温对空洞,凹痕的影响:
当模温偏高时就容易形成凹痕,而 在模温偏低时容易形成空洞
图3. 模温引发空洞或凹痕
> 添加蚀纹, 隐藏凹痕.
填充末端,排气不畅 处出现的气泡
> 塑化阶段: 气体没有排出
气熔 体体
塑 气熔 料 体体
塑 料
气熔 体体
料筒内部空气
* 螺杆转速太快 * 背压太低 * 回吸量太大/回吸速度太快
计量段 压缩段
加料段
吸入气体
排气
> 填充阶段: 射速太快,造成模腔内空气无法排出
> 树脂降解的瓦斯气体:
+ 料筒温度太高 + 料筒停留时间太长 + 混入其他易分解材料材料
熔体流动最末端 被压缩产生局部高温, 从而烧
焦材料, 产生焦斑.
加强筋和肋
采取措施:
(1) 减少气体, 水汽和材料降 解; (2) 加强排气 (3) 采用多级注射, 改变焦斑 位置
不同的熔体流相互会合的地方
浇口斑纹
物理原因: 当熔体流过浇口时, 由于速度过
快, 使得 流动发生不稳定甚至喷射 , 这些不 稳定流动的熔体遇到相对低温的模腔表面后迅 速冷却固化, 即使后来的材料通过保压也无法 填平, 于是在外层显现出浇口斑纹等缺陷
PMMA制成的调羹厚壁处 产生的空洞
物理原因: 一开始, 产品会形成
坚硬的冷却层, 并且根据模具的冷 却程度朝里或快或慢的发展.在厚壁 区域,中心部分任保持较高的温度和 粘性, 继续收缩, 如果此时冷却层 有足够的刚度抵抗其收缩应力, 则 在制品中心部分形成真空. 所以, 空洞一般发生在产品壁厚最 厚处!
3. 检查 螺杆和料桶 是否磨损. 喷 嘴和模具, 法兰和料筒, 喷嘴和法兰 之间的配合面, 是否有阶梯,不平整, 或损坏而使树脂滞留成为可能.
使用适合模具大小的成型机。
- 针对杂质
1. 请充分清洗:
常用的清洗方法: (1) 高粘度PE,PP (2) 化学清洗剂: (3) 拆螺杆,用铜刷刷
* 对于光学产品或要求较高的可采用一种材料一个料筒的方法.
> 抑制材料降解
(1) 降低机筒温度
(2) 减少材料在料桶内滞留时间
注意:
(3) 彻底清理料筒及各个辅机, 防止混料 (1)回吸速度太快
> 抑制水汽: 烘干材料
(2)螺杆是否太大 (3)模具型腔是否脏
> 模具上: 改善排气状况
(4)材料干燥
空洞
PMMA 厚壁处出现的空洞
两个例子共同特点: 空洞均发生在壁厚的地方
标题
企业介绍
演示者 日期
气泡
尼龙薄壁制品表面的气泡.
由于薄截面, 气泡使制品表面发 生拱起变形. 在模腔内被压缩的 气体在脱模瞬间或脱模后由于 不再受到模腔的容积限制而发 生凸起.
PC容器 内部的气泡.
由于产品表面足够的 刚度使气泡残留在产 品内部.
物理原因:
由于空气,材料降解或水分的原因,产生了 气体, 造成产品内部空隙或表面凸起. 特点: 气泡有着不同的尺寸和形状. 并且 可以发生在任何部位(即位置是不固定的).
注意:
区分是包风还是收缩而形 成的凹陷。
焦斑
PC材料制成的透明制品, 排 气不良发生在有 筋板 的地方
流动末端,排气不畅出险 的烧焦
透明PMMA产品在 熔 接痕 处产生排气不良
熔接痕 处产生排气不良
加强筋处排气不畅出现的烧焦。
常见的烧焦发生的地方
物理原因: 当流动末端排气
不畅时, 随着流动的继续, 气体
> 针对颜料混合不均:
+ 工艺上: 增加螺杆背压 降低螺杆速度; 增加料筒温度, 用直径较大或长径比较大的料筒;
PP制品在浇口附近的烧焦斑 纹, 这是熔体在热流道内发生 了降解
PE瓶胚
来自热流道分流道内的完 好的熔体
在热流道主体或主流道内 发生了降解的熔体
来自料桶内的材料也是 完好的.
黑点,灰黑斑纹的对策
- 针对加料降解
1. 检查料筒设定温度;热流道温度是否过高
建议用树脂温度计等测量实际温度。
2. 检查材料在料桶内滞留时间是否太长
模具上:
· 增大浇口尺寸 · 增大主流道和分流道的直径 · 浇口应尽可能设在空洞产生部位(较厚部分)的附近 · 减小产品壁厚
> 减慢浇口固化时间
·提高模具温度. 注意: 可能会诱发凹痕. · 加大浇口尺寸
> 材料上: 更换材料等级或添加助剂
凹痕
PS产品背部柱头 厚 度过大 产生凹陷
物理原因: 一开始, 产品会形成坚硬的冷
> 树脂分解
法兰和料桶 喷嘴和模具
喷嘴和法兰 螺杆止回阀
螺杆表面不平
注意:
喷嘴和模具, 法兰和料筒, 喷嘴和法兰之间的配合面, 是否有阶梯,不平整,或损坏而使树脂 滞留成为可能.
喷嘴和浇口套的匹配
> 杂料
+ 清洗不充分, 使上次生产使用的材料滞留在料筒里. + 异物混入. 特别是回料 . 或粉末太多
模温: 过低的模温会使不稳
定流动的熔体迅速固化, 从而 加剧浇口处的斑纹缺陷.
> 表面冷凝层的破裂和移动
F f
- 工艺上: 注射速度偏快 - 模具上: 浇口尺寸偏小 - 材料上: 材料流动性偏低
v
速度分布
F
模温: 过低的模温会使不稳f
定流动的熔体迅速固化, 从而 加剧浇口处的斑纹缺陷.
> 气体造成的斑纹
厚壁制品浇 口处的喷射纹
物理原因: 当熔体流过浇口时, 由于流速大
且黏性高, 使得浇口附近的材料和材料之间的 剪切力过大, 从而 表面冷却层的部分材料发 生断裂和错位, 这些错位迅速冷却固化后在外
层显现出浇口斑纹等缺陷
采用中心浇口PC产品 浇口附近的暗晕
物理原因: 当熔体流过浇口时, 由于流速大
直角转角
> 更改材料等级
当无法解决问题,且不可 改变模具形状时,改用其 他等级的材料也不失为一种对策.
圆角过渡
突起的顶针 调整长度
银纹
物理原因: 由于水汽,空气
或混有杂质, 当熔体流动时, 有的气体和杂质逐步渗到产 品表面, 使材料分层, 即使 很大的压力也无法使它们很 强的结合, 表现为银纹或银 斑.
银纹的对策
> 排除气体
+ 检查计量状态
* 检查预塑时间是否稳定 * 降低螺杆转速
*上下调节背压
+ 检查树脂温度:树脂分解
+ 检查排气口
偶尔会因排气不畅而产生银纹,因此应检查排气口的大小是否足够。
> 强化干燥 ; 同时确认模具是否漏水
确认干燥温度和干燥时间; 或采用水份检测仪进行水分检测.
> 有无污染物
特点: 总是沿着流动方向
> 水分
+ 材料的干燥不足
烘干的ABS和未烘干的ABS
+ 模具型腔漏水
> 气体
烘干的PMMA和未烘干的PMMA
> 杂料
* 料桶内上次生产未清理干净的料 * 辅机各部位及其管道内残留的上次生产的料 * 清理料管的PP或PE等
* 材料本身含有杂料; 特别注意回料的质量问题
另外添加有助染剂白油,润滑剂硅油,增塑剂丁二酯,以及稳定剂,抗静电剂的材料易产 生表面剥离和银纹.
2.排除污染
(1) 检查材料输送过程是否有异物混入可能 (2) 检查回料是否干净 (3) 检查附机和料筒(材料输送过程) 是否清理干净
- 排除多余气体
色差
ABS 制品表面色 差: 由于料桶温度 太低导致原料和色 母的混合不均
PMMA制品表面色差: 料桶内材料停留时间太 短导致混合不均
生成原因: - 颜料混料不均 - 材料降解
由于注射速度极低,出现 了明显的唱片纹
具体原因:
> 注射速度过 慢
> 模具温度偏低
> 材料粘度太大
滑痕
顶针处沿流动方 向上的晕斑.
PVC产品锐边过渡的区 域出现的大面积黯区
锐边过渡区出现 的毛糙现象
物理原因: 在注塑过程中,
型腔表面形成固化层, 由于 剪切力过大, 该固化层出现 断裂, 并发生移动, 在外观 上表现为毛糙.
有效保压偏低时产生凹痕
> 冷却时间不足
(1)冷却时间不够, 造成冷却层刚度不足,产生凹陷. (2)冷却时间不够,造成后收缩增加。 - 鉴于浇口位置的重要性,必须尽可能将其设置在厚壁处。
凹痕的对策
> 补充树脂: 增加型腔压力, 减小材料收缩
工艺上: ·确认转压点 · 提高保压压力;确认保压时间
设备上: ·检查螺杆及止回阀三件套是否磨损
F
f
v
速度分布
F f
滑痕的对策
> 调整注射速度(必要时采用多级注射)
一般偏向低的注射速度
开始时采用低速注射,直 到流体前端接触到斜面末 端, 然后用较高注射速度 进行加工.