《几种先进的连续生产技术》
先进生产技术

先进制造技术一,什么是柔性制造技术简称FMS,是一组数控机床和其他自动化的工艺设备,由计算机信息控制系统和物料自动储运系统有机结合的整体。
柔性制造系统由加工、物流、信息流三个子系统组成。
柔性制造系统是由统一的信息控制系统、物料储运系统和一组数字控制加工设备组成,能适应加工对象变换的自动化机械制造系统(Flexible Manufacturing System),英文缩写为FMS。
FMS的工艺基础是成组技术,它按照成组的加工对象确定工艺过程,选择相适应的数控加工设备和工件、工具等物料的储运系统,并由计算机进行控制,故能自动调整并实现一定范围内多种工件的成批高效生产(即具有“柔性”),并能及时地改变产品以满足市场需求。
FMS兼有加工制造和部分生产管理两种功能,因此能综合地提高生产效益。
FMS的工艺范围正在不断扩大,80年代中期投入使用的FMS,大都用于切削加工,也有用于冲压和焊接的。
采用FMS的主要技术经济效果是:能按装配作业配套需要,及时安排所需零件的加工,实现及时生产,从而减少毛坯和在制品的库存量,及相应的流动资金占用量,缩短生产周期;提高设备的利用率,减少设备数量和厂房面积;减少直接劳动力,在少人看管条件下可实现昼夜24小时的连续“无人化生产”;提高产品质量的一致性。
没有固定加工顺序和生产节拍,适应多品种小批量生产的机械制造系统。
FMS的工艺基础是成组技术,它按照成组的加工对象确定工艺过程,选择相适应的数控机床或工件、工具等物料储运系统。
柔性制造系统以计算机为核心进行系统管理,用无人搬运车进行工件传送,用数控技术实现自动化加工,具有监视切削状态和精度、诊断和复原等功能,还能在一定范围内完成一种零件加工到另一种零件加工的自动转换。
二,柔性制造系统-发展概况20世纪50年代,为了提高生产率,适用于大批量生产的组合机床和刚性自动线等专用设备得到很大发展。
60年代,随着小批量高精度加工产品的不断增加,数控机床和加工中心进入了鼎盛时期。
先进制造技术-3精密与超精密加工技术

先进制造技术之四
精密与超精密加工技术
6、3、1 研磨加工的机制和特点
超微细加工以电子束、离子束和激光束三束加工 为基础,采用沉积、刻蚀、溅射和蒸镀等加工手段进 行各种处理。
先进制造技术之四
精密与超精密加工技术
4、超精密加工的主要研究领域包括:
超精密加工技术是以高精度为目标的技术, 它必须综合应用各种新技术,在各个方面精益 求精的条件下,才有可能突破常规技术达不到 的程度界限,实现新的高精度指标。
6、2 超精密磨削
加工精度:0.1um,Ra0.002~0.02um的磨削方法 超精密磨削一般采用细粒度(80#-400#)砂轮,经过 精细修整,光磨4-6次,便可获得粗糙度为Ra 0.005 ~ 0.02 um的加工表面。
先进制造技术之四
精密与超精密加工技术
(1)超精密磨削表面的形成机制
超精密磨削获得的极低的表面粗糙度,主要靠砂轮精 细修整得到的大量的、等高性很好的微刃来实现微量切削 作用。
升,以后磨损逐渐减慢。 注:由于积屑瘤的原因,一般将研磨好的锋利刀
尖有意加工成理想的稳定的磨损状态。 2)切削速度和振动
提高切削速度有利于获得良好的加工表面,但注意 以不产生振动为准则。
先进制造技术之四
精密与超精密加工技术
(a) 直线刃刀头 (b) 直线刃刀头
(c) 圆弧刃刀头
先进制造技术之四
精密与超精密加工技术
精密与超精密加工技术
精细化工中的高真空连续精馏技术
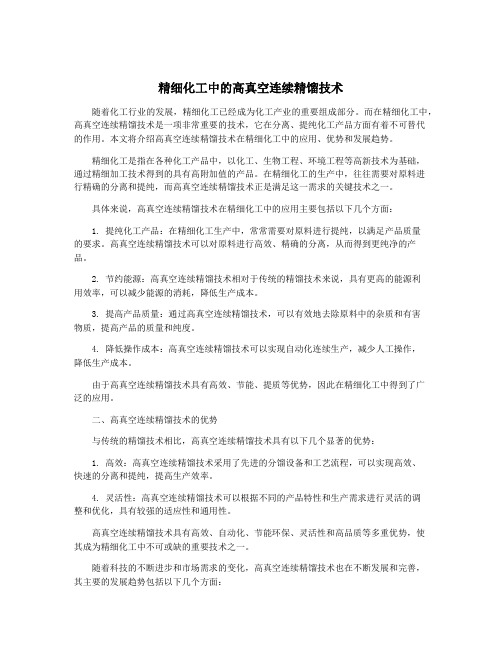
精细化工中的高真空连续精馏技术随着化工行业的发展,精细化工已经成为化工产业的重要组成部分。
而在精细化工中,高真空连续精馏技术是一项非常重要的技术,它在分离、提纯化工产品方面有着不可替代的作用。
本文将介绍高真空连续精馏技术在精细化工中的应用、优势和发展趋势。
精细化工是指在各种化工产品中,以化工、生物工程、环境工程等高新技术为基础,通过精细加工技术得到的具有高附加值的产品。
在精细化工的生产中,往往需要对原料进行精确的分离和提纯,而高真空连续精馏技术正是满足这一需求的关键技术之一。
具体来说,高真空连续精馏技术在精细化工中的应用主要包括以下几个方面:1. 提纯化工产品:在精细化工生产中,常常需要对原料进行提纯,以满足产品质量的要求。
高真空连续精馏技术可以对原料进行高效、精确的分离,从而得到更纯净的产品。
2. 节约能源:高真空连续精馏技术相对于传统的精馏技术来说,具有更高的能源利用效率,可以减少能源的消耗,降低生产成本。
3. 提高产品质量:通过高真空连续精馏技术,可以有效地去除原料中的杂质和有害物质,提高产品的质量和纯度。
4. 降低操作成本:高真空连续精馏技术可以实现自动化连续生产,减少人工操作,降低生产成本。
由于高真空连续精馏技术具有高效、节能、提质等优势,因此在精细化工中得到了广泛的应用。
二、高真空连续精馏技术的优势与传统的精馏技术相比,高真空连续精馏技术具有以下几个显著的优势:1. 高效:高真空连续精馏技术采用了先进的分馏设备和工艺流程,可以实现高效、快速的分离和提纯,提高生产效率。
4. 灵活性:高真空连续精馏技术可以根据不同的产品特性和生产需求进行灵活的调整和优化,具有较强的适应性和通用性。
高真空连续精馏技术具有高效、自动化、节能环保、灵活性和高品质等多重优势,使其成为精细化工中不可或缺的重要技术之一。
随着科技的不断进步和市场需求的变化,高真空连续精馏技术也在不断发展和完善,其主要的发展趋势包括以下几个方面:2. 自动化:随着智能制造技术的发展,高真空连续精馏技术将会更加智能化、自动化,实现智能监控、远程操作等功能。
机械行业的先进生产技术资料
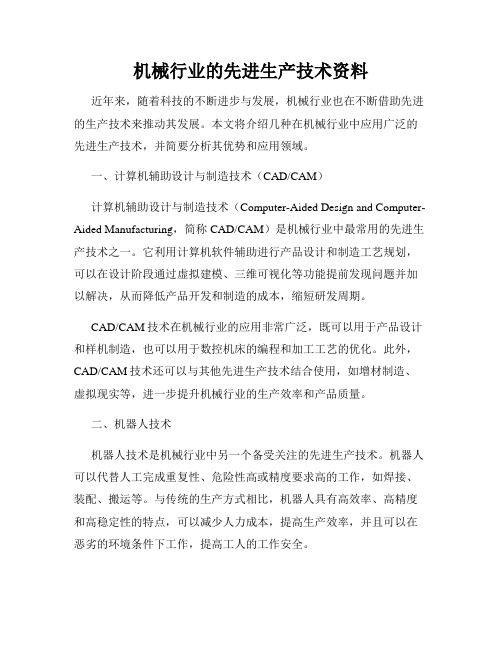
机械行业的先进生产技术资料近年来,随着科技的不断进步与发展,机械行业也在不断借助先进的生产技术来推动其发展。
本文将介绍几种在机械行业中应用广泛的先进生产技术,并简要分析其优势和应用领域。
一、计算机辅助设计与制造技术(CAD/CAM)计算机辅助设计与制造技术(Computer-Aided Design and Computer-Aided Manufacturing,简称CAD/CAM)是机械行业中最常用的先进生产技术之一。
它利用计算机软件辅助进行产品设计和制造工艺规划,可以在设计阶段通过虚拟建模、三维可视化等功能提前发现问题并加以解决,从而降低产品开发和制造的成本,缩短研发周期。
CAD/CAM技术在机械行业的应用非常广泛,既可以用于产品设计和样机制造,也可以用于数控机床的编程和加工工艺的优化。
此外,CAD/CAM技术还可以与其他先进生产技术结合使用,如增材制造、虚拟现实等,进一步提升机械行业的生产效率和产品质量。
二、机器人技术机器人技术是机械行业中另一个备受关注的先进生产技术。
机器人可以代替人工完成重复性、危险性高或精度要求高的工作,如焊接、装配、搬运等。
与传统的生产方式相比,机器人具有高效率、高精度和高稳定性的特点,可以减少人力成本,提高生产效率,并且可以在恶劣的环境条件下工作,提高工人的工作安全。
目前,机器人已经广泛应用于汽车制造、电子产品组装、物流等领域。
而随着人工智能和传感器技术的发展,机器人的智能化水平也在不断提高,将进一步拓展其在机械行业中的应用范围。
三、3D打印技术3D打印技术是一种快速制造技术,可以根据数字模型直接实现物理模型的制造。
与传统的加工方式相比,3D打印技术具有高度灵活性和多样性,可以制造出形状复杂、结构紧凑的零件,且无需额外的工装和模具。
在机械行业中,3D打印技术被广泛应用于快速原型制造、小批量生产和定制化生产。
它可以大大降低产品开发的成本和时间,加快新产品的上市速度,并且可以根据客户需求进行个性化定制,提高产品的附加值和市场竞争力。
提高生产效率的方法

提高生产效率的方法随着市场竞争的日益激烈,企业都在寻求提高生产效率的方法。
高效的生产能够降低成本、提升产品质量,并为企业带来更大的竞争优势。
本文将探讨几种提高生产效率的方法,以帮助企业实现更好的发展。
一、工作流程优化工作流程的优化是提高生产效率的关键。
通过减少不必要的环节和流程,排除生产中的瓶颈,可以加快生产过程并减少浪费。
为此,企业可以采取以下措施:1. 重新设计工作流程:评估当前的工作流程,找出存在的问题和瓶颈,并重新设计更为高效的流程。
例如,将一些独立的工序进行整合,降低生产过程中的等待和转运时间。
2. 自动化生产:采用先进的生产设备和自动化技术,可以大大提高生产效率。
自动化不仅可以减少人工操作的错误,还可以实现连续生产和更高的产量。
3. 使用物流管理系统:物流管理系统可以帮助企业更好地控制原材料和产品的流动,优化供应链,并提高生产效率。
通过实时跟踪和自动化管理,可以减少库存积压和运输时间。
二、员工培训和激励员工是企业最重要的资产,他们的技能水平和积极性直接影响生产效率。
因此,为员工提供培训和激励是提高生产效率的关键。
1. 培训员工:通过培训,提升员工的技能水平和工作效率。
可以组织内部培训或聘请外部专家进行培训,以确保员工具备所需的知识和技能。
2. 激励机制:建立激励机制,激发员工的积极性和创造力。
可以设立奖励制度,表彰优秀员工,并提供晋升和薪酬等方面的激励。
3. 团队合作:培养良好的团队合作精神,促进员工之间的合作和沟通。
通过设立团队目标和奖励团队绩效,可以提高团队的协作效率。
三、质量管理和持续改进提高产品质量和持续改进是提高生产效率的重要手段。
只有通过不断的质量管理和改进,才能提高生产效率和客户满意度。
1. 强化质量管理:建立严格的质量管理体系,确保产品符合标准和客户需求。
通过设立质量指标和检测标准,及时发现和纠正质量问题。
2. 持续改进:采用持续改进的理念,鼓励员工提出改进建议,并实施改进措施。
几种先进技术介绍教案.

2、CIMS的概念
• “CIMS”是一种基于CIM理念构成的数字化、信息化、 智能化、绿色化、集成优化的制造系统;它是信息时代 的一种新型生产制造模式。 • 一般包括以下两个基本要点: • ( 1 )企业生产经营的各个环节,如市场分析预测、产 品设计、加工制造、经营管理、 产品销售等一切的生 产经营活动,是一个不可分割的整体。 • ( 2 )企业整个生产经营过程从本质上看,是一个数据 的采集、传递、加工处理的过程,而形成的最终产 品 也可看成是数据的物质表现形式。因此对CIMS通俗的解 释可以是“用计算机通过信息集成实现现代化的生产制 造,以求得企业的总体效益。”整个 CIMS 的 研究开发, 即系统的目标、结构、组成、约束、优化和实现等方面, 体现了系统的总体性和系统的一致性。
• 6)自保护性、自维护性好。如设有切削力过载 保护、功率过载保护、行程与工作区域限制等。 导轨和各相对运动件等无须润滑或能自动加注润 滑,有故障诊断和预警功能。 7)对环境的适应性与保护性好。对工作环境的 温度、湿度、噪声、粉尘等要求不高,各种密封 件性能可靠、无渗漏,冷却液不外溅,能及时排 除烟雾、异味,噪声、振动小,能保护良好的生 产环境。 8)其他。如技术资料齐全,机床上的各种显示、 标记等清楚,机床外形、颜色美观且与系统协调。
简要叙述
1计算机辅助设计(CAD):利用计算机进行的一切设 计 ,包括有限元分析、计算机仿真、计算机辅助 绘图、几何建模等。其中AutoCAD是应用最成熟 的领域,而几何建模技术是CAD系统的核心技术。 2计算机辅助工程(CAE):利用计算机技术进行工程 设计中的各种精确分析、计算、设计等。 3计算机辅助工艺过程设计(CAPP):利用计算机辅 助编制工艺规程 4并行工程(CE):就是集成地、并行地设计产品及 其部件和相关各种过程的一种系统工作模式 5计算机辅助制造(CAM) 指利用计算机直接进行加 工制造、生产过程控制的技术系统
连续电镀生产线

连续电镀生产线随着现代工业的不断发展,电镀技术也得到了越来越广泛的应用。
为了满足市场需求,提高生产效率和质量,连续电镀生产线应运而生。
下面我们来详细介绍连续电镀生产线的相关知识。
一、连续电镀生产线的概述连续电镀生产线是一种全自动化的电镀设备,主要应用于零件表面的电镀加工。
这种生产线主要由前处理、电镀、后处理、自动输送系统等部分组成,能够实现全自动化的操作,提高生产效率和电镀质量。
二、连续电镀生产线的工作原理连续电镀生产线的工作原理主要分为以下几个步骤:1、前处理:包括清洗、脱脂、酸洗等工序,主要是为了去除物件表面的油污、锈蚀、氧化物等,以便于后续的电镀处理。
2、电镀:电镀工序是整个生产线的核心,主要是通过电解的方式在物品表面形成一层金属膜,起到保护和美化的作用。
常用的电镀方法有电解镀镍、电解镀铬、电解镀铜等。
3、后处理:经过电镀处理的物件需要进行后处理,包括洗涤、烘干、抛光等工序,以便于提高电镀质量。
4、自动输送系统:完成上述工作后,将制品输送到下一道工序,实现全自动化操作。
三、连续电镀生产线的优点连续电镀生产线具有以下几个优点:1、自动化程度高:整个生产线采用全自动化操作,减少了人工操作,提高了生产效率和工作效率。
2、生产能力强:连续电镀生产线能够连续进行电镀处理,不停机生产,提高了生产能力和生产效率。
3、稳定性好:生产线采用高精度的设备和控制系统,能够实现精准的电镀控制和稳定的工作状态。
4、电镀质量高:生产线配备了先进的检测设备和仪器,能够对电镀质量进行准确的检测和控制。
四、连续电镀生产线的应用领域连续电镀生产线主要应用于以下几个领域:1、汽车零部件:汽车零部件需要具有优异的耐腐蚀性和美观性,在这方面,连续电镀生产线能够发挥重要的作用。
2、电子零部件:连续电镀生产线对于电子零部件表面的镀铜、镀镍等工艺要求高,能够实现高质量的电镀加工。
3、家庭电器:家用电器有时需要进行电镀处理,以提高美观度和耐腐蚀性,这方面,连续电镀生产线也能够发挥作用。
先进生产方式

• JIT认为,浪费有七种形式:
(1) 过量生产造成的浪费 (2) 等待时间造成的浪费 (3) 搬运造成的浪费 (4) 工艺流程造成的浪费 (5) 库存造成的浪费 (6) 动作造成的浪费 (7) 产品缺陷造成的浪费
华中科技大学管理学院
产品成本增加
第四层次的浪费:多余的仓库、 多余的搬运工、多余的搬运设备、 多余的库存管理、…… 第三层次的浪费:过剩库存的浪费 第二层次的浪费(最大的浪费) 制造过剩的浪费 第一层次的浪费(过剩的生产能力的存在) 过多的人员、过剩的设备、过剩的库存 多余的劳务费 多余的折旧费 多余的利息支出
作为缓冲的库存
华中科技大学管理学院
通过降低库存暴露问题,然后解决问题,再降低库 存、暴露问题、解决问题……..使生产系统不断趋 于完善。
华中科技大学管理学院
3)它是一种综合的管理技术 ) 因为它涉及:产品设计、生产计划的编制、机 器改造、设备重新布置、工序的同期化、设备 的预防性维修、生产组织、劳动组织、人员再 培训等。
华中科技大学管理学院
下图为常见的用看板组织生产的过程: 下图为常见的用看板组织生产的过程:
2#
3#
移动看板 移动看板的移动
生产看板 生产看板的移动 容器的移动
华中科技大学管理学院
• 看板管理的主要规则: 看板管理的主要规则:
– 无论是生产看板还是移动看板,使用时必须附在 装有零件的容器上。 – 必须由需方凭移动看板到供方提取零件,或者, 由需方向供方发信号,供方凭移动看板传送零件。 – 要使用标准容器。 – 凭生产看板生产零件,容器装满时,一定要挂生 产看板。 – 次品不交给下道工序。
华中科技大学管理学院
2)减少调整准备时间(作业转换时间) )减少调整准备时间(作业转换时间)
精选先进制造工艺与装备

3.快速原型制造特点
1.结合CAD/CAM 技术、激光技术、计算机数控技术、精密伺服驱动技术以及新材料技术,真正意义上的数字化制造。2. 可将任意复杂形状的设计方案快速转换为三维的实体模型或样件3.CAD直接驱动,快速、准确、以及制造复杂模型。4.不需要任何刀具,模具及工装卡具的情况下,直接制造,方便快捷。5. 原材料的种类繁多;提高了新产品开发的一次成功率,缩短了开发周期,降低了研发成本。
与机械制造中的切削(其成形特征为连续、局部、去除成形)、锻造(其成特征为断续、整体、塑性成形)方法比较,轧制方法成形特征是连续、局部、塑性成形。零件轧制较之锻造也有其不足之处,即模具复杂、尺寸大、设备通用性差、工艺调整难度大等。因此,轧制技术适合于批量大的零件生产和专业化工厂的生产。
2. 零件轧制成形的优缺点
4.快速原型应用领域
1.工业造型、模具、家电、电子仪表、轻工、塑料、玩具、航空航天、军工、机械、汽车、摩托车、内燃机、建筑规划及模型、科研、医疗等。 2. 应用体现: a)支持快速产品开发 b)支持快速模具制造 c)支持医用实体制造
3.2先进切削技术与机床
(2)汽车覆盖件的冲压成形特点
1)一次拉伸成形2)拉胀复合成形3)局部成形4)变形路径变化
(3)汽车覆盖件设计的生产流程
制件设计-工艺分析-计算机模拟-模具设计-制造-调试-返修。计算机模拟1)使用软件:美国的DynaForm;日本的AutoForm2)特点:a)缩短模具制造时间 b)节省费用 c)提高零件的质量和使用性能 d)降低零件的废品率 f)减少原材料浪费
2.快速原型制造工艺
1.光固化成型工艺 (SLA—Stereo lithography Apparatus)2.分层实体制造工艺 (LOM—Laminated Object Manufacturing) 3.选择性激光烧结工艺 (SLS—Selected Laser Sintering) 4.熔融沉积造型工艺 (FDM—Fused Deposition Modeling)5.三维打印工艺(2DP—Three-dimensional printing)
露天矿生产技术
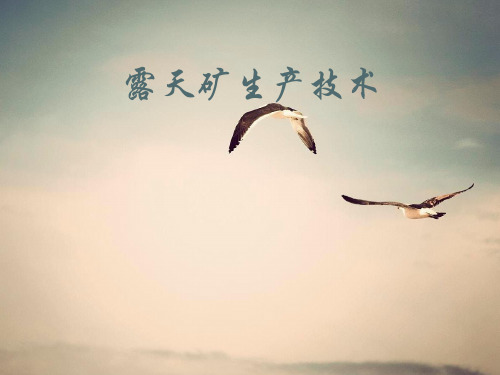
包括岩性、结构面和构造应力等。 ② 水文地质因素
水对边坡的稳定影响主要是降低岩石的抗剪强度、产生浮托力和 水平推力,降低边坡的稳定性。
③ 采矿技术因素 采矿技术因素主要包括边坡几何要素、爆破震动影响、边坡形状。
④ 影响排土场滑坡的因素 影响因素以排弃岩石的性质、排土场基底工程地质条件影响较大。
工艺系统布置在1290平盘,现排土机布置于北排土场1475平盘进行外 排。
工作面布置:
1290平 盘
破碎机
转载机
胶带
开采工艺
② 开采参数
台阶高度 /m
最小工作 平盘宽度
/m
15
105
台阶坡面 角/°
采掘带宽 度/m
穿爆参数
排土参数
硬岩:6*6 上排台阶高度:15m
65
40
软岩:8*8 下排台阶高度:30m
东露天矿北帮与工业场地各有一座110kV变电站,南北端帮各有一趟35kV线路,呈环 形布置。
安全职业健康及卫生
露天矿安全卫生危害主要包括有毒有害物品的危害与危害性作业 的危害。
1)有毒有害物品的危害 ① 烟尘;② 扬尘;③ 生产性噪声。 2)危害性作业的危害 ① 滑坡灾害;② 运输危害;③ 电气线路危害。
谢谢大家的聆听!
安全措施:佩戴口罩、安全帽与防砸鞋等保护设备,同时所有工 作人员在工作中都应该严格遵守安全规章。
生产技术与成本
中国煤炭工业协会不久前公布的煤炭经济运行形势报告显示,2014年前11 个月,煤炭企业利润同比下降44.4%,亏损企业亏损额同比增长61.6%,企业亏 损面达到70%。××集团2014年吨煤利润不购买一瓶矿泉水,2015年及今后一 段时期,煤炭价格回升仍属奢望。
几种先进的采矿技术及其应用
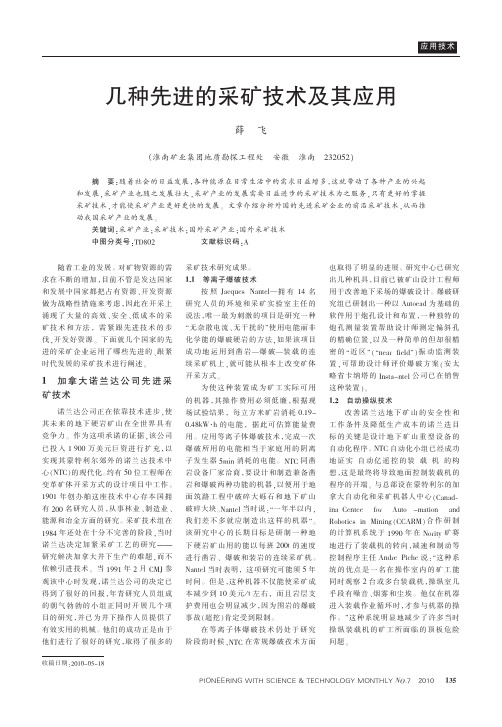
随着工业的发展。
对矿物资源的需求在不断的增加,目前不管是发达国家和发展中国家都把占有资源、开发资源做为战略性措施来考虑,因此在开采上涌现了大量的高效、安全、低成本的采矿技术和方法,需紧跟先进技术的步伐,开发好资源。
下面就几个国家的先进的采矿企业运用了哪些先进的、跟紧时代发展的采矿技术进行阐述。
1加拿大诺兰达公司先进采矿技术诺兰达公司正在依靠技术进步,使其未来的地下硬岩矿山在全世界具有竞争力。
作为这项承诺的证据,该公司已投入1900万美元巨资进行扩充,以实现其蒙特利尔郊外的诺兰达技术中心(NTC)的现代化。
约有50位工程师在变革矿体开采方式的设计项目中工作。
1901年创办舶这座技术中心存本国拥有200名研究人员,从事林业、制造业、能源和冶金方面的研究。
采矿技术组在1984年还处在十分不完善的阶段,当时诺兰达决定加紧采矿工艺的研究———研究解决加拿大井下生产的难题,而不依赖引进技术。
当1991年2月CMJ参观该中心时发现,诺兰达公司的决定已得到了很好的回报,年青研究人员组成的朝气勃勃的小组正同时开展几个项目的研究,并已为井下操作人员提供了有效实用的机械。
他们的成功正是由于他们进行了很好的研究,取得了很多的采矿技术研究成果。
1.1等离子爆破技术按照Jacques Nantel—拥有14名研究人员的环境和采矿实验室主任的说法,唯一最为刺激的项目是研究一种“无杂散电流、无干扰的”使用电能丽非化学能的爆破硬岩的方法,如果该项目成功地运用到凿岩—爆破—装载的连续采矿机上,就可能从根本上改变矿体开采方式。
为使这种装置成为矿工实际可用的机器,其操作费用必须低廉,根据现场试验结果,每立方米矿岩消耗0.19-0.48k W·h的电能,据此可估算能量费用。
应用等离子体爆破技术,完成一次爆破所用的电能相当于家庭用的阴离子发生器5min消耗的电能。
NTC同凿岩设备厂家洽商,要设计和制造兼备凿岩和爆破两种功能的机器,以便用于地面筑路工程中破碎大砾石和地下矿山破碎大块。
山东省化工行业安全生产先进适用技术装备推广目录(第一批)

低,碳排放量有所降低,固废和废水大幅降低。
替代技术应优先采用流化床工艺”。
1.高效性,微通道内径极小,通常在几微米到几百微米之间,反应物的扩
散和混合非常迅速,化学反应速率很高,有时可达常规反应器的数倍甚至
数十倍;
1.通过大幅度降低危险物质的在线量、连续化生产,实现本质安
2.精确性,流速和温度可以精确控制,便于精确控制反应物的投料比、反 全;
萃取机
3.液体停留时间短,液体存留量小;
4.易于实现多级逆流操作,适于深度提取,节省溶剂。
1.实现了机械化换人,降低劳动强度,减少操作人员数量,减少 溶剂使用量,可实现连续化生产,降低了安全风险; 2.体积小、投资少、成本低、效率高,操作简单,可有效提升企 业效益; 3.可实现人机一体化设计,具备设备故障自我诊断功能。
山东省化工行业安全生产先进适用技术装备推广目录(第一批)
序号
技术工艺装 备名称
主要技术特点
推广应用理由
1.内部链盘结构,结构简单,故障率低,可适用于工业化生产中的固体物
1
密闭式 输送投 统
管链 料系
料输送流程; 2.自动化程度高,无人值守,可实现远程监控和故障诊断; 3.密闭式设计可以有效防止物料与空气接触,减少污染和交叉污染的可能 性,同时避免了危险化学品原料在生产过程中泄漏;
应温度、压力等参数,从而得到更加稳定的目标产物;
2.提高产物的收率,降低单耗、能耗等;
3
微 通 道 反 应 3.安全性,微通道反应器具有较小的容积:减少了化学反应物的使用量和 3.2022年应急管理部《危险化学品生产建设项目安全风险防控指
器
储存量;
南》中要求“新建涉及危险化工工艺的精细化工生产建设项目,
第18章其它先进生产方式

其它先进生产方式除了MRPII和JIT以外,还有其它先进的组织生产的方式。
本章将介绍最优生产技术、敏捷制造和计算机集成制造等3种先进生产方式的基本思想和有关的概念。
第一节最优生产技术最优生产技术(Optimized Production Technology,OPT),是以色列物理学家Eli Goldratt 博士于本世纪七十年代提出的。
最初它被称作最优生产时间表 (Optimized Production Timetable),80年代才改称为最优生产技术。
后来Goldratt 又进一步将它发展成为约束理论(Theory of Constraints)。
OPT产生的时间不长,却取得了令人瞩目的成就,是继MRP和JIT(Just-in-Time)之后出现的又一项组织生产的新方式。
最优生产技术,作为一种新的生产方式,它吸收了MRP和JIT的长处。
其独特之处不仅在于提供了一种新的管理思想,而且在于它的软件系统。
OPT的两大支柱是OPT原理及OPT软件。
一、 OPT的目标OPT的倡导者认为,任何制造企业的真正目标只有一个,即在现在和将来都能赚钱。
要衡量一个企业是否能赚钱,通常采用以下三个指标:(1)净利润(Net Profit,NP) 即一个企业赚多少钱的绝对量。
净利润越高的企业,其效益越好。
(2)投资收益率(Return on Investment,ROI) 表示一定时期的收益与投资的比。
当两个企业投资大小不同时,单靠净利润是无法比较他们效益的好坏的。
(3)现金流量(Cash Flow,CF) 表示短期内收入和支出的钱。
没有一定的现金流量,企业也就无法生存下去。
但是,以上三个指标不能直接用于指导生产,因为它们太一般。
例如,究竟采用多大批量为好,是无法直接从这三个指标作出判断的。
因此,需要一些作业指标作桥梁。
如果这些作业指标好,以上三个指标就好,则说明企业赚钱。
按照OPT的观点,在生产系统中,作业指标也有三个:(1)产销率(Throughput,T) 按OPT的规定, 它不是一般的通过率或产出率,而是单位时间内生产出来并销售出去的量,即通过销售活动获取金钱的速率。
连续冲压工艺(3篇)
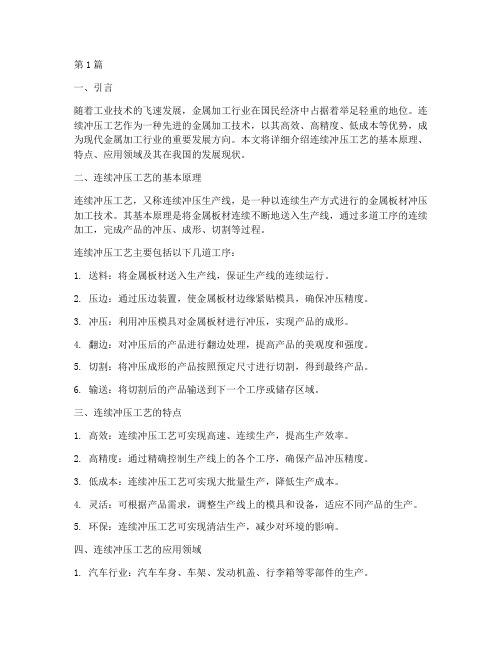
第1篇一、引言随着工业技术的飞速发展,金属加工行业在国民经济中占据着举足轻重的地位。
连续冲压工艺作为一种先进的金属加工技术,以其高效、高精度、低成本等优势,成为现代金属加工行业的重要发展方向。
本文将详细介绍连续冲压工艺的基本原理、特点、应用领域及其在我国的发展现状。
二、连续冲压工艺的基本原理连续冲压工艺,又称连续冲压生产线,是一种以连续生产方式进行的金属板材冲压加工技术。
其基本原理是将金属板材连续不断地送入生产线,通过多道工序的连续加工,完成产品的冲压、成形、切割等过程。
连续冲压工艺主要包括以下几道工序:1. 送料:将金属板材送入生产线,保证生产线的连续运行。
2. 压边:通过压边装置,使金属板材边缘紧贴模具,确保冲压精度。
3. 冲压:利用冲压模具对金属板材进行冲压,实现产品的成形。
4. 翻边:对冲压后的产品进行翻边处理,提高产品的美观度和强度。
5. 切割:将冲压成形的产品按照预定尺寸进行切割,得到最终产品。
6. 输送:将切割后的产品输送到下一个工序或储存区域。
三、连续冲压工艺的特点1. 高效:连续冲压工艺可实现高速、连续生产,提高生产效率。
2. 高精度:通过精确控制生产线上的各个工序,确保产品冲压精度。
3. 低成本:连续冲压工艺可实现大批量生产,降低生产成本。
4. 灵活:可根据产品需求,调整生产线上的模具和设备,适应不同产品的生产。
5. 环保:连续冲压工艺可实现清洁生产,减少对环境的影响。
四、连续冲压工艺的应用领域1. 汽车行业:汽车车身、车架、发动机盖、行李箱等零部件的生产。
2. 家电行业:冰箱、洗衣机、空调等家电产品的外壳、门板等。
3. 金属制品行业:金属管材、金属板件、金属容器等产品的生产。
4. 建筑行业:金属门窗、金属屋面等建筑材料的制作。
5. 航空航天行业:飞机、火箭等航空航天产品的零部件加工。
五、我国连续冲压工艺的发展现状近年来,我国连续冲压工艺得到了迅速发展,主要体现在以下几个方面:1. 产业链完善:我国已形成了较为完整的连续冲压产业链,涵盖了原材料供应、设备制造、模具设计、生产线建设等环节。
先进制造技术

激光加工技术及其应用进展综述闫朝宁(兰州理工大学机电工程学院152085201021)【摘要】激光加工技术是集光学、机械学、电子学、计算机学等为一体的高技术,是激光应用最有发展前途的领域。
目前已开发出20多种激光加工技术,如雨后春笋般地应用于各个新工艺领域,如激光切割、激光打标、激光打孔、激光焊接、激光表面热处理、激光快速成型、激光清洗、激光冗余修正、激光退火、激光光刻与存储等。
激光加工技术的出现是对传统的加工工艺和加工方法具有重大影响的技术变革,很快被广泛应用于汽车、电子电器、航空、冶金、机械制造等国民经济重要行业,推动了工业的快速发展,并产生了巨大经济效益。
【关键词】激光打孔;激光切割;激光焊接;激光表面改性由于激光具有方向性好、高能量和单色性好等一系列优点,自年代初间世以来,就受到科研领域的高度重视。
激光技术推动了诸多领域的迅猛发展,应用范围越来越广,在加工领域中的应用成果尤为显著。
我国激光加工市场前景广阔,预计平均以每年20%-30%速率递增,但在激光加工系统的可靠性、稳定性以及整体化、智能化、自动化水平与国外差距较大’,这是制约我国激光加工技术进一步发展的关键所在,国家正在积极采取措施,加速我国激光加工产业化的进程和发展。
一、激光孔加工技术激光打孔技术具有精度高、通用性强、效率高、成本低和综合技术经济效益显著等优点,已成为现代制造领域的关键技术之一。
目前,工业发达国家已将激光深微孔技术大规模地应用到飞机制造业、食品加工业、医药制造业等行业。
进入90年代,激光打孔朝着多样化、高速度、孔径更微小的方向发展。
(一)激光打孔技术介绍激光打孔技术具有精度高、通用性强、效率高、成本低和综合技术经济效益显著等优点,已成为现代制造领域的关键技术之一。
在激光出现之前,只能用硬度较大的物质在硬度较小的物质上打孔。
这样要在硬度最大的金刚石上打孔,就成了极其困难的事。
激光出现后,这一类的操作既快又安全。
但是,激光钻出的孔是圆锥形的,而不是机械钻孔的圆柱形,这在有些地方是很不方便的。
聚对苯二甲酸乙二酯的制备及其应用研究进展
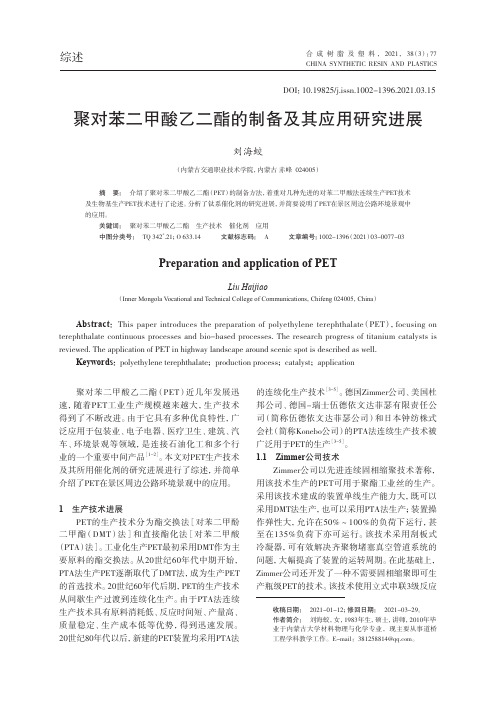
综述CHINA SYNTHETIC RESIN AND PLASTICS合 成 树 脂 及 塑 料 , 2021, 38(3): 77聚对苯二甲酸乙二酯(PET)近几年发展迅速,随着PET工业生产规模越来越大,生产技术得到了不断改进。
由于它具有多种优良特性,广泛应用于包装业、电子电器、医疗卫生、建筑、汽车、环境景观等领域,是连接石油化工和多个行业的一个重要中间产品[1-2]。
本文对PET生产技术及其所用催化剂的研究进展进行了综述,并简单介绍了PET在景区周边公路环境景观中的应用。
1 生产技术进展PET的生产技术分为酯交换法[对苯二甲酚二甲酯(DMT)法]和直接酯化法[对苯二甲酸(PTA)法]。
工业化生产PET最初采用DMT作为主要原料的酯交换法。
从20世纪60年代中期开始,PTA法生产PET逐渐取代了DMT法,成为生产PET 的首选技术。
20世纪60年代后期,PET的生产技术从间歇生产过渡到连续化生产。
由于PTA法连续生产技术具有原料消耗低、反应时间短、产量高、质量稳定、生产成本低等优势,得到迅速发展。
20世纪80年代以后,新建的PET装置均采用PTA法的连续化生产技术[3-5]。
德国Zimmer公司、美国杜邦公司、德国-瑞士伍德依文达菲瑟有限责任公司(简称伍德依文达菲瑟公司)和日本钟纺株式会社(简称Konebo公司)的PTA法连续生产技术被广泛用于PET的生产[3-5]。
1.1 Zimmer公司技术Zimmer公司以先进连续固相缩聚技术著称,用该技术生产的PET可用于聚酯工业丝的生产。
采用该技术建成的装置单线生产能力大,既可以采用DMT法生产,也可以采用PTA法生产;装置操作弹性大,允许在50%~100%的负荷下运行,甚至在135%负荷下亦可运行。
该技术采用刮板式冷凝器,可有效解决齐聚物堵塞真空管道系统的问题,大幅提高了装置的运转周期。
在此基础上,Zimmer公司还开发了一种不需要固相缩聚即可生产瓶级PET的技术。
提高煤矿生产效率的技术措施

提高煤矿生产效率的技术措施煤矿生产效率的提高是煤矿行业发展的关键问题之一。
随着社会对能源需求的不断增长,提高煤矿生产效率具有重要的意义。
本文将从技术措施的角度,探讨几种提高煤矿生产效率的方法。
一、自动化设备的应用随着科技的进步,自动化设备的应用在煤矿生产中扮演着越来越重要的角色。
自动化设备可以有效降低劳动强度,提高工作效率,减少人为错误带来的风险。
例如,自动化采掘设备可以自主进行煤矿掘进作业,减少对人力的依赖,提高生产效率。
另外,自动化设备还可以在生产过程中进行数据采集、监测和控制,提供实时的运行状态信息,方便管理人员进行生产调度和决策。
二、信息化管理系统的建立信息化管理系统可以全面、准确地掌握煤矿生产过程中的各项数据,实时监测生产状态,提高生产效率。
通过信息化管理系统,管理人员可以远程监控煤矿设备的运行情况,及时发现和解决存在的问题,提高设备利用率。
另外,信息化管理系统还可以对生产数据进行分析和挖掘,帮助管理人员找出生产过程中的瓶颈和问题,并提出改进措施,进一步提高生产效率。
三、提高煤矿开采效率煤矿生产效率的提高离不开对煤矿开采过程的优化。
其中,提高采煤效率是关键。
一方面,可以通过改进采煤工艺,选用高效的采煤设备,提高采煤效率。
例如,采用先进的连续采煤机,可以实现连续掘进、回采作业,提高煤矿开采效率。
另一方面,可以通过合理调整煤矿的生产布局,在保证安全的前提下,提高开采的效益。
例如,合理选择回采顺序、进行合理的煤柱设计等,都可以提高煤矿开采效率。
四、绿色环保技术的应用提高煤矿生产效率不仅需要关注经济效益,还需要注重环境保护。
因此,应用绿色环保技术是提高煤矿生产效率的重要途径之一。
煤矿企业可以通过减少煤矿废弃物的排放,提高矿山的回收利用率,减少环境污染。
例如,采用煤矸石回填法填埋废石,既可以减少占地面积,又可以提高煤矸石的回收利用率;采用煤矸石粉煤灰配制建筑材料,可以减少矿山废弃物的排放。
五、加强人员培训和管理人员的素质和管理水平对煤矿生产效率的提高起着决定性的作用。
先进工艺技术阶段

先进工艺技术阶段在当今工业发展迅速的时代,先进工艺技术层出不穷,不断推动着生产力的发展和工业繁荣。
先进工艺技术已成为推动经济增长、提高产品质量和降低生产成本的重要力量。
下面将介绍一些目前属于先进工艺技术阶段的几个方面。
首先,先进的生产自动化技术是目前工业领域的重要突破。
相对于传统的人工操作,自动化生产线可大大提高生产效率和产品质量。
通过引入机器人、传感器和自动控制系统,实现生产线上的无人操作,不仅能够减少人为因素导致的错误和不稳定性,还能够实现24小时连续生产,大大提高了生产能力和效率。
其次,3D打印技术是当今先进工艺技术中的一颗新星。
3D打印技术是一种将CAD模型直接打印成为三维实体的技术,它所实现的产品制造方式与传统加工方式相比,具有更高的灵活性和精确度。
通过3D打印技术,可以将产品的设计、制造和组装等工序统一到一个系统中,不仅能够减少传统制造所带来的中间环节,还能够大大缩短产品的开发周期和成本。
再次,先进的物联网技术也是目前工业生产中的一个重要突破。
物联网技术通过传感器、通信网络和数据处理系统的组合,实现物与物之间、人与物之间的互联互通。
在工业生产中,物联网技术可以实现设备之间的数据共享和交流,通过对设备运行状态的监测和预测,及时发现潜在问题并采取措施进行处理。
物联网技术还可以实现生产过程的全程可追溯,提高企业的生产效率和质量管理水平。
最后,先进的虚拟现实技术也是目前工业领域的一个热门发展方向。
虚拟现实技术通过引入计算机生成的环境和仿真模型,实现人机交互和沉浸式体验。
在工业生产中,虚拟现实技术可以用于产品设计、生产过程模拟和培训等领域。
通过虚拟现实技术,可以减少实际试验和模型制造所带来的成本和时间,同时还能够提高产品的设计精度和生产效率。
综上所述,先进工艺技术正不断推动着工业的发展和工业生产水平的提高。
生产自动化技术、3D打印技术、物联网技术和虚拟现实技术等,都是当前先进工艺技术阶段的重要代表。
- 1、下载文档前请自行甄别文档内容的完整性,平台不提供额外的编辑、内容补充、找答案等附加服务。
- 2、"仅部分预览"的文档,不可在线预览部分如存在完整性等问题,可反馈申请退款(可完整预览的文档不适用该条件!)。
- 3、如文档侵犯您的权益,请联系客服反馈,我们会尽快为您处理(人工客服工作时间:9:00-18:30)。
几种先进的连续生产技术
目前全世界钢铁企业的竞争白热化,西方技术领先的企业为保持其市场“食物链”顶层地位,依靠多领域扎实的基础科学功底和多年生产实践不间断的进行技术更新,提出新的生产方式,推出新的高端产品。
近几年“连续生产“的概念正在悄然兴起,它已经在管材、板材、棒材产品领域得到应用并逐步推广,由于其显著的优越性和巨大经济效益,值得我们密切关注其发展趋势。
第一,无头连续轧制技术
无头轧制是将1根无限长的轧件(坯料),经一次咬入后,连续在轧机中轧制,直到轧辊(孔型)磨损,不能再轧为止。
与传统轧制工艺相比,无头轧制没有轧件之间的时间间隔,增加了单位生产时间内的有效轧制时间,提高了作业效率;不存在咬入抛出轧件产生的冲击载荷,减少了轧件对轧机的冲击,降低了工艺设备事故和备品备件的消耗。
由于其工艺过程稳定,没有轧件头尾失张造成的尺寸偏差,提高了轧件尺寸精度;对于板材,也可以使轧件保持恒定张力,稳定生产传统热轧工艺几乎不可能生产的超薄规格钢板,根据日本的报道,采用无头轧制技术的优势包括:(1)将热轧常规的最小板厚1.2mm进一步减少至0.8mm,厚度精度不超过±(20~30)μm,且可轧制如1.2mm×1600mm的宽幅薄材(2)极薄热轧带钢尺寸的精度优于传统热轧带钢,组织性能均匀性和稳定性也明显优于传统产品;(3)采用分散控制的高响应张力控制技术可在0.5秒左右的时间内稳定地实现轧制中板厚变更。
对于棒材,定尺率得到提高,线材可以实现定重交货等等。
前苏联重型制造业中央科学研究院早在20世纪40年代末,在世界上率先着手对棒线材无头轧制技术进行研究,并于50年代研制出世界上第一套用于构造无头长坯的核心设备——移动式闪光对焊机,以实现在线预热钢坯的焊接。
20世纪90
年代,日本NKK公司和意大利达涅利公司也相继研制出了以移动式闪光焊机为核心设备用于棒线材生产的无头轧制产品。
NKK公司称之为棒材无头轧制系统(即EBRS—Endless Bar Rolling System),而达涅利公司则将该系统称为无头焊接轧制系统(即EWR-Endless Welding Rolling)。
1996年3月,世界上第一套采用感应对焊技术的工业化带钢无头轧制生产线在日本川崎制钢公司千叶厂3#热连轧机上正式投入运行。
1997年Posco(浦项)和Hitachi(日立)有限公司联合着手开始研制采用剪切、焊接工艺,进行中间坯连接的带钢无头轧制新工艺。
1998年4月,日本新日铁(Nippon)钢铁公司大分厂(Oita)研制成功了利用高能激光器对中间板坯实现对焊的钢板无头轧制生产线。
2000年,达涅利公司还成功地研制出了世界上第一套以连铸连轧技术为核心的棒线材无头轧制系统(即ECR—Endless Casting Rolling),用于意大利乌迪内ABS公司的50万吨/年特殊钢棒线材工业生产。
2006~2007年浦项(Posco)和日立(Hitachi)有限公司采用剪切、焊接工艺进行中间坯连接的带钢无头轧制新工艺投入工业化生产,这种基于摆剪概念的新型固态连接工艺,实现了无头轧制连接技术的创新。
2009年7、8月份意大利钢铁企业Acciaieria ArvediS.P.A与西门子公司联手打造的世界第一套ESP(Endless Strip Production)无头铸轧带钢生产线在Arvedi开始调试。
我国第一个引入国外无头轧制设备的是唐钢,后续包括新疆八一钢厂、涟钢、邢台钢铁等,唐钢和八一钢铁采用EWR焊接型无头轧制技术,邢钢采用Ebros焊接无头轧制技术。
图1 JFE 千叶工厂3#无头尾轧制生产工艺流程图
第二,连续油管技术
连续油管(Coiled Tubing ,CT)是由若干段长度在百米以上的柔性管通过对焊(直缝焊)或斜焊(螺旋焊)工艺焊接而成的无接头连续管,长度一般达几百米至几千米,连续油管的材质包括碳素钢、稀有金属,例如钛合金。
连续油管及其操纵设备称为盘管作业机或连续油管作业机(Coiled Tubing Unit,CTU)。
近几年, 连续油管在国外得到了快速发展,在性能、规格、长度等方面都有很大提高,新型连续油管作业机性能的改进使得连续油的应用更为广泛。
连续油管在国内的应用处在初级阶段具有很大的发展空间。
目前世界上几大主要连续油管与连续油管作业机的制造厂商均集中在美国。
三大连续油管制造公司是精密油管技术公司(Precision Tube Technology)、优质油管公司(Quality Tubing Inc)和西南管材公司(Southwesten Pipe Inc);世界上较大的连续油管作业供应商主要有:哈里伯顿公司、斯伦贝谢、威德福、BJ公司、Hydra Rig公司、Otis、CVDD公司、Bowen工具公司、Stewart Stevenson公司、加拿大DRECO能源公司。
这些公司占据了全球大部分连续油管作业市场。
在专业钢管生产领域Tenaris集团已经开发出海上和陆地用连续油管,钢级包括从HS-70到
HS-110,外径尺寸:1英寸-5英寸,壁厚范围:0.08英寸-0.3英寸。
2010年4月,美国石油协会正式出版第一版连续油管制造标准API spec 5ST 它是目前唯一公开发行的连续油管产品制造标准。
在术语中首次明确连续油管的定义为:由长度大于61m的钢管制成的管子,排除由无缝管对焊成所谓的连续油管。
同时对制造工艺、检验、涂层、文件控制等15个方面做了详细的规定。
我国的连续油管产品制造起步虽晚但进步较快。
2008年8月,宝鸡石油钢管有限责任公司采购应达工业(上海)公司的连续油管高频固态焊机、中频焊缝加热设备、全管体中频加热设备建成亚洲首条连续油管生产线。
设计年生产能力1.5万吨,产品管径25.4毫米至88.9毫米,壁厚1.91毫米至6.35毫米。
2009年,宝鸡钢管厂、武钢、钢铁研究总院联合开展连续油管系列产品研发攻关,成功实现了CT70、CT80和CT90钢级的开发,并且武钢获得独家供货权。
目前宝鸡的连续油管已经在辽河油田顺利下井,并出口到俄罗斯和中东地区。