95万吨每年催化裂化柴油加氢精制计算书
100万吨-年重油催化裂化的初步设计
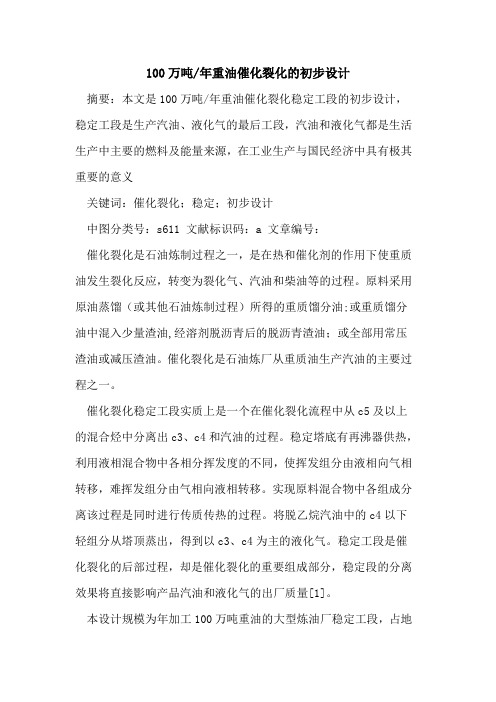
100万吨/年重油催化裂化的初步设计摘要:本文是100万吨/年重油催化裂化稳定工段的初步设计,稳定工段是生产汽油、液化气的最后工段,汽油和液化气都是生活生产中主要的燃料及能量来源,在工业生产与国民经济中具有极其重要的意义关键词:催化裂化;稳定;初步设计中图分类号:s611 文献标识码:a 文章编号:催化裂化是石油炼制过程之一,是在热和催化剂的作用下使重质油发生裂化反应,转变为裂化气、汽油和柴油等的过程。
原料采用原油蒸馏(或其他石油炼制过程)所得的重质馏分油;或重质馏分油中混入少量渣油,经溶剂脱沥青后的脱沥青渣油;或全部用常压渣油或减压渣油。
催化裂化是石油炼厂从重质油生产汽油的主要过程之一。
催化裂化稳定工段实质上是一个在催化裂化流程中从c5及以上的混合烃中分离出c3、c4和汽油的过程。
稳定塔底有再沸器供热,利用液相混合物中各相分挥发度的不同,使挥发组分由液相向气相转移,难挥发组分由气相向液相转移。
实现原料混合物中各组成分离该过程是同时进行传质传热的过程。
将脱乙烷汽油中的c4以下轻组分从塔顶蒸出,得到以c3、c4为主的液化气。
稳定工段是催化裂化的后部过程,却是催化裂化的重要组成部分,稳定段的分离效果将直接影响产品汽油和液化气的出厂质量[1]。
本设计规模为年加工100万吨重油的大型炼油厂稳定工段,占地面积约1000㎡,厂房为l型,分四个车间,吸收车间、解吸及再吸收车间和稳定车间,还有辅助设施,有控制室、配电室及生活区间。
在主要生产车间里有4个精馏塔、2个中间罐。
1.1原料规格100万吨/年重油催化裂化稳定工段的初步设计产品规格见如下表1-1[2]。
表1-1 原料规格1.2产品特点(1)汽油无色至淡黄色的易流动液体。
危险特性:极易燃烧。
其蒸气与空气可形成爆炸性混合物。
遇明火、高热极易燃烧爆炸。
与氧化剂能发生强烈反应。
其蒸气比空气重,能在较低处扩散到相当远的地方,遇明火会引着回燃。
(2)液化气危险特性:极易燃,与空气混合能形成爆炸性混合物。
120万吨柴油加氢精制装置操作规程讲义

120万吨/年柴油加氢精制装置操作规程第一章装置概况第一节装置简介一、装置概况:装置由中国石化集团公司北京设计院设计,以重油催化裂化装置所产的催化裂化柴油、顶循油,常减压装置生产的直馏柴油和焦化装置所产的焦化汽油、焦化柴油为原料,经过加氢精制反应,使产品满足新的质量标准要求。
新《轻柴油》质量标准要求柴油硫含量控制在0.2%以内,部分大城市车用柴油硫含量要求小于0.03%。
这将使我厂的柴油出厂面临严重困难,本装置可对催化柴油、直馏柴油、焦化汽柴油进行加氢精制,精制后的柴油硫含量降到0.03%以下,满足即将颁布的新《轻柴油》质量标准,缩小与国外柴油质量上的差距,增强市场竞争力。
2;装置建即22351m×/年延迟焦化装置共同占地面积为217m103m该项目与50万吨设在140万吨/年重油催化裂化装置东侧,与50万吨/年延迟焦化装置建在同一个界区内,共用一套公用工程系统和一个操作室。
本装置由反应(包括新氢压缩机、循环氢压缩机部分)、分馏两部分组成。
4t/a。
×10 装置设计规模:120二、设计特点:1、根据二次加工汽、柴油的烯烃含量较高,安定性差,胶质沉渣含量多的特点,本设计选用了三台十五组自动反冲洗过滤器,除去由上游装置带来的悬浮在原料油中的颗粒。
2、为防止原料油与空气接触氧化生成聚合物,减少原料油在换热器、加热炉炉管和反应器中结焦,原料缓冲罐采用氮气或燃料气保护。
3、反应器为热壁结构,内设两个催化剂床层,床层间设冷氢盘。
4、采用国内成熟的炉前混氢工艺,原料油与氢气在换热器前混合,可提高换热器的换热效果,减少进料加热炉炉管结焦,同时可避免流体分配不均,具有流速快、停留时间短的特点。
5、为防止铵盐析出堵塞管路与设备,在反应产物空冷器和反应产物/原料油换热器的上游均设有注水点。
6、分馏部分采用蒸汽直接汽提,脱除HS、NH,并切割出付产品石脑油。
32 1 120万吨/年柴油加氢精制装置操作规程7、反应进料加热炉采用双室水平管箱式炉,炉底共设有32台附墙式扁平焰气体燃烧器,工艺介质经对流室进入辐射室加热至工艺所需温度,并设有一套烟气余热回收系统,加热炉总体热效率可达90%。
化学氢耗的计算
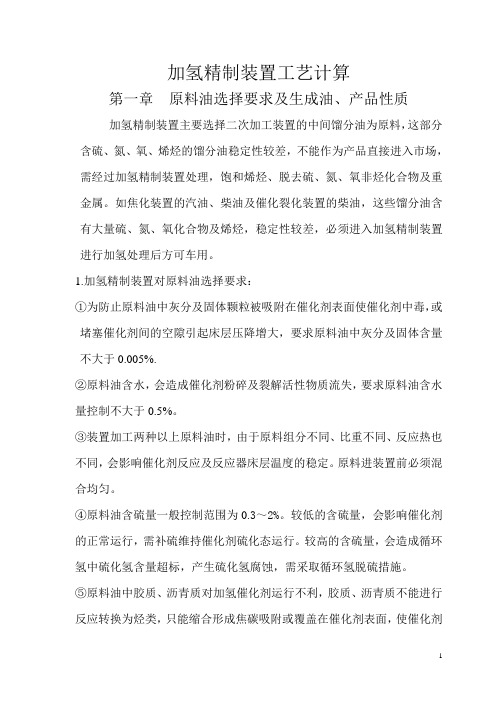
加氢精制装置工艺计算第一章原料油选择要求及生成油、产品性质加氢精制装置主要选择二次加工装置的中间馏分油为原料,这部分含硫、氮、氧、烯烃的馏分油稳定性较差,不能作为产品直接进入市场,需经过加氢精制装置处理,饱和烯烃、脱去硫、氮、氧非烃化合物及重金属。
如焦化装置的汽油、柴油及催化裂化装置的柴油,这些馏分油含有大量硫、氮、氧化合物及烯烃,稳定性较差,必须进入加氢精制装置进行加氢处理后方可车用。
1.加氢精制装置对原料油选择要求:①为防止原料油中灰分及固体颗粒被吸附在催化剂表面使催化剂中毒,或堵塞催化剂间的空隙引起床层压降增大,要求原料油中灰分及固体含量不大于0.005%.②原料油含水,会造成催化剂粉碎及裂解活性物质流失,要求原料油含水量控制不大于0.5%。
③装置加工两种以上原料油时,由于原料组分不同、比重不同、反应热也不同,会影响催化剂反应及反应器床层温度的稳定。
原料进装置前必须混合均匀。
④原料油含硫量一般控制范围为0.3~2%。
较低的含硫量,会影响催化剂的正常运行,需补硫维持催化剂硫化态运行。
较高的含硫量,会造成循环氢中硫化氢含量超标,产生硫化氢腐蚀,需采取循环氢脱硫措施。
⑤原料油中胶质、沥青质对加氢催化剂运行不利,胶质、沥青质不能进行反应转换为烃类,只能缩合形成焦碳吸附或覆盖在催化剂表面,使催化剂失活,导至加氢装置不能正常运行。
目前加氢精制原料一般选择焦化汽油、焦化柴油、催化柴油为原料。
也有的参炼其它二次油来补充加氢装置原料。
原料油性质2 加氢精制生成油、产品性质原料油经加氢精制,发生了性质变化,非烃化合物转化为烃类和硫化氢、氨盐及水。
不稳定的烯烃转化为烷烃。
加氢反应过程体积减小,液体收率增加。
加氢精制过程,汽油辛烷值降低,柴油十六烷提高,密度降低。
加氢精制过程也进行加氢裂解反应,伴有裂解气体产生。
加氢生成油、产品性质第二章装置加工能力的确定及物料平衡计算㈠加氢精制装置处理量、循环氢量的计算处理量:40万吨/年;年开工小时:8000h原料油密度:0.8663 1装置小时进料量计算:①质量进料量(G) =400000.000Kg/8000h=50000Kg/h②体积进料量(V)=50000Kg/h ÷ 0.8663=58m3/h2.装置各种氢气量的计算:ρ①新氢量的计算:设计耗氢:1.26%(w)新氢量= 50000Kg/h×1.26% ÷ 2 × 22.4 ÷ 95%= 7427NM3/h②循环氢量的计算:设计氢油比为550:1;氢纯度:95%;新氢补入量:7500Nm3/h 循环氢量= 550/0.95× 58= 33579Nm3/h③循环氢机排量的计算:循环氢机排量=33579Nm3/h - 7500Nm3/h=26078 Nm3/h㈡装置几种氢气组成及有关计算1 .工业氢组成及流量、平均分子量及气体重度计算= 669.64 ÷ 7500 × 22.4M平= 2ρ = 669.64 ÷ 7500= 0.0892. 高压分离器分离氢组成、流量、平均分子量及气体重度计算= 3958 ÷ 26078 × 22.4M平= 3.4ρ = 3958 ÷ 26078= 0.153.混氢组成、流量、平均分子量及气体重度计算平= 3.09ρ = 4627.9 ÷ 33578= 0.144. 反应器床层急冷氢量的计算①急冷氢量计算:(由表量计算)Q急= 新氢量+循氢机排量-混氢量②急冷氢量计算:(由油气热焓值计算)第三章加氢精制装置新氢耗量计算一氢气来源:①加氢精制装置氢气可来源于重整装置,但是重整氢纯度较低,一般在85%,影响加氢氢纯度。
加氢裂化装置能耗分析

冷高分+单塔汽提, 公用工程
12.91
8.0
300
中石油广 西钦州
240
热高分+双塔汽提 +循环氢脱硫, 公 用工程
11.43
7.5
350
1
加氢精制装置设计能耗分析
各炼油厂加氢精制装置原料主要性质
国内加氢裂化装置原料性质对比表 混合原 料硫含 量 ppm
24200
国内新建或在建 加氢裂化装置
组成(万吨 组成(万吨/a) 焦化汽油 焦化柴 油
中石油大连石化
混合去石脑油加氢再加工分离液化气 、轻重石脑油。
去催化裂化
装置原料性质、 装置原料性质、产品分布及质量 对装置工艺技术条件及用能分析 由以上原料与产品分布及规格上的差异定性分析,导致 装置工艺设计技术参数上的不同,主要技术参数对比如下:
装置名称 氢耗 循环氢油比 反应器入口压 力 循环氢脱硫 t胺液 原料 胺液/t原料 胺液 油 反应器总液 时空速h-1 时空速
项目 压力能回收 回收低温热 回收低温热 回收低温热 能耗增加Kg标油/t原料 ( 泉州石化-大连石化) -0.66 1.63 12.32 2.22 备注 回收了高能级能量 用来加热热水或除盐水外送 发1.0MPa蒸汽 发0.4 MPa蒸汽
总结
• 从收集到的国内加氢裂化装置资料来看, 装置原料性质、目的产品及收率是影响装 置能耗的主要因素,以中馏分油及尾油为 产品方案的装置,其设计压力、氢耗明显 低于我司以重石脑油、柴油为目的产品的 加氢裂化装置,进而影响到油品、补充氢 升压电耗增加。
中化泉州石化
3.08
738/1348/843 R101HT/R101HC /R102HC 1500
17.093/16.607 R101HC/R102HC 15.50
最新万吨年催化裂化反应—再生系统计算
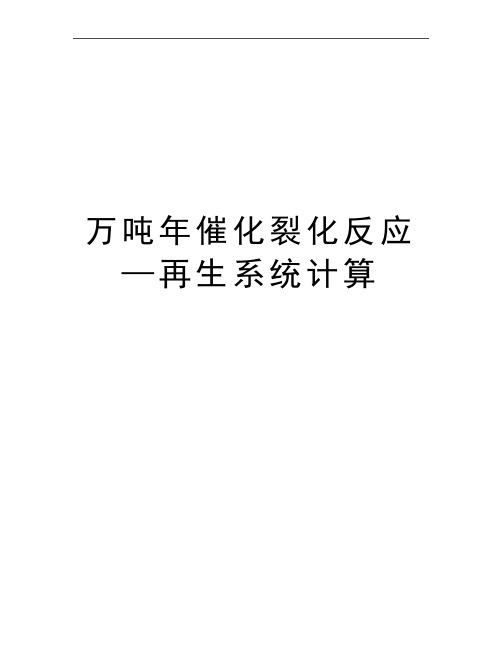
万吨年催化裂化反应—再生系统计算摘要催化裂化装置主要由反应—再生系统、分馏系统、吸收稳定系统和能量回收系统构成,其中反应—再生系统是其重要组成部分,是装置的核心。
设计中以大庆原油的混合蜡油与减压渣油作为原料,采用汽油方案,对装置处理量为250万吨/年(年开工8000小时)的催化裂化反应—再生系统进行了一系列计算。
根据所用原料掺油量低,混合后残炭值较低,其硫含量和金属含量都较小且由产品分布和回炼比较小,抗金属污染能力强,催化剂的烧焦和流化性能较好及在此催化剂作用下,汽油辛烷值较高这些特点,故采用汽油方案。
设计中,采用了高低并列式且带有外循环管的烧焦罐技术,并对烧焦罐式再生器和提升管反应器进行了工艺计算,其中再生器的烧焦量达32500㎏/h,烧焦罐温度为680℃,稀相管温度为720℃,由于烟气中CO含量为0,则采用高效完全再生。
在烧焦罐中,烧焦时间为1.8s,罐中平均密度为100㎏/m3,烧焦效果良好。
在提升管反应器设计中,反应温度为505℃,直径为1.62 m,管长为29 m,反应时间为3s,沉降器直径为2 m,催化剂在两器中循环,以减少催化剂的损失,提高气—固的分离效果,在反应器和再生器中分别装有旋风分离器,旋风分离器的料腿上装有翼阀,在提升管和稀相管出口处采用T型快分器。
由设计计算部分可知,所需产品产率基本可以实现。
关键词:催化裂化,反应器,再生器,提升管,烧焦罐,完全再生AbstractThe catalytic cracker constitutes reaction-regeneration system、fraction system、 absorption-stabilization system and power-recovery system. The most important and core part of the unit is reaction-regeneration system. The DaQing Crude wax oil and vacuumdistillation residue are taken as feedstock. This paper is a series of processing calculation mainly about reaction-regeneration system. With gasoline scheme, capacity is designed to be 150 Mt/a under the condition of 8000 hours’ operating time.After being mixed the contents of blending residuum, sulphur and metal as well as the carbon residue in feedstock are low. As the even distribution of product, superior properties of resisting metal pollution and the catalyst’s coke burning and fluidization as well as the higher octane number of gasoline with the function of this catalyst, the gasoline scheme are taken.In the design, technology of coke-burning drum with outsider-circulation tube is applied. The drum is of high-low parallel style. The processing calculation is about reproducer of coke-burning drum style and riser, coke-burning capacity is 32500㎏/h, the temperatures of coke-burning drum and dilute phase riser are respectively 680℃and 720℃. Accounting that there is no carbon monoxide in off-gase. The high efficient regeneration is applied. In the coke-burning drum, the scorching time is 1.8s and its average density is 100 ㎏/m3, thus the effect of coke-burning is good. The temperature of riser is 505℃. Its diameter is 1.62m and the length is 29m. While its reaction time is 3s and the diameter of settling vessel is 2m. Catalysts circulate in the drum and reactor. In order to reduce the loss of catalyst and improve the effect of gas-solid separation, cyclones are equipped in both reactor and reproducer. There is trickle vavle on the dipleg of the latter, whilethe T-rapid separation unit is fitted in the exit of riser and dilute phase riser. From the date, the unit can substantially reach the required yield. Keywords: Catalystic cracking, Reactor, Reproducer, Riser, Coke-burning drum毕业设计(论文)原创性声明和使用授权说明原创性声明本人郑重承诺:所呈交的毕业设计(论文),是我个人在指导教师的指导下进行的研究工作及取得的成果。
70万吨年催化裂化装置改造项目风险评估.资料
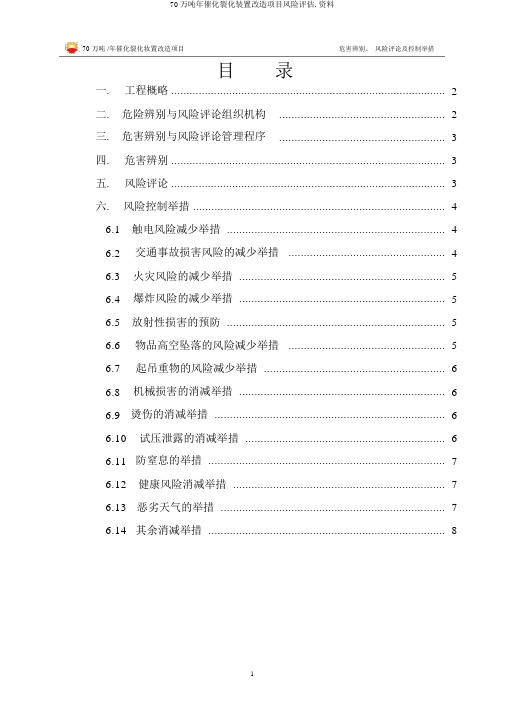
70 万吨 /年催化裂化妆置改造项目危害辨别、风险评论及控制举措目录一. 工程概略 (2)二. 危险辨别与风险评论组织机构 (2)三. 危害辨别与风险评论管理程序 (3)四. 危害辨别 (3)五. 风险评论 (3)六. 风险控制举措 (4)6.1 触电风险减少举措 (4)6.2 交通事故损害风险的减少举措 (4)6.3 火灾风险的减少举措 (5)6.4 爆炸风险的减少举措 (5)6.5 放射性损害的预防 (5)6.6 物品高空坠落的风险减少举措 (5)6.7 起吊重物的风险减少举措 (6)6.8 机械损害的消减举措 (6)6.9 烫伤的消减举措 (6)6.10 试压泄露的消减举措 (6)6.11 防窒息的举措 (7)6.12 健康风险消减举措 (7)6.13 恶劣天气的举措 (7)6.14 其余消减举措 (8)一 . 工程概略中国石油吉林石化分企业汽柴油质量升级和Ⅱ常减压装置改造工程70 万吨 /年催化裂化妆置改造项目是吉林石化千万吨炼油项目的要点工程之一,建设规模为140×104t/a。
工程地址位于吉林石化企业炼油厂厂区东侧南部,西侧为柴油加氢精制装置,东侧为新建循环水场,南侧为新建加氢中间罐区泵房,北侧为结合控制室,总用地约19096 ㎡。
本装置由反响 -重生系统、主风机组部分、分馏部分、气压机部分、汲取稳固部分、产汽部分和余热锅炉部分构成。
我单位肩负土建、钢构造、设施、工艺管线、电气、仪表专业的所有施工任务。
工程计划动工日期为2009 年 6 月 15 日,计划中交日期为2010 年 8 月 20 日。
二.危险辨别与风险评论组织机构依照企业程序言件《危害辨别微风险评论管理程序》,装置动工前,项目部成立了危害辨别微风险评论领导小组,组织机构以下:危害辨别微风险评论领导小组组长弓宝荣项目专职HSE 监察郭军海领导小组副组长张红军成员葛伟张俊奇生技供经财综产术应营务合办办办劳办办公公公资公公室室室办室室公邵李张室詹张高青洪晓华民山超伟霞各施工队 HSE 专业管理负责人施工班组HSE 管理负责人三 . 危害辨别与风险评论管理程序危害辨别微风险评论管理程序以下页图一所示:确立危害和影响成立鉴别准则确立相应的法例要求评论危害和影响记录重要危害和影响成立详尽目标和表现准则确立和评论风险控制举措实行选定的风险控制举措图一:危害辨别微风险评论管理程序图四 . 危害辨别工程动工前,项目部危害辨别微风险评论领导小组对施工过程中的各道工序、作业场所、人员的健康安全和环境保护方面进行了危害辨别,危害辨别主要内容有(不限于):动力机具、脚手架、吊车、载人吊篮、砂轮机、射钉枪、火焰切割、电焊、气瓶、发掘、噪音、照明、火灾、射线探伤、压力试验、高处作业、有限空间、物体坠落与安全网、荒弃物、灰尘等,详细清单见-1。
催化裂化柴油的精制

催化裂化柴油的精制重油催化裂化柴油是二次加工产品.由于其中含有大量的烯烃.芳烃和硫,氮,氧化合物.使得催化柴油特别是重油催化柴油的胶质含量比较高这些组分都是氧化.缩合反应的活I生组分从而造成催化裂化柴油的安定『生差其直观表现为颜色很快变深和生成沉淀.为了改善催化裂化柴油的安定性,必须对其进行精制.催化柴油的精制主要分为加氢精制和非加氢精制(化学精制)——加氢精制的优点是精制油收率高,安定性好.无三废排放,非烃化合物脱除率高,但一次性投资大,精制费用高.操作难度大等缺点限制了其应用;化学精制的优点是设备简单,一次性投资少,精制费用低,容易操作等.特别适合中小型炼厂泰州石油化工总厂自行研制了一种柴油化学除胶剂.可有效脱除柴油中的不安定组分.工艺简单,投资少,成本低.是目前非加氢■精制的有效手段.I取自泰州石化总厂催化裂化装置脱胶前馏出口化学除胶剂为自制.以液碱为主要成分.添加聚丙烯酰胺,叔丁醇等化学物质.在催化柴油中加入一定量的除胶剂后.搅拌.沉降.除去黑色胶质.水洗.脱水.2.结果与讨论GB252—2000标准规定柴油的色度不大于35号,氧化总不溶物不大于2.5rag/100mL.分析我厂催化裂化柴油.氧化总不溶物有时大于2.5mg/100mL,避光储存3个月后氧化总不溶物和色度均不合格.因此试验主要是考察氧化总不溶物含量和色度.21除胶剂加入量对精制效果的影响取催化柴油分析当天色度为20号氧化总不溶物为642rag/1OOmL.按一定比例加入除胶剂进行精制.结果显示使用量分别为1‰,3%0.5‰.7‰时,当天色度均为20号.氧化总不溶物分别为1.78rag/1OOmL.1.81rag/1OOmL. 178rag/1OOmL.179mg/1OOmL避光储存3个月后色度分别为30号.25号. 25号,25号氧化总不溶物分别为236rag/1OOmL212rag/1OOmL208rag/1OOmL.21Omg/1OOmL.可以看出,除胶剂能够稳定催化柴油的色度,降低氧化总不溶物.根据试验结果选取加入量为3%0.22精制温度对精制效果的影响取催化柴油+分析当天色度为15号.氧化总不溶物为52mg/1OOmL.分别在室温40.C,50.C,60.C,80.C精制.精制当天色度分别为15号.20号20号25号,25号.氧化总不溶物分别为1.17mg/1OOmL,128mg/1OOmL132mg/1OOmL1.52mg/1OOmL.136mg/ 1OOmL3个月后色度分别为25号.30 号.3.5号,5.0号.70号,氧化总不溶物分别为151mg/1OOmL183mg/1OOmL,192mg/1O0mL.179mg/1OOmL,163mg/1OOmL.根据试验结果.精制温度对催化柴油氧化总不溶物的影响不大.但对色度影响较大综合试验和装置的实际情况,选择精制温度为40.C. 23搅拌时间对精制效果的影响取催化柴油,分析当天色度为15号.氧化总不溶物为52mg/1OOmL.分别考察搅拌时间为05mIn.1rain,2mIn. 4mIn,10mIn时的精制效果,色度均为20号,氧化总不溶物分别为1.32g/1OOmL,129mg/100mL.1.31mg/1OOmL128mg/1OOmL.128mg/1OOmL.可见搅拌时间对精制影响不大.选择搅拌时间为1m-n,可以兼顾到生产的需要.24沉蜂时间对精制效果的影Ⅱ向取催化柴油分析当天色度为15号,氧化总不溶物为52mg/1OOmL分别考察沉降时间为05m[n.1mIn,2mIn, 3m-n.10mln时的精制效果,色度均为2 0号氧化总不溶物分别为179mg/1OOmL165mg/1OOmL.1.48mg/1OOmL.152mg/1OOmL.14gmg/1OOmL.可以看出,随着沉降时间的延长胶质脱除更彻底由于除胶剂本身在柴油中沉降速度较快.总体上对精制效果影响不大.考虑到生产需要.选择沉降1rain为宜.25除姣荆的使用范重分别选取装置平稳运行和装置不正常时的柴油样.用3‰除胶剂进行试验. 结果表明.使用除胶剂处理柴油.对柴油的质量有一定的要求.过差的柴油不能达到很好的精制效果.26精成本测算除胶剂价格以2800元/吨计.添加量为3‰,则催柴精制原料成本为84 元/吨3.结论1自制除胶剂能脱除柴油胶质.改善色度降低氧化总不溶物含量.延长储存时间.2自制除胶剂使用工艺条件为加剂量3%0,40.C搅拌1rain沉降1rain后除胶水洗.3自制除胶剂对催化柴油的质量有一定的要求,不能精制质量较差的柴油. r篓荤囊叶百,'。
万吨每年催化裂化柴油加氢精制计算书

一、全装置物料平衡1、物料平衡本设计的处理量为95万吨/年,反应阶段为其末期,每年开工时数按8000小时计算。
入方:①原料油=8000%10010109534⨯⨯⨯=118750公斤/小时=248000%10010954⨯⨯⨯=2850吨/天 ②重整氢=8000%70.210109534⨯⨯⨯=3206公斤/小时=248000%70.210954⨯⨯⨯=77吨/天 出方:①精制柴油=118750×96.95%=115128公斤/小时=2850×96.95%=2763吨/天②粗汽油=118750×1.52%=1805公斤/小时=2850×1.52%=43吨/天③高分排放气=118750×1.78%=2114公斤/小时=2850×1.78%=51吨/天④低分排放气=118750×0.31%=368公斤/小时=2850×0.31%=8.8吨/天⑤回流罐排放气=118750×2.084%=2475公斤/小时=2850×2.084%=59吨/天⑥溶于水中的硫化氢=118750×0.022%=26公斤/小时=2850×0.022%=0.6吨/天⑦溶于水中的氨气=118750×0.024%=28.5公斤/小时=2850×0.024%=0.7吨/天⑧设备漏损=118750×0.01%=12公斤/小时=2850×0.01%=0.3吨/天 2、化学耗氢量计算①计算杂质脱除率a)硫脱除率=18001801800-×100%=90%b)氮脱除率=26158261-×100%=77.8%c)硫醇硫脱除率=15115-×100%=93.3%d)氧脱除率(以酸度计算) 原料油含氧率=8642.01001656/108.53⨯⨯⨯-×100%=0.00192%精制油含氧率=8595.01001656/1014.03⨯⨯⨯-×100%=0.0000463%氧脱除率=00192.00000465.000192.0-×100%=97.58%e)烯烃饱和率(以溴价计算)烯烃饱和率=5.201.45.20-×100%=80%②化学耗氢量计算a) 每脱掉1%的硫消耗12.5Nm 3H 2/m 3原料油加氢脱硫耗氢量=8642.0100%901018005.126⨯⨯⨯⨯-=2.34Nm 3/T2.34×118750/22.4×10002=25kg/hr b) 每脱掉1%的氮消耗53.7Nm 3H 2/m 3原料油加氢脱氮耗氢量=8642.0100%8.77102617.536⨯⨯⨯⨯-=1.26Nm 3/T1.26×118750/22.4×10002=13kg/hr c) 每脱掉1%的氧消耗44.6Nm 3H 2/m 3原料油加氢脱氧耗氢量=8642.0100%6.971092.16.445⨯⨯⨯⨯-=0.0967Nm 3/T0.0967×118750/22.4×10002=1kg/hr d) 烯烃饱和耗氢量烯烃饱和耗氢量=(20.5-4.1)×10×22.4/160=22.96Nm 3/T22.96×118750/22.4×10002=243kg/hre) 饱和1%的芳烃消耗5.0Nm 3H 2/m 3原料油芳烃饱和耗氢量=8642.0568.05.411.43⨯⨯-)(=6.29Nm 3/T6.29×118750/22.4×10002=67kg/hrf) 每脱掉1%的硫醇硫消耗12.5Nm 3H 2/m 3原料油硫醇硫耗氢量=8642.0100%3.9310155.126⨯⨯⨯⨯-=0.02Nm 3/T0.0202×118750/22.4×10002=0.2kg/hr g) 加氢裂解耗氢量原料油裂解程度为3%,每裂解1分子原料,消耗3分子氢加氢裂解耗氢量=34.197%31000⨯×3×22.4=10Nm 3/T10.22×118750/22.4×10002=108kg/hr总化学耗氢量=2.34+1.26+0.0967+22.96+6.29+0.0202+10.22=43Nm 3/T =24.81+13.36+1.025+243.44+66.69+0.214+108.36=458kg/hr重量分数:加氢脱硫:899.45781.24×100%=5.42%加氢脱氮:899.45736.13×100%=2.92%加氢脱氧:899.457025.1×100%=0.22%烯烃饱和:899.45744.243×100%=53.16%芳烃饱和:899.45769.66×100%=14.56%硫醇脱硫:899.457214.0×100%=0.05%加氢裂解:899.45736.108×100%=23.66%3、化学反应放热量a).加氢脱硫反应放热量=600kcal/Nm 3×2.34Nm 3/T=1404kcal/T 1404kcal/T×118.75T/hr=166725kcal/hrb).加氢脱氮反应放热量=600kcal/Nm 3×1.26Nm 3/T=756kcal/T 756kcal/T×118.75T/hr=89775kcal/hrc).加氢脱氧反应放热量=600kcal/Nm 3×0.0967Nm 3/T=58.02kcal/T58.02kcal/T×118.75T/hr=6890kcal/hrd).加氢烯烃饱和反应放热量=1260kcal/Nm 3×22.96Nm 3/T=28929.6kcal/T28930kcal/T×118.75T/hr=3435438kcal/hre).加氢芳烃饱和反应放热量=540kcal/Nm 3×6.29Nm 3/T=3396.6kcal/T3397kcal/T×118.75T/hr=403394kcal/hrf).加氢裂解反应放热量=450kcal/Nm 3×10.22Nm 3/T=4599kcal/T4599kcal/T×118.75T/hr=546131kcal/hr总的反应放热量∑=1404+756+58.02+28930+3397+4599=39144kcal/T=166725+89775+6889.875+3435437.5+403393.75+546131.25=4648352.375kcal/hr重量分数:加氢脱硫:%59.3%100391441404=⨯加氢脱氮:%93.1%10039144756=⨯加氢脱氧:%15.0%1003914402.58=⨯烯烃饱和:%95.73%100391446.28929=⨯芳烃饱和:%68.8%100391446.3396=⨯加氢裂解:%76.11%100391444599=⨯4、纯氢平衡表入方:新氢=5.51095%7.27⨯⨯×2×87.68%/8000=1022kg/hr10002427.1022⨯=25T/d出方:化学耗氢量=458kg/hr 100024899.457⨯=10.99T/d排放耗氢量=5.675.2113×2×80.86%=525.9kg/hr1000249.525⨯=13T/d溶解耗氢(包括低分排放和回流罐排放):低分罐=11.18125.368×43.10%×2=18kg/hr回流罐=46.4475.2474×2.03%×2=2.kg/hr溶解耗氢总量∑=17.52+2.26=20kg/hr10002478.19⨯=0.47472T/d机械漏损:入方-出方=1022.27-(457.899+525.9+19.78)=18.691kg/hr100024691.18⨯=0.449T/d重量分数:化学耗氢:27.1022899.457×100%=44.79%排放耗氢:27.10229.525×100%=51.44%溶解耗氢:27.102278.19×100%=1.93%机械漏损:27.1022691.18×100%=1.83%5、硫化氢的物料平衡产生H 2S :3432%901018001187506⨯⨯⨯⨯-=204kg/hr 10002440.204⨯=5T/d排放H 2S :①高分排放:34%6.05.675.2113⨯⨯=66kg/hr ②低分排放:34%55.211.18125.368⨯⨯=18kg/hr③回流罐排放:34%85.446.4475.2474⨯⨯=92kg/hr④水中溶解:26kg/hr (在装置总物料平衡中已计算)⑤粗汽油中溶解:204.40-(66.34+17.62+91.79+26.125)=2.5kg/hr重量分数:高分排放:%10040.20466⨯=32.46%低分排放:10040.20418⨯%=8.62%回流罐排放:10040.20492⨯%=44.90%水中溶解:10040.20426⨯%=12.78%粗汽油中溶解:10040.2045.2⨯%=1.24%二、反应器的工艺设计入口温度为320℃,入口压力为4.0Mpa ,取塔径为3.4m ,出口压力为3.9Mpa ,选用固定床轴向冷壁式反应器,已知数据如下:表一在压力为4.0Mpa 时,温度与气化率和热焓的对应关系如下:加氢反应器入口注:物料包括原料油,新氢和循环氢表二在不同压力下,气化率与温度和热焓之间的对应关系如下:注:物料包括加氢生成油,反应生成气和循环氢图一3.90Mpa 下焓值与温度对应关系 图二3.90Mpa 下气化率与温度对应关系表三不同气化率下的油气平均分子量图三不同气化率的油气平均分子量1.催化剂装填体积(选空速=2.5h -1)空速=催化剂的体积时的体积油在C 20︒=催V 8000/2.86410957⨯=2.5催V ∴=54.96m 3假设D=3.4m ,则L=2V 4D π催⨯=24.314.396.544⨯⨯=5.06m 2.催化剂的当量直径(所选催化剂为mm 62.1⨯Φ)D p =6×F V =6×3323323106102.12)102.1(4/106)102.1(4/-----⨯⨯⨯⨯+⨯⨯⨯⨯⨯⨯⨯πππ=1.64×310-m 3.循环氢(选氢油比=300) 氢油比=油混合氢V V =2.864/8000/1095V 7⨯混合氢=300混合氢V ∴=41223.1Nm 3 混合氢w =混合氢V /22.4×M =18.64.221.41223⨯=11373.16kg/hr循环氢w =混合氢w -新氢w =11373.16-3206.25=8166.91kg/hr4.D E =0.335.反应器入口温度下物料的气化率和氢分压作4.0Mpa 下的H m ~t 、e w %~t 图,查得t=320℃时,e w =21%,H m =262.0Kcal/kg 由图可得:当e w =21%时,油气M =160.5g/mol入口2p H =总p ×油气纯氢纯氢m m m +=4.0×油气M e w⨯+⨯11875018.6/16.11373%08.83)18.6/(11373.16=3.06Mpa6.反应器出口温度及气化率根据热量衡算得:(原料油混合氢w w +)入口m H +Q×95%=(原料油混合氢w w +)出口m H(11373.16+118750)×262.0+39144×118750×310-×95%=(11373.16+118750)出口m H出口m H =295.94Kcal/kg作t ~H m 、e w %~H m 图,查得出口w e =36.0%,出口t =356℃ 7.出口氢分压反应生成气m =循环氢m +[1-(96.95%+1.52%)]×原料油m=1187500153.091.8166⨯+=9983.785kg/hr 由图可得:当e w =36.0%时,油气M =168g/mol出口2p H =总p ×油气原料油反应生成气反应生成气(M e w /%)52.1%95.96m 95.7/m %60.7795.7/m ⨯+⨯+⨯=3.9×168%0.369847.011875095.7/785.9983%60.77)95.7/(9983.785⨯⨯+⨯=2.52Mpa8..气体密度v ρt =(进口t +出口t )/2=(320+356)/2=338℃w e =(进w e +出w e )/2=(21%+36%)/2=28.5%气w =混合氢w +原料油w ×w e =11373.16+118750×28.5%=45216.91kg/hr 气V =[混合氢混合氢M w +油气原料油M e w w⨯]×22.4×869.995.31⨯×273273t +=[18.611373.16+25.164%5.28187501⨯]×22.4×869.995.31⨯×273273338+ =2631.72m 3/hr v ρ=气气V w =72.263191.45216=17.18kg/m 39.空塔线速u假设D=3.4m ,则S==(π/4)D 2=9.075m 2 u=S气V =3600075.972.2631⨯=0.081m/sec10.混合物粘度查分子量为164.25、温度为338℃下,石油馏分蒸汽粘度为i z =0.0082厘泊Tr=)()(K c K T T =40.182.33273338=+Pr=05.3297.195.3Pc P == 根据Tr 与Pr 氢的粘度图得2iH z =0.013厘泊[2]=193.052H 粘度:iy 总p p 2H =25.164%5.2811875018.616.11373%08.8318.616.11373⨯+⨯=0.747 混z =∑∑0.5iii0.5ii my z m y =5.05.05.05.005.193747.012747.00082.005.193747.01013.02747.0⨯-+⨯⨯⨯-+⨯⨯)()(=9.31×310-厘泊 11.求hv G =w e m m ⨯+原料油混合氢=11373.16+118750×28.5%=45216.91kg/hrL G =)(原料油w e 1m -=118750×(1-28.5%)=84906.25kg/hrL G /v G =84906.25/45216.91=1.878 v G =45216.91kg/hr=24.34/2048.091.45216⨯⨯π=1020.5磅/2尺·hr 根据v G 与L G /v G 关系图查得:h=0.18=1.133239.19.05])3.2/18.01(1064.1318.067.0[18.033.01000/1021.907.018.17103.6+⨯⨯⨯+⨯-⨯⨯⨯⨯⨯---)()( =0.1034Pa/m12.检验①=LpΔ0.1034Pa/m ,在0.023~0.115Pa/m 范围内 ②15.14.306.5D L >== ③=⨯=L Lp p ΔΔ0.1034×5.06=0.523 kg/cm 2<0.84kg/cm 完全符合要求。
催化裂化工艺计算总表
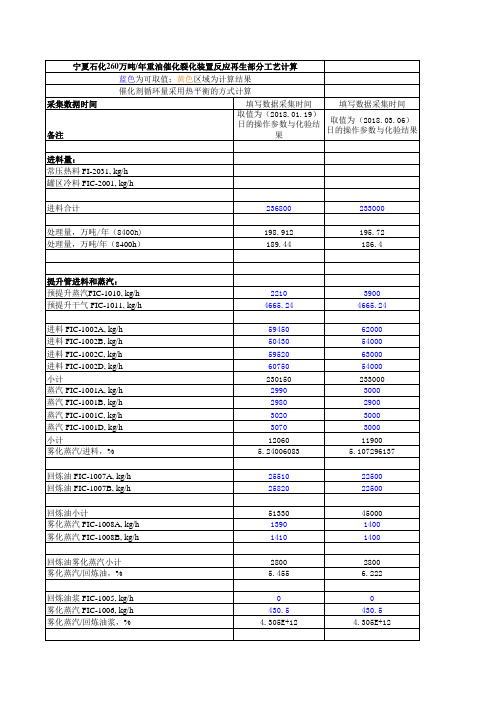
67.642 8455.224 1775.597 6679.627
79.02 8453.084 673.711 1004.226
95.520 6679.627 673.711 8084.530 336.855 1004.226 12050.717 1004.226
95.520 338.995 1355.982
19890.5 19890.5
6.930 6.93
1700 5000 2100 2700 3400
0 0 14900
34790.5
3216 192960
990 1358 550 168 150
0 3216 192960
21 0.008
0.9
0 0 0
39000
外取热器2产汽FI-1041,kg/h 小计,kg/h 给水温度TI-1063,TI-1055, oC
进料合计
236800
233000
处理量,万吨/年(8400h) 处理量,万吨/年(8400h)
198.912 189.44
195.72 186.4
提升管进料和蒸汽: 预提升蒸汽FIC-1010, kg/h 预提升干气 FIC-1011, kg/h
进料 FIC-1002A, kg/h 进料 FIC-1002B, kg/h 进料 FIC-1002C, kg/h 进料 FIC-1002D, kg/h 小计 蒸汽 FIC-1001A, kg/h 蒸汽 FIC-1001B, kg/h 蒸汽 FIC-1001C, kg/h 蒸汽 FIC-1001D, kg/h 小计 雾化蒸汽/进料,%
宁夏石化260万吨/年重油催化裂化装置反应再生部分工艺计算
蓝色为可取值;黄色区域为计算结果
重油催化裂化柴油吸附脱氮-加氢精制组合工艺的开发
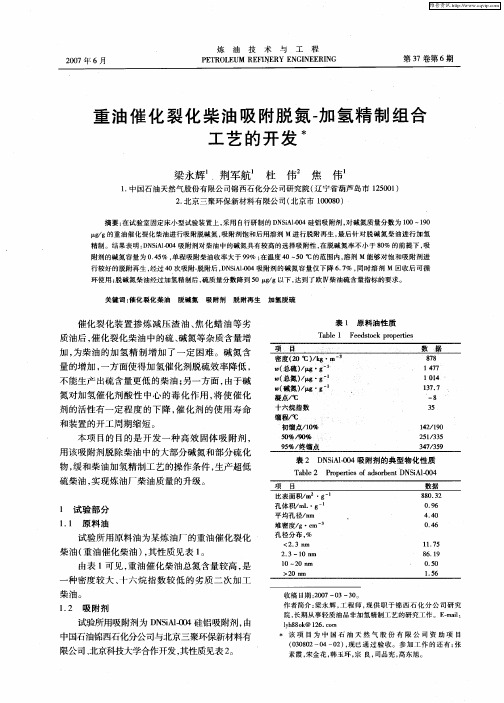
1 中国石油 天然气股份有 限公 司锦西石化分公 司研究 院( . 辽宁省葫芦岛市 150 ) 20 1 2 北京三 聚环保新材料有 限公 司( 京市 10 8 ) . 北 0 0 0
摘要 : 在试验室固定床小 型试验装置上 , 采用 自行研制 的 D SA - 4硅铝吸附剂, N i1 0 0 对碱 氮质量分数为 10~10 0 9
gg的重油催化裂化柴油进行吸附脱碱氮 , / 吸附剂饱和后用溶剂 M进行脱 附再生 , 最后针 对脱碱氮柴 油进行加氢
精制。结果表明 : N i1 0 D SA- 4吸附剂对柴油 中的碱氮具有较高 的选择吸附性 , 0 在脱碱氮率不小于 8 % 的前提下 , 0 吸 附剂的碱氮容量为 04 % , .5 单程吸附柴 油收率大于 9 % ; 9 在温度 4 5 0~ 0℃ 的范 围内, 溶剂 M能够对饱 和吸附剂进 行较好的脱附再 生 , 经过 4 0次吸附一 附后 , N i1 0 脱 D SA - 4吸附剂的碱氮容量仅 下降 6 7 , 0 . % 同时溶 剂 M 回收后可循
由表 1 见 , 油催 化柴油 总氮 含量 较高 , 可 重 是
一
种 密度 较大 、 十六 烷 指 数较 低 的劣 质 二 次加 工
收 稿 日期 :0 7—0 20 3—3 0。
柴油。
1 2 吸 附 剂 .
ห้องสมุดไป่ตู้
作者简介 : 梁永辉 , 工程 师 , 供职 于锦西 石化 分公 司研 究 现 院, 长期从事轻质油品非加氢精 制工艺 的研究工作。Ema : — i l
l h 8 k 1 6. o y 8 o @ 2 c m
试验所 用吸附剂为 D S ID N i - 4硅铝 吸附剂 , A( 由 中国石油锦西石化分公司与北京三聚环保新材料有
260万吨柴油加氢精制操作手册(新修改)
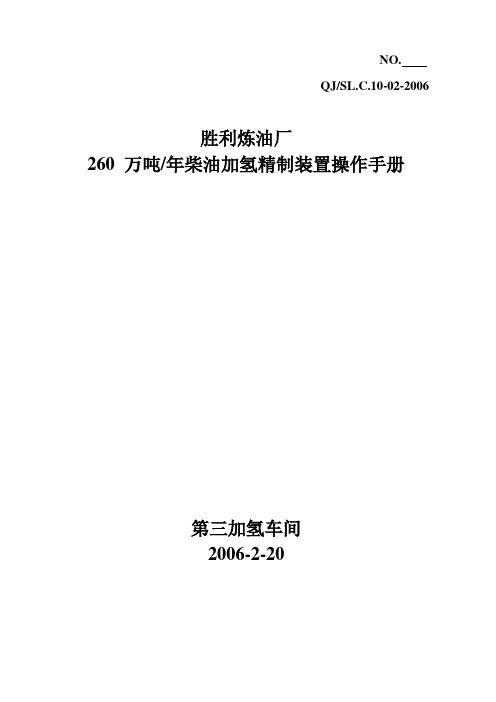
NO.QJ/SL.C.10-02-2006胜利炼油厂260 万吨/年柴油加氢精制装置操作手册第三加氢车间2006-2-20第一章:装置开工 (3)第一节:装置开工准备 (3)第二节:装置气密 (5)第三节原料—分馏系统油循环 (9)第四节催化剂装填及最终氢气气密 (9)第五节催化剂预硫化 (19)第六节初活稳定、切换原料油 (23)第七节脱硫系统开工 (25)第二章装置停工 (26)第一节准备工作及注意事项 (26)第二节反应系统停工 (27)第三节低压、分馏系统停工 (29)第四节脱硫停工 (32)第五节公用工程的停工 (34)第六节F-101烧焦 (35)第七节F-201烧焦 (37)第三章装置正常操作法 (38)第一节装置基本操作 (38)第二节装置联锁说明及操作 (54)第三节过滤器SR101的使用 (63)第四节机组操作法 (75)第五节高压泵操作规程 (89)第四章装置事故处理 (100)第一章:装置开工第一节:装置开工准备一、本装置开工前准备1、通知厂调度、化验、机、电、仪信息所等相关单位,装置准备开工。
2、公用工程投入正常运行,水、电、风、氮气、蒸汽等引入装置。
3、开工盲板准备好。
4、各控制阀校验完毕,各联锁调试好,各机泵、空冷等具备开工运行条件。
5、进行方案交底,操作人员熟练掌开工方案。
二、反应器升降压、升降温操作的规定制定本规定目的,是因为加氢反应器壳体绝大部分是由Cr-Mo钢制成,经长期高温和临氢状态后,会出现程度不同的回火脆化现象,在装置开停工阶段易出现开裂事故,为保证加氢反应器的安全运行和使用寿命,特编制本规定。
1、适用范围1.1本规定适用于加氢装置开停工阶段加氢反应器的升降压、升降温的操作限制以及相关要求。
1.2本规定适用于石油炼厂加氢和重整装置以及煤液化装置中 1.25Cr-0.5Mo-Si或2.25Cr-1Mo钢制反应器的一般升降压、升降温操作限制。
炼油厂其他相类似的反应器操作,也可参照执行。
浅谈催化裂化柴油精制

浅谈催化裂化柴油精制
鞠学贞;徐东刚;宋爱民
【期刊名称】《浙江化工》
【年(卷),期】2002(033)003
【摘要】@@ 山东垦利石化有限责任公司催化裂化装置年加工能力为45万吨,掺炼渣油量占总加工能力的25%左右.重油催化裂化为炼油行业带来了巨大的经济效益,但同时柴油安定性变差,影响了产品的销售.我公司针对自己的具体情况并借鉴外厂经验,自行设计了一套柴油精制系统,于2000年3月投入运行,实践证明:本公司催化裂化柴油安定性得到显著提高.
【总页数】1页(P41-41)
【作者】鞠学贞;徐东刚;宋爱民
【作者单位】垦利石化有限责任公司,山东省东营市,257500;垦利石化有限责任公司,山东省东营市,257500;垦利石化有限责任公司,山东省东营市,257500
【正文语种】中文
【中图分类】TE626
【相关文献】
1.加氢精制深度对催化裂化柴油性质的影响 [J], 郑仁垟;辛靖;张润强;李明丰
2.催化裂化柴油加氢精制-临氢降凝生产低凝柴油 [J], 王化国
3.催化裂化柴油及焦化柴油在 RN-10催化剂上的加氢精制 [J], 王胜军;林栩
4.催化裂化柴油加氢精制催化剂及其工艺条件 [J], 韩志波;马宝利;宁梓伊;刘茉
5.常渣催化裂化柴油加氢精制生产低硫车用柴油的研究 [J], 高连慧;陈丹;庄艳秋
因版权原因,仅展示原文概要,查看原文内容请购买。
催化裂化柴油馏分加氢精制提高十六烷值研究
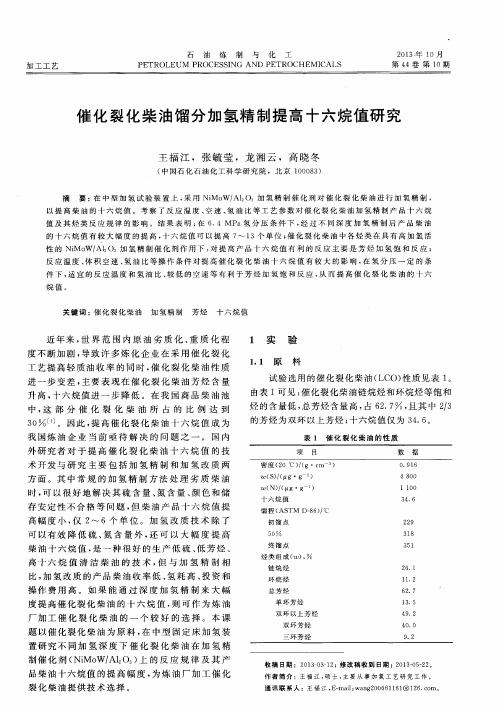
升高 , 十 六烷 值 进 一 步 降低 。在 我 国商 品 柴 油 池
石
油
炼
制
与
化
工
Байду номын сангаас
2 0 1 3年 第 4 4卷
1 . 2 催化剂 和试 验装 置 催化剂 采用 中国石 化 石油 化 工 科学 研 究 院 最 新开 发并 已工业 应 用 的 Ni Mo W/ AI O。型加 氢 精
石
加 工 工 艺
油
炼
制
与
化
工
2 01 3年 1 O月
P ETR0LEUM PROCES S I NG AND P ETR0CHEM I CAI S
第4 4 卷 第 1 O期
催 化 裂 化柴 油 馏 分 加 氢 精 制提 高 十 六烷 值 研 究
王 福 江 ,张毓 莹 ,龙 湘 云 ,高 晓 冬
双环 芳 烃 三 环芳 烃
置 研 究 不 同 加 氢 深 度 下 催 化 裂 化 柴 油 在 加 氢 精
制催化 剂 ( Ni Mo W/ A1 0 。 ) 上 的 反 应 规 律 及 其 产
收 稿 日期 :2 0 1 3 0 3 1 2 ;修 改稿 收 到 日期 :2 0 1 3 - 0 5 — 2 2 。
品柴 油 十 六烷 值 的 提 高 幅 度 , 为 炼 油 厂 加 工 催 化
裂 化 柴 油 提供 技 术 选 择 。
作 者 简 介 :王 福 江 , 硕士, 主 要 从 事加 氢工 艺研 究 工 作 。
100万吨催化裂化装置反应-再生系统工艺设计
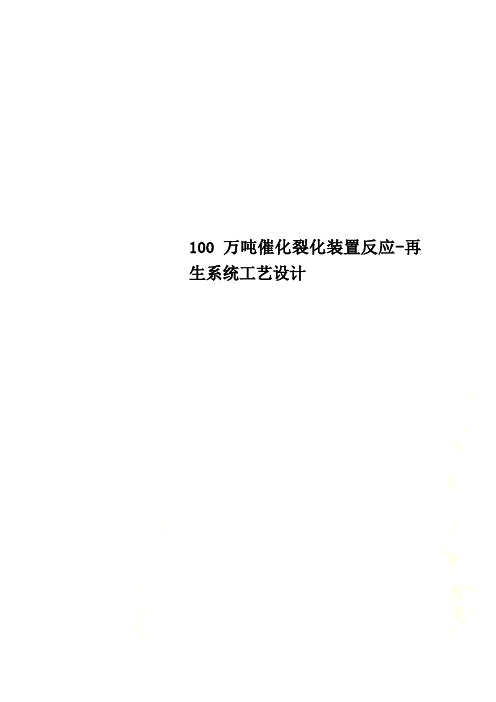
100万吨催化裂化装置反应-再生系统工艺设计兰州理工大学毕业设计设计题目:100万吨催化裂化装置反应-再生系统工艺设计院系:石油化工学院专业班级:化学工程与工艺学生姓名:王晶指导教师:赵秋萍2010年1 月14 日毕业设计任务书一、设计题目:100万吨催化裂化装置反应-再生系统工艺设计二、设计内容以某炼油厂的直馏馏分油为原料,建一个年产100万吨的催化裂化装置。
主要生产稳定汽油、轻柴油。
年开工按330天计算。
三、基本数据1、处理量:100万吨/年2、开工时:8000 小时/年3、原始数据及再生-反应及分馏操作条件原料油及产品性质分别见表1、表2产品的收率及性质见表3 再生器操作及反应条件见表4、提升管反应器操作条件表5 催化裂化分馏塔回流取热分配见表6分馏塔板形式及层数见表7 分馏塔操作条件表见8表1 原料油及产品性质物料,性质稳定汽油轻柴油回炼油回炼油浆原料油密度0.7423 0.87070.8800.99850.8995恩氏蒸馏℃初馏点54 199 288 22410%78 221 347 380 37730%106 257 360 425 43850%123 268 399 450 51070%137 300 431 470 55090%163 324 440 490 700终馏点183 339 465平均相对分子量表 2 原料油的主要性质项目数据项目数据密度0.8995 族组成分析/W%馏程℃饱和烃62.27 初馏点224 芳烃25 10% 377 胶质11.8830% 438 沥青质0.85350℃馏出率/v% 7.5 重金属含量/μg×g-1500℃馏出率/v%49 Ni 5.99 元素组成/w%V 4.77C 84.81 Na 0.32H 12.85 Fe 5.91硫0.77 残炭,W% 5.38/w%表 3 产品产率(质量分数)产品产率% 流量,t/h干气 5.0液化气11.0稳定汽油48.0轻柴油21.2油浆 6.0焦炭8.0损失0.8原料油100.0表4 再生器操作条件项目数据备注再生器顶部0.200压力/ MPa主风入再生162器温度/℃再生器密相700温度/℃待生剂温度/℃大气温度/℃25 大气压力/0.1013MPa空气相对湿70度/%烟气组成(体)/%CO2 14.2CO 0.2O2 4.0 焦碳组成/H/C,质待生剂含碳1.10量/%再生剂含碳0.02量/%烧焦碳量/t/h表5 提升管反应器操作条件项目数据备注提升管出口温505度/℃沉降器顶部压0.200力/ MPa原料预热温度235/℃回炼油进反应265器温度/℃回炼油浆进反350应器温度/℃催化剂活性/% 60.0剂油比 6.0反应时间/ S 3.0回炼比0.5催化剂循环量/t×h-1原料进料量/t×h-1回炼油/回炼油1:0.25浆表6 催化裂化分馏塔回流取热分配(参考)物料顶循环回流一中循环回流二中循环回流油浆循环回流取热比例%15~20 15~20 15~20 40~50 备注表7 分馏塔塔板形式及层数(参考)序号塔段塔板形式层数1 油浆换热段人字挡板或园型挡板6~82 回炼油抽出以下固舌形 23 回炼油抽出口上至一中回流抽出下口下固舌形,条形浮阀,填料10~124 一中回流固舌形,条形浮阀,填料3~45 轻柴油抽出以上至顶循环回流段抽出下固舌形,筛孔,条形浮阀,填料8~96 循环回流段固舌形,条形浮阀,填料3~4 分馏塔总塔板数28~32 表8 催化裂化分馏塔操作条件(参考)序号物料温度/℃压力/MPa塔板位置塔板类型1 分馏塔塔顶油气125 0.255 30 浮阀2 顶循环回流100 30 浮阀3 顶循环回流出塔160 27 浮阀4 富吸收油(再吸120 20 浮阀四、设计步骤(一)再生系统计算 收油,视为轻柴油)返分馏塔5 轻柴油抽出 22019 浮阀 6 一中回流返回 16018 浮阀 7 一中回流抽出 27516 固舌形 8 回炼油返回 2105 固舌形 9 回炼油抽出 2652 固舌形 10 油浆循环回流返回 2701 固舌形 11 回炼油浆抽出 350塔底 12 循环/外排油浆抽出 350 塔底13 轻柴油汽提蒸汽温度 250 1.014 反应油气进分馏塔500塔底1、燃烧计算;2、热量平衡;3、催化剂循环量计算;4、空床流速计算;(二)提升管反应器计算1、物料衡算;2、热量衡算;3、提升管工艺计算;4、旋风分离器工艺计算;五、要求(一)应完成的图:1、通过实习绘出带控制点的催化裂化装置工艺流程图,要求用CAD出图。
- 1、下载文档前请自行甄别文档内容的完整性,平台不提供额外的编辑、内容补充、找答案等附加服务。
- 2、"仅部分预览"的文档,不可在线预览部分如存在完整性等问题,可反馈申请退款(可完整预览的文档不适用该条件!)。
- 3、如文档侵犯您的权益,请联系客服反馈,我们会尽快为您处理(人工客服工作时间:9:00-18:30)。
一、全装置物料平衡1、物料平衡本设计的处理量为95万吨/年,反应阶段为其末期,每年开工时数按8000小时计算。
入方:①原料油=8000%10010109534⨯⨯⨯=118750公斤/小时=248000%10010954⨯⨯⨯=2850吨/天 ②重整氢=8000%70.210109534⨯⨯⨯=3206公斤/小时=248000%70.210954⨯⨯⨯=77吨/天 出方:①精制柴油=118750×96.95%=115128公斤/小时= 2850×96.95%=2763吨/天②粗汽油=118750×1.52%=1805公斤/小时=2850×1.52%=43吨/天③高分排放气=118750×1.78%=2114公斤/小时=2850×1.78%=51吨/天④低分排放气=118750×0.31%=368公斤/小时=2850×0.31%=8.8吨/天⑤回流罐排放气=118750×2.084%=2475公斤/小时=2850×2.084%=59吨/天⑥溶于水中的硫化氢=118750×0.022%=26公斤/小时=2850×0.022%=0.6吨/天⑦溶于水中的氨气=118750×0.024%=28.5公斤/小时=2850×0.024%=0.7吨/天⑧设备漏损=118750×0.01%=12公斤/小时=2850×0.01%=0.3吨/天 2、化学耗氢量计算①计算杂质脱除率a) 硫脱除率 =18001801800-×100% = 90%b) 氮脱除率 = 26158261-×100% = 77.8%c) 硫醇硫脱除率 = 15115-×100% = 93.3%d) 氧脱除率(以酸度计算)原料油含氧率 =8642.01001656/108.53⨯⨯⨯-×100% = 0.00192%精制油含氧率 = 8595.01001656/1014.03⨯⨯⨯-×100% = 0.0000463%氧脱除率=00192.00000465.000192.0-×100% = 97.58%e) 烯烃饱和率(以溴价计算)烯烃饱和率=5.201.45.20-×100% = 80%②化学耗氢量计算a) 每脱掉1%的硫消耗12.5Nm 3H 2/m 3原料油加氢脱硫耗氢量=8642.0100%901018005.126⨯⨯⨯⨯- = 2.34 Nm 3/T2.34×118750/22.4×10002=25kg/hrb) 每脱掉1%的氮消耗53.7Nm 3H 2/m 3原料油加氢脱氮耗氢量=8642.0100%8.77102617.536⨯⨯⨯⨯- = 1.26 Nm 3/ T1.26×118750/22.4×10002=13 kg/hrc) 每脱掉1%的氧消耗44.6Nm 3H 2/m 3原料油加氢脱氧耗氢量=8642.0100%6.971092.16.445⨯⨯⨯⨯- = 0.0967 Nm 3/ T0.0967×118750/22.4×10002=1kg/hrd) 烯烃饱和耗氢量烯烃饱和耗氢量=(20.5-4.1)×10×22.4/160 = 22.96 Nm 3/T22.96×118750/22.4×10002=243kg/hre) 饱和1%的芳烃消耗5.0Nm 3H 2/m 3原料油芳烃饱和耗氢量=8642.0568.05.411.43⨯⨯-)(=6.29 Nm 3/ T6.29×118750/22.4×10002=67kg/hrf) 每脱掉1%的硫醇硫消耗12.5Nm 3H 2/m 3原料油 硫醇硫耗氢量=8642.0100%3.9310155.126⨯⨯⨯⨯- = 0.02 Nm 3/ T0.0202×118750/22.4×10002=0.2kg/hrg) 加氢裂解耗氢量原料油裂解程度为3%,每裂解1分子原料,消耗3分子氢加氢裂解耗氢量=34.197%31000⨯×3×22.4 = 10Nm 3/T10.22×118750/22.4×10002=108kg/hr总化学耗氢量=2.34+1.26+0.0967+22.96+6.29+0.0202+10.22=43Nm 3/T =24.81+13.36+1.025+243.44+66.69+0.214+108.36=458 kg/hr重量分数:加氢脱硫:899.45781.24×100% =5.42%加氢脱氮:899.45736.13×100% =2.92%加氢脱氧:899.457025.1×100% =0.22%烯烃饱和:899.45744.243×100% =53.16%芳烃饱和:899.45769.66×100% =14.56%硫醇脱硫:899.457214.0×100% =0.05%加氢裂解:899.45736.108×100% =23.66%3、化学反应放热量a).加氢脱硫反应放热量=600 kcal/ Nm 3×2.34 Nm 3/T =1404kcal/T 1404 kcal/T×118.75T/hr=166725kcal/hr b).加氢脱氮反应放热量=600 kcal/ Nm 3×1.26 Nm 3/T =756kcal/T 756kcal/T×118.75T/hr=89775kcal/hr c).加氢脱氧反应放热量=600 kcal/ Nm 3×0.0967 Nm 3/T =58.02kcal/T58.02kcal/T×118.75T/hr=6890kcal/hrd).加氢烯烃饱和反应放热量=1260 kcal/ Nm 3×22.96 Nm 3/T =28929.6kcal/T28930kcal/T×118.75T/hr=3435438kcal/hr e).加氢芳烃饱和反应放热量=540 kcal/ Nm 3×6.29 Nm 3/T =3396.6kcal/T3397kcal/T×118.75T/hr=403394kcal/hr f). 加氢裂解反应放热量=450 kcal/ Nm 3×10.22 Nm 3/T =4599kcal/T4599 kcal/T×118.75T/hr=546131kcal/hr总的反应放热量∑=1404+756+58.02+28930+3397+4599=39144kcal/T=166725+89775+6889.875+3435437.5+403393.75+546131.25=4648352.375kcal/hr重量分数:加氢脱硫:%59.3%100391441404=⨯加氢脱氮:%93.1%10039144756=⨯ 加氢脱氧:%15.0%1003914402.58=⨯烯烃饱和:%95.73%100391446.28929=⨯芳烃饱和:%68.8%100391446.3396=⨯加氢裂解:%76.11%100391444599=⨯4、纯氢平衡表入方:新氢=5.51095%7.27⨯⨯×2×87.68%/8000 = 1022kg/hr10002427.1022⨯=25T/d出方:化学耗氢量=458kg/hr100024899.457⨯=10.99T/d排放耗氢量=5.675.2113×2×80.86% = 525.9kg/hr1000249.525⨯=13T/d溶解耗氢(包括低分排放和回流罐排放):低分罐=11.18125.368×43.10%×2=18kg/hr回流罐=46.4475.2474×2.03%×2=2. kg/hr溶解耗氢总量∑=17.52+2.26=20kg/hr10002478.19⨯=0.47472T/d机械漏损:入方-出方=1022.27-(457.899+525.9+19.78)=18.691kg/hr100024691.18⨯=0.449T/d重量分数:化学耗氢:27.1022899.457×100%=44.79%排放耗氢:27.10229.525×100%=51.44%溶解耗氢:27.102278.19×100%=1.93%机械漏损:27.1022691.18×100%=1.83%5、硫化氢的物料平衡产生H 2S :3432%901018001187506⨯⨯⨯⨯-=204kg/hr10002440.204⨯=5T/d排放H 2S :①高分排放:34%6.05.675.2113⨯⨯=66kg/hrT/d 6.110002434.66=⨯②低分排放:34%55.211.18125.368⨯⨯=18kg/hrT/d 4.010002462.17=⨯③回流罐排放:34%85.446.4475.2474⨯⨯=92kg/hrT/d 2.210002479.91=⨯④水中溶解:26kg/hr (在装置总物料平衡中已计算) T/d 6.0100024125.26=⨯⑤粗汽油中溶解:204.40-(66.34+17.62+91.79+26.125)=2.5kg/hr T/d 06.0100024525.2=⨯重量分数:高分排放:%10040.20466⨯=32.46%低分排放:10040.20418⨯%=8.62%回流罐排放:10040.20492⨯%=44.90%水中溶解:10040.20426⨯%=12.78%粗汽油中溶解:10040.2045.2⨯%=1.24%二、反应器的工艺设计入口温度为320℃,入口压力为4.0Mpa,取塔径为3.4m,出口压力为3.9Mpa,选用固定床轴向冷壁式反应器,已知数据如下:表一在压力为4.0Mpa时,温度与气化率和热焓的对应关系如下:加氢反应器入口温度℃气化率we(%)混合焓(Kcal/kg)226 4.72 186.64266 9.49 217.26310 19.09 254.15359 28.81 295.91374 38.65 311.58表二在不同压力下,气化率与温度和热焓之间的对应关系如下:系统压力P=3.9Mpa P=3.8Mpa P=3.7Mpa P=3.6Mpa气化率we(%)温度℃混合焓(Kcal/kg)温度℃混合焓(Kcal/kg)温度℃混合焓(Kcal/kg)温度℃混合焓(Kcal/kg)4.54 196 166.98 194 165.67 193 165.01 191.5 164.03 9.44 267 218.16 265 216.73 264 216.01 262 215.32 19.00 311 254.67 310 253.9328.68 341 281.62 339 279.8938.47 360 299.9248.38 375 315.31注:物料包括加氢生成油,反应生成气和循环氢图一 3.90Mpa下焓值与温度对应关系图二 3.90Mpa 下气化率与温度对应关系表三不同气化率下的油气平均分子量气化率w e (%)平均分子量10 155 20 160 30 165 40170图三 不同气化率的油气平均分子量1.催化剂装填体积(选空速=2.5h -1)空速=催化剂的体积时的体积油在C 20︒=催V 8000/2.86410957⨯=2.5催V ∴=54.96m 3假设D=3.4m ,则L=2V 4D π催⨯=24.314.396.544⨯⨯=5.06m 2.催化剂的当量直径(所选催化剂为mm 62.1⨯Φ)D p =6×F V =6×3323323106102.12)102.1(4/106)102.1(4/-----⨯⨯⨯⨯+⨯⨯⨯⨯⨯⨯⨯πππ=1.64×310-m 3.循环氢(选氢油比=300) 氢油比=油混合氢V V =2.864/8000/1095V 7⨯混合氢=300混合氢V ∴=41223.1Nm 3 混合氢w =混合氢V /22.4×M =18.64.221.41223⨯=11373.16kg/hr 循环氢w =混合氢w -新氢w =11373.16-3206.25=8166.91kg/hr4.D E =0.335.反应器入口温度下物料的气化率和氢分压作4.0Mpa 下的H m ~t 、e w %~t 图,查得t=320℃时,e w =21%,H m =262.0Kcal/kg 由图可得:当e w =21%时,油气M =160.5g/mol入口2p H =总p ×油气纯氢纯氢m m m +=4.0×油气M e w⨯+⨯11875018.6/16.11373%08.83)18.6/(11373.16=3.06Mpa6.反应器出口温度及气化率根据热量衡算得:(原料油混合氢w w +)入口m H +Q×95%=(原料油混合氢w w +)出口m H(11373.16+118750) ×262.0+39144×118750×310-×95%=(11373.16+118750)出口m H 出口m H =295.94Kcal/kg作t ~H m 、e w %~H m 图,查得出口w e =36.0%,出口t =356℃ 7.出口氢分压反应生成气m =循环氢m +[1-(96.95%+1.52%)]×原料油m=1187500153.091.8166⨯+=9983.785kg/hr由图可得:当e w =36.0%时,油气M =168g/mol出口2pH =总p ×油气原料油反应生成气反应生成气(M e w /%)52.1%95.96m 95.7/m %60.7795.7/m ⨯+⨯+⨯=3.9×168%0.369847.011875095.7/785.9983%60.77)95.7/(9983.785⨯⨯+⨯=2.52Mpa8..气体密度v ρt =(进口t +出口t )/2=(320+356)/2=338℃w e =(进w e +出w e )/2=(21%+36%)/2=28.5%mol g /25.164)105.28()1020/()155160(155M =-⨯--+=气w =混合氢w +原料油w ×w e =11373.16+118750×28.5%=45216.91kg/hr 气V =[混合氢混合氢M w +油气原料油M e w w⨯]×22.4×869.995.31⨯×273273t +=[18.611373.16+25.164%5.28187501⨯]×22.4×869.995.31⨯×273273338+ =2631.72m 3/hr v ρ=气气V w =72.263191.45216=17.18kg/m 39.空塔线速u假设D=3.4m ,则S==(π/4)D 2=9.075m 2 u=S气V =3600075.972.2631⨯=0.081m/sec10.混合物粘度查分子量为164.25、温度为338℃下,石油馏分蒸汽粘度为i z =0.0082厘泊Tr=)()(K c K T T =40.182.33273338=+ Pr=05.3297.195.3Pc P == 根据Tr 与Pr 氢的粘度图得2iH z =0.013厘泊[2]原料油原料油混合氢纯氢原料油混合氢油气)()(M e m 8308.0118.6m m e 1m m M ww ⨯+-⨯--+=34.197%5.281187508308.0118.611373.162%08.8318.611373.16%5.28111875016.13731⨯+-⨯⨯⨯--⨯+=)()( =193.052H 粘度:i y 总p p 2H =25.164%5.2811875018.616.11373%08.8318.616.11373⨯+⨯=0.747 混z =∑∑0.5iii0.5ii my z my =5.05.05.05.005.193747.012747.00082.005.193747.01013.02747.0⨯-+⨯⨯⨯-+⨯⨯)()( =9.31×310-厘泊 11.求hv G =w e m m ⨯+原料油混合氢=11373.16+118750×28.5%=45216.91kg/hrL G =)(原料油w e 1m -=118750×(1-28.5%) =84906.25kg/hr L G /v G =84906.25/45216.91=1.878 v G =45216.91kg/hr=24.34/2048.091.45216⨯⨯π=1020.5磅/2尺·hr 根据v G 与L G /v G 关系图查得:h=0.181.13p 1.09.19.05])3.2/1(367.0[h E 103.6h D h z u L p p v ++⨯-⨯⨯=∴-)(ρΔ混 =1.133239.19.05])3.2/18.01(1064.1318.067.0[18.033.01000/1021.907.018.17103.6+⨯⨯⨯+⨯-⨯⨯⨯⨯⨯---)()( =0.1034Pa/m12.检验 ①=LpΔ0.1034Pa/m ,在0.023~0.115Pa/m 范围内 ②15.14.306.5D L >==③=⨯=L Lpp ΔΔ0.1034×5.06=0.523 kg/cm 2<0.84kg/cm 完全符合要求。