30万吨年ABS树脂乳液聚合生产车间的工艺设计
聚合abs树脂生产的工艺流程
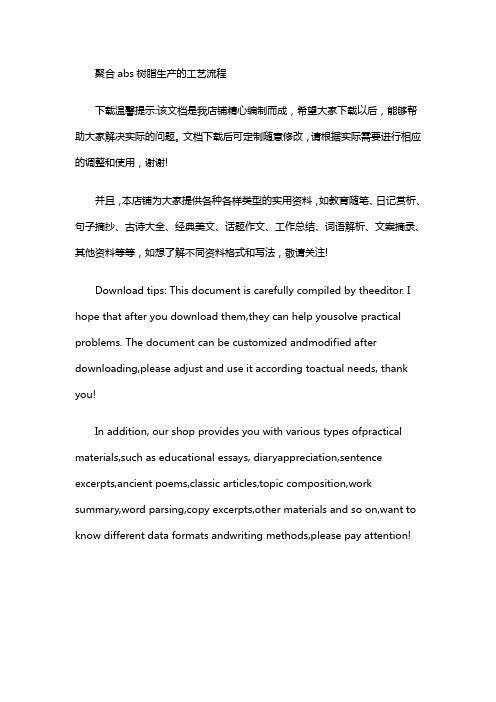
聚合abs树脂生产的工艺流程下载温馨提示:该文档是我店铺精心编制而成,希望大家下载以后,能够帮助大家解决实际的问题。
文档下载后可定制随意修改,请根据实际需要进行相应的调整和使用,谢谢!并且,本店铺为大家提供各种各样类型的实用资料,如教育随笔、日记赏析、句子摘抄、古诗大全、经典美文、话题作文、工作总结、词语解析、文案摘录、其他资料等等,如想了解不同资料格式和写法,敬请关注!Download tips: This document is carefully compiled by theeditor. I hope that after you download them,they can help yousolve practical problems. The document can be customized andmodified after downloading,please adjust and use it according toactual needs, thank you!In addition, our shop provides you with various types ofpractical materials,such as educational essays, diaryappreciation,sentence excerpts,ancient poems,classic articles,topic composition,work summary,word parsing,copy excerpts,other materials and so on,want to know different data formats andwriting methods,please pay attention!聚合ABS树脂生产是一种塑料制造过程,主要通过以下几个步骤进行:1. 原料准备:首先,需要准备ABS树脂的主要原料,包括丙烯腈(A)、丁二烯(B)和苯乙烯(S)。
30万吨年ABS树脂乳液聚合生产车间的工艺设计
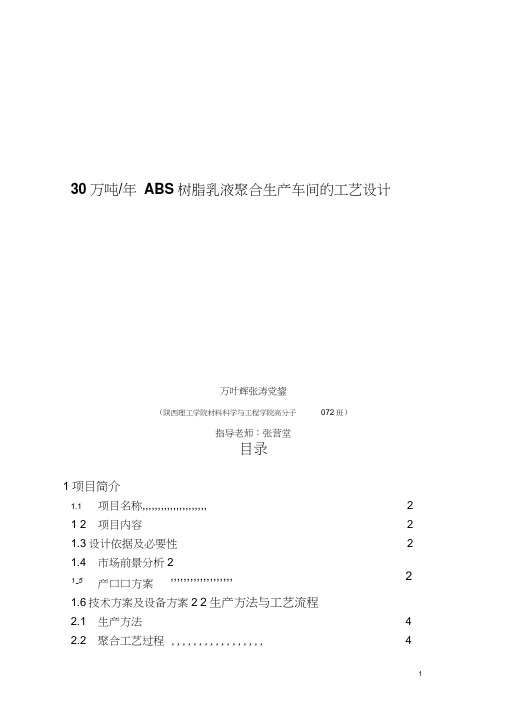
30万吨/年ABS树脂乳液聚合生产车间的工艺设计万叶辉张涛党鋆(陕西理工学院材料科学与工程学院高分子072班)指导老师:张营堂目录1项目简介1.1 项目名称,,,,,,,,,,,,,,,,,,,,, 2 1 2 项目内容 2 1.3设计依据及必要性 2 1.4 市场前景分析2,,,,,,,,,,,,,,,,,,, 2 1-5产口口方案1.6技术方案及设备方案2 2生产方法与工艺流程2.1 生产方法 4 2.2 聚合工艺过程,,,,,,,,,,,,,,,,, 42.3 工艺流程,,,,,,,,,,,,,,,,,, 92.4 工艺参数102.5 主要设备控制方案102.6 安全防护措施11 3物料衡算以及热量横算3.1 物料衡算123.2 热量衡算154设备工艺计算4.1 釜体的设计,,,,,,,,,,,,,,,,,, 174.2 搅拌器的确定,,,,,,,,,,,,,,,, 184.3 各物料进出管口直径确定,,,,,,,,,,,, 19 4.4 轴密封形式,,,,,,,,,,,,,,,,194.5 流体输送机械的选型设计,,,,,,,,,,,, 204.6 调节釜的设计,,,,,,,,,,,,,,, 204.7 单体预乳化罐的设计,,,,,,,,,,,, 204.8 过滤器的设计,,,,,,,,,, ,,, ,,215参考文献1项目简介1.1项目名称:30万吨/年ABS树脂乳液聚合生产车间的工艺设计。
1.2项目内容1、设计方案简介,选定的工艺流程、主要设备的型式进行简单的论述。
2、对选定的工艺流程进行物料衡算,对某些设备进行热量衡算,为设备的工艺计算提供依据。
3、主要设备的工艺设计计算,包括工艺参数的选定、原材料消耗计算、动力计算、设备的工艺尺寸计算及结构设计;典型辅助设备的选型和计算,包括典型辅助设备的工艺尺寸计算和型号规格的选定。
4、工艺流程图一单线图的形式绘制,标出主要设备、辅助设备和主要工艺参数测量点,并绘制工艺流程草图、PFD PID图。
30万吨年ABS树脂乳液聚合生产车间的工艺的设计说明
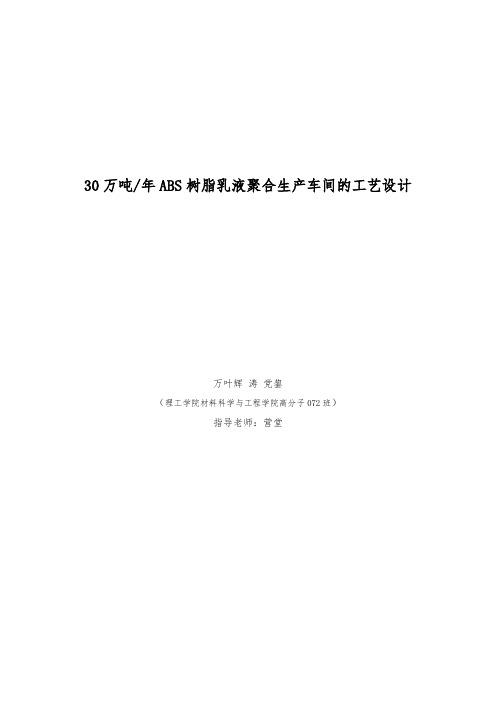
30万吨/年ABS树脂乳液聚合生产车间的工艺设计万叶辉涛党鋆(理工学院材料科学与工程学院高分子072班)指导老师:营堂目录1项目简介1.1项目名称 (2)1.2项目容 (2)1.3设计依据及必要性 (2)1.4市场前景分析 (2)1.5产品方案 (2)1.6技术方案及设备方案 (2)2生产方法与工艺流程2.1 生产方法 (4)2.2 聚合工艺过程 (4)2.3 工艺流程 (9)2.4 工艺参数 (10)2.5 主要设备控制方案 (10)2.6 安全防护措施 (11)3物料衡算以及热量横算3.1物料衡算 (12)3.2热量衡算 (15)4 设备工艺计算4.1釜体的设计 (17)4.2搅拌器的确定 (18)4.3各物料进出管口直径确定 (19)4.4轴密封形式 (19)4.5流体输送机械的选型设计 (20)4.6 调节釜的设计 (20)4.7 单体预乳化罐的设计 (20)4.8 过滤器的设计 (21)5参考文献1项目简介1.1项目名称:30万吨/年ABS树脂乳液聚合生产车间的工艺设计。
1.2项目容1、设计方案简介,选定的工艺流程、主要设备的型式进行简单的论述。
2、对选定的工艺流程进行物料衡算,对某些设备进行热量衡算,为设备的工艺计算提供依据。
3、主要设备的工艺设计计算,包括工艺参数的选定、原材料消耗计算、动力计算、设备的工艺尺寸计算及结构设计;典型辅助设备的选型和计算,包括典型辅助设备的工艺尺寸计算和型号规格的选定。
4、工艺流程图一单线图的形式绘制,标出主要设备、辅助设备和主要工艺参数测量点,并绘制工艺流程草图、PFD、PID图。
1.3设计依据及必要性依据设计任务书或可行性研究报告的批文,环境影响报告书的批文,技术引进报告的批文以及其他相关性文件等。
依据主要原料及物理性质、生产方法、生产能力。
ABS树脂是微黄色固体,有一定的韧性,密度约为1.04~1.06 g/cm3。
它抗酸、碱、盐的腐蚀能力比较强,也可在一定程度上耐受有机溶剂溶解。
30万吨ABS生产车间工业设计--本

30万吨ABS生产车间工业设计--本摘要ABS树脂是五大合成树脂之一,具有广阔的市场前景。
本设计对ABS树脂现有的生产技术、市场需求和发展状况进行了较全面的分析;主要叙述了乳液接枝本体SAN掺混法生产ABS树脂的生产方法及工艺条件,并对物料衡算、设备的选型、厂房的布置等方面也做了简要的介绍;对生产车间所需的各种生产设备和总投资成本进行了初步合算,并根据生产方法绘制出相应的工艺流程图。
关键词:ABS树脂生产技术市场态势物料衡算设备AbstractABS resin is one of the five synthetic resin, and has broad market prospects. The design on the existing production of ABS resin technology, market demand and the development of a more comprehensive analysis; described the production of ABS resin emulsion graft bulk SAN blending method production method and process condition sand material balance, equipment selection, plant layout has also made a brief introduction; a preliminary cost-effective production workshop a variety of production equipment and the total investment cost, and production methods to map out the process flow diagram.Keywords: ABS resin production technology market trend material balance equipment.目录........................................................................................................................... .....................- 2 - 第一章绪论.. (1)1. ABS树脂生产技术现状及进展 (1)1.1技术概况 (1)1.2 乳液接枝本体SAN掺混法 (2)1.2.1接枝用主干胶乳的合成 (2)1.3 ABS连续本体聚合法 (3)2 国内外ABS树脂生产与市场分析及预测[4] (4) 2.1生产情况分析预测 (4)2.2 市场分析及预测 (6)3发展趋势[2] (8)3.1 生产技术发展趋势 (8)3.2 产品发展趋势 (8)第二章工艺流程设计 (10)1. 生产方法、原料和主要工艺参数的选择 (10) 1.1 生产方法的选择 (10)1.2原料的选择 (10)1.3 主要工艺参数 (11)2. 聚合反应过程工艺流程叙述 (13)2.1 工艺流程方框图 (13)2.2 工艺流程叙述 (14)第三章工艺与设备计算 (17)3.1 基础数据 (17)3.2 物料衡算 (18)3.3 设备计算 (19)3.3.1釜数及其主要工艺参数的确定 (19)3.3.2 搅拌器的计算 (21)3.3.3 传热装置设计 (23)3.3.4 设计结果(以生产聚丁二烯胶乳为例) (23) 第四章辅助设备选型 (24)4.1反应釜卸料泵 (24)4.2 凝聚釜 (24)4.3 离心机 (25)4.4 混料槽 (26)4.5挤出机 (26)第五章厂址的选择及其厂房布置 (28)5.1 厂址选择 (28)5.2 厂房布置 (28)5.2.1 总图布置的选择原则 (28)5.2.2 车间区域划分及布置说明 (29)第六章安全、环保和三废处理 (30)6.1 安全方面 (30)6.1.1 主要物料的安全性质及防护 (30)6.1.2安全防护措施 (32)6.1.3 ABS聚合安全操作[23] (32)6.2 环保方面 (34)6.2.1 废水 (34)6.2.2 噪声 (34)6.3 污染防治措施 (35)6.3.1废水 (35)6.3.2 噪声 (35)6.4环保排放指标 (35)七章车间定员 (36)7.1 车间生产岗位及工作 (36)7.2 班次、人员编制 (36)第八章产品成本估算 (38)8.1 固定成本估算 (38)8.2 可变成本估算 (39)8.3 利润估算 (39)小结 (40)致谢 (41)参考文献 (42)第一章绪论ABS树脂是五大合成树脂之一,其抗冲击性、耐热性、耐低温性、耐化学药品性及电气性能优良,还具有易加工、制品尺寸稳定、表面光泽性好等特点,容易涂装、着色,还可以进行表面喷镀金属、电镀、焊接、热压和粘接等二次加工,广泛应用于机械、汽车、电子电器、仪器仪表、纺织和建筑等工业领域,是一种用途极广的热塑性工程塑料。
年产30万吨乳聚丁苯橡胶工艺

30万吨/年乳聚丁苯橡胶聚合车间的工艺设计韩裕明祝骞王金娟(0814054-325 333 254 )(陕西理工学院材料科学与工程学院高分子082班)指导老师:袁新强目录1产品及原料说明1.1丁苯橡胶的发展史 (4)1.2丁苯橡胶的中国发展史 (4)1.3丁苯橡胶的生产技术概况 (5)1.4丁苯橡胶市场前景分析 (6)2生产方法与工艺流程2.1 原料及产品结构与性能 (7)2.2 工艺方案选择依据 (7)2.3 生产工艺原理 (9)2.4 生产工艺流程 (10)2.4 主要设备控制方案 (13)3物料衡算以及热量横算3.1计算依据 (14)3.2反应釜的物料及热量恒算 (15)4 设备工艺计算4.1釜体的设计 (22)4.2搅拌器的确定 (23)4.3各物料进出管口直径确定 (24)4.4轴密封形式 (25)4.5流体输送机械的选型设计 (25)4.6调节釜的设计 (26)4.7过滤器的设计 (26)5 厂址车间、安全防护及三废处理设计5.1厂址及车间设置 (26)5.2安全防护设计 (28)5.3三废处理设计 (31)6参考文献前言丁苯橡胶(SBR)是由丁二烯和苯乙烯经过乳液或溶液聚合制得的共聚物,丁苯橡胶再配以增塑剂、稳定剂、高分子改性剂、填料、偶联剂和加工助剂,经过提炼、塑化、成型加工成各种材料。
在现代工业生产和人类生活中起着举足轻重的作用,因此SBR的生产和技术的改进越来越受到现代人的关注!当前,SBR生产面临着严重的挑战。
比如:生态环境的保护,潜在替代品的市场竞争,资源的进一步优化配置,能量的合理充分利用,生产过程的优化和高效率化,生产和使用效率的提高,应用技术和市场开拓等,都在不同程度上影响着SBR的进一步发展,在上述问题上仍有大量工作要做,对生态环境安全的配套助剂,环境保护技术(包括SBR废弃物的回收,再利用和处理)等方面,更需要花大力气加以研究。
本设计是以丁二烯和苯乙烯单体为原料,对年产能力为30万吨的SBR生产工艺的初步设计,收集有关的化工设计资料作参考,按课程设计大纲和设计任务书的要求进行设计。
ABS树脂的生产设计
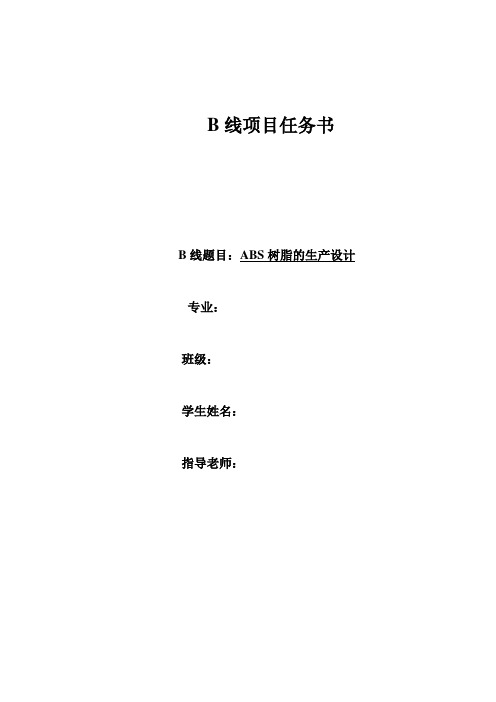
B线项目任务书B线题目:ABS树脂的生产设计专业:班级:学生姓名:指导老师:目录1.ABS简介2.发展简史3.反应机理4.生产工艺5.性能6.化学改性7.加工与应用8.市场态势分析1.ABS简介摘要:本文介绍了丙烯腈-丁二烯-苯乙烯共聚物的基本情况与生产工艺流程,介绍了ABS生产原料的来源及合成方法,工艺条件及相关工艺参数,以及对ABS进行化学改性。
对市场的分析及应用。
关键字:ABS 乳液聚合本体合成改性概念:ABS树脂是指丙烯腈-丁二烯-苯乙烯共聚物,ABS是Acrylonitrile Butadiene Styrene的首字母缩写,其是一种强度高、韧性好、易于加工成型的热塑型高分子材料。
结构:ABS树脂是丙烯腈(Acrylonitrile)、1.3-丁二烯(Butadiene)、苯乙烯(Styrene)三种单体的接枝共聚物。
它的分子式可以写为(C8H8)x·(C4H6)y·(C3H3N)z,但实际上往往是含丁二烯的接枝共聚物与丙烯腈-苯乙烯共聚物的混合物,其中,丙烯腈占15%~35%,丁二烯占5%~30%,苯乙烯占40%~60%,最常见的比例是A:B:S=20:30:50,此时ABS树脂熔点为175℃。
性质:ABS树脂是微黄色固体,有一定的韧性,密度约为1.04~1.06 g/cm3。
它抗酸、碱、盐的腐蚀能力比较强,也可在一定程度上耐受有机溶剂溶解。
ABS树脂可以在-25℃~60℃的环境下表现正常,而且有很好的成型性,加工出的产品表面光洁,易于染色和电镀。
因此它可以被用于家电外壳、玩具等日常用品。
常见的乐高积木就是ABS制品。
ABS树脂可与多种树脂配混成共混物,如PC/ABS、ABS/PVC、PA/ABS、PBT/ABS 等,产生新性能和新的应用领域,如:将ABS树脂和PMMA混合,可制造出透明ABS 树脂。
当共混的三种成分比例的调整时,树脂的物理性能会有一定的变化:1,3-丁二烯为ABS树脂提供低温延展性和抗冲击性,但是过多的丁二烯会降低树脂的硬度、光泽及流动性;丙烯腈为ABS树脂提供硬度、耐热性、耐酸碱盐等化学腐蚀的性质;苯乙烯为ABS树脂提供硬度、加工的流动性及产品表面的光洁度。
ABS装置PBL单元工艺设计
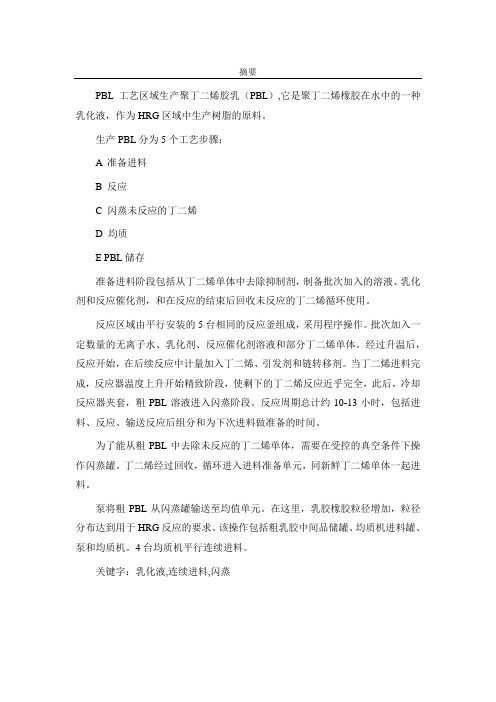
PBL工艺区域生产聚丁二烯胶乳(PBL),它是聚丁二烯橡胶在水中的一种乳化液,作为HRG区域中生产树脂的原料。
生产PBL分为5个工艺步骤:A 准备进料B 反应C 闪蒸未反应的丁二烯D 均质E PBL储存准备进料阶段包括从丁二烯单体中去除抑制剂,制备批次加入的溶液、乳化剂和反应催化剂,和在反应的结束后回收未反应的丁二烯循环使用。
反应区域由平行安装的5台相同的反应釜组成,采用程序操作。
批次加入一定数量的无离子水、乳化剂、反应催化剂溶液和部分丁二烯单体。
经过升温后,反应开始,在后续反应中计量加入丁二烯、引发剂和链转移剂。
当丁二烯进料完成,反应器温度上升开始精致阶段,使剩下的丁二烯反应近乎完全,此后,冷却反应器夹套,粗PBL溶液进入闪蒸阶段。
反应周期总计约10-13小时,包括进料、反应、输送反应后组分和为下次进料做准备的时间。
为了能从粗PBL中去除未反应的丁二烯单体,需要在受控的真空条件下操作闪蒸罐。
丁二烯经过回收,循环进入进料准备单元,同新鲜丁二烯单体一起进料。
泵将粗PBL从闪蒸罐输送至均值单元。
在这里,乳胶橡胶粒径增加,粒径分布达到用于HRG反应的要求。
该操作包括粗乳胶中间品储罐、均质机进料罐、泵和均质机。
4台均质机平行连续进料。
关键字:乳化液,连续进料,闪蒸AbstractThe PBL process area makes Polybutadiene Latex (PBL),an emulsion of polybutadiene rubber in water that is used as a row material to make resin in the HRG process area.a.Feed preparationb.Reactionc.Flash removal of unreacted butadiened.Homogenizatione.PBL storageFeed preparation includes the operations of removing inhibitor from butadiene monomer preparation of batch solutions,an emulsifierand reaction catalysts,and recover of unreacted butadiene from the end of the processfor recycle.Reaction area consists of five identical reactor installed in parallel.which operate in rsequence.A reactor is charged with batch quantities of demineralizedwater,emulsifier,reaction catalysts solution,and a partial charge of butadiene monomer.After heat up and initiation of reaction,butadiene,initiator,andchain transfer agent are metered to the reactor as the reaction proceeds.After the butadiene feed quantity is complete,reactor temperature is increased for the polishing step,which polymerizes the remaining butadiene to near-compltion.The reactor contents are then cooled before transferring the crude PBL solution to the Flash step.The total reactor cycle is 12-13 hours,including the steps of filling,reacting,transfer of reacted contents,and preparation for the next charge.The flash Tank operates under a controlled vacuum in order to remove unreacted butadeiene monomer from the crude PBL.The butadiene is recovered and recycled to the feed preparation area for use with fresh butadiene monomer feed.Crude PBL is pumped from the Flash size distribution is formed that is required for the use in the resin HRG reaction.This operation includes internediate ctude latex storage, homogenizer are fed continuously,in parallel.The PBL product discharges from the homogenizer to one of product storage tanks for testing,prior to bulk storage and feeding to the HRG resin production area. Keywords:Emulsion Feed continuously Flas目录摘要.................................................................................................. 错误!未定义书签。
年产30万吨聚氯乙烯合成工段工艺初步设计设计资料

年产30万吨聚氯⼄烯合成⼯段⼯艺初步设计设计资料毕业设计(论⽂)题⽬年产30万吨PVC合成⼯段的⼯艺初步设计作者学院化学化⼯学院专业材料化学学号指导教师摘要本设计是根据悬浮聚合,年产量为30万吨聚氯⼄烯(PVC)合成⼯段的初步⼯艺设计,根据株洲化⼯集团现场实习等有关资料及参考有关⽂献书籍,完成了物料衡算、热量衡算、主要设备和管道的设计与选型、经济分析、环境保护等。
此设计有说明书⼀份、CAD图纸四张,⼿绘图纸⼀张。
说明书内容包括:1.聚氯⼄烯的概况及主要合成⽅法; 2.PVC合成三个⼯段的简单介绍,其中重点介绍了合成⼯段的⽣产原理和流程;3.物料衡算、热衡算;4.主要设备的设计和选型;5.主要管道的设计及选型;6.经济分析;7.环境保护与安全⽣产技术。
图纸包括:1、合成⼯段⼯艺流程图 2、车间平⾯布置图 3、转化器的装配图 4、⼯⼚布置图 5、碱洗泡沫塔的装配图关键词:氯⼄烯;合成;悬浮聚合;聚氯⼄烯;设计ABSTRACTThe primary design for synthesis construction section of polyvinyl chloride 16000 tons per year was completed according to the information of Zhuzhou Chemical Industry Group scene practice and its relative dates. The equilibrium of material and equilibrium of heat quantity were calculated and the main equipments and pipelines were chosen. The design included a instruction booklet and three diagrams.The main contention of the instruction booklet included: the development history and trendency of producing polyvinyl chloride and vinyl chloride, the production principle and process of synthesis construction section, the calculation of the balance of material and calculation of heat quantity, the design and choice about the main equipments. the design and choice about the main pipelines, the disposal of three wastes processing security and fire protection technology.The diagrams comprised of 1 the technique flow chart with controlled point, 2 the factory floor-plan diagram and the main equipment installing picture, 3 the factory diagram.Keywords: vinyl chloride;;suspension polymerization;polyvinyl chloride;preliminary design⽬录引⾔....................................................................................................................................... - 1 -第⼀章聚氯⼄烯的概况及主要合成⽅法....................................................................... - 2 -1.1 聚氯⼄烯的概况............................................................................................... - 2 -1.1.1聚氯⼄烯的性质.................................................................................... - 2 -1.1.2聚氯⼄烯⼯业的发展概况.................................................................... - 2 -1.1.3聚氯⼄烯制品的开发与应⽤技术........................................................ - 3 -1.2 聚氯⼄烯合成⽅法........................................................................................... - 5 -1.2.1聚氯⼄烯(PVC)⼯艺简介...................................................................... - 5 -1.2.2典型聚合⼯艺概述................................................................................ - 5 -第⼆章聚氯⼄烯的⼯艺过程........................................................................................... - 9 -2.1 主要原料说明................................................................................................... - 9 -2.1.1氯化氢.................................................................................................... - 9 -2.1.2⼄炔........................................................................................................ - 9 -2.1.3氯⼄烯.................................................................................................. - 10 -2.1.4 其它辅助原料...................................................................................... - 11 -2.2 氯⼄烯的合成................................................................................................. - 12 -2.3 聚合⼯序......................................................................................................... - 14 -2.3.1.聚合⼯段流程简述............................................................................. - 14 -第三章物料衡算............................................................................................................... - 16 -3.1 计算依据......................................................................................................... - 16 -3.2 计算................................................................................................................. - 17 -3.2.1混合器的物料衡算.............................................................................. - 17 -3.2.2⽯墨冷却器的物料衡算...................................................................... - 18 -3.2.3多筒过滤器的物料衡算...................................................................... - 20 -3.2.4⽯墨预热器的物料衡算...................................................................... - 20 -3.2.5转化器的物料衡算.............................................................................. - 21 -3.2.6除汞器的物料衡算.............................................................................. - 21 -3.2.7⽔洗泡沫塔的物料衡算...................................................................... - 22 -3.2.8碱洗泡沫塔的物料衡算...................................................................... - 23 -3.2.9氯⼄烯合成的总物料衡算.................................................................. - 24 -第四章热量衡算............................................................................................................. - 24 -4.1 标况下有关物化数据..................................................................................... - 24 -4.2 衡算⽅法......................................................................................................... - 25 -4.3 计算................................................................................................................. - 25 -4.3.1⽯墨冷却器.......................................................................................... - 25 -4.3.2⽯墨预热器.......................................................................................... - 27 -4.3.3转化器.................................................................................................. - 28 -4.3.4冷却⽔消耗.......................................................................................... - 30 -第五章主要设备的计算与选型....................................................................................... - 31 -5.1 ⽯墨冷却器的选型......................................................................................... - 31 -5.2 ⽯墨预热器的选型......................................................................................... - 32 -5.3 转化器的设计................................................................................................. - 33 -5.4 泡沫⽔洗塔的设计......................................................................................... - 35 -5.5 主要设备⼀览表............................................................................................. - 38 -第六章主要管道管径计算和选型................................................................................. - 39 -6.1 HCl进料管...................................................................................................... - 39 -6.2 ⼄炔⽓进料管................................................................................................. - 40 -6.3 ⽯墨冷却器的进料管..................................................................................... - 40 -6.4 多筒过滤器进料管......................................................................................... - 40 -6.5 转化器进料出料管......................................................................................... - 41 -6.6 40%盐⽔进料管............................................................................................... - 42 -6.7 循环⽔管......................................................................................................... - 42 -第七章经济分析............................................................................................................... - 44 -7.1 基本介绍......................................................................................................... - 44 -7.1.1 预计产品成本..................................................................................... - 44 -7.1.2 经济分析........................................................................................... - 44 -7.2 ⽣产PVC所需原材料..................................................................................... - 44 -7.3 原材料及动⼒消耗......................................................................................... - 45 -7.4 投资估算......................................................................................................... - 45 -7.5 产品成本及部分⼚家的成品价格................................................................. - 45 -第⼋章安全⽣产............................................................................................................... - 47 -8.1 安全防⽕技术................................................................................................. - 47 -8.2 ⼄烯合成的安全技术..................................................................................... - 48 -8.3 ⼄炔爆炸......................................................................................................... - 48 -8.4 氯⼄烯的燃烧................................................................................................. - 49 -8.5 安全措施......................................................................................................... - 49 -第九章环境保护............................................................................................................... - 50 -9.1 废⽓的产⽣、中毒机理及处理..................................................................... - 50 -9.1.1 尾排氯⼄烯外逸的产⽣..................................................................... - 50 -9.1.2 中毒机理............................................................................................. - 50 -9.1.3 对VC泄露的综合治理....................................................................... - 50 -9.2 氯化汞触媒的产⽣、中毒机理及处理......................................................... - 51 -9.2.1 氯化汞触媒的产⽣............................................................................. - 51 -9.2.2 氯化汞中毒机理................................................................................. - 51 -9.2.3 废HgCl2触媒的处理......................................................................... - 51 -9.3 废⽔的产⽣、中毒机理及处理..................................................................... - 51 -9.3.1 废⽔排放标准..................................................................................... - 51 -9.3.2 废⽔的处理⽅法................................................................................. - 52 -9.4 其他三废的处理............................................................................................. - 52 -结论..................................................................................................................................... - 53 -参考⽂献............................................................................................................................. - 54 -引⾔本设计是根据设计任务书的要求,以实地考察的PVC⽣产⼯艺流程为参考并通过⼴泛查阅相关的化⼯⽣产设计资料对年产30万吨PVC的氯⼄烯合成⼯段进⾏了初步的设计。
毕业设计(论文)年产10万吨ABS树脂接枝粉料车间工艺设计

毕业设计摘要ABS树脂是聚丁二烯橡胶、单体苯乙烯和丙烯晴的接枝共聚物,它兼具三种组分的共同性能,无毒、无臭、耐冲击、质硬、尺寸稳定、耐化学腐蚀、电性能良好、易于成型加工,表面光洁和容易着色。
ABS树脂是目前产量最大、应用最广的热塑性工程塑料。
目前世界上ABS树脂合成仍广泛采用的是乳液接枝掺混法。
该法是用乳液接枝法生产高胶的ABS接枝粉料作为中间品,将中间品于本体AS聚合物进行掺混。
挤出造粒生产ABS树脂。
该法工艺成熟、流程短、设备少、生产品种多、适宜大规模生产。
本设计主要完成了ABS接枝粉料段的工艺流程设计、反应釜设计、车间布置设计、编制了设计。
关键词:ABS树脂、工艺、乳液接枝掺混法AbstractABS resin is Polybutadiene Rubber, styrene monomer and acrylonitrile graft copolymer, it combines three components of common, non-toxic, odourless, resistant to shocks, the quality is hard, good dimensional stability, chemical resistance, electrical properties, ease of forming, the surface is smooth and easy coloring. ABS resin is by far the most productive, the most widely used thermoplastic plastics.Synthesis of world ABS resin emulsion grafted mixing method is widely used. This Act was produced using emulsion grafting grafting of ABS high glue powder as an intermediate product, intermediate in the ontology AS polymer blending. Extrusion granulation production of ABS resin. The Act less short mature technology, process, equipment, production, varieties, suitable for mass production.This design ABS grafted powder process design, plant layout design, reactor design, preparation of design specifications.Keyword: ABS , craft , lotion copolymeriztion.目 录第一章 概 述 (1)第二章 生产配方及原料、辅助原料的技术规格 (4)2.1 生产ABS 粉料的配方及工艺条件 (4)2.1.1 生产聚丁二烯乳胶的配方及工艺条件 (4)2.1.2 ABS 接枝聚合的配方(质量份) (5)2.1.3 生产ABS 粉料的主要设备 (5)2.2 原料规格 (6)第三章 工艺流程简述 (9)3.1 简述 (9)3.2生产基本原理 (9)3.2.1 聚丁二烯乳胶的合成 (9)3.2.2 ABS 接枝共聚反应机理 (10)3.3 生产工艺过程 (11)3.3.1 简述 (11)3.3.2 PBL 的生产及单体回收的工艺过程 (12)3.3.3 生产ABS 粉料的工艺过程 (13)3.4 工艺技术特点 (13)第四章 工 艺 计 算 (14)4.1物料衡算 (14)4.1.1工艺流程示意图 (14)4.1.2 化学反应方程式: (14)4.1.3确定计算任务 (14)4.1.4 收集数据 (15)4.1.5计算基准 (15)4.1.6聚合计算 (15)4.2设备工艺计算 (18)4.2.1确定计算基准 (18)4.2.2确定操作方式 (18)4.2.3收集数据 (18)4.2.4反应釜的体积计算 (18)4.2.5反应釜直径0D 与筒体高0H 和封头的几何参数的确定 (19)4.2.6 轴封装置 (20)第五章 生产控制分析 (21)5.1 丁二烯聚合及ABS 聚合装置控制系统 (21)5.2 中央控制室 (21)第六章车间布置 (22)6.1概述 (22)6.2设计依据 (22)6.3车间布置要考虑的问题 (22)6.4车间厂房布置 (23)6.4.1厂房形式的选择 (23)6.4.2 厂房的轮廓 (23)6.5车间各部分组成 (23)6.5.1 工艺生产部门 (23)6.5.2 辅助生产部门及生活行政部门 (23)6.6车间设备布置 (23)6.6.1 满足生产工艺要求 (24)6.6.2 满足设备安装与检修对布置的要求 (24)6.6.3 符合建筑设计要求 (24)6.6.4 符合安全卫生标准 (24)第七章 ABS的物化特性及改性产品 (25)7.1ABS的物化特性 (25)7.2ABS的老化及防老措施 (26)7.2.1 自然老化对ABS性能的影响 (26)7.2.2 热氧老化对ABS性能的影响 (26)7.3产品的改性 (26)7.3.1 高抗冲ABS (26)7.3.2 透明ABS (26)7.3.3 耐热ABS (27)第八章安全技术 (28)8.1安全要点 (28)8.1.1 丁二烯贮罐区 (28)8.1.2 聚合系统 (28)8.1.3ABS树脂干燥系统 (28)8.1.4 其他部位 (28)8.2贮存和运输 (29)8.3回收 (29)8.4法律方面 (30)第九章环境保护 (31)9.1概述 (31)9.2污染源及组成 (31)9.2.1 废气污染源及组成 (31)9.2.2组成 (31)9.2.3 废渣(液)污染源及组成 (31)9.3污染物治理措施及预期效果 (32)9.3.1废气治理措施 (32)9.3.2 废水治理措施 (32)9.3.3 废渣(液)治理措施 (33)9.4绿化设计 (33)9.5环境管理与监测 (33)第十章人员编制 (35)第十一章技术经济指标 (37)11.1各种生产工艺技术经济指标 (37)11.2乳液接枝ABS粉末/本体AS熔融料掺混主要参数 (37)11.2.1 装置组成、生产规模、生产方案 (37)11.2.2 原料来源 (38)11.3物耗、能耗、成本 (38)11.3.1 原料及助剂消耗 (38)11.3.2 公用工程消耗 (39)11.3.3 成本 (39)11.4投资 (39)第十二章 ABS发展存在的问题及建议 (42)12.1国内ABS树脂生产存在的问题 (42)12.1.1 ABS树脂生产的原料 (42)12.1.2 产品品种 (42)12.1.3 ABS生产的环保问题 (42)12.2对国内ABS树脂生产的建议 (42)12.2.1 扩大ABS生产能力 (42)12.2.2 开发具有自主知识产权的核心技术 (42)致谢 (43)参考文献 (44)附录 (45)第一章概述ABS树脂,从组成上来看,可以从3个层次表述:它由碳、氢、氮三种元素组成;它是由丙烯腈,苯乙烯,丁二烯三种单体共聚得到的接枝共聚物;它是由苯乙烯丙烯腈在聚丁二烯乳胶上接枝得到的接枝橡胶,与游离的苯乙烯和丙烯腈的共聚物SAN或AS树脂,通过掺混挤压造粒而制得的产品。
abs乳液接枝乳液san掺混聚合生产工艺中问题及解决方案[工作]
![abs乳液接枝乳液san掺混聚合生产工艺中问题及解决方案[工作]](https://img.taocdn.com/s3/m/8d64d53cc1c708a1284a44e8.png)
abs 乳液接枝 - 乳液 san 掺混聚合生产工艺中的问题及解决方案篇一: ABS生产工艺生产技术ABS 树脂的生产方法好多,当前生界上工业装置上应用许多的是乳液接技掺合法和连续本体法。
1乳液接枝掺合工艺:乳液接枝掺合法是在ABS树脂的传统方法-- 乳液接枝法的基础上发展起来的,依据SAN共聚工艺不一样又可分为乳液接枝乳液 SAN掺合、乳液接枝悬浮SAN掺合、乳液接枝本体SAN 掺合三种,此中后二者在当前工业装置上应用许多。
这三种乳液接枝掺合工艺都包含下边几此中间步骤:丁二烯乳胶的制备、接枝聚合物的合成,SAN 共聚物的合成,掺混和后办理。
丁二烯胶乳的合成:丁二烯胶乳的合成是ABS生产过程中的一个主要单元,一般采纳乳液聚合工艺生产。
今生产技术当前比较成熟,控制胶乳中总的固含量(一般总的固含量越高生产成本越低),控制橡胶粒子的大小,在μ m,最幸亏μm范围内,粒径呈双峰散布 , 这样可使 ABS树脂产品拥有优秀的表面性能和韧性。
接枝聚合物的合成:聚丁二烯与苯乙烯、丙烯腈接枝是ABS生产工艺中的核心单元。
粒径呈双峰散布的聚丁二烯胶乳连续送入乳液接枝反响器与苯乙烯和丙烯腈单体混淆物进行接枝共聚反响。
单体与聚丁二烯之比提升则接枝聚合物和SAN共聚物的分子量及接枝度增添,内部接枝率一般随橡胶粒径的增添和橡胶交联密度的降低而增添。
在粒径和橡胶交联密度恒准时接枝度和接枝密度是决定ABS产品性能的要素。
SAN共聚物的合成:苯乙烯与丙烯晴共聚物合成方法有三种:乳液法、悬浮法和本体法。
本体法采纳热引起、连续聚合,产品纯净、质量较高,污染少,在SAN合成中正代替悬浮法,特别在大型ABS 生产装置上。
悬浮法采纳引起剂,间歇聚合、产品不如本体法纯净,产生的废水对环境有污染,但工艺简单,流程短,投资少,聚合热易撒出,对中小型装置而言悬浮法较为经济。
乳液法流程长,技术落伍,发达国家已基本裁减。
掺混和后办理:最后将获取的ABS接枝聚合物与SAN共聚物以不一样比率进行掺混,能够获取多种ABS树脂产品,掺混方法使产品具有很大的灵巧性。
年产30万吨PVC聚合工段的工艺初步设计说明书
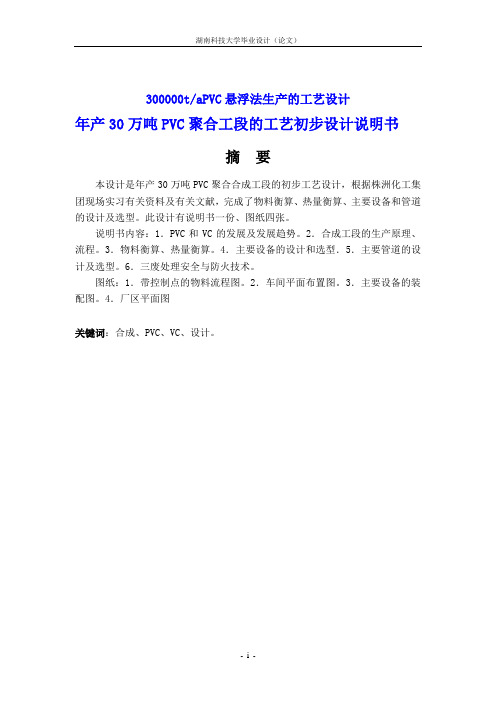
300000t/aPVC悬浮法生产的工艺设计年产30万吨PVC聚合工段的工艺初步设计说明书摘要本设计是年产30万吨PVC聚合合成工段的初步工艺设计,根据株洲化工集团现场实习有关资料及有关文献,完成了物料衡算、热量衡算、主要设备和管道的设计及选型。
此设计有说明书一份、图纸四张。
说明书内容:1.PVC和VC的发展及发展趋势。
2.合成工段的生产原理、流程。
3.物料衡算、热量衡算。
4.主要设备的设计和选型.5.主要管道的设计及选型。
6.三废处理安全与防火技术。
图纸:1.带控制点的物料流程图。
2.车间平面布置图。
3.主要设备的装配图。
4.厂区平面图关键词:合成、PVC、VC、设计。
The Preliminary Design about the Synthesis Construction Section of PVC 200000 tons per yearAbstractThe primary design for synthesis construction section of PVC 300000 tons per year was complete according to the information of Zhuzhou Chemical Industry Group scene practice and its relative dates. The equilibrium of material and equilibrium of heat quantity were calculated and the main equipments and pipelines were chosen. The design included a instruction booklet and four diagrams.The main contention of the instruction booklet included: 1 the development history and trendency of producing PVC and VC, 2 the production principle and process of synthesis construction section, 3 the calculation of the balance of material and calculation of heat quantity, 4 the design and choice about the main equipments. 5 the design and choice about the main pipelines, 6 the disposal of three wastes processing security and fire protection technology.The diagrams comprised of 1 the technique flow chart with controlled point, 2 the factory floor-plan diagram,3 the main equipment installing picture and the Site planKey Words: synthesis、PVC、VC、design.前言本设计是根据设计任务书的要求,以株州化工集团的PVC生产工艺流程为参考并通过查阅相关的化工生产设计资料对年产30万吨PVC的氯乙烯聚合合成工段进行了初步的设计。
年产三十万吨聚氯乙烯毕业设计1
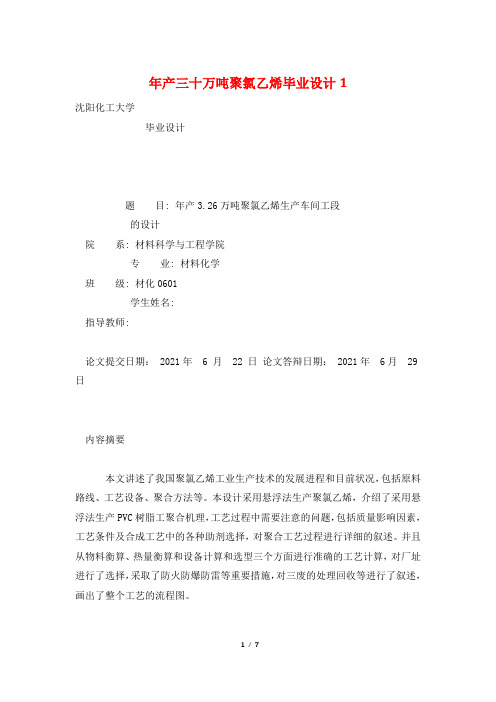
年产三十万吨聚氯乙烯毕业设计1沈阳化工大学毕业设计题目: 年产3.26万吨聚氯乙烯生产车间工段的设计院系: 材料科学与工程学院专业: 材料化学班级: 材化0601学生姓名:指导教师:论文提交日期: 2021年 6 月 22 日论文答辩日期: 2021年 6月 29日内容摘要本文讲述了我国聚氯乙烯工业生产技术的发展进程和目前状况,包括原料路线、工艺设备、聚合方法等。
本设计采用悬浮法生产聚氯乙烯,介绍了采用悬浮法生产PVC树脂工聚合机理,工艺过程中需要注意的问题,包括质量影响因素,工艺条件及合成工艺中的各种助剂选择,对聚合工艺过程进行详细的叙述。
并且从物料衡算、热量衡算和设备计算和选型三个方面进行准确的工艺计算,对厂址进行了选择,采取了防火防爆防雷等重要措施,对三废的处理回收等进行了叙述,画出了整个工艺的流程图。
关键词:聚氯乙烯;生产技术;悬浮法;乙炔法;乙烯法;防粘釜技术;目录第一章总论 (2)1.1 国内外 pvc发展状况及发展趋势 (2)1.2 单体合成工艺路线 (3)1.2.1乙炔路线 (3)1.2.2乙烯路线 (4)1.3聚合工艺实践方法 (5)1.3.1本体法聚合生产工艺 (5)1.3.2乳液聚合生产工艺·································································· 5 1.3.3悬浮聚合生产工艺.................................................................. 6 1.4最佳的配方、后处理设备的选择 (7)1.4.1配方的选择 (7)1.4.2后处理设备侧选择.................................................................. 7 1.5 防粘釜技术. (9)1.6原料及产品性能 (9)1.7 聚合机理 (11)1.7.1自由基聚合机理 (11)1.7.2链反应动力学机理................................................................ 12 1.7.3 成粒机理与颗粒形态.. (12)1.8影响聚合及产品质量的因素 (13)1.9工艺流程叙述 (14)1.10.1加料系统 (14)1.10.2聚合系统 (16)1.10.3浆料汽提及废水汽提系统 (17)1.10厂址的选择 (18)第二章工艺计算 (19)2.1物料衡算 (19)2.1.1聚合釜 (19)2.1.2 混料槽 (22)2.1.3汽提塔································· (23)2.1.4离心机 (26)2.1.5 沸腾床 (27)2.1.6 包装 (28)2.2热量衡算 (29)2.2.1聚合釜 (29)2.2.2沸腾床的热量计算................................................................ 34 2.3 设备的计算及选型 (40)2.3.1 聚合釜 (40)3.3.2 混料槽 (42)3.3.3 汽提塔 (42)3.3.4 离心机 (43)3.3.5内热式沸腾床的计算 (44)2.3.6泵、鼓风机、过滤器 (49)第三章非工艺部分 (52)3.1厂内的防火防爆措施 (52)3.2车间照明及采暖措施 (52)3.3防静电,防雷措施 (53)3.4三废处理情况 (54)3.4.1电石渣的处理 (54)3.4.2电石渣上清液的处理 (54)3.4.3 热水的综合利用 (54)3.4.4尾气的回收利用 (55)3.4.5转化水洗塔水的回收利用 (55)结束语 (56)附录 (58)。
30万吨-年聚丙烯项目装置设计

浅谈30万吨/年聚丙烯项目装置设计摘要:对管道的特点,介绍了管道的各种设计,包括装置布置设计、配管设计、管道应力设计、设备和管道的隔热设计、设备和管道的涂漆设计等,结合案例对管道设计更进一步研究,对管道的设计具有指导意义。
关键词:管道设计装置应力配管1 工程概况本套30万吨/年聚丙烯项目装置布置占地面积约51007m2。
共有设备约318台套,聚合区占地面积约为105m×71m,设备为露天布置。
挤压造粒单元布置在封闭厂房内,占地面积约为47m×44m。
本装置为引进意大利lyondell-basell公司的spherizone新工艺技术,tecnimont公司负责工艺包设计的年产三十万吨均聚物、无规共聚物的聚丙烯装置。
2 装置布置设计说明2.1聚合区设备布置按照工艺流程的顺序,聚合区内管廊以西,从北到南依次为、丙烯乙烯精制、丙烯供料罐、催化剂制备、反应框架、脱气干燥框架、共聚丙烯循环压缩。
聚合区内管廊以东,从南到北为丙烯循环气压缩、氢气循环气压缩、聚丙烯干燥循环、丙烯排放、氢气精制、冷冻单元及凝结水回收、夹套水冷却。
聚合区四周设明沟,盖有篦子板,把汇集的雨水、消防水和地面冲洗水排放至聚合区东南侧的污水池。
3装置设计3.1 装置布置的原则本装置的总平面布置原则是根据工艺生产特点、管廊以及各公用工程的现有接口条件,在有利生产、方便管理、满足安全的前提下,按工艺流程顺序确定工艺单元的相对位置,根据《石油化工企业设计防火规范》的要求确定间距,对于防火、防爆、防腐要求相近的适当集中布置,并考虑与全厂总面的衔接的原则上,还应满足下列要求:(1)装置布置设计应满足工艺流程的要求按物流顺序布置设备,对处理腐蚀性有毒粘稠物料的设备按物料性质紧凑布置,考虑事故因素,并按其分组,与其它区分开布置。
建筑物如控制室、实验室应布置在非危险区。
道路应布置成消防车易通行并避免死端。
(2)根据方便操作,便于安装和维修,经济合理和整齐美观的要求安排设备间距、净空高度,考虑操作通道及梯子平台的设置。
30万吨年产值聚氯乙烯悬浮聚合发生产车间工艺设计毕业设计说明书

30万吨年产值聚氯乙烯悬浮聚合发生产车间工艺设计毕业设计说明书毕业设计说明书悬浮聚合法30万吨/年聚氯乙烯车间工艺设计悬浮聚合法年产30万吨聚氯乙烯车间工艺设计摘要本文概述了聚氯乙烯的性质、应用、发展状况、工艺进展以及聚合过程中的影响因素,在此基础上确定了聚氯乙烯悬浮聚合的生产工艺路线和相关参数。
然后在物料衡算、热量衡算的基础上进行了设备选型、车间布置和经济核算。
文中还对防火防爆防雷和三废的处理回收等方案进行了简单的阐述。
最后绘制了带控制点的工艺流程图、主体设备图和车间布置图。
关键词:聚氯乙烯,悬浮聚合,反应釜,工艺设计The process design for PVC workshop of suspensionpolymerization with annual output of 300000 tonsAbstractThe properties, application, development and the technology progress of PVC were summaried in this paper. After the influence factors of synthesis process discussed, the production of acetic anhydride process route and related parameters are determined, and the material balance and heat balance of main equipments were calculated. Based on this, the equipments selection, workshop layout and economic accounting were accomplished. In addition, the protection of fire, lightning, poison and "three wastes" treatment recovery plan were simply discussed. Finally the process flow chart with control point, the figure of main equipments and workshop layout were drawed.Keywords:PVC;suspension polymerization;agitated reactor;process design目录1 绪论 (1)1.1 聚氯乙烯简介 (1)1.2 国内外聚氯乙烯悬浮聚合的工艺进展 (1)1.2.1 国内聚氯乙烯悬浮聚合的工艺进展 (2)1.2.2 国外聚氯乙烯悬浮聚合的工艺进展 (3)1.3 聚合工艺实践方法 (5)1.3.1 本体聚合生产工艺 (5)1.3.2 乳液聚合生产工艺 (5)1.3.3 悬浮聚合生产工艺 (5)1.4 悬浮聚合生产工艺的两种操作方法的比较 (6)1.4.1 连续式操作 (6)1.4.2 间歇式操作 (7)1.5 氯乙烯悬浮聚合生成聚氯乙烯过程中的影响因素 (7)1.5.1 纯水的影响 (7)1.5.2 乙炔的影响 (7)1.5.3 高沸物的影响 (8)1.5.4 聚合体系中氧的影响 (8)1.5.5 聚合体系中铁的影响 (8)1.5.6 分散剂的影响 (8)1.5.7 引发剂的影响 (9)1.5.8 涂釜剂的影响 (9)1.5.9 调节剂的影响 (9)1.5.10 聚合温度的影响 (9)1.5.11 无机添加剂的影响 (9)2 本设计的工艺流程和相关参数的设定 (11)2.1 本设计拟采用的方法 (11)2.1.1 生产方法 (11)2.1.2 反应机理 (11)2.2 本设计拟采用的工艺条件 (11)2.2.1 聚合釜的选择 (11)2.2.2 氯乙烯单体回收冷凝系统 (13)2.2.3 气提系统 (14)2.2.4 离心系统 (14)2.2.5 PVC树脂的干燥系统 (15)2.3 工况温度的选择 (15)2.4 本设计拟采用的生产工艺路线和工艺参数 (16) 2.4.1 生产工艺路线 (16)2.4.2 主要工艺参数 (16)2.4.3 工艺流程图 (17)3 物料衡算 (18)3.1 有关设计参数设定 (18)3.2 本工艺的配方 (18)3.3 聚合釜的物料衡算 (18)3.3.1 物料平衡图 (19)3.3.2 反应前后各物质的质量计算 (19)3.3.3 物料衡算表 (19)3.4 混料槽的物料衡算 (20)3.4.1 物料平衡图 (20)3.4.2 混料前后各物质的质量计算 (21)3.4.3 物料衡算表 (21)3.5 汽提塔的物料衡算 (21)3.5.1 物料平衡图 (21)3.5.2 汽提前后各物质的质量计算 (22)3.5.3 物料衡算表 (23)3.6 离心部分的物料衡算 (23)3.6.1 物料平衡图 (24)3.6.2 离心前后各物质的质量计算 (24)3.7 气流干燥部分的物料衡算 (24) 3.7.1 物料平衡图 (25)3.7.2 干燥前后各物质的质量计算 (25) 3.7.3 物料衡算表 (25)3.8 沸腾干燥部分的物料衡算 (25) 3.8.1 物料平衡图 (25)3.8.2 干燥前后各物质的质量计算 (26) 3.8.3 物料衡算表 (26)3.9 筛分部分的物料衡算 (26)3.9.1 物料平衡图 (26)3.9.2 筛分前后各物质的质量计算 (26) 3.9.3 物料衡算表 (26)3.10全过程物料衡算 (27)3.10.1 间歇操作过程物料衡 (27)3.10.2 连续操作过程物料衡算 (27)4 能量衡算 (29)4.1 热量衡算方程 (29)4.2 聚合釜的热量衡算 (29)4.2.1 有关参数的选择 (29)4.2.2 春季时聚合釜热量衡算 (30) 4.2.3 夏季时聚合釜热量衡算 (31) 4.2.4 秋季时聚合釜热量衡算 (32) 4.2.5 冬季时聚合釜热量衡算 (33) 4.3 汽提塔的热量衡算 (34)4.4 汽流干燥部分的热量衡算 (34) 4.4.1 气流干燥部分的相关数据 (35) 4.4.2 热量衡算 (35)4.5 沸腾干燥部分的热量衡算 (34) 4.5.1 相关数据的选择和设定 (39)5 设备选型 (45)5.1 聚合釜的选择 (45)5.1.1 釜外型尺寸及内部构件辅助设备的参数 (45) 5.1.2 聚合釜台数及设备后备系数的计算 (45) 5.1.3 聚合釜外形尺寸的设计 (46)5.1.4 搅拌装置的设计 (47)5.1.5 工艺管口的设计 (47)5.2 混料槽的选择 (49)5.3 汽提塔的选择 (49)5.3.1 塔尺寸及塔的特性参数 (49)5.3.2 操作工艺条件 (50)5.3.3 气提塔的数量 (50)5.4 离心机的选择 (50)5.5 气流干燥床的选择 (51)5.6 沸腾干燥床的选择 (52)5.6.1 适宜操作气速的计算 (52)5.6.2 沸腾床和挡板高度的计算 (53)5.6.3 分布板结构设计 (54)5.7 换热设备的选型和工艺计算 (55)5.7.1 气提塔中螺旋板换热器设计 (55)5.7.2 沸腾干燥中空气预热器设计 (57)5.8 流体输送机械的选型设计 (57)5.9 贮罐的选型和工艺设计 (57)5.9.1 原料氯乙烯单体的贮罐设计 (57)5.9.2 原料氯乙烯计量罐设计 (59)6 厂址选择及车间布置设计 (60)6.1 厂址选择的依据和原则 (60)6.2 车间厂房布置 (60)6.2.1 车间厂房布置的原则 (60)6.2.2 车间厂房结构设计 (61)6.2.3 车间各部分组成及布置要求 (61) 6.3 车间设备布置 (62)6.3.1 车间设备布置的原则 (62)6.3.2 车间设备布置的要求 (63)6.4 本设计的车间布置 (65)7 技术经济 (67)7.1 技术经济分析概述 (67)7.2 主要技术经济指标 (67)7.3 投资估算 (67)7.3.1 总投资费用估算 (67)7.3.2 成本估算 (68)7.3.3 收入、税收和利润 (70)7.3.4 经济评价 (71)8 安全操作、三废防治和环境保护 (73) 8.1 厂内的防火、防爆措施 (73)8.1.1 氯乙烯聚合的安全规范 (73)8.1.2 防火防爆措施 (73)8.2 废气防治 (75)8.2.1 废气危害 (75)8.2.2 废气防治措施 (75)8.3 废水防治 (75)8.3.1 废水危害 (75)8.3.2 废水防治措施 (75)8.4 废渣防治 (76)8.4.1 废渣危害 (76)8.4.2 废渣防治措施 (76)9 结论 (77)参考文献 (78)致谢 (81)1 绪论1.1 聚氯乙烯简介聚氯乙烯(Poly Vinyl Chloride)简称PVC,下同。
关于ABS的乳液聚合合成工艺学流程简介
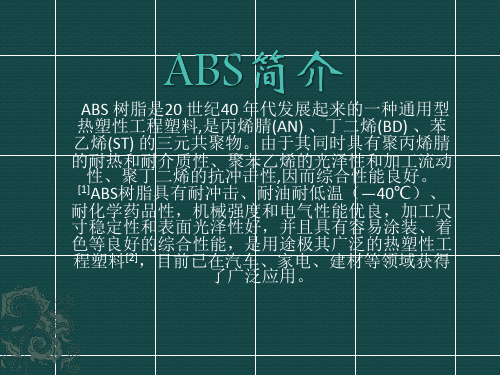
优点:聚合设备较简单,反应温度容易控制,操作方便,橡胶用量不收限 制故便于制造高冲品种,产品质量叫物理共混法有大幅度提高,课生产的 品种也较多。
此法是先将BD进行乳液聚合制备PBL,其次使PBL和部分ST、AN进行 乳液接枝聚合制成ABSL,然后再和用乳液接枝聚合法制得的SANL进 行共凝聚,经脱水、干燥得到ABS成品。该法为Marbon公司所开发, 于1978年将该项技术卖给了美国钢铁公司(USS)。工艺流程如下:
• 固体丁腈橡胶+固体SAN树脂共混 • 丁腈乳胶+SAN乳胶共凝聚
• 乳液聚合接枝 • 乳液-本体聚合接枝 • 本体-悬浮聚合接枝 • 连续本体聚合接枝
• 乳聚接枝ABS胶乳+乳聚SAN胶乳共凝聚 • 乳聚接枝ABS粉料+悬浮聚合SAN粒料共混 • 乳聚接枝ABS粉料+本体聚合SAN粒料共混
优点:接枝率容易控制;可以进行多品种生产。 缺点:此法存在着经典乳液聚合接枝法的同样缺点,并且还需要两套聚 合设备。
此法由日本东丽公司所开发,1977年工业化装置正式投入生产。此法 先使BD进行乳液聚合制备PBL,其次和少量ST、AN进行乳液接枝聚 合得到橡胶含量高的ABSL。然后,将此ABSL在专用的挤压脱水机中 进行凝聚、脱水。脱水后的物料用其余的ST,AN溶解后送入两个串 联的聚合釜进行本体聚合。在聚合过程中,利用ST、AN和ABSL凝聚 物带来的少量水分形成共沸物自聚合釜中蒸出,经冷凝分离出水分后, ST、AN返回聚合釜,借此除去大部分反应热。聚合完了后脱除未反 应单体、造粒得到ABS产品。工艺流程如下:
优点:据称,此法与乳聚接枝共混法比较,可降低能耗15%,废水量少。 缺点:生产品种较少,仍有少量废水排出。
年产20万吨ABS项目HRG单元工艺设计开题报告
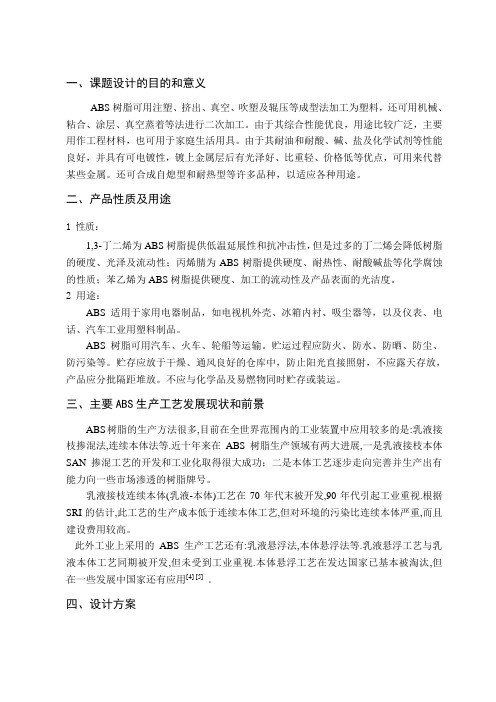
一、课题设计的目的和意义ABS树脂可用注塑、挤出、真空、吹塑及辊压等成型法加工为塑料,还可用机械、粘合、涂层、真空蒸着等法进行二次加工。
由于其综合性能优良,用途比较广泛,主要用作工程材料,也可用于家庭生活用具。
由于其耐油和耐酸、碱、盐及化学试剂等性能良好,并具有可电镀性,镀上金属层后有光泽好、比重轻、价格低等优点,可用来代替某些金属。
还可合成自熄型和耐热型等许多品种,以适应各种用途。
二、产品性质及用途1 性质:1,3-丁二烯为ABS树脂提供低温延展性和抗冲击性,但是过多的丁二烯会降低树脂的硬度、光泽及流动性;丙烯腈为ABS树脂提供硬度、耐热性、耐酸碱盐等化学腐蚀的性质;苯乙烯为ABS树脂提供硬度、加工的流动性及产品表面的光洁度。
2 用途:ABS适用于家用电器制品,如电视机外壳、冰箱内衬、吸尘器等,以及仪表、电话、汽车工业用塑料制品。
ABS树脂可用汽车、火车、轮船等运输。
贮运过程应防火、防水、防晒、防尘、防污染等。
贮存应放于干燥、通风良好的仓库中,防止阳光直接照射,不应露天存放,产品应分批隔距堆放。
不应与化学品及易燃物同时贮存或装运。
三、主要ABS生产工艺发展现状和前景ABS树脂的生产方法很多,目前在全世界范围内的工业装置中应用较多的是:乳液接枝掺混法,连续本体法等.近十年来在ABS树脂生产领域有两大进展,一是乳液接枝本体SAN掺混工艺的开发和工业化取得很大成功;二是本体工艺逐步走向完善并生产出有能力向一些市场渗透的树脂牌号。
乳液接枝连续本体(乳液-本体)工艺在70年代末被开发,90年代引起工业重视.根据SRI的估计,此工艺的生产成本低于连续本体工艺,但对环境的污染比连续本体严重,而且建设费用较高。
此外工业上采用的ABS生产工艺还有:乳液悬浮法,本体悬浮法等.乳液悬浮工艺与乳液本体工艺同期被开发,但未受到工业重视.本体悬浮工艺在发达国家已基本被淘汰,但在一些发展中国家还有应用[4] [5]。
四、设计方案1 HRG单元介绍:本公司采用乳液聚合的方法来制备ABS,生产过程主要有四个单元,分别为:(1)PBL单元,也就是聚丁二烯胶乳的制备。
乳液接枝聚合生产ABS树脂
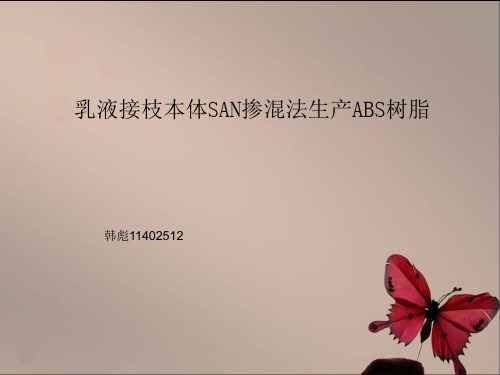
该法合成SAN树脂主要包括配料、聚合、脱挥和造粒等过程,把按比例配制的苯乙烯和 丙烯腈单体在少量溶剂存在的情况下被连续加入到采用蒸发冷凝散热的全混流反应器 进行反应,在物料达到75%转化率后送到真空条件下的脱挥器将未反应的苯乙烯、丙烯 腈单体和溶液闪蒸出去并回收循环利用,熔融的物料再经过造粒成为SAN树脂成品。 由苯乙烯单体、丙烯腈和溶剂乙苯以及回收液组成的物料经预热后进入聚合=30;70, 乙苯占单体重量的5%~10%。聚合反应温度为120~150摄氏度,压力0.196~0、294兆 帕,反应后从聚合釜出来的物料用齿轮泵送入第一脱挥器,在0、196兆帕压力下闪蒸 除去大部分丙烯腈和部分苯乙烯单体、乙苯等挥发组分。然后经管式加热器加热至240 摄氏度后,进入第二脱挥器,在2.67千帕压力下再脱除残余的苯乙烯单体等挥发组分。 整个系统用290摄氏度的热油保温。熔融的SAN送去挤条切粒,然后送至SAN料斗供与 ABS接枝粉料掺混使用。 4、掺混与造粒 ABS接枝基料与SAN树脂按一定比例混合,经挤出造粒,即为ABS树脂。ABS接枝共聚 物与SAN树脂的掺配一般包括宏观和微观上的混合两个部分,前者即两相的掺混,其混合 尺度在0.01~5mm级,主要目的是调整ABS乳料与SAN树脂及各种助剂的比例以生产不 同性能的品种;后者其混合尺度在钠米-微米级,主要目的是通过双螺杆挤出机的作用使 ABS接枝共聚物与SAN共聚物共混形成ABS的分散相和SAN的连续相,而分散相和连续 相的分子结构、化学组成、分子量大小及分布、加工条件对最终产品有直接影响。 ABS树脂的掺配方法有湿法和干法两种。相对而言,干法操作简单,对设备要求不高,工 艺条件也容易控制,但由于ABS接枝乳料要经过干燥程序,增加了与热空气接触的时间,容 易出现部分氧化的现象,造成ABS树脂外观发黄,使其价格大受影响,在市场竞争日益激烈 的今天,湿法共混越来越受到重视。经过双螺杆挤出机加热塑炼后,得到ABS树脂熔体,再 经过冷却后拉成条形,最后经切粒机切成粒状,就可以作为ABS商品出售了。
- 1、下载文档前请自行甄别文档内容的完整性,平台不提供额外的编辑、内容补充、找答案等附加服务。
- 2、"仅部分预览"的文档,不可在线预览部分如存在完整性等问题,可反馈申请退款(可完整预览的文档不适用该条件!)。
- 3、如文档侵犯您的权益,请联系客服反馈,我们会尽快为您处理(人工客服工作时间:9:00-18:30)。
30万吨/年ABS树脂乳液聚合生产车间的工艺设计万叶辉张涛党鋆(陕西理工学院材料科学与工程学院高分子072班)指导老师:***目录1项目简介1.1项目名称 (2)1.2项目内容 (2)1.3设计依据及必要性 (2)1.4市场前景分析 (2)1.5产品方案 (2)1.6技术方案及设备方案 (2)2生产方法与工艺流程2.1 生产方法 (4)2.2 聚合工艺过程 (4)2.3 工艺流程 (9)2.4 工艺参数 (10)2.5 主要设备控制方案 (10)2.6 安全防护措施 (11)3物料衡算以及热量横算3.1物料衡算 (12)3.2热量衡算 (15)4 设备工艺计算4.1釜体的设计 (17)4.2搅拌器的确定 (18)4.3各物料进出管口直径确定 (19)4.4轴密封形式 (19)4.5流体输送机械的选型设计 (20)4.6 调节釜的设计 (20)4.7 单体预乳化罐的设计 (20)4.8 过滤器的设计 (21)5参考文献1项目简介1.1项目名称:30万吨/年ABS树脂乳液聚合生产车间的工艺设计。
1.2项目内容1、设计方案简介,选定的工艺流程、主要设备的型式进行简单的论述。
2、对选定的工艺流程进行物料衡算,对某些设备进行热量衡算,为设备的工艺计算提供依据。
3、主要设备的工艺设计计算,包括工艺参数的选定、原材料消耗计算、动力计算、设备的工艺尺寸计算及结构设计;典型辅助设备的选型和计算,包括典型辅助设备的工艺尺寸计算和型号规格的选定。
4、工艺流程图一单线图的形式绘制,标出主要设备、辅助设备和主要工艺参数测量点,并绘制工艺流程草图、PFD、PID图。
1.3设计依据及必要性依据设计任务书或可行性研究报告的批文,环境影响报告书的批文,技术引进报告的批文以及其他相关性文件等。
依据主要原料及物理性质、生产方法、生产能力。
ABS树脂是微黄色固体,有一定的韧性,密度约为1.04~1.06 g/cm3。
它抗酸、碱、盐的腐蚀能力比较强,也可在一定程度上耐受有机溶剂溶解。
ABS树脂是丙烯腈—丁二烯—苯乙烯的三元共聚物。
ABS树脂外观微黄不透明,相对密度1.04。
它具有良好尺寸稳定性,突出的耐冲击性、耐热性、介电性、耐磨性,表面光泽性好,易涂装和着色等优点。
ABS树脂可以在-25℃~60℃的环境下表现正常,而且有很好的成型性,加工出的产品表面光洁,易于染色和电镀。
因此它可以被用于家电外壳、玩具等日常用品。
1.4市场前景分析:1997年世界ABS树脂生产能力为556万吨/年,主要产地是亚洲、北美和西欧。
亚洲的生产能力占世界总能力的60%以上。
目前世界ABS生产能力发展的特点是“西方不振、东方高涨”,未来几年内世界新增能力仍主要集中在亚洲地区,韩国、中国和中国台湾省以及马来西亚都将新建或扩建ABS树脂生产装置,虽然亚洲地区的这些新增计划不一定全部实现,但在未来几年还是会有较大的发展。
1999年,世界ABS树脂需求量为375、2万吨,1996-2010年的年均需求增长率为2.9%。
随着ABS树脂逐渐向高性能、多功能树脂发展,其需求量会大幅增加。
1.5产品方案:生产能力:ABS树脂30万吨/年;开工时间:330d/a,24h/d。
1.6技术方案及设备方案:(一)技术方案:ABS的工业生产方法很多,主要有乳液接枝、乳液接枝掺合法和连续本体法等。
乳液接枝法是使苯乙烯单体和丙烯腈接枝在聚丁二烯胶乳上得到的ABS树脂。
这种方法现已为乳液接枝掺合法所取代。
乳液接枝共混法是在ABS树脂的传统方法--乳液接枝法的基础上发展起来的,它将部分苯乙烯单体和丙烯腈与聚丁二烯胶乳进行乳液接枝共聚,而以另一部分苯乙烯单体和丙烯腈单体进行共聚生成SAN,然后再将两者以不同比例掺合可以得到各种牌号的ABS树脂。
这一方法根据SAN共聚工艺不同又可分为乳液接枝乳液SAN掺合、乳液接枝悬浮SAN掺合、乳液接枝本体SAN掺合三种,目前乳液接枝一乳液SAN 共混法在发达国家已被淘汰;乳液接枝一悬浮SAN掺混法只适合于中小型生产装置。
乳液聚合主要优点有:①聚合反应可在较低温度下进行,并能同时获得高聚合速率和高分子量;②以水为介质,比热容大,体系黏度小,有利于散热;③乳液产品(称胶乳)可以直接作为胶粘剂和表面处理剂加以使用,而没有易燃及污染环境等问题。
缺点:①聚合物以固体使用时,需要加破乳剂,会产生大量废水;②而且要洗涤、脱水、干燥,工序多,生产成本比悬浮聚合高;③产物中杂质含量较高。
(二)设备方案:该项目主要生产设备为聚合釜、凝聚釜、接枝釜、贮槽、混合槽、沸腾干燥器等大型设备以及各类机泵、各种仪表等。
2生产方法与工艺流程2.1 生产方法选择生产工艺路线就是指选择生产方法。
生产方法就是指在化工生产过程中使用何种原料、根据何种原理、选择实施何种方法,通过何种操作过程实现从原料变为产品的方法。
主要生产方法:采用低温乳液共聚方法制备丙烯腈含量约为20%(质量分数)的丁腈胶乳,之后制备丙烯腈含量为20%~30% AS树脂乳液,然后通过采用适当比例将两种乳液共聚、凝聚、分离、水洗、过滤、干燥和挤出造粒,即可得ABS树脂。
本项目基本工艺由原材料的配制、聚合、脱单体和成品包装等工序。
基本组分是:单体、引发剂、乳化剂、分散剂、终止剂、分子量调节剂和抗氧剂等。
2.1.1 原料选择:该项目选用的原料主要单体为:丁二烯,苯乙烯和丙烯腈。
2.1.2 聚合机理:连锁聚合(增长链一经引发,迅速增长,反应一开始就生成相对分子量很高的聚合物,而转化率随反应进行逐步增加的聚合反应。
)2.1.3 实施方法:本项目拟采用乳液接枝共混法。
2.1.4 操作过程:采用间歇式操作。
2.2 聚合工艺条件2.2.1单体的选择:ABS树脂是丙烯晴--丁二烯--苯乙烯共聚物,其特性是由三组份的配比及每一种组分的化学结构,物理形态控制。
丙烯腈表现的特性是耐热性、耐化学性、刚性、抗拉强度;丁二烯表现的特性是抗冲击强度;苯乙烯表现的特性是加工流动性,光泽性。
这三组分的结合,优势互补,使ABS树脂具有优良的综合性能。
(1)1,3-丁二烯1,3-丁二烯通常简称丁二烯,结构式为CH2=CH-CH=CH2 。
一般以乙腈、二甲基甲酰胺为抽提剂,从约含40%丁二烯的裂解C4中抽提而得,也可以采用丁烯氧化脱氢或其他方法得到。
目前世界丁二烯的年生产能力约为7000kt,主要用于生产聚丁二烯、丁苯橡胶、丁苯树脂、SBS、ABS等高分子材料。
中国丁二烯年生产能力约为50余万吨,20世纪70年代初开发成功丁烯氧化脱氢法生产丁二烯。
目前主要采用乙烯装置副产C4馏分溶剂萃取精馏法生产丁二烯。
表3 不同温度下丁二烯的稳定贮存时间由于丁二烯具有上述性质,在运输、贮存和适用时必须采取严格的安全措施,绝氧、氮封。
装贮丁二烯的压力容器必须符合压力容器设计、制造、使用等一切规范,并经专门机构检验;丁二烯贮罐要有明显标志(即红色危险物品标志)并定期进行气密性试验,试压之前要用水蒸气清洗、氮气置换。
此外在蒸馏、加热、室温下长期贮存丁二烯时需加入一定量的阻聚剂,如叔丁基邻苯二酚、氢醌等,加入量一般为(100~2000)×10-6,丁二烯贮罐气相中的氧含量应<0.3%。
(2)苯乙烯苯乙烯结构式为C6H5CH=CH2,是不饱和芳烃中最简单、最重要的成员,属于带有烯烃侧链并与苯环形成共轭体系的单环芳烃,广泛用作生产苯乙烯系树脂和合成橡胶的原料,如GPPS、HIPS、ABS、SAN、SMA、SBR等。
目前世界苯乙烯产量已达1900万吨/年,90%以上都是通过乙苯催化脱氢制得,中国苯乙烯产量约为80万吨/年。
表5 工业用苯乙烯质量标准(3) 丙烯腈丙烯腈结构式为CH2=CHCN。
目前,世界总生产能力约为4870kt/a,其中90%采用Sohio 法,中国丙烯腈生产能力约为430kt/a。
丙烯腈在常温常压下,是一种具有苦杏仁气味的无色透明液体。
表6 丙烯腈的主要物理性质表7 工业用丙烯腈规格2.2.2引发剂的选择引发剂是乳液聚合配方的重要组成部分,引发剂种类和用量直接关系到反应速率。
聚合物乳液的稳定性及产品的质量。
因此正确选择引发剂也是进行乳液聚合配方设计很重要的问题。
根据反应体系不同可采用水溶性和油溶性引发剂也可按自由基生成机理选用热引发剂. 在ABS 合成中,常用的引发剂有:过氧化氢异丙苯、过硫酸钾和偶氮二异丁腈等。
乳液聚合所采用的大多是水溶性引发剂。
水溶性较好的一般为无机过氧化物。
例如过硫酸铵、过硫酸钾。
他们的使用温度是60~90ºС.在过硫酸盐中,以过硫酸钾为引发剂,所得乳液耐水性较好,所以使用最广泛。
过硫酸钾在水中溶解度最小(1.75%~5.3%),价格最低。
所以我们选用过硫酸钾作为引发剂。
引发剂用量一般控制为单体总量的0.1%~2%之间。
2.2.3 乳化剂的选择能使两种互不相溶的液体形成稳定乳液、既具有亲油性有具有亲水性(用HLB 值表示其亲水亲油性,数值越高表示其亲水性越强)的物质成为乳化剂。
在用乳液法合成聚丁二烯胶乳及其与苯乙烯和丙烯腈的接枝反应中,常用的乳化剂有:硬脂酸钾、油酸钾、松香酸钾、十二烷基苯磺酸钠、十二烷基硫酸钠等。
表9 合成ABS常用乳化剂性状综合上述乳化剂参数及其性状,选用油酸钾作乳化剂。
油酸钾是质量符合表10的油酸皂化而成。
工业品油酸(顺式十八碳-9-烯酸)是从黄色到红色的油状液体,有猪油气味。
当曝露于空气中时颜色能变深。
不溶于水,溶于酒精、乙醚及多种有机溶剂。
精制级油酸为无色透明,相对密度0.895(20℃),凝固点13.2℃,沸点286℃(13.1kPa),闪点372℃。
易燃,无毒。
表10 油酸的质量指标油酸钾的配制方法是在油酸中加入定量软水,在搅拌下加入定量KOH ,升温至70~80℃,皂化0.5~1h。
配制好的油酸钾规格为PH值11~13,浓度15%~20%。
2.2.4分散介质(溶剂)的选择能使物质分散于介质中的助剂称为分散剂,分散剂分为无机粉末和水溶性有机高分子两大类。
在ABS 合成中常用的分散剂有活性磷酸钙、聚乙烯醇和亚甲基二萘二磺酸钠等。
综合考虑,选用聚乙烯醇作分散剂。
表11 聚乙烯醇的质量指标2.2.5 终止剂的选择用于终止聚合反应的物质成为终止剂。
ABS 聚合时应用最普遍的终止剂是俗称福美钠的二甲基二硫代氨基甲酸钠(C 2H 6NCS 2Na)。
2.2.6分子量调节剂的选择 在生产聚合物过程中,为了避免聚合物分子量过高和过度支化,或因交联而引起的加工或成型困难,通常向聚合体系中加入分子量调节剂。
ABS 树脂合成中,一般使用叔十二碳硫醇作为分子量调节剂。
2.2.7抗氧剂的选择能延缓或阻止高分子材料氧化变质过程的物质称为抗氧剂。
使用它不但能保证高分子材料顺利进行加工,而且还可延长其使用寿命。