固体火箭发动机壳体用材料综述
T1000 级碳纤维及其复合材料研究与应用进展

摘要本文介绍了T1000 级碳纤维的发展历程,综述了T1000 级碳纤维及其复合材料的研究及应用情况,指出了国产T1000 级碳纤维应用研究需要关注的问题。
1引言碳纤维是一种碳元素组成占总质量90%以上,具有高强度、高模量、耐高温等优点的纤维材料。
最早可追溯至18 世纪的爱迪生和斯旺,1959年日本首先发明了聚丙烯腈(PAN)基碳纤维,而当下碳纤维的核心技术和产能被日本、美国以及一些欧洲发达国家和地区掌控。
T1000 级碳纤维作为碳纤维中的高端产品,在航空航天领域有着极大的用途。
高性能碳纤维的研究可以改善固体火箭发动机消极质量、提升载药量、提高质量比,对于先进武器的发展研究以及航天探索有重大意义。
目前国外已经大量使用T1000 级碳纤维的缠绕容器和固体火箭发动机壳体,因此开展国产T1000级碳纤维及其复合材料的应用研究迫在眉睫。
碳纤维的制备包括物理、化学、材料科学等多个领域的内容,总体分为纺丝原液的聚合、聚丙烯腈原丝的纺制、预氧化和碳化三个步骤,有众多因素需要调控。
根据缺陷理论和最弱连接理论,制备过程中产生的缺陷是影响碳纤维性能的主要因素,为保证碳纤维的性能,需要对每个工艺流程中工艺参数精准调控,由于加工过程中的各参数之间相互作用十分复杂,且目前一些工艺流程中的实际形成和演变机理不明,也使得高性能碳纤维,尤其是T1000 级碳纤维的研制有很大困难。
T1000 级碳纤维的研究主要包括碳纤维本身性能的研究、碳纤维复合材料的改性研究、碳纤维复合材料使用性能的研究几个方面。
由于T1000 级碳纤维本身的高性能、价格昂贵等原因,且国产T1000 级碳纤维还没有正式投入应用的报道,在实际应用方面主要介绍国外T1000 级碳纤维在航空航天以及其他领域的应用情况。
2T1000 级碳纤维性能研究现状1962 年正式开展PAN 基碳纤维的研制,1986 年研制出T1000G 碳纤维。
2014 年 3 月,通过碳化精细控制技术在纳米层级内控制纤维结构,成功研发出T1100G 碳纤维,2017 年 6 月强度由6600MPa 更新至7000MPa,目前东丽已完成了T1200 碳纤维的量产。
_固体火箭发动机结构

壳体强度试验
水压试验: Ph 1.1 ~ 1.25Pm
th 30s
用探伤仪检查表面疵病
用x光检查内部夹杂
2016/10/9
5.1.2 连接底设计
类型:平板、曲面
要求:①强度足够,质量轻 ②密封,隔热性能好 ③和战斗部、燃烧室壳体谅解同轴性好 ④结构工艺性好
dPm F 1 n d1b 2 4nb
M
h 3dPm 2nb 2
2016/10/9
三角形螺纹:h 0.325t b 0.875t
M 0.637
dPm nt dP 0.286 m nt dPm nt dP n 0.7 m t
σt
ri re
z
ri 2 p m re2 ri2
燃烧室壳体应力分布图
re ——燃烧室壳体外半径; K p p m50C K p =1.1~1.2 ——燃烧室计算压强, 其值 p m pm 1 Ab 0 0 1 n p m 50C p eqk 40C 1 30 p1 1 60 p 2
re 3 pm re ri 2
燃烧室壳体应力分布图
2016/10/9
(b)按薄壁筒
t
rav
min
pm
r pm
min
pm
忽略 r
re re pm 2 pm / 2 2.3 pm 2 / 3 pm
1 3 2 1——连接底;2——壳体;3——后封头
2016/10/9
焊接结构
1
2
3
1——连接底;2——壳体;3——后封头
微型固体火箭发动机壳体模态分析

地 面试验证 明能够满足强度 要求 , 在飞行试 验 中均 出现 但
图 8 7阶 自振 模 态
过发动机熄火和爆炸 。
管质量对壳体 的影 响 。由于微 型固体 火箭 发动 机推进 剂
燃烧 时间很短 , 以忽略推进剂燃烧产 生的热载荷 。 所
2 3 壳体模态的 P / ehnc 计算 求解 . o r M ca i a 由于所选 择 的微型 固体火 箭发 动机 壳体 前后 均与其
的 Mehnc 模块在应用 范 围、业有 限元 分析 软件 , 但其 建模 功能 强 , 完成一 些 趋势分析方便快捷 。用 PoE g er 立的发动机 三维模 r ni e建 / n
型如 图 l 所示 。
他部件连接 , 其两端 的模 态受到抑 制。但壳体 侧部 的振 动 将极 大地 影 响壳体 与 药柱 的强 度 , 不稳 定燃 烧 的激励 在
豢 收稿 日期 :00— 3—1 21 0 4 作 者简介 : 吕忠波 (9 4 ) 男 , 16 一 , 高级 工程 师 , 主要从事枪械 、 弹药质量工作研究 。
图 2 1阶 自振 模 态
图 5 4阶 自振 模 态
图 3 2阶 自 模 态 振
图 5 5阶 自振 模 态
图 4 3阶 自振 模 态
图 7 5阶 自 模 态 振
3 8
四 川 兵 工 学 报
3 结 果 分 析
推进剂 的燃 烧波 动会 造成燃 烧室 即发 动机壳 体 内的 压力波动 , 这种压 力波 动会 成为发 动机 壳体 振动激 励 , 而 发动机壳体 的振 动会 引起 推进剂燃烧 的更大波 动 , 如此循
火箭发动机壳体结构
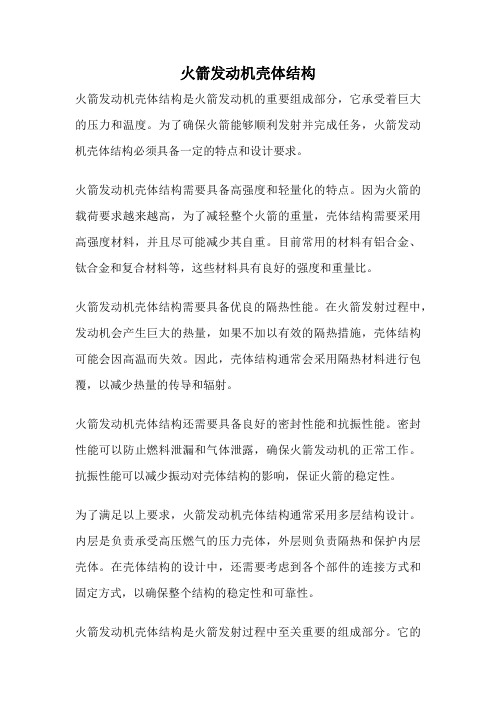
火箭发动机壳体结构
火箭发动机壳体结构是火箭发动机的重要组成部分,它承受着巨大的压力和温度。
为了确保火箭能够顺利发射并完成任务,火箭发动机壳体结构必须具备一定的特点和设计要求。
火箭发动机壳体结构需要具备高强度和轻量化的特点。
因为火箭的载荷要求越来越高,为了减轻整个火箭的重量,壳体结构需要采用高强度材料,并且尽可能减少其自重。
目前常用的材料有铝合金、钛合金和复合材料等,这些材料具有良好的强度和重量比。
火箭发动机壳体结构需要具备优良的隔热性能。
在火箭发射过程中,发动机会产生巨大的热量,如果不加以有效的隔热措施,壳体结构可能会因高温而失效。
因此,壳体结构通常会采用隔热材料进行包覆,以减少热量的传导和辐射。
火箭发动机壳体结构还需要具备良好的密封性能和抗振性能。
密封性能可以防止燃料泄漏和气体泄露,确保火箭发动机的正常工作。
抗振性能可以减少振动对壳体结构的影响,保证火箭的稳定性。
为了满足以上要求,火箭发动机壳体结构通常采用多层结构设计。
内层是负责承受高压燃气的压力壳体,外层则负责隔热和保护内层壳体。
在壳体结构的设计中,还需要考虑到各个部件的连接方式和固定方式,以确保整个结构的稳定性和可靠性。
火箭发动机壳体结构是火箭发射过程中至关重要的组成部分。
它的
设计要求必须满足高强度、轻量化、隔热性能、密封性能和抗振性能等要求。
只有在满足这些要求的前提下,火箭发动机才能够安全可靠地发射,并成功完成任务。
固体发动机复合材料壳体成型技术介绍
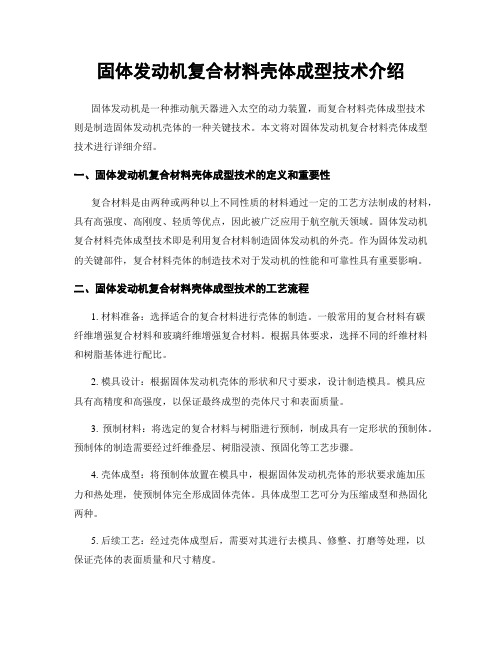
固体发动机复合材料壳体成型技术介绍固体发动机是一种推动航天器进入太空的动力装置,而复合材料壳体成型技术则是制造固体发动机壳体的一种关键技术。
本文将对固体发动机复合材料壳体成型技术进行详细介绍。
一、固体发动机复合材料壳体成型技术的定义和重要性复合材料是由两种或两种以上不同性质的材料通过一定的工艺方法制成的材料,具有高强度、高刚度、轻质等优点,因此被广泛应用于航空航天领域。
固体发动机复合材料壳体成型技术即是利用复合材料制造固体发动机的外壳。
作为固体发动机的关键部件,复合材料壳体的制造技术对于发动机的性能和可靠性具有重要影响。
二、固体发动机复合材料壳体成型技术的工艺流程1. 材料准备:选择适合的复合材料进行壳体的制造。
一般常用的复合材料有碳纤维增强复合材料和玻璃纤维增强复合材料。
根据具体要求,选择不同的纤维材料和树脂基体进行配比。
2. 模具设计:根据固体发动机壳体的形状和尺寸要求,设计制造模具。
模具应具有高精度和高强度,以保证最终成型的壳体尺寸和表面质量。
3. 预制材料:将选定的复合材料与树脂进行预制,制成具有一定形状的预制体。
预制体的制造需要经过纤维叠层、树脂浸渍、预固化等工艺步骤。
4. 壳体成型:将预制体放置在模具中,根据固体发动机壳体的形状要求施加压力和热处理,使预制体完全形成固体壳体。
具体成型工艺可分为压缩成型和热固化两种。
5. 后续工艺:经过壳体成型后,需要对其进行去模具、修整、打磨等处理,以保证壳体的表面质量和尺寸精度。
三、固体发动机复合材料壳体成型技术的优势1. 高强度和高刚度:复合材料具有较高的强度和刚度,能够承受更高的压力和负荷,提高发动机的性能和可靠性。
2. 轻量化设计:相比于传统的金属材料,复合材料具有较低的密度,可以实现固体发动机的轻量化设计,减轻整个航天器的重量,提高有效载荷。
3. 耐高温性能:固体发动机在工作过程中会产生高温,复合材料具有较好的耐高温性能,能够承受高温环境下的工作条件。
固体发动机 成分

固体发动机成分
固体发动机是一种使用固体推进剂作为动力源的发动机,广泛应用于导弹、火箭、航天器等领域。
固体发动机的成分主要包括固体推进剂、壳体、点火装置等。
其中,固体推进剂是固体发动机的核心成分,由多种材料组成,包括燃料、氧化剂、粘合剂、稳定剂、增塑剂等。
燃料是推进剂的主要成分,常用的有铝粉、镁粉、硼粉等,它们能够提供推进剂所需的能量。
氧化剂则是与燃料反应产生能量的物质,常用的有硝酸铵、高氯酸铵等。
粘合剂则用于将燃料和氧化剂粘结在一起,形成一个整体,常用的有聚氨酯、聚丁二烯等。
稳定剂和增塑剂则用于调节推进剂的性能,如改善其机械性能、延长其储存寿命等。
壳体是固体发动机的主要承受力部件,一般由高强度、高刚度的金属材料制成,如钢、铝合金等。
壳体的作用是保护固体推进剂,防止其在工作过程中受到破坏,并将推进剂产生的推力传递给导弹或火箭等载具。
点火装置是固体发动机的重要组成部分,用于点燃固体推进剂。
点火装置通常由点火药、点火器、传火管等组成。
当点火指令发出时,点火药被点燃,产生高温高压火焰,通过传火管将火焰传递到固体推进剂中,从而点燃推进剂。
总之,固体发动机的成分复杂多样,每种成分都扮演着重要的角色。
通过合理的配方和工艺设计,可以制造出性能稳定、可靠的固体发动机,为导弹、火箭等载具提供强大的动力支持。
双脉冲火箭发动机设计文献综述

---------------------------------------------------------------范文最新推荐------------------------------------------------------ 双脉冲火箭发动机设计+文献综述摘要20世纪50年代,固体火箭在技术上取得突破,并广泛应用于弹道导弹和运载火箭。
20世纪60年代起,国外在可控推力固体火箭发动机的理论和实验研究方面作了大量的工作,探索出了很多技术途径和设计方案。
固体火箭发动机具有使用安全性好、可靠性高、储存性能好、密度比冲高及勤务处理方便等优点,使其在战略、战术导弹武器领域内成为主要的动力装臵。
脉冲固体火箭发动机是兴起于20世纪末期的新型固体火箭发动机,它的出现为推进系统的发展开辟了新的发展方向,在航天和军事领域都有着潜在的应用价值。
本论文主要研究双脉冲火箭发动机总体结构、装药结构设计、燃烧室设计、喷管设计、点火装臵设计以及内弹道计算。
通过对双脉冲固体火箭发动机的设计了解了双脉冲固体火箭发动机的结构以及关键技术,为研制高性能固体火箭发动机奠定坚实的基础。
60131 / 16关键词脉冲固体火箭发动机动力装臵总体结构装药结构毕业设计说明书(论文)外文摘要TitleDouble Pulse Solid Rocket Motor DesignAbstractIn the 1950's, the solid rocket breakthrough a lot in the technical field , and the solid rocket motor are widely used in ballistic missiles and launch vehicles. In the 1960's, the foreign countries made a great mass of works in theoretical and experimental studies of controllable thrust solid rocket motor to explore a lot of technical approaches and designs. Solid rocket motor with the advantage of security, reliability, and storage performance density than the ascribed and service processing advantages of convenience, it become a major power plant in the strategic field of tactical missiles weapons. Pulse solid rocket motor is a new type of solid rocket motor which risen in the late 20th century, its---------------------------------------------------------------范文最新推荐------------------------------------------------------propulsion system development has opened a new direction of development, have potential applications in the aerospace and military fields. This paper mainly studies the dual-pulse rocket engine general structure, propellant structure design, the combustion chamber design, nozzle design, the ignition system design and interior ballistic calculation. The purpose of designing dual-pulse solid rocket motor is to understand the structure and key technology of dual-pulse solid rocket motor, and lay a solid foundation for the development of high-performance solid rocket motor.4.7燃烧室的强度校核255发动机喷管设计265.1喷管的型面设计265.2喷管壁厚273 / 165.3喷管的热防护276点火装臵的设计296.1点火药的选择296.2点火药量的计算296.3点火药盒设计307内弹道的计算317.1内弹道计算的基本方程31 7.2四阶龙格-库塔法介绍31 7.3计算步骤327.4曲线绘制33结论35---------------------------------------------------------------范文最新推荐------------------------------------------------------ 致谢36参考文献371绪论1.1课题的研究背景20世纪50年代,固体火箭在技术上取得突破,并广泛应用于弹道导弹和运载火箭。
固体火箭发动机的结构设计

固体火箭发动机的结构设计首先是推进剂。
固体火箭发动机的推进剂一般采用固态燃料,其中主要成分是氧化剂和燃料。
氧化剂常用的有硝酸铵(AN)和高氯酸铵(HTPB),燃料常用的有铝粉、甲醇和己烷等。
推进剂的选择应根据任务需求和性能要求进行,并考虑安全性、稳定性和可靠性等因素。
其次是燃烧室。
燃烧室是推进剂燃烧的空间,它的设计需要考虑燃烧效率、压力和温度等因素。
燃烧室一般采用圆柱形,其内壁通常采用耐高温和耐腐蚀的材料,例如不锈钢或陶瓷材料,以保证燃烧室的工作寿命。
然后是喷管。
喷管是固体火箭发动机排放高温高压燃气的出口,其结构设计对于发动机的推力性能和效率影响较大。
喷管一般采用膨胀马赫数为2-3的衔接形状,以提高燃气的出口速度。
喷管的材料需要具有耐高温和耐腐蚀性能,并且需要考虑喷管的冷却问题,常见的冷却方式有内冷却和外冷却等。
最后是推进剂注入装置。
推进剂注入装置主要负责将推进剂输送到燃烧室中进行燃烧。
注入装置一般由推进剂储存器、进气阀门、控制系统等组成。
在设计时需要考虑推进剂的供给能力、工作可靠性和安全性等因素,并配备相应的控制系统,确保推进剂在燃烧室中的喷射量和速度的准确控制。
除了上述几个关键部分,固体火箭发动机的结构设计还需考虑整体的重量、尺寸和结构强度等因素。
例如,为了减轻整机重量,可以采用轻质材料制造发动机壳体,同时提高材料的强度;为了提高结构强度和耐振性能,可以采用复合材料或金属层合材料制造壳体,并进行合理的人工振动试验和计算分析。
总的来说,固体火箭发动机的结构设计需要综合考虑推进剂的选择、燃烧室、喷管以及推进剂注入装置等关键部分,以实现火箭的高效推力、稳定燃烧和可靠使用。
同时,还需要考虑发动机的重量、尺寸和结构强度等因素,以提高整体性能和安全性。
在实际应用中,还需要根据具体任务需求进行细化设计和实验验证。
固体火箭发动机壳体用材料综述
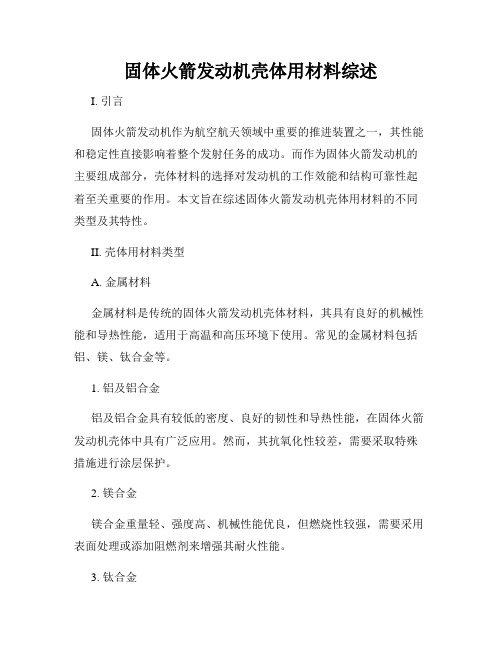
固体火箭发动机壳体用材料综述I. 引言固体火箭发动机作为航空航天领域中重要的推进装置之一,其性能和稳定性直接影响着整个发射任务的成功。
而作为固体火箭发动机的主要组成部分,壳体材料的选择对发动机的工作效能和结构可靠性起着至关重要的作用。
本文旨在综述固体火箭发动机壳体用材料的不同类型及其特性。
II. 壳体用材料类型A. 金属材料金属材料是传统的固体火箭发动机壳体材料,其具有良好的机械性能和导热性能,适用于高温和高压环境下使用。
常见的金属材料包括铝、镁、钛合金等。
1. 铝及铝合金铝及铝合金具有较低的密度、良好的韧性和导热性能,在固体火箭发动机壳体中具有广泛应用。
然而,其抗氧化性较差,需要采取特殊措施进行涂层保护。
2. 镁合金镁合金重量轻、强度高、机械性能优良,但燃烧性较强,需要采用表面处理或添加阻燃剂来增强其耐火性能。
3. 钛合金钛合金具有较高的强度、密度较低、抗氧化性能好等特点,是固体火箭发动机壳体中理想的材料之一。
然而,其造价较高,在使用过程中需要更加严格的控制和管理。
B. 复合材料复合材料是近年来在固体火箭发动机壳体材料中得到广泛应用的新兴材料,其具有良好的强度、刚度和耐火性能。
1. 碳纤维增强复合材料碳纤维增强复合材料具有极高的比强度和刚度,同时重量轻、耐腐蚀性好,逐渐成为固体火箭发动机壳体的理想选择。
然而,其制造工艺和成本较高。
2. 玻璃纤维增强复合材料玻璃纤维增强复合材料具有良好的耐火性能和机械性能,广泛应用于不同温度范围的固体火箭发动机壳体中。
然而,其比强度和刚度较低。
3. 陶瓷基复合材料陶瓷基复合材料以陶瓷为基体,在增强材料的加持下具有良好的高温和耐火性能,能够适应极端的工作环境和高温条件。
III. 壳体用材料特性A. 密度和强度发动机壳体材料的密度和强度直接影响着发动机的质量和结构强度。
因此,在材料选择时,需要权衡不同材料的密度和强度比。
B. 耐火性能固体火箭发动机在工作过程中会产生极高的温度,因此壳体材料需要具备良好的耐火性能,能够承受高温环境下的长时间工作。
30Cr3SiNiMoVA高强钢
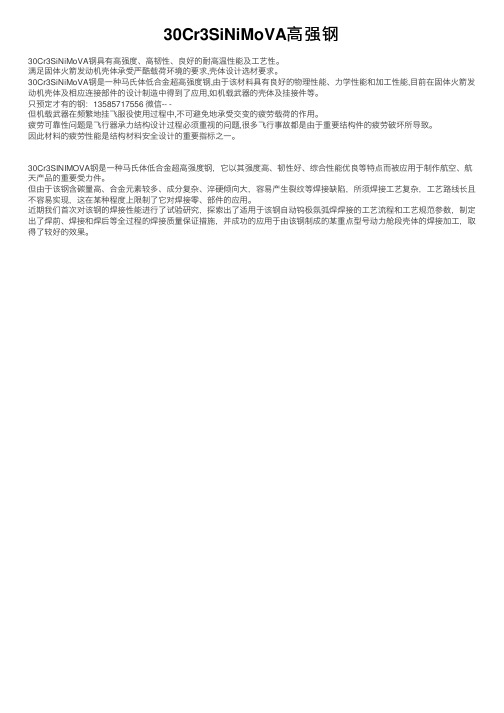
30Cr3SiNiMoVA⾼强钢
30Cr3SiNiMoVA钢具有⾼强度、⾼韧性、良好的耐⾼温性能及⼯艺性。
满⾜固体⽕箭发动机壳体承受严酷载荷环境的要求,壳体设计选材要求。
30Cr3SiNiMoVA钢是⼀种马⽒体低合⾦超⾼强度钢,由于该材料具有良好的物理性能、⼒学性能和加⼯性能,⽬前在固体⽕箭发动机壳体及相应连接部件的设计制造中得到了应⽤,如机载武器的壳体及挂接件等。
只预定才有的钢:135****7556微信-- -
但机载武器在频繁地挂飞服役使⽤过程中,不可避免地承受交变的疲劳载荷的作⽤。
疲劳可靠性问题是飞⾏器承⼒结构设计过程必须重视的问题,很多飞⾏事故都是由于重要结构件的疲劳破坏所导致。
因此材料的疲劳性能是结构材料安全设计的重要指标之⼀。
30Cr3SINIMOVA钢是⼀种马⽒体低合⾦超⾼强度钢,它以其强度⾼、韧性好、综合性能优良等特点⽽被应⽤于制作航空、航天产品的重要受⼒件。
但由于该钢含碳量⾼、合⾦元素较多、成分复杂、淬硬倾向⼤,容易产⽣裂纹等焊接缺陷,所须焊接⼯艺复杂,⼯艺路线长且不容易实现,这在某种程度上限制了它对焊接零、部件的应⽤。
近期我们⾸次对该钢的焊接性能进⾏了试验研究,探索出了适⽤于该钢⾃动钨极氛弧焊焊接的⼯艺流程和⼯艺规范参数,制定出了焊前、焊接和焊后等全过程的焊接质量保证措施,并成功的应⽤于由该钢制成的某重点型号动⼒舱段壳体的焊接加⼯,取得了较好的效果。
一种智能固体火箭发动机复合材料壳体的制作方法

一种智能固体火箭发动机复合材料壳体的制作方法智能固体火箭发动机是一种具有高可靠性和高性能的发动机。
它由复合材料壳体、内胆、推进剂、点火装置、推力控制系统等组成。
本文将重点介绍一种智能固体火箭发动机复合材料壳体的制作方法。
第一步:设计壳体结构在制作智能固体火箭发动机的壳体之前,首先需要进行结构设计。
设计要考虑到壳体的强度、重量和材料选择等因素。
设计师需要使用计算机辅助设计(CAD)软件进行模拟和分析,以确保壳体能够承受高温、高压和高速流动环境下的工作。
第二步:选择合适的材料复合材料在航天领域具有广泛应用,因为它具有高强度、低密度、抗腐蚀和耐高温等优点。
对于智能固体火箭发动机的壳体制作,常用的复合材料包括碳纤维增强复合材料(CFRP)和玻璃纤维增强复合材料(GFRP)。
根据设计要求和性能需求,选择合适的复合材料进行制作。
第三步:制作壳体制作壳体的主要步骤包括模具制作、预制件制作、层叠和硬化等。
1.模具制作:首先需要制作出适应壳体外形的模具。
模具可以采用金属或者树脂材料制作,具体选择取决于设计要求和制作工艺。
2.预制件制作:根据模具的形状,制作合适尺寸的预制件。
预制件可以采用预浸料或预浸织物的方式,将纤维和基体材料预先组合形成。
3.层叠:将预制件一层一层叠放在模具上,根据设计要求确保纤维的方向和层数等参数。
在层叠过程中,需要注意防止气泡和纤维错位等问题。
4.硬化:将层叠好的预制件放入烤箱或采用热压工艺进行硬化。
硬化过程中,树脂基体会固化,预制件与壳体结合形成一个整体。
第四步:加工和检测制作完壳体后,还需要进行加工和检测,以确保壳体的质量和性能。
1.加工:根据设计要求和壳体成品的尺寸,采用机械加工或手工修整等方式对壳体进行去毛边、打磨和修整等处理,使得壳体表面平整光滑。
2.检测:采用非破坏性检测方法,如超声波检测、X射线检测和红外热像检测等,对壳体进行质量检测。
这些检测方法可以发现壳体中的缺陷并排除,确保壳体的完整性和可靠性。
碳纤维/环氧固体火箭发动机壳体补强现状

壳体内压性能 的因素 , 介绍 了当前在碳 纤维/ 环氧树脂复合材料 壳体 补强方 面的主要工 作和不 足之处 , 并指 出今后
受 内压 强外 , 还要 承受 来 自全 弹 的轴 压 、 曲 、 转 弯 扭
突破 , 的 比强度 、 它 比模 量 跃居 各先 进纤 维之 首 。 固
体火箭发动机壳 体要求 复合材料具有高 的比强度、
比模 量 和 断裂应 变 。拉 伸模 量 为 (6 25—30 G a拉 2) P, 伸 强度 在 5 P 左 右 , Ga 断裂 延 伸 率 约 为 17 的高 强 .% 中模 碳 纤维 是理 想 的壳 体 增 强 材 料 , 因而 近 年 来 各 国都 在 大力 开发 高强 中模 碳 纤 维 , 1 出 了几 种 表 列 典 型 的航 天用 高强 中模碳 纤 维性 能 。
补 封头强 度 不足 。
的( . — .) , 13 14倍 可使壳体重量再度减轻 3 %左右 , 0 使 发 动机 质量 比高达 09 .3以上 。如 美 国最 新 的 “ 三 叉戟 Ⅱ( 5 ” 弹 的 第 工、 C )导 Ⅱ级 壳 体 及 “ 儒 ” 弹 侏 导 的第 1、 Ⅲ级壳体均采用 I 7 Ⅱ、 M 碳纤维/ 环氧复合 材料 。
维普资讯
第 3期
20 08年 9 月
纤
维
复
合
材
料
N 3 o. 3 5
FI BER C0 Ⅱ, S玎【 o 1 S
S p. 2 0 e ,O 8
详解固体火箭发动机

详解固体火箭发动机控制了太空,谁就控制了地球!谁控制了太空,谁就控制了未来!固体火箭发动机属于化学火箭发动机,用固态物质(能源和工质)作为推进剂。
固体推进剂点燃后在燃烧室中燃烧,产生高温高压的燃气,即把化学能转化为热能;燃气经喷管膨胀加速,热能转化为动能,以极高的速度从喷管排出从而产生推力推动导弹向前飞行。
固体火箭发动机主要由壳体、固体推进剂、喷管组件、点火装置等四部分组成,其中固体推进剂配方及成型工艺、喷管设计及采用材料与制造工艺、壳体材料及制造工艺是最为关键的环节,直接影响固体发动机的性能。
固体推进剂配方各种组分的混合物可以用压伸成型工艺预制成药柱再装填到壳体内,也可以直接在壳体内进行贴壁浇铸。
壳体直接用作燃烧室。
喷管用于超音速排出燃气,产生推力;喷管组件还要有推力矢量控制(TVC)系统来控制导弹的飞行姿势。
点火装置在点火指令控制下解除安全保险并点燃发火药产生高温高压火焰用于点燃壳体内的推进剂。
固体发动机的水平与复合材料工业和高分子化学材料工业的科技水平密不可分,可以说是一个国家科技水平的缩影。
固体火箭发动机结构图(潜入式全轴柔性摆动喷管)中、远程以上的固体弹道导弹通常由两级以上火箭发动机和前端系统(包括仪器舱、弹头、整流罩等)构成。
为了给弹头提供较为精确的关机点速度,有些末级固体发动机(如美国的民兵3导弹的第三级和我国巨浪-1的第二级)的前封头装有推力终止装置,接到关机指令,推力终止孔打开进行反向喷射,燃烧室迅速泄压,火焰熄灭,推力也就终止了,同时反向喷射提供了末级分离的推力;先进的弹道导弹(如美国的三叉戟C4/D5,法国的M4/M45/M51)则采用优化控制飞行弹道和姿势(即所谓能量管理)使推进剂耗尽关机的方法。
分导式多弹头(MIRV)导弹除多个主级发动机外还有一个末助推级(PBV,又称弹头母舱,由姿控系统、仪器舱及弹头支承/释放平台构成,一些先进单弹头导弹也有PBV),姿控发动机精确调整速度和姿势并逐个投放多弹头和诱饵对多个目标实施打击。
固体火箭超燃冲压发动机结构
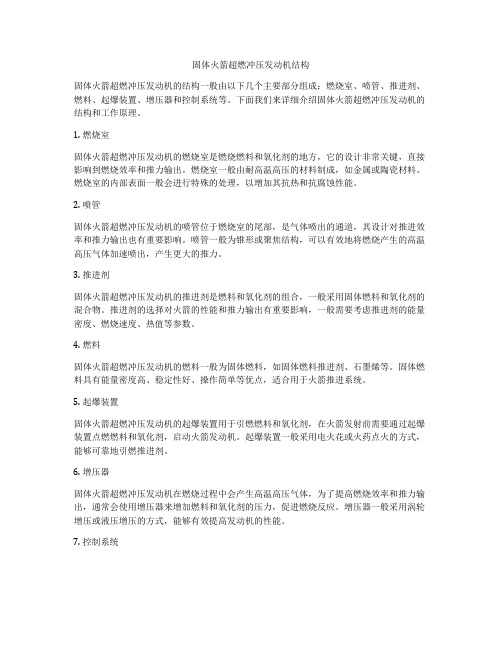
固体火箭超燃冲压发动机结构固体火箭超燃冲压发动机的结构一般由以下几个主要部分组成:燃烧室、喷管、推进剂、燃料、起爆装置、增压器和控制系统等。
下面我们来详细介绍固体火箭超燃冲压发动机的结构和工作原理。
1. 燃烧室固体火箭超燃冲压发动机的燃烧室是燃烧燃料和氧化剂的地方,它的设计非常关键,直接影响到燃烧效率和推力输出。
燃烧室一般由耐高温高压的材料制成,如金属或陶瓷材料。
燃烧室的内部表面一般会进行特殊的处理,以增加其抗热和抗腐蚀性能。
2. 喷管固体火箭超燃冲压发动机的喷管位于燃烧室的尾部,是气体喷出的通道,其设计对推进效率和推力输出也有重要影响。
喷管一般为锥形或聚焦结构,可以有效地将燃烧产生的高温高压气体加速喷出,产生更大的推力。
3. 推进剂固体火箭超燃冲压发动机的推进剂是燃料和氧化剂的组合,一般采用固体燃料和氧化剂的混合物。
推进剂的选择对火箭的性能和推力输出有重要影响,一般需要考虑推进剂的能量密度、燃烧速度、热值等参数。
4. 燃料固体火箭超燃冲压发动机的燃料一般为固体燃料,如固体燃料推进剂、石墨烯等。
固体燃料具有能量密度高、稳定性好、操作简单等优点,适合用于火箭推进系统。
5. 起爆装置固体火箭超燃冲压发动机的起爆装置用于引燃燃料和氧化剂,在火箭发射前需要通过起爆装置点燃燃料和氧化剂,启动火箭发动机。
起爆装置一般采用电火花或火药点火的方式,能够可靠地引燃推进剂。
6. 增压器固体火箭超燃冲压发动机在燃烧过程中会产生高温高压气体,为了提高燃烧效率和推力输出,通常会使用增压器来增加燃料和氧化剂的压力,促进燃烧反应。
增压器一般采用涡轮增压或液压增压的方式,能够有效提高发动机的性能。
7. 控制系统固体火箭超燃冲压发动机的控制系统用于监测和控制发动机的工作状态,根据需要调节推力输出和燃烧效率。
控制系统包括传感器、执行器、控制器等部分,能够确保发动机的正常运行和安全性。
综上所述,固体火箭超燃冲压发动机是一种高效推进系统,其结构复杂,但在现代航天领域有着重要的应用价值。
固体火箭发动机综述

固体火箭发动机综述
固体火箭发动机(solid rocket motor 简称:SRM)是指使用固体推进剂的化学火箭发动机,又称固体推进剂火箭发动机。
它由药柱、燃烧室、喷管和点火装置等部件组成。
按照燃烧室的结构形式,固体火箭发动机分为整体式固体发动机和分段式固体发动机等类型。
与液体火箭发动机相比较,固体火箭发动机具有结构简单,推进剂密度大,推进剂可以储存在燃烧室中常备待用和操纵方便可靠等优点。
因此,固体火箭发动机主要用作火箭弹,导弹和探空火箭的发动机,以及航天器发射和飞机起飞的助推发动机。
固体火箭发动机的优点包括:结构简单,没有复杂的燃料输送和贮存系统,部件较少,故障率相对较低;贮存和安全性好,固体燃料易于存储,不易泄漏,且具有较好的安全性,适合长期贮存;机动性好,固体火箭发动机推力大,响应速度快,适用于需要快速加速和变轨的场合,如军事导弹;制造工艺相对简单,固体火箭发动机的制造工艺相对简单,成本较低。
固体火箭发动机的缺点包括:比冲较低,固体燃料的能量密度一般低于液体燃料,导致发动机的推力效率较低;燃烧延续时间短,不适用于需要长时间推力的任务;燃料质量大,固体燃料的质量较大,限制了火箭的载荷能力;无法停机,一旦固体火箭发动机点燃,就无法在没有耗尽燃料的情况下停止工作,这对控制火箭的飞行轨迹带来挑战。
每种发动机技术的发展都符合其特定的应用需求和时代背景,随着技术的进步,这些发动机的性能也在不断提升和完善。
固体火箭发动机壳体用材料综述

固体火箭发动机壳体用材料综述固体火箭发动机是一种常见的火箭发动机类型,常用于航天器和导弹等航空航天应用中。
固体火箭发动机壳体作为发动机的重要部件,承受着高温、高压和高载荷等极端环境下的力学和热学应力。
因此,选用合适的材料对于固体火箭发动机壳体的性能和可靠性至关重要。
本文将对固体火箭发动机壳体材料的种类和特性进行综述。
铝合金是常用的壳体材料之一,具有良好的可加工性和强度。
常用的铝合金有2XXX、5XXX和7XXX系列等。
2XXX系列铝合金具有较高的强度,并有一定的抗热应力能力。
5XXX系列铝合金除具有较高的强度外,还具有良好的抗腐蚀性能。
7XXX系列铝合金是强度最高的铝合金,但在高温下会发生时效硬化。
镍基合金是一种耐高温合金,具有良好的耐热、抗氧化和抗蠕变性能。
常用的镍基合金有Inconel 718、Waspaloy和Hastelloy X等。
这些合金在高温下具有良好的力学性能和耐热性能,适合用于固体火箭发动机壳体。
钛合金是一种低密度、高强度的金属材料,具有良好的耐腐蚀性能和抗热应力能力。
常见的钛合金有Ti-6Al-4V、Ti-6Al-2Sn-4Zr-6Mo等。
这些合金在航空航天领域中被广泛应用,适合用于制造固体火箭发动机壳体。
复合材料由纤维增强树脂基体组成,具有优异的力学性能和轻质化特点。
常见的复合材料包括碳纤维增强复合材料、玻璃纤维增强复合材料和芳纶纤维增强复合材料等。
这些复合材料在轻质化和抗热性能方面具有显著优势,但在工艺性和成本方面存在一定的挑战。
高温陶瓷材料具有出色的耐火性、抗热震性和高强度等特点。
常见的高温陶瓷材料包括碳化硅(SiC)、氮化硅(Si3N4)和氧化铝(Al2O3)等。
这些材料在高温下具有稳定的力学性能和抗热性能,适合用于固体火箭发动机壳体。
综上所述,固体火箭发动机壳体材料的选用需要综合考虑力学性能、耐热性能、耐腐蚀性能和轻质化等因素。
不同材料具有各自的优点和适用范围,选择合适的材料对于提高固体火箭发动机的可靠性和性能至关重要。
火箭发动机的分类和特点

火箭发动机的分类和特点现代火箭发动机主要分固体推进剂和液体推进剂发动机。
所谓“推进剂”就是燃料(燃烧剂)加氧化剂的合称。
一、固体火箭发动机固体火箭发动机为使用固体推进剂的化学火箭发动机。
固体推进剂有聚氨酯、聚丁二烯、端羟基聚丁二烯、硝酸酯增塑聚醚等。
固体火箭发动机由药柱、燃烧室、喷管组件和点火装置等组成。
药柱是由推进剂与少量添加剂制成的中空圆柱体(中空部分为燃烧面,其横截面形状有圆形、星形等)。
药柱置于燃烧室(一般即为发动机壳体)中。
在推进剂燃烧时,燃烧室须承受2500~3500度的高温和102~2×107帕的高压力,所以须用高强度合金钢、钛合金或复合材料制造,并在药柱与燃烧内壁间装备隔热衬。
点火装置用于点燃药柱,通常由电发火管和火药盒(装黑火药或烟火剂)组成。
通电后由电热丝点燃黑火药,再由黑火药点火燃药拄。
喷管除使燃气膨胀加速产生推力外,为了控制推力方向,常与推力向量控制系统组成喷管组件。
该系统能改变燃气喷射角度,从而实现推力方向的改变。
药柱燃烧完毕,发动机便停止工作。
固体火箭发动机与液体火箭发动机相比较,具有结构简单,推进剂密度大,推进剂可以储存在燃烧到中常备待用和操纵方便可靠等优点。
缺点是“比冲”小(也叫比推力,是发动机推力与每秒消耗推进剂重量的比值,单位为秒)。
固体火箭发动机比冲在250~300秒,工作时间短,加速度大导致推力不易控制,重复起动困难,从而不利于载人飞行。
固体火箭发动机主要用作火箭弹、导弹和探空火箭的发动机,以及航天器发射和飞机起飞的助推发动机。
二、液体火箭发动机液体火箭发动机是指液体推进剂的化学火箭发动机。
常用的液体氧化剂有液态氧、四氧化二氮等,燃烧剂由液氢、偏二甲肼、煤油等。
氧化剂和燃烧剂必须储存在不同的储箱中。
液体火箭发动机一般由推力室、推进剂供应系统、发动机控制系统组成。
推力室是将液体推进剂的化学能转变成推进力的重要组件。
它由推进剂喷嘴、燃烧室、喷管组件等组成,见图。
- 1、下载文档前请自行甄别文档内容的完整性,平台不提供额外的编辑、内容补充、找答案等附加服务。
- 2、"仅部分预览"的文档,不可在线预览部分如存在完整性等问题,可反馈申请退款(可完整预览的文档不适用该条件!)。
- 3、如文档侵犯您的权益,请联系客服反馈,我们会尽快为您处理(人工客服工作时间:9:00-18:30)。
固体火箭发动机壳体用材料综述摘要:概述了国内外固体火箭发动机壳体用先进复合材料研究应用现状,同时对固体火箭发动机壳体的纤维缠绕成型工艺进行了阐述。
关键词:固体火箭发动机复合材料树脂基体纤维缠绕成型1 固体火箭发动机简介固体火箭发动机是当今各种导弹武器的主要动力装置,在航空航天领域也有相当广泛的应用。
它的特点是结构简单,因而具有机动、可靠、易于维护等一系列优点,非常适合现代化战争和航天事业的需要。
但固体火箭发动机部件在工作中要承受高温、高压和化学气氛下的各种复杂载荷作用,因此其材料通常具有极优异的性能,往往代表着当代材料科学的最先进水平。
标志当代高性能固体发动机的主要特征是:“高能、轻质、可控”,这三者都是以先进材料为基础和支柱的,选用具有优良比强度和卓越耐热性能的先进复合材料已成为提高发动机性能的一项决定性因素。
2 固体火箭发动机壳体用材料固体火箭发动机壳体既是推进剂贮箱又是燃烧室,同时还是火箭或导弹的弹体,因此,在进行发动机壳体材料设计时,应考虑如下几个基本原则[1]:a. 固体火箭发动机壳体就其工作方式来讲,是一个内压容器,所以壳体承受内压的能力是衡量其技术水平的首要指标;b. 发动机壳体是导弹整体结构的一部分,所以又要求壳体具有适当结构刚度;c. 作为航天产品,不仅要求结构强度高,而且要求材料密度小;d. 发动机点火工作时,壳体将受到来自内部燃气的加热,而壳体结构材料,尤其是壳体结构复合材料的强度对温度的敏感性较强,所以,在设计壳体结构材料时,不能仅限于其常温力学性能,而应充分考虑其在发动机工作过程中,可能遇到的温度范围内的全面性能。
评价和鉴定壳体材料的性能水平,固然要以最终产品是否满足使用要求为原则,但从设计选材的角度来说,也应有衡量的指标和尺度。
60年代以前一直沿用航空材料常用的比强度和比模量作为主要衡量指标。
70年代以后,考虑到固体发动机是一种高压容器,选用反映材料容器效率的容器特性系数PV/W 作为衡量指标。
目前为止,发动机壳体材料大体经历了四代发展过程,第一代为金属材料;第二代为玻璃纤维复合材料;第三代为有机芳纶复合材料;第四代为高强中模碳纤维复合材料。
2.1金属材料金属材料是最早应用的固体火箭发动机壳体材料,其中主要是低合金钢。
其优点是成本低、工艺成熟、便于大批量生产,特别是后来在断裂韧性方面有了重大突破,因此即便新型复合材料发展迅速,但在质量比要求不十分苛刻的发动机上仍大量使用。
从容器特性系数PV/W来看,金属材料壳体的特性系数都很低,超高强度钢通常为5km~8km,钛合金也只有7km~11km,远不能满足先进固体发动机的要求,因此壳体复合材料化将是大势所趋。
2.2纤维缠绕复合材料利用纤维缠绕工艺制造固体发动机壳体是近代复合材料发展史上的一个重要里程碑。
这种缠绕制品除了具有复合材料共有的优点外,由于缠绕结构的方向强度比可根据结构要求而定,因此可设计成能充分发挥材料效率的结构,其各部位载荷要求的强度都与各部位材料提供的实际强度相适应,这是金属材料所做不到的。
因此这种结构可获得同种材料的最高比强度,同时它还具有工艺简单、制造周期短、成本低等优点。
2.2.1玻璃纤维复合材料固体火箭发动机壳体使用的第一代复合材料是玻璃纤维复合材料。
第一个成功的范例是20世纪60年代初期的“北极星A2”导弹发动机壳体,它比“北极星A1”的合金钢壳体重量减轻了60%以上,成本降低了66%。
近年来我国玻璃钢壳体的研制也取得了重大进展。
尤其采用国内2#玻璃纤维/环氧树脂复合材料的壳体已成功地应用于多种发动机。
资料表明,国内已成功应用于型号发动机的玻璃钢壳体与目前法国M4导弹的402V发动机壳体水平相当,但比最先进的“海神”导弹发动机壳体的复合强度约低10%。
然而,玻璃钢虽然具有比强度较高的优点,但它的弹性模量偏低,仅有0.6×105MPa(单向环)。
这是由于复合材料中提供主要模量分数的高强2#玻璃纤维的弹性模量太低(0.85×105MPa,只是钢的2/5)的缘故,这一缺点引起发动机工作时变形量大,其应变一般为1.5%,甚至更大,而传统的金属壳体的应变一般小于0.8%。
这样大的变形量会给导弹总体带来很多不利因素;为了保证壳体的结构刚度,不得不增加厚度,从而造成强度富裕,消极重量增加等。
2.2.2芳纶复合材料为了满足高性能火箭发动机的高质量比要求(战略导弹发动机质量比要求在0.9 以上,某些宇航发动机的质量比已达到0.94),必须选用同时具有高比强度和高比模量的先进复合材料作为壳体的第二代材料,逐步取代玻璃纤维复合材料。
60 年代,美国杜邦公司首先对芳纶纤维进行了探索性研究,1965 年获得突破性进展。
其研制的“芳香族聚芳酰胺”高性能纤维(商品名为Kevlar)于1972 年开始了工业化生产。
继美国杜邦公司开发芳纶纤维之后,俄罗斯、荷兰、日本及中国等也相继开发了具有各自特色的一系列芳纶纤维。
表1列出了几种典型的航天用芳纶纤维力学性能。
芳纶纤维及其树脂基复合材料的问世,立即引起航空和导弹专家们的高度兴趣。
70年代初,美国将Kevlar49纤维增强环氧基复合材料成功地应用于固体导弹“三叉戟Ⅰ(C3)”的第一、二、三级发动机;至70年代末,美国又将Kevlar49纤维增强环氧基复合材料应用于洲际导弹MX,其发动机壳体采用Kevlar49纤维/HBRF缠绕结构,壳体由18个螺旋缠绕循环和51个环向缠绕循环构成。
还有最新的“三叉戟Ⅱ(C5)”导弹的第三级发动机也是由Kevlar49复合材料壳体制成,特别是美国新的战术导弹“潘新Ⅱ”两级发动机都是Kevlar49复合材料壳体。
还有前苏联的SS 20、SS 24和SS 25导弹各级发动机均采用APMOC纤维/环氧复合材料。
国内结合高质量比的固体发动机预研工作,也开展了芳纶复合材料的应用研究。
从1980年开始,利用进口的Kevlar49纤维进行了浸胶复丝的力学性能测试研究,与芳酰胺纤维相容性好的高性能树脂基体配方和预浸工艺研究,单向环、Φ150 小容器和Φ480 模拟容器的缠绕和性能测试;并在这些基础上结合设计部门的结构试验,开展了直径1m和2m的模样发动机壳体材料工艺试验。
研究资料表明:对于相同尺寸的发动机壳体,Kevlar49与高强2#玻璃纤维相比,Kevlar49复合材料容器效率提高近1/3,重量减轻1/3以上,同时,Kevlar49与高强2#玻璃纤维相比,Kevlar49复合材料容器环向应变减少35%,纵向应变减少26.4%,轴向伸长减少30.7%径向伸长减少33.8%,其刚度大为提高。
2.2.3碳纤维复合材料80 年代以来,碳纤维在力学性能方面取得重大突破,它的比强度、比模量跃居各先进纤维之首。
固体火箭发动机壳体要求复合材料具有高的比强度、比模量和断裂应变。
拉伸模量为265~320GPa,拉伸强度在5GPa左右,断裂延伸率约为1.7%的高强中模碳纤维是理想的壳体增强材料,因而近年来各国都在大力开发高强中模碳纤维。
表2列出了几种典型的航天用高强中模碳纤维力学性能。
碳纤维复合材料壳体PV/W 值是Kevlar49/环氧的1.3~1.4倍,可使壳体重量再度减轻30%,使发动机质量比高达0.93以上。
如美国最新的“三叉戟Ⅱ(C5)”导弹的第一、二级壳体及“侏儒”导弹的第一、二、三级壳体均采用IM 7碳纤维/环氧复合材料。
另外,碳纤维复合材料还具有有机纤维/环氧所不及的其它优良性能:比模量高,热胀系数小、尺寸稳定性好,层间剪切强度及纤维强度转化率都较高,不易产生静电聚集,使用温度高、不会产生热失强,并有吸收雷达波的隐身功能。
另外,目前最有希望解决未来发动机飞行生存能力的基本材料,预计用高性能碳纤维,加上多功能基体通过特种工艺技术途径,有可能使“三抗”结构材料成为现实。
2.3树脂基体2.3.1树脂基体的选择原则固体火箭发动机壳体就其主要工作方式而言,是一个内压容器。
它作为航天产品,不仅要求具有足够的强度、刚度和模量,而且要求密度低,即要求具有高的容器特性(PV/W)值[2]。
影响PV/W值的因素很多,基体树脂的性能是其中之一。
此外,发动机工作后,为使壳体在内部高温燃气的加热下仍保持足够的强度和刚度,树脂基体又应具有较高的热变形温度。
固体火箭发动机壳体用复合材料树脂基体的选择遵循如下原则[2]:第一个原则是热力学应变能原则。
树脂基体的热变形温度不低于120℃。
在树脂力学性能方面,主要考察拉伸性能,而拉伸性能的优劣应以拉伸强度和断裂伸长率的乘积—相对应变能来衡量。
相对应变能高的树脂基体其相应容器爆破压强将会高些。
对于大型发动机壳体制造用的环氧树脂应具有下列物理力学性能:拉伸强度≥80MPa;拉伸模量>2800MPa;断裂伸长率为4%~8%;热变形温度>120℃。
第二个原则是树脂体系的工艺性。
对于湿法缠绕来说,树脂系统在缠绕条件下的粘度及粘度的稳定性是最重要的工艺性要求。
为了得到较佳的容器性能,树脂系统在缠绕条件下的粘度一般应在0.2~0.8Pa·s范围,适用期在5h以上。
对于干法缠绕来说,树脂系统的使用期表现在预浸胶纱带的使用期上。
所选树脂系统应使预浸胶纱带的室温使用期不低于30h,一般应在两天以上,否则难于保证复合材料质量的稳定和可靠。
第三个原则是原材料的来源、毒性和经济性,还应考虑原材料性能的已知性。
2.3.2 树脂基体的现状与发展环氧树脂是普遍应用的先进复合材料树脂基体,它是最早应用的大型固体火箭发动机壳体缠绕用树脂。
按照增强材料分,固体火箭发动机壳体发展经历了三个阶段[3],从玻璃纤维到碳纤维,目前各国在新研制的固体火箭发动机上几乎都采用了碳纤维壳体,但基体树脂仍普遍采用环氧树脂,这是与环氧树脂较好的耐热性、良好的粘接性以及优异的工艺性能分不开的。
近年来,为了满足新型航空航天器的需要,不断提高热固性树脂基复合材料的使用温度及力学性能,各国都相继开发了许多新型耐高温树脂,主要有双马来酰亚胺(BMI)和聚酰亚胺(PI)等。
但由于其工艺性和价格等因素的制约,目前,火箭发动机壳体用树脂基体仍以环氧树脂为主。
许多科技工作者都致力于开发高性能环氧树脂,以与不断提高的纤维性能相匹配,更好地适应航空航天技术的发展。
目前,对于环氧树脂的改性,存在着两种不同的看法:一种认为断裂延伸率是影响容器特性(PV/W)的主要因素,应致力于开发高延伸率的高韧性环氧树脂;一种认为耐热性是主要因素,应致力于开发高耐热性的环氧树脂。
鉴于两种不同的观点,将就两个方面(耐热性与高延伸高韧)分别展开论述,这也代表了当今环氧改性的两个主要的方向。
(1)环氧树脂的增韧改性随着纤维增强材料性能的提高,如碳纤维,其延伸率可达2.3%左右,为了充分发挥增强纤维的性能,提高容器PV/W值,必须开发高延伸率的环氧树脂。