铝电解槽发展史资料讲解
第二篇铝电解槽

10.2 铝电解槽
10.2.1 铝电解的工作原理
• 电解质:冰晶石—氧化铝融盐, • 电流:直流电(4~22kA); • 电解温度:950~970℃; • 电极:阴、阳极均为碳质,阴极上析出铝、而阳 极上析出
CO2(70%)和CO(30%)气体; • 电解总反应:2Al2O3(aq)+3C(s)=4Al(l)+3CO2(g)
1自焙槽
2预焙槽
1自焙阳极电解槽 (1)侧插式 (2)上插式
2预焙阳极电解槽 (1)连续式 (2)不连续式
根据下料方式又可分为中间下料和边部下料 两种槽型。
电解槽的总体结构:
电解槽是在一个钢制槽壳,内部衬以耐火砖和保温层, 压型炭块镶于槽底,作为电解槽的阴极。电流通过电 解质由炭质阴极流入炭质阳极,完成电解过程。
自焙阳极旁插棒式电解槽
1.基础:绝缘; 2. 阴极:保温、坚固、密封防氧化、底糊防 侵蚀、挡板防淌料、侧部炭糊筑坡; 3. 阳极: 铝箱、钢 质框架; 4. 上部金属结构:支柱、平台、AO料斗、阳极升 降机构、槽帘和排烟系统 5. 导电母线和绝缘设施
下料,集气排烟装置等。
阳 极 装 置
(2)阴极装置 由钢制槽壳、阴极炭块组和保温材料砌体组成。
阴极装置
(3)母线装置 包括阴极母线,阳极母线,立柱母线和槽间母线。
槽 间 母 线
氧化铝下料装置立体图
氧化铝下料装置剖面图
10.2.3.1 不连续预焙阳极电解槽
依加料方式分:边部打壳电解槽、中部打壳电解槽 阳极炭块组:阳极导杆、钢爪、炭块。 阴极装置:阴极炭块、钢质导电棒 铝母线:阳极母线、阴极母线、立柱母线. 进电方式:一端进电、双端进电
23——密封圈 24——钢壳
【2019年整理】铝电解槽的发展进程
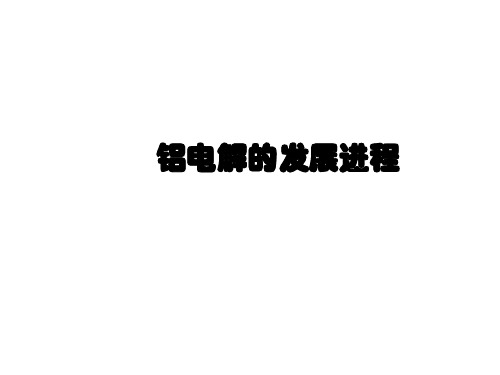
180~ 280
280~ 550
0.9~0.6
13900~13200
机械与自动 化
半机械化 操作
后期采用 多种作业 联合机组
今采用计 算机智能 模糊控制
系统
• 电解槽大型化是我国铝工业发展的基本特点
• 2005年全国生产铝厂147家 产量780. 万吨。其中:
•
160 kA槽约2400台 产能约110万吨 中铝1194台
• (5)维护电解槽的热平衡(和能量平衡)更 显出重要性,既需要确保极距以产生足够
• 我国的电解铝工业1954年第一家铝电解厂 (抚顺铝厂)投产,50多年来铝电解生产技术 已取得巨大成就。2001年开始我国原铝产 量一直居世界第一位。2007年原铝产量已 达到1255万t。截至2007年底,我国有铝电 解厂120余家,现已能设计、制造、装备 180kA、200kA、280kA、320kA、350kA 及400kA等容量的预焙阳极铝电解槽以及相 应的配套工程设施,包括炭素厂、原料运
• 80年代中叶,电解槽更加大型化,点式下 料量降低到每次2kg氧化铝,采用了单个或 多个废气的捕集系统,采用了微机过程控 制系统,对电解槽能量参数每5s进行采样, 还采用了自动供料系统,减少了灰尘对环 境的影响。进入90年代,进一步增大电解 槽容量,吨铝投资较以前更节省,然而大 型槽(特别是超过300kA的电解槽)能耗并不 低于80年代初期较小的电解槽,
,产量约300万吨 中铝2家30.5万吨(含在建) G320-30+S300-
348
11.3%
•
——在建最大槽为400kA
• 2006:934.92万吨(25.8——9);2007:1225.86万吨
• 2010年产能 2300万吨,产量1600万吨。
铝电解的基础知识

铝电解的基础知识尽管在⾃然界中含有极为丰富的铝,但铝第⼀次制取出来却是不到⼆百年前的事。
1825年丹麦的厄尔施泰(H·C·Oersted)在实验室中⽤钾汞齐还原⽆⽔氯化铝(AlCl3),在世界上第⼀次得到铝。
1845年法国⼈戴维尔(H·S·Deville)⽤钠还原NaCl·AlCl3混合盐也得到⾦属铝,并在法国进⾏⼩规模⽣产。
到1877年电解法投产以前,世界上仅⽤化学法⽣产⾦属铝,这⼀阶段,铝产量极低,使铝成为世界上极为昂贵的⾦属之⼀。
1886年,美国的霍尔和法国的埃鲁特发明了冰晶⽯—氧化铝熔盐电解法炼铝,很快电解铝取代了化学法,⽽且产量迅速提⾼,成本迅速下降,到⽬前为⽌的百年间,铝⼯业发展成为仅次于钢铁⼯业的第⼆⼤⾦属冶炼⼯业。
1.3现代铝电解的基本原理电解法炼铝就是冰晶⽯⼀氧化铝融盐电解法,它是以冰晶⽯作为溶剂,氧化铝为熔质,强⼤的直流电通⼊电解槽内,在阴极和阳极上起电化学反应。
电解产物,阴极上是铝液,阳极上是CO2和CO⽓体(炭素作阳极),这种⽅法就是电解法炼铝。
1.3.1阴极过程络合的3(液)1.3.1.2阴极副反应在铝电解过程中,除前⾯讲的两极主反应外,同时在两极上还发⽣着⼀些复杂的副反应.这些副反应对⽣产有害⽆益,⽣产中应尽量加以遏制。
⑴阴极副反应①铝在电解质中的溶解反应和损失:在铝电解过程中,处于⾼温状态下的阴极铝液和电解质的接触⾯上,必然有析出的铝溶解在电解质中,⼀般认为,阴极铝液在电解质⾥的溶解有以下⼏种情况:a. 溶解在熔融冰晶⽯中的铝,⽣成低价铝离⼦和双原⼦的钠离⼦。
2Al+Al3+=3Al+Al+6Na+=Al3++3Na2+b.在碱性电解质中,铝与氟化钠发⽣置换反应。
Al+3NaF=AlF3+3Na2+3O2-络合的) + 1.5C- 1.5教授⽅法:课堂讲授、讨论、提问。
铝电解槽发展史资料讲解
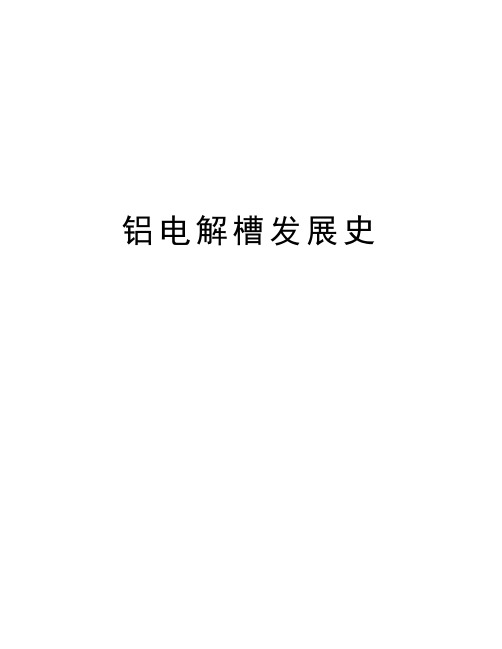
铝电解槽发展史铝电解槽发展史从1886年到现在,Hall—Heroult的冰晶石—氧化铝熔盐电解法,已经快有120年历史了,在此期间,此电解炼铝的工艺和方法原理没有变化,然而期电解槽的结构发生了很大变化。
铝电解生产由最初的电耗40kWh/kg.Al【】电流效率75%,(1889年Heroult槽)】和电耗31 kWh/kg.Al【电流效率80%,(1892年Hall槽)】,降到现在的电耗12.5 kWh/kg.Al(直流电耗),电流效率96%以上。
电解槽的容量(电流)由最初的几千安培,增加到现在的500kA。
电解槽结构按阳极特性来划分,经历了从预焙阳极到侧插自焙阳极,到上插自焙阳极,又到预焙阳极的阶段。
期间也出现过连续预焙阳极试验电解槽,但未成功推广。
电解槽初期阶段,是小型预焙阳极电解槽,图1.图1 1912年Heroult的12000A电解槽电耗25000k W·h/tAl,阴阳极电流密度1.0~1.2A/㎝2当时槽容量是12000A,电耗25000kw.h/t.Al,阳极电流密度1.0—1.2A/㎝2 ,特点是电流小,电压高,阳极电流密度大,电耗高,电流效率低。
现代铝工业上有两类、共四种形式的电解槽:·自焙阳极电解槽侧插棒式上插棒式·预焙阳极电解槽不连续式连续式自焙槽起始于1923年,是由挪威人在生产铁合金电路连续自焙电极的基础上发展起来的。
在20世纪60年代,侧插自焙槽最大电流达到100kA,上插自焙槽在20世纪50—70年代,在世界范围内得到了很大发展,其电解槽的最大电流达到了170—180kA,当时指标是:电流效率88~90%,电耗15000kw.h/t.Al。
自焙槽特点有:①使用的阳极糊靠电解槽自身的热量使其焙烧成良好的导电体,使电解槽上部散热得到合理利用。
综合节能。
②由于直接使用阳极糊,节省了预制阳极过程的成型,被烧,加工,阳极组装等工艺与工序工程,以及该过程需要的燃料和各种消耗及劳动费用于投资。
50 年中国铝工业发展历程
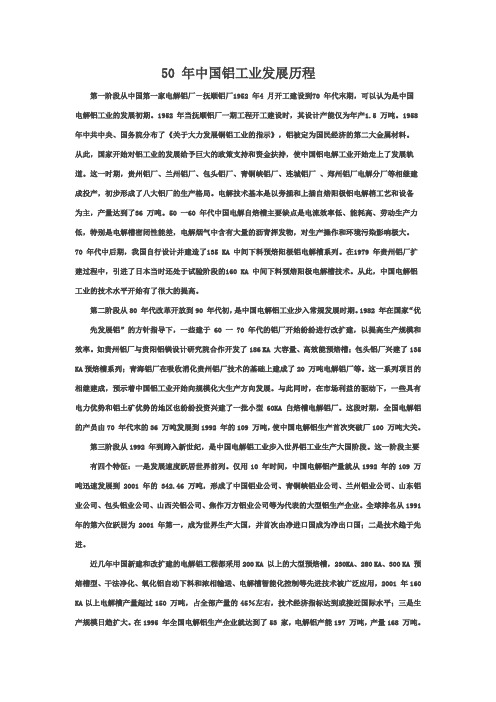
50 年中国铝工业发展历程第一阶段从中国第一家电解铝厂-抚顺铝厂1952 年4 月开工建设到70 年代末期,可以认为是中国电解铝工业的发展初期。
1952 年当抚顺铝厂一期工程开工建设时,其设计产能仅为年产1.5 万吨。
1958 年中共中央、国务院分布了《关于大力发展铜铝工业的指示》,铝被定为国民经济的第二大金属材料。
从此,国家开始对铝工业的发展给予巨大的政策支持和资金扶持,使中国铝电解工业开始走上了发展轨道。
这一时期,贵州铝厂、兰州铝厂、包头铝厂、青铜峡铝厂、连城铝厂、郑州铝厂电解分厂等相继建成投产,初步形成了八大铝厂的生产格局。
电解技术基本是以旁插和上插自焙阳极铝电解梢工艺和设备为主,产量达到了36 万吨。
50 一60 年代中国电解自焙槽主要缺点是电流效率低、能耗高、劳动生产力低,特别是电解槽密闭性能差,电解烟气中含有大量的沥青挥发物,对生产操作和环境污染影响极大。
70 年代中后期,我国自行设计并建造了135 KA 中间下料预焙阳极铝电解槽系列。
在1979 年贵州铝厂扩建过程中,引进了日本当时还处于试验阶段的160 KA 中间下料预焙阳极电解槽技术。
从此,中国电解铝工业的技术水平开始有了很大的提高。
第二阶段从80 年代改革开放到90 年代初,是中国电解铝工业步入常规发展时期。
1982 年在国家“优先发展铝”的方针指导下,一些建于60 一70 年代的铝厂开始纷纷进行改扩建,以提高生产规模和效率。
如贵州铝厂与贵阳铝镁设计研究院合作开发了186 KA 大容量、高效能预焙槽;包头铝厂兴建了135 KA预焙槽系列;青海铝厂在吸收消化贵州铝厂技术的基础上建成了20 万吨电解铝厂等。
这一系列项目的相继建成,预示着中国铝工业开始向规模化大生产方向发展。
与此同时,在市场利益的驱动下,一些具有电力优势和铝土矿优势的地区也纷纷投资兴建了一批小型60KA 白焙槽电解铝厂。
这段时期,全国电解铝的产员由70 年代末的36 万吨发展到1992 年的109 万吨,使中国电解铝生产首次突破厂100 万吨大关。
2-3铝电解槽结构
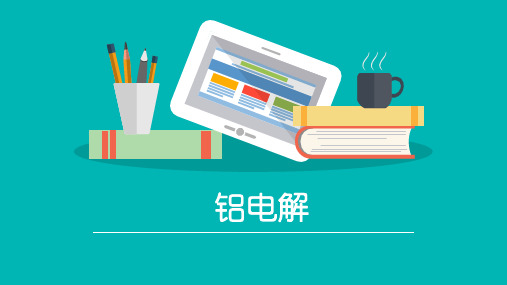
三、电解槽结构
自焙阳极旁插式电解槽 • 基础:绝缘 • 阴极:保温、坚固、密封防氧化、底糊
防侵蚀、挡板防淌料、侧部炭糊筑坡 • 阳极: 铝箱、钢质框架 • 上部金属结构:支柱、平台、AO料斗、
阳极升 降机构、槽帘和排烟系统 • 导电母线和绝缘设施
三、电解槽结构
自焙阳极上插式电解槽:
三、电解槽结构
四、电解槽系列
• 为保证系列的连续稳定运行,需备用电源;
• 电解槽排布方式:
• 横向排列 • 纵向排列
单行排列 双行排列
四、电解槽系列
铝电解
目录 CONTENTS
铝电解基本知识 铝电解槽结构 电解槽焙烧与启动 铝电解正常生产
02
铝电解槽结构
一、工作原理
• 电解质:冰晶石—氧化铝融盐, • 电流:直流电(4~22kA); • 电解温度:950~970℃; • 电极:阴、阳极均为碳质,阴极上析出铝、
而阳 极上析出CO2(70%)和CO2(30%) 气体; • 电解总反应: • 2Al2O3(aq)+3C(s)=4Al(l)+3CO2 (g)
部打壳电解槽
• 阳极炭块组:阳极导杆、钢爪、炭 块
• 阴极装置:阴极炭块、钢质导电棒 • 铝母线:阳极母线、阴极母线、立
柱母线
三、电解槽结构
连续预焙阳极电解槽 • 相对于非连续式有如下特点: 优点: • 无阳极残极,预焙炭块消耗量小; • 阳极电流分布均匀,故阳极消耗均匀; • 生产的连续性。 缺点: • 阳极不能用氧化铝保温,热损失大; • 炭块之间接缝存在接触电压降,故槽电压较大。
二、电解槽的发展
• 铝电解槽的发展从19世纪末至今已经有了一百多年的历史。 • 三个发展阶段: • 铝电解工业初期的小型预焙电解槽; • 20世纪20~40年代,相继采用旁插棒式自焙阳极和上插棒式自焙
4——铝电解
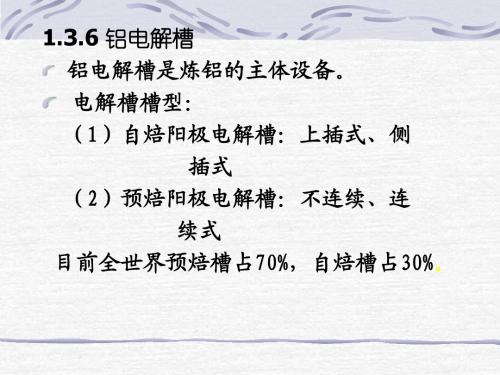
电流效率
最初低于80%,现在一般为90%,高的达到95% 以上
能耗
最初高达30-40kW· h/kg Al,现在降低到12-15 kW· h/kg Al。
生产机械化、自动化,电解槽气体 净化和综合利用 自焙槽和预焙槽比较:
(1)在电解过程中,阳极大约以0.8-1.0 mm/h速度连续消耗,自焙槽可连续使用, 而预焙槽不能连续使用,须定期更换; (2)自焙槽散发氟化物,沥青烟气,而预 焙槽不散发烟气,污染环境;
生产每吨铝所需要的电能量= { V/[0.3356× ] }×103kW·h 式中 V— 电解槽的总平均电压; — 电流效率 例:某电解槽的平均电压是4.25V,电流效率是92%, 则生产每吨铝所需的电能量
=[4.25/0.3356×0.92]×103 = 13765 kW· h
节电途径 (1)提高电流效率 (2)降低平均电压
从电解槽中取出的铝液通常含有三类杂 质: A、金属杂质; B、非金属固态夹杂物:氧化铝、炭、 碳化铝; C、气态夹杂物:H2、CO2、CO、CH4、 N2。其中最主要的是H2。 在1000℃,100g工业原铝大约溶解氢气 0.2-0.4cm3。 铝液中的氢有两种形态:原子氢和气态 氢。前者溶解在铝液中,后者吸附在固 态夹杂物颗粒上。
铝的电解精炼原理:
在阳极合金的各种金属元素当中,只有 铝在阴极上溶解出来。阳极合金中,如 铜、铁、硅之类比不活泼的金属元素, 并不溶解,仍然残留在合金内。阳极上 的电化学溶解反应是:Al - 3e = Al3+ 因此,电解液中除了原有的Al3+, Ba2+, Na+, F-, Cl-, AlF3-6, AlF4-之外,增加 了上述反应中的铝离子Al3+。
电解槽基础

电解槽生产启动管理
180KA电解槽焙烧技术标准
装炉准备及装炉操作
焙烧前电槽必须满足装备能源部电解槽内衬大修检查 标准的要求。 提前一天通知计算机站将槽控机调试好。 铺设焦粒。 清扫阴极,将阳极母线降至下限,回转计调为380。 将栅栏框架平整摆放在阳极投影区域,然后将筛分好 的煅后焦(1~5名模,其中2~4mm占75%)倒入框内, 用板尺刮平之后,取走栅栏框。每槽煅后焦量为 400~450Kg。 选择组装合格的阳极进行挂极,阳极应压实焦粒,不 允许有晃动。
二、电解槽母线结构及母线配短路母线4部分构成。 阳极母线 阳极母线采用铸造铝母线,两端用软铝母线与端头母线联结,以便阳极母线升降。 阳极母线端面尺寸为550×220mm2,长度为8100mm,端头母线与立柱母线采用 氩弧焊接。 阴极母线 阴极母线也采用铸造铝母线,A侧阴极母线断面尺寸为180×220mm2,B册阴极 母线断面尺寸有两种,分别为150×180mm2和150×300mm2。阴极钢板与阴极母 线的连接部分由爆炸焊板、阮铝母线及焊接钢板组成。 立柱母线 立柱母线采用铸造铝母线,每端4片,端面尺寸为440×125mm2,立柱母线与上 一台电解槽的阴极母线采用氩弧焊接,与本台槽阳极端头母线压接。 短路母线 电解槽停电短路采用地上短路。需要短路时将立柱母线与短路母线之间的绝缘板 抽出,然后将短路母线与立柱母线用螺栓压紧。操作时需停电3~5min。 母线配置 180KA中间下料预焙槽采用横向排列方式,双端进电,进电比为1:1阴极母线从 上流侧分8组进入槽底,然后从槽底纵向中心线处延伸到槽端,与下流侧阴极母 线相汇合,经斜立柱母线与下一台槽阳极母线相接
桁架与门式支架
电解槽的上部承重由钢制的桁架和门式支架承担。 桁架由角钢焊接制成,形状呈倒梯形,高1.3m, 与门式支架相连的边长为10.2m。桁架中部由角 钢制成的三角形支撑,以加强桁架的承栽能力。 门式支架由钢板制成门字形,其下部与槽壳铰 接,目的是消除因高温引起的变形和方便维修。 门式支架与槽壳的连接处加有绝缘垫板,以不使 上部结构与槽壳短路。
铝电解槽节能技术发展历程及特点分析

铝电解槽节能技术发展历程及特点分析电解铝是生产铝产品的重要方法,但是这种方法的传统利用存在着高能耗、高污染等问题,这些问题不进行解决,电解铝企业的发展会受到极大的限制。
文章对电解铝的具体生产问题做了分析与讨论,并基于问题对电解铝的节能、减排技术进行讨论与研究,旨在为实践提供帮助和指导。
标签:铝电解槽;节能技术;应用前言我国属于电解铝大国,最近几年我国的电解铝产量呈逐年增加的态势,到2018年年末我国的电解铝产量将达到3780万吨。
电解铝行业的利润空间在不断地减小,为了保证铝电解产业的健康稳定发展,就有必要对电解铝过程中的节能降耗这一问题引起足够的重视。
1 电解铝在生产过程中遇到问题第一是电解铝生产存在着明显的环境污染问题。
对我国目前的电解铝生产做实践性分析可知,企业在电解铝生产中主要利用的是熔盐电解的方式,其中以冰晶石一氧化铝材料为主[1]。
在生产的过程中,首先要做的工作是提升温度,使其达到冰晶石一氧化铝的熔点,由于此种材料的熔点比较高,所以在加热的过程中比较容易产生扬散的情况,这种情况会对环境造成严重的污染。
另外,在生产的过程中,电解方法的利用会导致许多游离氧的产生,而游离氧离子会和二氧化碳产生反应,进而污染环境。
第二是电解铝生产存在着高耗电、高耗能的问题。
对目前的电解铝生产做具体的分析发现,这种生产方式的电能消耗量非常巨大,而且对能源资源的需求量也比较高,这导致整个生产过程的能源供给高居不下。
这于我国目前的绿色经济发展理念不符,所以必须要对其进行改正。
第三是电解铝生产存在着一定的危害性。
从现实分析来看,电解铝生产废物,无论是固体废弃物还是废水、废烟,均含有比较多的有害物质,这些物质严重影响人体健康,所以必须要对其做控制。
2 电解铝生产节能对策2.1 低压生产技术①异性阴极节能技术。
该技术在目前的电解铝生产中利用普遍,其具有非常不错的效果,就该技术的具体利用来看,维修电解槽的时候,使用阴极带有凸台的异性阴极,可以有效的阻隔电解过程中所产生的铝液,以此可以实现对铝液流动速度和铝液界面的变形进行缓解,如此一来,电解槽的工作电压会得到有效的降低。
铝电解生产原理PPT课件

11
❖ 根据铝电解的基本原理,需要为反应 过程提供大量的直流电能,用以推动 反应向生成铝的方向进行;随着电解 反应的不断进行,炭阳极以及溶解于 电解质中的氧化铝不断消耗,生产中 需及时补充,使生产得以连续进行; 原则上冰晶石是不消耗的,但是由于 和杂质反应引起的化学损失、各种机 械损失以及在电解的高温融融状态下 的挥发损失,电解过程中也需要一定 的补充。
❖ 在电解质熔体中,增加AlF3的含量,则电解质粘度降低。 但是在酸性电解质中,AlF3和Al2O3的共同存在对粘度的影 响将不会十分明显;
❖ 4)在电解质熔体中,随着AlF3含量的增加,熔体中Al2O3 的溶解度随之降低;
❖ Al3+(络合)+3e﹦Al
❖ 目前铝工业仍然采用活性阳极,阳极本身参与反应。 在阳极炭块上是铝氧氟络合离子中的O2-放电,发 生电化学反应:
❖ 2 O2-(络)-4e+C﹦CO2
❖ CO2被认为是阳极第一反应产物,铝电解的结果只 消耗了Al2O3和C,因此整个电解过程总反应式为:
❖ Al.2O3+1.5C﹦2Al+1.5 CO2↑
.
2
一、铝的性质和用途
❖ 铝的化学性质非常活泼,与氧的亲和力很强。铝在 空气中能与氧迅速化合,生成一层致密而坚硬的氧 化铝薄膜,厚度为0.005~0.02μm,成为铝的天然保 护层,阻止铝继续被氧化,因而具有好的抗蚀性能, 还可以用阳极氧化或电镀的方法,在铝材和铝制品 的表面生成彩色鲜艳的氧化膜。
. 以轧成薄板和箔、拉成细丝、挤压成各种复杂形状 3
❖ 铝由于具有优良的物理性能,所以铝在国民经济各部 门和国防工业中得到了广泛的应用。铝作为轻型结构 材料,重量轻,强度大,陆、海、空各种运载工具, 特别是飞机、导弹、火箭、人造卫星等,均使用大量 的铝,一架超音速飞机的用铝量占其自身重量的70%, 一枚导弹用铝量占其总重量的10%以上。用铝和铝合 金制造的各种车辆,由于重量轻,可以减少能耗,所 节省的能量远远超过炼铝时所消耗的能量。在建筑工 业中用铝合金作房屋的门窗及结构材料,铝具有吸音 性能,音响效果也较好,所以广播室、现代化大型建 筑室内的天花板等也采用铝,用铝制作太阳能收集器, 可以节省能源。在电力输送方面,铝的用量居首位, 90%的高压电导线是用铝制作的。在食品工业上,从 仓库储槽到罐头盒,以至饮料容器大多用铝制成。在 其他方面,用铝粉作难熔金属(如钼等)的还原剂和作 炼钢过程中的脱氧剂,以及日常生活中的锅、盆、匙 等。
自焙阳极铝电解槽
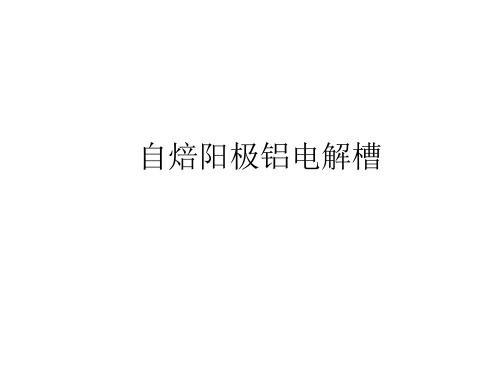
自焙阳极上插棒式电解槽
1-阳极框套 2-集气罩 3-燃烧器 4-阳极 5-阳极棒6-阳极棒的铝导杆 7-阳极母 线梁 8-槽壳 9-槽壳底部的型钢 10-阴极棒 11-侧部 12-保温层 13-阴极母线
自焙阳极侧插棒式电解槽
1-铝箱 2-阳极框架 3-阳极棒4-槽壳 5-底部加固型钢6-侧部炭块和底部 炭块7-阴极棒 8-保温层 9-阳极母线 10-阴极母线 11-槽帘自焙阳极源自电解槽自焙阳极电解槽的分类
上世纪20年代,铝工业开始采用自焙阳极电解槽,这 种阳极在电解过程中只要定期地补充阳极糊,阳极就可 以连续的使用。特点是没有残极,连续的阳极和电解过 程的连续性相适应,缺点是劳动条件差,污染严重。 自焙阳极电解槽分为上插式自焙阳极电解槽和侧插式 自焙阳极电解槽(旁插式)
铝电解槽节能技术发展历程及特点
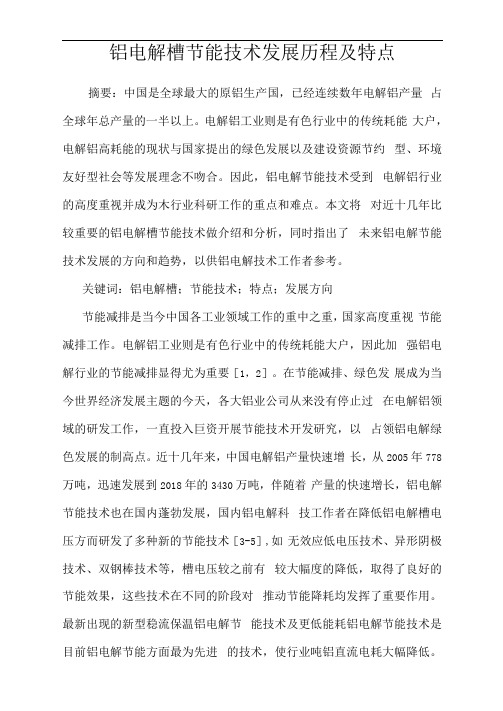
铝电解槽节能技术发展历程及特点摘要:中国是全球最大的原铝生产国,已经连续数年电解铝产量占全球年总产量的一半以上。
电解铝工业则是有色行业中的传统耗能大户,电解铝高耗能的现状与国家提出的绿色发展以及建设资源节约型、环境友好型社会等发展理念不吻合。
因此,铝电解节能技术受到电解铝行业的高度重视并成为木行业科研工作的重点和难点。
本文将对近十几年比较重要的铝电解槽节能技术做介绍和分析,同时指出了未来铝电解节能技术发展的方向和趋势,以供铝电解技术工作者参考。
关键词:铝电解槽;节能技术;特点;发展方向节能减排是当今中国各工业领域工作的重中之重,国家高度重视节能减排工作。
电解铝工业则是有色行业中的传统耗能大户,因此加强铝电解行业的节能减排显得尤为重要[1,2]。
在节能减排、绿色发展成为当今世界经济发展主题的今天,各大铝业公司从来没有停止过在电解铝领域的研发工作,一直投入巨资开展节能技术开发研究,以占领铝电解绿色发展的制高点。
近十几年来,中国电解铝产量快速增长,从2005年778万吨,迅速发展到2018年的3430万吨,伴随着产量的快速增长,铝电解节能技术也在国内蓬勃发展,国内铝电解科技工作者在降低铝电解槽电压方而研发了多种新的节能技术[3-5],如无效应低电压技术、异形阴极技术、双钢棒技术等,槽电压较之前有较大幅度的降低,取得了良好的节能效果,这些技术在不同的阶段对推动节能降耗均发挥了重要作用。
最新出现的新型稳流保温铝电解节能技术及更低能耗铝电解节能技术是目前铝电解节能方面最为先进的技术,使行业吨铝直流电耗大幅降低。
木文详细介绍各种节能技术, 通过对铝电解节能特点分析,为以后铝电解节能技术的研发提供一些参考,同时指出了未来铝电解节能技术发展的方向和趋势。
1铝电解节能技术现状我国的电解铝产量在国际上处于遥遥领先的地位,铝电解技术在国际上也处于领先水平,伴随着产量的不断增长,铝电解节能技术同样取得了巨大进步,形成了一系列先进技术,这些技术在节能降耗方而发挥了重要作用,下而就对这些有代表性的铝电解节能技术作较为详细的介绍和分析。
铝电解槽

• • • •
⑷炭阳极对阳极糊的要求
阳极糊要求有一定的塑性(或流动性),以便 阳极糊要求有一定的塑性(或流动性),以便 ), 填满拔棒后留下的孔洞; 填满拔棒后留下的孔洞;但流动时不能引起焦 粒偏析,孔洞不能被富含沥青的糊所填充, 粒偏析,孔洞不能被富含沥青的糊所填充,以 免此处焦化后孔隙率过高; 免此处焦化后孔隙率过高; 流动性与糊中沥青配比、沥青的软化点、 流动性与糊中沥青配比、沥青的软化点、阳极 上部温度等因素有关。 上部温度等因素有关。 阳极糊的质量主要取决于固定炭粒的粒度组成, 阳极糊的质量主要取决于固定炭粒的粒度组成, 沥青配比由粒度组成确定。 沥青配比由粒度组成确定。
预焙阳极电解槽
依加料方式分: 依加料方式分:边部打壳和中部打壳电解槽 • 阳极炭块组:阳极导杆、钢爪、炭块 阳极炭块组:阳极导杆、钢爪、 • 阴极装置:阴极炭块、钢质导电棒 阴极装置:阴极炭块、 • 铝母线:阳极母线、阴极母线、立柱母线 铝母线:阳极母线、阴极母线、 • 进电方式:一端进电、双端进电 进电方式:一端进电、
铝电解机理——两极过程 铝电解机理——两极过程
1.阴极过程: 阴极过程: Al3+(配离子)+3e=Al 配离子)+ 配离子)+3 配离子解离,配离子同时放电; 配离子解离,配离子同时放电; 分子比↑ 温度↑、Al 浓度↓ 阴极电流密度↑ 分子比↑、温度↑、A 2O3浓度↓,阴极电流密度↑ 铝钠析出电位差值减小,可能导致钠离子放电; →铝钠析出电位差值减小,可能导致钠离子放电; 采用酸性电解质体系,较低的电解温度, 采用酸性电解质体系,较低的电解温度,尽可能 大的A 浓度,良好的传质以防阴极上N 大的Al2O3浓度,良好的传质以防阴极上 a+过度 积累而放电。 积累而放电。 阳极过程: 2.阳极过程: 2O2-(配离子)+C-4e=CO2 配离子)+C- 配离子)+C-4 配位阴离子中的氧离子在炭阳极上放电析出O 配位阴离子中的氧离子在炭阳极上放电析出O2, 而后与C反应生成CO 而后与C反应生成CO2; 炭渣的存在,CO 气体渗入阳极孔隙与C再反应, 炭渣的存在,CO2气体渗入阳极孔隙与C再反应, 溶解在电解质中的铝再氧化等因素导致气体非纯 而是CO+CO 的混合物。 CO2,而是CO+CO2的混合物。
铝电解槽控机系统的发展与应用

铝电解槽控机系统的发展与应用作者:柴鹤翔来源:《中国科技博览》2013年第29期摘要:本文对铝电解槽控机发展史作了简要介绍,描述了X企业槽控机系统的应用情况,阐释了槽控机系统对铝电解生产的重要性。
关键词:铝电解槽槽控机系统中图分类号:TU8;TU758.7 文献标识码:A 文章编号:1009-914X(2013)29-548-011.引言铝电解是电解槽通以直流电,将氧化铝电解成金属铝的生产过程,该过程的控制以大型预焙铝电解槽自动控制机(简称槽控机)作为核心设备。
而槽控机运行的稳定与否,将直接影响到铝电解控制系统运行效果的好坏,其技术条件的优化,则主要靠自控技术的不断发展和控制水平的不断提高来实施。
2.铝电解槽控机系统的发展历程由于铝电解槽是一个复杂的系统,存在非线性、滞后等因素,故很难建立精确的数学模型,用传统的控制方法难以达到好的控制效果。
槽控机系统恰好在解决这类问题中表现出了优越性,它速度快、人性化、模糊能力强等特点为铝电解槽的控制提供了有效地解决途径。
2.1七零至九零年代的初期发展我国槽控机系统在铝电解上的应用始于70年代。
从1974年沈阳铝镁设计研究院与抚顺铝厂合作的第一台“多台槽巡回检测和阳极自动调整”装置,到1975年东北工学院研制成的工业控制用计算机LSK-74系统,再到80年代初贵铝全套引进的日本轻金属株式会社160kA预焙槽控制系统,再到后期的“日轻”技术翻版、自建的沈阳铝镁设计研究院研究的青海铝厂铝电解槽计算机控制系统。
系统的演进直至投产运行,充分表明了我国已有独立开发和制造铝电解控制系统的能力。
槽控机系统发展至此,虽使铝电解生产指标有了一定提高,但系统的造价高、可靠性差、缺少灵活性、难以满足复杂实时控制的要求等一系列弊端仍普遍存在,亟需有更先进的技术来取代。
2.2九零年代后的快速发展1992年,沈阳铝镁设计研究院和抚顺铝厂开始承担中国有色总公司“八五”攻关项目“智能型铝电解槽工业试验”,仅用时两年就在抚铝135kA铝电解槽上成功推广,智能化技术实现在我国铝电解生产上的首次应用。
电解铝基础知识简介
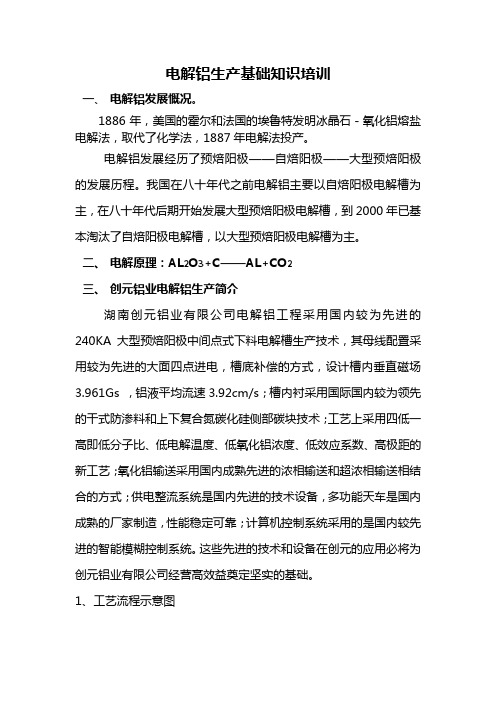
电解铝生产基础知识培训一、电解铝发展慨况。
1886年,美国的霍尔和法国的埃鲁特发明冰晶石-氧化铝熔盐电解法,取代了化学法,1887年电解法投产。
电解铝发展经历了预焙阳极——自焙阳极——大型预焙阳极的发展历程。
我国在八十年代之前电解铝主要以自焙阳极电解槽为主,在八十年代后期开始发展大型预焙阳极电解槽,到2000年已基本淘汰了自焙阳极电解槽,以大型预焙阳极电解槽为主。
二、电解原理:AL2O3+C——AL+CO2三、创元铝业电解铝生产简介湖南创元铝业有限公司电解铝工程采用国内较为先进的240KA大型预焙阳极中间点式下料电解槽生产技术,其母线配置采用较为先进的大面四点进电,槽底补偿的方式,设计槽内垂直磁场3.961Gs ,铝液平均流速3.92cm/s;槽内衬采用国际国内较为领先的干式防渗料和上下复合氮碳化硅侧部碳块技术;工艺上采用四低一高即低分子比、低电解温度、低氧化铝浓度、低效应系数、高极距的新工艺;氧化铝输送采用国内成熟先进的浓相输送和超浓相输送相结合的方式;供电整流系统是国内先进的技术设备,多功能天车是国内成熟的厂家制造,性能稳定可靠;计算机控制系统采用的是国内较先进的智能模糊控制系统。
这些先进的技术和设备在创元的应用必将为创元铝业有限公司经营高效益奠定坚实的基础。
1、工艺流程示意图220KV 交流电 排入大气屋顶烟气 排入大气铝 液废渣场铝锭2、电解槽电解槽是炼铝的主要设备。
外壳是钢壳,内衬是耐火材料和炭素材料,直流电流是由阳极经过电解质后到达铝液、阴极。
预焙阳极电解槽结构如图2。
1) 主要工艺参数电流强度(kA): 240阳极电流密度(A/cm2):阳极组数(组): 16(双阳极组块)阳极炭块组尺寸(mm): 1550×660×550每块阳极钢爪数(个): 4每个钢爪直径(mm): 140每个钢爪电流密度(A/cm2) 12.18铝导杆截面:(mm) 200×170槽膛面积:(mm) 11700×3840槽膛深度:(mm) 550操作面尺寸(mm) 大面 280小面 390中缝 180阴极炭块尺寸(mm) 3320×515×450阴极炭块组数(组) 20阴极钢棒尺寸(长×宽×高): 4280×65×180每组阴极炭块的阴极钢棒数(根) 2阳极升降速度(mm/min): 100图2 预焙阳极电解槽结构1——槽罩 2——钢爪梁 3——阳极 4——电解质 5——槽壳 6——涂层 7——铝 8——阴极炭块 9——阴极棒 10——保温砖 11——排烟装置 12——氧化铝 13——导杆 14——夹板 15——螺栓 16——打壳和筒式下料器17——氧化铝 18——壳面19——边部砖 20——侧部炭氮化硅复合块 21——结壳 22——人造伸腿 23——密封圈 24——钢壳槽壳尺寸:内壁(长×宽×高)(mm) 11940×4080×1357外壁(长×宽)(mm) 12684×4938摇篮架组数:活动(组) 17固定(组) 2阳极母线规格(mm) 550×180阳极最大行程(mm): 4002)槽上部结构电解槽由阳极、阴极和槽罩三部分组成,其中:阳极结构,包括阳极、阳极母线、阳极传动机构及腹板支承梁等。
- 1、下载文档前请自行甄别文档内容的完整性,平台不提供额外的编辑、内容补充、找答案等附加服务。
- 2、"仅部分预览"的文档,不可在线预览部分如存在完整性等问题,可反馈申请退款(可完整预览的文档不适用该条件!)。
- 3、如文档侵犯您的权益,请联系客服反馈,我们会尽快为您处理(人工客服工作时间:9:00-18:30)。
铝电解槽发展史
铝电解槽发展史
从1886年到现在,Hall—Heroult的冰晶石—氧化铝熔盐电解法,已经快有120年历史了,在此期间,此电解炼铝的工艺和方法原理没有变化,然而期电解槽的结构发生了很大变化。
铝电解生产由最初的电耗40kWh/kg.Al【】电流效率75%,(1889年Heroult槽)】和电耗31 kWh/kg.Al【电流效率80%,(1892年Hall槽)】,降到现在的电耗12.5 kWh/kg.Al(直流电耗),电流效率96%以上。
电解槽的容量(电流)由最初的几千安培,增加到现在的
500kA。
电解槽结构按阳极特性来划分,经历了从预焙阳极到侧插自焙阳极,到上插自焙阳极,又到预焙阳极的阶段。
期间也出现过连续预焙阳极试验电解槽,但未成功推广。
电解槽初期阶段,是小型预焙阳极电解槽,图1.
图1 1912年Heroult的12000A电解槽
电耗25000k W·h/tAl,阴阳极电流密度1.0~1.2A/㎝2当时槽容量是12000A,电耗25000kw.h/t.Al,阳极电流密度1.0—1.2A/㎝2 ,特点是电流小,电压高,阳极电流密度大,电耗高,电流效率低。
现代铝工业上有两类、共四种形式的电解槽:
·自焙阳极电解槽
侧插棒式
上插棒式
·预焙阳极电解槽
不连续式
连续式
自焙槽起始于1923年,是由挪威人在生产铁合金电路连续自焙电极的基础上发展起来的。
在20世纪60年代,侧插自焙槽最大电流达到100kA,上插自焙槽在20世纪50—70年代,在世界范围内得到了很大发展,其电解槽的最大电流达到了170—180kA,当时指标是:电流效率88~90%,电耗15000
kw.h/t.Al。
自焙槽特点有:
①使用的阳极糊靠电解槽自身的热量使其焙烧成良好的导电体,使电解槽上部散热得到合理利用。
综合节能。
②由于直接使用阳极糊,节省了预制阳极过程的成型,被烧,加工,阳极组装等工艺与工序工程,以及该过程需要的燃料和各种消耗及劳动费用于投资。
阳极的制造成本。
③不需要定期更换阳极,工艺简单,劳动强度低,对电解正常运行干扰少。
④机械化和自动化操作程度低,劳动强度大。
⑤集气效率低,劳动条件差。
⑥阳极糊产生的大量碳氢化合物等气体不能同电解产生的氟化氢等气体分开,混在一起,不容易回收,对环境污染。
图2、图3、图4为各个时期铝电解槽简图
图2 连续式预焙阳极电解槽简图
1—阳极炭块 2—阳极棒 3—阳极母线 4—槽壳
5—阳极炭块接缝 6—阴极炭块 7—阴极棒 8—保温层
图3 20世纪60~80年代以前广为使用现仍有少量存在的侧插阳极棒自焙
阳极电解槽
图4 20世纪80年代前广为使用的上插阳极棒自焙阳极电解槽
图5 当代的预焙阳极电解槽
预焙阳极电解槽的优点是:阳极已经预先焙烧好,不再在电解槽上散发沥青烟气,电解厂房烟害少;阳极压降低;电解槽上部金属结构和阳极结构简单;可以大型化,操作的机械化和自动化程度较高,电流效率高,电耗率较低。
当然,各种槽型各有优缺点。
表1列出了从1890年以来100余年各种电解槽的发展概况,表2列出了现代率电解槽的技术参数和生产指标。
表1 工业铝电解槽的发展概况
(表中η为电流效率,%;ω为电耗率,kw.h/kg)
表2 现代工业铝电解槽的技术参数和生产指标
随着阳极碳块制造技术的发展,特别是能生产出性能更好的预焙阳极炭块,推动了预焙阳极电解槽的发展。
点式下料技术的发明和应用,计算机技术推广,多功能天车的研发与推广,磁场设计更先进可靠,是预焙阳极电解槽的各项指标达到一个更好的水平。