机器人系统操作手册
ABB机器人操作手册中文版

ABB机器人操作手册中文版一、ABB 机器人简介ABB 机器人是在工业自动化领域广泛应用的先进设备,以其高精度、高速度和高可靠性而闻名。
它能够在各种复杂的生产环境中执行多种任务,如物料搬运、焊接、装配、喷涂等,大大提高了生产效率和质量。
二、机器人系统组成ABB 机器人系统主要由机器人本体、控制器、示教器和周边设备组成。
1、机器人本体由机械臂、关节和末端执行器构成。
机械臂的设计和结构决定了其运动范围和灵活性。
关节采用高精度的电机和传动装置,确保精确的位置和姿态控制。
2、控制器是机器人的“大脑”,负责控制机器人的运动、逻辑和通信。
具备强大的计算能力和丰富的接口,可与其他设备进行集成。
3、示教器用于对机器人进行编程和操作。
具有直观的界面和操作按钮,方便操作人员设置参数和下达指令。
4、周边设备包括传感器、工装夹具、输送线等,与机器人协同工作,完成特定的生产任务。
三、安全注意事项在操作 ABB 机器人之前,必须充分了解并严格遵守安全规定,以防止事故发生。
1、安装和调试阶段确保机器人安装牢固,周边环境安全无障碍物。
在调试时,应设置警示标识,防止无关人员进入工作区域。
2、操作运行阶段操作人员必须经过专业培训,熟悉机器人的操作流程和紧急停止方法。
避免在机器人运动范围内停留或进行任何可能干扰机器人运行的行为。
3、维护保养阶段在进行维护保养前,务必切断机器人的电源,并挂上“禁止合闸”的标识。
只有具备资质的人员才能进行维护保养工作。
四、机器人的启动与关闭1、启动检查机器人本体、控制器和周边设备的连接是否正常。
打开控制器电源,等待系统初始化完成。
通过示教器启动机器人,并进行必要的初始化设置。
2、关闭先停止机器人的当前任务。
通过示教器选择关闭机器人系统。
关闭控制器电源。
五、示教器的使用示教器是与机器人交互的重要工具,以下是其主要功能和操作方法。
1、界面介绍显示机器人的状态信息,如位置、速度、关节角度等。
包含编程、操作、监控等功能菜单。
机器人操作的说明书

机器人操作的说明书机器人操作手册1. 简介本机器人操作手册旨在向用户提供全面而易于理解的机器人操作指南。
通过本手册,用户可以了解机器人的基本操作方法,掌握使用机器人的技巧,以及遵守必要的安全规定,从而确保机器人的高效和安全运行。
2. 前提条件在开始操作机器人之前,请先确保以下条件已满足:2.1 供电:接通机器人的电源并确保稳定供电。
2.2 连接:将机器人与相关设备连接,并确保连接稳定可靠。
2.3 软件:安装并启动机器人操作所需的软件程序。
3. 启动机器人3.1 按下电源按钮,机器人将开始启动。
在启动期间,请确保机器人周围无障碍物,以防意外碰撞。
3.2 在机器人启动完成后,等待机器人完成自检程序。
一旦自检程序完成,机器人将进入待机模式,即待命状态。
4. 选择模式机器人提供多种模式供用户选择。
根据具体任务的要求,选择相应的模式:4.1 自动模式:机器人将自主执行任务,按照预设的程序和指令运行。
用户只需提供必要的输入参数,并监视机器人的运行状态。
4.2 手动模式:用户可以通过遥控器或者控制台手动控制机器人的运动和操作。
在手动模式下,用户可以更加灵活地控制机器人,并进行实时的调整和干预。
5. 基本操作以下是机器人的基本操作说明:5.1 运动控制:使用遥控器或者控制台上的控制按钮,控制机器人前进、后退、左转、右转等运动动作。
请注意操作时的环境安全,避免机器人与障碍物发生碰撞。
5.2 抓取物体:机器人配备抓取装置,可用于抓取和搬运物体。
在使用抓取装置时,请确保物体的重量在机器人负载范围之内,并注意物体的稳定和安全。
5.3 视觉操作:机器人配备摄像头和图像识别系统,可进行视觉操作。
通过摄像头观察环境,并使用图像识别系统对目标进行识别和跟踪。
6. 安全事项在操作机器人时,请遵守以下安全规定:6.1 注意观察:在机器人操作过程中,请始终保持警惕,注意观察机器人周围的环境,并避免与其他人员或物体发生碰撞。
6.2 安全距离:请与机器人保持安全距离,避免机器人运动时造成伤害。
机器人操作手册及使用指南(专业版)

机器人操作手册及使用指南(专业版)一、引言机器人已经成为现代社会不可或缺的一部分,为各行各业提供了许多便利。
本机器人操作手册及使用指南专为在机器人操作领域专业人士提供,旨在帮助各种机器人操作任务的顺利进行。
本手册将详细介绍机器人操作的基本原理、操作步骤以及常见问题的解决方案,以期为用户提供全面的指导和帮助。
二、基本原理1. 机器人分类机器人按照其用途和结构可以分为工业机器人、服务机器人、军用机器人等多种类型。
本手册主要关注工业机器人的操作方法和使用技巧。
2. 机器人工作原理机器人的工作原理包括感知、决策和执行三个主要步骤。
感知环节通过传感器收集环境信息,决策环节通过算法和逻辑进行任务规划和路径确定,执行环节通过执行器执行任务。
三、机器人操作步骤1. 准备工作在操作机器人之前,需要进行以下准备工作:- 确保机器人所需部件完好无损- 检查机器人的电源和供电设施是否正常- 确保机器人的控制器和程序运行正常2. 机器人启动根据具体机器人的型号和品牌,可通过以下步骤启动机器人:- 打开机器人的电源开关- 确保控制器与机器人正常连接- 检查机器人的各个节点是否在线3. 机器人操作根据具体任务需求,进行以下机器人操作:- 根据任务要求编写机器人控制程序- 将控制程序加载到机器人的控制器中- 启动机器人的执行任务4. 机器人沟通当机器人在执行任务时,可以通过以下方式与其进行沟通:- 利用机器人的语音交互系统进行语音指令- 利用机器人的触摸屏进行人机交互- 利用机器人的传感器进行姿态检测和互动五、机器人维护与故障排除1. 机器人维护为了确保机器人的正常运行,以下是一些常见的机器人维护注意事项:- 定期检查机器人的零部件是否磨损或松动- 清洁机器人的表面和传感器,避免灰尘和污渍影响机器人的工作效果- 定期校准机器人的传感器和执行器2. 故障排除在操作机器人过程中,可能会遇到各种故障,以下是一些常见故障及其解决方案:- 机器人不动:检查电源和电缆连接是否正常,检查控制器程序是否正确- 机器人动作异常:检查机器人的执行器是否正常,检查传感器是否损坏或松动- 机器人感知不准确:检查传感器是否干净,是否需要进行校准六、结论本机器人操作手册及使用指南(专业版)详细介绍了机器人操作的基本原理、操作步骤以及常见问题的解决方案。
ABB机器人操作手册
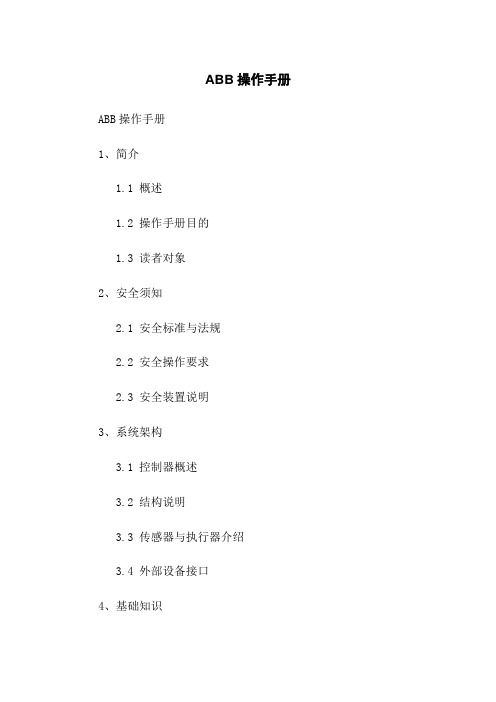
ABB操作手册ABB操作手册
1、简介
1.1 概述
1.2 操作手册目的
1.3 读者对象
2、安全须知
2.1 安全标准与法规
2.2 安全操作要求
2.3 安全装置说明
3、系统架构
3.1 控制器概述
3.2 结构说明
3.3 传感器与执行器介绍
3.4 外部设备接口
4、基础知识
4.1 坐标系
4.2 运动学
4.3 示教方式
5、操作流程
5.1 启动与关闭系统
5.2 运行基本程序
5.3 运动控制
5.4 异常处理
6、编程
6.1 编程语言介绍
6.2 基本指令与程序结构 6.3 变量与表达式
6.4 函数与子程序
6.5 任务与调度
7、维护与故障排除
7.1 维护计划
7.2 日常检查与保养
7.3 常见故障及排除方法
7.4 备件管理
8、附件
8.1 附件1:操作手册补充说明
8.2 附件2:故障排除流程图
法律名词及注释:
1.1 :根据国家《管理办法》,是自动执行人类工作的复杂机器。
2.2 安全操作要求:参考国际标准ISO10218-1和ISO10218-2,以确保操作期间的安全。
3.2 控制器:的核心部件,负责执行运动控制任务。
4.1 坐标系:操作空间的独立坐标系,用于描述位置及姿态。
6.1 编程语言介绍:编程语言包括指令语言和高级编程语言。
附件:
1、操作手册补充说明:详细描述了操作手册中特定部分的进一
步细化内容。
2、故障排除流程图:用于帮助用户在发生故障时准确诊断问题
并采取正确的解决步骤。
ABB工业机器人系统基本操作

ABB工业机器人系统基本操作一、启动机器人系统:1.按下机器人后面的电源按钮,机器人控制器将开始启动。
2.控制器启动后,显示器上将显示控制器的初始屏幕,输入密码并按下确认键。
3.控制器连接上时,按下“启动/停止”按钮,激活机器人。
二、设置工具:1.在机器人控制器的菜单中,找到“工具”选项。
2.进入“工具”选项后,可以选择现有的工具或添加新的工具。
3.设置完工具后,保存设置。
三、设置工件:1.在机器人控制器的菜单中,找到“工件”选项。
2.进入“工件”选项后,可以选择现有的工件或添加新的工件。
3.设置完工件后,保存设置。
四、创建程序:1.在机器人控制器的菜单中,找到“程序”选项。
2.进入“程序”选项后,选择“新建程序”。
3.在程序中添加所需的任务和指令,并保存程序。
五、运行程序:1.在机器人控制器的菜单中,找到“运行”选项。
2.进入“运行”选项后,选择要运行的程序。
3.根据需要选择执行方式,可以选择单步、连续、循环等执行模式。
4.按下“开始”按钮,机器人将开始执行程序。
六、监控机器人运行:1.在机器人控制器的菜单中,找到“监控”选项。
2.进入“监控”选项后,可以查看机器人的运行状态和参数。
3.可以通过监控界面对机器人的运行进行控制和调整。
七、停止机器人:1.在机器人控制器的菜单中,找到“停止”选项。
2.进入“停止”选项后,选择停止所有程序或停止当前程序。
3.按下“停止”按钮,机器人将停止运行。
八、关机机器人系统:1.在机器人控制器的菜单中,找到“关机”选项。
2.进入“关机”选项后,选择关机方式。
3.按下“确认”按钮,机器人控制器将开始关机。
本文中提到的是ABB工业机器人系统的基本操作方法,操作的具体步骤可能会因机器人型号和系统版本的不同而略有差异。
建议初次操作时,参考机器人操作手册或向ABB工作人员寻求帮助。
同时,注意在操作机器人时要遵守相关的安全规定,确保操作的安全性。
kuka机器人KRC2系统操作与编程手册

一、安全51.1 责任61。
2选用61.3 安全标示61。
4 一般安全规定61。
5关于营运者和操作者的特别安全措施71。
6 六轴机器人的死点81.7 机器人系统的安全要素:工作空间的限制81.8 机器人系统的安全要素:温度监控91。
9 机器人系统的安全要素:试运行模式91。
10 机器人的安全要素:使能按键91.11 机器人轴的松开装置91.12规划和结构:安全和工作空间101.13安装与操作101.14安装与操作:安装的安全111.15安全标记111。
16 KUKA 培训的安全指导111.17 受静电威胁的组件的处理13二、用户控制& 导航142。
1 系统概述142.1。
1 KR C2 的技术数据142.1。
2 KR C2 的PC 主机箱142。
1.3 PC- KR C2 PC 接口142。
1。
4 机器人上的序列号152.1.5 控制柜上的序列号152。
1.6 软件152。
1。
7 用户组162.2 基本术语162。
2。
1 KUKA 机器人系统的构成162.2.2 KUKA 示教器(KCP)162.2.3 机器人类型命名172。
2.4 KUKA 机器人的机械结构172.2。
5 KUKA 机器人轴的命名182.2.6 KUKA 机器人的工作范围(侧视图)182.2。
7 KUKA 机器人的工作范围(俯视图)182.2。
8 KUKA 机器人的载荷分配192.2。
9 KUKA 机器人上的负载(标准系列)192。
2.10 KR 125/2 的有效载荷表192.3 示教器202.3.1 KUKA 示教器(KCP)202。
3。
2 模式选择开关202。
3.3 模式列表202.3。
4 示教器窗口操作212.3。
5 窗口显示212。
3。
6窗口选择键212.3。
7软按键222.3。
8 状态窗口222.3.9消息窗口222.3。
10消息类型222.3.11 示教器运行程序232.3。
12 数字小键盘232.3.13 ASCII 字母键盘242。
kuka机器人操作与编程手册

KUKA机器人操作与编程手册简介KUKA机器人是德国KUKA机器人公司(KULG)生产的工业机器人。
它们被广泛应用于汽车制造、电子制造、建筑等各个领域。
本手册旨在为初学者提供一些关于KUKA机器人操作和编程的基础知识。
操作手册1. KUKA机器人的启动和关闭KUKA机器人的启动和关闭是使用KUKA KR C4控制器进行操作的。
下面是启动和关闭机器人的步骤:1.打开控制器电源2.使用控制器上的开关将机器人系统启动3.等待机器人系统自检完成4.通过控制器进行机器人的操作5.关闭机器人系统前,确保机器人处于安全位置6.使用控制器上的开关关闭机器人系统2. 机器人的基本移动KUKA机器人具有多种不同类型的运动,包括直线运动、旋转运动和关节运动。
下面是一些基本的机器人移动指令示例:•直线运动:LIN X100 Y100 Z100 A45 B45 C45•旋转运动:CIRC P100 P200 R50•关节运动:JNT J1=90 J2=453. 机器人编程语言KUKA机器人使用KRL(KUKA Robot Language)作为其编程语言。
KRL是一种结构化编程语言,类似于C或Pascal。
下面是一个简单的KRL程序示例:DEF myProgram()DECL int iDECL bool conditioni = 0condition = trueWHILE condition DOINC iIF i == 10 THENcondition = falseENDIFENDWHILEENDDEF4. 机器人的传感器和反馈KUKA机器人可以配备各种传感器,以便实时监测机器人的状态和周围环境的信息。
一些常见的传感器包括力传感器、视觉传感器和温度传感器。
通过这些传感器,机器人可以感知和适应外部环境的变化。
5. 机器人的安全措施在操作KUKA机器人时,安全是至关重要的。
以下是一些常见的机器人安全措施:•确保机器人周围没有障碍物•执行安全风险评估,并根据评估结果制定相应的操作计划•对机器人进行定期维护和检查,确保其正常运行•使用必要的个人防护设备,例如手套和护目镜结论本手册提供了初学者入门KUKA机器人操作和编程的基本知识。
SINUMERIK SINUMERIK ONE 机器人控制系统操作手册说明书

SINUMERIKSINUMERIK ONEMillingOperating ManualValid for:SINUMERIK ONESoftware versionCNC system software for SINUMERIK ONE V6.20 SINUMERIK Operate for PCU/PC V6.2007/2022A5E48384797B ADLegal information Warning notice systemThis manual contains notices you have to observe in order to ensure your personal safety, as well as to prevent damage to property. The notices referring to your personal safety are highlighted in the manual by a safety alert symbol, notices referring only to property damage have no safety alert symbol. These notices shown below are graded according tothe degree of danger.DANGERindicates that death or severe personal injury will result if proper precautions are not taken.WARNINGindicates that death or severe personal injury may result if proper precautions are not taken.CAUTIONindicates that minor personal injury can result if proper precautions are not taken.NOTICEindicates that property damage can result if proper precautions are not taken.If more than one degree of danger is present, the warning notice representing the highest degree of danger will be used. A notice warning of injury to persons with a safety alert symbol may also include a warning relating to property damage.Qualified PersonnelThe product/system described in this documentation may be operated only bypersonnel qualified for the specific task in accordance with the relevant documentation, in particular its warning notices and safety instructions. Qualified personnel are those who, based on their training and experience, are capable of identifying risks and avoiding potential hazards when working with these products/systems.Proper use of Siemens productsNote the following:WARNINGSiemens products may only be used for the applications described in the catalog and in the relevant technical documentation. If products and components from other manufacturers are used, these must be recommended or approved by Siemens. Proper transport, storage, installation, assembly, commissioning, operation and maintenance are required to ensure that the products operate safely and without any problems. The permissible ambient conditions must be complied with. The information in the relevant documentation must be observed.TrademarksAll names identified by ® are registered trademarks of Siemens AG. The remaining trademarks in this publication may be trademarks whose use by third parties for their own purposes could violate the rights of the owner.Disclaimer of LiabilityWe have reviewed the contents of this publication to ensure consistency with the hardware and software described. Since variance cannot be precluded entirely, we cannot guarantee full consistency. However, the information in this publication is reviewed regularly and any necessary corrections are included in subsequent editions.Siemens AGDigital Industries Postfach 48 4890026 NÜRNBERG GERMANYA5E48384797B ADⓅ 06/2022 Subject to change Copyright © Siemens AG 2019 - 2022.All rights reservedTable of contents1Introduction (17)1.1About SINUMERIK (17)1.2About this documentation (18)1.3Documentation on the internet (20)1.3.1Documentation overview SINUMERIK ONE (20)1.3.2Documentation overview SINUMERIK operator components (20)1.4Feedback on the technical documentation (22)1.5mySupport documentation (23)1.6Service and Support (24)1.7Important product information (26)2Fundamental safety instructions (27)2.1General safety instructions (27)2.2Warranty and liability for application examples (28)2.3Security information (29)3Fundamentals (31)3.1Product overview (31)3.2Operator panel fronts (32)3.2.1Overview (32)3.2.2Keys of the operator panel (34)3.3Machine control panels (42)3.3.1Overview (42)3.3.2Controls on the machine control panel (42)3.4User interface (46)3.4.1Screen layout (46)3.4.2Status display (47)3.4.3Actual value window (49)3.4.4T,F,S window (51)3.4.5Operation via softkeys and buttons (53)3.4.6Entering or selecting parameters (54)3.4.7Pocket calculator (56)3.4.8Pocket calculator functions (57)3.4.9Context menu (59)3.4.10Changing the user interface language (59)3.4.11Entering Chinese characters (60)3.4.11.1Function - input editor (60)3.4.11.2Entering Asian characters (62)3.4.12Entering Korean characters (63)3.4.13Protection levels (65)MillingOperating Manual, 07/2022, A5E48384797B AD3Table of contents3.4.14Work station safety (67)3.4.15Cleaning mode (67)3.4.16Display live image from a camera (68)3.4.17Online help in SINUMERIK Operate (69)4Multitouch operation with SINUMERIK Operate (73)4.1Multitouch panels (73)4.2Touch-sensitive user interface (74)4.3Finger gestures (75)4.4Multitouch user interface (78)4.4.1Screen layout (78)4.4.2Function key block (79)4.4.3Further operator touch controls (80)4.4.4Virtual keyboard (80)4.4.5Special "tilde" character (81)4.5Expansion with side screen (82)4.5.1Overview (82)4.5.2Sidescreen with standard windows (82)4.5.3Standard widgets (84)4.5.4"Actual value" widget (84)4.5.5"Zero point" widget (85)4.5.6"Alarms" widget (85)4.5.7"NC/PLC variables" widget (85)4.5.8"Axle load" widget (86)4.5.9"Tool" widget (86)4.5.10"Service life" widget (87)4.5.11"Program runtime" widget (87)4.5.12Widget "Camera 1" and "Camera 2" (87)4.5.13Sidescreen with pages for the ABC keyboard and/or machine control panel (88)4.5.14Example 1: ABC keyboard in the sidescreen (89)4.5.15Example 2: Machine control panel in the sidescreen (90)4.6SINUMERIK Operate Display Manager (91)4.6.1Overview (91)4.6.2Screen layout (92)4.6.3Operator controls (92)5Setting up the machine (97)5.1Switching on and switching off (97)5.2Approaching a reference point (98)5.2.1Referencing axes (98)5.2.2User agreement (99)5.3Operating modes (101)5.3.1General (101)5.3.2Modes groups and channels (103)5.3.3Channel switchover (103)5.4Settings for the machine (105)5.4.1Switching over the coordinate system (MCS/WCS) (105)5.4.2Switching the unit of measurement (105)Milling 4Operating Manual, 07/2022, A5E48384797B ADTable of contents5.4.3Setting the zero offset (107)5.5Measure tool (109)5.5.1Overview (109)5.5.2Manually measuring drilling and milling tools (109)5.5.3Measuring drilling and milling tools with the workpiece reference point (110)5.5.4Measuring drilling and milling tools with fixed reference point (111)5.5.5Measuring radius or diameter (112)5.5.6Fixed point calibration (113)5.5.7Measuring the drilling and milling tool length with electrical tool probe (113)5.5.8Calibrating the electrical tool probe (116)5.5.9Manually measuring a turning tool (for milling/turning machine) (117)5.5.10Manually measuring a turning tool using a tool probe (for milling/turning machine) (118)5.5.11Logging tool measurement results (120)5.6Measuring the workpiece zero (122)5.6.1Overview (122)5.6.2Sequence of operations (126)5.6.3Examples with manual swiveling (swiveling in JOG mode) (127)5.6.4Setting the edge (128)5.6.5Edge measurement (129)5.6.6Measuring a corner (134)5.6.7Measuring a pocket and hole (137)5.6.8Measuring a spigot (140)5.6.9Aligning the plane (145)5.6.10Defining the measurement function selection (147)5.6.11Logging measurement results for the workpiece zero (148)5.6.12Calibrating the electronic workpiece probe (149)5.6.12.1Calibration of length and radius or diameter (149)5.6.12.2Calibrate on sphere (151)5.7Settings for the measurement result log (153)5.8Zero offsets (155)5.8.1Display active zero offset (156)5.8.2Displaying the zero offset "overview" (157)5.8.3Displaying and editing base zero offset (158)5.8.4Displaying and editing settable zero offset (159)5.8.5Displaying and editing details of the zero offsets (160)5.8.6Deleting a zero offset (161)5.8.7Measuring the workpiece zero (162)5.9Monitoring axis and spindle data (164)5.9.1Specify working area limitations (164)5.9.2Editing spindle data (164)5.10Displaying setting data lists (166)5.11Handwheel assignment (167)5.12MDA (169)5.12.1Saving an MDA program (169)5.12.2Editing/executing a MDI program (170)5.12.3Deleting an MDA program (171)MillingOperating Manual, 07/2022, A5E48384797B AD5Table of contents6Execution in manual mode (173)6.1General (173)6.2Selecting a tool and spindle (174)6.2.1T, S, M windows (174)6.2.2Selecting a tool (176)6.2.3Starting and stopping a spindle manually (176)6.2.4Position spindle (177)6.3Traversing axes (179)6.3.1Traverse axes by a defined increment (179)6.3.2Traversing axes by a variable increment (180)6.4Positioning axes (181)6.5Swiveling (182)6.6Manual retraction (187)6.7Simple face milling of the workpiece (188)6.8Simple workpiece machining operations with milling/turning machines (191)6.8.1Simple workpiece face milling (milling/turning machine) (191)6.8.2Simple stock removal of workpiece (for milling/turning machine) (193)6.9Default settings for manual mode (197)7Machining the workpiece (199)7.1Starting and stopping machining (199)7.2Selecting a program (201)7.3Testing a program (202)7.4Displaying the current program block (203)7.4.1Displaying a basic block (203)7.4.2Display program level (203)7.5Correcting a program (205)7.6Repositioning axes (206)7.7Starting machining at a specific point (207)7.7.1Use block search (207)7.7.2Continuing program from search target (209)7.7.3Simple search target definition (210)7.7.4Defining an interruption point as search target (210)7.7.5Entering the search target via search pointer (211)7.7.6Parameters for block search in the search pointer (212)7.7.7Block search mode (212)7.7.8Block search for position pattern (215)7.8Controlling the program run (217)7.8.1Program control (217)7.8.2Use Powerride for program control (219)7.8.3Skip blocks (219)7.9Overstore (221)7.10Editing a program (223)Milling 6Operating Manual, 07/2022, A5E48384797B ADTable of contents7.10.1Searching in programs (223)7.10.2Replacing program text (225)7.10.3Copying/pasting/deleting a program block (226)7.10.4Renumbering a program (228)7.10.5Creating a program block (229)7.10.6Opening additional programs (230)7.10.7Editor settings (231)7.11Working with DXF files (235)7.11.1Overview (235)7.11.2Displaying CAD drawings (236)7.11.2.1Open a DXF file (236)7.11.2.2Cleaning a DXF file (236)7.11.2.3Enlarging or reducing the CAD drawing (237)7.11.2.4Changing the section (238)7.11.2.5Rotating the view (238)7.11.2.6Displaying/editing information for the geometric data (239)7.11.3Importing and editing a DXF file in the editor (240)7.11.3.1General procedure (240)7.11.3.2Specifying a reference point (240)7.11.3.3Assigning the machining plane (241)7.11.3.4Setting the tolerance (241)7.11.3.5Selecting the machining range / deleting the range and element (242)7.11.3.6Saving the DXF file (243)7.11.3.7Transferring the drilling positions (244)7.11.3.8Accepting contours (246)7.12Importing shapes from CAD programs (250)7.12.1Reading in CAD data into an editor and processing (252)7.12.1.1General procedure (252)7.12.1.2Import from CAD (252)7.12.1.3Defining reference points (253)7.12.1.4Viewing point information (256)7.12.1.5Creating a new contour (257)7.12.1.6Accepting the machining steps (258)7.13Display and edit user variables (260)7.13.1Overview (260)7.13.2Global R parameters (261)7.13.3R parameters (262)7.13.4Displaying global user data (GUD) (264)7.13.5Displaying channel GUDs (265)7.13.6Displaying local user data (LUD) (266)7.13.7Displaying program user data (PUD) (267)7.13.8Searching for user variables (267)7.14Displaying G Functions and Auxiliary Functions (270)7.14.1Selected G functions (270)7.14.2All G functions (272)7.14.3G functions for mold making (272)7.14.4Auxiliary functions (273)7.15Displaying superimpositions (275)7.16Mold making view (278)MillingOperating Manual, 07/2022, A5E48384797B AD7Table of contents7.16.1Overview (278)7.16.2Starting the mold making view (280)7.16.3Adapting the mold making view (280)7.16.4Specifically jump to the program block (281)7.16.5Searching for program blocks (282)7.16.6Changing the view (283)7.16.6.1Enlarging or reducing the graphical representation (283)7.16.6.2Moving and rotating the graphic (284)7.16.6.3Modifying the viewport (284)7.17Displaying the program runtime and counting workpieces (286)7.18Setting for automatic mode (288)8Simulating machining (291)8.1Overview (291)8.2Simulation before machining of the workpiece (299)8.3Simultaneous recording before machining of the workpiece (300)8.4Simultaneous recording during machining of the workpiece (301)8.5Setting the model quality (302)8.6Different views of the workpiece (303)8.6.1Plan view (303)8.6.23D view (304)8.6.3Side view (304)8.6.4Turning view (305)8.6.5Half section (305)8.7Editing the simulation display (307)8.7.1Blank display (307)8.7.2Showing and hiding the tool path (307)8.8Program control during the simulation (308)8.8.1Changing the feedrate (308)8.8.2Simulating the program block by block (309)8.9Changing and adapting a simulation graphic (310)8.9.1Enlarging or reducing the graphical representation (310)8.9.2Panning a graphical representation (311)8.9.3Rotating the graphical representation (311)8.9.4Modifying the viewport (312)8.9.5Defining cutting planes (312)8.10Displaying simulation alarms (314)9Generating a G code program (315)9.1Graphical programming (315)9.2Program views (316)9.3Program structure (320)9.4Fundamentals (321)9.4.1Machining planes (321)9.4.2Current planes in cycles and input screens (321)Milling 8Operating Manual, 07/2022, A5E48384797B ADTable of contents9.4.3Programming a tool (T) (322)9.5Generating a G code program (323)9.6Blank input (324)9.7Machining plane, milling direction, retraction plane, safe clearance and feedrate (PL, RP,SC, F) (326)9.8Selection of the cycles via softkey (327)9.9Calling technology functions (331)9.9.1Hiding cycle parameters (331)9.9.2Setting data for cycles (331)9.9.3Checking cycle parameters (331)9.9.4Programming variables (332)9.9.5Changing a cycle call (332)9.9.6 Compatibility for cycle support (333)9.9.7Additional functions in the input screens (333)9.10Measuring cycle support (334)10Creating a ShopMill program (335)10.1Program views (336)10.2Program structure (341)10.3Fundamentals (342)10.3.1Machining planes (342)10.3.2Polar coordinates (342)10.3.3Absolute and incremental dimensions (343)10.4Creating a ShopMill program (346)10.5Program header (347)10.6Program header (for milling/turning machine) (349)10.7Generating program blocks (352)10.8Tool, offset value, feed and spindle speed (T, D, F, S, V) (353)10.9Defining machine functions (355)10.10Call work offsets (357)10.11Repeating program blocks (358)10.12Specifying the number of workpieces (360)10.13Changing program blocks (361)10.14Changing program settings (362)10.15Selection of the cycles via softkey (364)10.16Calling technology functions (369)10.16.1Additional functions in the input screens (369)10.16.2Checking input parameters (369)10.16.3Setting data for technological functions (369)10.16.4Changing a cycle call (370)10.16.5Programming variables (370)10.16.6 Compatibility for cycle support (371)MillingOperating Manual, 07/2022, A5E48384797B AD9Table of contents10.17Measuring cycle support (372)10.18Example, standard machining (373)10.18.1Workpiece drawing (374)10.18.2Programming (374)10.18.3Results/simulation test (386)10.18.4G code machining program (388)11Programming technological functions (cycles) (391)11.1Know-how protection (391)11.2Drilling (392)11.2.1General (392)11.2.2Centering (CYCLE81) (393)11.2.3Drilling (CYCLE82) (394)11.2.4Reaming (CYCLE85) (398)11.2.5Deep-hole drilling 1 (CYCLE83) (399)11.2.6Deep-hole drilling 2 (CYCLE830) (405)11.2.7Boring (CYCLE86) (415)11.2.8Tapping (CYCLE84, 840) (417)11.2.9Drill and thread milling (CYCLE78) (424)11.2.10Positioning and position patterns (428)11.2.11Arbitrary positions (CYCLE802) (430)11.2.12Row position pattern (HOLES1) (433)11.2.13Grid or frame position pattern (CYCLE801) (434)11.2.14Circle or pitch circle position pattern (HOLES2) (436)11.2.15Displaying and hiding positions (438)11.2.16Repeating positions (440)11.3Milling (441)11.3.1Face milling (CYCLE61) (441)11.3.2Rectangular pocket (POCKET3) (443)11.3.3Circular pocket (POCKET4) (450)11.3.4Rectangular spigot (CYCLE76) (457)11.3.5Circular spigot (CYCLE77) (462)11.3.6Multi-edge (CYCLE79) (466)11.3.7Longitudinal groove (SLOT1) (470)11.3.8Circumferential groove (SLOT2) (476)11.3.9Open groove (CYCLE899) (482)11.3.10Long hole (LONGHOLE) - only for G code programs (491)11.3.11Thread milling (CYCLE70) (493)11.3.12Engraving (CYCLE60) (497)11.4Contour milling (504)11.4.1General (504)11.4.2Representation of the contour (504)11.4.3Creating a new contour (506)11.4.4Creating contour elements (507)11.4.5Changing the contour (512)11.4.6Contour call (CYCLE62) - only for G code program (513)11.4.7Path milling (CYCLE72) (514)11.4.8Contour pocket/contour spigot (CYCLE63/64) (519)11.4.9Predrilling contour pocket (CYCLE64) (521)11.4.10Milling contour pocket (CYCLE63) (524)Milling 10Operating Manual, 07/2022, A5E48384797B ADTable of contents 11.4.11Residual material contour pocket (CYCLE63) (529)11.4.12Milling contour spigot (CYCLE63) (530)11.4.13Residual material contour spigot (CYCLE63) (534)11.5Turning - milling/turning machine (537)11.5.1General (537)11.5.2Stock removal (CYCLE951) (537)11.5.3Groove (CYCLE930) (541)11.5.4Undercut form E and F (CYCLE940) (545)11.5.5Thread undercut (CYCLE940) (551)11.5.6Thread turning (CYCLE99), only for G code (557)11.5.6.1Special aspects of the selection alternatives for infeed depths (584)11.5.7Thread chain (CYCLE98) (585)11.5.7.1Special aspects of the selection alternatives for infeed depths (594)11.5.8Cut-off (CYCLE92) (595)11.6Contour turning - Milling/turning machine (599)11.6.1General information (599)11.6.2Representation of the contour (600)11.6.3Creating a new contour (601)11.6.4Creating contour elements (603)11.6.5Changing the contour (610)11.6.6Contour call (CYCLE62) (611)11.6.7Stock removal (CYCLE952) (612)11.6.8Stock removal residual (CYCLE952) (627)11.6.9Grooving (CYCLE952) (630)11.6.10Grooving residual material (CYCLE952) (641)11.6.11Plunge turning (CYCLE952) (645)11.6.12Plunge turning residual material (CYCLE952) (655)11.7Further cycles and functions (660)11.7.1Swivel plane (CYCLE800) (660)11.7.1.1Cylinder surface transformation with swivel plane (667)11.7.2Swiveling tool (CYCLE800) (671)11.7.2.1Swiveling tool/preloading milling tools - only for G code program (CYCLE800) (671)11.7.2.2Aligning turning tools (CYCLE800) - millling/turning machine (672)11.7.3High-speed settings (CYCLE832) (677)11.7.4Subroutines (681)11.7.5Adapt to load (CYCLE782) (683)11.7.6Interpolation turning (CYCLE806) (685)11.7.6.1Function (685)11.7.6.2Selecting/deselecting interpolation turning - CYCLE806 (686)11.7.6.3Calling the cycle (687)11.7.6.4Parameter (687)11.8Additional cycles and functions in ShopMill (688)11.8.1Transformations (688)11.8.2Translation (689)11.8.3Rotation (689)11.8.4Scaling (690)11.8.5Mirroring (691)11.8.6Cylinder surface transformation (691)11.8.7Straight or circular machining (694)11.8.8Programming a straight line (696)Table of contents11.8.9Programming a circle with known center point (697)11.8.10Programming a circle with known radius (698)11.8.11Helix (699)11.8.12Polar coordinates (700)11.8.13Straight polar (701)11.8.14Circle polar (701)11.8.15Obstacle (702)12Multi-channel view (705)12.1Multi-channel view (705)12.2Multi-channel view in the "Machine" operating area (706)12.3Multi-channel view for large operator panels (709)12.4Setting the multi-channel view (711)13Collision avoidance (713)13.1Activate collision avoidance (715)13.2Set collision avoidance (716)14Tool management (719)14.1Lists for the tool management (719)14.2Magazine management (721)14.3Tool types (722)14.4Tool dimensioning (725)14.5Tool list (732)14.5.1Additional data (735)14.5.2Creating a new tool (736)14.5.3Measuring the tool (738)14.5.4Managing several cutting edges (738)14.5.5Delete tool (739)14.5.6Loading and unloading tools (739)14.5.7Selecting a magazine (741)14.5.8Code carrier connection (742)14.5.9Managing a tool in a file (744)14.6Tool wear (747)14.6.1Reactivating a tool (749)14.7Tool data OEM (751)14.8Magazine (752)14.8.1Positioning a magazine (754)14.8.2Relocating a tool (754)14.8.3Deleting / unloading / loading / relocating all tools (755)14.9Tool details (757)14.9.1Displaying tool details (757)14.9.2Tool data (757)14.9.3Cutting edge data (758)14.9.4Monitoring data (760)14.10Changing a tool type (761)Table of contents14.11Graphic display (762)14.12Sorting tool management lists (764)14.13Filtering the tool management lists (765)14.14Specific search in the tool management lists (767)14.15Multiple selection in the tool management lists (769)14.16Settings for tool lists (770)14.17Working with Multitool (771)14.17.1Tool list for multitool (771)14.17.2Create multitool (772)14.17.3Equipping multitool with tools (774)14.17.4Removing a tool from multitool (775)14.17.5Deleting multitool (776)14.17.6Loading and unloading multitool (776)14.17.7Reactivating the multitool (777)14.17.8Relocating a multitool (778)14.17.9Positioning a multitool (779)15Managing programs (781)15.1Overview (781)15.1.1NC memory (784)15.1.2Local drive (784)15.1.3USB drives (786)15.1.4FTP drive (786)15.2Opening and closing the program (788)15.3Executing a program (790)15.4Creating a directory / program / job list / program list (792)15.4.1File and directory names (792)15.4.2Creating a new directory (792)15.4.3Creating a new workpiece (793)15.4.4Creating a new G code program (794)15.4.5Creating a new ShopMill program (794)15.4.6Storing any new file (795)15.4.7Creating a job list (796)15.4.8Creating a program list (798)15.5Creating templates (799)15.6Searching directories and files (800)15.7Displaying the program in the Preview (802)15.8Selecting several directories/programs (803)15.9Copying and pasting a directory/program (805)15.10Deleting a program/directory (807)15.10.1Deleting a program/directory (807)15.11Changing file and directory properties (808)15.12Set up drives (810)Table of contents15.12.1Overview (810)15.12.2Setting up drives (810)15.13Viewing PDF documents (816)15.14EXTCALL (819)15.15Execution from external memory (EES) (821)15.16Backing up data (822)15.16.1Generating an archive in the Program Manager (822)15.16.2Generating an archive via the system data (823)15.16.3Reading in an archive in the Program Manager (825)15.16.4Read in archive from system data (826)15.17Setup data (828)15.17.1Backing up setup data (828)15.17.2Reading-in set-up data (830)15.18Recording tools and determining the demand (832)15.18.1Overview (832)15.18.2Opening tool data (833)15.18.3Checking the loading (833)15.19Backing up parameters (835)15.20RS-232-C (838)15.20.1Reading-in and reading-out archives via a serial interface (838)15.20.2Setting V24 in the program manager (839)15.21Multiple clamping (841)15.21.1Multiple clamping (841)15.21.2Program header setting, "Clamping" (842)15.21.3Creating a multiple clamping program (843)16Service and diagnostics (845)16.1Alarm, error, and system messages (845)16.1.1Displaying alarms (845)16.1.2Displaying an alarm log (847)16.1.3Displaying messages (848)16.1.4Sorting, alarms, faults and messages (848)16.1.5Deactivating system alarms (849)16.2PLC and NC variables (851)16.2.1Displaying and editing PLC and NC variables (851)16.2.2Saving and loading screen forms (855)16.3Creating screenshots (856)16.4Version (857)16.4.1Displaying version data (857)16.4.2Save information (858)16.5Logbook (860)16.5.1Displaying and editing the logbook (860)16.5.2Making a logbook entry (861)16.6Remote diagnostics (863)16.6.1Setting remote access (863)Table of contents16.6.2Permit modem (864)16.6.3Request remote diagnostics (865)16.6.4Exit remote diagnostics (866)17Working with Manual Machine (867)17.1Manual Machine (867)17.2Measuring the tool (869)17.3Measuring the workpiece zero (870)17.4Setting the zero offset (871)17.5Set limit stop (872)17.6Simple workpiece machining (873)17.6.1Traversing axes (873)17.6.2Angular milling (874)17.6.3Straight and circular machining (875)17.6.3.1Straight milling (875)17.6.3.2Circular milling (876)17.7More complex machining (878)17.7.1Drilling with Manual Machine (879)17.7.2Milling with Manual Machine (880)17.7.3Contour milling with manual machine (881)17.7.4Turning with manual machine - milling/turning machine (881)17.8Simulation and simultaneous recording (883)18Teaching in a program (885)18.1Overview (885)18.2Select teach in mode (887)18.3Processing a program (888)18.3.1Inserting a block (888)18.3.2Editing a block (888)18.3.3Selecting a block (889)18.3.4Deleting a block (889)18.4Teach sets (891)18.4.1Input parameters for teach-in blocks (892)18.5Settings for teach-in (894)19Handheld terminals for multi-touch operation (895)19.1HT 8 (895)19.1.1HT 8 overview (895)19.1.2Traversing keys (897)19.1.3Machine control panel menu (898)19.1.4Virtual keyboard (900)19.2HT 10 (902)19.2.1HT 10: Overview (902)19.2.2Machine control panel menu (904)19.2.3Virtual keyboard (906)19.3Calibrating the touch panel (907)Table of contents20Ctrl-Energy (909)20.1Functions (909)20.2Ctrl-E analysis (910)20.2.1Displaying energy consumption (910)20.2.2Displaying the energy analyses (911)20.2.3Measuring and saving the energy consumption (912)20.2.4Tracking measurements (913)20.2.5Tracking usage values (913)20.2.6Comparing usage values (914)20.2.7Long-term measurement of the energy consumption (915)20.3Ctrl-E profiles (916)20.3.1Creating and editing energy-saving profiles (916)20.3.2Using the energy-saving profile (919)Index (921)。
- 1、下载文档前请自行甄别文档内容的完整性,平台不提供额外的编辑、内容补充、找答案等附加服务。
- 2、"仅部分预览"的文档,不可在线预览部分如存在完整性等问题,可反馈申请退款(可完整预览的文档不适用该条件!)。
- 3、如文档侵犯您的权益,请联系客服反馈,我们会尽快为您处理(人工客服工作时间:9:00-18:30)。
机器人系统操作手册专机部分一、检查1、动力电压交流400V 230V,如果打开柜门小心有电。
2、控制电源直流24V3、气压大于0.6兆帕二、上电图2-1 图2-1为未上电状态,如果需要上电需要做好上电前准备:1、检查急停开关是否复位;2、手动/自动开关打到手动;3、无报警信息;4、按下按钮,系统上电;5、上电正常注:紧急状况下,拍下急停按钮,系统断电。
系统复位按钮按下系统复位,可复位故障信息。
急停复位按钮按下急停复位蜂鸣器复位按钮按下可在故障发生时停止蜂鸣器灯测试按钮按下指示灯全亮,检测指示灯是否无输出HOME循环按钮按下设备回到HOME点,即设备初始位置系统暂停按钮按下专机和机器人进入暂停状态,再次按下暂停状态取消三、运行一)自动启动1、将手动/自动按钮切换到自动位置后,控制面板显示状态如下图所示,2、按下系统启动按钮系统启动,控制面板状态下图所示。
3、自动启动完成二)自动状态及单机控制(HMI)1、主画面(仅供参考)主画面,见上图,为设备上电后自动进入的默认页面。
(不同的区域设备号不同,以下以分拣C20为例)设备1723—>1#专机设备1723&1718 –> 1#机器人设备1718—>2#专机设备1713—>3#专机设备1713&1718 –> 2#机器人设备1708—>4#专机设备1708&1703 –> 3#机器人设备1703—>5#专机设备1698—>6#专机设备1698&1703 –> 4#机器人状态显示区:主画面左侧区域为状态显示区,主要显示设备的工作状态,每个工作状态对应一种颜色,例如:故障是紫色,准备好是黄色,运行是绿色。
专机选择区:主画面右侧区域为专机选择区,在自动运行过程中如果需要单台专机单独控制,选择对应按钮进入相应的画面即可。
报警信息区:主画面中下部区域为报警信息区,如果报警发生,此区域只显示简明的报警信息,具体报警内容还要参考报警页面内的内容。
操作按钮区:报警页面(F1) :进入报警画面,主要记录设备运行过程中出现的错误记录,详情见四故障处理。
主页面(F2) :设备上电后HMI启动的默认界面。
机器人(F3) :点击进入机器人画面。
手动页面(F4) :点击后进入手动操作页面。
选择设定(F5) :功能选择页面。
输入端子(F6) :西门子PLC输入端子状态显示页面。
输出端子(F7) :西门子PLC输出端子状态像是页面。
退出系统(F8) :HMI系统退出。
信息显示区:依次显示为:供货商标志系统名称时间甲方标志时间设置窗口,点击日期时间栏即可弹出次窗口,按照绿色条框的时间数据格式输入当前日期时间完成后“确认”按钮即可,如果放弃选择“取消”按钮。
2、机器人画面具体操作见屏幕提示说明。
3、手动画面点击红框区域画面转到手动画面。
专机手动操作画面。
正转启动,按钮第一次点击输送链条正向输入启动,底色变红;第二次点击正向输入停止,底色恢复绿色,或托盘输送到位自动停止。
隔板手指上升,按钮第一次点击龙门下降,底色变红;第二次点击龙门上升,底色恢复绿色。
手指插入,按钮第一次点击手指插入,底色变红;第二次点击手指退出,底色恢复绿色。
定位销上升,按钮第一次点击定位销上升,底色变红;第二次点击定位销下降,底色恢复绿色。
隔板拉开,按钮第一次点击手指拉开,底色变红;第二次点击手指闭合,底色恢复绿色。
电池顶升,按钮第一次点击电池顶起机构上升,底色变红;第二次点击电池顶起机构落下,底色恢复绿色。
反转启动,按钮第一次点击输送链条反向输入启动,底色变红;第二次点击反向输入停止,底色恢复绿色,或托盘送出到位自动停止。
专机1,按钮切换到专机1手动操作界面。
专机2,按钮切换到专机2手动操作界面。
专机3,按钮切换到专机3手动操作界面。
专机4,按钮切换到专机4手动操作界面。
专机5,按钮切换到专机5手动操作界面。
专机6,按钮切换到专机6手动操作界面。
注:此处说明仅以专机一画面为例,共六台专机,每台操作方式都相同。
4、自动运行监控及控制画面专机单机控制画面显示当前工作专机中的托盘任务号显示当前工作专机的工作状态,1表示单次抓取电池任务完成;2表示专机准备好向上位机申请托盘数据;3表示上位机任务分配完成,专机开始工作;4表示托盘分选完毕退出专机。
平时状态时底色是黄色,专机收到线体发送的接货申请信号后底色变成蓝色。
平时状态时底色是黄色,专机发送给线体的接货允许信号后专机允许线体输送新托盘,同时启动新托盘送入传送信号,底色变成蓝色。
平时状态时底色是黄色,专机检测到托盘进入后发送给线体接货完成信号,底色变成蓝色。
平时状态时底色是黄色,专机接收到上位机发送的托盘内分选完成信号(标志位=4)后向线体发送送货申请信号,底色变成蓝色。
平时状态时底色是黄色,专机发送送货申请信号后,线体工作允许则返回送货允许信号,专机可以向线体输送空托盘,底色变成蓝色。
平时状态时底色是黄色,线体接收到空托盘后向专机发出送货完成信号,底色变成蓝色。
注:1、线体是指托盘输送线;2、专机是指托盘电池取出机构;3、上位机是指软件控制系统。
在专机自动运行状态时,单台专机如果需要手动控制或者自动运行再次启动后可以用以下功能按钮实现控制的接续:按下后,1#专机单独转化为手动状态,其他按钮。
按下后,在1#专机手动状态时,1#专机初始化运行,专机各个部分自动依次返回初始位置。
备用。
1#专机内电池托盘准备好(龙门下降到位、指拨器插入到位以及托盘为新进入托盘)后,机器人自动取隔板。
1#专机电池顶出后机器人自动运行断开从新启动后,点击此按钮则机器人继续抓取电池。
1#专机电池抓取完毕后,点击此按钮则机器人开始放隔板。
注:专机共有六台,具体操作方式参考1#专机。
四、故障系统故障1系统未上电系统未上电,选择手动后点击系统上电按钮2控制柜急停按钮按下急停按下,故障消除后复位急停按钮3安全门未关闭安全门未关闭,请检查安全门是否关闭4主气路气压故障主气路压力不足 6 Bar,请检查气源是否正常1#专机故障1 指拨器插入错误专机一指拨器插入不到位,请检查磁环开关或者气缸2 指拨器退回错误专机一指拨器退回不到位,请检查磁环开关或者气缸3 指拨器打开错误专机一指拨器打开不到位,请检查磁环开关或者气缸4 指拨器关闭错误专机一指拨器关闭不到位,请检查磁环开关或者气缸5 电池顶升错误专机一电池顶升不到位,请检查磁环开关或者气缸6 电池下降错误专机一电池下降不到位,请检查磁环开关或者气缸7 龙门下降错误专机一龙门下降不到位,请检查磁环开关或者气缸8 龙门上升错误专机一龙门上升不到位,请检查磁环开关或者气缸9 定位销定位错误专机一定位销上升不到位,请检查磁环开关或者气缸10 定位销下降错误专机一定位销下降不到位,请检查磁环开关或者气缸空托盘1733未就位专机11电池分选目标1733托盘没有准备好一12 空托盘1732未就位专机电池分选目标1732托盘没有准备好一13 托盘数据为零专机一待分选托盘内没有电池14 输送进入错误专机一托盘输送进入专机超时,请检查托盘正否正常15 输送出去错误专机一托盘输送送出专机超时,请检查托盘是否正常16 指拨器进出错误专机一运行错误,请检查进出的输入输出信号是否正常17 指拨器开关错误专机一运行错误,请检查进出的输入输出信号是否正常18 电池升降错误专机一运行错误,请检查进出的输入输出信号是否正常19 龙门升降错误专机一运行错误,请检查进出的输入输出信号是否正常20 定位销错误专机一运行错误,请检查进出的输入输出信号是否正常21 输送链条错误专机一运行错误,请检查进出的输入输出信号是否正常22 变频器报警专机一请查看变频器屏幕,详见施耐德ATV312变频器说明书2#专机故障1 指拨器插入错误专机二指拨器插入不到位,请检查磁环开关或者气缸2 指拨器退回错误专机二指拨器退回不到位,请检查磁环开关或者气缸3 指拨器打开错误专机二指拨器打开不到位,请检查磁环开关或者气缸4 指拨器关闭错误专机二指拨器关闭不到位,请检查磁环开关或者气缸5 电池顶升错误专机二电池顶升不到位,请检查磁环开关或者气缸6 电池下降错误专机二电池下降不到位,请检查磁环开关或者气缸7 龙门下降错误专机二龙门下降不到位,请检查磁环开关或者气缸8 龙门上升错误专机二龙门上升不到位,请检查磁环开关或者气缸9 定位销定位错误专机二定位销上升不到位,请检查磁环开关或者气缸10 定位销下降错误专机二定位销下降不到位,请检查磁环开关或者气缸11 空托盘1733未就位专机二电池分选目标1733托盘没有准备好12 空托盘1732未就位专机二电池分选目标1732托盘没有准备好13 托盘数据为零专机二待分选托盘内没有电池14 输送进入错误专机二托盘输送进入专机超时,请检查托盘正否正常16 指拨器进出错误专机二运行错误,请检查进出的输入输出信号是否正常17 指拨器开关错误专机二运行错误,请检查进出的输入输出信号是否正常18 电池升降错误专机二运行错误,请检查进出的输入输出信号是否正常19 龙门升降错误专机二运行错误,请检查进出的输入输出信号是否正常20 定位销错误专机二运行错误,请检查进出的输入输出信号是否正常21 输送链条错误专机二运行错误,请检查进出的输入输出信号是否正常22 变频器报警专机二请查看变频器屏幕,详见施耐德ATV312变频器说明书23 空托盘1731未就位专机二电池分选目标1731托盘没有准备好24 空托盘1730未就位专机二电池分选目标1730托盘没有准备好3#专机故障1 指拨器插入错误专机三指拨器插入不到位,请检查磁环开关或者气缸2 指拨器退回错误专机三指拨器退回不到位,请检查磁环开关或者气缸3 指拨器打开错误专机三指拨器打开不到位,请检查磁环开关或者气缸4 指拨器关闭错误专机三指拨器关闭不到位,请检查磁环开关或者气缸5 电池顶升错误专机三电池顶升不到位,请检查磁环开关或者气缸6 电池下降错误专机三电池下降不到位,请检查磁环开关或者气缸7 龙门下降错误专机三龙门下降不到位,请检查磁环开关或者气缸8 龙门上升错误专机三龙门上升不到位,请检查磁环开关或者气缸9 定位销定位错误专机三定位销上升不到位,请检查磁环开关或者气缸10 定位销下降错误专机三定位销下降不到位,请检查磁环开关或者气缸11 空托盘1731未就位专机三电池分选目标1731托盘没有准备好12 空托盘1730未就位专机三电池分选目标1730托盘没有准备好13 托盘数据为零专机三待分选托盘内没有电池15 输送出去错误专机三托盘输送送出专机超时,请检查托盘是否正常16 指拨器进出错误专机三运行错误,请检查进出的输入输出信号是否正常17 指拨器开关错误专机三运行错误,请检查进出的输入输出信号是否正常18 电池升降错误专机三运行错误,请检查进出的输入输出信号是否正常19 龙门升降错误专机三运行错误,请检查进出的输入输出信号是否正常20 定位销错误专机三运行错误,请检查进出的输入输出信号是否正常21 输送链条错误专机三运行错误,请检查进出的输入输出信号是否正常22 变频器报警专机三请查看变频器屏幕,详见施耐德ATV312变频器说明书4#专机故障1 指拨器插入错误专机四指拨器插入不到位,请检查磁环开关或者气缸2 指拨器退回错误专机四指拨器退回不到位,请检查磁环开关或者气缸3 指拨器打开错误专机四指拨器打开不到位,请检查磁环开关或者气缸4 指拨器关闭错误专机四指拨器关闭不到位,请检查磁环开关或者气缸5 电池顶升错误专机四电池顶升不到位,请检查磁环开关或者气缸6 电池下降错误专机四电池下降不到位,请检查磁环开关或者气缸7 龙门下降错误专机四龙门下降不到位,请检查磁环开关或者气缸8 龙门上升错误专机四龙门上升不到位,请检查磁环开关或者气缸9 定位销定位错误专机四定位销上升不到位,请检查磁环开关或者气缸10 定位销下降错误专机四定位销下降不到位,请检查磁环开关或者气缸11 空托盘1729未就位专机四电池分选目标1729托盘没有准备好12 空托盘1728未就位专机四电池分选目标1728托盘没有准备好13 托盘数据为零专机四待分选托盘内没有电池14 输送进入错误专机四托盘输送进入专机超时,请检查托盘正否正常15 输送出去错误专机四托盘输送送出专机超时,请检查托盘是否正常16 指拨器进出错误专机四运行错误,请检查进出的输入输出信号是否正常18 电池升降错误专机四运行错误,请检查进出的输入输出信号是否正常19 龙门升降错误专机四运行错误,请检查进出的输入输出信号是否正常20 定位销错误专机四运行错误,请检查进出的输入输出信号是否正常21 输送链条错误专机四运行错误,请检查进出的输入输出信号是否正常22 变频器报警专机四请查看变频器屏幕,详见施耐德ATV312变频器说明书5#专机故障1 指拨器插入错误专机五指拨器插入不到位,请检查磁环开关或者气缸2 指拨器退回错误专机五指拨器退回不到位,请检查磁环开关或者气缸3 指拨器打开错误专机五指拨器打开不到位,请检查磁环开关或者气缸4 指拨器关闭错误专机五指拨器关闭不到位,请检查磁环开关或者气缸5 电池顶升错误专机五电池顶升不到位,请检查磁环开关或者气缸6 电池下降错误专机五电池下降不到位,请检查磁环开关或者气缸7 龙门下降错误专机五龙门下降不到位,请检查磁环开关或者气缸8 龙门上升错误专机五龙门上升不到位,请检查磁环开关或者气缸9 定位销定位错误专机五定位销上升不到位,请检查磁环开关或者气缸10 定位销下降错误专机五定位销下降不到位,请检查磁环开关或者气缸11 空托盘1729未就位专机五电池分选目标1729托盘没有准备好12 空托盘1728未就位专机五电池分选目标1728托盘没有准备好13 托盘数据为零专机五待分选托盘内没有电池14 输送进入错误专机五托盘输送进入专机超时,请检查托盘正否正常15 输送出去错误专机五托盘输送送出专机超时,请检查托盘是否正常16 指拨器进出错误专机五运行错误,请检查进出的输入输出信号是否正常17 指拨器开关错误专机五运行错误,请检查进出的输入输出信号是否正常18 电池升降错误专机五运行错误,请检查进出的输入输出信号是否正常19 龙门升降错误专机五运行错误,请检查进出的输入输出信号是否正常20 定位销错误专机五运行错误,请检查进出的输入输出信号是否正常22 变频器报警专机五请查看变频器屏幕,详见施耐德ATV312变频器说明书23空托盘1727未就位专机五电池分选目标1727托盘没有准备好24 空托盘1726未就位专机五电池分选目标1726托盘没有准备好6#专机故障1 指拨器插入错误专机六指拨器插入不到位,请检查磁环开关或者气缸2 指拨器退回错误专机六指拨器退回不到位,请检查磁环开关或者气缸3 指拨器打开错误专机六指拨器打开不到位,请检查磁环开关或者气缸4 指拨器关闭错误专机六指拨器关闭不到位,请检查磁环开关或者气缸5 电池顶升错误专机六电池顶升不到位,请检查磁环开关或者气缸6 电池下降错误专机六电池下降不到位,请检查磁环开关或者气缸7 龙门下降错误专机六龙门下降不到位,请检查磁环开关或者气缸8 龙门上升错误专机六龙门上升不到位,请检查磁环开关或者气缸9 定位销定位错误专机六定位销上升不到位,请检查磁环开关或者气缸10 定位销下降错误专机六定位销下降不到位,请检查磁环开关或者气缸11 空托盘1727未就位专机六电池分选目标1727托盘没有准备好12 空托盘1726未就位专机六电池分选目标1726托盘没有准备好13 托盘数据为零专机六待分选托盘内没有电池14 输送进入错误专机六托盘输送进入专机超时,请检查托盘正否正常15 输送出去错误专机六托盘输送送出专机超时,请检查托盘是否正常16 指拨器进出错误专机六运行错误,请检查进出的输入输出信号是否正常17 指拨器开关错误专机六运行错误,请检查进出的输入输出信号是否正常18 电池升降错误专机六运行错误,请检查进出的输入输出信号是否正常19 龙门升降错误专机六运行错误,请检查进出的输入输出信号是否正常21 输送链条错误专机六运行错误,请检查进出的输入输出信号是否正常22 变频器报警专机六请查看变频器屏幕,详见施耐德ATV312变频器说明书动作顺序(以专机1为例)1 托盘到达1722后向专机1(1723)发送货申请注(如果1722发申请没有任务号专机不会申请相应)2 1723专机1托盘允许后托盘流入到位3 专机开始工作3.1龙门架下降3.2指拨器插入托盘3.2.1 1723专机1托盘到位会向上位机申请任务信息(标志位改为2)3.2.2上位机响应后下发任务(标志位改为3)3.3压紧装置压紧到位3.4 机器人取隔板注:现阶段电池箱好多小胶丁残留会导致机器人扭矩报警,出现报警后按下专机1故障页面里机器人重起后试教器主画面按下夹具打开,上使能,回原点,进入运行页面,回待机点,运行。