PSP-2188+铜及铜合金的镀银
电镀配方大全-单金属镀液

单金属镀液电镀液是电镀化学品的核心嶷的配比是否科学、工艺条件是否合理是直接影响电镀层的质量。
电镀液是由主盐、导电盐、导电盐、缓冲剂、阳极去极化剂、络合剂和添加剂等组成,工艺条件包括pH值、温度、电流密度、阳极材料、电镀方法、搅拌形式和电镀时间等。
(1)主盐即能在阴极上沉积所要求的镀层金属盐。
通常主要是氰化物、氯化物、硫酸盐和焦磷酸盐等。
主盐浓度与其他组分的浓度应维持一个适当的比值,主盐浓度高,电镀液电导率和阴极电流效率都高,能使镀层光亮度和整平性较好,但电镀液带出损失量大,也增加了废液处理的难度。
主盐浓度低,电镀液分散能力和覆盖能力较好,对于外形复杂的镀件或预镀通常使用主盐浓度低的镀液。
(2)导电盐即能够提高镀电导率,对放电金属不起络合作用的碱金属或碱土金属的盐类,如镀镍使用的NaSO4、MgSO4、焦磷酸盐等,镀铜及铜合金使用的KNO3和NH4NO3等。
导是盐除了提高镀液的是导率之外,还能降低镀液的阴极化作用,对镀层结晶组织没有不利影响。
(3)缓冲剂它是由弱酸与弱酸盐、弱碱与弱碱盐组成的,在化学上称之共轭酸碱对组成的溶液均是酸碱缓冲剂。
多元酸的酸式溶液也是缓冲剂和NaHCO3、NaH2PO4、Na3HPO4等。
弱酸和H3BO3、NH4CL对碱有缓冲作用,弱碱如氨水对酸有缓冲作用。
缓冲剂的作用是在镀液遇到酸可碱时,均能维持镀液的pH值变化不大。
(4)阳极去极化剂是指在电镀过程中能使阳极电位变负、促进阳极活化的物质,常用的阳极去极化剂有氧化物、酒石酸盐和硫氰酸盐等。
(5)络合剂即能与主盐金属离子形成络合物的物质称为络合剂,如氰化物镀液中的NaCN或KCN,焦磷酸盐镀液中的K4P2O7或Na4P07等。
电镀液中的络合剂含量常高于络合金属离子所需要的量,多余部分称为游离的络合剂,如氰化物镀铜溶液中有NaCN总量的和NaCN游离量,其中游离量即为多余的没有与Cu2+离子络合的量。
游离量高阳极溶解性好,阴极极化作用大,镀层结晶细致,镀液分散能力和覆盖能力强,但阴极电流效率低,沉积速度减慢。
99.9白铜锡代替镍电镀工艺
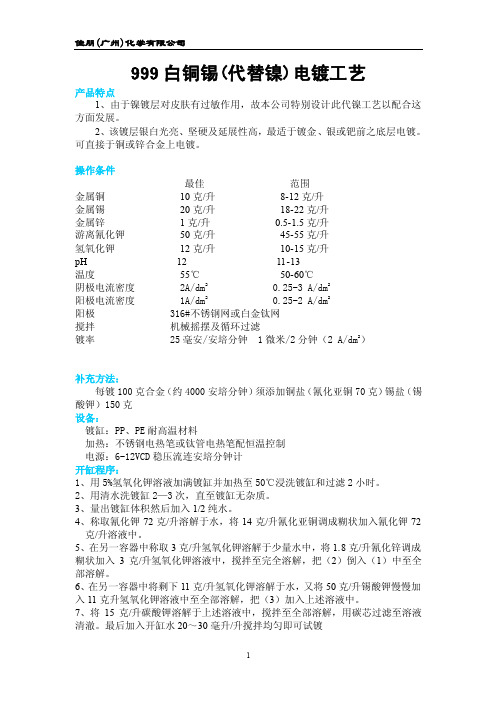
999白铜锡(代替镍)电镀工艺产品特点1、由于镍镀层对皮肤有过敏作用,故本公司特别设计此代镍工艺以配合这方面发展。
2、该镀层银白光亮、坚硬及延展性高,最适于镀金、银或钯前之底层电镀。
可直接于铜或锌合金上电镀。
操作条件最佳范围金属铜10克/升8-12克/升金属锡20克/升18-22克/升金属锌1克/升0.5-1.5克/升游离氰化钾50克/升45-55克/升氢氧化钾12克/升10-15克/升pH 12 11-13温度55℃50-60℃阴极电流密度 2A/dm2 0.25-3 A/dm2阳极电流密度 1A/dm2 0.25-2 A/dm2阳极 316#不锈钢网或白金钛网搅拌机械摇摆及循环过滤镀率 25毫安/安培分钟 1微米/2分钟(2 A/dm2)补充方法:每镀100克合金(约4000安培分钟)须添加铜盐(氰化亚铜70克)锡盐(锡酸钾)150克设备:镀缸:PP、PE耐高温材料加热:不锈钢电热笔或钛管电热笔配恒温控制电源:6-12VCD稳压流连安培分钟计开缸程序:1、用5%氢氧化钾溶液加满镀缸并加热至50℃浸洗镀缸和过滤2小时。
2、用清水洗镀缸2—3次,直至镀缸无杂质。
3、量出镀缸体积然后加入1/2纯水。
4、称取氰化钾72克/升溶解于水,将14克/升氰化亚铜调成糊状加入氰化钾72克/升溶液中。
5、在另一容器中称取3克/升氢氧化钾溶解于少量水中,将1.8克/升氰化锌调成糊状加入3克/升氢氧化钾溶液中,搅拌至完全溶解,把(2)倒入(1)中至全部溶解。
6、在另一容器中将剩下11克/升氢氧化钾溶解于水,又将50克/升锡酸钾慢慢加入11克升氢氧化钾溶液中至全部溶解,把(3)加入上述溶液中。
7、将15克/升碳酸钾溶解于上述溶液中,搅拌至全部溶解,用碳芯过滤至溶液清澈。
最后加入开缸水20~30毫升/升搅拌均匀即可试镀技术资料:镀层:成份:铜50%、锡50%密度:8.5g/cm385毫安/平方分米=1微米硬度:500-600VIC Kers特点:光亮及低气孔率镀层,具有良好的耐磨度及防腐能力1、添加1.42克/升铜盐可提高金属铜含量1克/升2、添加2.5克/升锡盐可提高金属锡含量1克/升3、添加1克/升铜盐可降低氰化钾1.8克/升4、添加1克/升氰化锌可提高金属锌0.5克/升5、调高pH值用氢氧化钾6、调低pH值用稀磷酸。
HB_航空

HB_航空航空(HB)(1) 金属材料?高温合金HB 5154—1988K401合金锭HB 5155—1996K403合金锭HB 5156—1988K405合金锭HB 5157—1988K406合金锭HB 5158—1988K211合金锭HB 5159—1988K412合金锭HB 5160—1988K214合金锭HB 5161—1988K417合金锭HB 5162—1988K418合金锭HB 5163—1988K419合金锭HB 5198—1982航空叶片用变形高温合金棒材 HB 5199—1982航空用高温合金冷轧薄板 HB 5284—1984航空用GH220合金热轧棒材技术条件 HB 5285—1984航空用GH698合金盘形锻件 HB 5330—1985航空用K9合金锭HB 5331—1985航空用K17G镍基铸造高温合金技术条件 HB 5332—1992GH99合金冷轧薄板HB 5333—1985航空用HGH99合金焊丝技术条件 HB 5406—1988铸造高温合金锭浮渣试验方法 HB 5407—1988等静压成型镁质坩埚HB 5417—1991GH1016合金棒材HB 5418—1988GH1016合金冷轧薄板HB 5419—1991GH1016合金圆饼、环坯和环形件 HB 5423—1989航空用GH710合金饼坯锻件 HB 5437—1989GH3044合金热轧或锻制棒材 HB 5438—1989GH3044合金圆饼、环坯和环形件 HB 5463—1990GH696合金热轧和锻制棒材 HB 5464—1990GH696合金冷拉棒材HB 5465—1990GH696合金冷轧薄板HB 5466—1990GH696合金冷轧弹簧钢带 HB 5467—1990GH696合金冷拉丝HB 5494—1992GH536合金冷轧(拔)无缝管 HB 5495—1992GH536合金冷轧薄板HB 5496—1992GH536合金圆饼、环坯和环形件 HB 5497—1992GH536合金热轧和锻制棒材 HB 5498—1992HGH536合金冷拉焊丝HB 5499—1992HGH150和HGH533合金冷拉焊丝 HB 6570—1992GH150合金棒材HB 6571—1992GH150合金冷轧薄板HB 6572—1992GH150合金圆饼、环坯和环形件 HB 6574—1992GH903低膨胀合金环坯和环形件HB 6702—1993WZ8系列用GH4169合金棒材 HB 6703—1993WZ8系列用GH500合金棒材 HB 7239—1995K418B合金锭HB 7240—1995DZ22B合金锭HB 7241—1995K423A合金锭HB 7569—1997DZ4合金锭HB 7570—1997DZ22合金锭HB/Z 38—1993K401合金冶炼工艺说明书 HB/Z 40—1993K401合金重熔工艺说明书 HB/Z 41—1993K403合金冶炼工艺说明书 HB/Z 42—1993K403合金重熔工艺说明书 HB/Z 43—1993K405合金冶炼工艺说明书 HB/Z 44—1993K405合金重熔工艺说明书 HB/Z 45—1993K406合金冶炼工艺说明书 HB/Z 46—1993K406合金重熔工艺说明书ML HB/Z 47—1993K211合金非真空冶炼工艺说明书 HB/Z 48—1993K211合金非真空重熔工艺说明书 HB/Z 49—1993K412合金冶炼工艺说明书HB/Z 50—1993K412合金重熔工艺说明书 HB/Z 51—1993K412合金非真空冶炼工艺说明书 HB/Z 52—1993K412合金电渣重熔工艺说明书 HB/Z 53—1993K214合金冶炼工艺说明书M HB/Z 54—1993K214合金重熔工艺说明书 HB/Z 55—1993K417合金冶炼工艺说明书 HB/Z 56—1993K417合金重熔工艺说明书 HB/Z 57—1993K418合金冶炼工艺说明书 HB/Z 58—1993K418合金重熔工艺说明书 HB/Z 69—1993K419合金冶炼工艺说明书 HB/Z 70—1993K419合金重熔工艺说明书 HB/Z 91—1985航空用高温合金涡轮叶片模锻件 HB/Z 131—1988铸造高温合金选用原材料技术要求 HB/Z 140—1989航空用高温合金热处理工艺说明书 HB/Z 154—1989航空用钢及高温合金熔炼和成材工艺认可规范HB/Z 155—1989航空用钢及高温合金供应厂工程认可规范?钢铁HB 094—1977黑色金属硬度及强度换算表 HB 5001—1992结构钢熔模铸件技术条件 HB 5024—1989航空用钢锻件HB 5137—19803Cr3Mo3VNb热作模具钢技术条件 HB 5138—19803Cr3Mo3VNb热作模具钢 HB 5139—19803Cr3Mo3VNb热作模具钢锻造(试行) HB 5140—19803Cr3Mo3VNb热作模具钢热处理HB 5252—1983航空用40CrMnSiMoVA超高强度钢钢棒 HB 5253—1983航空用40CrMnSiMoVA无发纹钢钢管 HB 5269—1983航空用高级优质结构钢钢棒 HB 5298—1985航空用不锈弹簧钢丝HB 5424—1989不锈钢耐热钢母合金铸锭HB 5430—1989不锈钢耐热钢熔模铸件HB 5451—1990不锈钢耐热钢熔模铸造压气机静子叶片 HB 6573—1992熔模钢铸件用标准参考射线底片 HB/Z 105—1986航空用不锈钢压气机叶片模锻件 HB/Z 5138—19803Cr3Mo3VNb热作模具钢冶炼和铸锭WX)?铝、镁合金HB 962—1986铸造铝合金HB 963—1990铝合金铸件HB 964—1982铸造镁合金技术标准HB 965—1982镁合金铸件技术标准HB 967—1970ZM-镁合金显微疏松X光透视分级标准 HB 5012—1986铝合金压铸件HB 5201—1982变形铝合金过烧金相检验标准 HB 5202—1982航空用铝及铝合金挤压棒材 HB 5203—1982航空用镁合金挤压型材HB 5204—1982航空用铝合金锻件和模锻件 HB 5300—1985LY12MCS、LY12CS、LY16MCGS铝合金挤压型材 HB 5301—1985LY12MCS、LY16MCGS铝合金板材 HB 5371—1987铝基中间合金锭HB 5372—1987铸造铝合金锭HB 5395—1988铝合金铸件X射线照相检验长形针孔分级标准 HB 5396—1988铝合金铸件X射线照相检验海绵状疏松分级标准HB 5397—1988铝合金铸件X射线照相检验分散疏松分级标准 HB 5401—1987LC9CgSi铝合金锻件HB 5446—1990铸造铝合金热处理HB 5462—1990镁合金铸件热处理HB 5471—19912024铝合金预拉伸板HB 5480—1991高强度铝合金优质铸件HB 6578—1992铝镁合金铸件检验用参考射线底片 HB 6690—1992镁合金锻件HB 6773—1993镁锆中间合金锭HB 7063—1994铝合金电导率和硬度HB 7264—1996镁稀土中间合金锭HB/Z 160—1990铸造铝合金熔炼HB/Z 220.1—1992铝合金砂型铸造HB/Z 220.2—1992铝合金金属型铸造HB/Z 220.3—1992铝合金低压铸造HB/Z 220.4—1992铝合金压力铸造HB/Z 220.5—1992铝合金熔模壳型铸造HB/Z 220.6—1992铝合金石膏精密铸造HB/Z 220.7—1992铝合金铸件浸渗HB/Z 276—1995变形铝合金零件热处理HB/Z 5123—1979镁合金铸造HB/Z 5126—1979变形铝合金热处理?钛及钛合金HB 5223—1982航空发动机盘用TC4钛合金模锻件 HB 5224—1982航空发动机饼坯用TC4钛合金模锻件 HB 5262—1983TC11钛合金压气机盘用饼(环)坯技术标准 HB 5263—1995TC11钛合金压气机盘模锻件ML HB 5264—1983TC11钛合金压气机盘及其饼坯金相组织标准 HB 5432—1989飞机用TC4钛合金锻件HB 5447—1990铸造钛合金HB 5448—1990钛及钛合金熔模精密铸件HB 6623.1—1992钛合金β转变温度测定方法(差热分析法) HB 6623.2—1992钛合金β转变温度测定方法(金相法) HB 6732—1993航空紧固件用TB3钛合金棒线材 HB 7238—1995钛合金环形锻件HB/Z 137—1988钛合金热处理工艺说明书?精密合金、铜合金及贵金属HB 5018—1997铸造铝镍钴永磁合金HBHB 5170—1981电接点用贵金属及其合金丝材锻平试验方法 HB 5171—1981含铜贵金属材料氧化亚铜金相检验标准 HB 5187—1996航空用贵金属及其合金电位器裸线 HB 5188—1996航空用贵金属及其合金电刷线材 HB 5189—1996航空用贵金属及其合金管材HB 5190—1996航空用贵金属及其合金板、带材 HB 5191—1996航空用贵金属及其合金丝材HB 5291—1984航空电位器用油性漆包贵金属合金线 HB 5302—1985航空发动机点火装置接点用PtIr25合金板材 HB 5312—1985航空用铜合金熔模铸件标准HB 5340—1989航空用贵金属及其合金显微维氏硬度试验方法 HB 5450—1990铜及铜合金锻件HB 6734—1993贵金属细丝拉伸杨氏模量试验方法 HB 7470—1996贵金属异形丝材HB/Z 135—1988航空用铍青铜热处理工艺说明书 HB/Z 161—1990弹性元件用精密合金热处理工艺说明书 HB/Z 192—1991软磁合金热处理工艺说明书HB/Z 216—1992铜及铜合金热处理工艺说明书 HB/Z 239—1993膨胀合金热处理工艺说明书HB/Z 327—1998磁滞合金热处理工艺说明书HB/Z 5015—1994电磁纯铁热处理工艺说明书 HB/Z 5016—1995硅钢片热处理工艺HB/Z 5019—1977铸造永磁合金熔炼HB/Z 5020—1997铸造铝镍钴永磁合金热处理?粉末冶金和涂层HB 5341—1986B-1000高温陶瓷涂层标准HB 5366—1986航空用碳石墨密封材料HB 5367.1—1986碳石墨密封材料抗压强度试验方法 HB 5367.2—1986碳石墨密封材料抗折强度试验方法 HB 5367.3—1986碳石墨密封材料开口气孔率测定方法 HB 5367.4—1986碳石墨密封材料热氧化失重测定方法 HB 5367.5—1986碳石墨密封材料肖氏硬度试验方法 HB 5367.6—1986碳石墨密封材料洛氏硬度(,,)试验方法 HB 5367.7—1986碳石墨密封材料密度测定方法 HB 5367.8—1986碳石墨密封材料热膨胀系数试验方法 HB 5367.9—1986碳石墨密封材料导热系数试验方法 HB 5367.10—1986碳石墨密封材料摩擦性能试验方法 HB 5367.11—1986碳石墨密封材料弹性模量试验方法 HB 5434.1—1989航空机轮刹车材料术语HB 5434.2—1989航空机轮刹车材料鉴定规则 HB 5434.3—1989航空机轮刹车材料硬度的测定方法 HB 5434.4—1989航空机轮刹车材料惯性台鉴定规范 HB 5434.5—1989航空机轮刹车材料压缩强度的测定方法 HB 5434.6—1989航空机轮刹车材料弯曲强度的测定方法 HB 5434.7—1989航空机轮刹车材料摩擦磨损性能的测定方法 HB 5434.8—1989航空机轮刹车材料密度的测定方法 HB 5434.9—1989航空机轮刹车材料拉伸强度的测定方法 HB 5434.10—1989航空机轮刹车材料与钢背间结合质量及烧结后钢背塑性的检验方法HB 5441.1—1989测量金属粉末粒度的筛分法 HB 5441.2—1989渗透性烧结金属材料含油率的测试方法 HB 5441.3—1989烧结金属材料(硬质合金除外)抗拉强度的测试方法 HB 5441.4—1989金属粉末松装密度的测试方法 HB 5441.5—1989金属粉末摇实密度的测试方法 HB 5441.6—1989金属粉末流动性的测试方法 HB 5441.7—1989渗透性烧结金属材料密度和开孔孔隙度的测试方法 HB 5441.8—1989烧结金属衬套径向压溃强度的测试方法 HB 5441.9—1989烧结金属材料(硬质合金除外) HB 5457—1990粉末冶金铜基离合器摩擦片HB 5458—1990粉末冶金铜基多孔轴承HB 5474—1991热喷涂涂层剪切强度试验方法 HB 5475—1991热喷涂涂层抗拉强度试验方法 HB 5476—1991热喷涂涂层结合强度试验方法 HB 5486—1991热喷涂涂层硬度试验方法HB 6738—1993热喷涂耐磨涂层质量检验HB 7055—1994粉末冶金软磁材料制件HB 7236—1995热喷涂封严涂层质量检验HB 7269—1996热喷涂热障涂层质量检验HB 7576—1997航空粉末冶金制品质量控制标准 HB 7627—1998爆炸喷涂碳化钨、碳化铬耐磨涂层质量检验 HB/Z 104—1986B-1000高温陶瓷涂层涂制工艺说明书 HB/Z 162—1990粉末冶金铜基离合器摩擦片制造工艺 HB/Z 163—1990粉末冶金铜基多孔轴承制造工艺 HB/Z 263—1994粉末冶金软磁材料制件制造工艺 HB/Z 5031—1977航空发动机封严涂层涂覆工艺WX)?CX 物理冶金及表面强化HB 6742—1993单晶叶片晶体取向的测定X射线背射劳厄照相法 HB/Z 26—1992航空零件喷丸强化工艺通用说明书 HB/Z 170—1990航空金属零部件挤压强化工艺通用说明书WX)(2)?锻造HB 5119—1979锻造术语HB 5355—1994锻造工艺质量控制HB 5402—1997锻件试制定型规范HB 7065—1994金属材料热变形用玻璃防护润滑剂规范 HB/Z 141—1989模锻件结构要素HB/Z 156—1989航空用钢及高温合金锻件生产工艺认可规范 HB/Z 199—1991钛合金锻造工艺HB/Z 210—1991HB/Z 283—1996钢的锻造工艺HB/Z 5139—19803Cr3Mo3VNb热作模具钢锻造?铸造HB 5117—1978锻造术语HB 5343—1994锻造工艺质量控制HB 5344—1986熔模铸造用聚合松香HB 5345—1986熔模铸造用硅酸乙酯HB 5346—1986熔模铸造用硅溶胶HB 5347—1986熔模铸造用电熔白刚玉粉HB 5348—1986熔模铸造用上店土砂、粉HB 5349—1986熔模铸造用锆石英粉HB 5350.1—1986熔模铸造模料线收缩率测定方法 HB 5350.2—1986熔模铸造模料热变形量测定方法 HB 5350.3—1986熔模铸造模料抗弯强度测定方法 HB 5350.4—1986熔模铸造模料表面硬度测定方法 HB 5350.5—1986熔模铸造模料灰分测定方法 HB 5350.6—1986熔模铸造模料粘度测定方法 HB 5350.7—1986熔模铸造熔模粘结剂湿润角测定方法 HB 5351.1—1986熔模铸造涂料粘度测定方法HB 5351.2—1986熔模铸造涂料比重测定方法(比重计法) HB 5351.3—1986熔模铸造涂料比重测定方法(容量法) HB 5351.4—1986熔模铸造涂料酸度测定方法(pH试纸法) HB 5351.5—1986熔模铸造涂料酸度测定方法(pH计法) HB 5351.6—1986熔模铸造涂料覆盖性测定方法 HB 5351.7—1986熔模铸造用耐火粉料粒度测定方法(扭力天平沉降分析法)HB 5352.1—1986熔模铸造型壳抗弯强度测定方法 HB 5352.2—1986熔模铸造型壳高温自重变形测定方法 HB 5352.3—1986熔模铸造型壳高温荷重变形测定方法 HB 5352.4—1986熔模铸造型壳透气性测定方法 HB 5352.5—1986熔模铸造用硅溶胶型壳干燥度测定方法 HB 5353.1—1986熔模铸造陶瓷型芯显气孔率吸水率和体积密度测定方法HB 5353.2—1986熔模铸造陶瓷型芯烧成收缩率测定方法 HB 5353.3—1986熔模铸造陶瓷型芯抗弯强度测定方法 HB 5353.4—1986熔模铸造陶瓷型芯热变形测定方法 HB 5353.5—1986熔模铸造陶瓷型芯及型壳线膨胀测定方法 HB 5353.6—1986熔模铸造陶瓷型芯溶失性测定方法 HB 6103—1986铸件尺寸公差HB HB 7578—1997铸件试制定型规范HB/Z 234—1993钛合金铸件热等静压工艺?焊接HB 458—1984航空工业用焊条的质量检验HB 459.1—1984HTJ1焊条技术条件HB 459.2—1984HTJ2焊条技术条件HB 460—1984HTJ3焊条技术条件HB 461.1—1984HTJ4焊条技术条件HB 461.2—1984HTJ5焊条技术条件HB 462.1—1984HTB1焊条技术条件HB 462.2—1984HTB2焊条技术条件HB 462.3—1984HTG1焊条技术条件HB 462.4—1984HTG2焊条技术条件HB 463—1984HTG3焊条技术条件HB 465—1965变形铝合金气焊接头的质量检验及缺陷修补标准HB 466—1965变形铝合金电阻点焊和滚焊的质量检验及缺陷修补标准HB 5120—1979焊接术语HB 5133—197930CrMnSiNi2A钢熔焊接头质量检验标准 HB 5135—1979结构钢和不锈钢熔焊接头质量检验 HB 5276—1984铝合金电阻点焊和缝焊质量检验 HB 5282—1984结构钢和不锈钢电阻点焊和缝焊质量检验 HB 5363—1995焊接工艺质量控制HB 5375—1987铝及铝合金熔焊质量检验HB 5376—1987钛及钛合金钨极氩弧焊质量检验 HB 5420—1989电阻焊电极与辅助装置用铜及铜合金 HB 5427—1989钛及钛合金电阻点焊和缝焊质量检验 HB 5456—1990高温合金钨极氩弧焊质量检验 HB 5484—1991钛及钛合金电子束焊接质量检验 HB 6737—1993高温合金电阻点焊和缝焊质量检验M HB 6771—1993银基钎料HB 6772—1993镍基钎料HB 7052—1993铝基钎料HB 7053—1993铜基钎料HB 7234—1995钛及钛合金钨极氩弧焊标准色块 HB 7575—1997高温合金及不锈钢真空钎焊质量检验 HB 7608—1998高温合金、不锈钢真空电子束焊接质量检验 HB/Z 77—1984铝合金电阻点焊和缝焊工艺HB/Z 78—1984结构钢和不锈钢电阻点焊和缝焊工艺 HB/Z 119—1987铝及铝合金熔焊工艺HB/Z 120—1987钛及钛合金钨极氩弧焊工艺 HB/Z 145—1989钛及钛合金电阻点焊和缝焊工艺 HB/Z 164—1990高温合金钨极氩弧焊工艺HB/Z 198—1991钛及钛合金电子束焊接工艺 HB/Z 238—1993高温合金电阻点焊和缝焊工艺 HB/Z 309—1997高温合金及不锈钢真空钎焊 HB/Z 315—1998高温合金、不锈钢真空电子束焊接工艺 HB/Z 328—1998镁合金铸件补焊工艺及检验HB/Z 5021—1977细丝二氧化碳气体保护焊HB/Z 5128—1979铝及铝合金点焊、滚焊前表面准备()HB/Z 5132—197930CrMnSiNi2A钢熔焊工艺HB/Z 5134—1979结构钢和不锈钢熔焊工艺?热处理HB 5013—1996热处理零件检验类别HB 5022—1994航空钢制件渗氮、氮碳共渗金相组织检验标准 HB 5023—1994航空钢制件渗氮、氮碳共渗渗层溶度测定方法 HB 5118—1978金属及合金热处理术语HB 5354—1994热处理工艺质量控制HB 5408—1988热处理用工业硝酸钾HB 5409—1988热处理用工业氯化钠HB 5410—1988热处理用工业氯化钾HB 5411—1988热处理用工业硝酸钠HB 5412—1988热处理用氩气HB 5413—1988热处理用氮气HB 5414—1988热处理用工业无水氯化钡HB 5415—1988热处理用淬火用油HB 5425—1989航空制件热处理炉有效加热区测定方法 HB 5492—1991航空钢制件渗碳、碳氮共渗金相组织检验标准 HB 5493—1991航空钢制件渗碳、碳氮共渗渗层深度测定方法 HB 6735—1993航空结构钢薄脱碳(含合金贫化)层和增碳(含增氮)层深度测定方法HB 7064.1—1994金属热处理盐浴化学分析方法酸度计法测定pH值 HB 7064.2—1994金属热处理盐浴化学分析方法酸度钡沉淀分离酸碱滴定法测定碳酸根含量HB 7064.3—1994金属热处理盐浴化学分析方法硫酸钡沉淀-EDTA滴定法测定硫酸根含量HB 7064.4—1994金属热处理盐浴化学分析方法硫酸钡比浊法测定硫酸根含量HB 7064.5—1994金属热处理盐浴化学分析方法银量法测定氯离子含量 HB 7064.6—1994金属热处理盐浴化学分析方法酸碱滴定测定总碱度含量 HB/Z 64—19813号涂料保护热处理工艺HB/Z 79—1995结构钢及不锈钢渗氮工艺说明书HB/Z 80—1997航空用不锈钢、耐热钢热处理说明书 HB/Z 136—1988航空结构钢热处理说明书HB/Z 159—1990航空用钢气体渗碳、碳氮共渗工艺说明书 HB/Z 191—1991航空结构钢不锈钢真空热处理说明书 HB/Z 262—1994金属热处理盐浴化学分析用试样的取样规范 HB/Z 316—1998热处理加热用中性盐浴?表面处理HB 5033—1977镀层和化学覆盖层的选择原则与厚度系列 HB 5034—1995零(组)件镀覆前质量要求HB 5035—1992锌镀层质量检验HB 5036—1992镉镀层质量检验HB 5037—1992铜镀层质量检验HB 5038—1992镍镀层质量检验HB 5039—1992黑镍镀层质量检验HB 5040—1977化学镀镍层质量检验HB 5041—1992硬铬、乳白铬镀层质量检验HB 5042—1992装饰铬镀层质量检验HB 5043—1992涨圈松孔铬镀层质量检验HB 5044—1992汽缸松孔铬镀层质量检验HB 5045—1992黑铬镀层质量检验HB 5046—1993锡镀层质量检验HB 5047—1977黄铜镀层质量检验HB 5048—1977铅镀层质量检验HB 5049—1993铅锡合金镀层质量检验HB 5050—1977铅铟扩散镀层质量检验HB 5051—1993银镀层质量检验HB 5052—1977金镀层质量检验HB 5053—1977钯镀层质量检验HB 5054—1977铑镀层质量检验HB 5055—1993铝及铝合金硫酸阳极氧化膜层质量检验 HB 5057—1993铝及铝合金硬质阳极氧化膜层质量检验 HB 5058—1993铝及铝合金绝缘阳极氧化膜层质量检验 HB 5059—1977电化学抛光质量检验HB 5060—1977铝及铝合金化学氧化膜层质量检验 HB 5061—1977镁合金化学氧化膜层质量检验 HB 5062—1996钢铁零件化学氧化(发蓝)膜层质量检验 HB 5063—1996钢铁零件磷化膜层质量检验HB 5064—1977铜及铜合金钝化膜层质量检验 HB 5065—1977铜及铜合金氧化膜层质量检验 HB 5066—1977喷镀锌层质量检验HB 5067—1985氢脆试验方法HB 5192—1981镀层和化学覆盖层表观腐蚀等级评定方法 HB 5193.1—1985镀层和化学覆盖层耐蚀性检验 HB 5193.2—1985镀层和化学覆盖层耐蚀性检验标准(二) HB 5196—1982镍镉扩散镀层质量检验HB 5197—1982有机材料挥发气氛对锌、镉镀层腐蚀试验方法 HB 5292—1984不锈钢酸洗钝化质量检验HB 5335—1994金属镀覆和化学覆盖工艺质量控制 HB 5360—1986 HB 5361—1986HB 5362—1986飞机常用金属防护层耐蚀性质量检验 HB 5364—1986WZL涂层质量检验HB 5373—1987铝及铝合金铬酸阳极氧化膜层质量检验 HB 5468—1991铂铝涂层检验标准HB 5472—1991金属镀覆和化学覆盖工艺用水水质规范 HB 5473—1991铝及铝合金化学转化膜质量检验 HB 7054—1994钛合金紧固件离子镀铝层质量检验 HB 7579—1997渗铝质量检验HB/Z 29—1981电化学抛光工艺HB/Z 31—1982镍镉扩散镀层通用工艺说明书 HB/Z 32—1982有机材料挥发气氛对锌、镉镀层的腐蚀与防护指南HB/Z 66—1981喷锌工艺HB/Z 83—1984不锈钢酸洗钝化处理工艺HB/Z 107—1986高强度钢零件低氢脆镀镉钛工艺 HB/Z 108—1986WZL涂层的涂覆工艺说明书HB/Z 118—1987铝及铝合金铬酸阳极氧化工艺HB/Z 187—1991铂铝涂层工艺HB/Z 193—1991铝及铝合金化学转化膜浸渍工艺 HB/Z 197—1991结构胶接铝合金磷酸阳极化工艺规范 HB/Z 233—1993铝及铝合金硫酸阳极氧化工艺 HB/Z 236—1993电镀铅锡合金工艺HB/Z 237—1993铝及铝合金硬质阳极氧化工艺 HB/Z 265—1994钛合金紧固件离子镀铝工艺 HB/Z 310—1997渗铝工艺HB/Z 318—1998镀覆前消除应力和镀覆后除氢处理规范 HB/Z 337—1999铝合金化学转化(阿洛丁)溶液分析方法 HB/Z 338.1,338.2—1999铝合金绝缘阳极氧化溶液分析方法HB/Z 339.1,339.3—1999铝合金铬酸阳极氧化溶液分析方法HB/Z 5068—1992电镀锌、电镀镉工艺HB/Z 5069—1992电镀铜工艺HB/Z 5070—1992电镀镍工艺HB/Z 5071—1978化学镀镍工艺HB/Z 5072—1992电镀铬工艺HB/Z 5073—1993电镀锡工艺HB/Z 5074—1993电镀银工艺HB/Z 5075—1978电镀金锑工艺HB/Z 5076—1993铝及铝合金绝缘阳极氧化工艺 HB/Z 5077—1978铝及铝合金化学氧化(磷酸-铬酸法)工艺 HB/Z 5078—1978镁合金化学氧化工艺HB/Z 5079—1996钢铁零件化学氧化工艺 HB/Z 5080—1996钢铁零件磷化工艺HB/Z 5081—1978铜及铜合金化学钝化工艺 HB/Z 5082—1978铜及铜合金氧化工艺HB/Z 5083—1978电镀溶液分析常用试剂 HB/Z 5084—1978氰化电镀锌溶液分析方法 HB/Z 5085.1,5085.8—1999氰化电镀镉溶液分析方法 HB/Z 5086—1978氰化电镀铜溶液分析方法 HB/Z 5087—1978酸性电镀铜溶液分析方法 HB/Z5088.1,5088.6—1999电镀镍溶液分析方法 HB/Z 5089—1978电镀黑镍溶液分析方法 HB/Z 5090—1978化学镀镍溶液分析方法 HB/Z 5091.1,5091.6—1999电镀铬溶液分析方法 HB/Z 5092—1978电镀黑铬溶液分析方法 HB/Z 5093—1978碱性电镀锡溶液分析方法 HB/Z 5094—1978酸性电镀锡溶液分析方法 HB/Z 5095—1978氰化电镀黄铜溶液分析方法 HB/Z 5096—1978电镀铅溶液分析方法HB/Z 5097—1978电镀铅锡合金溶液分析方法 HB/Z 5098—1978电镀铟溶液分析方法HB/Z 5099—1978氰化电镀银溶液分析方法HB/Z 5100—1978氰化电镀金溶液分析方法HB/Z 5101—1978电镀金锑合金溶液分析方法HB/Z 5102—1978电镀钯溶液分析方法HB/Z 5103—1978电镀铑溶液分析方法HB/Z 5104.1,5104.3—1999铝合金硫酸阳极氧化溶液分析方法 HB/Z 5105—1978电化学抛光溶液分析方法HB/Z 5106—1978铝合金化学氧化(磷酸铬酸法)溶液分析方法 HB/Z 5107—1978镁合金化学氧化溶液分析方法 HB/Z 5108.1,5108.3—1999磷化溶液分析方法HB/Z 5109—1978钝化溶液分析方法HB/Z 5110—1978电化学除油及化学除油溶液分析方法 HB/Z 5111—1978锌锡合金镀层分析方法HB/Z 5112—1978镉锡合金镀层分析方法HB/Z 5113—1978镉钛合金镀层分析方法HB/Z 5114—1978铅锡合金镀层分析方法HB/Z 5115—1978金锑合金镀层分析方法HB/Z 5116—1978金属镀层试纸鉴定法?防护包装HB 5028—1995航空机载设备干燥空气封存HB 5129—1979航空发动机干燥空气封存HB 5200—1982包装材料透湿率试验方法HB 5205—1982铝塑布复合薄膜HB 5206—1982包装材料对金属的接触腐蚀试验方法 HB 5226—1982金属材料和零件用水基清洗剂技术条件 HB 5227—1982金属材料和零件用水基清洗剂试验方法 HB 5334—1985飞机表面水基清洗剂HB/Z 65—1981飞机副油箱干燥空气封存工艺HB/Z 67—1981航空轴承封存工艺HB/Z 68—1981工序间防锈HB/Z 90—1985航空辅机产品运输包装设计HB/Z 109—1986气相缓蚀材料应用说明书HB/Z 5029—1995航空机载设备干燥空气封存工艺 HB/Z 5130—1979航空发动机干燥封存工艺(3) 金属材料测试方法? 化学成分分析HB 5218.1—1995铝合金化学分析方法 BCD HB 5218.2—1995铝合金化学分析方法碘量法测定铜含量 HB 5218.3—1995铝合金化学分析方法 HB 5218.4—1995铝合金化学分析方法高碘酸钾光度法测定锰含量 HB 5218.5—1995铝合金化学分析方法重量法测定硅含量HB 5218.6—1995铝合金化学分析方法硅钼蓝光度法测定硅含量 HB 5218.7—1995铝合金化学分析方法铜试剂分离-EDTA滴定法测定镁含量 HB 5218.8—1995铝合金化学分析方法二安替比林甲烷光度法测定钛含量 HB 5218.9—1995铝合金化学分析方法三正辛胺萃取-EDTA滴定法测定锌含量 HB 5218.10—1995铝合金化学分析方法双硫腙萃取分离-极谱法测定锌含量 HB 5218.11—1995铝合金化学分析方法丁二酮肟分离-EDTA滴定法测定镍含量 HB 5218.12—1995铝合金化学分析方法丁二酮肟萃取光度法测定镍含量 HB 5218.13—1995铝合金化学分析方法草酸盐重量法测定稀土总量 HB 5218.14—1995铝合金化学分析方法三溴偶氮胂光度法测定铈组稀土总量 HB 5218.15—1995铝合金化学分析方法二甲酚橙光度法测定溶解锆含量 HB 5218.16—1995铝合金化学分析方法槲皮素光度法测定溶解锆含量 HB 5218.17—1995铝合金化学分析方法极谱法测定铅含量HB 5218.18—1995铝合金化学分析方法硫酸亚铁铵滴定法测定铬含量 HB 5218.19—1995铝合金化学分析方法二苯卡巴肼光度法测定铬含量 HB 5218.20—1995铝合金化学分析方法苯基荧光酮光度法测定锡含量 HB 5218.21—1995铝合金化学分析方法铍试剂?光度法测定铍含量 HB 5218.22—1995铝合金化学分析方法 HB 5218.23—1995铝合金化学分析方法钽试剂萃取光度法测定钒含量 HB 5219.1—1998镁合金化学分析方法 BCO HB 5219.2—1998镁合金化学分析方法新铜试剂光度法测定铜含量 HB 5219.3—1998镁合金化学分析方法原子吸收光谱法测定铜含量 HB 5219.4—1998镁合金化学分析方法邻菲啉光度法测定铁含量 HB 5219.5—1998镁合金化学分析方法原子吸收光谱法测定铁含量ML HB 5219.6—1998镁合金化学分析方法高碘酸钾光度法测定锰含量(含锆、稀土) HB 5219.7—1998镁合金化学分析方法高碘酸钾光度法测定锰含量(不含锆、稀土) HB5219.8—1998镁合金化学分析方法原子吸收光谱法测定锰含量 HB 5219.9—1998镁合金化学分析方法硅钼蓝光度法测定硅含量 HB 5219.10—1998镁合金化学分析方法丁二酮肟萃取光度法测定镍含量 HB 5219.11—1998镁合金化学分析方法原子吸收光谱法测定镍含量 HB 5219.12—1998镁合金化学分析方法三正辛胺萃取EDTA容量法测定锌含量 HB 5219.13—1998镁合金化学分析方法原子吸收光谱法测定锌含量 HB 5219.14—1998镁合金化学分析方法 EDTA容量法测定锆含量 HB 5219.15—1998镁合金化学分析方法槲皮素光度法测定溶解锆含量 HB 5219.16—1998镁合金化学分析方法 EDTA容量法测定铝含量M HB 5219.17—1998镁合金化学分析方法铬天青S光度法测定铝含量 HB 5219.18—1998镁合金化学分析方法草酸盐重量法测定稀土总量 HB 5219.19—1998镁合金化学分析方法三溴偶氮胂光度法测定铈含量 HB 5219.20—1998镁合金化学分析方法原子吸收光谱法测定银含量 HB 5219.21—1998镁合金化学分析方法依来铬氰蓝R光度法测定铍含量HB 5220.1—1995高温合金化学分析方法库仑法测定碳含量HB 5220.2—1995高温合金化学分析方法气体容量法测定碳含量ML HB 5220.3—1995高温合金化学分析方法高频感应加热红外线吸收法测定碳含量 HB 5220.4—1995高温合金化学分析方法还原蒸馏吸光光度法测定硫含量 HB 5220.5—1995高温合金化学分析方法碘酸钾容量法测定硫含量HB 5220.6—1995高温合金化学分析方法高频感应加热红外线吸收法测定硫含量M HB 5220.7—1995高温合金化学分析方法乙醚萃取钼蓝吸光光度法测定磷含量 HB 5220.8—1995高温合金化学分析方法正丁醇三氯甲烷萃取吸光光度法测定磷含量 HB 5220.9—1995高温合金化学分析方法重量法测定硅含量HB 5220.10—1995高温合金化学分析方法硅钼蓝吸光光度法测定硅含量 HB 5220.11—1995高温合金化学分析方法硝酸铵氧化硫酸亚铁铵容量法测定锰含量HB 5220.12—1995高温合金化学分析方法氧化锌分离硫酸亚铁铵容量法测定锰含量 HB 5220.13—1995高温合金化学分析方法过碘酸钾吸光光度法测定锰含量 HB 5220.14—1995高温合金化学分析方法火焰原子吸收光谱法测定锰含量 HB 5220.15—1995高温合金化学分析方法过硫酸铵氧化亚铁容量法测定铬含量 HB 5220.16—1995高温合金化学分析方法硫酸亚铁铵容量法测定钒含量 HB5220.17—1995高温合金化学分析方法钽试剂三氯甲烷萃取吸光光度法测定钒含量 HB 5220.18—1995高温合金化学分析方法二安替比啉甲烷吸光光度法测定钛含量 HB 5220.19—1995高温合金化学分析方法铜铁试剂、铜试剂分离-EDTA容量法测定铝含量 HB 5220.20—1995高温合金化学分析方法铬天青S吸光光度法测定铝含量 HB 5220.21—1995高温合金化学分析方法 EDTA容量法测定钼含HB 5220.22—1995高温合金化学分析方法硫氰酸盐吸光光度法测定钼含量 HB 5220.23—1995高温合金化学分析方法丁二酮肟-EDTA容量法测定镍含量 HB 5220.24—1995高温合金化学分析方法丁二酮肟吸光光度法测定镍含量 HB 5220.25—1995高温合金化学分析方法铁氰化钾电位滴定法测定钴含量 HB。
详解仿金电镀工艺配方与操作技巧
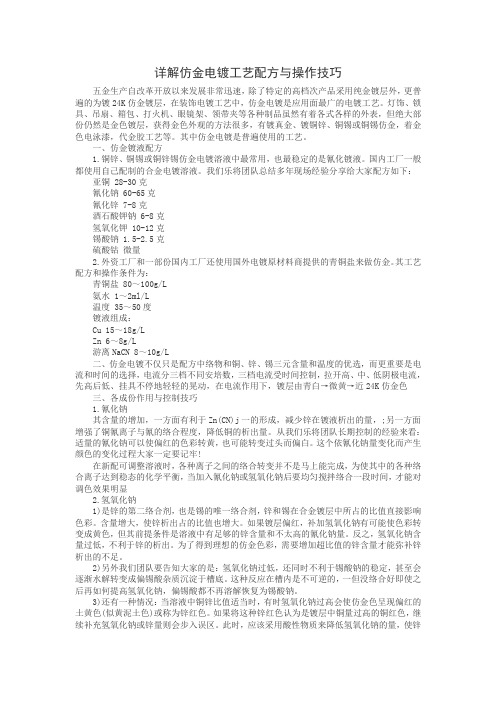
详解仿金电镀工艺配方与操作技巧五金生产自改革开放以来发展非常迅速,除了特定的高档次产品采用纯金镀层外,更普遍的为镀24K仿金镀层,在装饰电镀工艺中,仿金电镀是应用面最广的电镀工艺。
灯饰、锁具、吊扇、箱包、打火机、眼镜架、领带夹等各种制品虽然有着各式各样的外表,但绝大部份仍然是金色镀层,获得金色外观的方法很多,有镀真金、镀铜锌、铜锡或铜锡仿金,着金色电泳漆,代金胶工艺等。
其中仿金电镀是普遍使用的工艺。
一、仿金镀液配方1.铜锌、铜锡或铜锌锡仿金电镀溶液中最常用,也最稳定的是氰化镀液。
国内工厂一般都使用自己配制的合金电镀溶液。
我们乐将团队总结多年现场经验分享给大家配方如下:亚铜 28-30克氰化钠 60-65克氰化锌 7-8克酒石酸钾钠 6-8克氢氧化钾 10-12克锡酸钠 1.5-2.5克硫酸钴微量2.外资工厂和一部份国内工厂还使用国外电镀原材料商提供的青铜盐来做仿金。
其工艺配方和操作条件为:青铜盐 80~100g/L氨水 1~2ml/L温度 35~50度镀液组成:Cu 15~18g/LZn 6~8g/L游离NaCN 8~10g/L二、仿金电镀不仅只是配方中络物和铜、锌、锡三元含量和温度的优选,而更重要是电流和时间的选择,电流分三档不同安培数,三档电流受时间控制,拉开高、中、低阴极电流,先高后低、挂具不停地轻轻的晃动,在电流作用下,镀层由青白→微黄→近24K仿金色三、各成份作用与控制技巧1.氰化钠其含量的增加,一方面有利于Zn(CN)j一的形成,减少锌在镀液析出的量,;另一方面增强了铜氰离子与氰的络合程度,降低铜的析出量。
从我们乐将团队长期控制的经验来看:适量的氰化钠可以使偏红的色彩转黄,也可能转变过头而偏白。
这个依氰化钠量变化而产生颜色的变化过程大家一定要记牢!在新配可调整溶液时,各种离子之间的络合转变并不是马上能完成,为使其中的各种络合离子达到稳态的化学平衡,当加入氰化钠或氢氧化钠后要均匀搅拌络合一段时间,才能对调色效果明显2.氢氧化钠1)是锌的第二络合剂,也是锡的唯一络合剂,锌和锡在合金镀层中所占的比值直接影响色彩。
电镀原理及方法

电镀原理及方法电镀简单来说,电镀指借助外界直流电的作用,在溶液中进行电解反应,使导电体例如金属的表面沉积一金属或合金层N-L6u:i S电镀常用公式及数据z-p8j E.` y+h公式单镀层厚度合金镀层厚度侯氏槽一次电流分布六西格玛品质论坛 b k%i1U l O s.v5~ j2r镀液分散能力1.单镀层厚度2.合金镀层厚度.r5[8N&e8r Y3.侯氏槽一次电流分布CD=I(c1-c2 log L)六西格玛品质论坛9w L F.Gi U.H&^0I267ml、534ml 及1000ml 槽CD 电流密度(A/ft2)I 总电流(A)L 与高电流密度区边缘的距离(in)c1, c2 常数250ml 槽CD 电流密度(A/dm2)I 总电流(A)L 与高电流密度区边缘的距离(cm) 六西格玛品质论坛-E:C*}:H)I z$D"jc1, c2 常数%@!B(B ?:l常数V m q [2q(c S267ml及534ml槽-质量-SPC ,six sigma,TS16949,MSA,FMEA.p%` w U xc1=27.7 c2=48.71000ml槽六西格玛品质论坛'?3U h8A f H ?c1=18.0 c2=28.3250ml槽c1=5.10 c2=5.24L 介乎於0.64至8.25 cm-质量-SPC ,six sigma,TS16949,MSA,FMEA-m K O5s2[9Z4K l#s硫酸銅鍍液主要有硫酸銅、硫酸和水,甚至也有其他添加劑。
硫酸銅是銅離子(Cu2+)的來源,當溶解於水中會離解出銅離子,銅離子會在陰極(工件)還原(得到電子)沈積成金屬銅。
這個沈積過程會受鍍浴的狀況如銅離子濃度、酸鹼度(pH)、溫度、攪拌、電流、添加劑等影響。
| L(l&Z2DR陰極主要反應: Cu2+(aq) + 2e- →Cu (s)電鍍過程浴中的銅離子濃度因消耗而下降,影響沈積過程。
JIS H 3300:2009铜及び铜合金の継目无管(日文)
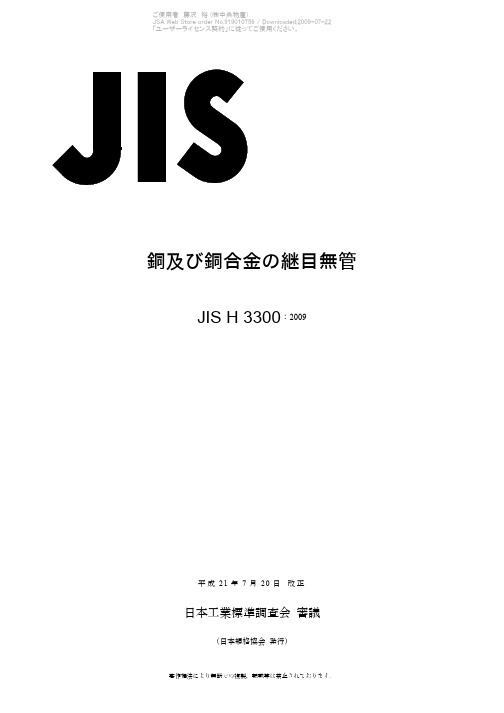
銅及び銅合金の継目無管JIS H 3300:2009平成21年7月20日改正日本工業標準調査会審議(日本規格協会発行)H 3300:2009 _____________________________________________________主 務 大 臣:経済産業大臣 制定:昭和52.5.1 改正:平成21.7.20 官 報 公 示:平成21.7.21 原案作成協力者:日本伸銅協会(〒110-0005 東京都台東区上野1-10-10 うさぎやビル TEL 03-3836-8801)審 議 部 会:日本工業標準調査会 標準部会(部会長 二瓶 好正) 審議専門委員会:非鉄金属技術専門委員会(委員会長 神尾 彰彦)この規格についての意見又は質問は,上記原案作成協力者又は経済産業省産業技術環境局 基準認証ユニット産業基盤標準化推進室(〒100-8901 東京都千代田区霞が関1-3-1 E-mail:qqgcbd@meti.go.jp 又はFAX 03-3580-8625)にご連絡ください。
なお,日本工業規格は,工業標準化法第15条の規定によって,少なくとも5年を経過する日までに日本工業標準調査会の審議に付され,速やかに,確認,改正又は廃止されます。
日本工業標準調査会標準部会 非鉄金属技術専門委員会 構成表氏名所属(委員会長) 神 尾 彰 彦 東京工業大学名誉教授 (委員) 木股 三 株式会社ビスキャス小 出 正 登 日本伸銅協会(三菱マテリアル株式会社) 近 藤 良太郎 社団法人日本電機工業会齋 藤 鐵 哉 独立行政法人物質・材料研究機構 下 村 孝 社団法人日本鉄道車輌工業会 田 中 護 史 財団法人日本船舶技術研究協会 田 村 泰 夫 日本鉱業協会中 野 利 彦 株式会社神戸製鋼所中 村 守 独立行政法人産業技術総合研究所 西 村 尚 東京都立大学名誉教授 林 央 独立行政法人理化学研究所 町 田 克 己 住友金属鉱山株式会社吉 田 英 雄 社団法人軽金属学会(住友軽金属工業株式会社) (専門委員) 野 原 慈 久財団法人日本規格協会H 3300:2009目 次ページ序文 (1)1適用範囲 (1)2引用規格 (1)3用語及び定義 (2)4種類,等級及び記号 (2)5品質 (3)5.1外観 (3)5.2化学成分 (3)5.3機械的性質及び物理的性質の試験項目 (5)5.4機械的性質 (8)5.5結晶粒度 (14)5.6押広げ性 (14)5.7へん平性 (14)5.8非破壊検査特性 (14)5.9導電率 (14)5.10水素ぜい性 (15)5.11時期割れ性 (15)5.12浸出性能 (15)6寸法及びその許容差 (15)6.1寸法の指定 (15)6.2代表寸法 (15)6.3寸法の許容差 (16)6.4直管の曲がりの最大値 (19)7試験 (20)7.1サンプリング (20)7.2化学分析試験 (20)7.3引張試験 (20)7.4硬さ試験 (20)7.5結晶粒度試験 (20)7.6押広げ試験 (21)7.7へん平試験 (21)7.8渦流探傷試験 (21)7.9水圧試験 (22)7.10空圧試験 (22)7.11導電率試験 (22)H 3300:2009 目次ページ7.12水素ぜい化試験 (23)7.13時期割れ試験 (23)7.14浸出性能試験 (23)8検査 (23)9表示 (24)附属書A(参考)銅及び銅合金継目無管の代表寸法 (25)解 説 (28)H 3300:2009まえがきこの規格は,工業標準化法に基づき,日本工業標準調査会の審議を経て,経済産業大臣が改正した日本工業規格である。
电镀层和化学处理层技术条件
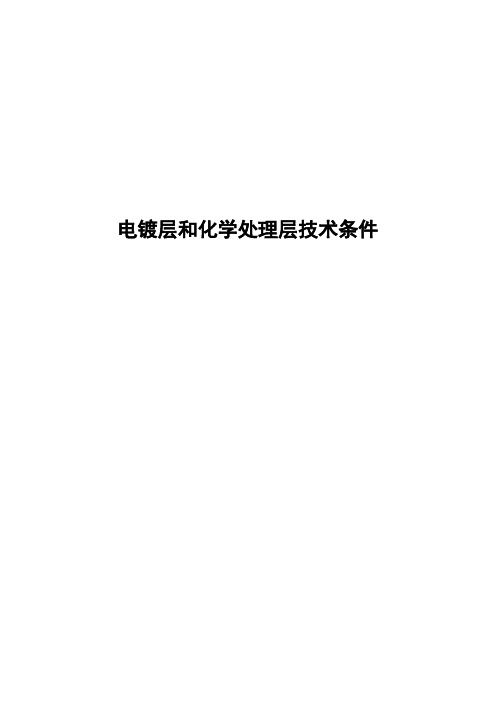
电镀层和化学处理层技术条件目录1 范围 (2)2 标准性引用文件 (2)3 技术要求 (2)3.1 使用条件 (2)3.2 选择原则 (2)3.3 锌电镀层 (3)3.4 铜电镀层 (3)3.5 镍镀层 (3)3.6 铬镀层 (4)3.7 锡镀层 (4)3.8 银镀层 (4)4 覆盖层厚度标识方法 (4)4.1 覆盖层组成部分 (4)4.2 紧固件镀层厚度 (7)5 外表质量及镀层检验 (7)5.1 外表质量 (7)5.2 湿热试验 (8)5.3 盐雾试验 (8)5.4 覆层 (8)6 运输及贮存 (8)6.1 运输 (8)6.2 贮存 (8)电镀层和化学处理层技术条件1 范围本标准规定了产品零〔部〕件金属电镀层和化学处理层〔以下简称覆盖层〕的使用条件分类、选用原则、厚度及标识方法、外表质量和镀层检验、运输及贮存。
本标准适用于产品零〔部〕件〔金属和非金属制件〕的电镀和化学处理。
本标准在图样、技术文件中引用时,其标注方法为:电镀层和化学处理按Q/JC J129。
2 标准性引用文件以下文件对于本文件的应用是必不可少的。
但凡注日期的引用文件,仅所注日期的版本适用于本文件。
但凡不注日期的引用文件,其最新版本〔包括所有的修改单〕适用于本文件。
GB/T 131—2006 产品几何技术标准〔GPS〕技术产品文件中外表结构的表示法GB/T 2423.4—2008 电工电子产品环境试验第2部分:试验方法试验Db:交变湿热〔12h+12h循环〕GB/T 2423.17—2008 电工电子产品环境试验第2部分:试验方法试验Ka:盐雾GB/T 2828.1—2012 计数抽样检验程序第1部分:按接收质量限〔AQL〕检索的逐批检验抽样计划GB/T 5267.1—2002 紧固件电镀层GB/T 9797—2005 金属覆盖层镍+铬和铜+镍+铬电镀层GB/T 9798—2005 金属覆盖层镍电沉积层GB/T 9799—2011 金属及其他无机覆盖层钢铁上经过处理的锌电镀层GB/T 11379—2008 金属覆盖层工程用铬电镀层GB/T 12599—2002 金属覆盖层锡电镀层技术标准和试验方法GB/T 12600—2005 金属覆盖层塑料上镍+铬电镀层GB/T 13346—2012 金属及其它无机覆盖层钢铁上经过处理的镉电镀GB/T 13911—2008 金属镀覆和化学处理标识方法GB/T 17461—1998 金属覆盖层锡-铅合金电镀层GB/T 17462—1998 金属覆盖层锡-镍合金电镀层ISO 4521 金属覆盖层工程用银和银合金电镀层3 技术要求3.1 使用条件覆盖层使用条件,按气候环境变化的程度分为三类。
塑胶件电镀设计手册
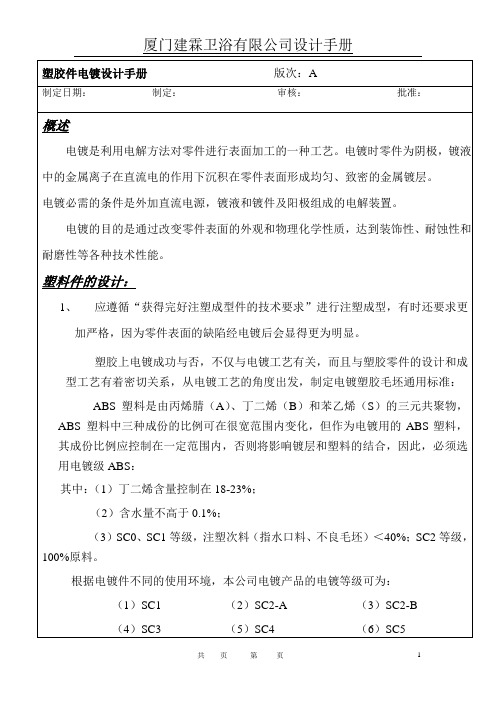
D、不影响零件性能的翘曲的允许的。
3、膜厚测试(ASTM B504)
PVD/SC2-A:
1、CASS 8H
2、冷热循环:75℃/1H→-30℃/1H共3个循环
PVD/SC2-B(KOHLER):
1、CASS 8 H
2、冷热冲击(-40℃小时→21℃1小时共3个循环→放置12—48小时,再进行79℃热水)(CSA B125)
(3)处理:烘箱内设定80℃,放置2Hr。
本公司生产之产品,按照最终客户的使用要求,可分为:装饰性镀件、功能性镀件。从最终客户的使用角度而言,装饰性镀件与功能性镀件无论是其外观、尺寸还是功能的要求都有明显的差别。据此,为了更好地满足顾客的使用要求,特制定本标准,明确在品质检验中对于毛坯件的不同要求。
其中:(1)丁二烯含量控制在18-23%;
(2)含水量不高于0.1%;
(3)SC0、SC1等级,注塑次料(指水口料、不良毛坯)<40%;SC2等级,100%原料。
根据电镀件不同的使用环境,本公司电镀产品的电镀等级可为:
(1)SC1(2)SC2-A(3)SC2-B
(4)SC3(5)SC4(6)SC5
2、零件的外形应有利于获得均匀的镀层,如较大的平面中间要稍微突起,突起度约为0.10----0.15mm/cm;不应有锐边,尖角和锯齿形,若必须有时,其边缘应尽量倒圆,外角的倒圆半径≥1mm、内角的倒圆半径为≥0.5mm;盲孔及凹槽的底棱边应圆滑过度,其半径宜>3mm;不应有盲孔,如必须有时,其深度应为它的直径1/2-1/3,否则对孔底的镀层应不做要求;V形沟槽的宽度与深之比应大于3,槽或孔之距离不要太近,其边缘都应倒圆。
接插件镀金、镀银层变色原因及防变色措施

接插件镀金、镀银层变色原因及防变色措施摘要:分别探讨了接插件镀金和镀银层变色的原因。
镀金层的变色原因如下:基体质量不符合要求,产品的设计及电镀工艺存在缺陷(包括产品前处理工艺、金阻挡层镀液体系的选择、镀液的维护、电镀工艺参数的选择和电镀方式等的不妥当),镀后处理不力,产品使用环境的差异等镀银层变色的原因如下:基体形状复杂且其表面粗糙度高,电镀工艺不完善,包装方式不当,产品使用环境差异等。
提出了镀层的防变色措施:提高基体质量,减少设计缺陷,改进电镀工艺,加强镀后工序管理,根据产品的使用环境对其制定不同的质量要求等关键词:接插件;镀金;镀银;变色;措施;1 前言在接插件的制造工艺中,为了保证产品的导电性能和可靠性,大部分产品的接触件以及部分产品的壳体均采用了镀金或镀银进行表面处理。
由于在产品的加工和使用过程中受到各种因素的影响,部分产品的镀层表面会在较短时间内出现变色现象。
而一旦镀层表面开始变色,产品的电气性能也会随之下降。
为了避免这种现象发生,针对金、银镀层的变色机理,人们采取了各种措施尽力延缓镀层在规定的时间内出现的颜色变化。
以下为目前在接插件制造行业中发生镀层变色原因的分析以及常用的解决镀金、镀银层变色问题的一些基本方法。
2 金镀层的变色原因金是一种比较稳定的金属元素,在大气环境中几乎不与其它物质反应,因此不会受到各种腐蚀气体侵袭而发生化学变化。
接插件金镀层变色的原因主要是受到基体金属(铜及铜合金)通过金层孔隙向镀层表面迁移的影响。
因为金层与基体金属之间存在着电位差,在遇到腐蚀介质时这种电位差会导致基体金属被腐蚀,当腐蚀物富集在金层表面时金层就改变了颜色。
在接插件的制造行业中导致金层很快变色的原因主要还体现在以下几个方面。
2.1 基体质量达不到要求基材杂质含量和基体表面光洁度是两项衡量电接触体基体质量的重要指标。
近几年来,由于市场竞争加剧,加上金属材料涨价因素,使得一些基体制造厂为了降低生产成本,采用一些不合规格的材料,甚至采用回收铜加工制造基体。
国家标准物质项目表(一级标准物质)-全国标准物质管理委员会

锆及锆合金化学分析方法第27部分:痕量杂质元素的测定电感耦合等离子体质谱法编制说明(预审稿)西北有色金属研究院2018.11《锆及锆合金化学分析方法第27部分:痕量杂质元素的测定-电感耦合等离子体质谱法》编制说明一、工作简况1.1 任务来源及计划要求根据国标委《国家标准委关于下达2017年第四批国家标准制修订计划的通知》(国标委综合〔2017〕128号)精神的文件精神,由西北有色金属研究院负责起草国家标准《锆及锆合金化学分析方法第27部分:痕量杂质元素的测定电感耦合等离子体质谱法》国家标准,项目计划编号为20173516-T-610,项目要求2018年度完成。
1.2 起草单位情况西北有色金属金属研究院成立于1965年。
是我国重要的稀有金属材料研究基地和行业技术开发中心、是国内稀有金属科研生产基地项目和稀有金属材料加工国家工程研究中心、金属多孔材料国家重点实验室、超导材料制备国家工程实验室、中国有色金属工业西北质量监督检验中心、层状金属复合材料国家地方联合工程研究中心等的依托单位,地处西安、宝鸡两地六区。
研究院现有资产总值64.6亿元,仪器设备3000多台套,占地3428亩,正式职工2874人,其中科技人员近千余人,有中国工程院院士1人,教授、高工200多人,博士、硕士300余名。
形成了以钛产业为主业,覆盖超导材料、金属纤维及制品、稀贵金属材料等产业的多元化格局,其产品广泛应用于航空、航天、航海、信息、电子、能源、环保等国民经济重要领域。
材料分析中心其前身可追溯至成立于1966年11月的西北有色金属研究院第三研究室(金属物理研究室)和第二研究室(化学分析研究室)。
在四十多年的发展中,中心完成各类课题320项,获奖成果24项,其中省部级科技进步二等奖4项、三等奖9项,市局级科技进步一等奖1项、二等奖1项。
制/修订国家、国家标准50多项;主持了《钛及钛合金化学分析方法》、《锆及锆合金化学分析方法》等标准方法,研制了《钛合金化学成分标准物质》一套,并获得科技部三等奖;申报专利10余项,发表论文500余篇。
金银铑多层复合电镀工艺

金银铑多层复合电镀工艺2016-11-25 14:32来源:内江洛伯尔材料科技有限公司作者:研发部金银铑多层复合电镀工艺多层贵金属金、银、铑电镀表面处理工艺是比较复杂,成本较高的工艺处理方法。
其中的镀金、镀银工序和镀铑工序的电镀液配方、电镀液pH值、电镀温度、电镀时间、电极电流密度等技术参数都有特殊的要求。
要获得贵金属金、银、铑多层复合电镀工艺技术参数需要通过长时间、甚至很多次的试验。
多层贵金属金、银、铑电镀首先要解决镀银工件表面变色问题,其次要解决工艺参数的合理性,如何避免多层复合电镀工件不出现镀层脱落现象是比较困难的事情。
工件的复合镀层稳定性是多层复合电镀工艺的重要指标。
现有技术镀银工序一般是采用传统的氰化物镀银配方,加进包括酒石酸锑钾组成的增硬剂和包括亚硒酸(或盐)、导电盐、催化剂、有机表面活性剂组成的光亮剂,利用现有吊镀和滚镀的镀银设备,在15°c-25°C温度下,阴极电流密度0. 1- 2 (安培/平方分米)的工艺条件下镀出银层。
镀金工艺通常是用电解或其他化学方法,使金子附着到金属或别的物体表面上,形成一层薄金。
因为各工厂实际的生产线,使用的设备、药水体系并不完全相同,所以需要针对产品和实际情况进行针对性的分析和处理来解决电镀金层发黑的问题。
电镀金层一般都很薄,反映在电镀金的表面问题有很多是由于电镀镍的表现不良而引起的。
传统电镀常见的问题是电镀镍层的厚度控制,电镀镍层偏薄会引起产品外观会有发白和发黑的现象,需要电镀到5UM左右的镍层厚度才足够。
其次是电镀镍缸的药水状况,如果镍缸的药水长期得不到良好的保养,没有及时进行碳处理,电镀出来的镍层容易产生片状结晶,镀层的硬度增力口、脆性增强,严重的会产生镀层发黑的问题。
这是很多人容易忽略的控制重点,也往往是产生问题的重要原因。
并且要及时进行彻底的碳处理,才能恢复药水的活性和电镀溶液的干净。
再其次是金缸的控制,金缸的控制一般只要保持良好的药水过滤和补充,金缸的受污染程度和稳定性比镍缸会好一些。
配方l无氰铜锌锡三元合金仿金镀液
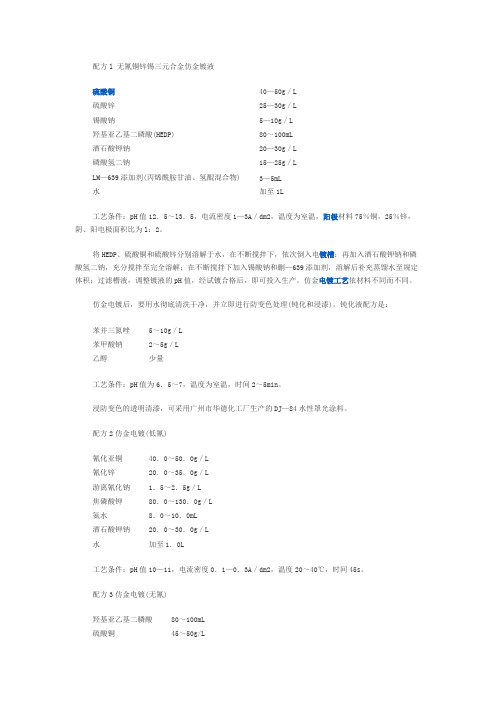
配方l 无氰铜锌锡三元合金仿金镀液硫酸铜40—50g/L硫酸锌25—30g/L锡酸钠5—10g/L羟基亚乙基二磷酸(HEDP)80~100mL酒石酸钾钠20—30g/L磷酸氢二钠15—25g/LLM—639添加剂(丙烯酰胺甘油、氢醌混合物)3—5mL水加至1L工艺条件:pH值12.5~l3.5,电流密度1—3A/dm2,温度为室温,阳极材料75%铜,25%锌,阴、阳电极面积比为l:2。
将HEDP、硫酸铜和硫酸锌分别溶解于水,在不断搅拌下,依次倒入电镀槽;再加入酒石酸钾钠和磷酸氢二钠,充分搅拌至完全溶解;在不断搅拌下加入锡酸钠和删—639添加剂,溶解后补充蒸馏水至规定体积;过滤槽液,调整镀液的pH值,经试镀合格后,即可投入生产。
仿金电镀工艺依材料不同而不同。
仿金电镀后,要用水彻底清洗干净,并立即进行防变色处理(钝化和浸漆)。
钝化液配方是:苯并三氮唑5~10g/L苯甲酸钠2~5g/L乙醇少量工艺条件:pH值为6.5~7,温度为室温,时间2~5min。
浸防变色的透明清漆,可采用广州市华德化工厂生产的DJ—84水性罩光涂料。
配方2仿金电镀(低氰)氰化亚铜40.0~50.0g/L氰化锌20.0~35.0g/L游离氰化钠1.5~2.5g/L焦磷酸钾80.0~130.0g/L氨水8.0~10.0mL酒石酸钾钠20.0~30.0g/L水加至1.0L工艺条件:pH值10—11,电流密度0.1—0.3A/dm2,温度20~40℃,时间45s。
配方3仿金电镀(无氰)羟基亚乙基二膦酸80~100mL硫酸铜45~50g/L硫酸锌20g/L碳酸钠20~30g/L柠檬酸钾20~30g/L添加剂1~2g/L水加至lL工艺条件:pH值13~13.5,电流密度1.5—3.5 A/dm2,阴阳极面积比为2:1,阳极用黄铜板,温度为室温,时间为40~60s。
配方4无氰电镀仿金镀液硫酸铜40~50g/L硫酸锌15~20g/L羟基亚乙基二膦酸(HEDP,100%)70~90g/L添加剂SC(上海皮革金属厂生产)150mL水加至1L工艺条件:pH值11~13,温度35—45℃,电流密度l.5~2A/dm2,时间30—45s。
金属镀层表示方法

指导性技术文件0BD.600.027金属镀覆和化学处理表示方法1范围本标准依据GB/T13911—92《金属镀履和化学处理表示方法》而制定的。
本 标准规定了金属镀覆和化学处理表示方法;及各种使用条下防止腐蚀的电镀层。
本标准适用于本公司产品零件、部件的金属镀覆和化学处理的表示方法。
2 引用标准GB9799—1988《金属覆盖层 钢铁上的锌电镀层》 GB9798—1988《金属覆盖层 镍电镀层》GB9800—1988《电镀锌和电镀镉的铬酸盐转化膜》 GB12599—1990《金属覆盖层 锡电镀层》GB12306—1990《金属覆盖层 工程用银和银合金电镀层》 3 表示方法3.1 金属镀覆的符号按下列顺序表示:。
3.1.1 基本材料在图样或有关的技术文件中有明确规定时,允许省略。
3.1.2 镀覆层特征、镀层厚度或后处理无具体要求时,允许省略。
例1 Fe/Ep.Zn12.c2C(钢材,电镀锌12μm 以上,彩虹铬酸盐处理2级C 型) 例2 Fe/Ep .Cu10Ni10bCr0.3mc1/60GD.600.027例3 Cu/ Ep .Ni10bCr0.3r(铜材,电镀光亮镍10μm 以上,普通铬0.3μm 以上) 例4 Cu/ Ep .Ag10(铜材,电镀银10μm 以上) 例5 Cu/ Ep .Sn8 (铜材,电镀锡8μm 以上) 3.2 化学处理和电化学处理的符号按下列顺序表示。
3.2.1 基体材料在图样或有关的技术文件中有明确规定时,允许省略。
3.2.2 对化学处理或电化处理的处理特征、后处理或颜色无具体要求时,允许省略。
例1 AI/Et .A .CI (BK )(铝材,电化学处理,阳极氧化,着黑色) 例2 Cu/Ct .P (铜材,化学处理,钝化)例3 Fe/ Ct .MnPh (钢材,化学处理,磷酸锰盐处理) 例4 AI/Et .Ec (铝材,电解着色) 4 表示符号4.1 基体材料表示符号常用基体材料的表示符号见表1 表14.2 镀覆方法、处理方法表示符号2/60GD.600.027表24.3 镀覆层表示符号镀覆层名称用镀层的化学元素符号表示。
接插件镀金、镀银层变色原因及防变色措施

【经验交流】!!收稿日期:"##$%#&%"’!!修回日期:"##$%#(%"#!!作者简介:沈涪()*$’%),男,高级工程师,主要从事电镀工艺研究工作。
作者联系方式:(+,-./)01-2345236-578.2-9:5,。
接插件镀金、镀银层变色原因及防变色措施沈涪(四川绵阳华丰企业集团公司,绵阳!&")###)摘!要:分别探讨了接插件镀金和镀银层变色的原因。
镀金层的变色原因如下:基体质量不符合要求,产品的设计及电镀工艺存在缺陷(包括产品前处理工艺、金阻挡层镀液体系的选择、镀液的维护、电镀工艺参数的选择和电镀方式等的不妥当),镀后处理不力,产品使用环境的差异等。
镀银层变色的原因如下:基体形状复杂且其表面粗糙度高,电镀工艺不完善,包装方式不当,产品使用环境差异等。
提出了镀层的防变色措施:提高基体质量,减少设计缺陷,改进电镀工艺,加强镀后工序管理,根据产品的使用环境对其制定不同的质量要求等。
关键词:接插件;镀金;镀银;变色;措施;中图分类号:;<)$’9)&;;<)$’9)=!!!!!文献标识码:>文章编号:)##?%""(@("##$))#%##)(%#’!"#$%&’%$()"*&+&"$,-"#$%&’%$(#+&%&-"$-.+"&*#+&/0(/1,"$,&%12+#341"-+,)/$$+)-/#&A A BC+D E156&-#")-:;0F :-18F85G H-I2.80.2335/6-268./JFIKL/-HF6:522F:H5I8MFIF 8H16.F6IF8LF:H.JF/49;0F :-18F85G H-I2.8K 0.2335/6F/F:HI56FL58.H MFIF -8G5//5M8:H0F 81N8HI-HF O1-/.K H4.825H 1L H5H0F 8H-26-I69PFGF:H8FQ.8H .26F8.325G LI56K 1:H -26F/F:HI5L/-H.23LI5:F88(.2:/16.23LI561:H LIFHIF-HK ,F2H ,H0F 5LH.525G N-H0848HF,G5I 35/6N-II.FI ,N-H0,-.2K HF2-2:F ,5LH.525G F/F:HI5L/-H.23LI5:F88L-I-,FHFI -26M-485G F/F:HI5L/-H.23,FH:9)9R58HKHIF-H,F2H8MFIF .2-6FO1-HF -26 6.GGFIF2:F 5G LI561:H -LL/.:-H.52F2J.I52,F2H8,FH:9S-18F85G 8./JFI F/F:HI56FL58.H H-I2.80.23MFIF -8G5//5M8::5,L/.:-HF680-LF 5G 81N8HI-HF8-260.30I51302F885G 81IK G-:F ,.2:5,L/FHF F/F:HI5L/-H.23LI5:F88,1281.H-N/F M-45G L-:T.23-266.GGFIF2:F 5G LI561:H -LL/.:-H.52F2J.I52,F2H8,FH:9;0F LIFJF2H.JF ,F-81IF8-3-.28H H-I2.80.23.2:/16F .,K LI5JF,F2H 5G 81N8HI-HF O1-/.H4,6F:IF-8.236FGF:H 5G 6F8.32,.,LI5J.23F/F:HI5L/-H.23LI5:F88,8HIF23H0F2.23H0F ,-2-3FK ,F2H 5G L58HKHIF-H,F2H -26.28H.H1H.236.GGFIF2H O1-/.H4IFK O1F8H8-::5I6.23H5H0F LI561:H -LL/.F6.2J-I.518F2J.I52K ,F2H8,FH:97+89/#,&::522F:H5I ;35/6F/F:HI5L/-H.23;8./JFI F/F:HI5KL/-H.23;H-I2.80.23;,F-81IF5*-’/#:&",,#+&&:C1-GF23+2HFILI.8F UI51L S59,V.-2K 4-23&")###,S0.2-;<前言!!在接插件的制造工艺中,为了保证产品的导电性能和可靠性,大部分产品的接触件以及部分产品的壳体均采用了镀金或镀银进行表面处理。
PSP-2188+铜及铜合金的镀银
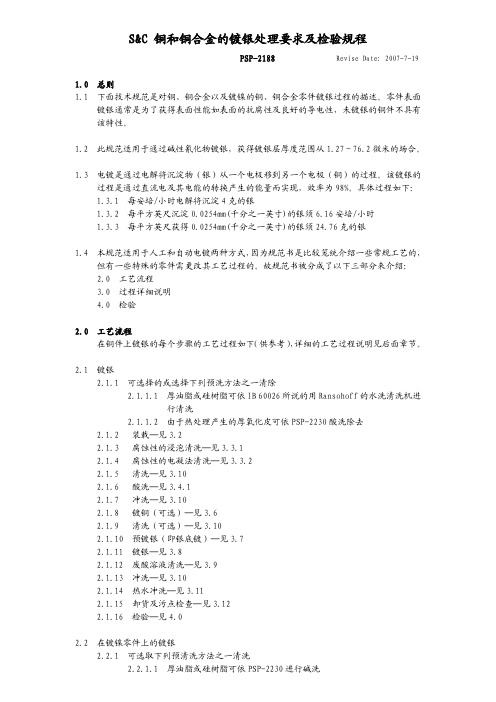
S&C 铜和铜合金的镀银处理要求及检验规程PSP-2188Revise Date: 2007-7-191.0 总则1.1 下面技术规范是对铜、铜合金以及镀镍的铜、铜合金零件镀银过程的描述。
零件表面镀银通常是为了获得表面性能如表面的抗腐性及良好的导电性,未镀银的铜件不具有该特性。
1.2 此规范适用于通过碱性氰化物镀银,获得镀银层厚度范围从1.27~76.2微米的场合。
1.3 电镀是通过电解将沉淀物(银)从一个电极移到另一个电极(铜)的过程。
该镀银的过程是通过直流电及其电能的转换产生的能量而实现,效率为98%。
具体过程如下:1.3.1 每安培/小时电解将沉淀4克的银1.3.2 每平方英尺沉淀0.0254mm(千分之一英寸)的银须6.16安培/小时1.3.3 每平方英尺获得0.0254mm(千分之一英寸)的银须24.76克的银1.4 本规范适用于人工和自动电镀两种方式,因为规范书是比较笼统介绍一些常规工艺的,但有一些特殊的零件需更改其工艺过程的。
故规范书被分成了以下三部分来介绍:2.0 工艺流程3.0 过程详细说明4.0 检验2.0 工艺流程在铜件上镀银的每个步骤的工艺过程如下(供参考),详细的工艺过程说明见后面章节。
2.1 镀银2.1.1 可选择的或选择下列预洗方法之一清除2.1.1.1 厚油脂或硅树脂可依IB 60026所说的用Ransohoff的水洗清洗机进行清洗2.1.1.2 由于热处理产生的厚氧化皮可依PSP-2230酸洗除去2.1.2 装载─见3.22.1.3 腐蚀性的浸泡清洗─见3.3.12.1.4 腐蚀性的电凝法清洗─见3.3.22.1.5 清洗─见3.102.1.6 酸洗─见3.4.12.1.7 冲洗─见3.102.1.8 镀铜(可选)─见3.62.1.9 清洗(可选)─见3.102.1.10 预镀银(即银底镀)─见3.72.1.11 镀银─见3.82.1.12 废酸溶液清洗─见3.92.1.13 冲洗─见3.102.1.14 热水冲洗─见3.112.1.15 卸货及污点检查─见3.122.1.16 检验─见4.02.2 在镀镍零件上的镀银2.2.1 可选取下列预清洗方法之一清洗2.2.1.1 厚油脂或硅树脂可依PSP-2230进行碱洗2.2.1.2 由于热处理产生的厚氧化皮可依PSP-2230酸洗除去2.2.2 装载─见3.22.2.3 腐蚀性的浸泡清洗─见3.3.12.2.4 腐蚀性的电凝法清洗─见3.3.22.2.5 清洗─见3.102.2.6 酸洗─见3.4.12.2.7 冲洗─见3.102.2.8 预镀镍(即镍底镀)--见PSP 25703.62.2.9 镀镍--见PSP 25703.72.2.10 废酸溶液清洗--见PSP 25703.82.2.11 冲洗--见3.102.2.12 酸洗--见3.4.22.2.13 冲洗--见3.102.2.14 预镀银(即银底镀)--见3.72.2.15 镀银--见3.82.2.16 废酸溶液清洗—见3.92.2.17 冲洗—见3.102.2.18 热水冲洗—见3.112.2.19 卸货及污点检查—见3.122.2.20 检验—见4.03.0 工序说明3.1 预清洗—有时买来的零件因为太脏或有斑点而不能用正常的预清洗程序进行适当的清洁。
镀银黑化件表面腐蚀问题的解决
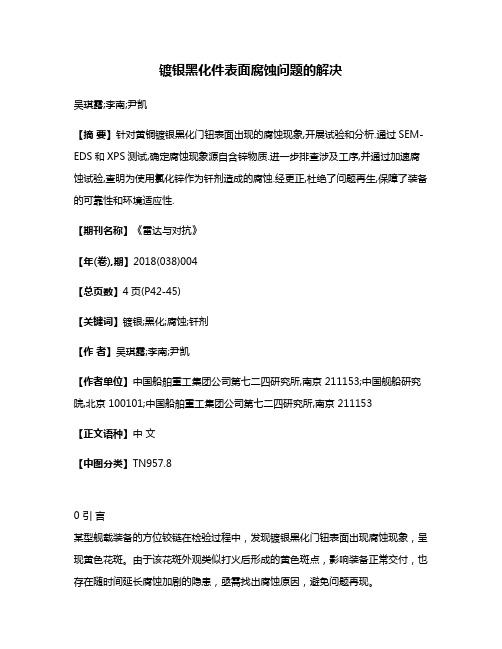
镀银黑化件表面腐蚀问题的解决吴琪露;李南;尹凯【摘要】针对黄铜镀银黑化门钮表面出现的腐蚀现象,开展试验和分析.通过SEM-EDS和XPS测试,确定腐蚀现象源自含锌物质.进一步排查涉及工序,并通过加速腐蚀试验,查明为使用氯化锌作为钎剂造成的腐蚀.经更正,杜绝了问题再生,保障了装备的可靠性和环境适应性.【期刊名称】《雷达与对抗》【年(卷),期】2018(038)004【总页数】4页(P42-45)【关键词】镀银;黑化;腐蚀;钎剂【作者】吴琪露;李南;尹凯【作者单位】中国船舶重工集团公司第七二四研究所,南京 211153;中国舰船研究院,北京 100101;中国船舶重工集团公司第七二四研究所,南京 211153【正文语种】中文【中图分类】TN957.80 引言某型舰载装备的方位铰链在检验过程中,发现镀银黑化门钮表面出现腐蚀现象,呈现黄色花斑。
由于该花斑外观类似打火后形成的黄色斑点,影响装备正常交付,也存在随时间延长腐蚀加剧的隐患,亟需找出腐蚀原因,避免问题再现。
1 问题分析铰链装配主要工序包括多次拆装、充气试验、电讯试验、钎焊铜镀银零件和油漆涂装。
经了解,近两年该零件也出现过多次类似花斑现象,特点如下:(1) 门钮存放长至2~3年,短至几个月,只要不进行钎焊装配,均无黄色斑点现象;(2) 门钮在装配前受检合格,无黄色斑点现象;(3) 腐蚀问题发现于铰链的零件钎焊工序后或整体涂装工艺后,产生黄色斑点的时间不固定;(4) 问题并不是每一批次都出现,同一批次也不是每个门钮都出现,黄色斑点的产生不具有规律性。
图1 砂纸打磨问题门钮综上,黄色斑点现象不是自然产生的,而是在外来物质或作用的影响下镀银黑化层发生的颜色变化。
用砂纸打磨问题门钮,如图1所示。
打磨掉黄色斑点后,露出完好镀银面,说明黄色斑点实际为镀银黑化层腐蚀变色。
2 试验方案从出现质量问题的门钮上切割出2个试样,如图2所示。
图2 表面分析样品图片及局部放大图(20×)样件a为无腐蚀现象的完好件,样件b为中心有黄斑的问题件,尺寸均为5mm×5 mm×1 mm左右。
无损检测标准
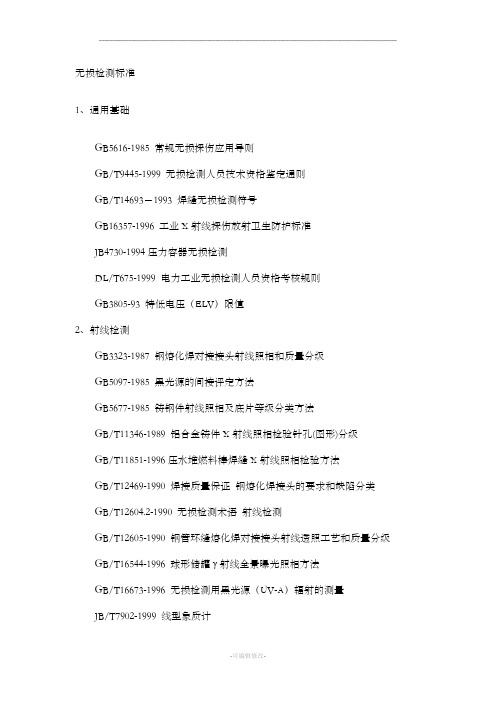
无损检测标准1、通用基础GB5616-1985 常规无损探伤应用导则GB/T9445-1999 无损检测人员技术资格鉴定通则GB/T14693-1993 焊缝无损检测符号GB16357-1996 工业X射线探伤放射卫生防护标准JB4730-1994压力容器无损检测DL/T675-1999 电力工业无损检测人员资格考核规则GB3805-93 特低电压(ELV)限值2、射线检测GB3323-1987 钢熔化焊对接接头射线照相和质量分级GB5097-1985 黑光源的间接评定方法GB5677-1985 铸钢件射线照相及底片等级分类方法GB/T11346-1989 铝合金铸件X射线照相检验针孔(图形)分级GB/T11851-1996压水堆燃料棒焊缝X射线照相检验方法GB/T12469-1990 焊接质量保证钢熔化焊接头的要求和缺陷分类GB/T12604.2-1990 无损检测术语射线检测GB/T12605-1990 钢管环缝熔化焊对接接头射线透照工艺和质量分级GB/T16544-1996 球形储罐γ射线全景曝光照相方法GB/T16673-1996 无损检测用黑光源(UV-A)辐射的测量JB/T7902-1999 线型象质计JB/T7903-1999工业射线照相底片观片灯JB/T8543.1-1997泵产品零件无损检测泵受压铸钢件射线检测方法及底片的等级分类JB/T9215-1999 控制射线照相图像质量的方法JB/T9217-1999射线照相探伤方法DL/T541-1994 钢熔化焊角焊缝射线照相方法和质量分级DL/T821-2002钢制承压管道对接焊接接头射线检验技术规程JB/T 6440-92 阀门受压铸钢件射线照相检验3、超声波检测GB1786-1990 锻制圆饼超声波检验方法GB/T2970-1991 中厚钢板超声波检测方法GB/T3310-1999 铜合金棒材超声波探伤方法GB/T4162-1991锻轧钢棒超声波检验方法GB4163-1984 不锈钢管超声波探伤方法GB5193-1985 钛及钛合金加工产品超声波探伤方法GB/T5777-1996无缝钢管超声波探伤检验方法GB/T6402-1991钢锻件超声波检验方法GB6519-1986 变形铝合金产品超声波检验方法GB7233-1987 铸钢件超声探伤及质量评级方法GB7734-1987 复合钢板超声波探伤方法GB/T7736-2001钢的低倍组织及缺陷超声波检验法GB/T8361-2001冷拉圆钢表面超声波探伤方法GB8651-2002金属板材超声波探伤方法GB8652-1988 变形高强度钢超声波检验方法GB11343-89 接触式超声波斜射探伤方法GB11344-89 接触式超声波脉冲回波法测厚GB11345-89 钢焊缝手工超声波探伤方法和探伤结果分级GB/T12604.1-1990无损检测术语超声检测GB/T12969.1-1991钛及钛合金管材超声波检验方法GB/T13315-1991 锻钢冷轧工作辊超声波探伤方法GB/T13316-1991铸钢轧辊超声波探伤方法GB15830-1995钢制管道对接环焊缝超声波探伤方法和检验结果的分级GB/T18256-2000 焊接钢管(埋弧焊除外)用于确认水压密实性的超声波检测方法JB1152-1981锅炉和钢制压力容器对接焊缝超声波探伤JB/T1581-1996 汽轮机、汽轮发电机转子和主轴锻件超声波探伤方法JB/T1582-1996 汽轮机叶轮锻件超声波探伤方法JB3144-1982锅炉大口径管座角焊缝超声波探伤JB4008-1985 液浸式超声纵波直射探伤方法JB4009-1985 接触式超声纵波直射探伤方法JB4010-1985 汽轮发电机用钢制护环超声探伤方法JB/T7602-1994 卧式内燃炉T形接头超声波探伤GB11259-1999 超声波检验用钢制对比试块的制作与校验方法JB/T8428-1996 校正钢焊缝超声检测仪器用标准试块JB/T8467-1996 锻钢件超声波探伤方法JB/T8931-1999 堆焊层超声波探伤方法JB/T9214-1999 A型脉冲反射式超声波探伤系统工作性能测试方法JB/T9630.2-1999汽轮机铸钢件超声波探伤及质量分级方法ZBY230-1984 A型脉冲反射式超声波探伤仪通用技术条件ZBY231-1984 超声探伤用探头性能测试方法DL505-1992 汽轮机焊接转子超声波探伤规程DL/T542-1994 钢熔化焊T形接头角焊缝超声波检验方法和质量分级DL/T694-1999 高温紧固螺栓超声波检验技术导则DL/T714-2000 汽轮机叶片超声波检验技术导则DL/T717-2000 汽轮机发电机组转子中心孔检验技术导则DL/T718-2000 火力发电厂铸造三通、弯头超声波探伤方法DL/T820-2002 管道焊接接头超声波检验技术规程ZB J04 001-87 A型脉冲反射式超声波探伤系统工作性能测试方法YB/T144-1998 超声探伤信号幅度误差测量方法JB/T 6903-92 阀门锻钢件超声波检查方法4、磁粉检测GB4956-1985磁性金属基体上非磁性覆盖层厚度测量磁性方法GB9444-1988 铸钢件磁粉探伤及质量评级方法GB10121-1988 钢材塔形发纹磁粉检验方法GB/T12604.5-1990无损检测术语磁粉检测GB/T15822-1995磁粉探伤方法JB/T6061-1992焊缝磁粉检验方法和缺陷磁痕的分级JB/T6063-1992 磁粉探伤用磁粉技术条件JB/T6065-1992 磁粉探伤用标准试片JB/T6066-1992 磁粉探伤用标准试块JB/T6439-1992阀门受压铸钢件磁粉探伤检验JB/T6912-1993泵产品零件无损检测----磁粉探伤JB/T8290-1998 磁粉探伤机JB/T8468-1996 锻钢件磁粉检验方法JB/T9628-1999汽轮机叶片磁粉检验方法JB/T9630.1-1999汽轮机铸钢件磁粉探伤及质量分级方法5、渗透检测GB9443-88 铸钢件渗透探伤及缺陷显示迹痕的评级方法GB/T12604.3-1990 无损检测术语渗透检测JB/T6062-92 焊缝渗透检验方法和缺陷迹痕的分级JB/T6064-92 渗透探伤用镀铬试块技术条件JB/T8543.2-1997泵产品零件无损检测渗透检测JB/T9216-1999 控制渗透探伤材料质量的方法JB/T9218-1999 渗透探伤方法JB/T 6902-92 阀门铸钢件液体渗透检查方法6、涡流检测GB4957-1985 非磁性金属基体上非导体覆盖层厚度测量涡流方法GB5126-1985 铝及铝合金冷拉薄壁管材涡流探伤方法GB5248-1985 铜及铜合金无缝管涡流探伤方法GB/T7735-1995钢管涡流探伤检验方法GB/T11260-1996 圆钢穿过式涡流探伤检验方法GB/T12604.6-1990无损检测术语涡流检测GB/T12968-1991 纯金属电阻率与剩余电阻比涡流衰减测量方法GB/T112969.2-1991 钛及钛合金管材涡流检验方法GB/T14480-1993 涡流探伤系统性能测试方法YB/T143-1998涡流探伤信号幅度误差测量方法YB/T145-1998钢管探伤对比试样人工缺陷尺寸测量方法7、声发射检测GB/T12604.4-1990 无损检测术语声发射检测GB/T18182-2000 金属压力容器声发射检测及结果评价方法JB/T6916-1993 在役高压气瓶声发射检测与评定方法JB/T7667-1995 在役压力容器声发射检测评定方法JB/T8283-1999 声发射检测仪器的性能测试方法8、其它检测GB/T12604.7-1995无损检测术语泄漏检测GB/T12604.8-1995 无损检测术语中子检测GB/T12604.9-1996无损检测术语红外检测GB/T12606-1990钢管及圆棒的漏磁探伤方法承压设备无损检测(JB/T4730.1~4730.6-2005)石油天然气钢质管道无损检测(SY/T4109-2005)常规无损探伤应用守则(GB5616-85)石油天然气工业承压钢管无损检测方法(SY/T6423.1~6423.7-1999)钢熔化焊对接接头射线照相和质量分级(GB/T3323-2005)钢制承压管道对接焊接接头射线检验技术规程(DL/T821-2002)铸钢件射线照相及底片等级分类方法(GB5677-85)钢管环缝熔化焊接头射线透照工艺和质量分级(GB/T12605-90)射线照相探伤方法(ZBJ04004-87)焊缝无损检测符号(GB/T14693-93)X射线探伤机(JJG40-2001)钢焊缝手工超声波探伤方法和探伤结果分级(GB/T11345-1989)电力建设施工及验收技术规范(管道焊缝超声波检验篇)(DL/T820-2002) 火力发电厂铸造三通、弯头超声波探伤方法(DL/T718-2000)管道焊接接头超声波检验技术规程(DL/T820-2002)锅炉大口径座角焊缝超声波探伤(JB/T3144-1982)钢的低倍组织及缺陷超声波检验法(GB/T7736-2001)高温紧固螺栓超声波检验技术导则(DL/T694-1999)电力建设施工及验收技术规范(管道焊缝超声波检验篇)(SDJ67-1987)无缝钢管超声波探伤检验方法(GB/T5777-1996)钢制管道对接环焊缝超声波探伤方法和检验结果的分级(GB/T15830-1995) 石油天然气钢质管道对接环焊缝全自动超声检测(SY/T0327-2003)A型脉反射式超声波探伤系统工作性能测试方法(ZBJ04001-87)常压钢质油罐焊缝超声波探伤(JB/T9212-99)钢锻件超声波检验方法(GB/T6402-1991)锻轧钢棒超声波检验方法(GB/T4162-91)磁粉探伤用磁粉技术条件(JB/T6063-92)常压钢制焊接储罐及管道磁粉检测技术标准(SY/T0443-98) 管道、储罐渗透检测方法(SY/T4080-95)铸钢件磁粉探伤及质量评级方法(GB944-88)钢材塔形发纹磁粉检验方法(GB10121-88)磁粉探伤方法(JB/T15822-1995)焊缝磁粉检验方法和缺陷磁痕的分级(JB/T6061-92)磁粉探伤用标准试片(JB/T6065-92)锻钢件磁粉检验方法(JB/T8468-96)磁粉探伤机(JB/T8290-95)常压钢制焊接储罐及管道渗透检测技术标准(SY/T0443-98) 焊缝渗透检验方法和缺陷痕迹的分级(JB/T6062-92)渗透探伤用镀铬试块技术条件(JB/T6064-92)控制渗透探伤材料质量的方法(ZBJ04003-87)渗透探伤方法(ZBJ04005-87)铸钢件渗透探伤及缺陷显示迹痕的评级方法(GB9443-88) 无损检测术语声发射检测(GB/T12604.4-90)金属压力容器声射检测及结果评价方法(GB/T18182-2000) 在役压力容器声发射检测评定方法(JB/T7667-95)Welcome To Download欢迎您的下载,资料仅供参考!。
金属覆盖层铜镀银厚度测试方法分析

62作者简介:张业真(1987— ),男,工程师,学士,从事低压电器检测工作。
张业真,朱翔,徐名中(福建省产品质量检验研究院,福建 福州 350002)摘 要:对标准GB/T 16921—2005与国家电网有限公司[2018]979号文件中对金属覆盖层镀银厚度试验要求与规定进行研究,提出在进行金属覆盖层铜镀银测试过程中,会因产品测试点不同部位、不同面、不同角度的变化,对铜镀银层厚度数值出现不一样的结果,对调整测试仪器中的测量距离是否会改变铜镀银层厚度数值进行了分析研究,并给出了在测试金属覆盖层铜镀银产品时应当注意的事项与测试方法。
关键词:铜镀银层;部位;角度;测量距离中图分类号:TM591 文献标识码:B 文章编号:1007-3175(2021)03-0062-04Abstract: According to the standard GB/T 16921—2005 and State Grid Co., Ltd. [2018] No. 979, the test requirements and regulations of the silver plating thickness of the metal coating are studied. It is proposed that in the process of testing the copper silver plating of the metal covering layer, different results will appear on the thickness of the copper silver plating layer due to the changes in different parts, different sides and different angles of the product test points, and to analyze and study whether adjusting the measuring distance in the test instrument will change the thickness of the copper silver-plated layer, and give the matters and test methods that should be paid attention to when testing the copper silver-plated product with the metal covering layer.Key words: copper silver plating layer; part; angle; measuring distanceZHANG Ye-zhen, ZHU Xiang, XU Ming-zhong(Fujian Inspection and Research Institute for Product Quality, Fuzhou 350002, China )Analysis on the Test Method of Copper Silver PlatingThickness of Metal Cover金属覆盖层铜镀银厚度测试方法分析0 引言金属覆盖层中铜镀银常应用于开关柜中手车触头、主母线、铜排搭接面、隔离开关触头以及其他相关金属带电部件上。
- 1、下载文档前请自行甄别文档内容的完整性,平台不提供额外的编辑、内容补充、找答案等附加服务。
- 2、"仅部分预览"的文档,不可在线预览部分如存在完整性等问题,可反馈申请退款(可完整预览的文档不适用该条件!)。
- 3、如文档侵犯您的权益,请联系客服反馈,我们会尽快为您处理(人工客服工作时间:9:00-18:30)。
S&C 铜和铜合金的镀银处理要求及检验规程PSP-2188Revise Date: 2007-7-191.0 总则1.1 下面技术规范是对铜、铜合金以及镀镍的铜、铜合金零件镀银过程的描述。
零件表面镀银通常是为了获得表面性能如表面的抗腐性及良好的导电性,未镀银的铜件不具有该特性。
1.2 此规范适用于通过碱性氰化物镀银,获得镀银层厚度范围从1.27~76.2微米的场合。
1.3 电镀是通过电解将沉淀物(银)从一个电极移到另一个电极(铜)的过程。
该镀银的过程是通过直流电及其电能的转换产生的能量而实现,效率为98%。
具体过程如下:1.3.1 每安培/小时电解将沉淀4克的银1.3.2 每平方英尺沉淀0.0254mm(千分之一英寸)的银须6.16安培/小时1.3.3 每平方英尺获得0.0254mm(千分之一英寸)的银须24.76克的银1.4 本规范适用于人工和自动电镀两种方式,因为规范书是比较笼统介绍一些常规工艺的,但有一些特殊的零件需更改其工艺过程的。
故规范书被分成了以下三部分来介绍:2.0 工艺流程3.0 过程详细说明4.0 检验2.0 工艺流程在铜件上镀银的每个步骤的工艺过程如下(供参考),详细的工艺过程说明见后面章节。
2.1 镀银2.1.1 可选择的或选择下列预洗方法之一清除2.1.1.1 厚油脂或硅树脂可依IB 60026所说的用Ransohoff的水洗清洗机进行清洗2.1.1.2 由于热处理产生的厚氧化皮可依PSP-2230酸洗除去2.1.2 装载─见3.22.1.3 腐蚀性的浸泡清洗─见3.3.12.1.4 腐蚀性的电凝法清洗─见3.3.22.1.5 清洗─见3.102.1.6 酸洗─见3.4.12.1.7 冲洗─见3.102.1.8 镀铜(可选)─见3.62.1.9 清洗(可选)─见3.102.1.10 预镀银(即银底镀)─见3.72.1.11 镀银─见3.82.1.12 废酸溶液清洗─见3.92.1.13 冲洗─见3.102.1.14 热水冲洗─见3.112.1.15 卸货及污点检查─见3.122.1.16 检验─见4.02.2 在镀镍零件上的镀银2.2.1 可选取下列预清洗方法之一清洗2.2.1.1 厚油脂或硅树脂可依PSP-2230进行碱洗2.2.1.2 由于热处理产生的厚氧化皮可依PSP-2230酸洗除去2.2.2 装载─见3.22.2.3 腐蚀性的浸泡清洗─见3.3.12.2.4 腐蚀性的电凝法清洗─见3.3.22.2.5 清洗─见3.102.2.6 酸洗─见3.4.12.2.7 冲洗─见3.102.2.8 预镀镍(即镍底镀)--见PSP 25703.62.2.9 镀镍--见PSP 25703.72.2.10 废酸溶液清洗--见PSP 25703.82.2.11 冲洗--见3.102.2.12 酸洗--见3.4.22.2.13 冲洗--见3.102.2.14 预镀银(即银底镀)--见3.72.2.15 镀银--见3.82.2.16 废酸溶液清洗—见3.92.2.17 冲洗—见3.102.2.18 热水冲洗—见3.112.2.19 卸货及污点检查—见3.122.2.20 检验—见4.03.0 工序说明3.1 预清洗—有时买来的零件因为太脏或有斑点而不能用正常的预清洗程序进行适当的清洁。
3.1.1 最早是电镀几个小件来检查镀层的附着力的。
虽然镀层厚度不会改变但是去油和酸洗的轮流清洗的程序会有所改变。
3.1.2 带有各种硅树脂或硅盐酸的加工零件会污染整个加工过程的,所以不会被允许预清洗。
更迭清洗的方式会被使用,会应用到2.1.1和2.2.1两种方式进行清洗。
3.2 装载—电镀电流是以每个镀架或者每个桶里的零件总面积和电镀厚度来决定的。
保持不间断的负载和调节电镀电流量,大多数零件标准的满负荷量是早已被确定的。
每个零件的满负荷量和相应的电镀安培数应该被列在每个零件的制造说明上。
对于没有被制定负荷量的零件来说,操作员或者工程师都应确定合适的电镀方式。
3.2.1 镀架上的所有零件都必须能放进高36英寸,宽18英寸,长40英寸的盒子里,为了能很方便的放进镀槽里。
任何一个镀架上的零件总重量不应超过300磅。
3.2.2 镀架上的零件必须要挂起来,这样做是为了消除气穴和条痕印。
3.2.3 装在桶里的零件不应超过180磅。
一个空桶的正常重量大约200~220磅左右加上180磅的零件后,起重量就已经满载了。
3.2.4 检查零件的必需电镀区,为可选的电镀区或允许有折痕的区域作上记号。
3.2.5 在制造说明中注明特别加工要求的地方。
3.3 去油污3.3.1 腐蚀性浸泡清洗—被有机或水性油脂清洁过的零件被适度的浸入热苛性碱溶液中浸泡。
好的操作方式要求在低气压下搅动溶液,再用再循环泵从溶液表面除去漂浮油。
3.3.1.1 在大多数情况下,所有用在铜、铜合金和锌上的腐蚀性浸泡清洗化合物都必须与之相配合。
溶液温度过高或溶液腐蚀性过强都会引起铜件发黑。
3.3.1.2 在苛性碱溶液里,溶解的金属会沉到盆里附在零件和涂锡的架子上。
这个时候需要加入粉末状的葡萄糖来进行清洗。
3.3.2 腐蚀性电凝清洗—第二遍热苛性碱溶液是用逆电流的方式从零件上除去不能溶解的物质。
这是零件被阳极清洗(即正极),物理上称“除去镀层”零件表面的污垢和金属粉尘。
每平方英尺10~15A的电流密度能充分清洗大多数零件,每平方英尺30A的电流密度是被用来清洗特定零件的。
让溶液循环流动再从溶液表面除去漂浮的杂质。
3.3.2.1 所有用在铜、铜合金和锌上的电凝清洗化合物都必须与之相配合。
否则会导致零件发黑或者易造成铜氧化。
3.3.2.2 如果相同的腐蚀材料被同时用在浸泡清洗和电凝清洗时,相当于零件没有被清洗,应当避免这种矛盾的混淆事件。
3.3.2.3 过载电流或者低溶解温度会导致零件的表面产生绿色氧化物。
产生绿色氧化物的零件要从加工过程中拿出来,然后依PSP-2230进行酸洗。
3.3.2.4 钨和钨银合金铁件在电凝清洗中的氧化会引起部件表面变粗糙。
因此当加工这些合金产品时,电凝清洗整流器必须要关掉。
3.4 酸洗—金属氧化物是用一定的酸侵蚀的方法从零件表面去除的。
在溶液中,酸的浓度、温度和时间都应该被控制,以避免在金属零件表面产生侵蚀或者不均匀分解。
在自动循环过程中,只有浓度和温度是不可控制的。
零件在酸洗和电镀之间不允许风干或者在任何清洗里保持很长时间。
虽然随后的冷水清洗可能会短时浸泡,但是过多的浸泡时间会导致过多的生锈而需要重新清洗,零件表面的快速氧化也是需要重新清洗的。
3.4.1 含硫磺酸,过氧化氢和各种不同稳定剂的酸溶液能很轻松的除去氧化的铜合金。
3.4.1.1 含银量超过万分之一的溶液可能会引起刚才洗干净的零件银黄着色。
银黄着色经常会导致电镀附着力变弱。
3.4.1.2 过度的溶解铜和过氧化氢化合物可能会导致零件表面侵蚀。
3.4.1.3 可能的话,硫磺酸浓度大量增大至25%,溶液允许冷却,至少达到室温。
这样沉淀铜就能被清除了。
3.4.1.4 当许多金属化合物沉淀的时候,无需搅动溶液就可以正常工作的。
3.4.1.5 溶液温度过高可能会引起表面出现过多的侵蚀点。
溶液放臵时间长了,溶液表面会产生一层含微粒的不溶解膜,也是会导致零件的电镀附着力变差。
3.4.1.6 溶液温度过高还会破坏化学物的稳定性,而破坏溶液。
3.4.2 含硫磺酸和专有化合物的酸溶液被用在镀银之前需镀镍的场合。
3.4.2.1 含铜量超过万分之0.5的溶液可能引起零件无法镀银。
3.5 整流器--所有的整流器都是风冷式的和1000A。
到达限定的温度或者电流后,整流器就会自动关闭。
3.5.1 电凝整流器电压范围是DC 2~18V。
如果要求达到一个特定的电流时,电压必须调节至输出电流读数达到这个特定的电流为止。
电压过高会引起零件表面烧灼或形成不可溶的氧化铜。
3.5.2 所有脉冲和电镀整流器都是用来控制电流和限定电压的。
整流器是用电压调节来控制输出要求的电流的。
如果要求的电流不能达到和电压超出了受限范围,那么负荷需要重新被调整。
3.5.3 所有脉冲电镀整流器是被电脑控制的。
脉冲电镀电流是通过操作员输入的数据和零件数据文件里获得的数据来计算的。
例如镀银计算见3.8.1。
3.6 镀铜(可选)--为了能获得较好的附着力,铍或碲合金和一些镀铅铜材料在镀银前可能需要镀一层铜。
合适的电镀程序是通过每个零件的反复试验而决定的。
通常快速镀铜1.778μm已经足够了。
3.6.1 对于铜件来说,镀铜的电流密度5~10A/ft2;对于黄铜和青铜合金件来说,镀铜的电流密度20~40A/ft2。
3.6.2 电流和沉积铜的相关叙述如下:3.6.2.1 在100%转化上,每安培-小时可以沉淀1.185克的铜。
3.6.2.2 每平方英尺沉淀0.0254mm(千分之一英寸)的铜须 17.7安培/小时。
3.6.2.3 每平方英尺获得0.0254mm(千分之一英寸)的铜须20.98克的铜。
3.6.3 一个类似于3.8.1的计算方式被用来评估电镀铜的电流。
3.6.4 阳极必定是被加了磷的铜。
3.6.5 添加剂是为了提高测量铜板、通孔电镀和所使用的电镀电流密度。
这种添加剂是锡镀液厂商为了减少锡镀液的污染物而提供的。
3.7 预镀银(即银底镀)—大多数铜合金在电镀之前都须银底镀。
(铍或碲合金和一些镀铅铜材料不可以银底镀;合适的电镀流程是通过每个零件的反复试验而决定的。
)这个在零件表面先镀一层薄银层的工艺步骤是为了提高覆盖率和附着力的。
所有零件在被浸入之前应带有最大DC 6V的负电荷。
这个不大于6V和10A/平方英尺范围的预镀可以在70秒内完成。
每平方英尺3~4A的电流密度可以很好的完成预镀。
预镀后的粗糙表面可以表明电流很大。
3.7.1 不可溶解的作过钝化处理的不锈钢正极被使用,可以让银从溶液中提取出来。
镀银量可以通过增加氰化银的方式进行补充。
3.7.2 被除去离子的淡水通常替代蒸馏水或者废酸洗液水。
3.7.3 钢或者铁制的桶不会用来装这种溶液,所有的金属组件不是不锈钢就是钛。
在溶液中所有直接接触的带电组件都是作过钝化处理的不锈钢。
所有带另一极电的组件可能是铜也可能是覆钛铜。
3.7.4 这个桶会被用50微米的过滤器以每小时1-1/2桶的速度过滤。
3.7.5 不含硫磺的活性炭可以用来清除有机污染物。
3.8 常规镀银—电镀这步通常所用的时间是整个电镀过程中最长的。
根据不同电镀厚度,电镀的时间也会有所不同5~60分钟不等。
在3.8.1中所描述的电镀电流大小是以电镀时间和镀层厚度为基础的。
这种计算方法不包括后面几种可变因素:零件的几何形状、加载方式(指需电镀的区域接近或远离正极)、暴露在外的架子或接触的桶和遮住的零件。