窑炉及陶瓷烧成
陶瓷工艺学第十章烧成与窑具

第四节 窑具
4.1 窑具种类 匣钵、棚板、支柱、各种耐火垫、
托板、辊棒和窑车材料等。
现代窑炉的重要标志之一,就是大幅度 减少了窑具的用量,采用多种高级耐火材料 窑具,满足快速烧成的需要。
4.2窑具的性能要求 (1)足够的结构强度
常温强度和高温强度
(2)良好的抗热震性能 破坏机理:裂纹不断扩展; 热膨胀系数小,产生应力小,不易破坏 熟料和基质的相互关系;相对量的多少 影响较大。
理论温度制度曲线
1400 1200 1000 800 600 400
200
脆性生坯
厚坯 薄坯
热塑性范围
中火保温
脆性瓷器
时间
1.2.2.3 釉烧方法
(1)一次烧成时,釉料的熔化温度与坯料的氧化分解 温度相适应,中火保温防止针孔、橘釉、黑心、鼓泡 等缺陷。 (2)冷却初期依据釉料要求确定冷却速度
光泽釉——快速冷却 结晶釉——结晶温度保温处理 (3)二次烧成 高温素烧低温釉烧:釉烧时可以不考虑坯体的脱 结构水及 氧化分解排气,素烧 时不考虑与釉的关系。 低温素烧高温釉烧:釉烧时可以不考虑 坯体的脱结构 水,要考虑氧化分解,素 烧时不考虑与釉的关系。
不同烧结温度及高温保温时间对产品性能的影响
注:摘自《陶瓷研究》杨世源
烧成温度(℃) 保温时间(min) 平均吸水率(%)
1020
30
16.4
1040
30
15.7
1060
30
14.92
1080
30
14.10
1100
30
13.92
1080
5
14.96
1080
15
14.7
1080
30
陶艺 陶瓷烧成课件
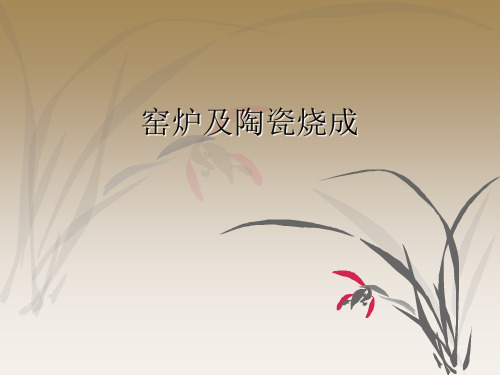
(2).龙窑——一般都是依山坡而建,坡的大 小缓急直接影响烧成时间和产量。
一般窑头坡度大,易上火,窑尾坡度小,易 存火,低的一端为火膛,高的一端有排烟 口。
龙窑的只要特点是升温快、降温也快,维持 火焰和还原时间长。使用的材料为松柴。
在我国南方比较多见。(如浙江龙泉、福建 德化、在景德镇的湖田也多出发现了龙 窑。)
一次烧成和二次烧成
一次烧成:是指经过成型、干燥或施釉后的 生坯,在烧成窑内一次烧成陶瓷产品的工艺 路线。 二次烧成:是指经过成型干燥的生坯,先在 素烧窑内进行第一次烧成(素烧)后的产品, 经拣选,施釉等工序后,再进行第二次烧成 (釉烧)的工艺路线。
设置烧制曲线
釉下烧成曲线
釉上烧成曲线
(三)升温曲线
使之变成“形如覆瓮”的蛋型, 所以也叫瓮形 窑或蛋形窑,景德镇人把这各独具地方特色, 独具技术优势的属于平焰式的窑叫镇窑。
电窑认识
以此款八边形顶 开盖窑炉为例。
此款窑为顶开 盖,小且轻便。 0.07立方、6kw、 220v、接线为4m ㎡以上的全铜 线。
窑炉结构
采用五层不同结构层完美结合。 最里层为高温砖,然后以高保温耐火棉保
150~500℃:坯体可快速升温,比较安全,失去结合 水,碳酸盐、黑云母的分解,气体很容易溢出。
500~700℃:较松散,石英在573℃有突变,膨胀系数 较大。
700~900℃:可快速加热坯体,比较安全,碳化物燃 烧成气体,并排出,坯体气孔增多,可不限制加热速 度,因为坯体很薄,可渗透性强。
• 900~1100℃:在烧成收缩很严重之前要减小制品间 的温差,在900度是升温较慢,盐酸盐分解许多气泡 在釉面玻化之前必须排出,快速升温会导致石膏混入 坯体或已干燥的可溶性盐类集中到一起,坯体炸裂。
窑炉烧成工艺技术

窑炉烧成工艺技术窑炉烧成工艺技术是指对陶瓷制品进行烧结和成型的一种工艺技术。
它是将制作好的陶瓷坯体经过高温烧制,使其发生物理和化学变化,在炉中进行一系列的处理,使其变得致密,增强强度和耐磨性的过程。
窑炉烧成工艺技术对于陶瓷制品的质量和性能有着重要影响。
窑炉烧成工艺技术的主要步骤包括:上物、砌炉、放坯、烧成和取坯等环节。
首先是上物,是指将制作好的陶瓷坯体放到窑炉里的过程。
在上物时需注意坯体摆放的方式,要做到整齐划一,使得每个坯体都能充分接触到热源,从而实现坯体的均匀加热。
接着是砌炉,即将上好的物品按照特定的方式摆放到窑炉中。
不同陶瓷产品的烧成工艺是不同的,因此需要根据产品的特性和炉型来进行合理的摆放。
常见的摆放方式有矩形排列、楔状排列等。
砌炉时还需要注意留有放坯道,方便进行放坯操作。
放坯是指将上好的陶瓷坯体放置在窑炉内的过程。
主要有手工放坯和机械放坯两种方式。
手工放坯通常用于小型窑炉,操作者根据物品大小、质量和窑炉容量等因素,将坯体放置在窑炉内适当的位置。
机械放坯则是通过机械设备将坯体精确地放置在预定位置。
烧成是窑炉烧成工艺技术的核心步骤。
通过加热使坯体达到一定的温度,使其中的有机物脱失、水分蒸发、胶结剂燃烧等过程发生。
烧成过程的控制很关键,需要根据陶瓷产品的特性和要求来控制温度升降速率、保温时间等参数。
同时,还需要防止窑炉内气氛的氧化还原和陶瓷表面的氧化等问题。
最后是取坯,即将烧成好的陶瓷制品从窑炉中取出。
这一步需要注意的是防止窑炉内外温度骤变引起陶瓷制品破裂。
通常使用自然冷却和缓冷两种方式来保证陶瓷制品的品质。
总结一下,窑炉烧成是对陶瓷制品进行烧结和成型的过程,其工艺技术的重要性不可忽视。
合理的上物、砌炉、放坯、烧成和取坯等步骤,能够保证陶瓷制品的质量和性能得到充分提升。
只有不断提高窑炉烧成工艺技术,才能生产出更加优质的陶瓷制品。
现代窑炉分类、节能的原理及烧成操作
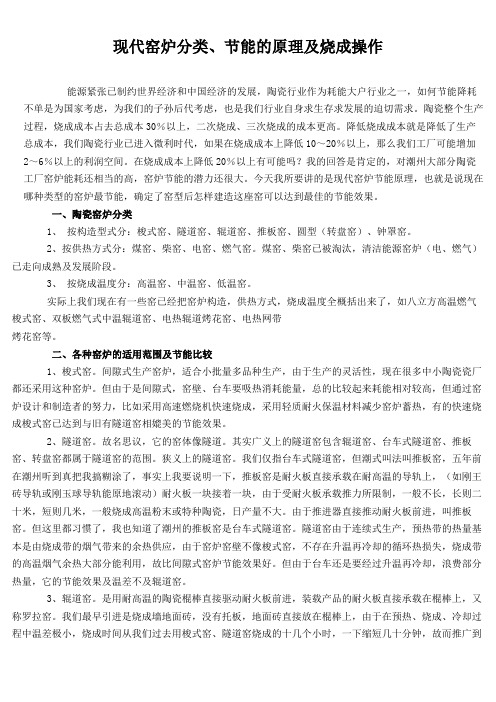
现代窑炉分类、节能的原理及烧成操作能源紧张已制约世界经济和中国经济的发展,陶瓷行业作为耗能大户行业之一,如何节能降耗不单是为国家考虑,为我们的子孙后代考虑,也是我们行业自身求生存求发展的迫切需求。
陶瓷整个生产过程,烧成成本占去总成本30%以上,二次烧成、三次烧成的成本更高。
降低烧成成本就是降低了生产总成本,我们陶瓷行业已进入微利时代,如果在烧成成本上降低10~20%以上,那么我们工厂可能增加2~6%以上的利润空间。
在烧成成本上降低20%以上有可能吗?我的回答是肯定的,对潮州大部分陶瓷工厂窑炉能耗还相当的高,窑炉节能的潜力还很大。
今天我所要讲的是现代窑炉节能原理,也就是说现在哪种类型的窑炉最节能,确定了窑型后怎样建造这座窑可以达到最佳的节能效果。
一、陶瓷窑炉分类1、按构造型式分:梭式窑、隧道窑、辊道窑、推板窑、圆型(转盘窑)、钟罩窑。
2、按供热方式分:煤窑、柴窑、电窑、燃气窑。
煤窑、柴窑已被淘汰,清洁能源窑炉(电、燃气)已走向成熟及发展阶段。
3、按烧成温度分:高温窑、中温窑、低温窑。
实际上我们现在有一些窑已经把窑炉构造,供热方式,烧成温度全概括出来了,如八立方高温燃气梭式窑、双板燃气式中温辊道窑、电热辊道烤花窑、电热网带烤花窑等。
二、各种窑炉的适用范围及节能比较1、梭式窑。
间隙式生产窑炉,适合小批量多品种生产,由于生产的灵活性,现在很多中小陶瓷瓷厂都还采用这种窑炉。
但由于是间隙式,窑壁、台车要吸热消耗能量,总的比较起来耗能相对较高,但通过窑炉设计和制造者的努力,比如采用高速燃烧机快速烧成,采用轻质耐火保温材料减少窑炉蓄热,有的快速烧成梭式窑已达到与旧有隧道窑相媲美的节能效果。
2、隧道窑。
故名思议,它的窑体像隧道。
其实广义上的隧道窑包含辊道窑、台车式隧道窑、推板窑、转盘窑都属于隧道窑的范围。
狭义上的隧道窑。
我们仅指台车式隧道窑,但潮式叫法叫推板窑,五年前在潮州听到真把我搞糊涂了,事实上我要说明一下,推板窑是耐火板直接承载在耐高温的导轨上,(如刚王砖导轨或刚玉球导轨能原地滚动)耐火板一块接着一块,由于受耐火板承载推力所限制,一般不长,长则二十米,短则几米,一般烧成高温粉末或特种陶瓷,日产量不大。
陶瓷烧成与窑炉热工
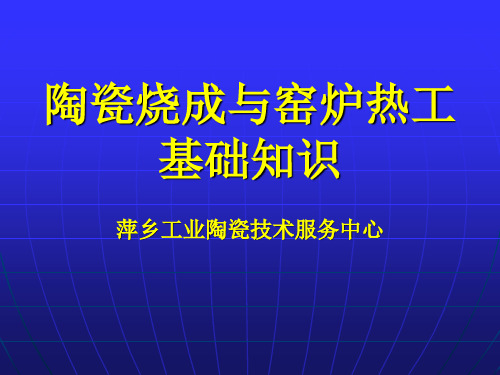
在还原气氛下 CaSO4+CO﹥910℃ CaSO3+CO2↑ CaSO31080~ 1100℃CaO+SO2↑ Fe2O3+CO1000~ 1100℃2Fe+CO2↑ CaO和Fe0促进烧成 致密化,减少泛黄 现象
(3)形成大量液相和莫来石 ①985℃开始出现液相,温度越高,液 985℃ 相越多 液相的作用: A、促使晶体(如莫来石)长大; B、填充坯体孔隙拉紧颗粒,促进坯体致密 化,提高瓷件抗蚀性和机械强度; C、液相会阻碍气体排出,易发生冲泡和变 形。 ②1100℃以上开始形成莫来石. 1100℃以上开始形成莫来石.
(四)、完全燃烧和不完全燃烧 )、完全燃烧和不完全燃烧
完全燃烧:燃料燃烧后完全转变为不 可再燃烧产物的一种燃烧方式 不完全燃烧:燃料燃烧后的烟气中有 可再燃烧产物的一种燃烧方式
(五)、燃料的种类 )、燃料的种类
1、固体燃料:柴、烟煤、无烟煤、煤 粉等 2、液体燃料:重油、柴油、焦油、液 态煤等 3、气体燃料:发生炉煤气、焦炉煤气、 液化石油气、天然气
(三)结构和原理图
七、隧道窑
(一)定义
隧道窑是连续烧成陶瓷制品的热工设备, 它的主体是一条隧道,是一种按逆流原 理工作的横焰式窑。
(二)隧道窑的特点: 隧道窑的特点:
1、利用烟气余热预热坯体,废气排出温度 低,约200℃ 低,约200℃; 2、产品冷却之热加热空气,可助燃或作干 燥介质,产品出窑温度低; 3、连续窑,窑体温度不变,不蓄热,热耗 低; 4、产量大,劳动条件好; 5、较适合产品单一的生产: 6、调控不便,一次投资大
1、水分蒸发期(室温~摄氏300℃) 水分蒸发期(室温~摄氏300℃ 此阶段主要是排出干燥中未除掉的水分。 要求:①入窑坯体水分小于2%否则,坯体 要求:①入窑坯体水分小于2%否则,坯体 有可能因水分蒸发而开裂;或与窑炉SO2 有可能因水分蒸发而开裂;或与窑炉SO2 发生化学反应,造成坯体蒙上一层“白霜” 发生化学反应,造成坯体蒙上一层“白霜” 或产生气泡缺陷;②加强窑内通风,使水 汽及时排除。此阶段坯体强度缓慢提高。 一般升温速度:20~35℃ 一般升温速度:20~35℃/hr
窑炉及陶瓷烧成

葫芦窑是景德镇人在元代把马蹄窑和龙窑的特点 结合起来,产生的新窑体。
葫芦窑综合了马蹄窑半倒焰的技术和龙窑窑体结 构的长处,形成了南北优势并存的产物。
第一讲
窑炉及陶瓷烧成
李萍 2013年5月
陶瓷是火的艺术。 烧成(烧结)是在热工设备中进行的。 这里热工设备指的是陶瓷生产窑炉及其附属设备。 烧结陶瓷的窑炉类型很多,同一种制品可在不同 类型的窑内烧成,同一种窑也可烧结不同的制品。
第一节 窑炉的发展历程——古代窑炉
1. 最原始烧陶的方法是不用窑的 垒坯露天烧:在地面上挖一浅坑或在地面铺上小 石头块,上面放上陶坯后,用干枝柴草围住周围 顶部,外面涂抹较稠的黄土泥,上留通风小孔, 地面点火烧制。
窑内容量大约在200-240m3左右,整个窑由多个室串联组成, 每个窑室有大有小,窑头与窑尾小,越接近中间越大,每个窑 室的隔墙下有通火孔,窑室的每个后顶上有排气口,同时每边 各开一个窑门,窑长因各地不同而异。
8. 明末景德镇创造发明了烧制温度达1300℃以上 的景德镇窑。
窑身如半个瓮俯覆,又似半个蛋形覆置,也象一个前 高后低的隧道。 景德镇窑是在明末清初时期,在葫芦窑基础上演化而 成的。其特点是把葫芦窑两室之间的折腰取消,使之 变成“形如覆瓮”的蛋型,所以也叫瓮形窑或蛋形窑, 景德镇人把这个独具地方特色,独具技术优势的属于
梭式窑
梭式窑是一种现代化的间歇窑,其结构与 隧道窑的烧成带相近,由窑室和窑车两大部 分组成,坯件码放在窑车棚架上,推进窑室 内进行烧制,在烧成冷却后将窑车和制品拉 出窑室外卸车,窑车的运动犹如织布机上的 梭子,故称为梭式窑。
古代陶瓷器烧制工序与窑炉设计

古代陶瓷器烧制工序与窑炉设计工序古代陶瓷器烧制的工序通常包括以下几个步骤:1. 瓷土的准备:选择合适的瓷土,将其经过处理和筛选,去除杂质,并进行湿磨,使其成为可塑性较好的瓷泥。
2. 成型:根据设计需求,将瓷泥进行成型,可以采用手工造型、模压或转盘成型等方法。
3. 干燥:将成型后的陶瓷制品进行适当的干燥,以去除内部的水分。
干燥的时间和方式需根据制品的大小和形状进行调整,以避免开裂。
4. 烧制:将干燥后的陶瓷制品放入窑炉中进行烧制。
烧制的温度和时间根据不同的陶瓷制品和釉料而定。
5. 上釉:在烧制后的陶瓷制品表面施加釉料,以增加光亮度、保护陶瓷,并增加装饰效果。
6. 二次烧制:经过上釉后的陶瓷制品再次放入窑炉中进行烧制,使釉料与制品更好地结合。
7. 装饰和修整:根据需要,对陶瓷制品进行装饰,并进行修整和打磨,使其达到更好的观赏效果。
8. 检验和包装:对最终的陶瓷制品进行质量检验,合格后进行包装。
窑炉设计要点古代陶瓷器的烧制离不开合理的窑炉设计。
下面是一些窑炉设计的要点:1. 窑炉材质:选择适合的耐火材料,如石英砂、耐火砖等。
对于高温烧制,需选择能承受高温的材料。
2. 窑炉结构:窑炉的结构应合理,包括炉膛、炉壁和烟囱等。
炉壁的厚度和材质需要根据烧制温度和时间进行选择,以保证良好的保温效果和热传导性能。
3. 燃料选择:燃料的选择应考虑燃烧温度、燃烧时间和燃烧产物对陶瓷制品的影响。
常见的燃料包括木材、煤炭和天然气等。
4. 窑炉控制:确保窑炉能够准确控制温度和烧制时间,可采用自动控制系统或人工控制方式。
5. 烟气处理:合理处理烟气,以减少对环境的污染,并保证烧制过程中的正常通风。
请注意,以上是古代陶瓷器烧制工序与窑炉设计的简要介绍,具体实践中会受到情况和需求的影响,需要进一步的研究和实践。
窑炉烧成工序安全操作规程
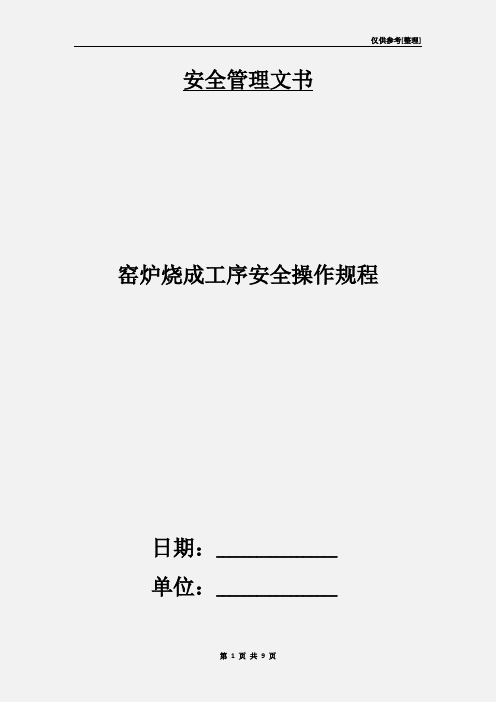
仅供参考[整理] 安全管理文书窑炉烧成工序安全操作规程日期:__________________单位:__________________第1 页共9 页窑炉烧成工序安全操作规程1目的确保烧成工艺的合理性及稳定性,从而保证产品质量稳定。
2职责2.1工艺部负责下达烧成工艺卡。
2.2窑炉主管、班长负责窑炉烧成曲线、压力制度和气氛制度的设定和调节。
2.3司炉工负责烧成工序的操作和当班产品质量改善。
2.4保养工负责窑炉的保养。
3主要生产设备及工具辊道窑窑体、进出砖平台、燃料供应和燃料系统、传动系统、排烟系统和冷却系统、自动控制系统;压力计、铁杆、铁钩、水平尺(管)、柴油小桶、直尺、肥皂水等。
4操作规范4.1窑炉常规检查内容4.1.1做好上班前的准备工作,开好班前会,进行5分钟6S检查。
4.1.2交接班时,要检查上一班工作记录、质检报表、温度记录表,了解上一班砖坯质量情况,如:砖坯的尺码、砖形、平整度、针孔状况、色号、是否对板、主要烧成缺陷等。
4.1.3监视煤气压力、供电电压、传动变频和各风机变频频率(责任人;炉工)4.1.4进砖时要注意干燥与窑炉速度一致,进砖保持整齐,产品无碰撞现象(责任人:保养)4.1.5严格控制好各区温度,特别是烧成带温度,将其稳定在烧成曲线要求的±2度范围内(责任人:炉工)。
随时观察表温,如果发现温度无论是超过设定温度并持续上升,还是低于设定温度并持续下降,如果不是疏砖引起,应着手检查控制电路、热电偶和执行器。
4.1.6检查各喷枪的燃烧情况,使所有喷枪无火星、无突突声,火焰无歪斜、火焰颜色呈淡蓝色透明状、无灰色烟雾。
4.1.7经常检查,定期添加石棉和更换孔砖周围的石棉保证隔热效果,无漏光、漏火、渗风现象,又不影响辊棒的灵活运转。
4.1.8经常检查煤气管道的密封性,如感觉有煤气泄露的味道,可用肥皂水进行检查,此项工作必须有两人在场,以防煤气中毒。
4.1.9保证辊棒运转连续平稳,输送顺畅,无叠砖,传动机构润滑良好。
陶瓷窑炉烧成技术

陶瓷窑炉烧成技术
陶瓷窑炉烧成技术是我国的传统文化重要的组成部分。
陶瓷烧成窑分类如下:
(一)隧道窑
隧道窑因其产量高,燃耗低,劳动条件好,易机械化、自动化,是目前陶瓷及耐火材料工业应用较多的现代化窑炉。
隧道窑的窑顶用耐火砖砌筑,或用耐火浇注料预制块砌筑。
窑底则由多台窑车组成。
窑车沿固定的导轨移动。
料坯放在窑车上由窑头推入窑内,经过预热、烧成和冷却,最后从窑尾出窑而获得成品。
(二)倒焰窑
倒焰窑是陶瓷工业目前常用的一种火焰窑炉,亦是烧制耐火制品的热工设备。
因为火焰在窑内是自窑顶倒向窑底的,所以叫倒焰窑。
倒焰窑为间歇操作。
其容积随生产的需要和工艺条件而变化,容量小的只有几立方米。
其外形可以分为圆窑和方窑两种。
圆窑窑内上下温差较小,约20℃左右,上下温度分布比较均匀,目前使用较多。
窑
的烧成制度、亦随烧成制品的材质而变动。
(三)梭式窑
梭式窑是一种窑车式的倒焰窑,其结构与传统的矩形倒焰窑基本相似。
梭式窑烧嘴安设在两侧窑墙上,窑底用耐火材料砌筑在窑车钢架结构上,即窑底吸火孔、支烟道设于窑车上,并使窑墙下部的烟道和窑车上的支烟道相连接;窑车在窑室底部轨道移动,窑车数视窑的容积而定;窑车之间及窑车与窑墙之间设有曲封和砂封。
陶瓷工艺学--8 烧成-09.10

这些碳素和有机物加热即发生氧化反应:
C(有机物)+O2
350º C
CO2
C(碳素)+O2
2H2 + O2
600º C
CO2
2H2O
250~ 920º C
S + O2
2CO+O2
SO2
2CO2
这些反应要在釉面熔融和坯体显气孔封闭前
结束。否则,就会产生烟熏、起泡等缺陷。
2. 硫化铁的氧化 FeS2+O2
1. 升温速度的确定
A.低温阶段:升温速度主要取决于坯体入窑时的 水分。
如果坯体进窑水分高、坯件较厚或装窑量大,则升
温过快将引起坯件内部水蒸气压力增高,可能产生开 裂现象; 对于入窑水分不大于1%~2%的坯体,一般强度也 大,在120℃前快速升温是合理的;对于致密坯或厚胎
坯体,水分排除困难,加热过程中,内外温差也较大,
3MgO4SiO2H2O
600~ 970º 3(MgOSiO )(原顽火辉石)+ SiO +H O C 2 2 2
蒙脱石脱水:
Al2O34SiO2nH2O
Al2O34SiO2+nH2O
5. 晶型转变
石英在573℃时, -石英迅速地转变为 -石英, 体积膨胀0.82%;在870℃-石英缓慢地转变为 -鳞石 英,体积膨胀16%。石英晶型转变造成的体积膨胀, 一部分会被本阶段的氧化和分解所引起的体积收缩所 抵消。如果操作得当,特别是保持窑内温度均匀,这 种晶型转变对制品不会带来多大的影响。 由粘土脱水分解生成的无定形Al2O3,在950℃时 转化为-Al2O3。随着温度的升高,-Al2O3与SiO2反应 生成莫来石晶体。
(三)高温玻化成瓷阶段 (从950℃到最高烧成温度)
中国古代陶瓷的制作与窑炉技术
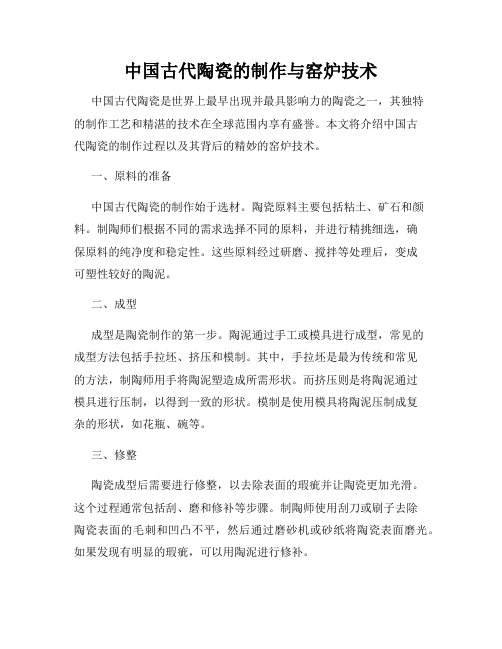
中国古代陶瓷的制作与窑炉技术中国古代陶瓷是世界上最早出现并最具影响力的陶瓷之一,其独特的制作工艺和精湛的技术在全球范围内享有盛誉。
本文将介绍中国古代陶瓷的制作过程以及其背后的精妙的窑炉技术。
一、原料的准备中国古代陶瓷的制作始于选材。
陶瓷原料主要包括粘土、矿石和颜料。
制陶师们根据不同的需求选择不同的原料,并进行精挑细选,确保原料的纯净度和稳定性。
这些原料经过研磨、搅拌等处理后,变成可塑性较好的陶泥。
二、成型成型是陶瓷制作的第一步。
陶泥通过手工或模具进行成型,常见的成型方法包括手拉坯、挤压和模制。
其中,手拉坯是最为传统和常见的方法,制陶师用手将陶泥塑造成所需形状。
而挤压则是将陶泥通过模具进行压制,以得到一致的形状。
模制是使用模具将陶泥压制成复杂的形状,如花瓶、碗等。
三、修整陶瓷成型后需要进行修整,以去除表面的瑕疵并让陶瓷更加光滑。
这个过程通常包括刮、磨和修补等步骤。
制陶师使用刮刀或刷子去除陶瓷表面的毛刺和凹凸不平,然后通过磨砂机或砂纸将陶瓷表面磨光。
如果发现有明显的瑕疵,可以用陶泥进行修补。
四、干燥和初烧修整完毕后的陶瓷需要在室温下进行干燥。
这个过程需要控制好湿度和温度,以免陶瓷出现开裂或变形。
干燥完毕后,陶瓷需要进行初烧。
初烧是将陶瓷放入窑炉中,提高温度,使陶瓷内部水分蒸发,并逐渐加热到800-1000摄氏度的温度。
五、施釉和绘画陶瓷经过初烧后,可以进行施釉和绘画。
施釉是将特殊的涂料涂抹在陶瓷表面,以提高其光滑度和防水性。
不同的釉料可以产生不同的效果,如透明釉、白釉和青瓷釉。
绘画则是在釉面上进行绘画,以装饰陶瓷。
绘画技巧包括描绘、绘花和题字等,经过烧制后,图案会与陶瓷融为一体。
六、二次烧制施釉和绘画完成后的陶瓷需要进行二次烧制。
这一步是将陶瓷放入窑炉中进行高温烧制,以使釉料和陶泥完全结合,并提高陶瓷的强度和耐久性。
二次烧制的温度和时间根据不同的陶瓷类型和窑炉技术有所不同。
七、窑炉技术窑炉是中国古代陶瓷制作的重要工具,也是陶瓷成功烧制的关键。
陶瓷有限公司烧成窑炉操作规程

陶瓷有限公司设备操作规程烧成窑炉操作规程1.每次停窑后重新点火前都要先将燃气管道内的空气经由排空管道排放干净,然后再关闭排空管的阀门,防止燃气爆炸。
2.启动传动,抽烟风机及助燃风机,点燃火枪.按升温曲线升温.3.温度达到800℃左右,启动急冷风机和抽热风机.4.适当调整马弗板上下位置,排烟风机前管道闸板开度,以便调节全窑压力分布,从而调节温度分布。
5.当窑温达到1180℃以上时,试放生砖坯,根据坯砖烧制情况细调窑炉温度曲线烧成周期.调整完毕,开始进砖.6.遇突然停电时,先检查确认燃气自动切断阀门装置已启动,开启备用发电机将辊棒传动“前进”改为“摆动”,来电后重新点火.7.停气时,先关闭燃气阀门,并停止砖坯入窑,待窑内无砖后,关闭所有风机.故障排除后,启动风机重新点火.8.需要停窑维修时,首先停止进砖,待窑内无砖时,关闭燃气阀门.调小抽烟风机及助燃风机,关闭抽热风机及急冷风机.温度降至200℃以下,停止所有风机及传动.9.每小时对窑炉温度、干燥器温度进行记录,每30分钟进行一次产品尺寸检测和记录,10.每小时一次目测砖的平直度,测量磨边后砖的平直度,出现不规则变形时,立即汇报,以便尽早处理。
11.每半小时一次侧量砖的尺寸,大时,高温带上下温度各加一度;小时,各减一度。
若一片砖的尺寸相差5㎜时调整上下烧咀的火焰长度,每次调节不得超过两节窑炉。
并做好标记,出砖后测量。
12.风机吸热口、闸板高度和窑炉转速等不得乱调,需要调整时报主任批准后方可进行,并做好记录。
13.窑炉两侧高温棉必须堵严,防止漏火引起火灾。
妥善保管窑炉两侧的消防器材,确保有效。
14.点火时要先打开排烟风机,再开电磁阀,开燃气,把烧咀点燃。
15.每次拆装烧咀出软管时,丝头必须使用生料带且拧紧,防止漏气。
16.窑炉控制室内禁止吸烟。
基于氢能利用的节能陶瓷干燥窑及烧成窑炉装备开发与应用方案(一)

基于氢能利用的节能陶瓷干燥窑及烧成窑炉装备开发与应用方案一、实施背景随着全球能源结构的转变,可再生能源的发展受到越来越多的关注。
氢能作为一种清洁、高效、可再生的能源,其在产业结构改革和能源转型中的作用日益凸显。
在建筑陶瓷、卫生洁具、汽车配件等产业中,传统的干燥窑和烧成窑炉装备能耗较高,排放的CO2对环境造成较大压力。
因此,开发基于氢能利用的节能陶瓷干燥窑及烧成窑炉装备具有重要意义。
二、工作原理1. 氢气制备通过水电解、天然气重整、生物质气化等方法制备氢气。
本方案中,将采用水电解法制备氢气,该方法制备的氢气纯度高,无碳排放。
2. 氢气储存与传输将制备好的氢气储存于高压储氢罐中,通过管道将氢气输送至干燥窑和烧成窑炉装备。
在传输过程中,需保证氢气的密封性和安全性。
3. 氢气应用在干燥窑中,利用氢气燃烧产生的热量对陶瓷制品进行干燥。
在烧成窑炉装备中,利用氢气作为燃料,通过燃烧产生的高温对陶瓷制品进行烧成。
在此过程中,需对燃烧产生的尾气进行处理,以保证排放达标。
三、实施计划步骤1. 装备设计根据陶瓷制品的生产工艺要求,设计节能陶瓷干燥窑及烧成窑炉装备。
在设计过程中,充分考虑氢气的特性,保证装备的安全性和可靠性。
2. 装备制造选择合适的材料和工艺,按照设计要求制造节能陶瓷干燥窑及烧成窑炉装备。
在制造过程中,对装备的性能进行检测和验证,确保装备满足生产要求。
3. 装备安装与调试将制造好的装备运输至生产现场,进行安装和调试。
在安装和调试过程中,对装备的性能进行检测和优化,确保装备能够正常运行。
4. 工艺与技术选择根据陶瓷制品的生产要求和现场实际情况,选择合适的工艺和技术。
在利用氢气进行干燥和烧成的过程中,需对温度、压力等参数进行精确控制,以保证产品质量和生产效率。
四、适用范围本方案适用于建筑陶瓷、卫生洁具、汽车配件等产业的干燥窑和烧成窑炉装备。
这些产业在生产过程中需要大量的热能,通过利用氢能进行干燥和烧成,可以有效降低能耗和减少碳排放,提高产品的竞争力。
窑炉烧成原理

窑炉烧成原理窑炉烧成原理一、引言窑炉是一种用于加热和处理物料的设备,它广泛应用于陶瓷、水泥、玻璃等行业中。
窑炉的主要作用是将原材料进行高温处理,使其形成所需的化学和物理特性,从而得到所需的产品。
二、窑炉分类根据不同的加热方式和工艺要求,窑炉可以分为多种类型。
其中最常见的有:1. 间歇式窑:在一个完整的生产周期内,物料只进入和出离开一次。
例如陶器制造中使用的龙窑。
2. 连续式窑:物料在一个连续流动的过程中进行加工和处理。
例如水泥生产中使用的回转窑。
3. 电阻加热式窑:使用电阻线圈或电极将电能转化为热能进行加热。
4. 燃气加热式窑:使用天然气或液化气等作为能源进行加热。
5. 燃油加热式窑:使用柴油或重油等作为能源进行加热。
三、原理介绍1. 物料预处理在进入窑炉之前,物料需要进行预处理。
这包括研磨、混合和筛分等步骤,以确保物料能够均匀地进入窑炉并得到充分的加热。
2. 窑内加热窑炉内部的加热方式取决于窑炉的类型和工艺要求。
在间歇式窑中,通常使用木材或天然气等作为能源进行加热。
在连续式窑中,通常使用液化气或重油等作为能源进行加热。
3. 物料变化在高温下,物料会发生一系列的化学和物理变化。
例如,在水泥生产过程中,原材料经过高温反应后会形成新的化合物,并逐渐硬化成为水泥。
4. 窑外冷却在窑内完成加工后,物料需要进行冷却。
这可以通过将其从窑内取出并放置在冷却设备中进行实现。
此时,物料仍然处于高温状态,并且需要逐渐降温才能达到所需的硬度和强度。
四、影响因素1. 温度:不同类型的物料需要不同的加热温度才能达到所需的化学和物理特性。
2. 时间:物料需要在适当的时间内进行加热和处理,以确保其能够达到所需的硬度和强度。
3. 窑炉类型:不同类型的窑炉对物料的加工方式和工艺要求有不同的影响。
4. 物料特性:不同类型的原材料具有不同的化学和物理特性,因此需要针对其特点进行相应的处理。
五、结论窑炉是一种重要的加工设备,广泛应用于陶瓷、水泥、玻璃等行业中。
陶瓷窑炉的烧成气氛控制技术

陶瓷窑炉的烧成气氛控制技术
我们都知道陶瓷在进行烧成的时候,气氛是一项最为重要的因素之一,气氛可以关系到陶瓷的性能,例如:颜色、釉面质量、晶粒等等。
因此在烧制陶瓷的时候一定要控制好烧成的气氛。
下面就为大家介绍一下窑炉技术之气氛控制。
要想控制好烧成气氛,我们可以从两个方面进行控制,一是控制好窑内的压力,二是控制好窑内气体的成分比例。
一、控制窑内压力
压力可以影响窑内空气的流动,空气的流动速度不同,陶瓷就与空气的接触速度也不一样,这样空气中的各种物质就与陶瓷结合的速度、密度都各不相同;并且压力还能影响温度,我们都知道压力越大,温度可以达到的高度就会越高,从而影响烧成。
我们可以通过调整排烟口、抽热口、抽湿口的位置与大小;调整风机的风量等来进行控制到合理的压力。
二、控制窑内气体成分
窑内主要的气体是氧气与一氧化碳、氢气等燃烧气体。
因此窑内的主要反应就是氧化反应和还原反应。
所以我们必须控制好氧气与可燃烧气体的比例,确保氧化反应和还原反应维持在最佳水平,这样才能使得陶瓷烧制在最佳水平。
我们可以采取的措施有:1、使得两类气体能够充分的混合在一起;2、供应充足的空气,3、确保烧制时的温度。
以上两大点就是我们陶瓷窑炉技术中的烧成气氛的控制技术,只有做到这两点才能够确保烧制出精美的瓷器。
陶瓷窑炉的发展历史及烧制原理

陶瓷窑炉的发展历史及烧制原理陶瓷窑炉是一种用来烧制陶瓷制品的设备,它在人类文明发展史上起到了重要的作用。
本文将就陶瓷窑炉的发展历史及烧制原理进行探讨。
一、陶瓷窑炉的发展历史陶瓷制品的烧制可以追溯到古代文明时期。
早在新石器时代末期,人类就开始使用简单的土坑或石坑进行陶瓷烧制。
这种原始的烧制方式主要依靠火焰直接燃烧的热量来完成,虽然简单粗糙,但为后来陶瓷窑炉的发展打下了基础。
随着社会的进步和科技的发展,人们开始对陶瓷窑炉进行改进和创新。
在中国,最早的陶瓷窑炉可以追溯到商代晚期,当时已经出现了成套的窑炉系统,如龙山时期的龙山窑炉。
这些窑炉采用了砖石和夯土等材料进行建造,具备一定的隔热和保温性能,使得烧制温度得以提高。
随着时间的推移,陶瓷窑炉的设计和结构也不断改进。
在唐宋时期,窑炉的规模不断扩大,烧制温度也得到了提高。
同时,还出现了多种类型的窑炉,如龙窑、官窑、定窑等,各具特色。
这些陶瓷窑炉的出现,标志着中国陶瓷工艺的高度发展。
随着欧洲文艺复兴的兴起,陶瓷窑炉的技术也传播到了西方。
在意大利文艺复兴时期,陶瓷窑炉的烧制温度得到了进一步提高,从而使得陶瓷制品的质量得到了显著提升。
同时,窑炉的结构也更加复杂,具备了更好的温度控制和热量利用效率。
二、陶瓷窑炉的烧制原理陶瓷窑炉的烧制原理主要包括燃烧和热传导两个方面。
燃烧是陶瓷窑炉烧制的基本过程。
在窑炉内部,燃料(如木材、煤炭等)经过点火后,产生的热量会使窑炉内部的温度升高。
燃料的选择和燃烧方式的控制直接影响着陶瓷制品的质量和烧制效率。
热传导是指热量在陶瓷窑炉中的传递过程。
在燃烧产生的高温环境下,陶瓷制品中的水分和有机物会被蒸发和燃烧,随着温度的升高,陶瓷材料中的结晶水和化学结合水也会逐渐释放出来。
同时,热量会通过辐射、传导和对流的方式从窑炉的内部向外部传递,使得陶瓷制品的温度逐渐升高。
在整个烧制过程中,窑炉内部的温度分布是不均匀的,需要通过合理的设计和控制来实现温度的均衡分布。
窑炉烧成原理

窑炉烧成原理概述窑炉烧成是指通过高温的加热作用,将加工后的陶瓷原料转化为具有一定物理、化学性能的成品陶瓷制品的过程。
窑炉烧成是整个陶瓷生产过程中至关重要的一环,它不仅决定了成品陶瓷制品的品质,而且对能耗、产率、环保等方面也有着重要影响。
窑炉烧成的基本原理可以从热传导、物质变化和传输等几个方面来解释。
下面将详细介绍窑炉烧成原理的基本知识。
1. 热传导热传导是窑炉烧成过程中的一个基本原理。
在窑炉内,燃料燃烧产生的热量通过传导、辐射和对流三种方式传递给陶瓷制品。
窑炉烧成过程中,热传导起着重要的作用。
热传导的基本原理是热量由高温区域传递到低温区域。
在窑炉内部,燃料燃烧产生的高温气体和燃烧产物会加热窑炉内的墙体和炉膛,从而使陶瓷制品得到加热。
热量会从高温区域的颗粒内部传导到表面,然后再通过传导传递到其他颗粒。
热传导的速度取决于颗粒的材料特性、尺寸和温度差。
热传导的过程会导致窑炉内温度的变化,从而影响到陶瓷制品的烧成效果。
因此,在窑炉烧成过程中,需要合理控制燃料的供给、窑炉内部的温度分布,以确保热传导能够顺利进行。
2. 物质变化窑炉烧成过程中,陶瓷原料会经历多种物质变化,从而转化为成品陶瓷制品。
物质变化包括烧结、结晶、相变等过程。
•烧结是指陶瓷原料在高温下发生的固相粒子间的结合作用。
在窑炉内,陶瓷原料经过初烧后,粒子之间会发生烧结现象,从而形成致密的陶瓷坯体。
烧结过程中,陶瓷颗粒之间的共晶相或液相可以起到“胶黏剂”的作用,促进颗粒的结合。
•结晶是陶瓷原料在高温条件下形成结晶相的过程。
结晶是陶瓷制品获得特殊性能的重要途径之一。
在窑炉内,陶瓷原料经过烧结后,部分成份会发生结晶反应,形成晶体结构。
结晶过程中,原子或分子重新排列,从而形成特定的结晶相,提高陶瓷制品的强度、硬度、耐磨性等性能。
•相变是指陶瓷原料在加热或冷却过程中发生物理或化学性质改变的过程。
相变包括固相变、液相变和气相变等。
在窑炉烧成过程中,陶瓷原料会经历多个温度区间,从而发生相变。
中国古代陶瓷的主要烧成技术
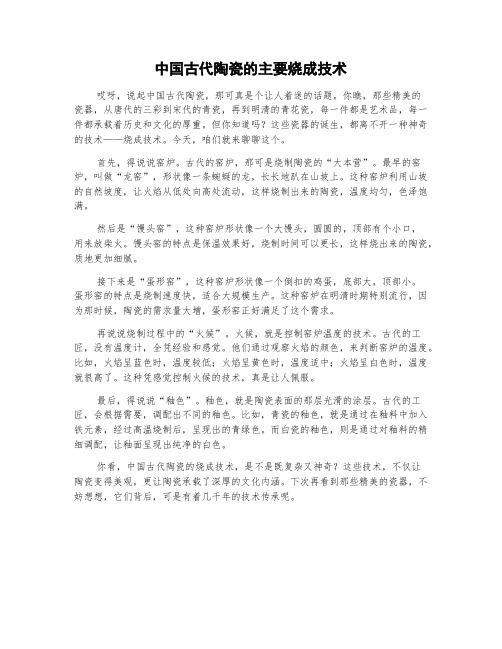
中国古代陶瓷的主要烧成技术哎呀,说起中国古代陶瓷,那可真是个让人着迷的话题。
你瞧,那些精美的瓷器,从唐代的三彩到宋代的青瓷,再到明清的青花瓷,每一件都是艺术品,每一件都承载着历史和文化的厚重。
但你知道吗?这些瓷器的诞生,都离不开一种神奇的技术——烧成技术。
今天,咱们就来聊聊这个。
首先,得说说窑炉。
古代的窑炉,那可是烧制陶瓷的“大本营”。
最早的窑炉,叫做“龙窑”,形状像一条蜿蜒的龙,长长地趴在山坡上。
这种窑炉利用山坡的自然坡度,让火焰从低处向高处流动,这样烧制出来的陶瓷,温度均匀,色泽饱满。
然后是“馒头窑”,这种窑炉形状像一个大馒头,圆圆的,顶部有个小口,用来放柴火。
馒头窑的特点是保温效果好,烧制时间可以更长,这样烧出来的陶瓷,质地更加细腻。
接下来是“蛋形窑”,这种窑炉形状像一个倒扣的鸡蛋,底部大,顶部小。
蛋形窑的特点是烧制速度快,适合大规模生产。
这种窑炉在明清时期特别流行,因为那时候,陶瓷的需求量大增,蛋形窑正好满足了这个需求。
再说说烧制过程中的“火候”。
火候,就是控制窑炉温度的技术。
古代的工匠,没有温度计,全凭经验和感觉。
他们通过观察火焰的颜色,来判断窑炉的温度。
比如,火焰呈蓝色时,温度较低;火焰呈黄色时,温度适中;火焰呈白色时,温度就很高了。
这种凭感觉控制火候的技术,真是让人佩服。
最后,得说说“釉色”。
釉色,就是陶瓷表面的那层光滑的涂层。
古代的工匠,会根据需要,调配出不同的釉色。
比如,青瓷的釉色,就是通过在釉料中加入铁元素,经过高温烧制后,呈现出的青绿色。
而白瓷的釉色,则是通过对釉料的精细调配,让釉面呈现出纯净的白色。
你看,中国古代陶瓷的烧成技术,是不是既复杂又神奇?这些技术,不仅让陶瓷变得美观,更让陶瓷承载了深厚的文化内涵。
下次再看到那些精美的瓷器,不妨想想,它们背后,可是有着几千年的技术传承呢。
- 1、下载文档前请自行甄别文档内容的完整性,平台不提供额外的编辑、内容补充、找答案等附加服务。
- 2、"仅部分预览"的文档,不可在线预览部分如存在完整性等问题,可反馈申请退款(可完整预览的文档不适用该条件!)。
- 3、如文档侵犯您的权益,请联系客服反馈,我们会尽快为您处理(人工客服工作时间:9:00-18:30)。
隧道窑始于1765年,当时只能烧陶瓷的釉上彩,到了 1810年,有可以用来烧砖或陶器的,从1906年起,才用 来烧瓷胎。
隧道窑一般是一条长的直线形隧道,其两侧及顶 部有固定的墙壁及拱顶,底部铺设的轨道上运行 着窑车。
据不同的制品来调节烧成温度。 缺点: 1、由于装窑、出窑均在窑内操作,故劳动强度大
2、热量损耗大,排出温度要很高,不然下部产品 烧不熟。
3 、是间歇式的,余热利用困难。
窑炉及陶瓷烧成
3. 梭式窑:
是间歇烧成的窑, 跟火柴盒的结构 类似,窑车推进 窑内烧成,烧完 了再往相反的方 向拉出来,卸下 烧好的陶瓷,窑 车如同梭子,故 而称为梭式窑。
窑炉及陶瓷烧成
火焰流向仍采用倒焰式,以对制品进行较 为均匀、全面的加热。
烧成后冷却了的制品随窑车拉出窑外,再 将另一部装好坯件的窑车推入窑内,进行 焙烧。
如此循环往复,象织布的梭子、桌子的抽 屉,故称为梭式窑、抽屉窑。
窑炉及陶瓷烧成
(二) 连续式窑
连续式窑炉的分类方法有多种,按制品的输送 方式可分为隧道窑、高温推板窑和辊道窑。
时燃料的灰渣经常会沾污制品而导致颜色不
良,为确保质量,就要采用匣钵。
清人朱琰在《陶说》中谈及匣钵时云:“瓷坯宜净, 一沾泥滓,即成斑驳,且窑风火气冲突伤坯,此所以 必用匣钵也。”
窑炉及陶瓷烧成
(2)若采用燃气窑、电窑等洁净能源的窑炉烧 制时(如陶艺),则趋向无钵烧制,窑内坯胎
的搁置主要以硅碳棚板为主。
窑炉及陶瓷烧成
2. 发热元件 电炉按炉温的高低可以分为低温(工作温度
低于700℃)、中温(工作温度为700—1250℃) 和高温(工作温度大于1250℃)三类。
➢ 炉温在1200℃以下,通常采用镍铬丝、 铁铬钨丝, ➢ 炉温为1350—1400℃时采用硅碳棒; ➢ 炉温为1600℃可采用二硅化钼棒为电热
2、热利用率高,燃料经济,因为热量的保 持和余热的利用都很良好,较倒焰窑可以 节省燃料50-60%左右。
3、烧成时间减短,而隧道窑约有10-20小 时左右就可以完成。
窑炉及陶瓷烧成
2、高温推板窑 椎扳式电热隧道窑的通道由一个或数个隧道所
组成,通道底由坚固的耐火砖精确砌成滑道,制 品装在推板上由顶推机构推入窑炉内烧成。
窑炉及陶瓷烧成
1、适于快速烧成— 不同产品在辊道窑中烧成的时间分别
为: 釉面砖35~50分钟; 瓷质砖50~100分钟, 卫生洁具8~10小时, 日用瓷12小时。 2、不必用窑车、匣钵、有的仅用耐火垫板
或不用垫板;
窑炉及陶瓷烧成
四. 窑炉辅助设备
1. 窑具——匣钵和棚板
(1)当窑炉为煤烧或柴烧等窑炉时,烧制
间歇式窑、连续式窑(隧道窑)、半连 续窑(龙窑、德化阶级窑)。
(5)按窑炉用途,分:
素烧窑、釉烧窑、烤花窑。
窑炉及陶瓷烧成
三. 现代陶瓷工业常见窑炉
(一) 间歇式窑炉 按其功能新颖性可分为电炉、高温倒焰窑、
梭式窑。
1、电炉
电炉(electric furnace)是电热窑炉的总称。
一般是通过电热元件把电能转变为热能,可分 为电阻炉、感应炉、电弧炉等。
体。
窑炉及陶瓷烧成
1. 热电偶
其主要作用除了 测试窑内温度之外, 还能在烧制时记录 连续升温以及恒温 的情况。 热电偶温度计可随 时掌握窑内温度的 变化情况而避免人 为的误差。
铂铑热电偶采用贵金属高纯铂金 为负极,铂铑合金为正极.
窑炉及陶瓷烧成
3. 烧制时需用眼睛不断地从观火孔观看:
窑内烧至暗红,则温度大约650-830 ℃。 如窑内烧至全红,这时温度大约在860-890℃。 火焰颜色为橙色时,温度大约在900-1000 ℃, 呈黄色时,大约1000-1200 ℃, 呈白色时大约在1230-1450 ℃; 窑内火呈蓝色时1450 ℃之上。
第 五章 窑炉及陶瓷烧成
窑炉及陶瓷烧成
二. 窑炉种类
按照不同标准,窑的分类大致有一下几种: (1)按使用燃料,分:
煤窑、油窑、气窑、电窑。
(2)按窑的外形,分:
馒头窑、马蹄窑、龙窑、葫芦窑、 圆窑、方窑、轮窑、隧道窑、
窑炉及陶瓷烧成
(3)按火焰特点,分:
直焰窑、倒焰窑、横焰窑。
(4)按生产工作情况,分:
梭式窑结构示意图 1-窑室;2-窑墙;3-窑顶;4-烧嘴;5-升降窑门; 6-支烟道;7-窑车;8-轨道
窑炉及陶瓷烧成
3. 梭式窑的结构特点是: 窑底改为窑车式,由1—2辆窑车组成。
窑车上砌有吸火孔、支烟道和主烟道。
窑车上的吸火孔、支烟道和主烟道可与窑体上的 排烟通道衔接起来,通往烟囱。
装钵、装车均在窑外进行,在室温下操作,大大 减轻了工人的劳动强度。
燃烧设备设在隧道窑的中部两侧,构成了固定的 高温带--烧成带。
燃烧产生的高温烟气在隧道窑前端烟囱或引风机 的作用下,同时逐步地预热进入窑内的制品,这 一段构成了隧道窑的预热带。
在隧道窑的窑尾鼓入冷风,冷却隧道窑内后一段 的制品,这一段便构成了隧道窑的冷却带。
窑炉及陶瓷烧成
隧道窑优点: 1、生产连续化,周期短,产量大,质量高。
窑炉及陶瓷烧成
第二节 陶瓷烧成
窑炉及陶瓷烧成
陶瓷烧成技术: 借助窑炉、窑具和燃料加热陶瓷生
坯,在受热过程中物料本身经过物 理化学反应达到各种程度的致密化 烧结的技术。 窑炉结构和窑具种类以及装烧方法 是影响成品质量最关键因素之一。 三大要素:土、水、火。
窑炉及陶瓷烧成
2、高温倒焰窑(reverse flame kiln)
倒焰窑工作流程
1-窑室;2-燃烧室;3-灰坑;4-窑底吸火孔;5-支烟道; 6-主烟道;7-挡火墙;8-窑墙;9-窑顶;10-喷火口
窑炉及陶瓷烧成
优点: 1. 对制品的加热比较充分,均匀。 2. 适应性很强,因为是间歇式的,所以可以根
窑炉及陶瓷烧成
3、辊(gun)道窑(roller kiln) 辊道窑是隧道窑的一种,只是传递烧结样品的
传递系统不是传统的窑车、推板,而是同步转动 的陶瓷或金属辊棒。 每条辊子在窑外传动机构的作用下不断地转动;
制品由隧道的预热端放置在辊子上,在辊子的转 动作用下通过隧道的预热带、烧成带和冷却带。