电炉炼钢
炼钢电炉种类

炼钢电炉种类引言炼钢电炉是一种利用电能作为热源,将生铁、废钢等原材料熔化并加以精炼的设备。
它具有高热效率、灵活性高、环境友好等优点,在炼钢工业中得到广泛应用。
本文将介绍几种常见的炼钢电炉种类,并分析其特点和应用范围。
1. 液压倾转式炼钢电炉液压倾转式炼钢电炉是一种通过液压机构控制炉体的倾转和转动,实现料材的混炼和炉渣的排除的炼钢电炉。
该种电炉结构简单,操作方便,能够有效控制温度和炉渣的流动。
它广泛应用于小型钢铁企业,特别适用于炼钢废料、废钢的回收利用。
液压倾转式电炉的工作原理是:首先将废钢材料装入炉体内,通过电能加热将其熔化;然后倾转炉体,使炉渣通过炉口流出;最后将炉体转动,使熔化的钢液均匀混合。
该电炉操作简单,生产效率高,能够满足小型钢铁企业的生产需求。
2. 水冷壳式炼钢电炉水冷壳式炼钢电炉是一种将冷却水进行循环利用,控制炉体温度的炼钢电炉。
它通过将电炉炉体的外壳进行水冷却,保持炉体温度在一定范围内。
水冷壳式电炉具有结构简单、使用安全、热效率高等特点。
该种电炉的制造材料常使用高硅酸铸石、耐火砖等耐火材料,并在炉体内衬设电极,通过电能加热将炉材料熔化。
冷却水通过壁面的管道流动,将炉体散热,使其保持适宜的温度。
水冷壳式电炉适用于小型和中型钢铁企业,可用于炼钢废料、废钢的再生利用。
3. 氧气底吹炼钢电炉氧气底吹炼钢电炉是一种利用高压氧气进行喷吹,提高炉内温度和炉渣脱硫的炼钢电炉。
它通过在炉底喷吹氧气,将炉内温度提高到所需温度,同时促进炉渣中的杂质氧化并排除。
氧气底吹炼钢电炉具有温度控制精确、炉渣质量好等优点。
氧气底吹炼钢电炉一般采用大型高炉的结构,内部设有电极和底吹氧气口。
底吹氧气通过喷口进入炉内,与炉料和炉渣进行充分交互反应。
该种电炉适用于大型钢铁企业,可以实现高温高质量的炼钢。
4. 耐火气体电炉耐火气体电炉是一种利用氮气、氩气等惰性气体进行保护的炼钢电炉。
它通过将炉体内充满惰性气体,将氧气排出,降低钢材中氧含量和杂质含量。
电炉炼钢

炉料熔化过程及供电
装料完毕即可通电熔化。炉料熔化过程图, 基本可分为四个阶段(期),即点弧、穿井、主 熔化及熔末升温。
点(起)弧期
从送电起弧至电极端部下降到深度为d电极为点 弧期。 此期电流不稳定,电弧在炉顶附近燃烧辐射,二 次电压越高,电弧越长,对炉顶辐射越厉害,并且热 量损失也越多。 为保护炉顶,在炉上部布一些轻薄料,以便让电 极快速进入料中,减少电弧对炉顶的辐射。 供电上采用较低电压、较低电流。
近些年,我国电炉流程的发展虽然受到重视, 但发展电炉短流程应慎重一些,可以适当发展, 不可盲目。因为在当前条件下,我国不具备电 能和废钢方面的优势,即不具备成本优势。在 江阴兴澄钢铁有限公司,已建成我国第一条四 位一体的特殊钢短流程生产线,工艺流程 为:100t直流电弧炉冶炼-LF、VD精炼-R=12m 大方坯连铸-热送全连轧,全套全新设备从德国 引进,能够开发生产合金结构钢、弹簧钢、齿 轮钢、易切削钢、轴承钢、高压锅炉管坯钢等 品种,将成为全国优质钢、特殊钢装备水平领 先、能力超百万吨的企业
2)双渣氧化法
又称氧化法,它的特点是冶炼过程有正常的氧 化期,能脱碳、脱磷,去气、夹杂,对炉料也无特殊要
求;还有还原期,可以冶炼高质量钢。
目前,几乎所有的钢种都可以用氧化法冶炼, 以下主要介绍氧化法冶炼工艺。
冶炼工艺
传统氧化法冶炼工艺是电炉炼钢法的基础。 其操作过程分为:补炉、装料、熔化、 氧化、还原与出钢六个阶段。因主要由熔化、氧 化、还原期组成,俗称老三期。 一、补炉 1)影响炉衬寿命的“三要素” • 炉衬的种类、性质和质量; • 高温电弧辐射和熔渣的化学浸蚀; • 吹氧操作与渣、钢等机械冲刷以及装料的冲击。
脱磷反应与脱磷条件:
脱磷反应:
2[P]+5(FeO)+4(CaO)=(4CaO· P2O5)+5 [Fe], △ H<0 分析:反应是在渣-钢界面上进行,是放 热反应。
电炉炼钢知识点总结图

电炉炼钢知识点总结图电炉炼钢是一种利用电能作为热源进行炼钢的工艺,在当今钢铁工业中应用广泛。
相比传统的炼钢方法,电炉炼钢具有能耗低、环保、生产效率高等优点,因此受到了越来越多的关注和应用。
本文将对电炉炼钢的相关知识点进行总结,以便读者更好地了解这一工艺。
一、电炉炼钢的基本原理电炉炼钢的基本原理是利用电阻加热的方式,将冶炼炉内的原料加热至熔化或半熔化状态,然后通过不同的工艺流程进行炼钢。
电炉主要分为两种类型:一种是电弧炉,另一种是感应炉。
电弧炉是通过电弧放电产生的高温加热原料,而感应炉则是通过感应加热的原理来实现加热。
不同类型的电炉在原理和工艺上有所不同,但基本原理都是利用电能进行加热冶炼。
二、电炉炼钢的工艺流程1. 准备原料:首先需要准备炼钢所需的原料,包括废钢、熔剂、脱氧剂等。
这些原料一般需要进行称重和配比,以确保炉内的化学成分符合要求。
2. 加料熔化:将准备好的原料装入电炉内,通过电能加热使其熔化。
在炼钢过程中,需要根据具体情况加入适量的熔剂和脱氧剂,以调整钢液的成分和性能。
3. 调整温度:在原料完全熔化后,需要根据钢液的工艺要求和加工工艺来调整温度,并保持在一定范围内。
4. 炉渣处理:在炉内的炼钢过程中,会产生一定的炉渣,需要及时处理和清理,以保证炉内钢液的纯净度。
5. 精炼:通过对钢液的搅拌和通入气体等方式,实现对钢液中夹杂物和气体的精炼,以提高钢液的质量。
6. 浇铸:最后,将经过炼钢的钢液浇入模具,并进行冷却凝固,得到成品钢材。
三、电炉炼钢的特点和优势1. 可控性强:电炉炼钢的加热过程可以通过电能控制,温度、时间等参数可以实现精准控制,以满足不同成分和性能要求的钢液。
2. 环保:电炉炼钢相比传统炼钢方法,产生的废气和废渣相对较少,对环境影响较小,符合当今的环保要求。
3. 能耗低:相比高炉等传统炼钢设备,电炉炼钢所需的能耗较低,有利于节能减排。
4. 适应性强:电炉炼钢可根据需要进行小批量生产,适应性较强,可以满足市场快速变化的需求。
电炉炼钢原理及工艺
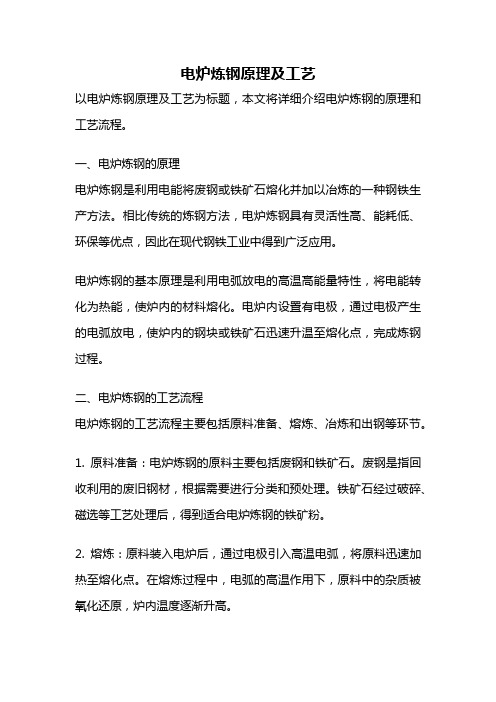
电炉炼钢原理及工艺以电炉炼钢原理及工艺为标题,本文将详细介绍电炉炼钢的原理和工艺流程。
一、电炉炼钢的原理电炉炼钢是利用电能将废钢或铁矿石熔化并加以冶炼的一种钢铁生产方法。
相比传统的炼钢方法,电炉炼钢具有灵活性高、能耗低、环保等优点,因此在现代钢铁工业中得到广泛应用。
电炉炼钢的基本原理是利用电弧放电的高温高能量特性,将电能转化为热能,使炉内的材料熔化。
电炉内设置有电极,通过电极产生的电弧放电,使炉内的钢块或铁矿石迅速升温至熔化点,完成炼钢过程。
二、电炉炼钢的工艺流程电炉炼钢的工艺流程主要包括原料准备、熔炼、冶炼和出钢等环节。
1. 原料准备:电炉炼钢的原料主要包括废钢和铁矿石。
废钢是指回收利用的废旧钢材,根据需要进行分类和预处理。
铁矿石经过破碎、磁选等工艺处理后,得到适合电炉炼钢的铁矿粉。
2. 熔炼:原料装入电炉后,通过电极引入高温电弧,将原料迅速加热至熔化点。
在熔炼过程中,电弧的高温作用下,原料中的杂质被氧化还原,炉内温度逐渐升高。
3. 冶炼:炉内温度达到要求后,加入适量的脱氧剂和合金元素,调整炉内成分,提高钢的质量。
同时,通过喷吹氧气等方式进行氧化剂的供给,控制冶炼过程中的氧化还原反应,进一步净化钢液。
4. 出钢:冶炼结束后,通过倒炉或倾炉等方式将炼好的钢液从电炉中倾出,进一步加工成所需的钢材。
出钢后,需要进行连铸、轧制等工艺,最终得到成品钢材。
三、电炉炼钢的特点和优势1. 灵活性高:电炉炼钢可灵活调整炉内温度和成分,适应不同的钢种和质量要求,具有较强的适应性和灵活性。
2. 能耗低:电炉炼钢相比传统炼钢方法,能耗更低。
电能可以高效转化为热能,提高能源利用效率,减少能源浪费。
3. 环保:电炉炼钢过程中没有燃料燃烧产生的废气和废渣,减少了对环境的污染。
另外,电炉炼钢可以使用废钢作为原料,有效促进了废钢的回收利用,减少了资源浪费。
4. 生产效率高:电炉炼钢的工艺流程简单,生产周期短,可以实现快速连续生产,提高生产效率。
电炉炼钢流程

电炉炼钢流程电炉炼钢是一种利用电能作为热源,通过电弧加热炉料,将废钢和铁合金等原料炼制成优质钢材的冶炼方法。
电炉炼钢流程通常包括预处理、炉料装入、炉前准备、炉内冶炼和炉后处理等环节。
下面将详细介绍电炉炼钢的流程及各个环节的操作步骤。
1. 预处理。
在进行电炉炼钢之前,首先需要对原料进行预处理。
这包括对废钢进行分类、清理和切割,对铁合金进行筛分和称重等工作。
同时,还需要对电炉进行检查和维护,确保电炉设备处于良好状态。
2. 炉料装入。
在炉料装入环节,操作人员需要按照炉料配比要求,将预处理好的废钢和铁合金装入电炉中。
同时,还需要加入适量的石灰、氧化铁等炼钢助剂,以调整炉料成分和保证冶炼质量。
3. 炉前准备。
在炉前准备阶段,操作人员需要对电炉进行预热,提高炉温至冶炼温度。
同时,还需要对电炉进行真空抽气或气体通风,以确保炉内气氛符合冶炼要求。
4. 炉内冶炼。
炉内冶炼是电炉炼钢的核心环节,操作人员需要根据工艺要求,通过电弧加热炉料,使其迅速熔化。
在冶炼过程中,还需要根据炉料状况进行合理的搅拌和氧化处理,以保证炼钢过程的顺利进行。
5. 炉后处理。
炉后处理是指在炼钢结束后,对冶炼产物进行处理和整理的环节。
这包括对炉渣进行清理和处理,对炼钢温度进行控制,以及对炼钢成品进行取样和检验等工作。
总结。
通过以上流程的介绍,我们可以看到,电炉炼钢是一个复杂的工艺过程,需要操作人员严格按照流程要求进行操作,以确保炼钢质量和生产效率。
同时,还需要对电炉设备进行定期维护和检查,以保证设备的正常运行和安全生产。
希望本文的介绍能够帮助大家更好地了解电炉炼钢的流程和操作要点,为相关行业的生产和管理工作提供参考和指导。
电炉炼钢工艺流程
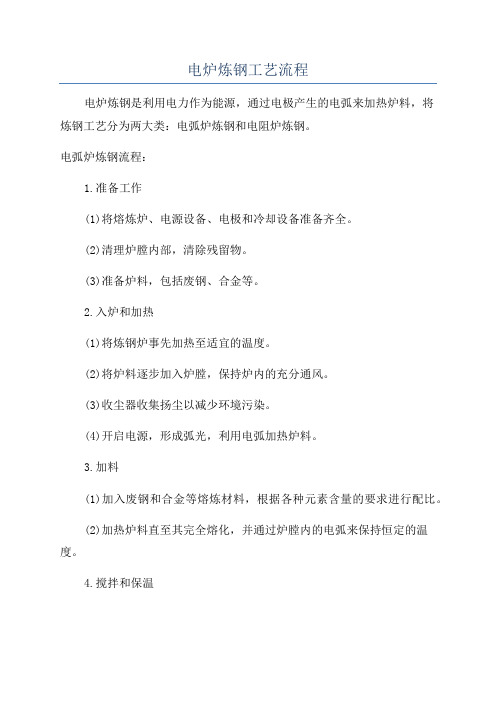
电炉炼钢工艺流程电炉炼钢是利用电力作为能源,通过电极产生的电弧来加热炉料,将炼钢工艺分为两大类:电弧炉炼钢和电阻炉炼钢。
电弧炉炼钢流程:1.准备工作(1)将熔炼炉、电源设备、电极和冷却设备准备齐全。
(2)清理炉膛内部,清除残留物。
(3)准备炉料,包括废钢、合金等。
2.入炉和加热(1)将炼钢炉事先加热至适宜的温度。
(2)将炉料逐步加入炉膛,保持炉内的充分通风。
(3)收尘器收集扬尘以减少环境污染。
(4)开启电源,形成弧光,利用电弧加热炉料。
3.加料(1)加入废钢和合金等熔炼材料,根据各种元素含量的要求进行配比。
(2)加热炉料直至其完全熔化,并通过炉膛内的电弧来保持恒定的温度。
4.搅拌和保温(1)通过搅拌装置(机械手、气枪等)对炉内炉料进行搅拌,以保证均匀加热。
(2)在最佳温度下保温,以提高合金和炉料的反应速度。
5.放钢和渣(1)根据钢种要求,加入脱氧剂和合金稀释剂。
(2)按照配方要求加入炉渣,帮助除去杂质和渣夹。
6.合金调整和测温(1)根据测温结果,调整冶炼条件,确保达到合适的温度。
(2)根据钢种需要,加入适量的合金元素,保证合金成分符合技术要求。
7.出钢(1)开启出钢口,将炼好的钢液顺利倾出。
(2)根据需要对炼钢炉进行钢包保温、修补等工作。
(3)将倾出的钢液进行调节和再加工,以满足用户要求。
(4)进行钢液的凝固和结晶,得到成品钢。
电阻炉炼钢流程:电阻炉是通过电流通过炉体自身的电阻产生热能,实现炉料加热熔化。
1.准备工作(1)检查电阻炉的各项设备和电源的正常运行。
(2)清理炉内和炉外的杂质和残留物。
(3)准备好炉料,包括废钢、矿石等。
2.入炉和加热(1)将炼钢炉预先加热至适宜的温度。
(2)逐步加入炉料,保持通风和顺畅的炉内气流。
(3)开启电源,使电流通过炉体,产生热能。
3.加料和熔化(1)加入炉料,实现其完全熔化。
(2)通过控制电流和炉内温度,保持炉料的恒定熔化状态。
4.炉内观察和保温(1)观察炉内炉料的状况,保持熔化状态的均匀性。
电炉炼钢原理及工艺
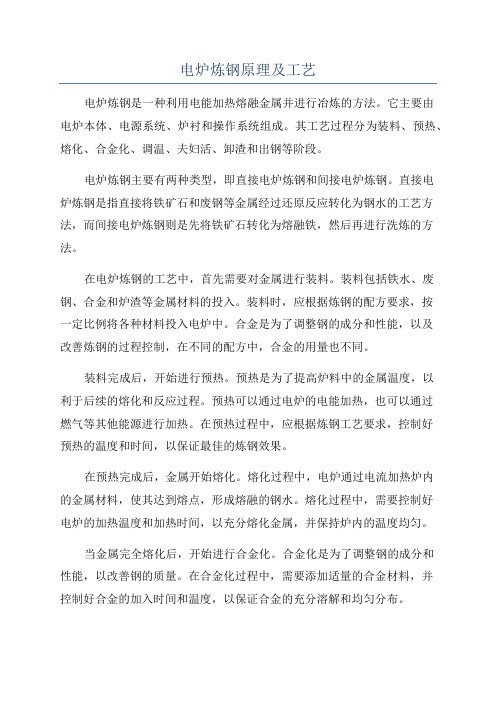
电炉炼钢原理及工艺电炉炼钢是一种利用电能加热熔融金属并进行冶炼的方法。
它主要由电炉本体、电源系统、炉衬和操作系统组成。
其工艺过程分为装料、预热、熔化、合金化、调温、夫妇活、卸渣和出钢等阶段。
电炉炼钢主要有两种类型,即直接电炉炼钢和间接电炉炼钢。
直接电炉炼钢是指直接将铁矿石和废钢等金属经过还原反应转化为钢水的工艺方法,而间接电炉炼钢则是先将铁矿石转化为熔融铁,然后再进行洗炼的方法。
在电炉炼钢的工艺中,首先需要对金属进行装料。
装料包括铁水、废钢、合金和炉渣等金属材料的投入。
装料时,应根据炼钢的配方要求,按一定比例将各种材料投入电炉中。
合金是为了调整钢的成分和性能,以及改善炼钢的过程控制,在不同的配方中,合金的用量也不同。
装料完成后,开始进行预热。
预热是为了提高炉料中的金属温度,以利于后续的熔化和反应过程。
预热可以通过电炉的电能加热,也可以通过燃气等其他能源进行加热。
在预热过程中,应根据炼钢工艺要求,控制好预热的温度和时间,以保证最佳的炼钢效果。
在预热完成后,金属开始熔化。
熔化过程中,电炉通过电流加热炉内的金属材料,使其达到熔点,形成熔融的钢水。
熔化过程中,需要控制好电炉的加热温度和加热时间,以充分熔化金属,并保持炉内的温度均匀。
当金属完全熔化后,开始进行合金化。
合金化是为了调整钢的成分和性能,以改善钢的质量。
在合金化过程中,需要添加适量的合金材料,并控制好合金的加入时间和温度,以保证合金的充分溶解和均匀分布。
合金化完成后,开始进行调温。
调温是为了得到合适的熔融铁水温度和钢水温度,以满足后续冶炼工艺的需求。
调温可以通过调节电炉的加热功率和炉内的温度控制装置来实现。
调温完成后,进行夫妇活。
夫妇活是为了提高钢水的纯净度和均匀性,以去除炉渣和杂质。
夫妇活可以通过在炉内注入草酸、石灰和氮气等化学物质,或者进行吹炼和搅拌来实现。
夫妇活完成后,开始卸渣。
卸渣是指将炉渣从熔融金属中移除的过程。
卸渣可以通过倾炉或者顶炉的方式来进行。
电炉炼钢流程
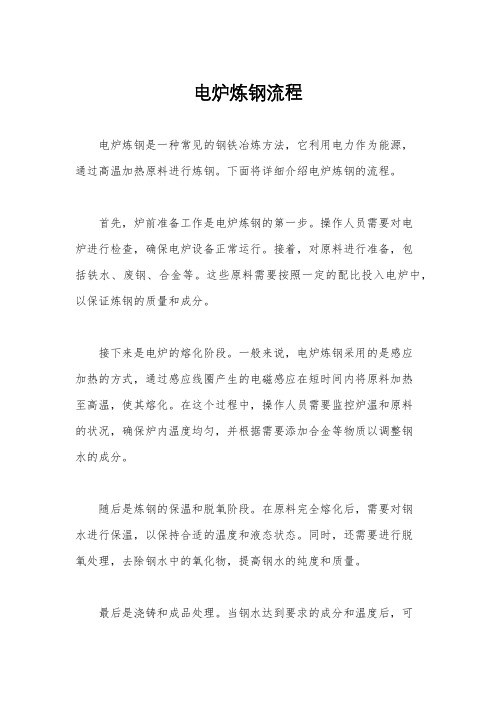
电炉炼钢流程
电炉炼钢是一种常见的钢铁冶炼方法,它利用电力作为能源,
通过高温加热原料进行炼钢。
下面将详细介绍电炉炼钢的流程。
首先,炉前准备工作是电炉炼钢的第一步。
操作人员需要对电
炉进行检查,确保电炉设备正常运行。
接着,对原料进行准备,包
括铁水、废钢、合金等。
这些原料需要按照一定的配比投入电炉中,以保证炼钢的质量和成分。
接下来是电炉的熔化阶段。
一般来说,电炉炼钢采用的是感应
加热的方式,通过感应线圈产生的电磁感应在短时间内将原料加热
至高温,使其熔化。
在这个过程中,操作人员需要监控炉温和原料
的状况,确保炉内温度均匀,并根据需要添加合金等物质以调整钢
水的成分。
随后是炼钢的保温和脱氧阶段。
在原料完全熔化后,需要对钢
水进行保温,以保持合适的温度和液态状态。
同时,还需要进行脱
氧处理,去除钢水中的氧化物,提高钢水的纯度和质量。
最后是浇铸和成品处理。
当钢水达到要求的成分和温度后,可
以进行浇铸。
操作人员需要将钢水倒入模具中,进行成型。
成型后的钢坯需要进行冷却和固化,然后进行后续的加工处理,最终得到成品钢材。
总的来说,电炉炼钢流程包括炉前准备、熔化、保温和脱氧、浇铸和成品处理几个关键步骤。
在实际操作中,需要严格控制每个环节,确保炼钢过程稳定、高效,最终得到优质的钢材产品。
电炉炼钢原理及工艺
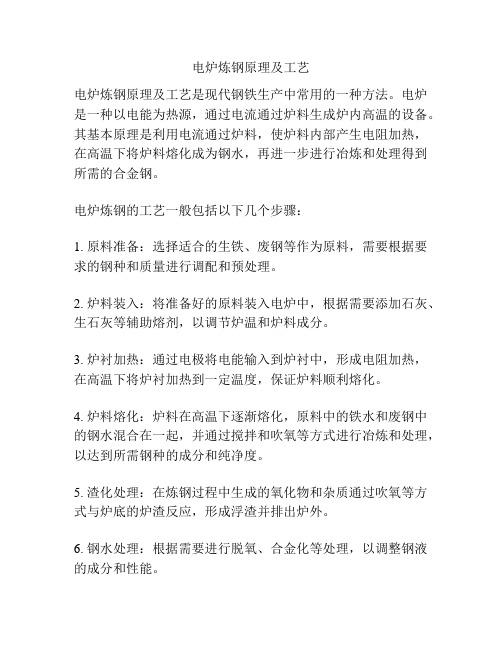
电炉炼钢原理及工艺
电炉炼钢原理及工艺是现代钢铁生产中常用的一种方法。
电炉是一种以电能为热源,通过电流通过炉料生成炉内高温的设备。
其基本原理是利用电流通过炉料,使炉料内部产生电阻加热,在高温下将炉料熔化成为钢水,再进一步进行冶炼和处理得到所需的合金钢。
电炉炼钢的工艺一般包括以下几个步骤:
1. 原料准备:选择适合的生铁、废钢等作为原料,需要根据要求的钢种和质量进行调配和预处理。
2. 炉料装入:将准备好的原料装入电炉中,根据需要添加石灰、生石灰等辅助熔剂,以调节炉温和炉料成分。
3. 炉衬加热:通过电极将电能输入到炉衬中,形成电阻加热,在高温下将炉衬加热到一定温度,保证炉料顺利熔化。
4. 炉料熔化:炉料在高温下逐渐熔化,原料中的铁水和废钢中的钢水混合在一起,并通过搅拌和吹氧等方式进行冶炼和处理,以达到所需钢种的成分和纯净度。
5. 渣化处理:在炼钢过程中生成的氧化物和杂质通过吹氧等方式与炉底的炉渣反应,形成浮渣并排出炉外。
6. 钢水处理:根据需要进行脱氧、合金化等处理,以调整钢液的成分和性能。
7. 出钢:达到要求后,将炉内的钢水倾倒到包铸机或连铸机中进行连铸或铸锭。
8. 后续处理:根据需要对钢水的温度、成分、物理性能等进行进一步调整和处理,以获得可供应市场的成品钢材。
总之,电炉炼钢是一种使用电能为热源的钢铁生产方法。
其原理是利用电阻加热炉料达到高温,将炉料熔化成钢水,再经过冶炼和处理得到所需的合金钢。
根据具体工艺要求,通过合理选料、调配、预处理、炉衬加热、炉料熔化、渣化处理、钢水处理等一系列步骤,最终获得合格的钢材产品。
电炉炼钢原理及工艺

电炉炼钢原理及工艺
电炉炼钢是利用电力作为热源,通过电弧加热的方式,将生铁
或废钢进行熔炼,加入适量的合金元素,最终得到符合特定要求的
钢铁产品的一种炼钢工艺。
电炉炼钢具有能耗低、环保、生产灵活
等优点,因此在现代钢铁工业中得到了广泛应用。
电炉炼钢的原理主要是通过电弧将炉料加热至熔化温度,同时
控制合金元素的加入,最终实现对炉料成分和温度的精确控制,从
而得到符合要求的钢铁产品。
电炉炼钢主要包括三种类型,直接电
弧炉、感应电炉和电渣重熔炉。
不同类型的电炉在原理和工艺上略
有不同,但基本的炼钢原理是相似的。
电炉炼钢的工艺流程一般包括,炉料装入、预热、电弧加热、
合金元素加入、脱氧、脱硫、炉渣处理等环节。
在整个工艺过程中,需要严格控制炉料的成分和温度,合理控制电弧加热的能量,确保
炼钢过程中的各项参数处于合适的范围,从而保证炼钢的质量。
电炉炼钢的原理和工艺虽然相对复杂,但是在实际生产中已经
得到了充分的验证和应用。
随着现代工艺技术的不断进步,电炉炼
钢的工艺也在不断完善和提高。
在炼钢过程中,需要考虑原料的选
择、电弧加热的控制、合金元素的加入、炉渣的处理等诸多因素,以确保最终生产出符合要求的钢铁产品。
总的来说,电炉炼钢是一种先进的炼钢工艺,其原理和工艺流程相对复杂,但是通过合理的控制和优化,可以实现对钢铁产品质量的精确控制。
随着工艺技术的不断进步,电炉炼钢必将在钢铁工业中发挥越来越重要的作用,为钢铁生产的发展做出更大的贡献。
电炉炼钢主要危险性分析
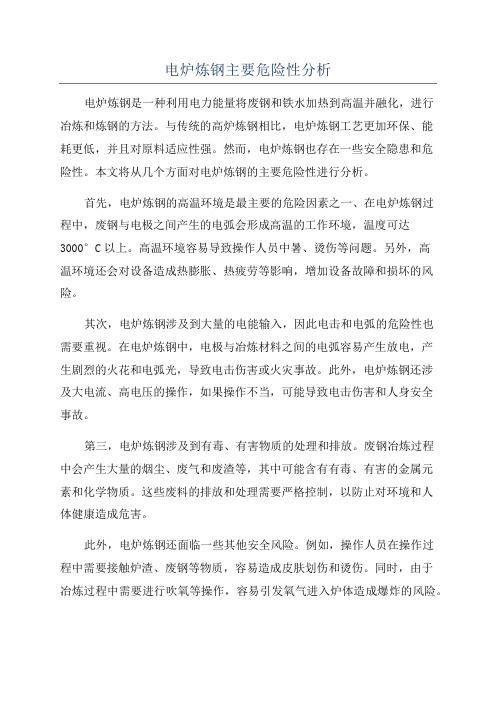
电炉炼钢主要危险性分析电炉炼钢是一种利用电力能量将废钢和铁水加热到高温并融化,进行冶炼和炼钢的方法。
与传统的高炉炼钢相比,电炉炼钢工艺更加环保、能耗更低,并且对原料适应性强。
然而,电炉炼钢也存在一些安全隐患和危险性。
本文将从几个方面对电炉炼钢的主要危险性进行分析。
首先,电炉炼钢的高温环境是最主要的危险因素之一、在电炉炼钢过程中,废钢与电极之间产生的电弧会形成高温的工作环境,温度可达3000°C以上。
高温环境容易导致操作人员中暑、烫伤等问题。
另外,高温环境还会对设备造成热膨胀、热疲劳等影响,增加设备故障和损坏的风险。
其次,电炉炼钢涉及到大量的电能输入,因此电击和电弧的危险性也需要重视。
在电炉炼钢中,电极与冶炼材料之间的电弧容易产生放电,产生剧烈的火花和电弧光,导致电击伤害或火灾事故。
此外,电炉炼钢还涉及大电流、高电压的操作,如果操作不当,可能导致电击伤害和人身安全事故。
第三,电炉炼钢涉及到有毒、有害物质的处理和排放。
废钢冶炼过程中会产生大量的烟尘、废气和废渣等,其中可能含有有毒、有害的金属元素和化学物质。
这些废料的排放和处理需要严格控制,以防止对环境和人体健康造成危害。
此外,电炉炼钢还面临一些其他安全风险。
例如,操作人员在操作过程中需要接触炉渣、废钢等物质,容易造成皮肤划伤和烫伤。
同时,由于冶炼过程中需要进行吹氧等操作,容易引发氧气进入炉体造成爆炸的风险。
此外,电炉炼钢还存在设备故障、电力故障等问题,这些问题可能导致生产中断、设备损坏等风险。
为了减少电炉炼钢的危险性,需要采取一系列的安全措施。
首先,操作人员需要接受相关的安全培训,熟悉电炉炼钢的操作规程和安全注意事项。
其次,应该配备适当的个人防护设备,如防护服、面罩、手套等,以保护操作人员的安全。
另外,应该加强设备的维护和监控,及时发现和修复设备故障,确保设备的正常运行。
此外,还需要建立完善的环境监测体系,对废气、废水等进行监测和治理,以减少对环境的危害。
电炉炼钢概述
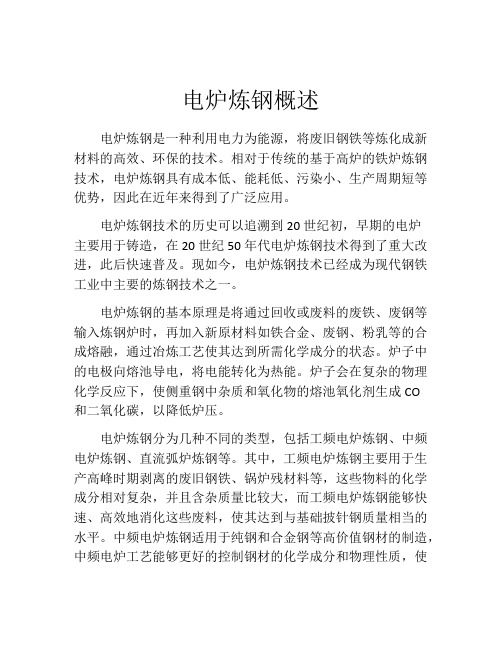
电炉炼钢概述电炉炼钢是一种利用电力为能源,将废旧钢铁等炼化成新材料的高效、环保的技术。
相对于传统的基于高炉的铁炉炼钢技术,电炉炼钢具有成本低、能耗低、污染小、生产周期短等优势,因此在近年来得到了广泛应用。
电炉炼钢技术的历史可以追溯到20世纪初,早期的电炉主要用于铸造,在20世纪50年代电炉炼钢技术得到了重大改进,此后快速普及。
现如今,电炉炼钢技术已经成为现代钢铁工业中主要的炼钢技术之一。
电炉炼钢的基本原理是将通过回收或废料的废铁、废钢等输入炼钢炉时,再加入新原材料如铁合金、废钢、粉乳等的合成熔融,通过冶炼工艺使其达到所需化学成分的状态。
炉子中的电极向熔池导电,将电能转化为热能。
炉子会在复杂的物理化学反应下,使侧重钢中杂质和氧化物的熔池氧化剂生成CO和二氧化碳,以降低炉压。
电炉炼钢分为几种不同的类型,包括工频电炉炼钢、中频电炉炼钢、直流弧炉炼钢等。
其中,工频电炉炼钢主要用于生产高峰时期剥离的废旧钢铁、锅炉残材料等,这些物料的化学成分相对复杂,并且含杂质量比较大,而工频电炉炼钢能够快速、高效地消化这些废料,使其达到与基础披针钢质量相当的水平。
中频电炉炼钢适用于纯钢和合金钢等高价值钢材的制造,中频电炉工艺能够更好的控制钢材的化学成分和物理性质,使得钢材的稳定性更高,更适用于一些重要领域的应用。
直流弧炉炼钢则适用于生产大表面积和高薄形态的钢板等产品。
总体来说,电炉炼钢技术具有很多优点,包括生产周期短,成本低,能确保产量等。
同时,它非常适合生产高质量和高品质的钢材,在环保方面,电炉炼钢也无疑是十分友好的,因为它不会排放污染物,也不会产生重金属等有害物质。
总的来说,随着科技的不断发展和对环保问题的关注,电炉炼钢技术在现代钢铁工业中的影响日益增强,同时它也为钢铁行业的可持续发展注入了新的动力。
未来,电炉炼钢技术还将继续演化和改进,在钢铁行业中扮演更重要的角色。
电炉炼钢原理及工艺
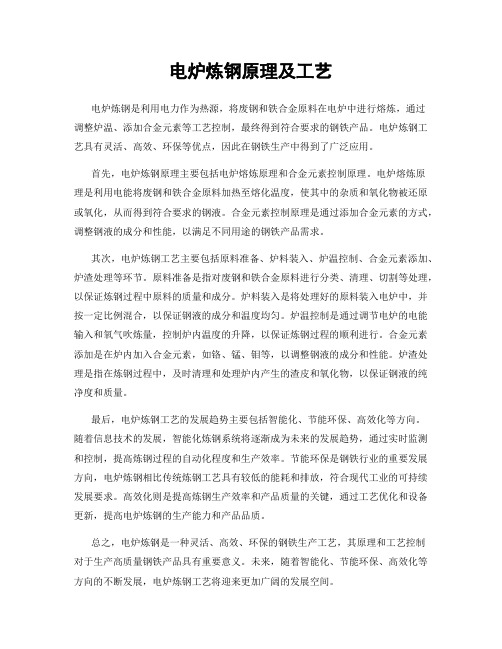
电炉炼钢原理及工艺电炉炼钢是利用电力作为热源,将废钢和铁合金原料在电炉中进行熔炼,通过调整炉温、添加合金元素等工艺控制,最终得到符合要求的钢铁产品。
电炉炼钢工艺具有灵活、高效、环保等优点,因此在钢铁生产中得到了广泛应用。
首先,电炉炼钢原理主要包括电炉熔炼原理和合金元素控制原理。
电炉熔炼原理是利用电能将废钢和铁合金原料加热至熔化温度,使其中的杂质和氧化物被还原或氧化,从而得到符合要求的钢液。
合金元素控制原理是通过添加合金元素的方式,调整钢液的成分和性能,以满足不同用途的钢铁产品需求。
其次,电炉炼钢工艺主要包括原料准备、炉料装入、炉温控制、合金元素添加、炉渣处理等环节。
原料准备是指对废钢和铁合金原料进行分类、清理、切割等处理,以保证炼钢过程中原料的质量和成分。
炉料装入是将处理好的原料装入电炉中,并按一定比例混合,以保证钢液的成分和温度均匀。
炉温控制是通过调节电炉的电能输入和氧气吹炼量,控制炉内温度的升降,以保证炼钢过程的顺利进行。
合金元素添加是在炉内加入合金元素,如铬、锰、钼等,以调整钢液的成分和性能。
炉渣处理是指在炼钢过程中,及时清理和处理炉内产生的渣皮和氧化物,以保证钢液的纯净度和质量。
最后,电炉炼钢工艺的发展趋势主要包括智能化、节能环保、高效化等方向。
随着信息技术的发展,智能化炼钢系统将逐渐成为未来的发展趋势,通过实时监测和控制,提高炼钢过程的自动化程度和生产效率。
节能环保是钢铁行业的重要发展方向,电炉炼钢相比传统炼钢工艺具有较低的能耗和排放,符合现代工业的可持续发展要求。
高效化则是提高炼钢生产效率和产品质量的关键,通过工艺优化和设备更新,提高电炉炼钢的生产能力和产品品质。
总之,电炉炼钢是一种灵活、高效、环保的钢铁生产工艺,其原理和工艺控制对于生产高质量钢铁产品具有重要意义。
未来,随着智能化、节能环保、高效化等方向的不断发展,电炉炼钢工艺将迎来更加广阔的发展空间。
电炉炼钢知识点总结

电炉炼钢知识点总结一、电炉炼钢的基本原理电炉炼钢是利用电能将生铁、废钢或铁合金作为主要原料,通过高温加热与熔融,加入合适的脱氧合金元素进行精炼,最终获得符合要求的钢水的工艺过程。
电炉炼钢主要依靠电弧能量加热熔化金属,通过电渣或氧下吹气使金属氧化物脱碳、脱硅、脱磷、脱硫,同时调整合金成分,最终得到符合要求的钢水。
二、电炉炼钢的主要工艺流程1.电弧炉的装料电弧炉装料时要根据炉子的规格与性能参数,配合合理的装料方案,通常按照一定比例混装生铁、废钢和铁合金,并加入适量的脱氧合金元素和渣料。
装料时要尽量均匀分布,防止料层不均匀导致炉子内部温度不均匀。
2.炉内燃烧与电弧熔炼电弧炉工作过程中,先点燃炉内燃料,形成初步熔融的金属料,然后接通电源,形成电弧加热金属料,使其完全熔化。
电弧能量直接作用在炼钢料上,既可以加热料中金属,也可以加热电炉底部和侧壁,使整个炉子的温度均匀。
3.氧气吹炼和脱氧合金元素加入在炉内形成熔池后,通过氧下吹或氧气桩等方式加入氧气进行吹炼,脱除炉内废气和不良成分,同时加入脱氧合金元素,使炉内金属达到合适的成分、温度和质量。
4.渣液处理和连铸过程最后一步是对炉内渣液进行处理,通过加入合适的矿物质进行还原、脱硅和脱氧等操作,最终得到净化的钢水。
随后将净化的钢水通过连续铸造工艺进行浇铸,成为成形的连铸坯料。
三、电炉炼钢的主要设备和工艺特点1.电弧炉电弧炉是电炉炼钢的关键设备,通过钢包、电极、电极架、转子、电子控制系统等部件组成,其优点是操作灵活、能耗低、生产周期短等。
2.电渣重熔炉电渣重熔炉是对废钢进行冶炼的主要设备,通过电渣电磁感应加热,使废钢迅速熔化。
其优点是炉内温度均匀、温度可控、冶炼环境稳定等。
3.电弧炉与LF精炼炉的联合工艺电弧炉与LF精炼炉的联合工艺是近年来发展的新工艺,通过将电炉炼钢与LF精炼技术结合起来,能够有效控制合金成分、温度和氧化物含量,提高钢水质量。
四、电炉炼钢的主要操作技术1.控制装料质量装料时要严格按照比例进行混装,控制原料质量和成分,防止过多的杂质与氧化物的夹杂。
电炉炼钢
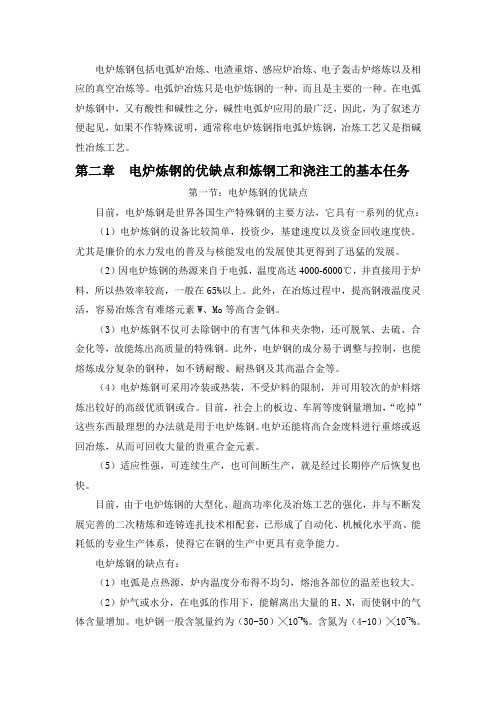
电炉炼钢包括电弧炉冶炼、电渣重熔、感应炉冶炼、电子轰击炉熔炼以及相应的真空冶炼等。
电弧炉冶炼只是电炉炼钢的一种,而且是主要的一种。
在电弧炉炼钢中,又有酸性和碱性之分,碱性电弧炉应用的最广泛,因此,为了叙述方便起见,如果不作特殊说明,通常称电炉炼钢指电弧炉炼钢,冶炼工艺又是指碱性冶炼工艺。
第二章电炉炼钢的优缺点和炼钢工和浇注工的基本任务第一节:电炉炼钢的优缺点目前,电炉炼钢是世界各国生产特殊钢的主要方法,它具有一系列的优点:(1)电炉炼钢的设备比较简单,投资少,基建速度以及资金回收速度快。
尤其是廉价的水力发电的普及与核能发电的发展使其更得到了迅猛的发展。
(2)因电炉炼钢的热源来自于电弧,温度高达4000-6000℃,并直接用于炉料,所以热效率较高,一般在65%以上。
此外,在冶炼过程中,提高钢液温度灵活,容易冶炼含有难熔元素W、Mo等高合金钢。
(3)电炉炼钢不仅可去除钢中的有害气体和夹杂物,还可脱氧、去硫、合金化等,故能炼出高质量的特殊钢。
此外,电炉钢的成分易于调整与控制,也能熔炼成分复杂的钢种,如不锈耐酸、耐热钢及其高温合金等。
(4)电炉炼钢可采用冷装或热装,不受炉料的限制,并可用较次的炉料熔炼出较好的高级优质钢或合。
目前,社会上的板边、车屑等废钢量增加,“吃掉”这些东西最理想的办法就是用于电炉炼钢。
电炉还能将高合金废料进行重熔或返回冶炼,从而可回收大量的贵重合金元素。
(5)适应性强,可连续生产,也可间断生产,就是经过长期停产后恢复也快。
目前,由于电炉炼钢的大型化、超高功率化及冶炼工艺的强化,并与不断发展完善的二次精炼和连铸连扎技术相配套,已形成了自动化、机械化水平高、能耗低的专业生产体系,使得它在钢的生产中更具有竞争能力。
电炉炼钢的缺点有:(1)电弧是点热源,炉内温度分布得不均匀,熔池各部位的温差也较大。
(2)炉气或水分,在电弧的作用下,能解离出大量的H、N,而使钢中的气体含量增加。
电炉钢一般含氢量约为(30-50)╳10-5%。
电炉炼钢操作方法
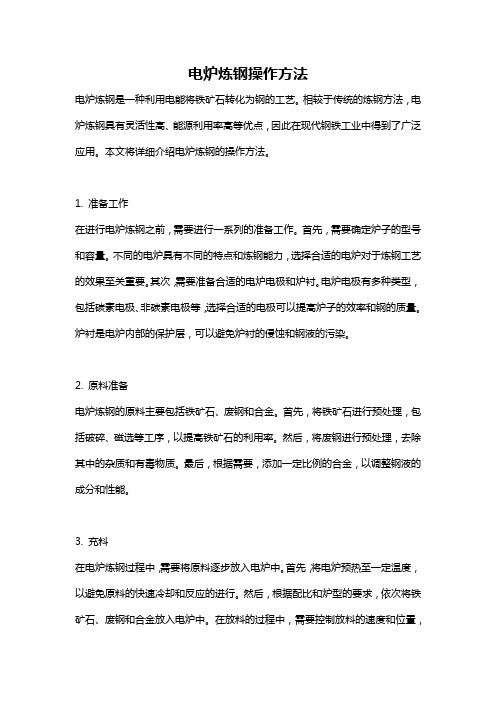
电炉炼钢操作方法电炉炼钢是一种利用电能将铁矿石转化为钢的工艺。
相较于传统的炼钢方法,电炉炼钢具有灵活性高、能源利用率高等优点,因此在现代钢铁工业中得到了广泛应用。
本文将详细介绍电炉炼钢的操作方法。
1. 准备工作在进行电炉炼钢之前,需要进行一系列的准备工作。
首先,需要确定炉子的型号和容量。
不同的电炉具有不同的特点和炼钢能力,选择合适的电炉对于炼钢工艺的效果至关重要。
其次,需要准备合适的电炉电极和炉衬。
电炉电极有多种类型,包括碳素电极、非碳素电极等,选择合适的电极可以提高炉子的效率和钢的质量。
炉衬是电炉内部的保护层,可以避免炉衬的侵蚀和钢液的污染。
2. 原料准备电炉炼钢的原料主要包括铁矿石、废钢和合金。
首先,将铁矿石进行预处理,包括破碎、磁选等工序,以提高铁矿石的利用率。
然后,将废钢进行预处理,去除其中的杂质和有毒物质。
最后,根据需要,添加一定比例的合金,以调整钢液的成分和性能。
3. 充料在电炉炼钢过程中,需要将原料逐步放入电炉中。
首先,将电炉预热至一定温度,以避免原料的快速冷却和反应的进行。
然后,根据配比和炉型的要求,依次将铁矿石、废钢和合金放入电炉中。
在放料的过程中,需要控制放料的速度和位置,避免原料的团聚和炉子的过热。
4. 炼钢过程电炉炼钢的关键步骤是炼钢过程。
炼钢分为两个阶段,即炉前期和炉后期。
在炉前期,通过适当加热和气体氧化作用,将原料中的杂质和有害物质氧化为易于移除的气体或溶解于钢液中。
同时,控制炉内的温度和压力,避免温度过高和压力过低导致的炉体的损坏。
在炉后期,主要进行还原反应和扩散作用。
通过控制电炉电极的供电和冷却,实现电炉炉内温度的控制。
同时,通过添加还原剂和合金,调整钢液的成分和温度,进一步提高钢液的质量和纯度。
在炉后期,还需要进行钢水的测温和取样,以及对炉内的温度和压力进行监测。
5. 出钢当钢液中的成分和温度达到要求时,可以进行出钢操作。
首先,停止向电炉供电,防止钢液受到过度搅拌和侵蚀。
电炉炼钢工艺流程

电炉炼钢工艺流程引言电炉炼钢是一种使用电能作为热源的钢铁生产工艺。
相比于传统的高炉炼钢工艺,电炉炼钢具有热效率高、灵活性强、环境友好等优势,因此在钢铁行业中得到了广泛应用。
本文将介绍电炉炼钢的工艺流程,对其进行详细解析。
工艺流程电炉炼钢的工艺流程主要包括以下几个步骤:1.原料准备:将所需的铁源、废钢、合金等原料进行分类、切割和称重。
2.充电与预热:将电炉充电至合适的电流和电压,并进行预热,使电炉达到工作温度。
3.加料:将经过预处理的原料加入电炉中。
根据不同钢种和产品要求,确定所需配料比例和加料时间。
加料时需要注意控制加料速度,以免引起剧烈反应。
4.加热炉温:通过通电使电流通过电极和炉料之间产生电阻加热效应,进一步提高炉内温度。
加热时需要控制加热速度和温度均匀性,避免温度过高或过低产生不良影响。
5.合金添加:根据需要,在适当的时机向电炉中加入所需的合金元素,以调节钢液成分和性能。
6.脱硫处理:在钢液中加入适量的脱硫剂,通过化学反应吸附和还原来去除钢液中的硫,以提高钢液的纯净度。
7.除渣操作:通过向电炉中加入适量的石灰、萤石等物质,使炉渣中的杂质和氧化物与其反应生成浮渣,并通过倾斜电炉或剧烈搅拌将浮渣排除。
8.温度调控:通过调节电炉的加热功率、加热时间和用气量,以及控制炉内温度均匀性,实现对钢液温度的精确调控。
9.试验取样:定期对炉内钢液进行取样,进行化学分析、显微组织观察等试验,以确保钢液质量符合要求。
10.出炉:当钢液温度和成分符合要求时,停止加热,打开电炉门,将钢液倒入铸钢包或连铸机中进行铸造。
特点与优势电炉炼钢工艺相比传统的高炉炼钢工艺具有以下特点和优势:1.灵活性强:电炉可以适应不同工艺要求和产品规格,可以生产特殊合金钢、超低碳钢等多种钢种。
2.节能环保:相比高炉工艺,电炉能源利用率更高,因为电能可以直接转化为热能,无需经过多个环节的能量转化。
同时,电炉不使用焦炭等固体燃料,减少了大量的煤炭消耗和烟气排放。
现代电炉炼钢工艺及设备

现代电炉炼钢工艺及设备
一、现代电炉炼钢工艺简介
电炉炼钢是指利用电能将固体金属原料熔化并进行精炼的冶炼方法。
与传统的高炉和转炉相比,电炉炼钢具有以下优势:
1. 能源利用率高,节能环保。
2. 生产周期短,适合小批量生产。
3. 操作灵活,易于自动化控制。
4. 可以利用废钢为原料,资源利用率高。
二、主要电炉炼钢工艺
1. 电渣炼钢
2. 等离子体电渣炼钢
3. 真空电渣炼钢
4. 电渣压力冶炼
三、电炉炼钢主要设备
1. 电弧炉
2. 精炼炉(如LF、VOD等)
3. 中间浇包
4. 连铸设备
5. 除尘、除渣等环保设备
四、电炉炼钢工艺控制及自动化
1. 电弧长度控制
2. 合金添加控制
3. 精炼过程控制
4. 连铸过程控制
5. 生产过程数据采集和管理
现代电炉炼钢工艺已日趋自动化、智能化,能够生产出高品质的特种钢材,是当今钢铁生产的重要方式。
电炉炼钢法
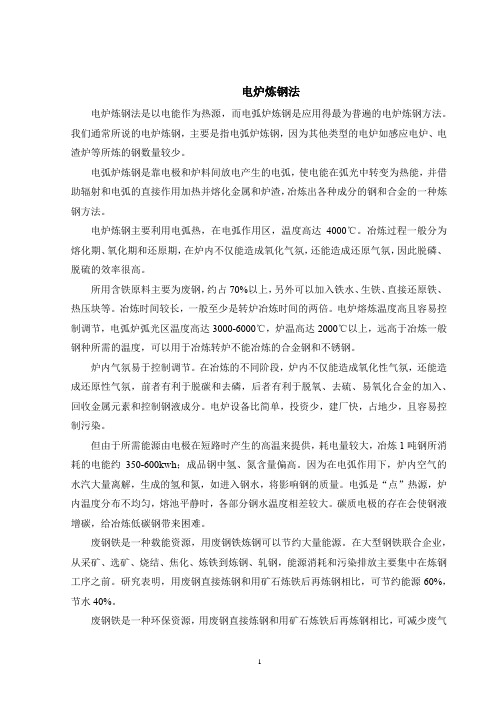
电炉炼钢法电炉炼钢法是以电能作为热源,而电弧炉炼钢是应用得最为普遍的电炉炼钢方法。
我们通常所说的电炉炼钢,主要是指电弧炉炼钢,因为其他类型的电炉如感应电炉、电渣炉等所炼的钢数量较少。
电弧炉炼钢是靠电极和炉料间放电产生的电弧,使电能在弧光中转变为热能,并借助辐射和电弧的直接作用加热并熔化金属和炉渣,冶炼出各种成分的钢和合金的一种炼钢方法。
电炉炼钢主要利用电弧热,在电弧作用区,温度高达4000℃。
冶炼过程一般分为熔化期、氧化期和还原期,在炉内不仅能造成氧化气氛,还能造成还原气氛,因此脱磷、脱硫的效率很高。
所用含铁原料主要为废钢,约占70%以上,另外可以加入铁水、生铁、直接还原铁、热压块等。
冶炼时间较长,一般至少是转炉冶炼时间的两倍。
电炉熔炼温度高且容易控制调节,电弧炉弧光区温度高达3000-6000℃,炉温高达2000℃以上,远高于冶炼一般钢种所需的温度,可以用于冶炼转炉不能冶炼的合金钢和不锈钢。
炉内气氛易于控制调节。
在冶炼的不同阶段,炉内不仅能造成氧化性气氛,还能造成还原性气氛,前者有利于脱碳和去磷,后者有利于脱氧、去硫、易氧化合金的加入、回收金属元素和控制钢液成分。
电炉设备比简单,投资少,建厂快,占地少,且容易控制污染。
但由于所需能源由电极在短路时产生的高温来提供,耗电量较大,冶炼1吨钢所消耗的电能约350-600kwh;成品钢中氢、氮含量偏高。
因为在电弧作用下,炉内空气的水汽大量离解,生成的氢和氮,如进入钢水,将影响钢的质量。
电弧是“点”热源,炉内温度分布不均匀,熔池平静时,各部分钢水温度相差较大。
碳质电极的存在会使钢液增碳,给冶炼低碳钢带来困难。
废钢铁是一种载能资源,用废钢铁炼钢可以节约大量能源。
在大型钢铁联合企业,从采矿、选矿、烧结、焦化、炼铁到炼钢、轧钢,能源消耗和污染排放主要集中在炼钢工序之前。
研究表明,用废钢直接炼钢和用矿石炼铁后再炼钢相比,可节约能源60%,节水40%。
废钢铁是一种环保资源,用废钢直接炼钢和用矿石炼铁后再炼钢相比,可减少废气186%、废水76%和废渣97%,有利于清洁生产和排废减量化。
电炉炼钢工艺

电炉炼钢工艺电炉炼钢是一种现代化的工艺,被广泛应用在钢铁制造业中。
与传统的高炉炼钢相比,电炉炼钢具有诸多优势,如能够更方便地控制钢的成分和温度,生产效率高,环境污染少等。
电炉炼钢的工艺主要包括以下几个步骤:1. 原料准备:将所需的生铁、废钢等原料按一定比例混合,并将其破碎成较小的颗粒。
同时,还需将焦炭和石灰石等辅助材料进行适量的准备。
2. 充料:将准备好的原料按一定比例倒入电炉中。
为了保证冶炼效果,一般将较好的质量原料放置在底部,而较差的原料放置在上层。
3. 熔化:通电后,电炉内产生较强的电流,这将使电炉内的电阻加热到高温,从而使原料逐渐熔化。
在熔化过程中,需要根据钢的成分要求适时地加入合适的脱硫剂和合金元素。
4. 炉渣处理:在熔化过程中,由于原料中含有一定的杂质,这些杂质将通过反应形成炉渣。
炉渣在冶炼中有着重要的作用,它能够吸附钢水中的硫、氧等有害元素,并保持炉内氧分压的平衡。
5. 温度控制:由于电炉炼钢过程中的温度较高,对于钢的成分和质量控制具有重要作用。
因此,在炉渣中加入一定量的铝和硅等元素,以保持合适的温度范围。
同时,电炉还需要配备温度传感器等设备,实时监控温度的变化。
6. 出钢:当融化的钢液达到所需的成分和温度条件时,将打开电炉底部的出钢口,将钢水倒出。
出钢的速度可以通过调节出钢口的开闭程度来控制。
总的来说,电炉炼钢是一种高效、灵活和环保的钢铁炼制工艺。
通过精确的控制和调节,可以获得高品质的钢材,并且可以适应不同规格和要求的钢铁生产。
随着技术的不断进步和优化,电炉炼钢工艺将在未来得到更广泛的应用。
电炉炼钢是21世纪钢铁产业发展的重要技术之一,它以其灵活性、高效性和环保性在钢铁生产中占据了重要的地位。
与传统的高炉炼钢相比,电炉炼钢具有许多优势,被广泛应用于不同领域,如建筑、机械制造、汽车制造等。
首先,电炉炼钢的灵活性给钢铁生产带来了极大的便利。
在电炉炼钢过程中,可以根据不同的需求和要求,调整钢水的成分和温度,以获得所需的特定钢种。
- 1、下载文档前请自行甄别文档内容的完整性,平台不提供额外的编辑、内容补充、找答案等附加服务。
- 2、"仅部分预览"的文档,不可在线预览部分如存在完整性等问题,可反馈申请退款(可完整预览的文档不适用该条件!)。
- 3、如文档侵犯您的权益,请联系客服反馈,我们会尽快为您处理(人工客服工作时间:9:00-18:30)。
9
宏观动力学
• 20世纪70年代后,炼钢反应宏观动力学研究开始活跃:
G.H.Geiger、Szekely等将化工学科的“三传”(热量、质量、
动量传递)用于分析研究冶金过程速率问题; 鞭岩、濑川清等提出了冶金反应工程学名称,引入化学反
应工程学有关反应器设计、单元操作、最优化等方法分析研
究冶金反应问题。 • 20世纪90年代后,冶金反应宏观动力学和反应工程学取得了重 要进展,有关炼钢冶炼和连铸过程流体流动、传热、反应等均 基本可以用数学模型加以描述并计算求解,反应动力学研究在 实际生产过程自动控制中也得到了广泛的采用。
7
热力学
20世纪40年代末至50年代,Schenck、Chipman等发表了大量有
关炼钢反应的平衡常数、标准自由能变化等基础数据; 20世纪60年代~80年代,E.T. Turkdogan、J.F. Elliott、松
下幸雄、不破佑、佐野信雄、水渡英昭等继续对炼钢化学反应
的平衡常数、标准自由能变化、活度、炉渣磷酸盐容量和硫酸 盐容量等进行了大量的研究和测定工作。
produced in a blast furnace(BF) or similar
process or the melting and refining of scrap and other forms of iron in a melting furnace, usually an electric arc furnace(EAF).
ton (220 metric ton) heat about every 45 minutes, the range is approximately 30 to 65 minutes. The major event times for the process are summarized below in Table 9.1.
• The basic operational
steps of the process(BOF) are shown shematically in Fig9.1.
20
Oxygen Steelmaking Processes
• The overall purpose of this process is to
18
Oxygen Steelmaking Processes
• The oxygen steelmaking process rapidly refines
a charge of molten pig iron and ambient scrap into steel of a desired carbon and temperature using high purity oxygen. • Steel is made in discrete batches called heats.
The furnace or converter is a barrel shaped,
open topped, refractory lined vessel that can rotate on a horizontal trunnion axis.
19
Oxygen Steelmaking Processes
10
交叉ห้องสมุดไป่ตู้科
炼钢学科进展还表现在冶金知识与材料、计算机、电磁、
环境等学科知识的交叉、融合和应用,如: 在氧气喷头和喷粉冶金中应用空气动力学中可压缩流体 和气相输送等知识; 在炼钢过程控制中广泛采用了声学、图像识别、专家
系统、神经元网络等方面知识;
在连铸过程采用电磁、金属压力加工等知识; 热力学、凝固等商务计算软件等。
liquid steel made from scrap and liquid hot
metal to approximately 1635℃(2975°F).
21
Oxygen Steelmaking Processes
• A typical configuration is to produce a 250
chemistry and temperature of the steel to be
tapped. Fluxes are minerals added early in the oxygen blow, to control sulfur and phosphorus and
to control erosion of the furnace refractory
20世纪80年代后,与炼钢反应有关的标准自由能变化、钢液中
组元活度相互作用系数、炉渣主要组元的活度、炉渣硫酸盐和 硫酸盐容量等大都有了较可靠的热力学数据;
8
微观动力学
• 炼钢反应动力学的研究开始得较晚,在20世纪50~60
年代,动力学方面的研究主要集中在微观动力学方面,
如化学反应级数、反应速度常数、反应活化能、多相 反应限制性环节等方面的研究;
EAF steelmaking
李岩
1
目录
• 炼钢历史 • 炼钢科学的发展
• 冶金流程图 • Overview of steelmaking processes ——Frenhan • • • • Oxygen Steelmaking Processes 电炉炼钢发展概况 电炉炼钢内容框架 Introduction of EAF
2
古代炼钢法
• 商代中期即公元前十四世纪开始使用陨铁,春秋
晚期即公元六世纪左右出现人工冶炼的铁器。 • 最初炼出的铁是用木炭加热和还原铁矿石得到的 块铁,强化鼓风和加高炉身后又炼出了生铁。 • 生铁在铸锻成器具过程中脱碳成钢是我国古代冶 金技术的特点。
3
西汉后期,生铁冶炼已达到较高水平,能够为炼钢
17
• The major element removed in OSM is carbon which is removed by oxidation to carbon
monoxide(CO).
• Other element such as silicon, phosphorous, sulfur and manganese are transferred to a slag phase. • In the EAF steelmaking process the chemical reactions are similar but generally less extensive.
fosters a speedy reaction and enables the
transfer of energy to the slag and steel bath. • Carbon, when oxidized, leaves the process in gaseous form, principally as carbon monoxide.
lining.
24
Oxygen Steelmaking Processes
• Input process variations such as analytical(hot
metal, scrap, flux and alloy) and measurement (weighing and temperature) errors contribute to
16
• Currently most all of the hot metal produced in the world is refined in an oxygen
steelmaking process(OSM).
• A small amount of hot metal is refined in open hearths, cast into pig for use in an EAF or refined in other processes.
charge materials.
25
Oxygen Steelmaking Processes
The principal elements are iron, silicon,
carbon, manganese and phosphorus, with lesser amounts of the liquid pig iron and the intense stirring provided when the oxygen jet is introduced, contribute to the
and their development——R.J. Fruehan
• For the purpose of steelmaking can be roughly defined as the refining or removal of unwanted elements or other impurities from hot metal
11
学科发展
• 在今后相当一段时间内,炼钢热力学不会再有显著
的发展,在宏观动力学和反应工程学方面还会有一 定的发展,而炼钢学科最重要的发展将会在液态钢 的凝固加工、减少排放和排放物和废弃物再回收利 用以及与信息、材料、环境等学科知识的交叉、融
合和应用方面。
12
现代炼钢流程
15
Overview of steelmaking processes
fast oxidation (burning or combustion) of
these elements and a resultant rapid, large energy release.
26
Oxygen Steelmaking Processes
• Silicon, manganese, iron and phosphorus form oxides which in combination with the fluxes, create a liquid slag. The vigorous stirring