蜂窝式低温脱硝催化剂的煅烧温度对催化性能的影响
scr脱硝催化剂参数
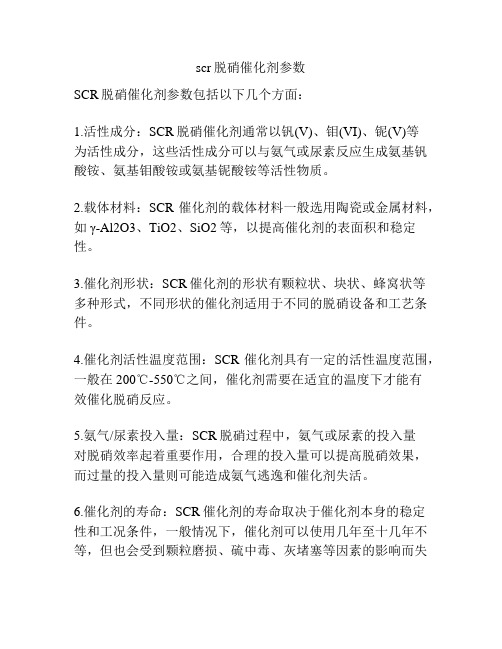
scr脱硝催化剂参数
SCR脱硝催化剂参数包括以下几个方面:
1.活性成分:SCR脱硝催化剂通常以钒(V)、钼(VI)、铌(V)等
为活性成分,这些活性成分可以与氨气或尿素反应生成氨基钒酸铵、氨基钼酸铵或氨基铌酸铵等活性物质。
2.载体材料:SCR催化剂的载体材料一般选用陶瓷或金属材料,如γ-Al2O3、TiO2、SiO2等,以提高催化剂的表面积和稳定性。
3.催化剂形状:SCR催化剂的形状有颗粒状、块状、蜂窝状等
多种形式,不同形状的催化剂适用于不同的脱硝设备和工艺条件。
4.催化剂活性温度范围:SCR催化剂具有一定的活性温度范围,一般在200℃-550℃之间,催化剂需要在适宜的温度下才能有
效催化脱硝反应。
5.氨气/尿素投入量:SCR脱硝过程中,氨气或尿素的投入量
对脱硝效率起着重要作用,合理的投入量可以提高脱硝效果,而过量的投入量则可能造成氨气逃逸和催化剂失活。
6.催化剂的寿命:SCR催化剂的寿命取决于催化剂本身的稳定
性和工况条件,一般情况下,催化剂可以使用几年至十几年不等,但也会受到颗粒磨损、硫中毒、灰堵塞等因素的影响而失
活。
因此,定期检查催化剂的状况,必要时进行清洗或更换是保持SCR脱硝系统正常运行的关键。
蜂窝状SCR催化剂应用于选择性催化还原(SCR)脱硝工艺

蜂窝状SCR催化剂应用于选择性催化还原(SCR)脱硝工艺蜂窝状SCR催化剂应用于选择性催化还原(SCR)脱硝工艺,在燃煤电厂、热电厂、燃气轮机组、垃圾焚烧、内燃机组、钢铁、石化等工业领域内起到广泛应用,适应温度从150℃至450℃。
蜂窝状催化剂是由活性组分及载体组成的匀质产品,主要由TiO2、V2O5、WO3等构成。
标准的蜂窝状催化剂的横截面(D×D)约为150mm ×150mm。
蜂窝状低温SCR催化剂蜂窝状低温脱硝催化剂配方独特、工艺新颖,SCR反应器布置灵活,适应于多种烟气工程,不受锅炉等烟气状况的影响。
特点:
1.多种原材料混炼烧制成型,整体活性高;
2.高温煅烧工艺烧成,抗瞬时高温能力强;
3.端面硬化处理,抗磨损性能强,机械寿命长;
4.脱硝效率高,氨逃逸率和二氧化硫转化率低;
5.特殊配方设计,抗中毒、抗磨损能力强;
6.具有高稳定性和耐用性;
7.体积小,比表面积大,经济性好;
8.根据实际烟气进行设计,针对性强,适用广。
蜂窝状低温SCR催化剂所选用的活性组分为无钒系列的催化剂,不会对环境造成二次污染。
催化剂呈现出较好的抗耐硫耐水性能,运行稳定,催化剂寿命可
靠,使得烟气净化流程更为合理,同时能耗降、运行成本以及一次性投资大幅降低。
玻璃炉窑和生物质发电烟气脱硝处理难点:主要是碱金属含量高,粘性大,尤其是燃料为石焦油的工况。
煅烧温度对Mo-Mn
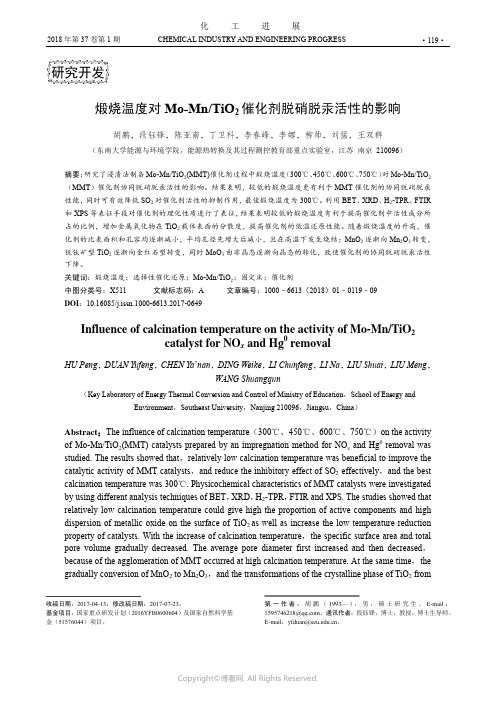
2018年第37卷第1期 CHEMICAL INDUSTRY AND ENGINEERING PROGRESS·119·化 工 进展煅烧温度对Mo-Mn/TiO 2催化剂脱硝脱汞活性的影响胡鹏,段钰锋,陈亚南,丁卫科,李春峰,李娜,柳帅,刘猛,王双群(东南大学能源与环境学院,能源热转换及其过程测控教育部重点实验室,江苏 南京 210096)摘要:研究了浸渍法制备Mo-Mn/TiO 2(MMT)催化剂过程中煅烧温度(300℃、450℃、600℃、750℃)对Mo-Mn/TiO 2(MMT )催化剂协同脱硝脱汞活性的影响。
结果表明,较低的煅烧温度更有利于MMT 催化剂的协同脱硝脱汞性能,同时可有效降低SO 2对催化剂活性的抑制作用,最佳煅烧温度为300℃。
利用BET 、XRD 、H 2-TPR 、FTIR 和XPS 等表征手段对催化剂的理化性质进行了表征,结果表明较低的煅烧温度有利于提高催化剂中活性成分所占的比例,增加金属氧化物在TiO 2载体表面的分散度,提高催化剂的低温还原性能。
随着煅烧温度的升高,催化剂的比表面积和孔容均逐渐减小,平均孔径先增大后减小,且在高温下发生烧结;MnO 2逐渐向Mn 2O 3转变,锐钛矿型TiO 2逐渐向金红石型转变,同时MoO 3由非晶态逐渐向晶态的转化,致使催化剂的协同脱硝脱汞活性 下降。
关键词:煅烧温度;选择性催化还原;Mo-Mn/TiO 2;固定床;催化剂中图分类号:X511 文献标志码:A 文章编号:1000–6613(2018)01–0119–09 DOI :10.16085/j.issn.1000-6613.2017-0649Influence of calcination temperature on the activity of Mo-Mn/TiO 2catalyst for NO x and Hg 0 removalHU Peng ,DUAN Yufeng ,CHEN Ya ’nan ,DING Weike ,LI Chunfeng ,LI Na ,LIU Shuai ,LIU Meng ,WANG Shuangqun(Key Laboratory of Energy Thermal Conversion and Control of Ministry of Education ,School of Energy andEnvironment ,Southeast University ,Nanjing 210096,Jiangsu ,China )Abstract :The influence of calcination temperature (300℃、450℃、600℃、750℃)on the activity of Mo-Mn/TiO 2(MMT) catalysts prepared by an impregnation method for NO x and Hg 0 removal was studied. The results showed that ,relatively low calcination temperature was beneficial to improve the catalytic activity of MMT catalysts ,and reduce the inhibitory effect of SO 2 effectively ,and the best calcination temperature was 300℃. Physicochemical characteristics of MMT catalysts were investigatedby using different analysis techniques of BET ,XRD ,H 2-TPR ,FTIR and XPS. The studies showed that relatively low calcination temperature could give high the proportion of active components and high dispersion of metallic oxide on the surface of TiO 2 as well as increase the low temperature reduction property of catalysts. With the increase of calcination temperature ,the specific surface area and total pore volume gradually decreased. The average pore diameter first increased and then decreased ,because of the agglomeration of MMT occurred at high calcination temperature. At the same time ,the gradually conversion of MnO 2 to Mn 2O 3,and the transformations of the crystalline phase of TiO 2 from第一作者:胡鹏(1993—),男,硕士研究生。
蜂窝式低温脱硝催化剂的煅烧温度对催化性能的影响
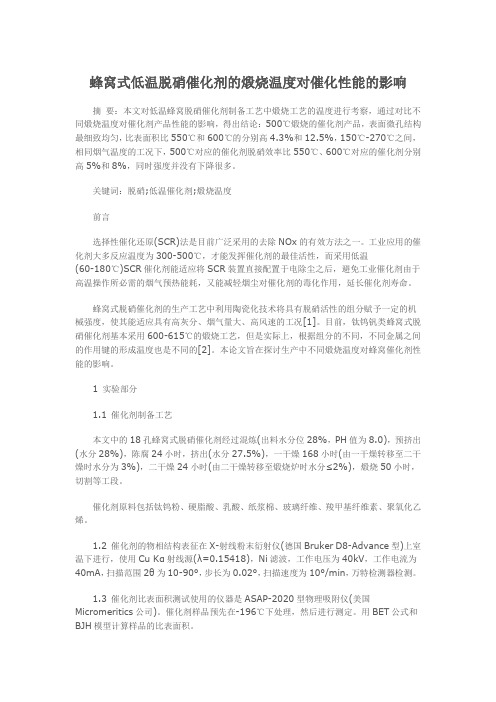
蜂窝式低温脱硝催化剂的煅烧温度对催化性能的影响摘要:本文对低温蜂窝脱硝催化剂制备工艺中煅烧工艺的温度进行考察,通过对比不同煅烧温度对催化剂产品性能的影响,得出结论:500℃煅烧的催化剂产品,表面微孔结构最细致均匀,比表面积比550℃和600℃的分别高4.3%和12.5%,150℃-270℃之间,相同烟气温度的工况下,500℃对应的催化剂脱硝效率比550℃、600℃对应的催化剂分别高5%和8%,同时强度并没有下降很多。
关键词:脱硝;低温催化剂;煅烧温度前言选择性催化还原(SCR)法是目前广泛采用的去除NOx的有效方法之一。
工业应用的催化剂大多反应温度为300-500℃,才能发挥催化剂的最佳活性,而采用低温(60-180℃)SCR催化剂能适应将SCR装置直接配置于电除尘之后,避免工业催化剂由于高温操作所必需的烟气预热能耗,又能减轻烟尘对催化剂的毒化作用,延长催化剂寿命。
蜂窝式脱硝催化剂的生产工艺中利用陶瓷化技术将具有脱硝活性的组分赋予一定的机械强度,使其能适应具有高灰分、烟气量大、高风速的工况[1]。
目前,钛钨钒类蜂窝式脱硝催化剂基本采用600-615℃的煅烧工艺,但是实际上,根据组分的不同,不同金属之间的作用键的形成温度也是不同的[2]。
本论文旨在探讨生产中不同煅烧温度对蜂窝催化剂性能的影响。
1 实验部分1.1 催化剂制备工艺本文中的18孔蜂窝式脱硝催化剂经过混炼(出料水分位28%,PH值为8.0),预挤出(水分28%),陈腐24小时,挤出(水分27.5%),一干燥168小时(由一干燥转移至二干燥时水分为3%),二干燥24小时(由二干燥转移至煅烧炉时水分≤2%),煅烧50小时,切割等工段。
催化剂原料包括钛钨粉、硬脂酸、乳酸、纸浆棉、玻璃纤维、羧甲基纤维素、聚氧化乙烯。
1.2 催化剂的物相结构表征在X-射线粉末衍射仪(德国Bruker D8-Advance型)上室温下进行,使用Cu Kα射线源(λ=0.15418),Ni滤波,工作电压为40kV,工作电流为40mA,扫描范围2θ为10-90°,步长为0.02°,扫描速度为10°/min,万特检测器检测。
蜂窝状催化剂的制备及其性能评价

孔隙率 εP
平均孔径 r/ ( nm)
76. 18 0. 188
3. 9
0. 67 0. 423 4. 94
(1) 水 催化剂粉体具有一定的水硬性 ,与水作用不能
得到塑性物料. 水只是暂时将粉体粘合在一起 ,干燥 焙烧后会重新解体 ,但水仍是成型中必不可少的助 剂 ,它可以在催化剂基本粉体表面形成液膜 ,加强粉 体间的润滑 ,在粘合剂和助挤剂的作用下改善粉体 间的结合能力 ,易于得到塑性物料. 水用量太少 ,粉 体不能被充分润湿 ,用量太大则会形成流性物料 ,而 非理想的塑性物料. 通过反复试验 ,水在捏合中分步 加入 ,用量控制在 20~30 mL/ 100 g 粉体.
以 TiO2 为主体的催化剂物料属于瘠性物料 , 具有一定的水硬性 ,与水混合易集结成团 ,无法通过 捏合得到塑性物料 ;另外基本粉体比较松散 ,无机械 强度 ,需添加粘合剂来增加粉体间的粘合力 ,提高成 型物料的机械强度 ;但因粘合剂与水作用会形成粘 性很强的胶状物 ,不能与粉体均匀混合 ,无法得到性 质均一的塑性膏体 ,成型过程中还需添加适量的助 挤剂 ;在粘合剂和助挤剂的共同作用下得到的塑性 膏体在干燥焙烧后会得到具有一定机械强度的物 料 ,但捏合挤压会造成部分催化剂孔闭塞 ,为改善成 型催化剂的孔结构 ,需添加适量的造孔剂 ;此外 ,还 需加入一定量的玻璃纤维 ,以提高催化剂的机械强 度.
?蜂窝状催化剂是以scr催化剂粉体为基体与成型助剂等通过混合捏合挤压成型干燥焙烧等过程得到由于活性成分在其中均匀分布即使催化剂表面有磨损仍可保持较强的活性所以蜂窝状催化剂在高灰和低灰情况下均可应用
第 28 卷 第 3 期 2008 年 6 月
动 力 工 程 Jo urnal of Power Engineering
脱硝反应温度
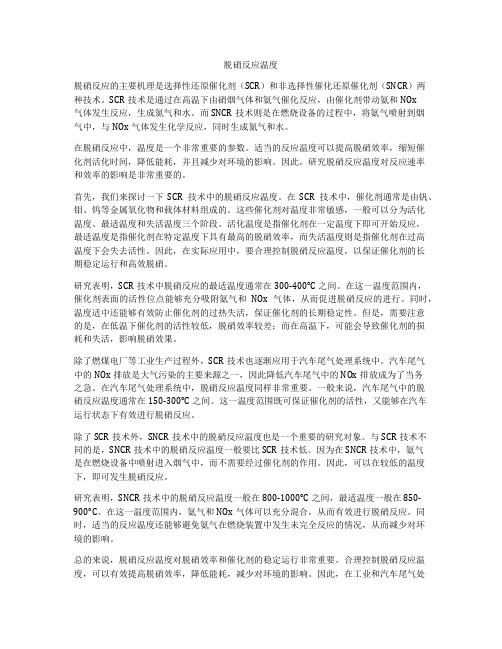
脱硝反应温度脱硝反应的主要机理是选择性还原催化剂(SCR)和非选择性催化还原催化剂(SNCR)两种技术。
SCR技术是通过在高温下由硝烟气体和氨气催化反应,由催化剂带动氨和NOx气体发生反应,生成氮气和水。
而SNCR技术则是在燃烧设备的过程中,将氨气喷射到烟气中,与NOx气体发生化学反应,同时生成氮气和水。
在脱硝反应中,温度是一个非常重要的参数。
适当的反应温度可以提高脱硝效率,缩短催化剂活化时间,降低能耗,并且减少对环境的影响。
因此,研究脱硝反应温度对反应速率和效率的影响是非常重要的。
首先,我们来探讨一下SCR技术中的脱硝反应温度。
在SCR技术中,催化剂通常是由钒、钼、钨等金属氧化物和载体材料组成的。
这些催化剂对温度非常敏感,一般可以分为活化温度、最适温度和失活温度三个阶段。
活化温度是指催化剂在一定温度下即可开始反应,最适温度是指催化剂在特定温度下具有最高的脱硝效率,而失活温度则是指催化剂在过高温度下会失去活性。
因此,在实际应用中,要合理控制脱硝反应温度,以保证催化剂的长期稳定运行和高效脱硝。
研究表明,SCR技术中脱硝反应的最适温度通常在300-400°C之间。
在这一温度范围内,催化剂表面的活性位点能够充分吸附氨气和NOx气体,从而促进脱硝反应的进行。
同时,温度适中还能够有效防止催化剂的过热失活,保证催化剂的长期稳定性。
但是,需要注意的是,在低温下催化剂的活性较低,脱硝效率较差;而在高温下,可能会导致催化剂的损耗和失活,影响脱硝效果。
除了燃煤电厂等工业生产过程外,SCR技术也逐渐应用于汽车尾气处理系统中。
汽车尾气中的NOx排放是大气污染的主要来源之一,因此降低汽车尾气中的NOx排放成为了当务之急。
在汽车尾气处理系统中,脱硝反应温度同样非常重要。
一般来说,汽车尾气中的脱硝反应温度通常在150-300°C之间。
这一温度范围既可保证催化剂的活性,又能够在汽车运行状态下有效进行脱硝反应。
脱硝催化剂热解析温度和时间
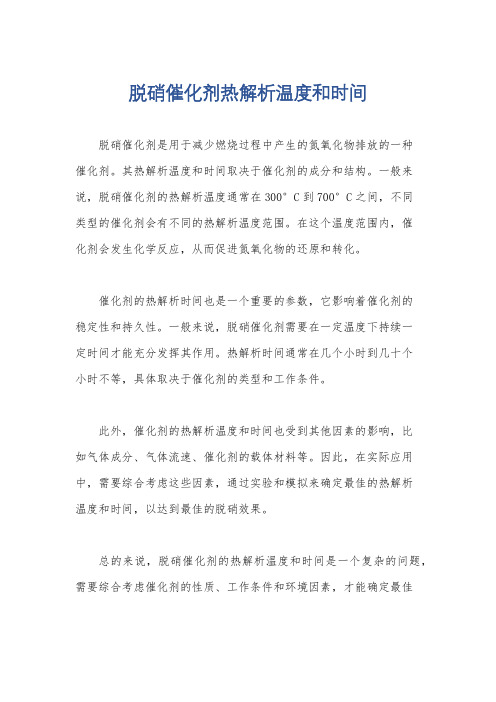
脱硝催化剂热解析温度和时间
脱硝催化剂是用于减少燃烧过程中产生的氮氧化物排放的一种
催化剂。
其热解析温度和时间取决于催化剂的成分和结构。
一般来说,脱硝催化剂的热解析温度通常在300°C到700°C之间,不同
类型的催化剂会有不同的热解析温度范围。
在这个温度范围内,催
化剂会发生化学反应,从而促进氮氧化物的还原和转化。
催化剂的热解析时间也是一个重要的参数,它影响着催化剂的
稳定性和持久性。
一般来说,脱硝催化剂需要在一定温度下持续一
定时间才能充分发挥其作用。
热解析时间通常在几个小时到几十个
小时不等,具体取决于催化剂的类型和工作条件。
此外,催化剂的热解析温度和时间也受到其他因素的影响,比
如气体成分、气体流速、催化剂的载体材料等。
因此,在实际应用中,需要综合考虑这些因素,通过实验和模拟来确定最佳的热解析
温度和时间,以达到最佳的脱硝效果。
总的来说,脱硝催化剂的热解析温度和时间是一个复杂的问题,需要综合考虑催化剂的性质、工作条件和环境因素,才能确定最佳
的参数。
在工程应用中,需要进行系统的实验和研究,以找到最适合具体情况的工作温度和时间。
焙烧温度对催化剂性能的影响

焙烧温度对催化剂性能的影响一. 焙烧温度对催化剂 Cu-Ni-Ce / S iO 2性能的影响團2 不同焙烧温度Cu NrCe/SK )2催化剂的XRD 图h 700C “ (.* 8(XJC )图2和表1是总负载量为10%的Cu-N i-Ce /SiO 2分别在600、700、800C 温度焙烧8h 得到的催化剂的XRD 图及半定量分析结果 当焙烧温度为600C 时,CuO 衍射峰的峰形较宽,峰强较弱,说 明此时CuOm 粒细小,晶体发育不完整,并且可能含有一定的非 晶成分.随着焙温度的提高,CuO 衍射峰的峰形由宽变窄,峰 强由弱变强,这说明CuO 晶粒尺寸逐渐长大,结晶逐渐趋于完 好.这和比表面积的测试结果一致(见表1).此外,由表1可知, 作为活性成分的CuO 和(Cu 0. 2 N i 0. 8 )O 随焙烧温度的升高而较 少,CeC 2量增大;可见,焙烧减小,活性可能降低,稳定性增 加。
• CuO15 25 J5 4555652&( ° )《3宛)就匚2一匕一 ¥ X叢I 培烧温度时懼化捌堵构的影响T 曲' 】tln % fjils'ia KIKII TiTnpiFliJTr 011 di rlyTiir -Htnii ufiarr 焙烧温度C ;i]O 轴含里w 打含里比表面稅“和MX>163 2m】站"图3是各催化剂表面Cu 元素的XPS 谱图.由图可知,不同焙烧温 度下制备的Cu-N i -Ce /SQ 2表面Csp 峰均比较尖锐,峰位对应的 结合能没有发生明显的变化,Cu2p3 /2峰位所对应的结合能大约 在934C 0eV,对应于CuO 勺Cu2p3 /2 XPS 谱图, 说明Cu 元素主 要是以CuO 形式存在于催化剂表面的.各焙烧温度下催化剂的 峰形均不对称,说明催化剂表面Cu 还有其它价态出现,可能就 是固溶体的存在,这与XRD 吉果一致.600 C 焙烧得到的催化剂 峰形的不对称性较大。
蜂窝状CuO/γ—A12O3催化剂表征及其烟气脱硝性能研究

t a l d e v i c e . Th e p r e p a r e d s a mp l e s we r e c h a r a c t e r i z e d b y t h e B ET s p e c i f i c s u r f a c e a r e a a n a l y z e r a n d X— r a y d i f f r a c t i o n( XRD) . Th e e f f e c t o f C u O l o a d i n g, c a l c i n e d t e mp e r a t u r e , a n d p r o mo t e r Ce O2 o n
[ 关
键
词]烟 气脱硝 ; 催化 剂 ; 蜂 窝载体 ; C u O/  ̄ , 一 A1 0。
[ 中 图分类 号]TQ4 2 6 [ 文献标 识码 ]A [ 文 章 编 号 ]1 0 0 2 — 3 3 6 4 ( 2 0 1 4 ) 0 2 — 0 0 3 0 — 0 6 [ - D OI 编 号]1 0 . 3 9 6 9 / j . i s s n . 1 0 0 2 — 3 3 6 4 . 2 0 1 4 . 0 2 . 0 3 0 S u r f a c e p r o p e r t i e s a n d f l u e g a s d e ni t r i f i c a t i o n p e r f o r ma nc e o f
h o n e y c o mb C u O/ y - Al 2 O3 c a t a l y s t s
W ANG Xu e t a o, J I AO Ye f a n, Z HUANG S h a l i , ZHANG Xi n g y u
低温烟气脱硝催化剂适用条件与动力

低温烟气脱硝催化剂适用条件与动力低温烟气脱硝催化剂是一种重要的环保材料,能有效促进烟气中NOx的催化还原,从而降低温度。
在低温脱硝方面,催化剂的适用条件和动力十分重要,它们直接影响着催化剂的脱硝效果和使用寿命。
本文将围绕这两个方面进行探讨。
一、低温烟气脱硝催化剂的适用条件1.温度适宜:通常来说,催化剂的适用温度在200℃以下,但是温度过低会影响反应速率和催化剂使用寿命,因此催化剂一般使用在120℃以上,这样既有利于反应速率,又有利于催化剂的长期使用。
2.硫氧化物浓度不高:硫氧化物是低温烟气脱硝中一个重要的干扰因素。
硫氧化物会降解催化剂的活性成分,从而降低催化剂的脱硝效果。
因此,若烟气中硫氧化物浓度过高,则需要先行进行脱硫处理,降低硫氧化物浓度,才能对其使用催化剂。
3.烟气中没有腐蚀性物质:有些烟气中含有大量的腐蚀性物质,如氯、镉、铅等等,当这些物质进入脱硝催化剂中时,会对催化剂造成损害,从而影响脱硝效果。
因此,在选择催化剂的时候,需要根据实际情况来选购适合自身的产品。
4.氧含量适合:氧在低温烟气脱硝反应中是一个必需的因素,但是氧过量会损害催化剂的活性,因此在使用催化剂的时候需要注意掌握适当的氧含量。
二、低温烟气脱硝催化剂的动力因素1.流量:烟气流量不仅直接影响着催化反应速率,同时也会影响催化剂的使用寿命。
因此,在使用催化剂的过程中,需要根据烟气中的气体组成、流量等因素确定催化剂的使用量和使用寿命。
2.空气负荷:空气负荷是指单位时间内吸入催化剂的氧气的量。
在低温烟气脱硝中,空气负荷不仅影响催化剂反应的速率,而且也直接影响着催化剂的脱硝效率和使用寿命。
3.水汽含量:水汽对低温烟气脱硝的催化反应速率以及催化剂的使用寿命都有着重要的影响。
一般来说,水汽会稀释烟气中的气体组成,从而影响催化反应速率;同时,水汽还会降低催化剂表面的活性成分,延长催化剂的使用寿命。
4.反应气体浓度:催化剂在使用的时候,反应气体的浓度也是一个至关重要的因素。
商用蜂窝式SCR脱硝催化剂产品性能分析
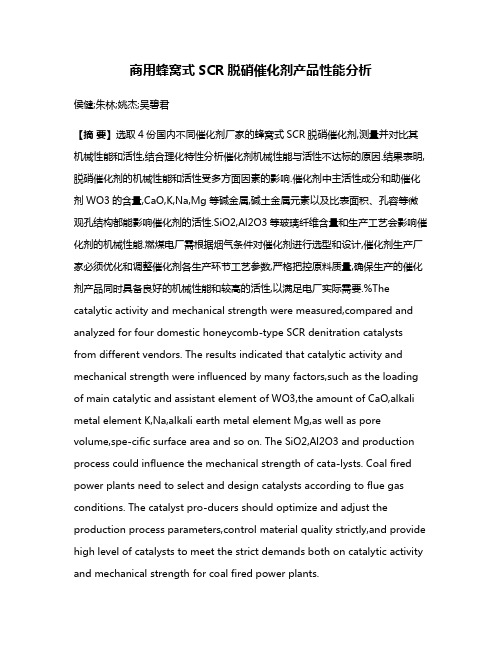
商用蜂窝式SCR脱硝催化剂产品性能分析侯健;朱林;姚杰;吴碧君【摘要】选取4份国内不同催化剂厂家的蜂窝式SCR脱硝催化剂,测量并对比其机械性能和活性,结合理化特性分析催化剂机械性能与活性不达标的原因.结果表明,脱硝催化剂的机械性能和活性受多方面因素的影响.催化剂中主活性成分和助催化剂WO3的含量,CaO,K,Na,Mg等碱金属,碱土金属元素以及比表面积、孔容等微观孔结构都能影响催化剂的活性.SiO2,Al2O3等玻璃纤维含量和生产工艺会影响催化剂的机械性能.燃煤电厂需根据烟气条件对催化剂进行选型和设计,催化剂生产厂家必须优化和调整催化剂各生产环节工艺参数,严格把控原料质量,确保生产的催化剂产品同时具备良好的机械性能和较高的活性,以满足电厂实际需要.%The catalytic activity and mechanical strength were measured,compared and analyzed for four domestic honeycomb-type SCR denitration catalysts from different vendors. The results indicated that catalytic activity and mechanical strength were influenced by many factors,such as the loading of main catalytic and assistant element of WO3,the amount of CaO,alkali metal element K,Na,alkali earth metal element Mg,as well as pore volume,spe-cific surface area and so on. The SiO2,Al2O3 and production process could influence the mechanical strength of cata-lysts. Coal fired power plants need to select and design catalysts according to flue gas conditions. The catalyst pro-ducers should optimize and adjust the production process parameters,control material quality strictly,and provide high level of catalysts to meet the strict demands both on catalytic activity and mechanical strength for coal fired power plants.【期刊名称】《工业安全与环保》【年(卷),期】2018(044)005【总页数】4页(P5-8)【关键词】SCR脱硝催化剂;蜂窝式;机械性能;活性;理化特性【作者】侯健;朱林;姚杰;吴碧君【作者单位】南京信息工程大学江苏省大气环境与装备技术协同创新中心南京210044;国电科学技术研究院南京210031;南京信息工程大学江苏省大气环境与装备技术协同创新中心南京210044;国电科学技术研究院南京210031;国电科学技术研究院南京210031;国电科学技术研究院南京210031【正文语种】中文0 引言据统计,目前绝大多数燃煤电厂都采用选择性催化还原(SCR)技术来脱除氮氧化物[1]。
焙烧温度对催化剂性能的影响

焙烧温度对催化剂性能的影响一.焙烧温度对催化剂Cu-Ni-Ce / S iO2 性能的影响图2 和表1 是总负载量为10% 的Cu-N i-Ce /SiO2分别在600、700、800℃温度焙烧8h得到的催化剂的XRD 图及半定量分析结果. 当焙烧温度为600℃时, CuO 衍射峰的峰形较宽, 峰强较弱, 说明此时CuO晶粒细小, 晶体发育不完整, 并且可能含有一定的非晶成分. 随着焙温度的提高, CuO 衍射峰的峰形由宽变窄, 峰强由弱变强, 这说明CuO 晶粒尺寸逐渐长大, 结晶逐渐趋于完好. 这和比表面积的测试结果一致(见表1). 此外, 由表1可知, 作为活性成分的CuO 和( Cu0. 2N i0. 8 )O随焙烧温度的升高而较少,CeO2量增大; 可见, 焙烧减小, 活性可能降低, 稳定性增加。
图3是各催化剂表面Cu元素的XPS谱图. 由图可知, 不同焙烧温度下制备的Cu-N i-Ce /SiO2表面Cu2p峰均比较尖锐, 峰位对应的结合能没有发生明显的变化, Cu2p3 /2峰位所对应的结合能大约在934℃0eV, 对应于CuO的Cu2p3 /2 XPS 谱图,说明Cu元素主要是以CuO 形式存在于催化剂表面的. 各焙烧温度下催化剂的峰形均不对称, 说明催化剂表面Cu还有其它价态出现, 可能就是固溶体的存在, 这与XRD结果一致. 600 ℃焙烧得到的催化剂峰形的不对称性较大。
图3 不同焙烧温度的Cu-N i-C e/SiO2催化剂表面上Cu2p的XPS图图4是各催化剂表面N i元素的XPS谱图. 由图可以看出, 不同焙烧温度下制备的催化剂, Ni2p3/2峰位所对应的结合能在854.8-855. 2eV; 与标准XPS图相对照可知, N i元素是以N i2+形式存在于催化剂表面的. 随着焙烧温度的升高, Cu-N i-C e /S iO2表面N i2p峰变得尖锐, 同时N i2p3 /2峰向高结合能方向移动, 结合能变化0. 4eV. 600 焙制得到的催化剂峰形的不对称性较大, 峰宽而强度弱, 说明催化剂表面N i还有其它价态出℃现, 可能是固溶体的存在, 这与XRD分析结果一致. 与XRD结果不同的是XPS分析得到催化剂表面有N iO存在。
低温脱硝催化剂使用温度

低温脱硝催化剂使用温度
低温脱硝催化剂是一种用于减少NOx排放的重要材料。
它通过在燃烧过程中将NOx转化为N2和H2O,使得机动车和工业生产过程中的NOx排放量大幅度下降。
然而,低温脱硝催化剂的使用温度是非常重
要的,因为它直接影响着催化剂的反应效率和寿命。
那么,低温脱硝
催化剂使用温度应该如何选择呢?
首先,我们需要了解催化剂的反应性质。
NOx主要存在于两种化合物中,分别为NO和NO2。
NO2的化学性质更加活泼,所以催化剂对NO2的反应比对NO的反应更快。
而催化剂的反应速率也随着温度的升高而升高。
因此,在选择使用温度时,我们通常会选择一个能够使
催化剂效率最大化的温度。
根据经验,低温脱硝催化剂的使用温度通常在150-450℃之间。
其中,最优的使用温度通常在200-400℃之间。
这是因为在这个温度范围内,催化剂的反应效率最高,可以将NOx转化为氮气和水的比例最大。
然而,催化剂的使用温度同时也取决于其化学成分和结构设计。
一些
催化剂需要在较低的温度下才能发挥作用,而一些催化剂则需要在较
高的温度下才能工作。
因此,在选择低温脱硝催化剂时,需要根据不
同的应用场景选择不同的催化剂类型和使用温度范围。
总之,低温脱硝催化剂的使用温度对其反应效率和寿命均具有重要作用。
最优的使用温度通常在200-400℃之间,但实际使用时需根据催化剂的化学成分和结构设计,以及场景中的NOx含量和温度范围等因素进行选择。
通过合理的催化剂选择和使用温度控制,可以有效地减少NOx的排放量,改善空气质量,保护生态环境。
蜂窝状涂覆型脱硝催化剂工艺分析

蜂窝状涂覆型脱硝催化剂工艺分析本课题采用堇青石作为基体材料,浸凃法涂覆载体涂层和负载钒钼活性组分,考察催化剂涂层黏结强度、微观形貌、催化活性等性能。
结果说明,在涂覆过程中,载体涂层吸附速率快,均约为0.5h就到达了吸附饱和,增加涂覆及浸渍次数,可显著增大载体涂层的整体负载量,但增量逐次递减。
载体涂层固化过程中,80℃的固载温度最宜,约1h负载量保持稳定。
随着近年来燃煤烟气和机动车辆尾气中NOx的大量排放,导致大气污染问题日益突出,人们环境保护意识逐渐提高,使得以NH3作为复原剂选择催化复原(NH3-SCR)大气中的氮氧化物技术成为目前一个研究热点并得到广泛应用。
蜂窝状整体挤出式催化剂已成功应用于工业烟气脱硝领域,但催化剂用量大、成本高。
此外,鉴于我国含砷的燃煤较多,需添加具有一定抗砷中毒效应的钼助剂。
催化剂中掺杂钼后,可以显著提高抗砷性,但是钼在一定程度上会降低整体式催化剂的机械强,因此市场上未见整体挤出式的钒钼钛催化剂。
整体式涂覆型催化剂较之于传统整体挤出式具有机械强度大、催化剂用量少、制备工艺简单及易于废旧再生、延长使用寿命等特点。
整体式催化剂主要由基体、涂层和活性组分构成。
由于堇青石具有良好的热稳定性、低廉的成本及良好的机械强度,成为应用广泛的基体材料,尤其在汽车工业中净化机动车尾气净化领域。
可作为整体式催化剂涂层的材料很多,最常用的主要有1.2催化剂制备将堇青石等体积浸渍于二氧化钛溶胶内,恒温20℃下浸渍50分钟后取出,将催化剂孔道内残余的胶液沥干,之后放置于80℃温度的烘箱内干燥2.5小时。
将其取出,降至室温后等体积浸渍于钒浸渍液,恒温20℃下浸渍50分钟后取出,将催化剂孔道内残余的浸渍液沥干,之后放置于80℃温度的烘箱内干燥2.5小时。
最后将制备好的催化剂降放置于马弗炉内,从室温缓慢升温至450℃,并在450℃保持5~7h。
炉冷至室温后取出称重,得到涂覆型催化剂成品。
2.结果和讨论2.1工艺优化2.1.1涂覆时间对涂覆量的影响图1 溶胶涂覆时间对载体涂层负载量的影响催化剂负载量的多少直接影响催化剂活性的高低,而负载量多少与涂覆时间长短有关。
SCR蜂窝式催化剂选择注意事项

SCR蜂窝式催化剂选择注意事项燃烧烟气中去除氮氧化物的过程,防止环境污染的重要性,已作为世界范围的问题而被尖锐地提了出来。
世界上比较主流的工艺分为:SCR和SNCR。
在SCR中使用的催化剂大多以TiO2为载体,以V2O5或V2O5-WO3或V2O5-MoO3为活性成分,制成蜂窝式、板式或波纹式三种类型。
应用于烟气脱硝中的SCR 催化剂可分为高温催化剂(345℃~590℃)、中温催化剂(260℃~380℃)和低温催化剂(80℃~300℃),不同的催化剂适宜的反应温度不同。
如果反应温度偏低,催化剂的活性会降低,导致脱硝效率下降,且如果催化剂持续在低温下运行会使催化剂发生损坏;如果反应温度过高,NH3容易被氧化,NOx生成量增加,还会引起催化剂材料的相变,使催化剂的活性退化。
SCR系统大多采用高温,反应温度区间为315℃~400℃。
SCR蜂窝式催化剂选择:催化剂类型、体积选择的主要依据是烟气量和烟气含尘量。
催化剂类型、体积选择的主要依据是烟气量和烟气含尘量。
烟气量大,所需的体积数量就大。
烟气含尘量搞,催化剂的孔径就必须大,否则就会造成堵灰现象。
如果催化剂层局部发生堵灰,其他位置的烟气流速就会相应提高。
这样就会出现催化剂严重的磨损现象。
就选择催化剂而言,关键准则是尽可能选择最小的催化剂体积(降低投资成本),最低的压降(降低运行成本)和较低的SO2/SO3的转化率(降低运行和维护费用)。
为了做出优化的解决方案,也需要对燃煤和烟气进行分析。
燃煤中SiO2含量高,就意味着飞灰对催化剂具有很大的磨蚀力。
所以,燃煤中有较高含量的SiO2尽量不使用薄壁催化剂。
燃煤中CaO含量高,很容易导致催化剂堵塞,避免此种堵塞发生的办法是选择较少孔数的催化剂。
燃煤中CaO含量高,会使引起催化剂中毒的物质大部分被飞灰吸附,也就意味着由于砷等物质带来的催化剂失效会大大减少,但部分催化剂会因为表面石膏的形成二老化。
温度对催化剂活性的影响

温度对催化剂活性的影响催化剂是化学反应中常用的一种物质,它能够在降低反应活化能的同时,不参与反应本身。
温度是催化剂活性的重要影响因素之一,在催化反应中起到至关重要的作用。
本文将就温度对催化剂活性的影响进行探讨。
一、温度对催化剂活性的作用机制及原理解析温度是分子运动的表现,提高温度会增加反应物分子的动能,加快反应速率。
对于许多催化反应来说,反应速率正比于表面反应物的浓度,而反应物在催化剂表面的浓度受催化剂表面活性位点数量的限制。
因此,温度的提高可以增加反应物在催化剂表面的吸附速率,从而提高催化剂活性。
温度对催化剂活性的影响主要有以下几个方面:1.活化能降低温度的升高可以显著降低反应物的活化能,使反应能够更容易发生。
催化剂能够通过提供额外的反应路径,降低反应物转化为产物所需的能量阈值。
催化剂提供的反应路径通常有较低的活化能,因此在催化剂存在的条件下,反应速率大大提高。
2.吸附能力增强温度的升高会增加催化剂表面的能量,使得反应物在催化剂表面吸附的能力增强。
吸附是催化剂参与反应的第一步,通过吸附能力的增加,反应物更容易与催化剂发生接触,从而增加反应速率。
3.反应速率提高在催化反应中,反应速率与反应物浓度有关。
温度的提高可以加快反应物的扩散速率,使反应物更快地接触到催化剂表面,并增加在催化剂上的吸附速率。
因此,提高温度可以明显增加催化剂活性。
4.平衡位置偏移某些催化反应是可逆反应,提高温度可以改变反应平衡位置,使反应向产物方向偏移。
温度升高会导致平衡常数的变化,使产物生成速率增加。
催化剂在这种情况下可以加快平衡位置的偏移,增加产物的生成。
二、温度对催化剂活性的实际应用温度对催化剂活性的影响在各类催化反应中得到了广泛应用。
以下是几个实际应用的例子:1.催化裂化反应催化裂化反应是石油工业中常见的一种反应,通过在高温下使用催化剂将重质石油原料转化为轻质产品。
高温能够提供足够的能量,使得催化剂能够降低重质烃分子的活化能,加快反应速率,提高反应效率。
- 1、下载文档前请自行甄别文档内容的完整性,平台不提供额外的编辑、内容补充、找答案等附加服务。
- 2、"仅部分预览"的文档,不可在线预览部分如存在完整性等问题,可反馈申请退款(可完整预览的文档不适用该条件!)。
- 3、如文档侵犯您的权益,请联系客服反馈,我们会尽快为您处理(人工客服工作时间:9:00-18:30)。
蜂窝式低温脱硝催化剂的煅烧温度对催化性能的影响
摘要:本文对低温蜂窝脱硝催化剂制备工艺中煅烧工艺的温度进行考察,通过对比不同煅烧温度对催化剂产品性能的影响,得出结论:500℃煅烧的催化剂产品,表面微孔结构最细致均匀,比表面积比550℃和600℃的分别高4.3%和12.5%,150℃-270℃之间,相同烟气温度的工况下,500℃对应的催化剂脱硝效率比550℃、600℃对应的催化剂分别高5%和8%,同时强度并没有下降很多。
关键词:脱硝;低温催化剂;煅烧温度
前言
选择性催化还原(SCR)法是目前广泛采用的去除NOx的有效方法之一。
工业应用的催化剂大多反应温度为300-500℃,才能发挥催化剂的最佳活性,而采用低温
(60-180℃)SCR催化剂能适应将SCR装置直接配置于电除尘之后,避免工业催化剂由于高温操作所必需的烟气预热能耗,又能减轻烟尘对催化剂的毒化作用,延长催化剂寿命。
蜂窝式脱硝催化剂的生产工艺中利用陶瓷化技术将具有脱硝活性的组分赋予一定的机械强度,使其能适应具有高灰分、烟气量大、高风速的工况[1]。
目前,钛钨钒类蜂窝式脱硝催化剂基本采用600-615℃的煅烧工艺,但是实际上,根据组分的不同,不同金属之间的作用键的形成温度也是不同的[2]。
本论文旨在探讨生产中不同煅烧温度对蜂窝催化剂性能的影响。
1 实验部分
1.1 催化剂制备工艺
本文中的18孔蜂窝式脱硝催化剂经过混炼(出料水分位28%,PH值为8.0),预挤出(水分28%),陈腐24小时,挤出(水分27.5%),一干燥168小时(由一干燥转移至二干燥时水分为3%),二干燥24小时(由二干燥转移至煅烧炉时水分≤2%),煅烧50小时,切割等工段。
催化剂原料包括钛钨粉、硬脂酸、乳酸、纸浆棉、玻璃纤维、羧甲基纤维素、聚氧化乙烯。
1.2 催化剂的物相结构表征在X-射线粉末衍射仪(德国Bruker D8-Advance型)上室温下进行,使用Cu Kα射线源(λ=0.15418),Ni滤波,工作电压为40kV,工作电流为40mA,扫描范围2θ为10-90°,步长为0.02°,扫描速度为10°/min,万特检测器检测。
1.3 催化剂比表面积测试使用的仪器是ASAP-2020型物理吸附仪(美国Micromeritics公司)。
催化剂样品预先在-196℃下处理,然后进行测定。
用BET公式和BJH模型计算样品的比表面积。
1.4 催化剂轴向和径向强度测试用的是QJ212C-100KN电子万能实验机(上海倾技仪器仪表有限公司),测试时催化剂需要切割成15cm*15cm*15cm。
1.5 催化剂脱硝实验
将成品15*15cm的催化剂切割成3.5*3.5cm的小块,SCR脱硝效率评价实验装置见图1。
将3.5*3.5cm的蜂窝催化剂填入SCR反应器中。
模拟电厂烟气成分体积分数含量:NO是670ppm、NH3是610ppm、O2是6.2%、SO2是100-160ppm、水是3%、平衡气体为99.999%高纯氮,烟气流量是1260ml.min-1,模拟烟气中的O2、NO、SO2等指标采用德国MRU公司的Vario Plus型烟气分析仪在线测量,利用TESTO350烟气分析仪对反应装置入口和出口处烟气的NO浓度进行分析。
脱硝效率计算公式:
2 实验结果比较
从图2中XRD的表征可以看出,500℃煅烧的催化剂没有WO3的峰,V2O3的峰很小,这是由于含量小的WO3和V2O3分散很均匀;而550℃和600℃煅烧出来的催化剂表面WO3和V2O3的峰很尖锐,说明在长时间高温下,WO3和V2O3发生了烧结团聚,晶粒变大导致的。
此结论与图3中的扫描电镜是吻合的。
由图3可以看出,500℃对应的催化剂具有更好的表面孔结构,微孔细致,分布均匀,550℃对应的催化剂表面局部有少量的团聚,而600℃煅烧的催化剂表面团聚更严重。
这种现象可能是由于500℃时,Ti 和W 以及V 和W 之间金属键作用已经形成,而且长时间的煅烧恰好将造孔剂燃烧挥发完全,再升高温度不仅会导致二氧化钛由锐钛型转向金红石型,导致比表面积的下降,也会造成钨等金属元素的烧结团聚,进而导致活性下降。
[3-4]
从比表面积也可以看出,500℃对应的催化剂比表面积比550℃和600℃的分别高4.3%和12.5%,虽然500℃对应的催化剂比表面积最大,但是三者相差很小。
说明500-600℃之间,温度对催化剂物理特性影响很小。
图4是不同煅烧温度的催化剂活性对比图,从前面XRD测试、比表面测试、扫描电镜结果可以看出500℃煅烧的催化剂具有更好的物理结构,在脱销活性评价中也得到了验证,500℃煅烧的催化剂具有最好的催化活性,烧结现象最严重的是600℃煅烧的催化剂,当然,其催化活性也是最差的。
500℃煅烧的催化剂脱硝效率比550℃、600℃对应的催化剂分别高5%、8%。
3 总结
本文中通过对比得出,500℃煅烧的催化剂产品,表面微孔结构更细致均匀,比表面积比550℃和600℃的分别高4.3%和12.5%,可以达到72m2/g。
150℃-270℃之间,相同烟气温度的工况下,500℃煅烧的催化剂脱硝效率比550℃、600℃对应的催化剂分别高5%、8%,且500℃对应的催化剂强力并未减少很多。
此论文中的结果可以对实际生产起到指导意义。