人为操作失误如何做8D报告
8D报告填写及手法运用

第七页,共65页。
8D报告(bàogào)填写
何谓(héwèi) 〝5W
2H〞 ?
1W --- who
谁
2W --- when
何时
3W --- where 何地
4W --- what
什么(shén me)
5W --- why me)
为什么(shén
1H --- How
怎样
2H --- How many 多少
第三十四页,共65页。
8D报告(bàogào)填写
D5:暂时(zànshí)改善对 策
采取适当举动使效果中止及不良不再发作 修正或取缔效果的根源(gēnyuán) 经过修正制程使进程再次遭到控制
第三十五页,共65页。
8D报告(bàogào)填写
进程措施(cuòshī)目的在于依次減少严重水平、 发作频度与检测水平等級。应思索以下类型的措施(cuòshī):
2答: 由于局部晶片在边缘,拿放时碰倒弧线 。
3问: 为什么会碰倒弧线?
3答: 由于依照惯例要求去取放PCB。
4问: 为什么按惯例要求去取放PCB?
4答: 由于并未在文件中明白取放要求 。
5问: 为什么未明白要求在技术文件中?
5答: 由于文件按惯例要求编制 。
由上可见,经常运用问5次为什么,就可以确认出效果的缘由 以及采取对策.
D3:暂时(zànshí)措施 〔1〕
围堵(wéi dǔ)/隔离效果 采取即时举动或应变对策控制效果影响范围 跟进客户或后序质量、消费要求 对不良品中止剖析并追溯到相关工序或集团 对异常隐患批次在制品或库存中止流转或外发(如有
需求) 清算仓库、工厂及现场中的不良品或可疑产品
第十六页,共65页。
手把手教你写客户满意的人为操作失误8D报告

手把手教你写客户满意的人为操作失误8D报告摘要:在商业领域,客户满意度是企业成功的关键因素之一、人为操作失误是客户满意度下降的主要原因之一、本报告将分享一些有效的方法,帮助企业避免人为操作失误,提升客户满意度。
报告内容包括:对人为操作失误的定义和影响、常见的人为操作失误、避免人为操作失误的措施等。
第一部分:引言(100字)客户满意度是企业生存和发展的核心。
然而,让客户满意并不容易,人为操作失误往往是导致客户满意度下降的重要原因之一、本报告将介绍人为操作失误的定义和影响,以及避免人为操作失误的措施,以帮助企业提升客户满意度。
第二部分:人为操作失误的定义和影响(200字)人为操作失误指的是由人员的不当行为或疏忽引起的错误。
这些错误可能包括不正确的操作流程、不准确的信息处理、延误的响应时间等。
人为操作失误对企业的影响不容小觑,它可能导致客户的不满、失去信任以及最终的流失。
因此,减少人为操作失误对于企业来说至关重要。
第三部分:常见的人为操作失误(300字)在客户服务过程中,常见的人为操作失误有很多,包括以下几个方面:1.信息处理错误:员工可能因疏忽处理客户的信息,导致错漏。
2.响应时间延误:员工响应客户请求的时间过长,给客户造成不良印象。
3.服务态度不佳:员工对客户的态度冷淡,缺乏热情和友善。
4.错误的解决办法:员工处理客户问题时,未选择合适的解决方案。
5.信息传递不清:员工之间沟通不畅,导致客户的问题无法及时解决。
第四部分:避免人为操作失误的措施(400字)为了避免人为操作失误,企业可以采取以下措施:1.培训与教育:通过培训员工掌握正确的操作流程和技能,提高他们的专业水平和处理能力。
2.建立明确的规章制度:制定明确的规章制度,明确员工的工作职责和行为准则。
3.引入技术支持:使用先进的技术工具和系统来协助员工处理客户的问题,减少人为操作失误的概率。
4.激励机制:建立激励机制,通过奖励和赞扬来鼓励员工积极向上,提高服务质量。
因产品漏装8d报告

因产品漏装8d报告1. 引言本报告旨在对公司最近发生的产品漏装问题进行分析,并提出相应的8D处理方案。
通过对该问题的深入分析和解决方案的实施,旨在改进公司的生产流程,提高产品质量,减少类似问题的再次发生。
2. 问题描述近期公司出现了产品漏装的问题。
漏装现象主要集中在产品装配的最后一个环节,致使部分产品出厂前未完成最后一个工序的装配工作。
问题主要出现在A产品线上,且已经影响了一批次的产品质量。
3. 问题分析经过仔细的调查和分析,我们发现以下原因可能导致了产品漏装问题:3.1 人为疏忽在产品装配过程中,操作人员可能出现了疏忽,未将产品按照规定的程序进行装配,或者未及时检查和确认产品装配工作。
3.2 工序指导不完善产品装配过程中缺乏明确的工序指导,导致操作人员对于最后一个工序的重要性认识不足,从而忽略了该环节的操作。
3.3 产线管理不到位对于产品装配的每一个环节,产线管理人员未能及时进行跟踪和监督,导致问题未能及时发现和纠正。
4. 解决方案针对以上问题,我们提出以下解决方案,并进行8D处理。
4.1 D1:建立问题解决团队成立由相关部门负责人和专业技术人员组成的解决团队,以确保问题得到全面和专业的解决。
4.2 D2:明确问题规模和损失对目前产品漏装问题的具体规模进行分析,估计已经造成的经济损失,并确定解决问题的紧急性和重要性。
4.3 D3:分析问题根本原因对产品漏装问题进行详细的分析和追溯,确定问题的根本原因,包括人为因素、工序指导和产线管理等。
4.4 D4:制定纠正措施针对问题的根本原因,制定相应的纠正措施。
包括进行员工培训,明确操作规程和标准,加强产线管理等。
4.5 D5:执行并验证纠正措施在实施纠正措施的同时,对措施的有效性进行验证,并及时调整和优化。
4.6 D6:预防措施在解决当前问题的同时,对类似问题的再次发生进行预防。
建立完善的产品装配工序指导和质量检查机制,加强产线管理,通过提高员工意识和技能培训,预防问题的发生。
喷漆产品划伤8d报告
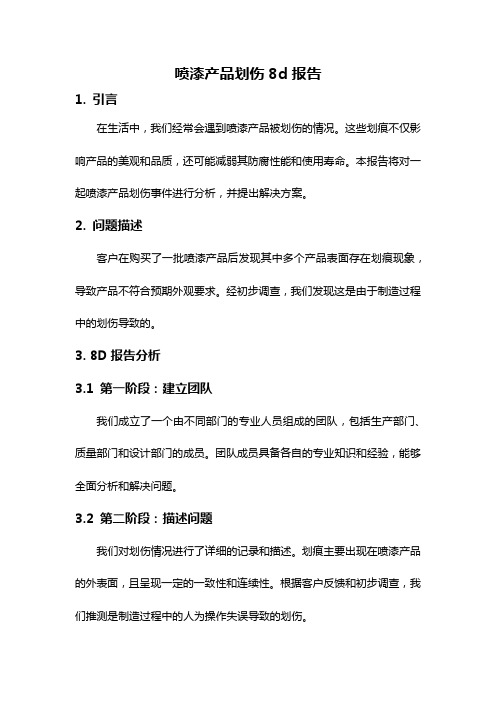
喷漆产品划伤8d报告1. 引言在生活中,我们经常会遇到喷漆产品被划伤的情况。
这些划痕不仅影响产品的美观和品质,还可能减弱其防腐性能和使用寿命。
本报告将对一起喷漆产品划伤事件进行分析,并提出解决方案。
2. 问题描述客户在购买了一批喷漆产品后发现其中多个产品表面存在划痕现象,导致产品不符合预期外观要求。
经初步调查,我们发现这是由于制造过程中的划伤导致的。
3. 8D报告分析3.1 第一阶段:建立团队我们成立了一个由不同部门的专业人员组成的团队,包括生产部门、质量部门和设计部门的成员。
团队成员具备各自的专业知识和经验,能够全面分析和解决问题。
3.2 第二阶段:描述问题我们对划伤情况进行了详细的记录和描述。
划痕主要出现在喷漆产品的外表面,且呈现一定的一致性和连续性。
根据客户反馈和初步调查,我们推测是制造过程中的人为操作失误导致的划伤。
3.3 第三阶段:短期控制措施为了避免进一步损失,我们立即采取短期控制措施。
首先,我们加强了制造过程的监督和检验,确保产品在制造过程中不再被划伤。
其次,我们对已经出货的产品进行了严格的质检,将有划痕的产品从市场中进行召回并进行修复。
3.4 第四阶段:根本原因分析为了解决问题并防止再次出现,我们进行了根本原因分析。
通过对制造过程的流程图和操作纪录的仔细审查,我们发现划伤主要是由于操作人员在搬运和装配产品时的不慎造成的。
他们没有按照规定的操作程序进行操作,导致产品被划伤。
3.5 第五阶段:纠正措施为了解决问题,我们采取以下纠正措施:- 对制造过程中的操作程序进行整理和优化,制定明确的操作规程,并加强对操作人员的培训和监督,以确保操作规程的正确执行。
- 调整了产品的搬运和装配流程,增加了相应的保护措施,避免产品在搬运和装配过程中被划伤。
3.6 第六阶段:长期措施为了确保问题从根本上解决,我们采取以下长期措施:- 建立质量管理体系,包括明确的质量标准和流程,以及相应的质量检验和监控措施,确保产品质量符合要求。
手把手教你写客户满意的人为操作失误D分析报告

其实首先我也想说,不仅是你的客户不喜欢这样的8D报告,我也不喜欢人家写整改措施动不动就写“操作工质量意识不强,加强培训”,“处罚当事人300块”等等.我在企业做质量负责人的时候,无论是我的供应商还是内部生产工程除了类似的问题,如果我SQE或过程质量工程师把这样的改进报告交给我,必然会得到我的一顿狠批.因为把质量问题的责任推卸给操作工,要么是不负责任的应付,要么就是不懂质量管理.因为在我的工作经历中,我所接触到的操作工,大多都是很朴实的工人.确实有刁钻耍滑的,但是少之又少.所以上述例子中的问题,无不可以从管理制度和方法上查找原因.首先说说外观缺陷一般说来,外观缺陷都是需要百分之百目测检验的,确实容易造成漏检的情况.但是还是可以从下面几个方面去查找原因和制定改进措施的.——外观检验标准是否具体、是否清晰、是否和顾客达成了一致.有些企业的外观标准上仅简单写了“无飞边毛刺、无磕碰伤”.但是在现场操作时,操作工和生产管理人员又认为“无磕碰伤是不可能的”,因而就按照自己的理解去掌握一个模糊的标准.规范的做法是,把产品按照功能面,逐一根据可能的缺陷确定可以接受的标准和不能接受的标准.然后以图文并茂的形式描述清楚.标准应清晰、易懂、没有歧义,而且是现实可行的.杜绝模糊的“外观标准参见限度样件”.如果有限度样件,也要有文字说明,限度样件是哪个方面哪个缺陷的限度样件,是缺陷样件还是合格样件,缺陷和合格的判定条件是什么,一定要说明清楚.——外观标准是否已经清晰、明确地培训传达到员工.杜绝笼统地说培训不到位,而仅仅就事论事在这个缺陷上培训这个员工,而同类的事情下次在另一个工位就另外一个问题又可能重复发生.如果是员工培训方面整改,一定从培训方法、培训流程、培训后考核方法、新员工上岗初期的互检和师傅陪伴等角度,在工作方法上和流程制度上找原因,加以整改,杜绝下次类似的事情发生.例如针对外观缺陷的培训,除了给新员工讲解外观标准或作业指导书,还应该结合大量的缺陷实物样件进行培训,让新员工做些缺陷判断的练习.在员工上岗初期,在标准界限附近的零件要请师傅或质量人员帮忙判断.要建立关键岗位管理和顶岗人员培训制度,杜绝新员工临时培训匆忙上岗.——岗位工作策划是否合理.例如有外观检验要求的工位的光源的光照度是否合适外观检验工作台的高度是否合适工件翻动和作业观察员工外观检验的观察作业的次序是否有策划并固化下来了也就是说,员工检验零件外观时,眼睛要看到哪几个面哪几个点,工件翻转次序和眼睛的行走路径是否是固定的外观检验和生产操作是否能够在限定的节拍内完成——常出现的外观缺陷是否张贴了质量警示卡,提醒员工特别注意——最后,也是最重要的,是否在源头上查找原因,致力于减少和杜绝外观缺陷例如针对磕碰伤问题,流水线上的产品运输辊道是否会磕碰零件产品和产品之间是否会发生磕碰物流周转工装是否合理是否存在工件堆叠员工操作过程、工件摆放过程是否存在磕碰风险第二个问题,标签贴错标签贴错在很多主机厂客户来说,也是一个很严重的问题.在有些客户那里如果发生标签贴错两次就可能直接导致受控发运.标签贴错可以从如下几个角度考虑改进.——现场打印,随用随打印,禁止事先打印标签.一般来说要求严格的主机厂会要求供应商在生产线的包装工位设置标签打印机.如果企业有多条生产线就应该在每条线边的下线包装工位设置独立的标签打印机.杜绝在办公室里打印了一堆的标签.有些企业有各种不同产品的,也可能有不同批次的,喜欢在办公室统一打印一堆标签,然后一堆标签拿到生产线边,包装时再从一堆标签里翻找出来贴上.或者先包装后,很多的包装箱堆叠在一起,然后一起贴标签.甚至有的企业在包装后放置几天,发运前再贴标签.这些不正确的做法,不出现问题才是不正常的.——如果客户没有独立打印机的明确要求,而且企业一时还不能做到独立标签打印机,也可以采用换型防错的方法来保证标签正确.换型防错的方法,我以后有机会再单独写文章介绍.简单地说,就是在多种产品共线生产的情况下,当准备切换加工某一种型号产品时,把原材料、产成品、半成品、工装、刀具、工具、辅具、各种作业指导书、各种记录表、包装材料,包括设备里面调用的程序和工艺参数,当然也包括标签,统统切换成准备生产的产品型号相一致的.而不一致的,确保从生产线上,从操作者可以拿到的范围内撤离或者封盖起来.使得误拿误用成为不可能,这就叫换型防错.在换型时,操作工利用换型防错点检表点检并记录所有的软硬件的切换得到了落实,班组长互检.第三个,数量短缺问题我也不赞同增加人员互检,因为效率很低.那么除了采用计数器之外,还可以从如下角度考虑改进:——如果是规则的产品,应该整齐摆放.一个包装盒或者一个料箱固定几排几列几层,这样点检数量就转换成了对排列形状的外观检查,数量确认就变得很直观.——如果同时在防护磕碰、挤压方面有要求,那就考虑定制成型吸塑盒、或带有分隔板的料盒来摆放产品,一个萝卜一个坑.坑没填满,缺件了,就是数量不够.——称重法.但是在零件数量很多,每个件的重量又在一定范围内波动时,就可能导致称重判定数量时的不准确.这时可以考虑在大包装内设置若干的小包装,而小包装的数量设置要考虑到总重量的波动范围的西格玛小于一个零件重量的六分之一.第四个问题,漏加工除了设置连续的生产线,设置过程防错之外,还可以从以下方面考虑改进:——增加自检和互检,在每道序放行之前,操作者检验自行检验本道序加工的内容是否完成,检验后放行或者再放入料架料盒.下道序在加工前检验上道序的加工或装配内容是否完成.——定置管理,定位存放.如果是单机作业,每个单机工位待加工件和已加工件一定要分开摆放,定置摆放.一般地,左手边是待加工件,右手边是已加工件.严禁混放,严禁待加工已加工件放置在同一料架或料盒.在在制品周转区,整料箱的在制品也要各个不同工序状态的产品分区摆放,且做好明显标识.——悬挂工序随行卡.针对单机作业的生产线,料架或料车要悬挂随行卡,在随行卡上标明工序状态.第五个问题,发错料最常见的错误是一个大包装多数正确的产品里面混进来一两只不同型号的产品.一般是由下列原因造成的,把这些方面改掉了,也就基本杜绝了混料问题.——针对这样的问题,最基本原因就是没有做好换型防错.在生产工位、在生产线边存在不同型号的产成品、在制品同时存在的现象.——或者在包装区、检验区,不同型号的产品同时存在,散放、混放.所以定置管理、5S,还是最基本的要求,不是简单的干净整齐的而已.除上述问题之外,还有一个被供应商常常使用的原因,就是“调试件被混在了合格件里报交”.这也是被我和很多主机厂的SQE们所深恶痛绝的一个说法.我们常常会追问,你怎么确定那个件就是调试件的零件上有追溯号吗调试件的检验记录和追溯号相对应吗即使真的是调试件被混入合格品的话,企业也需要在不合格品定置摆放和标识、调试品定置摆放和标识、开机前检查确认、首件确认,等几个方面的管理方法加以原因分析和改进.而不是简单地归结为认为操作失误.看完本文有任何观点想法,都可以在下方留言区畅所欲言延伸阅读:8D详解,工程师都要看8D的原名叫做8Eight-Disciplines,意思是8个人人皆知解决问题的固定步骤;也可以称为TOPSTeamOrientedproblemsolving即团队导向问题解决方法.8D主要用于汽车及类似加工行业的问题解决方法.原始是由Ford公司,全球化品质管制及改善的特殊必备方法,之后已成为QS9000/ISOTS16949、福特公司的特殊要求.8D是解决问题的8条基本准则或称8个工作步骤,但在实际应用中却有9个步骤:D0:征兆紧急反应措施D1:小组成立D2:问题说明D3:实施并验证临时措施D4:确定并验证根本原因D5:选择和验证永久纠正措施D6:实施永久纠正措施D7:预防再发生D8:小组祝贺SQE在给供应商做8D报告的培训的时候,必须跟供应商讲清楚,作为供应商在撰写8D报告的时候,务必要保证下面的问题被清楚准确有理有据地回答:D2-问题是什么D3~D6-问题如何解决D7-将来该问题如何预防然而作为SQE在审阅供应商的8D报告的时候,也务必保证以下的问题被如实回答:1.对零件的知识进行了充分的论证2.完全确定了根本原因并聚焦于该原因3.遗漏点已经被识别4.确定与根本相匹配的纠正措施5.纠正措施计划的验证已经被确定6.包括了实施纠正措施的时间计划7.有证据显示供方将把纠正措施纳入整个系统.8D的实施过程可能用到的质量工具总结如下:可靠性/设计验证DV/产品和过程确认/潜在失效模式及后果分析FMEA/控制计划CP/PPAP文件/SPC/DOE/QC7大工具D0:征兆紧急反应措施目的:主要是为了看此类问题是否需要用8D来解决,如果问题太小,或是不适合用8D来解决的问题,例如价格,经费等等,这一步是针对问题发生时候的紧急反应.关键要点:判断问题的类型、大小、范畴等等.与D3不同,D0是针对问题发生的反应,而D3是针对产品或服务问题本身的暂时应对措施.工具:趋势图/排列图/Paynter佩恩特图/ERA紧急反应措施D1:小组成立目的:成立一个小组,小组成员具备工艺/产品的知识,有配给的时间并授予了权限,同时应具有所要求的能解决问题和实施纠正措施的技术素质.小组必须有一个指导和小组长.关键要点:成员资格,具备工艺、产品的知识;目标;分工;程序;小组建设.工具:行动计划、时间管理、团队宪章、GanttChartPilotD2:问题说明目的:用量化的术语详细说明与该问题有关的内/外部顾客抱怨,如什么、地点、时间、程度、频率等.“什么东西出了什么问题”关键要点:收集和组织所有有关数据以说明问题;问题说明是所描述问题的特别有用的数据的总结;审核现有数据,识别问题、确定范围;细分问题,将复杂问题细分为单个问题;问题定义,找到和顾客所确认问题一致的说明,“什么东西出了什么问题”,而原因又未知风险等级.工具:质量风险评定,FMEA分析,5W2HWhat/Why/When/Where/Who/How/Howmany、折线图、直方图、排列图D3:实施并验证临时措施目的:保证在永久纠正措施实施前,将问题与内外部顾客隔离.原为唯一可选步骤,但发展至今都需采用关键要点:评价紧急响应措施;找出和选择最佳“临时抑制措施”;决策;实施,并作好记录;验证DOE、PPM分析、控制图等工具:方法:FMEA、DOE、PPM、SPC、检查表、记录表PDCAD4:确定并验证根本原因目的:用统计工具列出可以用来解释问题起因的所有潜在原因,将问题说明中提到的造成偏差的一系列事件或环境或原因相互隔离测试并确定产生问题的根本原因.关键要点:评估可能原因列表中的每一个原因;原因可否使问题排除;验证;控制计划工具:FMEA、PPM、DOE、鱼骨图、头脑风暴&关联图、5why法、稳健设计D5:选择并验证永久纠正措施目的:在生产前测试方案,并对方案进行评审以确定所选的校正措施能够解决客户问题,同时对其它过程不会有不良影响.关键要点:重新审视小组成员资格;决策,选择最佳措施;重新评估临时措施,如必要重新选择;验证;管理层承诺执行永久纠正措施;控制计划.工具:FMEA、设计验证和报告DVP&R、因果图、稳健设计、检查表、记录表D6:实施永久纠正措施目的:制定一个实施永久措施的计划,确定过程控制方法并纳入文件,以确保根本原因的消除.在生产中应用该措施时应监督其长期效果.关键要点:重新审视小组成员;执行永久纠正措施,废除临时措施;利用故障的可测量性确认故障已经排除;控制计划、工艺文件修改.工具::FMEA、防错、SPC、PPAPD7:预防再发生目的:修改现有的管理系统、操作系统、工作惯例、设计与规程以防止这一问题与所有类似问题重复发生.关键要点:选择预防措施;验证有效性;决策;组织、人员、设备、环境、材料、文件重新确定.工具:FMEA、控制计划CP、过程流程图Flow-chartD8:小组祝贺目的:承认小组的集体努力,对小组工作进行总结并祝贺.关键要点:有选择的保留重要文档;流览小组工作,将心得形成文件;了解小组对解决问题的集体力量,及对解决问题作出的贡献;必要的物质、精神奖励.。
8D报告解说及范例

工程问题 某产品为何浮高不良那么多 为何少锡会在J2之pin2&6
生产问题 为何会贴错Barcode 为何客户发现混料
检测问题 为何100%Q1测试不良 为何测试ok之产品重测
4
壹. 问题篇
问题的特性
问题的特性
问题的大小
• 必要时可用二个主题以上
注意事项:
• 不要涉及太大的范围
问题分析技术与管理
• 不要太长的活动期间
8D
16
壹. 问题篇 问题的出现
• 依公司目标管理方向 • 主管的方针、上司的提示及指引 • 浪费、不均、勉强的问题 • 提高效率、质量方面 • 考虑自行可解决的问题
8D
17
壹. 问题篇 主题决定--评价法
8D
25
查检表 (Check List)
地区
FAB 1
机 台
项目
ABC
温度不足
压力不足
转速不足 其他
FAB 2 ABC
8D
26
直方图 (Histogram)
• 目的:为便于判断产品质量特性之分配 状态,及其与规格之关系所绘制 之图形
• 通常先以层别法及查检表为前置作业
8D
27
直方图 (Histogram)
80.3 80.0 82.8 79.4 80.0 80.4 77.5 80.1 79.3 78.6
81.5 80.5 80.4 78.9 81.2 80.5 80.9 79.8 81.4 80.6
79.0 80.6 79.0 79.1 80.8 79.4 79.9 79.5 79.7 80.7
8D
教你如何做8D报告(品质精品)
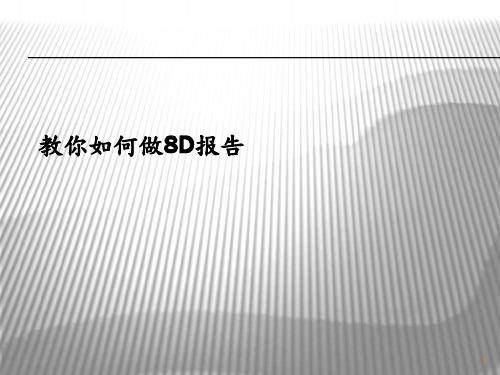
18
也就是我們常說的人, 事, 時, 地, 物
WHAT 什麼事情
WHEN 何時發生 WHO 與誰有關 WHERE 在何處發生
HOW MANY 發生的程度
問題描述
會惡化
是否須緊急處置
19
緊急處置
發生中 Holding
未發生 Sorting
品質問題
已發生
Tracing
20
D2階段 現狀分析(問題細部描述)—收集資料 Fact & Data Finding analysis
24
記錄用查檢表
責任部門
2003年各季LOSS TIME責任分類查檢 表
季度 第一季 第二季 第三季
制 造 1200
1050
890
品保
800
760
780
生管
180
160
100
制工
200
170
185
工程
60
55
78
採購
300
282
300
材倉
50
38
42
合計
2790
2515
2375
合計
3140 2340 440 555 193 882 130 7680
進行真因分析與驗證真因 5、 D5列出選定及驗證永久對策 6、 D6執行永久對策及效果確認 7、 D7防止再發及標準化 8、 D8認知與殘餘潛在問題
4
問題是什么?
當現狀與標准或目標有了差距時, 即遇到了問題
過去
現在
目標 未來
5
盤點工厂現存在的問題
VQA進料檢驗單位 合資單位 業務單位 工程單位 制造單位 IPQC FQC QA QE
8D报告完整版范文

8D报告完整版范文8D是一种问题解决方法,通过8个步骤来进行问题的分析和解决。
下面是一个完整版的8D报告,包含对问题的描述、团队成员、问题的分析、解决方案以及实施结果的评估。
1.问题描述:在公司生产线上,发现了一个质量问题,产品出现了大量次品,导致客户抱怨并要求退货。
问题主要体现在产品的外观质量方面,表面容易出现划痕和凹痕。
2.团队成员:该问题的解决由以下团队成员共同参与:-生产部门:负责产品制造的技术人员和操作工-质量控制部门:负责产品质量的技术人员和检验员-客户服务部门:负责与客户沟通和解决问题3.问题的分析:通过团队成员的讨论和原因分析,我们找到了导致产品质量问题的几个主要原因:-工人操作不规范:工人在产品组装和包装时没有按照操作规程进行操作,导致产品出现划痕和凹痕。
-零部件供应商的质量问题:部分零部件的质量不达标,容易导致产品出现质量问题。
-质量控制不严格:质量控制部门在产品质量检验中存在一定的盲区,没有发现产品质量问题。
4.解决方案:基于问题分析,我们提出了以下解决方案来解决产品质量问题:-进行员工培训:对所有参与生产的员工进行质量意识培训和操作规程培训,确保所有员工按照规范进行生产操作。
-与供应商合作:与零部件供应商建立长期合作关系,并要求供应商提供质量合格证明。
对于质量不达标的零部件,及时通知供应商进行更换或修复。
-加强质量控制:质量控制部门要加强对产品质量的检验,制定更为细致的产品质量检验标准,并对产品检测设备进行定期维护和校准。
5.解决方案的实施:我们按照上述解决方案,分别进行了以下实施步骤:-员工培训:与人力资源部门合作,组织了一次质量培训会议,邀请专业培训师对所有员工进行培训,培训内容包括质量的重要性、操作规程和注意事项等。
-供应商合作:质量控制部门与供应商进行了紧急会议,并要求供应商提供质量合格证明。
部分质量不达标的零部件得到了及时更换和修复。
-质量控制加强:质量控制部门对产品质量检验标准进行了更新,并对产品检测设备进行了定期维护和校准。
8D报告通用格式

8D报告通用格式第一篇:8D报告通用格式8D报告即处理投诉的八项原则1.组建团队2.问题描述:顾客的结论可能是对的,也可能是错的.要得出最终缺陷是什么3.及时反应:当出现投诉后,顾客产品怎么办?我们的库存怎么办?产品要不要召回要不要隔离要不要重验以上三项要在24小时完成4.根本原因分析:这是8D报告中最主要部分,写到最后只能分析出人机料法测量这几方面原因。
原则:循序渐进.(报告中描述不清楚的问题可提供照片)分析要深刻、到位,如:员工操作不当,不能当做原因,要分析是没有进行培训还是别的原因.前四项为5个工作日内完成.5.纠正措施:确定纠正措施是什么.6.结果的验证:7.预防再发生8.团队激励:肯定贡献,进行激励。
第二篇:178报告四是妥善解决历史遗留问题。
①根据市国资委发【2011】188号文《关于妥善解决我市国有企业职教幼教退休教师待遇问题的通知》,着实办理。
从2012年8月开始,经过幼儿园资格审核、上报人员资格认定,合格人员生活补贴核算等程序,最终有2人符合资格,至2013年10月上报工作圆满结束。
②陕人社178号文《关于对按计划招用的曾在我省国有、集体企业工作过的农业户籍人员发放养老补助有关问题的处理》,从2012年3月份开始接待60年代初精简下放人员的上访,历时1年9个月共计接待上访人次1800多次,共办理了符合条件人员786人。
此项工作的开展受到上访者的一致好评,并收到上访人员送出荣誉锦旗6面,对公司形象有着极大的宣传作用,对在职员工有着很好的激励作用。
并且解决了公司历史遗留问题,对社会稳定起到了一定的作用,使这些老员工从心灵上得到了安慰。
第三篇:报告关于对我市主城区存在脏乱差情况的调研报告市委、市政府:为积极推进我市创建文明城市工作,按照我办工作安排, 2月23日我办与区创城办工作人员一起走访了主城区城市道路,特别是市民反映比较强烈的路段,就我市主城区存在的脏乱差情况进行调研。
通过实地考察,了解了我市主城区存在的脏乱差情况实际情况和存在的主要问题,现将调研情况报告如下:一、基本情况我市主城区城市路段:中山路、新兴路、来昌路进一步核实,这几条路路面烂得比较严重,路面坑坑洼洼的“水塘”随处可见。
品质8d报告范文
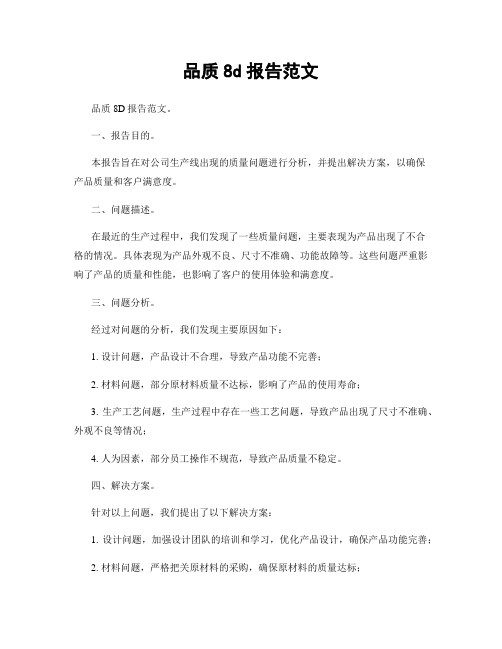
品质8d报告范文品质8D报告范文。
一、报告目的。
本报告旨在对公司生产线出现的质量问题进行分析,并提出解决方案,以确保产品质量和客户满意度。
二、问题描述。
在最近的生产过程中,我们发现了一些质量问题,主要表现为产品出现了不合格的情况。
具体表现为产品外观不良、尺寸不准确、功能故障等。
这些问题严重影响了产品的质量和性能,也影响了客户的使用体验和满意度。
三、问题分析。
经过对问题的分析,我们发现主要原因如下:1. 设计问题,产品设计不合理,导致产品功能不完善;2. 材料问题,部分原材料质量不达标,影响了产品的使用寿命;3. 生产工艺问题,生产过程中存在一些工艺问题,导致产品出现了尺寸不准确、外观不良等情况;4. 人为因素,部分员工操作不规范,导致产品质量不稳定。
四、解决方案。
针对以上问题,我们提出了以下解决方案:1. 设计问题,加强设计团队的培训和学习,优化产品设计,确保产品功能完善;2. 材料问题,严格把关原材料的采购,确保原材料的质量达标;3. 生产工艺问题,对生产工艺进行全面的审核和改进,确保产品生产过程中的每一个环节都符合标准;4. 人为因素,加强员工培训,提高员工操作技能,确保产品质量稳定。
五、实施计划。
为了解决上述问题,我们制定了以下实施计划:1. 设计问题,设立专门的设计改进小组,负责产品设计的优化和改进,定期进行设计评审;2. 材料问题,与供应商建立长期稳定的合作关系,对原材料进行严格的质量检测和管理;3. 生产工艺问题,对生产工艺进行全面的审查和改进,引进先进的生产设备和技术,提高生产效率和产品质量;4. 人为因素,加强员工培训,定期进行员工技能培训和考核,提高员工的操作技能和质量意识。
六、效果评估。
经过以上的改进和实施,我们预计可以达到以下效果:1. 产品质量得到显著提升,不合格率大幅下降;2. 客户投诉率明显降低,客户满意度得到提高;3. 公司形象得到提升,市场竞争力得到加强。
七、总结。
8D报告怎么做?步骤分解及案例都在这里!

8D报告怎么做?步骤分解及案例都在这里!8D起源于福特汽车公司处理产品质量问题的一种方法。
凡是福特公司的供应商遇到问题必须强制用这种方法。
后来其他的非福特公司的供应商也引进这个方法处理问题。
就这样家喻户晓,各行业通吃。
其实,8D不仅仅解决工作问题,解决家庭生活问题也很有效。
今天我们主要分享8D在处理质量问题上的案例应用。
01D0 现象及应急反应活动根据现象评估8D过程是否需要。
如果有必要,采取紧急反应行动(ERA)来保护顾客,并开始8D过程。
8D过程区别了症状和问题。
适用标准的大部分是症状。
没有症状,不会知道有问题。
▪️症状:指一个显示存在一个或多个问题的可测量的事件或结果。
这个事件的后果必须被一个或多个顾客经历;▪️问题:指同期望有偏差或任何由未知原因引起的有害的后果;▪️症状是问题的显示。
当收到客诉时,质量部门尽量在客户投诉报告上确认以下信息:·产品编号及品名·客户名称,联系人及地址·缺陷描述,不合格品数量·追溯信息,如LOT No,发货单编号等·索赔应尽量取得车型等信息如有,应从客户处得到样品,照片,标签及不合格率等必要的信息。
如是芯体泄露或严重投诉,收到投诉的人应立即通知质量经理,及至总经理。
QE或CE应在收到投诉一个工作日内与客户联系。
正常情况,要与客户沟通以下信息:·跨部门小组及联系方式·确认已得到的信息·调查问题所必需的其他信息·应急措施的进展·应急措施及纠正措施的预期完成时间·任何其它的客户要求,如:了解问题进展和期望的交货·所有与客户之间的回复均应记录。
QE(质量工程师)根据获得的信息,依据三现主义(现场,现物,现象)来确认不良状况;如果是可以目视的不良,尽量取得照片或样品(确认现物);对于不良发生场所状况尽量收集详细的情报(确认现场,现象)。
应急措施要在24小时内展开。
干货|如何写好一份8D报告

干货|如何写好一份8D报告一.什么是8D1.什么是8D8D 的原名叫做 8 Disciplines,又称团队导向问题解决方法。
•此方法以团队运作导向以事实为基础,避免个人主见之介入,使问题之解决能更具条理。
•面对问题应群策群力,互相帮助、相互提拔、如此才能彻底解决问题。
2.8D的作用•通过建立小组训练内部合作的技巧。
•提供问题有效解决的方法。
•防止相同或类似问题的再发生。
•提高顾客满意度,增强其对供方的产品和过程的信心。
3.何时采用8D1.重复发生,一直没有解决的问题2.比较重大的制程品质问题3.客户要求回复的品质投诉二、8D步骤D0.问题初步了解问题初步了解(立项和准备工作)•鉴定是否有进行8D 的必要;•立项和确定主题;•收集资料。
此过程尽量获取内部和外部的问题信息、数据、进行初步的分析和方案策划。
D1建立小组建立一个小组来解决问题和执行纠正计划,小组成员应具有过程和/或产品知识、分配的时间、权威和需要的技能。
建立小组需要考虑的要素:•小组的领导:谁来推动?•小组的资源:谁提供支持?•小组的成员:合作及分工?•人员的数量:多少为宜?选择小组成员的准则:D2问题描述以客户的角度和观点详细描述其所感受到的问题现象,将所遭遇的问题,以量化的方式,明确出所涉及的人,事,时,地,为何,如何,多少。
问题描述方法:5W/2HD3临时对策定义、验证和执行临时控制行动,保证在永久纠正措施实施前,将问题与内外部顾客隔离。
需要考虑的问题:1.防止继续产生不良品(减少不良品产生)。
2.减小产生的不良和后续可能产生不良对客户的影响。
确定并执行应先采取的临时措施,以遏制外界/内部客户问题的扩大。
•临时措施的确定应考虑从供应商零件库存---供应商零件在途品--内部零件/材料—生产制程—仓库储存—交付在途品—客户端减少和降低(消除)后果的产生。
•临时措施一直要持续实施至后续的永久对策的执行有效后,方可撤消。
•临时措施实施中,应及时跟踪和验证其效果。
手把手教你写客户满意的人为操作失误8D报告

其实首先我也想说,不仅就是您得客户不喜欢这样得8D报告,我也不喜欢人家写整改措施动不动就写“操作工质量意识不强,加强培训”,“处罚当事人300块”等等。
我在企业做质量负责人得时候,无论就是我得供应商还就是内部生产工程除了类似得问题,如果我SQE或过程质量工程师把这样得改进报告交给我,必然会得到我得一顿狠批。
因为把质量问题得责任推卸给操作工,要么就是不负责任得应付,要么就就是不懂质量管理。
因为在我得工作经历中,我所接触到得操作工,大多都就是很朴实得工人。
确实有刁钻耍滑得,但就是少之又少。
所以上述例子中得问题,无不可以从管理制度与方法上查找原因。
首先说说外观缺陷一般说来,外观缺陷都就是需要百分之百目测检验得,确实容易造成漏检得情况。
但就是还就是可以从下面几个方面去查找原因与制定改进措施得。
—-外观检验标准就是否具体、就是否清晰、就是否与顾客达成了一致。
有些企业得外观标准上仅简单写了“无飞边毛刺、无磕碰伤”。
但就是在现场操作时,操作工与生产管理人员又认为“无磕碰伤就是不可能得",因而就按照自己得理解去掌握一个模糊得标准、规范得做法就是,把产品按照功能面,逐一根据可能得缺陷确定可以接受得标准与不能接受得标准、然后以图文并茂得形式描述清楚。
标准应清晰、易懂、没有歧义,而且就是现实可行得。
杜绝模糊得“外观标准参见限度样件”。
如果有限度样件,也要有文字说明,限度样件就是哪个方面哪个缺陷得限度样件,就是缺陷样件还就是合格样件,缺陷与合格得判定条件就是什么,一定要说明清楚。
——外观标准就是否已经清晰、明确地培训传达到员工。
杜绝笼统地说培训不到位,而仅仅就事论事在这个缺陷上培训这个员工,而同类得事情下次在另一个工位就另外一个问题又可能重复发生。
如果就是员工培训方面整改,一定从培训方法、培训流程、培训后考核方法、新员工上岗初期得互检与师傅陪伴等角度,在工作方法上与流程制度上找原因,加以整改,杜绝下次类似得事情发生、例如针对外观缺陷得培训,除了给新员工讲解外观标准或作业指导书,还应该结合大量得缺陷实物样件进行培训,让新员工做些缺陷判断得练习、在员工上岗初期,在标准界限附近得零件要请师傅或质量人员帮忙判断。
个人犯错8d报告模板范本

个人犯错8d报告模板范本
个人犯错8D报告模板范本
报告编号:[编号]
报告日期:[日期]
报告人:[报告人]
报告对象:[报告对象]
1. 问题描述:
描述犯错的具体情况,包括错误的性质、时间、地点等。
2. 问题原因分析:
详细分析问题产生的根本原因,找出导致错误发生的具体因素。
3. 短期对策:
提出短期措施,确保问题不再出现或者降低问题的影响。
4. 客户通知:
如果错误对客户造成了影响,说明已向客户通知,并提供后续处理方案。
5. 长期对策:
提出长期解决问题的对策,以防止类似问题再次发生,并提出具体实施方法和时间表。
6. 预防措施:
提出预防措施,以避免类似问题在其他工作领域的发生。
7. 效果验证:
对实施的长期对策和预防措施进行效果验证,确保问题得到持久解决。
8. 结论:
总结整个报告,强调个人对错误的认识,并表示对问题产生的影响负责。
附:
- 相关证据材料(如有)
- 相关统计数据(如有)
- 相关参考文件(如有)
以上为个人犯错8D报告模板范本,供参考。
具体报告应根据具体问题进行个性化的调整和补充。
8D报告填写及手法运用

鱼骨图 / 因果图
❖ 功能分析
➢ 系统/零部件/生产过程
单独列出所有功能 应用技术:
➢ 功能树 ➢ 过程流程分析
应用资料:
➢ 设计要求书 ➢ 产品规范 ➢ 过程流程图
五个为什么方法 The Five Why Method
根 由 R oot C ause 为什麽?
真正原因
为什麽?
D3:临时措施 (1)
围堵/隔离问题 采取即时行动或应变对策控制问题影响范围 跟进客户或后序品质、生产要求 对不良品进行分析并追溯到相关工序或个人 对异常隐患批次在制品或库存停止流转或外发
(如有需要) 清理仓库、工厂及现场中的不良品或可疑产品
D3:临时措施(2)
为防止问题恶化并波及其他产品必须举一反三 尽快恢复客户信心 预先布置应变方案 采用产品追溯到生产批次和受影响范围
1问: 为什么缺划不良会从完检流到出货检? 1答: 因为缺划产品经分析多数为弧倒造成,
而个别弧倒产品造成的颈部受伤不稳定,有时亮有时不亮 。
2问: 为什么会有弧倒产生? 2答: 因为部分晶片在边缘,拿放时碰倒弧线 。 3问: 为什么会碰倒弧线? 3答: 因为按照常规要求去取放PCB。 4问: 为什么按常规要求去取放PCB? 4答: 因为并未在文件中明确取放要求 。 5问: 为什么未明确要求在技术文件中? 5答: 因为文件按常规要求编制 。 由上可见,经常利用问5次为什么,就可以确认出问题的原因以及
D2:问题的描述
以外部客户或内部部门反馈的述语进行描述 清楚明白客戶投诉或内部异常的不合格之处 只有数据才能准确说明问题,但来源必须真实 使用5W2H的方法去定义及收集问题的资料 定义问题时可用-图片、形象、图表
何谓 “5W 2H” ?
8D报告中人为因素应该怎么整改

制定改进措施,杜绝模糊标准、笼统培训和不合理策划
明确标准
制定清晰、具体的外观检测标准, 确保每个员工都能准确理解并执行 。
完善培训
加强员工培训,提高他们的技能水 平和质量意识,确保他们能够准确 掌握外观检测标准。
合理策划
根据生产需求和员工能力进行合理 的岗位策划,确保每个岗位的员工 都能够胜任其职责。
制定改进计划
根据分析的结果,制定改进计划,包括培训、流程改进或其他必 要的措施。
跟踪改进成果
对改进措施进行跟踪,以确保问题已得到解决并持续改进。
THANK YOU
建立严格的供应商评估体系
评估供应商的质量保证能力和他们是否遵守规 定的操作程序。
定期审计供应商
定期对供应商进行审计,以确保他们持续符合 要求。
建立奖惩制度
对于表现优秀的供应商给予奖励,对于造成问题的供应商进行惩罚。
分析原因并改进,而非简单归因于操作失误
进行根本原因分析
找出混料的根本原因,而不仅仅是表面现象。
配备警示卡
在关键质量控制点配备足够的警示 卡,提醒员工注意可能出现的问题 ,避免人为失误。
02
标签贴错问题
从现场打印、独立标签打印机或换型防错角度改进
01
现场打印
采用现场打印的方法可以减少标签贴错的问题。通过使用便携式打印
机,操作员可以在产品上直接打印标签,避免因标签贴错而产生的问
题。
02
独立标签打印机
班组长应定期对生产线上的产品标签进行互检,及时发现并纠
正标签错误员进行标签粘贴和识别方面的培训,提高操
作员对标签信息的认识和判断能力。
03
数量短缺问题
改进建议
规则产品整齐摆放、定制吸塑盒或料盒、称重法。
8d报告生产案例范文

8d报告生产案例范文案例背景近日,我司生产线上出现了一起质量问题,部分产品出现了严重的尺寸偏差现象。
为了彻底解决这个问题,我们迅速展开了8D报告的问题解决流程,并于XX月XX日完成功能过该案例。
问题描述在生产线上生产的产品尺寸偏差较大,超过了允许范围。
该问题对产品的质量造成了严重影响,需要尽快解决。
初步原因分析通过对问题进行初步调查和分析,我们发现可能的原因有:1. 模具老化导致的尺寸不稳定。
2. 操作工操作不当,没有按照规定的工艺流程进行生产。
3. 人为因素,例如操作工操作不规范。
问题解决措施针对问题的初步原因分析,我们制定了以下解决措施:1. 进行模具更换,确保新的模具尺寸稳定。
2. 重新培训操作工,提醒他们严格按照规定的工艺流程进行生产。
3. 强调操作工严格操作的重要性,加强对操作工的监督和管理。
8D报告步骤第一步:组建问题解决小组我们成立了一个专门的问题解决小组,由相关的技术人员、质量人员和生产人员组成。
第二步:问题描述和原因分析我们详细描述了问题,按照8D方法分析了问题的原因。
第三步:紧急应对措施在问题暴露后,我们立即采取了紧急应对措施,暂停了全部产线,并进行了模具的更换。
第四步:根本原因分析通过对问题的深入调查和分析,我们发现问题的根本原因是操作工操作不规范导致的。
第五步:长期解决方案为了彻底解决问题,我们制定了长期解决方案:重新培训操作工,提醒他们严格遵守操作规程,确保生产过程规范。
第六步:实施长期解决方案为了确保长期解决方案的有效实施,我们组织了培训课程,并加强了对操作工的管理和监督。
第七步:验证解决方案的有效性我们对解决方案进行了实际生产和质量监控,验证了解决方案的有效性。
第八步:预防措施为了避免类似问题再次发生,我们进一步加强了对模具使用寿命的监控和管理,并加强了操作工的培训和管理。
结果和总结通过本次的8D报告问题解决流程,我们成功解决了生产线上的尺寸偏差问题,并且在以后的生产中没有再次出现类似问题。
8d报告简洁版范文

8d报告简洁版范文
8D报告简洁版范文
问题描述:
某产品在生产过程中出现了质量问题,导致部分产品出现缺陷,并被客户投诉。
原因分析:
1. 设计问题:产品设计不合理、不稳定,导致产品无法正常运行。
2. 材料问题:使用了不合格的原材料,影响了产品的质量和稳定性。
3. 加工工艺问题:生产过程中存在操作不规范、流程不完善等问题,导致产品质量下降。
4. 人员培训问题:员工对于质量控制的要求认识不足,缺乏相应的培训和指导。
纠正措施:
1. 设计改进:对产品进行重新设计,解决原设计存在的问题,提高产品的可靠性和稳定性。
2. 材料改进:更换合格的原材料,确保产品的质量和稳定性。
3. 加工工艺改进:完善生产流程,加强员工培训,确保操作规范,提高产品的加工质量。
4. 培训计划:制定详细的培训计划,并进行定期培训,提高员工对于质量控制的认识和能力。
执行结果:
1. 设计改进后,产品质量稳定性得到了提高,客户投诉情况显著减少。
2. 更换合格的原材料后,产品的质量和稳定性得到了明显改善。
3. 加工工艺改进后,产品的加工质量和一致性得到了提高,缺陷率明显降低。
4. 培训计划的执行使得员工对于质量控制的理解和能力得到了提高,有效减少了人为因素造成的质量问题。
结论:
通过对问题的分析和改进措施的执行,质量问题得到了有效解决,产品质量和稳定性明显提高。
同时,相关部门也应加强对于质量控制的监督和管理,确保质量标准的执行和持续改进。
错发产品的8d报告

错发产品的8d报告1. 背景介绍在供应链管理的过程中,由于各种原因往往会出现错发产品的情况,也就是将错误的产品发给了客户。
这不仅会给公司形象带来负面影响,还可能导致客户不满意甚至追求法律责任。
因此,我们需要进行8D报告来解决这一问题。
2. 问题描述在最近的一次订单中,我们收到了客户XX公司的投诉,称他们收到的产品型号与实际订购的不一致。
经过进一步调查,发现由于人为操作失误,我们将错误的产品装运给了该客户。
造成了一定的经济损失和客户的不满意。
3. 8D报告流程D1 正确的定义问题我们首先需要确定问题的范围和具体情况,明确错发产品是如何发生的,以及影响的程度。
经过调查与客户的沟通,我们确认了该问题确实存在,并进行了详细的记录与分析。
D2 组建问题解决团队为了能够解决这个问题,我们委派了由多个部门组成的跨功能团队,包括生产、质量保证、销售等。
他们将以团队的形式协作,共同解决这个问题。
D3 急诊措施为了尽快缓解错误发货造成的影响,我们立即向客户致以最诚挚的歉意,并保证会在最短的时间内将正确的产品发给他们。
同时,我们也主动承担了由此带来的物流费用。
D4 根本原因分析我们对此问题进行了详细的原因分析,发现该问题的根本原因是我们内部流程管理存在缺陷,没有严格执行标准操作程序。
同时,考虑到员工可能存在的技术水平问题、系统错误等环节,我们也对此进行了仔细的分析。
D5 制定修正计划针对这个问题,我们制定了详细的修正计划。
首先我们会对内部流程进行审查与改进,加强员工培训,确保每个员工都严格按照标准操作程序进行工作。
同时,我们也会对系统进行修复与优化,减少系统错误可能导致的问题。
D6 实施修正计划我们立即开始执行修正计划,并设立了明确的执行时间表。
具体工作包括对员工进行培训、系统改进、制定新的流程等。
我们将严格按照计划执行,以确保问题得到及时解决。
D7 预防措施为了避免类似问题再次发生,我们将加强内部的流程纪律,要求每个员工都必须严格遵守操作规范。
- 1、下载文档前请自行甄别文档内容的完整性,平台不提供额外的编辑、内容补充、找答案等附加服务。
- 2、"仅部分预览"的文档,不可在线预览部分如存在完整性等问题,可反馈申请退款(可完整预览的文档不适用该条件!)。
- 3、如文档侵犯您的权益,请联系客服反馈,我们会尽快为您处理(人工客服工作时间:9:00-18:30)。
错、数量短缺、漏加工步骤、错发料等问题。
么写呢?总不可能什么都上防错吧?”
其实首先我也想说,不仅是你的客户不喜欢这样的8D 报告,我也不喜欢人家写整改措施动不动就写“操作工质量意识不强,加强培训”,“处罚当事人300 块”等等。
我在企业做质量负责人的时候,无论是我的供应商还是内部生产工程除了类似的问
狠批。
因为把质量问题的责任推卸给操作工,要么是不负责任的应付,要么就是不懂质量管理。
因为在我的工作经历中,我所接触到的操作工,大多都是很朴实的工人。
确实有刁钻耍滑的,但是少之又少。
所以上述例子中的问题,无不可以从管理制度和方法上查找原因。
首先说说外观缺陷
一般说来,外观缺陷都是需要百分之百目测检验的,确实容易造成漏检的情况。
但是还是可以从下面几个方面去查找原因和制定改进措施的。
——外观检验标准是否具体、是否清晰、是否和顾客达成了一致。
有些企业的外观标准上仅简单写了“无飞边毛刺、无磕碰伤”。
但是在现场操作时,操作工和生产管理人员又认为“无磕碰伤是不可能的”,因而就按照自己的理解去掌握一个模糊的标准。
规范的做法是,把产品按照功能面,逐一根据可能的缺陷确定可以接受的标准
和不能接受的标准。
然后以图文并茂的形式描述清楚。
标准应清晰、易懂、没有歧义,而且是现实可行的。
杜绝模糊的“外观标准参见限度样件”。
如果有限度样件,也要有文字说明,限度样件是哪个方面哪个缺陷的限度样件,是缺陷样件还是合格样件,缺陷和合格的判定条件是什么,一定要说明清楚。
——外观标准是否已经清晰、明确地培训传达到员工。
杜绝笼统地说培训不到位,而仅仅就事论事在这个缺陷上培训这个员工,而同类的事情下次在另一个工位就另外一个问题又可能重复发生。
如果是员工培训方面整改,一定从培训方法、培训流程、培训后考核方法、新员工上岗初期的互检和师傅陪伴等角度,在工作方法上和流程制度上找原因,加以整改,杜绝下次类似的事情发生。
例如针对外观缺陷的培训,除了给新员工讲解外观标准或作业指导书,还应该结合大量的缺陷实物样件进行培训,让新员工做些缺陷判断的练习。
在员工上岗初期,在标准界限附近的零件要请师傅或质量人员帮忙判断。
要建立关键岗位管理和顶岗人员培训制度,杜绝新员工临时培训匆忙上岗。
——岗位工作策划是否合理。
例如有外观检验要求的工位的光源的光照度是否合适?外观检验工作台的高度是否合适工件翻动和作业观察?员工外观检验的观察作业的次序是否有策划并固化下来了?也就是说,员工检验零件外观时,眼睛要看到哪几个面哪几个点,工件翻转次序和眼睛的行走路径是否是固定的?外观检验和生产操作是否能够在限定的节拍内完成?
——常出现的外观缺陷是否张贴了质量警示卡,提醒员工特别注意?
——最后,也是最重要的,是否在源头上查找原因,致力于减少和杜绝外观缺陷?例如针对磕碰伤问题,流水线上的产品运输辊道是否会磕碰零件?产品和产品之间是否会发生磕碰?物流周转工装是否合理?是否存在工件堆叠?员工操作过程、工件摆放过程是否存在磕碰风险?
第二个问题,标签贴错
标签贴错在很多主机厂客户来说,也是一个很严重的问题。
在有些客户那里如果发生标签贴错两次就可能直接导致受控发运。
标签贴错可以从如下几个角度考虑改进。
——现场打印,随用随打印,禁止事先打印标签。
一般来说要求严格的主机厂会要求供应商在生产线的包装工位设置标签打印机。
如果企业有多条生产线就应该在每条线边的下线包装工位设置独立的标签打印机。
杜绝在办公室里打印了一堆的标签。
有些企业有各种不同产品的,也可能有不同批次的,喜欢在办公室统一打印一堆标签,然后一堆标签拿到生产线边,包装时再从一堆标签里翻找出来贴上。
或者先包装后,很多的包装箱堆叠在一起,然后一起贴标签。
甚至有的企业在包装后放置几天,发运前再贴标签。
这些不正确的做法,不出现问题才是不正常的。
——如果客户没有独立打印机的明确要求,而且企业一时还不能做到独立标签打印机,也可以采用换型防错的方法来保证标签正确。
换型防错的方法,我以后有机会再单独写文章介绍。
简单地说,就是在多种产品共线生产的情况下,当准备切换加工某一种型号产品时,把原材料、产成品、半成品、工装、刀具、工具、辅具、各种作业指导书、各种记录表、包装材料,包括设备里面调用的程序和工艺参数,当然也包括标签,统统切换成准备生产的产品型号相一致的。
而不一致的,确保从生
产线上,从操作者可以拿到的范围内撤离或者封盖起来。
使得误拿误用成为不可能,这就叫换型防错。
在换型时,操作工利用《换型防错点检表》点检并记录所有的软硬件的切换得到了落实,班组长互检。
第三个,数量短缺问题
我也不赞同增加人员互检,因为效率很低。
那么除了采用计数器之外,还可以从如下角度考虑改进:
——如果是规则的产品,应该整齐摆放。
一个包装盒或者一个料箱固定几排几列几层,这样点检数量就转换成了对排列形状的外观检查,数量确认就变得很直观。
——如果同时在防护磕碰、挤压方面有要求,那就考虑定制成型吸塑盒、或带有分隔板的料盒来摆放产品,一个萝卜一个坑。
坑没填满,缺件了,就是数量不够。
——称重法。
但是在零件数量很多,每个件的重量又在一定范围内波动时,就可能导致称重判定数量时的不准确。
这时可以考虑在大包装内设置若干的小包装,而小包装的数量设置要考虑到总重量的波动范围的西格玛小于一个零件重量的六分之一。
第四个问题,漏加工
除了设置连续的生产线,设置过程防错之外,还可以从以下方面考虑改进:
——增加自检和互检,在每道序放行之前,操作者检验自行检验本道序加工的内容是否完成,检验后放行或者再放入料架料盒。
下道序在加工前检验上道序的加工或装配内容是否完成。
——定置管理,定位存放。
如果是单机作业,每个单机工位待加工件和已加工件一定要分开摆放,定置摆放。
一般地,左手边是待加工件,右手边是已加工件。
严禁混放,严禁待加工已加工件放置在同一料架或料盒。
在在制品周转区,整料箱的在制品也要各个不同工序状态的产品分区摆放,且做好明显标识。
——悬挂工序随行卡。
针对单机作业的生产线,料架或料车要悬挂随行卡,在随行卡上标明工序状态。
第五个问题,发错料
最常见的错误是一个大包装多数正确的产品里面混进来一两只不同型号的产品。
一般是由下列原因造成的,把这些方面改掉了,也就基本杜绝了混料问题。
——针对这样的问题,最基本原因就是没有做好换型防错。
在生产工位、在生产线边存在不同型号的产成品、在制品同时存在的现象。
——或者在包装区、检验区,不同型号的产品同时存在,散放、混放。
所以定置管理、5S,还是最基本的要求,不是简单的干净整齐的而已。
除上述问题之外,还有一个被供应商常常使用的原因,就是“调试件被混在了合格件里报交”。
这也是被我和很多主机厂的SQE们所深恶痛绝的一个说法。
我们常常会追问,你怎么确定那个件就是调试件的?零件上有追溯号吗?调试件的检验记录和追溯号相对应吗?即使真的是调试件被混入合格品的话,企业也需要在不合格品定置摆放和标识、调试品定置摆放和标识、开机前检查确认、首件确认,等几个方面的管理方法加以原因分析和改进。
而不是简单地归结为认为操作失误。