辽河化肥厂实习
化肥厂实习心得体会
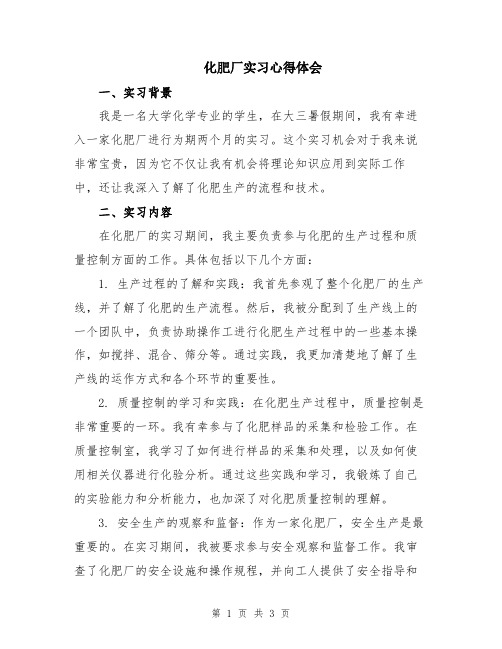
化肥厂实习心得体会一、实习背景我是一名大学化学专业的学生,在大三暑假期间,我有幸进入一家化肥厂进行为期两个月的实习。
这个实习机会对于我来说非常宝贵,因为它不仅让我有机会将理论知识应用到实际工作中,还让我深入了解了化肥生产的流程和技术。
二、实习内容在化肥厂的实习期间,我主要负责参与化肥的生产过程和质量控制方面的工作。
具体包括以下几个方面:1. 生产过程的了解和实践:我首先参观了整个化肥厂的生产线,并了解了化肥的生产流程。
然后,我被分配到了生产线上的一个团队中,负责协助操作工进行化肥生产过程中的一些基本操作,如搅拌、混合、筛分等。
通过实践,我更加清楚地了解了生产线的运作方式和各个环节的重要性。
2. 质量控制的学习和实践:在化肥生产过程中,质量控制是非常重要的一环。
我有幸参与了化肥样品的采集和检验工作。
在质量控制室,我学习了如何进行样品的采集和处理,以及如何使用相关仪器进行化验分析。
通过这些实践和学习,我锻炼了自己的实验能力和分析能力,也加深了对化肥质量控制的理解。
3. 安全生产的观察和监督:作为一家化肥厂,安全生产是最重要的。
在实习期间,我被要求参与安全观察和监督工作。
我审查了化肥厂的安全设施和操作规程,并向工人提供了安全指导和培训。
通过这样的实践,我更加深入地了解了安全生产的重要性,也提高了自己的安全意识。
三、实习收获通过这次化肥厂的实习,我收获了很多,主要可以总结为以下几点:1. 理论知识与实践相结合:在学校里,我们学习了大量的化学理论知识,但是这些知识都是理论性的,很难直接应用到实际工作中。
通过实习,我有机会将所学的理论知识应用到实际工作中,真正感受到了科学知识的力量。
2. 学习团队合作和沟通能力:在化肥厂的实习期间,我与其他团队成员密切合作,共同完成了工作任务。
这样的合作需要良好的沟通和协调能力,而这正是我在实习中得到锻炼的地方。
通过与团队成员的合作,我意识到一个好的团队是可以事半功倍的。
3. 提高实验和分析能力:在化肥厂的实习期间,我参与了化肥样品的采集和检验工作。
化肥厂实习专题报告
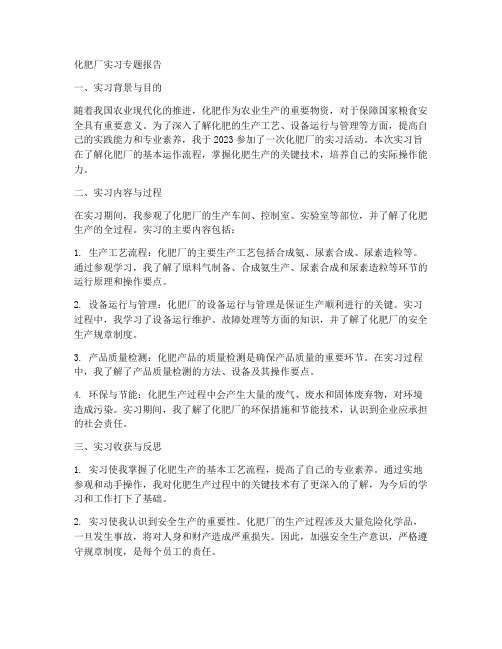
化肥厂实习专题报告一、实习背景与目的随着我国农业现代化的推进,化肥作为农业生产的重要物资,对于保障国家粮食安全具有重要意义。
为了深入了解化肥的生产工艺、设备运行与管理等方面,提高自己的实践能力和专业素养,我于2023参加了一次化肥厂的实习活动。
本次实习旨在了解化肥厂的基本运作流程,掌握化肥生产的关键技术,培养自己的实际操作能力。
二、实习内容与过程在实习期间,我参观了化肥厂的生产车间、控制室、实验室等部位,并了解了化肥生产的全过程。
实习的主要内容包括:1. 生产工艺流程:化肥厂的主要生产工艺包括合成氨、尿素合成、尿素造粒等。
通过参观学习,我了解了原料气制备、合成氨生产、尿素合成和尿素造粒等环节的运行原理和操作要点。
2. 设备运行与管理:化肥厂的设备运行与管理是保证生产顺利进行的关键。
实习过程中,我学习了设备运行维护、故障处理等方面的知识,并了解了化肥厂的安全生产规章制度。
3. 产品质量检测:化肥产品的质量检测是确保产品质量的重要环节。
在实习过程中,我了解了产品质量检测的方法、设备及其操作要点。
4. 环保与节能:化肥生产过程中会产生大量的废气、废水和固体废弃物,对环境造成污染。
实习期间,我了解了化肥厂的环保措施和节能技术,认识到企业应承担的社会责任。
三、实习收获与反思1. 实习使我掌握了化肥生产的基本工艺流程,提高了自己的专业素养。
通过实地参观和动手操作,我对化肥生产过程中的关键技术有了更深入的了解,为今后的学习和工作打下了基础。
2. 实习使我认识到安全生产的重要性。
化肥厂的生产过程涉及大量危险化学品,一旦发生事故,将对人身和财产造成严重损失。
因此,加强安全生产意识,严格遵守规章制度,是每个员工的责任。
3. 实习使我关注到环保与节能问题。
化肥生产过程中产生的废气、废水和固体废弃物对环境造成严重污染,企业应采取有效措施减少环境污染,实现可持续发展。
4. 实习使我意识到实际操作能力的重要性。
理论联系实际,才能更好地将所学知识应用于实际工作中。
化肥厂实习心得
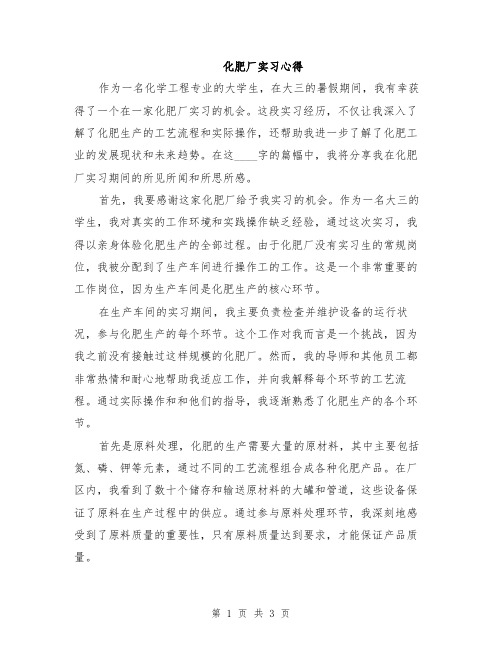
化肥厂实习心得作为一名化学工程专业的大学生,在大三的暑假期间,我有幸获得了一个在一家化肥厂实习的机会。
这段实习经历,不仅让我深入了解了化肥生产的工艺流程和实际操作,还帮助我进一步了解了化肥工业的发展现状和未来趋势。
在这____字的篇幅中,我将分享我在化肥厂实习期间的所见所闻和所思所感。
首先,我要感谢这家化肥厂给予我实习的机会。
作为一名大三的学生,我对真实的工作环境和实践操作缺乏经验,通过这次实习,我得以亲身体验化肥生产的全部过程。
由于化肥厂没有实习生的常规岗位,我被分配到了生产车间进行操作工的工作。
这是一个非常重要的工作岗位,因为生产车间是化肥生产的核心环节。
在生产车间的实习期间,我主要负责检查并维护设备的运行状况,参与化肥生产的每个环节。
这个工作对我而言是一个挑战,因为我之前没有接触过这样规模的化肥厂。
然而,我的导师和其他员工都非常热情和耐心地帮助我适应工作,并向我解释每个环节的工艺流程。
通过实际操作和和他们的指导,我逐渐熟悉了化肥生产的各个环节。
首先是原料处理,化肥的生产需要大量的原材料,其中主要包括氮、磷、钾等元素,通过不同的工艺流程组合成各种化肥产品。
在厂区内,我看到了数十个储存和输送原材料的大罐和管道,这些设备保证了原料在生产过程中的供应。
通过参与原料处理环节,我深刻地感受到了原料质量的重要性,只有原料质量达到要求,才能保证产品质量。
其次是反应过程,化肥的生产涉及到多道化学反应,这些反应需要精确的控制温度、压力和催化剂等因素。
在实习期间,我亲眼目睹了反应釜内的化学反应,不仅了解了反应原理和过程,而且深入了解了控制参数对反应的影响。
这个环节对我的挑战是确保反应的安全和高效进行,因为任何小的偏差都可能导致反应失败或产品质量下降。
最后是产品精炼和包装,化肥生产后需要进行精炼和包装,以提高产品的纯度和质量,并为销售做准备。
在这个环节中,我学到了如何使用各种化学和物理方法对产品进行处理,以去除杂质和提高产品的质量。
化肥厂实习报告一千五百字
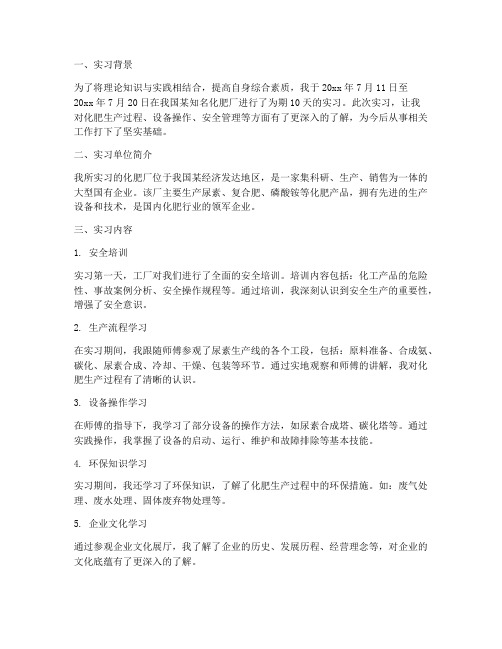
为了将理论知识与实践相结合,提高自身综合素质,我于20xx年7月11日至20xx年7月20日在我国某知名化肥厂进行了为期10天的实习。
此次实习,让我对化肥生产过程、设备操作、安全管理等方面有了更深入的了解,为今后从事相关工作打下了坚实基础。
二、实习单位简介我所实习的化肥厂位于我国某经济发达地区,是一家集科研、生产、销售为一体的大型国有企业。
该厂主要生产尿素、复合肥、磷酸铵等化肥产品,拥有先进的生产设备和技术,是国内化肥行业的领军企业。
三、实习内容1. 安全培训实习第一天,工厂对我们进行了全面的安全培训。
培训内容包括:化工产品的危险性、事故案例分析、安全操作规程等。
通过培训,我深刻认识到安全生产的重要性,增强了安全意识。
2. 生产流程学习在实习期间,我跟随师傅参观了尿素生产线的各个工段,包括:原料准备、合成氨、碳化、尿素合成、冷却、干燥、包装等环节。
通过实地观察和师傅的讲解,我对化肥生产过程有了清晰的认识。
3. 设备操作学习在师傅的指导下,我学习了部分设备的操作方法,如尿素合成塔、碳化塔等。
通过实践操作,我掌握了设备的启动、运行、维护和故障排除等基本技能。
4. 环保知识学习实习期间,我还学习了环保知识,了解了化肥生产过程中的环保措施。
如:废气处理、废水处理、固体废弃物处理等。
5. 企业文化学习通过参观企业文化展厅,我了解了企业的历史、发展历程、经营理念等,对企业的文化底蕴有了更深入的了解。
1. 安全生产意识通过实习,我深刻认识到安全生产的重要性。
在生产过程中,我们要严格遵守安全操作规程,确保自身和他人的生命安全。
2. 理论与实践相结合实习让我将所学理论知识与实际生产相结合,提高了自己的实践能力。
在今后的工作中,我将不断学习,努力提高自己的综合素质。
3. 团队合作精神在实习过程中,我与同事们互相帮助、共同进步,培养了良好的团队合作精神。
在今后的工作中,我将充分发挥团队协作的力量,为企业发展贡献力量。
化肥厂实习报告

化肥厂实习报告
在化肥厂进行为期一个月的实习,让我对化肥生产过程有了更深入的了解。
在
这段时间里,我深入参观了化肥生产线,学习了化肥的生产工艺和技术,也了解了化肥行业的发展现状和未来趋势。
首先,化肥厂的生产线非常复杂,需要经过多道工序才能完成。
从原料的采购、储存,到生产过程中的混合、反应、干燥,再到包装和运输,每一个环节都需要严格控制,以确保化肥的质量和安全。
在实习期间,我有幸参与了生产线的各个环节,亲身感受到了化肥生产的复杂性和精细化要求。
其次,化肥的生产工艺涉及到许多化学原理和技术。
在实习期间,我学习了化
肥的基本成分和配比,了解了不同种类化肥的生产工艺和特点。
同时,我还学习了化肥生产中常用的设备和仪器,掌握了化肥生产过程中的常见问题处理方法。
这些知识和技能的学习,为我将来从事化肥生产和研发工作打下了坚实的基础。
此外,我还了解了化肥行业的发展现状和未来趋势。
随着农业现代化的推进和
农业生产的需求不断增长,化肥作为农业生产的重要支撑,市场需求量不断增加。
同时,化肥行业也在不断进行技术创新和产业升级,推动行业的可持续发展。
在实习期间,我参与了一些关于化肥行业发展的讨论和学习,对化肥行业的前景有了更清晰的认识。
总的来说,这段时间的化肥厂实习经历让我受益匪浅。
通过实践学习,我不仅
对化肥生产过程有了更深入的了解,也学到了许多实用的技能和知识。
同时,我也对化肥行业的发展有了更清晰的认识,为我未来的职业发展指明了方向。
希望在将来的工作中,能够将这些所学所得充分发挥,为化肥行业的发展做出自己的贡献。
化肥厂的实习报告总结

化肥厂实习报告总结首先,我要感谢学院领导和老师给我提供了一次宝贵的实习机会,让我能够深入化肥厂进行实践学习。
这次实习不仅让我对化肥生产过程有了更直观的了解,还使我丰富了专业知识,提高了自己的综合素质。
以下是我在化肥厂实习期间的一些收获和体会。
一、实习基本情况实习期间,我们参观了化肥厂的各个生产车间,如转化、脱碳、碳化、合成氨和尿素合成车间等。
通过实地观看和听取工人师傅的讲解,我对化肥生产的整个流程有了更加清晰的认识。
同时,我们还学习了化工厂的安全知识和环保要求,了解了化肥生产过程中可能出现的安全隐患及应对措施。
二、实习单位的介绍化肥厂作为我国重要的基础化工企业,在国民经济中占有重要地位。
实习单位承担着化肥的科研、生产、销售等工作,为我国农业发展做出了巨大贡献。
在实习过程中,我们深刻感受到了化肥厂严谨的工作氛围和员工们敬业的精神风貌。
三、实习中的收获和体会1. 专业知识的丰富:通过实习,我对化肥生产过程中的化学反应、设备原理和操作技术有了更深入的了解,使我的专业知识得到了巩固和提高。
2. 实践能力的提升:在实习过程中,我们亲自参与了部分生产操作,提高了自己的实践能力。
同时,通过观察和分析生产过程中的问题,锻炼了我们的问题解决能力。
3. 团队合作与沟通能力的培养:实习期间,我们与工人师傅、同学和老师们密切合作,共同解决生产中的问题。
这使我更加明白了团队合作和沟通的重要性。
4. 安全意识与环保意识的增强:实习过程中,我们深入了解了化肥生产过程中的安全问题和环保要求,使我更加重视安全生产和环境保护。
四、今后的努力方向1. 深入学习专业知识,提高自己的理论水平。
2. 加强实践操作能力,为今后的工作打下坚实基础。
3. 注重团队合作与沟通,提升自己的综合素质。
4. 强化安全意识与环保意识,为我国化肥产业的可持续发展贡献力量。
总之,这次化肥厂实习让我受益匪浅。
在今后的学习和工作中,我将不断努力,充分发挥所学知识,为我国化肥产业的发展贡献自己的力量。
化肥厂实习心得

化肥厂实习心得实习时间:____年7月1日至____年7月31日实习地点:化肥厂一、实习目的本次实习的主要目的是通过在化肥厂实习,了解化肥生产过程和工作流程,提升对化肥生产技术和管理的认识,以及培养实践操作和解决问题的能力。
二、实习内容1.了解化肥生产工艺流程:在实习的第一天,我参观了化肥厂的生产车间,了解了化肥的制作过程。
首先是原料进料、炒料和混料,然后是粉碎、筛分和干燥,最后是造粒和包装。
通过参观和听取导师的讲解,我对化肥的生产过程有了更深入的了解。
2.学习化肥质量检测方法:在实习期间,我还学习了化肥质量检测的方法。
我了解了不同化肥品种的检测指标和方法,例如氮、磷、钾含量的检测,PH值的测定等。
我在实验室进行了一系列的实验,学习了使用仪器设备进行化肥质量检测的技术。
3.参与化肥生产操作:在实习的后期,我有机会参与化肥生产的一些操作。
我参与了化肥的配料和混料过程,学习了如何准确地称量和混合化肥原料。
我还参与了化肥的造粒和包装过程,亲自操作设备完成化肥的生产。
这些实践操作使我进一步了解了化肥生产过程中的操作和注意事项。
4.实习报告撰写:在实习结束后,我根据自己的实习经验和所学知识,撰写了一份实习报告。
报告中包括了化肥生产过程的介绍、化肥质量检测方法的学习和实践、参与化肥生产的操作和体会等内容。
通过撰写实习报告,我进一步整理和总结了实习期间所学的知识和经验。
三、实习收获通过在化肥厂的实习,我获得了以下收获:1.了解化肥生产的全过程:通过参观和实践,我对化肥的生产过程有了更全面和深入的了解。
我了解了从原料进料到最终产品包装的整个过程,对化肥生产的工艺流程有了清晰的认识。
2.学习化肥质量检测的方法:在实验室实习的过程中,我学习了化肥质量检测的方法和技术。
我了解了不同化肥品种的检测指标和方法,掌握了一些常用的仪器设备的使用方法。
3.锻炼实践操作能力:在参与化肥生产的操作中,我锻炼了实践操作的能力。
通过亲自操作设备和参与生产过程,我学会了如何准确地操作和控制化肥生产设备,提高了自己的实际操作技能。
化肥厂实习报告范文

实习报告一、实习单位简介实习单位为我所在的某化肥厂,该化肥厂是一家集化肥研发、生产、销售为一体的综合性企业,主要生产氮肥、磷肥、钾肥等系列产品。
厂区占地面积广阔,拥有现代化的生产设备和技术,员工队伍庞大,是我省化肥行业的龙头企业。
二、实习目的和意义实习的目的在于将课堂上学到的理论知识与实际工作相结合,提高自己的实践能力和综合素质。
通过实习,我能够更好地了解化肥生产的过程,掌握化肥生产的基本技能,为将来的学习和工作打下坚实的基础。
三、实习内容和过程在实习期间,我参与了化肥生产的全过程,包括原料准备、生产操作、产品包装和销售等环节。
在实习过程中,我严格遵守实习单位的规章制度,认真履行实习岗位职责,虚心向工人师傅请教,努力提高自己的实际操作能力。
1.原料准备:我了解了化肥原料的来源、性质和用途,参与了原料的储存、输送和预处理等工作。
2.生产操作:我在工人师傅的指导下,学会了操作化肥生产设备,了解了生产工艺流程,参与了生产过程中的各项操作。
3.产品包装:我了解了化肥产品的包装要求和技术,参与了产品包装线的操作,确保产品包装的质量和美观。
4.销售环节:我了解了化肥产品的市场销售策略和渠道,参与了销售业务的开展,提高了自己的销售技巧。
四、实习收获和体会通过实习,我收获颇丰,具体表现在以下几个方面:1.掌握了化肥生产的基本工艺流程和操作技能,提高了自己的实践能力。
2.了解了化肥行业的市场现状和发展趋势,为将来的学习和工作提供了有益的参考。
3.学会了与工人师傅沟通、协作,培养了自己的团队精神和待人处事的能力。
4.深刻认识到安全的重要性,了解了化肥生产中的安全知识和措施,提高了自己的安全意识。
五、实习总结通过化肥厂实习,我将理论知识与实际工作相结合,提高了自己的实践能力和综合素质。
在实习过程中,我深刻认识到学习的重要性,努力提高自己的实际操作能力。
同时,我也学会了与团队合作、待人处事,为将来的学习和工作打下了坚实的基础。
2024年化肥厂实习心得(二篇)
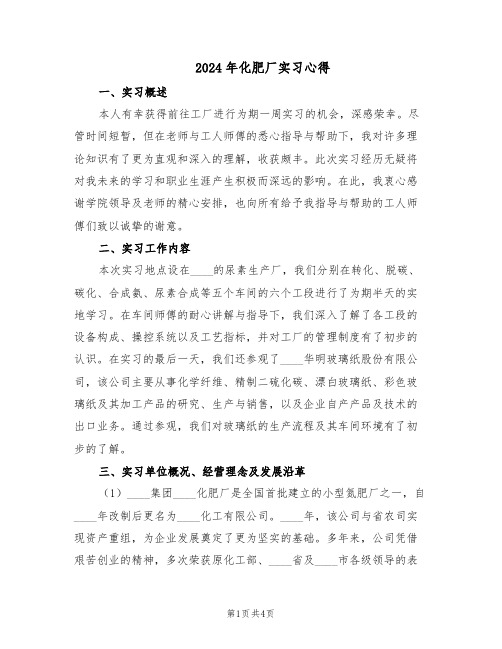
2024年化肥厂实习心得一、实习概述本人有幸获得前往工厂进行为期一周实习的机会,深感荣幸。
尽管时间短暂,但在老师与工人师傅的悉心指导与帮助下,我对许多理论知识有了更为直观和深入的理解,收获颇丰。
此次实习经历无疑将对我未来的学习和职业生涯产生积极而深远的影响。
在此,我衷心感谢学院领导及老师的精心安排,也向所有给予我指导与帮助的工人师傅们致以诚挚的谢意。
二、实习工作内容本次实习地点设在____的尿素生产厂,我们分别在转化、脱碳、碳化、合成氨、尿素合成等五个车间的六个工段进行了为期半天的实地学习。
在车间师傅的耐心讲解与指导下,我们深入了解了各工段的设备构成、操控系统以及工艺指标,并对工厂的管理制度有了初步的认识。
在实习的最后一天,我们还参观了____华明玻璃纸股份有限公司,该公司主要从事化学纤维、精制二硫化碳、漂白玻璃纸、彩色玻璃纸及其加工产品的研究、生产与销售,以及企业自产产品及技术的出口业务。
通过参观,我们对玻璃纸的生产流程及其车间环境有了初步的了解。
三、实习单位概况、经营理念及发展沿革(1)____集团____化肥厂是全国首批建立的小型氮肥厂之一,自____年改制后更名为____化工有限公司。
____年,该公司与省农司实现资产重组,为企业发展奠定了更为坚实的基础。
多年来,公司凭借艰苦创业的精神,多次荣获原化工部、____省及____市各级领导的表彰,包括“六好企业”、“精神文明工厂”、“全国环境优美工厂”等殊荣。
裕农牌碳铵、尿素等产品更是荣获部优、省优称号。
自____年起,公司不断引进先进技术进行技术改造,采用多套先进的进口和国产DCS计算机控制系统,使得产品产量与质量持续提升,成本不断降低。
目前,公司已具备年产____万吨合成氨、____万吨尿素、____万吨碳铵、____万吨复合肥的化肥生产能力。
在“质量第一、用户至上”的经营宗旨指导下,公司产品深受用户好评与市场青睐,多次获得行业认可与表彰。
化肥厂认识实习报告

一、实习概述随着我国农业现代化进程的加快,化肥产业作为支撑农业发展的关键产业,其重要性日益凸显。
为了更好地了解化肥生产过程,提高自身实践能力,我于2023年8月1日至8月15日在某大型化肥厂进行了为期两周的认识实习。
在此期间,我深入了解了化肥生产的基本流程、工艺原理以及安全生产等方面的知识,收获颇丰。
二、实习单位简介某化肥厂成立于上世纪80年代,是我国较早的化肥生产企业之一。
经过多年的发展,该厂已成为一家集化肥研发、生产、销售为一体的大型企业。
厂区占地面积约1000亩,员工1000余人。
主要生产尿素、复合肥、磷酸二铵等化肥产品,产品销往全国各地。
三、实习内容1. 安全生产教育实习的第一天,工厂对全体实习生进行了安全生产教育。
通过观看安全事故案例视频、讲解安全生产知识,使我对化工生产过程中的安全隐患有了更深刻的认识。
同时,学习了如何正确使用防护用品,提高自我保护意识。
2. 生产工艺流程学习在实习期间,我跟随技术人员参观了化肥生产车间,了解了尿素生产的基本流程。
主要包括:合成氨、转化、脱碳、碳化、合成、冷却、造粒、干燥、包装等环节。
通过实地观察和讲解,我对化肥生产的各个环节有了直观的认识。
3. 设备操作与维护在实习过程中,我学习了化肥生产设备的基本操作和维护方法。
包括合成塔、转化炉、碳化塔、合成氨压缩机等设备的操作原理、安全注意事项及故障排除方法。
通过实践操作,提高了我的动手能力。
4. 环保知识学习化肥生产过程中会产生大量的废气、废水、废渣等污染物。
在实习期间,我了解了工厂在环保方面的措施,如废气处理、废水处理、废渣处理等。
这使我认识到,环保是企业可持续发展的重要保障。
5. 企业文化学习通过参观企业文化展示馆,我了解了企业的历史、发展历程、企业精神等。
这使我更加坚定了为企业发展贡献力量的信念。
四、实习收获1. 理论与实践相结合通过这次实习,我将课本上的理论知识与实际生产过程相结合,加深了对化肥生产过程的理解,提高了自己的实践能力。
化肥厂的实习报告总结

一、实习背景在2023年的暑假,我有幸参加了化肥厂的实习活动。
这次实习是在学院的组织下,旨在让我们这些即将步入社会的大学生,能够将理论知识与实际操作相结合,加深对化工行业特别是化肥生产流程的理解。
实习期间,我在厂领导的关心和同事们的帮助下,不仅学到了丰富的专业知识,也体验了职场的生活。
二、实习内容1. 安全教育与培训实习的第一天,我们便接受了全面的安全教育与培训。
工厂的技术骨干详细讲解了化工厂的安全操作规程,强调了化工产品的危险性,尤其是硫酸、氨气等易引起中毒或爆炸的化学品。
通过这次培训,我深刻认识到安全生产的重要性。
2. 质量检测与环保由于我们专业是分析检测方向,因此实习的重点之一是学习化工产品的质量检测。
工人师傅详细介绍了硫酸、氮肥等产品的检测方法。
此外,环保问题也是化肥厂不可忽视的环节,我们学习了硫酸尾气处理、污水处理等环保措施。
3. 生产工艺与设备在实习期间,我们参观了化肥生产的主要环节,包括原料的预处理、反应过程、产品的分离与纯化等。
同时,我们还了解了各种生产设备的工作原理和操作方法。
4. 销售与市场除了生产环节,我们还了解了化肥产品的销售和市场情况。
通过参观销售部门,我们学习了如何进行市场调研、客户沟通和销售策略的制定。
三、实习体会1. 理论与实践相结合通过这次实习,我深刻体会到理论知识与实际操作相结合的重要性。
在课堂上学习到的知识,在实习过程中得到了验证和拓展。
2. 团队协作与沟通在实习过程中,我学会了如何与同事、师傅们进行有效沟通,共同完成工作任务。
团队协作能力的提升,对我今后的工作具有重要意义。
3. 职业素养与责任感实习让我认识到,作为一名化工行业从业者,必须具备高度的职业素养和责任感。
安全生产、环境保护、产品质量等都是我们不可忽视的责任。
4. 终身学习与适应能力化工行业是一个不断发展的行业,新技术、新工艺层出不穷。
在实习过程中,我意识到终身学习的重要性,以及适应行业发展的能力。
化肥有限公司毕业实习报告
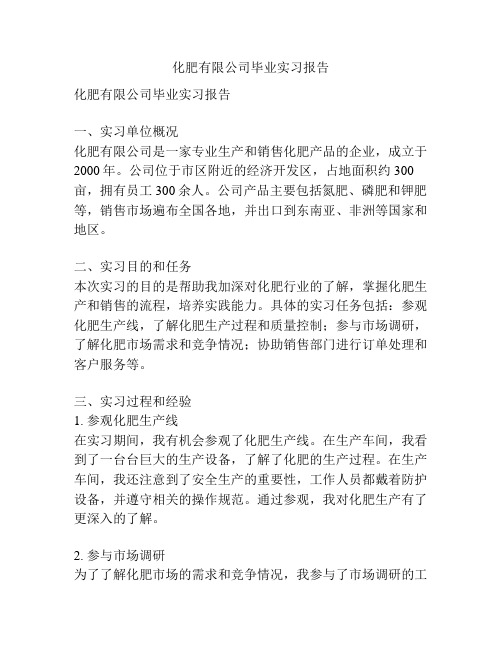
化肥有限公司毕业实习报告化肥有限公司毕业实习报告一、实习单位概况化肥有限公司是一家专业生产和销售化肥产品的企业,成立于2000年。
公司位于市区附近的经济开发区,占地面积约300亩,拥有员工300余人。
公司产品主要包括氮肥、磷肥和钾肥等,销售市场遍布全国各地,并出口到东南亚、非洲等国家和地区。
二、实习目的和任务本次实习的目的是帮助我加深对化肥行业的了解,掌握化肥生产和销售的流程,培养实践能力。
具体的实习任务包括:参观化肥生产线,了解化肥生产过程和质量控制;参与市场调研,了解化肥市场需求和竞争情况;协助销售部门进行订单处理和客户服务等。
三、实习过程和经验1. 参观化肥生产线在实习期间,我有机会参观了化肥生产线。
在生产车间,我看到了一台台巨大的生产设备,了解了化肥的生产过程。
在生产车间,我还注意到了安全生产的重要性,工作人员都戴着防护设备,并遵守相关的操作规范。
通过参观,我对化肥生产有了更深入的了解。
2. 参与市场调研为了了解化肥市场的需求和竞争情况,我参与了市场调研的工作。
我负责收集和整理市场数据,包括各类化肥产品的价格、市场份额、市场规模等信息。
通过市场调研,我了解到化肥市场需求较大,但也存在激烈的竞争。
在市场调研中,我锻炼了自己的数据分析和整理能力。
3. 协助销售部门进行订单处理和客户服务在销售部门,我负责协助处理订单和提供客户服务。
我学习了订单处理的流程,包括接收订单、确认订单、安排生产和发货等。
同时,我也参与了客户服务的工作,通过电话、邮件等方式与客户进行沟通,解答他们的疑问和提供技术支持。
通过这些工作,我提高了自己的沟通能力和团队合作能力。
四、实习中遇到的挑战和解决方法在实习过程中,我遇到了一些困难和挑战,例如对于化肥生产的流程和技术了解不够、处理订单时遇到的问题等。
在面对这些困难时,我积极主动地向公司的老师和同事请教,并通过查阅相关资料和参加培训课程来提高自己的专业知识和实践能力。
同时,我也改善了自己的学习方法和沟通方式,逐渐克服了困难。
化肥厂实习报告(推荐14篇)
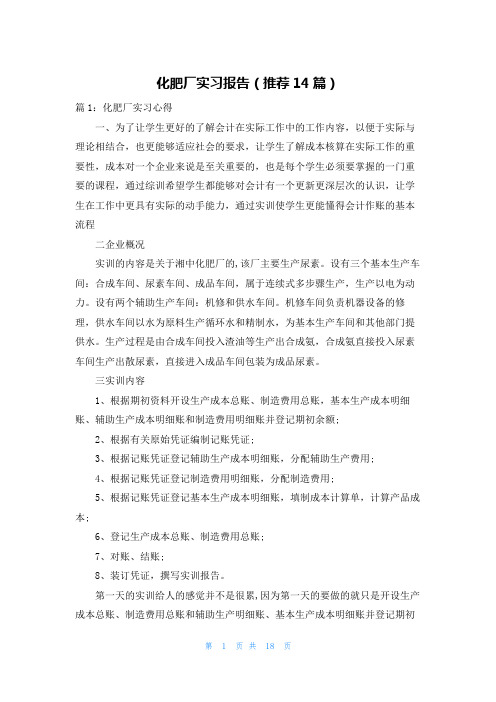
化肥厂实习报告(推荐14篇)篇1:化肥厂实习心得一、为了让学生更好的了解会计在实际工作中的工作内容,以便于实际与理论相结合,也更能够适应社会的要求,让学生了解成本核算在实际工作的重要性,成本对一个企业来说是至关重要的,也是每个学生必须要掌握的一门重要的课程,通过综训希望学生都能够对会计有一个更新更深层次的认识,让学生在工作中更具有实际的动手能力,通过实训使学生更能懂得会计作账的基本流程二企业概况实训的内容是关于湘中化肥厂的,该厂主要生产尿素。
设有三个基本生产车间:合成车间、尿素车间、成品车间,属于连续式多步骤生产,生产以电为动力。
设有两个辅助生产车间:机修和供水车间。
机修车间负责机器设备的修理,供水车间以水为原料生产循环水和精制水,为基本生产车间和其他部门提供水。
生产过程是由合成车间投入渣油等生产出合成氨,合成氨直接投入尿素车间生产出散尿素,直接进入成品车间包装为成品尿素。
三实训内容1、根据期初资料开设生产成本总账、制造费用总账,基本生产成本明细账、辅助生产成本明细账和制造费用明细账并登记期初余额;2、根据有关原始凭证编制记账凭证;3、根据记账凭证登记辅助生产成本明细账,分配辅助生产费用;4、根据记账凭证登记制造费用明细账,分配制造费用;5、根据记账凭证登记基本生产成本明细账,填制成本计算单,计算产品成本;6、登记生产成本总账、制造费用总账;7、对账、结账;8、装订凭证,撰写实训报告。
第一天的实训给人的感觉并不是很累,因为第一天的要做的就只是开设生产成本总账、制造费用总账和辅助生产明细账、基本生产成本明细账并登记期初余额,然后就是根据实训资料上的原始凭证编制记账凭证,都是一些财务会计方面的知识,所以觉得不是很难,感觉也还蛮好的。
到第二天的时候,就开始分配计算辅助生产费用,制造费用并登记明细账。
分配辅助成产费用采用的是交互分配法,其中,机修车间的间接费用不通过“制造费用”账户核算,其辅助生产成本采用多栏式账,费用项目进行明细核算;而供水车间设“直接材料、燃料及动力、直接人工、制造费用”四个成本项目,间接费用通过“制造费用”账户核算,采用品种法计算循环水和精制水的成本,供水车间制造费用按工时比例法分配。
化肥厂实习心得范文

化肥厂实习心得范文我在化肥厂进行为期两个月的实习,这段实习经历不仅让我对化肥行业有了更深入的了解,还提升了我的实践能力和团队合作意识。
以下是我在化肥厂实习的心得体会。
首先,在实习期间,我有幸参观了整个化肥生产线,深入了解了从原料采购到成品包装的全过程。
我了解到化肥的生产流程需要经历原料处理、配料、反应、过滤、结晶、干燥等多个环节,每个环节都非常重要,任何一个环节的问题都可能会影响到产品的质量。
通过参观和学习,我对化肥的生产过程有了更深入的认识,也明白了保证产品质量的重要性。
其次,在实习期间,我有机会参与了部分化肥产品的质检工作。
化肥产品的质检工作非常细致,需要对产品进行外观、成分、密度、颗粒度等多个方面的检测。
我从中学到了如何正确操作化肥质检设备,并且了解了质检报告的编写流程。
通过质检工作,我认识到质量控制是化肥厂必不可少的一环,只有做好质检工作,才能确保产品的合格率和市场竞争力。
另外,在实习期间,我还参与了化肥生产的实际操作工作。
化肥生产过程需要使用各种设备和机器,我学习了如何正确操作这些设备,并且了解了一些常见故障的排除方法。
在实际操作中,我充分感受到了工作的细致性和复杂性,需要不断地积累经验并灵活应对各种问题。
同时,我也明白了团队合作的重要性,只有团队成员之间相互配合,才能顺利地完成工作任务。
除了技术方面的学习,我还通过与同事们的交流和观察,学到了一些职场生存技巧。
在化肥厂实习期间,我遇到了很多问题和挑战,但是通过与同事们的交流,我得到了很多帮助和指导。
我发现在职场中,良好的沟通和合作能力是非常重要的,只有与他人保持良好的关系,才能得到更多的支持和帮助。
总结来说,化肥厂实习的经历让我收获颇丰。
通过参观、学习和实践,我深入了解了化肥的生产过程和质检工作,并学会了正确操作相关设备。
同时,我也体会到了团队合作和职场沟通的重要性。
这段实习经历不仅为我提供了宝贵的实践机会,还帮助我提升了实践能力和团队合作意识。
化肥厂实习报告

化肥厂实习报告目录1. 概述1.1 背景介绍1.2 实习单位简介1.3 实习内容2. 实习收获2.1 专业技能提升2.2 求职竞争力增强3. 实习心得体会3.1 工作中的困难与挑战3.2 收获与成长3.3 未来规划1. 概述1.1 背景介绍在化肥厂实习期间,我通过实际操作和学习,加深了对化肥生产流程和技术的了解,提升了自己的专业知识和实践能力。
1.2 实习单位简介化肥厂是一家专业生产化肥产品的企业,拥有先进的生产设备和技术团队。
实习期间,我有幸能够深入了解其生产流程和质量管理体系。
1.3 实习内容在化肥厂实习期间,我的主要工作内容包括参与化肥生产过程中的操作调整、质量监控和现场管理工作,以及参与相关技术改进和质量控制项目。
2. 实习收获2.1 专业技能提升通过实习,我熟练掌握了化肥生产中的操作流程和技术要点,提升了自己在化工领域的实际操作能力和生产管理能力。
2.2 求职竞争力增强实习经历丰富了我的实践经验,增强了自身的综合素质和团队合作能力,为将来的就业和发展打下了坚实的基础。
3. 实习心得体会3.1 工作中的困难与挑战在化肥厂实习期间,我面临过生产中的一些技术难题和管理挑战,但通过团队合作和自身努力,最终都得到了解决,并取得了一定的成果。
3.2 收获与成长通过实习,我不仅提升了自己的专业技能和实践能力,还培养了解决问题的能力和团队协作意识,使自己得到了全面的成长和发展。
3.3 未来规划在未来的学习和工作中,我将继续努力提升自己的专业能力和实践经验,不断完善自己,为实现更高的职业目标而努力奋斗。
化肥厂实习报告
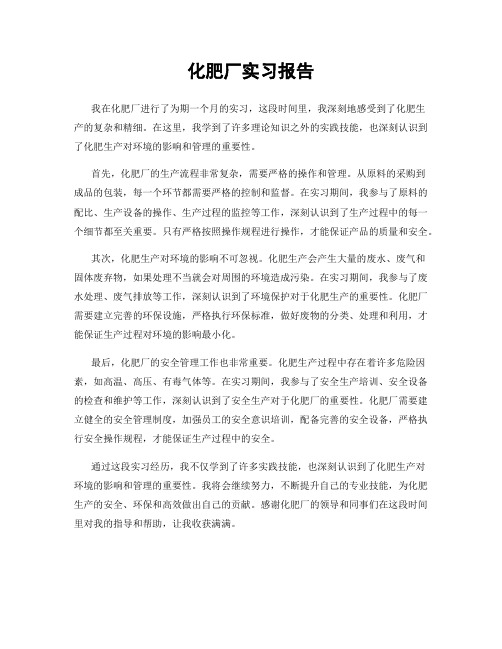
化肥厂实习报告我在化肥厂进行了为期一个月的实习,这段时间里,我深刻地感受到了化肥生产的复杂和精细。
在这里,我学到了许多理论知识之外的实践技能,也深刻认识到了化肥生产对环境的影响和管理的重要性。
首先,化肥厂的生产流程非常复杂,需要严格的操作和管理。
从原料的采购到成品的包装,每一个环节都需要严格的控制和监督。
在实习期间,我参与了原料的配比、生产设备的操作、生产过程的监控等工作,深刻认识到了生产过程中的每一个细节都至关重要。
只有严格按照操作规程进行操作,才能保证产品的质量和安全。
其次,化肥生产对环境的影响不可忽视。
化肥生产会产生大量的废水、废气和固体废弃物,如果处理不当就会对周围的环境造成污染。
在实习期间,我参与了废水处理、废气排放等工作,深刻认识到了环境保护对于化肥生产的重要性。
化肥厂需要建立完善的环保设施,严格执行环保标准,做好废物的分类、处理和利用,才能保证生产过程对环境的影响最小化。
最后,化肥厂的安全管理工作也非常重要。
化肥生产过程中存在着许多危险因素,如高温、高压、有毒气体等。
在实习期间,我参与了安全生产培训、安全设备的检查和维护等工作,深刻认识到了安全生产对于化肥厂的重要性。
化肥厂需要建立健全的安全管理制度,加强员工的安全意识培训,配备完善的安全设备,严格执行安全操作规程,才能保证生产过程中的安全。
通过这段实习经历,我不仅学到了许多实践技能,也深刻认识到了化肥生产对环境的影响和管理的重要性。
我将会继续努力,不断提升自己的专业技能,为化肥生产的安全、环保和高效做出自己的贡献。
感谢化肥厂的领导和同事们在这段时间里对我的指导和帮助,让我收获满满。
参观化肥厂实习报告

一、实习简述为增强实践能力,提高专业技能,拓宽知识视野,我于2021年8月1日至8月5日参加了化肥厂的实习。
此次实习是在我国某知名化肥厂进行,为期五天。
在这五天里,我跟随厂里的技术骨干和工人师傅们,对化肥的生产过程、设备操作、安全管理等方面进行了深入学习。
二、实习过程介绍1. 实习第一天实习第一天,厂里安排了安全培训。
在培训课上,技术骨干师傅详细讲解了化肥生产过程中的安全注意事项,包括易燃易爆物质、有毒有害气体等。
通过培训,我对化肥生产的安全问题有了更深入的了解,认识到安全操作的重要性。
2. 实习第二天实习第二天,我跟随工人师傅参观了化肥生产车间。
在参观过程中,师傅们详细介绍了化肥的生产流程,包括原料预处理、合成、尿素合成、尿素造粒等环节。
我还了解了各种设备的工作原理和操作方法。
3. 实习第三天实习第三天,我参加了化肥生产线的实际操作。
在师傅的指导下,我学习了如何操作尿素造粒设备,掌握了设备启动、运行、维护等基本技能。
4. 实习第四天实习第四天,我跟随技术骨干师傅参观了化肥厂的研发中心。
在这里,我了解到化肥厂在技术创新、产品研发等方面取得的成果,如新型化肥、生物肥料等。
5. 实习第五天实习第五天,我参加了化肥厂的生产调度会议。
在会议上,我了解到化肥厂的生产计划、原材料采购、产品销售等方面的情况。
同时,我还与厂里的技术人员进行了交流,就生产过程中遇到的问题进行了探讨。
三、实习心得体会1. 安全生产意识的重要性通过此次实习,我深刻认识到安全生产意识的重要性。
在化肥生产过程中,存在许多易燃易爆、有毒有害物质,稍有不慎就会发生事故。
因此,我们必须时刻保持警惕,严格遵守安全操作规程。
2. 专业技能的提升实习过程中,我学习了化肥生产的基本原理、设备操作方法等,使我的专业技能得到了很大提升。
我相信,这些知识将在今后的工作中发挥重要作用。
3. 团队合作精神在实习过程中,我与同事们相互帮助、共同进步,形成了良好的团队氛围。
化肥厂实习报告
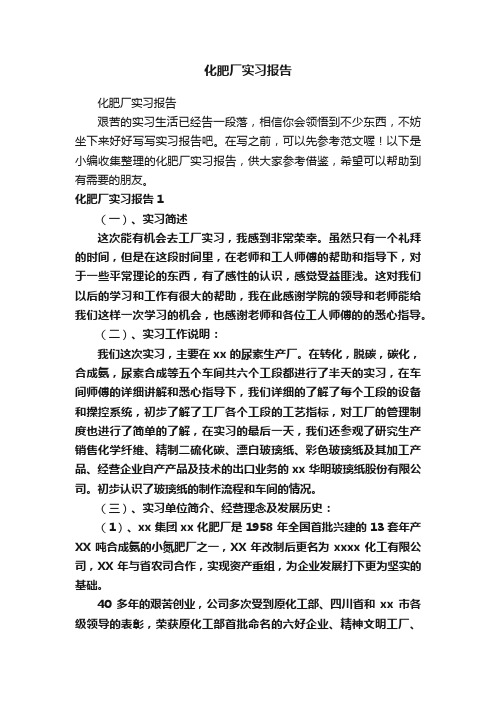
化肥厂实习报告化肥厂实习报告艰苦的实习生活已经告一段落,相信你会领悟到不少东西,不妨坐下来好好写写实习报告吧。
在写之前,可以先参考范文喔!以下是小编收集整理的化肥厂实习报告,供大家参考借鉴,希望可以帮助到有需要的朋友。
化肥厂实习报告1(一)、实习简述这次能有机会去工厂实习,我感到非常荣幸。
虽然只有一个礼拜的时间,但是在这段时间里,在老师和工人师傅的帮助和指导下,对于一些平常理论的东西,有了感性的认识,感觉受益匪浅。
这对我们以后的学习和工作有很大的帮助,我在此感谢学院的领导和老师能给我们这样一次学习的机会,也感谢老师和各位工人师傅的的悉心指导。
(二)、实习工作说明:我们这次实习,主要在xx的尿素生产厂。
在转化,脱碳,碳化,合成氨,尿素合成等五个车间共六个工段都进行了半天的实习,在车间师傅的详细讲解和悉心指导下,我们详细的了解了每个工段的设备和操控系统,初步了解了工厂各个工段的工艺指标,对工厂的管理制度也进行了简单的了解,在实习的最后一天,我们还参观了研究生产销售化学纤维、精制二硫化碳、漂白玻璃纸、彩色玻璃纸及其加工产品、经营企业自产产品及技术的出口业务的xx华明玻璃纸股份有限公司。
初步认识了玻璃纸的制作流程和车间的情况。
(三)、实习单位简介、经营理念及发展历史:(1)、xx集团xx化肥厂是1958年全国首批兴建的13套年产XX吨合成氨的小氮肥厂之一,XX年改制后更名为xxxx化工有限公司,XX年与省农司合作,实现资产重组,为企业发展打下更为坚实的基础。
40多年的艰苦创业,公司多次受到原化工部、四川省和xx市各级领导的表彰,荣获原化工部首批命名的六好企业、精神文明工厂、全国环境优美工厂等殊荣。
裕农牌碳铵、尿素获部优、省优。
xx年以来公司不断进行技术改造,先后采用四套先进的进口和国产dcs计算机控制系统,使产品产量、质量不断提高,成本不断降低。
目前,公司具有年产10万吨合成氨、13万吨尿素、10万吨碳铵、10万吨复合肥的化肥生产能力。
化肥厂实习报告总结

一、实习背景为了深入了解我国化肥工业的发展现状,提高自己的专业素养,我于2021年6月至8月在某大型化肥厂进行了为期两个月的实习。
此次实习,我深入了解了化肥生产的全过程,包括原料准备、反应、分离、干燥、包装等环节,并对化肥行业的发展趋势进行了思考。
二、实习内容1. 实习岗位及职责实习期间,我被安排在合成车间进行实习,主要负责以下几个方面的工作:(1)了解化肥生产的基本原理和工艺流程;(2)熟悉合成车间的设备、仪表及操作规程;(3)参与化肥生产的各个环节,如原料准备、反应、分离、干燥、包装等;(4)协助车间师傅处理生产过程中出现的问题,确保生产顺利进行。
2. 实习过程(1)原料准备在原料准备环节,我学习了如何对原料进行筛选、粉碎、混合等处理,以确保原料质量符合生产要求。
同时,我还了解了原料储存、运输等方面的知识。
(2)反应在反应环节,我学习了合成氨、尿素等化肥生产的基本原理和工艺流程。
通过观察和操作,我掌握了反应过程中的温度、压力、流量等参数的控制方法,以及如何调整反应条件以获得最佳生产效果。
(3)分离分离环节是化肥生产过程中的关键环节。
我学习了如何利用冷却、结晶、过滤等方法将反应产物与未反应的原料、副产物等分离。
此外,我还了解了分离过程中可能出现的故障及处理方法。
(4)干燥干燥环节是将分离后的湿物料进行干燥处理,以获得符合质量要求的化肥产品。
我学习了干燥设备的工作原理、操作方法以及干燥过程中可能出现的故障及处理措施。
(5)包装包装环节是对干燥后的化肥产品进行包装,以保障产品在运输、储存过程中的质量。
我了解了包装材料的选用、包装设备的使用以及包装过程中的注意事项。
三、实习收获1. 理论联系实际通过实习,我深刻体会到理论知识在实践中的重要性。
在实习过程中,我不仅巩固了课堂所学知识,还学会了如何将理论知识运用到实际生产中。
2. 提高动手能力在实习过程中,我亲自动手操作设备,处理生产过程中出现的问题,提高了自己的动手能力。
- 1、下载文档前请自行甄别文档内容的完整性,平台不提供额外的编辑、内容补充、找答案等附加服务。
- 2、"仅部分预览"的文档,不可在线预览部分如存在完整性等问题,可反馈申请退款(可完整预览的文档不适用该条件!)。
- 3、如文档侵犯您的权益,请联系客服反馈,我们会尽快为您处理(人工客服工作时间:9:00-18:30)。
一、辽河化肥厂概况 (2)二、产品在国民经济中的地位、意义 (2)三、原料,主要中间品,产品的性质 (3)四、产品的生产方法、基本原理(合成) (4)五、工艺流程图 (5)六、主要设备特点 (7)七、氨合成工艺条件 (9)八、其他 (11)九、实习心得体会 (11)一、辽河化肥厂概况辽河化肥厂座落在辽河三角洲,是依附于辽河油田产品——天然气为原料的大型石油化工企业,是名列我国500家大型企业之榜者。
企业上市后隶属于深圳辽河通达化工股份有限公司,现有员工1200人。
自投产以来连年超设计产量,年上缴利税一亿多元,居全国同行业先进水平。
现有年生产能力:合成氨60万吨,尿素110万吨,复合肥20万吨;该厂在发展生产的同时,以加强环境管理为先导,用先进技术治理断后,使能源、资源的利用率不断提高,污染物排放量不断下降。
目前,厂总排污口日排水量约8000吨(含生活污水),行业特点主要污染物NH3—N平均在40ppm 左右,低于国家验收标准(120ppm)2倍;低于化工行业标准(80ppm)1倍;高于省地方标准(25ppm)0.6倍。
“三废”资源利用率接近100%,水的重复利用率达到了92.19%,吨氨耗水量为425m3吨氨排水量6.62m3,氨流失量0.53kg/t。
曾获得“全国环保先进企业”、“化工六好企业”、“无泄漏工厂”、“清洁文明工厂样板厂”、“花园式工厂”等荣誉称号。
二、产品在国民经济中的地位、意义氨本身除了是主要的氮肥原料外,亦是重要的化工原料,可制成各种炸药。
同时氨,尿素和硝酸也是氨基树脂,聚酰胺树脂,硝化纤维素等高分子化合物的原料。
以其为原料可以制得塑料,合成纤维,油漆,感光材料等产品。
对于一氧化碳,氢气合成气等生产氨的原料,可进行综合利用,以联产甲醇及羧基合成甲醇,醋酸,酸酐等一系列碳一化工产品,减少废物的排放,减轻对对环境的污染。
提高企业经济效益,实现可持续发展已成为当今合成氨工业生产技术发展方向。
据资料统计:1997 年世界合成氨年产量达103.9Mt。
预计2000 年产量将达111.8Mt。
其化肥用氨分别占氨产量的81.7%和82.6%。
我国1996 年合成氨产量已达30.64Mt,专家预测2000 年将达36Mt,2020 年将增加至45Mt。
即今后20 年间将增加到现在的1.5 倍。
因而合成氨的持续健康发展还有相当长的路要走。
未来我国合成氨氮肥的实物产量将会超过石油和钢铁。
合成氨工业是农业的基础。
它的发展对我国国民经济的发展有重大影响。
因此,我国现有众多的化肥生产装置应成为改造扩建增产的基础。
我国七十至九十年代先后重复引进30 多套大化肥装置,耗费巨额资金,在提高了化肥生产技术水平的同时,也受到国外的制约。
今后我国应在引进国外先进技术的基础上着力国内开发研究自力更生,走出一条具有中国特色的社会主义民族工业的发展道路。
过去引进建设一套大型化肥装置,耗资数十亿元。
当今走改造扩建增产的道路,可使投资节省1/2—2/3的巨额资金用于农田水利建设和农产品深加工,这一举措将在加快农村经济发展,提高农民生活水平,缩小城乡差距发挥重要作用。
三、原料,主要中间品,产品的性质合成氨的原料是氢气和氮气。
氮气来源于空气,可以在制氢的过程中直接加入空气,或在低温下将空气液化、分离而得;氢气来源于水或含有烃的各种燃料。
工业上普遍采用的是以焦炭煤天然气重油等燃料与水蒸气作用的气化方法。
反应方程式为3H2+N2=2NH3+Q无色气体,有刺激性恶臭味。
分子式NH3。
分子量17.03。
相对密度0.7714g/l。
熔点-77.7℃。
沸点-33.35℃。
自燃点651.11℃。
蒸气密度0.6。
蒸气压1013.08kPa(25.7℃)。
蒸气与空气混合物爆炸极限16~25%(最易引燃浓度17%)。
氨在20℃水中溶解度34%,25℃时,在无水乙醇中溶解度10%,在甲醇中溶解度16%,溶于氯仿、乙醚,是许多元素和化合物的良好溶剂。
水溶液呈碱性,0.1N水溶液PH值为11.1。
液态氨将侵蚀某些塑料制品,橡胶和涂层。
遇热、明火,难以点燃而危险性较低; 但氨和空气混合物达到上述浓度范围遇明火会燃烧和爆炸,如有油类或其它可燃性物质存在,则危险性更高四、产品的生产方法、基本原理(合成)净化后的合成气中含有氢气和氨气,在大约29.9kg/cm2G的压力和37C的温度下送至合成气压缩机103-J的进口。
此合成气压缩机是一蒸汽透平驱动的二缸,段间冷却离心式压缩机,二段缸内有一分隔开的循环叶轮。
经一段缸压缩后的合成气在段间冷却器116-C中被冷却水冷却,然后在段间氨冷器129-C中被氨冷降温,氨冷后的合成气补充气中冷凝下来的水,在段间分离罐105-F中分离出去,分离器顶部设有一根管线可以把气体回流至压缩机一段缸。
分离器底有一根管线可以把合成气中分离出来的水返回至合成气压缩机进口罐104-F,以调节其液位。
用段间冷却器和氨冷器冷却去压缩机二段缸的气体,以获得最佳的体积效率,并保证去压缩机的气体不带水,除水步骤能延长合成塔内催化剂的使用寿命,并能获得高纯度的产品氨。
五、工艺流程图流程简述1、分流进塔:反应气分成两部分进塔,一部分经塔外换热器预热,依次进入塔内换热管、中心管,送到催化剂第一床层,另一部分经环隙直接进入冷管束,两部分气体在菱形分布器内汇合,继续反应,这样使低温未反应气直接竟如冷管束,稍加热后,作为一、二段间的冷激气,从而减少冷管面积和占用空间,提高了催化剂筐的有效容积,并强化了床层温度的可调性。
同时仅有65~70%的冷气进入塔内换热器和中心管,减轻了换热器负荷,因而减少了换热面积,相对增加了有效的高压容积,也使出塔反应气温度提高(310~340℃),即回收热品位提高。
气体分流进塔还使塔阻力和系统阻力比传流程小。
2、进塔外换热器的冷气不经环隙,这样温度更低,使进水冷器的合成气温度更低(约75℃左右),提高了合成反应热的利用率,降低了水冷器的负荷和冷却水的消耗。
3、水冷后的合成气直接进入冷交管间,由上而下边冷凝边分离,液氨在重力和离心力的作用下分离,既提高了分离效果,又减小了阻力。
4、塔后放空置于水冷、冷交后,气体经连续冷却,冷凝量多,因此气体中氨含量低,惰气含量高,故放空量少,降低了原料气消耗。
5、塔前补压:循环机设于冷交之后,气体直接进塔,使合成反应处于系统压力最高点,有利于反应,同时循环机压缩的温升不消耗冷量,降低了冷冻能耗。
6、设备选用结构合理,使消耗低,运行平稳,检修量减少,工艺趋于完善。
六、主要设备特点(1)合成塔进入合成塔的其他主要由两部分组成,一部分是占气体总量65%-70%的主反应气,从塔底进入位于塔内最底层的换热器和中心管进行加热,升温至360℃-370℃,进入第一催化剂床层反应,反应温度达到470℃-480℃,,另外一部分为为热护气和冷护气的混合气体,约占总气体量的30%-35%,由下而上进入合成塔内件与壳层的环隙,从塔顶顶部进入催化剂层冷管束,被管外热气加热至250℃,上升至冷激分气盒进入催化剂第二床层。
主反应气与热护气和冷护气的混合气体在第一反应床层混合后依次进入第二、第三床层反应。
进入合成塔内件与壳层环隙的气体主要起保护作用:因为合成氨的反应条件为高温高压,而塔设备的材料决定了其只能在反应时承受高温或者高压,而不能同时承受高温高压,进入环隙的保护气在加压后压力和塔内的压力相当,避免了塔内件承受高压而只承受高温,同时气体处于低温状态可以吸收反应放出的热量,避免了塔的壳层承受高温而只承受高压。
反应放出的热量对保护气加热也实现了能量的充分利用。
(2)一段转化炉一段转化炉为方格式炉子,整个炉子由辐射段、过渡段、对流段、出口烟道、引风机组成。
辐射段是炉子的主体,里面设置完成转化过程的“竖琴” 系统,它由进口急风管、猪尾管、转化管、下集气管、上升管和输气总管组成、炉顶设烧嘴向下喷烧供热,对流段有多组换热器,用烟道气加热其他介质。
原料气脱硫后,则希望以比较经济的方法将原料气转化生成氢气。
原料气蒸汽混合气与镍催化剂接触,同时提高温度和压力来促进此反应。
该反应是一吸热反应,需要一段炉供给恒定的热量以维持适合一段转化反应的温度。
在一段炉和二段炉中,催化剂促使两个同时发生的平衡反应,它们是蒸汽-甲烷反应:22242222244H CO O 2H CH H CO O H CO 3+→++→++→+完全,则总反应为:如果两个反应进行的很:和一氧化碳的变换反应H CO O H CH但事实上不是这样的,二段炉出口气中含有大量的CO ,大部分未变换的CO 再变换中氧化成2CO 从而提高产氢率。
一段转化炉炉管内装有环状或圆柱状的镍催化剂,各炉管内催化剂装填应均匀,从而保证其压降相等,使通过每根转化管的气体分配均匀。
如果某根转化管的压降不正常,则可能会发生过热或转化不充分,造成操作不正常。
(3)二段转化炉二段转化炉为立式圆筒形反应器。
受压主体为碳钢制圆筒壳,两端为锥形封头,由于内部温度高,在壳外部有水夹套,这样既可降低壳体温度,也可是壳体受热均匀。
空气-蒸汽由混合器均匀喷出,工艺气则通过带孔的环形分布板,这样可保证空气-蒸汽和工艺气均匀混合燃烧。
转化炉下部为带孔的耐火金刚玉砖拼成的球形承重拱。
出一段炉的经部分转化的气体经过一段有水夹套的输送管线107-D ,沿切线方向进入二段炉(103-D )的入口室,二段转化炉进口的温度大约830C ︒。
一段转化后的气体仍含有较多的甲烷,为了进一步转化则需要更高的温度。
这个任务在内热式二段炉里完成。
在此加入空气,于是气体中的与空气中的氧燃烧2H ,同时气体中的4CH 、CO 也可能燃烧,放出大量的热,温度可达1200-1250C ︒,因此,残余的4CH 继续转化。
出口温度降到900-1000C ︒左右。
进入二段转化的空气,也为合成提供了N2。
(4)热交换器热交换器为管式换热器,进热交换器的冷气不经过合成塔的间隙,这样使温度更低,使进水冷器的合成气温度更低,提高了合成反应热利用,同时也降低了水冷器的负荷和冷却水的消耗。
(5)循环机循环机设与冷交换热气之后,气体经循环机加压后直接进塔,使合成反应处于系统压力最高点,有利于反应。
气体在设备中流动和反应都会使得整个体系的压力降低,循环机起到补充系统压力的作用七、氨合成工艺条件(1)温度:合成塔壁≤150℃进塔主气流175℃-185℃分流气出塔150℃-160℃零米360℃-380℃一段热点460℃-470℃二段进口400℃-430℃废锅进口310℃-340℃废锅出口190℃-200℃水冷进口≤75℃水冷出口≤30℃氨冷出口 0—5℃(2)压力:系统压力≤31.4 Mpa输氨压力≤1.9 Mpa放氨压力≤2.55 Mpa氨蒸发压力≤2.45 Mp a废锅蒸汽压力≤1.3 Mpa总回收压力: 0.4-0.7 Mpa (3)气体成分:补充气CO+CO2≤20PPm进塔H2/N22.0-2.8进塔CH4+Ar 20%进塔NH3%:≤2.5%八、其他转化反应炉该炉是合成氨生产的关键设备。