JB1265-85汽轮机转子和主轴真空处理的碳钢和合金钢锻件技术条件
技术标准目录1

技术标准目录世界钢号对照手册------中国标准出版社01. GB 222—84-87-02 钢的化学分析用试样取样法及成品化学成分允许偏差02. GB/T 228—87—02 金属材料室温拉伸试验方法03. GB/T 229—94 金属夏比缺口冲击试验方法04. GB/T 231.1—02 金属布氏硬度试验第1部分:试验方法(GB/T6269-97)GB/T 231.2—02 金属布氏硬度试验第2部分:硬度计的检验与校准(GB/T6269-97) GB/T 231.3—02 金属布氏硬度试验第3部分:标准硬度块的标定(GB/T6270-97)05. GB/T 699—88—99 优质碳素结构钢技术条件06. GB/T 1159—98 轴系锻件技术条件(中国船舶工业总公司)07. GB 1299—85 合金工具钢技术条件08. GB/T 1591—94 低合金高强度结构钢09. GB 1979—80 结构钢低倍组织缺陷评级图10. GB/T 3077—88—99 合金结构钢技术条件11. GB/T 3907—99 船用锻钢件超声波探伤(ZB U05 008—99)12. GB 4091—83 常规控制图 *13. GB/T 4162—84—91 锻轧钢棒超声波探伤方法14. GB 5216—85 保证淬透性结构钢技术条件15. GB/T 6402—91 钢锻件超声波检验方法16. GB 8539—87 齿轮材料及热处理质量检验的一般规定17. GB 10051.1—88 起重吊钩 *18. GB 10561—89 钢中非金属夹杂物显微评定方法19. GB 11261—89 高碳铬轴承钢化学分析法20. GB 11880—89 模锻锤和大型机械锻压机用模块技术条件21. GB/T 16180—96 职工工伤与职业病致残程度鉴定22. GB/T 17107—97 锻件用结构钢牌号和力学性能23. GB/T 19001—94 质量体系设计、开发、…和服务的质量保证模式 (旧)—00 质量管理体系要求24. JB/T 1581—96 汽轮机、汽轮发电机转子和主轴锻件超声波探伤方法25. JB/T 1582—96 汽轮机叶轮锻件超声波探伤方法26. JB/T 1265-85-93-02 25~200 MW汽轮机转子体和主轴锻件技术条件JB/T 1266-85-93-02 25~200 MW汽轮机轮盘及叶轮锻件技术条件JB/T 1267-85-93-02 50~200 MW汽轮发电机转子锻件技术条件JB/T 1268-85 -02 50~200 MW汽轮发电机无磁性护环锻件技术条件JB/T 1269-85-93-02 汽轮发电机磁性环锻件技术条件JB/T 1270-85-93-02 水轮机、水轮发电机大轴锻件技术条件JB/T 1271-85-93-02 交、直流电机轴锻件技术条件JB/T 7022—93—02 工业汽轮机转子体锻件技术条件JB/T 7023—93-02 水轮发电机镜板锻件技术条件JB/T 7025—93—04 25 MW以下汽轮机转子体和主轴锻件技术条件JB/T 7026—93-04 50 MW以下汽轮发电机转子锻件技术条件JB/T 7028—93—04 25 MW以下汽轮机轮盘及叶轮锻件技术条件JB/T 7029—93-04 50 MW以下汽轮发电机无磁性护环锻件技术条件27. JB 4249—86 锤上钢质自由锻件机械加工余量与公差28. JB/T 4385—99 锻件工艺标准汇编JB/T 9178—99 锻件工艺标准汇编JB/T 9179—99 锻件工艺标准汇编29. JB 4726~4728-94-00 压力容器用钢锻件30. JB 4730—94 超声检测31. JB 4741~4743—00 压力容器用镍铜合金热轧板材无缝管锻件32. JB/T 5000. 8—07 锻件33. JB/T 5000.15—98 锻钢件无损探险伤34. JB/T 5942—91 工程机械自由锻件通用技术条件 *35. JB/T 5944—91 工程机械热处理件通用技术条件 *36. JB/T 6031—92 工程机械钢质模锻件通用技术条件 *37. JB/T 6393—92 大型锻件用合金工具钢38. JB/T 6395—92 大型齿轮、齿圈锻件 (振华)39. JB/T 6396—92 大型合金钢锻件40. JB/T 6397—92 大型碳素结构钢锻件41. JB/T 6903—93 阀门锻钢件超声波检查方法42. JB/T 6908—93 容积式压缩机锻件技术条件43. JB/T 8888-99 环芯法测量汽轮机、汽轮发电机转子锻件残余应力的试验方法44. JB/T 9020—99 大型锻造曲轴的超声波检验45. JB/T 9638—99 汽轮机用联轴器等重要技术条件 (ZB K54 032—89) (南汽)46. ZBJ32.002—88 水压机上自由锻件复杂程度分类及折合系数47. ZBJ32 003.1~8—88 水压机上自由锻件机械加工余量与公差48. JB/ZQ 4000.7—86 锻件通用技术要求 (材料化学成分)JB/ZQ 4287—86 优质碳素结构钢JB/ZQ 4288—86 合金结构钢JB/ZQ 4292—86 弹簧钢JB/ZQ 4293—86 碳素工具钢JB/ZQ 4294—86 合金工具钢JB/ZQ 4295—86 不锈钢、耐酸、耐热锻件用钢49. QJ 501—89 不绣耐酸钢、耐热钢锻件技术条件 (航天部)50. SDZ 016—85 锻件通用技术条件 (水利电力部)51. YB/T 036.7—92 冶金设备制造通用技术条件锻件(冶金工业部)(武汉船用)52. JFSS I3-77-82-95 船用钢锻件超声波探伤标准(日本铸锻)(上重)53. DIN 17210-86 材料标准 (德国)54. 锻件和铸件的超声波探伤55. 锻钢件 (中国船级社)56. Q/HZJ 560—00 船用锻钢件技术条件(杭重)57. Q/HZJ 561—00 船用锻钢件超声波探伤(杭重)58. P3C—AG42 普通超声波探伤 (南汽)59. NB 2074 经调质的一般锻件和型钢制件技术条件 (南汽)NB 2075 经正火回火的合金钢锻件和型钢制件技术条件 (南汽)NB 2076 经正火的炭素钢锻件及型钢制件技术条件 (南汽)NB 0108 汽轮机金属材料(毛坯)技术条件总则 (南汽)60. NB 2077 氮化件和渗碳件技术条件(南汽)61. PS 84350 KA 超声波探伤(上汽600008)62. PDS 10109AA 碳钢结构型钢(上汽)63. DY-RD-E56 喷嘴组和静叶锻件外协调质热处理技术条件(上汽)64. B/HJ 408—95 调质的一般锻件和型钢制件毛坯技术条件(哈汽)65. B/HJ 410—96 中间轴和联轴器等合金钢锻件订货技术条件(哈汽)66. B/HJ 424—93 氮化件技术条件(哈汽)67. ZP 4501—95 碳钢、低合金钢锻件超声波探伤方法及评定验收标准(振华)68. Q/ZP ZJ-15—02(附件二)低合金钢锻件超声波探伤方法及评定验收标准(试行)(振华)69. ZBJ 72022—88 大型往复活塞压缩机重要锻件的超声波探伤检查(上海八一)70. Q/BQB101~190-99 宝钢企业标准71. SDD2000—001 交直流电机轴锻件供货技术协议超声波探伤及…(上海电机厂)72. SG 0712—84 空气预热器端轴超声波探伤标准 (上海臻辉)73. Q/LK 905—92 锻件超声波探伤质量标准(洛矿)74. TA 021—000A 一般公差线尺寸和角度尺寸的未注公差(天津阿尔斯通)75. BPEG BG21.JT.01~03 材料技术条件 (北京电力总厂)76. ZJ/OM 003—4102 立柱探伤验收规范(广东佛陶)77. 0—0001—9202—00 调质(正火)齿轮轴、齿轮锻件技术条件(杭汽)78. 0—0001—9202—01 渗碳、气化齿轮轴、齿轮锻件技术条件(杭汽)79. 0—0001—9001—30 耐热不锈钢(杭汽)80. 0—0001—3242—01 钢制管法兰技术条件(杭汽)81. HTA 4480—93 透平齿轮增速机主要零件制造技术条件(杭氧)82. NG 0401—00 锅炉锻件技术条件(杭锅)83. Q34—18—99 外协锻件超声波探伤验收规范(杭齿)84. Q34—31—99 外协锻件订货验收技术条件(杭齿)85. ZB T59 004—88 自卸汽车-液压缸技术条件86. FL-DGJ-2005-B 风电齿轮箱锻钢件技术条件(重庆齿轮箱有限责任公司)。
常用铸钢件技术条件

中国长江动力公司(集团)武汉汽轮发电机厂企业标准Q/CCFH3002-2002常用铸钢件技术条件2002-08-15发布2002-09-01实施武汉汽轮发电机厂前言由于我厂产品品种较多,铸钢件均有相应的标准,为了使我厂铸钢件设计、生产、检验及订货采用统一的标准,生产出符合有关国家标准及国际标准的铸钢件,以适应国内国外市场的需求,特制定本标准。
本标准参照JB/T10087-2001《汽轮机承压铸钢件技术条件》、JB/T7350-1994《轴流式水轮机不锈钢叶片铸件》等标准,结合我厂的生产实际情况而制定。
本标准不包括汽轮机精铸叶片内容。
本标准由情报信息中心提出并归口。
本标准起草单位:铸钢厂本标准主要起草人:祝联升本标准自实施之日起代替ZBK54038-90、JB/T10087-1999、Q/CCF H3002-1998。
常用铸钢件技术条件1范围本标准规定了汽轮机、水轮机、发电机等产品铸钢件的技术要求、检验和试验方法、标识及合格证书等。
本标准适用于我厂铸钢的订货、生产和检验。
2规范性引用文件GB/T222-1984 钢的化学分析用试样取样法及成品化学成分允许偏差GB/T223 钢铁及合金化学分析方法GB/T228-1987 金属拉伸试验方法GB/T229-1994 金属夏比缺口冲击试验方法GB/T231 金属布氏硬度试验方法GB/T5677-1985 铸钢件射线照相及底片等级分类方法GB/T6414-1999 铸件尺寸公差与机械加工余量GB/T9443-1988 铸钢件渗透探伤及缺陷显式迹痕的评级方法GB/T11351-1989 铸件重量公差GB/T11352-1989 一般工程用铸造碳钢件JB/T4058-1999 汽轮机清洁度JB/T5105 铸件模样起模斜度JB/T9629-1999 汽轮机承压件水压试验技术条件JB/T9630.1-1999 汽轮机铸钢件磁粉探伤及质量分级方法JB/T9630.2-1999 汽轮机铸钢件超声波探伤及质量分级方法JB/T10087-2001 汽轮机承压铸钢件技术条件Q/CCF J3307 铸钢件补焊技术条件3订货及图样要求3.1铸件图样必须注明钢种牌号及选用标准号。
电力行业常用技术规范
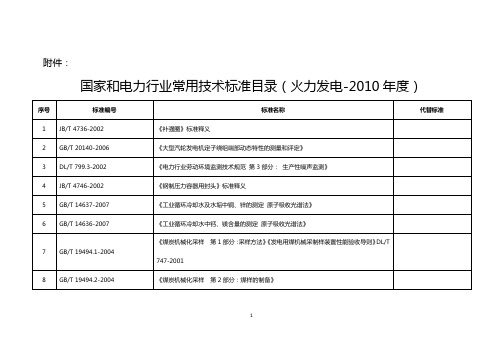
52
JJG 856-1994
500℃以下工作用辐射温度计检定规程
53
DL/Z 713-2000
500KV变电所保护和控制设备抗扰度要求
54
HJ/T 24-1998
500kV超高压送变电工程电磁辐射环境影响评价技术规范
55
DL/T 5122-2000
500kV架空送电线路勘测技术规程
27
JJG 2062-1990
13.81 ~ 273.15K温度计量器具检定系统
28
GB/T 17215.321-2008
1级和2级静止式交流有功电度表
GB/T 17215-2002
29
GB/T 17442-1998
1级和2级直接接入静止式交流有功电度表验收检验
30
DL/T 610-1996(2005)
84
JJG 158-1994
标准补偿式微压计检定规程
85
JJG 153-1996
标准电池检定规程
86
JJG 183-92
标准电容器检定规程
87
GB/T 20000.3-2003
标准化工作指南 第3部分:引用文件
GB/T1.22-1993
88
JJG 161-2010
标准水银温度计检定规程
JJG 161-1994
DL/T 378-2010
变压器出线端子用绝缘防护罩通用技术条件
75
DL/T 574-2010
变压器分接开关运行维修导则
DL/T574-1995
76
GB/T 7065-2004
变压器用压力释放阀
77
GB/T 7069-2004
给水泵汽轮机技术协议

山东里能集团煤炭地下气化发电示范工程2×300MW机组给水泵汽轮机合同附件(技术部分)买方:山东里能集团卖方:上海汽轮机有限公司2003年11月中国·上海目录附件1 技术协议 (2)1.总则 (2)2.工程概况 (2)3.设计和运行条件 (3)4.技术要求 (5)5.质量保证 (23)6.清洁、油漆、包装、运输与储存 (25)7.技术数据表 (26)附件2 供货范围 (38)1. 一般要求 (38)2. 供货范围 (38)附件3技术资料及交付进度 (46)1. 一般要求 (46)2. 资料提交基本要求 (46)3 图纸资料清单 (47)附件5 监造(检验)和性能验收试验 (51)1. 概述 (51)2. 工厂检验 (51)3.设备监造 (52)4. 性能验收试验 (55)附件7 技术服务和设计联络 (57)1 卖方现场技术服务 (57)2 培训 (59)3 设计联络 (60)附件11 其它 (60)附件1 技术协议1. 总则1.1 本合同附件适用于山东里能集团煤炭地下气化发电示范工程2×300MW火电机组给水泵汽轮机的设计、结构、性能、安装和试验等方面的技术要求。
1.2 本合同附件提出的是最低限度的技术要求,并未规定所有的技术要求和适用的标准,卖方提供一套满足本合同附件和所列标准要求的高质量产品及其相应服务。
对国家有关安全、环保等强制性标准,必须满足其要求。
1.3 卖方须执行本合同附件所列标准。
有矛盾时,按较高标准执行。
卖方在设备设计和制造中所涉及的各项规程,规范和标准必须遵循现行最新版本的标准。
1.4 合同签订3个月内,按本合同附件的要求,卖方提出给水泵汽轮机的设计、制造、检验/试验、装配、安装、调试、试运、验收试验、运行和维护等标准清单给买方,由买方确认。
1.5 设备采用的专利涉及到的全部费用均被认为已包含在设备报价中,卖方应保证买方不承担有关设备专利的一切责任。
锻压技术标准

GB 4064-83 电气设备安全设计导测
GB 5091-85 压力机的安全装置技术条件
TJ 36/79 工业企业设计卫生标准
GB 2893-82 安全色
GB 2894-1996 安全标志
ZB/J 62006 锻压机械噪声限值
TJ 232(一)(二) 机械设备安装工程施工及验收规范
GB 6441-86 企业职工伤亡事故分类
GB 13318-91 锻造车间安全生产通则
JB/T 6055-92 锻造车间环境保护导则
JB/T 6056-92 冲压车间环境保护导则
GB/T 221-2000 钢铁产品牌号表示方法
GB/T 222-1984 钢的化学分析用试样取样法及成品化学成分允许编差
GB/T 223-1997 钢铁及合金化学分析方法
GB/T 224-1987 钢的脱碳层深度测定法
GB/T 230-2004 金属洛氏硬度试验方法
GB/T 231-2002 金属布氏硬度试验方法
GB/T 4340 金属维氏硬度试验方法
GB/T 4341 金属肖氏硬度试验方法
YB 25-1977 钢中非金属夹杂物显微评级方法
GB/T 4236-1984 钢的硫印检验方法
GB/T 12604.1-90 无损检测术语超声检测
GB/T 1814-1979 钢材断口检验法
GB/T 1979-2001 结构钢低倍组织缺陷评级图
GB/T 2971-80 碳素钢和低合金钢断口检验方法
GB/T 10623-1989 金属力学性能名词解释
GB/T 6394-2002 金属平均晶粒度测定法
火力发电厂金属技术监督规程修订版

ICS 27.100F20备案号:26317-2009中华人民共和国电力行业标准火力发电厂金属技术监督规程The technical supervision codes for metalin fossil-fuel power plant(征求意见稿)中华人民共和国国家能源局发布目次前言...................................................................................................................................................................... I I1 范围 (1)2 规范性引用文件 (1)3总则 (3)4名词术语 (3)5金属材料的监督 (4)6焊接质量的监督 (5)7主蒸汽管道和再热蒸汽管道及导汽管的金属监督 (5)8高温联箱的金属监督 (11)9 受热面管子的金属监督 (14)10汽水分离器和锅筒的金属监督 (16)11 给水管道和低温联箱的金属监督 (17)12 汽轮机部件的金属监督 (17)13 发电机部件的金属监督 (19)14 紧固件的金属监督 (20)15 大型铸件的金属监督 (20)16 金属技术监督管理 (21)附录A (规范性引用文件) 金属技术监督工程师职责 (19)附录B (资料性引用文件) 电站常用金属材料和重要部件国内外技术标准 (20)附录C (规范性引用文件) 电站常用金属材料硬度值 (24)附录D (规范性引用文件) 低合金耐热钢蠕变损伤评级 (26)I前言本标准是根据根据国能科技【2014】298号第一批能源领域行业标准制修订计划修订的。
本标准与DL 438-2009相比,主要作了以下修订:——在章节的内容、编排顺序上作了一些的较大的调整;——将原规程“1范围”中高温部件温度的界定由400℃改为450℃,对400~450℃温度范围服役的部件的检验监督规程中单独作出规定。
中华人民共和国电力行业标准

中华人民共和国电力行业标准DL/T 715-2000DL/T 715-2000火力发电厂金属材料选用导则Selection guidelines for the metallic materialof fossil-fired power plants2000-11-03发布 2001-01-01实施中华人民共和国国家经济贸易委员会发布1 范围本标准规定了金属材料选用的技术要求,及金属材料的基本检验项目、方法和质量要求。
本标准适用于火力发电厂在役机组部件的维修与更换、新机组重要部件金属材料的选用和替代,以及超期服役机延寿的技术改造。
国外牌号金属材料的国产化、代用和维修也可参照本标准执行。
2引用标准下列标准所包含的条文,通过在本标准中引用而构成为本标准的条文。
本标准出版时,所示版本均为有效。
所有标准都会被修订,使用本标准的各方应探讨使用下列标准最新版本的可能性。
GB/T222-1984 钢的化学分析用试样取样法及成品化学成分允许偏差GB/T223-1994 钢铁及合金化学分析方法GB/T224-1987 钢的脱碳层深度测定法GB/T226-1991 钢的低倍组织及缺陷酸蚀试验法GB/T228-1987 金属拉伸试验方法GB/T229-1994 金属夏比缺口冲击试验方法GB/T230-1991 金属洛氏硬度试验方法GB/T231-1984 金属布氏硬度试验方法GB/T232-1988 金属弯曲试验方法GB/T233-1982 金属顶锻试验方法GB/T241-1990 金属管液压试验方法GB/T242-1997 金属管扩口试验方法GB/T244-1997 金属管弯曲试验方法GB/T245-1997 金属管卷边试验方法GB/T246-1997 金属管压扁试验方法GB/T699-1988 优质碳素结构钢技术条件GB713-1997 锅炉用钢板GB/T1220-1992 不锈钢棒GB/T1221-1992 耐热钢棒GB/T1997-1980 结构钢低倍组织缺陷评级图GB/T2039-1997 金属拉伸蠕变及持久试验方法GB/T2970-1991 中厚钢板超声波探伤方法GB/T2975-1998 钢及钢产品力学性能试验取样位置及试样制备GB/T3077-1988 合金结构钢技术条件GB3087-1982 低中压锅炉用无缝钢管GB/T3323-1987 钢熔化焊对接接头射线照相和质量分级GB/T3620.1-1994 钛及钛合金牌号和化学成分GB/T3625-1995 换热器及冷凝器用钛及钛合金管GB/T 4160-1984 钢的应变时效敏感性试验方法(夏比冲击法)GB/T4334.1-1984 不锈钢 10%草酸浸蚀试验方法GB/T4334.2-1984 不锈钢硫酸-硫酸铁腐蚀试验方法GB/T4334.3-1984 不锈钢 65%硝酸腐蚀试验方法GB/T4334.4-1984 不锈钢硝酸-氢氟酸腐蚀试验方法GB/T4334.5-1984 不锈钢硫酸-硫酸铜腐蚀试验方法GB/T4334.6-1984 不锈钢 5%硫酸腐蚀试验方法GB/T4338-1995 金属高温拉伸试验方法GB/T4340-1984 金属维氏硬度试验方法GB/T4698-1996 海绵钛、钛及钛合金化学分析方法GB/T5121-1996 铜及铜合金化学分析方法GB5248-1998 铜及铜合金无缝管涡流探伤方法GB5310-1995 高压锅炉用无缝钢管GB/T5313-1985 厚度方向性能钢板GB/T5777-1996 无缝钢管超声波探伤方法GB/T6397-1986 金属拉伸试验试样GB6654-1996 压力容器用碳素钢和低合金钢厚钢板GB/T7735-1995 钢管涡流探伤方法GB8000-1987 热交换器用黄铜管内应力氨熏检验方法GB/T8732-1988 汽轮机叶片用钢GB/T8890-1998 热交换器用铜合金管GB/T10121-1988 钢材塔形发纹磁粉检验方法GB/T10561-1989 钢中非金属夹杂物显微评定方法GB/T12606-1990 钢管及圆钢棒的漏磁探伤方法GB/T12969.1-1991 钛及钛合金管材超声波检验方法GB/T12969.2-1991 钛及钛合金管材涡流检验方法GB13296-1991 锅炉、热交换器用不锈钢无缝钢管GB/T13298-1991 金属显微组织检验方法DL/T439-1991 火力发电厂高温紧固件技术导则DL/T712-2000 火力发电厂凝汽器管选材导则JB/T1265-1993 25~200MW汽轮机转子体和主轴锻件技术条件JB/T1266-1993 50~200MW汽轮发电机转子锻件技术条件JB/T1267-1993 50~200MW汽轮发电机转子锻件技术条件JB/T1268-1993 50~200MW汽轮发电机无磁性护环锻件技术条件JB/T1581-1996 汽轮机、汽轮发电面转子和主轴超声波探伤方法JB/T1582-1996 汽轮机叶轮超声波探伤方法JB/T3375-1991 锅炉原材料入厂检验JB4010-1985 汽轮发电机用钢制护环超声波探伤方法JB/T7027-1993 300~600MW汽轮机转子体锻件技术条件JB/T7030-1993 300~600MW汽轮发电机无磁性护环锻件技术条件JB/T7178-1993 300~600MW汽轮发电机转子锻件技术条件JB/T9021-1999 汽轮机主轴和转子锻件的热稳定性试验方法JB/T9625-1999 锅炉管道附件承压铸钢件技术条件JB/T9629-1999 汽轮机承压件水压试验技术条件JB/T9630.1-1999 汽轮机承铸钢件的磁粉探伤及质量分级方法JB/T10087-1999 汽轮机铸钢件技术条件YB(T)41-1993 锅炉用碳素钢和低合金钢厚钢板YB/T5148-1993 金属平均晶粒度测定方法YS/T347-1994 单相铜合金晶粒度测定法3 选材的基本原则3.1 应综合考虑材料的使用性能、工艺性能和经济性。
大锻件用钢 28CrMoNiV材料技术要求

国外相近牌号
(德国)DIN 28CrMoNiV 49
500℃
550℃
600℃
σb
700
626
596
584
555
479
423
365
σ0.2
550
496
472
455
433
393
364
326
高温长时性能(15)
温度
470℃
480℃
490℃
500℃
510℃
520℃
530℃
蠕变
σ10-4
σ10-5
持久
σ104
396
377
358
338
319
299
278
σ105
336
焊 接
焊接性差。
冷加工
说 明
*采用真空碳脱氧时,Si≤0.10%
** AKV为三个冲击试样的平均值。
其它性能(15)
组织稳定性:经525℃长期时效,组织性能无明显变化。
断裂韧性:J0.05=73.5N/mm,KJ0.05=128.9 MPa·m1/2
Ji=29.4N/mm,J0.2=210.7N/mm
金属材料技术条件
大锻件用钢28CrMoNiV
化学成分
C
Si
Mn
S
P
Cr
Ni
Mo
V
Cu
Al
DZ2.6.28-95
0.25
~
0.30
≤0.30
0.35
~
0.85
≤0.015
≤0.015
0.90
~
1.20
0.50
~
0.75
- 1、下载文档前请自行甄别文档内容的完整性,平台不提供额外的编辑、内容补充、找答案等附加服务。
- 2、"仅部分预览"的文档,不可在线预览部分如存在完整性等问题,可反馈申请退款(可完整预览的文档不适用该条件!)。
- 3、如文档侵犯您的权益,请联系客服反馈,我们会尽快为您处理(人工客服工作时间:9:00-18:30)。
JB 1265-85汽轮机转子和主轴真空处理的碳钢和合金钢锻件技术条件本标准适用于蒸汽参数不超过565C,用经真空处理的钢锻制的电站汽轮机主轴和整体转子锻件。
1订货条件1. 1需方应在订货合同中规定锻件的级别、要求的试验项目、补充要求(附录A)和任选项目。
1. 2需方应提供标明机械性能试验试样位置、锻件和中心孔尺寸的粗加工图、和最终的精加工图。
2制造2. 1冶炼和浇注2. 1. 1锻件用钢应在碱性电弧炉中冶炼,并需真空处理。
2. 1. 2经需方同意,也承诺采纳其它冶炼工艺。
2. 1. 3钢水应在浇注前或浇注中进行真空处理,以去除有害气体,专门是氢。
在真空处理过程中真空系统的能力,必须大到足以便开浇时的两分钟内就能将初始增高的压强降至低值。
2. 2切头切尾每个钢锭应有足够的切除量,以确保成品锻件无缩孔,无严峻的偏析及有害的缺陷。
2. 3锻造必须尽可能使整个锻件得到平均的组织。
锻件在锻压时应使整个截面金属充分锻透,专门是保持锻件与钢锭的轴线大致重合。
钢锭较好的一端应为联轴器端。
2. 4热处理2. 4. 1锻件锻后热处理,必须至少进行一次相当高于相变温度的正火处理。
随后,锻件应进行回火处理。
2. 4. 2性能热处理,应在锻件第一次粗加工后进行。
关于1、2、3、4、9和10级钢应为正大和回火。
关于5、6、7和8级钢应为淬火和回火。
正火处理时,供方可选择使锻件在静止空气或鼓风中冷却,征得需方同意,1、2、3、4、9和10级钢可采纳较快的冷却速度。
可采纳液体淬火、喷水或喷雾冷却得到较快的冷却速度。
2. 4. 2. 1正火或淬火处理应高于相变温度,但要低于锻后热处理的正火温度。
2 • 4. 2. 2回火温度尽量高些,以满足机械性能要求。
1〜7和10级钢回火温度不得低于580 °C ,8级钢不得低于565C, 9级钢不得低于650C。
2. 4. 3在性能热处理,及随后的粗加工和打中心孔后,锻件应在最终回火温度以下不低于55C的温度范畴内排除应力,但不得低于550 C o2 • 4. 3. 1征得需方预先同意,排除应力温度能够是接近、等于或稍超过最终回火温度,以便调整最终强度或韧性,如排除应力温度在最终回火温度的15C范畴内或稍高一些,则必须作附加抗拉试验。
2. 5机械加工2. 5. 1锻件性能热处理前,所有表面应进行第一次粗加工。
2. 5. 2锻件在性能热处理后,排除应力和热稳固性试验之前,应进行第二次粗加工。
2. 5. 3供方可在排除应力处理往常对锻件打中心孔。
需方另有要求时按附录A.A.2执行2 • 5 • 3. 1按需方订货图规定的尺寸和公差打中心孔。
为了去除由超声波检测出来的不承诺的中心缺陷,也承诺按需方规定的订货图注明的或经需方同意的极限范畴扩大中心孔2. 5. 4发运的锻件应符合订货图规定的粗糙度和尺寸要求。
3技术要求3. 1化学成分钢的化学成分应符合表工的要求。
注:02〜a和10级钢可采纳真空碳脱氧,现在硅含量上限为0. 10%, 用户有要求时,9级钢可见附录A.7规定。
②见附录A。
1规定。
③1级钢可随意加钒。
④2〜10级钢应报告作为参考。
注:残余变形值为0. 2%时的屈服强度;主轴不做径向试验。
3-1 -1供方对每炉钢水进行分析,以测定表工规定的元素的百分含量。
对多炉合浇制成的锻件,则要对每炉钢水进行分析,并报告权重平均分析结果,其结果应符合表工的要求。
31 -2供方应对每件锻件进行产品分析,分析结果应符合表1的要求,但承诺有表2的偏差。
3. 2机械性能3. 2. 1锻件的机械性能应符合表3的规定。
3. 3无损检验3. 3. 1 一样要求3. 3. 1. 1锻件不得有裂纹、折叠、缩孔和其它不承诺的缺陷。
3. 3. 1. 2需方可要求超声波、磁粉、着色探伤、酸浸等检验,以便评定缺陷和保证锻件质量要求。
3. 3. 2磁粉检验3. 3. 2. 1锻件应由需方对其全部外圆表面进行磁粉检验。
如有要求,也可在供方进行。
3. 3. 2. 2带有裂纹缺陷,或由非金属夹杂引起的长度等于或超过3. 2 mm的线状缺陷的锻件,若不能清除,则锻件应予拒收。
3. 3. 3超声波检验3. 3. 3. 1供方应对锻件进行超声波俭验,以证明无有害的缺陷。
3. 3. 3. 2已记录到超声波缺陷讯号的锻件,应通知需方。
按游动讯号和静止讯号的当量、个数和位置提出报告,如果对该缺陷讯号有异议,应采纳常规的或双方都能同意的验收检验方法来确定锻件是否报废。
3. 3. 4中心孔检验3. 3.4. 1如用窥膛仪或磁粉检验检查内孔,锻件应按订货图规定精镗(或研磨)中心孔。
3. 3.4. 2供方应对中心孔进行检验,如检验时遇到不承诺的缺陷,应将缺陷的位置和性质通知需方,协商一致后,方米取下一步措施。
3. 3. 5热稳固性试验3. 3. 5. 1锻件经排除应力后,需进行热稳固性试验,以测定稳固性或高温运行条件下产生的挠曲倾向。
注:如需方同意,排除应力可作为热稳固性试验的一部分进行。
3. 3. 5. 2试验应符合试验时锻件在加热室内的最小区段和最低的热稳固性试验温度规定。
3. 3. 6尺寸、公差和粗糙度。
3. 3. 6. 1每件锻件应符合需方订货图规定的尺寸、公差和粗糙度要求。
4试验方法和规则4. 1化学分析4. 1. 1钢的化学成分分析方法按GB 223?1《钢铁化学分析方法》或JB/ZQ 6121?4及有关化学分析方法进行。
4. 1. 2每炉(每包)钢水可于浇注时取样,测定钢水的化学成分。
如试样丢失或不符合分析要求,供方可在钢锭或锻件表面邻近合适部位取代替试样。
代替试样的部位与化学分析结果一起通知对方。
4. 1. 3产品分析的试样取自每个锻件,或取自供检验的原尺寸延伸部的1/2半径处,或取自径向验收试样。
每件取一个试样。
4. 2机械性能4. 2. 1机械性能试验(抗拉强度、屈服强度及缺口韧性等)按JB/ZQ 6117—84方法进行。
屈服强度采用残余变形法测定。
4. 2. 2抗拉试样的数量和位置应符合订货图的规定。
试样尺寸采纳直径为12. 5mm、标距长度为50.0mm的标准试样。
4. 2. 3缺口韧性试样取自订货图标明的锻件本体径向试捧。
试样采纳夏氏V型缺口A型试样。
切口方向应为切向。
4. 3无损检验4. 3. 1磁粉检验按JB/ZQ 6101 —84方法进行。
4. 3. 2超声波检验按JB 1581 —85《汽轮机,汽轮发电机转子和主轴锻件超声波探伤方法》进行。
4. 3. 2. 1超声波检验应在性能热处理后,在锻件所有可探测的外圆表面上进行。
•4. 3. 3中心孔检验用窥膛仪或双方确认的其它检验方法进行。
4. 3. 4热稳固性试验按JB/ZQ 6106 一84方法进行。
4. 4复试4. 4. 1当机械性能试验结果不符合要求时,承诺进行复试。
4 • 4 • 2如果任一试样试验结果不合格,应在锻件上取试样相邻的两个试样来复试。
但试样如因白点、断裂或裂纹缘故而不合格,则不得复试。
复试结果,两个试样都必须满足规定要求。
4. 5重新热处理4 •5 • 1如果锻件的任一机械性能试验复试结果仍不合格时,供方可对锻件进行重新热处理。
但如未经需方同意,重新热处理不得超过三次。
重新热处理后的锻件按4. 2. 2款或4. 2. 3款规定进行试验。
4. 5. 2如补充要求规定了中心孔芯捧性能,则芯棒余料必须放回孔内,一起进行重新回火处理。
4 •5 • 3如果包括正火或淬火在内的完整的重新热处理,双方应协商一致确认芯料在孔内重新热处理区段的可行性。
5检查和验收。
5• 1供方应向需方的检验员提供必要的方便条件,以便检验员进行工作。
需方的检验不应对供方的生产造成不必要的阻碍。
除非另有规定或双方同意,交货前的一切试验和检验应在制造场地进行。
5. 2供方应向需方提供订货合同规定的合格证书份数。
应报告的项目:“订货合同号;b. 订货图号;c. 标准号和用钢级别;d. 熔炼号;e. 钢水和产品化学成分分析结果;f .机械性能验收结果;g. 全部无损检验结果和标有所记录到的缺陷位置和取向的草图;h. 机械性能的热处理工艺要紧数据;i. 合同已规定的补充要求的结果。
5. 3锻件必须全部满足订货合同要求,始得验收。
5. 3. 1锻件在制造场地验收后,发觉了不承诺的缺陷,应予拒收。
5 • 3 • 2以4 • 1 • 2款为依据退货的锻件,应于锻件验收后60天内通知供方;如对锻件进行全面质量复核,作为锻件退货依据应于锻件收到后200天内通知供方。
代表退货材料的试样,应从退货通知发出之日起保留90天,以备供方复审。
6打印和包装6• 1制造厂应在每件锻件相当于钢锭下部的端面上打上供方厂名称或标志、合同号、熔炼号、锻件卡号。
6 • 1 • 1试样的编号应与锻件的编号、需方订货图上规定的试样位置和类别编号一致。
6・2锻件外表面应涂以防锈漆,并作合适的防护。
爱护好中心孔,用木塞堵严,以幸免在运输和保管时损坏或腐蚀。
附录A。
锻件化学成分和性能补充要求(补充件)下列补充要求,在合同上规定时,才予以实施。
其详细内容应经双方协商确认。
A.1钼含量:如因运行温度的需要,需方可规定2、3、4、5、6和7级钢的最小钼含量为0.40。
A.2中心孔芯棒的性能:需方可要求性能热处理后套取中心孔芯棒。
A.2 . 1中心孔芯棒直径由双方协商确定。
A.2 . 2需方可于订货图上规定,在中心孔芯棒上确定位置,来切取拉伸试样或冲击试样,以便进行机械性能试验。
A.2 . 3机械性能验收值应由双方商定。
A.3持久强度性能,由供方或需方进行持久试验。
并按订货图标示位置和要求切取试样。
A.3 . 1持久强度试验按JB/ZQ 6156?4方法进行。
A.3 . 2试样的尺寸和形状及持久强度试验的要求应双方协商。
A.4最小回火脆性的专门要求对有专门用途的5、6、7级钢锻件能够规定严格的化学成分和补充的缺口韧性要求,备汪如下:A.4 .工钢水分析元素5、6、7级钢成分(%)碳w 0. 28锰w 0. 40磷w 0. 012硫w 0. 015硅w 0. 10镍3.25 〜4 . 00铬1.25 〜2 . 00钼0.25 〜0 .45钒0.05〜0 .15铜W 0. 20锑*锡*A.4 . 2按4. 2. 3款规定的位置,切取需要数量的冲击试样,以测定时期冷却条件下的FATT50值。
试验前,试样应经如下的时期冷却:595C保温1h;炉冷至540C保温15h;炉冷至525C保温24h;炉冷至495C保温48h;炉冷至470C保温72h;炉冷至315 C或较低温度,空冷至室温A, 5备选的热处理工序A.5.1第二次回火工序应在2.4 • 2款规定的回火工序之后,但在2.5.2 款2.5. 3款规定的工序之前进行。