半固态成型技术
金属半固态成形

金属半固态成形一、引言金属半固态成形是一种新兴的金属成形技术,它是在半固态状态下对金属进行成形加工,具有高效、高精度、高质量等优点。
近年来,随着科技的不断进步和人们对产品质量的要求越来越高,金属半固态成形技术得到了广泛的应用和研究。
二、什么是金属半固态成形1.定义金属半固态成形是指在合适温度下,将金属材料加工到一定程度时,使其呈现出部分晶粒熔化和部分晶粒未熔化的状态。
这种状态被称为半固态状态。
在这个状态下进行成型加工可以得到具有优异性能的零件。
2.特点(1)高效:相比传统的铸造和锻造工艺,金属半固态成形具有更快的生产速度。
(2)高精度:由于采用了先进的数控技术和模具制造技术,使得加工精度更高。
(3)高质量:由于采用了先进的材料处理方法和模具制造技术,使得产品质量更高。
三、金属半固态成形的工艺流程1.原材料制备:将金属材料经过特殊处理,使其呈现出半固态状态。
2.模具设计:根据产品的形状和尺寸,设计出合适的模具。
3.加热处理:将金属材料加热到合适的温度,使其呈现出半固态状态。
4.成型加工:将半固态金属材料放入模具中进行成型加工。
5.冷却处理:将成型后的零件进行冷却处理,使其达到稳定状态。
6.后续加工:根据需要对零件进行后续加工和表面处理。
四、金属半固态成形的应用领域1.航空航天领域:由于航空航天领域对于零件质量和性能要求非常高,因此金属半固态成形技术在该领域得到了广泛应用。
例如飞机发动机叶片、涡轮叶片等高精度零部件都可以采用该技术进行生产。
2.汽车制造业:汽车制造业是金属半固态成形技术的另一个重要应用领域。
例如汽车发动机缸体、曲轴等高精度零部件都可以采用该技术进行生产。
3.医疗器械领域:金属半固态成形技术在医疗器械领域的应用也越来越广泛。
例如人工关节、牙科种植体等高精度零部件都可以采用该技术进行生产。
五、金属半固态成形的未来发展趋势1.智能化:随着科技的不断进步,金属半固态成形技术将更加智能化,通过计算机控制和自动化设备,使得生产效率更高、产品质量更稳定。
精确成型技术 第十三讲 半固态成形技术

合金制备方法 紊流效应法
紊流效应法和粉末法 研究开发之中,应用少。
半固态成形方法
➢流变成形 ➢触变成形
✓铸造成形 ✓锻造成形 ✓挤压成形 ✓轧制成形
流变触变成形工艺过程
成形方法
流变成形:利用经搅拌等工艺获得的近球 状晶半固态浆料,在保持其处于固液两 相区温度时直接进行成形。
➢ 流变压铸
➢ 流变锻造 ➢ 流变轧制
应变诱发熔化激活法
合金制备方法
合金制备方法
变形诱导熔化激活法 金属坯料纯净度高,生产效率较高。增 加了预变形工序,生产成本提高,且坯 料直径受到限制。是在实际备方法
倾斜体冷却法
合金制备方法
倾斜冷却体法 是一种从球形晶核形核和长大的热力学 和动力学条件着手(晶粒游离理论)的 浆料制备方法,装置简单,成本低、效 率高,占地面积小。搅拌和剪切作用弱。 特别适合于高熔点铁合金的半固态浆料 的制备。
《材料精确成形技术》 第十三讲
半固态成形技术
➢原理与工艺特点 ➢半固态合金制备方法 ➢半固态成形方法
技术的起源
1971年美国麻省理工学院的D.B.Spencer 和M.C.Flemings发明了一种搅动铸造 (stir cast)新工艺,用旋转双桶机械搅拌 法制备出Sn-15%Pb流变浆料。
工艺原理
工艺特点
➢ 生产成本低。成形温度低,近净成形节省能 源和节约金属;充型平稳、热负荷小,热疲 劳强度下降使模具寿命延长。
➢ 有利于制造金属基复合材料。利用半固态金 属的高粘度,使密度差大、固溶度小的金属 制成合金,可有效地使不同材料混合,制成 新的复合材料。
工艺特点
半固态合金制备方法
➢机械搅拌法 ➢电磁搅拌法 ➢应变诱发熔化激活法(SIMA) ➢喷射沉积法(Ospray)
金属材料成型_6.2_半固态成形技术路线
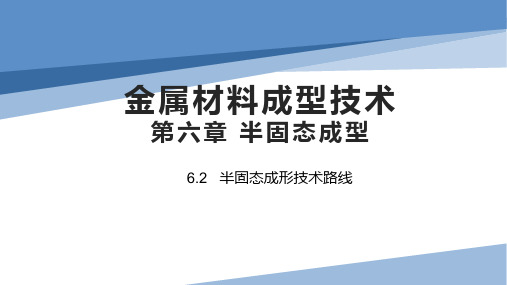
图6-8 半固态成形技术的两种工艺路线
对于流变成形,由于把浆料制备和加工成形相承接,具有生产效率高 、整体流程短的特点,近年来发展十分迅速,不过浆料的保存和输送难度 大,设备自动化控制复杂,成本相对高。对于触变成形,浆料的制备和最 终成形可分开进行,成形厂方甚至可以不参与熔炼制浆,只需提供二次 加热,工业污染小,而且半固态坯料输送方便,易于实现自动化,因而在 国外较早得到了广泛应用,不过这种方式的缺点是坯料经过冷却和再加热 的过程,能源消耗有所增加。
图6-9 机械搅拌制备半固态浆料
b、电磁搅拌法
电磁搅拌法是目前半固态成形工业生产上最成熟最广泛被应用的制浆 方法,它是在感应线圈中通入一定相位的交变交流,从而产生变换旋转的 磁场,而金属液中便有感应电流产生,洛伦兹力就驱使金属熔体产生剧烈 运动,使非枝晶凝固模式取代传统的枝晶凝固趋势,从而获得含有球形固 相的半固态浆料。如图6-10所示,按熔体被搅拌力驱动的流动方式,一般 分为垂直式、水平式、螺旋式。电磁搅拌采用无接触式地对合金熔体进行 搅动,对合金污染极大降低,且通过调节电流、磁场强度和频率等参数就 能实现搅拌效果的控制,可以连续高效地制备坯料,适用于工业化的生产 应用。但由于电磁搅拌的集肤效应,通常认为,直径大于150mm的铸坯 不宜采用电磁搅拌法。
c、注射成型法
注射成型法是将低熔点金属颗粒进行加热至半固态成型,尺寸为几毫米的合金 粒子在料筒中边被加热边被螺旋体剪切推进,通过螺旋强制对流的搅拌作用,得 到细小均匀球状晶的半固态浆料组织,然后以高速(注塑十倍速度)注入模腔里 。这种方法非常适于相对较活泼的镁合金材料,在整个浆料制备和成型工艺中可 以不使用保护气体和防氧化剂,不需要配备熔化炉,而且不会产生浮渣、炉渣等 ,兼顾安全性和环保。
第9章半固态成形技术
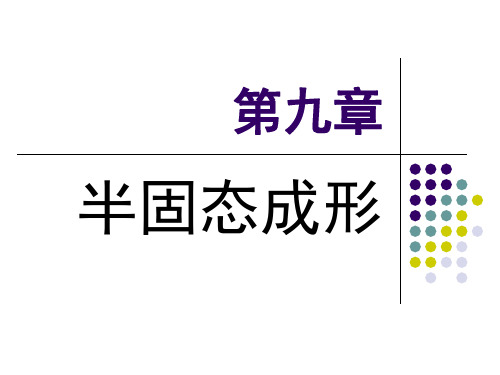
液态加工 (铸造成形)
半固态加工 (流变/触变成形)
固态加工 (塑性成形)
重力铸造 精密铸造 压力铸造
高流 速变 连铸 续造
铸 造
液态模锻 液态铸轧 连续铸挤 半固态轧制 半固态挤压 半固态压铸 半固态锻造
连连 续铸 带轻 液压 芯下 压 下
轧制 锻压 挤压 超塑成形 特种固体成形
图1 金属在高温下三态成形加工方法的相互关系
②枝晶臂根部熔断机制。
晶体在表面积减小的正常长大过 程中,枝晶臂由于受到流体的快速 扩散、温度涨落引起的热震动及在 根部产生应力的作用,有利于熔断, 同时固相中根部溶质含量较高,也 降低熔点,促进此机制的作用,机 理如图9所示。
图9 枝晶臂发生熔断示意图
③枝晶臂弯曲机制。 此机制认为,位错的产生并积累导致塑性变形。在两相区,位错
图8 球形微粒固态金属加工两种方法(流变成形和触变成形)的工艺流程图
半固态浆料搅动时的组织演变受很多因素影响,半固态浆料的 温度、固相分数和剪切速率是三个基本因素。
有色金属半固态组织的演变机制主要有以下三种:
①枝晶臂根部断裂机制。因剪切力的作用使枝晶臂在根部断裂。
最初形成的树枝晶是无位错和切口的理想晶体,很难依靠沿着自 由浮动的枝晶臂的速度梯度方向产生的力来折断。因此,必须加强 力搅拌,在剪切力作用下从根部折断。
(1)半固态成形技术定义
半固态成形原理
利用非枝晶半固态金属(Semi-Solid Metals,简称SSM)独有的 流变性和搅熔性来控制铸件的质量。
半固态 成形方法
流变成形 rheoforming
在金属凝固过程中,对其施以剧烈的搅拌作 用,充分破碎树枝状的初生固相,得到一种 液态金属母液中均匀地悬浮着一定球状初生 固相的固-液混合浆料(固相组分一般为50%左 右),即流变浆料,利用这种流变浆料直接进 行成形加工的方法称之为半固态金属的流变 成形。
半固态成形
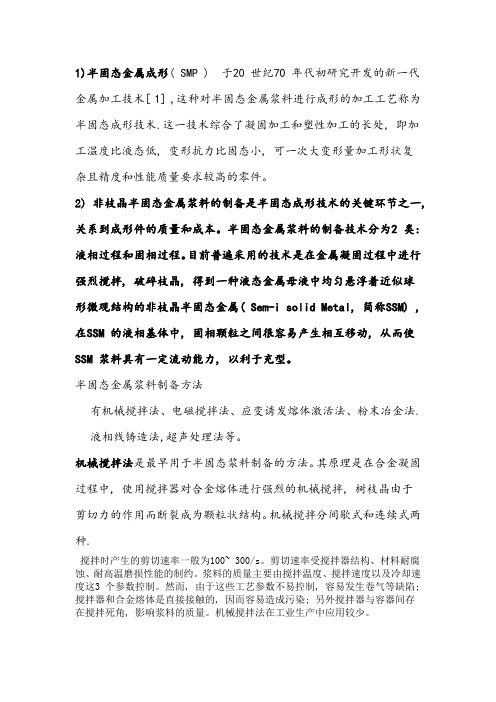
1)半固态金属成形( SMP ) 于20 世纪70 年代初研究开发的新一代金属加工技术[ 1] ,这种对半固态金属浆料进行成形的加工工艺称为半固态成形技术.这一技术综合了凝固加工和塑性加工的长处, 即加工温度比液态低, 变形抗力比固态小, 可一次大变形量加工形状复杂且精度和性能质量要求较高的零件。
2) 非枝晶半固态金属浆料的制备是半固态成形技术的关键环节之一, 关系到成形件的质量和成本。
半固态金属浆料的制备技术分为2 类: 液相过程和固相过程。
目前普遍采用的技术是在金属凝固过程中进行强烈搅拌, 破碎枝晶, 得到一种液态金属母液中均匀悬浮着近似球形微观结构的非枝晶半固态金属( Sem-i solid Metal, 简称SSM) , 在SSM 的液相基体中, 固相颗粒之间很容易产生相互移动, 从而使SSM 浆料具有一定流动能力, 以利于充型。
半固态金属浆料制备方法有机械搅拌法、电磁搅拌法、应变诱发熔体激活法、粉末冶金法.液相线铸造法,超声处理法等。
机械搅拌法是最早用于半固态浆料制备的方法。
其原理是在合金凝固过程中, 使用搅拌器对合金熔体进行强烈的机械搅拌, 树枝晶由于剪切力的作用而断裂成为颗粒状结构。
机械搅拌分间歇式和连续式两种.搅拌时产生的剪切速率一般为100~ 300/s。
剪切速率受搅拌器结构、材料耐腐蚀、耐高温磨损性能的制约。
浆料的质量主要由搅拌温度、搅拌速度以及冷却速度这3 个参数控制。
然而, 由于这些工艺参数不易控制, 容易发生卷气等缺陷; 搅拌器和合金熔体是直接接触的, 因而容易造成污染; 另外搅拌器与容器间存在搅拌死角, 影响浆料的质量。
机械搅拌法在工业生产中应用较少。
电磁搅拌法是应用最为广泛的一种方法。
它利用旋转磁场使金属液内部产生感应电流, 并在洛伦兹力的作用下发生强迫对流, 从而达到搅拌的目的。
产生旋转磁场的方法有两种, 一种是在感应线圈中通入交变电流, 另一种则采用旋转永磁体的方法。
3~4半固态成型

半固态铸造生产线及自动化
半固态流变成形生产线 该系统由铝合金熔化炉、挤压铸造机、转盘式制 浆机、自动浇注装置、坩埚自动清扫、喷涂料装置等 组成。其工艺过程为:浇注机械手3将铝液从熔化炉2 中浇入制浆机4的金属容器中冷却;同时浆料搬运机 械手5从制浆机的感应加热工位抓取小坩埚,搬运至 挤压铸造机并浇人压射室中成形;随后继续旋转将空 坩埚返回送至回转式清扫装置上的空工位,并从另一 个工位抓去一个清扫过的小坩埚旋转放置到制浆机上; 制浆机和清扫机同时旋转一个角度,进入下一个循环。
半固态铸造成形装备
半固态铸造成形装备主要包括半固态浆料 制备装备、半固态成形装备、辅助装置等。 按流变铸造和触变铸造分类,又有流变铸 造装备和触变铸造装备。 半固态浆料的制备方法主要有机械搅拌、 电磁搅拌、单辊旋转冷却、单/双螺杆法等。 其基本原理都是利用外力将固液共存体中的固 相树枝晶打碎、分散,制成均匀弥散的糊状金 属浆料。最新发展的还有倾斜冷却板法、冷却 控制法、新MIT法等。
半固态铸造成形装备
一步法— 流变铸造 半固态铸造成形是在液态金属凝固的过程中进行强烈 的搅动,使普通铸造凝周易于形成的树枝晶网络骨架被打 碎而形成分散的颗粒状组织形态,从而制得半固态金属液, 然后将其铸成坯料或压成铸件。 根据其工艺流程的不同,半固态铸造可分为流变铸造 二步法— 和触变铸造两大类。 触变铸造 流变铸造是将从液相到固相冷却过程中的金属液进行 强烈搅动,在一定的固相分数下将半固态金属浆料压铸或 挤压成形,又称“一步法”; 触变铸造是先由连续铸造方法制得具有半固态组织的 锭坯,然后切成所需长度,再加热到半固态状,再压铸或 挤压成形,又称“二步法”。
半固态铸造的其他装置
流变铸造采用“一步法”成形,半 固态浆料制备与成形联为一体,装备 较为简单; 触变铸造采用“二步法”成形,除 有半固态浆料制备及坯料成形装备外, 还有下料装置、二次加热装置、坯料 重熔测定控制装置等。
半固态加工技术的发展及其研究现状
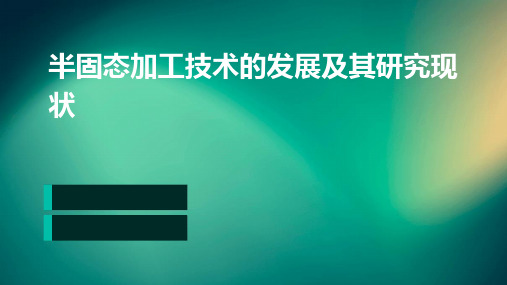
技术瓶颈与挑战
流变行为复杂
半固态加工过程中,材料的流变行为受多种因素影响,如温度、 应变速率等,导致加工过程难以控制。
界面问题
在半固态加工过程中,由于固液两相的存在,界面问题成为一大挑 战,如固液界面稳定性、颗粒分散等。
设备与工艺匹配
半固态加工需要特殊的设备和工艺,如何实现设备和工艺的匹配, 提高加工效率是亟待解决的问题。
未来发展前景与展望
拓展应用领域
随着半固态加工技术的不断成熟, 其应用领域将进一步拓展,如航 空航天、汽车、新能源等领域。
绿ቤተ መጻሕፍቲ ባይዱ可持续发展
半固态加工技术具有节能减排的潜 力,未来将在绿色可持续发展领域 发挥重要作用。
智能化与自动化
随着智能制造技术的发展,半固态 加工将实现智能化与自动化,提高 加工效率和产品质量。
01
02
03
汽车工业
研究半固态加工技术在汽 车零部件制造中的应用, 提高零部件的性能和轻量 化水平。
航空航天工业
探索半固态加工技术在航 空航天领域的应用,满足 高性能、轻质材料的需求。
电子产品
研究半固态加工技术在电 子产品外壳、连接器等制 造中的应用,实现产品的 小型化、轻薄化。
04 半固态加工技术的挑战与 前景
输标02入题
应用领域:航空航天业
01
03
优势特点:半固态加工技术能够控制零件的内部结构 和微观组织,提高零件的疲劳寿命和可靠性,满足航
空航天器的高性能要求。
04
技术应用:半固态加工技术用于制造航空航天器的关 键零部件,如发动机叶片、机翼结构件等。
成功应用的案例三
案例名称
医疗器械制造
应用领域
医疗器械制造业
021100849翁丽玉半固态成形
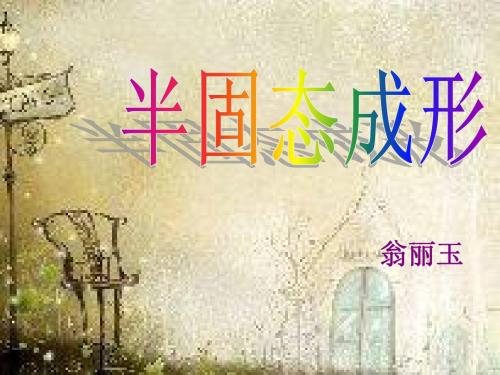
半固态成形优点
• 与传统的金属液态成形和塑性成形相比,半固态成形 具有许多优势: • (1)半固态材料流动性能与变形性能好,提高了生产率, 可 实现短流程生产; • (2)能够实现材料的近净成形生产,节约了原材料; • (3)半固态成形产品具有良好的内部组织和整体性能, 内部 气孔、偏析等缺陷少.组织细小,塑性和力学性 能都有提高; • (4)半固态成形温度比全液态成形温度低,对模具的热 冲击小,提高了成形模具的使用寿命; • (5)半固态浆料有较高的黏度,有利于提高材料的均匀 性,可以生产其他工艺所不能生产的复合材料和新型 合金。
半固态锻造
• 是将加热到50% 左右体积液相的半固态的坯 料在锻模中进行以压缩变形为主的模锻来获得 所需的形状和性能的制品的加工方法
半固态挤压
• 半固态挤压是用加热炉将坯料加热到半固态, 然后放入挤压模腔, 用凸模施加压力,通过凹模 口挤出所需制品。
半固态轧制
• 半固态轧制是在轧机的入口处设置加热炉, 将 具有球状晶的金属合金材料加热到半固态后, 送入轧辊间轧制的方法。半固态轧制的对象主 要是板材的轧制成形。
参考文献
• [1] 谭建波,李迅.李立新,等.半固态金属成形技术 的发展及应用现状[J].河北科技大学学报。 2003.24(4):24—28 • [ 2] 陈体军, 郝 远 .金属的半固态成形技术与应用[ J] . 铸造, 2001, 50( 11) : 645- 6491 • [ 3] 吴炳尧.半固态金属铸造工艺的研究现状及发展前 景[ J].铸造, 1999, ( 3) : 45- 481 • [ 4] 闫淑芳, 扬卵生. 半固态金属浆科制备工艺的研究 进展[ J] . 铸造技术, 2005, 26( 2) : 155- 158.
半固态金属成形技术

二、半固态成形技术的发展简史
起源和发展
半固态加工起源于美国。20世纪70年代初,麻省理工学院 Spencer和Flemings等人发现凝固过程中的金属材料经强力搅 拌,会生成近球状晶或球状晶组织。 30多年的发展历程中,SSM技术在制坯、重熔加热、零件成 形、组织与力学性能、加工环节数值模拟以及合金流变学研究 等许多方面取得重大进展。目前,这项技术已广泛应用于汽车 工业领域,在航空、航天以及国防工业领域也正处于应用的起 步阶段,具有广阔的前景。 半固态金属加工技术是近多年来才诞生和发展起来的现代 冶金加工新技术。它虽然诞生晚, 但发展很快, 只用十几年的 时间就从试验室过渡到试生产, 又很快实现了产业化和商品化。 被世人称为新一代的合金成形工艺。
三、半固态金属加工的优缺点
优点:
(1) 由于在半固态, 合金具有独特的触变 行为, 可成型复杂的薄壁的零部件
(2)加工件的精度高, 几乎是近净成形, 尺 寸公差接近机加精度 (3)成形件表现平整光滑, 内部组织致密, 缺陷少, 晶粒细小, 力学性能高,可达锻 件性能
(4)节省原材料、能源, 生产同样的零部件, 它与普通铸造相比, 节能约35% (5)成品率高, 几乎达100%
半固态金属成形
一、概念
半固态金属成形技术(Semi-Solid Metal processing,SSM),它是利用在固-液态区间 获得一种液态金属母液中均匀地悬浮着一定固 相组分(50%-60%)合金的混合浆料进行加工 成形的方法。 半固态成形是利用金属材料从固态向液态, 或从液态向固态的转换过程中具有半固态的特 性所实现的成形。
影响因素对结构影响的具体分析
1、板长固定,不同板角下的组织形貌
20度
5度
7.5度
半固态压铸工艺过程

半固态压铸工艺( Semi-Solid(Metal(Casting,简称SSM或SSMC)是一种介于传统铸造和锻造之间的先进金属成型技术。
它利用金属在半固态状态下的流变特性进行成型,结合了铸造和锻造的优点。
半固态压铸工艺过程主要包括以下几个步骤:
1.(金属熔炼:首先将金属原料加热至熔点,形成液态金属。
2.(半固态处理:将液态金属冷却至半固态,即部分凝固状态。
这一过程可以通过搅拌、振动或其他方法实现,目的是使金属在半固态时形成均匀的微观结构,包括细小的固态颗粒和液态金属相。
3.(半固态金属的预热:将半固态金属加热至适当的温度,以确保其具有良好的流动性和可塑性。
这一步骤对于保证成型质量至关重要。
4.(压铸成型:将预热后的半固态金属注入压铸模具中。
由于半固态金属的流动性好,可以在较低的压力下填充模具,减少成型缺陷。
5.(冷却与凝固:半固态金属在模具中冷却并凝固,形成所需的零件形状。
6.(脱模与后处理:冷却后的零件从模具中取出,进行必要的后处理,如去毛刺、热处理、表面处理等,以满足最终产品的性能要求。
半固态压铸工艺的优点包括:
提高材料利用率:由于半固态金属的流动性好,可以减少材料浪费,提高材料利用率。
减少成型缺陷:半固态金属的流动性和可塑性有助于减少成型过程中的缺陷,如气孔、缩孔等。
提高生产效率:半固态压铸工艺可以在较低的压力下成型,缩短了生产周期,提高了生产效率。
改善产品性能:半固态压铸工艺可以产生细小的晶粒结构,提高材料的力学性能和耐磨性。
半固态压铸工艺广泛应用于汽车、航空航天、电子和消费品等领域,用于生产各种复杂的金属零件。
半固态成形

日本在20世纪80年代后期就组成了半固志成形公司, Speed Star Wheel公司已应用半固态成形技术牛产铝台金轮 毂。Rheotech公司包括了14个钢铁企业和4个有色金属公司, 从1988年到1994年共投资30亿日元进行开发研究半固态成形 技术。日本制钢所已批量生产镁合金半固态触变铸造机,可 以铸造壁厚为0.5mm的零件,据报道该公司已为全球制造了 100台。另外,日本宇部公司设计制造的新型流变铸造机既 可以进行半固态模锻,又可以进行触变铸造与流变铸造,该 机已出售给奥地利,在2000年投产。
(3)工艺参数控制严格,不利于实现工业生产。
由于半固态成形对固相率控制严格,这就要求温度及冷 却条件等因素控制在较小的波动范围内,这样对于工业生产 的实现提出了更高的要求。同时,利用机械搅拌制备高固相 率的半固态材料比较困难。另外,二次(重熔)加热技术是 半固态成形技术中一个重要的技术环节,在二次加热过程中 要求加热速度较快才能达到理想的效果,这样就对设备提出 了更高的要求。因此,在工业生产中某个参数稍有波动,或 者操作工人的疏忽等,都会对成形工艺有重大影响。因此, 不但技术条件要求严格,而且对操作者的素质提出了更高的 要求对操作者的素质一套严格的控制系统,并对工人的素质 进行提高,才能较好地实现工业化生产。
2. 成形性能好,可实现短流程生产。
半固态材料流动性能与变形性能良好,经过强烈搅拌的固相 分数为40% - 60%的半固态金属的表观黏度在0.1-10Pa.s之间,与 黄油(0.1 Pa.s)、甘油(l Pa.s)及蜂蜜( 10 Pa.s)的表观黏度相当,仅 比水或者液态金属的黏度高出2-4个数量级,表现出很好的流动 性。与固态成形相比,半固态金属中存在液相组元,塑性变形机 理不同于固态塑性成形。塑性变形主要是由于晶粒之间的旋转和 相对滑移引起的,液相起到“润滑”作用,金属流动阻力显著降 低,复杂的零件也可用很少的工步成形。由于半固态合金材料具 有特殊的流变性能,易于加工成形,半固态铸造直接可以生产出 精度较高的产品。与传统生产方法相比,半固态成形可实现近终 形生产,提高了生产率、节约了原材料。与常规金属模铸造相比, 半固态成形汽车零件生产率与成材率高的特点尤为突出。
半固态射出成形技术

半固态射出成形技术第一节触变成形技术(一)背景触变成形主要发展里程如表1所示。
Dow Chemical早在1977年开始就尝试将半固态的概念应用在镁合金上,经过十余年的研究,于1988年制作出300吨雏型机。
1900年Dow Chemical 与另外五家公司联合成幺Thixomat公司,负责技术的商品化及授权,以及应用技术的研发,1991年获得触变成形设备及制程的美国专利,之后陆续取得26国专利。
目前Thixomat授权生产触变成形机的公司仅限于日本制钢所(JSW)及加拿大Husky两家,JSW的机型包括75、220、450、650、及850吨,1998年夏天已推出1600吨机器;Husky刚取得授权不久,初期预定开发90、225、500、及900吨等机种。
1997年为止全世界用于实际生产之机器约65台,估计1998年底可达100台。
现有客户三十余家,分布在日本、美国、加拿大、瑞典、德国、新加坡、韩国、台湾等地,其中九成以上的客户原本是从事塑料射出成形。
另一方面,美国能源部自1997年3月起展开一个400万美金,为期三年的计画,支持Thixomat与Alcoa、Husky以及美国三大汽车厂合作研究铝合金的触变成形,目标产品包括汽车用厚肉(8~10mm)结构件及薄壳(<1mm)连结件,未来可能进一步扩及金属基复合材料(metal-matrix composites)的成形技术。
(二)技术简介触变成形是由塑料射出成形衍生应用在金属的成形制程,米粒大小的金属颗粒原料在氩气保护的料斗进入料管,经螺杆旋转磨擦及料管外加热器提供热量,温度逐渐升高至其固相线温度(solid us temperature)以上,形成部分熔融状态,此时螺杆同时计量后退将半固态黏浆推挤到蓄料区,待蓄储存的黏浆达到所需的量后,螺杆停止转动,高速射出系统驱动杆往前推送黏浆进入模穴。
待工件完全凝固后射出单元后退,螺杆进行下一循环的剪切输送计量,夹模单元则开模顶出,同时进行清除废料及喷离型剂等动作。
半固态金属成形技术

半固态金属成形技术1. 引言半固态金属成形技术是一种新兴的金属加工技术,它将固态和液态的金属材料的优点结合在一起,可以制造出具有高强度、高精度、复杂形状的金属零件,具有极高的应用价值。
本文将介绍半固态金属成形技术的基本原理、应用范围、优点和发展前景。
2. 基本原理半固态金属成形技术的基本原理是将铸造过程中合金中铸晶的分布状态控制在半固态状态,通过控制合金的热状态和机械变形来实现金属成形。
具体而言,就是将合金熔融后,在一定的时间和温度范围内,控制其冷却速度,使合金中的铸晶呈现出部分熔化和形变状态,从而达到半固态的状态。
3. 应用范围半固态金属成形技术可以应用于航空航天、汽车、船舶、机械等领域的制造。
具有如下优点:(1)可以直接制造出高强度、高精度、复杂形状的零件,避免了加工中的残余应力和失真;(2)可以大幅减少加工成本,节约了材料和时间成本;(3)可以提高金属材料的性能和质量,增加产品寿命和安全性;(4)可以生产大尺寸、高质量的零件,提高了生产效率和产能。
4. 优点半固态金属成形技术具有以下优点:(1)成形精度高,可以实现微米级的精度控制;(2)成本低,可以节省大量人力、物力和时间成本;(3)高性能材料制造,可以生产出高强度、高耐热、高耐腐蚀的材料,扩展了金属材料的应用范围;(4)可持续发展,可以对既有材料进行再加工和再利用。
5. 发展前景半固态金属成形技术是一种有前途的金属制造技术,目前已经进入实际应用阶段。
未来,它将逐步替代传统的金属成形工艺,成为重要的先进制造技术之一。
同时,随着科学技术的不断发展,半固态金属成形技术也将不断创新和完善,提高成形速度和效率,扩大应用范围。
预计在未来的十年内,半固态金属成形技术将会取得重要的技术突破,推动金属制造行业的成型和发展。
6. 结论半固态金属成形技术是一种健康、可持续发展的金属制造技术。
它具有高效、高精度、高性能、低成本等优点,可以适应不同的金属制造领域的需求。
铝合金半固态成形技术应用及发展
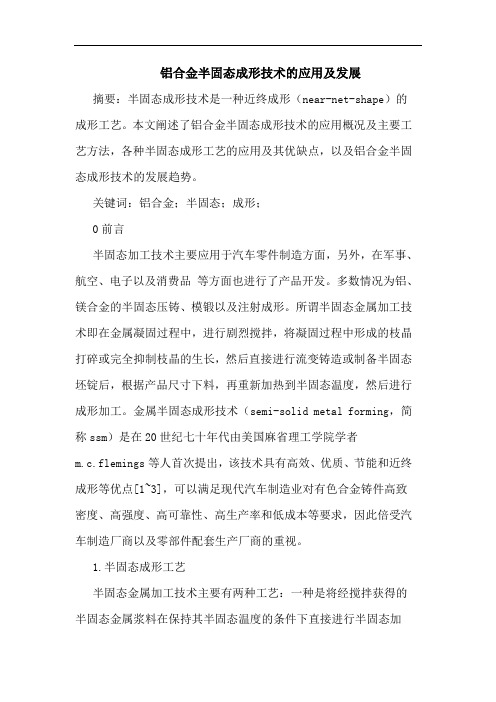
铝合金半固态成形技术的应用及发展摘要:半固态成形技术是一种近终成形(near-net-shape)的成形工艺。
本文阐述了铝合金半固态成形技术的应用概况及主要工艺方法,各种半固态成形工艺的应用及其优缺点,以及铝合金半固态成形技术的发展趋势。
关键词:铝合金;半固态;成形;0前言半固态加工技术主要应用于汽车零件制造方面,另外,在军事、航空、电子以及消费品等方面也进行了产品开发。
多数情况为铝、镁合金的半固态压铸、模锻以及注射成形。
所谓半固态金属加工技术即在金属凝固过程中,进行剧烈搅拌,将凝固过程中形成的枝晶打碎或完全抑制枝晶的生长,然后直接进行流变铸造或制备半固态坯锭后,根据产品尺寸下料,再重新加热到半固态温度,然后进行成形加工。
金属半固态成形技术(semi-solid metal forming,简称ssm)是在20世纪七十年代由美国麻省理工学院学者m.c.flemings等人首次提出,该技术具有高效、优质、节能和近终成形等优点[1~3],可以满足现代汽车制造业对有色合金铸件高致密度、高强度、高可靠性、高生产率和低成本等要求,因此倍受汽车制造厂商以及零部件配套生产厂商的重视。
1.半固态成形工艺半固态金属加工技术主要有两种工艺:一种是将经搅拌获得的半固态金属浆料在保持其半固态温度的条件下直接进行半固态加工,即流变成形(rheoforming);另一种是将半固态浆料冷却凝固成坯料后,根据产品尺寸下料,再重新加热到半固态温度,然后进行成形加工,即触变成形(thixoforming),后者在目前的生产条件下占主导地位。
通常铝合金的半固态加工技术主要有三道工序:半固态坯料的制备、二次重熔和触变成形。
触变成形作为半固态加工技术的最后一道工序,是影响半固态成形件组织和性能的关键工序,直接影响着半固态成形件的组织和性能。
半固态金属加工技术可分为半固态金属铸造法和锻造法。
1.1半固态铸造工艺半固态压铸工艺是目前半固态金属铸造成形的主要成形工艺。
半固态成形技术的工艺流程

半固态成形技术的工艺流程半固态成形技术(Semi-Solid Forming Technology)是一种将合金材料由液态逐渐转变为半固化状态进行成形的高效率制造技术。
下面我将详细介绍半固态成形技术的工艺流程。
半固态成形技术的工艺流程主要包括以下几个步骤:1. 材料准备:选择适合半固态成形的合金材料,通常是金属合金。
合金的主要成分、比例和杂质控制对成品的质量有重要影响。
合金材料经过预处理、熔炼、再结晶等工艺,制备成符合要求的原料。
2. 半固态化处理:原料合金通过加热,使其处于半固态状态。
半固态是指合金同时具有液相成分和固相成分,且两者之间呈现出部分固相悬浮的混合状态。
通过控制半固态化温度和时间,使合金材料达到理想的半固态状态。
3. 成型形式选择:根据产品的形状、尺寸和结构等要求,选择最适合的成型形式。
常用的成型形式有温锻、挤压、注射等。
挤压是其中最常用的成型形式,特点是简单、成本低、生产效率高。
4. 成型设备准备:根据选择的成型形式,准备相应的设备。
例如,在挤压成型中,需要准备好挤压机,根据产品的尺寸和结构确定模具的设计。
5. 成型过程:将半固态合金材料装填到成型模具中,然后施加压力进行成型。
成型过程中,合金材料由半固态状态逐渐变形为固态状态。
压力的大小、速度和时间等参数需要根据具体产品要求进行调控。
6. 去除模具和后处理:成型完成后,将产品从模具中取出,并进行必要的后处理。
后处理包括去除余温、切割、打磨、喷漆等工艺,以使产品满足要求的精度和表面质量。
7. 检测与质量控制:通过一系列的检测手段,对成品进行质量控制。
常用的检测方法包括尺寸测量、化学分析、金相显微镜观察等。
根据产品要求和行业标准,对成品进行合格与否的判定。
整个工艺流程中,原料准备、半固态化处理和成型过程是关键环节,因为这些环节直接影响到成品的质量和性能。
精确控制半固态化温度和时间,以及成型过程中的温度、压力和速度等参数,能够使成品达到精密度高、尺寸稳定、表面质量好的要求。
- 1、下载文档前请自行甄别文档内容的完整性,平台不提供额外的编辑、内容补充、找答案等附加服务。
- 2、"仅部分预览"的文档,不可在线预览部分如存在完整性等问题,可反馈申请退款(可完整预览的文档不适用该条件!)。
- 3、如文档侵犯您的权益,请联系客服反馈,我们会尽快为您处理(人工客服工作时间:9:00-18:30)。
半固态成形技术及其应用【摘要】本文介绍了半固态成形技术的基本原理、技术优点,重点论述了搅拌、非搅拌浆料制备方法的优缺点及触变、流变、注射成形工艺的特点,并阐述了半固态成形技术工业化应用的现状和发展前景.【关键词】半固态成形技术原理浆料制备成形方法应用1前言20世纪70年代,美国麻省理工学院的Flemimgs提出了金属半固态成形技术(SSM),就是金属在凝固过程中,进行剧烈搅拌,或控制固一液态温度区间,得到一种液态金属母液中均匀地悬浮着一定固相组分的固液混合浆料(固相组分甚至可高达60%),这种半固态金属浆料具有流变特性,即半固态金属浆料具有很好的流动性,易于通过普通加工方法制成产品,采用这种即非完全液态,又非完全固态的金属浆料加工成形的方法,就称为半固态成形技术。
2半固态成形工艺的基本原理2.1半固态组织的形成机理2.1.1枝晶断裂机制在合金的凝固过程中,当结晶开始时晶核是以枝晶方式生长的。
在较低温度下结晶时,经搅拌的作用,晶粒之间将产生相互碰撞,由于剪切作用致使枝晶臂被打断,这些被打断的枝晶臂将促进形核,形成许多细小的晶粒。
随着温度的降低,这些小晶粒从蔷薇形结构将逐渐演化成更简单的球形结构。
2.1.2 枝晶熔断机制在剧烈的搅拌下,晶粒被卷入高温区后,较长的枝晶臂容易被热流熔断,这是由于枝晶臂根部的直径要比其它部分小一些,而且二次枝晶臂根部的溶质含量要比它表面稍微高一些,因此枝晶臂根部的熔点要低一些,所以搅拌引起的热扰动容易使枝晶臂根部发生熔断。
枝晶碎片在对流作用下,被带入熔体内部,作为新的长大核心而保存下来,晶粒逐渐转变为近球形。
2.1.3 晶粒漂移、混合—抑制机制在搅拌的作用下,熔体内将产生强烈的混合对流,凝固过程是就在激烈运动的条件下进行,因而是一种动态的凝固过程。
结晶过程是晶体的形核与长大的过程,强烈的对流使熔体温度均匀,在较短的时间内大部分熔体温度都降到凝固温度,再由于成分过冷,熔体中存有大量的有效形核质点,在适宜条件下能以非均匀形核的方式形成大量晶核,而混合对流引起的晶粒漂移又极大的增大了形核率。
然而在长大过程中,强烈的混合对流则极大的改善了熔体中的传热和传质过程,对晶体的生长起到了强烈的抑制作用。
由于混合对流作用,使得熔体的温度和成分相对均匀。
所谓的混合—抑制机制正是指这种环境不利于择优生长,或者说这种生长方式受到了强烈地抑制,而只能选择各个方向长大,于是获得了球状的非枝晶组织。
2.1.4 枝晶弯曲机制V ogel和Doherty 等人认为枝晶臂在流动应力作用下会发生弯曲,并且位错的产生将导致塑性变形的产生。
在固相线以上温度时,位错间发生攀移并且互相结合形成晶界,当相邻晶粒的取相差超过20 ,晶粒晶界能超过固-液界面能的两倍,液体就将润湿晶界并沿着晶界迅速渗透,从而使枝晶臂与主干分离。
2.2半固态合金的流变性能和触变特性影响半固态合金流变性能的主要因素是浆料的固相分数、等温温度和剪切速率。
当剪切速率一定时,表观粘度随固相分数的增加而增加,流型变化为牛顿流体—拟塑性流体—宾汉姆流体。
相比半固态合金的流变性,触变性强调的是表观粘度与剪切时间的依赖关系,它表征半固态浆液的依时行为。
即在剪切作用下,合金液的表观粘度随时间连续下降。
静止时表观粘度随之恢复。
3半固态成形的技术优点1)材料在半固态变形抗力显著降低,可以以较小的力加工较大型零件,加工机械设备可以小型化,简单化,因此可以减少设备投资,节约能源;2)材料在半固态流动性,变形性好,即使很复杂的零件也可以用很少的工步成形,这一点和普通锻造相比是一个显著的优势,并且,半固态成形可以更方便地制造出接近最终形状的制品,缩短了加工周期,提高了材料利用率,有利于节能节材;3)半固态金属合金的温度较液态金属低,成形模具工作温度低于普通压铸,对模具及设备热冲击小,有利于改善模具工作条件,提高模具寿命,从而降低生产成本;4)半固态成形制品结构微细,析出物均一分散,没有普通铸件中存在的粗大枝晶,可改善材料的力学性能,防止内部缺陷,制品整体性能提高;5)利用半固态浆体的高粘性,容易均一地掺入非金属材料和比重差大的金属,制造新的复合材料和新成分的合金,为新材料的研制提供了一条新路。
4半固态浆料制备技术与传统铸造成形相比,半固态金属浆料中包含有类球形的固相颗粒,减少了凝固收缩并提高了补缩能力,从而减轻或者消除了缩松倾向,因而组织优良的半固态金属浆料或坯料的制备是实现半固态金属加工技术的基础及关键。
目前,半固态成形浆料制备主要可分为搅拌法和非搅拌法两大类。
4.1搅拌法4.1.1 机械搅拌法机械搅拌时搅拌叶片与金属熔体直接接触,设备构造简单、工艺参数容易控制。
机械搅拌过程中可以获得很高的剪切速率,利于形成细小的近球形微观结构,但是搅拌槽内部往往存在搅拌不到的死区,影响浆料的均匀性,搅拌叶片的腐蚀以及它对半固态金属浆料的污染,都会对坯料质量带来不利的影响。
4.1.2 电磁搅拌法电磁搅拌属于非接触式搅拌技术,利用电磁感应力将初生的枝晶破碎,其特点是金属液纯净,适用于高熔点合金和大批量生产。
但由于感应电磁力从熔池边界到熔体中心逐渐衰减,当熔融金属四周有凝固外壳形成时,搅拌效果大大减弱,因此不适合制备大尺寸的半固态金属锭料。
同时,电能消耗大,能源供给和搅拌器定子等装置体积大。
电磁搅拌与连铸设备相结合可以为后续触变成形连续生产锭料。
4.2非搅拌法非搅拌制备技术主要包括:应变诱导熔体活化法、喷射沉积法、粉末冶金法、冷却斜槽法、低过热度浇注法等。
这些工艺各具特色,其中某些技术已成功应用于工业化生产中。
4.2.1 应变诱发熔化激活技术(SIMA)应变诱发熔化激活技术(SIMA)是先将合金原材料进行冷变形,然后加热到固液两相区间,在加热过程中,原料先发生再结晶,然后部分融化,使初生相转变成颗粒状,形成半固态材料。
该方法已成功应用于制备不锈钢、铜合金等较高熔点合金中,但由于增加了预变形工序使生产成本提高,与电磁搅拌法相比,它仅仅用于生产小直径坯料。
4.2.2 喷射沉积法喷射沉积法的原理是先将固态金属融化成液态金属,然后雾化为熔滴颗粒,在喷射气体作用下部分凝固的微滴直接沉积在收集基板上。
当每个熔滴所受的剪切力能打碎熔滴内部形成的枝晶时,熔滴凝固后便成为颗粒状。
当加热使其局部融化时,就会得到具有球形颗粒固相的半固态金属浆料。
目前,采用该法对铝合金、黑色金属及金属基复合材料进行了试验并取得成功。
该方法与其他方法相比成本较高,只适用于制备有特殊要求的大尺寸坯料。
4.2.3 低过热度浇注法低过热度浇注法的原理是降低浇注温度,使合金组织逐渐得到细化,当浇注温度接近合金的液相线温度时,可以获得半固态组织。
该法工艺简单,如果得到应用,将会进一步降低半固态成形件的价格,扩大半固态金属的应用范围。
综上所述,制坯方法较多且各具特点,但从生产效率、简便、可靠以及经济原则考虑,在目前乃至今后较长一段时间内,半固态浆料制备方法主要采用电磁搅拌连铸工艺。
5半固态成形工艺半固态合金成形方法很多,但是,其中的流变成形、触变成形和注射成形是三种主要成形方式。
5.1流变加工在凝固期间,对合金施加搅拌,使浆料中形非枝晶固相,然后像液态金属压铸一样直接将半固态浆料注入压型中成形,这种工艺称为流变加工。
由于半固态金属浆料的保存和输送很不方便,因而目前实际成熟应用的流变成形技术只有一种,即射铸技术。
5.2触变加工触变成形工艺是将已制备好的半固态金属浆料快速冷却,凝固成锭坯后,根据产品所需尺寸下料,经二次加热重新加热到固液两相区温度区域进行非枝晶处理,利用它的触变性能进行成形的技术。
该方法是当今半固态成形的主要工艺方法,按成形的方式可以分为:半固态锻造、半固态挤压、半固态轧制、半固态压铸等类型。
5.2.1 半固态锻造半固态锻造是将加热到半固态的坯料,在锻模中进行以压缩变形为主的模锻以获得所需形状、性能制品的加工方法。
半固态锻造可以成形变形抗力较大的高固相率的半固态材料,并达到一般锻造难以达到的复杂形状。
而且,可以用于制造用普通锻造难以成形的许多超合金,有可能用半固态锻造技术制造出特殊材料的耐热零件。
5.2.2 半固态挤压半固态挤压的加工工步和热挤压加工的情况基本相同,即用加热炉将坯料加热到半固态,然后放入挤压模腔,用凸模施加压力,通过凹模口挤出所需制品。
半固态的坯料在挤压模腔内处于密闭状态,流动变形的自由度低,内部的固相成分、液相成分不易单独流动,除挤压开始时若干液相成分有先行流出的倾向外,在进入正常挤压状态后,两者一起从模口挤出,在长度方向上得到稳定均一的制品。
半固态挤压和其它半固态成形方法相比,研究得最多的是各种铝合金和铜合金的棒、线、管、型材等制品。
制品的内部组织及机械性能容易制造均一,也容易操作,今后应用的前景十分广阔,是难加工材料、粒子强化金属基复合材料、纤维强化金属基复合材料成形加工的不可缺少的技术。
5.2.3 半固态轧制具有球状晶的金属合金材料加热到处于半固态时,仅有保持其固体形状不被破坏的强度,变形抗力很低,这种性质对轧制成形有利,现在开发的一种半固态轧制工艺是在轧机的入口处设置加热炉,将被轧制材料加热到所要求的半固态后,送入轧辊间轧制的方法。
对象主要是板材的轧制成形。
5.2.4 半固态压铸半固态压铸主要有两种工艺,分别被称为流变铸造和触变铸造。
流变铸造是在金属凝固过程中施以搅拌,对具有球状晶的半凝固金属进行压铸加工。
触变铸造是指将经搅拌凝固的具有球状晶的材料凝固后,切割成所需长度,在压铸前再加热到半熔化状态,然后进行加工的方法。
普通压铸工艺有一个缺点是液态金属射出时空气卷进制品中形成气泡,在半固态压铸时,通过控制半固态金属的粘度和固相率,进行调整,可以抑制气泡的产生,因此可以加工容易产生气泡,普通压铸工艺难以成形的制品,并可以经热处理提高性能,从而有可能应用到重要零件上,并可以制造锻造难以形成的复杂形状的制品。
5.3注射成形注射成形是直接把熔化的金属液冷却至适宜的温度,并辅以一定的工艺条件压射入型腔成形,该方法类似于塑料的注射成形法。
6工业生产中的应用6.1在铝合金制备中的应用目前半固态最成功和最广泛的应用是在铝合金的制备中。
其原因不仅是因铝合金的熔点较低和使用范围广泛,而且铝合金是具有较宽液固共存区的合金体系。
为此,成为人们首先深入研究的对象,特别值得一提的是半固态成形技术已开始应用于制备铝合金制品。
半固态成形技术的主要市场是汽车工业,成形工艺以铝合金的触变成形为主。
目前,用半固态成形技术生产的汽车零件包括刹车制动筒、转向系统零件、摇臂、发动机活塞、轮毂、传动系统零件、燃油系统以及汽车空调零件等,已经应用于一些名牌轿车上,取得良好的经济效益。
随着对汽车精密化、轻量化、高速、节能等整体功能要求的提高,半固态铝镁合金件的需求量将进一步增多。