金属材料检验
金属材料的缺陷检测与分析

金属材料的缺陷检测与分析第一章引言金属材料在各个领域都有广泛应用,其中包括航空、汽车、建筑、电力等行业。
然而,金属材料在生产过程中难免会产生缺陷,如裂纹、气孔、夹杂等,这些缺陷将会对产品的质量、性能以及寿命产生严重影响。
因此,金属材料的缺陷检测与分析非常重要。
第二章金属材料的缺陷检测方法2.1 目测法目测法是一种简单易行、成本低廉、快速有效的缺陷检测方法。
它适用于表面缺陷的检测,如裂纹、气孔等。
但是,对于隐蔽缺陷,如内部孔洞、异物等,目测法并不适用。
2.2 Z-向超声检测法Z-向超声检测法是一种常用的金属材料缺陷检测方法。
它适用于测量金属材料Z-向方向的裂纹、气孔等缺陷,具有高精度、高灵敏度、非破坏性等特点。
但是,对于X、Y向缺陷的检测,需要使用其他的检测方法。
2.3 钻探检测法钻探检测法是通过钻孔取样的方式对金属材料进行检测。
这种方法适用于隐蔽缺陷的检测,如内部孔洞、异物等。
但是,由于需要对材料进行钻孔,因此会对材料的形状、尺寸、性能产生影响。
2.4 射线检测法射线检测法是一种常用的金属材料缺陷检测方法。
这种方法适用于对金属材料的内部和外部缺陷进行检测。
它具有高精度、高可靠性、非破坏性等特点。
但是,由于射线的辐射性,会对人员和环境造成较大的影响,需要进行严格的安全控制。
第三章金属材料缺陷分析方法3.1 金相分析法金相分析法是一种基于显微镜的分析方法。
它可以对金属材料的组织结构进行观察和分析,进而对其缺陷进行判断。
这种方法具有高精度、高效率、非破坏性等特点,广泛应用于金属材料的缺陷分析。
3.2 X射线衍射分析法X射线衍射分析法是用于分析材料晶体结构和组织结构的一种方法。
它通过对X射线的散射进行分析,推断出材料的晶体结构和组织结构。
这种方法具有快速、准确等特点,可以用于对金属材料的缺陷分析。
3.3 电子显微镜分析法电子显微镜分析法是一种基于电子的分析方法。
它通过对材料的电子结构进行观察和分析,进而得出材料的组织结构和缺陷分析结果。
金属材料检测
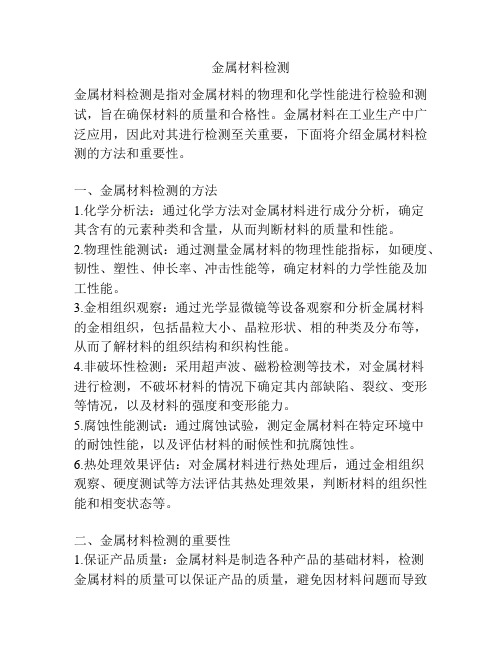
金属材料检测金属材料检测是指对金属材料的物理和化学性能进行检验和测试,旨在确保材料的质量和合格性。
金属材料在工业生产中广泛应用,因此对其进行检测至关重要,下面将介绍金属材料检测的方法和重要性。
一、金属材料检测的方法1.化学分析法:通过化学方法对金属材料进行成分分析,确定其含有的元素种类和含量,从而判断材料的质量和性能。
2.物理性能测试:通过测量金属材料的物理性能指标,如硬度、韧性、塑性、伸长率、冲击性能等,确定材料的力学性能及加工性能。
3.金相组织观察:通过光学显微镜等设备观察和分析金属材料的金相组织,包括晶粒大小、晶粒形状、相的种类及分布等,从而了解材料的组织结构和织构性能。
4.非破坏性检测:采用超声波、磁粉检测等技术,对金属材料进行检测,不破坏材料的情况下确定其内部缺陷、裂纹、变形等情况,以及材料的强度和变形能力。
5.腐蚀性能测试:通过腐蚀试验,测定金属材料在特定环境中的耐蚀性能,以及评估材料的耐候性和抗腐蚀性。
6.热处理效果评估:对金属材料进行热处理后,通过金相组织观察、硬度测试等方法评估其热处理效果,判断材料的组织性能和相变状态等。
二、金属材料检测的重要性1.保证产品质量:金属材料是制造各种产品的基础材料,检测金属材料的质量可以保证产品的质量,避免因材料问题而导致产品的性能差、寿命短等问题。
2.确保安全可靠性:金属材料在一些关键领域应用,如航空航天、核能、化工等,对金属材料的安全可靠性要求极高,检测材料的性能可以确保产品在使用中的安全性和可靠性。
3.优化加工工艺:金属材料的性能会直接影响到产品的加工工艺和质量,通过检测材料的力学性能、组织性能等参数,可以优化加工工艺,提高产品的加工效率和质量。
4.节约成本:金属材料的质量不合格将会导致生产过程中的损失,如废品率提高、生产效率低下等,而及时发现和修复问题,可以节约成本,提高企业的经济效益。
5.科研发展:金属材料的检测研究可以为科学研究提供基础数据和参考依据,促进新材料的研发和创新,推动金属材料行业的发展。
使用无损检测技术进行金属材料硬度检测的方法

使用无损检测技术进行金属材料硬度检测的方法无损检测技术是一种用于金属材料硬度检测的重要方法。
它可以无需破坏材料,准确、快速地测量金属材料的硬度,为工程师和科学家提供了宝贵的信息。
本文将介绍使用无损检测技术进行金属材料硬度检测的方法,并探讨其应用领域和优势。
首先,无损检测技术在金属材料硬度检测中的常用方法之一是超声波检测。
该技术基于超声波在不同材料中传播速度的差异来评估材料的硬度。
通过发送超声波脉冲到待测材料中,然后测量超声波传播的时间来计算材料的声速。
由于声速与材料的硬度密切相关,因此可以根据声速的差异来推断材料的硬度。
超声波检测方法无需破坏材料,操作简单,非常适用于实时监测和大规模生产的应用。
另一种常用的无损检测技术是磁性材料硬度测试方法。
该方法利用了磁场感应原理来测量材料的硬度。
通过将磁感应器放置在待测材料表面,施加标准磁场,然后测量由磁感应器感应到的磁感应强度,可以根据磁感应强度的变化来推断材料的硬度。
这种方法适用于各种金属材料,包括钢铁和铝合金等。
相比于其他方法,磁性材料硬度测试方法具有高精度、可重复性好、不受工件形状和尺寸限制的优点,因此在工业应用中得到广泛应用。
除了超声波和磁性材料硬度测试方法外,还有其他无损检测技术可以用于金属材料硬度检测。
例如,压痕法是一种基于金属材料在受力下变形的原理来检测硬度的方法。
通过在待测材料表面施加一定的压力,然后测量压痕的直径或深度,可以推断材料的硬度。
这种方法适用于各种金属材料,尤其适用于大尺寸和非均匀材料。
压痕法具有简单、精确、可靠的特点,被广泛应用于金属材料硬度检测领域。
使用无损检测技术进行金属材料硬度检测具有许多优势。
首先,它能够准确、快速地测量金属材料的硬度,无需破坏材料,大大提高了工作效率。
其次,无损检测技术适用于各种金属材料,包括铁、铜、铝等常见材料,具有较广泛的适用性。
此外,无损检测技术可以用于在线监测和大规模生产过程,为工程师和科学家提供了实时、准确的数据,有助于优化工艺和改进产品质量。
金属材料成分检测
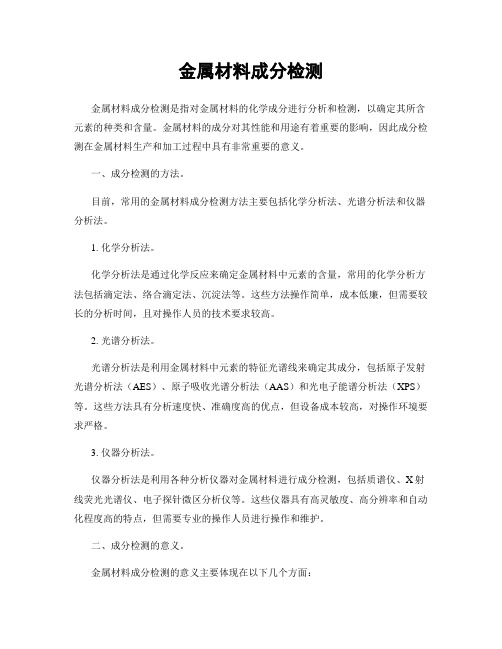
金属材料成分检测金属材料成分检测是指对金属材料的化学成分进行分析和检测,以确定其所含元素的种类和含量。
金属材料的成分对其性能和用途有着重要的影响,因此成分检测在金属材料生产和加工过程中具有非常重要的意义。
一、成分检测的方法。
目前,常用的金属材料成分检测方法主要包括化学分析法、光谱分析法和仪器分析法。
1. 化学分析法。
化学分析法是通过化学反应来确定金属材料中元素的含量,常用的化学分析方法包括滴定法、络合滴定法、沉淀法等。
这些方法操作简单,成本低廉,但需要较长的分析时间,且对操作人员的技术要求较高。
2. 光谱分析法。
光谱分析法是利用金属材料中元素的特征光谱线来确定其成分,包括原子发射光谱分析法(AES)、原子吸收光谱分析法(AAS)和光电子能谱分析法(XPS)等。
这些方法具有分析速度快、准确度高的优点,但设备成本较高,对操作环境要求严格。
3. 仪器分析法。
仪器分析法是利用各种分析仪器对金属材料进行成分检测,包括质谱仪、X射线荧光光谱仪、电子探针微区分析仪等。
这些仪器具有高灵敏度、高分辨率和自动化程度高的特点,但需要专业的操作人员进行操作和维护。
二、成分检测的意义。
金属材料成分检测的意义主要体现在以下几个方面:1. 保证产品质量。
通过成分检测,可以确保金属材料的成分符合产品标准和技术要求,保证产品质量稳定。
2. 提高生产效率。
成分检测可以及时发现材料中的杂质和不良元素,避免因材料质量不合格而导致的生产事故和损失,提高生产效率。
3. 保障产品安全。
部分金属材料中含有有害元素,如铅、汞等,通过成分检测可以及时发现并加以控制,保障产品使用安全。
4. 促进技术创新。
成分检测可以为新材料的研发和应用提供重要的数据支持,促进技术创新和产业升级。
三、成分检测的应用。
金属材料成分检测广泛应用于钢铁、有色金属、合金等各种金属材料的生产和加工领域,包括建筑、航空航天、汽车制造、电子电器等行业。
1. 钢铁行业。
在钢铁行业,成分检测对于保证钢铁产品的强度、韧性、耐腐蚀性等性能具有重要意义,可以有效提高钢铁产品的使用寿命和安全性。
金属材料检测

金属材料检测金属材料检测是指对各种金属材料进行质量和性能的检验和评定,以确保其符合相关标准和要求。
金属材料广泛应用于工程、建筑、航空航天、汽车、电子等领域,其质量和性能直接影响着产品的安全性和可靠性。
因此,金属材料的检测工作显得尤为重要。
一、金属材料检测的意义。
金属材料检测是保障产品质量和安全的重要环节。
通过对金属材料的检测,可以及时发现材料中存在的缺陷、杂质、裂纹等问题,避免因材料质量问题而导致的产品失效和安全事故。
同时,金属材料检测也可以评定材料的物理性能、化学成分、组织结构等特性,为材料的选择和使用提供科学依据。
二、金属材料检测的方法。
1. 物理性能检测。
物理性能检测是对金属材料的硬度、强度、韧性、塑性等性能进行测试和评定的过程。
常用的方法包括拉伸试验、冲击试验、硬度测试等,通过这些测试可以了解材料的力学性能,为材料的选用和加工提供参考依据。
2. 化学成分分析。
化学成分分析是对金属材料中各种元素含量进行测试和分析的过程。
常用的方法包括光谱分析、化学分析等,通过这些分析可以准确地确定材料中各种元素的含量,保证材料符合相关标准和要求。
3. 金相组织检测。
金相组织检测是对金属材料的组织结构进行观察和分析的过程。
通过金相显微镜等设备可以观察材料的晶粒结构、相组成等特征,为材料的热处理和加工提供依据。
4. 表面质量检测。
表面质量检测是对金属材料表面缺陷、氧化层、涂层等进行检查和评定的过程。
通过目视检查、显微镜观察、表面粗糙度测试等方法可以评定材料表面的质量状况。
三、金属材料检测的意义。
金属材料检测是保障产品质量和安全的重要环节。
通过对金属材料的检测,可以及时发现材料中存在的缺陷、杂质、裂纹等问题,避免因材料质量问题而导致的产品失效和安全事故。
同时,金属材料检测也可以评定材料的物理性能、化学成分、组织结构等特性,为材料的选择和使用提供科学依据。
四、金属材料检测的发展趋势。
随着科学技术的不断发展,金属材料检测技术也在不断创新和完善。
金属纯度检测方法
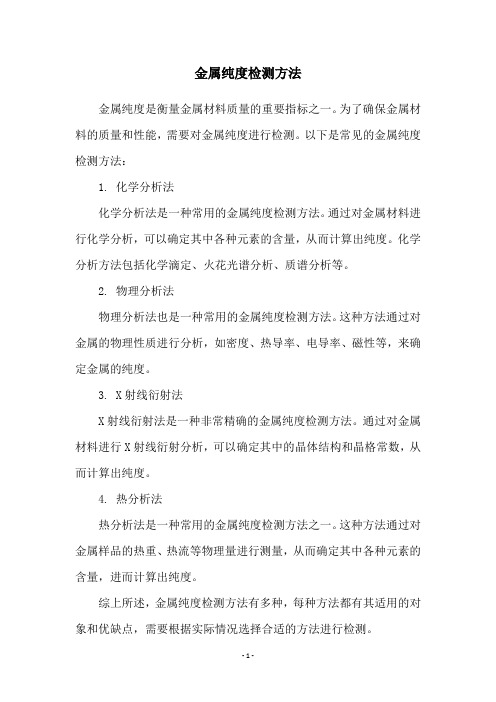
金属纯度检测方法
金属纯度是衡量金属材料质量的重要指标之一。
为了确保金属材料的质量和性能,需要对金属纯度进行检测。
以下是常见的金属纯度检测方法:
1. 化学分析法
化学分析法是一种常用的金属纯度检测方法。
通过对金属材料进行化学分析,可以确定其中各种元素的含量,从而计算出纯度。
化学分析方法包括化学滴定、火花光谱分析、质谱分析等。
2. 物理分析法
物理分析法也是一种常用的金属纯度检测方法。
这种方法通过对金属的物理性质进行分析,如密度、热导率、电导率、磁性等,来确定金属的纯度。
3. X射线衍射法
X射线衍射法是一种非常精确的金属纯度检测方法。
通过对金属材料进行X射线衍射分析,可以确定其中的晶体结构和晶格常数,从而计算出纯度。
4. 热分析法
热分析法是一种常用的金属纯度检测方法之一。
这种方法通过对金属样品的热重、热流等物理量进行测量,从而确定其中各种元素的含量,进而计算出纯度。
综上所述,金属纯度检测方法有多种,每种方法都有其适用的对象和优缺点,需要根据实际情况选择合适的方法进行检测。
金属材料成分检测

金属材料成分检测金属材料成分检测是指对金属材料中的元素成分进行分析和检测的过程。
金属材料的成分对其性能和用途具有重要影响,因此成分检测是金属材料质量控制的重要环节。
本文将介绍金属材料成分检测的常用方法和注意事项。
一、常用方法。
1. 光谱分析法,光谱分析法是一种常用的金属成分检测方法,包括原子吸收光谱法(AAS)、原子发射光谱法(AES)和光电子能谱法(XPS)等。
这些方法通过测量金属材料中元素的特征光谱,来确定其成分含量。
2. 化学分析法,化学分析法是通过化学反应来确定金属材料中元素的含量,包括滴定法、显色滴定法、络合滴定法等。
这些方法对于某些特定元素的检测具有较高的准确度和灵敏度。
3. 质谱分析法,质谱分析法是一种高灵敏度的成分检测方法,能够对金属材料中微量元素进行准确的定量分析。
质谱分析法广泛应用于高纯度金属材料的成分检测。
二、注意事项。
1. 样品制备,在进行金属材料成分检测前,需要对样品进行适当的制备处理,包括样品的粉碎、溶解、稀释等步骤。
样品制备的质量直接影响到成分检测的准确性和可靠性。
2. 仪器校准,在进行成分检测时,需要对检测仪器进行严格的校准,确保其测量结果的准确性。
定期的仪器维护和校准是保证成分检测准确的关键。
3. 数据分析,成分检测后,需要对检测数据进行准确的分析和处理,排除可能的干扰因素,得出准确的成分含量结果。
4. 质量控制,在成分检测过程中,需要建立严格的质量控制体系,包括质量控制样品的使用、实验操作的规范、数据处理的标准化等,确保检测结果的准确性和可靠性。
三、结论。
金属材料成分检测是确保金属材料质量的重要手段,准确的成分检测结果对于金属材料的生产和应用具有重要意义。
在进行成分检测时,需要选择合适的检测方法,严格控制样品制备和仪器校准,进行准确的数据分析和质量控制,以获得可靠的成分检测结果。
通过本文的介绍,相信读者对金属材料成分检测有了更深入的了解,希望本文对您的工作和学习有所帮助。
金属材料检测工作总结范文
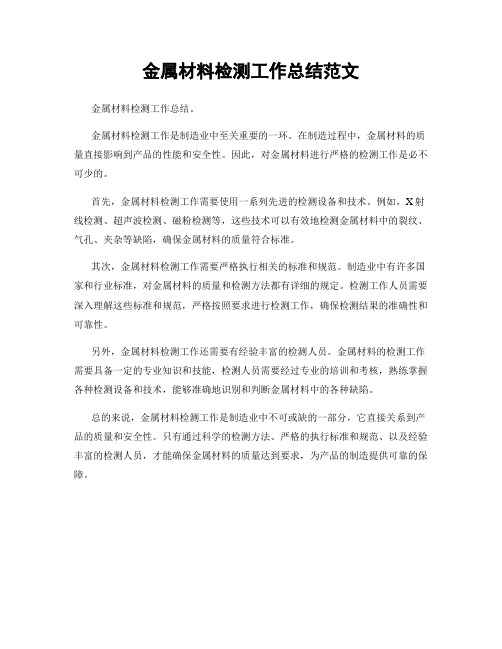
金属材料检测工作总结范文金属材料检测工作总结。
金属材料检测工作是制造业中至关重要的一环。
在制造过程中,金属材料的质量直接影响到产品的性能和安全性。
因此,对金属材料进行严格的检测工作是必不可少的。
首先,金属材料检测工作需要使用一系列先进的检测设备和技术。
例如,X射线检测、超声波检测、磁粉检测等,这些技术可以有效地检测金属材料中的裂纹、气孔、夹杂等缺陷,确保金属材料的质量符合标准。
其次,金属材料检测工作需要严格执行相关的标准和规范。
制造业中有许多国家和行业标准,对金属材料的质量和检测方法都有详细的规定。
检测工作人员需要深入理解这些标准和规范,严格按照要求进行检测工作,确保检测结果的准确性和可靠性。
另外,金属材料检测工作还需要有经验丰富的检测人员。
金属材料的检测工作需要具备一定的专业知识和技能,检测人员需要经过专业的培训和考核,熟练掌握各种检测设备和技术,能够准确地识别和判断金属材料中的各种缺陷。
总的来说,金属材料检测工作是制造业中不可或缺的一部分,它直接关系到产品的质量和安全性。
只有通过科学的检测方法、严格的执行标准和规范、以及经验丰富的检测人员,才能确保金属材料的质量达到要求,为产品的制造提供可靠的保障。
- 1、下载文档前请自行甄别文档内容的完整性,平台不提供额外的编辑、内容补充、找答案等附加服务。
- 2、"仅部分预览"的文档,不可在线预览部分如存在完整性等问题,可反馈申请退款(可完整预览的文档不适用该条件!)。
- 3、如文档侵犯您的权益,请联系客服反馈,我们会尽快为您处理(人工客服工作时间:9:00-18:30)。
分享]金属材料的检验金属材料属于冶金产品,从事金属材料生产、订货、运输、使用、保管和检验必须依据统一的技术标准--冶金产品标准。
对从事金属材料的工作人员必须掌握标准的有关内容。
我国冶金产品使用的标准为国家标准(代号为"国标"GB"")、部标(冶金工业部标准"YB"、一机部标准"JB"等、)企业标准三级。
(一)包装检验根据金属材料的种类、形状、尺寸、精度、防腐而定。
1.散装:即无包装、揩锭、块(不怕腐蚀、不贵重)、大型钢材(大型钢、厚钢板、钢轨)、生铁等。
2.成捆:指尺寸较小、腐蚀对使用影响不大,如中小型钢、管钢、线材、薄板等。
3.成箱(桶):指防腐蚀、小、薄产品,如马口铁、硅钢片、镁锭等。
4.成轴:指线、钢丝绳、钢绞线等。
对捆箱、轴包装产品应首先检查包装是否完整。
(二)标志检验标志是区别材料的材质、规格的标志,主要说明供方名称、牌号、检验批号、规格、尺寸、级别、净重等。
标志有;5.涂色:在金属材料的端面,端部涂上各种颜色的油漆,主要用于钢材、生铁、有色原料等。
6.打印:在金属材料规定的部位(端面、端部)打钢印或喷漆的方法,说明材料的牌号、规格、标准号等。
主要用于中厚板、型材、有色材等。
7.挂牌:成捆、成箱、成轴等金属材料在外面挂牌说明其牌号、尺寸、重量、标准号、供方等。
金属材料的标志检验时要认真辨认,在运输、保管等过程中要妥善保护。
(三)规格尺寸的检验规格尺寸指金属材料主要部位(长、宽、厚、直径等)的公称尺寸。
8.公称尺寸(名义尺寸):是人们在生产中想得到的理想尺寸,但它与实际尺寸有一定差距。
9.尺寸偏差:实际尺寸与公称尺寸之差值叫尺寸偏差。
大于公称尺寸叫正偏差,小于公称尺寸叫负偏差。
在标准规定范围之内叫允许偏差,超过范围叫尺寸超差,超差属于不合格品。
10.精度等级:金属材料的尺寸允许偏差规定了几种范围,并按尺寸允许偏差大小不同划为若干等级叫精度等级,精度等级分普通、较高、高级等。
11.交货长度(宽度):是金属材料交货主要尺寸,指金属材料交货时应具有的长(宽)度规格。
12.通常长度(不定尺长度):对长度不作一定的规定,但必须在一个规定的长度范围内(按品种不同,长度不一样,根据部、厂定)。
13.短尺(窄尺):长度小于规定的通常长度尺寸的下限,但不小于规定的最小允许长度。
对一些金属材料,按规定可交一部分"短尺"。
14.定尺长度:所交金属材料长度必须具有需方在订货合同中指定的长度(一般正偏差)。
15.倍尺长度:所交金属材料长度必须为需方在订货合同中指定长度的整数倍(加锯口、正偏差)。
规格尺寸的检验要注意测量材料部位和选用适当的测量工具。
(四)数量的检验金属材料的数量,一般是指重量(除个别例垫板、鱼尾板以件数计),数量检验方法有:17.按实际重量计量:按实际重量计量的金属材料一般应全部过磅检验。
对有牢固包装(如箱、合、桶等),在包装上均注明毛重、净重和皮重。
如薄钢板、硅钢片、铁合金可进行抽检数量不少于一批的5%,如抽检重量与标记重量出入很大,则须全部开箱称重。
18.按理论换算计量:以材料的公称尺寸(实际尺寸)和比重计算得到的重量,对那些定尺的型板等材都可按理论换算,但在换算时要注意换算公式和材料的实际比重。
(五)表面质量检验表面质量检验主要是对材料、外观、形状、表面缺陷的检验,主要有:19.椭圆度:圆形截面的金属材料,在同一截面上各方向直径不等的现象。
椭圆度用同一截面上最大与最小的直径差表示,对不同用途材料标准不同。
20.弯曲、弯曲度:弯曲就是轧制材料。
在长度或宽度方向不平直、呈曲线形状的总称。
如果把它们的不平程度用数字表示出来,就叫弯曲度。
21.扭转:条形轧制材料沿纵轴扭成螺旋状。
22.镰刀弯(侧面弯):指金属板,带及接近矩形截面的形材沿长度(窄面一侧)的弯曲,一面呈凹入曲线,另一面对面呈凸出曲线,称为"镰刀弯"。
以凹入高度表示。
23.瓢曲度:指在板或带的长度及宽度方向同时出现高低起伏的波浪现象,形成瓢曲形,叫瓢曲度。
表示瓢曲程度的数值叫瓢曲度。
24.表面裂纹:指金属物体表层的裂纹。
25.耳子:由于轧辊配合不当等原因,出现的沿轧制方向延伸的突起,叫作耳子。
26.括伤:指材料表面呈直线或弧形沟痕通常可以看到沟底。
27.结疤:指不均匀分布在金属材料表面呈舌状,指甲状或鱼鳞状的薄片。
28.粘结:金属板、箔、带在迭轧退火时产生的层与层间点、线、面的相互粘连。
经掀开后表面留有粘结痕迹,叫粘结。
29.氧化铁皮:氧化铁皮是指材料在加热、轧制和冷却过程中,在表面生成的金属氧化物。
30.折叠:是金属在热轧过程中(或锻造)形成的一种表面缺陷,表面互相折合的双金属层,呈直线或曲线状重合。
31.麻点:指金属材料表面凹凸不平的粗糙面。
32.皮下气泡:金属材料的表面呈现无规律分布大小不等、形状不同、周围圆滑的小凸起、破裂的凸泡呈鸡爪形裂口或舌状结疤,叫作气泡。
表面缺陷产生的原因主要上由于生产、运输、装卸、保管等操作不当。
根据对使用的影响不同,有的缺陷是根本不允许超过限度。
有些缺陷虽然不存在,但不允许超过限度;各种表面缺陷是否允许存在,或者允许存在程度,在的关标准中均的明确规定。
(六)内部质量检验的保证条件金属材料内部质量的检验依据是根据材质适应不同的要求,保证条件亦不同,在出厂和验收时必须按保证条件进行检验,并符合要求,保证条件分;33.基本保证条件:对材料质量最低要求,无论是否提出,都得保证,如化学成份,基本机械性能等。
34.附加保证条件:指根据需方在订货合同中注明要求,才进行检验,并保证检验结果符合规定的项目。
35.协议保证条件:供需双方协商并在订货合同中加以保证的项目。
36.参改条件:双方协商进行检验项目,但仅作参考条件,不作考核。
金属材料内部质量检验主要有机械性能、物理性能、化学性能、工艺性能、化学成分和内部组织检验。
机械性能、工艺性能第一部分已介绍,这里只对化学成分和内部组织的检验方法的原理及简单过程做概括介绍。
(七)化学成分检验化学成分是决定金属材料性能和质量的主要因素。
因此,标准中对绝大多数金属材料规定了必须保证的化学成分,有的甚至作为主要的质量、品种指标。
化学成分可以通过化学的、物理的多种方法来分析鉴定,目前应用最广的是化学分析法和光谱分析法,此外,设备简单、鉴定速度快的火花鉴定法,也是对钢铁成分鉴定的一种实用的简易方法。
37.化学分析法:根据化学反应来确定金属的组成成分,这种方法统称为化学分析法。
化学分析法分为定性分析和定量分析两种。
通过定性分析,可以鉴定出材料含有哪些元素,但不能确定它们的含量;定量分析,是用来准确测定各种元素的含量。
实际生产中主要采用定量分析。
定量分析的方法为重量分析法和容量分析法。
重量分析法:采用适当的分离手段,使金属中被测定元素与其它成分分离,然后用称重法来测元素含量。
容量分析法:用标准溶液(已知浓度的溶液)与金属中被测元素完全反应,然后根据所消耗标准溶液的体积计算出被测定元素的含量。
38.光谱分析法:各种元素在高温、高能量的激发下都能产生自己特有的光谱,根据元素被激发后所产生的特征光谱来确定金属的化学成分及大致含量的方法,称光谱分析法。
通常借助于电弧,电火花,激光等外界能源激发试样,使被测元素发出特征光谱。
经分光后与化学元素光谱表对照,做出分析。
39.火花鉴别法:主要用于钢铁,在砂轮磨削下由于摩擦,高温作用,各种元素、微粒氧化时产生的火花数量、形状、分*、颜色等不同,来鉴别材料化学成分(组成元素)及大致含量的一种方法。
(八)内部质量检验常见的内部组织缺陷有:40.疏松:铸铁或铸件在凝固过程中,由于诸晶枝之间的区域内的熔体最后凝固而收缩以及放出气体,导致产生许多细小孔隙和气体而造成的不致密性。
41.夹渣:被固态金属基体所包围着的杂质相或异物颗粒。
42.偏析:合金金属内各个区域化学成分的不均匀分布。
43.脱碳:钢及铁基合金的材料或制件的表层内的碳全部或部分失掉的现象。
另外,汽泡、裂纹、分层、白点等也是常见的内部组织缺陷,对内部组织(晶粒、组织)及内部组织缺陷的检验办法常用有:44.宏观检验:利用肉眼或10倍以下的低倍放大镜观察金属材料内部组织及缺陷的检验。
常用的方法有断口检验、低倍检验、塔形车削发纹检验及硫印试验等。
主要检验气泡、夹渣、分层、裂纹晶粒粗大、白点、偏析、疏松等。
45.显微检验:显微检验又叫作高倍检验,是将制备好的试样,按规定的放大倍在相显微镜下进行观察测定,以检验金属材料的组织及缺陷的检验方法。
一般检验夹杂物、晶粒度、脱碳层深度、晶间腐蚀等。
46.无损检验:无损检验有磁力探伤、萤光探伤和着色探伤。
磁力探伤用于检验钢铁等铁磁性材料接近表面裂纹、夹杂、白点、折叠、缩孔、结疤等。
萤光探伤和着色探伤用于无磁性材料如有色金属、不锈钢、耐热合金的表面细小裂纹及松孔的检验。
47.超声波检验:又叫超声波探伤。
利用超声波在同一均匀介质中作直线性传播。
但在不同两种物质的界面上,便会出现部分或全部的反射。
因此,当超声波迂到材料内部有气孔、裂纹、缩孔、夹杂时,则在金属的交界面上发生反射,异质界面愈大反射能力愈强,反之愈弱。
这样,内部缺陷的部位及大小就可以通过探伤仪萤光屏的波形反映出来。
常用的超声波探伤有X光和射线探伤。