熔体强度
pc材料熔体强度

PC(聚碳酸酯)是一种常用的工程塑料,具有优异的物理性能和化学稳定性。
PC材料的熔体强度是指在熔融状态下,材料抵御外部力量的能力。
本文将详细介绍PC材料的熔体强度及其影响因素。
一、熔体强度的定义熔体强度是指材料在熔融状态下的抗拉强度。
它反映了材料在高温下的耐力能力,也是评估材料加工性能的重要指标之一。
熔体强度越高,表示材料在高温下具有更好的稳定性和耐用性。
二、影响熔体强度的因素1. 分子结构:PC材料由聚合物分子组成,分子结构的不同会直接影响熔体强度。
一般来说,分子链越长、分支越少,熔体强度就越高。
2. 熔体温度:熔体温度是影响熔体强度的关键因素之一。
熔体温度越高,分子间的相互作用力就越小,分子链的移动性就会增加,从而提高熔体强度。
3. 加工工艺:材料的加工工艺对熔体强度也有重要影响。
例如,挤出、模压等加工方法可以使材料分子链排列更加有序,提高熔体强度。
4. 添加剂:适量添加增强剂、稳定剂等可以改善材料的熔体强度。
增强剂通常是纤维状或颗粒状的填充材料,它们能够增加材料的刚度和强度。
三、熔体强度的测试方法常用的测试方法包括拉伸试验、热变形试验等。
拉伸试验可以直接测量材料在熔融状态下的抗拉强度和伸长率,从而评估熔体强度。
热变形试验则可以模拟材料在高温下的流变性能和稳定性。
四、应用领域由于PC材料具有较高的熔体强度,广泛应用于各种领域。
PC材料常用于制造电子产品外壳、汽车零部件、光学器件等。
其优异的熔体强度保证了产品在高温、高压等恶劣条件下的稳定性和可靠性。
五、总结PC材料的熔体强度是评估其加工性能和耐用性的关键指标之一。
分子结构、熔体温度、加工工艺和添加剂等因素都会对熔体强度产生影响。
通过合理的材料设计和加工工艺选择,可以提高PC 材料的熔体强度,满足不同领域的需求。
在实际应用中,我们需要根据具体的要求和条件选择合适的PC 材料,并进行相应的加工工艺控制,以确保产品的质量和性能。
同时,我们也需要继续开展研究,不断改进PC材料的熔体强度,推动其在更广泛领域的应用。
塑料加工助剂-熔体强度和熔体压力

石陶网-塑料用加工助剂全球塑料行业的发展非常迅速,年均增长率达到了4%~6%,超过了全球GDP 的增长水平。
这种增长最重要的原因就是塑料材料继续在替代着传统材料如金属、木材、和矿物。
其实,树脂中添加的各种添加剂对于塑料材料的成功应用也大有帮助。
在使用到的各类型添加剂中,聚合物抗冲击改性剂和加工助剂为聚合物提供了最独到和最宝贵的卓越性能,同时还提高了产品的加工性能。
增韧处理、流变性能控制、外观美观性、加工性能以及经济因素都是重要的性质属性。
种种这些添加剂已经使用多年,经过长期的发展衍生出了一系列广泛品种。
造成这种情况的一个主要原因是乳液聚合过程各种多样,这就使得科学家们不断去设计适合的聚合物组分、聚合物结构、聚合物形态以及聚合物分子量/分子量分布。
由于生产成本低,而且所得的乳液产品易于分离,因此,乳液聚合在商业化生产中还是非常有吸引力的。
1956年,第一种用于乳液聚合技术的聚合物添加剂被开发出来,它是由甲基丙烯酸酯-丁二烯-苯乙烯(MBS)制备的核壳结构抗冲击改性剂。
随后出现的是各种丙烯酸类加工助剂和丙烯酸类抗冲击改性剂。
最初,这些添加剂主要用来改善聚氯乙烯(PVC)的加工性能和韧性。
而用于PVC的加工助剂主要是{TodayHot}为了促进PVC的熔融、提升熔体强度、提高分散性能和表面质量。
超高分子量加工助剂则是发泡PVC中的重要组成部分。
借助加工助剂,PVC泡沫能够获得更加均一的发泡结构,减少闭泡的破裂而且泡沫密度会更低一些。
起润滑作用的加工助剂能够有效防止熔融的塑料粘结在金属表面,改善制品表面质量,提高生产效率。
有很多塑料材料的应用范围非常有限,这是因它们要么不具备所需的物理性质,要么其加工性能非常差,加工助剂正是用来增强塑料的熔体加工性、提高产量、减少停车检修时间以及提供产品更好的质量的。
20世纪50年代,罗门哈斯公司率先开发出了第一种商业化生产的加工助剂产品,该产品被用于硬质PVC生产。
在此之后,这种前所未有的技术很快被业界所熟知,并且因而引发了PVC工业的生产热潮。
熔体拉伸流变仪在聚合物熔体强度测试中的应用

Rheological Testing Equipments 熔体拉伸流变仪在聚合物熔体强度测试中的应用CHOOSHIN速度梯度方向平行于流动方向,例:吹塑成型中离开模口后的流动,纺丝中离开喷丝口后的牵伸.流动方向速度梯度的方向拉伸粘度(t): CHOOSHINηa ηtB AC B: ηt 与σ无关:聚合度低的线性高物:POM 、PA-66A :ηt 随σ↑ 而↑,支化聚合物。
如支化PEC :ηt 随σ↑而↓,高聚合度PP拉伸粘度与拉伸应力的关系:高拉伸应变速率在低拉伸应变速率下,熔体服从特鲁顿关系式拉伸粘度(ηt )曲线CHOOSHIN拉伸粘度与拉伸应变速率的关系从结构变化分析:拉伸流动中会发生链缠结,使拉伸粘度降低,但同时链发生伸展并沿流动方向取向,分子间相互作用增加,流动阻力增加,伸展粘度变大.拉伸粘度取决于这两个因素哪一个占优势.典型的拉伸流动曲线Log e Log e平台加工区域应变硬化CHOOSHIN宙兴熔体拉伸简介聚合物熔体拉伸流变仪RHEOTENS主要用于测试熔体强度和测定拉伸流动行为。
它以等速或线性或指数加速方式,通过拉伸一个垂直熔体线料来测量聚合物熔体拉伸特性。
它可以测量拉伸线料的力值,并且可计算拉伸应力、拉伸比和拉伸粘度。
它能辨别在其他测试分析方法(包括剪切测试)中不能测出的微小的差别,显示了其不同的分子结构对拉伸流动的影响。
利用上述流变参数等,进一步分析可得到(1)结构信息,如:分子量分布(MWD),支化等。
拉伸流动比剪切流动更敏感地反映聚合物材料的摹写结构因素。
(2)加工信息,如:模拟实际加工条件,评估拉伸流动的作用,优化工艺条件,提高生产效率等。
(3)验证本构方程,除剪切数据外,拉伸实验数据也为发展材料方程提供了一幅全貌式的图像。
挤出机齿轮泵产生持续恒定的体积流力值测量砝码宙兴熔体拉伸技术特点自由选取测试速度自由选取加速方式,线性或指数模式RHEOTENS 97 软件提供仪器参数设定,试验控制及数据分析拉伸轮表面为齿面,光滑面及锥形光滑面三种导向轮可避免熔体束粘结和缠绕在拉伸轮上。
熔指、熔体强度和熔体粘度
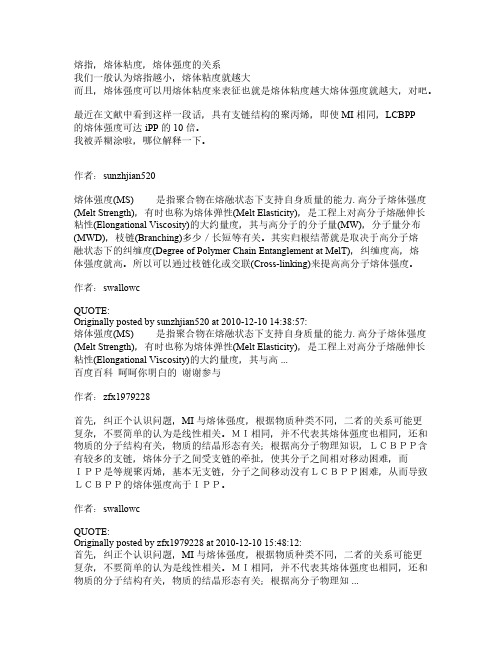
熔指,熔体粘度,熔体强度的关系我们一般认为熔指越小,熔体粘度就越大而且,熔体强度可以用熔体粘度来表征也就是熔体粘度越大熔体强度就越大,对吧。
最近在文献中看到这样一段话,具有支链结构的聚丙烯,即使MI相同,LCBPP的熔体强度可达iPP的10倍。
我被弄糊涂啦,哪位解释一下。
作者:sunzhjian520熔体强度(MS) 是指聚合物在熔融状态下支持自身质量的能力. 高分子熔体强度(Melt Strength),有时也称为熔体弹性(Melt Elasticity),是工程上对高分子熔融伸长粘性(Elongational Viscosity)的大约量度,其与高分子的分子量(MW),分子量分布(MWD),枝链(Branching)多少/长短等有关。
其实归根结蒂就是取决于高分子熔融状态下的纠缠度(Degree of Polymer Chain Entanglement at MelT),纠缠度高,熔体强度就高。
所以可以通过枝链化或交联(Cross-linking)来提高高分子熔体强度。
作者:swallowcQUOTE:Originally posted by sunzhjian520 at 2010-12-10 14:38:57:熔体强度(MS) 是指聚合物在熔融状态下支持自身质量的能力. 高分子熔体强度(Melt Strength),有时也称为熔体弹性(Melt Elasticity),是工程上对高分子熔融伸长粘性(Elongational Viscosity)的大约量度,其与高 ...百度百科呵呵你明白的谢谢参与作者:zfx1979228首先,纠正个认识问题,MI与熔体强度,根据物质种类不同,二者的关系可能更复杂,不要简单的认为是线性相关。
MI相同,并不代表其熔体强度也相同,还和物质的分子结构有关,物质的结晶形态有关;根据高分子物理知识,LCBPP含有较多的支链,熔体分子之间受支链的牵扯,使其分子之间相对移动困难,而IPP是等规聚丙烯,基本无支链,分子之间移动没有LCBPP困难,从而导致LCBPP的熔体强度高于IPP。
熔体强度和弯曲模量

熔体强度和弯曲模量
熔体强度是材料在高温下的抗拉强度,通常用于评估材料在高温环境下的稳定性和可靠性。
在高温下,材料的分子结构会发生变化,因此熔体强度可以反映材料在高温下的变形和破坏行为。
对于高温工作环境下的材料,熔体强度是一个至关重要的指标,例如航空航天领域的发动机部件和高温合金材料等。
弯曲模量是指材料在受力时的抗弯性能,它反映了材料在受力时的刚度和变形能力。
弯曲模量通常用于评估材料在受弯应力下的性能表现,对于需要承受弯曲负载的结构材料,如桥梁、建筑结构和机械零件等,弯曲模量是一个非常重要的指标。
熔体强度和弯曲模量的测试和评估对于材料的选择和设计具有重要意义。
通过对这两个指标的评估,可以帮助工程师和设计师选择合适的材料,并对结构的性能进行合理的预测和设计。
同时,研究和改进材料的熔体强度和弯曲模量也是材料科学和工程领域的重要研究方向,可以为新材料的开发和应用提供重要的参考和支持。
总之,熔体强度和弯曲模量作为材料力学性能的重要指标,在材料工程中具有重要的意义。
通过对这两个指标的研究和评估,可
以为材料的选择、设计和应用提供重要的参考,同时也为材料科学和工程领域的发展提供了重要的支持。
PVC塑化、黏度、流动性

PVC-U的塑化性能、熔体粘度与熔体强度一、塑化度的定义:PVC树脂是由多层粒子聚合而成。
在硬质PVC加工过程中多层粒子结构的形态会发生很大变化。
这种变化是在受热和剪切力的同时作用下产生的。
首先是50-250μm的树脂颗粒破碎游离出1―2μm的初级粒子(或称二次粒子)。
随着加工的进行(如物料在料筒内的输送)物料受到更高温度和剪切力的作用初级粒子破碎。
一般当料温高于190℃时次级粒子可以全部破碎晶体熔化粒子边界消失而形成三维网络结构。
这种三维网络的形成过程称为凝胶化或塑化。
所以,塑化度的重点,是粒子边界消失。
消失的程度决定了塑化度的高低。
假设有10g塑化度100%的PVC颗粒,通过某种不会破坏PVC分子结构的方式,将该颗粒进行破碎。
分别测量破碎为100万份和破碎为1万份后的两种材料的塑化,二者会有显著的不同。
破碎100万份的塑化度会低于破碎1万份的。
这就要求我们关注加工过程中所体现的塑化不足的真实原因。
例如:管材挤出时,相同的材料、设备、挤出模具与工艺。
A条件下,口模光滑,产出的管材表面也是光滑的,进行二氯甲烷试验完全无腐蚀;B条件下,口模表面吸附了较多的析出物,造成管材表面哑光或者粗糙,进行二氯甲烷试验时,可能会出现一定程度的腐蚀。
这种结果显然是口模粗糙导致了管材表面熔体出现破裂现象;除了清理口模,我们假设有一种高度光滑的材料,我们把这种材料加入到PVC混好料中,这种材料不会影响PVC的塑化度,但是挤出时,会析出到管材表面,改善了熔体与口模之间的摩擦力,二氯甲烷试验则会完全无腐蚀。
又例如:生产PVC管件时,相同的材料、设备、注塑模具与工艺。
A条件下,管件烘箱试验完全无开裂;B条件下,将浇口套内径由8mm更换为4mm,此时甚至可能出现无法注满型腔的现象。
即使注满,烘箱试验时,也极为容易出现浇口开裂的现象。
上述两个例子,都是成型过程发生了变化,对材料塑化度的要求没有变化,但是对加工性能提出了更高的要求。
扭矩法测定聚烯烃的熔体强度
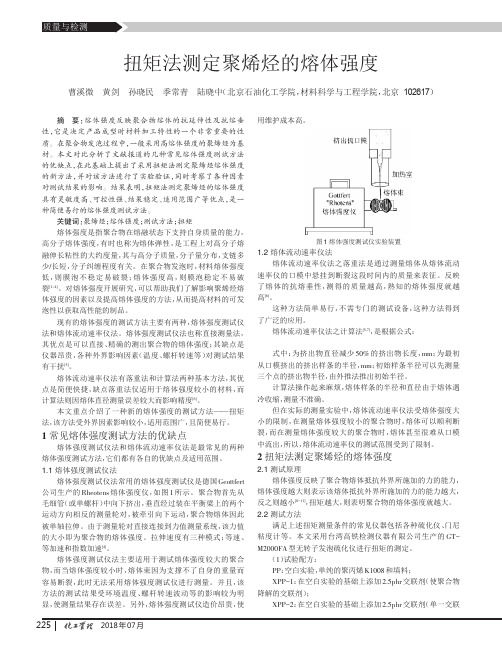
质量与检测
扭矩法测定聚烯烃的熔体强度
熔体流动速率仪法之计算法[5,7],是根据公式:
式中:为挤出物直径减少 50% 的挤出物长度,mm;为最初 从口模挤出的挤出样条的半径,mm;初始样条半径可以先测量 三个点的挤出物半径,由外推法推出初始半径。
计算法操作起来麻烦,熔体样条的半径和直径由熔体强度大 小的限制,在测量熔体强度较小的聚合物时,熔体可以顺利断 裂,而在测量熔体强度较大的聚合物时,熔体甚至很难从口模 中流出,所以,熔体流动速率仪的测试范围受到了限制。
图 2 实际曲线与理想曲线
根据测试数据我们可以得出这样的判定,无论以 ML 或 MH 来代表 XPP 的熔体强度,分析所得的关键影响因素及其最佳水 平均是基本一致的;但考虑到,若在 XPP 制备过程中,假定交联 反应已充分完成(这种假定是合理的,因为在反应条件下,交联 剂的半衰期均小于 1min,而实际反应时间为 10min),则其扭矩 曲线应该是随着时间延长其扭矩应该是逐步减小的,随着时间 的推移逐渐平衡;但实测数据正好相反,即随着测试时间的延 长,扭矩仍有增大的趋势,说明制备的 XPP 在测试过程中仍会 发生进一步的交联反应导致扭矩增大,这种情况可能是由于: 1)材料中残留有未分解的交联剂,这些交联剂在测试过程中进 一步分解,2)据文献报道,机械力也会产生分子链的断裂、产生 自由基,从而导致测试过程中材料发生交联反应、扭矩增大。
1 常见熔体强度测试方法的优缺点
熔体强度测试
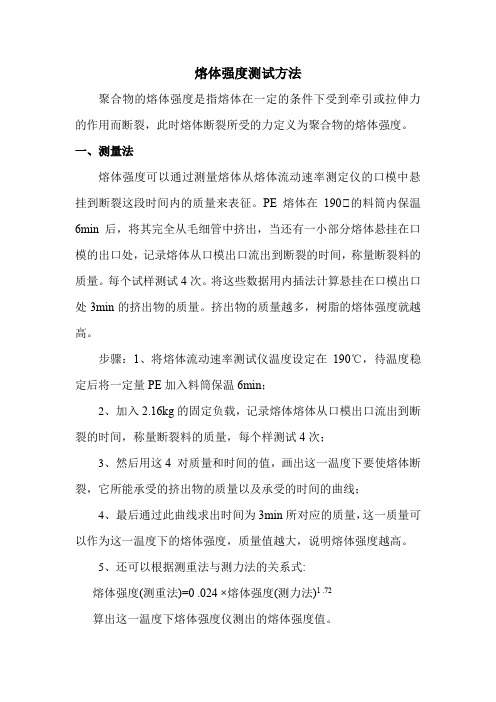
熔体强度测试方法聚合物的熔体强度是指熔体在一定的条件下受到牵引或拉伸力的作用而断裂,此时熔体断裂所受的力定义为聚合物的熔体强度。
一、测量法熔体强度可以通过测量熔体从熔体流动速率测定仪的口模中悬挂到断裂这段时间内的质量来表征。
PE熔体在190℃的料筒内保温6min后,将其完全从毛细管中挤出,当还有一小部分熔体悬挂在口模的出口处,记录熔体从口模出口流出到断裂的时间,称量断裂料的质量。
每个试样测试4次。
将这些数据用内插法计算悬挂在口模出口处3min的挤出物的质量。
挤出物的质量越多,树脂的熔体强度就越高。
步骤:1、将熔体流动速率测试仪温度设定在190℃,待温度稳定后将一定量PE加入料筒保温6min;2、加入2.16kg的固定负载,记录熔体熔体从口模出口流出到断裂的时间,称量断裂料的质量,每个样测试4次;3、然后用这4 对质量和时间的值,画出这一温度下要使熔体断裂,它所能承受的挤出物的质量以及承受的时间的曲线;4、最后通过此曲线求出时间为3min所对应的质量,这一质量可以作为这一温度下的熔体强度,质量值越大,说明熔体强度越高。
5、还可以根据测重法与测力法的关系式:熔体强度(测重法)=0 .024 ×熔体强度(测力法)1 .72算出这一温度下熔体强度仪测出的熔体强度值。
二、测量长度法聚乙烯的熔体强度与熔体流动速率存在以下关系:熔体强度=熔体流动速率2022105.8r l ∆⨯- 式中,为挤出物直径减少50%的挤出物长度,mm ;0r 为最初从口模挤出的挤出物样条的半径,mm ;0r 可分别测量挤出物的长度为1.59、6.35和12.70mm 时挤出物的半径,由外推法而得;还可通过测量同一根挤出物样条上5个不同位置的直径,作该散点图的拟合曲线,再在曲线上用插值法得到,然后由上述关系式得出熔体强度。
l ∆l ∆。
高熔体强度聚丙烯的研究解析

高熔体强度聚丙烯的研究简介1 PP概述聚丙烯(PP),分子量一般为10~50万。
1957年由意大利蒙特卡迪尼(Mont-ecati ni)公司实现工业化生产。
聚丙烯为白色蜡状材料,外观与聚乙烯相近,但密度比聚乙烯小,透明度大些,软化点在165℃左右,热性能好,在通用树脂中是唯一能在水中煮沸,并能在130℃下消毒的品种,脆点-10~20℃,具有优异的介电性能。
溶解性能及渗透性与PE相近。
作为一种通用塑料,聚丙烯具有较好的综合性能,聚丙烯的成型收缩率较聚乙烯小,具有良好的耐应力开裂性。
因而被广泛应用于制造薄膜、电绝缘体、容器、包装品等,还可用作机械零件如法兰、接头、汽车零部件、管道等,聚丙烯还可以拉丝成纤维。
在近年来所举的通用塑料工程塑料化技术中,聚丙烯作为首选材料不断地引起了人们的重视。
但PP也存在低温脆性、机械强度和硬度较低以及成型收缩率大、易老化、而热性差等缺点。
因此在应用范围上,尤其是作为结构材料和工程塑料应用受到很大的限制。
为此,从70年代中期国内外就采用化学或物理改性方法对PP进行了大量的研究开发特别是针对提高PP的缺口冲击强度和低温韧性方面进行了多种增强增韧改性研究开发。
常见的改性方法有共聚改性、共混改性和添加成核剂等。
1.1 PP生产方法和种类中国聚丙烯的工业生产始于20世纪70年代,经过30多年的发展,生产技术、工艺也趋于多样化,已经基本上形成了淤浆法、液相本体-气相法、间歇式液相本体法、气相法等多种生产工艺并举,大中小型生产规模共存的生产格局。
中国的大型聚丙烯生产装置以引进技术为主,中型和小型聚丙烯生产装置以国产化技术为主。
由最初的浆液工艺发展到目前广泛使用的液相本体法和气相法,液相本体法因其不使用稀释剂、流程短、能耗低,现已显示出后来居上的优势。
(1)淤浆法:在稀释剂(如己烷)中聚合,是最早工业化的方法;(2)液相本体法:在70℃和3MPa的条件下,在液体丙烯中聚合;(3)气相法:在丙烯呈气态条件下聚合。
高熔体强度聚丙烯的研究解析

高熔体强度聚丙烯的研究解析高熔体强度聚丙烯的研究简介1 PP概述聚丙烯(PP),分子量一般为10~50万。
1957年由意大利蒙特卡迪尼(Mont-ecatini)公司实现工业化生产。
聚丙烯为白色蜡状材料,外观与聚乙烯相近,但密度比聚乙烯小,透明度大些,软化点在165℃左右,热性能好,在通用树脂中是唯一能在水中煮沸,并能在130℃下消毒的品种,脆点-10~20℃,具有优异的介电性能。
溶解性能及渗透性与PE相近。
作为一种通用塑料,聚丙烯具有较好的综合性能,聚丙烯的成型收缩率较聚乙烯小,具有良好的耐应力开裂性。
因而被广泛应用于制造薄膜、电绝缘体、容器、包装品等,还可用作机械零件如法兰、接头、汽车零部件、管道等,聚丙烯还可以拉丝成纤维。
在近年来所举的通用塑料工程塑料化技术中,聚丙烯作为首选材料不断地引起了人们的重视。
但PP也存在低温脆性、机械强度和硬度较低以及成型收缩率大、易老化、而热性差等缺点。
因此在应用范围上,尤其是作为结构材料和工程塑料应用受到很大的限制。
为此,从70年代中期国内外就采用化学或物理改性方法对PP进行了大量的研究开发特别是针对提高PP的缺口冲击强度和低温韧性方面进行了多种增强增韧改性研究开发。
常见的改性方法有共聚改性、共混改性和添加成核剂等。
1.1 PP生产方法和种类中国聚丙烯的工业生产始于20世纪70年代,经过30多年的发展,生产技术、工艺也趋于多样化,已经基本上形成了淤浆法、液相本体-气相法、间歇式液相本体法、气相法等多种生产工艺并举,大中小型生产规模共存的生产格局。
中国的大型聚丙烯生产装置以引进技术为主,中型和小型聚丙烯生产装置以国产化技术为主。
由最初的浆液工艺发展到目前广泛使用的液相本体法和气相法,液相本体法因其不使用稀释剂、流程短、能耗低,现已显示出后来居上的优势。
(1)淤浆法:在稀释剂(如己烷)中聚合,是最早工业化的方法;(2)液相本体法:在70℃和3MPa的条件下,在液体丙烯中聚合;(3)气相法:在丙烯呈气态条件下聚合。
熔体破裂

挤出物表面出现凹凸不平或外形发生畸变以至支离或断裂的总称。
其起因在于挤出时所用的剪应力过高。
以致熔体各点所表现的弹性应变不一致。
从而使挤出物在弹性恢复过程中出现畸变,以致断裂的现象。
熔体强度是指熔融的聚合物能否很好的支持自身重量的量度指标和加工工艺性关系密切,熔体强度随分子量的增加而增加,随MWD的加宽而增加。
如果熔体强度过小,那么在加工的时候就很容易造成熔体的破裂,制品表面不光滑,形成鲨鱼皮!熔体破裂现象高聚物熔体在挤出过程中,当剪切速率或剪切应力超过某一临界值时挤出物的外观由光滑而变得粗糙、呈竹节状,甚至碎块状,这就是熔体破裂现象。
导致熔体破裂的原因至今仍不完全清楚,一般有两种说法,其一是高聚物熔体的流道壁面滑移现象〔1〕;其二是口模内熔体各点受力作用的历史不同〔2〕。
熔体破裂发生的区域通常是入口区、流道壁面、以及出口区。
研究表明:熔体破裂畸变的量值随口模入口的流线程度提高而减小〔3〕,因此,口模设计时,应尽量减小口模入口角。
由于存在临界剪切速率或临界剪切应力,所以,挤出成型过程中,一般应以达到临界剪切速率或临界剪切应力的挤出速率作为挤出的上限速率,口模设计时应考虑这一点。
熔体破裂是指当一定熔融体流动速率的聚合物熔体,在恒温下通过喷嘴孔时其流速超过某值后,熔体表面发生明显横向的裂纹.对制品的影响:1外观2力学性能处理方法:增大喷嘴,浇道,进料口截面,减少注塑速度,提高料温.底料韧性太差熔体破裂(Melt Fracture),剪切应力超过临界剪切应力后引起的熔体破裂。
一般发生在分子量分布比较窄的LLDPE中。
可以是共挤中层与层之间的剪切应力超过剪切应力(这个时候一般引起透明度下降,在国外的文章中一般叫这种为MA TT;或者ORANGE PELL)也可以是熔体与模具表面的剪切应力大引起的(这个时候,一般表现为表面出现连续的鲨鱼皮现象,一般叫SHARKSKIN)另外还有slip-stick和gross fracture两种熔体破裂,slip-stick一般表现为间歇性鲨鱼皮,gross fracture一般表现为膜泡葫芦形。
高熔体强度聚丙烯牌号

高熔体强度聚丙烯牌号全文共四篇示例,供读者参考第一篇示例:高熔体强度聚丙烯是一种在塑料工业中广泛应用的聚合物材料,具有优良的物理性能和化学稳定性,是一种重要的工程塑料。
高熔体强度聚丙烯主要通过聚合丙烯单体而成,是一种高分子化合物。
在市场上有许多不同的牌号可以选择,下面将介绍几种常见的高熔体强度聚丙烯牌号及其特点。
首先是牌号PP-HM03,这是一种具有较高熔体强度的聚丙烯,适用于各种高强度要求的塑料制品制造。
该牌号的聚丙烯具有优异的刚度和强度,耐热性能较好,具有良好的耐化学腐蚀性能。
PP-HM03广泛应用于汽车零部件、工业设备配件、建筑材料等领域。
除了上述几种常见的高熔体强度聚丙烯牌号外,市场上还有许多其他牌号可供选择。
不同的牌号具有不同的物理性能和化学性能,适用于不同的工程环境和制造要求。
在选用高熔体强度聚丙烯牌号时,需要考虑制品的具体用途和要求,选择适合的牌号可以确保制品具有良好的性能和可靠性。
对于生产厂家来说,选择合适的高熔体强度聚丙烯牌号也可以提高生产效率和降低生产成本。
综合以上所述,高熔体强度聚丙烯是一种具有广泛应用前景的工程塑料材料,不同的牌号适用于不同的工程环境和制造要求。
在选择牌号时需根据具体需求做出合适的选择,以确保制品具有良好的性能和可靠性。
在未来,高熔体强度聚丙烯将继续在各个领域发挥重要作用,为塑料工业的发展做出更大的贡献。
第二篇示例:高熔体强度聚丙烯,是一种具有优异性能的聚合物材料。
在目前的塑料行业中,具有高熔体强度的聚丙烯成为了备受关注的焦点。
高熔体强度聚丙烯的主要特点是其具有更高的结晶度和更好的物理性能,能够抵抗较大的拉伸和压缩力,并具有更好的耐热性和机械性能。
在许多领域中,高熔体强度聚丙烯都得到了广泛应用。
特别是在包装行业、医疗器械、农业等领域,高熔体强度聚丙烯的应用越来越多。
这得益于其优异的性能和耐用性,使其成为了许多行业中不可或缺的材料。
在高熔体强度聚丙烯牌号中,优质的产品有许多种。
熔体强度 剪切速率

熔体强度剪切速率
熔体强度和剪切速率是聚合物熔体加工过程中的两个重要参数,它们之间存在着密切的关系。
首先,让我们了解一下熔体强度的概念。
熔体强度是指聚合物熔体在受到外力作用时抵抗流动的能力。
这个强度越大,表明熔体受到外力作用时越不容易流动。
简单来说,熔体强度是衡量聚合物熔体加工性能的重要指标,对于注塑、挤出、吹塑等加工工艺有着重要的影响。
接下来,我们来看看剪切速率的概念。
剪切速率是指单位时间内作用于聚合物熔体的外力。
这个速率越高,表明聚合物熔体受到的外力越大,也就越容易流动。
在注塑过程中,流道的剪切速率是一个关键的工艺参数,它影响着熔体的流动和填充行为。
熔体强度和剪切速率之间存在着一定的关系。
一般来说,随着剪切速率的增加,熔体强度会降低。
这是因为在外力作用下,聚合物熔体的分子链会发生取向和拉伸,导致熔体强度的降低。
因此,在加工过程中,需要根据聚合物熔体的特性和加工工艺要求,合理选择剪切速率和熔体强度,以保证加工过程的顺利进行和制品质量的稳定。
在实际加工过程中,可以通过调整加工温度、压力、注射速度等工艺参数来控制熔体强度和剪切速率。
例如,提高加工温度可以降低熔体强度,提高注射速度则可以增加剪切速率。
通过合理的工艺参数选择,可以获得良好的加工效果和制品质量。
综上所述,熔体强度和剪切速率是聚合物熔体加工过程中的两个重要参数,它们之间存在着密切的关系。
了解它们的概念和关系有助于更好地理解加工过程和优化加工工艺。
- 1、下载文档前请自行甄别文档内容的完整性,平台不提供额外的编辑、内容补充、找答案等附加服务。
- 2、"仅部分预览"的文档,不可在线预览部分如存在完整性等问题,可反馈申请退款(可完整预览的文档不适用该条件!)。
- 3、如文档侵犯您的权益,请联系客服反馈,我们会尽快为您处理(人工客服工作时间:9:00-18:30)。
熔体强度(MS)是指聚合物在熔融状态下支持自身质量的能力. 高分子熔体强度(Melt Strength),有时也称为熔体弹性(Melt Elasticity),是工程上对高分子熔融伸长粘性(Elongational Viscosity)的大约量度,其与高分子的分子量(MW),分子量分布(MWD),枝链(Branching)多少/长短等有关。
其实归根结蒂就是取决于高分子熔融状态下的纠缠度(Degree of Polymer Chain Entanglement at MelT),纠缠度高,熔体强度就高。
所以可以通过枝链化或交联(Cross-linking)来提高高分子熔体强度。
一般来说,熔体强度高的产品比较适合挤出,熔体强度低的产品比较适合注塑;熔体强度和熔指在数值上是成相反方向的,也就是说熔体强度越高,熔指越低。
但是是否适合挤出或注塑是没有明显区分的,和工艺条件有关。
还有,注塑的熔体强度体现在高剪切下的,因此这里还是需要注意的。
熔体强度不光和分子量有关,和分子中的支链的数量和长度关系很大。
有的时候可以用熔体黏度来表征熔体强度。
聚丙烯(PP)泡沫塑料是20世纪70年代初开发的一种新型材料,它除具有一般发泡制品已知的特点外,还有良好的热稳定性、耐应力开裂性能及较高的拉伸强度和冲击强度,而且具有良好的可回收性,有利于环保。
所有的这些特点使得PP泡沫塑料在汽车、包装、日用品和结构材料等各个领域具有显著的优越性。
目前,国外少数国家如美国、德国及意大利等已经实现了PP泡沫塑料的工业化生产。
我国近些年才开始PP泡沫塑料方面的研究,至今技术仍不成熟,工业化生产还处于起步阶段。
1 PP发泡中的普遍问题PP发泡研究中普遍存在的问题是PP为结晶性聚合物,结晶度较高,在温度到达结晶熔融温度后,其熔体粘度迅速下降,使发泡过程中产生的气体很难保持住。
因此如何提高PP的熔体强度是其发泡成型中一个必须解决的问题。
2 提高PP熔体强度的方法为了解决PP的发泡问题,必须改善PP的熔体强度。
目前主要有下列4种方法,即采用高熔体强度PP(HMSPP)、PP部分交联、PP共混改性、PP/无机物复合材料。
2.1 采用HMSPP分子中含有支链结构的PP即为HMSPP。
HMSPP的熔体强度一般是普通PP的1.5-15倍。
长支链结构改变了普通PP所具有的应变软化的特征,改善了PP在加工过程中的缺陷。
20世纪90年代,HMSPP在发泡成型方面的优势开始显现。
1992年,J.J. Park等采用HMSPP 进行发泡成型研究,发现HMSPP可以有效阻止气体流失,减少泡孔合并,提高PP泡沫塑料的体积膨胀率。
2002-2004年,H.E. Naguib等研究发现,在使用CO2和异戊烷作发泡剂进行挤出发泡时,HMSPP所得制品与线性PP相比,泡孔密度小,泡孔合并现象少。
2006年,Y.Masayuki等在研究中指出,HMSPP的拉伸粘度明显高于普通PP,熔体强度提高。
2007年Hee-Soo Kim等用不同分子量的马来酸酐对PP进行接枝然后进行后处理,发现在一定范围内,PP的分子量越高,接枝后PP的热稳定性越好,熔体强度提高。
由于具有支链结构的HMSPP的熔体强度高,在发泡过程中泡孔不易合并或塌陷,开孔率低,泡孔结构好,因此对其开发利用具有很大意义。
然而,HMSPP的制备需经过复杂的化学反应过程,而且工艺条件难以控制。
目前国外一些公司相继开发出了HMSPP,如奥地利PCD 聚合物公司开发的B6033,Chisso America公司推出的Expan PP,比利时Montell公司生产的Profax PF814,以及Exxon、Rmoco、Shell等公司通过改变聚合方法生产出的HMSPP。
此外,Rexene、Quantum Chemical、ICI及Huntsman等公司也开发了不同牌号的HM-SPP产品。
而国内在该方面的研究才刚刚起步,目前只有北京化工研究院和扬子石化研究院成功研制出了HMSPP。
2.2 PP部分交联交联就是高分子链之间通过支链连结成一个三维空间网状结构。
PP经过适当交联之后,熔体强度会有显著提高。
交联的方法有辐射交联和化学交联两种。
2.2.1 辐射交联辐射交联是在光或各种高能射线的作用下进行的,比较常用的是电子辐射和60Coγ射线辐射。
20世纪80年代中期,日本Nojiri等研究了PP辐射交联发泡过程,通过加入酚类化合物提高交联效率。
1987年,Hi-mont公司采用电子阴极射线辐射直链PP,使其产生长链支化,生产出较高重均分子质量和较高支化度的PP。
1995年,Basell等研究了一种制备具有高熔体强度PP的方法。
在氮气气氛、室温条件下,通过小剂量辐射高分子量PP,在其结晶阶段诱发边界反应,使其分子链断裂并移植、交联,从而获得具有支链结构的PP、并发现该种产物有利于发泡。
2004年,Debras等研究了电子辐射量至少为5MeV,使用10kGy辐射剂量的情况下制备具有高熔体强度的PP,这种方法类似于Basell的技术。
2007年,A.B.Lugao等对PP辐射交联做了系统的研究,分析了PP辐射交联的技术并对PP辐射交联进行了展望。
国内,北京化工研究院的乔金梁等成功进行了低辐射剂量辐射交联生产发泡PP材料及制品的研究,并申请了专利。
2003年,北京化工大学王永斌等在PP中加入双官能度敏化剂SR213,再经60Coγ射线辐射后,制得了具有长链支化结构、微凝胶含量的PP。
这种PP克服了普通PP熔体强度方面的缺陷,其拉伸强度、冲击强度等力学性能都有较大程度的提高,并且凝胶含量很小,能满足进一步成型加工的需要。
然而,PP与其它聚烯烃相比,由于其本身分子结构的特点,交联比较困难,而且成本较高,因此目前实际应用仍比较少。
2.2.2 化学交联化学交联在PP中的应用比辐射交联要晚一些,是改善PP熔体强度的一种较常见的方法。
化学交联是在有机过氧化物作用下生成自由基,然后进一步分解或发生交联反应。
初期PP的化学交联研究主要是加入少量的有机过氧化物进行化学交联。
PP在有机过氧化物的作用下发生交联,但同时又易发生降解,解决方法是添加合适的助交联剂。
通常采用多官能团的物质作为助交联剂。
国外Chodak公司研究了在有多官能团单体存在情况下PP的化学交联,选用的单体是双马来酸二丙烯酯(DAM)和四甲基丙烯酸季戊四醇酯(PETM)。
结果表明,多官能团单体可显著提高交联效率。
20世纪80年代,关于PP化学交联发泡过程的研究较多,国外发表了很多专利。
1982年,德国Elohmar通过PP和聚丁烯或(乙烯/乙酸乙烯酯)共聚物(E/VAC)混合,利用有机过氧化物交联进行低密度发泡PP制品的生产。
1985年,日本Kimura等在其专利中介绍了一种新的化学交联方法。
首先将交联剂、发泡剂与基体PP熔融混合后注入到加有润滑剂的长形口模中,然后加热熔体使交联剂和发泡剂分解,使PP交联和发泡剂分解都在口模中完成,最后将混合物熔体注入低压区发泡成型。
制得酌泡沫样品泡孔均匀、泡孔结构较好。
1996年,日本Ueno等利用PP和1,2-聚丁二烯共混进行发泡。
在高温高压下,1,2-聚丁二烯中具有化学活性的乙烯基侧链在热和剪切作用下发生分子间交联或分子内环化,反应后的产物与PP分子链紧密缠绕在一起,降低子混合体系的粘弹特性的温度敏感度,扩大了PP的发泡温度范围,提高了PP的发泡倍率和发泡性能,制得了泡孔结构均匀、表面规整的泡沫塑料制品。
2002年,G.Kotzev用叔丁基过氧化乙烷和对苯二酚分别作为交联剂和交联助剂,对PP/低密度聚乙烯(LDPE)共混物进行交联反应注射成型,制得的交联发泡样品的泡孔大部分是球形结构,且泡孔分布均匀。
研究表明,作为交联助剂的对苯二酚的含量对凝胶含量和泡孔结构影响很大。
当对苯二酚含量过多或过少时,PP分子降解严重,粘度低,从而使泡孔合并增加,泡孔形状不规则且分布不均匀。
2005年,A.Marcilla等研究了不同的过氧化物及聚丁二烯浓度对PP交联的影响,发现随着聚丁二烯用量的增加,交联度提高。
2006年,A.Thitithammawong等研究了PP与环氧天然橡胶的交联,讨论了不同的氧化剂类型、浓度及温度对交联效率的影响,并指出合适的氧化剂是获得良好交联的重点。
国内在PP交联发泡研究方面起步较晚,近些年也做了很多研究。
1998年,北京燕山石化研究所的孟翠省使用过氧化二异丙苯(DCP)作为交联剂和二乙烯基苯作为助交联剂,通过合理选择发泡剂和工艺路线,得出了制备PP发泡专用料的合理配方和最佳的工艺路线。
2001年,北京化工大学鲍洪杰等介绍了一步法交联PP挤出发泡成型技术。
首先将混有发泡剂、交联剂和其它助剂的PP在挤出机内进行塑化,与此同时发生适度的交联反应。
控制工艺条件,在具有适当的熔体粘度后令发泡剂完全分解。
而后混合体系经挤出在机头口模处发泡。
山西省应用化学研究所的张红宇在PP中加入不同含量的引发剂DCP及交联剂对PP进行化学交联,提高了PP的熔体强度。
2002年,四川大学的孙洲渝利用DCP与乙烯类化合物分别作为交联剂和助交联剂、双氰胺改性偶氮二甲酰胺(ADC)为发泡剂,制得了可发性微孔PP注射粒料。
2003年,华北工学院李迎春等以DCP为交联剂,二乙烯基苯为助交联剂,使PP在发泡前交联,并利用压制成型方法制得了泡孔均匀、细密的泡沫板材。
PP部分交联之后,提高了熔体强度,改善了发泡性能。
然而,由于PP分子结构的特点,在交联的同时易发生降解,交联过程比其它聚烯烃要困难得多。
此外,在PP交联反应时加入的化学交联剂通常对人体有害,所制得的交联发泡产品可降解回收性差,不利于环保,PP 的部分交联方法仍有待于进一步研究、改善。
2.3 PP共混改性PP与其它聚合物共混改性可以获得良好的发泡性能,此技术受到了足够重视,发展很快,是当今研究的热点。
2.3.1 不同PP共混由于聚合方法不同,分子量及分子结构不同,PP性能也有很大差异。
通过将不同PP共混可以提高PP的发泡性能。
早在1969年,德国Eberle等就进行了相关的研究,将高分子量等规PP和低分子量PP进行混合。
由于低分子量PP不仅与化学发泡剂具有较好的亲和性,又与高分子量PP充分相容,因而化学发泡剂可均匀分散于整个聚合物体系中,从而制得泡孔结构较好的制品。
1990年,美国Amoco公司通过将不同比例的低粘度等规PP和高粘度无规PP共混进行挤出发泡成型,制得了密度低于0.2g/cm3、泡孔结构较好的制品。
2002年,A.C. Chang等分别从结构和力学性能方面对普通PP和HMSPP的混合物进行了大量的研究,发现HMSPP的加入提高了材料的拉伸弹性模量及熔体强度,与此同时,材料的横纵断面强度也得到了提高。