{选篇}一份老外的TPM讲义 ln
TPM培训讲义[1]
![TPM培训讲义[1]](https://img.taocdn.com/s3/m/6268eddd960590c69ec376a0.png)
2.生产保养的历史 ---TPM的产生
1994年--发展:
最近,有关ISO9000及ISO14000的验证取得,已经成为TP M优秀奖获奖厂商在实施TPM活动中的一环。以往,TP M总是让人觉得只有大企业才会实施,在中小型企业似乎没 有实施TPM的本钱,鉴于此,各国在近几年也在致力研究 推广适合中小企业的TPM,期使整体产业都能受益。 2000年--新发展: 贯穿全公司管理流程的活动已经成为新TPM的重要主题, 另一个结合Lean精神的消除浪费活动,从以往以设备为主 的八大浪费扩展为全公司的20大浪费或30大浪费改善活动。
TPM培训讲义[1]
3.生产保养的历史 ---纪元
TPM培训讲义[1]
3.TPM的定义
1971年的定义: 1.以达到设备的最高效率为目标 2.建立以保养预防、预防保养、改良保养之设备生涯为
对象的全面生产保养制度 3.规划设备的人(计划部门)、使用者(制造部门)和保养
的人(保养部门)等,所有关系者共同参与 4.从高阶主管到第一线全员参加 5.以自主的小集团活动来推动PM
TPM培训讲义[1]
3.TPM的定义
1989年的定义:
1.以建立出追求生产系统效率化极限的企业体质为目标 2.在现场现物所构筑的生产系统中,以全体生命周期为对
象,追求「零故障」、「零不良」、「零灾害」,防止 所有损失于未然 3.从高阶主管到第一线全员参加 4.以重复小集团活动来达成零损失
TPM培训讲义[1]
4.TPM的活动重点 ---TPM展开的五大重点(1989年之前)
1.设备效率化的个别改善(以管理者及技术支持者来进行6大 损失之对策) 2.建立以作业人员为中心的5S(自主保养)体制 3.建立保养部门的计划保养体制 4.操作及保养技能的训练 5.建立设备初期管理的体制
TPM讲义教材[1]
![TPM讲义教材[1]](https://img.taocdn.com/s3/m/cff34fdfc77da26925c5b091.png)
設备的改善 营运的系統化
保养组织的效率化
操作失误的防止 設备清扫的实施 日常点检的实施 定期点检的实施 故障解析的实施 保养计划的确立
修理整备技能提升 预防保养的实施
改良保养的实施
润滑管理
预备品的管理
TPM讲义教材[1]
. 自主保全和专门保全的技能分担
目标
设 备 综 合 效 率 90 以 上
PPT文档演模板
PPT文档演模板
TPM讲义教材[1]
故障的分类及损失结构
损失
结果 故障,停止损失 P 小停止损失 Q 换工程调整损失 C 速度低下损失 D 性能低下损失 S 成品不良损失 M 保养费用损失
人员过剩损失 灾害发生损失
P:生产量 C:成 本 S:安 全
Q:品 质 D:交货期 M:士 气
----------致命故障 MTBF ---------长时间故障 分析 --------- 一般故障
2)测定老化的活动(主要依据 5感) •日常点检 •定期点检的一部分
3)恢复老化的活动 •小整备(简单的部品交换,异常时的应急措施) •故障,其它缺陷发生时迅速正确的联络 •突发修理的援助
PPT文档演模板
TPM讲义教材[1]
. 保全部门的作用
1) 本来业务的保全活动 •以老化测定和老化复原为中心的活动和定期保全,预知保全,改良保全等相比 是技术, 技能要求领域的主力
2) 运转部门的自主保全活动支援 •设备的机能,构造,部品名称,不分解的话就不能进行不好部位的重点指导 •螺丝,折叶等的连接处的相关教育指导 •润滑,油料种类的统一,加油基准的作成指导 (加油介绍,油种,周期) •点检技能的教育指导,点检技能的作成指导(POINT,周期) •老化,基本条件,缺陷等不合理工程的迅速处理 •发生源,困难改小对策,效率化等改善活动的技术援助 •日日活动(对于现场,现物会议,保全等邀请事项的听取)实践
TPM讲义
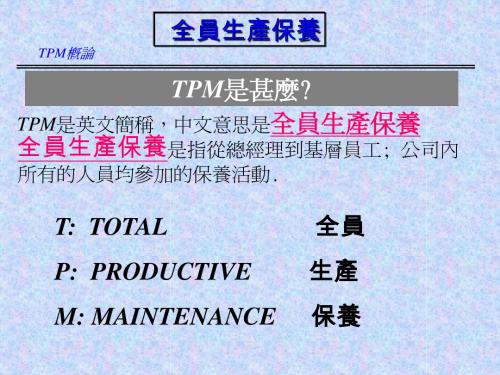
說
明
計劃停止損失 故障損失 換模、換線換失 刀具損失
极 小 化 1/10 极小化 刀具壽命 的极大化
之休止時間朝向极小化損失
對所有的設備都要達到0 盡量在短時間內(10分鐘以內),調整0 縮小誤差, 使不均壽命延長
暖機損失
短暫停機損失 速度降低損失 不良、修機損失
极小化
1/10 0 0
盡量在短時間內(10分鐘以內)
全員生產保養
TPM概論
TPM是甚麼? TPM是英文簡稱,中文意思是全員生產保養 全員生產保養是指從總經理到基層員工; 公司內
所有的人員均參加的保養活動.
T: TOTAL
全員
P: PRODUCTIVE
M: MAINTENANCE
生產
保養
全員生產保養
TPM概論
為何要實施TPM?
為了克服外在嚴苛的經濟環境,求取永續生存及全體員工的福祉而導入 TPM活動,來革新生產方式,改革企業體質,使公司立足臺灣,技冠全球.
全員生產保養
TPM概論
故障的种類
●功能停止型故障 設備因突發性停止的故障 ●功能降低型故障 設備在運轉,但依然會發生工程 不良等其他損失的故障
全員生產保養
TPM概論
達到效率化的指標
設備總合效率=時間稼動率 * 性能稼動率 * 良品率
◎故障損失
◎換模、換線調整 損失 ◎短暫停機空轉 損失 ◎速度降低損失 ◎不良、修理 損失
全員生產保養
TPM概論
設備總合數率之計算方法
性能稼動率
性能稼動率是由速度稼動率及淨稼動率而來 速度稼動率意味著速度之差,也就是設備本來的能力 (周期時間、衝程數)與速度的比率, 換言之,即在確認其是否在一定的速度(基準度數、周 期時間)下實際稼 如果設備運轉速度降低時,其損失速度又是如何的一种 計算方式
TPM公开课讲义PPT82页课件

第二步:消除问题源和难以清洗检查的区域
问题源和难以清洗检查的区域从根本上杜绝污垢改进设备,使清洗,检查,上润滑油更容易缩短作业时间 需要创造和革新
确定污染源
我如何才能止住这些污染?
发生源对策的原则:发生源的根绝→发生量的极小化→防止飞散→防止侵入
实践性发生源对策活动一次是不够的。应反复思考、反复实验
3)保全技术的研究,开发和保全标准的设定4)保全实绩的记录和保全情报系统,保全效果测定系统的构筑5)故障解释手法的研究,重大故障的复发防止活动的实践6)设备设计,开发部门的协助(MP设计,初期管理活动)7)预备品,器工具,技术资料的管理
保全部门的作用
TPM与PM差异
区分
TPM
PM
目的与目标
以设备维护人员为中心的PM,通过对设备设计、制作和保全方法,追求极限设备综合效率,并不涉及到设备使用方法的极限综合生产效率。
TM
TM
TL
I.E.Mngr.IIE经理
Manuf.Mngr.制造部经理
自主维护小组
步骤2:领导职责
从步骤1 起跟踪问题 向TPM小组介绍改善活动 鼓励、讲授和提供指导,使TPM小组和新小组轻松理解;示范好奇心如何导致改进 促进小组成员提出改进提案 管理改善提案汇编表并确保维修工作迅速实施
信赖性
强度向上
负荷的减轻
程度向上
保全性
监督条件的开发
检查作业的改善
整备作业的改善
整备品质的向上
正常运转
正确操作
准备交替调整
日常保全
清扫 · 潜在缺陷的找出 · 措施
加油
拧紧
使用条件, 老化的日常检查
小整备
定期保全
定期点检
TPM培训讲义课件

01
根据生产需求,明确设备应具备的功能、性能参数及技术要求
。
设计方案评估与优化
02
对设备设计方案进行全面评估,确保满足生产需求、降低成本
、提高可靠性。
设备布局与配套设施规划
03
合理规划设备布局,确保设备安全、高效运行;同时考虑配套
设施如电力、气源、排水等。
设备采购、安装及调试流程
01
02
03
设备采购
按照预防性维护计划,对设备进行定期检查、保养、更换易损件等 活动,防止设备故障发生。
建立检查记录与档案
对每次检查、保养、维修等活动进行记录,建立设备档案,方便后 续管理和维护。
03
CATALOGUE
计划保全与故障排除技巧
计划保全策略制定及实施步骤
设备状况评估
定期检查设备运行状态,收集 设备运行数据,评估设备性能
确定团队领导及核心成 员角色定位
建立有效的团队协作与 沟通机制
设定团队目标与工作计 划
培训需求分析和课程体系设计
01
02
03
04
调研分析员工技能现状及培训 需求
制定针对不同岗位和层级的培 训课程
设计符合TPM理念的课程体 系架构
评估课程效果并持续优化更新
内部讲师选拔培养及激励机制
制定内部讲师选拔标准与流程
01
02
03
04
维修流程梳理
对设备维修流程进行全面梳理 ,明确各环节职责及工作要求
。
维修效率提升措施
制定并实施维修效率提升措施 ,如采用快速维修工具、优化
维修步骤等。
维修人员培训
加强维修人员技能培训,提高 维修效率和质量。
维修备件管理
一份老外的tpm讲义.ppt

7
Performance Excellence:
Expanding the Strategy through TPM
Introduction Role in Lean Manufacturing Role of the Operator in TPM Autonomous Maintenance Implementation Equipment Performance: Measurement and Management
5
Total Productive Maintenance
What it is:
1. Optimizes equipment efficiency 2. Implements a company wide Preventive Maintenance system 3. Involves production equipment designers, operators, and maintenance
Lecture notes Participant manual
2
Table of Contents
Executive Overview
Session 1.0 Session 2.0 Session 3.0 Session 4.0 Session 5.0
Introduction……………………………………...3
* High safety risk tasks
* Basic adjustments
20
Maintenance Task Allocation between Production and Maintenance
TPM——讲义PPT课件

•2020/3/28
•29
2 自主保养step2导入推动 哲理小故事
•小蜗牛:为什么我们从生下来,就要背负这个又重又硬的壳呢? •妈妈:因为我们的身体没有骨骼的支撑,只能爬,又爬不快,所以
要这个壳的保护!
•小蜗牛:毛虫姐姐没有骨头,也爬不快,为什么她不用背这壳呢? •妈妈:因为毛虫姐姐能变成蝴蝶,天空会保护她啊。
2 -原因
表
文件中所有带有“为什么”的语句都3 -为会什么定? 义真正的3根-原源因 (通常需要至少5个“为什么”)
4 -为什么?
4 -原因
5 -为什么?
5 –根源
•2020/3/28
•35
2 自主保养step2导入推动
5Why质量工具简介
注意!!!
五个为什么
问五次为什么
5
•2020/3/28
•36
•2020/3/28
•8
1 TPM基础概念回顾
“一套三表”的概念
何谓“一套三表”?
《自主保养暂定基准书》----岗位操作员每月例行常规保养项目标准
《自主保养查检表》--------依照《自主保养暂定基准书》的执行记 录
《不良点标签汇总表》------执行保养的过程中发现异常(不良点) 记录,
并追踪复原、改善
奇怪为什麽?每周都要 换 O型密封圈。
换上一个 O型密封圈, 再换上一个活塞杆。
•2020/3/28
•20
2 自主保养step2导入推动
一个月之后,汽缸又
开 始漏油。
为什么 活塞杆
又
损坏,认真观察发现是
工
•2020/3/28
•21
2 自主保养step2导入推动
换上一个 O型密封圈, 再换上一个活塞杆, 加上一个盖子。
tpm讲义大全[1]
![tpm讲义大全[1]](https://img.taocdn.com/s3/m/17f951c527284b73f342508d.png)
PPT文档演模板
tpm讲义大全[1]
波及世界的TPM
1.亚洲地区(日本以外)
韩国(现代汽车,三星,LG) 台湾(中华映管) 新加坡(纳基工业) 印度尼西亚(尤尼利巴) 马来西亚
2.欧洲国家
比利时(VOLVO EUROPA) 德国(VW) 波兰(SAAB-VALMET) 法国(SOLLAC.FOS、MBK、RENAULT雷诺车) 意大利(FIAT) 瑞典、荷兰 葡萄牙
4- MP保全预防
Maintenance Prevention
5- PM生产保全
Productive maintenance
1950年以前,半自动、手动操作设备多,结构也简 单,常采用的方法。在设备出现故障后再维护。
1950年以后,人们发现设备故障总在某部位出现, 因此在维护时主要去查找薄弱部位并对其改良。
而TPM(Total Productive Maintenance),是“全员生产保 全”的简称,目的是在各个环节上持续不断地进行改善,积小善为
大善,最终达成整体上的创新飞跃;同时通过标准化活动,将创新 取得的成果持久地加以保持。
海信之所以作出这个决定,最直接的诱因源于韩国三星的TPI/ TPM。三星因为推行TPI/TPM之后,整个集团的管理发生了脱胎换 骨的变化。事实上,在三星大力推行TPI/TPM之前,排名韩国前三 个大集团公司之间存在的差距并不大。但是,1997年亚洲金融危机的 爆发,促使三星加大了推行TPI/TPM,并裁减冗员30%。此后,三
Total Perfect Manufacturing
Total Plant Management 全面工厂管理创新
Total Profitable Management
PPT文档演模板
TPM培训讲义课件142张

• 只要我们坚持做下去,我们也敢于象日本人那样,追求并 期待“零”目标的实现。
第二部分:TPM活动内容
一、自主保全
(一)、什么是自主保全
第一部分:认识TPM
一、什么是TPM
TPM即全员效率维修(Total Productive Maintenance)。 定义:
以最有效的设备利用为目标,以维修预防、预防维 修、改善维修和事后维修综合构成生产维修为总运行体 制,由设备的全程管理部门、使用、维修等所有有关人 员,从最高经营管理者到第一线作业人员全体参与,以 自主的小组活动来推行生产维修,使损失最小化,效益 最大化的活动。 要点:效率最大化、全员参与
自主保全活动就是以操作人员为主,对设备和装置 依据特定的标准,凭五官进行外表层面的检查。通过一 定的教育训练,使之自主开展清扫、点检、加油、紧固 等设备保全活动,及进一步能对微小的故障做简单的修 理和改善。
我们可以尝试开展如下活动: 1)保养(清扫):对设备工作环境进行清洁和整顿。 2)点检:对设备基本工作环境、外部条件、外观等 进行检查。
备等。 个别改善:针对设备缺陷展开的改善活动。 品质保全:通过设备维修活动改善和提高产品品质的活动。 设备前期管理:即从方案规划、采购到投入服役的全程管理。 教育训练:技术及管理培训,不断提高员工技术技能。 安全与卫生:人员操作安全与环境卫生标准。使人机处于良好工
作状态。 间接部门效率化:提高间接业务部门关联业务效率。
四、 TPM的内容
企业经营效率化
核心是全员参与,预防为主 零故障、零灾害、零不良、……零损失
TPM培训讲义精品课件

TPM培训讲义精品课件一、教学内容本讲义依据TPM(Total Productive Maintenance)培训教材第四章“设备维护与故障排除”进行设计,详细内容包括设备维护的基本原则、常见设备故障诊断方法、预防性维护的实施步骤以及设备故障排除技巧。
二、教学目标1. 理解设备维护的重要性,掌握设备维护的基本原则。
2. 学会诊断常见设备故障,并能提出合理的解决方案。
3. 掌握预防性维护的实施步骤,提高设备运行效率。
三、教学难点与重点1. 教学难点:设备故障诊断方法及故障排除技巧。
2. 教学重点:设备维护基本原则、预防性维护实施步骤。
四、教具与学具准备1. 教具:PPT课件、设备维护与故障排除案例视频、设备模型。
2. 学具:笔记本、教材、笔。
五、教学过程1. 导入:通过展示设备维护与故障排除的实践情景,引发学生对设备维护的关注。
2. 设备维护基本原则讲解:讲解设备维护的基本原则,结合实际案例进行分析。
3. 设备故障诊断方法:介绍常见设备故障诊断方法,如直观诊断、仪器诊断等。
4. 预防性维护实施步骤:详细讲解预防性维护的实施步骤,包括维护计划的制定、实施、检查和改进。
5. 故障排除技巧:通过例题讲解,让学生学会设备故障排除的技巧。
6. 随堂练习:让学生分组讨论,针对给定设备故障案例,提出解决方案。
六、板书设计1. 设备维护基本原则定期维护预防为主随时检查记录分析2. 设备故障诊断方法直观诊断仪器诊断专家系统3. 预防性维护实施步骤制定维护计划实施维护检查维护效果改进维护计划七、作业设计1. 作业题目:请简述设备维护的基本原则。
请列举至少三种设备故障诊断方法,并简要说明其优缺点。
请结合实际案例,说明预防性维护实施步骤。
2. 答案:设备维护的基本原则:定期维护、预防为主、随时检查、记录分析。
设备故障诊断方法:直观诊断:简单易行,但受限于个人经验和技能。
仪器诊断:准确度高,但需要专业设备和培训。
八、课后反思及拓展延伸2. 拓展延伸:推荐学生阅读相关资料,了解设备维护与故障排除的最新技术和发展趋势。
TPM讲义

故
突 發 型
小停止 5分以下
小 停 止 分 析
---機能低下型
障
P:Production C:Cost S:Safety
劣 化 型 ---品質低下型
精度劣化 磨耗,動搖 腐蝕,變形 溫度及異音 動作不良 污穢,塵埃 原料附著 漏氣,漏油, 滴水
(看板)運用手段 生產平準化(多樣化) 批次小準備時間少 標準作業 1)Cycle Time 2)作業順序 3)標準化 自動化運用防止停機的技巧--防呆fool proof) 二大支柱 零庫存
突發邦聯損失 準備損失 停機損失 速度損失 不良整修損失
目視管理 Andon 可利用率真(盡量保持設備於可用狀態) 保養確實 縮短準備時間 從作業改善至設備改善 暖機損失
M M Q T 分 B 析 F 分 析
設備損失結構分析圖
] l c * * * z H ~ v T ] B p ( | C 10 ,t O ] I * p w , O } O *1700 ,TPM , C * ~ ` ~ L u { ~ * * * { C } x v * * * B ] [ u *( * * * * B B * } ~ ` ,O , d o G v u ( ---( [ [ C.Tz } ,l ] ,w [ ,u )L _ , ] , t . [ . u . = H W w . ), o , | d , w d w q . [ , | V `, g L ,I ,@ _ ] . i . U Z 10 M J. V , m
k (Method)
w Q q J v F u v v e m
TPM讲义

- 从设备的设计就开始对设备进行控制 - 最终目的是实现无故障和方便日常维护
• Planed Maintenance
计划维护 (PM)
• Predictive Maintenance 预测维护 (PM)
3
PM的发展历史
• Preventative Maintenance • Corrective Maintenance • Maintenance Prevention • Planed Maintenance • Predictive Maintenance 预防性维护 纠正性维护 维护的预防 计划维护 预测维护 美国
0
设计 制作 测试 安装 试运行 接收
时间 问题
问题
很多问题导致难以维持和改进
29
自主安全管理-SHE金字塔
设备灾害 疲劳累积 慢性损失 微缺陷搁置
TPM — 安全,健康,环境(SHE) TPM — 消灭3K (肮脏,劳累,危险 ) TPM — 创造零灾害,零公害的工厂环境(设备灾害和人员灾害)
30
Page 7
Bestway Consultants
TPM目标—零损失
• Zero Accident • Zero Defect • Zero Breakdown • Zero Waste
TPM
TPM
15
零事故 零缺陷 零故障 零浪费
扮演的角色
零故障的五个对策
建立设备 基本条件
保持设备 建立设备 基本状况 操作状况
清洁 SEIKETSU Setting standards 修养 SHITSUKE Sticking to rules
9
TPM的基础—VCS
看得见的管理 一目了然的管理
TPM培训讲义优质课件
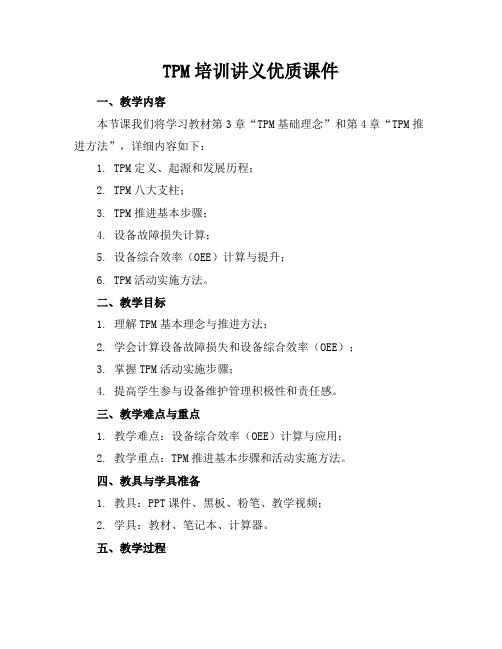
TPM培训讲义优质课件一、教学内容本节课我们将学习教材第3章“TPM基础理念”和第4章“TPM推进方法”,详细内容如下:1. TPM定义、起源和发展历程;2. TPM八大支柱;3. TPM推进基本步骤;4. 设备故障损失计算;5. 设备综合效率(OEE)计算与提升;6. TPM活动实施方法。
二、教学目标1. 理解TPM基本理念与推进方法;2. 学会计算设备故障损失和设备综合效率(OEE);3. 掌握TPM活动实施步骤;4. 提高学生参与设备维护管理积极性和责任感。
三、教学难点与重点1. 教学难点:设备综合效率(OEE)计算与应用;2. 教学重点:TPM推进基本步骤和活动实施方法。
四、教具与学具准备1. 教具:PPT课件、黑板、粉笔、教学视频;2. 学具:教材、笔记本、计算器。
五、教学过程1. 导入:通过一个实践情景引入,让学生解TPM在生产企业中重要性;2. 理论讲解:详细讲解TPM定义、起源、发展历程、八大支柱等;3. 例题讲解:以某企业为例,讲解设备故障损失和设备综合效率(OEE)计算;4. 随堂练习:让学生分组讨论,计算并分析某生产线设备综合效率;5. 活动实施:讲解TPM推进基本步骤和活动实施方法,让学生结合实际案例进行讨论;六、板书设计1. TPM定义、起源和发展历程;2. TPM八大支柱;3. 设备故障损失计算公式;4. 设备综合效率(OEE)计算公式;5. TPM推进基本步骤;6. 案例分析:某生产线设备综合效率计算。
七、作业设计1. 作业题目:(1)简述TPM定义、起源和发展历程;(2)列举TPM八大支柱;(3)计算某设备设备综合效率(OEE),并提出提升OEE措施;(4)结合实际,设计一份TPM推进计划。
2. 答案:(1)见教材第3章;(2)见教材第3章;(3)见例题讲解;(4)根据实际情况设计。
八、课后反思及拓展延伸1. 反思:本节课教学效果,包括学生参与度、理解程度等;2. 拓展延伸:引导学生关注TPM在国内外企业中应用,解先进管理理念和方法。
- 1、下载文档前请自行甄别文档内容的完整性,平台不提供额外的编辑、内容补充、找答案等附加服务。
- 2、"仅部分预览"的文档,不可在线预览部分如存在完整性等问题,可反馈申请退款(可完整预览的文档不适用该条件!)。
- 3、如文档侵犯您的权益,请联系客服反馈,我们会尽快为您处理(人工客服工作时间:9:00-18:30)。
2
Table of Contents
Executive Overview
Session 1.0 Session 2.0 Session 3.0 Session 4.0 Session 5.0
Introduction……………………………………...3
Role in Lean Manufacturing…………………….8
Role of the Operator in TPM…………………..18
Autonomous Maintenance Implementation……22 Equipment Performance: Measurement & Management………………….56
3
Total Productive Maintenance
一份老外的TPM讲义
Performance Excellence Series Training Module Elements
Executive Overview Lecture notes
Knowledge Breakthrough
Tools Workbook
Lecture notes Participant manual
11
Present Conditions
Operators view machines as responsible for major production And limit their roles to equipment operation and inspecting for quality While maintenance workers view their function as responding to recurring breakdowns
4
Total Productive Maintenance A series of methods to ensure that process machines are always able to perform their functions so that production is never interrupted.
Typical success results after implementation of TPM: Breakdowns: 1/30 to 1/100 of prior level Machine defects: 1/30 to 1/40 of prior level Productivity: 30 - 100 percent increase
= get around the problem
Solution = Work in batches
“We use the time it works to mass produce”
Today:
Objective = One piece flow Quality every time
Means = TPM
8
The Nine types of won • Delays (waiting time) • Transportation • Process • Inventories • Motions • Defective products • Untapped resources • Misused resources
5
Total Productive Maintenance
What it is:
1. Optimizes equipment efficiency 2. Implements a company wide Preventive Maintenance system 3. Involves production equipment designers, operators, and maintenance
“We organize so it works continuously”
10
Goals of TPM
Achieve zero equipment breakdowns and zero defects through prevention. Establish prevention by
Maintaining normal conditions Early detection of abnormalities Quick response
TPM targets reduction of these equipment oriented wastes
9
TPM: A Lean Manufacturing Method
TPM and one-piece flow:
Yesterday: Problem = machine breakdown
source: K. Shirose, TPM For Workshop Leaders, p. 10
7
Performance Excellence:
Expanding the Strategy through TPM
Introduction Role in Lean Manufacturing Role of the Operator in TPM Autonomous Maintenance Implementation Equipment Performance: Measurement and Management
Do these problems sound familiar? Equipment is always breaking down Operating machines at rated speeds creates defects Setups and adjustments take too long Minor machine stoppages are eroding productivity
department personnel 4. Involvement from Management down to floor workers 5. Implemented through small, self directed team activities
6
Total Productive Maintenance