熔融石英的性能特点和使用
熔融石英透镜 硅电容

熔融石英透镜硅电容
熔融石英透镜和硅电容都是在光学和电子领域中非常重要的材料和组件。
让我们分别从熔融石英透镜和硅电容的特性、应用和制造工艺等方面来进行全面的回答。
首先,熔融石英透镜是一种光学透镜材料,具有优异的光学性能和化学稳定性。
它具有高透射率、低色散、优良的热稳定性和机械强度等特点。
熔融石英透镜广泛应用于激光器、光学仪器、摄影镜头、天文望远镜等领域。
其制造工艺包括熔融成型、精密磨削和抛光等步骤,要求高精度和表面质量。
其次,硅电容是一种重要的电子元件,用于存储电荷或调节电路的频率和相位。
硅电容具有稳定性好、温度稳定性高、损耗小等特点。
它广泛应用于集成电路、射频电路、通信系统等领域。
制造硅电容的工艺主要包括硅晶圆制备、沉积绝缘层、金属化和封装等步骤,要求高纯度和稳定性。
从材料特性来看,熔融石英透镜注重光学性能和化学稳定性,而硅电容注重电学性能和稳定性。
从应用领域来看,熔融石英透镜主要应用于光学仪器和光学系统中,而硅电容主要应用于电子电路
和通信系统中。
从制造工艺来看,熔融石英透镜的制造需要精密的磨削和抛光工艺,而硅电容的制造需要复杂的硅晶圆加工和金属化工艺。
总的来说,熔融石英透镜和硅电容在光学和电子领域中都具有重要的地位,它们分别以优异的光学性能和电学性能在不同的领域发挥作用,制造工艺和应用也有所不同。
希望以上回答能够满足你的要求。
炉料中电融石英作用

炉料中电融石英作用一、引言电融石英是一种重要的工业原料,广泛应用于玻璃、陶瓷、电子、光学等领域。
在炉料中,电融石英作为一种添加剂或主要成分,发挥着重要的作用。
本文将对电融石英的物理和化学特性进行概述,重点阐述其在炉料中的作用,并对相关结论进行总结。
二、电融石英的物理和化学特性电融石英,也称为熔融石英,是一种天然或合成的高纯度石英矿物。
它具有高纯度、高熔点、低膨胀系数等优良的物理和化学特性。
电融石英的熔点高达1713℃,且膨胀系数较低,具有良好的热稳定性和耐高温性能。
此外,电融石英还具有优良的化学稳定性和绝缘性能。
三、电融石英在炉料中的作用在炉料中,电融石英主要作为添加剂或主要成分,发挥着重要的作用。
以下是电融石英在炉料中的主要作用:1.提高耐火性:由于电融石英具有高熔点和低膨胀系数,因此可以提高炉料的耐火性。
在高温下,电融石英能够保持稳定的结构,降低炉料的热膨胀,从而提高炉衬的使用寿命。
2.增强绝缘性:电融石英具有优良的绝缘性能,可以作为绝缘材料应用于炉料中。
在高温下,电融石英能够保持稳定的绝缘性能,降低炉料的导电性,从而保证生产的稳定性和安全性。
3.改善机械性能:电融石英可以提高炉料的硬度和耐磨性,从而提高炉料的机械性能。
这有助于提高炉料的耐磨损和耐腐蚀性能,延长其使用寿命。
4.优化产品性能:在玻璃、陶瓷等行业中,电融石英可以作为主要成分或添加剂,优化产品的光学、电气、物理和化学性能。
例如,在玻璃制造中,加入适量的电融石英可以调整玻璃的折射率、硬度、热稳定性等性能指标。
5.降低生产成本:电融石英具有高纯度和优良的化学稳定性,可以降低生产过程中的杂质含量和反应温度,从而降低生产成本和提高产品质量。
四、结论综上所述,电融石英在炉料中发挥着重要的作用。
它具有高纯度、高熔点、低膨胀系数等优良的物理和化学特性,可以提高炉料的耐火性、增强绝缘性、改善机械性能、优化产品性能并降低生产成本。
因此,在玻璃、陶瓷、电子、光学等行业中,电融石英作为添加剂或主要成分被广泛应用。
熔石英光学元件

熔石英光学元件熔石英光学元件是一种在光学领域中广泛使用的重要材料,由于其独特的光学性能和良好的化学稳定性,被广泛应用于激光器、光纤通信、光学仪器以及光学传感器等领域。
下面将从熔石英光学元件的定义、特性及应用等方面进行介绍。
熔石英光学元件是指由熔融石英材料制成的光学器件。
熔融石英是一种高纯度的二氧化硅(SiO2)材料,其制备过程中的高温熔融和特殊工艺使得其具有良好的光学性能。
熔石英光学元件具有高透过率、低色散、低吸收、低散射等优点,能够有效地传输和控制光的能量。
熔石英光学元件具有多种特性。
首先是高透过率。
石英的透光率在紫外、可见光和近红外光谱范围内都非常高,能够使光线以较低的损耗通过元件。
其次是低色散。
石英的色散性能优秀,能够使不同波长的光线经过元件后聚焦点基本重合,从而提高光学系统的分辨率和成像质量。
此外,熔石英光学元件还具有优异的化学稳定性和热稳定性,能够在各种恶劣环境下稳定工作。
熔石英光学元件在激光器领域有着广泛的应用。
激光器是一种将电能、光能和其他形式的能量转换为激光输出的器件。
熔石英光学元件作为激光器中的关键部件之一,能够承受高能量密度的激光束,具有优异的光学损伤阈值和热导率。
它们可以用作激光腔内的光学窗口、透镜、偏振器等,用于控制激光的传输、调制和聚焦等功能。
同时,熔石英光学元件还可以用于激光器的输出耦合和光束整形等应用。
熔石英光学元件在光纤通信领域也有重要应用。
光纤通信是一种利用光信号传输数据的通信方式。
熔石英光学元件可以用作光纤通信系统中的耦合器、分束器、合束器等关键器件,用于将光信号输入和输出光纤,实现光信号的传输和分配。
其高透过率和低损耗的特性保证了光信号的高效传输,而优异的色散特性则有助于提高光纤通信系统的传输带宽和距离。
熔石英光学元件还在光学仪器和光学传感器等领域得到广泛应用。
光学仪器是一种利用光学原理来观测、测量和分析物体的仪器。
熔石英光学元件可以用作显微镜、光谱仪、激光干涉仪等光学仪器中的关键光学元件,用于采集、调节和分析光信号。
熔融石英的性能特点和使用解析
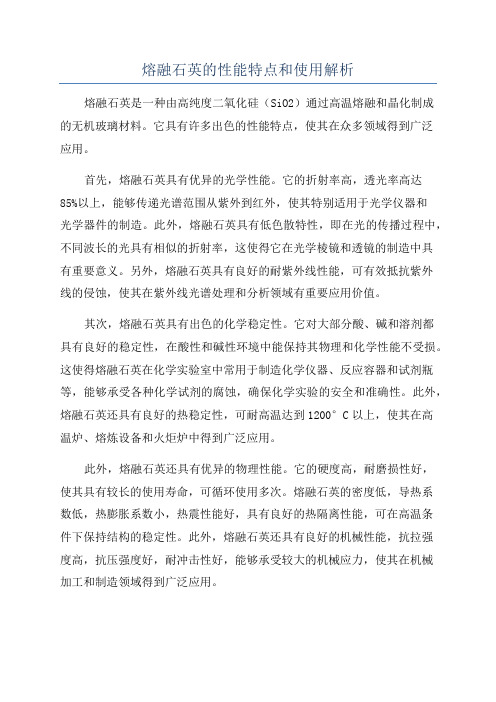
熔融石英的性能特点和使用解析熔融石英是一种由高纯度二氧化硅(SiO2)通过高温熔融和晶化制成的无机玻璃材料。
它具有许多出色的性能特点,使其在众多领域得到广泛应用。
首先,熔融石英具有优异的光学性能。
它的折射率高,透光率高达85%以上,能够传递光谱范围从紫外到红外,使其特别适用于光学仪器和光学器件的制造。
此外,熔融石英具有低色散特性,即在光的传播过程中,不同波长的光具有相似的折射率,这使得它在光学棱镜和透镜的制造中具有重要意义。
另外,熔融石英具有良好的耐紫外线性能,可有效抵抗紫外线的侵蚀,使其在紫外线光谱处理和分析领域有重要应用价值。
其次,熔融石英具有出色的化学稳定性。
它对大部分酸、碱和溶剂都具有良好的稳定性,在酸性和碱性环境中能保持其物理和化学性能不受损。
这使得熔融石英在化学实验室中常用于制造化学仪器、反应容器和试剂瓶等,能够承受各种化学试剂的腐蚀,确保化学实验的安全和准确性。
此外,熔融石英还具有良好的热稳定性,可耐高温达到1200°C以上,使其在高温炉、熔炼设备和火炬炉中得到广泛应用。
此外,熔融石英还具有优异的物理性能。
它的硬度高,耐磨损性好,使其具有较长的使用寿命,可循环使用多次。
熔融石英的密度低,导热系数低,热膨胀系数小,热震性能好,具有良好的热隔离性能,可在高温条件下保持结构的稳定性。
此外,熔融石英还具有良好的机械性能,抗拉强度高,抗压强度好,耐冲击性好,能够承受较大的机械应力,使其在机械加工和制造领域得到广泛应用。
最后,熔融石英具有良好的电气性能。
它是一种优质的绝缘材料,具有高击穿电压和低介电常数,使其在电子器件、电力设备和电子元件的制造中得到广泛应用。
此外,熔融石英还具有良好的介电损耗、耐电功率和耐电弧性能,是制造电气绝缘材料的理想选择。
总之,熔融石英具有优异的光学性能、化学稳定性、物理性能和电气性能,使其在光学仪器、化学实验室、高温设备和电子器件等领域发挥重要作用。
随着科学技术的不断进步和应用需求的不断增加,熔融石英的应用前景将更加广阔。
熔融石英导热系数

熔融石英导热系数(最新版)目录1.熔融石英的定义与性质2.熔融石英的导热系数3.熔融石英导热系数的测量方法4.熔融石英导热系数的影响因素5.熔融石英导热系数的应用领域正文熔融石英是一种由石英晶体熔融而成的高纯度硅酸盐材料,具有高热稳定性、高导热性、低热膨胀系数等优良性能。
在工业生产和科研领域中,熔融石英被广泛应用于制作高温炉、玻璃纤维等高温绝缘材料。
因此,研究熔融石英的导热系数对于优化其性能及应用具有重要意义。
熔融石英的导热系数是指在单位时间内,单位厚度的熔融石英在单位温差下所传递的热量。
熔融石英的导热系数受其成分、温度、压力等诸多因素影响,因此测量熔融石英导热系数的方法也较为复杂。
通常采用热电偶法、激光脉冲法、热流传感器法等技术手段进行测量。
熔融石英导热系数的测量方法有其独特之处。
例如,热电偶法需要将熔融石英试样与导热系数已知的材料进行热电偶热平衡,然后根据热电偶产生的热电势差来计算熔融石英的导热系数。
而激光脉冲法则利用激光在熔融石英中传播的时间来计算导热系数。
这些方法都需要在特定条件下进行,以保证测量结果的准确性。
熔融石英导热系数的影响因素包括化学成分、温度、压力等。
成分不同,熔融石英的晶体结构和粒度分布会有所差异,进而影响其导热性能。
温度对熔融石英导热系数的影响尤为明显,随着温度的升高,熔融石英的导热系数也会相应增加。
而压力的变化则会导致熔融石英的晶体结构发生变化,从而影响其导热性能。
熔融石英导热系数在多个领域具有广泛的应用。
如在高温炉设计中,根据熔融石英的导热系数可以优化炉体结构,提高热效率,降低能耗。
此外,在玻璃纤维生产中,通过调整熔融石英的导热系数,可以改善玻璃纤维的性能,提高产品质量。
总之,熔融石英导热系数是评估其性能及应用的重要指标。
熔融石英的性能特点和使用资料
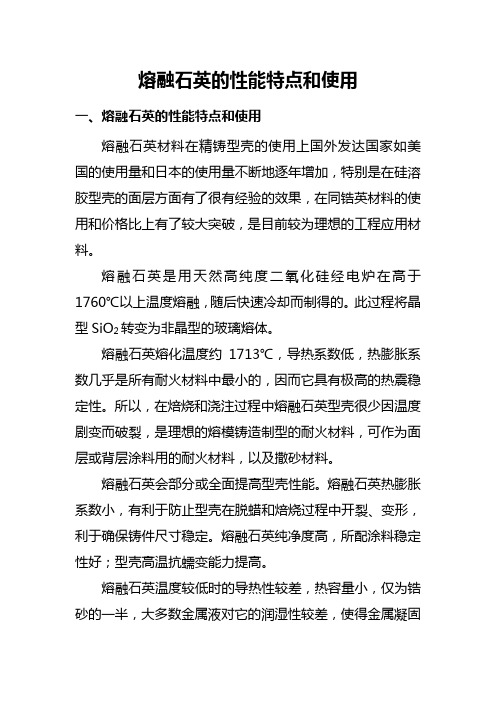
熔融石英的性能特点和使用一、熔融石英的性能特点和使用熔融石英材料在精铸型壳的使用上国外发达国家如美国的使用量和日本的使用量不断地逐年增加,特别是在硅溶胶型壳的面层方面有了很有经验的效果,在同锆英材料的使用和价格比上有了较大突破,是目前较为理想的工程应用材料。
熔融石英是用天然高纯度二氧化硅经电炉在高于1760℃以上温度熔融,随后快速冷却而制得的。
此过程将晶型SiO2转变为非晶型的玻璃熔体。
熔融石英熔化温度约1713℃,导热系数低,热膨胀系数几乎是所有耐火材料中最小的,因而它具有极高的热震稳定性。
所以,在焙烧和浇注过程中熔融石英型壳很少因温度剧变而破裂,是理想的熔模铸造制型的耐火材料,可作为面层或背层涂料用的耐火材料,以及撒砂材料。
熔融石英会部分或全面提高型壳性能。
熔融石英热膨胀系数小,有利于防止型壳在脱蜡和焙烧过程中开裂、变形,利于确保铸件尺寸稳定。
熔融石英纯净度高,所配涂料稳定性好;型壳高温抗蠕变能力提高。
熔融石英温度较低时的导热性较差,热容量小,仅为锆砂的一半,大多数金属液对它的润湿性较差,使得金属凝固层与型壳内表面间易产生间隙,热导率进一步减小,有利于壁薄铸件充型。
在高温下熔融石英的透明度高,能通过辐射传热,使其导热能力超过硅酸铝类壳。
而使铸件冷却较快,更易获得健全铸件。
铸件冷却时方石英又从高温型转变为低温型,同时体积产生骤变,使型壳出现无数裂纹,强度剧降,有利于脱壳进行。
熔融石英为酸性,能采用碱煮、碱爆等化学清砂方法去除型壳。
熔模铸造用熔融石英,其中SiO2所占的质量分数应为99.5%,配涂料用的粉料最好是270目或320目细粉占50%(质量分数),200目和120目粉各占25%(质量分数)。
①为0℃~1200℃间的膨胀系数平均值。
②400℃的热导率。
③1200℃热导率。
熔融石英及制品有三大特点:在所有耐火材料中,线膨胀系数最小(在1000℃的热胀率0.05);热导率最低,在1000℃热导率0.836W/(m·K)(0.02cal/cm·s·℃);抗热震性最好(在1200℃~水冷的抗震性),10次都不产生裂纹。
熔融石英的性能特点和使用解读

熔融石英的性能特点和使用一、熔融石英的性能特点和使用熔融石英材料在精铸型壳的使用上国外发达国家如美国的使用量和日本的使用量不断地逐年增加,特别是在硅溶胶型壳的面层方面有了很有经验的效果,在同锆英材料的使用和价格比上有了较大突破,是目前较为理想的工程应用材料。
熔融石英是用天然高纯度二氧化硅经电炉在高于1760℃以上温度熔融,随后快速冷却而制得的。
此过程将晶型SiO2转变为非晶型的玻璃熔体。
熔融石英熔化温度约1713℃,导热系数低,热膨胀系数几乎是所有耐火材料中最小的,因而它具有极高的热震稳定性。
所以,在焙烧和浇注过程中熔融石英型壳很少因温度剧变而破裂,是理想的熔模铸造制型的耐火材料,可作为面层或背层涂料用的耐火材料,以及撒砂材料。
熔融石英会部分或全面提高型壳性能。
熔融石英热膨胀系数小,有利于防止型壳在脱蜡和焙烧过程中开裂、变形,利于确保铸件尺寸稳定。
熔融石英纯净度高,所配涂料稳定性好;型壳高温抗蠕变能力提高。
熔融石英温度较低时的导热性较差,热容量小,仅为锆砂的一半,大多数金属液对它的润湿性较差,使得金属凝固层与型壳内表面间易产生间隙,热导率进一步减小,有利于壁薄铸件充型。
在高温下熔融石英的透明度高,能通过辐射传热,使其导热能力超过硅酸铝类壳。
而使铸件冷却较快,更易获得健全铸件。
铸件冷却时方石英又从高温型转变为低温型,同时体积产生骤变,使型壳出现无数裂纹,强度剧降,有利于脱壳进行。
熔融石英为酸性,能采用碱煮、碱爆等化学清砂方法去除型壳。
熔模铸造用熔融石英,其中SiO 2所占的质量分数应为99.5%,配涂料用的粉料最好是270目或320目细粉占50%(质量分数),200目和120目粉各占25%(质量分数)。
①为0℃~1200℃间的膨胀系数平均值。
耐火材料 化学组成 化学性质熔点/℃莫氏硬度 密度/(g/cm 3)膨胀系数①/×10-71/℃ 热导率/[W/(m 2.k)] 浸出性比较 颜色熔融石英 SiO 2 酸性 1713 7 2.251.951②在热浓碱和氢酸条件下有良好的可溶性 白色电熔刚玉 Al 2O 3 两性 2030 9 3.99~4.0 86 12.560②在热碱条件下反应很差 白色 莫来石 3Al 2O 3·2SiO 2 两性2030 6~72.7~2.9541.214② 在热碱条件下有轻微反应 灰色到棕黄色 高岭石 熟料 弱酸性 1700~1790 ~5 2.4~2.6 50- 在热碱条件下有轻微反应 灰色到棕黄色 锆砂 ZrSiO 4 弱酸性 <1948 7~8 4.5~4.9 46 2.094③在热碱条件下有中等反应 白色到棕黄色 氧化锆ZriO 2碱性26007~85.760-②400℃的热导率。
熔融石英坩埚制作

熔融石英坩埚制作熔融石英坩埚是一种常用的实验器皿,主要用于高温下进行化学反应、熔炼和烧结等实验操作。
熔融石英坩埚具有高温稳定性、耐腐蚀性和良好的热传导性能,因此被广泛应用于实验室、化工、冶金等领域。
熔融石英坩埚由纯度较高的熔融石英材料制成,其主要成分是二氧化硅(SiO2)。
石英材料具有良好的耐热性和化学稳定性,能够在高温下保持结构的稳定性,不易发生热膨胀或热裂纹现象。
同时,石英材料还具有优异的耐腐蚀性,可以在酸碱等腐蚀性介质中稳定使用。
制作熔融石英坩埚的过程相对复杂,需要经过多道工艺。
首先,选用高纯度的石英砂作为原料,经过研磨和筛分等处理,得到均匀细腻的石英粉末。
然后,将石英粉末与适量的粘结剂混合,经过搅拌和压制,形成坩埚的原型。
接下来,将原型进行烘干处理,使其内部的粘结剂蒸发,使得原型具有一定的强度和形状稳定性。
最后,将烘干后的原型放入高温炉中进行烧结,使其成为坚硬的石英坩埚。
熔融石英坩埚的使用方法相对简单,一般需要注意以下几点。
首先,在使用前应将石英坩埚进行预热处理,以避免温度突变造成的热裂纹。
其次,在装载试样或进行熔炼等操作时,应尽量避免将试样直接接触到石英坩埚的底部,以免试样与坩埚产生粘附或反应。
另外,在加热或冷却过程中,应尽量避免急剧的温度变化,以免引起热应力而导致石英坩埚的破裂。
熔融石英坩埚的应用范围非常广泛。
在化学实验室中,石英坩埚常用于高温下进行有机合成反应、催化反应和热分解等实验操作。
在冶金领域,石英坩埚常用于金属熔炼、铁矿石还原和钢铁冶炼等工艺过程。
此外,石英坩埚还广泛应用于玻璃工艺、电子工业和光学仪器等领域,如光纤制备、半导体材料熔炼和光学镀膜等。
熔融石英坩埚是一种重要的实验器皿,具有高温稳定性、耐腐蚀性和良好的热传导性能。
通过选用高纯度的石英材料,并经过多道工艺制作而成。
石英坩埚广泛应用于实验室、化工、冶金等领域,在高温下进行化学反应、熔炼和烧结等实验操作。
在使用时,需要注意预热处理和避免温度突变。
熔融石英行业标准

熔融石英行业标准汇报人:***2024-01-04•熔融石英概述•熔融石英行业标准制定•熔融石英产品质量标准目录•熔融石英生产工艺标准•熔融石英产品应用标准•熔融石英行业发展趋势与展望01熔融石英概述1 2 3熔融石英是一种天然产出的二氧化硅矿物,经过高温熔化后形成的一种非晶态硅酸盐材料。
熔融石英熔融石英的形成需要经过高温熔化过程,通常在1700℃以上的高温下,石英颗粒熔化成液体,经过冷却后形成熔融石英。
形成过程熔融石英具有低膨胀系数、高化学稳定性、高耐热性等特点,同时具有优良的透光性、绝缘性和加工性能。
物理性质高化学稳定性熔融石英具有较高的化学稳定性,耐酸、耐碱、耐腐蚀,不易与其它物质发生化学反应。
优良的透光性和绝缘性熔融石英具有优良的透光性和绝缘性,广泛应用于光学仪器、玻璃制品、陶瓷等领域。
高耐热性熔融石英具有较高的耐热性,能够在高温环境下长期使用,不易变形、开裂或烧蚀。
低膨胀系数熔融石英的膨胀系数较低,具有较好的热稳定性,能够承受温度变化引起的热应力。
熔融石英作为重要的光学材料之一,广泛应用于光学仪器、棱镜、透镜等领域。
光学仪器熔融石英可以代替部分玻璃制品,如高温炉、电炉等设备使用的耐高温玻璃。
玻璃制品熔融石英可以作为陶瓷材料的原料之一,提高陶瓷产品的耐热性和绝缘性能。
陶瓷熔融石英还可以应用于半导体、航空航天、汽车等高科技领域,作为重要的非金属材料之一。
其它领域熔融石英的应用领域02熔融石英行业标准制定制定标准的必要性规范市场秩序通过制定行业标准,规范熔融石英产品的生产、销售和使用,确保产品质量和安全,避免劣质产品扰乱市场。
提高产业竞争力统一的标准有利于熔融石英产业的规范化发展,提高产品质量和降低生产成本,增强产业的整体竞争力。
促进技术创新标准的制定可以引导企业进行技术创新和产品升级,推动熔融石英行业的技术进步和产业升级。
对熔融石英行业现状进行深入调研,明确标准制定的目的和范围,成立标准制定工作组。
熔融石英的性能特点和使用解读

熔融石英的性能特点和使用一、熔融石英的性能特点和使用熔融石英材料在精铸型壳的使用上国外发达国家如美国的使用量和日本的使用量不断地逐年增加,特别是在硅溶胶型壳的面层方面有了很有经验的效果,在同锆英材料的使用和价格比上有了较大突破,是目前较为理想的工程应用材料。
熔融石英是用天然高纯度二氧化硅经电炉在高于1760℃以上温度熔融,随后快速冷却而制得的。
此过程将晶型SiO2转变为非晶型的玻璃熔体。
熔融石英熔化温度约1713℃,导热系数低,热膨胀系数几乎是所有耐火材料中最小的,因而它具有极高的热震稳定性。
所以,在焙烧和浇注过程中熔融石英型壳很少因温度剧变而破裂,是理想的熔模铸造制型的耐火材料,可作为面层或背层涂料用的耐火材料,以及撒砂材料。
熔融石英会部分或全面提高型壳性能。
熔融石英热膨胀系数小,有利于防止型壳在脱蜡和焙烧过程中开裂、变形,利于确保铸件尺寸稳定。
熔融石英纯净度高,所配涂料稳定性好;型壳高温抗蠕变能力提高。
熔融石英温度较低时的导热性较差,热容量小,仅为锆砂的一半,大多数金属液对它的润湿性较差,使得金属凝固层与型壳内表面间易产生间隙,热导率进一步减小,有利于壁薄铸件充型。
在高温下熔融石英的透明度高,能通过辐射传热,使其导热能力超过硅酸铝类壳。
而使铸件冷却较快,更易获得健全铸件。
铸件冷却时方石英又从高温型转变为低温型,同时体积产生骤变,使型壳出现无数裂纹,强度剧降,有利于脱壳进行。
熔融石英为酸性,能采用碱煮、碱爆等化学清砂方法去除型壳。
熔模铸造用熔融石英,其中SiO 2所占的质量分数应为99.5%,配涂料用的粉料最好是270目或320目细粉占50%(质量分数),200目和120目粉各占25%(质量分数)。
①为0℃~1200℃间的膨胀系数平均值。
耐火材料 化学组成 化学性质熔点/℃莫氏硬度 密度/(g/cm 3)膨胀系数①/×10-71/℃ 热导率/[W/(m 2.k)] 浸出性比较 颜色熔融石英 SiO 2 酸性 1713 7 2.251.951②在热浓碱和氢酸条件下有良好的可溶性 白色电熔刚玉 Al 2O 3 两性 2030 9 3.99~4.0 86 12.560②在热碱条件下反应很差 白色 莫来石 3Al 2O 3·2SiO 2 两性2030 6~72.7~2.9541.214② 在热碱条件下有轻微反应 灰色到棕黄色 高岭石 熟料 弱酸性 1700~1790 ~5 2.4~2.6 50- 在热碱条件下有轻微反应 灰色到棕黄色 锆砂 ZrSiO 4 弱酸性 <1948 7~8 4.5~4.9 46 2.094③在热碱条件下有中等反应 白色到棕黄色 氧化锆ZriO 2碱性26007~85.760-②400℃的热导率。
熔融石英熔点

熔融石英熔点
熔融石英熔点
熔融石英是一种重要的耐高温材料,常见于工业领域中的一些高温熔炼和制造过程当中。
熔融石英拥有优异的高温稳定性、抗热冲击性、电绝缘性能以及优异的化学稳定性等特点,因此在高温条件下,其物理性质和化学性质能够保持稳定,不会发生明显的变化。
然而,我们在熔融石英的应用中,经常会考虑到的一个基本参数就是它的熔点。
熔点是熔融石英性质的一个重要表征参数,它通常表示熔融状态的相变温度,即熔融石英通过加热二十多度,从固态转变为流动状态的温度。
下面我们就来简要介绍一下熔融石英的熔点。
熔融石英的化学成分是SiO2,其分子式为SiO2。
由于结构紧
密而且化学成分稳定,熔点较高,一般在1713度左右。
在低
温下,SiO2长成的是六角柱体晶体结构,叫六方石英,其他SiO2晶体在高压高温下都可以转变为六方石英。
而在高温下,六方石英也可以熔化为熔融石英,从固态转化为液态。
在实际应用中,熔融石英的熔点可能会受到多种因素的影响,例如化学成分、杂质含量、晶体结构等等。
同时在熔炼熔融石英的过程中,加热速率和加热方式等也会对熔点产生影响。
需要注意的是,熔融石英不仅存在于高温高压物理实验中,也广泛应用于工业制造领域。
比如,它可以制成熔融石英玻璃、
熔融陶瓷、熔融石英管等,这些在工业生产中有着重要的应用。
总结一下,熔融石英的熔点是它的一个基本性质,通常表示熔融状态的相变温度。
在实际应用中,有很多因素可能会影响熔点的测定,需要特别注意。
熔融石英作为一种优异的耐高温、耐化学腐蚀性能的材料,在工业制造中的应用前景非常广阔。
熔融石英的性能特点和使用
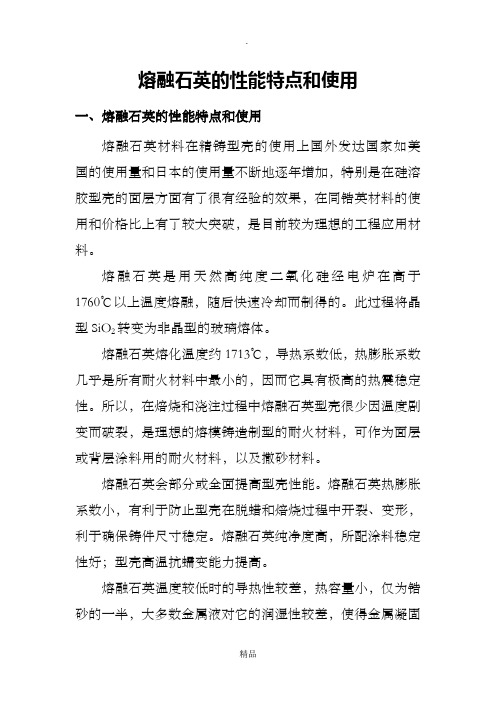
熔融石英的性能特点和使用一、熔融石英的性能特点和使用熔融石英材料在精铸型壳的使用上国外发达国家如美国的使用量和日本的使用量不断地逐年增加,特别是在硅溶胶型壳的面层方面有了很有经验的效果,在同锆英材料的使用和价格比上有了较大突破,是目前较为理想的工程应用材料。
熔融石英是用天然高纯度二氧化硅经电炉在高于1760℃以上温度熔融,随后快速冷却而制得的。
此过程将晶型SiO2转变为非晶型的玻璃熔体。
熔融石英熔化温度约1713℃,导热系数低,热膨胀系数几乎是所有耐火材料中最小的,因而它具有极高的热震稳定性。
所以,在焙烧和浇注过程中熔融石英型壳很少因温度剧变而破裂,是理想的熔模铸造制型的耐火材料,可作为面层或背层涂料用的耐火材料,以及撒砂材料。
熔融石英会部分或全面提高型壳性能。
熔融石英热膨胀系数小,有利于防止型壳在脱蜡和焙烧过程中开裂、变形,利于确保铸件尺寸稳定。
熔融石英纯净度高,所配涂料稳定性好;型壳高温抗蠕变能力提高。
熔融石英温度较低时的导热性较差,热容量小,仅为锆砂的一半,大多数金属液对它的润湿性较差,使得金属凝固层与型壳内表面间易产生间隙,热导率进一步减小,有利于壁薄铸件充型。
在高温下熔融石英的透明度高,能通过辐射传热,使其导热能力超过硅酸铝类壳。
而使铸件冷却较快,更易获得健全铸件。
铸件冷却时方石英又从高温型转变为低温型,同时体积产生骤变,使型壳出现无数裂纹,强度剧降,有利于脱壳进行。
熔融石英为酸性,能采用碱煮、碱爆等化学清砂方法去除型壳。
熔模铸造用熔融石英,其中SiO2所占的质量分数应为99.5%,配涂料用的粉料最好是270目或320目细粉占50%(质量分数),200目和120目粉各占25%(质量分数)。
①为0℃~1200℃间的膨胀系数平均值。
②400℃的热导率。
③1200℃热导率。
熔融石英及制品有三大特点:在所有耐火材料中,线膨胀系数最小(在1000℃的热胀率0.05);热导率最低,在1000℃热导率0.836W/(m·K)(0.02cal/cm·s·℃);抗热震性最好(在1200℃~水冷的抗震性),10次都不产生裂纹。
熔融石英 材料参数
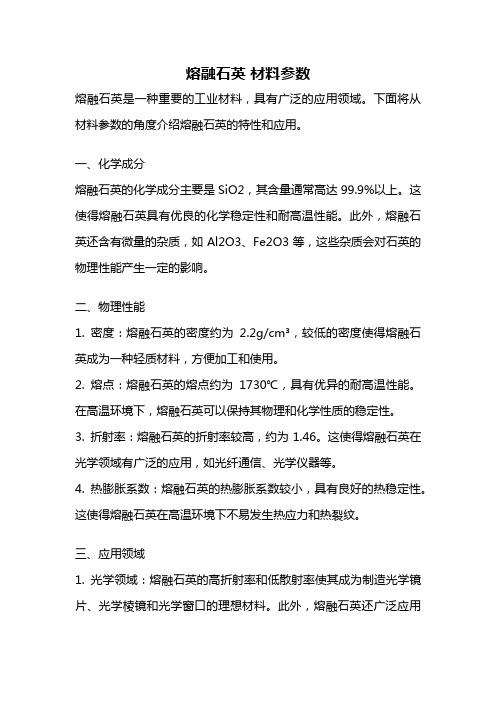
熔融石英材料参数熔融石英是一种重要的工业材料,具有广泛的应用领域。
下面将从材料参数的角度介绍熔融石英的特性和应用。
一、化学成分熔融石英的化学成分主要是SiO2,其含量通常高达99.9%以上。
这使得熔融石英具有优良的化学稳定性和耐高温性能。
此外,熔融石英还含有微量的杂质,如Al2O3、Fe2O3等,这些杂质会对石英的物理性能产生一定的影响。
二、物理性能1. 密度:熔融石英的密度约为2.2g/cm³,较低的密度使得熔融石英成为一种轻质材料,方便加工和使用。
2. 熔点:熔融石英的熔点约为1730℃,具有优异的耐高温性能。
在高温环境下,熔融石英可以保持其物理和化学性质的稳定性。
3. 折射率:熔融石英的折射率较高,约为1.46。
这使得熔融石英在光学领域有广泛的应用,如光纤通信、光学仪器等。
4. 热膨胀系数:熔融石英的热膨胀系数较小,具有良好的热稳定性。
这使得熔融石英在高温环境下不易发生热应力和热裂纹。
三、应用领域1. 光学领域:熔融石英的高折射率和低散射率使其成为制造光学镜片、光学棱镜和光学窗口的理想材料。
此外,熔融石英还广泛应用于光纤通信、激光器和光学仪器等领域。
2. 电子领域:熔融石英具有优异的电绝缘性能和低介电损耗,可用于制造半导体材料、集成电路基板和电子器件。
3. 化学领域:熔融石英具有优良的化学稳定性,能够耐受酸、碱等强腐蚀介质的侵蚀。
因此,熔融石英被广泛应用于化学反应器、石油化工设备和半导体制造等领域。
4. 机械领域:熔融石英具有高硬度和优异的耐磨性,可用于制造高精度的机械零件和磨料工具。
5. 医疗领域:熔融石英在医疗器械中的应用越来越广泛,如石英玻璃针、石英玻璃管等。
其优良的化学稳定性和高温耐受性使其成为一种理想的医疗材料。
熔融石英作为一种重要的工业材料,具有优良的化学稳定性、耐高温性能和优异的物理性能。
其广泛的应用领域涵盖光学、电子、化学、机械和医疗等各个领域。
随着科技的不断发展,熔融石英在各个领域的应用前景将会更加广阔。
熔融石英原料-概述说明以及解释

熔融石英原料-概述说明以及解释1.引言1.1 概述熔融石英是一种高纯度的无色、透明的硅石材料,具有优异的热稳定性、化学稳定性和机械性能。
它是以天然石英矿石或人工合成的石英晶体为原料,通过高温熔炼加工而得。
熔融石英原料在许多领域得到广泛应用,尤其在光电子、光通信、光纤、半导体、光学仪器等高科技领域具有重要地位。
它可以用来制造光纤、激光器件、光学器件、半导体材料、太阳能电池、液晶面板、光纤通信设备等高科技产品。
随着现代科技的发展和工业生产的需求不断增加,熔融石英原料的市场前景非常广阔。
特别是在新能源、新材料、新技术的推动下,熔融石英原料的需求将进一步增加。
因此,熔融石英原料的生产和研究具有重要意义。
本文将对熔融石英的定义和特性进行介绍,并探讨熔融石英的生产过程、应用领域和市场前景。
最后,对熔融石英原料的重要性、发展趋势进行分析,并提出相应的建议和展望。
通过本文的研究,有助于促进熔融石英原料的应用和发展,推动相关领域的技术创新和产业进步。
文章结构是一个重要的指导框架,可以帮助读者清晰地了解文章的组织和内容。
下面是文章1.2部分"文章结构" 的内容:1.2 文章结构本文将按以下结构进行阐述:第二部分是正文部分,包括以下子章节:2.1 熔融石英的定义和特性:介绍熔融石英的定义以及其在化学成分、物理性质等方面的特点,使读者对熔融石英有一个基本的了解。
2.2 熔融石英的生产过程:详细介绍熔融石英的生产过程,包括原料的选择、熔炼工艺、石英坯体的制备等环节。
通过对生产过程的描述,读者将能够了解熔融石英是如何被制造出来的。
2.3 熔融石英的应用领域:探讨熔融石英在各个行业中的应用情况,如光电子、半导体、太阳能产业等。
同时介绍一些具体的应用案例,以便读者更好地理解熔融石英在这些领域中的作用。
2.4 熔融石英的市场前景:分析熔融石英在全球市场中的发展态势,包括市场规模、市场竞争态势以及各个地区市场的现状和趋势。
熔融石英热导率
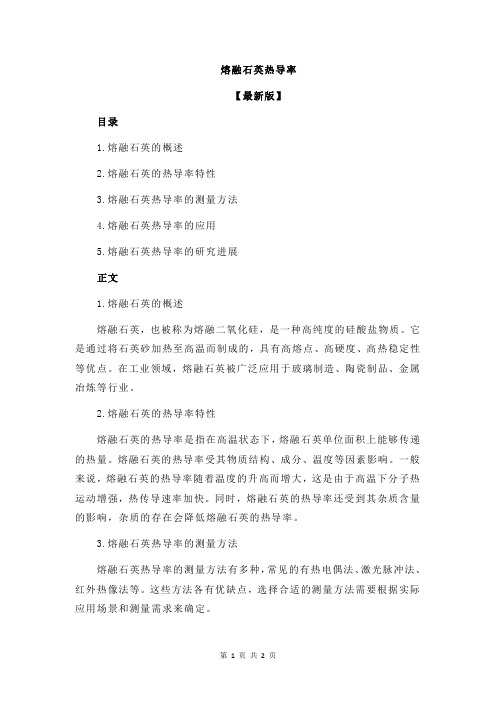
熔融石英热导率【最新版】目录1.熔融石英的概述2.熔融石英的热导率特性3.熔融石英热导率的测量方法4.熔融石英热导率的应用5.熔融石英热导率的研究进展正文1.熔融石英的概述熔融石英,也被称为熔融二氧化硅,是一种高纯度的硅酸盐物质。
它是通过将石英砂加热至高温而制成的,具有高熔点、高硬度、高热稳定性等优点。
在工业领域,熔融石英被广泛应用于玻璃制造、陶瓷制品、金属冶炼等行业。
2.熔融石英的热导率特性熔融石英的热导率是指在高温状态下,熔融石英单位面积上能够传递的热量。
熔融石英的热导率受其物质结构、成分、温度等因素影响。
一般来说,熔融石英的热导率随着温度的升高而增大,这是由于高温下分子热运动增强,热传导速率加快。
同时,熔融石英的热导率还受到其杂质含量的影响,杂质的存在会降低熔融石英的热导率。
3.熔融石英热导率的测量方法熔融石英热导率的测量方法有多种,常见的有热电偶法、激光脉冲法、红外热像法等。
这些方法各有优缺点,选择合适的测量方法需要根据实际应用场景和测量需求来确定。
4.熔融石英热导率的应用熔融石英的热导率在工业生产中有着广泛的应用,例如在玻璃制造过程中,通过测量熔融石英的热导率,可以有效地控制玻璃的熔化温度和熔融程度,从而保证玻璃制品的质量。
此外,熔融石英热导率还用于评估金属冶炼过程中的热传导性能,以及陶瓷制品的热稳定性等。
5.熔融石英热导率的研究进展近年来,随着科研技术的不断发展,熔融石英热导率的研究取得了很多重要成果。
例如,研究人员通过对熔融石英的微观结构进行调控,成功提高了其热导率;此外,新型熔融石英材料的研发也取得了突破,这些新材料具有更高的热导率和更好的热稳定性。
熔融石英导热系数

熔融石英导热系数摘要:1.熔融石英的概述2.熔融石英的导热系数3.熔融石英导热系数的影响因素4.熔融石英导热系数的应用5.结论正文:1.熔融石英的概述熔融石英,也被称为熔融二氧化硅,是一种高温下形成的硅酸盐矿物。
它是由石英砂或石英石在高温下熔融而成的,具有良好的导热性能、高硬度和化学稳定性。
在工业生产中,熔融石英被广泛应用于高温炉、玻璃工业和陶瓷行业等领域。
2.熔融石英的导热系数熔融石英的导热系数是指在单位时间、单位厚度和单位温度差下,熔融石英所传导的热量。
熔融石英的导热系数通常在10-20 W/(m·K)之间,这意味着它是一种优良的导热材料。
3.熔融石英导热系数的影响因素熔融石英的导热系数受多种因素影响,主要包括以下几点:(1)温度:随着温度的升高,熔融石英的导热系数也会增加。
(2)压力:在一定范围内,熔融石英所承受的压力与其导热系数成正比。
(3)成分:熔融石英中的杂质和成分对其导热系数有一定影响,如氧化铝、氧化钠等成分的加入可以提高熔融石英的导热性能。
4.熔融石英导热系数的应用由于熔融石英具有较高的导热系数,因此在高温工业生产领域具有广泛的应用。
以下是熔融石英导热系数的一些应用实例:(1)高温炉:熔融石英可用于制作高温炉的内衬,提高炉子的热效率和稳定性。
(2)玻璃工业:熔融石英作为玻璃熔炉的隔热材料,有助于降低炉子的能耗和提高玻璃的品质。
(3)陶瓷行业:熔融石英可用于制作高温窑炉的耐火材料,提高陶瓷制品的质量和产量。
5.结论熔融石英是一种具有优良导热性能的硅酸盐矿物,广泛应用于高温工业生产领域。
熔融石英双面光学平晶
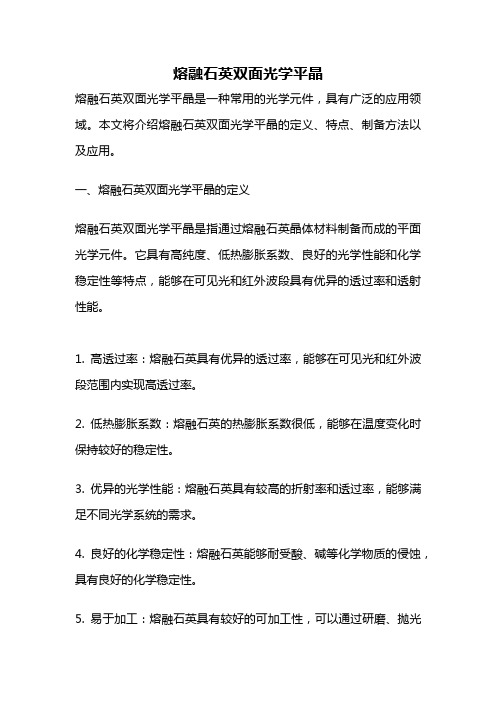
熔融石英双面光学平晶熔融石英双面光学平晶是一种常用的光学元件,具有广泛的应用领域。
本文将介绍熔融石英双面光学平晶的定义、特点、制备方法以及应用。
一、熔融石英双面光学平晶的定义熔融石英双面光学平晶是指通过熔融石英晶体材料制备而成的平面光学元件。
它具有高纯度、低热膨胀系数、良好的光学性能和化学稳定性等特点,能够在可见光和红外波段具有优异的透过率和透射性能。
1. 高透过率:熔融石英具有优异的透过率,能够在可见光和红外波段范围内实现高透过率。
2. 低热膨胀系数:熔融石英的热膨胀系数很低,能够在温度变化时保持较好的稳定性。
3. 优异的光学性能:熔融石英具有较高的折射率和透过率,能够满足不同光学系统的需求。
4. 良好的化学稳定性:熔融石英能够耐受酸、碱等化学物质的侵蚀,具有良好的化学稳定性。
5. 易于加工:熔融石英具有较好的可加工性,可以通过研磨、抛光等方法制备成各种形状和尺寸的光学元件。
三、熔融石英双面光学平晶的制备方法熔融石英双面光学平晶的制备主要包括以下几个步骤:1. 原料准备:选择高纯度的石英砂作为原料,并进行粉碎、筛分等处理。
2. 熔融:将石英砂放入石英坩埚中,通过高温熔融处理,使其成为熔融石英。
3. 成型:将熔融石英倒入成型模具中,使其成为所需形状的光学平晶。
4. 调整尺寸:通过研磨、抛光等工艺,对光学平晶进行尺寸调整和表面处理。
5. 检测:对成品进行光学性能、尺寸精度等方面的检测,确保产品质量。
四、熔融石英双面光学平晶的应用熔融石英双面光学平晶在光学领域有广泛的应用,主要包括以下几个方面:1. 光学仪器:熔融石英双面光学平晶可用于制作光学仪器的镜片、透镜等元件,如显微镜、望远镜、光谱仪等。
2. 光学通信:熔融石英双面光学平晶可用于制作光纤通信中的耦合器、分束器等元件,提高光信号的传输效率和质量。
3. 光学传感:熔融石英双面光学平晶可用于制作光学传感器,如温度传感器、压力传感器等,实现对光学信号的检测和测量。
熔融石英砖 方石英

熔融石英砖方石英
熔融石英砖是一种由高纯度石英砂经过高温熔融后制成的一种耐火材料。
石英砂是一种主要成分为二氧化硅的矿石,经过高温熔融后形成石英玻璃,再经过冷却和成型制成石英砖。
熔融石英砖因其高纯度、耐高温、耐腐蚀等特点,在工业领域得到广泛应用。
从材料的角度来看,熔融石英砖由高纯度的石英砂制成,因此具有优异的耐高温性能和化学稳定性。
这使得熔融石英砖在高温环境下能够保持稳定的物理和化学性质,不易受到腐蚀和磨损,适用于各种工业窑炉和炉子的内衬。
从应用领域来看,熔融石英砖主要用于冶金、玻璃、化工等行业的高温设备内衬,如玻璃窑、炼铁炉、炼钢炉等。
其耐高温、耐腐蚀的特性使得其能够在这些恶劣的工作环境下长期稳定运行,保障生产设备的正常运转。
此外,熔融石英砖还具有良好的隔热性能和导热性能,能够有效减少能源损耗,提高设备的能效。
这使得熔融石英砖在工业生产中得到广泛应用,为工业生产提供了可靠的保障。
总的来说,熔融石英砖作为一种耐火材料,在工业领域具有重要的应用价值,其优异的耐高温、耐腐蚀性能,使其成为各种高温设备的理想内衬材料。
同时,熔融石英砖的应用也为工业生产提供了稳定可靠的保障,提高了生产效率和能源利用效率。
熔融石英的性能特点和使用
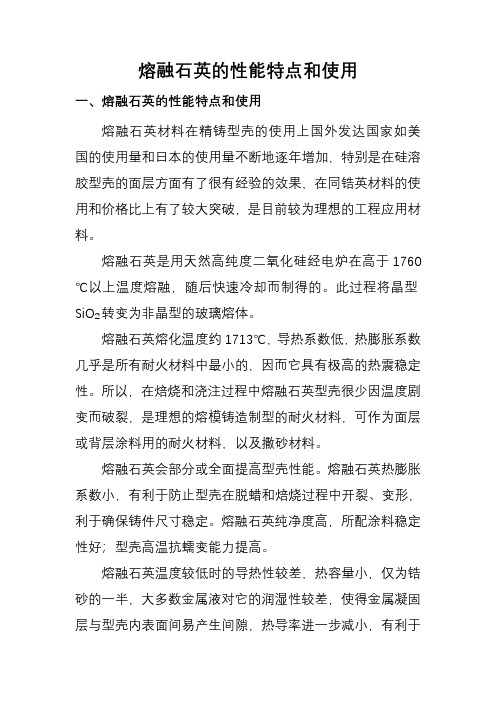
熔融石英的性能特点和使用一、熔融石英的性能特点和使用熔融石英材料在精铸型壳的使用上国外发达国家如美国的使用量和日本的使用量不断地逐年增加,特别是在硅溶胶型壳的面层方面有了很有经验的效果,在同锆英材料的使用和价格比上有了较大突破,是目前较为理想的工程应用材料。
熔融石英是用天然高纯度二氧化硅经电炉在高于1760℃以上温度熔融,随后快速冷却而制得的。
此过程将晶型SiO2转变为非晶型的玻璃熔体。
熔融石英熔化温度约1713℃,导热系数低,热膨胀系数几乎是所有耐火材料中最小的,因而它具有极高的热震稳定性。
所以,在焙烧和浇注过程中熔融石英型壳很少因温度剧变而破裂,是理想的熔模铸造制型的耐火材料,可作为面层或背层涂料用的耐火材料,以及撒砂材料。
熔融石英会部分或全面提高型壳性能。
熔融石英热膨胀系数小,有利于防止型壳在脱蜡和焙烧过程中开裂、变形,利于确保铸件尺寸稳定。
熔融石英纯净度高,所配涂料稳定性好;型壳高温抗蠕变能力提高。
熔融石英温度较低时的导热性较差,热容量小,仅为锆砂的一半,大多数金属液对它的润湿性较差,使得金属凝固层与型壳内表面间易产生间隙,热导率进一步减小,有利于②400℃的热导率。
③1200℃热导率。
熔融石英及制品有三大特点:在所有耐火材料中,线膨胀系数最小(在1000℃的热胀率0.05);热导率最低,在1000℃热导率0.836W/(m·K)(0.02cal/cm·s·℃);抗热震性最好(在1200℃~水冷的抗震性),10次都不产生裂纹。
二、熔融石英涂料配制使用操作工艺(一)本操作工艺适用于硅溶胶,制壳的表面层或过渡层。
(二)本工艺使用的硅溶胶同锆英粉涂料即SiO230%。
(三)本工艺操作中的润湿剂,消泡剂同锆英粉涂料。
(四)本操作中使用的流杯粘度计为詹氏(Zahn)5#杯,出口孔径为Φ5.28mm。
(五)涂料配制:1、熔融石英粉的配制,320目(网号:0.044)275目(网号:0.052)200目(网号:0.076)120目(网号:0.125)熔融石英粉中的SiO2的质量分数为99.5%以上。
- 1、下载文档前请自行甄别文档内容的完整性,平台不提供额外的编辑、内容补充、找答案等附加服务。
- 2、"仅部分预览"的文档,不可在线预览部分如存在完整性等问题,可反馈申请退款(可完整预览的文档不适用该条件!)。
- 3、如文档侵犯您的权益,请联系客服反馈,我们会尽快为您处理(人工客服工作时间:9:00-18:30)。
熔融石英的性能特点和使用一、熔融石英的性能特点和使用熔融石英材料在精铸型壳的使用上国外发达国家如美国的使用量和日本的使用量不断地逐年增加,特别是在硅溶胶型壳的面层方面有了很有经验的效果,在同锆英材料的使用和价格比上有了较大突破,是目前较为理想的工程应用材料。
熔融石英是用天然高纯度二氧化硅经电炉在高于1760 C以上温度熔融,随后快速冷却而制得的。
此过程将晶型SiO2转变为非晶型的玻璃熔体。
熔融石英熔化温度约1713 C,导热系数低,热膨胀系数几乎是所有耐火材料中最小的,因而它具有极高的热震稳定性。
所以,在焙烧和浇注过程中熔融石英型壳很少因温度剧变而破裂,是理想的熔模铸造制型的耐火材料,可作为面层或背层涂料用的耐火材料,以及撒砂材料。
熔融石英会部分或全面提高型壳性能。
熔融石英热膨胀系数小,有利于防止型壳在脱蜡和焙烧过程中开裂、变形,利于确保铸件尺寸稳定。
熔融石英纯净度高,所配涂料稳定性好;型壳高温抗蠕变能力提高。
熔融石英温度较低时的导热性较差,热容量小,仅为锆砂的一半,大多数金属液对它的润湿性较差,使得金属凝固层与型壳内表面间易产生间隙,热导率进一步减小,有利于壁薄铸件充型。
在高温下熔融石英的透明度高,能通过辐射传热,使其导热能力超过硅酸铝类壳。
而使铸件冷却较快,更易获得健全铸件。
铸件冷却时方石英又从高温型转变为低温型,同时体积产生骤变,使型壳出现无数裂纹,强度剧降,有利于脱壳进行。
熔融石英为酸性,能采用碱煮、碱爆等化学清砂方法去除型壳。
熔模铸造用熔融石英,其中SiO2所占的质量分数应为99.5%,配涂料用的粉料最好是270目或320目细粉占50%(质量分数),200目和120目粉各占25% (质量分数)。
①为0 C〜1200 C间的膨胀系数平均值。
②400 C的热导率。
③1200 C热导率。
熔融石英及制品有三大特点:在所有耐火材料中,线膨胀系数最小(在1000 C的热胀率0.05 );热导率最低,在1000 C热导率0.836W/ (m • K)(0.02cal/cm • s ・C);抗热震性最好(在1200 °C〜水冷的抗震性),10次都不产生裂纹。
二、熔融石英涂料配制使用操作工艺(一)本操作工艺适用于硅溶胶,制壳的表面层或过渡层。
(二)本工艺使用的硅溶胶同锆英粉涂料即SiO230%。
(三)本工艺操作中的润湿剂,消泡剂同锆英粉涂料。
(四)本操作中使用的流杯粘度计为詹氏(Zahn)5#杯,出口孔径为①5.28mm。
(五)涂料配制:1、熔融石英粉的配制,320目(网号:0.044 )275目(网号:0.052 )200目(网号:0.076 )120目(网号:0.125 )熔融石英粉中的SiO2的质量分数为99.5%以上。
其中:320目占50% , 200目占25% , 120目占25% , 百分数的计算为质量分数,即重量比例。
2、涂料粘度为50 ~60秒,严格控制不得低于50秒,60 秒时是最佳粘度。
它可获得最好的表面光洁度铸件;用于生产碳钢或430系列时粘度可以降到40秒。
(六)挂砂:1、用熔融石英砂80〜100目(50〜100 目)50% ,用刚玉砂80目,50%。
2、用熔融石英砂80~100 目(50~100 目)100%,(50~100 目)3、用刚玉砂80目100%。
以上3种挂砂都可以采用,只是铸件根据的不同,结合表面质量在生产现场机动操作。
(七)注意事项:1、涂料配制严格控制比例,不得有随意性,严格现场的操作跟踪。
流杯粘度测量要准确,每次做面层前必须测量粘度。
2、需要做二层面层时,第二次即过渡层时,涂料粘度为28 ~36 秒。
3、表面制壳技术是认真、细致的操作技术,要保证涂料厚度均匀一致,否则会生产出有渗透性或麻点的铸件。
挂砂重力相对一致均匀,面面俱到。
4、熔融石英湿膜情况下的面层在不同粘度下的厚度为:50秒粘度为0.2mm,40秒粘度为0.18mm,30 秒粘度为0.15mm ,20 秒粘度为0.12mm 。
5、熔融石英砂:50〜100目为国家标准网号的0.325〜0.15 号,筛孔尺寸为ASTME11 -70 的0.3 〜0.15mm。
6、第二层的挂砂可同原锆英粉面层工艺时的操作一致,也可用30~50目(筛孔尺寸0.6〜0.3mm )的熔融石英砂。
三、熔融石英——制壳耐火材料新秀熔融石英在精铸中应用虽然已有相当长的历史,但以往主要用作陶瓷型芯,用作型壳则主要用于面层,背层很少使用。
这种状况近10年来在美、欧各国有很大改变。
2001年美国著名耐火材料生产厂商Minco 公司,公布了对美国熔模铸造企业制壳耐火材料使用现状的调查统计数据,各种耐火材料消耗量所占比例(质量分数)大致如下:铝-硅系耐火材料55% ;熔融石英30% ;刚玉9%,锆石6%。
可见在美国精铸业中,熔融石英异军突起,现已是仅次于铝-硅系材料,远远超过锆石等其他耐火材料,迅速成为制壳耐火材料的新秀。
1、熔融石英与铝-硅系材料的比较2000年Mincolnc.在美国第48届精铸年会和INCAST 杂志2001年第3期上发表论文,对熔融石英和铝-硅系耐火材料进行了全面的分析对比。
1.1型壳质量熔融石英密度为2.2g/cm 3,铝-硅系材料为2.7g/cm 3爲故同样厚度型壳,前者质量明显小于后者,有利于减轻工人劳动强度和机械手操作。
1.2热膨胀率图1和图2所示分别为脱蜡和焙烧过程中, 这2种材料 热膨胀率的比较。
热膨胀系数小是熔融石英的一个很大的优 点,有利于减小加热时型壳内外因温度差造成的热应力,因 而有利于防止脱蜡和焙烧过程中型壳开裂和变形。
同时,对 提高铸件尺寸精度也甚为有利。
所以,铸造尺寸公差要求严 格的产品,就更适合采用熔融石英图1 •脱蜡过程中2种材抖热膨胀率的比较图2培烧过程中2种材料热膨胀率的比较0.4 0200400 600 800 1 (XM 1 200温度广C(保&2h )22 40+:~0. 6 -0.80.3876114 152190228ur/r6 05O25 _T4O H O1.3力学性能和透气性表1所列为2种材料制得型壳的力学性能和透气性比较,结果显示,湿强度(抗弯强度)和断裂韧度,熔融石英型壳稍低于铝-硅系型壳,但透气性却远高于铝-硅系型壳表1熔融石英和铝硅系材料型壳性能比较1.4咼温抗蠕变能力当采用熔融石英撒砂代替铝-硅系材料时型壳高温抗蠕变能力提高(见图3)熔融石英在高温下(约1200 C)结晶化转变可作为这种现象的一种解释(见图4)。
ffl 4熔融石英型売在加找过程中的相变1.5脱壳性容易脱壳和清理是熔融石英迅速崛起的最重要原因。
不 同材料型壳残留强度试验结果见表2。
可见熔融石英型壳残留强度大大低于铝 -硅系材料。
这是因为熔融石英大约在 1200 C 高温下会转变为方石英。
实践证明,在浇注温度下, 型壳中大约有70%熔融石英转变为方石英。
当型壳温度下降 至300 C 左右,方石英又由高温型转变为低温型,同时体积 骤变(见图4)无数裂纹随之产生,型壳强度剧降,于是, 脱壳性大为改善。
此外,对于全铝-硅系型壳来说,如时何e图3 不同材料在高湛丁变形量的比較?*-泾>燃F 6200400600 BOO 1 000 1 200 保型2 h)采用碱煮、碱爆等化学清理方法,碱溶液只能溶解粘结剂中的二氧化硅,对耐火粉、粒料却无能为力。
但对熔融石英型壳来说,无论粘结剂还是耐火材料,碱都有强烈的腐蚀作用。
试验表明,在质量分数为50%的KOH熔液中沸腾碱煮,全熔融石英型壳经109min 就大部分溶解,而铝-硅系耐火砂、粉则看不出有什么变化。
所以,采用熔融石英,有利于碱煮、碱爆等化学清理。
减少耗碱量,提高效率。
表2熔融石英和铝-硅系型壳残留强度对比MPa1.6充型难易当温度低于600 C时,熔融石英热导率较铝-硅系材料差(见图5),而比热容又只有锆石的一半,这些因素都有利于薄壁铸件的充型。
但温度高于600 C,由于熔融石英透明度高(夜间浇注时,甚至可透过型壳看见其中流动的钢液),因此辐射散热快,铸件冷却快,更容易获得健全致密的铸件,这对于铸造铝合金薄壁件甚为有利,但同时也会使铸件产生裂纹的趋向增加。
ffi 5 2呼林料的热导率比较与铝-硅系耐火材料比较,尽管熔融石英有着上述诸多优 点,但毕竟价格较贵,是否采用,各厂可自行权衡。
如何使 用,是用于面层,还是用于背层;是单独用,还是与其他材 料混合用;是用粉料,还是用作撒砂料;都需要根据具体情 况,才能获得最佳效果。
2、熔融石英和锆石的比较Jerry D.发表于2002年美国第50届精铸年会的论文, 对用于精铸面层的 2种主要耐火材料——熔融石英和锆石 进行了全面的分析对比。
2.1锆石的优缺点 2.1.1锆石的优点(1) 锆石粉粒度分布宽,一般无需级配,配制成的涂 料浆流变性就很适合涂挂,涂料覆盖性、流平性均属一流。
此外,由于密度大,空料时涂料浆流淌快。
(2) 锆石砂粒形好,多为球形 (见图6),流动性好, 容易充填蜡模上的孔洞、凹槽等不易充填的部位,很适合200 * 400600$00 1 000 1 200 I 4Wft®代8 S4 2 a作为面层撒砂料匕)烧1*需莫砂(bmX-tJr图6 墀敝茗英莎舸特不巧的粧形时比2.1.2锆石的缺点(1)经常发生周期性货源短缺,供应紧张,价格较贵。
(2)由于锆石是天然矿产,所以含有某些有机物和其他杂质在所难免。
其中有的(特别是Fe2O3、磷酸钙等)会和涂料中的粘结剂、添加剂或其他耐火材料反应,造成涂料浆PH改变而迅速老化变质,铸件表面也容易出现硅酸铁黑褐色斑疤或丘疹。
(3)由于环保法规越来越严格,近来,美、欧各国普遍更加关注锆石中放射性元素可能造成的环境问题,这又可能使其价格进一步攀升。
2.2熔融石英的优缺点2.2.1熔融石英的优点(1)熔融石英的价格比锆石便宜,加上密度又比锆石低得多(前者2.2g/cm 3,后者4.7〜4.9g/cm 3),所以,用熔融石英代替锆石,可降低制壳成本(2)熔融石英原材料经过精选,再经电弧重熔,并剔除方石英,因此杂质少,纯度高(见表 3 )。
所以涂料浆稳定性向来不成问题。
实践证明,熔融石英一硅溶胶涂料稳定性通常可长达1年以上。
表3美国Minco公司制壳用熔融石英粉的化学成分(%)(3 )高温晶化,低温相变,使铸件表面容易清理干净222熔融石英的缺点(1)粉料粒度分布范围窄,再加上密度小,不利于涂料流淌、滴落;由于熔融石英涂料浆透明度高,使操作者难于识别涂料厚度和均匀程度。
(2)作为面层撒砂,熔融石英砂粒形为多角形(见图6),再加上密度小,容易架桥,形成浮砂。
2.3应用熔融石英应注意的一些问题采用熔融石英作面层耐火材料需要特别注意它的适用范围。