3-内检测技术
建筑门窗检测技术三性检测部分

试验检测设备
检测装置由压力箱、试件安装系统、供压系 统、淋水系统及测量系统(包括空气流量、压力 差及位移测量装置)组成。检测装置的构成如图 1 所示。
第31页/共76页
门窗气密性、水密性、抗风压检测
检测标准:
标准号:GB/T 7106-2008
标准名:《建筑外门窗气密、水密和抗风
试件应为按所提供图样生产的合格产品或研制的试件, 不得附有任何多余的零配件或采用特殊的组装工艺或改善措 施。
试件必须按照设计要求组合、装配完好,并保持清洁、 干燥。
相同类型、结构及规格尺寸的试件,应至少检测三樘。
第43页/共76页
检测准备
试件安装要求: 试件应安装在安装框架上。 试件与安装框架之间的连接应牢固并密封。安装 好的试件要求垂直,下框要求水平,下部安装框不应 高于试件室外侧排水孔。不应因安装而出现变形。 试件安装后,表面不可沾有油污等不洁物。 试件安装完毕后,应将试件可开启部分开关5次。 最后关紧。
士q1 = ±q1’/4.65………给…定系…数 ……… (5) 士q2 = ±q2’/4.65………… ………… (6)
将三樘试件的±q1’值或±q2’值分别平均 后对照表1确定按照第缝49页长/共和76页按面积各自所属等级。
水密性 检测方法
检测分为稳定加压法和波动加压法。
工程所在地为热带风暴和台风地区的工程 检测,应采用波动加压法;定级检测和工程所在 地为非热带风暴和台风地区的工程检测,可采用 稳定加压法。
定级检测:为确定外门窗抗风压性能指标值P3和 水密性能指标值△P而进行的检测。
工程检测:为确定外门窗是否满足工程设计要求 的抗风压和水密性能而进行的检测。
第39页/共76页
3-3 渗透检测的标准

3-3 渗透检测的标准
目的
制定渗透检测的标准目的是为了使检测工作能够顺利展开。
适用范围
此方法适用于渗透检测
渗透检测的检查员
持有许作业可证的人才能执行渗透检测
渗透检测的方法
1.应当把焊缝和热影响区作为一个检测区域而进行检测。
2.一般情况下,只要材料的表面温度在40 ℃以内都可以进行渗透检测。
3.检测准备工作必须清除掉表面的杂质,如碎片、铁锈、油漆,特别是需要检测的表面更需
要完全的清除干净。
4.渗透检测维持的时间大于或等于10分钟。
5.一般情况下,检测工作完成后,要完全清除掉检测表面的显色剂。
评定
1.必须根据独立的评定标准对缺陷进行评定。
2.如果缺陷不能够被精确的评定,则要用研磨机磨在0.5mm以内,然后再进行渗透检测。
检测报告
检测结果必须记录在附件列出的“渗透检测报告”的清单里。
供热管道内检测机器人发展现状及关键技术

供热管道内检测机器人发展现状及关键技术供热管道是城市供热系统的重要组成部分,其安全稳定运行对于保障居民的温暖过冬至关重要。
然而,由于长期使用、腐蚀、磨损等原因,供热管道可能会出现各种缺陷和故障,如裂缝、腐蚀坑、堵塞等。
为了及时发现和评估这些问题,保障供热管道的安全运行,供热管道内检测机器人应运而生。
一、供热管道内检测机器人的发展现状1、国外发展现状在国外,一些发达国家早在几十年前就开始了对供热管道内检测技术的研究。
例如,德国、美国、日本等国家的相关企业和科研机构已经研发出了多种类型的供热管道内检测机器人,并在实际应用中取得了良好的效果。
这些机器人通常具有较高的检测精度和可靠性,能够适应不同管径和工况的供热管道。
2、国内发展现状相比之下,我国在供热管道内检测机器人领域的研究起步较晚,但近年来发展迅速。
目前,国内一些高校、科研机构和企业也在积极开展相关研究和开发工作,并取得了一定的成果。
一些国产的供热管道内检测机器人已经开始在部分地区进行试点应用,但其性能和可靠性与国外先进产品相比仍存在一定差距。
二、供热管道内检测机器人的类型1、漏磁检测机器人漏磁检测是一种常用的无损检测方法,漏磁检测机器人通过在管道内产生磁场,并检测磁场的变化来判断管道是否存在缺陷。
这种机器人具有检测速度快、准确性高的优点,但对于较小的缺陷容易漏检。
2、超声检测机器人超声检测机器人利用超声波在管道壁中的传播和反射来检测缺陷。
它能够检测出较小的缺陷,并且对管道壁的厚度测量较为准确,但检测效率相对较低。
3、涡流检测机器人涡流检测机器人通过在管道内产生涡流,并检测涡流的变化来判断管道的缺陷情况。
这种机器人对表面缺陷检测较为敏感,但对深层缺陷的检测能力有限。
三、供热管道内检测机器人的关键技术1、驱动与行走技术供热管道内检测机器人需要在管道内自由行走,因此驱动与行走技术是关键之一。
目前,常见的驱动方式有轮式、履带式和蠕动式等。
轮式驱动速度快,但在复杂管道内的适应性较差;履带式驱动稳定性好,但结构复杂;蠕动式驱动适用于小管径管道,但行走速度较慢。
油气管道三轴高清漏磁内检测机器人设计验证
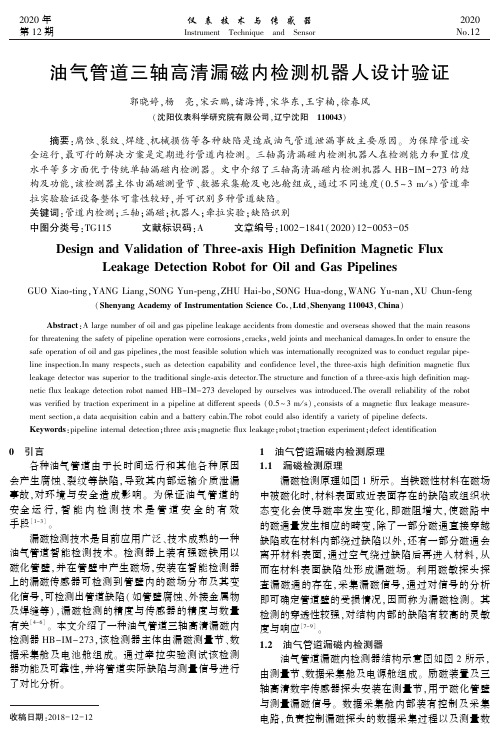
㊀2020年㊀第12期仪表技术与传感器Instrument㊀Technique㊀and㊀Sensor2020㊀No.12㊀收稿日期:2018-12-12油气管道三轴高清漏磁内检测机器人设计验证郭晓婷,杨㊀亮,宋云鹏,诸海博,宋华东,王宇楠,徐春风(沈阳仪表科学研究院有限公司,辽宁沈阳㊀110043)㊀㊀摘要:腐蚀㊁裂纹㊁焊缝㊁机械损伤等各种缺陷是造成油气管道泄漏事故主要原因㊂为保障管道安全运行,最可行的解决方案是定期进行管道内检测㊂三轴高清漏磁内检测机器人在检测能力和置信度水平等多方面优于传统单轴漏磁内检测器㊂文中介绍了三轴高清漏磁内检测机器人HB-IM-273的结构及功能,该检测器主体由漏磁测量节㊁数据采集舱及电池舱组成,通过不同速度(0.5 3m/s)管道牵拉实验验证设备整体可靠性较好,并可识别多种管道缺陷㊂关键词:管道内检测;三轴;漏磁;机器人;牵拉实验;缺陷识别中图分类号:TG115㊀㊀㊀文献标识码:A㊀㊀㊀文章编号:1002-1841(2020)12-0053-05DesignandValidationofThree⁃axisHighDefinitionMagneticFluxLeakageDetectionRobotforOilandGasPipelinesGUOXiao⁃ting,YANGLiang,SONGYun⁃peng,ZHUHai⁃bo,SONGHua⁃dong,WANGYu⁃nan,XUChun⁃feng(ShenyangAcademyofInstrumentationScienceCo.,Ltd,Shenyang110043,China)Abstract:Alargenumberofoilandgaspipelineleakageaccidentsfromdomesticandoverseasshowedthatthemainreasonsforthreateningthesafetyofpipelineoperationwerecorrosions,cracks,weldjointsandmechanicaldamages.Inordertoensurethesafeoperationofoilandgaspipelines,themostfeasiblesolutionwhichwasinternationallyrecognizedwastoconductregularpipe⁃lineinspection.Inmanyrespects,suchasdetectioncapabilityandconfidencelevel,thethree⁃axishighdefinitionmagneticfluxleakagedetectorwassuperiortothetraditionalsingle⁃axisdetector.Thestructureandfunctionofathree⁃axishighdefinitionmag⁃neticfluxleakagedetectionrobotnamedHB-IM-273developedbyourselveswasintroduced.Theoverallreliabilityoftherobotwasverifiedbytractionexperimentinapipelineatdifferentspeeds(0.5 3m/s),consistsofamagneticfluxleakagemeasure⁃mentsection,adataacquisitioncabinandabatterycabin.Therobotcouldalsoidentifyavarietyofpipelinedefects.Keywords:pipelineinternaldetection;threeaxis;magneticfluxleakage;robot;tractionexperiment;defectidentification0㊀引言各种油气管道由于长时间运行和其他各种原因会产生腐蚀㊁裂纹等缺陷,导致其内部运输介质泄漏事故,对环境与安全造成影响㊂为保证油气管道的安全运行,智能内检测技术是管道安全的有效手段[1-3]㊂漏磁检测技术是目前应用广泛㊁技术成熟的一种油气管道智能检测技术㊂检测器上装有强磁铁用以磁化管壁,并在管壁中产生磁场,安装在智能检测器上的漏磁传感器可检测到管壁内的磁场分布及其变化信号,可检测出管道缺陷(如管壁腐蚀㊁外接金属物及焊缝等),漏磁检测的精度与传感器的精度与数量有关[4-6]㊂本文介绍了一种油气管道三轴高清漏磁内检测器HB-IM-273,该检测器主体由漏磁测量节㊁数据采集舱及电池舱组成㊂通过牵拉实验测试该检测器功能及可靠性,并将管道实际缺陷与测量信号进行了对比分析㊂1㊀油气管道漏磁内检测原理1.1㊀漏磁检测原理漏磁检测原理如图1所示㊂当铁磁性材料在磁场中被磁化时,材料表面或近表面存在的缺陷或组织状态变化会使导磁率发生变化,即磁阻增大,使磁路中的磁通量发生相应的畸变,除了一部分磁通直接穿越缺陷或在材料内部绕过缺陷以外,还有一部分磁通会离开材料表面,通过空气绕过缺陷后再进入材料,从而在材料表面缺陷处形成漏磁场㊂利用磁敏探头探查漏磁通的存在,采集漏磁信号,通过对信号的分析即可确定管道壁的受损情况,因而称为漏磁检测㊂其检测的穿透性较强,对结构内部的缺陷有较高的灵敏度与响应[7-9]㊂1.2㊀油气管道漏磁内检测器油气管道漏磁内检测器结构示意图如图2所示,由测量节㊁数据采集舱及电源舱组成㊂励磁装置及三轴高清数字传感器探头安装在测量节,用于磁化管壁与测量漏磁信号㊂数据采集舱内部装有控制及采集电路,负责控制漏磁探头的数据采集过程以及测量数㊀㊀㊀㊀㊀54㊀InstrumentTechniqueandSensorDec.2020㊀图1㊀漏磁检测原理图2㊀管道漏磁内检测器结构示意图据的预处理和存储,是内检测的核心㊂电池舱为内检测器提供电源,保证内检测器在管道内部运行过程中正常运转[10-11]㊂1.3㊀三轴漏磁检测原理管道内三轴示意图如图3所示㊂图3㊀管道内三轴示意图三轴漏磁内检测器工作原理与传统单轴漏磁内检测器基本相同,其区别是三轴漏磁内检测器在一个传感器内轴向正交布置了3个霍尔传感器,分别测量管道轴向㊁周向及径向的磁通量变化情况㊂因此,这种多维数据综合反应了管道内部缺陷的尺寸特征,提高了不同类型缺陷的探测能力和缺陷尺寸的测量精度[12]㊂1.4㊀三轴漏磁信号图4为40mmˑ40mmˑ0.8mm矩形缺陷的三轴漏磁信号二维曲线图㊂可以看出,漏磁场的轴向分量关于纵轴对称;径向分量关于原点对称,且在靠近原点两侧各有一个大小相等㊁方向相反的极值㊂研究表明:轴向㊁径向和周向信号的幅值表示缺陷的深度信息;三轴信号的跨度表示缺陷的长度信息;信号的条带数表示缺陷的宽度信息[13-15]㊂2㊀漏磁内检测机器人设备2.1㊀机器人整机273管径三轴高清漏磁内检测机器人设备主要由漏磁测量节㊁数据采集舱及电池舱组成,如图5所示,图5中1Gs=10-4T㊂漏磁测量节由24个漏磁探头组成,每个探头内封装有4组三轴漏磁传感器㊂因此,整(a)轴向(b)径向(c)周向图4㊀矩形缺陷的三轴漏磁信号图5㊀三轴高清漏磁内检测机器人个圆周上每个轴向上有96个传感器,平均3.75ʎ分布1个漏磁传感器㊂2.2㊀磁路系统结构该设备磁路系统如图6所示,由钢刷㊁磁铁㊁磁轭㊁探头㊁探头座组成㊂磁铁通过钢刷导磁,以磁化管壁㊂探头通过探头座固定于磁轭上㊂探头与管壁贴合,可测量管壁内外有无缺陷情况㊂2.3㊀探头内部结构漏磁复合传感器探头组成结构如图7所示㊂三轴漏磁传感器经过I2C通讯协议传输到ARM-STM32控制探头系统㊂利用PCB打印涡流传感器线圈,代替传㊀㊀㊀㊀㊀第12期郭晓婷等:油气管道三轴高清漏磁内检测机器人设计验证55㊀㊀图6㊀磁路系统结构图7㊀复合传感器探头结构框图统的手工缠绕线圈,减少了线圈体积空间,增强了线圈的稳定性及不易损性㊂涡流线圈经过控制系统提供的激励,检测的信号经过涡流线圈接收电路进行接收,通过SPI协议传输给ARM-STM32控制探头系统㊂由控制系统进行采集和存储后,经过数据输出驱动器传输到1.5m外的数据采集系统㊂2.4㊀数据采集及存储系统涡流线圈经过激励后,通过涡流传感器线圈接收电路对其信号进行接收,接收电路图如图8所示㊂图8㊀涡流传感器线圈接收电路结构图线圈的两端分别接入INA㊁INB信号端,电路处理过程中,由LC振荡激励电路为涡流传感器线圈提供激励电压㊁激励频率等参数,当涡流传感器线圈检测到管壁内壁缺陷时,发生阻抗变化,由电感值测量电路检测到电感值,经过寄存器和逻辑处理器处理后,进行阈值比较,转成SPI通讯协议输出信号,从而判断管壁的缺陷情况㊂图9为数据采集存储结构㊂由SPI通讯协议输出的CSB㊁SCLK㊁SDI㊁SDO信号经过传输线传输到单片机采集系统,单片机主控选图9㊀数据采集存储结构图择ARM-STM32系列芯片㊂其中,CLKIN表示外部时基时钟输入,CLDO外接一个15nF电容从引脚连接到GND,CSB表示可以将多个通道连接在相同的SPI总线上,SCLK表示SPI通讯协议时钟输入,SDI表示SPI数据输入连接到SPI主机的MOSI,SDO表示SPI数据输出连接到SPI主机的MISO㊂传感器检测数据经过SPI协议,传输到ARM-STM32控制探头系统,系统中包含高精度时钟模块㊁稳压电源模块㊁存储模块㊁总线协议模块㊁FATFS文件管理模块对传感器数据进行采集和存储,并通过显示模块显示当前输出信号㊂3㊀漏磁内检测机器人现场测试及数据分析3.1㊀现场牵拉实验为验证设备可靠性与功能完整性,进行设备投产前牵拉实验㊂该设备牵拉前后状态如图10所示㊂在不同速率下(0.5 3m/s),共在管道内牵拉12次,总运行里程约1km㊂实验完成后,该设备整体结构完好㊂(a)牵拉实验前(b)牵拉实验后图10㊀现场牵拉实验前后检测器状态图㊀㊀㊀㊀㊀56㊀InstrumentTechniqueandSensorDec.2020㊀3.2㊀采集数据分析图11 图13分别为管道焊缝㊁外加金属及金属缺失实物图及检测器采集到的三轴漏磁信号曲线㊂由(a)管道焊缝实物图(b)周向管道焊缝(c)轴向管道焊缝(d)径向管道焊缝图11㊀管道焊缝与三轴数据分量图图中可以看出,检测器对管道焊缝㊁外加金属及金属缺失检出效果明显㊂焊缝与金属增加曲线信号变化方向相同,而与金属缺失信号曲线方向相反㊂根据曲线变化情况可分辨缺陷类型㊂(a)管道外加金属实物图(b)周向信号管道外加金属(c)轴向信号管道外加金属(d)径向信号管道外加金属图12㊀管道外加金属与三轴数据分量图㊀㊀㊀㊀㊀第12期郭晓婷等:油气管道三轴高清漏磁内检测机器人设计验证57㊀㊀(a)管道金属缺失实物图(b)周向信号金属缺失(c)轴向信号金属缺失(d)径向信号金属缺失图13㊀管道金属缺失与三轴数据分量图4㊀结论本文研发的油气管道三轴高清漏磁内检测器HB-IM-273,主体由漏磁测量节㊁数据采集舱及电池舱组成㊂通过牵拉实验测试该检测器功能及可靠性,并将管道实际缺陷与测量信号进行了对比分析,得到以下结论:经过不同速度条件下(0.5 3m/s)牵拉实验检验,设备整体可靠性较好;三轴传感器能够明确分辨出各种类型管道缺陷,包括焊缝㊁外加金属㊁金属缺失等㊂参考文献:[1]㊀鲍庆军,帅健.油气管道内检测技术研究进展[J].当代化工,2017,46(2):298-301.[2]㊀HUANGK.3⁃Ddefectprofilereconstructionfrommagneticfluxleakagesignaturesusingwaveletbasisfunctionneuralnetworks[D].Ames:IowaStateUniversity,2000.[3]㊀杨理践,沈博,高松巍.应用于管道内检测器的管道地理坐标测量方法[J].仪表技术与传感器,2013(11):84-87.[4]㊀刘刚.管道漏磁内检测关键技术问题研究[D].沈阳:沈阳工业大学,2010.[5]㊀吴欣怡,赵伟,黄松岭.基于漏磁检测的缺陷量化方法[J].电测与仪表,2008,45(5):24-26;41.[6]㊀杨理践,耿浩,高松巍.长输油气管道漏磁内检测技术[J].仪器仪表学报,2016,37(8):1736-1746.[7]㊀冯庆善,张海亮,王春明,等.三轴高清漏磁检测技术优势及应用现状[J].油气储运,2016,35(10):1050-1054.[8]㊀杨理践,邢磊,高松巍.三轴漏磁缺陷检测技术[J].无损探伤,2013,37(1):9-12.[9]㊀廖肖晓,周绍骑,刘胜群.三轴交流漏磁检测的有限元仿真[J].自动化与仪器仪表,2015(9):14-18.[10]㊀白港生,徐志,吴楠勋.三轴高清晰度漏磁腐蚀检测器的研制[J].石油机械,2014,42(10):103-106.[11]㊀单少卿,陈世利,靳世久,等.高清晰度三轴管道内检测器漏磁数据采集系统[J].传感器与微系统,2012,31(5):118-121.[12]㊀王富祥,冯庆善,张海亮,等.基于三轴漏磁内检测技术的管道特征识别[J].无损检测,2011,33(1):79-84.[13]㊀丁战武,何仁洋,刘忠.管道漏磁检测缺陷信号的仿真分析与量化模型[J].无损检测,2013,35(3):30-33.[14]㊀吴德会,刘志天,苏令锌.双传感器差分峰值侦测的漏磁检测新方法[J].仪器仪表学报,2016,37(6):1218-1225.[15]㊀刘金海,付明芮,唐建华.基于漏磁内检测的缺陷识别方法[J].仪器仪表学报,2016,37(11):2572-2581.作者简介:郭晓婷(1987 ),工程师,硕士,主要研究方向为管道内无损检测技术研究㊂E⁃mail:tingting0924@163.com杨亮(1985 ),工程师,博士研究生,主要研究方向为管道检测技术研究及相关设备研发㊂E⁃mail:yangliang850223@163.com。
管道内检测介绍PPT课件

电子设备模块 IV
磁化管壁模块 MV
四、检测流程
漏磁检测的探测能力
漏磁检测系统的探测能力(适用于所有类型的管道,例如无缝管道、直 缝焊管道、螺旋焊接管道等)目前能够探测到管道内如下类型的特征: (a)金属损失
(1)腐蚀相关 环焊缝附近 凹陷相关 管壁外
(2)划伤相关 (b)修补夹板下面的金属损失 (c)制造缺陷相关的金属损失 (d)环焊缝、直焊缝、螺旋焊缝 (e)包括环焊缝内环形裂纹在内的环焊缝异常 (f)凹陷 (g)制造型缺陷 (h)施工损坏 (i)标称管壁厚度不符
二、内部检测的可行性
(一)海检中心简介
中国石化集团胜利石油管理局海上石油工程技术检验中 心 (简称“海检中心)成立于1990年,业务上受中国石化集 团公司安全环保局和科技开发部归口管理,具有国家安全生 产监督管理总局颁发的“海洋石油生产设施(浅海)发证检 验机构”资质、“海洋石油天然气专业设备检验检测机构” 资质,是国内仅有的两家发证检验机构之一,也是石油石化 行业唯一一家具有发证检验资质的单位。同时具有国家质量 监督检验检疫总局颁发的“无损检测机构A级”资质,国家建 设部颁发的无损检测工程专业承包壹级资质,是中国石化集 团唯一一家A级资质无损检测机构,迈入全国检测行业20强行 列。
四、检测流程
漏磁检测原理
四、检测流程
内、外部缺陷判定的原理
位于智能模块(IV)上的第二组传感器用来区分内部 缺陷和外部缺陷。
四、检测流程
管线裂纹检测的原理
位于智能模块(IV)上的第二组传感器可以检测裂纹 的长度、深度。
四、检测流程
漏磁检测步骤:
1.对缺陷检测装置标定 2.将缺陷检测装置放入投放装置内,接收端准备好检测装置的接收等工作; 3.检测装置通电,同时开始计时; 4.打开清管流程,检测装置在压差的驱动下启动,以的 速度运行,并开始
三级探伤检测标准

三级探伤检测标准三级探伤检测是一种常用的无损检测方法,广泛应用于航空航天、汽车制造、铁路运输、石油化工等领域。
它通过检测材料内部的缺陷和异物来评估材料的质量和完整性,确保其符合相关标准和要求。
本文将介绍三级探伤检测的标准和要点,以便相关人员能够准确、规范地进行检测工作。
1. 检测设备和工艺。
三级探伤检测通常使用超声波、射线和磁粉等技术和设备进行。
在进行检测前,需要对设备进行校准和检测,确保其准确性和稳定性。
在进行检测时,需要根据具体材料和缺陷的特点选择合适的检测工艺,以获得准确的检测结果。
2. 检测标准和要求。
三级探伤检测的标准和要求是指导检测工作的重要依据。
根据不同行业和材料的相关标准,对于不同类型的缺陷和材料的检测要求也有所不同。
因此,在进行检测工作时,需要严格遵循相关标准和要求,确保检测结果的准确性和可靠性。
3. 检测人员素质和培训。
进行三级探伤检测的人员需要具备一定的专业知识和技能,能够熟练操作检测设备和工艺,并能够准确判断和评估检测结果。
因此,对于检测人员的素质和培训也是非常重要的。
只有经过专业培训和合格考核的人员才能够进行三级探伤检测工作。
4. 检测结果的评定和记录。
在进行三级探伤检测后,需要对检测结果进行准确的评定和记录。
对于合格的材料,需要及时进行标记和记录,以便后续的使用和追溯。
对于不合格的材料,需要进行详细的记录和分析,并采取相应的措施进行修复或处理。
5. 检测工作的质量控制和改进。
三级探伤检测工作需要进行质量控制和改进,以确保检测结果的准确性和可靠性。
对于检测中发现的问题和不足,需要及时进行改进和调整,以提高检测工作的质量和效率。
总结。
三级探伤检测是一项重要的无损检测方法,对于保障材料的质量和安全具有重要意义。
通过严格遵循相关标准和要求,提高检测人员的素质和技能,加强检测工作的质量控制和改进,可以确保三级探伤检测工作的准确性和可靠性,为各行业的生产和运输提供可靠的保障。
3-2红外检测技术 [兼容模式]
![3-2红外检测技术 [兼容模式]](https://img.taocdn.com/s3/m/767953816529647d27285278.png)
红外热波检测技术周正干2013/10/173红外热波检测技术的特点和优势0红外热波检测设备1红外热波检测技术的应用2什么是红外热波检测3红外热波检测技术的特点和优势0红外热波检测设备1红外热波检测技术的应用2什么是红外热波检测红外热波无损检测技术在20世纪90年代起源于美国,与传统的热成像技术不同,热波检测要根据不同的检测对象采用主动式控制加热来激发被检物的内部损伤和缺陷,通过快速热图采集和基于热波理论的图像处理技术实现损伤探测。
红外热波无损检测技术的基本原理是利用红外热波(Thermal Wave )在被检测对象中的传播情况得到被检测对象的内部组织情况和不连续性的相关信息。
该技术的基础是热波理论,主要研究热源,特别是变化性热源(如周期、脉冲、阶梯函数热源)与媒质材料之间的相互作用。
被加热后,不同媒质材料表面及表面下的物理结构特性和边界条件将影响热波的传输进而以某种方式影响媒质表面的温度场变化。
通过控制热激励方法和测量材料表面的温度场变化,可以获取材料的均匀性信息以及其表面以下的结构信息,从而达到检测和探伤的目的。
☐红外热波无损检测技术的核心具体地讲,就是针对被检物的材质、结构和缺陷类型以及特定的检测条件,设计不同特性的热源(如:高能闪光灯、超声波、电磁、热风等)并用计算机控制进行周期、脉冲等函数形式的加热,同时采用红外热成像技术对时序热波信号进行捕捉和数据采集,采用专用软件进行实时图像信号处理和分析并最终显示检测结果。
☐在红外热波无损检测技术中,目前最常用的一种热激励方式就是用高能闪光灯提供脉冲形式的热源,这是一种采用主动式控制热激励的方法。
典型的脉冲加热红外热波无损检测系统的原理示意图高能闪光灯由功率几千瓦量级的电源提供能量;瞬间闪光之后,热波在待测物体(试件)中传播,试件表面的温度反映表面以下的热传导特性;红外热像仪实时记录试件表面温度;计算机对整个系统进行控制,并对实时热图进行记录和处理。
3-内检测技术
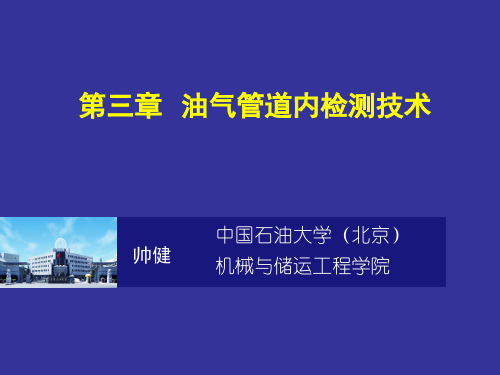
21
(4)测绘工具
• 采用精密惯性制导仪器,记录管道极微小的移动;
• 用于测绘管道的纵断面和路径;
• 与GPS联合使用能为地质断层、沉陷区、永冻土地区等提
供优良的监测。
22
测绘工具
• 高精度提供真实空间坐标:
–所有缺陷的坐标; –弯曲应变/曲率;
–绝对弯曲应变;
–监测土体或其它外部因素导致的管线移动;
超声检测器——超声回波技术,压缩波。
12
超声检测
• 超声检测扫描管道壁厚,可得到缺陷的河床表面, 容许采用先进的缺陷评价方法。
13
金属损失检测
漏磁与超声检测技术比较 • 漏磁检测属于间接测量,对管道介质、环境等因 素要求较超声波方法宽松,目前普遍采用; • 超声检测直接测量管道壁厚,虽然检测结果精确 度较高,但其对管道的清洁度要求较高,同时还 要求有耦合剂,限制了其应用范围。
27
管道机械特征
• 场地弯曲和河流穿越处——高土体运动的敏感性; • 内涂层——某些工具对内涂层有所损害; • T型结构——使检测器失速; • 管道上安装的设备:如孔板流量计(气体管线)、压 力罐(原油管线)、y-型分支接头和斜接弯头等;
• 自燃材料——特别是硫化亚铁,应防止火灾。
28
3、介质类型、流量和速度
• 20世纪60年代,在美国诞生了 管道内检测器,称Smart Pig & Intelligence Pig,是一种 集成了多种技术的高技术装置。 • 内检测也称为在线检测,内检 测器在管道内由输送介质推动, 在移动过程中检测管壁,不需 要中断管线运行。 • 内检测已经是管道完整性管理 的首要(常规)手段。
金属损失腐蚀缺陷等裂纹应力腐蚀裂纹等几何管壁凹陷压扁测绘路径1金属损失检测mfl技术漏磁通量泄漏检测技术漏磁检测器的基本原理如果管壁没有缺陷则磁力线封闭于管壁之内均匀分布
管道内检测技术及发展趋势_石永春
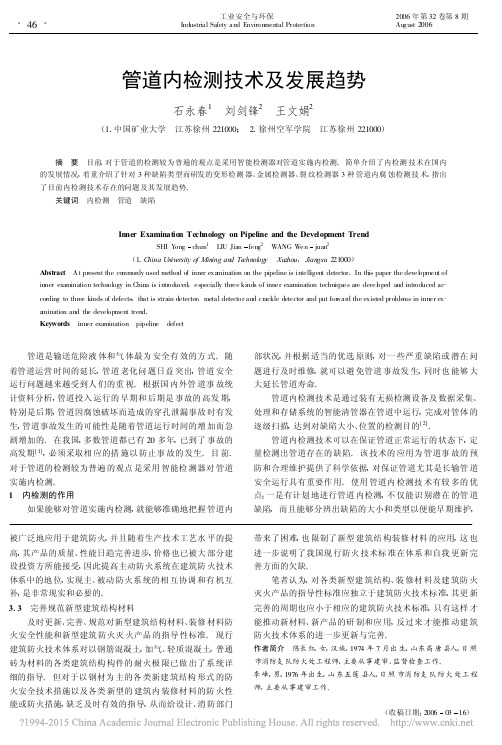
管道内检测技术及发展趋势石永春1 刘剑锋2 王文娟2(1.中国矿业大学 江苏徐州221000; 2.徐州空军学院 江苏徐州221000) 摘 要 目前,对于管道的检测较为普遍的观点是采用智能检测器对管道实施内检测。
简单介绍了内检测技术在国内的发展情况,着重介绍了针对3种缺陷类型而研发的变形检测器、金属检测器、裂纹检测器3种管道内腐蚀检测技术,指出了目前内检测技术存在的问题及其发展趋势。
关键词 内检测 管道 缺陷Inner Examinatio n Technology on Pipeline and the Development TrendSHI Y ong chun1 LIU Jian feng2 WANG Wen juan2(1.C hina Univer sity of Mining and Te chnol ogy Xuz hou,Jiangsu221000)Abstract At present the co mmonly used method of inner exa mination on the pipeline is intell igent detector.In this paper the devel opment of inner examination technol ogy in China is introduced,es peciall y three kinds of inner examination techniques are devel oped and introduced ac-cording to three kinds of defects,that is strain detector,metal detector and crackle detector and put for ward the existed proble ms in inner ex-a mination and the devel opment trend.Keywords inner examination pipeline defect 管道是输送危险液体和气体最为安全有效的方式。
质量“三检”制度

质量“三检”制度为了加强项目工程施工现场质量的过程控制管理,确保工程施工质量满足设计及规范要求,保证项目在质量实施过程中对每道工序质量都能撑握在预控当中,根据业主单位、公司要求及工程实际施工要求,结合工程施工实际情况,特制定本制度。
一、三检制分解1.1自检责任人:作业班组组长;职责:初检是保证施工质量的基础,要求班组人员相互间进行检查、监督和把关。
每一道工序完成后,由该班组按照工序或单元工程规定的检查(检测)项目逐项检查与,真实地填写施工记录,并由班组长本人签字。
在施工过程中,根据质量控制要求,严格规范施工程序。
班组是按照作业规程施工的主体,也是保证工程质量的主体。
初检合格后,负责初检资料的整理与上报,并为复检工作做好现场准备。
实施程序:(1)、施工班组人员在操作过程中,必须按相应的检验批质量验收记录表进行自检,经自检达到质量标准,并经组长验收后,方准继续进行施工。
(2)、班组长对所施工的,必须按相应的质量验收记录表中所列(工序操作前由技术负责人交底时提供该工序检验表)的检查内容,在施工过程中逐项地检查班组每个成员的操作质量。
在完成后逐项地进行自检,并认真填写自检记录,经自检达标后方可请施工员组织质量验收。
(3)施工员除督促班组认真自检、填写自检记录,为班组创造自检条件(如提供有关表格、协助解决检测工具等)外,还要对班组操作质量进行中间检查。
在班组自检达标且有自检记录的基础上,逐项地进行检查,经检查达标后,方可请项目专业质量检查员进行质量核验。
责任人:技术员;职责:复检是在班组初检的基础上,由现场技术员对初检所形成的相关记录进行复核。
复检的主要内容是:检查初检项目是否齐全;检验数据是否准确;检查结果与施工记录是否相符等,并负责做好复检验收工作。
复检验收合格后负责复检资料的整理与上报(专职质检员或技术负责人)并为终检工作做好现场准备。
实施程序:(1)班组长在自检合格的情况下,可以申请现场技术员进行检验批工程质量核验。
压力管道全面检验与内检测规范内容分析

压力管道全面检验与内检测规范内容分析发布时间:2021-06-17T01:45:19.947Z 来源:《中国科技人才》2021年第9期作者:贺斌林庄刚刘强[导读] 对于管道使用单位而言,由于法定检验没有明确的定义,在保证管道安全前提下各种特种设备相关规范规定的管道“体检”类型较多。
本文对管道全面检验与内检测、外检测等检测方式涉及到的现有规范内容进行分析、讨论,同时给出修改建议。
山东省特种设备检验研究院日照分院山东省日照市 276800摘要:近年来,经济的飞速发展极大的推动了各行各业的发展和进步。
在实际的工业生产领域,压力管道是十分关键的存在。
压力管道的正常运行是保证工业生产可以顺利开展的基础和前提。
因此,研究压力管道的检验问题具有重要的现实意义。
关键词:压力管道;全面检验;内检测;规范内容引言对于管道使用单位而言,由于法定检验没有明确的定义,在保证管道安全前提下各种特种设备相关规范规定的管道“体检”类型较多。
本文对管道全面检验与内检测、外检测等检测方式涉及到的现有规范内容进行分析、讨论,同时给出修改建议。
1全面检验日期与内检测、外检测的逻辑关系从规范的逻辑上分析可以得出以下论证:论证(1):管道企业在进行全面检验时,由于采用外检测的方法进行检验,那么由检验单位出具全面检验报告时,结合全面检验和合于使用评价结果,在合于使用评价结论报告中确定下一次的全面检验日期。
在该种情况中,“下一次外检测日期”与“下一次全面检验日期”属于同一个日期。
论证(2):管道企业在进行全面检验时,由于采用内检测的方法进行检验,那么由检验单位出具全面检验报告,结合全面检验和合于使用评价结果,在合于使用评价结论报告中确定下一次的全面检验日期。
在该种情况中,“下一次内检测日期”与“下一次全面检验日期”属于同一个日期。
从D7003第十六条内容分析可知,管道企业选择合适的全面检验方法,并没有要求全面检验同时采用内检测和外检测的方法,既然是由管道企业来选择,那么企业可以只采用一种方法完成全面检验。
三级点检的方法及要求

三级点检的方法及要求三级点检是一种全面检查设备和设施状况的方法。
它被广泛应用于生产现场和工业设备的保养和维修中,旨在确保设备的可靠性、生产效率和安全性。
下面是三级点检的方法和要求的详细说明。
一、三级点检的方法1.准备工作:准备工作主要包括掌握设备的使用说明书、技术资料和维修记录,在进行点检前对设备进行充分的了解。
2.设备检查:(1)外观检查:检查设备外部是否有明显的损坏、腐蚀、漏油等情况,同时检查设备的附件和连接部件是否齐全。
(2)操作检查:检查设备的各个操作部件是否灵活可靠,如手柄、开关、按钮等。
(3)电气检查:检查设备的电气部分是否正常工作,如电源接线是否接地良好、电源开关是否正常、电气设备的安全开关是否齐全等。
(4)机械检查:检查设备的机械部分是否正常工作,如传动部件是否有异常声音、传动装置是否润滑良好等。
(5)液压和气动检查:对液压和气动系统进行检查,检查油压和气压是否正常,管路是否有漏油、漏气等。
(6)测量检查:对设备的测量部件进行检查,如压力表、温度计、流量计等是否准确。
3.数据记录:根据点检结果,准确地记录设备的运行状况。
将设备的工作参数、异常情况和维修记录等信息进行整理和分析。
4.问题解决:对于检查出的问题,制定相应的解决方案,并在必要时进行维修或更换设备。
同时,及时与设备使用者、维修人员和管理人员进行沟通,确保问题能够及时解决。
二、三级点检的要求1.全面性:点检要覆盖设备的所有重要部位和关键部件,包括外观、操作、电气、机械、液压和气动系统等。
不能有遗漏。
2.准确性:点检时应准确记录设备的工作参数和异常情况,确保对设备的检查结果准确无误。
3.规范性:点检操作应按照标准操作程序进行,遵循相关的操作规程和安全规范,确保操作的规范性和安全性。
4.及时性:点检要在规定的时间内完成,不能拖延和遗漏。
特别是对于发现的问题,要及时报告和解决,防止问题的进一步扩大。
5.记录和分析能力:点检人员要具备记录和分析设备运行状况的能力。
压力管道内检测技术要点分析

压力管道内检测技术要点分析摘要:现阶段我国的城市化建设规模可以说是越来越大,许多特殊资源的运输都是需要应用压力管道进行保护的,这主要考虑到了部分资源的易燃易爆特点,因此保证压力管道的安全性十分重要。
对于管道的定期维护而言,除了管道外部之外,内部的情况更为复杂,因此内检测技术越来越受到重视,管道的完整性、内腐蚀等问题都是需要考虑到的。
笔者将会以压力管道为研究对象,针对部分内检测技术的要点进行分析。
关键词:压力管道;内检测技术;技术要点引言压力管道具有高度的特殊性,一般用于工业、燃气系统的运输工作,在我国的现代化经济建设中发挥着重要的作用。
我国很多管线的使用时间是比较长的,其中存在的安全隐患是比较多的,比如说管体老化、腐蚀等,严重者会导致管道穿孔而影响工作效率。
相关企业必须要重视压力管道的内检测并做好事故预防工作。
1.压力管道检验内容和方法从目前的国家规范来看,对管道的检测方法有三大类,通过这些方法的检测,使各种设备达到一定标准,能够正常使用。
这三种检验方法包括内部检验、外部检验和水压试验。
检测需要按照一定的流程进行,在正式进行检验之前,先从宏观层面上检查各种设备的外观是否符合要求,安全控制系统能否正常工作,相关工作人员是否具有一定资质等,在整体管理上确保符合要求后,下一步就是具体对各种设备管道全面检查,无论是内部检查、外部检查、还是水压实验,都需要按照相关的技术要求标准,规范化操作,对其中有问题的地方做到早发现早处理,检查完毕后,为了进一步确定设备是否能够正常运行,一般要进行预实验,模拟实际应用环境,检验设备的运行情况,确保没有问题后,才能投入使用。
同时对容易出现裂纹的部位要给予更多的关注,定期检查其安全性和完整性,对出现问题的地方及时解决。
2.压力管道内检测技术要点2.1漏磁检测技术漏磁检测是基于铁磁性材料具有较高磁导率这一特性上的,如果钢管因腐蚀而出现缺陷,那么缺陷部位的磁导率要较正常部位的偏低。
3TOFD技术原理及应用介绍

3tofd在铁路行业的应用案例
• 案例一:应用3tofd技术对某铁路大桥进行检测 • 检测目的:检测大桥结构损伤、裂缝等问题,确保其安全运行。 • 检测方法:采用3tofd扫描仪对大桥表面进行扫描,获取数据后进行智能分析。 • 检测结果:发现大桥存在多处损伤和裂缝,及时进行了维修和加固。 • 案例二:应用3tofd技术对某铁路隧道进行检测 • 检测目的:检测隧道内部衬砌、排水系统等问题,确保其安全、可靠性。 • 检测方法:采用3tofd扫描仪对隧道表面进行扫描,获取数据后进行智能分析。 • 检测结果:发现隧道存在衬砌破损、排水不畅等问题,及时进行了维修和改造。
经济性
3tofd技术可以节省大量人力、物力和财力资源, 不需要开窗口、不需要大量人员参与检测,同时 可以减少误判的概率,因此具有很高的经济性。
03
3tofd在铁路行业的应用
铁路行业概况
1
铁路运输是我国重要的交通方式,具有大运量 、高速度、安全可靠等特点。
2
铁路行业涵盖了铁路建设、运营、管理等多个 环节,是一个庞大且复杂的系统。
3
我国铁路发展迅速,路网规模和技术水平已居 世界前列。
3tofd在铁路行业的应用范围
3tofd在铁路行业的应用主要涉及以下几个方面
线路检测:检测铁路线路的几何尺寸、表面缺陷等, 保障行车安全和线路畅通。
设备检测:对铁路设备进行实时监测、诊断和检测, 确保其安全、稳定运行。
安全检测:对铁路安全设施进行检测,如护栏、标线 、信号灯等,确保其功能完好。
06
3tofd技术前景展望
3tofd技术未来发展方向
提升检测精度
通过研发更高效的信号处理算法和更精确的检测技术,提高3tofd技术的检测精度。
内检测技术对城市高压燃气管道设计的要求

第 28卷 第 8期
煤 气 与 热 力
a.尢 缺 陷 工 件
b.有 缺 陷 32_件
图 1 漏 磁 检 测 原 理
的储 存设备 中。当检测 装置经 过缺 陷或其他 特征 物 (如 螺旋焊缝 、连接 焊缝 、三 通接 口和 阀 门等 )时 ,会
有漏 磁通 泄漏 出管壁而 被传感器 测得 。测试 系统 工 作 完毕 ,将 其从地 下 管道 中取 出并 将 数 据传 输 到 计 算 机 中 ,然 后对沿 途测得 的数据 进行处 理 和分析 ,可
漏 磁检 测器有标 准 清晰度漏 磁检测 器 和高清 晰
度漏磁 检测器 ,其性 能指标 见表 1。
表 1 漏 磁 检 测 器 的 性 能指 标
性 能 指 标 周 向传 感 器 间距 /mm
标 准 清 晰 度 高 清 晰 度
维普资讯
第 28卷 第 8期 2008年 8月
劫
爨燃气输配与储运甏
%
%
煤 气 与 热 力
GAS & HEAT
V01.28 No.8 Aug. 2008
内检测 技术 对城 市 高压 燃气 管道设 计 的要 求
李 帆 , 翟瑞 隆 , 王 浩 , 洪 险峰
1 概 述 管道 内检测技 术可 以在 保证管 道正 常运行 的状
态下 ,定量检 测 出管 道存 在 的缺 陷。该 技术 的应 用 为管道事故 的预 防和 合 理维 护提 供 了科 学 依 据 ,对 保 证管道 安全运行具 有重要 作用 ¨J。
近年 来 ,管道 内检 测技 术 在油 气 长输管 道检测 领域 广泛应 用 ,也逐 步应用 于城市天 然气高 压管道 。 以往 燃气高 压管道 的设 计 仅 考虑 清 管球 的通 过 ,由 于管 道 内检 测检测 器 的 尺寸 大 于清 管球 ,造 成 在役 燃气 高压管 道需做相 应 的改 造才能适 应检测 器 的通 过。 因此 ,有 必要对 各 种 检测 精 度下 不 同管 径 的燃 气 高压管道 和管件 设 计作 出规定 ,以适 应今 后 管 道 内检测 的需 要 。 2 漏磁 检 测 器原 理及 结构
三期现场机械检查内容格试

三期现场机械检查内容格试经过大量的实验和研究,科学家们已经研发出了称为“三期现场机械检查内容格试”的新型技术。
这套技术能够让机械检查的结果更准确,更快速地了解机器的状态,从而帮助企业提升生产维护效率,大大提高企业的整体效益。
三期现场机械检查内容格试是一种使用计算机自动分类和判断机器状态的技术,它融合了物理、电子、控制、机械、自动化等先进技术,能够深入分析出机器的实时状态。
三期现场机械检查实际上是一种有效的技术,它能够有效地提供量化的数据,从而使企业更加容易做出决策。
三期现场机械检查内容格试的具体内容包括:1.设备的全面安装检查:要避免漏洞、错误、损坏等情况,确保设备安装正确;2.机器操作安全检查:检查有无安全问题,要确保机器操作过程中不会出现意外;3.仪表参数校准检查:根据实际情况,操作仪表参数的校准,确保机器的输出能够满足预期的要求;4.定期维护检查:仔细检查机器的调校情况,定期更换机器部件以确保机器的稳定工作;5.电气系统检查:检查机器的电气系统是否正常,提供完整的电气系统测试报告;6.备件库存检查:检查各类备件库存是否充足,根据实际需求补充备件;7.故障维修检查:及时发现机器故障,根据故障情况提供快速的维修服务。
以上是三期现场机械检查内容格试的具体内容,企业实施起来,能够极大地提升企业的维护效率,降低企业生产维护成本,提高企业的整体效益。
因此,企业应当积极采用这项新型技术,充分发挥它的作用,达到实现企业经济效益的目标。
大量的证据表明,三期现场机械检查内容格试能够更有效地解决企业面临的机械设备维护问题,比传统的技术更加可靠、实用。
除了可以准确识别故障的种类、部位、原因,它还拥有直观的人机交互界面,使得机械检查更加容易。
此外,三期现场机械检查内容格试能够根据不同的检查结果,快速提供生产运行的报告。
总之,三期现场机械检查内容格试不仅能够有效地检测机械系统的状况,还能够根据实时的数据快速提供可靠的报告,大大降低了企业生产维护的成本。
内检测技术在城市燃气管道的应用

内检测技术在城市燃气管道的应用摘要:燃气作为人们日常生活的重要资源之一,决定着人们生活的水平与质量。
而由于燃气大多是通过金属管道进行输配送,随着使用时间的延长,金属管道极易受到不良因素影响而产生腐蚀、损坏等现象,导致燃气出现泄漏,由此而造成大量经济损失,甚至还会出现一些安全事故问题。
为此,在日常工作中,燃气部门需要定期组织专业人员,借助内检测等技术方式,结合现代化设备设施,对城市燃气管道进行检测,将检测结果进行收集分析,如果出现管道损坏问题时,需要及时组织人员进行修补,避免对人们日常生活及社会整体运转发展造成影响。
关键词:内检测技术;城市燃气管道引言:燃气管道作为城市运转的重要环节,对人们日常生活水平有着极大地影响,为此,在日常工作中,有关部门需要提高对燃气管道管理维护工作的重视,积极引用内检测等现代化技术,如果发现部分燃气管道存在堵塞、破损等问题时,需要及时组织技术与维修人员进行处理,以此来保障城市正常稳定的运转与发展下去。
一、内检测技术应用于城市燃气管道的主要原理通常情况下,所谓管道内检测主要是借助检测器等设备设施的应用,利用管道内存在的介质在检测器前后所产生的压差,对检测器进行推动,使其保持前进运动,并在向前运动的过程中,对内部状况及管道自身变形、腐蚀及寒风损伤等方面的信息进行收集,便于工作人员直观了解管道自身的具体状况。
此外,当管道内部由于腐蚀等作用的影响并产生杂质沉积等现象时,工作人员可以实现在检测器外部表装配一定的清洁器具,对管壁进行刮削处理[1]。
二、燃气管道应用内检测技术的必要性在燃气管道设计施工及运转时,其主要以金属材料制成,随着使用时间的延长,再加之管道周边环境等因素的影响,极易出现腐蚀、损坏等问题,且部分管道焊缝极易受到不良因素影响而出现损坏,降低管道整体的密封性,增加了燃气泄漏问题出现的概率。
为此,燃气部门需要组织专业人员,借助内检测等现代先进技术与设备设施的应用,对燃气管道进行内检测,充分了解燃气管道内部腐蚀、损坏的具体状况,如果存在质量与安全隐患时,则需要组织技术人员进行专业的维修处理,在最大程度上降低燃气管道事故问题出现的概率。
- 1、下载文档前请自行甄别文档内容的完整性,平台不提供额外的编辑、内容补充、找答案等附加服务。
- 2、"仅部分预览"的文档,不可在线预览部分如存在完整性等问题,可反馈申请退款(可完整预览的文档不适用该条件!)。
- 3、如文档侵犯您的权益,请联系客服反馈,我们会尽快为您处理(人工客服工作时间:9:00-18:30)。
花格线
秦京线 陕京输气管道 西气东输 中石化鲁宁
5
检测工具
• 自六十年代以来,经历了数代技术改造,形成了 四类特定功能的管道内检测装置:
–金属损失——腐蚀缺陷等 –裂纹——应力腐蚀裂纹等 –几何——管壁凹陷、压扁 –测绘——路径
6
(1)金属损失检测
MFL技术——漏磁通量泄漏检测技术
–为不在原始设计/建设的详细说明范围内的区域提供参
考。
23
存在问题
• 所有的内检测器对于缺陷的探测、描述、定位及确定大小 的可靠性仍不稳定; • 检测器的工作环境极其苛刻(高压、低/高温),检测器 不可避免地由于运行速率、杂质等引起检测结果偏差或设 备损坏; • 分析检测结果的方法不一致。 • 完成检测是一个多步骤的过程,取决于算法与判读人员的 经验。 • 目前还没有针对如何诊断、分析、识别三维缺陷大小的推 荐做法。
• 某些介质可能损坏检测器(如腐蚀性介质);
• 不充足流;
• 限制正常产品流量;
• 速度调节:加旁通。
29
4、检测方式
• 磁通泄漏测量(MFL)可以在气体管道和液体
管道内进行,但应该考虑产品的组分。
• 超声波探伤(UT)测量:最适合液体管道,在
检测之前应验证检测工具对液体的适配性。
30
• 气体管道,在“段塞”流中工具,应考虑的因
–足够的球筒长度:容纳检测器。
26
管道机械特征——防止损害或堵塞工具
• 内径变化(如变形、凹痕、缩径、单向阀等); • 探针; • 土壤移动的区域; • 管壁厚度(通过厚壁管道比薄壁管道需要更大的压力差);
• 弯头(大多数能够通过3D的弯曲半径);
• 反向弯曲(弯头之间没有直管段)——存在障碍或是卡住 的危险; • 阀门——阀挡板应该尽可能的处于全开位置;
根据超声导波在管壁中的传播特性检测裂纹。
18
• 裂纹缺陷的检测尽管已经成功,但:
–检测灵敏度低;
–数据解释难(大量的假数据显示);
–检测的费用高;
–可靠性有待提高。
• 可靠地检测裂纹仍然具有挑战性。
19
(3)几何检测工具
• 检测凹坑、皱折、椭圆度等几何
缺陷.
• 原理:
–机械测径装置
–电磁
• 管子变形工具
素:
–消除气体圈闭; –支路气体引起的污染; –经过阀门、支管等处液体数量减少;
–控制段塞流的速度。
31
• 管道的几何检测(测径器) • 确保后续工具通过:
–首先运行测径器;
–制定对于测径/弯曲数据的响应计划; –如果有必要,可运行模拟检测工具; –在测径/弯曲检测过程中,使用统一基准。
32
5、清管
• 检测之前应清管;
• 预先评价沉积物的历史数据,如氧化物、尘、
石蜡等;
• 经常清管作业有助于制定检测方案;
• 服务商应提出清管的要求。
33
6、信息收集
• 在初步计划阶段应该复验并识别物理约束;
• 给承包商提供尽可能多的信息; • 和承包商讨论清管的信息; • 对较老的设施,补充现场信息。
34
补充信息
–利用惯性制导提供凹坑或其
他变形的时钟位置
20
几何检测数据
• 局部变形(如凹陷)用内径与名义管径的绝对偏离的百分
比度量;
• 常规的测径器能够用于确定尺寸、壁厚变化以及其他潜在
的变形限制;
• 更多成熟的变形工具可识别最大偏离、周向位置、曲率、 形状、翘曲和褶皱等,具有提供更精确量化管道变形的能 力。
如果管壁没有缺陷,则磁力线封闭于管
壁之内,均匀分布。如果管内壁或外壁
有缺陷,磁通路变窄,磁力线发生变形,
部分磁力线将穿出管壁产生漏磁。
漏磁检测器的基本原理
7
漏磁检测器结构:
• 驱动节:装有皮碗产生压差推动装置行走和清管工作;
• 测量节:励磁装置和传感器,产生和测量漏磁信号; • 计算机节:是系统的核心,测量过程控制和测量数据的处理与存储;
第三章 油气管道内检测技术
中国石油大学(北京) 帅健 机械与储运工程学院
内容概要
• 内检测工具 • 内检测作业应考虑的因素
2
1、内检测工具介绍
• 20世纪60年代,在美国诞生了 管道内检测器,称Smart Pig & Intelligence Pig,是一种 集成了多种技术的高技术装置。 • 内检测也称为在线检测,内检 测器在管道内由输送介质推动, 在移动过程中检测管壁,不需 要中断管线运行。 • 内检测已经是管道完整性管理 的首要(常规)手段。
24
2、检测作业应考虑的因素
• 不仅要选择合适的检测器,还要评价管道系统本身对 检测作业的适用性。 • 考虑的因素
– 管道特征;
– 介质类型、流量和速度; – 检测方式; – 清管; – 信息收集。
25
(1)管道特征
• 收、发球筒:
–永久性或临时性的均可;
–有效的工作空间:装、卸检测器的作业的空间;
3
必要性
• 政府法规、安全和环境保护要求; • 基线检测和周期性检测
– 基线检测建立管道基本资料
– 周期性检测是对缺陷监控的重要手段
• 为管道安全运行和合理维护提供科学依据。
4
内检测技术在国内的应用
1989年从德国引进第一台φ273、 φ529、 φ720漏磁检测器。
先后检测
鲁宁线 阿塞线
10
漏磁检测技术的特点
优点:
– 应用相对较为简单,对检测环境的要求不高,具有较高的可信度, 而且可兼用于输油和输气管道
缺点:
– 对于很浅、长且宽的金属损失缺陷,难以检测。 – 测试精度与管壁厚有关,厚度越大,精度越低。其使用范围通常 在12mm以下。 – 运行速度影响检测结果的准确性。
11
金属损失检测
超声检测器——超声回波技术,压缩波。
12
超声检测
• 超声检测扫描管道壁厚,可得到缺陷的河床表面, 容许采用先进的缺陷评价方法。
13
金属损失检测
漏磁与超声检测技术比较 • 漏磁检测属于间接测量,对管道介质、环境等因 素要求较超声波方法宽松,目前普遍采用; • 超声检测直接测量管道壁厚,虽然检测结果精确 度较高,但其对管道的清洁度要求较高,同时还 要求有耦合剂,限制了其应用范围。
• 有文献来源的内部考查
– 图纸、测量记录等; – 焊缝总数和接头长度记录; – 购货记录; – 测径器运行记录; – 常规清管器运行结果; – 测量盘运行;
– 第三方施工活动记录
• 实地考察——服务商和运营商实地考察设施 • 以前的检测
35
14
(2)裂纹检测技术
• 裂纹检测仍然是一项挑战性的工作,尝试过用多 种无损检测技术:
– 超声
– 横向漏磁通
– 弹性波 – 超声导波 – 远场涡流
15
超声
• 超声是唯一取得成功的管道裂纹检测技术 • 和检测金属损失不同的是,采用的是45剪切波。
16
弹性波
• 从充满液体的轮子发射超声波
17
EMAT (电磁声能转换装置)
27
管道机械特征
• 场地弯曲和河流穿越处——高土体运动的敏感性; • 内涂层——某些工具对内涂层有所损害; • T型结构——使检测器失速; • 管道上安装的设备:如孔板流量计(气体管线)、压 力罐(原油管线)、y-型分支接头和斜接弯头等;
• 自燃材料——特别是硫化亚铁,应防止火灾。
28
3、介质类型、流量和速度
• 电池节:为检测装置在管道中长时间工作提供充足的电能。
8
金属损失检测
• 漏磁信号与缺陷
9
• 常规分辨率分类检测缺陷; • 高分辨率能进行缺陷几何尺寸的详细鉴别和定位,进行分 类。此外,可以使用更先进的缺陷评价方法; • 横向磁通泄漏(MFL)工具在圆周方向上磁化管道。这类
工具对轴向缺陷较敏感。
21
(4)测绘工具
• 采用精密惯性制导仪器,记录管道极微小的移动;
• 用于测绘管道的纵断面和路径;
• 与GPS联合使用能为地质断层、沉陷区、永冻土地区等提
供优பைடு நூலகம்的监测。
22
测绘工具
• 高精度提供真实空间坐标:
–所有缺陷的坐标; –弯曲应变/曲率;
–绝对弯曲应变;
–监测土体或其它外部因素导致的管线移动;