小车自动往复运动PLC控制系统
组态王监控三菱PLC的小车往复变速运动控制

组态王监控三菱PLC 的小车往复变速运动控制系统设计一、 系统组成由三相异步电机拖动小车在轨道上做往返变速运动,变频器控制电机实现正反转和变频调速。
PLC 接收按钮和小车左右限位开关的信号,控制变频器的工作状态。
用PLC 的编程口和USB-SC-09编程电缆与计算机通信,也可以在PLC 上安装FX2N-232-BD 通信功能板,用232串口线与计算机通讯。
二、 P LC 控制电路三、 在PLC 参数设定和控制程序表1 PLC 的I/O 端口分配输入输出X0 变频器异常保护BC 端 Y0 电机正转STF X1 变频器通电按钮 Y1 电机反转STR X2 变频器断电按钮 Y2 电机低速RL X3 小车停止按钮 Y3 电机中速RM X4 小车右行按钮 Y4 电机高速RH X5 小车左行按钮 Y10 变频器通电KM X6 小车加速按钮 X7 小车减速按钮 X10 小车左边限位开关 运行组态王监控程序L1L2L3表2 电机转速设定电机转速档PLC端口Y4 Y3 Y2变频器端口RH RM RL变频器参数设定1档001 OFF OFF ON Pr.06=10(10Hz)2档010 OFF ON OFF Pr.05=20(20Hz)3档011 OFF ON ON Pr.24=30(30Hz)4档100 ON OFF OFF Pr.04=40(40Hz)5档101 ON OFF ON Pr.25=50(50Hz)6档110 ON ON OFF Pr.26=60(60Hz)7档111 ON ON ON Pr.27=70(70Hz)在GXDeveloper或GXworks2编程软件中设置PLC通信参数:也可以在梯形图程序中初始化PLC通信参数:PLC控制程序:四、 组态王监控系统1、画面设计2、设备和通信设置用USB-SC-09编程电缆把PLC和电脑连接起来,PLC接通电源,安装USB-SC-09驱动程序后。
打开设备管理器,找到“Prolific USB-to-Serial Comm Port(COM3)”端口,然后双击该项弹出端口设置对话框,进行通信设置。
小车自动往返控制PLC课程设计

小车自动往返控制PLC课程设计一、课程目标知识目标:1. 学生能理解PLC(可编程逻辑控制器)的基本原理和结构,掌握其在小车自动往返控制系统中的应用。
2. 学生能掌握基本的逻辑控制语句和程序设计方法,实现对小车的自动往返控制。
3. 学生能了解传感器的工作原理,并将其应用于PLC控制系统中,实现小车行进中的障碍物检测和避让。
技能目标:1. 学生能运用PLC编程软件进行程序设计,实现小车自动往返控制的功能。
2. 学生能通过实际操作,调试和优化PLC控制程序,提高小车的运行效率和稳定性。
3. 学生能运用相关工具和仪器进行电路搭建和故障排查,培养实际操作能力和问题解决能力。
情感态度价值观目标:1. 学生通过课程学习,培养对自动化技术和PLC控制系统的兴趣,激发创新意识和探索精神。
2. 学生在小组合作中,学会沟通与协作,培养团队精神和责任感。
3. 学生能够关注PLC技术在工业生产和日常生活中的应用,认识到科技对社会发展的推动作用,树立正确的价值观。
课程性质:本课程为实践性较强的课程,注重理论知识与实际操作的结合,培养学生动手能力和创新能力。
学生特点:学生为高年级学生,具备一定的电子技术基础和编程能力,对新技术和新知识有较高的学习热情。
教学要求:教师需结合学生特点,采用任务驱动法、案例教学法和小组合作法等教学方法,引导学生主动探索,提高课程教学效果。
同时,注重过程评价,关注学生知识掌握和技能提升,培养其情感态度价值观。
通过分解课程目标为具体学习成果,便于后续教学设计和评估。
二、教学内容1. PLC基础知识:包括PLC的组成、工作原理、编程语言及编程软件的使用,重点讲解与小车自动往返控制相关的基础知识。
- 教材章节:第一章 PLC概述,第二章 PLC组成与工作原理,第三章 编程语言与编程软件。
2. 逻辑控制语句:介绍PLC常用的逻辑控制语句,如与、或、非、定时器、计数器等,通过实例分析,让学生掌握逻辑控制语句的应用。
plc小车自动往返毕业设计

plc小车自动往返毕业设计
PLC小车自动往返毕业设计可以按照以下步骤进行:
1. 确定设计要求:确定PLC小车自动往返的具体功能和要求,包括小车的移动方式、起止点、速度控制、停顿时间等。
2. 系统设计:设计整个系统的硬件部分,包括PLC控制器、
电机驱动、传感器以及其他必要的电路和接口。
3. 程序设计:编写PLC控制程序,实现小车自动往返的逻辑
控制,包括起动、停止、方向控制以及速度控制等。
4. 系统调试:将硬件部分和程序部分进行整合,测试系统的正常运行,调试可能出现的问题,确保系统稳定可靠。
5. 性能优化:通过调整程序和参数,对系统进行优化,提高小车的移动速度、精度和稳定性。
6. 结果评估:对设计的系统进行评估和测试,检查是否符合设计要求和预期效果,并进行必要的改进和调整。
7. 文档撰写:撰写毕业设计报告,详细记录设计的整个过程,包括设计原理、实施步骤、测试结果和分析等。
8. 学术交流:参加学术交流活动,向其他同行和专业人士展示设计成果,并从他们的反馈中得到进一步改进的建议。
以上步骤只是一个大致的指导,在具体实施过程中可能还会根据具体情况进行一些调整和改变。
同时,也需要注意安全问题,确保设计和实施过程中不会造成任何人身伤害或设备损坏。
基于西门子S7—200PLC的小车自动往返运动系统分析

基于西门子S7—200PLC的小车自动往返运动系统分析在日常生活中的生产车间由于工作台的面积有限,这就要求有一运料的小车能及时的将成品运到指定的成品車间,由于操作工人对工作的熟练程度不同等原因,将会使工作台上的成品数量不同,这就要求操作工根据自己的需要及时呼来装料小车将成品运走。
小车需要将每个工作台上的成品都及时运走,这就要求小车在每个工作台的限时限量的装货。
但由于每个工作台的呼叫都是随机的,因此,小车运行及停靠应该是根据工作台的呼叫而决定的,而不是按预先设定的顺序依次运行,这样就提高了小车的效率。
实现了一定的车间智能化,提高了系统的可靠性,节约了一定的人力资源。
标签:自动往返限时限量控制程序一、控制任务及要求1.每个工作台都有一个呼叫按扭。
当需要小车过来装袋时,按一下按扭,系统接到呼叫信号就登记下来,同时通过点亮记忆灯来表示呼叫信号已接到。
智能运料小车就会通过程序判断自己的闲忙程度来确定到来的具体时间。
原则是谁先登记先接谁,不能截车。
2.封装打包时有以下基本要求。
每次最多装20袋,每次最多停留10秒,如果不到10秒种就把20袋都装完了,这时如果有其他工作呼叫,我们就控制小车运行。
如用尽10秒时间到小车仍然装不到20袋。
此时如果出现或者早已有呼叫信号,小车也会立即运行离开。
3.如果20袋货物已经装完了,等待10秒钟的时间也到了,此时如果没有其他的工作台呼叫小车,本个工作台可以继续装运货物,注意一旦有其他的工作台呼叫小车,小车立运行到达呼叫的工作台。
4.本系统增加数码指示,可以实时监测用数码管显示小车的停止位置。
5.呼叫信号要遵从先呼先去原则。
不能顺向截车,只要车上的货物达到60袋,小车此时直接到达卸料区,不再响应其他工作台的呼叫,但是小车要存储他们的呼叫顺序直到小车卸完料后再按顺序工作装料。
6.本系统设有一个启动按钮,一个停止按钮。
7.工作台和工作台之间的距离通过旋转编码器测量小车运行距离。
设定每4个工作台加一个成品装卸库。
小车自动往复运动PLC控制系统

小车自动往复运动PLC控制系统简介自动化控制系统是现代工业生产的重要组成部分,在许多工业领域中有着广泛应用,其中PLC控制系统是其中的重要一员。
本文将介绍PLC控制系统在小车自动往复运动控制中的应用和实现方法。
PLC控制系统PLC即可编程逻辑控制器,它是一种数字化电子设备,主要用于工业自动化控制领域。
PLC控制系统由CPU、输入输出模块、程序存储器、数据存储器、通信模块等组成。
其主要功能是将输入的各种信号经过处理后控制输出信号控制继电器或执行器的工作。
控制系统设计概述在本文中,我们需要设计一个小车自动往复运动的控制系统。
首先我们需要定义控制系统的输入、输出以及控制目的:输入1.感应开关:用来检测小车到达终点位置的开关。
2.按钮:用来手动启动和停止小车。
3.限位开关:用来检测小车是否到达起始位置的开关。
输出1.电机:用来驱动小车运动。
2.灯:用来指示小车当前的运动状态。
控制目的设计一个控制系统,使小车能够自动往复地进行运动。
当小车到达终点位置时,控制系统需要自动将电机反向,使小车回到起始位置。
当按下按钮时,控制系统需要立即停止电机的运动。
程序设计下面是控制系统的程序设计流程,在编写程序之前,需要对控制系统的性能、特点和需求有一个深入的了解。
开发PLC程序1.定义输入输出口:// 定义输入口I:1.0I:1.1I:1.2// 定义输出口Q:1.0Q:1.12.编写PLC程序:LD I:1.0// 检测限位开关,判断小车是否在起始位置OUT Q:1.0// 驱动电机运动LD I:1.1// 检测感应开关,判断小车是否到达终点位置LDN I:1.2// 检测按钮是否按下AND I:1.0,I:1.1// 如果小车在起始位置并且到达了终点位置,转向运动OR N I:1.2// 如果按钮按下,即时停止电机运动OUT Q:1.1// 控制灯的亮灭JMP M100 // 重新执行程序设计控制器将输入输出口与PLC程序进行连接,并设置运行模式,测试程序是否正常。
基于PLC的小车自动往返运动控制系统2
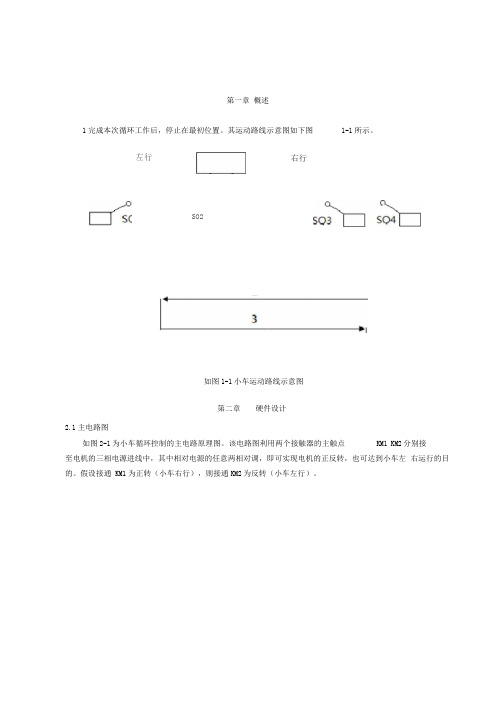
第一章概述1完成本次循环工作后,停止在最初位置。
其运动路线示意图如下图如图1-1小车运动路线示意图2.1主电路图如图2-1为小车循环控制的主电路原理图。
该电路图利用两个接触器的主触点KM1 KM2分别接至电机的三相电源进线中,其中相对电源的任意两相对调,即可实现电机的正反转,也可达到小车左右运行的目的。
假设接通KM1为正转(小车右行),则接通KM2为反转(小车左行)。
左行右行SO21-1所示。
第二章硬件设计图2-1小车循环控制的主电路原理2.2 I/O 地址分配如表2-1为小车循环运动 PLC 控制的I/O 分配表。
在运行过程中,这些 I/O 口分别起到了控制 各阶段的输入和输岀的作用,并且也使小车的控制过程更清晰明了,动作与结果显示更加方便直接。
KM 32.3I/O 接线图如图2-2为小车循环运动PLC控制的I/O接线图。
在进行调试过程时,在PLC模块上,当I0.0有输入信号,即按下SQ1;当I0.1有输入信号,也即按下SQ2以此类推,I/O接线图就是把实际的开关信号变成调试时的输入信号。
同理,输出信号也是利用PLC模块把小车的实际运动用Q0.0、Q0.1的状态表现岀来。
图2-2小车循环运动PLC控制的I/O接线图2.4元件列表如表2-2为小车循环运动PLC控制的元件列表。
在本次设计中就是利用这些元件,用若干导线连接起来组成了我们需要的原理图、I/O接线图。
3.1程序流程图如图3-1为小车循环运动PLC控制的程序流程图。
小车在一个周期内的运动由4段组成。
设小车最初在左端,当按下启动按钮,则小车自动循环地工作,若按下停止按钮,则小车完成本次循环工作后,停止在最初位置。
首先小车位于初始位置,按下SB1启动后,小车向右行驶;当碰到行程开关SQ4小车转向,向左行驶;碰到行程开关SQ2小车再一次转向,向右行驶;碰到行程开关SQ3,小车又向左行驶,直到再次碰到SQ1,然后开始依次循环以上过程。
若不按下停止按钮SB2则小车一直进行循环运动,若此时按下停止按钮SB2小车又碰到行程开关SQ1,则小车回到初始位置。
小车自动往返PLC控制系统程序设计与调试.

小车自动往返PLC 控制系统程序设计与调试小车自动往返PLC 控制系统电气原理图,如图1-2-41所示。
小车自动往返PLC 控制系统梯形图程序,如图1-2-42所示。
KM1KM2Q0.0Q0.11LFU4220V ACSB2SB3SQ4SQ3SQ2SQ11M L1N FRFU3I0.0I0.1I0.2I0.3I0.4I0.5220V ACFU2FR1KM1FU1M 3~QS1L3L2L1U11V11W11W12V12U12W13V13U13U V WKM2PETKM2KM1SB1I0.6图1-2-41 小车自动往返PLC 控制系统电气原理图2.系统调试(1)在教师现场监护下进行通电调试,将程序写入PLC ,验证系统功能是否符合控制要求。
(2)如果出现故障,学生应独立检修。
线路检修完毕和梯形图修改完毕应重新调试,直至系统正常工作。
3.工艺要求(1)熟悉所用电器元件的作用和控制线路的工作原理。
列出I/O 分配表,配齐所有电器元件,并检查质量。
(2)绘制元件布置图,经教师检查合格后,在控制板上安装电器元件。
电器安装应牢固,并符合工艺要求。
(3)线路安装应遵循由内到外、横平竖直的原则;尽量做到合理布线、就近走线;编码正确、齐全;接线可靠,不松动、不压皮、不反圈、不损伤线芯。
(4)安装完毕进行自检,该过程学生可使用万用表来检查线路。
要求确保无误后才允许通电调试。
图1-2-42 小车自动往返PLC 控制系统梯形图程序。
送料小车自动往返的PLC控制
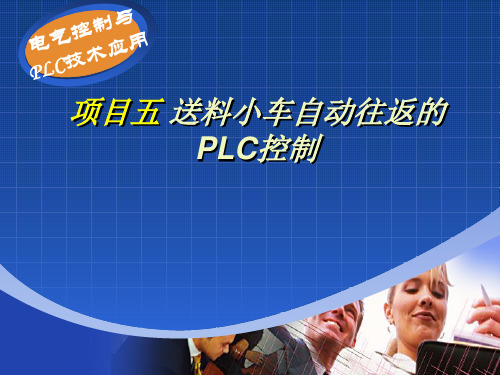
2
编址方式
Company Logo
高位 按位寻址 V0.2
7
高位 按字节寻址 VB0
7
高位
按字寻址 VW0
VB0
15
高位
按双字寻址 VD0
VB0
31
低位
V0.2
0
位号
字节号
区域号
低位
VB0 0
字节号
字节寻址标志字母 区域号
低位
VB1
VW0
0
字节号 字寻址标志字母 区域号
VB1
VB2
VB3
VD0
字节号 双字寻址标志字母 区域号
❖ 3. 热电偶、热电阻扩展模块
❖ 4. PROFIBUS-DP通信模块
5.5 S7-200 PLC内部器件
Company Logo
31
PLC数据类型
2
编址方式
3
寻址方式
4
元件功能及地址分配
31
PLC数据类型
Company Logo
❖ 最基本的存储单位是位(bit),8位二进制数组成1个 字节(Byte),其中的第0位为最低位(LSB),第7位为 最高位(MSB)。两个字节(16位)组成1个字(Word), 两个字(32位)组成1个双字(Double word)。把位、 字节、字和双字占用的连续位数称为长度。
❖ 中型PLC的I/O点数在256~1024之间, 功能比较丰富,兼有开关量和模拟量的控制 能力,适用于较复杂系统的逻辑控制和闭环 过程的控制。
❖ 大型PLC的I/O点数在1024点以上。用于 大规模过程控制,集散式控制和工厂自动化 网络。
5.4 西门子S7-200 PLC识别与检测
Company Logo
自动往返小车控制系统plc

自动往返小车控制系统-plc中州大学毕业设计学号: 201025090206 设计题目:自动往返小汽车的控制系统的设计学院:工程技术学院专业:机电一体化班级: 10级对口2班姓名:杨丽丽指导教师:上官同英日期: 2013 年 3 月 5 日诚信声明本人郑重声明:所提交的毕业设计(论文)是本人在指导教师的指导下,独立工作所取得的成果并撰写完成的,郑重确认没有剽窃、抄袭等违反学术道德、学术规范的侵权行为。
文中除已经标注引用的内容外,不包含其他人或集体已经发表或撰写过的研究成果。
对本文的研究做出重要贡献的个人和集体,均已在文中作了明确的说明并表示了谢意。
本人完全意识到本声明的法律后果由本人承担。
毕业设计(论文)作者签名:指导导师签名:签字日期:签字日期:毕业设计任务书班级: 10机电对口2班学生:杨丽丽学号 201025090206设计题目:自动往返小汽车的控制系统的设计摘要:设计一个能自动往返于起跑线与终点线之间的小汽车的控制系统。
但不能用人工遥控(包括有线和无线)。
跑道宽度0.5m,表面贴有白纸,两侧有挡板,挡板与地面垂直,其高度不低于20cm。
在跑道的A、B、C、D各点处画有2cm宽的黑线,各段的长度与下图所示:设计内容及要求:1.设计完成的功能要求:1)、车辆从起跑线出发(出发前,车体不得超出起跑线),到达终点线后停留10秒,然后自动返回起跑线(允许倒车返回)。
2)、BC间为限速区,车辆往返均要求低速通过,但不允许在限速区内停车。
3)、在往返过程中随时显示当前行车时间和路程,直接回到终点。
(显示装置应安装在小车上面。
)2.设计内容要求(1)根据设计要求确定系统中输入/输出信号的种类、数量和特点。
(2)确定CPU的选型与硬件接口等的配置。
(3)进行硬件设计,主要是整个系统的电路原理图的绘制。
(4)进行软件设计,根据控制要求编写控制系统的控制程序和监控程序。
(5)撰写毕业设计说明书。
3. 设计说明书的要求:1)、分析控制要求、控制对象,确定控制方案;3)、根据控制要求选择单片机及相关控制元件的型号;3)、画出该控制系统的总体硬件原理图;4)、画出程序流程图;5)、源程序清单,并加注释; 6)、其它按照毕业设计指导所述要求。
小车自动往复运动PLC控制系统

目录第1章课程设计的方案 (1)1.1 PLC运料小车的基本介绍 (1)第2章运料小车控制系统 (2)2.1 系统的运行方式 (2)2.2控制系统的方案设计 (2)第3章控制系统硬件结构设计 (3)3.1系统的基本硬件结构组成 (3)3.2硬件结构框图 (3)3.3小车的控制主电路 (4)3.4 PLC接线图及说明............................. 错误!未定义书签。
第4章控制系统软件结构设计 (5)4.1软件设计流程图及思路 (5)4.2 I/O地址分配 (9)4.3梯形图及功能说明 (10)第5章课程设计总结 (16)参考文献 (17)第1章课程设计的方案1.1 PLC运料小车的基本介绍工厂运输现大多采用地面运输,地面运输主要采用叉车及手推运料小车,叉车需专人驾驶且无固定轨道,在车间内运行极不安全,手推运料小车需人为动力,劳动强度大,运输效率低。
随着经济的发展,运料小车不断扩大到工业运输的各个领域,从手动到自动,逐渐形成了机械化、自动化。
早期运料小车电气控制系统多为继电器-接触器组成的复杂系统,这种系统存在设计周期长、体积大、成本高等缺陷,几乎无数据处理和通信功能,必须有专人负责操作。
后来,单片机应用到运料小车控制系统中。
但是单片机开发周期长,使用难,开发成本高,批量成本低,对人要求高,而且其稳定性不够高。
由于PLC 开发周期短,使用容易,开发成本低,批量成本高,对操作人员技术要求要求不高,并且稳定性好,抗干扰能力强,使得对基于PLC的运料小车控制系统的开发研究逐步加强。
PLC(Programmable Logical Controller)是20世纪70年代以来以微处理器为核心,综合计算机技术、自动控制技术和通信技术发展起来的一种新型工业自动控制装置。
由于它具有功能强、可靠性高、配置灵活、使用方便以及体积小、重量轻等优点,使其在自动化控制的各个领域中得到了广泛的应用。
基于PLC的小车自动往返控制系统设计

基于PLC的小车自动往返控制系统设计针对当前小车在运动过程中控制精度低、自动化水平低等问题,论文以自动往返运动小车为研究对象,在分析了可编程逻辑器特点的基础之上,开展了基于PLC的小车自动往返控制系统的硬件设计、软件设计,最后对进行了总结,为自动往返小车的运行提供了一种可行方案。
标签:PLC,控制系统,小车1. 引言在实际工业生产过程中,运动小车的控制技术水平不仅影响生产成本,同时严重制约着生产效率及产品质量。
在影响产品质量的因素中,除材质等因素外,运动小车的自动化程度也是其中之一。
早期的小车控制技术,大多都是接触器、继电器、形成开关等元器件,这些元器件组成的系统的控制精度不高,再加上人为因素增大了其随意性、降低了运动精度等。
随着控制技术的发展,再加上人们对小车自动化控制的要求越来越高,相应的控制技术也逐步被应用。
可编程逻辑控制器凭借自身精度高、稳定性好、编程容易等独特优势,已逐步取代传动的电路控制,成为控制技术领域的主流产品。
基于当前市场背景,研发一套实用意义强的小车自动往返控制系统势在必行。
2.系统方案设计2.1 plc控制技术的概述。
可编程逻辑控制器作为人类社会发展过程中一项重要发明,从第一台PLC 控制器问世至今,已被应用于各行各业,尤其是近些年来,伴随着先进技术的不断涌现及编程软件的不断优化,编程方式越来越容易,控制成本越来越低,plc 控制技术应用也越来越广泛。
2.1.1 PLC控制技术的特点。
可编程逻辑控制控制技术作为一种目前应用最广的控制技术,相比其他控制技术,可编程逻辑控制技术有其独特的优势,具体如下:2.1.3 控制系统的总体方案设计。
通过对自动往返小车控制系统工艺流程和结构特点的分析,依据实际控制需求,该控制系统可分为过程控制和直接控制。
基于以上所述,该自动往返小车的控制系统方案如图所示。
其中可编程逻辑控制器为该系统的核心,直接通过导线连接完成与相关设备的对话。
3控制系统硬件设计3.1.2 plc类型的选择与应用.基于本课题的控制对象,用于该控制系统的可编程逻辑控制器要具有一定数字量的输入输出能力,方能满足该课题控制要求,具体功能如下:(1)数字量输出点:通过控制KM1及KM2的线圈,来实现三相异步电动机的正反转,该控制共需要2个数字输出点。
0203 小车自动往复运行控制程序设计

任务分析
任务分析
说明 PLC软元件
X0
输入
X1
X2
X3
Y0 输出
Y1
元件文字符号 SB1 SB2 SQ1 SQ2
元件名称 启动按钮 停止按钮 行程开关 行程开关
KM1
右行接触器
KM2
左行接触器
控制功能 启动控制 停止控制 A点位置检测 B点位置检测 正转接通或分
断电源 反转接通或分
断电源
知识储备
《PLC应用技术》
电动机控制程序设计
小车自动往复运行控制程序设计
布置任务
小车自动往复运行控制 程序设计
当按下启动按钮时,小车从A点出发向B点运行。 当小车运行到B点,小车立即从B点向A点运行。 依照此过程,小车在A、B两点之间往复运行。当 按下停止按钮时,小车停止运行。当再次按下启 动按钮时,小车能按照停止前的原方向重新运行。
当小车行驶到B限位点时, 由于B点行程开关动作,使 得X3常闭触点断开,M0线 圈和Y0线圈相继失电,小车 右行停止。同时,M1线圈 得电并自锁,M1常开触点 闭合,M1触点驱动Y1线圈 得电,小车开始向左行驶。
当小车行驶到A限位点时,由于B点行程 开关动作,使得X2常闭触点断开,M1线 圈和Y1线圈相继失电,小车右行停止。 同时,M0线圈得电并自锁,M0常开触点 闭合,M0触点驱动Y0线圈得电,小车再 次向右行驶。
任务实施
› (2)用触点比较指令编写的控制程序
当小车行驶到A限位点时,由于A点行 程开关动作,使得X2常闭触点断开, M1线圈和Y1线圈相继失电,小车右 行停止。同时,M0线圈得电并自锁, M0常开触点闭合,M0触点驱动Y0线 圈得电,小车再次向右行驶。 按下停止按钮,小车停止运行。当再 次按下启动按钮时, PLC执行[= C0 K1]指令,如果(C0)=1,则小车再 次向右行驶;PLC执行[= C1 K1]指 令,如果(C1)=1,则小车再次向左 行驶。
小车自动往复运动PLC控制系统
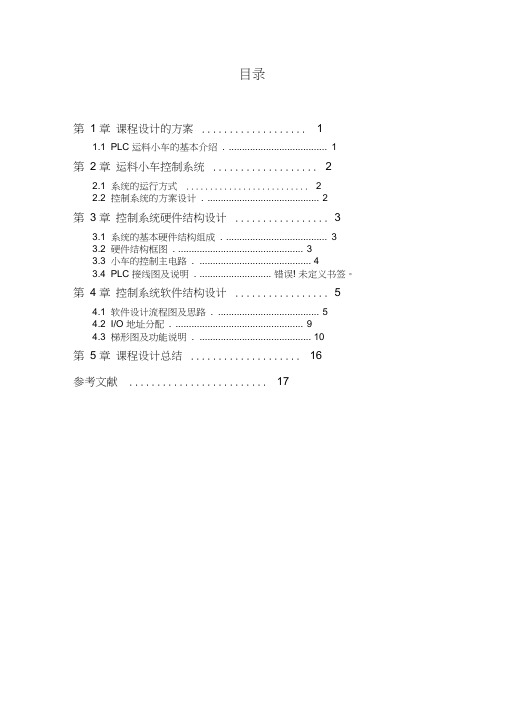
目录第 1 章课程设计的方案 (1)1.1 PLC 运料小车的基本介绍. (1)第 2 章运料小车控制系统 (2)2.1 系统的运行方式 (2)2.2 控制系统的方案设计. (2)第 3 章控制系统硬件结构设计 (3)3.1 系统的基本硬件结构组成. (3)3.2 硬件结构框图. (3)3.3 小车的控制主电路. (4)3.4 PLC 接线图及说明. ........................... 错误! 未定义书签。
第 4 章控制系统软件结构设计.. (5)4.1 软件设计流程图及思路. (5)4.2 I/O 地址分配. (9)4.3 梯形图及功能说明. (10)第 5 章课程设计总结 (16)参考文献 (17)第 1 章课程设计的方案1.1 PLC 运料小车的基本介绍工厂运输现大多采用地面运输,地面运输主要采用叉车及手推运料小车,叉车需专人驾驶且无固定轨道,在车间内运行极不安全,手推运料小车需人为动力,劳动强度大,运输效率低。
随着经济的发展,运料小车不断扩大到工业运输的各个领域,从手动到自动,逐渐形成了机械化、自动化。
早期运料小车电气控制系统多为继电器- 接触器组成的复杂系统,这种系统存在设计周期长、体积大、成本高等缺陷,几乎无数据处理和通信功能,必须有专人负责操作。
后来,单片机应用到运料小车控制系统中。
但是单片机开发周期长,使用难,开发成本高,批量成本低,对人要求高,而且其稳定性不够高。
由于PLC 开发周期短,使用容易,开发成本低,批量成本高,对操作人员技术要求要求不高,并且稳定性好, 抗干扰能力强,使得对基于PLC的运料小车控制系统的开发研究逐步加强。
PLC(Programmable Logical Controller) 是20世纪70 年代以来以微处理器为核心,综合计算机技术、自动控制技术和通信技术发展起来的一种新型工业自动控制装置。
由于它具有功能强、可靠性高、配置灵活、使用方便以及体积小、重量轻等优点,使其在自动化控制的各个领域中得到了广泛的应用。
基于PLC的小车循环运动控制系统的设计
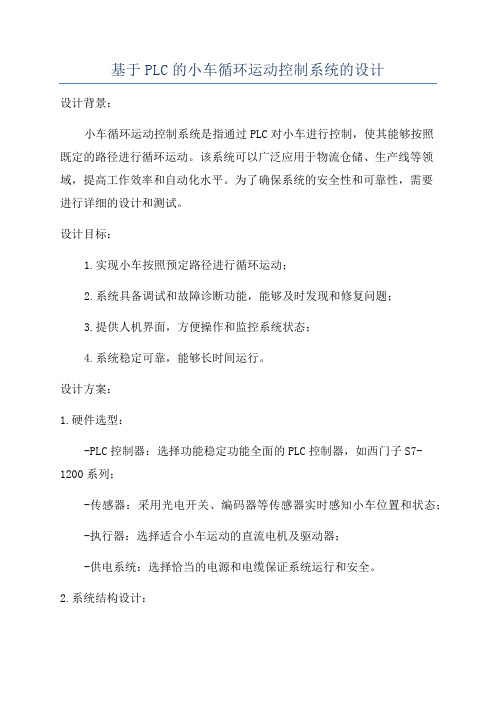
基于PLC的小车循环运动控制系统的设计设计背景:小车循环运动控制系统是指通过PLC对小车进行控制,使其能够按照既定的路径进行循环运动。
该系统可以广泛应用于物流仓储、生产线等领域,提高工作效率和自动化水平。
为了确保系统的安全性和可靠性,需要进行详细的设计和测试。
设计目标:1.实现小车按照预定路径进行循环运动;2.系统具备调试和故障诊断功能,能够及时发现和修复问题;3.提供人机界面,方便操作和监控系统状态;4.系统稳定可靠,能够长时间运行。
设计方案:1.硬件选型:-PLC控制器:选择功能稳定功能全面的PLC控制器,如西门子S7-1200系列;-传感器:采用光电开关、编码器等传感器实时感知小车位置和状态;-执行器:选择适合小车运动的直流电机及驱动器;-供电系统:选择恰当的电源和电缆保证系统运行和安全。
2.系统结构设计:-PLC控制器:负责接收和处理传感器信号,并通过控制程序实现小车的控制;-输入模块:接收传感器信号,并将其转化为PLC可识别的数据;-输出模块:控制执行器的运动方向和速度;-人机界面:通过HMI人机界面实现操作和监控系统状态。
3.系统控制程序设计:-设计小车的运动路径,确定循环运动的起点和终点;-通过编程软件编写控制程序,包括传感器数据采集、运动控制、故障监测和处理等功能;-确定小车的控制方式,可以选择位置控制、速度控制或者PID控制;-根据系统需求和硬件特性进行调试和优化,确保系统的稳定性和准确性。
4.人机界面设计:-使用HMI设计软件进行界面设计,包括控制面板和状态监控界面;-提供启动、停止、重置等操作按钮,方便操作和控制小车;-实时显示小车的位置、速度和状态,以及故障信息和警报提示;-实现数据记录和报表生成,便于数据分析和系统优化。
5.系统测试和调试:-进行硬件连接和调试,确保传感器、执行器等设备正常工作;-编写和调试控制程序,验证小车的循环运动功能;-模拟故障情况,测试系统的故障检测和处理能力;-根据实际情况进行系统优化和调整,确保系统的稳定性和可靠性。
小车往复运动PLC自动控制说明书.doc
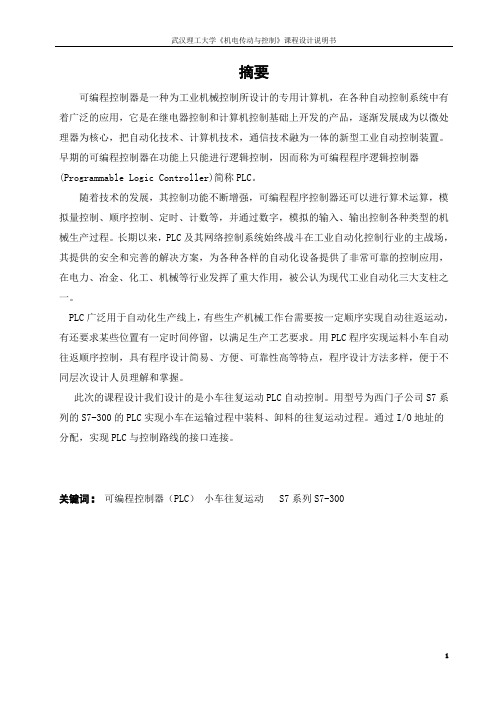
可编程控制器是一种为工业机械控制所设计的专用计算机,在各种自动控制系统中有着广泛的应用,它是在继电器控制和计算机控制基础上开发的产品,逐渐发展成为以微处理器为核心,把自动化技术、计算机技术,通信技术融为一体的新型工业自动控制装置。
早期的可编程控制器在功能上只能进行逻辑控制,因而称为可编程程序逻辑控制器(Programmable Logic Controller)简称PLC。
随着技术的发展,其控制功能不断增强,可编程程序控制器还可以进行算术运算,模拟量控制、顺序控制、定时、计数等,并通过数字,模拟的输入、输出控制各种类型的机械生产过程。
长期以来,PLC及其网络控制系统始终战斗在工业自动化控制行业的主战场,其提供的安全和完善的解决方案,为各种各样的自动化设备提供了非常可靠的控制应用,在电力、冶金、化工、机械等行业发挥了重大作用,被公认为现代工业自动化三大支柱之一。
PLC广泛用于自动化生产线上,有些生产机械工作台需要按一定顺序实现自动往返运动,有还要求某些位置有一定时间停留,以满足生产工艺要求。
用PLC程序实现运料小车自动往返顺序控制,具有程序设计简易、方便、可靠性高等特点,程序设计方法多样,便于不同层次设计人员理解和掌握。
此次的课程设计我们设计的是小车往复运动PLC自动控制。
用型号为西门子公司S7系列的S7-300的PLC实现小车在运输过程中装料、卸料的往复运动过程。
通过I/O地址的分配,实现PLC与控制路线的接口连接。
关键词:可编程控制器(PLC)小车往复运动 S7系列S7-300第一章方案概述 (3)1.1 小车往复运动PLC自动控制设计 (3)1.2 往复运动的实现要求 (3)1.3 设计系统要求 (3)第二章原理控制线路图 (5)2.2 PLC I/O接线原理图 (6)2.3 顺序功能图 (7)2.4控制程序梯形图 (8)第三章系统仿真与运行 (12)3.1 组态 (12)3.2 调用函数 (13)3.3完成仿真 (13)结束语 (14)参考文献 (15)附录 (16)第一章方案概述该方案的目的是实现运料小车的往复运动,在运送过程中,根据站点的不同进行往复,是按照顺序进行运送的设计,并通过对电机的控制实现一定的循环。
- 1、下载文档前请自行甄别文档内容的完整性,平台不提供额外的编辑、内容补充、找答案等附加服务。
- 2、"仅部分预览"的文档,不可在线预览部分如存在完整性等问题,可反馈申请退款(可完整预览的文档不适用该条件!)。
- 3、如文档侵犯您的权益,请联系客服反馈,我们会尽快为您处理(人工客服工作时间:9:00-18:30)。
第2章 运料小车控制系统
2.1
图1系统的运行方式
按下启动按钮SB1,系统启动小车首先在原位启动装料定时器进行装料,15s后停止装料,小车右行。右行至限位开关SQ2处右行停止启动卸料定时器,进行卸料。10s后,卸料停止,小车左行。左行至限位开关SQ1处左行停止,进行装料。如此循环一直进行下去,直到按下停止按钮SB2。
3.2
该设计采用开关作为输入信号,控制直流电机的正反转,从而实现运料小车的左行和右行,其输入输出地址分配表如表1,输入输出接口电路图如图2。图2中指示灯包括红灯和绿灯,红灯表示小车正在装料,绿灯表示小车正在卸料,当指示灯熄灭时表示小车装料或卸料工作完成。利用电磁阀线圈的得电和失电来控制小车卸料阀门的开启和关闭。
M0.7
小车所在站编号=呼叫编号
M1.0
小车所在站编号<呼叫编号
4.3梯形图及功能说明
(1)行程开关
在该程序中,5个站的行程开关分别用数字0~4来表示,当小车在1号站时,行程开关I0.7得电,将数字0传送到数据寄存器AC0;当小车在2号站时,行程开关I1.0得电,将数字1传送到数据寄存器AC0。依次类推,当小车在5号站时,行程开关I1.3得电,将数字4传送到数据寄存器AC0。所对应的梯形图如图7所示。
第1章 课程设计的方案
1.1 PLC运料小车的基本介绍
工厂运输现大多采用地面运输,地面运输主要采用叉车及手推运料小车,叉车需专人驾驶且无固定轨道,在车间内运行极不安全,手推运料小车需人为动力,劳动强度大,运输效率低。随着经济的发展,运料小车不断扩大到工业运输的各个领域,从手动到自动,逐渐形成了机械化、自动化。早期运料小车电气控制系统多为继电器-接触器组成的复杂系统,这种系统存在设计周期长、体积大、成本高等缺陷,几乎无数据处理和通信功能,必须有专人负责操作。后来,单片机应用到运料小车控制系统中。但是单片机开发周期长,使用难,开发成本高,批量成本低,对人要求高,而且其稳定性不够高。由于PLC 开发周期短,使用容易,开发成本低,批量成本高,对操作人员技术要求要求不高,并且稳定性好,抗干扰能力强,使得对基于PLC的运料小车控制系统的开发研究逐步加强。
PLC(Programmable Logical Controller)是20世纪70年代以来以微处理器为核心,综合计算机技术、自动控制技术和通信技术发展起来的一种新型工业自动控制装置。由于它具有功能强、可靠性高、配置灵活、使用方便以及体积小、重量轻等优点,使其在自动化控制的各个领域中得到了广泛的应用。
图7 行程开关梯形图
(2)小车启停辅助继电器
图3运料小车系统硬件结构图
3.3
针对这种PLC,其输入可以直接采用AC220V,输出电压为DC24V,直流电机为12V,故需要进行电压转换,具体转换电路如图3所示。图3中采用2个DC24V继电器和1个12V直流电源来实现直流电机的正反转,2个继电器线圈直接接到可编程控制器的输出端。当继电器线圈1得电时,继电器1的触点由k1转换到k2,而继电器线圈2的触点状态不变,电流流向如I1所示,驱使DC12V电机按一定方向运转;当继电器线圈2得电。时,继电器线圈1触点状态不变,而继电器线圈2的触点由k3转换到k4,电流流向如I2所示,驱使DC12V电机按相反的方向运转。
1号站呼叫按钮开关
I0.3
2号站呼叫按钮开关
I0.4
3号站呼叫按钮开关
I0.5
4号站呼叫按钮开关
I0.6
5号站呼叫按钮开关
I0.7
1号站行程开关
I1.0
2号站行程开关
I1.1
3号站行程开关
I1.2
4号站行程开关
I1.3
5号站行程开关
这个控制系统需要控制的外部设备只有控制小车电器,所以输出点应该有2个。具体的输出分配如表2所示。
图4小车的控制主电路
第4章 控制系统软件结构设计
4
(1)编程软件
本系统的编程软件采用西门子STEP7-Micro/WIN软件。
(2)流程图
本系统的流程图如图6所示。
(3)程序的构成
开始运行程序,PLC将运行已经设置好的程序和参数,按下启动按钮小车开始启动。按停止按钮小车停止。为了防止小车在装有货物的情况下再次装料,该设计要求在启动开始按钮后小车先左行,到达行程开关a,启动卸料程序进行卸料,卸料程序包括定时器1开始计时、绿指示灯变亮、卸料阀门打开,其中定时器所定时间能够满足卸料需要,卸料阀门关闭开启定时器2,定时时间到,小车右移,当运行到行程开关b时,启动定时器3,同时红指示灯变亮,小车进行装料,定时时间到,装料结束,红指示灯熄灭,然后小车左行,如此循环工作,直到按下停止按钮,小车停止。程序设计如图4所示。
表2 输出地址分配
输出地址
对应的外部设备
Q0.0
电机反转继电器(左行)
Q0.1
电机正转继电器(右行)
内部继电器地址分配如表3所示。
表3内部继电器地址分配
内部继电器地址
功能说明
M0.0
小车运行/停止
M0.1
1号站呼叫
M0.2
2号站呼叫
M0.3
3号站呼叫
M0.4
4号站呼叫
M0.5
5号站呼叫
M0.6
小车所在站编号>呼叫编号
2.2控制系统的方案设计
系统的控制结构原理图如图2所示。
图2系统控制结构原理图
第3章 控制系统硬件结构设计
3
小车送料系统的结构组成由电源,一个装有三相异步电动机的运料小车,一个PLC模块,2个行程开关行程开关以监测小车是否到达该站点,一个启动按钮(SB1),用于启动小车,一个停止按钮(SB2)用于小车的急停,一个指示灯和一电磁阀显示控制小车状态。
4.2小车自动运行的功能图
4.3小车自动运行的程序梯形图
图6 控制系统流程图
4.2 I/O地址分配
这个控制系统的输入有启动按钮开关、停止按钮开关、5个呼叫按钮开关、5个行程开关共12输入点。具体的输入分配如表1所示。
表1 输入地址分配
输入地址
对应的外部设备
I0.0
启动按钮开关
I0.1
停止按钮开关
I0.2