石墨化坩埚
坩埚石墨化度对SiC单晶生长过程的影响

万方数据12期刘军林等:坩埚石墨化度对sjc单晶生长过程的影响・1945・g=【(O.344一面02)/O.0086]×100%(1)SiC2(曲=2C(s)+si(g)这里,g是石墨化度,函02是石墨结构(002)而的面间距。
表l给出了不同坩埚的如和g值。
图1晶体生长速度与籽晶温度的关系Fig.1o∞wtlIrateversusseedstcmperaturo图2不同坩埚的xRD谱图Fig2XRDpattemsofdl‰地ntcmcibks表1坩埚A.B,c的如2和暑值!!坠!竺!苎壁!竺璺墨:!!竺!!!!!!竺!!皂生垒:曼兰翌璺竺cnlcjblen啪ber矗02,nmg/%A0.337180.2BO336686.4C0336290.7图3是晶体生长后坩埚壁的sEM照片。
从图3可知,坩埚A的内壁有明显的损失,原来的表面已经基本上看不见'厂。
与坩埚A相比,坩埚B的损失比较小,并且保留了一部分原来的表面;而坩埚c的内壁基本上完好无损,只是在原来的表面上有一些反应掉的小坑。
按照Herro的报道”6J,在晶体生长过程中,坩埚内壁与坩埚内的气相有碳的交换,反应前后坩埚质量几乎不发生变化,交换机制如反应式(2)所示。
(2)图3在2150℃牛长5h后不同坩埚内壁的sEM形貌Fi93sEMimagesofdifr秆entgfaphitecruciblewall8a缸rgrowingat2150℃for5h:(a)crucibleA,(b)crucibleB,and(c)cruciblec在实验一p发现,石墨坩埚在晶体生长过程中不仅和气相交换碳,而且是一个消耗性的碳源。
高温下sic+c系统中的气相主要有si,sic2和si2ci7J。
晶体生长过程中所发生的反应主要有如下几种:2sic(。
)2sifg】+sic2(g)(3)2SiC(。
)=C(s)+Si2C(g)(4)2C(s)+Si(曲=SiC2(g)(5)si2c(g)3c(s)+2si(g)(6)si(g)+sic2(g)22sic(。
用于艾奇逊型石墨化炉的匣钵坩埚[实用新型专利]
![用于艾奇逊型石墨化炉的匣钵坩埚[实用新型专利]](https://img.taocdn.com/s3/m/5674a52a2379168884868762caaedd3383c4b5b0.png)
(19)中华人民共和国国家知识产权局(12)实用新型专利(10)授权公告号 (45)授权公告日 (21)申请号 201721339529.1(22)申请日 2017.10.18(73)专利权人 陕西三义高科石墨新材料有限公司地址 722306 陕西省宝鸡市眉县金渠镇霸王河工业园眉兴大道40号(72)发明人 汪应成 (74)专利代理机构 北京科亿知识产权代理事务所(普通合伙) 11350代理人 宋秀珍(51)Int.Cl.C01B 32/205(2017.01)(ESM)同样的发明创造已同日申请发明专利(54)实用新型名称用于艾奇逊型石墨化炉的匣钵坩埚(57)摘要提供一种用于艾奇逊型石墨化炉的匣钵坩埚,具有坩埚本体和与其适配的坩埚盖,坩埚本体由厚度均匀的底板和侧壁一体化成型制成外形为直棱柱状的匣钵结构,其内具有与坩埚本体外形相同且一次成型制得的坩埚槽,且棱柱转角通过圆角过渡;与坩埚本体外侧壁相平齐匹配设有坩埚盖,坩埚盖下端一体化制有纳入坩埚槽槽口内且外缘与坩埚槽槽口侧壁相贴合的凸出部,凸出部中间切割制有减轻盖体自重并增加盖体支撑强度的内凹棱锥空腔。
本实用新型改善了艾奇逊型石墨化炉石墨化提纯生产时产能低电耗大的现状,在保证坩埚机械强度的基础上,能为企业带来提升产能并节约电费支出的双重收益,更具现实意义和推广价值。
权利要求书1页 说明书4页 附图7页CN 207435031 U 2018.06.01C N 207435031U1.用于艾奇逊型石墨化炉的匣钵坩埚,具有坩埚本体(1)和与其适配的坩埚盖(2),其特征在于:所述坩埚本体(1)由厚度均匀的底板(101)和侧壁(102)一体化成型制成外形为直棱柱状的匣钵结构,其内具有与坩埚本体(1)外形相同且一次成型制得的坩埚槽(103),且棱柱转角通过圆角(104)过渡;与坩埚本体(1)外侧壁相平齐匹配设有坩埚盖(2),所述坩埚盖(2)下端一体化制有纳入坩埚槽(103)槽口内且外缘与坩埚槽(103)槽口侧壁相贴合的凸出部(201),所述凸出部(201)中间切割制有减轻盖体自重并增加盖体支撑强度的内凹棱锥空腔(202)。
一种艾奇逊石墨化炉的坩埚装炉结构

一种艾奇逊石墨化炉的坩埚装炉结构1. 简介艾奇逊石墨化炉是一种常用于实验室和工业生产中的加热设备,其主要作用是将样品加热至高温,以进行化学反应、材料测试等。
而炉子的坩埚装炉结构则是炉子的重要组成部分之一,起着承载样品、传导热能的关键作用。
在本文中,我们将从深度和广度两个方面分析一种艾奇逊石墨化炉的坩埚装炉结构。
2. 深度分析艾奇逊石墨化炉的坩埚装炉结构通常由坩埚、坩埚支撑、加热元件和炉体组成。
坩埚作为放置样品的容器,通常采用耐高温、耐腐蚀的石墨材料制成,以确保其在高温下的稳定性和耐用性。
坩埚支撑是用于支撑坩埚的组件,通常由陶瓷或金属材料制成,以保证坩埚在加热过程中的稳定性和安全性。
加热元件则是负责向坩埚输送热能的部分,通常采用石墨加热管或电阻丝,在提供均匀加热的也需要结合控温系统来确保温度的精确控制。
炉体则是将上述部件整合在一起的外部结构,通常采用金属材料制成,以提供外部保护和稳定支撑。
3. 广度分析从广度上来看,艾奇逊石墨化炉的坩埚装炉结构在不同领域有着广泛的应用。
在化学实验室中,它常用于进行样品燃烧分析、氧化还原实验等化学反应,要求坩埚装炉结构在高温高压下仍具有稳定的性能。
在材料科学领域,坩埚装炉结构则常用于材料的热处理、晶体生长等过程,对材料的纯净度和温度控制有着较高的要求。
而在工业生产中,艾奇逊石墨化炉的坩埚装炉结构更是承载着生产线的连续运行和产品质量的稳定性,需要具备高耐磨、高抗腐蚀等特性。
总结回顾通过对一种艾奇逊石墨化炉的坩埚装炉结构深度和广度的分析,我们更加全面地了解了这一炉子的重要组成部分。
坩埚、坩埚支撑、加热元件和炉体的优秀设计和稳定性能,为炉子的高效运行和样品加热提供了坚实的保障。
在将来的设计和应用中,我们需要更加重视坩埚装炉结构的稳定性和可靠性,以应对不同领域的需求和挑战。
个人观点作为一个炉子的重要组成部分,坩埚装炉结构的设计和性能对炉子的整体表现和使用效果有着至关重要的影响。
石墨电极用途
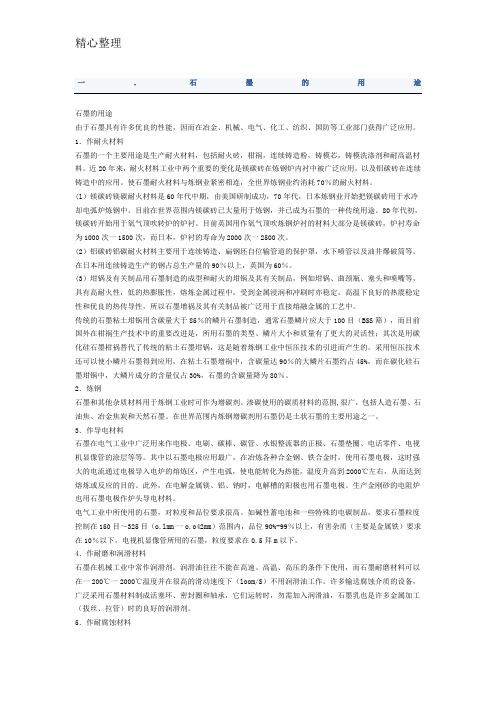
人造石墨99.20.40.200.100.050.005―0.84鳞片石墨85.313.20.060.440.350.060――煅烧石油焦(中硫)96.50.40.400.301.500.6000.150.77 煅烧石油焦(低硫)98.30.40.100.200.300.0800.040.800 干燥焦炭87.79.00.301.001.001.000―0.64优质无烟煤90.02.52.003.50.250.6001.100.64沥青焦97.00.50.500.50.40.7000.200.55料.坩埚及有关制品用石墨制造的成型和耐火的坩埚及其有关制品,例如坩埚、曲颈瓶、塞头和喷嘴等,具有高耐火性,低的热膨胀性,熔炼金属过程中,受到金属浸润?和冲刷时亦稳定,高温下良好的热震稳定性和优良的热传导性,所以石墨坩埚及其有关制品被广泛用于直接熔融金属的工艺中.2炼钢(最重要的来了石墨和其他杂质材料用于炼钢工业时可作为增碳剂。
渗碳使用的碳质材料的范围很广,包括人造石墨、石油焦、冶金焦炭和天然石墨。
在世界范围内炼钢增碳剂用石墨仍是土状石墨的主要用途之一。
石墨在电气工业中广泛用来作电极、电刷、碳棒、碳管、水银整流器的正极、石墨垫圈、电话零件、电视机显像管的涂层等等。
其中以石墨电极应用最广,在冶炼各?种合金钢、铁合金时,使用石墨电极,这时强大的电流通过电极导入电炉的熔炼区,产生电弧,使电能转化为热能,温度升高到2000度左右,从而达到熔炼或反?应的目的。
此外,在电解金属镁、铝、钠时,电解槽的阳极也用石墨电极。
生产金刚砂的电阻炉也用石墨电极作炉头导电材料。
4作耐磨和润滑材料石墨在机械工业中常作润滑剂。
润滑油往往不能在高速、高温、高压的条件下使用,而石墨耐磨材料可以在-200---2000温度并在很高的滑动速度下不用润滑油工作。
许多输送腐蚀介质的设备,广泛采用石墨材料槽的阳极导电材料都是采用石墨化电极或连续自焙电极(阳极糊、有时用预焙阳极)。
电子束蒸发石墨坩埚

电子束蒸发石墨坩埚
电子束蒸发石墨坩埚(EBGD)是一种利用电子束蒸发将石墨坩埚蒸发在基底上的金属制作技术。
电子束蒸发石墨坩埚技术利用电子束以节省时间、提高效率和减少污染的方式进行植入和蒸发。
此外,它还可以用于部分基底植入和蒸发,可大大提高产品的可靠性和性能。
电子束蒸发石墨坩埚技术最初是用于制造微电子器件的,通常用于微处理器的源极、汲极装配、铜结构的填充和封装等。
另外,它还可以用于复杂的抗反射和结构化窗口等应用。
电子束蒸发石墨坩埚技术的优势在于它的稳定性、精确性、节省时间以及低污染。
有了电子束蒸发石墨坩埚技术,制造商可以更加精确地控制体积和形状,而且可以在很短的时间内完成工作。
此外,它还可以很大程度地降低污染,可以减少污染物排放量,也不会有任何有害废料产生。
电子束蒸发石墨坩埚技术的应用遍及微电子行业,它可以被应用于电路板制造、芯片封装和其他相关应用中。
它使得基底可以更加平滑和精确,也可以使封装变得更加简单,更加稳定,效率更高。
此外,电子束蒸发石墨坩埚技术还可以应用于医疗和汽车行业,如制造医疗作用装置、生物传感组件等。
在汽车行业,它可以用于制造发动机及其他汽车部件,也可以用于车身的美容细节。
在总结,电子束蒸发石墨坩埚技术的应用非常广泛,它不仅可
以用于微电子行业,还可以用于医疗、汽车行业等。
电子束蒸发石墨坩埚技术具备很多优势,它可以节省时间、提高效率、降低污染,而且可以大大提高产品的可靠性和性能。
电子束蒸发石墨坩埚技术的应用前景非常广阔,希望未来能更好地服务于电子行业。
石墨坩埚锂电负极

石墨坩埚锂电负极
石墨坩埚锂电池负极是目前锂电池技术中的一种重要材料。
与传统的电池负极材料相比,石墨坩埚锂电池负极具有更高的能量密度和更长的使用寿命。
本文将从石墨坩埚锂电池负极的制备、性能和应用等方面进行详细介绍。
一、石墨坩埚锂电池负极的制备
石墨坩埚锂电池负极是通过将石墨粉末与聚合物混合,制成混合物后涂布在铜箔上而制备的。
在制备过程中,需要严格控制石墨粉末的粒度和分布,以及混合物的配比和涂布厚度等参数,以保证负极材料的性能和稳定性。
二、石墨坩埚锂电池负极的性能
石墨坩埚锂电池负极具有以下几个优点:
1.高能量密度:石墨坩埚锂电池负极的能量密度比传统的电池负极材料高出很多,可以实现更长时间的使用。
2.长寿命:石墨坩埚锂电池负极的寿命比传统的电池负极材料长,可以实现更多的充放电循环。
3.较低的内阻:石墨坩埚锂电池负极的内阻比传统的电池负极材料低,可以实现更高的输出功率。
三、石墨坩埚锂电池负极的应用
石墨坩埚锂电池负极广泛应用于移动电源、电动车、无人机等领域。
在移动电源领域,石墨坩埚锂电池负极可以实现更长时间的使用,满足人们日常生活和工作的需求。
在电动车领域,石墨坩埚锂电池负极可以实现更高的输出功率,提高电动车的行驶性能。
在无人机领域,石墨坩埚锂电池负极可以实现更长的使用寿命和更高的能量密度,提高无人机的续航能力和飞行性能。
石墨坩埚锂电池负极是目前锂电池技术中的一种重要材料,具有高能量密度、长寿命和较低的内阻等优点,广泛应用于移动电源、电动车、无人机等领域。
坩埚用途及注意事项
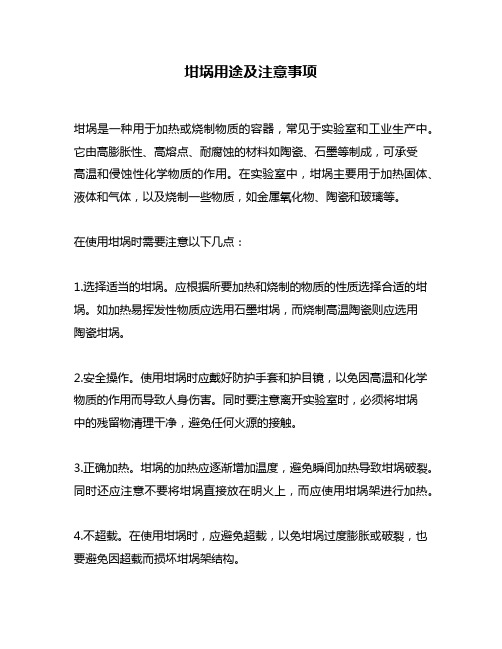
坩埚用途及注意事项
坩埚是一种用于加热或烧制物质的容器,常见于实验室和工业生产中。
它由高膨胀性、高熔点、耐腐蚀的材料如陶瓷、石墨等制成,可承受
高温和侵蚀性化学物质的作用。
在实验室中,坩埚主要用于加热固体、液体和气体,以及烧制一些物质,如金属氧化物、陶瓷和玻璃等。
在使用坩埚时需要注意以下几点:
1.选择适当的坩埚。
应根据所要加热和烧制的物质的性质选择合适的坩埚。
如加热易挥发性物质应选用石墨坩埚,而烧制高温陶瓷则应选用
陶瓷坩埚。
2.安全操作。
使用坩埚时应戴好防护手套和护目镜,以免因高温和化学物质的作用而导致人身伤害。
同时要注意离开实验室时,必须将坩埚
中的残留物清理干净,避免任何火源的接触。
3.正确加热。
坩埚的加热应逐渐增加温度,避免瞬间加热导致坩埚破裂。
同时还应注意不要将坩埚直接放在明火上,而应使用坩埚架进行加热。
4.不超载。
在使用坩埚时,应避免超载,以免坩埚过度膨胀或破裂,也要避免因超载而损坏坩埚架结构。
5.及时清理。
使用坩埚后要及时清理,避免化学物质长时间附着在坩埚内表面,影响坩埚的使用寿命和成分精度。
总之,正确使用坩埚并注意维护可以使其更长久地服务于实验室和工业生产,并确保实验的准确性和安全性。
浅谈石墨化生产工艺技术

68引言近年来随着绿色、环保、可持续发展的迫切需要,国家正在大力推行电动新能源汽车,锂离子新能源动力电池迎来了快速发展的浪潮,锂离子电池的开发成为了目前的热点。
锂离子电池因其具有出色的电化学性能,并且还有能量密度高、循环性能优异、寿命长、工作电压高、自放电小、使用的材料成本低易获取和无记忆效应等优点,广泛的的应用在了新能源汽车、储能设备、电子产品、航空航天等领域,具有广阔良好的应用前景。
石墨化过程是使碳材料二维空间无序的六角碳原子平面逐渐变成三维有序空间的重叠。
一般而言,石墨化是从1700℃开始石墨化,在温度升高过程中,晶体增长,石墨化度提高,层间距变小,2300℃时接近标准石墨。
石墨化可以使碳原子进行重排,得到良好的导热性和低热膨胀系数,并且可以排除杂质,增加纯度。
目前在人造石墨石墨化过程中,从发现到大批量生产的百年来,人们提出了三种主要的石墨化理论假说。
一、石墨化机理 1.碳化物转化理论碳化物转化理论最早是由艾奇逊提出,依据合成碳化硅实验,他认为碳材料是先与矿物质(氧化铁、氧化铝、二氧化硅)形成碳化物,然后碳化物在高温条件下分解成为金属蒸气和石墨,其化学反应公式:�C 2322452235C220017002+↑ → + → +°−°−S i SiC C O SiC C SiO C2.再结晶理论再结晶理论由塔曼提出,认为碳材料本身就有很小的石墨晶体,在石墨化时石墨晶体与晶体连接在一起形成大的晶体,而且石墨化过程中也会有新的晶体产生。
石墨化的难易程度和结构有关,松散的材料距离长难连接,密实的碳材料更容易连接,容易石墨化。
但实际上通过XRD分析,发现大多数碳材料中并没有晶体结构,因此再结晶理论并没有得到广泛认可。
3.微晶生长理论此理论最早是德拜和谢乐一起提出,他们认为:碳材料是稠环芳香烃化合物,是最原始的物质,在加热过程中,这些稠环芳香烃化合物会经过分解和聚合等反应,生成炭青质。
石墨坩埚使用说明书

石墨坩埚使用说明书一、石墨坩埚特别注意事项:1.注意不要给予机械性外力撞击,不要从高处落下或撞击。
2.不要被水淋湿,需存放于干燥的地方。
3.筑熔干燥后,不要使其接触水。
4.使用期间不要将火焰直接对准坩埚(喷到坩埚底部),若喷到时坩埚底部会有明显的黑色痕迹。
5.停炉后剩余之铝、铜料要尽量取出,坩埚内不要留残液。
6.酸化物(除渣剂等)之使用需适量,以免侵蚀坩埚,过量使用会侵蚀坩埚造成破裂。
7.投入原料时不撞击坩埚,不使用机械力量。
二、保存及搬运:1.石墨坩埚怕水,绝对要避免潮湿及被水淋到。
2.留意表面碰伤,勿直接把坩埚放于地板上,需放置于栈板上。
3.勿在地板横向滚动,立向在地上推转时地上需垫厚纸板或破布等较软的东西,以免碰伤磨伤底部。
4.搬运时请特别注意,切勿落地或碰击到。
三、坩埚安装:1.坩埚底座(坩台)需与坩埚底径相同或较大,坩台高度需高于喷火口,以免火喷到坩埚。
2.用耐火砖作坩台应以圆形耐火砖,需平坦没有弯曲,勿用半块或凹凸不平之砖材,最好是用进口之石墨坩台为佳。
3.坩台需放置在熔为、解熔之中心点,上面以焦炭粉、稻草灰或耐火棉等作垫,避免坩埚与坩台粘住,坩埚放上去后,需于熔中央,且需水平(最好用水平尺量)。
4.坩埚与炉体之尺寸要配合,坩埚与熔壁之间距离应适当,最少需40mm以上。
5.有嘴坩埚装炉时,坩埚嘴下面与耐火砖接触间隙应预留约30-50MM之空隙,且底下不能垫任何东西,嘴与炉壁用耐火棉抹平。
炉壁需有固定耐火砖(三点)与坩埚需垫上厚约3mm之瓦楞纸板作为加温后之热胀空间。
四、预热烘干处理:1.使用前4-5小时将坩埚搬放于油炉边预热,对坩埚除湿表面有帮助。
2.新坩埚使用前先在坩埚内放置木炭或木材燃烧四小时左右,对坩埚之除湿有帮助。
3.新坩埚炉内升温预热时间如下:0℃--200℃慢速升温4H油0℃--300℃慢速升温1H电200℃--300℃慢速升温4H炉300℃--800℃慢速升温4H炉300℃--400℃慢速升温4H400℃--600℃快速升温保持2H4.停炉后,开炉预热时间如下:油炉及电炉:0℃--300℃慢速升温1H300℃--600℃慢速升温4H600℃-快速升温到需要之度数a.电炉:停工时最好是持续保温,温度定在600℃左右;如不保温,汤料需尽量舀出来,勿留在坩埚内太多;如遇停电时需迅速把料取出。
负极材料石墨化坩埚
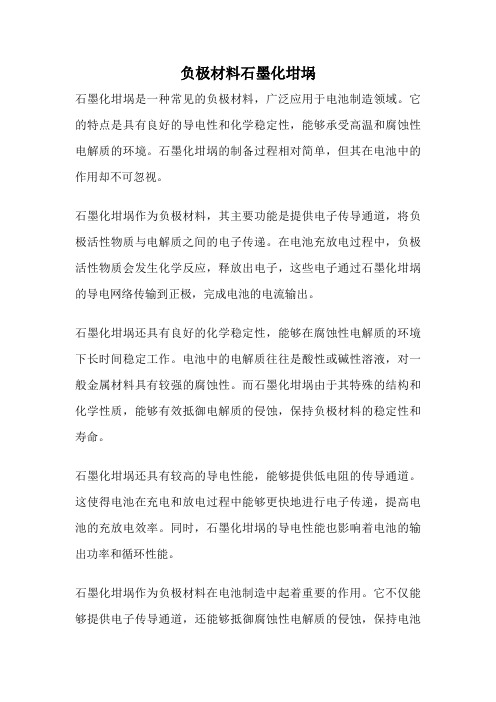
负极材料石墨化坩埚
石墨化坩埚是一种常见的负极材料,广泛应用于电池制造领域。
它的特点是具有良好的导电性和化学稳定性,能够承受高温和腐蚀性电解质的环境。
石墨化坩埚的制备过程相对简单,但其在电池中的作用却不可忽视。
石墨化坩埚作为负极材料,其主要功能是提供电子传导通道,将负极活性物质与电解质之间的电子传递。
在电池充放电过程中,负极活性物质会发生化学反应,释放出电子,这些电子通过石墨化坩埚的导电网络传输到正极,完成电池的电流输出。
石墨化坩埚还具有良好的化学稳定性,能够在腐蚀性电解质的环境下长时间稳定工作。
电池中的电解质往往是酸性或碱性溶液,对一般金属材料具有较强的腐蚀性。
而石墨化坩埚由于其特殊的结构和化学性质,能够有效抵御电解质的侵蚀,保持负极材料的稳定性和寿命。
石墨化坩埚还具有较高的导电性能,能够提供低电阻的传导通道。
这使得电池在充电和放电过程中能够更快地进行电子传递,提高电池的充放电效率。
同时,石墨化坩埚的导电性能也影响着电池的输出功率和循环性能。
石墨化坩埚作为负极材料在电池制造中起着重要的作用。
它不仅能够提供电子传导通道,还能够抵御腐蚀性电解质的侵蚀,保持电池
的稳定性和寿命。
同时,石墨化坩埚还能够提高电池的充放电效率和输出功率。
在未来的电池技术发展中,石墨化坩埚有望进一步优化,为电池的性能提供更好的支持。
高纯石墨坩埚的技术指标和特点
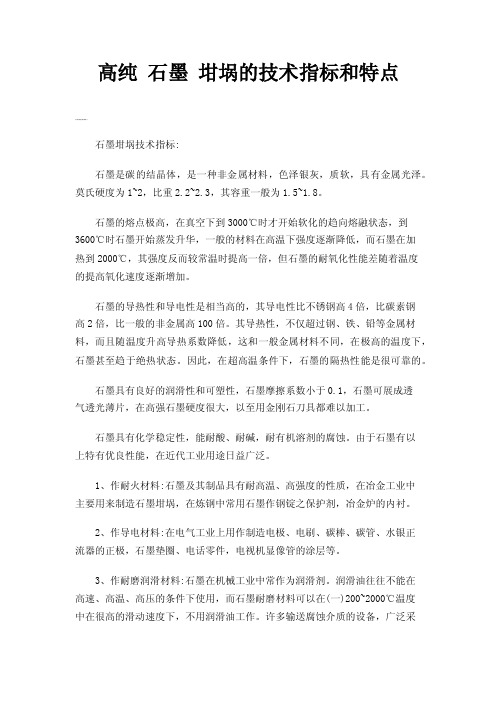
高纯石墨坩埚的技术指标和特点石墨坩埚技术指标:石墨是碳的结晶体,是一种非金属材料,色泽银灰,质软,具有金属光泽。
莫氏硬度为1~2,比重2.2~2.3,其容重一般为1.5~1.8。
石墨的熔点极高,在真空下到3000℃时才开始软化的趋向熔融状态,到3600℃时石墨开始蒸发升华,一般的材料在高温下强度逐渐降低,而石墨在加热到2000℃,其强度反而较常温时提高一倍,但石墨的耐氧化性能差随着温度的提高氧化速度逐渐增加。
石墨的导热性和导电性是相当高的,其导电性比不锈钢高4倍,比碳素钢高2倍,比一般的非金属高100倍。
其导热性,不仅超过钢、铁、铅等金属材料,而且随温度升高导热系数降低,这和一般金属材料不同,在极高的温度下,石墨甚至趋于绝热状态。
因此,在超高温条件下,石墨的隔热性能是很可靠的。
石墨具有良好的润滑性和可塑性,石墨摩擦系数小于0.1,石墨可展成透气透光薄片,在高强石墨硬度很大,以至用金刚石刀具都难以加工。
石墨具有化学稳定性,能耐酸、耐碱,耐有机溶剂的腐蚀。
由于石墨有以上特有优良性能,在近代工业用途日益广泛。
1、作耐火材料:石墨及其制品具有耐高温、高强度的性质,在冶金工业中主要用来制造石墨坩埚,在炼钢中常用石墨作钢锭之保护剂,冶金炉的内衬。
2、作导电材料:在电气工业上用作制造电极、电刷、碳棒、碳管、水银正流器的正极,石墨垫圈、电话零件,电视机显像管的涂层等。
3、作耐磨润滑材料:石墨在机械工业中常作为润滑剂。
润滑油往往不能在高速、高温、高压的条件下使用,而石墨耐磨材料可以在(一)200~2000℃温度中在很高的滑动速度下,不用润滑油工作。
许多输送腐蚀介质的设备,广泛采用石墨材料制成活塞杯,密封圈和轴承,它们运转时勿需加入润滑油。
石墨乳也是许多金属加工(拔丝、拉管)时的良好的润滑剂。
4、石墨具有良好的化学稳定性。
经过特殊加工的石墨,具有耐腐蚀、导热性好,渗透率低等特点,就大量用于制作热交换器,反应槽、凝缩器、燃烧塔、吸收塔、冷却器、加热器、过滤器、泵设备。
石墨化厢式炉装炉操作规程

石墨化厢式炉装炉操作规程1. 引言本操作规程旨在明确石墨化厢式炉装炉的操作步骤和注意事项,以确保装炉工作的安全和高效进行。
操作人员在进行装炉工作时,应仔细阅读本规程,并严格按照规程的要求进行操作。
2. 装炉前准备2.1. 检查炉内环境在装炉前,操作人员应先检查炉内环境,确保其符合装炉要求。
具体步骤如下:•检查炉内是否有杂质、尘埃等杂物,如有应先清理干净。
•检查炉内的石墨块和导电件是否完好,如有损坏应及时更换。
•检查加热元件是否安装牢固,如有松动应进行紧固。
2.2. 准备装炉材料在装炉前,操作人员应准备好所需的装炉材料,包括待加热的物品、坩埚、石墨块等。
具体步骤如下:•确认待加热的物品的尺寸、形状等参数,并选择合适的坩埚和石墨块进行装炉。
•检查坩埚是否干净,如有杂质应进行清洗。
•将坩埚放入石墨化厢式炉中,将待加热物品放入坩埚内。
2.3. 确保安全操作在装炉前,操作人员应确保安全操作,避免发生意外事故。
具体措施如下:•确保操作人员佩戴防护眼镜、防护手套等个人防护装备。
•确保操作人员熟悉炉的紧急停机操作,并在必要时熟悉相关应急预案。
3. 装炉操作步骤3.1. 打开炉门在装炉前,操作人员应先打开炉门。
具体步骤如下:•将炉门锁定装置解锁。
•缓慢打开炉门,以免突然开启导致炉内产生风暴。
3.2. 装入坩埚和物品打开炉门后,操作人员应将坩埚和待加热物品装入炉内。
具体步骤如下:•将预先准备好的坩埚小心地放入炉腔内。
•将待加热物品小心地放入坩埚内,注意避免物品与坩埚壁接触。
3.3. 关闭炉门在装入坩埚和物品后,操作人员应及时关闭炉门。
具体步骤如下:•确保坩埚和物品放置妥善后,缓慢关闭炉门。
•利用炉门锁定装置将炉门锁定。
3.4. 操作炉控系统装入坩埚和关闭炉门后,操作人员应进行炉控系统的操作设置。
具体步骤如下:•预约炉控系统的加热曲线和保持时间,根据待加热物品的要求进行设置。
•启动炉控系统,确保加热曲线和保持时间设置生效。
石墨坩埚出现裂痕的原因

1靠近石墨坩埚底部(有可能导致坩埚底部脱落)
1可能由于硬物撞击造成,如:将铸料扔进坩埚中,或者使用铁棒等硬物敲击底部。
2大约在石墨坩埚一半的位置
2原因可能是将坩埚放置在炉渣上或不适合的坩埚底座上,再取出坩埚时,如果坩埚钳夹取的位置过于靠上,并且用力过大,就会造成坩埚钳下部的坩埚表面出现裂纹
3在使用带有石墨坩埚嘴的坩埚时,坩埚嘴下部有横向裂纹
3没有正确安装坩埚,在安装新坩埚时,如果耐火土被紧紧挤在坩埚嘴下面,在使用过程中,坩埚冷却收缩时会使受力点集中在坩埚嘴部位,而产生裂纹
3星状裂纹
1在坩埚的底部
1由于热膨胀导致
2在坩埚的侧面
2通常为加热后楔形物膨胀所致
4洞/破口
1在尚未变薄的坩埚壁上出现大洞
问题描述
原因分析
1纵向裂纹
1)石墨坩埚在长时间使用后,坩埚壁出现纵向裂纹,并且裂纹处的坩埚壁较薄。
1)石墨坩埚即将或已经达到使用寿命,坩埚壁会变薄,承受不 Nhomakorabea过大的外力
2初次使用(或接近全新)的坩埚在下沿出现裂纹并贯穿坩埚底部
2将冷却的坩埚放入高温的热火中,或当坩埚的冷却状态下,对坩埚底部进行过快加热。该损坏情况一般还伴随釉面剥落的现象
3由石墨坩埚顶部边沿延伸的纵向裂纹
3对石墨坩埚进行过快的加热所造成,尤其是当坩埚底部和下沿受热速度远远过于顶部的时候。在坩埚顶部边缘的锲入操作也容易造成该损坏。不合适的坩埚钳或者对上沿的敲击也会造成坩埚顶部边缘的硬伤和明显的损坏。
4石墨坩埚侧面的纵向裂纹(裂纹没有延伸到坩埚顶部或底部)
4通常有内部压力所造成。如:将冷却的楔形铸料横向放入坩埚中,当楔形铸料在受热膨胀后就会造成该中损坏。
1大部分是由重击所导致,如:把铸锭扔进坩埚里
石墨坩埚使用注意事项

坩埚产品使用须知1、坩埚规格号即铜之容量(#/千克)2、石墨坩埚谨防潮湿,存放时必须放在干燥处或木架上。
3、搬运时轻拿轻放,严禁摔震。
4、使用前需在干燥设备或炉旁热烘烤,温度逐升到500℃。
5、坩埚应放在炉口平面以下避免炉盖磨损坩埚上口。
6、加料时应根据坩埚溶量,不可加料太多,太紧避免膨胀坩埚。
7、出炉工具和坩夹要符合坩埚外形,夹其中部避免局部受力损坏坩埚。
8、清除坩埚内外壁溶渣和粘焦时应轻敲避免损坏坩埚。
9、坩埚与炉壁之间应保持适当距离,坩埚应放在炉内正中。
10、使用过量助燃剂、添加剂将减少坩埚使用寿命。
11、使用过程中,每周将坩埚转动一次,可延长坩埚使用寿命。
12、避免强氧化火焰直喷坩埚侧面和底砣坩锅的使用注意事项一常规操作1. 检验:使用前一定要检验坩埚,防止任何可能的损坏,确保坩埚的完好。
使用中一定要随时检查坩埚,包括:埚壁的磨损、损伤、确保坩埚不带病作业。
2. 安装: A、安装前检查线圈泥浆填塞状况是否良好,形状近似圆形,如有必要修复并充分干燥。
B、紧贴线圈泥浆填塞家一层光滑的平面介质,如云母或玻璃丝布,并保证叠加层方向相同。
C、安装接地保护和布置地线。
D、在炉子底部加入3~4英寸的垫料,并轻轻捣打,每层除掉气体且在作下一层前刮平捣打的垫料。
3. 打制:清除金属飞溅物,避免使用时产生局部过热而损坏线圈。
4. 注意:A、放在线圈中心,可能会产生过热点和裂纹。
B、坩埚底部不能低于最低的线圈。
C、检查坩埚高度和水平,如有必要必须进行调节。
D、用木楔将坩埚固定在电炉线圈中心。
E、在坩埚和炉壁之间加入干燥的振动背衬细粉,(必须是非烧结的)厚度为坩埚直径的十分之一。
F、捣打到离坩埚顶部大约50~75MM时,应当使用可塑料密封坩埚顶部,并在可塑料上制作通风孔,帮助干燥。
二、坩埚的使用1. 坩埚的预热A、坩埚预热是延长坩埚使用寿命的方面之一,许多情况下,坩埚是在预热期间损坏的,这种损坏在熔化金属之前是不明显的。
石墨化炭块用途

石墨化炭块用途石墨化炭块是一种能够提供高温稳定性的新型材料,广泛应用于热处理、化工、电力等行业,因其出色的物理性能和化学稳定性,石墨化炭块的用途非常广泛。
一、在热处理行业的应用1.1 超高温炉炉膛衬里石墨化炭块的高温稳定性和高强度使其成为最理想的炉膛衬里材料之一,因此在高温炉生产过程中,石墨化炭块可以被用于制作超高温炉。
石墨化炭块能够承受高温高压,以及承载重量。
除了具备高温稳定性,石墨化炭块还具备出色的导热性能,能够减少热冲击和温度不稳定性。
1.2 热机仪器设备石墨化炭块可以用于制作热机仪器设备,如试验炉、高温炉等。
石墨化炭块在高温下具备优异的物理性能和化学稳定性,不易氧化,抗酸碱侵蚀。
因此,石墨化炭块被广泛应用于制作高温热机仪器设备。
1.3 其他应用领域在一些特殊的热处理领域,石墨化炭块也具有一定的应用价值。
例如,它可以被用于制作高温反应器、石墨坩埚等高温工具。
此外,石墨化炭块还可以被用于制作气氛传感器、火煤研究等类似应用。
2.1 反应器石墨化炭块可被用于制作化学反应器,适用于低至高温环境,不但能耐化学腐蚀,更具防爆和泄漏的安全性。
2.2 吸附剂石墨化炭块可以用于制作吸附剂,在化工合成反应中,吸附剂可以分子筛分离杂质,从而提高合成反应的效率和产率。
石墨化炭块吸附剂因其具有大比表面积、多孔性强等优点,被应用于催化剂、脱色剂、去重剂等各个领域。
3.1 电阻器石墨化炭块可以用于制作电阻器,因其高温稳定性和导电性能良好,可以作为电子部件,用于各种电力设备及传输、接收所需的电路和电子部件。
3.2 碳电极石墨化炭块可以用于制作碳电极。
碳电极的石墨化炭块具有很强的良好的导电性能和充电容量,因此被广泛应用于制造充电宝、电子笔等高容量的电子产品。
总之,石墨化炭块具有广泛的用途,在热处理、化工、电力等领域,被广泛应用。
未来随着工程技术进一步的提高及应用领域的拓展,石墨化炭块所扮演的角色也将愈发重要。
一种用于锂电池负极材料生产用石墨坩埚及其制备工艺

一种用于锂电池负极材料生产用石墨坩埚及其制备工艺以下是一种用于锂电池负极材料生产用石墨坩埚及其制备工艺:
1. 配料:按照石墨、碳黑、碳纤维、树脂、固化剂的重量比例进行配料,混合均匀。
2. 模具处理:将模具内壁清理干净,并涂覆脱模剂。
3. 料浆充填:将配制好的料浆充填到模具中,确保料浆均匀分布。
4. 振动密实:对料浆进行振动密实,以排除料浆中的气泡。
5. 预热:将模具放入预热炉中进行预热,温度控制在200℃左右。
6. 浇注固化:将预热好的料浆浇注到模具中,并放入固化炉中进行固化。
固化温度控制在180℃左右,固化时间控制在2小时左右。
7. 脱模:将固化好的石墨坩埚从模具中脱出。
8. 石墨化处理:将脱模后的石墨坩埚放入石墨化炉中进行石墨化处理,温度控制在2500℃左右,处理时间控制在2小时左右。
9. 冷却:将石墨化处理后的石墨坩埚进行自然冷却。
10. 打磨抛光:对石墨坩埚的内壁进行打磨抛光,以提高其平滑度。
11. 质量检测:对石墨坩埚进行质量检测,合格的石墨坩埚即可用于锂电池负极材料的生产。
这种制备工艺制备出的石墨坩埚具有良好的导电性、耐高温性和抗腐蚀性,能够满足锂电池负极材料生产的要求。
同时,该制备工艺操作简单,成本低廉,具有较好的实用价值。
串接石墨化炉热处理石墨粉的方法及其石墨坩埚[发明专利]
![串接石墨化炉热处理石墨粉的方法及其石墨坩埚[发明专利]](https://img.taocdn.com/s3/m/c01cb91704a1b0717ed5dddf.png)
专利名称:串接石墨化炉热处理石墨粉的方法及其石墨坩埚专利类型:发明专利
发明人:蔡洵,蔡苏卫
申请号:CN200710057475.4
申请日:20070529
公开号:CN101066760A
公开日:
20071107
专利内容由知识产权出版社提供
摘要:本发明涉及一种串接石墨化炉热处理石墨粉的方法及其石墨坩埚,属于热处理技术领域。
串接石墨化炉热处理石墨粉的方法,对石墨粉进行加热处理,其中,串接石墨化炉热处理石墨粉过程为:(1)装粉。
将石墨粉装入石墨坩埚内至填满。
(2)封盖。
用盖子将石墨坩埚端口密封。
(3)装炉。
将装好石墨粉的石墨坩埚头尾相接依次放入串接石墨化炉中。
(4)加热。
接通电源,使坩埚温度达到2500-3500度,保持4-10小时。
(5)冷却。
将石墨坩埚冷却至室温。
石墨坩埚,为人造石墨材质,其石墨坩埚截面为多孔蜂窝结构,内孔配有密封盖。
本发明具有加热速度快、节省能源、石墨化质量好、温度分布均匀、热效率高、生产能力高等优点。
申请人:蔡洵
地址:102600 北京市大兴区郁花园1里18-6-502
国籍:CN
更多信息请下载全文后查看。
- 1、下载文档前请自行甄别文档内容的完整性,平台不提供额外的编辑、内容补充、找答案等附加服务。
- 2、"仅部分预览"的文档,不可在线预览部分如存在完整性等问题,可反馈申请退款(可完整预览的文档不适用该条件!)。
- 3、如文档侵犯您的权益,请联系客服反馈,我们会尽快为您处理(人工客服工作时间:9:00-18:30)。
成型坩埚生产线
成型坩埚生产原料主要为煅烧石油焦和沥青,,其生产过程主要包括筛分配料、混捏、压型冷却、机加工等工序,分述如下:
(1)筛分配料
煅烧石油焦原料由般烧石油焦生产线产品料仓装吨包,叉车转运至成型车间原料暂存区待用,首先进行筛分处理。
煅烧石油焦吨包采用行车调运至筛分前料仓,直接坐落于料仓内,通过吨包底部卸料口卸入料仓内,生产时由料仓底部落入密闭皮带输送机,送入直线筛分机筛分处理,筛分粒度为≤1m、1~2m、2~4m、4~6 m和>6m等级粒度,振筛上和筛下物分别通过筛分机落料口落入吨包内。
>6m原料由行车吊运至雷蒙磨机粉磨处理,粉磨后物料通过旋风收集器+袋式除尘器收集,收集后物料卸入吨包,重新进行分处理,废气由排气排放。
筛分形成的各粒度原料由行车吊运吨包,通过吨包坐落于配料料仓卸入料仓内,料仓底部设置自动配料系统,通过设计各粒度配料比例,通过配料系统称重进行配料,之后通过螺旋输送机送入混捏机混捏本项目对皮带输送机设置密闭皮带通廊,配料过程采用密闭的螺旋输送机配料,通过加强生产环境管理等措施控制无组织排放,符合清洁生产源头控制要求。
该工序废气污染源主要为原料筛分粉尘(G2-1),采取筛分前料仓顶部和底部筛分机配料料仓顶部设置侧吸罩,收集废气配套4台袋式除尘器净化处理;原料粉墨粉尘(G2-2),采取4台雷蒙磨机配套4套袋式除尘净化处理后;噪声污染源主要为行车(N5)筛分机(N9)雷蒙磨机(N10)运行过程中产生的机械噪声;固体废物污染源主要为袋式除尘器尘灰(S2),作为原料利用。
(2)混捏
混捏工序主体设备为混提机,混过程以煅烧石油焦为原料,熔融沥青为粘结剂,具体工艺过程如下
①沥青熔融
混捏过程粘结剂采用熔融沥青,本项目设置2座10平方米沥青融化槽袋装固态块状原料沥青由汽车运输进厂,暂存于焙烧煅烧原料库内,生产时由化槽顶部进料口人工投入,沥青融化槽装有导热油盘管间接加热,导热油管由坩埚焙烧生产线余利用系统导热油提供,同时设置1台备用电导热油炉,用于坩埚烧生产线检修时热源,导热油加热温度120℃,使块状沥青融化,除去水分,加热过程中产生的沥青烟由通过沥青融化槽设置集气管道负压收集后,进入电捕焦油净化装置净化处理后排放,沥青熔融后保持温度100℃静置2-3d,充分排出水分,之后泵入混捏机使用。
本项目采用中温沥青,中温青软化点为86℃,本项日加热温度为120 ℃,苯并芘的熔点为179℃,沸点为475℃,因此由于本项目加热温度较低未达到苯并芘的沸点,沥青培化和混捏过程中基本无苯并能挥发出来,后续不再识别苯并能污染因子,
②混捏
混捏机通过一对互相配合和旋转的叶片(2形)所产生强器剪切作用而使半干状态的稠物料迅速获得均匀的混合排,混捏机加热方式为环导热油加热,加热温度120℃,冷却方式为水冷却,采用液压缸及启盖,出料方式为螺杆挤出。
混捏机设置石油焦和沥青两个进料口,进料完成后,加盖混捏缸盖进行密闭混捏,本项目共设置1000L混捏机4台,
混捏完成后的糊料过放料口放入压型工序压型机凉料增,冷却至80℃用
③工艺先进行分析
目前国内混捏机加热方式可分为电加热、蒸汽加和酒环导热油加热三种形式,其中电加热方式加热较快,不需要配套加热设各,比较方便,适用于单纯生产成型坩埚无余热利用的工业企业:活汽加热比较均匀,但需另外配套蒸汽生产设备,加热温度较低,不再适用于现今的生产要求:导油加热加热均匀,加热温度高,而且针对围套般统石油焦生产的企业来讲,可以实现余热利用,达到节能降耗的目的,具有十分越的实用性,是国家目前首推的加热的方式。
本项目混捏机采用导热油加热,不但生产效果好,而且可以充分利用烧石油焦生产的生产余热,不要配套供热没备,满足余热利用、节能降耗的清洁生产要求,生产工艺可达到国内先进水平,对余热的利用节省了能源的消耗,降低了因额外提供能源带来的化石燃料燃烧污染,属环境友好型生产工艺。
该工序废气污染源主要为沥青熔化槽和混捏机青烟废气(G2-3),项目采取沥青融化槽设置收集管道和混捏机顶部设置集气罩的方式收集沥青烟,收集的废气采用电捕焦油净化装置净化处理。
噪声污染源主要为泵类(N3)、风机(N7)、混捏机(N11)运行过程中产生的机械噪声。
固体废物污染源主要为电捕除尘器补给的废焦油灰(S4),为危险废物,送有资质的危险废物处置单位处置。
(3)压型冷却
混捏机混捏完成后的糊料通过排料管道排入液压成型机凉料槽,谅料槽周围设置冷却水盘管,将糊料冷却至軟化工艺温度80℃后,通过螺旋挤出装入压机具中。
本项目压机果用液压成型机,共设置2台,压力由液压系统提供,装有物料的坩埚模具在压机内压模压下成型,形成成型的坩埚.压制完成后模具内通入冷却水进一步冷却形成固态坩埚,
之后坩埚退出模具,形成成型坩埚产品,运至机加工车间机加工处理。
本项目压机自带模具,不进行压机模具的生产
该工序噪声污染源主要为液压成型机(N12)运行过程中产生的机械噪声;固体废物污染源主要为压机液压系統定期更换的废液压油(S5),为危险废物,送有资质的危险废物处置单位处置。
(4)机加工
成型坩埚出模具后,又车转运至机加工车间,采用磨床打磨边角,车床整形,镗床磨圆后即为成型坩埚产品,运至副产品库暂存外售或运至焙烧车间焙烧自用。
该工序废气污染源主要为打磨粉尘(G2-4),项目采取各加工工位设置集气理的方式收集废气,废气进入袋式除尘器净化处理。
噪声污染源主要为磨床(N13)、车床(MN14)、體床(N15)运行过程中产生的机械噪声;固体废物污染源主要为除尘器除尘灰(S2),作为原料利用。
本项目焙烧坩埚采用石墨化炉焙烧产出,以坩埚成型生产线成型坩埚为原料,以不同粒度的煅烧石油焦为保温料和电阻料,以冶金焦为填充料,采用石墨化炉进行焙烧,焙烧车间设置8台(1组)石墨化炉,焙烧温度1300℃。
生产工艺流程可分为装坩埚装炉焙烧冷却清炉等工序。
具体如下:
(1)装坩埚
装坩埚工序所用原料为成型坩埚和填充料,成型坩埚由机加工车间或副产品库叉至煅烧焙烧原料库,外购成品治金焦由吨包汽车外运暂存于煅烧焙烧原料库。
装坩埚过程在原料库内进行,设置两套负压吸料装锅系统。
采用负压吸料方式装坩埚,将治金焦装入坩埚内。
该工序废气污染源主要为负压装锅粉尘(G3-1),项目采取负压吸料,设置袋式除尘器净化处理。
噪声污染源主要为风机(N7)运行
过程中产生的机械噪声,固体废物污染源主要为袋式除尘器除尘灰(S2),作为原料利用。
(2)装炉
装有填充充料的坩埚采用行车装入石墨化炉膛内,装炉过程共分为三层,坩塌间距50mm,坩埚之间需填充的0~4m粒径煅烧石油焦作为保温料,电阻料外侧填充4一6m煅烧石油焦作为电阻料。
保温料和电阻料由煅烧车间成品料仓内装吨包叉车转运至焙烧车间。
装炉时,首先在电阻料和保温料界限位置装入一层钢板,之后采用行车吊运坩埚装第一层,之后采用行车直接吊运电阻料吨包,在钢板范围内装入一层电阻料,之后采用同样方式再装第二层和第三层。
坩埚和电阻料装炉完毕后采用同样的方式在钢板和炉壁之间装入保温料
为控制装炉过程中产尘量,装炉行车需将吨包下降至最低位置,减少落料高程,装炉过程中设置围挡,吨包卸完后及时人工平整压实不进行翻动等措施控制无组织排放。
该工序噪声污染源主要为行车(N5)运行过程中产生的机械噪声。
(3)焙烧
装炉完成后,加盖炉盖,启动供电系统送电,炉内坩埚、电阻料在电流作用下发热,温度逐渐升高,通过控制供电电压,使焙烧温度按照一定的升温曲线进行升温陪烧,升温陪烧温度达到1300℃后,停止供电,完成焙烧过程。
陪烧过程产生的焙烧烟气通过炉膛顶层负压收集通道收集,通道内设置点火装置使挥发份点火燃烧,烟气再经双碱法脱硫袋+式除尘后排放。
该工序废气污染源主要为坩埚焙烧烟气(G3-2),项目采取负压收集+点火燃烧+电捕焦油净化装置袋式除尘器十双碱法脱硫净化措施净化处理。
废水污
染源主要为脱硫浊环水(R6),部分循环使用,部分进入生产废水处理站处理。
噪声污染源主要为风机(N7)、泵类(M3)运行过程中产生的机械噪声。
固体废物污染源主要为袋式除尘器除尘灰(S2),作为原料利用;脱硫石膏(S3)送建材企业作为原料利用。
(4)冷却清炉
焙烧完成后的炉料自然冷却降温,8台烧炉交替运行。
降温时,物料由外向内逐步降温,炉顶保温料和电阻料温度降至60℃时,打开炉盖,通过行车将炉顶保温料和电阻料通过专用抓斗铲装出炉露出坩埚层,待坩塌层完全冷却后,用行车取出坩埚,之后依次清理第二层、第三层坩埚。
清出的保温料和电阻料通过行车抓斗铲装转运至车间内原料暂存间内分区暂存重复利用。
坩埚内治金焦通过负压卸锅系统吸出暂存于吨包内重复利用。
保温料、电阻料和填充料均可重复利用,烧过程中会有烧损,主要是硫份、挥发份、水分逸出和碳氧化生成二氧化碳逸出,烧损不足部分补充新料,焙烧坩埚采用又车运输至负极材料车间待用。
该工序废气污染源主要为负压卸锅粉尘(C3-3),项目采取负压吸料,设置袋式除尘器净化处理
(5)生产工艺先进行分析
目前,国内坩埚焙烧工艺对于清炉、卸炉基本无成型的污染治理描施,生产过程粉尘基本以无组织形式排放,大多数企业仍沿用原始的人工装料,该方法不可避免会产生大量的抛酒遗漏,粉尘产生量较大,本项目针对清炉、卸炉过程采取负压吸料,由手工装
料优化为自动化设备装料,同时通过降低落料高程、设置临时围挡的防止控制粉尘的无组织排放,经优化后一方面大大降低了粉尘的产生量,更有利于粉尘的收集处理,将无组织排放转化为有组织排放,清洁生产水平优于国内先进水平。
通过最大程度的将无组织排放
转化为有组织排放,尽最大可能降低了生产过程对周边环境的污染影响,属环境友好型生产工艺。