机器人误差分析
SLAM问题中机器人定位误差分析与控制
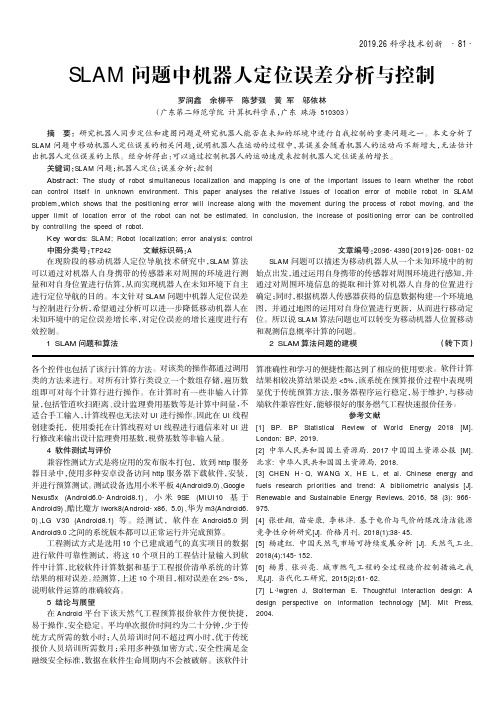
2019.26科学技术创新各个控件也包括了该行计算的方法。
对该类的操作都通过调用类的方法来进行。
对所有计算行类设立一个数组存储,遍历数组即可对每个计算行进行操作。
在计算时有一些非输入计算量,包括管道吹扫距离、设计监理费用基数等是计算中间量,不适合手工输入,计算线程也无法对UI 进行操作。
因此在UI 线程创建委托,使用委托在计算线程对UI 线程进行通信来对UI 进行修改来输出设计监理费用基数,税费基数等非输入量。
4软件测试与评价兼容性测试方式是将应用的发布版本打包,放到http 服务器目录中,使用多种安卓设备访问http 服务器下载软件,安装,并进行预算测试。
测试设备选用小米平板4(Android9.0)、Google Nexus5x (Android6.0-Android8.1)、小米9SE (MIUI10基于Android9)、酷比魔方iwork8(Android-x86,5.0)、华为m3(Android6.0)、LG V30(Android8.1)等。
经测试,软件在Android5.0到Android9.0之间的系统版本都可以正常运行并完成预算。
工程测试方式是选用10个已建成通气的真实项目的数据进行软件可靠性测试,将这10个项目的工程估计量输入到软件中计算,比较软件计算数据和基于工程报价清单系统的计算结果的相对误差。
经测算,上述10个项目,相对误差在2%-5%,说明软件运算的准确较高。
5结论与展望在Android 平台下该天然气工程预算报价软件方便快捷,易于操作,安全稳定。
平均单次报价时间约为二十分钟,少于传统方式所需的数小时;人员培训时间不超过两小时,优于传统报价人员培训所需数月;采用多种强加密方式,安全性满足金融级安全标准,数据在软件生命周期内不会被破解。
该软件计算准确性和学习的便捷性都达到了相应的使用要求。
软件计算结果相较决算结果误差<5%,该系统在预算报价过程中表现明显优于传统预算方法,服务器程序运行稳定,易于维护,与移动端软件兼容性好,能够很好的服务燃气工程快速报价任务。
工业机器人运动学标定及误差分析(精)
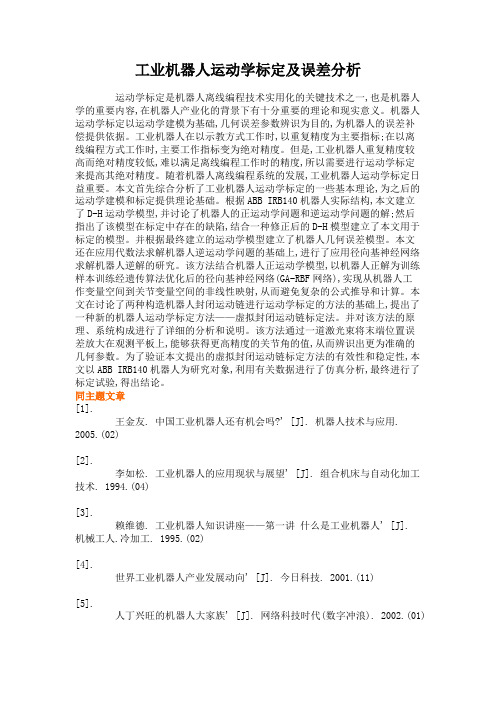
工业机器人运动学标定及误差分析运动学标定是机器人离线编程技术实用化的关键技术之一,也是机器人学的重要内容,在机器人产业化的背景下有十分重要的理论和现实意义。
机器人运动学标定以运动学建模为基础,几何误差参数辨识为目的,为机器人的误差补偿提供依据。
工业机器人在以示教方式工作时,以重复精度为主要指标;在以离线编程方式工作时,主要工作指标变为绝对精度。
但是,工业机器人重复精度较高而绝对精度较低,难以满足离线编程工作时的精度,所以需要进行运动学标定来提高其绝对精度。
随着机器人离线编程系统的发展,工业机器人运动学标定日益重要。
本文首先综合分析了工业机器人运动学标定的一些基本理论,为之后的运动学建模和标定提供理论基础。
根据ABB IRB140机器人实际结构,本文建立了D-H运动学模型,并讨论了机器人的正运动学问题和逆运动学问题的解;然后指出了该模型在标定中存在的缺陷,结合一种修正后的D-H模型建立了本文用于标定的模型。
并根据最终建立的运动学模型建立了机器人几何误差模型。
本文还在应用代数法求解机器人逆运动学问题的基础上,进行了应用径向基神经网络求解机器人逆解的研究。
该方法结合机器人正运动学模型,以机器人正解为训练样本训练经遗传算法优化后的径向基神经网络(GA-RBF网络),实现从机器人工作变量空间到关节变量空间的非线性映射,从而避免复杂的公式推导和计算。
本文在讨论了两种构造机器人封闭运动链进行运动学标定的方法的基础上,提出了一种新的机器人运动学标定方法——虚拟封闭运动链标定法。
并对该方法的原理、系统构成进行了详细的分析和说明。
该方法通过一道激光束将末端位置误差放大在观测平板上,能够获得更高精度的关节角的值,从而辨识出更为准确的几何参数。
为了验证本文提出的虚拟封闭运动链标定方法的有效性和稳定性,本文以ABB IRB140机器人为研究对象,利用有关数据进行了仿真分析,最终进行了标定试验,得出结论。
同主题文章[1].王金友. 中国工业机器人还有机会吗?' [J]. 机器人技术与应用. 2005.(02)[2].李如松. 工业机器人的应用现状与展望' [J]. 组合机床与自动化加工技术. 1994.(04)[3].赖维德. 工业机器人知识讲座——第一讲什么是工业机器人' [J].机械工人.冷加工. 1995.(02)[4].世界工业机器人产业发展动向' [J]. 今日科技. 2001.(11)[5].人丁兴旺的机器人大家族' [J]. 网络科技时代(数字冲浪). 2002.(01)[6].余力. 工业机器人在西班牙的应用' [J]. 管理科学文摘. 1994.(05)[7].曹祥康. 关于工业机器人产业化问题的思考' [J]. 机器人技术与应用. 2000.(01)[8].李瑞峰. 新一代工业机器人系列产品开发' [J]. 机器人. 2001.(S1)[9].王永林. 工业机器人技术概述与前瞻' [J]. 兵工自动化. 2004.(04)[10].刘远江. 中国工业机器人市场调查' [J]. 机器人技术与应用.2005.(02)【关键词相关文档搜索】:机械制造及其自动化; 工业机器人; 运动学标定; 绝对精度; 误差分析; GA-RBF网络; 虚拟封闭运动链【作者相关信息搜索】:上海交通大学;机械制造及其自动化;杨建国;夏天;。
工业机器人误差建模与分析

量#?*表示基于第 *关节坐标系的末端微分运动列矢量#该 式即为机器人运动误差传递模型&
"机器人误差参数仿真分析
根据表 $ 数据和式'$$( 误差模型使用 ?B7<BJ 进行分析#
将得到的末端位置误差运用 \=-79EBH<=法分别在各误差参
数独立作用 与 各 误 差 参 数 共 同 作 用 进 行 仿 真# 统 计 样 本 为
:科技风 ;<;= 年 ; 月
机械化工 !"#$%&$'(') *+&,-./&$01$21(3$&)%)$%3%'%
工业机器人误差建模与分析
梁 睿4李冬英4李 斌4王蒙宽
邵阳学院机械与能源工程系!湖南邵阳!A""BBB
摘4要当前工业机器人重复定位精度高一般都能达到 %&%$??以下绝对定位误差精度较低比重复定位精度高了 $2) 个数量级成为了制约工业机器人发展应用的主要因素首先利用矩阵法建立工业机器人误差模型再利用 \=-79EBH<=数值 仿真法运用控制变量法研究各连杆参数误差对机器人末端位置的影响仿真结果表明前三关节的关节转角误差和连杆扭 角误差对末端位置误差起到主导作用其余参数误差可以忽略不计
,=A**44 %44%4%
7)*
7C
*
79* 7**
'1(
考虑所有杆件误差后末端位姿矩阵为!
0L WMHX:M1 W( 6$ X:e$ ) ( 6) X:6) ) 1( 61 X:e1 ) '5( 将式'5( 展开后忽略高阶微分项得!
0
C0W(*W$6$1 161*Y$ C6*61*X$ 1601
机器人的误差鲁棒性分析与控制

机器人的误差鲁棒性分析与控制一直是机器人研究中的一个重要领域。
随着机器人技术的不断发展,人们对机器人系统的性能要求也越来越高。
在实际应用中,机器人系统可能会遇到各种干扰和噪声,这会导致机器人系统产生误差。
因此,研究机器人的误差鲁棒性分析与控制对于提高机器人系统的稳定性和鲁棒性具有重要意义。
机器人的误差主要包括建模误差、环境干扰和参数摄动等。
建模误差是由于对机器人系统进行建模时所做的近似和简化导致的误差。
环境干扰是由于外部环境的变化或不确定性引起的误差。
参数摄动是由于机器人系统参数的不确定性或变化导致的误差。
这些误差会对机器人系统的性能产生不利影响,因此需要进行误差鲁棒性分析与控制。
误差鲁棒性分析是指通过对机器人系统进行建模和分析,确定系统受到误差影响时的响应特性。
在误差鲁棒性分析中,一般会考虑系统的稳定性、收敛性、抗干扰能力和鲁棒性等性能指标。
通过对机器人系统误差的分析,可以评估系统对误差的敏感性,从而确定系统的误差鲁棒性。
误差鲁棒性控制是指通过设计合适的控制策略和算法,降低机器人系统对误差的敏感性,提高系统的鲁棒性和稳定性。
常用的误差鲁棒性控制方法包括鲁棒控制、自适应控制、滑模控制和神经网络控制等。
这些控制方法可以有效地抑制系统误差,提高系统对干扰和摄动的抵抗能力。
在机器人的误差鲁棒性分析与控制中,建模是一个极为关键的环节。
准确的模型可以帮助我们更好地理解系统的特性,设计更有效的控制策略。
建模误差和参数摄动是误差鲁棒性分析的主要难点之一。
如何准确地建立系统模型,如何有效地估计参数摄动,是需要认真研究和解决的问题。
另外,环境干扰也是机器人系统误差的重要来源。
环境干扰可能包括风力、摩擦力、重力等外部因素对机器人系统的影响。
针对不同类型的环境干扰,我们需要设计相应的控制策略来降低系统误差。
例如,可以采用自适应控制算法来对抗环境干扰,提高系统的鲁棒性。
在实际应用中,机器人系统常常需要在复杂和多变的环境下进行操作。
工业机器人运动学标定及误差分析研究
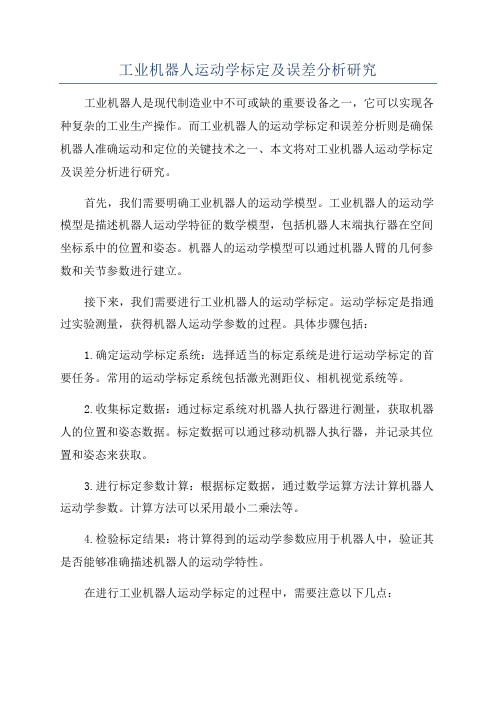
工业机器人运动学标定及误差分析研究工业机器人是现代制造业中不可或缺的重要设备之一,它可以实现各种复杂的工业生产操作。
而工业机器人的运动学标定和误差分析则是确保机器人准确运动和定位的关键技术之一、本文将对工业机器人运动学标定及误差分析进行研究。
首先,我们需要明确工业机器人的运动学模型。
工业机器人的运动学模型是描述机器人运动学特征的数学模型,包括机器人末端执行器在空间坐标系中的位置和姿态。
机器人的运动学模型可以通过机器人臂的几何参数和关节参数进行建立。
接下来,我们需要进行工业机器人的运动学标定。
运动学标定是指通过实验测量,获得机器人运动学参数的过程。
具体步骤包括:1.确定运动学标定系统:选择适当的标定系统是进行运动学标定的首要任务。
常用的运动学标定系统包括激光测距仪、相机视觉系统等。
2.收集标定数据:通过标定系统对机器人执行器进行测量,获取机器人的位置和姿态数据。
标定数据可以通过移动机器人执行器,并记录其位置和姿态来获取。
3.进行标定参数计算:根据标定数据,通过数学运算方法计算机器人运动学参数。
计算方法可以采用最小二乘法等。
4.检验标定结果:将计算得到的运动学参数应用于机器人中,验证其是否能够准确描述机器人的运动学特性。
在进行工业机器人运动学标定的过程中,需要注意以下几点:1.标定精度要求:根据具体需求,确定工业机器人的运动学标定精度。
标定精度要求越高,则标定过程中需要收集的数据越多。
2.标定环境准备:保证标定环境的准确度和稳定性。
避免干扰因素对机器人运动学参数的影响。
3.标定数据处理:在收集标定数据后,需要对数据进行处理,去除异常值和噪声,以提高标定结果的准确性。
4.标定误差分析:对标定结果进行误差分析,评估标定精度。
常见的误差包括位置误差、姿态误差等。
1.关节间隙误差:机器人的关节存在间隙,会导致机器人运动学参数的偏差。
因此需要对机器人关节间隙进行误差分析,以减小误差对机器人定位的影响。
2.传动误差:机器人关节传动装置存在误差,如传动精度和传动回差等。
串联机器人误差建模与精度标定方法研究

2023-10-29CATALOGUE 目录•引言•串联机器人误差建模•精度标定方法研究•实验与分析•结论与展望01引言串联机器人作为自动化生产中的重要组成部分,其精度和稳定性对生产过程具有重要影响。
目前,串联机器人在实际应用中存在不同程度的误差问题,这使得研究误差建模和精度标定方法具有重要意义。
研究背景与意义当前,针对串联机器人的误差建模和精度标定方法研究已取得一定成果。
然而,现有方法在精度、稳定性、实用性等方面仍存在不足,难以满足实际生产中对串联机器人精度的需求。
研究现状与问题研究内容与方法最后,对实验结果进行分析和讨论,提出改进措施以提高串联机器人的精度和稳定性。
然后,设计实验验证误差模型的准确性和精度标定方法的可行性。
其次,建立串联机器人的误差模型,包括几何误差模型和运动学误差模型。
本研究旨在开发一种高效、准确的串联机器人误差建模与精度标定方法。
首先,对串联机器人的结构和工作原理进行详细分析,为误差建模提供基础。
02串联机器人误差建模串联机器人误差来源分析由于制造过程中各种因素的影响,如材料、工艺、设备等,导致机器人各部件存在制造误差。
制造误差装配误差运动学误差环境因素机器人在组装过程中,由于零件之间的配合关系不准确,产生装配误差。
由于机器人运动学参数的不准确,如关节角度、关节偏移等,导致的运动学误差。
如温度、湿度、气压等环境因素的变化,对机器人的精度产生影响。
03误差传递矩阵通过建立误差传递矩阵,可以描述机器人各部件误差对末端执行器误差的影响程度。
基于多体系统理论的误差建模01多体系统理论多体系统理论是研究多个刚体或柔性体相互运动的力学理论,可用于串联机器人的误差建模。
02基于多体系统理论的误差建模方法利用多体系统理论建立机器人的误差模型,考虑了各部件之间的相互运动关系,能够更准确地描述机器人的误差行为。
通过实验验证误差模型的准确性和精度,对比分析实际运动轨迹与理论运动轨迹的差异。
实验验证参数优化自适应算法根据实验结果对误差模型进行参数优化,提高模型的预测精度和鲁棒性。
电力铁塔攀爬机器人位姿综合误差分析
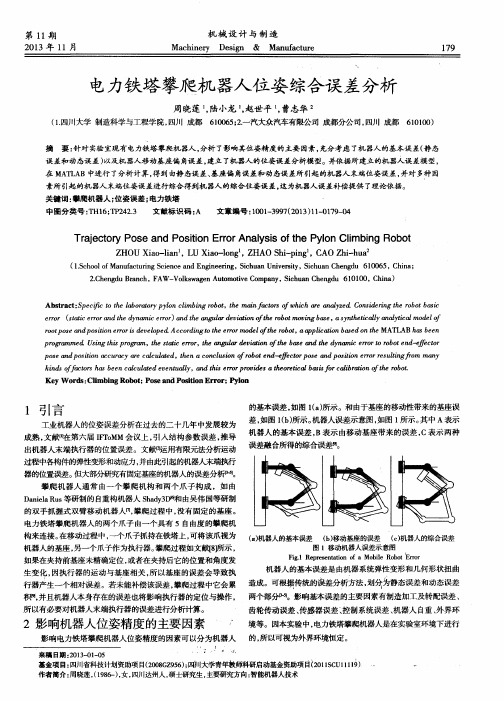
( 1 . S c h o o l o f M a n u f a c t u r i n g S c i e n c e a n d E n g i n e e r i n g , S i c h u a n U n i v e r s i t y , S i c h u a n C h e n g d u 6 1 0 0 6 5 , C h i n a ; 2 . C h e n g d u B r a n c h , F A W— V o l k s w a g e n A u t o m o t i v e C o m p a n y , S i e h u a n C h e n g d u 6 1 0 1 0 0 , C h i n a )
r o o t p o s e a n d p o s i t i o n e r r o r i s d e v e o l p e .A d c c o r d i n g t o t h e e r r o r od m el o ft h e r o b o t , a a p p l c i ti a o nb se a do n t e h M A T L A B h a s b e e n
T r a j e c t o r y P o s e a n d P o s i t i o n E r r o r A n a l y s i s o f t h e P y l o n C l i mb i n g R o b o t
定位噪声下机器人轨迹跟踪与编队误差分析
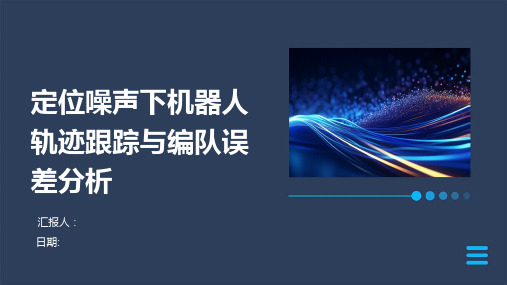
基于卡尔曼滤波的编队误差校正算法设计
算法流程
状态预测
首先对机器人编队的位姿进行初始估计, 然后利用卡尔曼滤波器对位姿进行实时校 正,以减小编队误差。
测量更新
根据机器人运动学模型和传感器测量数据 ,对机器人位姿进行预测。
反馈控制
利用卡尔曼滤波器对预测值进行更新,并 考虑测量噪声的影响。
根据实验结果对算法性能进行评估,包括估计误差、响应速度、鲁 棒性等方面。
06
实验结果与讨论
实验环境与参数设置
实验场地:室内实验场地,长10米,宽 8米。
定位噪声水平:根据不同实验组别,定 位噪声水平有所不同。
通信协议:无线通信,传输距离100米 。
机器人数量:5个。
传感器配置:每个机器人配备激光雷达 和GPS传感器。
编队情况下,高定位噪声对机 器人轨迹跟踪误差的影响更为 显著,这可能与编队中机器人 的协同作业有关。
07
结论与展望
研究成果总结
建立了定位误差模型 本研究通过建立定位误差模型, 对机器人定位误差进行了定量分 析,为后续轨迹跟踪和编队控制 提供了基础。
验证了算法的有效性 通过实验验证了所提算法在定位 误差、轨迹跟踪和编队控制方面 的有效性,证明了本研究的成果 。
编队误差模型
机器人定位误差
由于传感器和导航系统的限制,每个机器人可能存在定位误差。这种误差可能导 致编队形状的不稳定和偏离期望轨迹。
通信延迟
在分布式控制系统中,机器人之间的通信可能存在延迟,这可能导致编队中的机 器人不同步或出现碰撞。
Hale Waihona Puke 差补偿算法设计反馈控制反馈控制是一种常用的误差补偿方法,其中机器人的输出通 过反馈回路与期望输出进行比较,并产生修正误差的输出。 这种控制方法可以有效地减小跟踪误差和干扰的影响。
《田间机器人的双目视觉系统误差分析研究》范文
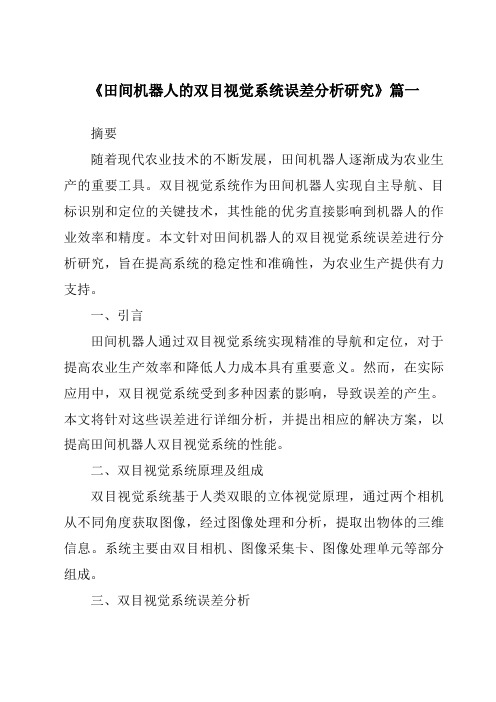
《田间机器人的双目视觉系统误差分析研究》篇一摘要随着现代农业技术的不断发展,田间机器人逐渐成为农业生产的重要工具。
双目视觉系统作为田间机器人实现自主导航、目标识别和定位的关键技术,其性能的优劣直接影响到机器人的作业效率和精度。
本文针对田间机器人的双目视觉系统误差进行分析研究,旨在提高系统的稳定性和准确性,为农业生产提供有力支持。
一、引言田间机器人通过双目视觉系统实现精准的导航和定位,对于提高农业生产效率和降低人力成本具有重要意义。
然而,在实际应用中,双目视觉系统受到多种因素的影响,导致误差的产生。
本文将针对这些误差进行详细分析,并提出相应的解决方案,以提高田间机器人双目视觉系统的性能。
二、双目视觉系统原理及组成双目视觉系统基于人类双眼的立体视觉原理,通过两个相机从不同角度获取图像,经过图像处理和分析,提取出物体的三维信息。
系统主要由双目相机、图像采集卡、图像处理单元等部分组成。
三、双目视觉系统误差分析1. 相机标定误差:相机标定是双目视觉系统的关键步骤,标定误差会导致图像的畸变和失真,进而影响三维信息的提取。
2. 光照条件变化:光照条件的变化会导致图像的亮度、对比度和色彩等信息发生变化,从而影响双目视觉系统的匹配精度。
3. 遮挡和干扰物:田间环境中存在大量的遮挡物和干扰物,如杂草、土堆等,这些物体的存在会影响双目相机的匹配过程,导致误差的产生。
4. 图像处理算法:图像处理算法的优劣直接影响到双目视觉系统的性能。
算法的不稳定性和不准确性会导致匹配误差和定位误差的产生。
四、误差解决方案1. 优化相机标定方法:采用高精度的相机标定方法,减少标定误差,提高图像的畸变和失真校正效果。
2. 增强光照条件适应性:通过改进相机和图像处理算法,提高双目视觉系统对光照条件变化的适应性,减少光照条件变化对匹配精度的影响。
3. 抗遮挡和干扰物设计:通过改进匹配算法和增加传感器等手段,提高双目视觉系统对遮挡物和干扰物的抗干扰能力,减少误差的产生。
全方位装配机器人的刚度误差分析

第4期2021年4月机械设计与制造Machinery Design&M anufacture287全方位装配机器人的刚度误差分析叶长龙,万缯齐,于苏洋,姜春英(沈阳航空航天大学机电工程学院,辽宁沈阳110136)摘要:为了提高工作效率并节约劳动力,设计了一种可执行装配任务的全方位装配机器人,此机器人能在实际工程中 执行一些简单的装配任务。
为提高机器人在执行装配作业任务时的装配精度,对其刚度误差进行分析。
根据机器人的结 构特点并结合旋量理论对并联机构各支链进行建模,推导出机器人的刚度模型。
通过仿真分析得出了支链长度以及载荷 对系统刚度的理论影响。
结合实验测试对刚度矩阵进行修正,得出不同姿态下系统刚度引起的误差。
详细分析误差的产 生的原因,提出了减小误差的改进方案。
关键词:装配精度;刚度分析;旋量理论;误差分析中图分类号:T H16;TP242文献标识码:A文章编号:1001-3997(2021 )04-0287_06Stiffness Error Analysis of an Omni-Directional Assembly RobotYE Chang-long, WAN Zeng-qi, YU Su-yang, JIANG Chun-ying(S c h o o l o f M e c h a t r o n i c s E n g i n e e r i n g Shenyang Ae ro spa ce U n i v e r s i t y,L i a o n i n g Shenyang110136,China)Abstract:7/i order to improve work efficiency and save labor^an omni-directional assembly robot that can perform assembly tasks is designed.The robot can perform some simple assembly tasks in actual engineering.In order to improve the assembly precision of robot in the execution of assembly tasks,the stiffness error is analyzed.A ccording to the structural characteristics of t he robot and the theory of s crew^the branches of the parallel mechanism are modeled,and the stiffness model o f the robot is derived.Through the simulation analysis ythe theoretical influence of the length of the branch and the load on the stiffness of the system is obtainedThe stiffness matrix is modified by combining experimental tests to obtain the error caused by the system stiffness under different attitudes.A detailed analysis of the causes of the error is presented jcuid an improved scheme for reducing the error is proposedKey Words: Assembly Accuracy;Stiffness Analysis;Screw Theory;Error Analysisl引言机器人以其多功能性以及良好的适应性被广泛应用于生产 实践中。
工业机器人编程技巧与误差分析

工业机器人编程技巧与误差分析工业机器人是现代制造业中的重要设备,在生产线上扮演着关键的角色。
工业机器人编程是确保机器人正常运行、完成各项生产任务的重要环节。
本文将介绍一些工业机器人编程的技巧,并分析常见的误差问题及其解决方案。
一、工业机器人编程技巧1. 合理的姿态选择:在编程过程中,选择合适的机器人姿态对于实现任务的精确性和效率至关重要。
合理的姿态选择可以避免机器人在操作过程中发生碰撞或增加误差。
在进行工业机器人编程时,需要根据具体任务的要求,确定机器人的姿态,包括机器人的位置、角度和方向等。
同时,还需要考虑到机器人的动作范围和工作环境的限制,以确保机器人能够顺利完成任务。
2. 路径规划:路径规划是工业机器人编程中的关键步骤。
通过合理地规划机器人的运动轨迹,可以减少机器人运动路径的长度,提高编程效率。
路径规划还可以避免机器人在运动过程中发生碰撞或碰撞风险,从而确保生产过程的安全性。
在路径规划过程中,可以使用各种算法和方法,例如最短路径算法、曲线拟合算法和直线插补算法等。
选择合适的路径规划算法可以提高机器人的精确性和运动效率。
3. 多点编程:多点编程是一种常用的工业机器人编程技巧,可以使机器人按照预定的路线依次执行各个任务点,从而提高生产效率。
在多点编程中,需要依次指定机器人的目标位置,并确定各个点之间的路径和运动方式。
多点编程可以通过机器人编程软件实现,通过添加和编辑任务点,可以灵活地进行生产任务的调整和管理。
4. 动作组编程:动作组编程是工业机器人编程的一种重要技巧,可以使机器人完成复杂的运动任务。
在动作组编程中,需要将不同的动作和运动组合在一起,形成一个完整的运动序列,并确保各个动作之间的协调和同步。
动作组编程可以增加机器人的灵活性和生产能力,适用于一些复杂的装配、喷涂和搬运等任务。
二、工业机器人误差分析及解决方案1. 位置误差:位置误差是工业机器人运动过程中常见的误差之一。
位置误差可能由于机器人位置检测的不准确性或机械结构的松动等原因导致。
机器人位姿误差的分析与综合共3篇
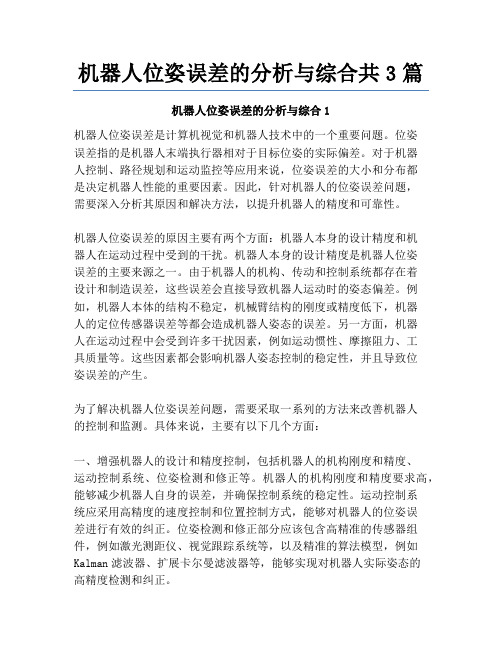
机器人位姿误差的分析与综合共3篇机器人位姿误差的分析与综合1机器人位姿误差是计算机视觉和机器人技术中的一个重要问题。
位姿误差指的是机器人末端执行器相对于目标位姿的实际偏差。
对于机器人控制、路径规划和运动监控等应用来说,位姿误差的大小和分布都是决定机器人性能的重要因素。
因此,针对机器人的位姿误差问题,需要深入分析其原因和解决方法,以提升机器人的精度和可靠性。
机器人位姿误差的原因主要有两个方面:机器人本身的设计精度和机器人在运动过程中受到的干扰。
机器人本身的设计精度是机器人位姿误差的主要来源之一。
由于机器人的机构、传动和控制系统都存在着设计和制造误差,这些误差会直接导致机器人运动时的姿态偏差。
例如,机器人本体的结构不稳定,机械臂结构的刚度或精度低下,机器人的定位传感器误差等都会造成机器人姿态的误差。
另一方面,机器人在运动过程中会受到许多干扰因素,例如运动惯性、摩擦阻力、工具质量等。
这些因素都会影响机器人姿态控制的稳定性,并且导致位姿误差的产生。
为了解决机器人位姿误差问题,需要采取一系列的方法来改善机器人的控制和监测。
具体来说,主要有以下几个方面:一、增强机器人的设计和精度控制,包括机器人的机构刚度和精度、运动控制系统、位姿检测和修正等。
机器人的机构刚度和精度要求高,能够减少机器人自身的误差,并确保控制系统的稳定性。
运动控制系统应采用高精度的速度控制和位置控制方式,能够对机器人的位姿误差进行有效的纠正。
位姿检测和修正部分应该包含高精准的传感器组件,例如激光测距仪、视觉跟踪系统等,以及精准的算法模型,例如Kalman滤波器、扩展卡尔曼滤波器等,能够实现对机器人实际姿态的高精度检测和纠正。
二、改进机器人运动的控制算法和结构,包括路径规划、运动监测和控制器设计等。
针对机器人运动的过程中,偏差和干扰干扰因素的影响,应该采用自适应的控制算法来对机器人进行实时控制。
限制关节智能控制方法应该采用过程伺服控制,通过运动监测对机器人的位置变化进行实时补偿,并优化控制器的设计,提高控制器的精度和反应速度。
探讨机器人的误差分析

探讨机器人的误差分析通常工业机器人的精准度是由机器人的手部工作执行器的位置与姿态误差来表述的,它是反映机器人工作性能的主要指标之一。
现阶段学者们针对机器人误差方面的研究主要可以分成这几个方面:一个是对机器人误差进行理论上的预测,一个是进行实验来分析机器人误差的起因、程度,还有一类是专门针对如何避免或者减少机器人误差而进行的补偿技术的研究。
现阶段主要是运用建立在机器人正运动学的解的基础之上的分析方法来进行机器人手部工作执行器的位置和姿态的静态误差分析。
一般通过矢量算法和矩阵算法,在机器人机构参数已知,包括杆长参数值已知,关节孔心距值已知和设置初始制造误差值的情况下,对累积到手部的位置和姿态的误差值进行分析和研究。
这种分析方法一般情况下是将整个机构想象成刚体来进行的,故这种方法不考虑机构在运动过程中发生的形变,只是讨论分析其运动改变量引起的误差和机构长度等参数引起的误差。
机器人误差问题的提出是在工业机器人诞生二十多年之后,由 A.Kuman和K.J.Waldron在1978年首次提出机器人位置误差问题。
第二年,他们在第五届国际机构学与机器科学世界大会(IFToMM)上又对机器人的位置精度的分析研究提出了一种比较完整的方法。
A.Kuman和K.J.Waldron在Denavit-Hartenberg的坐标系中采用了两个3x3变换矩阵与一个三维的平移的列矢量组成了相邻构件间的坐标变换矩阵,其中假设研究对象的结构参数是已知的,而且不存在误差,以此为基础建立了机器人末端执行器的位置误差的表达式。
在1983年的第六届国际机构学与机器科学世界大会上,帕拉卡什和库曼将机器人机构的长度,关节孔心距等误差考虑到了整体误差模型中,并推导出了其模型的表达式。
1984年时,吴奇壕把保罗的机器人机构的运动分析的方法运用到静态误差的分析之中,推导出了因构件的结构参数的误差和关节运动变量的误差而引起的机器人手部工作单元在笛卡尔空间相对于整体坐标系的位置误差改变的趋势。
工业机器人原点误差分析与补偿江俊林

工业机器人原点误差分析与补偿江俊林发布时间:2023-07-04T05:38:15.916Z 来源:《科技新时代》2023年8期作者:江俊林[导读] 机器人的相对定位精度是工业生产机器人的一个非常重要的特征。
机器人动力学主要参数的标定可以提高相对定位精度,因此在学术界和工业界都进行了大量的科学研究。
校准主要动态参数所需的主要参数包括关节扭转角、关节偏移和曲轴长度,这些参数通常与机器人本身的机械系统有关。
校准后的机器人在制造区运输和安装后,主要参数不会发生太大变化。
然而,在使用机器人的过程中,机器人的起点可能存在误差,这可能会导致许多问题,如上位机软件的基本理论计算模型与实际工业模型不一致、精度降低以及专用工具平面坐标校准中的误差。
身份证号:36012119741108XXXX 摘要:机器人的相对定位精度是工业生产机器人的一个非常重要的特征。
机器人动力学主要参数的标定可以提高相对定位精度,因此在学术界和工业界都进行了大量的科学研究。
校准主要动态参数所需的主要参数包括关节扭转角、关节偏移和曲轴长度,这些参数通常与机器人本身的机械系统有关。
校准后的机器人在制造区运输和安装后,主要参数不会发生太大变化。
然而,在使用机器人的过程中,机器人的起点可能存在误差,这可能会导致许多问题,如上位机软件的基本理论计算模型与实际工业模型不一致、精度降低以及专用工具平面坐标校准中的误差。
关键词:工业机器人;原点误差;补偿措施1工业机器人原点误差产生原因工业生产机器人是一种健身运动致动器,由多个部件和旋转关节串联而成。
它可以根据移动端执行器的指定位置完成所需的工作。
由于安装误差、曲轴和关节的变形、运动对之间的摩擦及其环境温度以及末端负载的变化等各种因素,机器人末端执行器的具体到达位置和基本理论位置之间也会存在一些误差,从而产生机器人的起点误差。
根据各种误差要素的成因,危害机器人相对定位精度的误差要素可分为关节误差要素、几何误差要素和非几何误差要素。
abb 机器人 工具坐标 误差

abb 机器人工具坐标误差ABB机器人是工业自动化领域中常见的机器人品牌之一,其具有高精度、高效率和高可靠性的特点。
然而,由于各种因素的影响,ABB 机器人在使用过程中可能会出现工具坐标误差的问题。
本文将就ABB机器人工具坐标误差进行分析和讨论。
我们需要了解什么是ABB机器人的工具坐标。
工具坐标是指机器人末端执行器(工具)相对于机器人基坐标系的位置和姿态信息。
在ABB机器人中,通常使用笛卡尔坐标系(XYZ坐标系)来描述工具坐标。
工具坐标的准确性对于机器人的精度和稳定性至关重要。
工具坐标误差主要分为两个方面,即位置误差和姿态误差。
位置误差是指实际工具位置与期望工具位置之间的差异,而姿态误差是指实际工具姿态与期望工具姿态之间的差异。
这些误差可能会导致机器人在工作过程中无法精确地完成所需的任务,甚至可能造成产品质量问题。
造成ABB机器人工具坐标误差的因素有很多,下面我们将逐一进行分析。
首先是机器人本身的因素。
ABB机器人由许多零部件组成,如关节、传感器、执行器等。
这些零部件之间的装配精度和磨损程度都会对工具坐标的准确性产生影响。
另外,机器人的刚度和结构稳定性也会对工具坐标误差产生影响。
如果机器人的刚度较低或结构不稳定,就会导致工具坐标的变化,进而影响机器人的精度。
其次是环境因素。
环境因素包括温度、湿度、震动等因素。
温度变化会导致机器人零部件的热膨胀或收缩,从而引起工具坐标的变化。
湿度和震动也会对机器人的精度和稳定性产生影响,进而影响工具坐标的准确性。
第三是操作人员的因素。
操作人员在使用ABB机器人时需要进行编程、调试和维护等操作。
如果操作人员在编程或调试过程中存在错误或不当操作,就有可能导致工具坐标的误差。
因此,操作人员需要接受专业培训,掌握正确的操作方法和技巧,以减小工具坐标误差的发生。
最后是外部干扰因素。
外部干扰因素包括电磁干扰、电源波动等。
电磁干扰可能会影响机器人的传感器和执行器的工作,进而影响工具坐标的准确性。
机器人误差分析
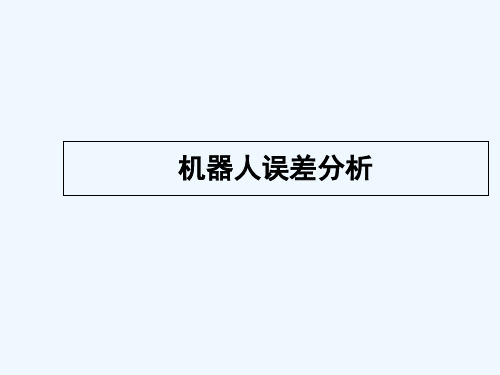
机器人手部相对于机座坐标系的平移误差和旋转误差就相当于微分平移 矢量和旋转矢量,即
d0=0.1i+0j+0.05k,
&0=0i+0j+0.01k0.01 0 0.1 0 0 0 0 0.05 0 0 1 0 0 0.05 0 0 1 0 1 10 0 0 0 5 0 1 0 0
0.01 0
由此可得机器人手部位姿的为偏差为 0 -0.01 0 0.1 dM02=J0M02= 0.01 0 0 0 -0.01 = 0 0 0 0 0 0 0 0 0.05 0 0 0
0.01 0.1
0
0
0
0
0
0
0.05
0
10
感谢您的关注
4
机器人误差模型概 述
由于机器人的误差包括系统误差与随机误差,因此也就相应的产生了 概率型和常规模型两类建模方式。 概率模型用随机变量描述误差源,建立机器人机构运动模型。进而通 过积或Monte Carlo方法,求解机器人对于指定的误差范围,其手部被 定位于该范的概率值,然后绘制出机器人工作空间某一截面上的概率 等值曲线,以了解机人末端位姿误差的分布规律。 常规模型则是根据误差源本身所遵循的物理规律和机器人运动方程, 直接者间接地求解出机器人末端的误差模型。根据误差源本身的特性, 常规模型又以分为静态误差模型和动态误差模型。在机器人静态建模 方面,一般是把静态差因素作为相应变量的微小量,利用机构运动学 分析方法,推导出机器人静态差的数学模型。文献利用微分法,通过 误差传递矩阵给出了机器人末端位的数学模型,并基于这一模型编程 计算了位姿精度的概率等高线。文献提了通过直接对各个误差的微小 位移矢量进行合成,建立手部位姿误差数学模型微小位移合成法。更 常用的方法是在D-H坐标下,通过对机器人的4×4齐次换矩阵求偏导, 建立起误差模型。但是,这种建模方法有一个严重的缺点就是机器人 本体含有两个连续的平行连杆时,微小误差模型就不再适用了。
协作机器人技术的误差校正与补偿技巧

协作机器人技术的误差校正与补偿技巧随着科技的不断发展,机器人在各个领域的运用越来越广泛,其中协作机器人成为了研究热点。
协作机器人是指能够与人类进行安全而高效的合作工作的机器人。
然而,由于制造和使用过程中存在的各种因素,协作机器人的运动轨迹可能会产生误差。
为了保证机器人的精确工作,误差校正与补偿技巧成为了协作机器人技术中重要的一环。
一、误差校正技巧1. 重复定位在机器人执行任务时,定位精度对于保证工作的精确性至关重要。
重复定位是一种通过不断测试与调整来校正机器人定位误差的方法。
具体而言,通过对同一位置进行多次定位并记录误差,分析其规律并进行校正,可以提高机器人的定位精确度。
2. 执行反馈控制执行反馈控制是指机器人在执行任务过程中通过传感器实时获取执行结果,并将结果反馈给控制系统的一种技术手段。
通过分析反馈数据,可以判断机器人执行任务时是否存在误差,并及时做出校正。
例如,当机器人与人类进行协作时,如果机器人的位置偏离了预定的轨迹,可以通过对机器人的位置进行调整,使其与人类的动作更为协调。
3. 校正模型建立校正模型的建立是一种较为复杂的误差校正技巧。
通过对机器人系统的建模与分析,可以得到机器人系统的误差模型,并据此进行误差的校正。
例如,可以通过建立运动学或动力学模型,将机器人的运动误差进行建模,并通过对模型参数的校正来实现误差的补偿。
二、补偿技巧1. 摩擦力补偿在机器人的运动过程中,摩擦力是不可避免的因素之一,会对机器人的运动轨迹产生影响。
因此,补偿摩擦力是改善机器人运动精度的一种重要技巧。
摩擦力补偿可以通过增加机器人的驱动力或通过控制算法来抵消摩擦力的影响,从而实现机器人运动的准确性。
2. 温度补偿温度是影响机器人运动精确度的重要因素之一。
随着机器人系统的长时间运行,温度的变化会导致机械部件的膨胀或收缩,从而影响机器人的精确性。
因此,通过设置传感器来实时监测机器人系统的温度,并根据温度变化对机器人的运动进行补偿,可以有效减少温度对机器人运动的影响。
机器人示教误差成因分析及消除
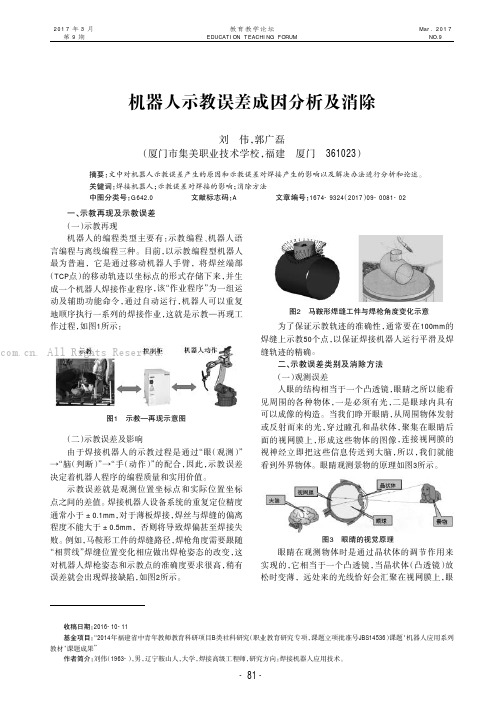
机器人示教误差成因分析及消除收稿日期:2016-10-11基金项目:“2014年福建省中青年教师教育科研项目B 类社科研究(职业教育研究专项,课题立项批准号JBS14536)课题‘机器人应用系列教材’课题成果”作者简介:刘伟(1963-),男,辽宁鞍山人,大学,焊接高级工程师,研究方向:焊接机器人应用技术。
一、示教再现及示教误差(一)示教再现机器人的编程类型主要有:示教编程、机器人语言编程与离线编程三种。
目前,以示教编程型机器人最为普遍,它是通过移动机器人手臂,将焊丝端部(TCP 点)的移动轨迹以坐标点的形式存储下来,并生成一个机器人焊接作业程序,该“作业程序”为一组运动及辅助功能命令,通过自动运行,机器人可以重复地顺序执行一系列的焊接作业,这就是示教—再现工作过程,如图1所示:(二)示教误差及影响由于焊接机器人的示教过程是通过“眼(观测)”→“脑(判断)”→“手(动作)”的配合,因此,示教误差决定着机器人程序的编程质量和实用价值。
示教误差就是观测位置坐标点和实际位置坐标点之间的差值。
焊接机器人设备系统的重复定位精度通常小于±0.1mm ,对于薄板焊接,焊丝与焊缝的偏离程度不能大于±0.5mm ,否则将导致焊偏甚至焊接失败。
例如,马鞍形工件的焊缝路径,焊枪角度需要跟随“相贯线”焊缝位置变化相应做出焊枪姿态的改变,这对机器人焊枪姿态和示教点的准确度要求很高,稍有误差就会出现焊接缺陷,如图2所示。
为了保证示教轨迹的准确性,通常要在100mm 的焊缝上示教50个点,以保证焊接机器人运行平滑及焊缝轨迹的精确。
二、示教误差类别及消除方法(一)观测误差人眼的结构相当于一个凸透镜,眼睛之所以能看见周围的各种物体,一是必须有光,二是眼球内具有可以成像的构造。
当我们睁开眼睛,从周围物体发射或反射而来的光,穿过瞳孔和晶状体,聚集在眼睛后面的视网膜上,形成这些物体的图像,连接视网膜的视神经立即把这些信息传送到大脑,所以,我们就能看到外界物体。
机器人传动误差诊断

机器人传动误差诊断机器人传动误差诊断机器人传动误差诊断是一项重要的任务,可以帮助我们准确地确定机器人传动系统中存在的问题。
以下是一个逐步思考的过程,用于诊断机器人传动误差的步骤。
第一步:观察和记录机器人的运动表现观察机器人在运动过程中是否存在异常,例如运动速度突然变慢或快,或者运动轨迹有明显的偏差。
记录下这些观察结果,将它们作为后续分析的依据。
第二步:检查机器人传动系统的主要部件仔细检查机器人传动系统的主要部件,包括电动机、减速器和传动带/链等。
检查它们是否存在明显的损坏或松动。
确保所有连接件都牢固,并且没有明显的物理损伤。
第三步:测量机器人传动系统的运动参数使用合适的设备测量机器人传动系统的运动参数,例如速度、位置和加速度。
将这些数据与理论值进行比较,以确定是否存在明显的误差。
第四步:分析测量数据仔细分析测量数据,寻找任何异常或不一致之处。
比较不同时间点的测量结果,看是否存在明显的变化。
如果发现数据存在较大偏差,这可能意味着机器人传动系统存在问题。
第五步:排除其他因素的可能性除了机器人传动系统本身的问题外,还需要考虑其他可能的因素,例如环境因素或其他机器人部件的故障。
排除这些因素的可能性,以确保诊断结果的准确性。
第六步:修复或更换有问题的部件根据诊断结果,确定机器人传动系统中具体存在问题的部件。
尝试修复这些部件,例如紧固松动的连接件或更换损坏的部件。
在更换部件时,确保选择合适的替代品,并按照制造商的指示进行安装。
第七步:重新测试机器人运动表现在修复或更换有问题的部件后,重新测试机器人的运动表现。
与之前的测量结果进行比较,看是否有明显的改善。
如果机器人的运动表现仍然存在问题,可能需要重新评估和调整机器人传动系统的其他部分。
通过逐步的思考和分析,我们可以准确地诊断机器人传动误差,并采取适当的措施进行修复。
这有助于提高机器人的运动精度和稳定性,确保其正常运行。
- 1、下载文档前请自行甄别文档内容的完整性,平台不提供额外的编辑、内容补充、找答案等附加服务。
- 2、"仅部分预览"的文档,不可在线预览部分如存在完整性等问题,可反馈申请退款(可完整预览的文档不适用该条件!)。
- 3、如文档侵犯您的权益,请联系客服反馈,我们会尽快为您处理(人工客服工作时间:9:00-18:30)。
= &z 0 -&x dy
-&y &x 0 dz
0 00 0 因此,J可看成是有&和d两个矢量组成的,&称为微分旋转矢量,d称为微分平移矢量,分别表示为
&=&xi+&yj+&zk
d=dxi+dyj+dzk &和d合称为微分运动矢量,用D表示为
dx
dy D = dz
d
或
D=
&x
&
&y
&z
Page ▪ 7
7
已知一个二自由度机器人及其坐标系,如下图所示。
误差计算
图1 二自由度机器人手部的微分变化
Page ▪ 8
ቤተ መጻሕፍቲ ባይዱ
8
若因杆件1下关节轴承装配或制造不当,使杆件1沿关节轴线有0.05单位 的偏差,又由于两杆件的执行器运动不准确,旋转执行器使杆件1多转 一个0.01rad的偏差角,移动执行器使杆件2移动了一个0.1单位的偏差 距离。若杆件1的长度L1=5单位,试求当机器人关节变量取O1=90度, d2=10单位时,机器人手部位姿的偏差。
J0= 0.01 0 0 0 0 0 0 0.05 0 00 0
由此可得机器人手部位姿的为偏差为 0 -0.01 0 0.1
dM02=J0M02= 0.01 0 0 0 0 0 0 0.05 0 000
00 10 01 00
1 10 05 00 01
-0.01 0 0 0.05 = 0 0 0.01 0.1
Page ▪ 3
3
机器人误差分类
▪ 按照误差的来源和特性,可将它们分为不同的类型。从误差的来源来看,主要是指机械 零件、部件的制造误差、整机装配误差、机器人安装误差,还包括温度、负载等的作用 使得机器人杆件产生的变形,传动机构的误差,控制系统的误差(如插补误差、伺服系 统误差、检测元器件)等。我们将与机器人几何结构有关的机械零件、部件的制造误差、 整机装配误差、机器人安装误差、关节编码器的电气零点通常和关节的机械零点不相一 致等因素引起的误差称为几何误差。
Page ▪ 6
6
微分变换矩阵
由微分变换矩阵J=trans(dx,dy,dz)Rot(k,do)-I的定义可以看出,它包含了微分平移和微分旋转 两个变换。
经推导得出,微分变换矩阵为
J=[trans(dx,dy,dz)Rot(x,&x)Rot(y,&y)Rot(z,&z)-I]
0 -&z &y dx
机器人误差分析
机器人重复精度
▪ 重复精度是在到达同一组关节角的重复指令控制下,末端执行器以一 定的姿态到达一定位置的准确度。按ISO标准描述,在对每个目标点的 多次测量时,存在一个实际测定点的系列分布,通过对其分布的标准 偏差计算(多次,累积∑),就可以定义这一分布。一个±3次标准偏 差(记做±3σ——亦即共6σ)可以覆盖无限个实际点中99.74%的位置 分布情形。这个发散度即称作重复精度,它是指某一指定目标点处的 重复精度。
▪ 则从杆件坐标系i-1到i杆件坐标系i的齐次变换为:
▪ Ai=Rot (θi)Trans (ai) Trans( d i)Rot (αi)Rot(βi)
▪ 众所周知,机器人各杆件的制造、安装过程必然使得其参数的名义值与实际
▪ 相应参数值是有微小偏差的。我们用δai、δαi、δdi、δβi和δθi来表示这些杆件 参数误差。如果杆件有转动关节副,则δai、δαi、δdi和δβi是恒量偏差,而δθi 是码盘偏差。前四个恒量偏差具体表现为关节之间相互位置与名义值不符,码 盘偏差也就是关节的实际零位与编码盘的零位不重合。
Page ▪ 4
4
机器人误差模型概 述
▪ 由于机器人的误差包括系统误差与随机误差,因此也就相应的产生了 概率型和常规模型两类建模方式。
▪ 概率模型用随机变量描述误差源,建立机器人机构运动模型。进而通 过积或Monte Carlo方法,求解机器人对于指定的误差范围,其手部被 定位于该范的概率值,然后绘制出机器人工作空间某一截面上的概率 等值曲线,以了解机人末端位姿误差的分布规律。
▪ 根据误差特性来分,又可将误差分为确定性误差、时变误差和随机性误差三种。确定性 误差不随时间变化,可以事先进行测量,如之前提到的几何误差就属于这一类。时变误 差又可分为缓变和瞬变两类,如因为温度产生的热变形随时间变化很慢,属于缓变误差; 而运动轴相对于数控指令间存在的跟踪误差取决于运动轴的动态特性,并随时间变化, 属于瞬变误差。随机性误差事先无法精确测量,只能利用统计学的方法进行估计,如外 部环境振动就是一种十分典型的随机性误差。
▪ 按影响类型可分为静态误差和动态误差。前者主要包括连杆尺寸变化、齿轮磨损、关节 柔性以及连杆的弹性弯曲等引起的误差;后者主要为振动引起的误差。
▪ 在诸多影响机器人精度的因素中,几何误差要占据80%左右的比例,因此机器人运动学 标定主要研究制造误差、安装误差、编码器零位误差等造成的几何误差。事实上,由于 在参数识别和补偿中通常使用最小二乘拟合方法,而所使用的数据同时受到所有误差的 影响,所以没有必要单独考虑其它因素的影响。
0 0 0 0.05 0 00 0
Page ▪ 10
10
感谢您的关注
▪ 常规模型则是根据误差源本身所遵循的物理规律和机器人运动方程, 直接者间接地求解出机器人末端的误差模型。根据误差源本身的特性, 常规模型又以分为静态误差模型和动态误差模型。在机器人静态建模 方面,一般是把静态差因素作为相应变量的微小量,利用机构运动学 分析方法,推导出机器人静态差的数学模型。文献利用微分法,通过 误差传递矩阵给出了机器人末端位的数学模型,并基于这一模型编程 计算了位姿精度的概率等高线。文献提了通过直接对各个误差的微小 位移矢量进行合成,建立手部位姿误差数学模型微小位移合成法。更 常用的方法是在D-H坐标下,通过对机器人的4×4齐次换矩阵求偏导, 建立起误差模型。但是,这种建模方法有一个严重的缺点就是机器人 本体含有两个连续的平行连杆时,微小误差模型就不再适用了。
Page ▪ 5
5
机器人几何误差模 型
▪ 由于讨论的是理论上的运动学模型,可以不考虑经典D-H模型的缺陷造成的影 响。但在标定中进行误差建模时,必须注意到这一点。所以我们在标定过程中 采用的实际模型是根据经典D-H模型结合Hayti提出的修正后的D-H模型(MDH模型)来建立的。当相邻两关节轴不平行时,我们采用经典D-H参数( θi , di ,αi和ai)何特征;当相邻两关节轴平行时,我们使用修正D-H参数( θi , di ,αi,ai和βi)。其中其中βi为绕yi轴旋转的角度,用来描述坐标系Fi到从平行位 置旋转微小角度后的新坐标系F′i之间的旋转。修正D-H模型(M-DH模型)的5 个参数分别为关节角θi、偏距di、连杆长度ai、扭角αi和βi。当相邻关节不平行 时,扭角βi定义为零;当相邻关节平行时,di定义为零。
由题意可知,机器人手部在机座坐标系中的位姿矩阵为
M02= 0 0 1 15 100 5 010 0 000 1
机器人手部相对于机座坐标系的平移误差和旋转误差就相当于微分平移 矢量和旋转矢量,即 d0=0.1i+0j+0.05k, &0=0i+0j+0.01k
Page ▪ 9
9
由此可得 0 -0.01 0 0.1
▪ 通常,现代工业机器人的重复精度都是很高的,如IRB140机器人达到 0.03毫米(ISO试验平均值)。
Page ▪ 2
2
机器人绝对精度
▪ 机器人的绝对精度表示其实际位姿与其控制器预期位姿的接近程度。绝对精 度的高低是以机器人末端操作器的位姿误差来衡量的。机器人位姿误差即按 某种操作规程指令所产生的末端实际位姿与该操作规程所预期产生的末端位 姿之间的差异,可通过按正向运动变化矩阵计算出的空间位姿(X ,Y ,Z ,O ,A, T)与实际测量位姿(X ′,Y ′,Z ′,O ′,A′ ,T′)相减计算得到。