不锈钢论文大纲及文献资料
绪论

304不锈钢1、绪论1.1课题背景1.1.1 不锈钢发展我国不锈钢产业发展进步较晚,建国以来到改革开放前,我国不锈钢的需求主要是以工业和国防尖端使用为主。
改革开放后,国民经济的快速发展,人民生活水平的显著提高,拉动了不锈钢的需求。
进入上世纪90年代后,我国不锈钢产业进入快速发展期,不锈钢需求的增速远高于全球水平。
1990年以来,全球不锈钢表观消费量以年均6%的速度增长,而90年代的10年间,我国不锈钢表观消费量是世界年均增长率的2.9倍。
进入21世纪,我国不锈钢产业高速增长。
2000年-2006年,我国不锈钢消费量年平均增长率在21.17%以上。
其中,2001年,我国不锈钢表观消费量达到205万吨,超过美国成为世界第一不锈钢消费大国。
2008年,中国不锈钢表观消费量达到624.00万吨,同比下降5.17%。
2011年11月份,我国不锈钢产量增长了11.1%至1250万吨。
生产不锈钢制品33.68万吨,同比增长65.25%。
其中广东省是我国不锈钢制品的主要生产基地,其产量达183.7万吨,同比增长41.76%,占全国总产量的78.62%。
目前,我国不锈钢行业原材料中的铬镍在国外是供大于求,而在我国是供不应求的状况;不锈钢则是产能过剩,供大于求,盈利空间波动频繁。
随着不锈钢行业竞争的不断加剧,大型不锈钢生产企业间并购整合与资本运作日趋频繁,国内优秀的不锈钢生产企业愈来愈重视对行业市场的研究,特别是对企业发展环境和客户需求趋势变化的深入研究。
正因为如此,一大批国内优秀的不锈钢品牌迅速崛起,逐渐成为不锈钢行业中的翘楚!编辑本段品质特性1.1.2 各产品由于用途的不同,其加工工艺和原料的品质要求也不同材质。
①DDQ(deep drawing quality)材:是指用于深拉(冲)用途的材料,也就是大家所说的的软料,这种材料的主要特点是延伸率较高(≧53%),硬度较低(≦170%),内部晶粒等级在7.0~8.0之间,深冲性能极佳。
不锈钢 参考论文1

南京艺术学院高等教育自学考试毕业论文姓名:黄金晶准考证号: 060210156560专业方向:环艺设计论文题目:浅析不锈钢饰面在酒店室内设计中的应用指导教师:张晓冬2011年11月南京艺术学院自学考试办公室印制浅析不锈钢饰面在酒店室内设计中的应用【内容摘要】伴随时代的发展,不锈钢饰面加工工艺的进步,不锈钢饰面以其优异性受到众多设计师的青睐。
在酒店室内环境设计中,不锈钢饰面不仅仅停留在酒店厨房、办公等后场区域,还在诸如酒店客房、酒店会所得以大面积应用,本文以索菲特酒店为例,从不锈钢饰面的发展现状、分类特点及在酒店不同区域空间的设计分析了不锈钢饰面在现代酒店室内设计中的应用。
【关键词】不锈钢饰面酒店设计应用随着中国经济腾飞,国民整体收入的提高,国际连锁酒店纷纷入驻中国,带动了国内酒店产业的长足发展。
而酒店室内设计的风格体现着一个品牌酒店特有的文化。
由于不锈钢饰面拥有造型可塑性、整体效果搭配通用性、氛围营造华丽性及保洁便捷性等其他饰面所无可比拟的优势。
在酒店室内设计中大量出现的不锈钢饰面的应用,精确定位酒店装饰风格、文化内涵以及烘托氛围。
本文便通过正在进行室内装饰施工的上海华敏世纪索菲特大酒店为案例,分析了不锈钢饰面在酒店室内设计的应用。
尔后我们便可以窥知不锈钢饰面今后在酒店室内设计中具有的点睛之效。
1.不锈钢饰面发展现状1910~1914年诞生了组织分别为马氏体、铁素体和奥氏体的不锈钢,随着各种工业的发展,不锈钢为适应工作条件通过增减碳含量和添加多种其它的合金元素而衍生出了许多新型的不锈钢。
而关于不锈钢钢种的最主要的研究和发展是集中在两个方面:第一个方面是改善钢的耐腐蚀性;第二个方面是发展高强度不锈钢(即沉淀硬化不锈钢),这种钢是二次大战后随着航空、航天和火箭技术的进展而发展起来的。
现阶段不锈钢根据其自身材质特性被广泛运用在第一类建筑物内外装饰,厨房用具,化学刻度,航空机器;第二类建筑材料,汽车零件,加用电器,厨房器具,饭盒等;第三类钎、刀机器零部件,医院用具,手术用具等。
金属不锈钢毕业论文外文文献翻译及原文
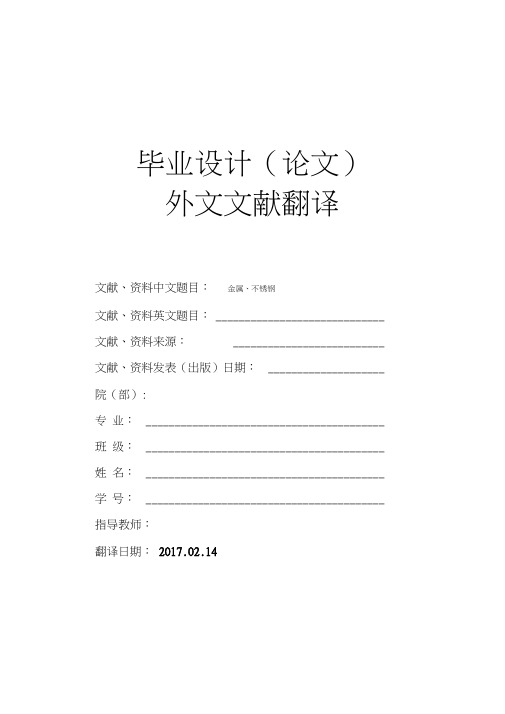
毕业设计(论文)外文文献翻译文献、资料中文题目:金属、不锈钢文献、资料英文题目:_____________________________ 文献、资料来源: __________________________ 文献、资料发表(出版)日期: ____________________ 院(部):专业:_________________________________________ 班级:_________________________________________ 姓名:_________________________________________ 学号:_________________________________________ 指导教师:翻译日期:2017.02.14Unit 1 MetalsThe use of metals has always bee n a key factor in the developme nt of the social systems of man. Of the roughly 100 basic eleme nts of which all matter is composed, about half are classified as metals. The dist in ctio n betwee n a metal and a nonm etal is n ot always clear-cut. The most basic definition centers around the type of bonding existing between the atoms of the element, and around the characteristics of certa in of the electro ns associated with these atoms. In a more practical way, however, a metal can be defi ned as an eleme nt which has a particular package of properties.Metals are crystalline when in the solid state and, with few exceptions (e.g. mercury), are solid at ambie nt temperatures. They are good con ductors of heat and electricity and are opaque to light. They usually have a comparatively high den sity. Many metals are ductile-that is, their shape can be cha nged perma nen tly by the applicati on of a force without break ing. The forces required to cause this deformation and those required to break or fracture a metal are comparatively high, although, the fracture forces is not n early as high as would be expected from simple con siderati on of the forces required to tear apart the atoms of the metal.One of the more significant of these characteristics from our point of view is that of crystallinity.A crystalline solid is one in which the constituent atoms are located in a regular three-dime nsional array as if they were located at the corners of the squares of a three-dime nsional chessboard. The spaci ng of the atoms in the array is of the same order as the size of the atoms, the actual spaci ng being a characteristic of the particular metal. The direct ions of the axes of the array defi ne the orie ntati on of the crystal in space. The metals commo nly used in engin eeri ng practice are composed of a large number of such crystals, called grains. In the most general case, the crystals of the various grains are randomly oriented in space. The grains are everywhere in in timate con tact with one ano ther and joined together on an atomic scale. The regi on at which they join is known as a grain boun dary.An absolutely pure metal (i.e. one composed of only one type of atom) has never been produced. Engineers would not be particularly interested in such a metal even if it were to be produced, because it would be soft and weak. The metals used commercially in evitably contain small amounts of one or more foreign elements, either metallic or nonmetallic. These foreign eleme nts may be detrime ntal, they may be ben eficial, or they may have no in flue nee at all on a particular property. If disadvantageous, the foreign elements tend to be known as impurities. If advantageous, they tend to be known as alloying elements. Alloying elements are commonly added deliberately in substantial amounts in engineering materials. The result is known as an alloy.The distinction between the descriptors metaland alloy ” is not clear-cut. The term metal" may be used to encompass both a commercially pure metal and its alloys. Perhaps it can be said that the more deliberately an alloyi ng additi on has bee n made and the larger the amount of the additi on, the more likely it is that the product will specifically be called an alloy .In any event, the chemical compositi on of a metal or an alloy must be known and con trolled with in certa in limits if con siste nt performa nee is to be achieved in service. Thus chemical compositi on has to be take n in to acco unt whe n develop ing an un dersta nding of the factors which determ ine the properties of metals and their alloys.Of the 50 or so metallic eleme nts, only a few are produced and used in large qua ntities in engin eeri ng practice. The most importa nt by far is iron, on which are based the ubiquitous steels and cast irons (basically alloys of iron and carb on). They acco unt for about 98% by weight of all metals produced. Next in importa nee for structural uses (that is, for structures that are expected tocarry loads) are alu minum, copper, ni ckel, and tita nium. Alu minum acco unts for about 0.8% by weight of all metals produced, and copper about 0.7%, leav ing only 0.5% for all other metals. As might be expected, the rema in ders are all used in rather special applicati ons. For example, ni ckel alloys are used principally in corrosion-and heat-resistant applications, while titanium is used exte nsively in the aerospace in dustry because its alloys have good comb in ati ons of high stre ngth and low density. Both nickel and titanium are used in high-cost, high-quality applications, and, in deed, it is their high cost that tends to restrict their applicati on.We cannot discuss these more esoteric properties here. Suffice it to say that a whole complex of properties in additi on to structural stre ngth is required of an alloy before it will be accepted in to, and survive in, engineering practice. It may, for example, have to be strong and yet have reas on able corrosi on resista nee; it may have to be able to be fabricated by a particular process such as deep draw ing, mach ining, or weldi ng; it may have to be readily recyclable; and its cost and availability may be of critical importa nee.翻译如下:第一单元金属在人类社会的发展中,金属的应用起着关键性的作用。
不锈钢焊接技术论文
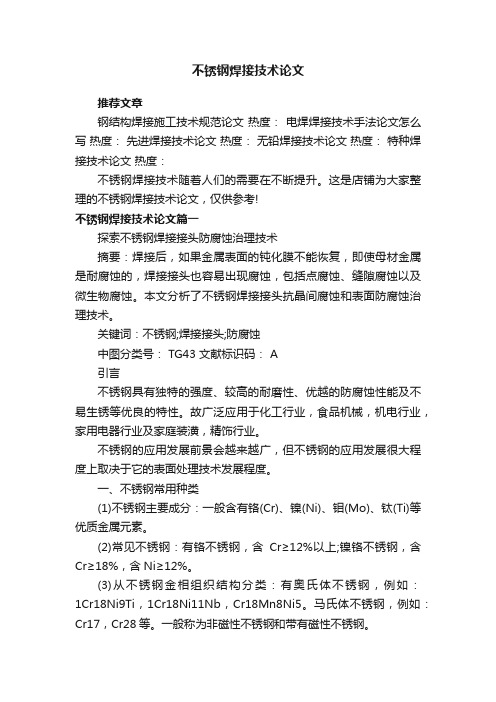
不锈钢焊接技术论文推荐文章钢结构焊接施工技术规范论文热度:电焊焊接技术手法论文怎么写热度:先进焊接技术论文热度:无铅焊接技术论文热度:特种焊接技术论文热度:不锈钢焊接技术随着人们的需要在不断提升。
这是店铺为大家整理的不锈钢焊接技术论文,仅供参考!不锈钢焊接技术论文篇一探索不锈钢焊接接头防腐蚀治理技术摘要:焊接后,如果金属表面的钝化膜不能恢复,即使母材金属是耐腐蚀的,焊接接头也容易出现腐蚀,包括点腐蚀、缝隙腐蚀以及微生物腐蚀。
本文分析了不锈钢焊接接头抗晶间腐蚀和表面防腐蚀治理技术。
关键词:不锈钢;焊接接头;防腐蚀中图分类号: TG43 文献标识码: A引言不锈钢具有独特的强度、较高的耐磨性、优越的防腐蚀性能及不易生锈等优良的特性。
故广泛应用于化工行业,食品机械,机电行业,家用电器行业及家庭装潢,精饰行业。
不锈钢的应用发展前景会越来越广,但不锈钢的应用发展很大程度上取决于它的表面处理技术发展程度。
一、不锈钢常用种类(1)不锈钢主要成分:一般含有铬(Cr)、镍(Ni)、钼(Mo)、钛(Ti)等优质金属元素。
(2)常见不锈钢:有铬不锈钢,含Cr≥12%以上;镍铬不锈钢,含Cr≥18%,含Ni≥12%。
(3)从不锈钢金相组织结构分类:有奥氏体不锈钢,例如:1Cr18Ni9Ti,1Cr18Ni11Nb,Cr18Mn8Ni5。
马氏体不锈钢,例如:Cr17,Cr28等。
一般称为非磁性不锈钢和带有磁性不锈钢。
二、不锈钢焊接方法常用不锈钢焊接方法对不锈钢最常用的焊接方法是手工焊(MMA),其次是金属极气体保护焊(MIG/MAG)和钨极惰性气体保护焊(TIG).虽然这些焊接方法对不锈钢工业的大多数人而言是熟悉的,但是我们认为这个领域值得深入探讨.1、手工焊(MMA)手工焊是一种非常普遍的、易于使用的焊接方法.电弧的长度靠人的手进行调节,它决定于电焊条和工件之间缝隙的大小.同时,当作为电弧载体时,电焊条也是焊缝填充材料.这种焊接方法很简单,可以用来焊接几乎所有材料.对于室外使用,它有很好的适应性,即使在水下使用也没问题.大多数电焊机可以TIG 焊接.在电极焊中,电弧长度决定于人的手:当你改变电极与工件的缝隙时,你也改变了电弧的长度.在大多数情况下,焊接采用直流电,电极既作为电弧载体,同时也作为焊缝填充材料.电极由合金或非合金金属芯丝和焊条药皮组成.这层药皮保护焊缝不受空气的侵害,同时稳定电弧.它还引起渣层的形成,保护焊缝使它成型.电焊条即可是钛型焊条,也可是缄性的,这决定于药皮的厚度和成分.钛型焊条易于焊接,焊缝扁平美观.此外,焊渣易于去除.如果焊条贮存时间长,必须重新烘烤.因为来自空气的潮气会很快在焊条中积聚.2、MIG/MAG焊接这是一种自动气体保护电弧焊接方法.在这种方法中,电弧在保护气体屏蔽下在电流载体金属丝和工件之间烧接.机器送入的金属丝作为焊条,在自身电弧下融化.由于MIG/MAG焊接法的通用性和特殊性的优点,至今她仍然是世界上最为广泛的焊接方法.它使用于钢、非合金钢、低合金钢和高合金为基的材料.这使得它成为理想的生产和修复的焊接方法.当焊接钢时,MAG可以满足只有0.6mm厚的薄规格钢板的要求.这里使用的保护气体是活性气体,如二氧化碳或混合气体.唯一的限制是当进行室外焊接时,必须保护工件不受潮,以保持气体的效果.3、TIG焊接电弧在难熔的钨电焊丝和工件之间产生.这里使用的保护气体是纯氩气,送入的焊丝不带电.焊丝既可以手送,也可以机械送.也有一些特定用途不需要送入焊丝.被焊接的材料决定了是采用直流电还是交流电.采用直流电时,钨电焊丝设定为负极.因为它有很深的焊透能力,对于不同种类的钢是很合适的,但对焊缝熔池没有任何“清洁作用”.TIG焊接法的主要优点是可以焊接大材料范围广.包括厚度在0.6mm及其以上的工件,材质包括合金钢、铝、镁、铜及其合金、灰口铸铁、普通干、各种青铜、镍、银、钛和铅.主要的应用领域是焊接薄的和中等厚度的工件,在较厚的截面上作为焊根焊道使用.三、提高焊接接头抗晶间腐蚀能力的措施由于晶界碳化铬沉淀析出而引起晶界贫铬是奥氏体不锈钢晶间腐蚀的主要原因,因此提高抗晶间腐蚀能力,防止晶间腐蚀的途径都是从控制碳化铬的沉淀来考虑,即从碳化铬沉淀的分量、部位和沉淀物形成动力等方面考虑。
不锈钢论文

目录空一格一引言 (2)二钢渣 (2)(一)钢渣中金属的回收 (2)(二)钢渣用于铁水预处理脱磷 (2)1、含磷废水 (2)五、结论 .......................................................................................... 错误!未定义书签。
参考文献 (4)致谢 (5)附件 (6)注意:目录要自动生成保留三级目录高炉喷煤及富氧操作的探讨摘要:喷吹辅助燃料技术是现代高炉炼铁生产广泛采用的新技术。
它也是现代高炉炉况调节所不可缺少的重要手段之一。
其中喷吹煤粉受到世界各个国家或地区的高度重视。
本文就介绍了高炉喷煤工艺流程中的各个系统即:原煤贮运系统,制粉系统,煤粉输送系统,喷吹系统,供气系统,煤粉计量设施,最新设计的还包括整个喷煤系统的计算机控制中心。
关键词:制粉输送喷吹富氧一引言钢渣生产率约为粗钢产量的12%~20%,把钢渣作为废物遗弃不仅占用大量的土地资源,还对环境造成了污染。
为了适应钢铁工业的快速发展,近年来…………….。
二钢渣(一)钢渣中金属的回收钢渣中含有相当数量的铁,平均含金属铁约为10%左右。
国外较早采取了从钢渣中回收废钢铁的做法,前苏联马钢用机械破碎法处理钢渣,从中回收了金铁…………………….。
(二)钢渣用于铁水预处理脱磷通常铁水预处理所用的脱磷剂是由石灰、烧结矿和萤石组成的。
其中,石灰提供脱磷所需的碱剂,烧结矿提供氧化剂,萤石起助熔作用。
,沉淀作用。
钢渣表面的部分氧化物在水溶液中发生水解会使PH值上升,从而产生Cu(OH)2沉淀,尤其在溶液初始PH值较高的情况下,沉淀作用往往是Cu2+外被去除的重要原因。
1、含磷废水传统除磷的方法主要是沉淀法、结晶法、生物法和吸附与离子交换法等。
其中通过吸附去除磷,不仅速度快且没有二次污染,操作相对简单。
钢渣用于除磷主要具有2种作用:例图图1 高炉内型图表1 高炉的各区内进行的主要反应和特征表1 高炉的各区内进行的主要反应和特征参考文献1 唐清华,马树涵等.高炉喷吹煤粉知识问答.北京:冶金工业出版社,20022 郝素菊,蒋武锋,方觉.高炉炼铁设计原理.北京:冶金工业出版社,20033 董一诚等.高炉生产知识问答.北京:冶金工业出版社,20024 由文泉,赵文革.实用高炉炼铁技术.北京:冶金工业出版社,20025 周传典.高炉炼铁生产技术手册.北京:冶金工业出版社,20036 解广安.炼铁工艺.冶金工业部工人视听教材编辑部,1995致谢本论文是在导师***老师的悉心指导下完成的。
不锈钢 毕业论文
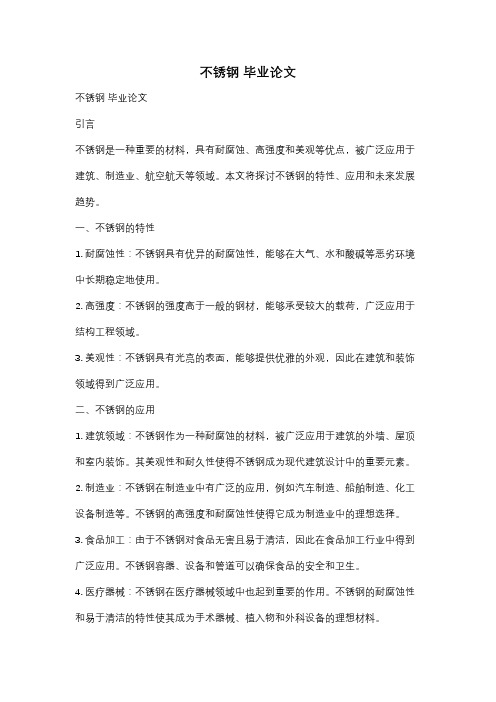
不锈钢毕业论文不锈钢毕业论文引言不锈钢是一种重要的材料,具有耐腐蚀、高强度和美观等优点,被广泛应用于建筑、制造业、航空航天等领域。
本文将探讨不锈钢的特性、应用和未来发展趋势。
一、不锈钢的特性1. 耐腐蚀性:不锈钢具有优异的耐腐蚀性,能够在大气、水和酸碱等恶劣环境中长期稳定地使用。
2. 高强度:不锈钢的强度高于一般的钢材,能够承受较大的载荷,广泛应用于结构工程领域。
3. 美观性:不锈钢具有光亮的表面,能够提供优雅的外观,因此在建筑和装饰领域得到广泛应用。
二、不锈钢的应用1. 建筑领域:不锈钢作为一种耐腐蚀的材料,被广泛应用于建筑的外墙、屋顶和室内装饰。
其美观性和耐久性使得不锈钢成为现代建筑设计中的重要元素。
2. 制造业:不锈钢在制造业中有广泛的应用,例如汽车制造、船舶制造、化工设备制造等。
不锈钢的高强度和耐腐蚀性使得它成为制造业中的理想选择。
3. 食品加工:由于不锈钢对食品无害且易于清洁,因此在食品加工行业中得到广泛应用。
不锈钢容器、设备和管道可以确保食品的安全和卫生。
4. 医疗器械:不锈钢在医疗器械领域中也起到重要的作用。
不锈钢的耐腐蚀性和易于清洁的特性使其成为手术器械、植入物和外科设备的理想材料。
三、不锈钢的未来发展趋势1. 新型不锈钢材料的研发:随着科技的进步,研发出更具优异性能的不锈钢材料是未来的发展方向。
例如,耐高温不锈钢、耐磨损不锈钢等,将进一步拓宽不锈钢的应用领域。
2. 环保可持续发展:不锈钢的生产过程中会产生大量的废水和废气,对环境造成一定的影响。
因此,未来的发展趋势将会更加注重环保可持续发展,减少对环境的负面影响。
3. 与其他材料的结合应用:不锈钢与其他材料的结合应用将会成为未来的趋势。
例如,将不锈钢与玻璃、陶瓷等材料结合,可以创造出更具创新性和多样性的产品。
结论不锈钢作为一种重要的材料,具有耐腐蚀、高强度和美观等优点,被广泛应用于建筑、制造业、医疗器械等领域。
未来的发展趋势将会更加注重新型材料的研发、环保可持续发展以及与其他材料的结合应用。
毕业论文---不锈钢的焊接工艺的研究

前言进入20世纪90年代以来,我国不锈钢的消费量增长很快。
1997年我国不锈钢的表观消费量超过了 100万1,2001年达到220万t,居世界第一位。
以后逐年大幅度增长,2005年达到522万t。
连续5年成为世界上最大的不锈钢消费国家。
不锈钢由于其优良的耐腐蚀性能,在我国的经济建设中占有举足轻重的地位,被广泛应用于船舶、车辆、汽车、宇航、桥梁、建筑、压力容器、贮罐、建筑机械、管线及家电设备等行业。
在不锈钢加工工艺中,焊接是最主要的必不可少的加工技术。
焊接件的数量、品种、规格在不断地增加,对焊接工艺和质量的要求也越来越高。
而且随着技术的引进,国外的不少不锈钢的品种和牌号、新焊接材料、新焊接技术、新焊接工艺在国内市场所占的比重逐步增加,因此对国内的焊接技术人员也提出了许多新的问题。
焊接性是指同种金属材料或异种金属材料在焊接加工条件下,能够形成具备一定使用性能的焊接接头的特性。
焊接性应包括两个方面的意义:一是结合性,即一定的金属材料在指定的焊接工艺条件下,对煶接缺陷的敏感性,即工艺焊接性;二是使用性能,是金属材料在指定的焊接条件下所形成的焊接接头适用使用条件的程度,也称使用焊接性。
焊接性与材料、工艺、结构和使用条件等因素都有密切的关系,不能脱离开这些因素而单纯从材料本身的性能来评价焊接性。
与国外相比,我国的不锈钢焊接技术水平存在一定的差距,主要表现在焊接设备(国内目前无一家具有自主知识产权的先进设备生产厂家,高端焊机完全依赖进口,中低端焊机厂家之间竞争激烈,在技术研发方面投入少)、焊接工艺(大部分焊接工程技术人员及焊工不熟悉不锈钢的焊接)和焊接材料(焊材研发能力弱,优质焊材主要靠进口)等方面。
另外,我国执行的标准同国外相比,也比较落后,因此,迫切需要我们加强不锈钢焊接工艺与材料的研究工作,致力于产品质量的提高,保证产品质量的稳定,迅速缩小与国外先进水平的差距。
同时加强对高品质特种不锈钢焊材的研制开发与生产,适应市场的需求,降低成本,增强自身的竞争能力,为我国的经济建设做贡献。
不锈钢材质报告范文

不锈钢材质报告范文
报告题目:不锈钢材料介绍
报告人:
报告日期:
不锈钢材料简介
不锈钢是一种高强度、高耐腐蚀、耐高温、耐低温、耐磨损的合金材料。
它主要成分有Fe(铁)、Cr(铬)、Ni(镍)、Mn(锰)、Si (硅)、C(碳)、Mo(钼)等元素。
这种材料可以形成抗腐蚀的自然保护膜,并可以在潮湿环境下长期的保持非常可靠的性能。
不锈钢材料性能
不锈钢材料具有良好的物理和化学性能,具有优良的抗腐蚀性,特别是在高温下的工作环境,可以长期保持其良好的性能。
同时,不锈钢材料还具有良好的韧性和焊接性,可以通过焊接来实现其结构的完整性和稳定性。
不锈钢材料应用范围
由于具有良好的抗腐蚀性、耐磨损性、韧性和焊接性,不锈钢材料在化学工程、机械制造、军工工业、航空航天等领域得到了广泛应用,如制造制作军用飞机零件,船舶外壳和船舶装备的零件等。
而在日常生活中,不锈钢材料应用于厨具,厨房设施、家具、汽车零件、护栏等行业。
不锈钢材料优势
不锈钢材料的优势在于其耐腐蚀性、耐磨损性、韧性和焊接性等,不易受到有害因素的影响,可以长久的保持其良好的性能;同时,不锈钢材料不需要维护。
不锈钢的特性及应用和发展

不锈钢的特性及应用和发展摘要:本文主要介绍了不锈钢的各部分特征和应用,以及不锈钢的发展趋势。
关键词:不锈钢应用发展趋势不锈钢在人们的日常生活中应用越来越多,其耐腐蚀性、高强度性、可焊接性以及可重复利用的性能在工业建材中位置极其重要,本文主要介绍了不锈钢的各部分特征和应用,以及不锈钢的发展趋势。
一、不锈钢的发展历史人类从十八世纪就在寻找一种价格较为低廉,具有良好的综合性能,并可以在大气条件下是不锈蚀的材料。
经过一百多年的努力,终于在1910至1914年之间陆续发明了不锈钢。
作为现代不锈钢的基础,马氏体不锈钢、铁素体不锈钢和奥氏体不锈钢先后问世。
现在大量应用的奥氏体不锈钢是在1909至1912年间,后来,通过对V2A钢的耐蚀性和机械性的不断研究,发展成现在的18-8系不锈钢。
二、不锈钢的特征1.不锈钢不会产生腐蚀、点蚀、锈蚀或磨损。
由于不锈钢具有良好的耐腐蚀性所以它能使结构部件永久地保持工程设计的完整性。
含铬不锈钢还集机械强度和高延伸性于一身,易于加工制造,加上其使用寿命长、可循环和再利用、没有排放、耐腐蚀、耐高温等优势。
2.不锈钢最具有高强度、高韧性和高耐开裂性的建材。
例如飞机的关键承力件需高强高不锈钢,由于不锈钢的高强度、高韧性、高耐应力腐蚀开裂以及良好的抗冲击性能,飞机的一些关键承力结构件如起落架、大梁、大应力接头、高应力紧固件等仍在继续使用高强度钢。
飞机向长寿命、高可靠性方向的发展,采用高强度不锈钢制作某些重要零部件已成为主要发展趋势,这使得高强度不锈钢材料成为航空产品达到高性能、长寿命与高可靠性的重要物质与技术基础。
3.不锈钢具有可持续、可再生和可重复利用的特征。
首先,钢铁像纸、玻璃和铝等其他常用材料一样是可再生的,而且不锈钢中的镍等金属,它的再生远远早于其他材料的再生。
再次,不锈钢可重复利用,如一种新型的不锈钢葡萄酒瓶盛装的葡萄酒,这种不锈钢葡萄酒瓶不含BPA(一种化学物质,可能会引发癌变和其他功能紊乱),并且可以重复使用。
不锈钢毕业论文

不锈钢毕业论文不锈钢毕业论文随着社会的进步和科技的发展,不锈钢作为一种重要的材料,在各个领域得到了广泛应用。
它具有耐腐蚀、抗氧化、美观等优点,成为了建筑、制造业、医疗器械等行业的首选材料。
本文将从不锈钢的特性、应用领域、加工工艺等方面进行探讨,旨在深入了解不锈钢的发展和应用。
一、不锈钢的特性不锈钢是一种合金材料,主要由铁、铬、镍等元素组成。
它具有耐腐蚀、抗氧化、高强度等特点。
首先,不锈钢具有良好的耐腐蚀性能,可以在潮湿、酸碱等恶劣环境中长时间使用,不会生锈和腐蚀。
其次,不锈钢具有良好的抗氧化性能,可以在高温环境下保持材料的稳定性。
此外,不锈钢还具有高强度、良好的塑性和可焊性等特点,使其在各个领域得到广泛应用。
二、不锈钢的应用领域不锈钢由于其优异的性能,在各个领域都有广泛的应用。
首先,建筑行业是不锈钢的主要应用领域之一。
不锈钢可以用于建筑的外墙、屋顶、门窗等部位,不仅美观大方,而且具有耐候性和耐腐蚀性。
其次,制造业也是不锈钢的重要应用领域。
不锈钢可以用于制造汽车零部件、厨具、电器等产品,具有优异的耐蚀性和强度,能够满足不同行业的需求。
此外,医疗器械、食品加工设备、化工设备等领域也广泛使用不锈钢,因为它符合卫生要求、无毒无味、易清洗等特点。
三、不锈钢的加工工艺不锈钢的加工工艺对于最终产品的质量和性能具有重要影响。
首先,不锈钢的切割工艺是加工过程中的重要环节。
常见的切割方法有火焰切割、等离子切割、激光切割等,不同的切割方法适用于不同的厚度和形状的不锈钢材料。
其次,不锈钢的成型工艺也是关键步骤。
常见的成型方法有冲压、弯曲、拉伸等,通过这些工艺可以将不锈钢材料加工成各种形状和尺寸的零部件。
最后,不锈钢的焊接工艺也是不可忽视的。
常见的焊接方法有手工电弧焊、氩弧焊、激光焊等,不同的焊接方法适用于不同的不锈钢材料和应用领域。
四、不锈钢的发展趋势随着科技的进步和工艺的改进,不锈钢在未来有着广阔的发展前景。
首先,不锈钢的新材料研发将成为发展的重点。
不锈钢论文大纲及文献资料
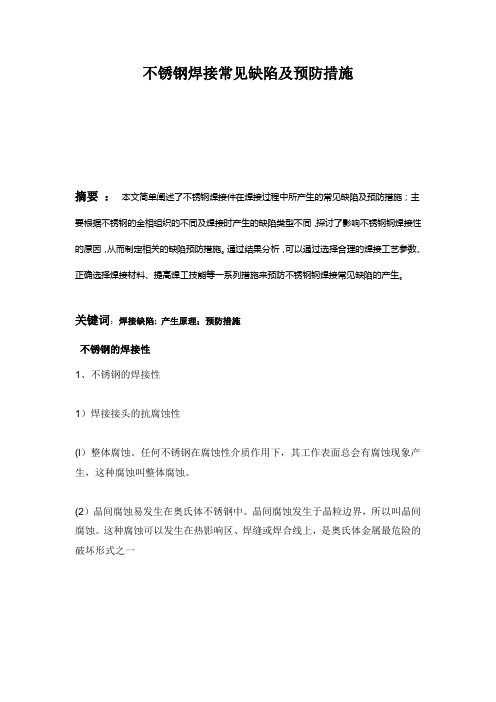
不锈钢焊接常见缺陷及预防措施摘要:本文简单阐述了不锈钢焊接件在焊接过程中所产生的常见缺陷及预防措施;主要根据不锈钢的金相组织的不同及焊接时产生的缺陷类型不同,探讨了影响不锈钢钢焊接性的原因,从而制定相关的缺陷预防措施。
通过结果分析,可以通过选择合理的焊接工艺参数、正确选择焊接材料、提高焊工技能等一系列措施来预防不锈钢钢焊接常见缺陷的产生。
关键词:焊接缺陷; 产生原理;预防措施不锈钢的焊接性1、不锈钢的焊接性1)焊接接头的抗腐蚀性(l)整体腐蚀。
任何不锈钢在腐蚀性介质作用下,其工作表面总会有腐蚀现象产生,这种腐蚀叫整体腐蚀。
(2)晶间腐蚀易发生在奥氏体不锈钢中。
晶间腐蚀发生于晶粒边界,所以叫晶间腐蚀。
这种腐蚀可以发生在热影响区、焊缝或焊合线上,是奥氏体金属最危险的破坏形式之一目录一、绪论 1二、本论 1 (一)不锈钢焊接缺陷 11.不锈钢焊接缺陷的概念及分类 12.不锈钢常见缺陷的特征 1 (二)影响不锈钢焊接的因素 11.焊接前的准备 12.焊接参数 1(三)不锈钢焊接缺陷的形成原因及分析预防措施 11.气孔产生的原因及解决方法 12 .裂纹产生的原因及解决方法 13.电弧产生的偏吹及解决方法1三、结论 1致谢 1 参考文献 1一、绪论随着工业技术的发展,焊接技术被广泛用于大型与高参数设备制造中。
焊接是大型安装工程建设中的一项关键工作,其质量的好坏、效率的高低直接影响工程的安全运行和制造工期。
因此确保焊接质量、预防焊接热裂纹的产生成为一个重要的课题。
实践证明,母材及焊接材料的质量、坡口加工和装配精度、坡口表面清理状况、焊接设备、焊接工艺参数、焊接工艺规程、焊接技术水平、外部环境等,任何一个环节处理不当,都会产生焊接缺陷,影响焊接质量。
本文阐述了常见焊接热裂纹的预防措施,从而更好的制定不锈钢焊接的预防措施二、本论(一)不锈钢焊接缺陷1.1 焊接缺陷的概念及分类焊接缺陷是指焊接过程中在焊接接头中产生的金属不连续、不致密或连接不良的现象。
不锈钢可行性研究报告范文

不锈钢可行性研究报告范文一、研究背景不锈钢是一种具有抗腐蚀性能的金属材料,主要由铁、铬、镍及其他元素组成。
其主要特点是耐腐蚀、耐磨损、坚固耐用,具有良好的加工性和装饰性。
在工业、建筑、航空航天、机械制造等领域都有广泛的应用。
目前,不锈钢在各行各业中的应用越来越广泛,但在一些特殊领域的应用还存在一些问题,比如在某些环境下不锈钢的耐腐蚀性能会受到影响,从而影响其使用寿命和安全性。
因此,有必要对不锈钢的可行性进行研究,以寻找提升其性能的方法和措施。
二、研究目的本研究旨在探讨不锈钢在不同环境条件下的耐腐蚀性能,分析不同因素对其性能的影响,为其在不同领域中的应用提供参考和建议,为相关行业的发展和提升提供支持。
三、研究方法1.文献综述:通过查阅相关文献资料,了解不锈钢在不同环境下的性能表现和存在的问题。
2.实地调研:通过实地调研,了解不锈钢在实际应用中的情况和存在的挑战,收集样本进行实验分析。
3.实验研究:通过实验研究,对不锈钢在不同环境条件下的耐腐蚀性能进行测试,并对实验结果进行分析和总结。
四、研究内容1.不锈钢的组成和性能不锈钢主要由铁、铬、镍以及其它元素组成,具有耐腐蚀、耐磨损、坚固耐用的特点。
常见的不锈钢有奥氏体不锈钢、铁素体不锈钢和马氏体不锈钢等。
2.不锈钢在不同环境下的性能表现不锈钢在不同环境条件下的性能表现会有所不同,主要是由于不锈钢的组成、结构和制造工艺不同导致的。
在盐水、酸性、碱性等环境中,不锈钢的耐腐蚀性能会受到影响,从而导致其使用寿命和安全性受到威胁。
3.不锈钢的改进和优化为了提升不锈钢的耐腐蚀性能,可以采取一些改进和优化措施,比如选择合适的不锈钢材料、优化材料结构、表面处理等方法,可以有效提升不锈钢的使用寿命和安全性。
五、研究结论通过研究我们发现,不锈钢在不同环境下的性能表现确实存在一些差异,主要是由不同因素的影响导致的,包括材料的组成、结构、制造工艺等方面。
为了提升不锈钢的使用寿命和安全性,我们可以通过选择合适的不锈钢材料、优化材料结构、表面处理等方法来改进和优化不锈钢的性能。
201系不锈钢文献综述

摘要IABSTRACT II目录III第一章文献综述1.1 200系列不锈钢的现状及发展1.1.1 200系列不锈钢的现状1.1.2 200 系列不锈钢特点1.1.3 200 系列不锈钢的应用及发展1.1.4 200 系列不锈钢性能的改进1.2 201不锈钢1.3 201不锈钢的设计原理1.4 不锈钢的腐蚀 51.4.1不锈钢的全面腐蚀1.4.2不锈钢的局部腐蚀1.5 稀土元素在不锈钢中的应用1.5.1稀土的作用机理1.5.2 稀土元素对不锈钢组织的影响1.5.2 稀土元素对不锈钢耐腐蚀性的影响1.5.3 钢中加入稀土的方法1.6 课题的主要研究内容第一章文献综述1.1 200系列不锈钢的现状及发展1.1.1 200系列不锈钢的现状近年来以中国和印度为中心,扩大了200系列不锈钢的生产和应用范围,其产量已占世界年不锈钢总产量的8%左右;我国镍资源缺乏,供不应求,因此为适应不锈钢产业高速发展的要求,根据我国的资源情况,大力发展以锰、氮代镍型和节镍型不锈钢,是中国发展不锈钢产业走“节镍”之路的又一个重要方向。
200系列不锈钢是由美国在二战时期首先开发成功的。
当时,美方的镍供应量严重不足,在这种情况下,美国开发出了这种节镍型的奥氏体不锈钢。
二战结束后,美国镍的供应状况逐步改善,因此,300系列不锈钢的生产不再受原料紧张的制约,200系列不锈钢就没有再得到更大的发展。
几位参与开发200系列不锈钢的印度人对这种以锰、氮代镍型奥氏体不锈钢在印度进一步进行研究、应用,结果取得了很大的成功。
于是,造成了200系列不锈钢在美国开发、在印度发展的历史现象。
不锈钢是指具有抗腐蚀性能的一类钢种,按化学成份与金相组织分类如图1.1所示。
图1.1 不锈钢的分类Figure 1.1 the classification of stainless steel奥氏体不锈钢可分为铬镍系奥氏体不锈钢和铬锰系奥氏体不锈钢两个系列。
镍系奥氏体不锈钢(300系列)是以镍为主要奥氏体化元素,因其在多种腐蚀介质中均具有优秀的耐腐蚀性能和良好的综合力学性能、工艺性能及可焊性,所以在化工、石油、海洋、食品、轻工等众多领域具有广泛的用途。
奥氏体不锈钢论文

封面摘要:奥氏体不锈钢,是指在常温下具有奥氏体组织的不锈钢。
碳溶解在γ-Fe中的间隙固溶体,常用符号A表示。
它仍保持γ-Fe的面心立方晶格。
其溶碳能力较大,在727℃时溶碳为ωc=0.77%,1148℃时可溶碳2.11%。
奥氏体是在大于727℃高温下才能稳定存在的组织。
奥氏体塑性好,是绝大多数钢种在高温下进行压力加工时所要求的组织。
那为什么在室温这种低温环境下也可得到奥氏体组织呢?原因就在于奥氏体不锈钢含有大量使奥氏体区扩大的合金元素Ni,而镍抑制铁素体的产生,从而使得在室温下钢的金相组织成为奥氏体组织。
此类钢除耐氧化性酸介质腐蚀外,如果含有Mo、Cu等元素还能耐硫酸、磷酸以及甲酸、醋酸、尿素等的腐蚀。
此类钢除耐氧化性酸介质腐蚀外,如果含有Mo、Cu 等元素还能耐硫酸、磷酸以及甲酸、醋酸、尿素等的腐蚀。
此类钢中的含碳量若低于0.03%或含Ti、Ni,就可显著提高其耐晶间腐蚀性能。
高硅的奥氏体不锈钢浓硝酸具有良好的耐蚀性。
由于奥氏体不锈钢具有全面的和良好的综合性能,在各行各业中获得了广泛的应用。
本文主要介绍奥氏体不锈钢在不同腐蚀介质中易发生的局部腐蚀类型、腐蚀机理与控制腐蚀的方法。
关键词:奥氏体不锈钢腐蚀介质腐蚀机理前言奥氏体铬镍不锈钢包括著名的18Cr-8Ni钢和在此基础上增加Cr、Ni含量并加入Mo、Cu、Si、Nb、Ti等元素发展起来的高Cr-Ni系列钢。
奥氏体不锈钢无磁性而且具有高韧性和塑性,但强度较低,不可能通过相变使之强化,仅能通过冷加工进行强化,如加入S,Ca,Se,Te等元素,则具有良好的易切削性。
奥氏体不锈钢的机械性能表20℃温度下高合金奥氏体不锈钢的机械性能高温下高合金奥氏体不锈钢的强度(Rp0.2MPa)。
铁素体不锈钢,在使用状态下以铁素体组织为主的不锈钢。
含铬量在11%~30%,具有体心立方晶体结构。
多用于制造耐大气、水蒸气、水及氧化性酸腐蚀的零部件。
这类钢存在塑性差、焊后塑性和耐蚀性明显降低等缺点,因而限制了它的应用。
不锈钢磨削加工分析论文

不锈钢磨削加工分析论文1前言不锈钢零件为达到表面质量和加工精度要求,通常采用磨削加工方法。
由于不锈钢韧性大、导热系数小、弹性模量小,故在磨削加工中常存在如下问题:1)砂轮易粘附堵塞;2)加工表面易烧伤;3)加工硬化现象严重;4)工件易变形。
不难看出,砂轮和磨削液的选择直接影响磨削效率和加工精度。
本文对影响粘附堵塞和表面粗糙度的因素进行实验研究。
2实验条件和方法试件材料选用1Gr18Ni9Ti,其机械性能:σb=530MPa、σ=40%、硬度HB=187.试件尺寸直径φ50mm、长300mm、φ50外圆表面精车,两端面打中心孔。
实验在MGB1420外圆磨床上进行,砂轮为P400×40×203,磨削方式为外圆纵向磨削,为提高试验结果的可靠性,进行重复试验,观察平均效应,消除随机因素的影响,同时尽量保持磨削条件基本不变,通过改变砂轮的粒度、硬度、磨料,更换磨削液、磨削用量来考查对磨削效果的影响。
3实验结果分析3.1砂轮的粒度对粘附率的影响选用的白刚玉、硬度K、粒度分别为36、46、60、80号的四个砂轮,对试件进行外圆纵向磨削,磨削长度为600mm,检测粘附率,结果如表1所示:表1粘附率%磨削深度/mm0.010.020.030.04砂轮粒度36103222334642444345604365--808985--从表1中可以看出,砂轮越细,粘附越严重,这是由于磨粒之间存在着空洞,磨削时切屑可存于空洞中;而砂轮越细,空洞越小,砂轮很快失去容屑空间,造成堵塞。
3.2砂轮硬度对粘附率的影响选用磨料为白刚玉、粒度46,硬度分别为H、J、K、L级的砂轮,对试件进行磨削,磨削行程600mm,检测粘附率。
结果如表2所示:表2磨削深度/mm0.010.020.030.04砂轮粒度H18171616J22212021K36363838L42444345从表2中可以看出,砂轮硬度越高,粘附越严重。
这是由于硬度低的砂轮,磨粒在磨削力作用下,易于从砂轮表面脱落,形成新的容屑空间,不易堵塞。
不锈钢耐腐蚀性研究相关论文文献综述
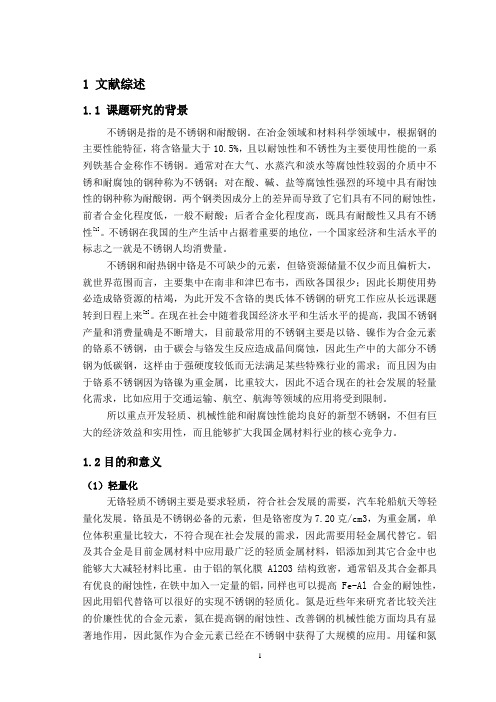
1 文献综述1.1 课题研究的背景不锈钢是指的是不锈钢和耐酸钢。
在冶金领域和材料科学领域中,根据钢的主要性能特征,将含铬量大于10.5%,且以耐蚀性和不锈性为主要使用性能的一系列铁基合金称作不锈钢。
通常对在大气、水蒸汽和淡水等腐蚀性较弱的介质中不锈和耐腐蚀的钢种称为不锈钢;对在酸、碱、盐等腐蚀性强烈的环境中具有耐蚀性的钢种称为耐酸钢。
两个钢类因成分上的差异而导致了它们具有不同的耐蚀性,前者合金化程度低,一般不耐酸;后者合金化程度高,既具有耐酸性又具有不锈性[1]。
不锈钢在我国的生产生活中占据着重要的地位,一个国家经济和生活水平的标志之一就是不锈钢人均消费量。
不锈钢和耐热钢中铬是不可缺少的元素,但铬资源储量不仅少而且偏析大,就世界范围而言,主要集中在南非和津巴布韦,西欧各国很少;因此长期使用势必造成铬资源的枯竭,为此开发不含铬的奥氏体不锈钢的研究工作应从长远课题转到日程上来[2]。
在现在社会中随着我国经济水平和生活水平的提高,我国不锈钢产量和消费量确是不断增大,目前最常用的不锈钢主要是以铬、镍作为合金元素的铬系不锈钢,由于碳会与铬发生反应造成晶间腐蚀,因此生产中的大部分不锈钢为低碳钢,这样由于强硬度较低而无法满足某些特殊行业的需求;而且因为由于铬系不锈钢因为铬镍为重金属,比重较大,因此不适合现在的社会发展的轻量化需求,比如应用于交通运输、航空、航海等领域的应用将受到限制。
所以重点开发轻质、机械性能和耐腐蚀性能均良好的新型不锈钢,不但有巨大的经济效益和实用性,而且能够扩大我国金属材料行业的核心竞争力。
1.2目的和意义(1)轻量化无铬轻质不锈钢主要是要求轻质,符合社会发展的需要,汽车轮船航天等轻量化发展。
铬虽是不锈钢必备的元素,但是铬密度为7.20克/cm3,为重金属,单位体积重量比较大,不符合现在社会发展的需求,因此需要用轻金属代替它。
铝及其合金是目前金属材料中应用最广泛的轻质金属材料,铝添加到其它合金中也能够大大减轻材料比重。
不锈钢材质报告范文

不锈钢材质报告范文不锈钢是一种常用的金属材料,广泛应用于制造业、建筑业和家居装饰等领域。
它具有抗腐蚀、耐高温、强度高等优点,因此备受青睐。
本篇报告将从不锈钢的组成、特性、应用领域和未来发展等方面进行探讨。
不锈钢是由铁、碳、铬和其他合金元素组成的合金材料。
其中,铬是最重要的合金元素之一,它与铁的化学反应产生一种稳定的氧化层,能够有效地防止钢铁生锈。
此外,其他合金元素如镍、钼和钒等也可以添加到不锈钢中,以增强其特性,如耐高温、耐腐蚀等。
不锈钢具有以下几个特点。
首先,不锈钢具有良好的耐腐蚀性能,能够在大部分的化学介质中稳定地工作。
其次,不锈钢具有较高的强度和硬度,在高温和低温环境下依然能够保持稳定的物理性能。
此外,不锈钢还具有良好的可塑性和焊接性,便于加工和制造。
不锈钢的应用领域非常广泛。
首先,不锈钢被广泛应用于制造业,如汽车工业、航空航天工业和电子工业等。
其次,不锈钢在建筑业有着重要的应用,如制作建筑结构、门窗和装饰材料等。
此外,不锈钢还用于家居装饰、厨具和医疗设备等领域,因为它具有卫生、易清洁的特点。
未来,不锈钢有着广阔的发展前景。
首先,随着人们对环境保护意识的增强,不锈钢作为一种可回收的材料将更受青睐。
其次,随着科技的不断进步,不锈钢的制造工艺和质量控制将不断提高,使其更加适应各种复杂环境的应用需求。
此外,不锈钢的合金化和功能化将成为未来的发展方向,以满足不同行业对材料性能的特殊要求。
总结起来,不锈钢是一种重要的金属材料,具有良好的耐腐蚀性、强度和可塑性等特点。
它的应用领域广泛,包括制造业、建筑业和家居装饰等。
未来,不锈钢有着广阔的发展前景,将在可持续发展和技术创新的推动下不断演进和壮大。
2205双相不锈钢焊接、热处理、金相分析论文

1 前言双相不锈钢发展应用开始于20世纪30年代,至今已发展了三代双相不锈钢。
第一代双相不锈钢:(1) 以美国在20世纪40年代开发的AISI329钢为代表,含高Cr、Mo,耐局部腐蚀性能好,但含碳量较高(C≤0.10%),焊接后其接头耐腐蚀性和韧性都较差,使钢在应用上受到限制,只适用于铸锻件。
(2) 日本在美国329钢基础上降低了含碳量,开发了SUS329J1钢,可作为焊接用钢。
(3) 60年代中期,瑞典开发了著名的3RE60钢,特点是超低碳,含Cr量为18%。
焊接及成型性能良好,使之成为第一代双相不锈钢的代表钢种。
第二代双相不锈钢:(1) 20世纪80年代瑞典先开发了不含Mo的超低碳型双相不锈钢。
代表钢种为SAF2304钢。
(2) 而后在第一代双相钢的基础上开发了含氮的超低碳型双相不锈钢。
典型钢种是瑞典开发的SAF2205钢,使双相钢应用范围很广。
第三代双相不锈钢:(1) 20世纪50年代后期发展了超级双相不锈钢,其特点是含碳量低(≤0.03%)含Mo、N量高(Mo约为4%,N约为0.3%);钢中铁素体含量达到40~45%;具有优良的抗点蚀能力,其PRE值大于40。
代表钢种为SAF2507钢。
双相不锈钢作为一种特殊的不锈钢材料,正在被日益广泛地应用于压力容器等相关的设备中。
双相不锈钢与奥氏体不锈钢相比,在抗晶间腐蚀、腐蚀、点蚀、间隙腐蚀,特别是抗氯化物导致的应力腐蚀开裂方面具有绝对的优势。
在石油、化工领域里应用前景非常远大。
如表1-1所示为部分双相不锈钢的牌号与化学成分[1]。
表1-1 部分双相不锈钢的牌号与化学成分数据来源:2004年2月《焊接设备与材料[J].焊接技术》2 双相不锈钢双相不锈钢系指不锈钢中既有奥氏体(α),又有铁素体(γ)组织结构的钢种,而且此二相组织要独立存在,且含量较大。
一般认为,在奥氏体基体上有≥15%铁素体或在铁素体基体上有≥15%的奥氏体,均可称为奥氏体+铁素体双相不锈钢,本文简称为双相不锈钢。
不锈钢焊接论文

不锈钢焊接摘要:本项目为非标产品除尘脱硫塔的制作、安装,其材质为超低碳不锈钢一316L,塔内为酸性介质,因此对焊缝抗腐蚀要求较高。
为严禁渗碳现象发生,施工过程对工艺选择及防护要求非常严格。
为此文中对焊工、焊接方法选择,施工工具和场地选择都提出了严格要求。
此设备薄壁,主体部分壳体仅吕=3mm,直径最大处甲二 2.sm,相对高度约为16m,焊接施工过程中要防止变形,装配过程施工难度较大,反变形的控制也是文中的亮点之一。
为保证焊缝耐腐蚀性能,必须在焊缝施焊完毕后较短时间内酸洗钝化以保证焊缝表面耐腐蚀性。
本论文从焊接准备、焊接施工工艺、焊接检验及安全防护四方面详述了除尘脱硫塔的高质量的焊接制作过程要求。
关键词:含硫废气防渗碳手工电弧焊变形小电流分段焊退焊法焊接工艺焊件组对点固后应尽快焊接,以防长时间放置变形或定位焊缝被氧化或破坏。
并且正式施焊前应对定位焊缝进行检查,如有缺陷处理后方可进行。
引弧应在坡口内正式起焊点后或引弧板上进行,严禁在坡口外的母材表面引弧和试验电流,并防止电弧擦伤母材。
电弧引燃并稳定燃烧后方可移到起焊点正式开始焊接。
应注意起弧和收弧处的质量,收弧时填满弧坑。
焊接时把钢板平铺在制作平台上或把卷好的钢板放在转胎或支座上,使卷好的钢板在焊接时能容易的绕其轴线转动,以便选择方便施焊的焊接位置。
此时可以选择平焊也可选择立焊位置,采用间隔分段、顺序焊接。
为保证焊缝防腐蚀效果,与常规容器焊接顺序相反,本设备内层最后焊接,焊接时人在设备内部,尽量选择平焊位置以保证焊接质量。
层间接头应错开。
焊接操作要点要严格控制引起腐蚀的一切因素,焊接过程中必须控制以下几点:a、施焊前坡口处必须清理干净,禁止油脂污染防止焊接时引起气孔和渗碳,必要时可用丙酮擦拭清理。
b、避免飞溅和在坡口以外的部位引弧;c、焊缝表面要求光洁,彻底清除残渣;d、焊缝根部接触腐蚀介质时不宜余留垫板或锁边,要保证焊透;e、避免层间温度过高,必要时可采用水冷。
不锈钢研究报告范文

不锈钢研究报告范文不锈钢是一种合金钢,由于其具有较高的耐腐蚀性、耐高温性和机械性能,在许多领域得到广泛应用。
本报告旨在探讨不锈钢的研究进展及其应用领域。
一、不锈钢的研究进展不锈钢的研究主要集中在合金元素、材料组织和制备工艺等方面。
首先,合金元素的添加可以改变不锈钢的特性。
例如,添加铬元素可以提高不锈钢的耐腐蚀性能;添加镍元素可以提高不锈钢的强度和塑性。
其次,材料的组织对不锈钢的性能也有影响。
通过控制材料的相变和晶界结构,可以优化不锈钢的力学性能和耐蚀性能。
最后,制备工艺的创新对于提高不锈钢的性能至关重要。
采用新的制备工艺,如高温变形和冷变形等,可以获得具有较高强度和塑性的不锈钢材料。
二、不锈钢的应用领域不锈钢在许多领域都有广泛的应用。
首先,不锈钢在建筑领域得到广泛应用。
不锈钢板材、管材和型材可以用于建筑立面、屋顶和室内装饰等。
其次,不锈钢在汽车工业中也有重要的应用。
由于其耐腐蚀性能和高温性能,不锈钢可以用于汽车的排气系统、液压系统和制动系统等。
此外,不锈钢还可用于制作厨房用具、化工设备、医疗器械等。
三、不锈钢研究的挑战尽管不锈钢已取得了许多研究进展和广泛应用,但仍面临一些挑战。
首先,不锈钢的生产成本相对较高,限制了其在一些领域的应用。
其次,不锈钢在高温和高应力环境下可能会发生形变和断裂等问题。
最后,不锈钢的耐腐蚀性能还有待进一步提高,以满足特定工况下的需求。
综上所述,不锈钢的研究进展和应用领域都取得了较大的进展,但仍面临一些挑战。
未来的研究应重点关注不锈钢的成本降低、性能提高和应用拓展等方面,以推动不锈钢行业的发展。
- 1、下载文档前请自行甄别文档内容的完整性,平台不提供额外的编辑、内容补充、找答案等附加服务。
- 2、"仅部分预览"的文档,不可在线预览部分如存在完整性等问题,可反馈申请退款(可完整预览的文档不适用该条件!)。
- 3、如文档侵犯您的权益,请联系客服反馈,我们会尽快为您处理(人工客服工作时间:9:00-18:30)。
不锈钢焊接常见缺陷及预防措施
摘要:本文简单阐述了不锈钢焊接件在焊接过程中所产生的常见缺陷及预防措施;主要根据不锈钢的金相组织的不同及焊接时产生的缺陷类型不同,探讨了影响不锈钢钢焊接性的原因,从而制定相关的缺陷预防措施。
通过结果分析,可以通过选择合理的焊接工艺参数、正确选择焊接材料、提高焊工技能等一系列措施来预防不锈钢钢焊接常见缺陷的产生。
关键词:焊接缺陷; 产生原理;预防措施
不锈钢的焊接性
1、不锈钢的焊接性
1)焊接接头的抗腐蚀性
(l)整体腐蚀。
任何不锈钢在腐蚀性介质作用下,其工作表面总会有腐蚀现象产生,这种腐蚀叫整体腐蚀。
(2)晶间腐蚀易发生在奥氏体不锈钢中。
晶间腐蚀发生于晶粒边界,所以叫晶间腐蚀。
这种腐蚀可以发生在热影响区、焊缝或焊合线上,是奥氏体金属最危险的破坏形式之一
目录
一、绪论 1
二、本论 1 (一)不锈钢焊接缺陷 1
1.不锈钢焊接缺陷的概念及分类 1
2.不锈钢常见缺陷的特征 1 (二)影响不锈钢焊接的因素 1
1.焊接前的准备 1
2.焊接参数 1
(三)不锈钢焊接缺陷的形成原因及分析预防措施 1
1.气孔产生的原因及解决方法 1
2 .裂纹产生的原因及解决方法 1
3.电弧产生的偏吹及解决方法1
三、结论 1
致谢 1 参考文献 1
一、绪论
随着工业技术的发展,焊接技术被广泛用于大型与高参数设备制造中。
焊接是大型安装工程建设中的一项关键工作,其质量的好坏、效率的高低直接影响工程的安全运行和制造工期。
因此确保焊接质量、预防焊接热裂纹的产生成为一个重要的课题。
实践证明,母材及焊接材料的质量、坡口加工和装配精度、坡口表面清理状况、焊接设备、焊接工艺参数、焊接工艺规程、焊接技术水平、外部环境等,任何一个环节处理不当,都会产生焊接缺陷,影响焊接质量。
本文阐述了常见焊接热裂纹的预防措施,从而更好的制定不锈钢焊接的预防措施二、本论
(一)不锈钢焊接缺陷
1.1 焊接缺陷的概念及分类
焊接缺陷是指焊接过程中在焊接接头中产生的金属不连续、不致密或连接不良的现象。
它直接影响产品质量和安全可靠性,造成焊接结构的实效,以至发生破坏事故。
常见焊接缺陷分为在宏观上可分为七种:
(1)裂纹在焊接应力及其它致脆因素共同作用下,焊接接头中局部地区的金属原子结合力遭到破坏而形成的新界面而产生缝隙;
(2)气孔焊接时,熔池中的气泡在时未能逸出而残留下来所形成的空穴;
(3)未熔合熔焊时,焊道与母材之间或焊道之间未完全熔化结合的部分;点焊时母材与母材之间未完全熔化结合的部分;
(4)未焊透焊接时接头根部未完全熔透的现象;
(5)夹渣焊后残留在焊缝中的熔渣;
(6)夹钨焊接过程中,由于某些原因,使钨极强烈的发热,端部熔化、蒸发,使钨极过渡到焊缝中,并残留在焊缝内形成夹钨;
(7)形状缺陷焊缝表面形状可以反映出来的不良状态。
1.2 常见焊接缺陷的特征
常见焊接缺陷的主要特征有:
(1)裂纹具有尖锐的缺口和大的长宽比;1、刚性裂缝2、毛隙裂缝3、碳、硫元素造成的裂缝
(2)气孔出现在铸件内部或表层,截面形状呈圆形、椭圆形或针头形状,孤立存在或成群分布的孔洞;内部气孔,表面气孔,接头气孔。
(3)未熔合可以分为坡口未熔合、焊道之间未熔合、焊缝根部未熔合;
(4)未焊透减少了焊缝的有效面积,使接头强度下降;
(5)夹渣主要存于焊道之间和焊道与母材之间;
(6)夹钨钨极残留在焊缝内;
(7)电弧产生偏吹
(二)影响不锈钢焊接的因素
2.1.焊接前的准备:
4mm一下的厚度不用开破口,直接焊接,单面一次焊透。
4到6 mm厚度对接焊缝可采用不开破口接头双面焊。
6 mm以上,一般开V或U,X形坡口。
其次:对焊件,填充焊丝进行除油和去氧化皮。
以保证焊接质量
2.2焊接参数
包括焊接电流,钨极直径,弧长,电弧电压,焊接速度,保护气流,喷嘴直径等。
1,焊接电流是决定焊缝成形的关键因素。
通常根据焊件材料,厚度,及坡口形状来决定的。
2,焊极直径根据焊接电流大小决定,电流越大,直径也越大。
3,焊弧和电弧电影,弧长范围约0.5到3mm,对应的电弧电压为8~10V。
4,焊速:选择时要考虑到电流大小,焊件材料敏感度,焊接位置及操作方式等因素决定。
(三)不锈钢焊接常见缺陷的产生原因及分析
3.1气孔的产生及解决方法:
(1)内部气孔:有两种形状。
一种是球状气孔多半是产生在焊缝的中部。
产生的原因: a)焊接电流过大;b)电弧过长;c)运棒速度太快;d)
熔接部位不洁净; e)焊条受潮等。
上述造成气孔原因如进行适当调整和注意焊接工艺及操作方法,就可以得到解决。
(2)表面气孔:产生表面气孔的原因和解决方法:a)母材含C、S、Si 量高容易出现气孔。
其解决办法或是更换母材,或是采用低氢渣系的焊条。
b)焊接部位不洁净也容易产生气孔。
因此焊接部位要求在焊接前清除油污,铁锈等脏物。
使用低氢焊条焊接时要求更为严格。
c)焊接电流过大。
使焊条后半部药皮变红,也容易产生气孔。
因此要求采取适宜的焊接规范。
焊接电流最大限度以焊条尾部不红为宜。
d)低氢焊条容易吸潮,因此在使用前均需在350℃的温度下烘烤1小时左右。
否则也容易出现气孔。
(3)焊波接头气孔:使用低氢焊条往往容易在焊缝接头处出现表面和内部气孔,其解决办法:焊波接头时,应在焊缝的前进方向距弧坑9~10mm处开始引弧,电弧燃烧后,先作反向运棒返向弧坑位置,作充分熔化再前进,或是在焊缝处引弧就可以避免这种类型的气孔产生。
3.2裂缝的产生及解决方法
(1)刚性裂缝:往往在焊接当中发现焊缝通身的纵裂缝,主要是在焊接时产生的应力造成的。
在下列情况下焊接应力很大: a)被焊结构刚性大; b)焊接电流大,焊接速度快; c)焊缝金属的冷却速度太快。
因而在上述的情况下很容易产生纵向的长裂缝。
解决办法:采用合理的焊接次序或者在可能的情况下工件预热,减低结构的刚性。
特厚板和刚性很大的结构应采用低氢焊条使用合适的电流和焊速。
(2)碳、硫元素造成的裂缝:被焊母材的碳和硫高或偏析大时容易产生裂缝。
解决办法:将焊件预热,或用低氢焊条。
(3)毛隙裂缝:毛隙裂缝是在焊敷金属内部发生,不发展到外部的毛状微细裂缝。
考虑是焊敷金属受急速冷却而脆化,局部发生应力及氢气的影响。
对此的防止方法是:使其焊件的冷却速度缓慢些,可能的条件下焊件进行预热,或者使用低氢焊条可得到满意的解决。
3.3电弧产生偏吹
使用低氢焊条在直流电焊机上焊接时往往发生偏吹现象。
可以用下面方法解决。
(1)地线放在电弧偏吹的方向。
(2)地线分成两个以上。
(3)顺着电弧偏吹的方向进行焊接。
(4)采取短弧操作。
三、结论
参考文献
1.英若采.《熔焊原理及金属材料焊接》.机械工业出版社.2000.5.
参考内容:第四章焊接冶金缺陷;第四节焊接热裂纹
2.陈宝国.《焊接技术》.化学工业出版社.2007.1.
参考内容:第1章不锈钢的焊接
3.张文明,焦万才.《焊条电弧焊》.辽宁科学技术出版社.2007.
4.
参考内容:第四章焊接缺陷;第二节焊接缺陷与对策
4.刘政军,徐德昆,《不锈钢焊接及质量控制》.化学工业出版社.2008
参考内容:第四章奥氏体不锈钢焊接.第二节埋弧焊
5.贾凤祥,《不锈钢焊接钢管》山西科学技术出版社200
6.10
参考内容:第三章不锈钢焊管原料及焊接材料,第二节金属的焊接性。