热流道系统详细介绍
热流道系统的分类

热流道系统的分类在应用热流道技术时,浇口型式的正确选择至关重要。
浇口型式直接决定热流道系统元件的选用及模具的制造与使用。
1热尖式热流道系统2浇套式热流道系统3阀式热流道系统每种类型的热流道系统都有其重要的应用特点与适用范围。
在选用浇口与热流道系统种类时需要考虑很多因素,其中最重要的是塑料基体种类与添加剂、零件的重量与尺寸壁厚、零件的质量要求、工具寿命及零件产量要求等。
1、热尖式热流道系统(HOT TIP)其工作原理就是通过位于喷嘴前端的镶件HOT TIP与冷却系统相结合,以对浇口处的塑料成型加工温度进行精确的调整和控制。
因而喷嘴镶件HOT TIP的制造材料与形状设计非常重要。
热尖式(HOT TIP)热流道系统可以用于加工绝大多数结晶型和非结晶型塑料如PP、PE、PS、LCP、PA、PET、PBT、PEEK、POM、PEI、PMMA、 ABSPVC、PC、PSU、TPU等。
一般来说,热尖式浇口多用于中小尺寸零件的加工,尤其适用于微小零件的加工。
浇口截面直径大多在0.5mm- 2.0mm之间。
浇口截面直径的确定主要由零件重量与壁厚决定,当然也要考虑材料与零件质量要求。
若使用截面直径较小的浇口,注射充模阶段结束后浇口封闭快、零件上浇口痕迹小、零件表面美观质量好。
如果浇口直径过小,将导致塑料流经浇口时剪切速率过高,会严重损坏塑料熔体分子链结构或塑料中的添加材料,致使制品质量不合格无法满足使用要求。
在对浇口尺寸的选择上一惯做法是根据零件浇口处壁厚来初步确定浇口大小:浇口直径 =(0.75-1.0)零件浇口处壁厚。
加工易流塑料取较小值,加工难流动的塑料或对剪切敏感的塑料则取较大值。
通常热尖式浇口直接开在零件上,亦可将其开在冷浇道上再将冷浇口开在零件上。
这就是热流道与冷流道相结合的一种模具系统。
在应用热尖式浇口制作塑料零件时,总会或多或少在零件上留下浇口痕迹。
很多时侯浇口痕迹会高出零件表面,影响到零件的美观或影响到与其它零件的装配。
简介
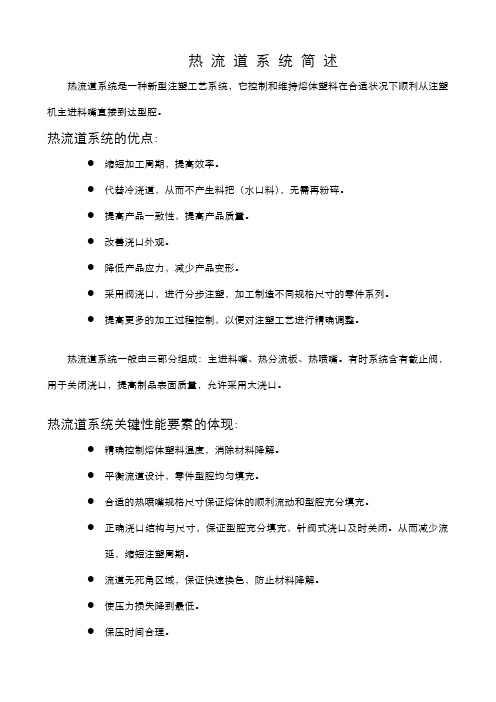
热流道系统简述
热流道系统是一种新型注塑工艺系统,它控制和维持熔体塑料在合适状况下顺利从注塑机主进料嘴直接到达型腔。
热流道系统的优点:
●缩短加工周期,提高效率。
●代替冷浇道,从而不产生料把(水口料),无需再粉碎。
●提高产品一致性,提高产品质量。
●改善浇口外观。
●降低产品应力,减少产品变形。
●采用阀浇口,进行分步注塑,加工制造不同规格尺寸的零件系列。
●提高更多的加工过程控制,以便对注塑工艺进行精确调整。
热流道系统一般由三部分组成:主进料嘴、热分流板、热喷嘴。
有时系统含有截止阀,用于关闭浇口,提高制品表面质量,允许采用大浇口。
热流道系统关键性能要素的体现:
●精确控制熔体塑料温度,消除材料降解。
●平衡流道设计,零件型腔均匀填充。
●合适的热喷嘴规格尺寸保证熔体的顺利流动和型腔充分填充。
●正确浇口结构与尺寸,保证型腔充分填充,针阀式浇口及时关闭。
从而减少流
延,缩短注塑周期。
●流道无死角区域,保证快速换色,防止材料降解。
●使压力损失降到最低。
●保压时间合理。
热流道系统简介

热浇道系统简介现时常见的热浇道系统,主要由分流板、热咀和温度控制器三大部份组成。
热浇道系统是透过精密的温控手段,将熔融塑料通过精密设计的分流板和热嘴,直接输送至模腔里,其好处包括:有效减低浇道的压力;熔体的流动性得到提高;材料密度均匀;产品的内应力减少,使产品获得较小的变形、较好的产品表面质量和力学性能。
热浇道系统的另一特点,是热嘴直接将熔融塑料注入模腔内,在脱模的过程中,浇口自然断开,消除了传统注塑工艺带来的浇道废料,除免去处理浇道废料的后加工工序外,更消除了废料所带来的附加热量,缩短冷却时间,获得更快的生产周期。
热浇道技术已成熟要获得理想的注塑效果,热浇道需要确保其内的塑料熔体在注射、保压和冷却阶段保持正确的温度。
最早期的热浇道系统,在温度控制上未臻完善,随着后期的逐步改良,现时的热浇道技术已相当成熟。
本文会简介热浇道的发展简史和其基本结构,希望加深读者对这方面的认识。
绝缘式浇道系统绝缘式浇道系统是最早期的热浇道系统,其工作原理是昨用塑料本身极低的热传递系防止热量散于失于模板中,以保持塑料的熔融状态。
在浇道的设计上,口径尽量加大,以使浇道中央的塑料在首次充填后,借着塑化材料不断地流通而保持熔融。
至于浇道最外层接触模板的塑料,会因遇冷而凝结成固化层,在固化层中间就是不断流通的塑料通道。
一旦形成固化层,在熔融塑料与模板间会产生不错的绝热效果,足以确保熔融塑料在快速连续地生产下不致发生浇道全面凝结。
但是只要有任何短暂的生产停顿,还是不能避免整条浇道的固化。
绝缘式浇道难于控制熔融塑料温度这种原始的热浇道系统难于控制熔融塑料的温度,导致浇道冷凝与浇口阻塞的现象不断发生。
为了解决此问题,就有了热探捧的出现,即在浇口前的通道中,加装一支管形加热器,藉此控制熔融塑料的温度,同时,浇口的控制、成品的顶出均获得改善。
事实上,早期的绝热式浇道系统只适用于低黏度塑料,随着高黏度及成型性较差的工程塑料的不断出现,对流动通道中熔融塑料的温度控制也越重要,所以又衍生出歧管式浇道系统。
热流道基础知识普及

应用实例
应用前 应用后
四、浇口形状实例
•
开放式热咀
•
针阀式热咀
Sprue水口 Runner流道
Nozzle熱嘴
3、减少成本的应用实例
4、热流道系统的优缺点
优点 节省原料, 减少注塑週期,提高生产效率 原材料100%产品化,,减少二次料引起的 不良 提高产品品质(压力,产品的内应力降低) 缺点 模具成本上升 维护保修需要专业的人员
模具设计要充分检验
延长模具寿命 不需要預留流道位,减少模具尺寸. 容易定澆 口位.
热流道常识培训 资料
一、热流道系统简介 二、热流道结构 三、热流道辅助设备 四、浇口形状实例
五、提问
一 、 热流道系统简介
1、定义
塑胶注塑模具中为了促进塑胶熔体在型腔中 的流动,把主流道和分流道用适当的方法加热,使
塑胶一直保持熔融状态,实现连续注塑的机构就是
热流道系统。
2、冷、热流道对比
Manifold分流板
2、电磁阀
* 分气缸油缸 气缸所需要的压力为6KG~8KG/CM2 油缸所需的压力为10KG~30KG/CM2 电磁阀 电磁阀的输入电压是24V
下行 气压电磁阀
*
上行
下行
液压压电磁阀
上行
cooling
3、 时间控制器
* 多个 型腔注塑量和形状不一样或 大型产品用多个点成型时,产品会打不 满或者有较严重的熔接痕。 * 为了改善这些问题,利用时间控 制器和电磁阀组,来控制每个入水口的 注塑顺序达到好的效果。
二、热流道结构
三、热流道辅助设备
1、温控箱
* PID智能控制 * 1组表芯承受的最大电流15 * J型,K型可调整 * 华氏,摄氏可调整 * SSR PWM * 具有SOFT START 功能 * 国际化的标准表芯
热流道系统介绍
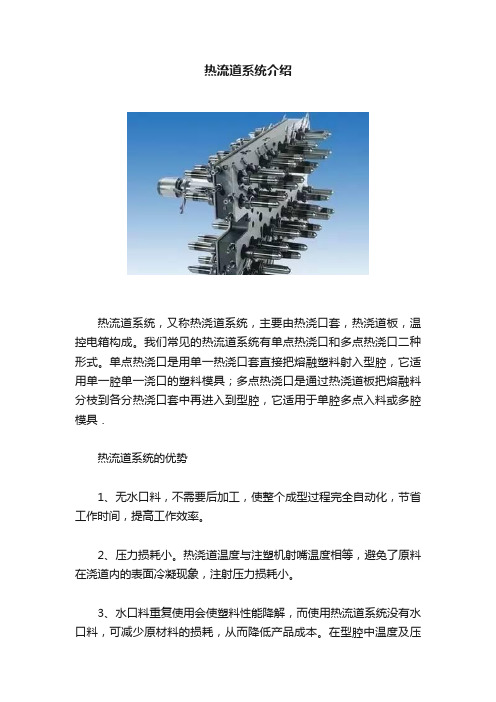
热流道系统介绍热流道系统,又称热浇道系统,主要由热浇口套,热浇道板,温控电箱构成。
我们常见的热流道系统有单点热浇口和多点热浇口二种形式。
单点热浇口是用单一热浇口套直接把熔融塑料射入型腔,它适用单一腔单一浇口的塑料模具;多点热浇口是通过热浇道板把熔融料分枝到各分热浇口套中再进入到型腔,它适用于单腔多点入料或多腔模具.热流道系统的优势1、无水口料,不需要后加工,使整个成型过程完全自动化,节省工作时间,提高工作效率。
2、压力损耗小。
热浇道温度与注塑机射嘴温度相等,避免了原料在浇道内的表面冷凝现象,注射压力损耗小。
3、水口料重复使用会使塑料性能降解,而使用热流道系统没有水口料,可减少原材料的损耗,从而降低产品成本。
在型腔中温度及压力均匀,塑件应力小,密度均匀,在较小的注射压力下,较短的成型时间内,注塑出比一般的注塑系统更好的产品。
对于透明件、薄件、大型塑件或高要求塑件更能显示其优势,而且能用较小机型生产出较大产品。
4、热喷嘴采用标准化、系列化设计,配有各种可供选择的喷嘴头,互换性好。
独特设计加工的电加热圈,可达到加热温度均匀,使用寿命长。
热流道系统配备热流道板、温控器等,设计精巧,种类多样,使用方便,质量稳定可靠。
热流道系统应用的不足之处1、整体模具闭合高度加大,因加装热浇道板等,模具整体高度有所增加。
2、热辐射难以控制,热浇道最大的毛病就是浇道的热量损耗,是一个需要解决的重大课题。
3、存在热膨胀,热胀冷缩是我们设计时要考虑的问题。
4、模具制造成本增加,热浇道系统标准配件价格较高,影响热浇道模具的普及。
热流道模具的优点热流道模具在当今世界各工业发达国家和地区均得到极为广泛的应用。
这主要因为热流道模具拥有如下显着特点:1、缩短制件成型周期因没有浇道系统冷却时间的限制,制件成型固化后便可及时顶出。
许多用热流道模具生产的薄壁零件成型周期可在5秒钟以下在纯热流道模具中因没有冷浇道,所以无生产废料。
这对于塑料价格贵的应用项目意义尤其重大。
热流道系统

热流道系统 热流道系统是通过加热的办法来保证流道和浇口的塑料保持 融融状态。热流道系统一般由热喷嘴、分流板、温控箱和附 件等几部分组成。热喷嘴一般包括两种:开放式热喷嘴和针 阀式热喷嘴。由于热喷嘴形式直接决定热流道系统选用和模 具的制造,因而常相应的将热流道系统分成开放式热流道系 统和针阀式热流道系统。
热流道系统工作原理是在塑料模具内安装加
热器;利用加热和温度控制的原理使模具的
浇口保持融融状态。犹如注塑机的炮台直接
延伸到产品型腔的进浇点,使产品更直接轻
松成型。
目录
• • • • • • • • • • • 热流道系统简介 原理 热流道分类 由模具的结构来探讨其差异性 热流道与模具业 塑胶材料特性介绍 热流道模具的优点 热流道模具的缺点 热流道系统的组成 热流道应用主要技术关键 热流道模具的应用范围
热流道系统简介
热流道在成型生产上面起着非常大的作用。热流 道系统是一个Байду номын сангаас合体。不是指单个产品。它其中 包括了热喷嘴、温控器、分流板等。这些一起就 组成了热流道系统。
热流道系统详细介绍

热流道知识热流道分类:绝热流道、冷流道、热流道。
绝热流道的设计复杂,但效果和维护成本非常低,不会耽误工时。
冷流道和热流道斑竹基本上谈到了特点。
我再具体补充一些自己的看法。
热流道分类:开放式、针阀式。
开放式结构简单、对材料的局限性较高,易出现拉丝和泄露,表面质量差,在国外的高精密模具中应用较少,同一副模具可和不同厂家的针阀式混用。
很多公司能自己制造。
针阀式热流道节省材料,塑件表面美观,同时内部质量紧密、强度高。
现在世界上有两大类针阀式热流道(根据注射原理):气缸式和弹簧式。
气缸式依*控制器和时序控制器控制气缸推动针阀的关闭,结构较复杂,但本身设计简单。
主要有DME(美国)热流道是通过加热的办法来保证流道和浇口的塑料保持熔融状态。
由于在流道附近或中心设有加热棒和加热圈,从注塑机喷嘴出口到浇口的整个流道都处于高温状态,使流道中的塑料保持熔融,停机后一般不需要打开流道取出凝料,再开机时只需加热流道到所需温度即可。
因此,热流道工艺有时称为热集流管系统,或者称为无流道模塑。
热流道技术的优、缺点热流道技术与常规的冷流道相比有以下的好处:1、节约原材料,降低成。
2、缩短成型周期,提高机器效率3、改善制品表面质量和力学性能。
4、不必用三板式模具即可以使用点浇口。
5、可经济地以侧浇口成型单个制品。
6、提高自动化程度。
7、可用针阀式浇口控制浇口封冻。
8、多模腔模具的注塑件质量一致。
9、提高注塑制品表面美观度。
但是,每一项技术都会有自身的缺点存在,热流道技术也不例外:1、模具结构复杂,造价高,维护费用高。
2、开机需要一段时间工艺才会稳定,造成开价废品较多。
3、出现熔体泄露、加热元件故障时,对产品质量和生产进度影响较大。
上面第三项缺点,通过采购质量上等的加热元件、热流道板以及喷嘴并且使用时精心维护,可以减少这些不利情况的出现。
热流道系统的结构热流道系统一般由热喷嘴、分流板、温控箱和附件等几部分组成。
热喷嘴一般包括两种:开放式热喷嘴和针阀式热喷嘴。
热流道系统

热流道系统一、概述:热流道系统是塑胶模具生产设备中的重要组成部分,热流道系统一般由热喷嘴、分流板、温控箱和附件等几部分组成。
配合使用于各种不同类型的塑胶零件成型,其工作原理是在注射模内装上分流板及热嘴,利用加热和温度控制的原理,使模具的流道部分保持熔融状态,制品的浇口如同直接接触到注塑机的射嘴一样,那么成品在脱模时就不会拖着一条或者多条胶口。
一套完整的热流道系统是由平衡式分流板、热嘴、高精度温度控制器组成。
伴随着模具行业的发展,热流道系统也日益发展起来。
温控箱包括主机、电缆、连接器和接线插座等。
热流道附件通常包括加热器和热电偶、流道密封圈、接插件及接线盒等。
塑料温度的控制。
在热流道模具应用中塑料温度的控制极为重要。
许多生产过程中出现的加工及产品质量问题直接来源于热流道系统温度控制得不好。
如使用热针式浇口方法注射成型时产品浇口质量差问题,多型腔模具中的零件填充时间及质量不一致问题等,如果可能应尽量选择具备多区域分别控温的热流道系统,以增加使用的灵活性及应变能力。
而且,随着目前模具要求变高,对温控要求提出更高的要求,目前在该领域能够投入研发生产的单位并不多,国内还在采用80年代初期从国外进口仿制产品。
二、4回路温控器的开发应用厦门宇电自动化科技有限公司采用存储容量的单片CPU,大量采用SMD贴片工艺,仅用2片线路板,4层板技术。
采用14位A/D转换器,0.2级精度。
开发全新的4路PID温度调节工控D5模块,可安装在DIN导轨上,每个模块安装宽度仅为22.5mm,是目前全球同类产品中安装宽度最小的;且在22.5mm宽度内。
该产品既可通过与计算机通讯来实现对仪表的各项操作及参数显示,也可采用1394连线外接宇电E8型专用显示器设置仪表内部全部参数,按照安装操作更灵活方便。
AI-7048D5多回路温控系统图图1实现了多路并行控制,控制精度更高,集成度更大,反应灵敏。
D5系列工控模块不仅可以通过RS485通讯接口与计算机或触摸屏连接组建测控系统;PLC配套使用,作为PLC的扩充温控系统(无论从性价比还是专业性角度来看,都超过PLC的模拟量控制功能),操作人员直接通过中文显示的触摸屏进行操作,比操作仪表和记录仪更直观简便。
热流道转冷流道结构

热流道转冷流道结构
热流道系统和冷流道系统是塑料注塑模具中用于导热和冷却的两个重要组成部分。
它们的结构和功能不同,而热流道转冷流道是一种在注塑成型过程中可以实现动态切换的系统。
热流道系统(Hot Runner System):
热流道系统是指通过将热的塑料材料注射到模具中的热流道中,以维持塑料材料的熔融状态,并直接将热的塑料材料注入成型部件的一种系统。
热流道系统主要包括加热元件、热流道模块、温度控制系统等。
冷流道系统(Cold Runner System):
冷流道系统是指通过在注塑模具中设置冷却通道,使塑料材料在流道中冷却成型后再进入成型部件的一种系统。
冷流道系统的主要组成部分包括冷却通道、模具底板等。
热流道转冷流道结构:
热流道转冷流道结构是一种可以在注塑成型过程中动态切换热流道和冷流道的系统,以满足不同注塑产品的要求。
这种结构通常包
括以下特点:
热流道部分:
在需要的时候,热流道部分可以通过加热元件,将塑料材料维持在熔融状态,并通过热流道注射到模具中。
冷流道部分:
在另一种情况下,系统可以通过控制冷却通道,将塑料材料冷却成型后再进入成型部件,实现冷流道注塑。
切换机构:
热流道转冷流道结构通常会配备相应的切换机构,用于在注塑过程中动态切换热流道和冷流道。
温度控制系统:
配备相应的温度控制系统,以确保在切换过程中模具和热流道、冷流道的温度能够被精确控制。
这种热流道转冷流道结构可以灵活应对不同注塑产品的生产需求,提高生产效率和产品质量。
这种系统适用于需要灵活切换生产模式、生产不同型号产品的注塑模具。
热流道工作原理

热流道工作原理
热流道工作原理是指通过电加热将热能传导至流道系统,以保持塑料材料在注塑过程中的熔融状态,实现高效、准确的注塑成型。
其工作原理主要包括以下几个步骤:
1. 加热:通过热流道系统中的加热元件(如电热管或热板)向流道传递热能,将塑料原料加热至熔融温度。
2. 保温:热能将传导至整个流道系统,包括模具中的流道和喷嘴。
在注塑过程中,热流道必须保持一定的温度,以确保塑料材料始终处于熔融状态,避免冷却造成流道堵塞。
3. 注射:熔融塑料通过喷嘴进入模具的腔体中。
在注塑过程中,热流道会保持塑料材料的熔融温度,提高塑料流动性,同时避免材料过早冷却导致注塑不良。
4. 冷却:在塑料材料填充腔体后,冷却系统会开始发挥作用,冷却模具温度以使塑料材料凝固成型。
与传统注塑相比,热流道可以通过独立的冷却控制,更精确地调整冷却速度和温度,以提高注塑成型品质和效率。
热流道工作原理通过控制温度进行熔融和冷却的优化,能够有效避免流道堵塞、减少材料损耗和工艺参数调试时间,提高注塑产能和制品质量,成为现代注塑技术中不可或缺的重要工艺手段。
热流道的原理及应用图解
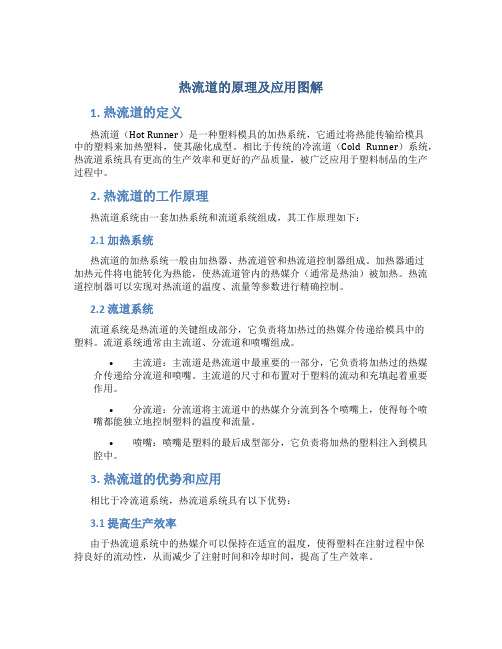
热流道的原理及应用图解1. 热流道的定义热流道(Hot Runner)是一种塑料模具的加热系统,它通过将热能传输给模具中的塑料来加热塑料,使其融化成型。
相比于传统的冷流道(Cold Runner)系统,热流道系统具有更高的生产效率和更好的产品质量,被广泛应用于塑料制品的生产过程中。
2. 热流道的工作原理热流道系统由一套加热系统和流道系统组成,其工作原理如下:2.1 加热系统热流道的加热系统一般由加热器、热流道管和热流道控制器组成。
加热器通过加热元件将电能转化为热能,使热流道管内的热媒介(通常是热油)被加热。
热流道控制器可以实现对热流道的温度、流量等参数进行精确控制。
2.2 流道系统流道系统是热流道的关键组成部分,它负责将加热过的热媒介传递给模具中的塑料。
流道系统通常由主流道、分流道和喷嘴组成。
•主流道:主流道是热流道中最重要的一部分,它负责将加热过的热媒介传递给分流道和喷嘴。
主流道的尺寸和布置对于塑料的流动和充填起着重要作用。
•分流道:分流道将主流道中的热媒介分流到各个喷嘴上,使得每个喷嘴都能独立地控制塑料的温度和流量。
•喷嘴:喷嘴是塑料的最后成型部分,它负责将加热的塑料注入到模具腔中。
3. 热流道的优势和应用相比于冷流道系统,热流道系统具有以下优势:3.1 提高生产效率由于热流道系统中的热媒介可以保持在适宜的温度,使得塑料在注射过程中保持良好的流动性,从而减少了注射时间和冷却时间,提高了生产效率。
3.2 降低生产成本热流道系统减少了冷却时间和废品产生,降低了生产成本。
同时,由于去除了冷道系统,可以减少注塑机的锁模力,降低了设备的投资成本。
3.3 改善产品质量热流道系统可以精确控制塑料的温度和流量,保证了每个喷嘴注入的塑料质量一致,减少了产品的热变形和缺陷。
热流道系统在以下领域有广泛的应用:•医疗器械:热流道系统被广泛应用于制造医疗器械,如注射器、输液器等。
由于产品的精度和质量要求较高,热流道系统能够满足其生产需求。
热流道的工作原理

热流道的工作原理
热流道的工作原理是利用热流来保持塑料在熔融状态,并将其顺利注入模具中形成所需产品。
以下是热流道的工作原理:
1. 注塑机加热:首先,注塑机中的加热机会将塑料原料加热至熔融状态。
熔融的塑料会被注塑机的射嘴推送进入热流道系统。
2. 热流道设置:热流道系统位于模具中,由多个加热器和控制系统构成。
每个热流道通常由一个或多个加热器、温度传感器、控制器和阀门组成。
3. 热流系统加热:加热器通过加热热流道系统,使其达到所需的注塑温度。
热流道与注塑件的接触面通常被加热至稍高于塑料熔点的温度,以确保塑料保持在熔融状态。
4. 塑料注入:一旦热流道达到所需温度,射嘴开始注入熔融塑料。
热流道系统中的控制器能够准确控制塑料流动的速度和压力。
5. 模具填充:熔融塑料通过热流道系统进入模具,填充模具的空腔。
模具的形状和设计决定了塑料产品的最终形态。
6. 冷却和固化:一旦塑料填充完毕,热流道系统会停止供应热流,并通过冷却系统来降低模具温度,使塑料迅速冷却和固化。
7. 产品弹出:当塑料固化后,模具会分开,并通过退模机构将成品弹出。
这样,热流道系统可以准备下一周期的注塑过程。
总的来说,热流道通过加热和控制塑料的温度和流动,确保塑料保持在正确的状态并注入模具中,以实现高质量的塑料制品生产。
热流道知识点总结
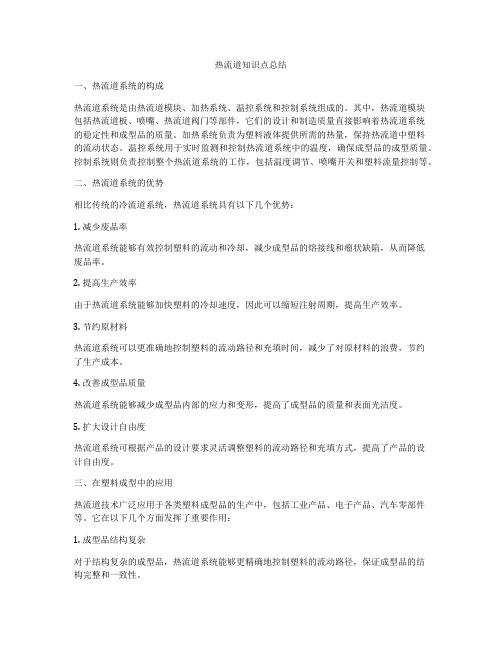
热流道知识点总结一、热流道系统的构成热流道系统是由热流道模块、加热系统、温控系统和控制系统组成的。
其中,热流道模块包括热流道板、喷嘴、热流道阀门等部件,它们的设计和制造质量直接影响着热流道系统的稳定性和成型品的质量。
加热系统负责为塑料液体提供所需的热量,保持热流道中塑料的流动状态。
温控系统用于实时监测和控制热流道系统中的温度,确保成型品的成型质量。
控制系统则负责控制整个热流道系统的工作,包括温度调节、喷嘴开关和塑料流量控制等。
二、热流道系统的优势相比传统的冷流道系统,热流道系统具有以下几个优势:1. 减少废品率热流道系统能够有效控制塑料的流动和冷却,减少成型品的熔接线和瘤状缺陷,从而降低废品率。
2. 提高生产效率由于热流道系统能够加快塑料的冷却速度,因此可以缩短注射周期,提高生产效率。
3. 节约原材料热流道系统可以更准确地控制塑料的流动路径和充填时间,减少了对原材料的浪费,节约了生产成本。
4. 改善成型品质量热流道系统能够减少成型品内部的应力和变形,提高了成型品的质量和表面光洁度。
5. 扩大设计自由度热流道系统可根据产品的设计要求灵活调整塑料的流动路径和充填方式,提高了产品的设计自由度。
三、在塑料成型中的应用热流道技术广泛应用于各类塑料成型品的生产中,包括工业产品、电子产品、汽车零部件等。
它在以下几个方面发挥了重要作用:1. 成型品结构复杂对于结构复杂的成型品,热流道系统能够更精确地控制塑料的流动路径,保证成型品的结构完整和一致性。
2. 薄壁成型热流道系统能够加速塑料的冷却速度,使得薄壁成型更容易实现,避免了因塑料冷却不均匀而产生的熔接线和卡痕等缺陷。
3. 高精度成型对于精度要求高的成型品,热流道系统能够保证成型品的尺寸精度和表面质量,提高了成型品的可靠性和一致性。
四、热流道系统的设计和调试1. 热流道系统的设计热流道系统的设计需要根据成型品的结构和要求进行合理的布局和尺寸确定。
设计时需要考虑塑料的流动路径、冷却时间、喷嘴的布置位置等因素,以保证成型品的质量和生产效率。
注塑模具热流道
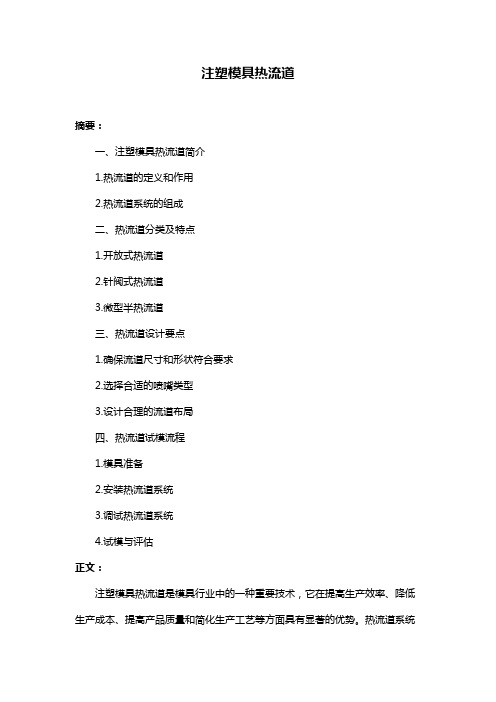
注塑模具热流道
摘要:
一、注塑模具热流道简介
1.热流道的定义和作用
2.热流道系统的组成
二、热流道分类及特点
1.开放式热流道
2.针阀式热流道
3.微型半热流道
三、热流道设计要点
1.确保流道尺寸和形状符合要求
2.选择合适的喷嘴类型
3.设计合理的流道布局
四、热流道试模流程
1.模具准备
2.安装热流道系统
3.调试热流道系统
4.试模与评估
正文:
注塑模具热流道是模具行业中的一种重要技术,它在提高生产效率、降低生产成本、提高产品质量和简化生产工艺等方面具有显著的优势。
热流道系统
由热喷嘴、分流板、温控箱和附件等组成,其核心部件是热喷嘴,其作用是将熔融塑料从注塑机喷嘴引导到模具中。
根据热喷嘴的结构形式,热流道主要分为开放式热流道、针阀式热流道和微型半热流道。
开放式热流道结构简单,适用于小型模具;针阀式热流道具有较好的封闭性能,适用于较大型模具;微型半热流道则结合了开放式和针阀式的优点,稳定好用,故障率低。
在设计热流道时,应确保流道尺寸和形状符合要求,选择合适的喷嘴类型,并设计合理的流道布局。
此外,还需考虑热流道的冷却系统、流道材料和加工工艺等因素。
热流道试模流程包括模具准备、安装热流道系统、调试热流道系统和试模与评估。
在试模过程中,需检查热流道系统的运行状况,如喷嘴是否堵塞、流道是否畅通、温度控制是否准确等,以保证生产过程中热流道系统的稳定运行。
热流道1

现阶段国内外热流道系统发 展的现状及成果
热流道模具的结构元件 热流道系统的电热元件和温控系统 热流道系统热平衡分析,热量和充模力的计 算 热流道模具的CAD/CAE/CAM 热流道的大型模具和精密成型模具 热流道的叠层式模具和双元素注射模 热流道模具的快速换料工艺
26
国内热流道系统的进展
结构元件 电热元件和温控系统 热平衡分析,热量和充模力的计算 热流道的大型模具和精密成型模具 热流道的叠层式模具和多层共注射模 热流道模具的快速换料工艺
——应用概况 应用概况
无流道注射成型法问世于上世纪50年代,其 应用推动虽经历了一个较长时间,但其市场占有 率仍逐年上升.在80年代中期,美国的热流道模 具占注塑模总数的15~17%,欧洲为12~15%, 日本约为10%.到了90年代,美国生产的塑料注 射模具中热流道模具已占40%以上,在大型制品 的注射模具中则占90%以上采用了热流道.
8
各种塑料对绝热流道和热流道 的适用性
聚乙烯 (PE) 绝 热 流 道 井式 喷嘴 延长 喷嘴 主流 道喷 嘴 点浇 口型 半绝热流 道 加热流道 可 可 可 聚丙烯 (PP) 可 可 可 聚苯 乙烯 (PS) 稍难 可 稍难 聚甲醛 ( POM ) 稍难 可 稍难 ABS 不可 可 不可 聚氯 乙烯 ( PVC ) 不可 不可 不可 聚碳 酸酯 (PC) 不可 不可 不可
无 流 道 模
半热流道模具 热流道模具
按浇口方式分
侧浇口式 热流道板式 内加热式 外加热式
按加热方式分
喷嘴加热方式 叠层热流道式
11
热流道结构示意图
12
热流道系统的主要组成部分
热流道板(manifolds) 内加热式 热喷嘴(hot nozzles ) 外加热式 针阀式 加热元件(heating elements) 热传感器(sensors and thermal couples ) 温度控制器(temperature controllers)
热流道系统介绍与选用
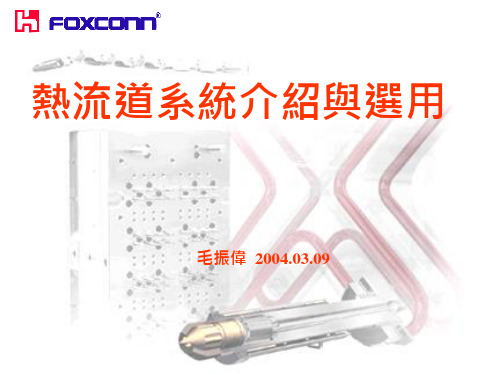
熱流道系統膠口類型分類 二﹑點膠口
熱流道系統膠口類型分類 三﹑直接膠口
熱流道系統膠口類型分類 四﹑邊緣膠口
熱流道的選擇
射出重量﹐塑膠材料﹐膠口位置與痕跡﹐ 射出重量﹐塑膠材料﹐膠口位置與痕跡﹐這三 個要素彼此影響﹐ 個要素彼此影響﹐共同決定熱流道的選擇
熱流道的選擇 •SHOT WEIGHT
•控制塑膠流動 控制塑膠流動
閥澆口可以按照程序控制的順序,人為的控制打 開或者關閉,因此在充填過程中實現對塑膠的流 動的控制.
熱 流 道 系 統 的 組 成 部 分
:
熱流道系統膠口Leabharlann 型分類 一﹑閥膠口•No gate vestige •For a wide variety of resins •Pneumatically operated valve stem
流道縮短或者甚至沒有流道,從而起到減少廢料 的作用;另外由于成型條件的改善使成型品的良 率提高,從而起到減少材料浪費的作用.
•縮短循環時間 縮短循環時間
為了對成品保壓,流道通常設計成厚度較大,以確 保其最后凝固.采用熱流道系統可以減少或取消 流道,因此可以節省花費在流道凝固上的CYCLE TIME.
6.
•減少壓力損失 減少壓力損失
•減少了在流道上的壓力損失 •由于流道的減少,熱量損失相應減少,從而塑膠的 流動性較佳,充填過程中的壓力損失相應較少.
熱流道系統的特點 : •控制澆口痕跡 控制澆口痕跡
熱流道系統所獨有的一種澆口類型:閥澆口,澆口 由氣動/液動的閥針控制打開或者關閉.成品保壓 完成后由閥針將澆口封閉,避免成品表面出現明 顯的澆口拉斷的痕跡.
熱流道系統介紹與選用
毛振偉 2004.03.09
什么是熱流道系統
关于热流道系统
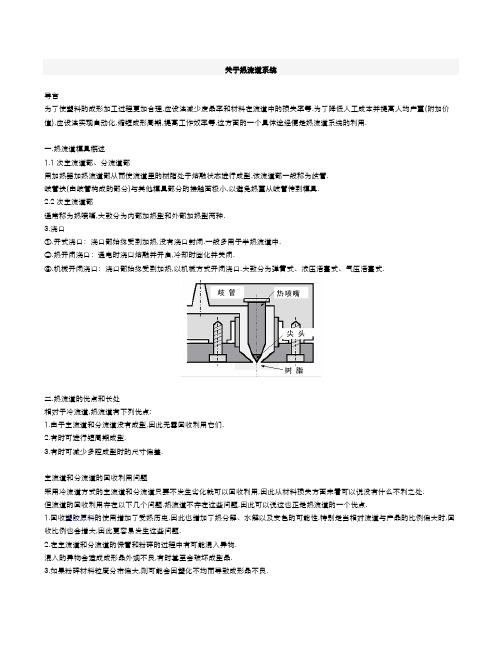
关于热流道系统导言为了使塑料的成形加工过程更加合理,应设法减少废品率和材料在流道中的损失率等.为了降低人工成本并提高人均产量(附加价值),应设法实现自动化,缩短成形周期,提高工作效率等.这方面的一个具体途经便是热流道系统的利用.一.热流道模具概述1.1次主流道部、分流道部用加热器加热流道部从而使流道里的树脂处于熔融状态进行成型.该流道部一般称为歧管.岐管块(由岐管构成的部分)与其他模具部分的接触面极小,以避免热量从岐管传到模具.2.2次主流道部通常称为热喷嘴,大致分为内部加热型和外部加热型两种.3.浇口①.开式浇口:浇口部始终受到加热,没有浇口封闭.一般多用于半热流道中.②.热开闭浇口:通电时浇口熔融并开启,冷却时固化并关闭.③.机械开闭浇口:浇口部始终受到加热,以机械方式开闭浇口.大致分为弹簧式、液压活塞式、气压活塞式.二.热流道的优点和长处相对于冷流道,热流道有下列优点:1.由于主流道和分流道没有成型,因此无需回收利用它们.2.有时可进行短周期成型.3.有时可减少多腔成型时的尺寸偏差.主流道和分流道的回收利用问题采用冷流道方式的主流道和分流道只要不发生劣化就可以回收利用,因此从材料损失方面来看可以说没有什么不利之处.但流道的回收利用存在以下几个问题.热流道不存在这些问题,因此可以说这也正是热流道的一个优点.1.回收塑胶原料的使用增加了受热历史,因此也增加了热分解、水解以及变色的可能性.特别是当相对流道与产品的比例偏大时,回收比例也会增大,因此更容易发生这些问题.2.在主流道和分流道的保管和粉碎的过程中有可能混入异物.混入的异物会造成成形品外观不良,有时甚至会破坏成型品.3.如果粉碎材料粒度分布偏大,则可能会因塑化不均而导致成形品不良.均化粒度或再次挤出又会增加成本并延长受热历史,从而导致劣化.此外,混合使用新料和粉碎材料时,如果粒度大小不同,则在料斗或料仓中可能会发生分离.此时应在混合的同时一点一点地加料.成型周期1.虽然冷流道被设计得尽可能地短而细,但相对于成形品的厚度来说,主流道和分流道通常还是偏粗.此处的冷却和固化有时会成为短周期成型的决定因素,这是因为固化时间与厚度的平方成正比.在一般成形中,螺杆塑化必须在冷却时间内结束,因此当主流道和分流道部分的塑化时间需要延长时,成形周期将会变长.(不过,对于可进行复合动作(模具开合期间也能进行螺杆塑化)的成形机,这个问题的影响将会减轻.这种方式的成形机有利于薄壁产品的短周期成形.)2.模具的打开量热流道无需主流道和分流道的脱模过程,因此可缩短开模行程,进而缩短成型周期.多个模腔的尺寸精度模腔数增多,尺寸和品质偏差就会增大,因此精密成形时,模腔数不宜太多(1-4个即可).3-1)可通过1-4腔的模具和小型成形机的组合来增加成型机的台数或②形成多个模腔(16~32个)来进行成型.在后一种情况下,如果流道平衡不良,尺寸和品质偏差就会增大.在这种情况下,如果将冷流道和热流道组合成半热流道模具,有时便可按冷流道部分的尺寸偏差(=整体的尺寸偏差)来成型.例如,32腔模具(在等长的冷流道板块上制作8个模腔,并在4个板块上分别装有热喷嘴)的尺寸偏差如下:·1个模腔的尺寸偏差:0.035~0.040%·1个板块(8个模腔)的尺寸偏差:0.10~0.12%·全部32个模腔的尺寸偏差:0.12%(但表示为3σ/×100%)三.热流道的缺点和问题缺点1.如果模具价格高而生产数量少,则可能体现不出其价格优势.2.树脂滞留在歧管和热喷嘴内时容易劣化.3.改换树脂或改换颜色时一般比较费时.注意事项1.变色树脂温度、滞留时间与成形品变色之间的关系跟在注射成形机的机筒内滞留时一样,树脂温度高的时候必须缩短滞留时间.根据热喷嘴种类的不同,有时必须设定较高的温度,此时就要特别注意变色问题.此外,变色会因树脂和等级而异,因此就所使用的材料而言,建议在把握好这些关系的基础上来选择热流道系统.2.异物在有些形状的歧管中,树脂有时会滞留在死角并发生劣化.此外,在热喷嘴的固化层内有时也会产生异物.经过改性(如阻燃性等)的高机能性材料是比较容易产生异物的,此时也要像处理变色问题那样切记把握好树脂特性.3.银纹银纹是由粒料中的水分、热分解时所产生的挥发成分以及成形过程中卷入的空气等而产生的.树脂温度高时必须降低吸湿度,因此应比采用冷流道时更加注意加强预干燥.此外,来自热喷嘴内的分解层的挥发成分也会产生银纹,因此有时需要经常清除该分解层.这也会降低作为热流道的优点之一的生产效率.4.压力损失有些类型的热喷嘴会出现很大的压力损失.在内部加热型热喷嘴中,如果流动层偏薄,压力损失就会增大,从而不得不通过提高树脂温度来成形,此时应特别注意变色和分解情况等.5.摩损对于基于强化材料和填充材料(其中含有玻璃纤维和硅石之类的容易引起钢材摩损的材料)的复合材料等级,建议也像冷流道的模具设计那样采用耐摩损的热流道系统.6.改换颜色、改换树脂如果歧管等部件中有死角(树脂不流动的部分)或像内部加热式的热喷嘴那样有固化层,则在改换颜色和改换树脂时将花费更多时间.换言之,对于热喷嘴形式,外部加热型比内部加热型更为有利.四.热流道的种类4-1.歧管虽然也有热流道内装有加热器的内部加热型,但几乎所有的歧管都是外部加热型.加热时一般使用加热筒.温度分布会因加热器和温度传感器的个数、位置等而发生变化,因此设计时应注意这一点.为了使温度分布尽可能均匀,有时要使用与热喷嘴位置相符的不规则形状的护套加热器.歧管的流道从功能上来说会发生流向变化,因此模具加工时容易形成死角.此外,树脂会发生碳化,因此有时必须清理歧管.在完成上述维护并重新组装时,如果接合部分出现间隙或阶差,也会出现树脂不流动的死角.因此在结构设计时必须事先考虑到这一点.4-2.热喷嘴1.内部加热型热喷嘴内的鱼雷形筒中装有加热器.多用于通过热平衡来开合浇口的模具中.热喷嘴外筒虽受到空气隔热层的隔热,但仍被冷却,因此热喷嘴外筒的里面的树脂形成不流动的固化层.这样一来,熔融树脂可以通过的有效流路(流动层)的厚度就变薄了.固化层和流动层各自的厚度会随着热喷嘴的温度而变化.流动层变薄则压力损失增大.同时,固化层和流动层的界面会因温度偏差而移动,于是滞留时间延长,而且已经变色和分解的树脂也有进入流动层的机会.因此,必须在对热喷嘴定期进行分解和清扫这一前提条件下来设计模具结构.为了顺利进行稳定成型,这一点非常重要.外部加热型的热喷嘴是从外部加热的,因此熔融树脂的流路中内部加热型那样的鱼雷形筒.当以机械方式打开或关闭浇口时,应将机构装在内部以便浇口开闭,因此必须做成外部加热型的热喷嘴.3.关于内部加热型与外部加热型的温度分布内部加热型和外部加热型的加热方式不同.内部加热型的温度分布更广.此外,内部加热型的流路阻力会增大,因此必须相对提高设定温度,从而更容易造成变色和热分解.对热稳定性不佳的树脂进行成型时,务必要事先研究这一点.对此,外部加热型的热喷嘴内的温度分布较小,难以发生变色和热分解,但由于是从流路外壁来加热的,因此热难以传到流路中央部分,从而使中央部分的温度略低于壁面.对于外部加热型且浇口为热开闭式来说,由于结构上存在问题,因此很难避免产生冷料.此外,与内部加热型不同,热喷嘴外围的温度偏高,因此模腔面的热传导会增大,而且根据加热方法,有时会在短周期成型方面造成不利影响.4-3.浇口1.开式浇口开式浇口多用于外部加热型中,因来自热喷嘴的传热而始终处于打开状态.因此浇口封闭时间也就是制品封闭时间(浇口断开所处位置的固化时间).优点是最简易而又便于操作,但也有容易发生浇口堵塞和拉丝的缺点.用作开式浇口的浇口堵塞和拉丝现象的对策,这种浇口是通过与本体部分不同的加热回路,并在前端的尖头与成型周期保持同步的情况下来进行开闭的一种机构.本机构通过通电来打开浇口,通过冷却来关闭浇口.因此,如果延长通电时间,则可能会起到扩大浇口之类的效果.此外,这一方法还有这样一个优点:在使用多个热喷嘴的多腔模具的情况下,浇口平衡可通过调节各个热喷嘴的通电时间和电流等而比较容易达到.3.机械开闭浇口热喷嘴中装有活塞,弹簧、油压或气压使活塞往复运动,从而使浇口时开时闭.另外,由于没有浇口封闭(属于机械性关闭),因此不必考虑成型周期.这一方法既可减少大浇口下落时的流动阻力,同时对浇口周围的喷射纹等流痕也有效.但问题是只有在浇口固化前才能关闭浇口,因此很容易出现保压不足的状态,而且据说根本不适用于精密成型.尤其是在材料的结晶速度很快而产品的壁厚偏薄的情况下更应特别注意.使用时应将浇口下落处的壁厚和浇口直径设计得大一些.对于复合材料以及含有玻璃纤维等无机填料的工程塑料,应注意活塞和浇口部位的摩损并避免树脂进入滑动部分.此外,使用时还要注意并熟练应对多腔模具的各个模腔在浇口封闭时的定时偏差、因浇口固化而无法关闭浇口时出现的模具损伤等.五.典型的成型条件在内部加热的情况下,热喷嘴的鱼雷形筒(torpedo)中内置有加热器,或者热喷嘴外筒受到空气隔热层的隔热,并被冷却.这样一来,热喷嘴外筒内侧面上的树脂就会形成不流动的固化层.因此熔融树脂所流经的有效通路(流动层)的厚度也会比外部加热时更薄. 作为一个大致标准,外部加热部分(歧管或外部加热型热喷嘴)的温度应与机筒温度相同,而内部加热部分(内部加热型热喷嘴)的温度应为机筒温度加20~40℃.不过这些条件也会因金属冷却、加热器与热电偶的位置关系、隔热等因素而发生变化.。
热流道的原理
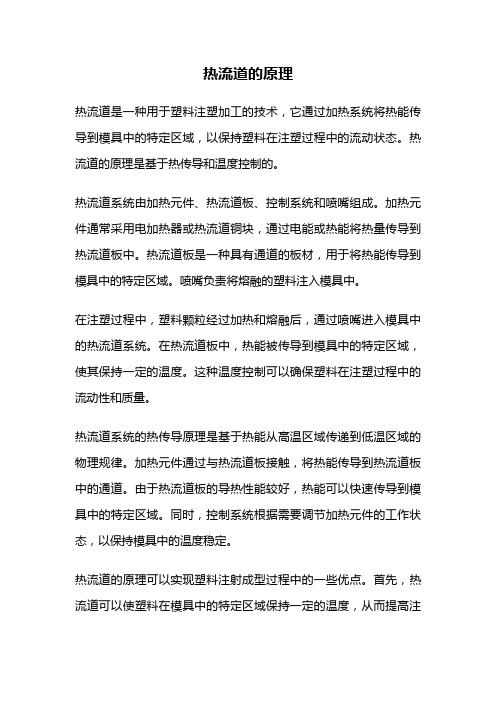
热流道的原理热流道是一种用于塑料注塑加工的技术,它通过加热系统将热能传导到模具中的特定区域,以保持塑料在注塑过程中的流动状态。
热流道的原理是基于热传导和温度控制的。
热流道系统由加热元件、热流道板、控制系统和喷嘴组成。
加热元件通常采用电加热器或热流道铜块,通过电能或热能将热量传导到热流道板中。
热流道板是一种具有通道的板材,用于将热能传导到模具中的特定区域。
喷嘴负责将熔融的塑料注入模具中。
在注塑过程中,塑料颗粒经过加热和熔融后,通过喷嘴进入模具中的热流道系统。
在热流道板中,热能被传导到模具中的特定区域,使其保持一定的温度。
这种温度控制可以确保塑料在注塑过程中的流动性和质量。
热流道系统的热传导原理是基于热能从高温区域传递到低温区域的物理规律。
加热元件通过与热流道板接触,将热能传导到热流道板中的通道。
由于热流道板的导热性能较好,热能可以快速传导到模具中的特定区域。
同时,控制系统根据需要调节加热元件的工作状态,以保持模具中的温度稳定。
热流道的原理可以实现塑料注射成型过程中的一些优点。
首先,热流道可以使塑料在模具中的特定区域保持一定的温度,从而提高注塑过程中的流动性和充填性能。
其次,热流道可以减少或消除塑料制品中的熔接线、气泡和短射等缺陷,提高制品的质量。
此外,热流道还可以缩短注塑周期,提高生产效率。
然而,热流道系统也存在一些问题和挑战。
首先,热流道系统的设计和制造相对复杂,需要考虑材料的选择、通道的结构和加热控制等因素。
其次,热流道系统的维护和保养比较困难,需要定期清洁和更换加热元件。
此外,热流道系统的成本相对较高,不适用于所有注塑加工。
热流道是一种基于热传导和温度控制的塑料注塑加工技术。
它通过加热系统将热能传导到模具中的特定区域,以保持塑料在注塑过程中的流动状态。
热流道系统的设计和制造相对复杂,需要考虑材料的选择、通道的结构和加热控制等因素。
尽管存在一些问题和挑战,但热流道系统在提高注塑过程中的质量和效率方面具有重要作用。
热流道结构知识点总结

热流道结构知识点总结热流道结构在塑料注射成型过程中扮演着重要的角色,它可以帮助提高注射成型的效率和质量。
本文将会总结热流道结构的相关知识点,包括热流道系统的基本原理、组成部分、优点和缺点、应用范围等内容。
一、热流道系统的基本原理热流道系统是一种在注射模具中用于传送加热的热载体,保持塑料材料在注射成型过程中的流动状态,以保证产品的成型质量和提高生产效率。
热流道系统的基本原理包括:1. 热载体传导热量:热流道系统中通常采用热载体(如热油、热水)传导热量,将热能传递到模具的热流道中,使塑料材料在注射成型过程中能够始终保持在合适的流动状态。
2. 控制模具温度:通过控制热载体的温度和流量,可以实现对注射模具中的温度进行精确的控制。
这样可以避免塑料材料在成型过程中受温度变化的影响,保证产品的尺寸稳定性和表面质量。
3. 优化成型条件:热流道系统可以根据不同的产品形状和材料特性,灵活调节模具中不同部位的温度,以实现最佳的注射成型效果。
二、热流道系统的组成部分热流道系统由多个组成部分组成,主要包括热流道控制器、加热装置、温度探测器、热流道喉口等。
1. 热流道控制器:负责对热流道系统的温度、压力等参数进行实时监控和调节,以确保注射成型过程中的稳定性和一致性。
2. 加热装置:通常采用电加热或加热用的热管,通过对热载体进行加热,传递热能到热流道系统中。
3. 温度探测器:用于监测热流道系统中的温度变化,反馈给热流道控制器,以实现自动调节和控制。
4. 热流道喉口:负责将加热好的热载体传递到模具的热流道中,为塑料材料提供适宜的加热条件。
三、热流道系统的优点和缺点热流道系统相比传统的冷流道系统具有许多优点,但也存在一些缺点。
1. 优点:(1)节能减耗:热流道系统采用热载体传导热量,可以有效减少注射成型过程中的能耗,提高生产效率。
(2)减少生产环境污染:热流道系统可以降低产品的废料率,提高成型质量,减少生产环境的污染。
(3)提高产品质量:热流道系统可以精确控制模具中不同部位的温度,保证产品的尺寸稳定性和表面质量。
- 1、下载文档前请自行甄别文档内容的完整性,平台不提供额外的编辑、内容补充、找答案等附加服务。
- 2、"仅部分预览"的文档,不可在线预览部分如存在完整性等问题,可反馈申请退款(可完整预览的文档不适用该条件!)。
- 3、如文档侵犯您的权益,请联系客服反馈,我们会尽快为您处理(人工客服工作时间:9:00-18:30)。
热流道知识热流道分类:绝热流道、冷流道、热流道。
绝热流道的设计复杂,但效果和维护成本非常低,不会耽误工时。
冷流道和热流道斑竹基本上谈到了特点。
我再具体补充一些自己的看法。
热流道分类:开放式、针阀式。
开放式结构简单、对材料的局限性较高,易出现拉丝和泄露,表面质量差,在国外的高精密模具中应用较少,同一副模具可和不同厂家的针阀式混用。
很多公司能自己制造。
针阀式热流道节省材料,塑件表面美观,同时内部质量紧密、强度高。
现在世界上有两大类针阀式热流道(根据注射原理):气缸式和弹簧式。
气缸式依* 控制器和时序控制器控制气缸推动针阀的关闭,结构较复杂,但本身设计简单。
主要有DME(美国)热流道是通过加热的办法来保证流道和浇口的塑料保持熔融状态。
由于在流道附近或中心设有加热棒和加热圈,从注塑机喷嘴出口到浇口的整个流道都处于高温状态,使流道中的塑料保持熔融,停机后一般不需要打开流道取出凝料,再开机时只需加热流道到所需温度即可。
因此,热流道工艺有时称为热集流管系统,或者称为无流道模塑。
热流道技术的优、缺点热流道技术与常规的冷流道相比有以下的好处:1、节约原材料,降低成。
2、缩短成型周期,提高机器效率3、改善制品表面质量和力学性能。
4、不必用三板式模具即可以使用点浇口。
5、可经济地以侧浇口成型单个制品6、提高自动化程度。
7、可用针阀式浇口控制浇口封冻。
8、多模腔模具的注塑件质量一致。
9、提高注塑制品表面美观度。
但是,每一项技术都会有自身的缺点存在,热流道技术也不例外:1、模具结构复杂,造价高,维护费用高。
2、开机需要一段时间工艺才会稳定,造成开价废品较多。
3、出现熔体泄露、加热元件故障时,对产品质量和生产进度影响较大。
上面第三项缺点,通过采购质量上等的加热元件、热流道板以及喷嘴并且使用时精心维护,可以减少这些不利情况的出现。
热流道系统的结构热流道系统一般由热喷嘴、分流板、温控箱和附件等几部分组成。
热喷嘴一般包括两种:开放式热喷嘴和针阀式热喷嘴。
由于热喷嘴形式直接决定热流道系统选用和模具的制造,因而常相应的将热流道系统分成开放式热流道系统和针阀式热流道系统。
分流板在一模多腔或者多点进料、单点进料但料位偏置时采用。
材料通常采用P20 或H13 分流板一般分为标准和非标准两大类,其结构形式主要由型腔在模具上的分布情况、喷嘴排列及浇口位置来决定。
温控箱包括主机、电缆、连接器和接线公母插座等。
热流道附件通常包括:加热器和热电偶、流道密封圈、接插件及接线盒等。
热流道系统的分类一般说来,热流道系统分为单头热流道系统、多头热流道系统以及阀浇口热流道系统。
单头热流道系统主要由单个喷嘴、喷嘴头、喷嘴连接板、温控系统等组成。
单头热流道系统塑料模具结构较简单。
将熔融状态塑料由注塑机注入喷嘴连接板,经喷嘴到达喷嘴头后,注入型腔。
需要控制尺寸d、D、L 和通过调整喷嘴连接板的厚度尺寸,使定模固定板压紧喷嘴连接板的端面,控制喷嘴的轴向位移,或者直接利用注塑机喷嘴顶住喷嘴连接板的端面,也可达到同样目的。
在定模固定板的合适位置设置一条引线槽,让电源线从模具内引出与安装在模具上的接线座连接。
多头热流道系统塑料模具结构较复杂。
熔融状塑料由注塑机注入喷嘴连接板,经热流道板流向喷嘴后到达喷嘴头,然后注入型腔。
热流道系统的喷嘴与定模板有径向尺寸D1 配合要求和轴向尺寸限位要求。
喷嘴头与定模镶块有径向尺寸d 配合要求,保证熔融状态的塑料不溢流到非型腔部位,并要求定模镶块的硬度淬硬50HRC 左右。
分型面到热喷嘴轴向定位面之间的距离L 必须严格控制,该尺寸应根据常温状态下喷嘴的实际距离L′加上模具正常工作温度下喷嘴的实际延伸量ΔL确定。
为了保证喷嘴与热流道板贴合可靠,不使热流道板产生变形,在喷嘴的顶部上方设有调整垫,该调整垫与喷嘴自身的轴向定位面一起限制了喷嘴在轴向的移动,且有效地控制了热流道板可能产生的变形。
在常温状态下,调整垫与热流道板和定模固定板之间控制0.025mm 间隙以便模具受热后,在工作温度状态时调整垫恰好压紧。
热流道系统的定位座和定位销一起控制了热流道板在模具中的位置。
定位座与定模板有径向尺寸D2 配合要求,而且深度h 必须控制准确,定位座的轴向起着支承热流道板的作用,直接承受注射机的注射压力。
定位销与热流道板固定板有配合要求。
热流道板与模板之间必须留有足够的空隙,以便包裹隔热材料。
热流道板和固定板必须设有足够的布线槽,让电源线从模具内引出与安装在模具上的接线座连接。
喷嘴连接板与定模固定板之间有径向尺寸D1 配合要求,以便注塑机的注射头与模具上的喷嘴连接板配合良好。
在热流道板附近,将定模板、热流道板固定板、定模固定板用螺钉连接起来,增强热流道板的刚性。
阀浇口热流道系统塑料模具结构最复杂。
它与普通多头热流道系统塑料模具有相同的结构,另外还多了一套阀针传动装置控制阀针的开、闭运动。
该传动装置相当于一只液压油缸,利用注射机的液压装置与模具连接,形成液压回路,实现阀针的开、闭运动,控制熔融状态塑料注入型腔。
热流道塑料模具设计程序第一,根据塑件结构和使用要求,确定进料口位置。
只要塑件结构允许,在定模镶块内喷嘴和喷嘴头不与成型结构干涉,热流道系统的进料口可放置在塑件的任何位置上。
常规塑件注射成形的进料口位置通常根据经验选择。
对于大而复杂的异型塑件,注射成形的进料口位置可运用计算机辅助分析(CAE) 模拟熔融状塑料在型腔内的流动情况,分析模具各部位的冷却效果,确定比较理想的进料口位置。
第二,确定热流道系统的喷嘴头形式。
塑件材料和产品的使用特性是选择喷嘴头形式的关键因素,塑件的生产批量和模具的制造成本也是选择喷嘴头形式的重要因素。
第三,根据塑件的生产批量和注射设备的吨位大小,确定每模的腔数。
第四,由已确定的进料口位置和每模的腔数确定喷嘴的个数。
如果成形某一产品,选择一模一件一个进料口,则只要一个喷嘴,即选用单头热流道系统;如果成形某一产品,选择一模多腔或一模一腔二个以上进料口,则就要多个喷嘴,即选用多头热流道系统,但对有横流道的模具结构除外。
第五,根据塑件重量和喷嘴个数,确定喷嘴径向尺寸的大小。
目前相同形式的喷嘴有多个尺寸系列,分别满足不同重量范围内的塑件成形要求。
第六,根据塑件结构确定模具结构尺寸,再根据定模镶块和定模板的厚度尺寸选择喷嘴标准长度系列尺寸,最后修整定模板的厚度尺寸及其他与热流道系统相关的尺寸。
第七,根据热流道板的形状确定热流道固定板的形状,在其板上布置电源线引线槽,并在热流道板、喷嘴、喷嘴头附近设计足够的冷却水环路。
第八,完成热流道系统塑料模具的设计图绘制。
热流道的设计概念热流道一个重要的步骤是热流道的设计概念。
一个详细的设计概念,包括歧管和压板,它们将成为模具审核中的一个重要部分歧管用于保证让熔液通道能够以最有效的方式进行布置。
在理想的情况下,熔液通道采用对称方式设计,所有下行流道的流动长度与转弯数量都是一致的。
在采用多型腔模具或非对称式模具的情况下,熔液通道可能包括人造长度和转弯点,以便能够适当地平衡这个系统。
这种概念对设计人员和热流道设计人员均有所帮助,可以保证最佳的岐管设计。
在一个需要3 个注入口的零件上,为了控制零件上的接缝线,就要解决塑料流量平衡的问题。
通过一个详细的岐管设计,可以评价流量的平衡和岐管的布置,保证下行流道能够满足客户模具基座的需要。
最后的结果是将单一的直接注入口和单型腔模具上两个从热到冷的注入口组合在一起(图3)。
图3 单型腔和3 注入口模具熔液通道的概念设计此外,还要采用压板技术,保证能够设计出客户要求的闭合高度和关键特点。
由于在喷嘴中包括热流道喷嘴,模具设计人员还要确认注入口的接近处和冷却是否能满足热流道制造商的要求。
对热流道评价的主要因素包括:流量平衡和岐管热分布的情况;通道尺寸;高压应用领域中的岐管材料强度;注入口的尺寸;冷却和注入口的接近;能够承受研磨性和腐蚀性树脂的成分。
热流道是一种复杂而具有一定优越性的模具零件。
在模具生产项目中,CAE 计算机辅助工程分析、树脂试验和设计概念等,都可以由热流道供货商来完成。
在一个项目的初期,如果让热流道供货商共同参与工作,那么的设计人员就能够进一步优化最终产品。
热流道系统的发展方向当前,国内外热流道模具的主要发展趋势可归纳为以下几个方面。
元件的小型化,以实现小型制品的一模多腔和大型制品多浇口充模。
通过缩小喷嘴空间,可在模具上配置更多型腔,提高制品的产量和注射机的利用率。
在90 年代,Master 公司开发的喷嘴最小可至15.875mm;Husky 公司开发的多浇口喷嘴,每个喷嘴有4 个浇口,浇口距可近至9.067mm;Osco 公司开发的组合复式喷嘴,每个喷嘴有12 个浇口探针,可用于48 腔模具的成型。
MoldMaters 公司针对小型制件的空间限制,在2001 年开发了用于小制件的喷嘴,含整体加热器、针尖和熔体通道,体积直径小于9mm,浇口距仅为10mm, 可成型重量为1~30g 的制品;协力热流道公司开发的迷你型热流道系统,浇口距可近到8.00mm,尤其适用于电子类较小的产品。
当前,用户要求模具设计和制造周期越来越短,将热流道元件标准化不仅有利于减少设计工作的重复和降低模具的造价,并且十分便于对易损零部件的更换和维修。
据报道,Polyshot 公司已开发出快换热流道模具系统,尤其适于注射压力为70kN 的小型注射机。
Husky、Presto 和Moldmasters等公司的喷嘴、阀杆和分流板都作为标准型便于快速更换和交付模具,现在国外只需4 周即可交付模具,在国内制作模具最快2 周即可交付热流道模具。
热流道模具设计整体可靠性提高。
如今国内外各大模具公司对热流道板的设计和热喷嘴相连接部分的压力分布、温度分布、密封等问题的研究开发极为重视。
叠层热流道注射模的开发和利用也是一个热点。
叠式模具可有效增加型腔数量,而对注射机合模力的要求只需增加10%~15%。
叠式热流道模具在国外一些发达国家已用于工业化.叠式热流道模具在国内的注塑行业已得到广泛应用,如一次性餐具,瓶盖, 瓶盖防盗扣及提手等小件大批量产品.如国内的协力热流道公司在叠式热流道的设计制作及使用方面积累了丰富的经验.改善热流道元件材料的目的在于提高喷嘴和热流道的耐磨性和用于敏感材料成型。
如使用钼钛等韧性合金材料制造喷嘴,以金属粉末注射成型经烧结制成热流道元件已成为可能。
开发精确的温控系统。
在热流道模具模塑中,开发更精密的温控装置,控制热流道板和浇口中的熔融树脂的温度是防止树脂过热降解和产品性能降低的有效措施。
将热流道用于共注。
通过支管和热喷嘴元件的有效组合设计可使共注成型与热流道技术相结合,由此成型3 层、5 层甚至更多层的复合塑料制品。
例如Kortec 公司开发出了熔体输送系统和共注喷嘴;Incoe 公司的多出口、多模腔共注支管生产线能用于多材料多组分共注射。