6SIGMA改进案例
六西格玛经典案例

六西格玛经典案例在六西格玛质量管理方法中,通过分析和改进业务流程,以减少缺陷和提高效率,从而实现优秀质量和高度效益。
以下是三个经典的六西格玛案例。
1. Motorola的六西格玛实践Motorola是六西格玛的奠基者之一、20世纪80年代,Motorola采用六西格玛方法,以改进生产过程并提高质量。
在一个以缺陷率而不是零缺陷为标准的产业中,Motorola在一年内将缺陷率从超过三十万个降低到每百万个产品中只有5个。
六西格玛的成功引起了其他公司的注意,并成为其他公司实施质量管理的典范。
2. General Electric(GE)的六西格玛实施GE是六西格玛的早期采用者,它将六西格玛引入公司的各个部门和业务领域。
公司的首席执行官杰克·韦尔奇在1995年将六西格玛作为公司的战略重点。
GE在实施过程中的一个成功案例是其航空发动机业务部门,该部门通过六西格玛方法降低了生产过程中的缺陷率,并提高了航空发动机的性能和可靠性。
GE的成功证明了六西格玛可以在各种行业中实现卓越的结果。
3.美国政府的六西格玛应用六西格玛方法不仅在企业界取得成功,而且在政府部门中也有很好的应用。
美国政府决定在1995年引入六西格玛方法,以提高效率并减少浪费。
例如,美国联邦航空管理局(FAA)使用六西格玛方法改进了飞行管制和管理过程,减少了航班延误和事故。
美国海军也采用了六西格玛方法来改善军舰维护和修理过程,提高了战斗力和减少了成本。
以上是六西格玛的三个经典案例,它们都展示了通过六西格玛方法来实现质量改进和效益提高的潜力。
这些案例证明了六西格玛是一个非常有力的质量管理方法,可以在各个领域带来显著的结果。
无论是在制造业、服务业还是政府部门,六西格玛都能够提供一个可靠的框架来解决质量和效率方面的挑战。
精益六西格玛的改善案例

精益六西格玛的改善案例案例:汽车制造流程改善背景:汽车制造公司在生产过程中遇到了一些问题。
产品质量不稳定,交付时间延长,成本高涨,因此需要通过改善流程来提高生产效率和降低成本。
目标:-提高产品质量稳定性,降低缺陷率-缩短交付时间,提高客户满意度-降低制造成本,提高利润率方法:1.项目选择:选择一个关键的制造流程进行改善。
在该公司中,组装过程是最关键且容易出现问题的环节,因此选择组装流程作为改善项目。
2.流程分析:通过流程图和价值流图,对组装流程进行详细分析。
识别出每个环节中的瓶颈和浪费,如等待时间、运输时间、不必要的重复工作等。
3.数据收集:收集关于缺陷率、交付时间和成本的数据。
这些数据将成为决策的基础。
4.根本原因分析:使用工具如鱼骨图、五力模型、因果图等,找出导致问题的根本原因。
可能的原因包括不合理的工作流程、不合适的设备、员工技能不足等。
5.解决方案设计:根据根本原因分析的结果,设计出改进方案。
例如,通过优化工作流程、提高设备质量、加强员工培训等。
6.实施改进:在一定范围内进行试点实施改进方案,收集数据并评估效果。
根据数据的结果,对方案进行调整和改进,直到达到预期的效果。
7.控制改进:建立一套监控体系,确保改进效果能够持续。
通过设立关键绩效指标(KPI)和改进计划,对改进方案进行监控和调整。
结果:经过精益六西格玛方法学的改进,该汽车制造公司取得了显著的效果:-产品质量稳定性得到明显提高,缺陷率显著降低。
-交付时间缩短,客户满意度有了显著提升。
-制造成本明显降低,利润率得以提高。
结论:。
六西格玛改善案例

六西格玛改善案例在组织和管理领域中,六西格玛是一种用于改善流程和提高绩效的方法论。
它的目标是通过减少变异性和错误来提高效率和质量。
以下是一个关于如何应用六西格玛来改善一个制造公司的案例。
ABC制造公司是一家生产家具的公司,在市场上享有良好声誉。
然而,随着竞争的加剧,公司面临着许多挑战,包括生产过程中的效率低下和产品质量的变异性。
为了解决这些问题,公司决定采用六西格玛方法来改善其生产流程。
首先,公司选择了一个重要的关键绩效指标(KPI)来衡量其生产流程的效率。
他们选择了“产品生产时间”,这是指从原材料到成品的生产周期。
目标是减少产品生产时间,以提高生产效率。
接下来,公司成立了一个由六西格玛专家和相关部门的代表组成的团队。
他们接受了六西格玛培训,并开始了项目的实施。
团队成员使用一系列的工具和技术来收集和分析数据,以找出生产流程中的瓶颈和缺陷。
团队发现,在生产过程中存在许多浪费和低效率的环节。
例如,生产设备的运行时间不足,人力资源没有充分利用,并且原材料的供应链管理也不稳定。
这些问题导致了生产周期的延长和产品质量的变化。
为了改进这些问题,团队采取了以下措施:1.优化生产设备的使用率:通过调整生产计划和使用先进的生产技术,确保设备的运行时间最大化。
2.优化人力资源:通过员工培训和合理分配工作任务,确保人力资源的充分利用。
3.改进供应链管理:与供应商建立紧密合作关系,以确保原材料的及时供应和质量。
4.实施质量控制措施:建立严格的质量管理体系,包括监控和检查生产过程中的关键环节,以确保产品质量的一致性。
这些措施的实施取得了积极的效果。
公司的产品生产时间大大缩短,生产效率显著提高。
此外,产品质量的变异性也显着减少,客户对产品的满意度明显提高。
在六西格玛方法的帮助下,ABC制造公司成功地改善了其生产流程,提高了生产效率和产品质量。
这个案例表明,通过使用六西格玛方法,企业可以发现问题所在,并找到解决问题的有效方法。
精益六西格玛案例分析
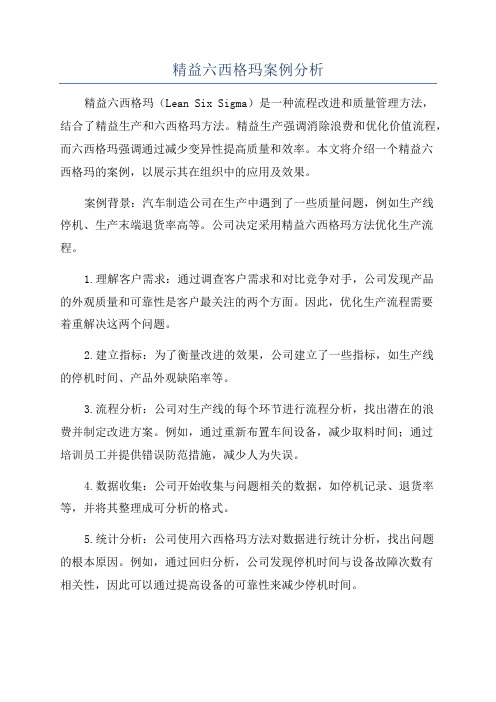
精益六西格玛案例分析精益六西格玛(Lean Six Sigma)是一种流程改进和质量管理方法,结合了精益生产和六西格玛方法。
精益生产强调消除浪费和优化价值流程,而六西格玛强调通过减少变异性提高质量和效率。
本文将介绍一个精益六西格玛的案例,以展示其在组织中的应用及效果。
案例背景:汽车制造公司在生产中遇到了一些质量问题,例如生产线停机、生产末端退货率高等。
公司决定采用精益六西格玛方法优化生产流程。
1.理解客户需求:通过调查客户需求和对比竞争对手,公司发现产品的外观质量和可靠性是客户最关注的两个方面。
因此,优化生产流程需要着重解决这两个问题。
2.建立指标:为了衡量改进的效果,公司建立了一些指标,如生产线的停机时间、产品外观缺陷率等。
3.流程分析:公司对生产线的每个环节进行流程分析,找出潜在的浪费并制定改进方案。
例如,通过重新布置车间设备,减少取料时间;通过培训员工并提供错误防范措施,减少人为失误。
4.数据收集:公司开始收集与问题相关的数据,如停机记录、退货率等,并将其整理成可分析的格式。
5.统计分析:公司使用六西格玛方法对数据进行统计分析,找出问题的根本原因。
例如,通过回归分析,公司发现停机时间与设备故障次数有相关性,因此可以通过提高设备的可靠性来减少停机时间。
6.解决问题:公司根据数据和分析结果制定了一些解决方案,如增加设备维护频率、招聘更有经验的操作员等。
7.测试和验证:公司对解决方案进行测试,并跟踪指标的变化。
例如,公司实施了新的设备维护计划,并在一段时间后再次收集停机数据进行对比分析。
8.控制和持续改进:公司建立了一套控制措施,以确保改进效果的持续。
例如,定期对生产线进行巡检,培训新员工并提供继续教育,以保持高质量的生产。
通过采用精益六西格玛方法,该汽车制造公司取得了显著的改进效果。
例如,生产线的停机时间减少了50%;产品外观缺陷率下降了30%;退货率减少了20%。
这些改进不仅提高了产品质量和可靠性,还降低了生产成本。
六西格玛改进案例

六西格玛改进案例以六西格玛改进案例为题,列举如下10个案例:1. 生产流程改进案例:在一个制造业公司,生产流程中存在着许多瑕疵品。
为了提高产品质量,该公司采用了六西格玛方法进行改进。
通过分析生产过程中的关键环节,确定了引起瑕疵品的主要原因,并通过改进工艺和设备,减少了瑕疵品的产生率。
2. 供应链管理改进案例:一家零售公司的供应链管理存在着库存过剩和缺货的问题,导致了销售额下降。
为了解决这个问题,该公司运用了六西格玛方法,对供应链中的各个环节进行了优化。
通过提高库存预测的准确性,优化订货策略,以及改进供应商管理,该公司成功解决了库存过剩和缺货问题。
3. 客户投诉处理改进案例:一家电信运营商的客户投诉率较高,影响了公司的声誉。
为了改善客户满意度,该公司运用了六西格玛方法,对客户投诉处理流程进行了改进。
通过提高投诉处理的效率和质量,该公司成功降低了客户投诉率,并提升了客户满意度。
4. 销售流程改进案例:一家保险公司的销售流程存在着繁琐和低效的问题,导致了销售人员的工作效率低下。
为了提高销售业绩,该公司采用了六西格玛方法,对销售流程进行了改进。
通过简化流程、优化销售工具和培训销售人员,该公司成功提升了销售人员的工作效率和销售业绩。
5. 质量管理改进案例:一家制药公司的质量管理体系存在着缺陷,导致了产品质量不稳定。
为了提高产品质量,该公司采用了六西格玛方法,对质量管理体系进行了改进。
通过加强质量控制、改进检验方法和加强员工培训,该公司成功提升了产品质量的稳定性。
6. 项目管理改进案例:一个IT项目存在着进度延误和成本超支的问题,导致了项目无法按时交付。
为了解决这个问题,该公司采用了六西格玛方法,对项目管理进行了改进。
通过优化项目计划、加强资源管理和改进沟通机制,该公司成功提高了项目的进度控制和成本控制能力。
7. 售后服务改进案例:一家家电企业的售后服务存在着响应速度慢和问题解决率低的问题,导致了客户的不满意。
6西格玛课题优秀案例
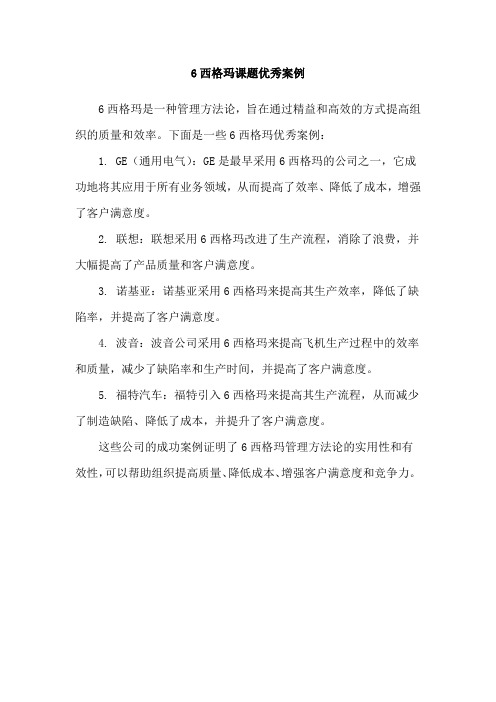
6西格玛课题优秀案例
6西格玛是一种管理方法论,旨在通过精益和高效的方式提高组织的质量和效率。
下面是一些6西格玛优秀案例:
1. GE(通用电气):GE是最早采用6西格玛的公司之一,它成功地将其应用于所有业务领域,从而提高了效率、降低了成本,增强了客户满意度。
2. 联想:联想采用6西格玛改进了生产流程,消除了浪费,并大幅提高了产品质量和客户满意度。
3. 诺基亚:诺基亚采用6西格玛来提高其生产效率,降低了缺陷率,并提高了客户满意度。
4. 波音:波音公司采用6西格玛来提高飞机生产过程中的效率和质量,减少了缺陷率和生产时间,并提高了客户满意度。
5. 福特汽车:福特引入6西格玛来提高其生产流程,从而减少了制造缺陷、降低了成本,并提升了客户满意度。
这些公司的成功案例证明了6西格玛管理方法论的实用性和有效性,可以帮助组织提高质量、降低成本、增强客户满意度和竞争力。
6sigma改善实例

1 2 3 4 5 6 7 8 9 10
2.34 2.35 2.31 2.31 2.28 2.30 2.31 2.30 2.30 2.34
2.31 2.30 2.33 2.30 2.33 2.31 2.34 2.35 2.36 2.33
对螺母高度进行分析
假设数据无差异性: 假设数据无差异性: HO:(MA-MB)=0无差异 HO:(MA-MB)=0无差异 Ha:(MA-MB)≠0有差 Ha:(MA-MB)≠0有差 (MA 进行正态检验: 1. 进行正态检验: stat>BasilStatistics>NormalyTe st P >0.05 数据属于正态分布. 数据属于正态分布. 2.对两组数据进行双七检验. 2.对两组数据进行双七检验. 对两组数据进行双七检验 Stat>BasieStatisitics>Pairedt P >0.05. 兩組數據無顯著性差異, 兩組數據無顯著性差異,故原假設 成立.
螺丝孔爆裂不良分析
工艺不正确
成型条件不当
塑胶材质变动 涂装冶具异常
螺母寸法偏大 素壳螺母孔∮经偏小 素壳有结合线
法
料
验证成形条件不当导致部品螺丝孔裂, 验证成形条件不当导致部品螺丝孔裂,抽取三次正常量 产时的成形条件参数的料温与注射时间进行比较. 产时的成形条件参数的料温与注射时间进行比较.
项目 批次
• 假设正常量产时寸法无差异,HO=(MA-MB)=0对三组数据进行正态检验,三 假设正常量产时寸法无差异,HO=(MA-MB)=0对三组数据进行正态检验, ,HO=(MA 对三组数据进行正态检验 组数据全部附合. 组数据全部附合. • 对三组数据进行效双七检验.P>0.05 对三组数据进行效双七检验.P>0.05 • 我们没有理由拒绝原假设,故素材∮径无差异性. 我们没有理由拒绝原假设,故素材∮径无差异性.
六西格玛案例6SIGMA确定改进机会课件

范例:小组授权书
产品交付
业务专案
我们目前的X产品平均递送时间是72小时.客户要求48小时.我 们的竞争者可以满足48小时的要求.结果是,我们最近10个月中 每个月损失了1.5%的客户($75,000/月),在同样的10个月内新的 销售额下降了10%($60,000/月).降低我们的递送时间,我们预计 现有客户基础下降可低于0.3%, 新的销售额将在原有的基础上
Page 11
项目范围
目的
➢ 项目范围确定了业务改进机会的边界。
项目范围
➢ 流程及行动的边界,起始和终止步骤是什么? ➢ 业务的什么部分被包括在内? ➢ 业务的什么部分没有被包括在内? ➢ 如果有的话,什么是在小组边界外的?
Page 12
小组挑选
目的
➢ 挑选你的小组成员并分派责任。
小组挑选
➢ 谁对谁负责,负责什么? ➢ 谁是项目担保人?他/她对小组的责任是什么? ➢ 项目小组怎样协调他们的工作? ➢ 谁是小组领导人?小组领导人的责任是什么? ➢ 谁在小组之上? ➢ 小组多久汇报一次?怎样汇报? ➢ 需要什么类型的小组成员?在什么阶段需要他们?
Page 27
职能分布流程图
• 与流程分解图一样,职能分布流程图按顺序显示了流程的步骤, 它也阐明了每个流程在那里和被谁执行.
特征 • 用如以下所列的符号来表示流程流向,决定要点和执行活动. • 职能分布流程图通常要用相当多的时间来准备,但是它们对在
执行改进前了解流程特别有帮助.它们 需要熟悉流程每个领 域人的输入.
Page 8
业务专案
业务专案阐明 • 业务专案描述了项目执行的收益,业务专案解
决以下问题:
➢ 项目和其他业务工作有结合起来吗? ➢ 项目小组的重点是什么? ➢ 小组工作应该在哪里开始和结束? ➢ 项目对其他业务单元和雇员有什么影响? ➢ 项目会收到什么收益? ➢ 收益的价已经被量化了吗?
六西格玛案例分析
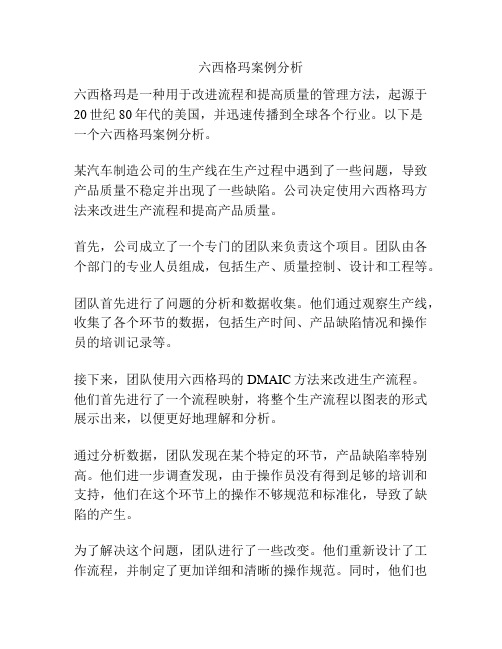
六西格玛案例分析六西格玛是一种用于改进流程和提高质量的管理方法,起源于20世纪80年代的美国,并迅速传播到全球各个行业。
以下是一个六西格玛案例分析。
某汽车制造公司的生产线在生产过程中遇到了一些问题,导致产品质量不稳定并出现了一些缺陷。
公司决定使用六西格玛方法来改进生产流程和提高产品质量。
首先,公司成立了一个专门的团队来负责这个项目。
团队由各个部门的专业人员组成,包括生产、质量控制、设计和工程等。
团队首先进行了问题的分析和数据收集。
他们通过观察生产线,收集了各个环节的数据,包括生产时间、产品缺陷情况和操作员的培训记录等。
接下来,团队使用六西格玛的DMAIC方法来改进生产流程。
他们首先进行了一个流程映射,将整个生产流程以图表的形式展示出来,以便更好地理解和分析。
通过分析数据,团队发现在某个特定的环节,产品缺陷率特别高。
他们进一步调查发现,由于操作员没有得到足够的培训和支持,他们在这个环节上的操作不够规范和标准化,导致了缺陷的产生。
为了解决这个问题,团队进行了一些改变。
他们重新设计了工作流程,并制定了更加详细和清晰的操作规范。
同时,他们也加强了对操作员的培训和技能提升。
在新的工作流程和操作规范的指导下,生产线的产品缺陷率明显下降。
并且,在实施改进后的几个月内,产品缺陷率一直稳定在一个较低的水平上。
通过这个案例的分析,我们可以看到六西格玛方法在这个汽车制造公司的生产线改进中发挥了重要的作用。
通过数据收集和分析,团队能够准确地找到问题的根源,并制定相应的改进方案。
通过重新设计工作流程和加强对操作员的培训,生产线的产品质量得到了明显的提高。
这个案例也展示了六西格玛方法在提高流程稳定性和质量方面的潜力。
6西格玛课题优秀案例

6西格玛课题优秀案例
六西格玛是一种质量管理方法,旨在通过统计学的方法和工具来降低产品和服务的缺陷率,提高生产效率和降低成本。
下面是一些六西格玛课题的优秀案例:
1. LG 电子的微波炉门泄漏问题:LG 电子在制造微波炉时遇到
了门泄漏问题,这严重影响了产品质量和品牌形象。
通过使用六西格玛方法,LG 电子的团队确定了问题的根本原因,并制定了改进计划,最终成功解决了这个问题。
2. 波音公司的飞机维修成本降低:波音公司使用六西格玛方法来降低飞机的维修成本,通过分析和测量,确定了问题的的根本原因,并采取了一系列措施来减少维修成本。
这项改进不仅降低了公司的运营成本,还提高了飞机的可靠性和安全性。
3. 沃尔玛的库存管理优化:沃尔玛使用六西格玛方法来优化库存管理,通过测量和分析问题,制定了一套优化方案,成功地降低了库存成本和提高了供应链的效率。
4. 通用电气的生产效率提高:通用电气使用六西格玛方法来提高生产效率,通过分析和测量,确定了问题的根本原因,并采取了一系列措施来提高效率,最终提高了公司的盈利能力。
这些案例展示了六西格玛方法在各个领域的应用和成功的结果,不仅提高了产品或服务的质量,还降低了成本和提高了生产效率。
6SIGMA某工作案例1精编版

Code
Factor
Levels
最佳值
A
Nut Dim
+1
4.1
B
C/L Dim
-1
3.6
D
Bond
+1
3
E
Point Height
+1
Байду номын сангаас0.5
Nut 拔出力越大越好,为了得到最大Nut Force,(Max Y) 调整X’s 的水准 .并进行Confirming Test.
NOV-23-2000
I-Phase 小结
Nut 业体更换, Diameter 尺寸保证,Nut 成型情况改善;Carriage Lower设计改善,Bond涂抹量标准化;Carriage Lower设计改善,增加与Nut 接触面积;对不良C/L Diameter进行改善,全部采用现地化部品;对Nut 拔出力进行管理,确保Nut 与C/L的结合情况。
在此种条件下对100ea 测试Nut Force ,对Data 进行Process Capability Analysis.
NOV-23-2000
I
工程能力:改善前:6438PPM改善后:493PPM向上率:92.4%
Process Capability Analysis for Nut Force
改善前
改善后
6,438PPM
493PPM
NOV-23-2000
I-Phase 小结
Nut 业体更换, Diameter 尺寸保证,Nut 成型情况改善;Carriage Lower设计改善,Bond涂抹量标准化;Carriage Lower设计改善,增加与Nut 接触面积;对不良C/L Diameter进行改善,全部采用现地化部品;对Nut 拔出力进行管理,确保Nut 与C/L的结合情况。
六西格玛改善案例

对关键因子的控制方案如表
关键因 子
详情
控制方案
频率
实施 者
确认 者
1
晾干 温度
需要提高晾 干温度来缩 短晾干时间
检查和控制 加热系统
2次/ 班
组长
生产 经理
需要提高传
传送 送带速度来 检查和控制 2 带速 缩短产品在 传送带调速
度 传送带上的 器的位置
2次/ 班
组长
Байду номын сангаас
生产 经理
时间
35
改善后产品装配线过程能力控制
在传送带上方加一套带自动控制的加热系统。自动指的 是设定具体问题以后系统会将温度保持的设定的范围之内, 如本案中的45±5℃,意思是当问题低于40℃时,加热系统自 动启动加热装置,使温度达到设定的范围;当温度高于50℃ 时,加热系统自动关闭加热装置,停止加热使温度回到设定 范围。同时为了减少因加热造成的粘接剂挥发过快而影响环 境问题,我们增加了一套排风系统,及时将挥发的粘接剂排 到厂外。
所有的点接近参考
线,说明数据遵循
26
着正态分布。
双样本T检验
从图中可以得:P-值为 0.585及 0.248,均大于显著 性水平σ(0.05),运用双样本T检验是有效的。其检验 结果如图
由图中数据可知,P值=0.000<0.05,证明此因子为 重要显著因子 。 27
双样本T检验
验证X2 运用双样本T检验,结果如图
23
项目关键影响因素识别
RPN(risk priority number) 风险系数是事件发生的频率、严 重程度和检测等级三者乘积,用来衡量可能的工艺缺陷。RPN 数值在 1—10 为最好的情况,10—50 对产品有较小的危害; 51—100 对产品有中等危害,需进行改善;101—1000 对产品有 严重危害,需深入调查分析。
六西格玛项目案例

六西格玛项目案例六西格玛是一种以数据为基础的管理方法,旨在通过减少变异和提高流程稳定性来改善组织绩效。
下面我们将通过一个实际的案例来介绍六西格玛项目的实施过程和效果。
某电子制造公司在生产过程中遇到了质量问题,产品的不良率居高不下,给公司的声誉和利润带来了严重影响。
为了解决这一问题,公司决定引入六西格玛项目管理方法进行改善。
首先,公司成立了一个由跨部门人员组成的六西格玛团队,确定了项目的范围和目标,制定了改善计划。
团队首先进行了对生产流程的全面分析,采集了大量的数据并进行了统计和分析。
通过对数据的分析,他们发现了导致产品不良的关键因素,并确定了改善的方向。
在确定了改善方向后,团队对生产流程进行了调整,并制定了一系列的改善措施。
这些措施包括优化设备设置、改进操作流程、加强员工培训等。
在实施改善措施的过程中,团队遇到了一些困难和阻力,但他们通过充分的沟通和协调,成功地克服了这些问题。
同时,团队还对改善效果进行了持续的监控和评估,确保改善措施的有效性和持久性。
经过几个月的努力,公司的产品不良率显著下降,生产效率和质量得到了显著提高。
同时,公司还在生产成本、员工满意度等方面取得了显著的改善。
这些改善不仅带来了经济效益,也提升了公司的竞争力和声誉。
通过这个案例,我们可以看到,六西格玛项目管理方法的有效性和实用性。
通过系统的数据分析和全面的流程优化,公司成功地解决了质量问题,取得了显著的改善效果。
这个案例也充分展示了团队合作和持续改进的重要性,以及六西格玛项目管理方法在实际中的应用前景。
总的来说,六西格玛项目管理方法是一种非常有效的管理工具,可以帮助组织解决复杂的问题,提高绩效和竞争力。
希望更多的组织能够引入六西格玛方法,实现持续改进和可持续发展。
6西格玛改善案例解析
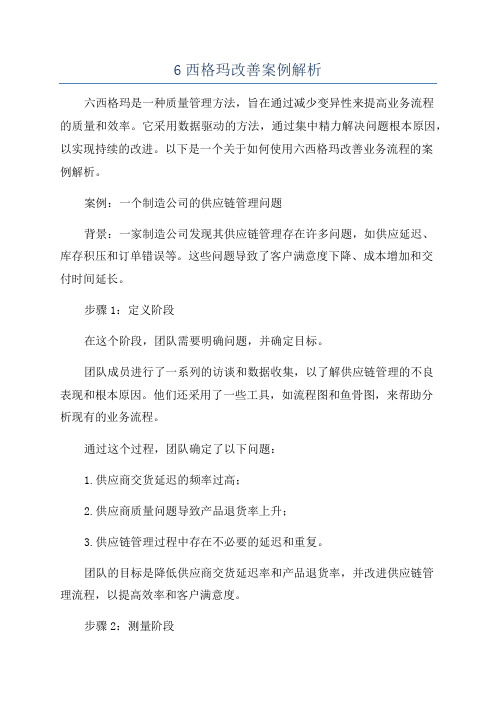
6西格玛改善案例解析六西格玛是一种质量管理方法,旨在通过减少变异性来提高业务流程的质量和效率。
它采用数据驱动的方法,通过集中精力解决问题根本原因,以实现持续的改进。
以下是一个关于如何使用六西格玛改善业务流程的案例解析。
案例:一个制造公司的供应链管理问题背景:一家制造公司发现其供应链管理存在许多问题,如供应延迟、库存积压和订单错误等。
这些问题导致了客户满意度下降、成本增加和交付时间延长。
步骤1:定义阶段在这个阶段,团队需要明确问题,并确定目标。
团队成员进行了一系列的访谈和数据收集,以了解供应链管理的不良表现和根本原因。
他们还采用了一些工具,如流程图和鱼骨图,来帮助分析现有的业务流程。
通过这个过程,团队确定了以下问题:1.供应商交货延迟的频率过高;2.供应商质量问题导致产品退货率上升;3.供应链管理过程中存在不必要的延迟和重复。
团队的目标是降低供应商交货延迟率和产品退货率,并改进供应链管理流程,以提高效率和客户满意度。
步骤2:测量阶段在这个阶段,团队需要收集关于问题的数据,并量化问题的影响。
团队成员收集并分析了供应商交货延迟率和产品退货率的数据,并确定了相关的指标和测量方式。
通过数据分析,团队发现供应商交货延迟率为10%,产品退货率为5%。
步骤3:分析阶段在这个阶段,团队使用统计工具和质量工具来分析问题的原因。
团队使用了流程图和鱼骨图来分析供应链管理的问题。
他们还使用了直方图、散点图和控制图等统计工具来确定问题的原因。
通过分析,团队发现供应商交货延迟的主要原因是缺乏有效的供应商评估和监控机制,产品退货率的主要原因是供应商质量问题。
步骤4:改进阶段在这个阶段,团队需要提出解决问题的解决方案,并实施改进措施。
团队提出以下改进方案:1.建立供应商评估和监控机制,定期对供应商进行评估,并设置合理的交货期限。
2.加强供应商质量管理,与供应商建立更紧密的合作关系,并提供培训和支持,以改进他们的生产流程和质量控制。
质量管理6Sigma项目案例

6Sigma项目案例一个PCBA工厂波峰焊工序的6Sgma项目改善。
因为波峰焊成为制约PCBA质量的瓶颈。
当前首次通过率为15%,DPMO为30000PPM{种产品每块板焊点数(机会数)为532点}。
2001年9月,该公司成产了一支6Sigma项目改善队伍,其组织结构如下:1.讨论是否选此项目为6Sigma项目。
经小组讨论,大家一致认同此项目为6Sigma项目,理由是:(1)目前焊接DPMO与客户要求存在很大差距,已引起客户强烈投诉。
(2)造成DPMO低的原因不详。
(3)尚未找到改善方法。
(4)实施6Sigma项目改善后可带来大的财务收益和客户满意度的极大提高。
(5)公司人力、物力、财务允许,且技术不是非常复杂。
2.确定项目CTQ关键质量特性。
3.制定6Sigma项目计划书。
4.明确各部门人员职责及其绩效考核方法。
5.确定6Sigma项目所需资源和培训日程。
具体工作分工如下:一、确定项目CTQ及项目Y波峰焊工序是客户特别关注的影响产品品质的关键工序,客户最关注的是焊点一次成功率要高,转化CTQ为焊点的DPMO要小。
故波峰焊点一次成功率为本项目的CTQ,项目Y 衡量CTQ的参数为焊点DPMO。
二、制定6Sigma项目计划书胡伟和张兵根据PCBA焊接状况和已有的DATA制定的6Sigma项目方案如下:6Sigma项目方案三、各成员职责与绩效考核办法续表四、项目资源及培训安排项目资源配置项目培训安排五、项目实施日程安排六、完成Y的测量系统分析本项目中Y的数据为离散二元数据,对其进行分析时需用离散数据的GAGER&R分析进行。
方法:取50块各有一个指定焊点的PCBA,这些焊点有合适焊点、有临界焊点、有不合格焊点,由5个检查员将每块板检查两次,两次之间的时间间隔为一周。
离散数据GAGER&R评估参数:总的一致百分比:用来评估检验员结果一致辞的次数的百分比可重复性百分比:用来评估检验员检查同一部件结果一致的能力可再现性百分比:用来评估多个检验员检验同一部件的结果一致的能力计算公式为:一致百分比=一致的总次数机会的总次数本例计算结果=89%如结果>85%,检验结果可接受。
六西格玛改善案例

六西格玛改善案例山东工商学院SHANDONG INSTITUTE OF BUSINESS AND TECHNOLOGY毕业论文(设计)GRADUATION THESIS (DESIGN)论文,设计,题目基于六西格玛的威高集团注射器质量研究 Title Of Thesis(Design)分院,系别,管理科学与工程学院 Department专业班级工业工程工业061 SpecialiClassty论文,设计,作者论文完成日期易孟良 2010年06月02日 Author of Thesis(Design) Date论文,设计,指导教师指导教师职称刘利军教授 AdvisoThe Title of Advisorr基于六西格玛的威高集团注射器质量研究Quality Rsearch on Sringe Based on Six Sigmafor WEGO.Ltd作者:易孟良山东工商学院指导教师对毕业论文,设计,的评语Advisor’s Comments on Graduation Thesis (Design) 评语,指导教师,签章,Signature of Advisor日期Date评阅人意见评阅人姓名: 职称:选项标准: A很同意 B同意 C基本同意 D不同意评价项目 A B C D选题符合专业培养目标,体现综1 合训练基本要求选题 2 题目难易适度质 3 题目工作量适当量4 有理论意义或实际价值5 查阅文献资料能力强分能6 综合运用知识能力强力 7 研究方案的设计能力强项水8 研究方法和手段的运用能力强平评 9 外文应用能力强价 10 文题相符成 11 写作水平高果 12 写作规范质13 篇幅适度量14 成果有理论或实际价值总体评价: 优 ? 良 ? 中 ? 及格 ? 不及格 ?评阅人评语:评阅人签字: 年月日答辩,评审,委员会意见Appraisal of Defence Commission答辩,评审,成绩Mark of Defence鉴定意见Appraisal & Comments主任,签章,Signature of Dean日期Date基于六西格玛的威高集团注射器质量研究摘要本设计是基于威高集团注射器车间的六西格玛质量研究,首先根据客户的需求和过程控制关键特性选定了六西格玛改进项目,然后对选定的项目运用D(定义)、M(测量)、A(分析)、I(改进)、C(控制)的模式进行改进。
六西格玛经典案例

六西格玛经典案例1. 引言六西格玛(Six Sigma)是一种质量管理方法,旨在通过降低产品和过程的变异性来提高质量和效率。
这个方法最早由日本公司Toyota引入,并于20世纪80年代由Motorola公司推广到全球。
六西格玛的核心思想是通过收集和分析数据来识别和消除导致质量问题和不必要浪费的根本原因。
在过去的几十年里,许多企业采用了六西格玛来改进其业务流程和产品质量。
本文将介绍几个六西格玛的经典案例,展示六西格玛的强大潜力和实际应用效果。
2. Motorola公司的成功案例Motorola公司在20世纪80年代是最早应用六西格玛的企业之一。
当时,该公司生产的传呼机存在严重的质量问题,导致市场份额大幅下降。
为解决这个问题,Motorola决定采用六西格玛方法来改善产品质量。
Motorola首先对传呼机生产过程进行了详细的调查和数据分析,找出了导致质量问题的根本原因。
然后,他们采取一系列措施来消除问题,如改进生产设备、培训员工和优化生产流程。
结果,Motorola成功地降低了传呼机的缺陷率,提高了产品质量,并重塑了自己在市场上的形象,重新夺回了市场份额。
这个案例显示了六西格玛的实际效果,并证明了通过数据分析和改善措施可以显著提高产品质量。
3. General Electric公司的成本降低案例General Electric(GE)是一个全球性的多元化企业,拥有众多业务部门。
在90年代初,GE公司面临着巨大的竞争压力和成本问题。
GE采用六西格玛方法来降低成本,并在其电力业务部门中开展了一项改进项目。
该项目通过分析电力设备的生产流程,并使用六西格玛工具找出了浪费和低效的环节。
随后,GE采取了一系列措施来改进生产流程,降低成本,如优化设备配置、改进工作流程和培训员工。
通过六西格玛项目的实施,GE成功地降低了电力设备生产的成本,并提高了生产效率。
这个案例证明了六西格玛可以应用于各种行业和业务部门,帮助企业降低成本、提高效率。
基于六西格玛管理的银行流程改善案例

基于六西格玛管理的银行流程改善案例六西格玛(Six Sigma)是一种管理方法论,旨在通过降低质量缺陷来提高业务流程的效率和一致性。
在银行业中,六西格玛可以应用于各个业务流程,如开户、贷款审批、客户服务等。
下面是一个基于六西格玛管理的银行流程改善案例。
案例一:贷款审批流程改善问题描述:银行的贷款审批流程存在问题,导致审批时间较长,客户投诉率较高。
1.确定目标:改进贷款审批流程,提高审批效率和客户满意度。
2.收集数据:收集贷款审批的各个环节的数据,包括申请材料收集时间、内部审批时间、客户反馈等。
3.分析数据:根据收集到的数据,分析贷款审批流程中存在的瓶颈和问题,比如申请材料收集不及时、内部审批流程复杂等。
4.改进措施:针对分析结果,提出改进措施,如优化申请材料收集流程,简化内部审批流程等。
5.实施改进:根据改进措施,对贷款审批流程进行改进,并进行试点运行。
6.监控结果:监控改进后的流程效果,比如贷款审批时间的减少、客户投诉率的下降等。
7.标准化改进:如果改进效果良好,将改进后的流程标准化,确保持续的质量改进。
通过六西格玛的方法,银行在贷款审批流程上进行了改进,取得了显著的效果。
贷款审批时间从原来的两周减少到了一周,客户投诉率下降了50%。
这不仅提高了银行的工作效率,还提升了客户体验和满意度。
此外,银行还可以应用六西格玛的方法改进其他业务流程,比如客户服务流程。
在客户服务流程上,银行可以通过分析客户投诉数据,找出问题的根本原因,并提出解决方案。
比如,如果客户投诉主要是因为服务人员的不专业或者服务流程不清晰,银行可以进行培训和制定清晰的服务流程,以提高客户满意度。
总结起来,六西格玛是一种有效的管理方法论,可以帮助银行在各个业务流程上实现质量的持续改进。
通过收集数据、分析问题、制定改进措施并监控结果,银行可以不断提高业务流程的效率和一致性,以提升整体的竞争力和客户满意度。
六西格玛成功(6sigma)案例学习[优秀范文五篇]
![六西格玛成功(6sigma)案例学习[优秀范文五篇]](https://img.taocdn.com/s3/m/51b2a8e3c0c708a1284ac850ad02de80d5d80658.png)
六西格玛成功(6sigma)案例学习[优秀范文五篇]第一篇:六西格玛成功(6sigma)案例学习6sigma成功案例**电子:步伐稳健行走于6σ之路2000年12月,第十届台湾品质奖的颁奖典礼上,在评审“品质不折不扣”的理念下,**电子以多年来致力追求品质的决心与成就,脱颖而出,获得台湾品质奖。
细察**电子追求品质的努力、实践品质的过程,得以知道这个奖得来实至名归。
**电子自1994年起,就在董事长许胜雄的领导下,努力实践6σ(Six Sigma)的品质策略。
何谓6σ?σ在字面上的定义是为统计学上的标准差,简单来说,σ是一个测量品质的标准工具,它代表一种绩效目标,也是一种品质改善的观念。
达到6σ表示每百万次中只会出现3.4个错误,几乎等于零缺点。
σ曾经协助许多世界级企业展现惊人的成绩,它曾经使通用电气(GE)公司迈向营运的高峰,被杰克韦尔奇称许为通用所采用的过最重要的管理措施;也是西方企业力抗日本企业反败为胜的法宝。
提起**电子导入6 σ的原由,**电子副总经理陈乃源表示:“起源于为了满足顾客对品质的要求。
”在未实行6 σ前,**电子所生产的产品错误率颇高,无法达到客户满意,除容易引起顾客的抱怨,相对也缺乏竞争力。
为了提高竞争力,**电子决定导入6 σ。
当时**电子派遣了一批人员到美国接受6σ的训练课程,其中成员包含总经理、数位副总及相关人员,陈乃源也是其中之一。
受训回国后,陈乃源全心投入**电子执行6 σ的架构规划。
陈乃源指出:“实践6 σ的基本原则,是以顾客需求为出发点,一切改善都必须以顾客需求为主,它讲求从制造过程开始改进,而不是看产品产出最后的结果,因为产品事后的修补往往要花费更多的成本。
品质改善最重要的是要从根源做起,也就是在设计时就减少错误的机会。
尤其是在产品生命周期急速缩短的今天,已没有时间让你尝试错误了,也无法再像过去一样等生产过程结束后再统计错误,必须在设计的时候就减少错误的发生,把线上的制程能力及零件的制造能力都计算、考虑进去,让产品合于标准,将制造流程改善,一次就做好,使得后续不至于有错误发生。
- 1、下载文档前请自行甄别文档内容的完整性,平台不提供额外的编辑、内容补充、找答案等附加服务。
- 2、"仅部分预览"的文档,不可在线预览部分如存在完整性等问题,可反馈申请退款(可完整预览的文档不适用该条件!)。
- 3、如文档侵犯您的权益,请联系客服反馈,我们会尽快为您处理(人工客服工作时间:9:00-18:30)。
Y/N Agree Y Y Y Y Y Y Y Y Y N Y Y Y Y Y
Y/N Agree Y Y Y Y Y Y Y Y Y N Y Y Y Y Y
% APPRAISER SCORE(1) -> % SCORE VS. ATTRIBUTE
(2)
100.00% -> 100.00%
93.33% 93.33%
0.045 UCL=0.04401 4.3 4.2
D M A I C
Binomial Process Capability Report for 不良数
Rate of Defectives
%Defective e
Proportion n
4.1 4.0 3.9 3.8 3.7 3.6 10000 20000 30000 40000
目标水准 10500 3.86σ 47.25万元/年
COPQ
COPQ 计算 TABLE
▶ COPQ (外观不良浪费) 计算公式 (外观不良浪费 外观不良浪费) = 〔浪费产品数量 〕* 产品公司内预算单价 ▶ 改善前 COPQ = 42000 * 45元 = 189.6万元/年 189.6万元 万元/ ▶ 改善目标 COPQ = 10500 * 45元 = 47.25万元/年 47.25万 ▶ 经营贡献金额 = 改善前 COPQ – 改善目标 COPQ = 142.35万元/年 142.35万元 万元/ 6 Sigma 的技法执行 Project,找出最佳的改善条件,把门壳废弃不良最小化 Project,找出最佳的改善条件, — 以树立好的改善计划为基础,节减计划定为减少1.4百万,对公司经营做贡献 以树立好的改善计划为基础,节减计划定为减少1.4百万, 1.4百万 — 改善结束日 - 2003年 2月 2003年 28日止促进结束 28日止促进结束
Count
D M A I C
改善目标树立
6 Sigma 的技法执行 Project,找出最佳的改善条件,把门壳废弃不良最小化 Project,找出最佳的改善条件,
现况 门壳废弃 40000PPM 来自 中国最大的资料库下载 不良率
目标
效果
10000PPM 10000PPM
75%减少 75%减少
为了Gage 计划? ▣ 为了Gage R&R 收集 Data 计划
D M A I C
测定项目 : 门壳外观不良 测定方式 : 检验员检验 SAMPLE 数 : 良品 2个,不良 13个 个 不良 个 : 2 次反复 测定次数 来自 中国最大的资料库下载测定员 : 现场作业者 名 现场作业者3名 : 2002年11月 05日 测定日期 年 月 日 Data 数量 : 总90 Data
REF生产加工 REF生产加工
来自 中国最大的资料库下载
门壳废弃外观不良改善
Project No. : Division : G/B Name :
1
(V 营销管 训资 载)
Project 促进背景
现在不良率:4% 不良达成目标:1% 急待改善和解决现在的问题 &VOC
Voice Of Customer
◆ 内部顾客 - 组力工程 : 门壳 性能未达到关联,要求改善门壳外观 品质. 门壳外观 ◆ 外部客户 - 消费者 : 要求供应高品质、优良外观的产品 .
(V 营销管 训资 载)
3
D M A I C
Project 对象项目选定
Input
门壳 投入
资材投入
D M A I C
门壳预冲
VA
NVA
门壳折弯
VA
NVA
来自 中国最大的资料库下载
门壳辊压
VA VA
NVA
涂装
NVA
最终检查
NVA
装车移动
Output
门壳 完成品
(V 营销管 训资 载) 9
Data Collection
Project Schedule
Plan
02. 11月 月
来自 中国最大的资料库下载
Doing
02 . 12月 月 03. 01月 月 03. 02月 月
DEFINE
MEASURE ANALYZE IMPROVE CONTROL
(V 营销管 训资 载)
数据来源: 数据来源: 2002.1.1~2002.10.30
A /L 门 壳 不 良 分 析
40000
划伤不良 1位, 凸点不良 2位,毛刺不良 位 位 毛刺不良 3位 占全体不良的 75.8% 位
100 80
30000
来自 中国最大的资料库下载
20000
60 40
10000
经营者的要求 (VOB) 现在的问题 来自 中国最大的资料库下载
要求供应同等品质的 废弃不良过多材料费上升 加工产品 因此对外竞争力变弱 要求改善加工部品品质 生产良品数量增加
对加工部品的工程不良率40,000 ppm以下 对加工部品的工程不良率40,000 ppm以下, Cpk 向上活动展开中 以下,
2100 5 .1 9 5 .1
2050 4 .9 1 0 0 .0
前3位均为外观品质不良有必要对门壳外观进行重点改善 位均为外观品质不良有必要对门壳外观进行重点改善 因此选定为改善C.T.Q 因此选定为改善C.T.Q
(V 营销管 训资 载) 4
Percent
(V 营销管 训资 载)
13
Analyze
Cause & Effect Diagram
前处理不良 露底
D M A I C
C
涂漆不良 涂装时
C
铲脚印 包装
资材不良
木架 涂料 环境
模具不良
超寿命
线条
C
凹点
凸点
N
底漆 检查时
C
模具老化
▣ 为了工程能力分析收集 Data 计划 计划?
Data 收集工程 :门壳外观 最终检查工程 门壳外观 Data 收集期间 : 2002年 1月 01日 ~ 10月 3日 止 年 月 日 月 日 Data 数量 : 门壳 别1次 , 取Sample 15个 次 个
(V 营销管 训资 载) 10
93.33% 93.33% 93.33%
SCREEN % EFFECTIVE SCORE(3) -> 93.33% SCREEN % EFFECTIVE SCORE vs. ATTRIBUTE (4) ->
(V 营销管 训资 载)
11
工程能力分析
P Chart
(V 营销管 训资 载) 2
Define
Problem Statement:
因加工工程的工程废弃不良增加,资材 Loss 过多 为了高效率的 产品外观品质,需提高加工品的信赖性 .
来自 中国最大的资料库下载
D M A I C
因加工部品的INPUT检查, 运输、包装划伤等废弃现象频繁.
Gage R&R ( Q.C Gage )
Attribute Gage R & R Effectiveness
DATE: 2002-11-5 NAME: HUANGJIANXIN PRODUCT: 3313 Spark Plug BUSINESS: F&SP
Operator #2 Try #1 Try #2 划伤 划伤 毛刺 毛刺 pass pass 划伤 划伤 毛刺 毛刺 凸点 凸点 毛刺 毛刺 划伤 划伤 凸点 凸点 毛刺 pass 划伤 划伤 pass pass 凸点 凸点 凸点 凸点 划伤 划伤 Operator #3 Try #1 Try #2 划伤 划伤 毛刺 毛刺 pass pass 划伤 划伤 毛刺 毛刺 凸点 凸点 毛刺 毛刺 划伤 划伤 凸点 凸点 pass 毛刺 划伤 划伤 pass pass 凸点 凸点 凸点 凸点 划伤 划伤
0.040
P=0.03962
0.035
LCL=0.03524
来自 中国最大的资料库下载 0 1 2 3 4 5
6
7
8
9
10
Sample Number
Sample Size
Cumulative %Defective
4.1
Summary Stats
(denotes 95% C.I.) Average P: 0.0396216 (0.0388, 0.0404)
D M A I C
SCORING REPORT
Attribute Legend 1 pass 2 fail
5
(use d in com putations)
All operators agree within and All Operators between each Other agree with s tandard
D M A I C
Project Team
支援
来自 中国最大的资料库下载
PART长 PART长
社员 (工程改善 工程改善) 工程改善
社员 (工程改善 工程改善) 工程改善
社员 (DATA 收集 收集)
(V 营销管 训资 载)
6
D M A I C
D M A I C
◆毛刺 毛刺:板材冲切后的毛边大于0.2mm 为毛刺不良 外观不良 = 定义为门壳表面有 毛刺 + 凸点 + 毛刺
Project .Y.——减少门壳外观不良的活动 .Y.——减少门壳外观不良的活动
(V 营销管 训资 载)
8
Process Flow Diagram
3.8
3.9
4.0
4.1
水准: ▣ σ水准 Process Z=3.36 σ 水准
(V 营销管 训资 载)