典型模具设计
第9章 UG注塑模设计实例——典型三板模

• 9.1.1 设计流程
型腔布局
分型
型腔
型芯 调入模架
AP 、 BP 板处理
标准件调入,浇注系统,冷 却系统设计,开腔处理,出 工程图纸……
• 9.1.2设计前准备
一、产品信息 产品名称:PORT,材料:ABS,收缩率:0.5%,产品重量:173g
二、注塑机信息 注塑机型号:HTF450*2A 注射重量:1296g 合模力:4500KN,拉杆内距离(mm):780X780 最大模厚780mm,最小模厚330mm 定位圈直径200mm,喷嘴直径4mm,喷嘴球头SR15mm, 喷嘴最大伸入高度50mm 顶棍孔直径60mm
UGNX8.0注塑模具设计教程
第9章 UG注塑模设计实例——典型 三板模
教学要求
• 学习整副模具的设计过程及设计细节, 熟悉模具设计的流程及设计要点。
• 掌握MoldWizard设计典型三板模方法, 标准模架的设计和调用过程。
本章内容
• 9.1典型三板模:电器装饰盖模具设计实例
导入产品
设计工件
三、模具设计基本信息 模具寿命:20万 型腔数目:一模一腔 浇口形式:直浇口 取件方式:人工取件 顶出方式:机械顶出
• 9.1.3 设计准备
一、项目初始化 二、模具坐标系设置 三、设置工件
初始化后产品
模具CSYS
工件
• 9.1.4分型
型腔
分型面
型芯
• 9.1.5 添加模架
一、导入模架、调整模架 二、定模板【AP】设计 三、动模板【BP】设计
斜顶2设计
斜顶镜像结果
• 9.1.8顶出系统设计
一、顶针设计 二、修剪顶针 三、顶出系统复位 四、垃圾钉
顶针设计
顶出复位
ug注塑模具设计实例

ug注塑模具设计实例以下是一个简单的注塑模具设计实例,模具设计的基本概念和步骤。
设计案例:一个简单的塑料瓶盖模具1. 确定产品尺寸和形状产品是一个简单的塑料瓶盖,直径为20mm,高度为3mm。
瓶盖表面有纹理,以增加摩擦力,方便开启。
2. 确定模具结构模具采用典型的双板模结构,由动模板和定模板组成。
动模板上设有型腔,定模板上设有浇口和流道。
3. 确定型腔布局由于瓶盖尺寸较小,可以采用一模一腔的布局。
型腔布置在动模板上,浇口和流道布置在定模板上。
4. 设计浇口和流道浇口和流道的设计需要考虑塑料的填充和流动。
本例中,采用点浇口,浇口直径为1mm,流道直径为4mm。
5. 设计推出机构推出机构用于将成型后的产品从模具中推出。
本例中,采用推杆推出,推杆直径为8mm,数量为4个。
推杆安装在动模板上,推出时推动瓶盖脱离型腔。
6. 设计冷却系统冷却系统用于将成型过程中的热量从模具中带走,防止产品变形和开裂。
本例中,采用水管冷却,水管直径为4mm,布置在动模板和定模板上。
7. 设计排气系统排气系统用于将成型过程中的气体从模具中排出,防止气体的积聚和压力的升高。
本例中,采用排气槽,排气槽直径为2mm,数量为4个。
排气槽布置在定模板上。
8. 设计模具零件加工工艺性模具零件的加工需要考虑其工艺性。
本例中,采用数控加工中心进行加工,材料选择不锈钢。
9. 设计模具装配工艺性模具装配需要考虑其工艺性。
本例中,采用螺钉连接动模板和定模板,并使用定位销进行定位。
以上是一个简单的注塑模具设计实例,希望能帮助您更好地理解模具设计的基本概念和步骤。
常见的压铸模具结构及设计
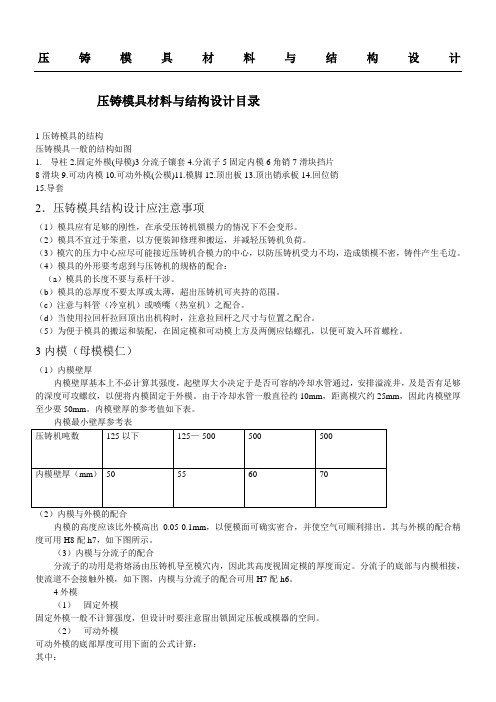
压铸模具材料与结构设计压铸模具材料与结构设计目录1压铸模具的结构压铸模具一般的结构如图1.导柱2.固定外模(母模)3分流子镶套4.分流子5固定内模6角销7滑块挡片8滑块9.可动内模10.可动外模(公模)11.模脚12.顶出板13.顶出销承板14.回位销15.导套2.压铸模具结构设计应注意事项(1)模具应有足够的刚性,在承受压铸机锁模力的情况下不会变形。
(2)模具不宜过于笨重,以方便装卸修理和搬运,并减轻压铸机负荷。
(3)模穴的压力中心应尽可能接近压铸机合模力的中心,以防压铸机受力不均,造成锁模不密,铸件产生毛边。
(4)模具的外形要考虑到与压铸机的规格的配合:(a)模具的长度不要与系杆干涉。
(b)模具的总厚度不要太厚或太薄,超出压铸机可夹持的范围。
(c)注意与料管(冷室机)或喷嘴(热室机)之配合。
(d)当使用拉回杆拉回顶出出机构时,注意拉回杆之尺寸与位置之配合。
(5)为便于模具的搬运和装配,在固定模和可动模上方及两侧应钻螺孔,以便可旋入环首螺栓。
3内模(母模模仁)(1)内模壁厚内模壁厚基本上不必计算其强度,起壁厚大小决定于是否可容纳冷却水管通过,安排溢流井,及是否有足够的深度可攻螺纹,以便将内模固定于外模。
由于冷却水管一般直径约10mm,距离模穴约25mm,因此内模壁厚至少要50mm。
内模壁厚的参考值如下表。
内模最小壁厚参考表(2)内模与外模的配合内模的高度应该比外模高出0.05-0.1mm,以便模面可确实密合,并使空气可顺利排出。
其与外模的配合精度可用H8配h7,如下图所示。
(3)内模与分流子的配合分流子的功用是将熔汤由压铸机导至模穴内,因此其高度视固定模的厚度而定。
分流子的底部与内模相接,使流道不会接触外模,如下图,内模与分流子的配合可用H7配h6。
4外模(1)固定外模固定外模一般不计算强度,但设计时要注意留出锁固定压板或模器的空间。
(2)可动外模可动外模的底部厚度可用下面的公式计算:其中:h:外模底部之厚度(mm)p:铸造压力(kg/cm2)L:模脚之间距(mm)a:成品之长度(mm)b:成品之宽度(mm)B:外模之宽度(mm)E:钢的杨氏模数=2.1×106kg/cm2d:外模在开模方向的最大变形量(mm),一般取d≤0.05mm.例:某铸件长300mm,宽250mm,铸造压力选定280(kg/cm2),外模之宽度560(mm),模脚之间距360(mm),最大变形量取0.05(mm)。
典型注塑模设计-项目1-模块三

1.排气系统
大多数情况下可利用模具分型面或模具零件间的配合间隙自然地排气 ,其间隙值通常为0.01~0.03mm,以不产生溢料为限。
排气与引气系统的设计
相关理论知识
2.引气系统的设计 大型深壳形制品包紧型芯形成真空,难以脱模,需要引气装置。 镶拼式侧隙引气 气阀式引气 相关理论知识
能合理地设计浇注系统
能合理地进行成型零件设计
能正确地绘制模具装配图和零件工作图
1.能设计合理的冷却系统 2.能设计合理的排气系统 3.能绘制合理的冷却水道布置图
学习目标
工作任务
根据图示的塑件零件图以及已确定的总体结构方案,设计本模具的冷却系统和排气系统,并绘制冷却水道布置图。
冷却系统设计
低粘度-低模温
单击此处添加正文,文字是您思想的提炼,为了演示发布的良好效果,请言简意赅地阐述您的观点。您的内容已经简明扼要,字字珠玑,但信息却千丝万缕、错综复杂,需要用更多的文字来表述;但请您尽可能提炼思想的精髓,否则容易造成观者的阅读压力,适得其反。正如我们都希望改变世界,希望给别人带去光明,但更多时候我们只需要播下一颗种子,自然有微风吹拂,雨露滋养。恰如其分地表达观点,往往事半功倍。当您的内容到达这个限度时,或许已经不纯粹作用于演示,极大可能运用于阅读领域;无论是传播观点、知识分享还是汇报工作,内容的详尽固然重要,但请一定注意信息框架的清晰,这样才能使内容层次分明,页面简洁易读。如果您的内容确实非常重要又难以精简,也请使用分段处理,对内容进行简单的梳理和提炼,这样会使逻辑框架相对清晰。
根据图示的塑件零件图以及已确定的总体结构方案,设计本模具的冷却系统和排气系统并绘制冷却水道布置图。
练习
高粘度-高模温
3弯曲模具设计实例(PPT)
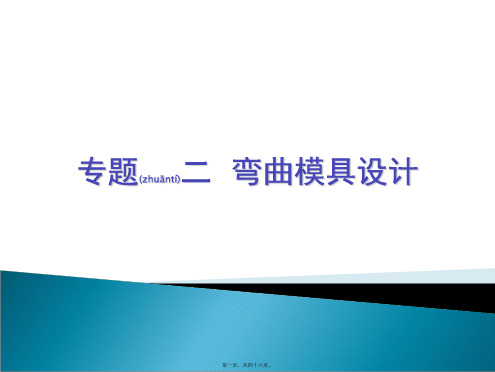
第二页,共四十六页。
2.1.1 弯曲变形过程分析 1. 弯曲变形过程:弯曲变形的含义、变形过程三阶段
、弯曲回弹、自由弯曲、矫正(jiǎozhèng)弯曲。 2. 弯曲变性特点:网格法、中性层 2.1.2 弯曲件质量分析
弯裂、回弹、偏移等
第三页,共四十六页。
2.1.3 弯曲件的工艺性:指弯曲件的结构形状、尺寸 、精度、材料及技术要求(yāoqiú)是否符合弯曲加工的工 艺要求(yāoqiú)。
第十九页,共四十六页。
2.2.1 弯曲模典型结构 模具设计本卷须知:a. 准确、可靠的定位,防止弯
曲中偏移;b. 弯曲结束(jiéshù)时能得到校正力;c. 成形后能方便、平安地取出;d. 考虑磨损,模具 留有修模余量。 弯曲模具分类:单工序模、连续弯曲模、复合弯曲模 和通用弯曲模。
第二十页,共四十六页。
第十页,共四十六页。
5. 增加工艺缺口、槽和工艺孔 a. 为提高精度,对于弯曲时圆角变形区侧面可以
产生畸变(jībiàn)的弯曲件,可以预先在折弯线的两端切 出工艺缺口或槽,以防止畸变(jībiàn)对弯曲件宽度尺寸 的影响。
第十一页,共四十六页。
b. 当工件局部边缘局部弯曲时,为防止弯曲局部受力 不均匀而产生变形和裂纹(liè wén),应于线切槽或冲工艺孔 。
弯曲半径较小、材料强度较大的弯曲件时,必须对
弯曲力进行计算。
a. 自由弯曲时的弯曲力
V形弯曲件 F自=0.6Kbt²σb/(r+t)
U形弯曲件 F自=0.7Kbt²σb/(r+t)
其中:b-弯曲件宽度;t-弯曲件厚度;r-内圆
角弯曲半径;
σb-弯曲材第十七料页,共四的十六页抗。 拉强度〔Mpa〕;K-
第9章UG注塑模设计实例——典型三板模
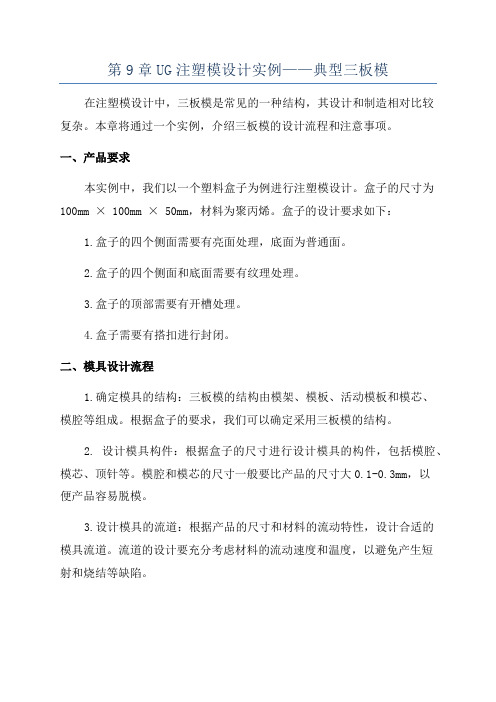
第9章UG注塑模设计实例——典型三板模在注塑模设计中,三板模是常见的一种结构,其设计和制造相对比较复杂。
本章将通过一个实例,介绍三板模的设计流程和注意事项。
一、产品要求本实例中,我们以一个塑料盒子为例进行注塑模设计。
盒子的尺寸为100mm × 100mm × 50mm,材料为聚丙烯。
盒子的设计要求如下:1.盒子的四个侧面需要有亮面处理,底面为普通面。
2.盒子的四个侧面和底面需要有纹理处理。
3.盒子的顶部需要有开槽处理。
4.盒子需要有搭扣进行封闭。
二、模具设计流程1.确定模具的结构:三板模的结构由模架、模板、活动模板和模芯、模腔等组成。
根据盒子的要求,我们可以确定采用三板模的结构。
2. 设计模具构件:根据盒子的尺寸进行设计模具的构件,包括模腔、模芯、顶针等。
模腔和模芯的尺寸一般要比产品的尺寸大0.1-0.3mm,以便产品容易脱模。
3.设计模具的流道:根据产品的尺寸和材料的流动特性,设计合适的模具流道。
流道的设计要充分考虑材料的流动速度和温度,以避免产生短射和烧结等缺陷。
4.设计模具的冷却系统:冷却系统的设计对模具的寿命和产品质量有着重要的影响。
在设计模具的冷却系统时,要尽可能将冷却水排布均匀,以提高冷却效果。
5.设计模具的顶出装置:根据产品的需求,设计合适的顶出装置。
在设计顶出装置时,要考虑产品的尺寸和材料的特性,以确保产品的成品率。
6.模具的装配和调试:根据设计图纸进行模具的装配和调试。
在调试过程中,要注意模具的开合性能和脱模性能,以确保模具的正常运行。
三、注意事项1.三板模设计中,模板的尺寸要比产品的尺寸大一定的空隙,以保证产品的成品尺寸。
2.模板的亮面处理和纹理处理需要在模具的组装和调试过程中完成。
3.流道的设计要尽可能简单和直接,以减少材料的回流和温度的损失。
4.冷却系统的设计要充分考虑到材料的流动路径和尺寸,以提高冷却效率。
5.模具的顶出装置设计要合理,以确保产品的成品率。
注塑模具典型结构与设计
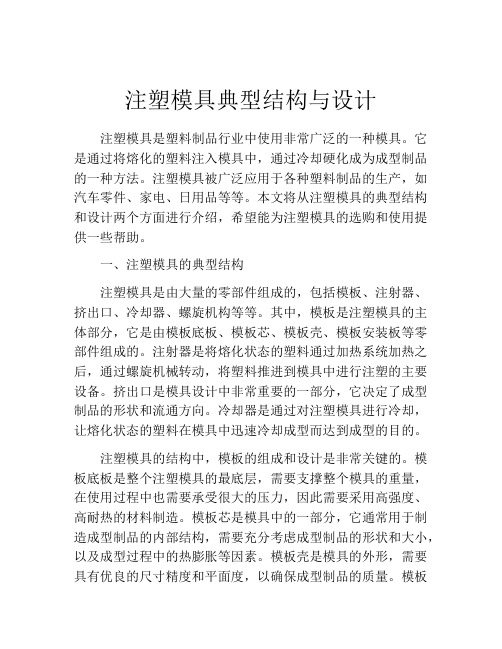
注塑模具典型结构与设计注塑模具是塑料制品行业中使用非常广泛的一种模具。
它是通过将熔化的塑料注入模具中,通过冷却硬化成为成型制品的一种方法。
注塑模具被广泛应用于各种塑料制品的生产,如汽车零件、家电、日用品等等。
本文将从注塑模具的典型结构和设计两个方面进行介绍,希望能为注塑模具的选购和使用提供一些帮助。
一、注塑模具的典型结构注塑模具是由大量的零部件组成的,包括模板、注射器、挤出口、冷却器、螺旋机构等等。
其中,模板是注塑模具的主体部分,它是由模板底板、模板芯、模板壳、模板安装板等零部件组成的。
注射器是将熔化状态的塑料通过加热系统加热之后,通过螺旋机械转动,将塑料推进到模具中进行注塑的主要设备。
挤出口是模具设计中非常重要的一部分,它决定了成型制品的形状和流通方向。
冷却器是通过对注塑模具进行冷却,让熔化状态的塑料在模具中迅速冷却成型而达到成型的目的。
注塑模具的结构中,模板的组成和设计是非常关键的。
模板底板是整个注塑模具的最底层,需要支撑整个模具的重量,在使用过程中也需要承受很大的压力,因此需要采用高强度、高耐热的材料制造。
模板芯是模具中的一部分,它通常用于制造成型制品的内部结构,需要充分考虑成型制品的形状和大小,以及成型过程中的热膨胀等因素。
模板壳是模具的外形,需要具有优良的尺寸精度和平面度,以确保成型制品的质量。
模板安装板则用来固定注塑模具,在使用过程中需要具有足够的稳定性和强度。
二、注塑模具的设计注塑模具的设计是非常复杂的,需要考虑很多因素,如成型制品的材料、形状、大小、特殊需求等等。
正确定义注塑模具的设计是确保成型制品的质量和提高生产效率的关键。
以下是一些注塑模具设计的基础要求:1、形状和尺寸:注塑模具的形状和尺寸需要完全符合成型制品的要求,同时需要符合成型机的规格和性能。
在注塑模具的设计中,需要确保成型制品的尺寸精确、表面平滑、无气泡、无毛刺等缺陷。
2、材料特性:在注塑模具的设计中,需要充分考虑成型制品的材料性质,如硬度、强度、耐磨性、耐腐蚀性等因素。
典型的挤出模具设计

典型的挤出模具设计挤出模具是一种常用于橡塑制品加工的模具,通过材料在模具中连续挤出,使其形成具有一定形状和尺寸的产品。
挤出模具广泛应用于塑料、橡胶、硅胶、硬质泡沫等各种材料的生产中,能够制造出各种管材、板材、条材、异型材等产品。
典型的挤出模具设计需要考虑材料特性、产品形状和尺寸等多个因素。
首先,挤出模具设计需要根据材料的特性来确定模具的结构和参数。
不同材料具有不同的流动性、熔体温度和粘度,对模具的设计产生不同的要求。
例如,一些材料具有较高的熔体温度和较高的黏度,需要采用加热设备和较大的流道截面积来确保材料能够顺利挤出。
而一些材料具有较低的流动性,需要增加收缩率和壁厚等参数来避免产品出现瑕疵。
因此,设计师需要了解材料的特性,合理确定模具的结构和参数。
其次,挤出模具设计需要考虑产品的形状和尺寸。
不同的产品形状对模具的设计产生不同的要求。
例如,圆形管材的模具需要设计圆形的出模口和流道,以保证挤出的产品具有良好的圆度和尺寸一致性。
而异型材的模具需要根据产品的形状和结构设计复杂的挤出口和流道,以确保产品能够顺利挤出,并且具有良好的表面质量和尺寸精度。
因此,设计师需要根据产品的形状和尺寸,合理确定模具的结构和参数。
再次,挤出模具设计需要考虑模具的制造和使用成本。
模具的制造和使用成本直接影响到产品的竞争力和市场占有率,因此设计师需要在满足产品形状和质量要求的前提下,尽量减少模具的制造和使用成本。
一方面,可以通过合理设计模具的结构和参数,减少模具的复杂度和制造难度。
另一方面,可以选择合适的材料和加工工艺,提高模具的耐磨性和使用寿命,降低维护和更换的频率。
因此,设计师需要综合考虑多个因素,合理选择模具的结构、材料和加工工艺,以实现最佳的经济效益。
最后,挤出模具设计还需要考虑产品的生产效率和质量稳定性。
生产效率和质量稳定性是企业提高竞争力和降低成本的关键。
模具的设计应充分考虑产品的生产工艺和生产效率,提高生产效率和降低不良品率。
模具设计PPT课件

2021/3/9
20
第三章 模具设计
抽取模具元件
❖ 创建完模具体积块后,可以从工件抽取它们 以产生模具元件
2021/3/9
21
第三章 模具设计
铸模
❖ 可以通过浇道、流道和浇口来模拟填充模具 型腔,从而创建铸模,如图所示分别是参照 零件和铸模,铸模的上面有浇注系统。
❖ 铸模可以用于检查前面设计的完整性和正确 性,如果出现不能生成铸模文件的现象,极 有可能是先前的模具设计有差错或者参照零 件有几何交错的现象,应当向前检查。
❖ 6. 提取模具体积块以生成模具元件。提取完毕后模具元件即 成为功能齐全的Pro/ENGINEER零件,它可在零件模式中调 出可在绘图中使用也可用Pro/NC进行加工
❖ 7. 创建表示已填充模具型腔的模制件系统将根据减去提取部 分后工件中剩余的体积块来自动创建模制件(铸模)
❖ 8. 定义模具开口的步骤在每步中检查与静态零件的干涉必要 时修改模具元件
❖ 对于塑料模具,浇注系统一般由主流道、分流道、 冷料井和浇口组成
❖ 浇注系统的设计方法 :使用【实体】特征中切割材
料方式来建立浇注系统,; 或直接利用模具特征中
的【流道】特征建立浇注系统,利用流道特征可以 快速创建标准流道。
2021/3/9
25
第三章 模具设计
侧浇口
❖ 侧浇口
2021/3/9
26
2021/3/9
4
第三章 模具设计
❖ 3.1.2 创建模具文件
2021/3/9
5
第三章 模具设计
3.2 加载参照模型
❖ 根据型腔数目的多少,模具可以分为单腔模 具和多腔模具
2021/3/9
6
第三章 模具设计
基于AutoCAD的典型注塑模具设计
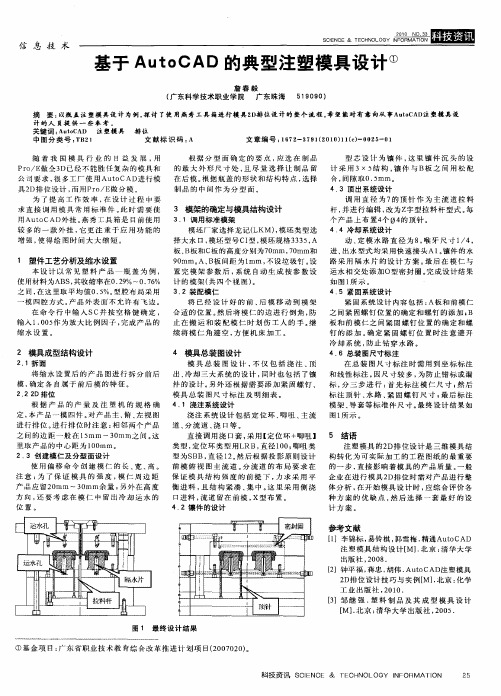
根 据 产 品 的 产 量 及 注 塑 机 的 规 格 确 4. 浇注 系统设 计 1 定 , 产 品 一 模 四件 。 产 品主 、 、 本 对 俯 左视 图 浇 注 系 统 设 计 包 括 定 位 环 、 咀 、 流 唧 主
模架 、 套 等 标 准 件 尺 寸 。 终 设 计 结 果 如 导 最
计 的 人 员提 供 一 些 参 考 。 关 键 词 : tC 注 塑模 具 排 位 Auo AD
中图分 类号 : B2 T 1
文 献标 识码 : A
文 章编 号 : 7 -3 9 ( 0 0 1 () 0 5 0 1 7 l2 1 ) 1c一0 2 - 1 62
随 着 我 国 模具 行 业 的 日益 发 展 , 用
计 采 用 3×5结 构 , 件 与 B板 之 间 用 松 配 镶 间隙 取0. mm。 5 在 后 模 。 据 瓶 盖 的形 状 和 结构 特 点 , 择 合 , 根 选 制 品 的 中 间 作 为 分 型面 。 4 3 顶 出系统 设计 .
为 了提 高 工 作 效 率 , 设 计 过 程 中 要 在 调 用 直 径 为 7 顶 针 作 为 主 流 道 拉 料 的 求 直 接 调 用 模 具 常 用 标 准 件 。 时 需 要 使 3 模架 的确定与模具结构 设计 此 杆 , 进 行 编辑 , 为 Z 型拉 料 杆 型 式 。 并 改 字 每 用 Aut oCAD外 挂 。 秀 工具 箱 是 目前 使 用 3. 燕 1调 用标 准模 架 个产 品上 布 置4 0 的 顶 针 。 个 4 较 多的 一 款 外 挂 , 更 注 重 于 应 用 功 能 的 它 模坯 厂 家 选择 龙 记 ( LKM) 模坯 类 型 选 4 , 4冷 却 系统设 计 增 强 , 得 绘 图时 间 大 大 缩 短 。 使 择 大 水 口, 模坯 型 号 C 型 , I 模坯 规 格 3 3 , 3 5A 动 、 模 水 路 直 径 为 8 喉 牙 尺 寸 l 4, 定 , /
冷冲压模具设计与制造实例

例8.2.1冲裁模设计与制造实例工件名称:手柄工件简图:如图8.2.1所示。
生产批量:中批量材料:Q235-A钢材料厚度:1.2mm1.冲压件工艺性分析此工件只有落料和冲孔两个工序。
材料为Q235-A钢,具有良好的冲压性能,适合冲裁。
工件结构相对简单,有一个φ8mm的孔和5个φ5mm的孔;孔与孔、孔与边缘之间的距离也满足要求,最小壁厚为3.5mm(大端4个φ5mm的孔与φ8mm孔、φ5mm的孔与R16mm外圆之间的壁厚)。
工件的尺寸全部为自由公差,可看作IT14级,尺寸精度较低,普通冲裁完全能满足要求。
2.冲压工艺方案的确定该工件包括落料、冲孔两个基本工序,可有以下三种工艺方案:方案一:先落料,后冲孔。
采用单工序模生产。
方案二:落料-冲孔复合冲压。
采用复合模生产。
方案三:冲孔-落料级进冲压。
采用级进模生产。
方案一模具结构简单,但需两道工序两副模具,成本高而生产效率低,难以满足中批量生产要求。
方案二只需一副模具,工件的精度及生产效率都较高,但工件最小壁厚3.5mm接近凸凹模许用最小壁厚3.2mm,模具强度较差,制造难度大,并且冲压后成品件留在模具上,在清理模具上的物料时会影响冲压速度,操作不方便。
方案三也只需一副模具,生产效率高,操作方便,工件精度也能满足要求。
通过对上述三种方案的分析比较,该件的冲压生产采用方案三为佳。
3.主要设计计算(1)排样方式的确定及其计算设计级进模,首先要设计条料排样图。
手柄的形状具有一头大一头小的特点,直排时材料利用率低,应采用直对排,如图8.2.2所示的排样方法,设计成隔位冲压,可显著地减少废料。
隔位冲压就是将第一遍冲压以后的条料水平方向旋转180°,再冲第二遍,在第一次冲裁的间隔中冲裁出第二部分工件。
搭边值取2.5mm和3.5mm,条料宽度为135mm,步距离为53 mm,一个步距的材料利用率为78%(计算见表8.2.1)。
查板材标准,宜选950mm×1500mm的钢板,每张钢板可剪裁为7张条料(135mm×1500mm),每张条料可冲56个工件,故每张钢板的材料利用率为76%。
冲压模具结构设计200例
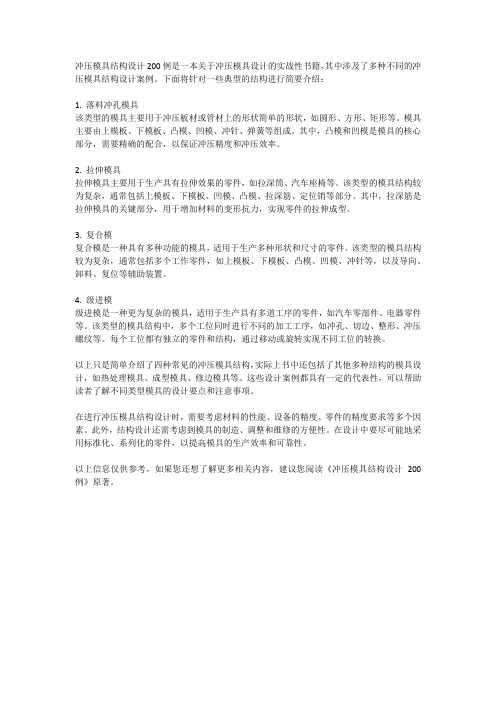
冲压模具结构设计200例是一本关于冲压模具设计的实战性书籍,其中涉及了多种不同的冲压模具结构设计案例。
下面将针对一些典型的结构进行简要介绍:1. 落料冲孔模具该类型的模具主要用于冲压板材或管材上的形状简单的形状,如圆形、方形、矩形等。
模具主要由上模板、下模板、凸模、凹模、冲针、弹簧等组成。
其中,凸模和凹模是模具的核心部分,需要精确的配合,以保证冲压精度和冲压效率。
2. 拉伸模具拉伸模具主要用于生产具有拉伸效果的零件,如拉深筒、汽车座椅等。
该类型的模具结构较为复杂,通常包括上模板、下模板、凹模、凸模、拉深筋、定位销等部分。
其中,拉深筋是拉伸模具的关键部分,用于增加材料的变形抗力,实现零件的拉伸成型。
3. 复合模复合模是一种具有多种功能的模具,适用于生产多种形状和尺寸的零件。
该类型的模具结构较为复杂,通常包括多个工作零件,如上模板、下模板、凸模、凹模、冲针等,以及导向、卸料、复位等辅助装置。
4. 级进模级进模是一种更为复杂的模具,适用于生产具有多道工序的零件,如汽车零部件、电器零件等。
该类型的模具结构中,多个工位同时进行不同的加工工序,如冲孔、切边、整形、冲压螺纹等。
每个工位都有独立的零件和结构,通过移动或旋转实现不同工位的转换。
以上只是简单介绍了四种常见的冲压模具结构,实际上书中还包括了其他多种结构的模具设计,如热处理模具、成型模具、修边模具等。
这些设计案例都具有一定的代表性,可以帮助读者了解不同类型模具的设计要点和注意事项。
在进行冲压模具结构设计时,需要考虑材料的性能、设备的精度、零件的精度要求等多个因素。
此外,结构设计还需考虑到模具的制造、调整和维修的方便性。
在设计中要尽可能地采用标准化、系列化的零件,以提高模具的生产效率和可靠性。
以上信息仅供参考,如果您还想了解更多相关内容,建议您阅读《冲压模具结构设计200例》原著。
babyplast-小型注塑机模具设计指导
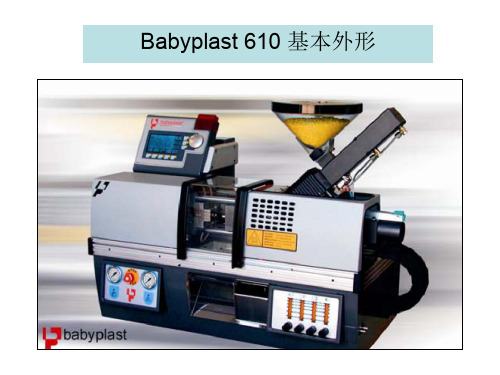
4.2.3, 针板导套型号:EGBH8-10,punch,长度与标准模板尺寸 不匹配,需要出图返工长度。
4.2.4, 注意顶出干涉
顶针板顶出时,直径30的圆内不能 有物体高出针板表面
• 4.3 当设计前后模仁底面都加有垫板时,必须加管边定位(见附图1) • 4.4 水路设计尽必须满足下面要求(见附图1,附图2)
1/8NPT
水冷却时连接部 件
Ace定制水嘴
1
2
普通水管 4
3 Dme快速接头
接JP251 快速接头
• B: 高温模具冷却,采用油冷,连接方式见附图
油冷时连接部件
Ace定制水嘴
1 耐高温油管
7 5
1/16NPT 1/8NPT油嘴接头 ace定制
高 温水油管一头是1/8NPT内牙封油, 另一头是1/4NPT内牙封油
一般模具冷却采用水冷连接方式见附图连接模具螺牙116npt18npt接jp251快速接头水冷却时连接部高温模具冷却采用油冷连接方式见附图油冷时连接部件ace定制水嘴耐高温油管116npt18npt18npt油嘴接头ace定制配件1是油冷和水冷共用件耐高温水油管一头是18npt内牙封油另一头是14npt内牙封油46圆形顶针底板和面板防呆设计见附图4为防止顶针板装错方向3d设计时要求设计人员将平工在top面
板。(隔热板统一为3mm,供应商MISUMI)
• 4.6 圆形顶针底板和面板防呆设计(见附图4)
为防止顶针板装错 方向,3d设计时, 要求设计人员将平 位画好。平位槽加 工在top面。
在TOP面磨下出 2MM的平位
附图4
5,Babyplast 几种典型模具结构设计范例
.5.1司筒顶出结构设计
在顶针底板后增加垫板和限位套筒,但必须要满足50这尺寸和足够的顶出行程。
模具设计典型T型件冲压模具设计
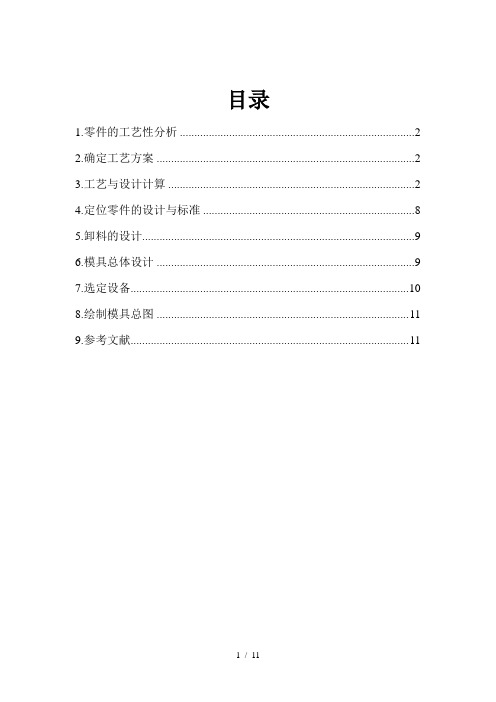
目录1.零件的工艺性分析 (2)2.确定工艺方案 (2)3.工艺与设计计算 (2)4.定位零件的设计与标准 (8)5.卸料的设计 (9)6.模具总体设计 (9)7.选定设备 (10)8.绘制模具总图 (11)9.参考文献 (11)典型T 型件冲压模具设计工件为垫片,矩形薄板结构。
材料为Q235,厚度为2,年产量为10万件,上下表面为非加工面,不得有毛刺缺陷等。
1.零件的工艺性分析。
零件尺寸标注完整、清晰,IT 等级最高为11级,利用普通冲裁方式可达到图样要求。
由于该件外形简单,形状规则,适于冲裁加工。
材料为Q235钢,b σ=450MPa 。
2.确定工艺方案零件属于大批量生产,工艺性较好。
但是不宜采用复合模具。
如果采用落料后再冲孔,则效率太低,而且质量不易保证。
由于该件的生产批量比较大,因此确定该零件的工艺方案为冲孔—落料级进模,考虑到凹模刃口强度,中间还留一空步。
排样如图:图13.工艺与设计计算(1)冲裁力的计算根据 τLt F =0L —冲裁件周长(mm ); t —材料厚度(mm ); τ—材料抗剪强度(MPa ); 考虑到实际因素影响实际冲裁力增大取1.3倍则b Lt Lt F F στ≈==3.13.10式中:F —最大可能冲裁力;b σ—材料抗拉强度因此 冲孔力F 1=1.3×92×2×450=107640N落料力F 2=1.3×244×2×450=142740N 卸料力、推件力根据经验公式计算:(2)卸料力的计算F F 卸卸K =式中:卸F —卸料力(N );卸K —卸料力系数(查表取0.05);F —冲裁力(N )(为冲裁力和切断力的总和); 故卸料力为卸F =(53820+142740)×0.05=9828N(3)推件力的计算F F 推推K =n式中: 推F —推件力(N );n —梗塞在凹模内料的个数,n=h/t ,h 为凹模刃壁垂直部分高度(mm ),t 为材料厚度; 推K —推件力系数(查表取0.050);F —冲裁力(N ); 因此冲孔部分推件力:n 11推推K =F F =107640×0.050×8÷2=21528N切断部分推件力:n 22推推K =F F =142740×0.050×8÷2=28548N所以2121推推卸总F F F F F F ++++==310284N(4)压力中心的计算查表2-18确定搭边值,矩形件 边长50l >或圆角t 2r ≤,取工件间1a =2,沿边a=2.2。