液压缸的设计计算..
液压缸设计计算范文
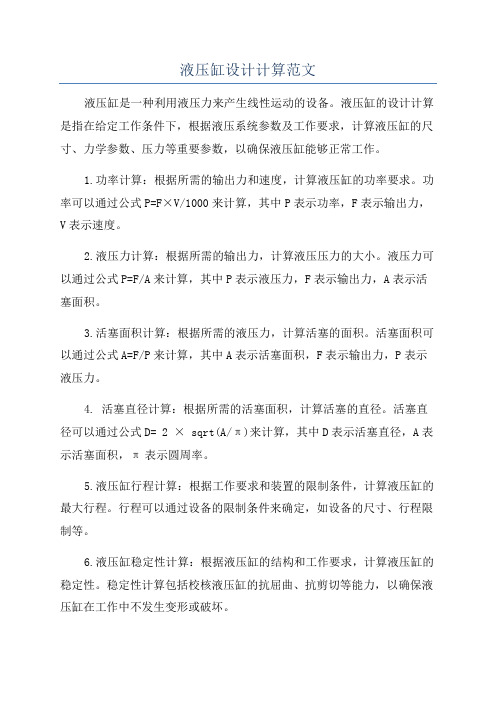
液压缸设计计算范文液压缸是一种利用液压力来产生线性运动的设备。
液压缸的设计计算是指在给定工作条件下,根据液压系统参数及工作要求,计算液压缸的尺寸、力学参数、压力等重要参数,以确保液压缸能够正常工作。
1.功率计算:根据所需的输出力和速度,计算液压缸的功率要求。
功率可以通过公式P=F×V/1000来计算,其中P表示功率,F表示输出力,V表示速度。
2.液压力计算:根据所需的输出力,计算液压压力的大小。
液压力可以通过公式P=F/A来计算,其中P表示液压力,F表示输出力,A表示活塞面积。
3.活塞面积计算:根据所需的液压力,计算活塞的面积。
活塞面积可以通过公式A=F/P来计算,其中A表示活塞面积,F表示输出力,P表示液压力。
4. 活塞直径计算:根据所需的活塞面积,计算活塞的直径。
活塞直径可以通过公式D= 2 × sqrt(A/π)来计算,其中D表示活塞直径,A表示活塞面积,π表示圆周率。
5.液压缸行程计算:根据工作要求和装置的限制条件,计算液压缸的最大行程。
行程可以通过设备的限制条件来确定,如设备的尺寸、行程限制等。
6.液压缸稳定性计算:根据液压缸的结构和工作要求,计算液压缸的稳定性。
稳定性计算包括校核液压缸的抗屈曲、抗剪切等能力,以确保液压缸在工作中不发生变形或破坏。
7.寿命计算:根据液压缸的设计参数和工作条件,计算液压缸的寿命。
寿命计算包括根据液压缸的设计寿命和使用条件,计算液压缸的可靠性和寿命预测。
在进行液压缸设计计算时,需要考虑以下几个重要因素:1.工作条件:包括工作压力、工作温度、介质类型等。
2.力学要求:包括输出力、速度、行程等。
3.设备限制:包括装置的尺寸、行程限制等。
4.安全要求:包括液压缸的稳定性、可靠性等。
在进行液压缸设计计算时,需要根据实际情况进行具体分析。
一般来说,液压缸的设计计算是一个复杂的工作,需要涉及力学、流体力学、材料力学等多个学科的知识,并以此为基础进行具体计算。
液压缸计算公式
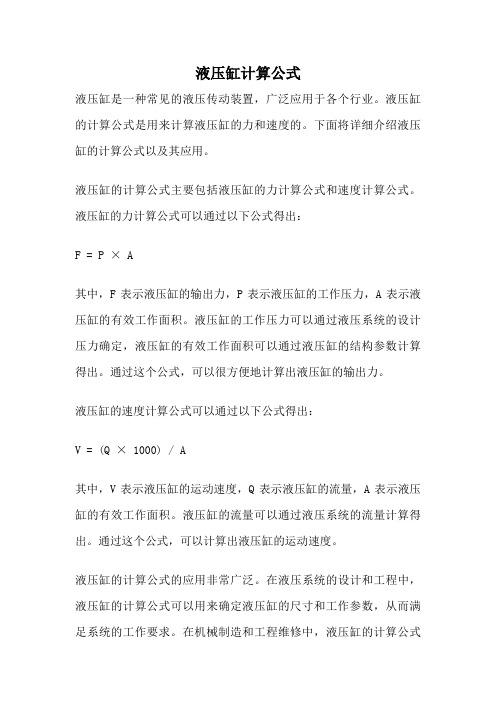
液压缸计算公式液压缸是一种常见的液压传动装置,广泛应用于各个行业。
液压缸的计算公式是用来计算液压缸的力和速度的。
下面将详细介绍液压缸的计算公式以及其应用。
液压缸的计算公式主要包括液压缸的力计算公式和速度计算公式。
液压缸的力计算公式可以通过以下公式得出:F = P × A其中,F表示液压缸的输出力,P表示液压缸的工作压力,A表示液压缸的有效工作面积。
液压缸的工作压力可以通过液压系统的设计压力确定,液压缸的有效工作面积可以通过液压缸的结构参数计算得出。
通过这个公式,可以很方便地计算出液压缸的输出力。
液压缸的速度计算公式可以通过以下公式得出:V = (Q × 1000) / A其中,V表示液压缸的运动速度,Q表示液压缸的流量,A表示液压缸的有效工作面积。
液压缸的流量可以通过液压系统的流量计算得出。
通过这个公式,可以计算出液压缸的运动速度。
液压缸的计算公式的应用非常广泛。
在液压系统的设计和工程中,液压缸的计算公式可以用来确定液压缸的尺寸和工作参数,从而满足系统的工作要求。
在机械制造和工程维修中,液压缸的计算公式可以用来评估液压缸的工作性能和故障排除。
液压缸的计算公式还可以用来优化液压系统的设计。
通过合理选择液压缸的尺寸和工作参数,可以提高液压系统的效率和稳定性。
同时,液压缸的计算公式也可以用来对液压系统进行性能测试和评估,为系统的优化提供依据。
液压缸的计算公式是液压系统设计和工程应用中的重要工具。
通过合理应用这些公式,可以方便地计算液压缸的力和速度,从而满足系统的工作要求。
液压缸的计算公式的应用范围广泛,对于液压系统的设计、制造和维修都具有重要意义。
希望本文的介绍对读者有所帮助。
液压缸的设计计算
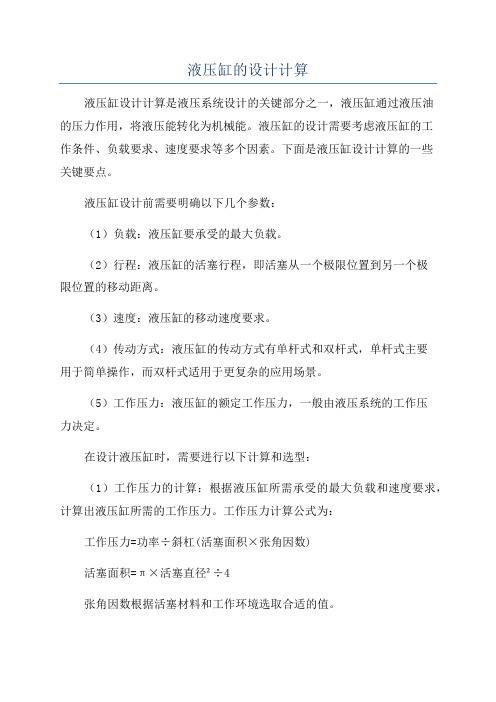
液压缸的设计计算液压缸设计计算是液压系统设计的关键部分之一,液压缸通过液压油的压力作用,将液压能转化为机械能。
液压缸的设计需要考虑液压缸的工作条件、负载要求、速度要求等多个因素。
下面是液压缸设计计算的一些关键要点。
液压缸设计前需要明确以下几个参数:(1)负载:液压缸要承受的最大负载。
(2)行程:液压缸的活塞行程,即活塞从一个极限位置到另一个极限位置的移动距离。
(3)速度:液压缸的移动速度要求。
(4)传动方式:液压缸的传动方式有单杆式和双杆式,单杆式主要用于简单操作,而双杆式适用于更复杂的应用场景。
(5)工作压力:液压缸的额定工作压力,一般由液压系统的工作压力决定。
在设计液压缸时,需要进行以下计算和选型:(1)工作压力的计算:根据液压缸所需承受的最大负载和速度要求,计算出液压缸所需的工作压力。
工作压力计算公式为:工作压力=功率÷斜杠(活塞面积×张角因数)活塞面积=π×活塞直径²÷4张角因数根据活塞材料和工作环境选取合适的值。
(2)液压缸尺寸的计算:根据所需承受的最大负载和工作压力,计算出液压缸的尺寸。
液压缸尺寸计算公式为:活塞面积=承受的负载÷工作压力活塞直径=(4×活塞面积÷π)^0.5根据液压缸的类型和具体要求,还需要进行一些其他计算,如活塞杆直径、带式液压缸的带宽和带材厚度的计算等。
(3)液压缸速度的计算:根据液压缸的移动速度要求,结合液压缸的流量特性和阀门的流量系数等参数,计算出所需的液压缸速度。
液压缸速度计算公式为:流量=活塞面积×速度速度=流量÷活塞面积其中,流量需要根据阀门流量系数、压差等因素计算得出。
为了确保液压缸的工作效果和可靠性,设计时还需要考虑液压缸的密封性、液压阀的选型、活塞材料的选择和润滑等方面的计算和选型。
总结起来,液压缸的设计计算包括工作压力的计算、液压缸尺寸的计算以及液压缸速度的计算等。
液压油缸压力计算公式液压油缸设计计算公式
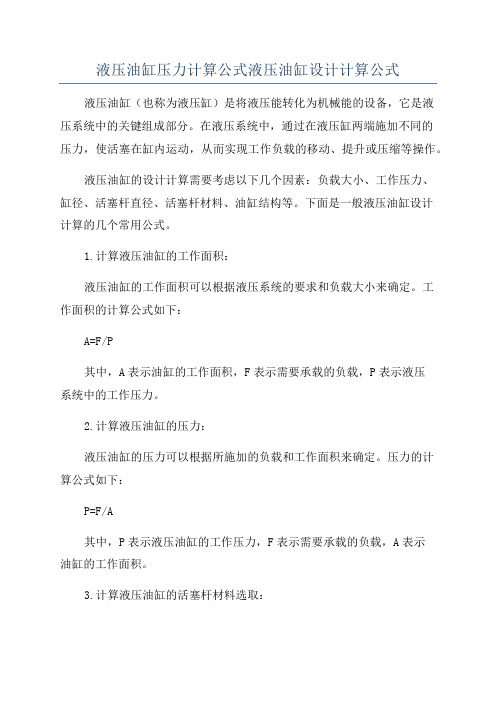
液压油缸压力计算公式液压油缸设计计算公式液压油缸(也称为液压缸)是将液压能转化为机械能的设备,它是液压系统中的关键组成部分。
在液压系统中,通过在液压缸两端施加不同的压力,使活塞在缸内运动,从而实现工作负载的移动、提升或压缩等操作。
液压油缸的设计计算需要考虑以下几个因素:负载大小、工作压力、缸径、活塞杆直径、活塞杆材料、油缸结构等。
下面是一般液压油缸设计计算的几个常用公式。
1.计算液压油缸的工作面积:液压油缸的工作面积可以根据液压系统的要求和负载大小来确定。
工作面积的计算公式如下:A=F/P其中,A表示油缸的工作面积,F表示需要承载的负载,P表示液压系统中的工作压力。
2.计算液压油缸的压力:液压油缸的压力可以根据所施加的负载和工作面积来确定。
压力的计算公式如下:P=F/A其中,P表示液压油缸的工作压力,F表示需要承载的负载,A表示油缸的工作面积。
3.计算液压油缸的活塞杆材料选取:液压油缸的活塞杆材料需要根据所承载负载和工作压力来选择,以满足强度和刚度的要求。
常见的活塞杆材料有碳钢、不锈钢、铬钼合金钢等。
一般用弯曲应力公式进行计算,考虑到材料的抗弯刚度,活塞杆的直径可以根据以下公式得到:d=((32*M*L)/(π*σ))^(1/3)其中,d表示活塞杆的直径,M表示活塞杆所承受的最大弯矩,L表示活塞杆的长度,σ表示选定材料的抗弯应力。
4.计算液压油缸的活塞直径:液压油缸的活塞直径可以通过活塞面积和活塞杆直径计算得到。
计算公式如下:D=(4*A)/(π*d^2)其中,D表示液压油缸的活塞直径,A表示油缸的工作面积,d表示活塞杆的直径。
5.计算液压油缸的油缸容积:液压油缸的油缸容积可以通过活塞面积和活塞行程来计算。
计算公式如下:V=A*l其中,V表示油缸的容积,A表示油缸的工作面积,l表示活塞的行程。
通过上述公式的计算,可以得到液压油缸的设计参数,从而满足液压系统的工作要求。
需要注意的是,在实际设计过程中,还应该考虑其他因素,如密封结构、摩擦损失、液压系统的动态响应等,以确保液压油缸的安全可靠运行。
液压的缸设计计算
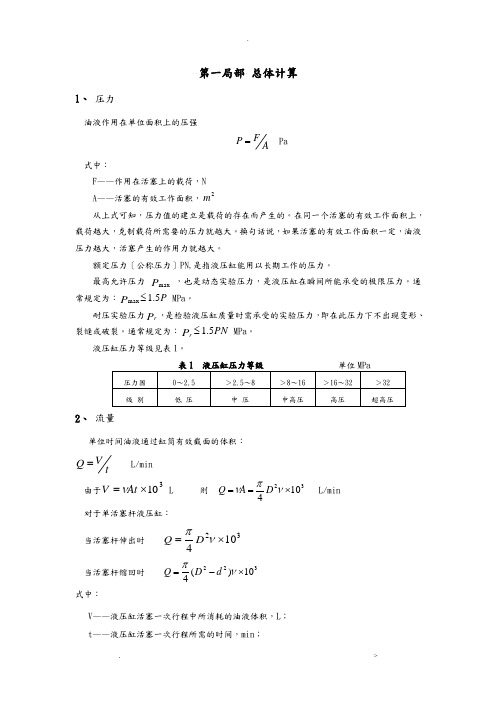
第一局部 总体计算1、 压力油液作用在单位面积上的压强AFP = Pa式中:F ——作用在活塞上的载荷,N A ——活塞的有效工作面积,2m从上式可知,压力值的建立是载荷的存在而产生的。
在同一个活塞的有效工作面积上,载荷越大,克制载荷所需要的压力就越大。
换句话说,如果活塞的有效工作面积一定,油液压力越大,活塞产生的作用力就越大。
额定压力〔公称压力〕PN,是指液压缸能用以长期工作的压力。
最高允许压力 P max ,也是动态实验压力,是液压缸在瞬间所能承受的极限压力。
通常规定为:P P 5.1max ≤ MPa 。
耐压实验压力P r ,是检验液压缸质量时需承受的实验压力,即在此压力下不出现变形、裂缝或破裂。
通常规定为:PN P r 5.1≤ MPa 。
液压缸压力等级见表1。
2、 流量单位时间油液通过缸筒有效截面的体积:tVQ = L/min由于310⨯=At Vν L 则 32104⨯==νπνD A Q L/min对于单活塞杆液压缸: 当活塞杆伸出时32104⨯=νπD Q当活塞杆缩回时 32210)(4⨯-=νπd D Q式中:V ——液压缸活塞一次行程中所消耗的油液体积,L ; t ——液压缸活塞一次行程所需的时间,min ;D ——液压缸缸径,m ; d ——活塞杆直径,m ; ν——活塞运动速度,m/min 。
3、速比液压缸活塞往复运动时的速度之比: 式中:1v ——活塞杆的伸出速度,m/min ; 2v ——活塞杆的缩回速度,m/min ;D ——液压缸缸径,m ; d ——活塞杆直径,m 。
计算速比主要是为了确定活塞杆的直径和是否设置缓冲装置。
速比不宜过大或过小,以免产生过大的背压或造成因活塞杆太细导致稳定性不好。
4、液压缸的理论推力和拉力活塞杆伸出时的理推力: 6261110410⨯=⨯=p D p A F πN活塞杆缩回时的理论拉力: 62262210)(410⨯-=⨯=p d D p F F πN式中:1A ——活塞无杆腔有效面积,2m ; 2A ——活塞有杆腔有效面积,2m ;P ——工作压力,MPa ; D ——液压缸缸径,m ; d ——活塞杆直径,m 。
液压缸的设计和计算
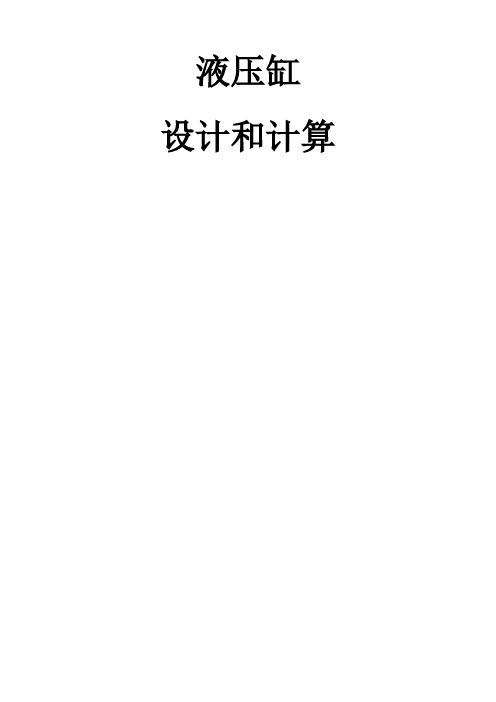
液压缸设计和计算液压缸的设计和计算液压缸的设计是整个液压系统设计中的一部分,它是在对整个系统进行了工况分析,编制了负载图,选定了工作压力之后进行的; 一、设计依据:1了解和掌握液压缸在机械上的用途和动作要求;2了解液压缸的工作条件;3了解外部负载情况;4了解液压缸的最大行程,运动速度或时间,安装空间所允许的外形尺寸以及缸本身的动作;5设计已知液压系统的液压缸,应了解液压系统中液压泵的工作压力和流量的大小、管路的通径和布置情况、各液压阀的控制情况;6了解有关国家标准、技术规范及参考资料;二、设计原则:1保证缸运动的出力、速度和行程;2保证刚没各零部件有足够的强度、刚度和耐用性;3保证以上两个条件的前提下,尽量减小缸的外形尺寸;4在保证刚性能的前提下,尽量减少零件数量,简化结构;5要尽量避免缸承受横向负载,活塞杆工作时最好承受拉力,以免产生纵向弯曲;6缸的安装形式和活塞杆头部与外部负载的连接形式要合理,尽量减小活塞杆伸出后的有效安装长度,增加缸的稳定性;三、设计步骤:1根据设计依据,初步确定设计档案,会同有关人员进行技术经济分析;2对缸进行受力分析,选择液压缸的类型和各部分结构形式;3确定液压缸的工作参数和结构尺寸;4结构强度、刚度的计算和校核;5根据运动速度、工作出力和活塞直径,确定泵的压力和流量;6审定全部设计计算资料,进行修改补充;7导向、密封、防尘、排气和缓冲等装置的设计;8绘制装配图、零件图、编写设计说明书;四、液压缸设计中应注意的问题液压缸的设计和使用正确与否,直接影响到它的性能和是否易于发生故障;所以,在设计液压缸时,必须注意以下几点:1、尽量使液压缸的活塞杆在受拉状态下承受最大负载,或在受压状态下具有良好的稳定性;2、考虑液压缸行程终了处的制动问题和液压缸的排气问题;3、正确确定液压缸的安装、固定方式;4、液压缸各部分的结构需根据推荐的结构形式和设计标准进行设计,尽可能做到结构简单、紧凑、加工、装配和维修方便;5、在保证能满足运动行程和负载力的条件下,应尽可能地缩小液压缸的轮廓尺寸;6、要保证密封可靠,防尘良好;五、计算液压缸的结构尺寸1、缸筒内径D 根据负载的大小来选定工作压力或往返运动速度比,求得液压缸的有效工作面积,从而得到缸筒内径D,再从GB2348-80标准中选取最近的标准值作为所设计的缸筒内径;液压缸的有效工作面积为…… 24D p F A π== 以无杆腔作工作腔时………… p FD π4=以有杆腔作工作腔时………… 24d p F D +=π 2、活塞杆外径d 通常先从满足速度或速度比的要求来选择,然后再校核其结构强度和稳定性;若速度比为v λ,则 vv Dd λλ1-= 也可根据活塞杆受力状况来确定:受拉力作用时,d =~; 受压力作用时,则有3、缸筒长度L 缸筒长度L 由最大工作行程长度加上各种结构需要来确定,即:l —— 活塞的最大工作行程;B —— 活塞宽度,一般为~1D ;A —— 活塞杆导向长度,取~D ;M —— 活塞杆密封长度,由密封方式定;C —— 其他长度; 注意:从制造工艺考虑,缸筒的长度最好不超过其内径的20倍;六、强度校核对液压缸的缸筒壁厚δ、活塞杆直径d和缸盖固定螺栓的直径,在高压系统中必须进行强度校核;1、缸筒壁厚校核δ 缸筒壁厚校核分薄壁和厚壁两种情况;当D/δ≥10时为薄壁,壁厚按下式进行校核:δ≥δδδ2[δ]当D/δ<10时为厚壁,壁厚按下式进行校核:δ≥δ2(√[δ]+0.4δδ[δ]−1.3δδ−1)pt ——缸筒试验压力,随缸的额定压力的不同取不同的值D ——缸筒内径σ——缸筒材料许用应力2、活塞杆直径校核活塞杆的直径d按下式进行校核:3、液压缸盖固定螺栓直径校核液压缸盖固定螺栓直径按下式计算:F ——液压缸负载k ——螺纹拧紧系数~Z ——固定螺栓个数σ——螺栓材料许用应力七、液压缸稳定性校核活塞杆轴向受压时,其直径d一般不小于长度L的1/15;当L/d≥15时,须进行稳定性校核,应使活塞杆承受的力F不能超过使它保持稳定工作所允许的临界负载Fk ,以免发生纵向弯曲,破坏液压缸的正常工作;Fk 的值与活塞杆材料性质、截面形状、直径和长度以及缸的安装方式等因素有关,验算可按材料力学有关公式进行;• 当活塞杆细长比 21/ψψ>k r l 时,则• 当活塞杆细长比21/ψψ≤k r l 且120~2021=ψψl -- 安装长度,其值与安装方式有关;Ψ1 -- 柔性系数,对钢取Ψ1=85;Ψ2 -- 末端系数,由液压缸支承方式决定;E -- 活塞杆材料的弹性模量,对钢取E=× 1011Pa ;J -- 活塞杆横截面惯性矩;A -- 活塞杆横截面面积;f -- 由材料强度决定的实验数值,对钢取f=×108 N /m2; α--系数,对钢取α=1/5000;rk --活塞杆横截面的最小回转半径;八、缓冲计算液压缸的缓冲计算主要是估计缓冲时缸中出现的最大冲击压力,以便用来校核缸筒强度、制动距离是否符合要求;液压缸在缓冲时,缓冲腔内产生的液压能E 1和工作部件产生的机械能E 2分别为:当E 1=E 2时,工作部件的机械能全部被缓冲腔液体所吸收,则有九、油缸的试验1.油缸试验压力,低于16MPa乘以工作压力的,高于16乘以工作压力的;2.最低启动压力:是指液压缸在无负载状态下的最低工作压力,它是反映液压缸零件制造和装配精度以及密封摩擦力大小的综合指标;3.最低稳定速度:是指液压缸在满负荷运动时没有爬行现象的最低运动速度,它没有统一指标,承担不同工作的液压缸,对最低稳定速度要求也不相同;4.内部泄漏:液压缸内部泄漏会降低容积效率,加剧油液的温升,影响液压缸的定位精度,使液压缸不能准确地、稳定地停在缸的某一位置;。
常用液压设计计算公式
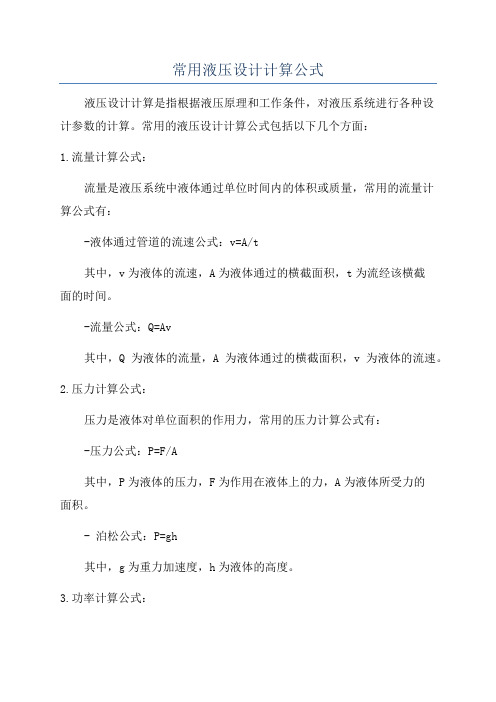
常用液压设计计算公式液压设计计算是指根据液压原理和工作条件,对液压系统进行各种设计参数的计算。
常用的液压设计计算公式包括以下几个方面:1.流量计算公式:流量是液压系统中液体通过单位时间内的体积或质量,常用的流量计算公式有:-液体通过管道的流速公式:v=A/t其中,v为液体的流速,A为液体通过的横截面积,t为流经该横截面的时间。
-流量公式:Q=Av其中,Q为液体的流量,A为液体通过的横截面积,v为液体的流速。
2.压力计算公式:压力是液体对单位面积的作用力,常用的压力计算公式有:-压力公式:P=F/A其中,P为液体的压力,F为作用在液体上的力,A为液体所受力的面积。
- 泊松公式:P=gh其中,g为重力加速度,h为液体的高度。
3.功率计算公式:功率是液压系统中单位时间内产生或消耗的能量,常用的功率计算公式有:-功率公式:P=Q×P其中,P为液体的功率,Q为液体的流量,P为液体的压力。
-功率公式:P=F×v其中,P为液体的功率,F为作用在液体上的力,v为液体的流速。
4.流速计算公式:流速是单位时间内液体通过管道的速度,常用的流速计算公式有:-流速公式:v=Q/A其中,v为液体的流速,Q为液体的流量,A为液体通过的横截面积。
- 流速公式:v=√(2gh)其中,v为液体的流速,g为重力加速度,h为液体的高度。
5.根据功率计算液压缸的力和速度:-液压缸力的计算公式:F=P/A其中,F为液压缸的力,P为液体的压力,A为液压缸的有效工作面积。
-液压缸速度的计算公式:v=Q/A其中,v为液压缸的速度,Q为液体的流量,A为液压缸的有效工作面积。
以上是液压设计常用的一些计算公式,根据具体液压系统的工作条件和设计要求,可以选择适合的公式进行计算。
在实际设计中,还需要考虑液体的黏度、泄漏、阻力等因素对计算结果的影响,综合考虑才能得到更精确的设计结果。
液压缸的计算范文
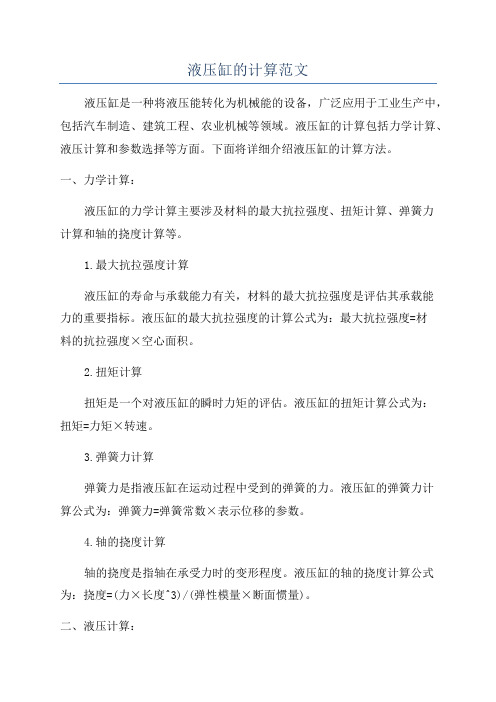
液压缸的计算范文液压缸是一种将液压能转化为机械能的设备,广泛应用于工业生产中,包括汽车制造、建筑工程、农业机械等领域。
液压缸的计算包括力学计算、液压计算和参数选择等方面。
下面将详细介绍液压缸的计算方法。
一、力学计算:液压缸的力学计算主要涉及材料的最大抗拉强度、扭矩计算、弹簧力计算和轴的挠度计算等。
1.最大抗拉强度计算液压缸的寿命与承载能力有关,材料的最大抗拉强度是评估其承载能力的重要指标。
液压缸的最大抗拉强度的计算公式为:最大抗拉强度=材料的抗拉强度×空心面积。
2.扭矩计算扭矩是一个对液压缸的瞬时力矩的评估。
液压缸的扭矩计算公式为:扭矩=力矩×转速。
3.弹簧力计算弹簧力是指液压缸在运动过程中受到的弹簧的力。
液压缸的弹簧力计算公式为:弹簧力=弹簧常数×表示位移的参数。
4.轴的挠度计算轴的挠度是指轴在承受力时的变形程度。
液压缸的轴的挠度计算公式为:挠度=(力×长度^3)/(弹性模量×断面惯量)。
二、液压计算:液压计算是液压缸设计中的重要过程,主要涉及液压缸的压力计算、液体流量计算和功率计算等。
1.压力计算液压缸的压力计算是指在给定的液体流量和缸的截面积下,计算液压缸所需的压力。
压力计算公式为:压力=力/面积。
2.流量计算液压缸的流量计算是指在给定的工作压力下,计算液压缸所需的液体流量。
流量计算公式为:流量=需要的液体流量/时间。
3.功率计算液压缸的功率计算是指在给定的压力和流量下,计算液压缸的功率。
功率计算公式为:功率=压力×流量。
三、参数选择:液压缸的参数选择是确保其正常工作的关键步骤,主要包括推力、速度、行程、缸筒直径和活塞杆直径等参数的选择。
1.推力的选择液压缸的推力是指在给定的工作条件下,液压缸所能提供的最大力。
推力的选择应满足工作条件所需的最小信号力。
2.速度的选择液压缸的速度是指液压缸的活塞在单位时间内的位移速度。
速度的选择应满足工作条件所需的最大速度。
液压缸设计计算实例
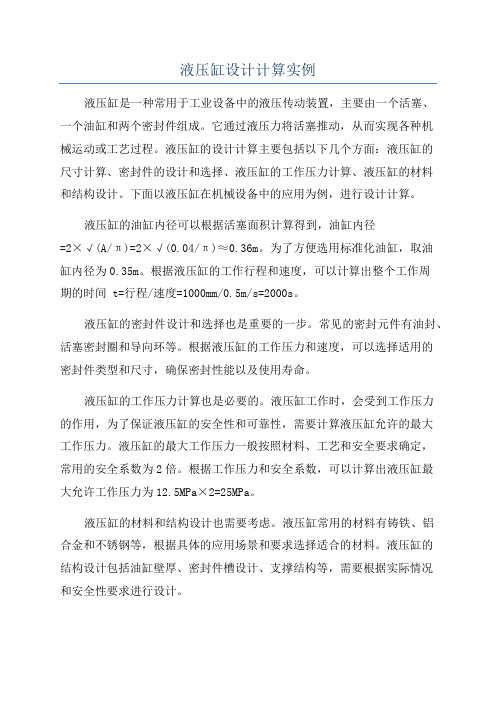
液压缸设计计算实例液压缸是一种常用于工业设备中的液压传动装置,主要由一个活塞、一个油缸和两个密封件组成。
它通过液压力将活塞推动,从而实现各种机械运动或工艺过程。
液压缸的设计计算主要包括以下几个方面:液压缸的尺寸计算、密封件的设计和选择、液压缸的工作压力计算、液压缸的材料和结构设计。
下面以液压缸在机械设备中的应用为例,进行设计计算。
液压缸的油缸内径可以根据活塞面积计算得到,油缸内径=2×√(A/π)=2×√(0.04/π)≈0.36m。
为了方便选用标准化油缸,取油缸内径为0.35m。
根据液压缸的工作行程和速度,可以计算出整个工作周期的时间 t=行程/速度=1000mm/0.5m/s=2000s。
液压缸的密封件设计和选择也是重要的一步。
常见的密封元件有油封、活塞密封圈和导向环等。
根据液压缸的工作压力和速度,可以选择适用的密封件类型和尺寸,确保密封性能以及使用寿命。
液压缸的工作压力计算也是必要的。
液压缸工作时,会受到工作压力的作用,为了保证液压缸的安全性和可靠性,需要计算液压缸允许的最大工作压力。
液压缸的最大工作压力一般按照材料、工艺和安全要求确定,常用的安全系数为2倍。
根据工作压力和安全系数,可以计算出液压缸最大允许工作压力为12.5MPa×2=25MPa。
液压缸的材料和结构设计也需要考虑。
液压缸常用的材料有铸铁、铝合金和不锈钢等,根据具体的应用场景和要求选择适合的材料。
液压缸的结构设计包括油缸壁厚、密封件槽设计、支撑结构等,需要根据实际情况和安全性要求进行设计。
综上所述,液压缸设计计算涉及液压缸的尺寸计算、密封件的设计和选择、液压缸的工作压力计算、液压缸的材料和结构设计等方面。
通过合理计算和选取,可以设计出安全可靠的液压缸,满足机械设备的工作需求。
液压缸标准值计算公式

液压缸标准值计算公式液压缸是一种常见的液压传动元件,广泛应用于各种机械设备中。
在设计和选择液压缸时,需要计算出液压缸的标准值,以确保其性能和使用效果。
本文将介绍液压缸标准值的计算公式,帮助读者更好地理解液压缸的工作原理和设计方法。
液压缸标准值的计算公式主要包括液压缸的推力、速度和功率等参数。
在计算这些参数时,需要考虑液压缸的工作压力、有效面积、活塞直径、活塞杆直径等因素。
下面将分别介绍液压缸推力、速度和功率的计算公式。
1. 液压缸推力的计算公式。
液压缸的推力是指液压缸在工作过程中所能产生的推力大小。
液压缸推力的计算公式为:F = P × A。
其中,F表示液压缸的推力,单位为牛顿(N);P表示液压缸的工作压力,单位为帕斯卡(Pa);A表示液压缸的有效面积,单位为平方米(m²)。
根据这个公式,我们可以通过液压缸的工作压力和有效面积来计算出液压缸的推力大小。
在实际应用中,需要根据具体的工作要求和负载情况来选择合适的液压缸推力,以确保液压缸能够正常工作。
2. 液压缸速度的计算公式。
液压缸的速度是指液压缸在工作过程中的运动速度。
液压缸速度的计算公式为:V = Q / A。
其中,V表示液压缸的速度,单位为米每秒(m/s);Q表示液压缸的流量,单位为立方米每秒(m³/s);A表示液压缸的有效面积,单位为平方米(m²)。
根据这个公式,我们可以通过液压缸的流量和有效面积来计算出液压缸的速度大小。
在实际应用中,需要根据具体的工作要求和运动速度来选择合适的液压缸速度,以确保液压缸能够满足工作需求。
3. 液压缸功率的计算公式。
液压缸的功率是指液压缸在工作过程中所需的功率大小。
液压缸功率的计算公式为:P = F × V。
其中,P表示液压缸的功率,单位为瓦特(W);F表示液压缸的推力,单位为牛顿(N);V表示液压缸的速度,单位为米每秒(m/s)。
根据这个公式,我们可以通过液压缸的推力和速度来计算出液压缸所需的功率大小。
液压缸缸体长度的计算公式

液压缸缸体长度的计算公式
液压缸缸体长度的计算公式是根据液压系统中的工作压力、缸体直径和活塞杆长度来确定的。
液压缸是一种用液压力驱动的推拉装置,广泛应用于各种工程和机械设备中。
液压缸的缸体长度计算公式如下:
缸体长度 = 活塞杆长度 + 2 ×缸体壁厚
其中,活塞杆长度指的是液压缸活塞杆的长度,缸体壁厚是液压缸缸体壁的厚度,通常为设计要求的一小部分。
这个公式的基本原理是根据液压系统的工作压力和活塞杆的长度确定液压缸的推力需求,然后根据推力需求确定缸体的尺寸。
活塞杆长度是由液压缸的应用需求和操作环境决定的;缸体壁厚是为了保证液压缸的结构强度和安全性而设计的。
在实际应用中,还需考虑液压缸的材质和制造工艺,以及缸体与其他部件的连接方式,从而综合考虑各种因素来确定液压缸的合适长度。
此外,还需进行合理的安全余量设计,以确保液压缸在工作过程中的稳定性和可靠性。
总之,液压缸缸体长度的计算公式是基于液压系统的工作压力、活塞杆长度和缸体壁厚来确定的。
这个公式可以为液压缸的设计和制造提供参考,并确保液压缸在工作过程中具备所需的推拉能力和结构强度。
液压设计需要哪些计算公式
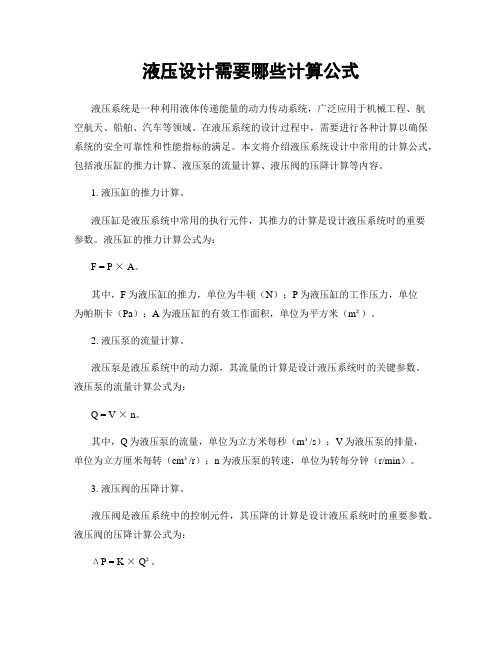
液压设计需要哪些计算公式液压系统是一种利用液体传递能量的动力传动系统,广泛应用于机械工程、航空航天、船舶、汽车等领域。
在液压系统的设计过程中,需要进行各种计算以确保系统的安全可靠性和性能指标的满足。
本文将介绍液压系统设计中常用的计算公式,包括液压缸的推力计算、液压泵的流量计算、液压阀的压降计算等内容。
1. 液压缸的推力计算。
液压缸是液压系统中常用的执行元件,其推力的计算是设计液压系统时的重要参数。
液压缸的推力计算公式为:F = P × A。
其中,F为液压缸的推力,单位为牛顿(N);P为液压缸的工作压力,单位为帕斯卡(Pa);A为液压缸的有效工作面积,单位为平方米(m²)。
2. 液压泵的流量计算。
液压泵是液压系统中的动力源,其流量的计算是设计液压系统时的关键参数。
液压泵的流量计算公式为:Q = V × n。
其中,Q为液压泵的流量,单位为立方米每秒(m³/s);V为液压泵的排量,单位为立方厘米每转(cm³/r);n为液压泵的转速,单位为转每分钟(r/min)。
3. 液压阀的压降计算。
液压阀是液压系统中的控制元件,其压降的计算是设计液压系统时的重要参数。
液压阀的压降计算公式为:ΔP = K × Q²。
其中,ΔP为液压阀的压降,单位为帕斯卡(Pa);K为液压阀的流量系数,是与液压阀的结构和工作原理相关的参数;Q为液压阀的流量,单位为立方米每秒(m³/s)。
4. 液压管路的压力损失计算。
液压管路是液压系统中的传输元件,其压力损失的计算是设计液压系统时的重要参数。
液压管路的压力损失计算公式为:ΔP = f × L × (Q/D)²。
其中,ΔP为液压管路的压力损失,单位为帕斯卡(Pa);f为液压管路的摩阻系数,是与管路材料和管路形状相关的参数;L为液压管路的长度,单位为米(m);Q为液压管路的流量,单位为立方米每秒(m³/s);D为液压管路的直径,单位为米(m)。
液压缸设计步骤和液压缸计算方法档
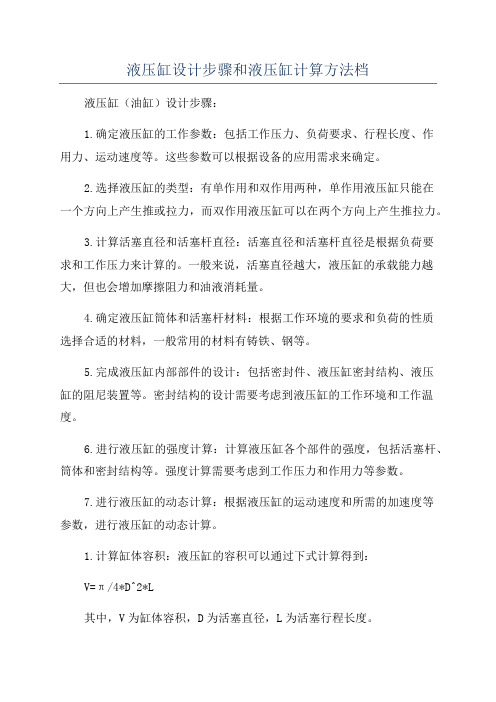
液压缸设计步骤和液压缸计算方法档液压缸(油缸)设计步骤:1.确定液压缸的工作参数:包括工作压力、负荷要求、行程长度、作用力、运动速度等。
这些参数可以根据设备的应用需求来确定。
2.选择液压缸的类型:有单作用和双作用两种,单作用液压缸只能在一个方向上产生推或拉力,而双作用液压缸可以在两个方向上产生推拉力。
3.计算活塞直径和活塞杆直径:活塞直径和活塞杆直径是根据负荷要求和工作压力来计算的。
一般来说,活塞直径越大,液压缸的承载能力越大,但也会增加摩擦阻力和油液消耗量。
4.确定液压缸筒体和活塞杆材料:根据工作环境的要求和负荷的性质选择合适的材料,一般常用的材料有铸铁、钢等。
5.完成液压缸内部部件的设计:包括密封件、液压缸密封结构、液压缸的阻尼装置等。
密封结构的设计需要考虑到液压缸的工作环境和工作温度。
6.进行液压缸的强度计算:计算液压缸各个部件的强度,包括活塞杆、筒体和密封结构等。
强度计算需要考虑到工作压力和作用力等参数。
7.进行液压缸的动态计算:根据液压缸的运动速度和所需的加速度等参数,进行液压缸的动态计算。
1.计算缸体容积:液压缸的容积可以通过下式计算得到:V=π/4*D^2*L其中,V为缸体容积,D为活塞直径,L为活塞行程长度。
2.计算活塞面积:根据活塞直径计算活塞面积,可以通过下式计算得到:A=π/4*D^2其中,A为活塞面积,D为活塞直径。
3.计算活塞杆面积:根据活塞杆直径计算活塞杆面积,可以通过下式计算得到:A'=π/4*D'^2其中,A'为活塞杆面积,D'为活塞杆直径。
4.计算推力:根据工作压力和活塞面积计算液压缸的推力,可以通过下式计算得到:F=P*A其中,F为液压缸的推力,P为工作压力,A为活塞面积。
5.计算液压缸的速度:液压缸的速度可以通过可控阀门来调节,一般使用油流量来计算液压缸的速度,可以通过下式计算得到:V=Q/A其中,V为液压缸的速度,Q为油流量,A为活塞面积。
液压系统计算公式
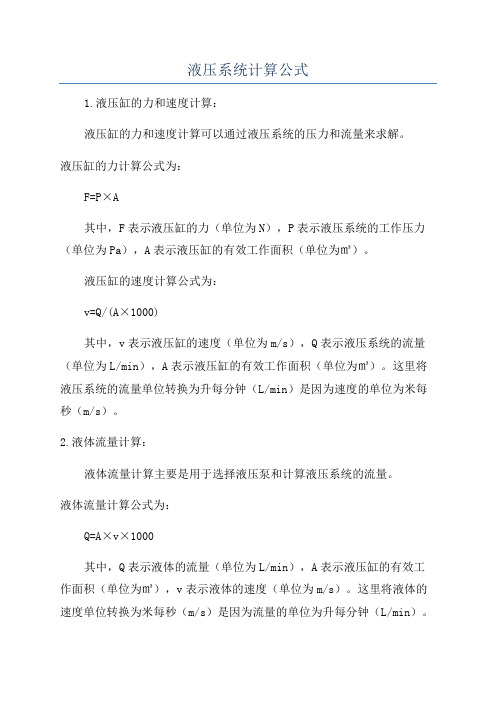
液压系统计算公式1.液压缸的力和速度计算:液压缸的力和速度计算可以通过液压系统的压力和流量来求解。
液压缸的力计算公式为:F=P×A其中,F表示液压缸的力(单位为N),P表示液压系统的工作压力(单位为Pa),A表示液压缸的有效工作面积(单位为㎡)。
液压缸的速度计算公式为:v=Q/(A×1000)其中,v表示液压缸的速度(单位为m/s),Q表示液压系统的流量(单位为L/min),A表示液压缸的有效工作面积(单位为㎡)。
这里将液压系统的流量单位转换为升每分钟(L/min)是因为速度的单位为米每秒(m/s)。
2.液体流量计算:液体流量计算主要是用于选择液压泵和计算液压系统的流量。
液体流量计算公式为:Q=A×v×1000其中,Q表示液体的流量(单位为L/min),A表示液压缸的有效工作面积(单位为㎡),v表示液体的速度(单位为m/s)。
这里将液体的速度单位转换为米每秒(m/s)是因为流量的单位为升每分钟(L/min)。
3.泵和马达的工作参数计算:液压系统中的泵和马达是系统的核心部件,其工作参数计算涉及到流量、压力、功率等方面。
泵的工作参数计算公式为:Pump Power (KW) = (Flow Rate (L/min) × Pressure (Bar)) ÷ 600其中,Pump Power表示泵的功率(单位为千瓦,KW),Flow Rate表示泵的流量(单位为L/min),Pressure表示泵的压力(单位为巴,Bar)。
马达的工作参数计算公式为:Motor Power (KW) = (Torque (Nm) × Speed (RPM)) ÷ 9550其中,Motor Power表示马达的功率(单位为千瓦,KW),Torque表示马达的扭矩(单位为牛顿米,Nm),Speed表示马达的转速(单位为转每分钟,RPM)。
4.液体管道的压力损失计算:液体管道的压力损失计算主要用于确定液体输送过程中的管道直径和管道长度。
液压缸的设计与计算
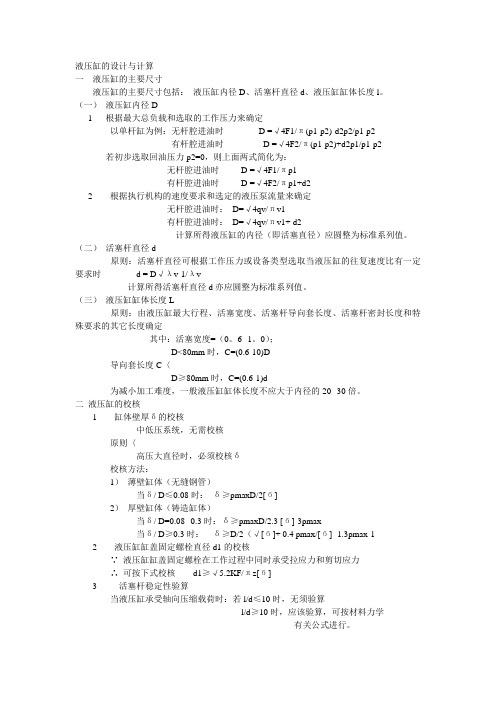
液压缸的设计与计算一液压缸的主要尺寸液压缸的主要尺寸包括:液压缸内径D、活塞杆直径d、液压缸缸体长度l。
(一)液压缸内径D1 根据最大总负载和选取的工作压力来确定以单杆缸为例:无杆腔进油时 D =√4F1/π(p1-p2)-d2p2/p1-p2有杆腔进油时 D =√4F2/π(p1-p2)+d2p1/p1-p2 若初步选取回油压力p2=0,则上面两式简化为:无杆腔进油时 D =√4F1/πp1有杆腔进油时 D =√4F2/πp1+d22 根据执行机构的速度要求和选定的液压泵流量来确定无杆腔进油时:D=√4qv/πv1有杆腔进油时:D=√4qv/πv1+ d2计算所得液压缸的内径(即活塞直径)应圆整为标准系列值。
(二)活塞杆直径d原则:活塞杆直径可根据工作压力或设备类型选取当液压缸的往复速度比有一定要求时 d = D√λv-1/λv计算所得活塞杆直径d亦应圆整为标准系列值。
(三)液压缸缸体长度L原则:由液压缸最大行程、活塞宽度、活塞杆导向套长度、活塞杆密封长度和特殊要求的其它长度确定其中:活塞宽度=(0。
6--1。
0);D<80mm时,C=(0.6-10)D导向套长度C〈D≥80mm时,C=(0.6-1)d为减小加工难度,一般液压缸缸体长度不应大于内径的20--30倍。
二液压缸的校核1 缸体壁厚δ的校核中低压系统,无需校核原则〈高压大直径时,必须校核δ校核方法:1)薄壁缸体(无缝钢管)当δ/ D≤0.08时:δ≥pmaxD/2[б]2)厚壁缸体(铸造缸体)当δ/ D=0.08--0.3时:δ≥pmaxD/2.3 [б]-3pmax当δ/ D≥0.3时:δ≥D/2(√[б]+ 0.4 pmax/[б] -1.3pmax-12 液压缸缸盖固定螺栓直径d1的校核∵液压缸缸盖固定螺栓在工作过程中同时承受拉应力和剪切应力∴可按下式校核d1≥√5.2KF/πz[б]3 活塞杆稳定性验算当液压缸承受轴向压缩载荷时:若l/d≤10时,无须验算l/d≥10时,应该验算,可按材料力学有关公式进行。
- 1、下载文档前请自行甄别文档内容的完整性,平台不提供额外的编辑、内容补充、找答案等附加服务。
- 2、"仅部分预览"的文档,不可在线预览部分如存在完整性等问题,可反馈申请退款(可完整预览的文档不适用该条件!)。
- 3、如文档侵犯您的权益,请联系客服反馈,我们会尽快为您处理(人工客服工作时间:9:00-18:30)。
工作压力/MPa p≤10
速比
1.33
10<p<20 1.46~2
p>20 2
3,缸筒内径
(1)动力较大的液压设备(如拉床、刨床、车床、组合机床、工程机械及矿 山机械等)的缸筒内径,通常根据最大牵引力 来确定。然后再按速度要求 计算所需流量,或者按已经选定的流量来验算速度。
“流体传动与控制”课程单元探究式教学小组
组长:常乐 组员:常乐,韦城,曹杰,甘建宇
第四章 液压缸
4.1液压缸的类型及其特点 4.2液压缸的设计计算
4.1液压缸的类型及其特点
• (1)液压缸的类型
压直 缸线
运 动 液
单作用缸 双作用缸
摆动液压缸
特种缸 单叶片
双叶片
柱塞式 活塞式 弹簧复位式 多级伸缩式 单活塞杆式 双活塞杆式 多级伸缩式
2,设计原则
(1)保证缸运动的出力、速度和行程 (2)保证缸每个零件有足够的强度、刚度和耐用性 (3)在保证以上两个条件的前提下,尽量减小缸的外形尺寸 (4)在保证缸性能的前提下,尽量减少零件数量,简化结构 (5)要尽量避免缸承受横向负载,活塞杆工作时最好承受拉力,以免产生纵向弯曲 (6)缸的安装形式和活塞杆头部与外部负载的连接形式要合理,尽量减小活塞杆伸 出后的有效安装长度,增加缸的稳定性
• 不计容积损失时,差动连接缸的伸出速度:
3 q /A1 A2 4q / d 2 (m/s)
• 活塞推力:
F3 pA1 A2 m d 2 pm / 4 10 6
(N)
单杆
双杆
3.伸缩式液压缸
形式:单作用和双作用
特点:总行程较长,收缩后很短,适用于空间小而行程长的 场合
供油量不变,各级活塞依次伸出速度和推力:
A2
4qv
(D2 d
2
)
(m/s)
• (2)活塞两方向运动时的作用力不相等
• 活塞杆推力:
F1
4
D2
p
4
D2 d 2
p0 m 10 6
(N)
• 活塞杆拉力:
F2
4
D2 d 2
p
4
D2
p0 m
10 6
(N)
• (3)液压缸的差动连接
单杆活塞液压缸在其左右两腔相互连通并输入压力油时称 之为“差动连接”。
(N)
4.摆动液压缸
图(a)为单叶片摆动液压缸,其输出扭矩和回转角速度为:
T
b
R1
R2
m
prdr
b 2
R12
R22
pm
(Nm)
8q D2 d 2
b
(1/s)
(3)其他液压缸及特点
• 1.串联液压缸(增力缸):用于径向尺寸受限制 且要求处理较大的情况
• 2.增压液压缸
pA
4
D2
(7)选择缸盖的结构形式,计算厚度和强度 (8)审定全部设计计算资料,进行修改补充 (9)选择适当的密封结构,设计缓冲、排气和防尘等装置 (10)绘制装配图和零件图,编制技术文件
二,基本参数计算
1. 工作负载 FR 缸的工作负载包括机构稳定功能工作状态下的静负载 Fe 摩擦阻力Ff 、和启动惯性阻力 Fi FR Fe Ff Fi
目的:为及时排除积留在缸内的空气,在两 端最高处设计排气装置以避免部件的不均匀 运动和油液的氧化以及液压装置元件的腐蚀。
液压缸的设计计算
一,设计依据、原则和步骤 二,基本参数计算 三,液压缸强度计算
一,设计依据、原则和步骤
1,设计依据
(1)了解和掌握液压缸在机械上的用途和动作要求。 (2)了解液压缸的工作条件 (3)了解外部负载情况 (4)了解液压缸的最大行程,运动速度或时间,安装空间所允 许的外形尺寸以及缸本身的动作 (5)设计已知液压系统的液压缸,应了解液压系统中液压泵的 工作压力和流量大小、管路的通径和布置情况、各种液压阀的 控制情况。 (6)了解有关国家标准、技术规范及参考资料
各项载荷均应在满负荷状态下计算,其中摩擦阻力按启动状静摩擦阻力计算。 缸自身的摩擦阻力已经用机械效率 的η形m 式在牵引力计算中加以考虑,故不 再计入。缸的牵引力等于工作负载。
2,速比
速比是指双作用单杆液压缸活塞杆缩回速度 v2与伸出速度 v1之比。
v2 / v1 D2 /(D2 d 2 )
ห้องสมุดไป่ตู้
活塞干的直径选择
工作压力p /(MPa)
pB
4
d2
•
输入输出压力关系:
pB
D d
2
pA
• 3.齿条液压缸
(4)缓冲装置
可调式
不可调式 目的:避免造成机械冲击和噪声,引起破坏性事故或严重影
响机械精度
原理:使活塞在接近缸盖时,在缓冲油腔内产生足够的缓冲 压力,即增大缸的回油阻力,降低活塞的移动速度,避免 撞击缸盖
常用缓冲装置结构简图
(5)排气装置
i 4qi / Di 2 (m/s)
Fi Di2 pi / 4 Di2 di2 p0 / 4mi 106 (N)
双作用缸各级活塞杆缩回运动速度和牵引力:
i' 4q ' / Di2 di2
(m/s)
F ' Di2 di2 pi' / 4 Di2 p0 / 4m' 106
对于无杆腔 :
D 4FR 106 pd 2
( p p0 )m ( p p0 )
对于有杆腔:
D
4FR 106 pd 2
( p p0 )m ( p p0 )
两式中, FR 为缸的最大推力,N;m为缸的机械效率,通常取 m =0.95;
为P0回油背压,MPa;p为进口工作压力,MPa;d为活塞杆直径,m。
齿条传动式
(2)常用液压缸及其特点
• 1.柱塞式液压缸
推力和运动速度计算式:
F Ap d2 p
4
(N)
4q
d 2
(m/s)
例图:
2.活塞式液压缸
• 1)单杆活塞液压缸
• 活(塞1杆)伸供出油速度量:不1变 时qA,1v 活4塞qD往2v 复运(动m/的s) 速度不等
活塞杆缩回速度:2
qv
3,设计步骤
(1)根据设计依据,初步确定设计方案,会同有关人员进行技术经济分析 (2)对缸进行受力分析,选择适当的结构形式、安装方式 (3)根据工作负载、重力、摩擦力和惯性力确定液压缸在形成各阶段上负载的变化 规律及有关的技术数据 (4)根据工作负载和选定的额定压力,确定活塞端面面积并计算活塞直径和缸筒外 径 (5)根据缸径和运动速度之比或者工作负载和材料的许用应力,确定活塞杆的直径 (6)根据运动速度、工作出力和活塞直径,确定液压泵的压力和流量