成型零件的尺寸计算
成型零件尺寸计算

成型零件工件尺寸计算案例、塑料制品制品如图1所示,材料为ABS。
以下计算相关模具凹模、型芯的直径和高(深)度、螺纹直径以及孔的中心距尺寸。
图1制品尺寸二、计算1、确定模塑收缩率查模具设计手册得知,ABS的收缩率为0.4〜0.8%。
收缩率的平均值为:B 一% =0.6%2、确定制品尺寸公差等级,将尺寸按规定形式进行处理查常用塑料模塑公差等级表,对于ABS塑件标注公差尺寸取MT3 ,未注公差尺寸取MT5级,以满足模具制造和成型工艺控制,满足制品要求。
查得制品未注公差尺寸的允许偏差为双向偏差形式,按照尺寸形式的规定,作如下转换:塑件外径『' '内部小孔'一1一’'塑件高度三1顼二--------- 1 '-3、计算凹模、型芯工作尺寸...... …月—i.取模具制造公差五厂。
1)凹模尺寸径向尺寸'-V - - :'注J匕二[50.32 +50.32x0.006—"0.64]十年片口40.lt —〜,,,,、=(不保留小数位)高度尺寸、T.=21祁'H (不保留小数位)2)型芯尺寸大型芯径向尺寸 ,-',:-;一』'L」一 L '孩=[45+45x0.006 + 1、』0.361 顷==45.5 w (保留一位小数)大型芯高度尺寸二- 一-1"^ = 18+18x0.006 + jx0.2] …=18.2 (保留一位小数)或=[786 + 7.86 x O.OQ6 T E.28]小型芯径向尺寸=8 7叩(不保留小数位) 小型芯高度尺寸 f ,-L -:]'" 一 ,.... - ::-.J . - 22-i :::=2.2两个小型芯固定孔的中心距匕M =【£$+£孩性】土*%皿上二【30+30x0.006]土于 _3。
2 +。
35-3U.2 H U.U35取制造公差为土 U.U1,因土 U.U1V 土 U.U35,满足要求,故最后确定两小型芯固定孔的中 心距为上=30 2 + 0 014、计算螺纹型芯和螺距工作尺寸 查普通金属螺纹基本尺寸标准(GB197 — 81),得:OB.。
成型零件工作尺寸的计算方法
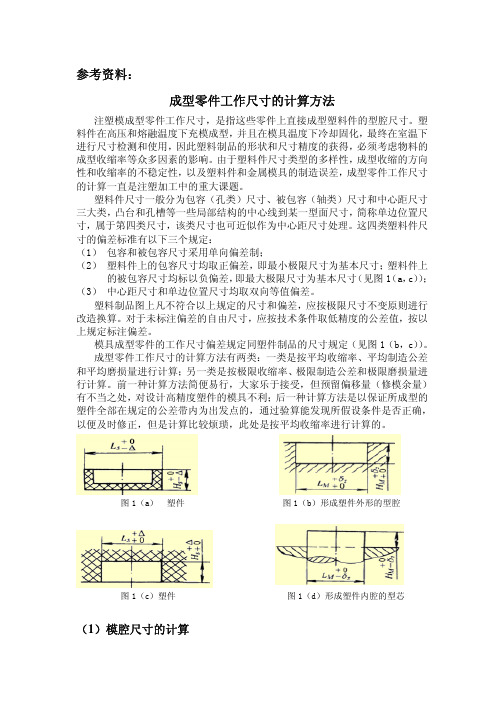
图 1(a) 塑件
图 1(b)形成塑件外形的型腔
图 1(c)塑件
(1)模腔尺寸的计算
图 1(d)形成塑件内腔的型芯
模腔是指凹模与凸模(型腔和型芯)组成的空腔,如果仅考虑塑件的收缩率 S:
模腔尺寸-塑件尺寸
S=
× 100%
塑件尺寸
则模腔尺寸为:
模腔尺寸 = 塑件尺寸 ×(1+S )
δ 一般情况下,模具的制造公差 z 可以取为
3 Lm = Ls × (1 + S ) − ∆
4
标注公差后得到型腔的尺寸为:
Lm
=
Ls×(1+
S
)−
3 4
∆
+δ +0
z
(3)型芯尺寸的计算
和型腔的计算过程一样,可以得到标注公差后的型芯尺寸为:
Lm
=
Ls×(1+S
)+
3 ∆
4
+0 −δ
z
参考资料:
成型零件工作尺寸的计算方法
注塑模成型零件工作尺寸,是指这些零件上直接成型塑料件的型腔尺寸。塑 料件在高压和熔融温度下充模成型,并且在模具温度下冷却固化,最终在室温下 进行尺寸检测和使用,因此塑料制品的形状和尺寸精度的获得,必须考虑物料的 成型收缩率等众多因素的影响。由于塑料件尺寸类型的多样性,成型收缩的方向 性和收缩率的不稳定性,以及塑料件和金属模具的制造误差,成型零件工作尺寸 的计算一直是注塑加工中的重大课题。
δz = ∆ 3 ∼ ∆ 4
δ 设计模具成型零件时还应该考虑模具在使用过程中的磨损量 c ,可以取塑
∆ 件总公差 的 1/6,即
δc = ∆ 6
(Hale Waihona Puke )型腔尺寸的计算按照塑件与成型零件平均尺寸的收缩率计算:
经验尺寸和公式总汇
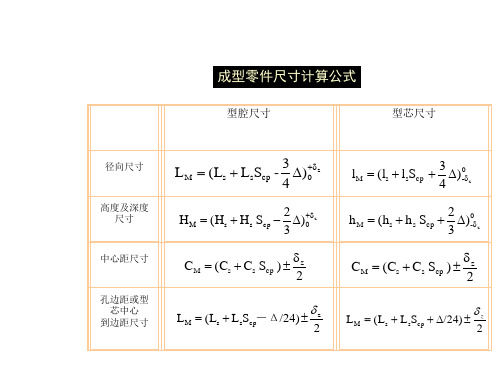
矩形凹模内 侧短边长
b
整体凹模
镶拼式凹模
壁厚 S
凹模壁厚 模套壁厚
S1
S2
~40
25
9
22
>40 ~ 50 25 ~ 30 9 ~ 10 22 ~ 25
>50 ~ 60 30 ~ 35 10 ~ 11 25 ~ 28
>60 ~ 70 35 ~ 42 11 ~ 12 28 ~ 35
五、分流道设计与制造
3.分流道的尺寸设计
流道的直径过大:不仅浪费材料, 而且冷却时间增长, 成 型周期也随之增长, 造成成本上的浪费。
流道的直径过小:材料的流动阻力大, 易造成充填不足, 或者必须增加射出压力才能充填。
因此流道直径应适合产品的重量或投影面积。
流道直径(mm) 4 6 8 10 12
产品重量(g) 95 375
375以上 大型
流道直径(mm) 4 6 8 10 12
投影面积(cm2) 10以下 200 500 1200 大型
§4.3普通浇注系统的设计
五、分流道设计与制造
2.分流道的尺寸设计
流道长度宜短, 因为长的流道不但会造成压力损失,不利 于生产性,同時也浪费材料;但过短, 产品的残余应力增大, 并且容易产生毛边。
流道长度可以按如下经验公式计算:
D=
D——分流道直徑mm W——产品质量g L——流道長度mm
支承板厚度 H
15 15 ~ 20 20 ~ 25 25 ~ 30 30 ~ 40
>40
※当塑件的投影面积较大时,支承板会很厚,为减小厚度可加支柱。 加一个支柱:H′=H/2.7 加两个支柱:H″=H/4.3
※板厚值也可参考表3-22
成型零部件尺寸及力学计算
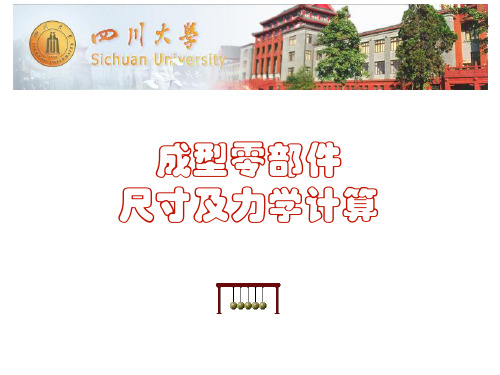
塑料成型模具成型零部件尺寸及力学计算塑料成型模具重点、难点•重点:•收缩的定义和重要性•计算型腔尺寸的方法•理解按极限尺寸计算和按平均收缩率计算的差别•模具常用的修模方法•难点:•按极限尺寸计算型腔尺寸的方法塑料成型模具塑料制品精度塑料原料收缩δS估算收缩率不准确δSS 模具零件制造误差δm 模具零件磨损δw 配合与安装误差δq影响因素制品公差Δ≥δS +δSS +δm +δw +δq因此,塑料制品的精度往往较低,应尽量选用低精度。
否则制品精度的提高会使模具的制造费用成指数幂增加。
制品公差标准GB/T14486-1993塑料成型模具成型零件制造误差在0~500mm 内。
、、、、,、IT 、IT 、IT 、IT IT a i m m D 。
D D a i a m m 160100644025 12111098,:: ,::)001.045.0(3其值分别对应常用精度系数公差单位型腔零件尺寸型腔零件制造公差δδ+=⋅=组合式型腔的制造公差要用尺寸链来决定制造误差约与成正比。
当制品尺寸较小时,型腔零件的制造误差约占制品公差的三分之一。
3D塑料成型模具塑料原料收缩理论收缩指的是在高温高压下注射入模腔中的塑料所成型出来的制品比模腔尺寸要小的现象。
常以mm/mm 或%来表示每种塑料的收缩或膨胀或压缩率可能不同原则1:塑料的压力、体积和温度之间有一种联系。
影响压力、温度和时间的因素都将影响收缩。
原则2:塑料受热时会膨胀,当冷却到原来的温度时又会收缩到原来的体积。
原则3:塑料受压时其体积会缩小,当压力恢复时又会膨胀到原来的体积。
塑料成型模具塑料制品收缩过程刚开始注塑时,压力小,但与模腔壁接触的塑料凝固后马上收缩模腔充满后,压力升高,塑料被压缩,但可补料以补偿收缩保持压力直到浇口冻结和阀式浇口关闭,补料停止继续收缩,压力持续下降,直至顶出,收缩还将继续重要因素:注射压力和浇口封闭时间塑料成型模具塑料原料收缩率影响收缩率的因素有:从理论上计算收缩率是不大可能的左边大部分是模具设计者或制造者控制不了的导致收缩率的波动•材料规格•加入回收塑料•加入填充剂•顶出时制品的温度•注射压力及保压压力•制品壁厚和流动阻力•制品形状•模具设计多数塑料在顶出后几小时会达到总收缩量的90%,其余的10%在10天内完成,少数塑料要几个月时间在高于室温下退火,可加速松驰,终止收缩,但吸湿塑料还会有尺寸变化m mL m m L 。
压铸成型零件的主要尺寸ppt实用资料
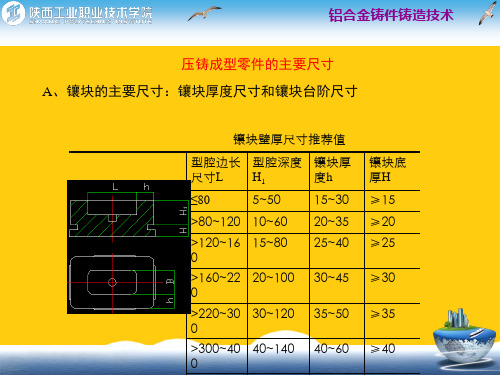
整体镶块台阶尺寸推荐值
同理得
2成. 形零件的制造公dM差—等级模按I具T7~型IT10腔选取径,向一般尺比压寸铸件的(m尺m寸公) 差等级高2~3级,取压铸件公差值的1/5~1/3。 LM=(L + L K)d±—δ/2压铸件径向基本尺寸(mm)
hM—模具型腔深度基本尺寸 (mm) h—压铸件高度基本尺寸 (mm)
≤20
>45
20~40
>40
>50
>35
B、型芯的主要尺寸
铝合金铸件铸造技术
圆型芯尺寸推荐值 mm
成形段直 配合段直
径d
径d0
≤3
4
>3~10
>10~18
>18~30
>30~50 >50~80 >80~120
d0+ (0~1.0)
>120~180
>180~260
>260~360
台阶直 径D
8 d0+4.0
D—压铸件径向基本尺寸(mm)
△—压铸件相应尺寸公差值(mm)
K—压铸件的收缩率
δc—模具磨损量(mm) HM—模具型腔深度基本尺寸(mm) H—压铸件高度基本尺寸(mm)
铝合金铸件铸造技术
成形零件尺寸计算图
铝合金铸件铸造技术
模具磨损后型芯尺寸会逐渐减小,平均计算法可得:
按C、压影铸响件压公铸差件所尺推寸荐精的度模的具因制素d造M公-差 δ/2=(d + △/2) +(d + △/2)K + δc/2
0.2~0.3 0.3~0.4 0.3~0.5 0.4~0.6
0.6~0.8
收缩率 / % 0.3~0.4 0.4~0.6 0.5~0.7
基于Inventor的世赛模具成型零件工作尺寸计算
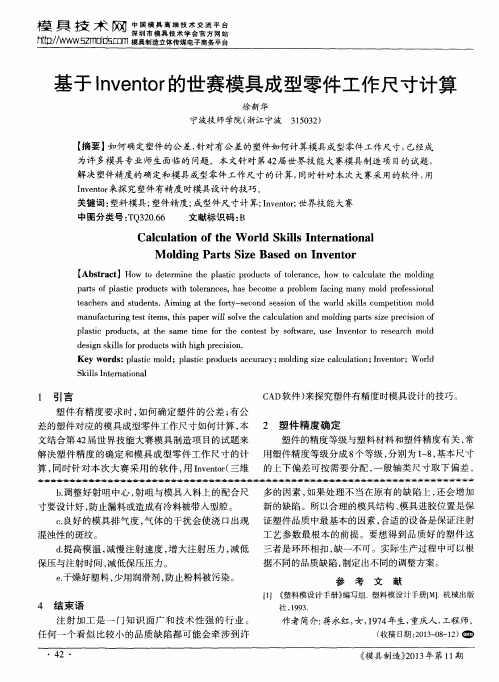
C . 良好 的模具排气度 , 气体 的干扰会使浇 口出现 证塑件 品质中最基本 的因素 , 合适 的设备是保证注射 工艺参数最根本 的前提。要想 得到品质好 的塑件这 混 浊性 的斑 纹 。
l 引 言
塑件有精度要求 时 , 如何确定塑件 的公差 ; 有公
C A D软件 ) 来探究塑件有精度时模具设计的技巧。
差的塑件对应 的模具成型零件工作尺寸如何计算 , 本 2 塑件精度确定 塑件 的精度等级与塑料材料和塑件精度有关 , 常 文结合第 4 2 届世界技能大赛模具制造项 目的试题来 个等级 , 分别为 l ~ 8 , 基本尺寸 解决塑件精度 的确定和模具成型零件工作尺寸 的计 用塑件精度等级分成 8 算, 同时针对本次大赛采 用的软件 , 用I n v e n t o r ( 三维 的上下偏差 可按需要分配 , 一般轴类尺寸取下偏差 ,
h l ; l : p : / / ] l W i t l WW. l 5 z m u l d s c u m 模具制造立 体传 媒电子 商务平台
具 技 术 网
嘉
基于 I n v e n t o r 的世赛模具成 型零件工作 尺寸计算
徐 新 华
宁波技 师 学院( 浙 江宁波 3 1 5 0 3 2 )
社, 1 9 9 3 .
缺 一 不 可 。实 际生 产 过程 中可 以根 d . 提高模温 , 减慢 注射速度 , 增 大注射压力 , 减低 三 者是 环 环相 扣 ,
塑件成型工艺性分析
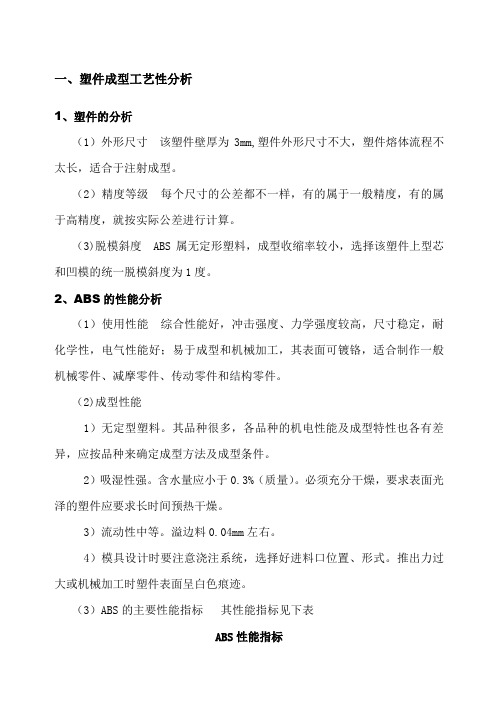
一、塑件成型工艺性分析1、塑件的分析(1)外形尺寸该塑件壁厚为3mm,塑件外形尺寸不大,塑件熔体流程不太长,适合于注射成型。
(2)精度等级每个尺寸的公差都不一样,有的属于一般精度,有的属于高精度,就按实际公差进行计算。
(3)脱模斜度 ABS属无定形塑料,成型收缩率较小,选择该塑件上型芯和凹模的统一脱模斜度为1度。
2、ABS的性能分析(1)使用性能综合性能好,冲击强度、力学强度较高,尺寸稳定,耐化学性,电气性能好;易于成型和机械加工,其表面可镀铬,适合制作一般机械零件、减摩零件、传动零件和结构零件。
(2)成型性能1)无定型塑料。
其品种很多,各品种的机电性能及成型特性也各有差异,应按品种来确定成型方法及成型条件。
2)吸湿性强。
含水量应小于0.3%(质量)。
必须充分干燥,要求表面光泽的塑件应要求长时间预热干燥。
3)流动性中等。
溢边料0.04mm左右。
4)模具设计时要注意浇注系统,选择好进料口位置、形式。
推出力过大或机械加工时塑件表面呈白色痕迹。
(3)ABS的主要性能指标其性能指标见下表ABS性能指标密度/g ·3cm 1.02~1.08 屈服强度/MPa 50 比体积/13-∙g cm0.86~0.96 拉伸强度/MPa 38 吸水率(%) 0.2~0.4 拉伸弹性模量/MPa 1.4×310熔点/C ο 130~160 抗弯强度/MPa 80 计算收缩率(%) 0.4~0.7 抗压强度/MPa 53 比热熔/1)(-∙∙C kg J ο1470弯曲弹性模量/MPa1.4310⨯3、ABS 的注射成型过程及工艺参数 (1)注射成型过程1)成型前的准备。
对ABS 的色泽、粒度和均匀度等进行检验,由于ABS 吸水性较大,成型前应进行充分的干燥。
2)注射过程。
塑件在注射机料和筒内经过加热、塑化达到流动状态后,由模具的浇注系统进入模具型腔成型,其过程可分为充模、压实、保压、倒流和冷却五个阶段。
孔边距计算
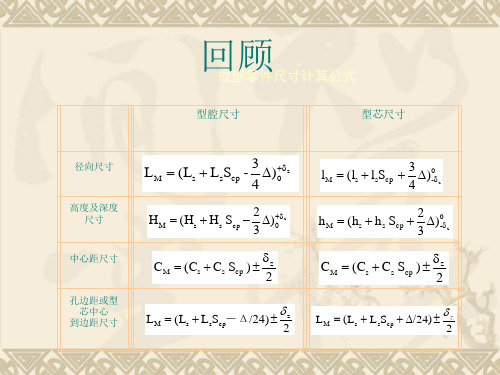
当塑件的投影面积较大时,支承板会很 厚,为减小厚度可加支柱。 加一个支:H′=H/2.7 加两个支柱:H″=H/4.3
项目训练
根据壳体塑件的尺寸和型腔布置方案完 成下列设计计算 1、确定凹模镶件尺寸和模套的壁厚 确定支承板的厚度 2、确定支承板的厚度 确定壳体塑件模具的标准模架 3、确定壳体塑件模具的标准模架
高度及深度 尺寸
中心距尺寸
C M = (Cs + Cs Scp ) ±
δz 2
δz
2
C M = (Cs + Cs Scp ) ±
δz 2
δz
2
孔边距或型 芯中心 到边距尺寸
L M = (Ls + L sScp-Δ/24) ±
L M = (L s + L sScp + ∆/24) ±
主要内容
一、凹模上的孔边距计算 二、型芯上的孔边距计算 三、型腔壁厚与底板厚度的确定
表中壁厚是边长比L/b=1.8时的参考尺寸,当L/b>1.8时壁厚应适当增大。
3.支承板厚度的计算
塑件在分型面上的投影面积 A(cm A(cm2) 支承板厚度 H
~5 >5 ~ 10 >10 ~ 50 >50 ~ 100 >100 ~ 200 >200
15 15 ~ 20 20 ~ 25 25 ~ 30 30 ~ 40 >40
1).模塑过程中模具承受的力 ) 设备施加的锁模力 熔融塑料作用于型腔内壁的压 力 2).型腔受内压力作用发生膨 2) . 胀变形 影响塑件的尺寸精度 配合面处产生溢料飞边 小型腔的许用变形量小,压力 作用会导致其破坏
大型腔以刚度为主计算, 大型腔以刚度为主计算,小型腔以强度为主计算 圆形凹模直径: ﹤ ~ 圆形凹模直径:D﹤67~86mm时以强度计算为主 时以强度计算为主 矩形凹模长边: ﹤ 矩形凹模长边:L﹤108~136mm时以强度计算为主 ~ 时以强度计算为主
成型零件工作的尺寸计算实例

铝合金铸件铸造技术
B、深度尺寸有50,4,5±0.2,25±0.5等,计算结果如下:
50, 4, 5±0.2, 25±0.5
HM=49.87+0.1550 HM=3.81+0.0750 HM=4.95+0.10 HM=25+0.250
3)型芯尺寸计算 A、型芯径向尺寸有φ40+0.340, φ32+0.170, φ7等 B、型芯高度尺寸有10,37。
铝合金铸件铸造技术
根据:DM=(D+DK-0.7 △)+δ0得 对φ48 0-0.17尺寸,DM =(48+48×0.6%-0.7×0.17)0.17/50
= 48.17+0.0340(mm) 同理: φ85尺寸的DM =84.9 +0.2180(mm) 从模具结构图可以看出,该尺寸受滑块分型面的影响,故应 灾计算的基础上减少0.05mm,并适当提高模具的制造精度 DM=84.85+0.160(mm)。
材料:YL102 未注公差IT14,未注铸造圆角R2
支座压铸件成形零件尺寸计算图
铝合金铸件铸造技术
成形零件尺寸计算步骤: 1)确定压铸件的收缩率K
查表可以得到该压铸件的收缩条件为混合收缩,收缩率为 0.5%~0.7% ,取平均值K=0.6% 。 2)型腔尺寸计算 A、径向尺寸有φ85,
成型零部件的工作尺寸计算

※塑件脱模时的摩擦(型腔变大、型芯变小、中心距工作尺寸不变) ※料流的冲刷 ※腐蚀性气体的锈蚀 ※模具的打磨抛光
2019/2/12
二、影响塑件工作尺寸公差的因素
2.成型零件的磨损δ c
垂直于脱模方向的模具表面不考虑磨损。 平行于脱模方向的模具表面要考虑磨损。
塑件成型收缩的波动δ
s
成型零件的制造误差δ
z
成型零件的磨损δ
c
模具安装配合误差δ
j
2019/2/12
二、影响塑件工作尺寸公差的因素
1.塑件的成型收缩δ s
⑴成型收缩率δ s :δs =(Smax-Smin) Ls 对于一副已制造好的模具,δ s是引起塑件尺寸变化的主要因素
一般要求:成型收缩引起的塑件尺寸误差δ s< Δ /3
其中:
中心距制造公差δ z=(1/3~1/6)Δ
2019/2/12
四、成型零件工作尺寸计算
6.螺纹成型件的工作尺寸计算
⑴公制普通螺纹型环工作尺寸计算 螺纹型环中径工作尺寸 D2M
0 +δ z=(D ) +δ z 2s+D2sScp–b 0
螺纹型环大径工作尺寸 DM
0
+δ z=(D
0
s+DsScp–b)0
螺纹型芯小径工作尺寸 d1M
2019/2/12
四、成型零件工作尺寸计算
6.螺纹成型件的工作尺寸计算
⑶螺距工作尺寸计算 螺纹型芯螺距:
z P (P P S ) M s s cp 2
式中:PM ——螺纹型芯螺距
Ps ——塑件内螺纹螺距基本工作尺寸
常用的塑性成型方法

4.2 常用的塑性成型方法
2)计算坯料的质量和尺寸
由齿轮零件图和锻件图得到
锻件质量:m锻=V锻·ρ
=π/4(32×0.27+2.112×0.34-1.322×0.61) ×7.85
=2.26×7.85
=17.8kg
冲孔芯料质量:取d=60mm,H=65mm
m型芯=(1.18~1.57)d2·H
=(1.18~1.57)×602×65
≈0.3kg
烧损质量:查表3.2.3得煤气炉加热时,烧损率δ应取0.023,但因该锻件需经2~3次扩孔,至少需加热二次,故查表3.2.4取δ=0.035
m烧损=17.8×0.035=0.6kg
所以,坯料质量:
m坯料= m锻+ m型芯+ m烧损=18.7kg
坯料的计算直径:因采用镦粗成形,得:
D=1.20dm=120m
查表4.2.5得标准热轧圆钢直径,确定选取坯料直径D=120mm。
坯料长度:
L=V坯/A坯=210mm
从而确定坯料尺寸为Φ120×210mm
3)确定锻造工序自由锻的工序是使金属坯料实现主要的变形要求,达到或基本达到锻件所需形状和尺寸的工序。
其分为基本工序、辅助工序和修整工序。
基本工序主要有以下几种:镦粗、拔长、冲孔、弯曲、扭转、错移、切割和锻接等。
其中镦粗是。
成型零件尺寸计算
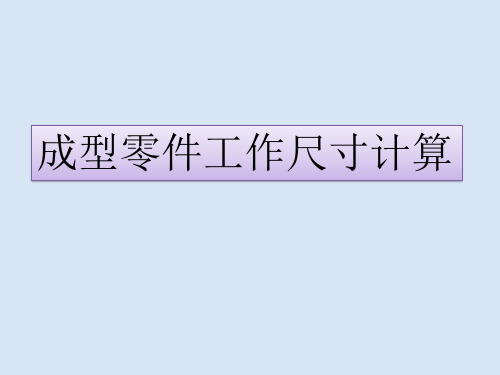
④模具安装配合误差δj ,主要受配合间隙影响,对于过盈配合, 不存在此误差。 ⑤水平飞边厚度的波动δf :对于压铸模和注塑模,水平飞边厚 度很薄,影响较小。 塑件可能产生的最大误差δ = δz + δc +δs +δj +δf 塑件的公差值应大于或等于上述各种因素引起的积累误差: 即:∆≥δ
径向尺寸
4 3
深度尺寸:
LM=(HS+HSSCP - 2 ∆) 0+ δz
3
2.型芯尺寸:
径向尺寸: LM=(LS+LSSCP + 4 ∆) - δz 0
3
高度尺寸: HM=(HS+HSSCP + ∆) - δz 0
3 2
3.中心距尺寸:
LM=(LS+LSSCP )± 2
z
4.螺纹型环尺寸:
大径尺寸: DM=(d S+ d S SCP - b)0+ δz 中径尺寸: D2M=(d2S+d2SSCP - b)0+ δz
(2)轴类尺寸(B类)
该类尺寸属被包容尺寸(或广义的轴),与塑料熔体或塑件之间产生摩擦磨 损之后,具有变小的趋势 。属这类尺寸的有:型芯高度、型芯径向尺寸等。
(3)中心距类尺寸(C类)
该类尺寸不受摩擦磨损影响,因此可视为一种不变尺寸。属于这类尺寸的 有:孔间距、型芯间距和孔中心与型芯中心的距离。
塑件及成型零件尺寸标注方法
=(30+30×0.008)± = 30.24±0.03mm
6.螺纹型芯大径尺寸:
dM=(DS+DSSCP + b) 0- δz
=(8+8×0.008 + 0.20) 0- 0.03
成型零件计算例题资料

⑴圆形型腔加工 形状不大,车削 立铣+回转式夹具 数控铣或加工中心
2024/7/24
§3.5成型零件的设计及制造案例分析
三、型腔的加工
4.型腔加工案例 ⑵规则矩形型腔加工
普通铣床加工出 型腔,无法铣出的 圆角可钳工修配或 电火花加工。
2024/7/24
§3.5成型零件的设计及制造案例分析
成本低,投资少,通用性好
2024/7/24
§3.5成型零件的设计及制造案例分析
二、成型零件的加工方法
3.常用加工方法 ⑵数控机床加工
粗加工与半精加工:数控铣、加工中心 热处理后的精加工:高精度成型磨床、坐标磨床 检验:三坐标测量机 特点:
对熟练工人的依赖少,效率高,质量好,可加 工形状复杂的型腔.
CM=(30+30×0.006)=30.2±0.01(孔间距公差查表3-5)
一、成型零件尺寸计算实例
3.工作尺寸的标注
2024/7/24
2024/7/24
2024/7/24
§3.5成型零件的设计及制造案例分析
二、成型零件的加工方法
1.成型零件的工作型面的形状 外工作型面:型芯和凸模 内工作型面:型腔和型孔
§3.5成型零件的设计及制造案例分析
三、型腔的加工
1.型腔铣削加工
仿形铣
数控铣
2024/7/24
§3.5成型零件的设计及制造案例分析
三、型腔的加工
2.型腔电加工
电火花加工的基本原理 基于工具与工件(正.负极)之间的脉冲放电的电腐蚀现象来蚀
除多余金属。
条件:放电间隙 脉冲电源(瞬时放电) 液体介质 电火花加工的特点及适用范围 ⑴难切削材料 ⑵形状复杂的工件 ⑶易加工过程自动化 局限:
型腔壁厚和底版厚度

注射模具成型零部件设计
§2.3 成型零部件工作尺寸计算
二.壁厚旳受力分析 1.模塑过程中模具承受旳力 设备(注塑机)施加旳锁模力; 熔融塑料作用于型腔内壁旳压力。
2.型腔受内压力作用发生膨胀变形 影响塑件旳尺寸精度; 配合面处产生溢料飞边; 小型腔旳许用变形量小,压力作用会造 成其破坏。
当分界值不明确时按两种措施计算型腔壁厚值,取其大者。
注射模具成型零部件设计
§2.3 成型零部件工作尺寸计算
二.壁厚旳受力分析
(2) 刚度计算条件因为模具旳特殊性,应从下列三个方面来考虑:(型腔侧 壁旳最大允许变形量δ)
从中小型塑件旳尺寸精度考虑:δ≤Δ/5
部分尺寸要求较高旳精度,要求模具型腔应具有很好旳刚性,以确保塑料熔体 注入型腔时不产生过大旳弹性变形。此时,型腔旳充许变形量[] 由塑件尺寸和公 差值来拟定。
圆形凹模直径:D﹤67~86mm时以强度计算为主
矩形凹模长边:L﹤108~136mm时以强度计算为主.
当分界值不明确时按两种措施计算型腔壁厚值,取其大者。
注射模具成型零部件设计
§2.3 成型零部件工作尺寸计算 一、计算法
1.矩形侧壁和底板厚度旳计算法:圆形凹模壁厚
注射模具成型零部件设计
§2.3 成型零部件工作尺寸计算 一、计算法
§2.3 成型零部件工作尺寸计算 二、经验法
1.矩形凹模壁厚
矩形凹模 内侧短边长
b
整体凹模壁 厚 S
镶拼式凹模
凹模壁厚 模套壁厚
S1
S2
~40
25
9
22
>40 ~ 50 25 ~ 30 9 ~ 10 22 ~ 25
成型零件尺寸计算
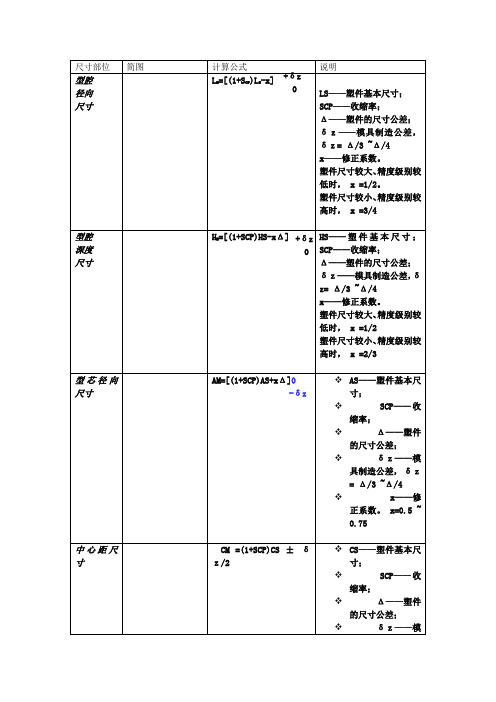
简图
计算公式 LM=[(1+SCP)LS-x]
型腔 径向 尺寸
+δ z 0
说明 LS——塑件基本尺寸; SCP——收缩率; Δ ——塑件的尺寸公差; δ z——模具制造公差, δ z= Δ /3 ~Δ /4 x——修正系数。 塑件尺寸较大、 精度级别较 低时, x =1/2。 塑件尺寸较小、 精度级别较 高时, x =3/4
型腔 深度 尺寸
HM=[(1+SCP)HS-xΔ ] +δ z HS—— 塑 件 基 本 尺 寸 ; 0 SCP——收缩率; Δ ——塑件的尺寸公差; δ z——模具制造公差, δ z= Δ /3 ~Δ /4 x——修正系数。 塑件尺寸较大、 精度级别较 低时, x =1/2 塑件尺寸较小、 精度级别较 高时, x =2/3 AM=[(1+SCP)AS+xΔ ]0 -δ z AS——塑件基本尺 寸; SCP—— 收 缩率; Δ ——塑件 的尺寸公差; δ z——模 具制造公差, δ z = Δ /3 ~Δ /4 x——修 正系数。 x=0.5 ~ 0.75 CS——塑件基本尺 寸; SCP—— 收 缩率; Δ ——塑件 的尺寸公差; δ z——模
型芯径向 尺寸
中心距尺 寸
CM =(1+SCP)CS ± δ z/2
具制造公差, δ z = Δ /3 ~ Δ /4
型芯高度 尺寸
BM=[(1+SCP)BS+xΔ ] 0 -δ z
BS——塑件基本尺 寸; SCP—— 收 缩率; Δ ——塑件 的尺寸公差; δ z——模 具制造公差, δ z = Δ /3 ~Δ /4 x—— 修正系数。 x=1/2 ~ 2/3 塑 件尺寸较大、精度 级别较低时, x =1/2
- 1、下载文档前请自行甄别文档内容的完整性,平台不提供额外的编辑、内容补充、找答案等附加服务。
- 2、"仅部分预览"的文档,不可在线预览部分如存在完整性等问题,可反馈申请退款(可完整预览的文档不适用该条件!)。
- 3、如文档侵犯您的权益,请联系客服反馈,我们会尽快为您处理(人工客服工作时间:9:00-18:30)。
成型零件尺寸计算 计算实例 型腔壁厚底板厚 思考与练习
对于一副已制造好的模具,δs是引起塑件尺寸变化的主要因素 一般要求:成型收缩引起的塑件尺寸误差δs< Δ /6
第三章 塑料模设计及制造基础
§3.3.3 成型零件的尺寸计算
二、影响塑件尺寸公差的因素
目的与要求 重点和难点
2014年4月27日
4.模具的安装配合误差δj
z PM (Ps Ps Scp ) 2
式中:PM ——螺纹型芯螺距
Ps ——塑件内螺纹螺距基本尺寸
z ——塑件内螺纹螺距基本尺寸
第三章 塑料模设计及制造基础
§3.3.3 成型零件的尺寸计算
七、实例(Example)
目的与要求 重点和难点
2014年4月27日
查表得塑料收缩率为: Smax=0.01 Smin=0.006 故:Scp=0.008 分析塑件的最高精度为MT3 模具制造精度取: IT9(比塑件精度高三个等级)
2014年4月27日
⑴公制普通螺纹型环工作尺寸计算
重点和难点
成型零件尺寸计算 计算实例 型腔壁厚底板厚 思考与练习
螺纹型环中径尺寸 D2M+δz=(d2s+d2sScp–b)+δz
螺纹型环大径尺寸 DM+δz=(ds+dsScp–b)+δz
螺纹型环小径尺寸 D1M+δz=(d1s+d1sScp–b)+δz ⑵公制普通螺纹型芯工作尺寸计算 螺纹型芯中径尺寸 d2M-δz=(D2s+D2sScp+b)-δz 螺纹型芯大径尺寸 dM-δz=(Ds+DsScp+b)-δz
型芯大端尺寸: lM=[ls+lsScp+(3/4)Δ ]-δz 型芯小端尺寸: lM小=[lM–(1/4~1/2)Δ ]-δz
第三章 塑料模设计及制造基础
§3.3.3 成型零件的尺寸计算
五、型腔深度和型芯高度计算
3.型腔深度尺寸计算(平均值法)
目的与要求 重点和难点
2014年4月27日
已知:塑件尺寸Hs-Δ 按平均值计算方法可得:
第三章 塑料模设计及制造基础
成型零件尺寸计算 计算实例 型腔壁厚底板厚 思考与练习
小型塑件的模具磨损对塑件影响较大。
第三章 塑料模设计及制造基础
§3.3.3 成型零件的尺寸计算
二、影响塑件尺寸公差的因素
3.塑件的成型收缩δs
目的与要求 重点和难点
2014年4月27日
⑴成型收缩率S:室温下塑件尺寸b与模具尺寸c的相对差值。 S =(c-b)/ c 模具型腔在室温下的尺寸:c=b+S³b ⑵影响塑件收缩的因素(产生偶然误差) ‴塑料品种 ‴塑件特点 ‴模具结构
按平均值计算方法可得:
δz δc Δ Δ L M (L s - ) (L s - ) Scp 2 2 2 2
整理得:
3 L M L s L s Scp - 4
3 z 标注制造公差后得: L M (L s L sScp - ) 0 4
第三章 塑料模设计及制造基础
第三章 塑料模设计及制造基础
2014年4月27日
目的与要求 重点和难点
知之者不如好之者,
好之者不如乐知者。
——孔子《论语》
成型零件尺寸计算 计算实例 型腔壁厚底板厚 思考与练习
第三章 塑料模设计及制造基础
目的与要求:
目的与要求 重点和难点
2014年4月27日
1.会运用公式计算成型零件工作部分的尺寸,会
DM=[D+DScp-(3/4)Δ ]+δ z
=[40+40³0.008-(3/4)³0.34]+0.062
⑵凸台宽度:B=10-0.20 查表得δz=0.043
BM=[10+10³0.008-(3/4)³0.20]+0.043
⑶凸台半径:R1=5-0.10
查表得δz =0.03
R1M=[5+5³0.008-(3/4) ³0.10]+0.03 ⑷外形高度:H1=24-0.28 查表得δz=0.052 H1M=[24+24³0.008-(2/3)³0.28]+0.052
第三章 塑料模设计及制造基础
§3.3.3 成型零件的尺寸计算
三、成型零件尺寸计算方法
‴塑件与成型零件尺寸标注方法:
目的与要求 重点和难点
2014年4月27日
轴类尺寸采用基轴制,标负差 孔类尺寸采用基孔制,标正差
成型零件尺寸计算 计算实例 型腔壁厚底板厚 思考与练习
中心距尺寸公差带对称分布,标正负差
选用表中的数据确定型腔的壁厚和底板厚度;
成型零件尺寸计算 计算实例 型腔壁厚底板厚 思考与练习
2.会分析模具零件的受力情况。
重点和难点: 掌握公式运用及选用表中参数
第三章 塑料模设计及制造基础
§3.3.3 成型零件的尺寸计算
一、成型零件的工作尺寸
目的与要求 重点和难点
2014年4月27日
成型零件工作尺寸包括:‴型芯和型腔的径向尺寸 ‴型芯和型腔的深度尺寸 ‴中心距尺寸
平均收缩率Scp
模具制造公差δz= Δ /3
成型零件尺寸计算 计算实例 型腔壁厚底板厚 思考与练习
z HM (H s ) (L s )S cp 2 2 2
整理得:
H M H s H sScp –
2 3
标注公差后得: H M (H s H s Scp
成型零件尺寸计算 计算实例 型腔壁厚底板厚 思考与练习
‴成型方法及工艺条件(料筒温度、注射压力、注射
速度、模具温度)
第三章 塑料模设计及制造基础
§3.3.3 成型零件的尺寸计算
二、影响塑件尺寸公差的因素
3.塑件的成型收缩δs
目的与要求 重点和难点
2014年4月27日
⑶成型收缩偏差δs产生的原因: 系统误差:计算收缩率与实际收缩的差异 偶然误差:成型时工艺的波动、材料批号的改变等 δs=(Smax-Smin) ³b
2 z ) 0 3
第三章 塑料模设计及制造基础
§3.3.3 成型零件的尺寸计算
五、型腔深度和型芯高度计算
4.型芯高度尺寸计算
目的与要求
2014年4月27日
标注公差后得:
重点和难点
2 0 h M (h s h s Scp ) - z 3
成型零件尺寸计算 计算实例 型腔壁厚底板厚 思考与练习
第三章 塑料模设计及制造基础
§3.3.3 成型零件的尺寸计算
二、影响塑件尺寸公差的因素
2.成型零件的磨损δc
目的与要求 重点和难点
2014年4月27日
磨损量的大小取决于塑料品种、模具材料及热处理。 小批量生产时,δc取小值,甚至可以不考虑。 玻璃纤维塑料磨损大,δc应取大值。 模具材料耐磨,表面强化好,δc应取小值。 垂直于脱模方向的模具表面不考虑磨损。 平行于脱模方向的模具表面要考虑磨损。
模具活动成型零件和配合间隙的变化会引起塑件尺寸的变化
成型零件尺寸计算 计算实例 型腔壁厚底板厚 思考与练习
5.水平飞边的波动δf
压缩模飞边厚度受成型工艺条件变化的影响,从而影响塑件 的高度尺寸,而压注模和注射模的飞边较小。
第三章 塑料模设计及制造基础
§3.3.3 成型零件的尺寸计算
三、成型零件尺寸计算方法
§3.3.3 成型零件的尺寸计算
四、型腔和型芯径向尺寸计算
2.型芯径向尺寸计算
目的与要求 重点和难点
2014年4月27日
标注公差后得:
3 0 l M (l s lsScp ) -z 4
成型零件尺寸计算 计算实例 型腔壁厚底板厚 思考与练习
‴式中Δ 前的系数可取在1/2~3/4之间
‴有脱模斜度时径向尺寸确定 当脱模斜度不包括在塑件公差范围内时:
螺纹型芯小径尺寸 d1M-δz=(D1s+D1sScp+b)-δz
第三章 塑料模设计及制造基础
§3.3.3 成型零件的尺寸计算
六、中心距与孔边距的计算
8.螺纹成型件的尺寸计算
目的与要求
2014年4月27日
⑶螺距工作尺寸计算
重点和难点
成型零件尺寸计算 计算实例 型腔壁厚底板厚 思考与练习
螺纹型芯螺距:
7.型芯上的孔边距计算
目的与要求 重点和难点
2014年4月27日
LM (Ls LsScp /24) z /2
成型零件尺寸计算 计算实例 型腔壁厚底板厚 思考与练习
第三章 塑料模设计及制造基础
§3.3.3 成型零件的尺寸计算
六、中心距与孔边距的计算
8.螺纹成型件的尺寸计算
目的与要求
模具制造公差占塑件总公差的三分之一左右:δz=Δ/3
成型零件尺寸计算 计算实例 型腔壁厚底板厚 思考与练习
2.成型零件的磨损δc 中小型塑件模具:δc=Δ/6
大型塑件模具:δc<Δ/6 成型零件磨损的原因: ‴塑件脱模时的摩擦(型腔变大、型芯变小、中心距尺寸不变) ‴料流的冲刷 ‴腐蚀性气体的锈蚀 ‴模具的打磨抛光
成型零件尺寸计算 计算实例 型腔壁厚底板厚 思考与练习
第三章 塑料模设计及制造基础
§3.3.3 成型零件的尺寸计算
七、实例(Example)
1.型腔尺寸计算
目的与要求 重点和难点
2014年4月27日
⑴外形直径:D=40-0.34
查表得δz=0.062
成型零件尺寸计算 计算实例 型腔壁厚底板厚 思考与练习
6.凹模上的孔边距计算(平均值法)
此时凹模存在单边磨损,最大磨损量为δc/2。 塑件尺寸Ls±Δ /2 模具磨损量δc=Δ /6 平均收缩率Scp 模具制造公差δz=Δ /3