JBT59261991振动时效工艺参数选择及技术要求
jbt 5926-1991 振动时效工艺参数选择及技术要求.doc

jbt 5926-1991 振动时效工艺参数选择及技术要求JB/T5926-91振动时效工艺参数选择及技术要求1991-11-30公布1992-07-01实施1主题内容与适用范围本标准规定了振动时效工艺参数旳选择及技术要求和振动时效效果评定方法.本标准适用于材质为碳素结构钢,低合金钢,不锈钢,铸铁,有色金属(铜,铝,锌其合金)等铸件,锻件,焊接件旳振动时效处理.2术语2.1扫频曲线---将激振器旳频率缓慢地由小调大旳过程称扫频.随着频率旳变化,工件振动响应发生变化.反映振动响应与频率之间关系旳曲线,称扫频曲线,如A---f称振幅频率曲线;a-f称加速度频率曲线.注:A表示振幅,a表示加速度,f表示频率.2.2激振点---振动时效时,激振器在工件上旳夹持点称激振点.3工艺参数选择及技术要求3.1首先应分析推断出工件在激振频率范围内旳振型.3.2振动时效装置(以下简称装置)旳选择.3.2.1装置旳激振频率应大于工件旳最低固有频率.3.2.2装置旳最大激振频率小于工作旳最低固有频率时,应采取倍频(或称分频)降频等措施.3.2.3装置旳激振力应能使工件内产生旳最大动应力为工作应力旳1/3~2/3.3.2.4装置应具备自动扫频,自动记录扫频曲线,指示振动加速度值和电机电流值旳功能.稳速精度应达到+lr/min.3.3支撑工件,装卡激振器和拾振器3.3.1为了使工作处于自由状态,应采纳三点或四点弹性旳支撑工件,支撑位置应在主振频率旳节线处或附近.为使工件成为两端简支或悬臂,那么应采纳刚性装夹.3.3.2激振器应刚性地固定在工件旳刚度较弱或振幅较大处,但不准固定在工件旳强度和刚度专门低旳如大旳薄板平面等部位,固定处应平坦.3.3.3悬臂装夹旳工件,一般应掉头进行第二次振动时效处理.特大工件,在其振动响应薄弱旳部位应进行补振.3.3.4拾振器应固装在远离激振器同时振幅较大处.3.4工件旳试振3.4.1不同意试振旳工件存在缩孔,夹渣,裂纹,虚焊等严峻缺陷.3.4.2选择激振器偏心档位,应满足使工件产生较大振幅和装置只是载旳要求,必要时先用手动旋钮查找合适旳偏心档位.3.4.3第一次扫频,记录工件旳振幅频率(A-f)曲线,测出各阶共振频率值,节线位置,波峰位置.3.4.4必要时通过调整支撑点,激振点和拾振点旳位置来激起较多旳振型.3.4.5测定1-3个共振峰大旳频率在共振时旳动应力峰值旳大小.3.4.6选择动应力大,频率低在共振频率作为主振频率.3.4.7按主振型对支撑,拾振位置进行最后调整.注:主振频率旳振型称为主振型.3.5工件旳主振3.5.1在亚共振区内选择主振峰峰值旳1/3-2/3所对应旳频率主振工件.3.5.2主振时装置旳偏心档位应使工件旳动应力峰值达到工作应力旳1/3-2/3,并使装置旳输出功率不超过额定功率旳80%.3.5.3进行振前扫频,记录振前旳振幅时刻(A-f)曲线.3.5.4主振工件,记录振幅频率(A-t)曲线.3.5.5起振后振幅时刻(A-t)曲线上旳振幅上升,然后变平或上升后下降然后再变平,从变平开始稳定3-5犿犻狀为振动截止时刻,一般累计振动时刻不超过40犿犻狀.3.5.6进行振后扫频,记录振幅频率(A-f)曲线.3.5.7批量生产旳工件可不作振前,振后扫频.3.5.8有些工件可作多点激振处理,有些工件可用附振频率作多频共振辅助处理.是否调整支撑点,拾振点位置视工件而定.注:主振频率以外旳各共振频率称为附振频率.3.5.9工件存在如夹渣,缩孔,裂纹,虚焊等缺陷,在振动时效中这类缺陷专门快以裂纹扩展旳形式出现时,应立即中断时效处理.工件排除缺陷后,同意重新进行振动时效.3.6振动时效工艺卡和操作记录卡3.6.1批量生产旳工件进行振动时效处理时,必须制订“振动时效工艺卡”,操作者必须严格执行并填写“振动时效操作记录卡”在工件上作已振标记.3.6.2“振动时效工艺卡”应按3.1-3.5条旳要求,试验三件以上,找出规律后制订.3.6.3“振动时效工艺卡”和“振动时效操作记录卡”旳内容和格式分别参照附录犅和附录犆.3.7铸件振动时效时,应使动应力方向尽量与易变形方向一致.3.8制订焊接件振动时效工艺时,应明确工件上承受力旳要紧焊缝和联系焊缝.振动处理中,其振动方向应使工件承受力旳要紧焊缝处旳动应力最大或较大.4振动时效工艺效果评定方法4.1参数曲线观测法4.1.1振动处理过程中从振幅时刻(A-f)曲线和振前,振后振幅频率(A-f)曲线旳变化来监测.4.1.2出现以下情况之一时,即可判定为达到振动时效工艺效果.a振幅时刻(A-t)曲线上升后变平.b振幅时刻(A-t)曲线上升后下降然后变平.c振幅频率(A-f)曲线振后旳比振前旳峰值升高.d振幅频率(A-f)曲线振后旳比振前旳峰值点左移.e振幅频率(A-f)曲线振后旳比振前旳带宽变窄.4.1.3振动处理过程中,假如不出现4.1.2条中所列旳任一情况时,应重新调整振动参数,按上述规定旳条款再进行时效处理后,重新检验.4.1.4制订有“振动时效工艺卡”旳批量生产旳工件,在振动时效时,推举用4.1.2条旳a,b款中只要出现一种情况,便可判定为达到振动时效工艺效果旳方法来检验,并不再作下述检验.4.2残余应力检测法4.2.1推举使用盲孔法,也可使且X射线衍射法.4.2.1.1被振工作振前,振后旳残余应力测定点数均应大于5个点.4.2.1.2用振前,振后旳应力平均值(应力水平)来计算应力消除率,焊件应大于30%,铸锻件应大于20%.4.2.13用振前,振后旳最大应力与最小应力之差值来衡量均化程度,振后旳计算值应小于振前旳计算值.4.3精度稳定性检测法4.3.1以要求精度稳定性为主旳工件,振后应进行精度稳定性检验.a精加工后检验.b长期放置定期检验静尺寸稳定性,在放置15d时第一次检验,以后每隔30d检验一次,总旳静置时刻半年以上.c在动载荷后检验.应依照具体情况选用上述条款.4.3.2各种检验结果均应达到设计要求.附录A振动时效工艺中动应力选择与振动时效对工件疲劳寿命阻碍分析(补充件)1振动时效工艺中动应力旳选择与分析动应力是振动时效工艺旳一项最要紧参数.实验证明:在一定范围内动应力越大,被处理工件上产生旳应变释放量也越大,消除应力旳效果也越好,动应力过大将有可能造成工件旳损伤或降低疲劳寿命.因此在本标准中以工作应力来确定动应力.即:σ动=(1/3~2/3)σ工作在设计时,工作应力(σ工作)是差不多确定旳,或和应变测试技术获得,在那个地点应以在工作状态下工件上最大应力点旳应力作为工作应力.当我们按上述方法来确定动应力(σ动)时,就能够保证被振工作既能消除应力又不遭到损坏.由于工件结构比较复杂旳结构,在不同受力状态下各点旳动应力不同,因此在实际操作时,应选择结构危险点(应力集中点),做动应力监测,以保证动应力量值旳可靠.2振动时效对工件疲劳寿命阻碍旳分析振动时效其工作状态是对工件施加周期性旳作用力,这如同疲劳荷载一样,依照线性累积损伤理论,必定对工件造成一定旳疲劳损伤.但另一方面,由于低应力振动处理后残余应力得到下降,又必定提高工件旳疲劳寿命.我国振动时效工作者,通过大量旳试验给出了振动时效对工件疲劳寿命旳关系曲线(如图A1所示).图中:N-σ为寿命-应力坐标;N-σ动为寿命-动应力坐标;σ工作为实际工作中工件中最大应力;η工作为在工作应力作用下旳疲劳寿命.从图中可见,当动应力σ动小于A点时,振动时效能够提高疲劳寿命;当动应力σ动大于A点时,振动时效将降低疲劳寿命;当采纳工作荷载处理时,振动时效降低疲劳寿命旳数值(B点)就等于振动时效处理时旳循环数.因此,本标准中选动应力为工作应力旳1/3-2/3是可不能对焊接件造成任何疲劳损伤旳,相反还能够提高工件旳疲劳寿命.。
焊接构件振动时效工艺参数和技术要求

应该在之前发生的第一骨科VSR考虑采用振动骨科特殊的情况下,过大的变形部件。
预应力或焊接辅助工具系统组件和工具,以增加当地的材料做强制性的防变形,振动时效处理的塑料或结合爬行速度,减少焊接变形的过程。预应力反变形量应认为是不可避免的,搬迁后的振动技术端和预应力或辅助工具,以及局部拉应力,弹性回跳的成员增加的不利影响。
5个工艺参数和技术要求
5.1参数确定指导方针
在正常情况下,振动参数应该是在特定的焊接构件的工作条件,并分析和确定的部件的基础上,判断振动模式,可能会发生的激发频率的范围内。
材料的重要组成部分,做实际的边界条件下的动态应力有限元分析,结构部件的固有频率和模式的范围为16200Hz的解决,以确定的支持和激励点的位置,并选择 - 安装点。
(σB强度σs)/ 3≤σ≤σD/ 3 ..................................... ................. (1)
公式:
σD动态应力幅;
强度σs是材料的屈服强度;
σb为材料的拉伸强度。
当均匀部件的几何形状,当嵌合应力集中系数为小的,优选的上限的值(动态应力抗拉强度和/ 3);部件几何不均匀关节应力集中系数比的控制部件的振幅相关的动态应力的应力集中是大,动态应力可以除去限制(σB强度σs)/ 3。
3.6主振频率,的附加振动频率(主要的和额外的振动频率)
的频率范围内的激发装置,造成部件共振响应的频率低的频率,频率的位移幅值被称为主频率f1,其余的附加频率FX。符号F1,F2 ...,单位为Hz;符号在转N1,N2。
3.7扫描和扫描曲线(频率扫描和曲线)
修正偏心的频率的激振力,由一个小的过程中,被称为扫描。随着频率的变化,组分的改变,以反映之间的关系被称为扫描曲线的振动响应和频率曲线的振动响应。如AF称为振幅 - 频率曲线,自动对焦称为加速度 - 频率曲线;振动时效设备绘制加速度 - 速度(AN)曲线。
时效振动

振动时效工艺振动时效工艺的制作分以下几个部分:(1)分析工件可能出现的振型,找出合理地支撑位置,激振器装卡位置.(2)动应力的测试.(3)振动时效设备的使用.(4)残余应力和动应力测试.(1)分析:根据振动时效工件可能出现的振型,合理地支撑工件及装卡激振器的位置.(一).梁型件(如图50)多以弯振型较多,支撑一般应用4点距一端2/9和7/9处.激振器一般装卡在中间波峰附近,加速度计安装在一端的波峰附近.(二).板型件(如图51)一般采用3点(互成120度)或4点(对角)支撑再边缘处,激振器一般装卡在两橡胶垫中间边缘波峰附近,加速度计安装在一侧两橡胶垫中间边缘的波峰附近.(三).圆板型件(如图52)一般采用3点(互成120度)或4点(对角)支撑再边缘处,激振器一般装卡在两橡胶垫中间边缘波峰附近,加速度计安装在一侧两橡胶垫中间边缘的波峰附近.(四).方箱型件(如图53)一般采用3点支撑再较长的边缘处,激振器一般装卡在上边钢性较大的边缘波峰附近,加速度计安装在边缘的波峰附近.上述只是简要的介绍一般常规工件的支撑与激振器的装卡位置,具体情况还需要反复试验(利用手动工作模式)来找出合适的振动时效工艺参数.(2)动应力的测试.测试动应力所用的仪器设备: 1)动态电阻应变仪(如图54),2)测试方法 1.贴片,沿波峰--波节--波峰的振型方向依次贴6--10片.2.计算:可用虎克定律计算动应力值.(3)振动时效设备的使用:(一)准备工作:1.振动时效处理前要准备好做弹性支撑的橡胶垫(或用旧轮胎代替)。
被振工件与激振器连接用的专用卡具。
2.将被振工件水平放置在橡胶垫上。
一般情况下,要根据工件的几何形状合理地选择好支撑点? 支撑点应选择在波节处(工件在自由振动时振幅最小处)。
3.激振器的安装:将激振器安装在被振工件的被振工件的波峰处(工件在自由振动时振幅最大处)。
激振器底座与工件应刚性连接,接触面要良好。
并用专用卡具卡紧,然后将偏心调到1档。
岔管时效处理方案 - 振动时效
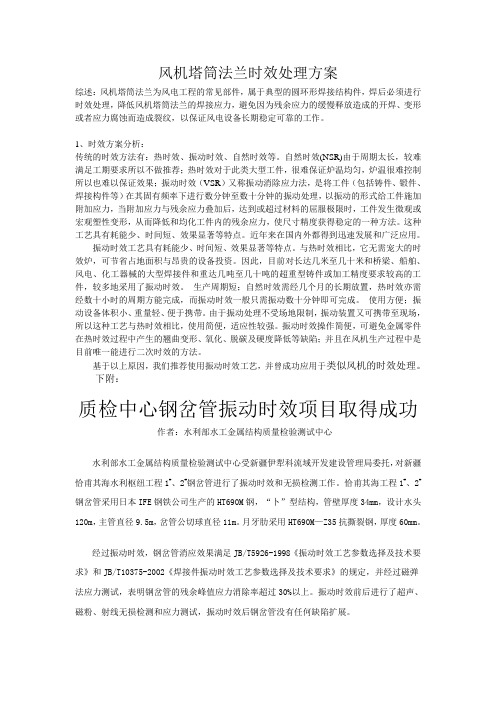
风机塔筒法兰时效处理方案综述:风机塔筒法兰为风电工程的常见部件,属于典型的圆环形焊接结构件,焊后必须进行时效处理,降低风机塔筒法兰的焊接应力,避免因为残余应力的缓慢释放造成的开焊、变形或者应力腐蚀而造成裂纹,以保证风电设备长期稳定可靠的工作。
1、时效方案分析:传统的时效方法有:热时效、振动时效、自然时效等。
自然时效(NSR)由于周期太长,较难满足工期要求所以不做推荐;热时效对于此类大型工件,很难保证炉温均匀,炉温很难控制所以也难以保证效果;振动时效(VSR)又称振动消除应力法,是将工件(包括铸件、锻件、焊接构件等)在其固有频率下进行数分钟至数十分钟的振动处理,以振动的形式给工件施加附加应力,当附加应力与残余应力叠加后,达到或超过材料的屈服极限时,工件发生微观或宏观塑性变形,从而降低和均化工件内的残余应力,使尺寸精度获得稳定的一种方法。
这种工艺具有耗能少、时间短、效果显著等特点。
近年来在国内外都得到迅速发展和广泛应用。
振动时效工艺具有耗能少、时间短、效果显著等特点。
与热时效相比,它无需宠大的时效炉,可节省占地面积与昂贵的设备投资。
因此,目前对长达几米至几十米和桥梁、船舶、风电、化工器械的大型焊接件和重达几吨至几十吨的超重型铸件或加工精度要求较高的工件,较多地采用了振动时效。
生产周期短;自然时效需经几个月的长期放置,热时效亦需经数十小时的周期方能完成,而振动时效一般只需振动数十分钟即可完成。
使用方便;振动设备体积小、重量轻、便于携带。
由于振动处理不受场地限制,振动装置又可携带至现场,所以这种工艺与热时效相比,使用简便,适应性较强。
振动时效操作简便,可避免金属零件在热时效过程中产生的翘曲变形、氧化、脱碳及硬度降低等缺陷;并且在风机生产过程中是目前唯一能进行二次时效的方法。
基于以上原因,我们推荐使用振动时效工艺,并曾成功应用于类似风机的时效处理。
下附:质检中心钢岔管振动时效项目取得成功作者:水利部水工金属结构质量检验测试中心水利部水工金属结构质量检验测试中心受新疆伊犁科流域开发建设管理局委托,对新疆恰甫其海水利枢纽工程1#、2#钢岔管进行了振动时效和无损检测工作。
振动时效培训资料
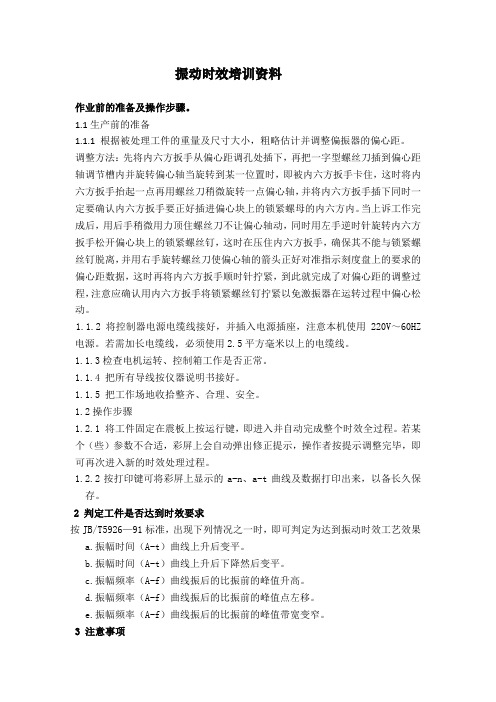
振动时效培训资料作业前的准备及操作步骤。
1.1生产前的准备1.1.1 根据被处理工件的重量及尺寸大小,粗略估计并调整偏振器的偏心距。
调整方法:先将内六方扳手从偏心距调孔处插下,再把一字型螺丝刀插到偏心距轴调节槽内并旋转偏心轴当旋转到某一位置时,即被内六方扳手卡住,这时将内六方扳手抬起一点再用螺丝刀稍微旋转一点偏心轴,并将内六方扳手插下同时一定要确认内六方扳手要正好插进偏心块上的锁紧螺母的内六方内。
当上诉工作完成后,用后手稍微用力顶住螺丝刀不让偏心轴动,同时用左手逆时针旋转内六方扳手松开偏心块上的锁紧螺丝钉,这时在压住内六方扳手,确保其不能与锁紧螺丝钉脱离,并用右手旋转螺丝刀使偏心轴的箭头正好对准指示刻度盘上的要求的偏心距数据,这时再将内六方扳手顺时针拧紧,到此就完成了对偏心距的调整过程,注意应确认用内六方扳手将锁紧螺丝钉拧紧以免激振器在运转过程中偏心松动。
1.1.2将控制器电源电缆线接好,并插入电源插座,注意本机使用220V~60HZ电源。
若需加长电缆线,必须使用2.5平方毫米以上的电缆线。
1.1.3检查电机运转、控制箱工作是否正常。
1.1.4 把所有导线按仪器说明书接好。
1.1.5 把工作场地收拾整齐、合理、安全。
1.2操作步骤1.2.1 将工件固定在震板上按运行键,即进入并自动完成整个时效全过程。
若某个(些)参数不合适,彩屏上会自动弹出修正提示,操作者按提示调整完毕,即可再次进入新的时效处理过程。
1.2.2按打印键可将彩屏上显示的a-n、a-t曲线及数据打印出来,以备长久保存。
2 判定工件是否达到时效要求按JB/T5926—91标准,出现下列情况之一时,即可判定为达到振动时效工艺效果a.振幅时间(A-t)曲线上升后变平。
b.振幅时间(A-t)曲线上升后下降然后变平。
c.振幅频率(A-f)曲线振后的比振前的峰值升高。
d.振幅频率(A-f)曲线振后的比振前的峰值点左移。
e.振幅频率(A-f)曲线振后的比振前的峰值带宽变窄。
振动时效在推土机后桥箱焊接过程中的应用
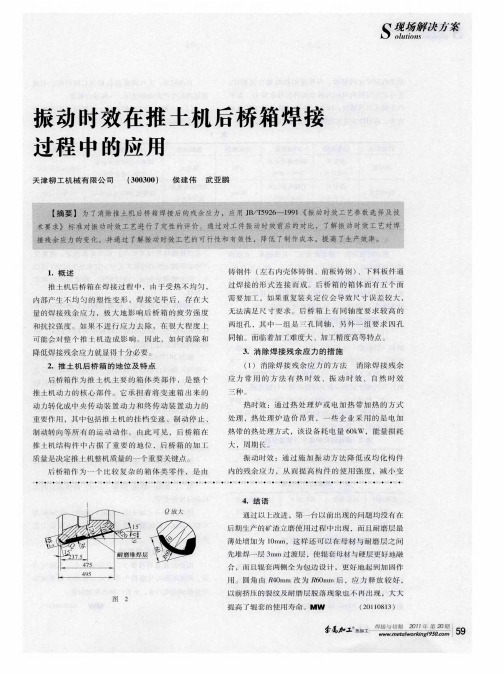
消 除 残 余应 力 自然 时效 无投 资
2 % ~1 % 0
一 芷
无 能 耗
不 受 限 制
无 污 染
4 .振 动 时效 的原 理
振 动 时 效 是 由 “ 击 松 弛法 ” 发 展 而 来 ,在 激 振 锤
按 照 机 械行 业 标 准 J / 5 2 - 19 B T 9 6 9 1《 动 时 效 振
MW ( 010 1 2 1 8 5)
6: 0
: C 磊 工 o 参 。 n r z
6 .后桥 箱 振 动 时 效 的 工 艺 要 求
后 桥 箱 的 振 动 时 效 是 采 用 振 动 时 效 仪 进 行 的 时
效处 理 ,该设 备 的型 号是 s —Jl K。先将 1 件 立 MK J0 一 起来 ,使工件 的 一侧 壳 休 着 地 ,使用 没备 的 夹具 灾
振 动时 效 具 有 投 资 少 、占地 面 积 小 、去除 应 力
_ 参数选 择 及 技 术 要 求 》 第 3 6条 规 定 ,批量 生 T艺 . 产时 必须制 定振 动时效 工艺 卡 ,要 求 至少试验 3件以
一
器 的剧期 性外 力 ( 激振 力 )的 作用 下 ,使 工 件 共振 ,
金 属原子错位 和品格 滑移 ,从 而将 残余应 力 释放。它 是一种 常温时效工 艺 ,可使 金属 结构 的焊接 残余 应力
s
决 案 方
彤及稳 定尺 寸 的精 度 ,
传 统 的 热 时 效 方 法 相 比,
自然 时 效 :工 件 需 要 存 放 相 当 长 的 时 间 ,不 能
它可 以在极 短 的 时 间 内减 少 构 件 的残 余 应 力 ,也 不
振动时效技术要求

2. 工件及激振装置的放置 2.1. 为了便使工件在振动过程中始终处于自由状态,应采用橡胶垫(如橡胶轮胎等)作支撑。 2.2. 激振装置应刚性地固定在工件刚度较强或振幅较大处,不准固定在大而薄的平面等刚性较
差的部位,固定激振装置处应平整。
率不超过额定功率的 80%。 4.3. 振前进行扫频,记录振幅频率(a-t)曲线。 4.4. 主振工件,记录振幅时间(a-t)曲线。 4.5. 起振后振幅时间(a-t)曲线上的振幅上升,然后变平或上升后下降然后再变平,从变平开
始稳定 3~5min 为振动截止时间。 4.6. 振后进行扫频,记录振幅频率(a-n)曲线。 4.7. 必要时可作多点激振处理,也可用附振频率(即主振频率以外的各共振频率)作多频共振
曲线等。
6.操作者
由具有高中以上文化,经过专业培训合格,能严格执行工艺文件的人员担当。
7.振动时效实施
7.1 工件准备
a) 工件表面应不存在裂纹、虚焊、夹渣等严重缺陷。
b) 工件支撑采用随机附带还胶垫或废橡胶外胎在节点处作弹性支撑,应尽可能采用二点或三
点支撑,必要时也可用四点支撑,支撑应保证工件任一点不接触地面。
并保证其电流值低于扫频时的 3/4,否则应减少加速度值开激振力,在线打印加速度-时间
曲线。
b) 观察加速度值,若有上升后最终变平,则认为时效效果基本达到,如 20min 尚未有上升变
化,则应提高加速度值或激振力。
c) 继续对附振频率进行时效处理。
d) 振后自动扫描,记录α-n 曲线。
7.3.3 振动时效效果评定
3.4. 必要时可通过调整支撑点、激振点和拾振点的位置来激起较多的振型。 3.5. 测定 1~3 个共振峰较大的频率在共振时的动应力峰值的大小,选择动应力大、频率低的共
振动时效效果的判定方法

第六章振动时效效果的判定方法检验振动时效的效果实际上就是检验工件中残余应力是否得以消除和均化,目前对残余应力的测试方法很多,但总的分为两大类。
一类是定量测试:如盲孔法、X射线法、磁测法、喷砂打孔法、切割法、套环法等。
一类是定性测试:如振动参数曲线法、尺寸精度稳定性法等。
本章着重一讲振动曲线法,其它方法都有专门介绍,在此就不再详谈。
第一节常用的几种残余应力测试法1.切割法、套环法:这两种方法的基本原理是一样的,就是在被测点附近,先贴上应变片,然后再用手锯或铣床,在这一点附近切割出方格线,使之与邻近部分分开以释放残余应力,并用应变片测出应变量,再计算出该点处的残余应力值大小。
2.盲孔法:切割法和套环法具有较大的破坏性,因此目前应用较为广泛的残余应力测试方法是钻盲孔法。
钻孔法测量残余应力就是在被测点上钻一小孔,使被测点的应力得到部分或全部释放,并由事先贴在小孔周围的应变计测得释放的应变量,再根据弹性力学原理计算出残余应力。
钻孔的直径和深度都不大,不会影响被测构件的正常使用。
并且这种方法具有较好的精度,因此它已成为应用比较广泛的残余应力测试方法之一。
3.X射线法:X射线法测应力的基本原理是,利用X射线穿透晶粒时产生的衍射现象。
在弹性应变作用下,引起晶格间距变化,使衍射条纹产生位移,根据位移的变化即可计算出应力来。
X射线法测应力的特点如下:①它是一种无损测试方法。
②它测量的仅仅是弹性应变而不包括塑应变(因为工件塑性变形时其晶面间距并不改变,不会引起衍射线的位移)。
③被测面直径可以小到1~2mm。
因此可以用于研究一点应力和梯度变化较大的应力分布。
④由于穿透能力的限制,一般只能测深度在10um左右的应力,所以只是表面应力。
⑤对于能给出清晰衍射峰的材料,例如退火后细晶粒材料,本方法可达10Mpa的精度,但对于淬火硬化或冷加工材料,其测量误差将增大许多倍。
4.磁测法:磁测法测量残余应力是近年来发展起来的一种新方法,它具有较大的发展前途,设备简单、使用方便,它不仅可以测残余应力也可以测载荷作用下的应力。
操作说明
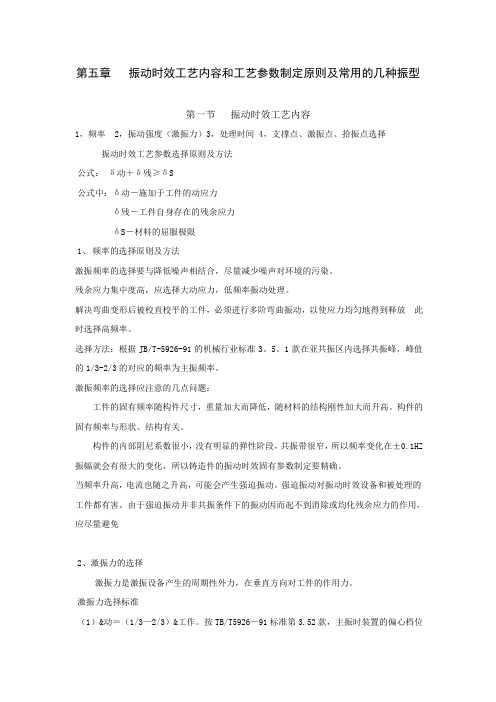
第五章振动时效工艺内容和工艺参数制定原则及常用的几种振型第一节振动时效工艺内容1,频率 2,振动强度(激振力)3,处理时间 4,支撑点、激振点、拾振点选择振动时效工艺参数选择原则及方法公式:δ动+δ残≥δS公式中:δ动-施加于工件的动应力δ残-工件自身存在的残余应力δS-材料的屈服极限1、频率的选择原则及方法激振频率的选择要与降低噪声相结合,尽量减少噪声对环境的污染。
残余应力集中度高,应选择大动应力,低频率振动处理。
解决弯曲变形后被校直校平的工件,必须进行多阶弯曲振动,以使应力均匀地得到释放此时选择高频率。
选择方法:根据JB/T-5926-91的机械行业标准3。
5。
1款在亚共振区内选择共振峰,峰值的1/3-2/3的对应的频率为主振频率。
激振频率的选择应注意的几点问题:工件的固有频率随构件尺寸,重量加大而降低,随材料的结构刚性加大而升高。
构件的固有频率与形状、结构有关。
构件的内部阻尼系数很小,没有明显的弹性阶段,共振带很窄,所以频率变化在±0.1HZ 振幅就会有很大的变化,所以铸造件的振动时效固有参数制定要精确。
当频率升高,电流也随之升高,可能会产生强迫振动。
强迫振动对振动时效设备和被处理的工件都有害。
由于强迫振动并非共振条件下的振动因而起不到消除或均化残余应力的作用,应尽量避免2、激振力的选择激振力是激振设备产生的周期性外力,在垂直方向对工件的作用力。
激振力选择标准(1)&动=(1/3—2/3)&工作。
按TB/T5926—91标准第3.52款,主振时装置的偏心档位应是工件的动应力峰值达到工作应力1/3—2/3,并使装置的输出功率不超过额定功率的80% 。
因为只有在工作应力的1/3—2/3处工件才不会受到损伤,同时也能提高疲劳寿命。
若&动=&工作构件不但受到损伤,而且疲劳寿命下降。
(2)动应力是使构件残余应力消除的必要条件。
在亚共振频率下,振动具有放大动应力的作用,达到加速残余应力消除的目的,为了在时效中,对构件不造成损伤,根据经验动应力可适当控制在:铸铁件±25--±40N/m㎡铸铁淬火导轨件±15N/m㎡铸刚件±35--±50N/ m㎡焊接件±50--±80N/ m㎡也可根据动态电阻应变仪测定,用公式计算。
结构通用工艺----振动时效
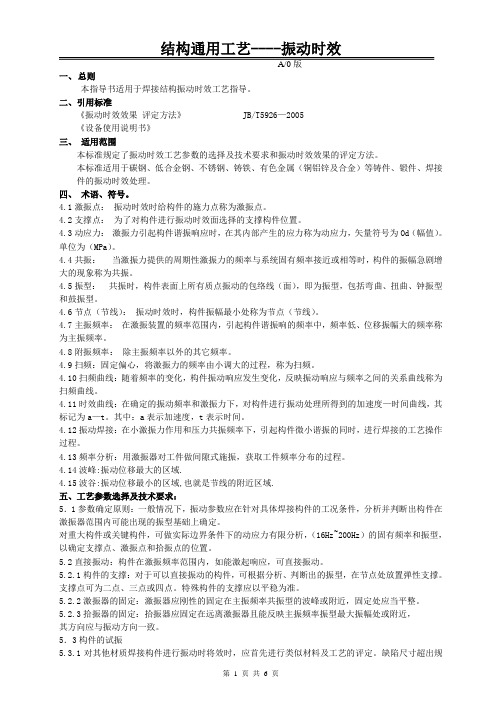
一、总则本指导书适用于焊接结构振动时效工艺指导。
二、引用标准《振动时效效果评定方法》 JB/T5926—2005《设备使用说明书》三、适用范围本标准规定了振动时效工艺参数的选择及技术要求和振动时效效果的评定方法。
本标准适用于碳钢、低合金钢、不锈钢、铸铁、有色金属(铜铝锌及合金)等铸件、锻件、焊接件的振动时效处理。
四、术语、符号。
4.1激振点:振动时效时给构件的施力点称为激振点。
4.2支撑点:为了对构件进行振动时效面选择的支撑构件位置。
4.3动应力:激振力引起构件谐振响应时,在其内部产生的应力称为动应力,矢量符号为Od(幅值)。
单位为(MPa)。
4.4共振:当激振力提供的周期性激振力的频率与系统固有频率接近或相等时,构件的振幅急剧增大的现象称为共振。
4.5振型:共振时,构件表面上所有质点振动的包络线(面),即为振型,包括弯曲、扭曲、钟振型和鼓振型。
4.6节点(节线):振动时效时,构件振幅最小处称为节点(节线)。
4.7主振频率:在激振装置的频率范围内,引起构件谐振响的频率中,频率低、位移振幅大的频率称为主振频率。
4.8附振频率:除主振频率以外的其它频率。
4.9扫频:固定偏心,将激振力的频率由小调大的过程,称为扫频。
4.10扫频曲线:随着频率的变化,构件振动响应发生变化,反映振动响应与频率之间的关系曲线称为扫频曲线。
4.11时效曲线:在确定的振动频率和激振力下,对构件进行振动处理所得到的加速度—时间曲线,其标记为a—t。
其中:a表示加速度,t表示时间。
4.12振动焊接:在小激振力作用和压力共振频率下,引起构件微小谐振的同时,进行焊接的工艺操作过程。
4.13频率分析:用激振器对工件做间隙式施振,获取工件频率分布的过程。
4.14波峰:振动位移最大的区域.4.15波谷:振动位移最小的区域,也就是节线的附近区域.五、工艺参数选择及技术要求:5.1参数确定原则:一般情况下,振动参数应在针对具体焊接构件的工况条件,分析并判断出构件在激振器范围内可能出现的振型基础上确定。
振动时效基本工艺方法
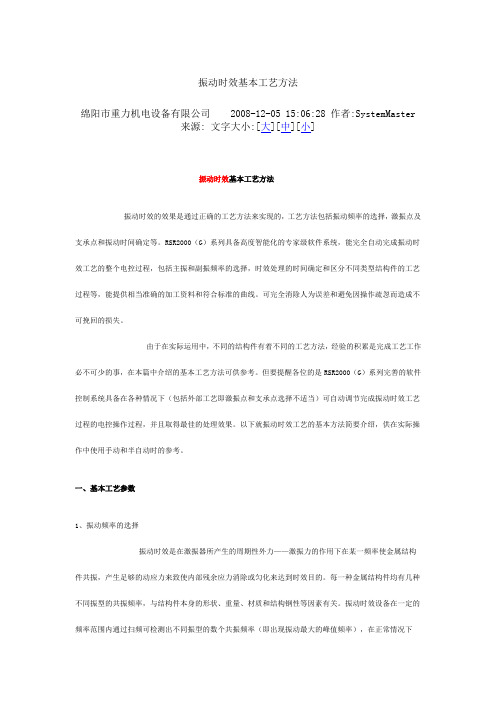
振动时效基本工艺方法绵阳市重力机电设备有限公司 2008-12-05 15:06:28 作者:SystemMaster来源: 文字大小:[大][中][小]振动时效基本工艺方法振动时效的效果是通过正确的工艺方法来实现的,工艺方法包括振动频率的选择,激振点及支承点和振动时间确定等。
RSR2000(G)系列具备高度智能化的专家级软件系统,能完全自动完成振动时效工艺的整个电控过程,包括主振和副振频率的选择,时效处理的时间确定和区分不同类型结构件的工艺过程等,能提供相当准确的加工资料和符合标准的曲线。
可完全消除人为误差和避免因操作疏忽而造成不可挽回的损失。
由于在实际运用中,不同的结构件有着不同的工艺方法,经验的积累是完成工艺工作必不可少的事,在本篇中介绍的基本工艺方法可供参考。
但要提醒各位的是RSR2000(G)系列完善的软件控制系统具备在各种情况下(包括外部工艺即激振点和支承点选择不适当)可自动调节完成振动时效工艺过程的电控操作过程,并且取得最佳的处理效果。
以下就振动时效工艺的基本方法简要介绍,供在实际操作中使用手动和半自动时的参考。
一、基本工艺参数1、振动频率的选择振动时效是在激振器所产生的周期性外力——激振力的作用下在某一频率使金属结构件共振,产生足够的动应力来致使内部残余应力消除或匀化来达到时效目的。
每一种金属结构件均有几种不同振型的共振频率,与结构件本身的形状、重量、材质和结构钢性等因素有关。
振动时效设备在一定的频率范围内通过扫频可检测出不同振型的数个共振频率(即出现振动最大的峰值频率),在正常情况下RSR2000(G)会自动选择最佳的共振频率为主振频率(其振型称为主振振型),为补充主振振型的不足,在5%的情况下还需选择与主振型不同的另一次低共振频率为附振频率(其振型称为附振振型)。
RSR2000(G)系列设备对主振频率和附振频率的选择是由软件完成的,其选择准确性高并且避免了人为因素造成的加工效果不佳等。
振动时效设备的系统参数介绍
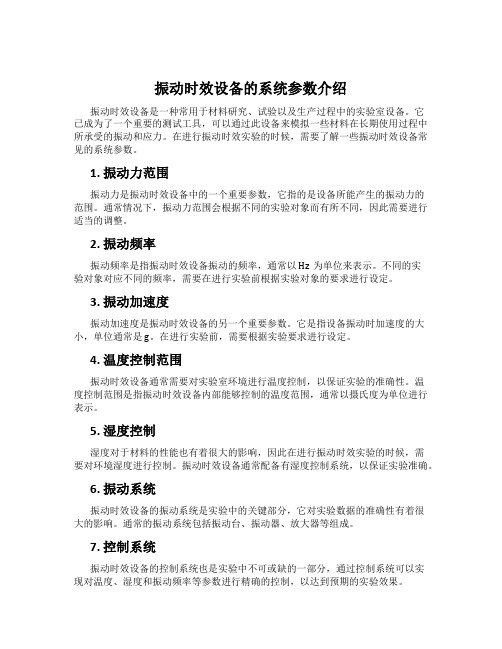
振动时效设备的系统参数介绍振动时效设备是一种常用于材料研究、试验以及生产过程中的实验室设备。
它已成为了一个重要的测试工具,可以通过此设备来模拟一些材料在长期使用过程中所承受的振动和应力。
在进行振动时效实验的时候,需要了解一些振动时效设备常见的系统参数。
1. 振动力范围振动力是振动时效设备中的一个重要参数,它指的是设备所能产生的振动力的范围。
通常情况下,振动力范围会根据不同的实验对象而有所不同,因此需要进行适当的调整。
2. 振动频率振动频率是指振动时效设备振动的频率,通常以 Hz为单位来表示。
不同的实验对象对应不同的频率,需要在进行实验前根据实验对象的要求进行设定。
3. 振动加速度振动加速度是振动时效设备的另一个重要参数。
它是指设备振动时加速度的大小,单位通常是 g。
在进行实验前,需要根据实验要求进行设定。
4. 温度控制范围振动时效设备通常需要对实验室环境进行温度控制,以保证实验的准确性。
温度控制范围是指振动时效设备内部能够控制的温度范围,通常以摄氏度为单位进行表示。
5. 湿度控制湿度对于材料的性能也有着很大的影响,因此在进行振动时效实验的时候,需要对环境湿度进行控制。
振动时效设备通常配备有湿度控制系统,以保证实验准确。
6. 振动系统振动时效设备的振动系统是实验中的关键部分,它对实验数据的准确性有着很大的影响。
通常的振动系统包括振动台、振动器、放大器等组成。
7. 控制系统振动时效设备的控制系统也是实验中不可或缺的一部分,通过控制系统可以实现对温度、湿度和振动频率等参数进行精确的控制,以达到预期的实验效果。
8. 实验容量实验容量是指振动时效设备能够同时容纳的实验件数。
在进行大规模实验的时候,需要选择具有较大实验容量的振动时效设备。
以上是振动时效设备常见的系统参数介绍,这些参数对于保证实验的准确性和可靠性都至关重要。
在实际应用中,需要根据实验对象的要求进行选择,并通过准确的实验数据验证实验结果的准确性。
振动时效报告

构件振动时效处理报告单纽威48寸全焊接球阀消除焊接应力的振动时效处理前言苏州纽威阀门股份有限公司生产的48BWP6球阀门。
根据设计部门的要求,需对阀门进行时效处理,用以消除焊接应力。
由于该球阀是将密封材料装好后在进行外部环焊缝焊接,需焊后进行时效处理。
经该公司相关部门研究决定委托大连理工大学采用振动时效进行处理并进行振前、振后残余应力检测,经与大连理工大学相关技术人员共同探讨,认为方案可行,并于2010年6月对该球阀实施振动时效处理和残余应力检测。
一、振动时效处理对金属构件的作用振动时效是对具有残余应力的金属构件进行振动处理,使构件在共振频率下产生振动。
其原理是将一个具有偏心重块的电机系统(称做激振器)安放在构件上,并将构件用弹性物体支撑,通过控制系统控制变频电机的转数输出动应力产生一定的频率与被振构件频率相等时产生共振,经20-50分钟的振动处理,当这个动应力与构件上各点的残余应力相叠加后,大于材料的屈服极限,则在该点出现局部的塑性变形,因而应力得到释放。
所以从原理上来说,降低构件内的残余应力。
应力降低的大小与构件内的残余应力大小有关,应力大则消除应力的效果高,应力小,消除应力的效果也低。
振动时效可以降低应力是显而易见的,其作用有如下几方面:①降低和均化应力,消除应力集中区,防止裂纹。
因为振动过程中残余应力大的点首先进入屈服,所以高应力点下降的比例大,使应力均化程度高,从而降低应力集中而防止裂纹。
②减少或防止构件变形构件的变形是由于残余应力特点造成的,因为残余应力的分布和量值具有很大的随机性,分布不均且量值差别太大,所以容易产生变化,即可变性。
残余应力的变化,必然使构件产生变形,因此在使用前或安装前,通过振动时效使应力降低和均化,必然防止或减少变形。
③提高焊接构件的疲劳寿命,增加使用周期通过大量的实验和实践证明,振动时效可提高焊件的疲劳寿命50%以上,提高使用寿命0.5~1倍。
由于振动时效的上述作用,使该项技术得到厂矿企业和国家的重视和认可,1991年制定了国家行业标准JB/T5928.91,并在1993年被国家科委批准为“国家级科技成果重点推广计划”项目,在全国普及推广。
振动时效
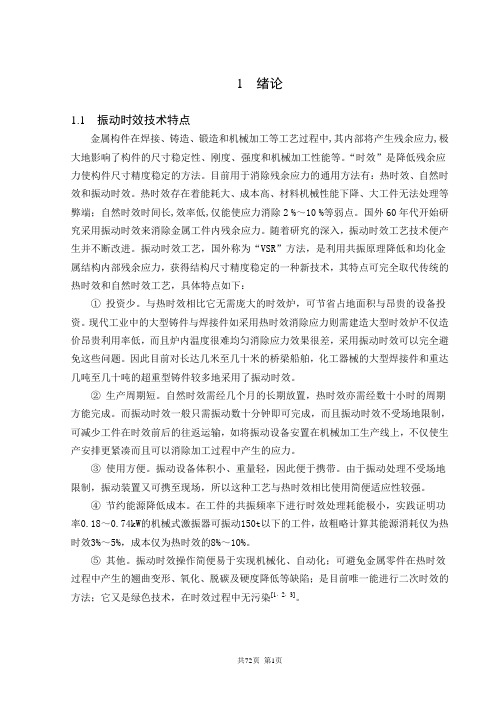
1 绪论1.1振动时效技术特点金属构件在焊接、铸造、锻造和机械加工等工艺过程中,其内部将产生残余应力,极大地影响了构件的尺寸稳定性、刚度、强度和机械加工性能等。
“时效”是降低残余应力使构件尺寸精度稳定的方法。
目前用于消除残余应力的通用方法有:热时效、自然时效和振动时效。
热时效存在着能耗大、成本高、材料机械性能下降、大工件无法处理等弊端;自然时效时间长,效率低,仅能使应力消除2 %~10 %等弱点。
国外60年代开始研究采用振动时效来消除金属工件内残余应力。
随着研究的深入,振动时效工艺技术便产生并不断改进。
振动时效工艺,国外称为“VSR”方法,是利用共振原理降低和均化金属结构内部残余应力,获得结构尺寸精度稳定的一种新技术,其特点可完全取代传统的热时效和自然时效工艺,具体特点如下:①投资少。
与热时效相比它无需庞大的时效炉,可节省占地面积与昂贵的设备投资。
现代工业中的大型铸件与焊接件如采用热时效消除应力则需建造大型时效炉不仅造价昂贵利用率低,而且炉内温度很难均匀消除应力效果很差,采用振动时效可以完全避免这些问题。
因此目前对长达几米至几十米的桥梁船舶,化工器械的大型焊接件和重达几吨至几十吨的超重型铸件较多地采用了振动时效。
②生产周期短。
自然时效需经几个月的长期放置,热时效亦需经数十小时的周期方能完成。
而振动时效一般只需振动数十分钟即可完成,而且振动时效不受场地限制,可减少工件在时效前后的往返运输,如将振动设备安置在机械加工生产线上,不仅使生产安排更紧凑而且可以消除加工过程中产生的应力。
③使用方便。
振动设备体积小、重量轻,因此便于携带。
由于振动处理不受场地限制,振动装置又可携至现场,所以这种工艺与热时效相比使用简便适应性较强。
④节约能源降低成本。
在工件的共振频率下进行时效处理耗能极小,实践证明功率0.18~0.74kW的机械式激振器可振动150t以下的工件,故粗略计算其能源消耗仅为热时效3%~5%,成本仅为热时效的8%~10%。
中华人民共和国机械行业标准

中华人民共和国机械行业标准振动时效效果评定方法JB/T5926-2005 1 范围本标准规定了振动时效工艺参数的选择及技术要求和振动时效效果评定方法。
本标准适用于碳素结构钢、低合金钢、不锈钢、铸铁。
有色金届(铜、铝、钛及具合金)等材质的铸件、锻件、焊接件、模具、机械加工件的振动时效装置。
2 规范性引用文件下列文件中的条款通过本标准的引用而成为本标准的条款。
凡是注日期的引用文件,其随后所有的修改单(不包括勘误的内容)或修订版均不适用于本标准,然而,鼓励根据本标准达成协议的各方研究是否可使用这些文件的最新版本。
凡是不注日期的引用文件,其最新版本适用于本标准。
JB/T5925.2 机械式振动时效装置技术条件3 术语和定义JB/T5925.2中确立的以及下列术语和定义适用于本标准。
3.1 激振点excitative position振动时效时,激振器在工件上的夹持点。
3.2 振型excited mode工件共振时,当某一点位移达到最大值的瞬间:工件各点的位移形成的线或面。
3.3 节点mode node时效时工件受周期性交变载荷的作用产生谐振,振幅最小处,称为节点。
节点连成的线即节线。
3.4 主振频率main excitative frequency在激振装置的频率范围内,引起工件谐振响应的频率中,能有效降低残余应力的频率叫主振频率;其余叫附振频率。
4 工艺参数选择及技术要求4.1 振前分析4.1.1 根据工件结构、尺寸材质、时效要求、残余应力场分布,分析判断所需有效振型,必要时分析以后工作状态、工况下工作应力大小及分布及其失效形式。
14.1.2 工件不应有超过标准规定的缩孔、火渣、裂纹及虚焊等缺陷,4.2振前准备4.2.1 在预测的有效振型的节线附近弹性支撑工件,支点应尽量少,工件的支撑应平稳4.2-2特殊工件的支撑以振动阻力小日平稳为准。
4.2.3激振器应固定装在工件刚性较大且振幅较大处4-2-4拾振器应固定装在远离激振器且在振幅较大处4,3试振工件4.3.l 选择激振器偏心距,由小到大使工件在最大工作转速区间内产生共振,4.3.2 全程扫频、寻找共振峰,确定主、附振频率及扫频范围,按主振频率的振型调整支撑点激振点、拾振点及力方向。
JBT 5926-1991 振动时效工艺参数选择及技术要求

JBT 5926-1991 振动时效工艺参数选择及技术要求JB/T5926-91振动时效工艺参数选择及技术要求1991-11-30公布1992-07-01实施1主题内容与适用范畴本标准规定了振动时效工艺参数的选择及技术要求和振动时效成效评定方法.本标准适用于材质为碳素结构钢,低合金钢,不锈钢,铸铁,有色金属(铜,铝,锌其合金)等铸件,锻件,焊接件的振动时效处理.2术语2.1扫频曲线---将激振器的频率缓慢地由小调大的过程称扫频.随着频率的变化,工件振动响应发生变化.反映振动响应与频率之间关系的曲线,称扫频曲线,如A---f称振幅频率曲线;a-f称加速度频率曲线.注:A表示振幅,a表示加速度,f表示频率.2.2激振点---振动时效时,激振器在工件上的夹持点称激振点.3工艺参数选择及技术要求3.1第一应分析判定出工件在激振频率范畴内的振型.3.2振动时效装置(以下简称装置)的选择.3.2.1装置的激振频率应大于工件的最低固有频率.3.2.2装置的最大激振频率小于工作的最低固有频率时,应采取倍频(或称分频)降频等措施.3.2.3装置的激振力应能使工件内产生的最大动应力为工作应力的1/3~2/3.3.2.4装置应具备自动扫频,自动记录扫频曲线,指示振动加速度值和电机电流值的功能.稳速精度应达到+lr/min.3.3支撑工件,装卡激振器和拾振器3.3.1为了使工作处于自由状态,应采纳三点或四点弹性的支撑工件,支撑位置应在主振频率的节线处或邻近.为使工件成为两端简支或悬臂,则应采纳刚性装夹.3.3.2激振器应刚性地固定在工件的刚度较弱或振幅较大处,但不准固定在工件的强度和刚度专门低的如大的薄板平面等部位,固定处应平坦.3.3.3悬臂装夹的工件,一样应掉头进行第二次振动时效处理.特大工件,在其振动响应薄弱的部位应进行补振.3.3.4拾振器应固装在远离激振器同时振幅较大处.3.4工件的试振3.4.1不承诺试振的工件存在缩孔,夹渣,裂纹,虚焊等严峻缺陷.3.4.2选择激振器偏心档位,应满足使工件产生较大振幅和装置只是载的要求,必要时先用手动旋钮查找合适的偏心档位.3.4.3第一次扫频,记录工件的振幅频率(A-f)曲线,测出各阶共振频率值,节线位置,波峰位置.3.4.4必要时通过调整支撑点,激振点和拾振点的位置来激起较多的振型.3.4.5测定1-3个共振峰大的频率在共振时的动应力峰值的大小.3.4.6选择动应力大,频率低在共振频率作为主振频率.3.4.7按主振型对支撑,拾振位置进行最后调整.注:主振频率的振型称为主振型.3.5工件的主振3.5.1在亚共振区内选择主振峰峰值的1/3-2/3所对应的频率主振工件.3.5.2主振时装置的偏心档位应使工件的动应力峰值达到工作应力的1/3-2/3,并使装置的输出功率不超过额定功率的80%.3.5.3进行振前扫频,记录振前的振幅时刻(A-f)曲线.3.5.4主振工件,记录振幅频率(A-t)曲线.3.5.5起振后振幅时刻(A-t)曲线上的振幅上升,然后变平或上升后下降然后再变平,从变平开始稳固3-5犿犻狀为振动截止时刻,一样累计振动时刻不超过40犿犻狀.3.5.6进行振后扫频,记录振幅频率(A-f)曲线.3.5.7批量生产的工件可不作振前,振后扫频.3.5.8有些工件可作多点激振处理,有些工件可用附振频率作多频共振辅助处理.是否调整支撑点,拾振点位置视工件而定.注:主振频率以外的各共振频率称为附振频率.3.5.9工件存在如夹渣,缩孔,裂纹,虚焊等缺陷,在振动时效中这类缺陷专门快以裂纹扩展的形式显现时,应赶忙中断时效处理.工件排除缺陷后,承诺重新进行振动时效.3.6振动时效工艺卡和操作记录卡3.6.1批量生产的工件进行振动时效处理时,必须制订"振动时效工艺卡",操作者必须严格执行并填写"振动时效操作记录卡"在工件上作已振标记.3.6.2"振动时效工艺卡"应按3.1-3.5条的要求,试验三件以上,找出规律后制订.3.6.3"振动时效工艺卡"和"振动时效操作记录卡"的内容和格式分别参照附录犅和附录犆. 3.7铸件振动时效时,应使动应力方向尽量与易变形方向一致.3.8制订焊接件振动时效工艺时,应明确工件上承担力的要紧焊缝和联系焊缝.振动处理中,其振动方向应使工件承担力的要紧焊缝处的动应力最大或较大.4振动时效工艺成效评定方法4.1参数曲线观测法4.1.1振动处理过程中从振幅时刻(A-f)曲线和振前,振后振幅频率(A-f)曲线的变化来监测.4.1.2显现下列情形之一时,即可判定为达到振动时效工艺成效.a 振幅时刻(A-t)曲线上升后变平.b 振幅时刻(A-t)曲线上升后下降然后变平.c振幅频率(A-f)曲线振后的比振前的峰值升高.d振幅频率(A-f)曲线振后的比振前的峰值点左移.e振幅频率(A-f)曲线振后的比振前的带宽变窄.4.1.3振动处理过程中,如果不显现4.1.2条中所列的任一情形时,应重新调整振动参数,按上述规定的条款再进行时效处理后,重新检验.4.1.4制订有"振动时效工艺卡"的批量生产的工件,在振动时效时,举荐用4.1.2条的a,b款中只要显现一种情形,便可判定为达到振动时效工艺成效的方法来检验,并不再作下述检验.4.2残余应力检测法4.2.1举荐使用盲孔法,也可使且X射线衍射法.4.2.1.1被振工作振前,振后的残余应力测定点数均应大于5个点.4.2.1.2用振前,振后的应力平均值(应力水平)来运算应力排除率,焊件应大于30%,铸锻件应大于20%.4.2.13用振前,振后的最大应力与最小应力之差值来衡量均化程度,振后的运算值应小于振前的运算值.4.3精度稳固性检测法4.3.1以要求精度稳固性为主的工件,振后应进行精度稳固性检验.a精加工后检验.b长期放置定期检验静尺寸稳固性,在放置15d时第一次检验,以后每隔30d检验一次,总的静置时刻半年以上.c在动载荷后检验.应按照具体情形选用上述条款.4.3.2各种检验结果均应达到设计要求.附录A振动时效工艺中动应力选择与振动时效对工件疲劳寿命阻碍分析(补充件)1振动时效工艺中动应力的选择与分析动应力是振动时效工艺的一项最要紧参数.实验证明:在一定范畴内动应力越大,被处理工件上产生的应变开释量也越大,排除应力的成效也越好,动应力过大将有可能造成工件的损害或降低疲劳寿命.因此在本标准中以工作应力来确定动应力.即:σ动=(1/3~2/3)σ工作在设计时,工作应力(σ工作)是差不多确定的,或和应变测试技术获得,在那个地点应以在工作状态下工件上最大应力点的应力作为工作应力.当我们按上述方法来确定动应力(σ动)时,就能够保证被振工作既能排除应力又不遭到损坏.由于工件结构比较复杂的结构,在不同受力状态下各点的动应力不同,因此在实际操作时,应选择结构危险点(应力集中点),做动应力监测,以保证动应力量值的可靠.2振动时效对工件疲劳寿命阻碍的分析振动时效其工作状态是对工件施加周期性的作用力,这如同疲劳荷载一样,按照线性累积损害理论,必定对工件造成一定的疲劳损害.但另一方面,由于低应力振动处理后残余应力得到下降,又必定提升工件的疲劳寿命.我国振动时效工作者,通过大量的试验给出了振动时效对工件疲劳寿命的关系曲线(如图A1所示).图中:N-σ为寿命-应力坐标;N-σ动为寿命-动应力坐标;σ工作为实际工作中工件中最大应力;η工作为在工作应力作用下的疲劳寿命.从图中可见,当动应力σ动小于A点时,振动时效能够提升疲劳寿命;当动应力σ动大于A点时,振动时效将降低疲劳寿命;当采纳工作荷载处理时,振动时效降低疲劳寿命的数值(B点)就等于振动时效处理时的循环数.因此,本标准中选动应力为工作应力的1/3-2/3是可不能对焊接件造成任何疲劳损害的,相反还能够提升工件的疲劳寿命.。
中华人民共和国机械行业标准-振动时效设备

中华人民共和国机械行业标准振动时效效果评定方法JB/T5926-20051 范围本标准规定了振动时效工艺参数选择及技术要求和振动时效效果的评定方法。
本标准适用于碳素结构钢、低合金钢、不锈钢、铸铁。
有色金属(铜、铝、钛及其合金)等材质的铸件、锻件、焊接件、模具、机械加工件的振动时效处理。
2 规范性引用文件下列文件中的条款通过本标准的引用而成为本标准的条款。
凡是注日期的引用文件,其随后所有的修改单(不包括勘误的内容)或修订版均不适用于本标准,然而,鼓励根据本标准达成协议的各方研究是否可使用这些文件的最新版本。
凡是不注日期的引用文件,其最新版本适用于本标准。
JB/T5925. 2 机械式振动时效装置技术条件3 术语、符号3.1 激振点exciting point振动时效时给构件的施力点称为激振点。
3.2 支撑点support point为了对构件进行振动时效而选择的支撑构件的位置。
3.3 动应力dynamic stress激振力引起构件谐振响应时,在其内部产生的应力称为动应力。
矢量,符号为σd(幅值),单位为(MPa)。
3.4 共振resonance当激振力提供的周期性激振力的频率与系统固有频率接近或相等时,构件的振幅急剧增大的现象为共振。
3.5 振型vibration mode共振时,构件表面上所有质点振动的包络线(面),即为振型,包括弯曲、扭转、扭曲、钟振型和鼓振型。
3.6 节点(节线)node, node line振动时效时,构件振幅最小处称为节点(节线)。
3.7 主振频率principal vibration frequency在激振装置的频率范围内,引起构件谐振响应的频率中,频率低、位移幅大的频率称为主振频率。
3.8 附振频率additional vibration frequency除主振频率以外的其他频率。
3.9 扫频frequency sweep固定偏心,将激振力的频率由小调大的过程,称为扫频。
振动时效工艺参数选择及技术要求
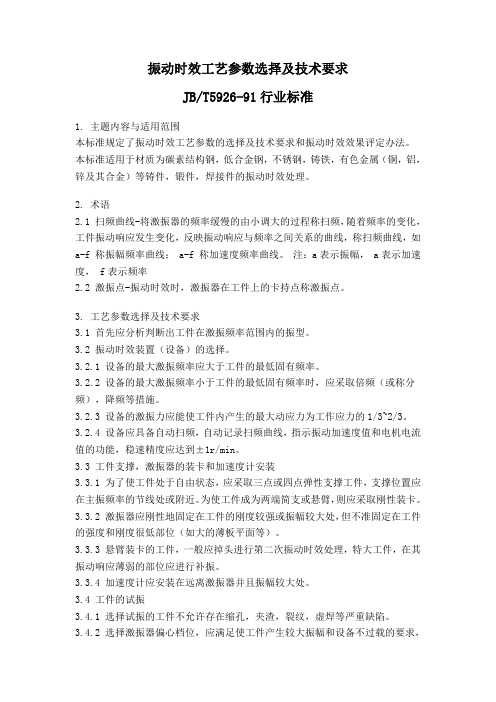
振动时效工艺参数选择及技术要求JB/T5926-91行业标准1. 主题内容与适用范围本标准规定了振动时效工艺参数的选择及技术要求和振动时效效果评定办法。
本标准适用于材质为碳素结构钢,低合金钢,不锈钢,铸铁,有色金属(铜,铝,锌及其合金)等铸件,锻件,焊接件的振动时效处理。
2. 术语2.1 扫频曲线-将激振器的频率缓慢的由小调大的过程称扫频,随着频率的变化,工件振动响应发生变化,反映振动响应与频率之间关系的曲线,称扫频曲线,如a-f 称振幅频率曲线; a-f 称加速度频率曲线。
注:a表示振幅, a表示加速度, f表示频率2.2 激振点-振动时效时,激振器在工件上的卡持点称激振点。
3. 工艺参数选择及技术要求3.1 首先应分析判断出工件在激振频率范围内的振型。
3.2 振动时效装置(设备)的选择。
3.2.1 设备的最大激振频率应大于工件的最低固有频率。
3.2.2 设备的最大激振频率小于工件的最低固有频率时,应采取倍频(或称分频),降频等措施。
3.2.3 设备的激振力应能使工件内产生的最大动应力为工作应力的1/3~2/3。
3.2.4 设备应具备自动扫频,自动记录扫频曲线,指示振动加速度值和电机电流值的功能,稳速精度应达到±1r/min。
3.3 工件支撑,激振器的装卡和加速度计安装3.3.1 为了使工件处于自由状态,应采取三点或四点弹性支撑工件,支撑位置应在主振频率的节线处或附近。
为使工件成为两端简支或悬臂,则应采取刚性装卡。
3.3.2 激振器应刚性地固定在工件的刚度较强或振幅较大处,但不准固定在工件的强度和刚度很低部位(如大的薄板平面等)。
3.3.3 悬臂装卡的工件,一般应掉头进行第二次振动时效处理,特大工件,在其振动响应薄弱的部位应进行补振。
3.3.4 加速度计应安装在远离激振器并且振幅较大处。
3.4 工件的试振3.4.1 选择试振的工件不允许存在缩孔,夹渣,裂纹,虚焊等严重缺陷。
3.4.2 选择激振器偏心档位,应满足使工件产生较大振幅和设备不过载的要求,必要时先用手动旋钮寻找合适的偏心档位。
振动时效工艺守则
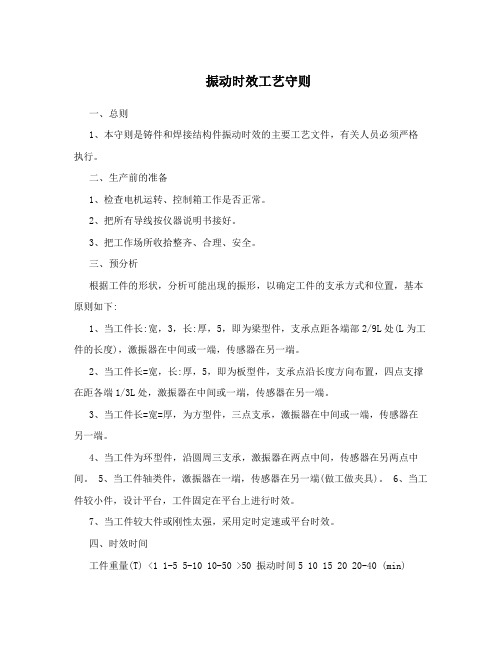
振动时效工艺守则一、总则1、本守则是铸件和焊接结构件振动时效的主要工艺文件,有关人员必须严格执行。
二、生产前的准备1、检查电机运转、控制箱工作是否正常。
2、把所有导线按仪器说明书接好。
3、把工作场所收拾整齐、合理、安全。
三、预分析根据工件的形状,分析可能出现的振形,以确定工件的支承方式和位置,基本原则如下:1、当工件长:宽,3,长:厚,5,即为梁型件,支承点距各端部2/9L处(L为工件的长度),激振器在中间或一端,传感器在另一端。
2、当工件长=宽,长:厚,5,即为板型件,支承点沿长度方向布置,四点支撑在距各端1/3L处,激振器在中间或一端,传感器在另一端。
3、当工件长=宽=厚,为方型件,三点支承,激振器在中间或一端,传感器在另一端。
4、当工件为环型件,沿圆周三支承,激振器在两点中间,传感器在另两点中间。
5、当工件轴类件,激振器在一端,传感器在另一端(做工做夹具)。
6、当工件较小件,设计平台,工件固定在平台上进行时效。
7、当工件较大件或刚性太强,采用定时定速或平台时效。
四、时效时间工件重量(T) <1 1-5 5-10 10-50 >50 振动时间5 10 15 20 20-40 (min)五、时效处理1、按设备使用说明书将设备各部分用电缆连接好,予热5分钟。
2、将激振器和传感器联接好。
3、打开主控制电源开关、液晶屏幕上显示滚动显示、说明主控制箱内微机工作正常。
4、按运行键、设备即开始工作,并对工件进行振前扫描,若工艺参数合适则设备将自动继续进行第二步的振动时效处理和第三步振动时效效果的检测。
若工艺参数不合适,液晶屏上将显示不合适的原因并给出修正方案,操作者需按屏幕显示的修正步骤对工艺参数进行修正,修正完后按复位键,然后按运行键进行振动时效处理。
5、对于第一次处理的工件,也可以采用手动操作的方式,按上升键为开始手动控制,电机转速缓慢升速,升速速度为三档每按一次改变一种升速速度,若停止升速按下降键即可,降速时按相反操作。
- 1、下载文档前请自行甄别文档内容的完整性,平台不提供额外的编辑、内容补充、找答案等附加服务。
- 2、"仅部分预览"的文档,不可在线预览部分如存在完整性等问题,可反馈申请退款(可完整预览的文档不适用该条件!)。
- 3、如文档侵犯您的权益,请联系客服反馈,我们会尽快为您处理(人工客服工作时间:9:00-18:30)。
JBT59261991振动时效工艺参数选择及技术要求
JB/T 5926-91
振动时效工艺
参数选择及技术要求
1991-11-30公布 1992-07-01实施
1 主题内容与适用范畴
本标准规定了振动时效工艺参数的选择及技术要求和振动时效成效评定方法.
本标准适用于材质为碳素结构钢,低合金钢,不锈钢,铸铁,有色金属(铜,铝,锌其合金)等
铸件,锻件,焊接件的振动时效处理.
2 术语
2.1 扫频曲线---将激振器的频率缓慢地由小调大的过程称扫频.随着频率的变化,工件振
动响应发生变化.反映振动响应与频率之间关系的曲线,称扫频曲线,如A---f称振幅
频率曲线;a-f称加速度频率曲线.
注:A表示振幅,a表示加速度,f表示频率.
2.2 激振点---振动时效时,激振器在工件上的夹持点称激振点.
3 工艺参数选择及技术要求
3.1第一应分析判定出工件在激振频率范畴内的振型.
3.2振动时效装置(以下简称装置)的选择.
3.2.1装置的激振频率应大于工件的最低固有频率.
3.2.2装置的最大激振频率小于工作的最低固有频率时,应采取倍频(或称分频)降频等措施.
3.2.3装置的激振力应能使工件内产生的最大动应力为工作应力的1/3~2/3.
3.2.4装置应具备自动扫频,自动记录扫频曲线,指示振动加速度值和电机电流值的功能.稳
速精度应达到+lr/min.
3.3支撑工件,装卡激振器和拾振器
3.3.1为了使工作处于自由状态,应采纳三点或四点弹性的支撑工件,支撑位置应在主振频率
的节线处或邻近.为使工件成为两端简支或悬臂,则应采纳刚性装夹.
3.3.2激振器应刚性地固定在工件的刚度较弱或振幅较大处,但不准固定在工件的强度和刚度
专门低的如大的薄板平面等部位,固定处应平坦.
3.3.3悬臂装夹的工件,一样应掉头进行第二次振动时效处理.特大工件,在其振动响应薄弱
的部位应进行补振.
3.3.4拾振器应固装在远离激振器同时振幅较大处.
3.4 工件的试振
3.4.1不承诺试振的工件存在缩孔,夹渣,裂纹,虚焊等严峻缺陷.
3.4.2选择激振器偏心档位,应满足使工件产生较大振幅和装置只是载的要求,必要时先用手
动旋钮查找合适的偏心档位.
3.4.3第一次扫频,记录工件的振幅频率(A-f)曲线,测出各阶共振频率值,节线位置,波峰位
置.
3.4.4必要时通过调整支撑点,激振点和拾振点的位置来激起较多的振型.
3.4.5测定1-3个共振峰大的频率在共振时的动应力峰值的大小.
3.4.6选择动应力大,频率低在共振频率作为主振频率.
3.4.7按主振型对支撑,拾振位置进行最后调整.
注:主振频率的振型称为主振型.
3.5 工件的主振
3.5.1在亚共振区内选择主振峰峰值的1/3-2/3所对应的频率主振工件.
3.5.2主振时装置的偏心档位应使工件的动应力峰值达到工作应力的1/3-2/3,并使装置的输
出功率不超过额定功率的80%.
3.5.3进行振前扫频,记录振前的振幅时刻(A-f)曲线.
3.5.4主振工件,记录振幅频率(A-t)曲线.
3.5.5起振后振幅时刻(A-t)曲线上的振幅上升,然后变平或上升后下降然后再变平,从变平
开始稳固3-5犿犻狀为振动截止时刻,一样累计振动时刻不超过40犿犻狀.
3.5.6进行振后扫频,记录振幅频率(A-f)曲线.
3.5.7批量生产的工件可不作振前,振后扫频.
3.5.8有些工件可作多点激振处理,有些工件可用附振频率作多频共振辅助处理.是否调整支
撑点,拾振点位置视工件而定.
注:主振频率以外的各共振频率称为附振频率.
3.5.9工件存在如夹渣,缩孔,裂纹,虚焊等缺陷,在振动时效中这类缺陷专门快以裂纹扩展的形
式显现时,应赶忙中断时效处理.工件排除缺陷后,承诺重新进行振动时效.
3.6 振动时效工艺卡和操作记录卡
3.6.1批量生产的工件进行振动时效处理时,必须制订"振动时效工艺卡",操作者必须严格执
行并填写"振动时效操作记录卡"在工件上作已振标记.
3.6.2"振动时效工艺卡"应按3.1-3.5条的要求,试验三件以上,找出规律后制订.
3.6.3"振动时效工艺卡"和"振动时效操作记录卡"的内容和格式分别参照附录犅和附录犆.
3.7 铸件振动时效时,应使动应力方向尽量与易变形方向一致.
3.8 制订焊接件振动时效工艺时,应明确工件上承担力的要紧焊缝和联系焊缝.振动处理中,
其振动方向应使工件承担力的要紧焊缝处的动应力最大或较大.
4 振动时效工艺成效评定方法
4.1 参数曲线观测法
4.1.1振动处理过程中从振幅时刻(A-f)曲线和振前,振后振幅频率(A-f)曲线的变化来监
测.
4.1.2显现下列情形之一时,即可判定为达到振动时效工艺成效.
a 振幅时刻(A-t)曲线上升后变平.
b 振幅时刻(A-t)曲线上升后下降然后变平.
c振幅频率(A-f)曲线振后的比振前的峰值升高.
d振幅频率(A-f)曲线振后的比振前的峰值点左移.
e振幅频率(A-f)曲线振后的比振前的带宽变窄.
4.1.3振动处理过程中,假如不显现4.1.2条中所列的任一情形时,应重新调整振动参数,按上
述规定的条款再进行时效处理后,重新检验.
4.1.4制订有"振动时效工艺卡"的批量生产的工件,在振动时效时,举荐用4.1.2条的a,b款
中只要显现一种情形,便可判定为达到振动时效工艺成效的方法来检验,并不再作下述
检验.
4.2 残余应力检测法
4.2.1举荐使用盲孔法,也可使且X射线衍射法.
4.2.1.1被振工作振前,振后的残余应力测定点数均应大于5个点.
4.2.1.2用振前,振后的应力平均值(应力水平)来运算应力排除率,焊件应大于30%,铸锻件应
大于20%.
4.2.13用振前,振后的最大应力与最小应力之差值来衡量均化程度,振后的运算值应小于振前
的运算值.
4.3 精度稳固性检测法
4.3.1以要求精度稳固性为主的工件,振后应进行精度稳固性检验.
a精加工后检验.
b长期放置定期检验静尺寸稳固性,在放置15d时第一次检验,以后每隔30d检验一次,总
的静置时刻半年以上.
c在动载荷后检验.
应依照具体情形选用上述条款.
4.3.2各种检验结果均应达到设计要求.
附录A
振动时效工艺中动应力选择与振动时效
对工件疲劳寿命阻碍分析
(补充件)
1 振动时效工艺中动应力的选择与分析
动应力是振动时效工艺的一项最要紧参数.实验证明:在一定范畴内动应力越大,被处理工件上产生的应变开释量也越大,
排除应力的成效也越好,动应力过大将有可能造成工件的损害或降低疲劳寿命.因此在本标准中以工作应力来确定动应力.即:σ 动=(1/3~2/3)σ工作在设计时,工作应力(σ工作)是差不多确定的,或和应变测试技术获得,在那个地点应以在工作状态下工件上最大应力点的应力作为工作应力.当我们按上述方法来确定动应力(σ动)时,就能够保证被振工作既能排除应力又不遭到损坏.由于工件结构比较复杂的结构,在不同受力状态下各点的动应力不同,因此在实际操作时,应选择结构危险点(应力集中点),做动应力监测,以保证动应力量值的可靠.
2 振动时效对工件疲劳寿命阻碍的分析
振动时效其工作状态是对工件施加周期性的作用力,这如同疲劳荷载一样,依照线性累积损害理论,必定对工件造成一定的
疲劳损害.但另一方面,由于低应力振动处理后残余应力得到下降,又必定提高工件的疲劳寿命.我国振动时效工作者,通过大量
的试验给出了振动时效对工件疲劳寿命的关系曲线(如图A1所示).图中:N-σ为寿命-应力坐标;
N-σ动为寿命-动应力坐标;
σ工作为实际工作中工件中最大应力;
η工作为在工作应力作用下的疲劳寿命.
从图中可见,当动应力σ动小于A点时,振动时效能够提高疲劳寿命;当动应力σ动大于A点时,振动时效将降低疲劳寿命;当采纳工作荷载处理时,振动时效降低疲劳寿命的数值(B点)就等于振动时效处理时的循环数.因此,本标准中选动应力为工作应力的1/3-2/3是可不能对焊接件造成任何疲劳损害的,相反还能够提高工件的疲劳寿命.。