壳体腔体类零件CNC精密加工修订稿
cnc产品质量和生产效率的改进措施
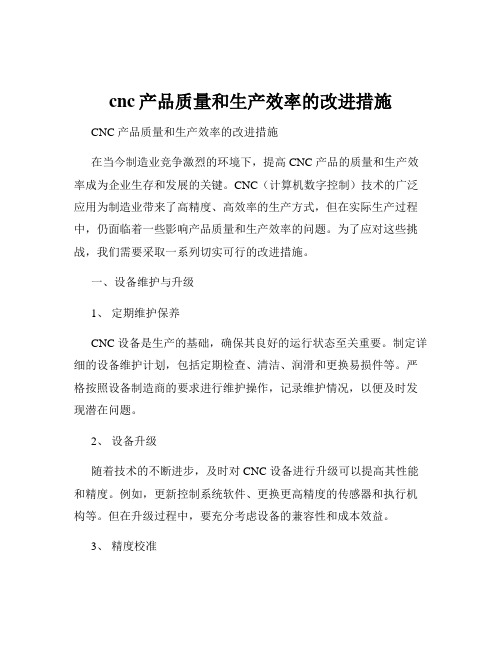
cnc产品质量和生产效率的改进措施CNC 产品质量和生产效率的改进措施在当今制造业竞争激烈的环境下,提高 CNC 产品的质量和生产效率成为企业生存和发展的关键。
CNC(计算机数字控制)技术的广泛应用为制造业带来了高精度、高效率的生产方式,但在实际生产过程中,仍面临着一些影响产品质量和生产效率的问题。
为了应对这些挑战,我们需要采取一系列切实可行的改进措施。
一、设备维护与升级1、定期维护保养CNC 设备是生产的基础,确保其良好的运行状态至关重要。
制定详细的设备维护计划,包括定期检查、清洁、润滑和更换易损件等。
严格按照设备制造商的要求进行维护操作,记录维护情况,以便及时发现潜在问题。
2、设备升级随着技术的不断进步,及时对 CNC 设备进行升级可以提高其性能和精度。
例如,更新控制系统软件、更换更高精度的传感器和执行机构等。
但在升级过程中,要充分考虑设备的兼容性和成本效益。
3、精度校准定期对设备进行精度校准,确保加工出来的产品符合设计要求。
使用高精度的测量仪器,如三坐标测量机,对设备的定位精度、重复精度等进行检测和调整。
二、刀具与夹具的优化1、刀具选择与管理根据加工材料和工艺要求,选择合适的刀具类型、材质和几何参数。
建立刀具库存管理系统,及时补充和更换磨损的刀具。
对刀具的使用情况进行跟踪和分析,优化刀具的使用寿命和切削参数。
2、夹具设计与改进夹具的设计直接影响产品的加工精度和生产效率。
设计夹具时,要考虑工件的定位、夹紧方式和稳定性。
采用标准化、模块化的夹具设计,提高夹具的通用性和互换性。
同时,不断改进夹具结构,减少装夹时间和误差。
三、编程与工艺优化1、优化编程方法编程人员应熟练掌握各种编程软件和编程语言,采用高效的编程策略。
例如,合理运用刀具路径规划、切削参数设置和循环指令等,减少空行程和切削时间。
2、工艺参数优化通过试验和数据分析,优化切削速度、进给量、切削深度等工艺参数。
结合材料特性和加工要求,确定最佳的工艺方案,提高加工效率和表面质量。
模具CNC加工标准参考课件
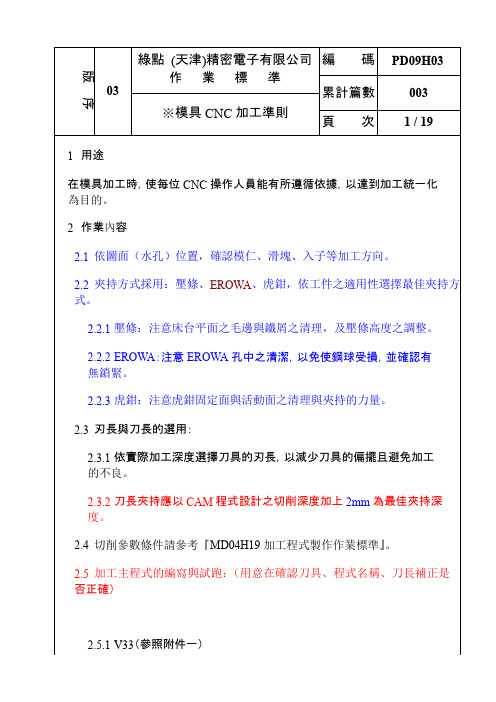
IF[#5GT40]GOTO999
#33=105
#1=#5
#17=#21
#32=1
M98P8100
03
綠點(天津)精密電子有限公司
作業標準
編碼
PD09H03
累計篇數
003
※模具CNC加工準則
頁次
7/19
N6
M98P401(6)
IF[#6EQ0]GOTO990
IF[#6GT40]GOTO999
#33=108
#1=#8
#17=#24
#32=1
M98P8100
N9
M98P401(9)
IF[#9EQ0]GOTO990
IF[#9GT40]GOTO999
#33=109
#1=#9
#17=#25
#32=1
M98P8100
N10
M98P401(10)
IF[#10EQ0]GOTO990
IF[#10GT40]GOTO999
2.8.4注意加工完之成品保護以防止撞傷等受損現象發生。
2.8.5注意任何加工中之異常處理,如刀具斷裂、磨耗等更換。
3其他:
3.1本作業標準每年九月,由責任單位負責召集有關單位檢討,並將檢討
結果送事業單位主管審核。
3.2審核完成後,呈群主管核准,保存於製造單位,公佈後立即實施,修訂
時亦同。
3.3本次修改為統一彙整切削參數以及調整格式進行修訂。
2.8其它(注意事項)
2.8.1加工前先利用一次元確認加工物之X、Y、Z有無過切。
2.8.2注意加工前校模時毛邊的清理,以免尋邊造成誤差。
03
綠點(天津)精密電子有限公司
cnc加工品质和工作效率的改良方案
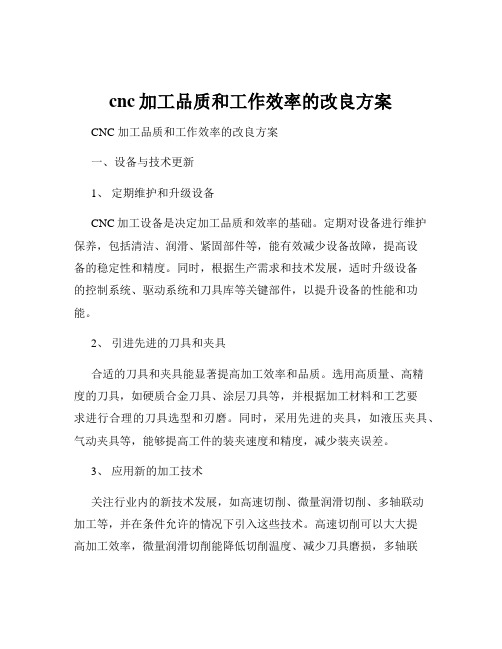
cnc加工品质和工作效率的改良方案CNC 加工品质和工作效率的改良方案一、设备与技术更新1、定期维护和升级设备CNC加工设备是决定加工品质和效率的基础。
定期对设备进行维护保养,包括清洁、润滑、紧固部件等,能有效减少设备故障,提高设备的稳定性和精度。
同时,根据生产需求和技术发展,适时升级设备的控制系统、驱动系统和刀具库等关键部件,以提升设备的性能和功能。
2、引进先进的刀具和夹具合适的刀具和夹具能显著提高加工效率和品质。
选用高质量、高精度的刀具,如硬质合金刀具、涂层刀具等,并根据加工材料和工艺要求进行合理的刀具选型和刃磨。
同时,采用先进的夹具,如液压夹具、气动夹具等,能够提高工件的装夹速度和精度,减少装夹误差。
3、应用新的加工技术关注行业内的新技术发展,如高速切削、微量润滑切削、多轴联动加工等,并在条件允许的情况下引入这些技术。
高速切削可以大大提高加工效率,微量润滑切削能降低切削温度、减少刀具磨损,多轴联动加工则可以实现复杂形状的一次加工成型,提高加工精度和表面质量。
二、工艺优化1、合理规划加工路径在编程时,通过优化刀具路径,减少空行程和重复切削,能够有效提高加工效率。
例如,采用环切或行切的方式进行粗加工,然后再进行精加工,可以减少刀具的磨损和加工时间。
同时,合理安排加工顺序,先加工基准面和重要部位,再加工次要部位,能够保证加工精度。
2、优化切削参数切削参数的选择直接影响加工效率和品质。
通过实验和经验积累,确定最佳的切削速度、进给量和切削深度,以达到高效切削的目的。
同时,根据不同的加工材料和刀具,实时调整切削参数,避免过度切削或切削不足。
3、采用新工艺和方法例如,采用电火花加工、电解加工等特种加工方法来解决一些传统加工难以完成的任务,或者采用复合加工工艺,将多种加工方法集成在一台设备上,减少工序转换和装夹次数,提高生产效率。
三、人员培训与管理1、提高操作人员技能水平定期组织操作人员参加培训课程,学习新的加工技术和工艺,掌握设备的操作和维护知识。
铝合金薄壁深腔的数控加工
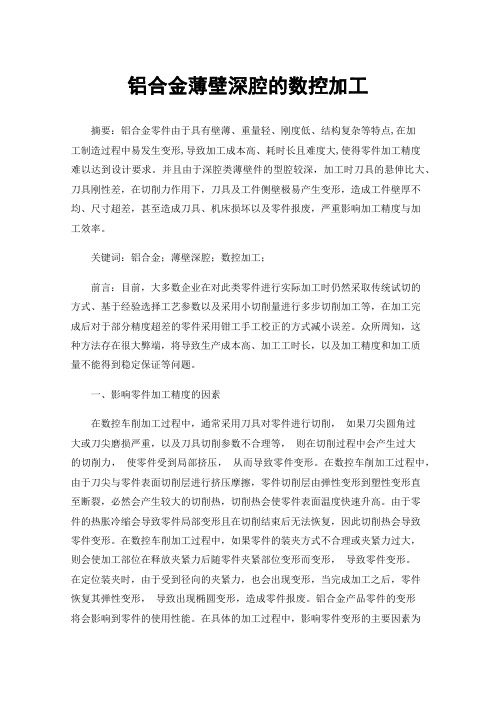
铝合金薄壁深腔的数控加工摘要:铝合金零件由于具有壁薄、重量轻、刚度低、结构复杂等特点,在加工制造过程中易发生变形,导致加工成本高、耗时长且难度大,使得零件加工精度难以达到设计要求。
并且由于深腔类薄壁件的型腔较深,加工时刀具的悬伸比大、刀具刚性差,在切削力作用下,刀具及工件侧壁极易产生变形,造成工件壁厚不均、尺寸超差,甚至造成刀具、机床损坏以及零件报废,严重影响加工精度与加工效率。
关键词:铝合金;薄壁深腔;数控加工;前言:目前,大多数企业在对此类零件进行实际加工时仍然采取传统试切的方式、基于经验选择工艺参数以及采用小切削量进行多步切削加工等,在加工完成后对于部分精度超差的零件采用钳工手工校正的方式减小误差。
众所周知,这种方法存在很大弊端,将导致生产成本高、加工工时长,以及加工精度和加工质量不能得到稳定保证等问题。
一、影响零件加工精度的因素在数控车削加工过程中,通常采用刀具对零件进行切削,如果刀尖圆角过大或刀尖磨损严重,以及刀具切削参数不合理等,则在切削过程中会产生过大的切削力,使零件受到局部挤压,从而导致零件变形。
在数控车削加工过程中,由于刀尖与零件表面切削层进行挤压摩擦,零件切削层由弹性变形到塑性变形直至断裂,必然会产生较大的切削热,切削热会使零件表面温度快速升高。
由于零件的热胀冷缩会导致零件局部变形且在切削结束后无法恢复,因此切削热会导致零件变形。
在数控车削加工过程中,如果零件的装夹方式不合理或夹紧力过大,则会使加工部位在释放夹紧力后随零件夹紧部位变形而变形,导致零件变形。
在定位装夹时,由于受到径向的夹紧力,也会出现变形,当完成加工之后,零件恢复其弹性变形,导致出现椭圆变形,造成零件报废。
铝合金产品零件的变形将会影响到零件的使用性能。
在具体的加工过程中,影响零件变形的主要因素为切削力、切削热和夹紧力。
切削过程中,产生的切削力大小直接影响到切削热和夹紧力,切削热引起铝合金材料的热变形;施加在零件上的夹紧力引起薄壁零件的冷变形;从而容易产生切削力下的振动变形。
先进数控机床零件加工工艺优化及质量控制
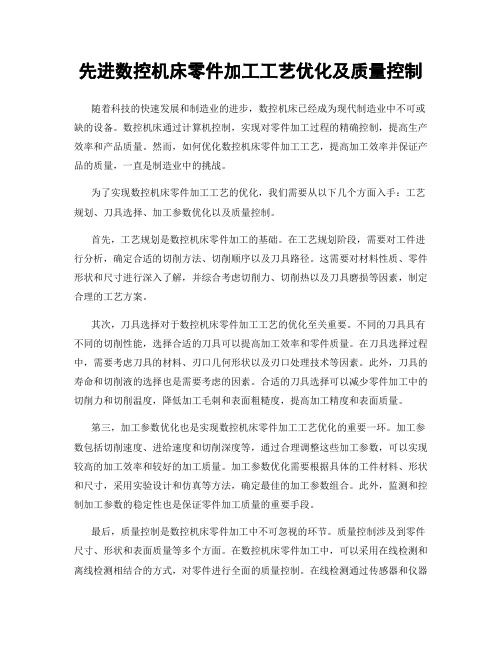
先进数控机床零件加工工艺优化及质量控制随着科技的快速发展和制造业的进步,数控机床已经成为现代制造业中不可或缺的设备。
数控机床通过计算机控制,实现对零件加工过程的精确控制,提高生产效率和产品质量。
然而,如何优化数控机床零件加工工艺,提高加工效率并保证产品的质量,一直是制造业中的挑战。
为了实现数控机床零件加工工艺的优化,我们需要从以下几个方面入手:工艺规划、刀具选择、加工参数优化以及质量控制。
首先,工艺规划是数控机床零件加工的基础。
在工艺规划阶段,需要对工件进行分析,确定合适的切削方法、切削顺序以及刀具路径。
这需要对材料性质、零件形状和尺寸进行深入了解,并综合考虑切削力、切削热以及刀具磨损等因素,制定合理的工艺方案。
其次,刀具选择对于数控机床零件加工工艺的优化至关重要。
不同的刀具具有不同的切削性能,选择合适的刀具可以提高加工效率和零件质量。
在刀具选择过程中,需要考虑刀具的材料、刃口几何形状以及刃口处理技术等因素。
此外,刀具的寿命和切削液的选择也是需要考虑的因素。
合适的刀具选择可以减少零件加工中的切削力和切削温度,降低加工毛刺和表面粗糙度,提高加工精度和表面质量。
第三,加工参数优化也是实现数控机床零件加工工艺优化的重要一环。
加工参数包括切削速度、进给速度和切削深度等,通过合理调整这些加工参数,可以实现较高的加工效率和较好的加工质量。
加工参数优化需要根据具体的工件材料、形状和尺寸,采用实验设计和仿真等方法,确定最佳的加工参数组合。
此外,监测和控制加工参数的稳定性也是保证零件加工质量的重要手段。
最后,质量控制是数控机床零件加工中不可忽视的环节。
质量控制涉及到零件尺寸、形状和表面质量等多个方面。
在数控机床零件加工中,可以采用在线检测和离线检测相结合的方式,对零件进行全面的质量控制。
在线检测通过传感器和仪器设备实时监测加工过程中的各个参数,及时发现加工异常,及早采取措施进行调整和修正。
离线检测通过对加工零件进行测量和检查,对成品进行质量评估和控制。
壳体腔体类零件CNC精密加工

壳体腔体类零件C N C精密加工Last revision date: 13 December 2020.东莞市朝瑞自动化设备制造有限公司成立于2015-04-01,具体地址是在东莞市大朗镇新马莲骏马路68号B栋,自营外贸进出口权的英文名字为DSH GLOBAL PARTS MACHINING CO.,LTD。
朝瑞公司自成立以来,一直致力于专业为全球客户生产高精密模具和各种定制化的自动化设备及零部件加工产品。
朝瑞公司目前具体在以下几个方面能够为全球客户提供具有高品质,低成本,且按时保证交期的产品。
01:各种金属和非金属精密零部件的CNC原型打样,批量加工和OEM,CM组装。
02:生产线上用的专用自动化工装夹具设备的设计和制造。
03:汽车模具零配件的精密加工。
04:塑胶注塑模具的设计,制造和塑胶件的量产。
05:五金冲压模具的设计,制造和冲压件的量产。
06:铝,锌和镁精密铸造模具的设计,制造和压铸件的量产。
我们的客户遍及全球尤其欧美地区。
目前产品所涉及的行业也包括诸多领域,比如:智能机器人,通讯设备,汽车,履带滑板车,医疗设备,专用检测设备,打印机,航空航天设备和水下探测设备等。
我们有能力与客户一起从新产品的工程开发就开始参与,直到新产品进入正式大批量生产。
我们可以为客户改善加工工艺流程以便降低成本同时控制产品品质。
我们自己工厂有许多先进的CNC精密加工设备,我们有一个富有技术和管理经验的工程和品质团队来保证我们的服务。
朝瑞公司期望能够在自动化设备和工装夹具模具的行业中,为客户提供全球化一流的精密零部件加工产品。
朝瑞模具公司总会不断的从客户的角度去思考和解决问题,不断的提升对客户的最佳服务意识,以实现客户以最低的成本,快速的采购到高品质的产品。
朝瑞公司一直希望能与客户建立长久的双赢合作关系,以根据客户的切实需求,协助客户研发和创新。
5、现场化的模具检测技术精密模具的发展,对测量的要求越来越高。
精密的三坐标测量机,长期以来受环境的限制,很少在生产现场使用。
CNC机床加工中的零件加工质量保证与控制

CNC机床加工中的零件加工质量保证与控制CNC机床是一种高精度自动化加工设备,已经广泛应用于各种制造业领域。
而在CNC机床加工过程中,零件加工质量的保证与控制是至关重要的。
本文将从工艺规划、机床选择、刀具选用、工艺参数控制这几个方面来论述CNC机床加工中的零件加工质量保证与控制。
1. 工艺规划在CNC机床加工中,工艺规划是决定零件加工质量的关键。
首先,对于不同的零件加工过程,需要制定相应的工艺路线和工艺流程。
工艺路线要考虑到零件的形状、尺寸和加工要求,以及机床的特点和刀具的选择。
而在工艺流程中,需要详细规定每个工序的切削刀具、切削速度、进给量等参数。
只有合理的工艺规划,才能确保零件加工的质量。
2. 机床选择CNC机床的选择直接影响着零件加工的质量。
首先,要选择适合零件加工的机床类型。
例如,对于复杂形状的零件,可以选择五轴联动机床,以实现多角度、多方向的加工。
其次,要考虑机床的精度和稳定性。
精度高的机床可以保证零件加工的尺寸精度和表面质量;而稳定性好的机床可以提高加工效率和稳定性。
最后,要注意机床的维护保养,定期进行润滑和检修,以保证机床的正常运行和寿命。
3. 刀具选用刀具是CNC机床加工中的关键工具,对零件加工质量有着重要的影响。
合理的刀具选用可以提高加工效率和加工质量。
首先,要根据零件材料和加工要求选择合适的刀具材料。
例如,对于加工硬度高的材料,可以选用硬质合金刀具,以提高切削效果和寿命。
其次,要根据零件形状和加工工艺选择不同类型的刀具,如铣刀、钻头、车刀等。
最后,要根据工艺参数和切削要求选择合适的刀具尺寸和刀具角度,以确保零件加工的质量。
4. 工艺参数控制在CNC机床加工中,工艺参数控制是提高零件加工质量的关键。
首先,要控制刀具进给量和切削速度。
合适的刀具进给量可以保证切削过程中的稳定性和效率;而合适的切削速度可以保证刀具切削力的平衡,避免刀具磨损和零件表面质量的损失。
其次,要控制刀具的刀具角度和切削方向。
CNC操作规范与质量控制

CNC操作规范与质量控制在现代制造业中,计算机数控(CNC)技术已经成为生产过程中不可或缺的重要环节。
为了确保CNC加工的质量和效率,操作规范和质量控制显得尤为重要。
本文将从CNC操作规范和质量控制两个方面进行详细阐述。
一、CNC操作规范1.1 程序编写规范在编写CNC加工程序时,应遵循以下规范:- 确保程序逻辑清晰,注释详细,易于理解和修改。
- 避免程序中出现死循环和逻辑错误,确保程序的稳定性和可靠性。
- 严格遵守加工工艺要求,确保零件加工精度和表面质量。
1.2 设备操作规范操作CNC设备时,应注意以下规范:- 在操作之前,应对设备进行全面检查,确保设备运行正常。
- 严格按照操作手册和工艺要求进行操作,避免操作失误导致零件损坏。
- 定期对设备进行维护保养,确保设备长期稳定运行。
二、质量控制2.1 零件加工质量控制在CNC加工过程中,应注意以下质量控制要点:- 对零件加工前后进行精密测量,确保加工精度符合要求。
- 定期对刀具和夹具进行检查和更换,避免刀具磨损和夹具变形影响加工质量。
- 对加工过程中产生的废品进行分类和分析,及时发现问题并进行改进。
2.2 加工工艺质量控制控制加工工艺质量是确保CNC加工质量的关键:- 对加工工艺参数进行合理设置和调整,确保加工过程稳定和高效。
- 对加工过程进行实时监控和记录,及时发现问题并采取措施解决。
- 定期对加工工艺进行评估和改进,提高加工效率和质量水平。
三、CNC操作规范与质量控制的意义CNC操作规范和质量控制的重要性不言而喻:- 遵循规范操作和质量控制可以有效提高生产效率,减少生产成本。
- 严格控制加工质量可以确保产品质量稳定,提高客户满意度。
- 规范操作和质量控制是现代制造业发展的必然趋势,也是企业提升竞争力的重要手段。
四、CNC操作规范与质量控制的挑战与对策在实际操作中,CNC操作规范和质量控制面临一些挑战:- 人员技术水平参差不齐,规范操作和质量控制需培训和提升。
富士康cnc提案改善范文

富士康cnc提案改善范文尊敬的领导和同事们:咱在富士康干CNC这活儿也有段时间了,发现有些地方就像鞋子里的小石子,不弄出来总是硌得慌,所以今天来提几个改善的点子,希望能让咱这工作干得更顺溜儿。
一、关于CNC刀具管理的改善。
1. 现状。
咱每天要用好多刀具来加工那些精密的零件,可现在刀具的存放和领取有点乱套。
刀具就那么乱七八糟地堆在工具箱里,每次找个合适的刀具都得翻个底朝天,就像在一堆乱麻里找线头一样。
而且领刀具的流程也麻烦,要填一堆单子,跑来跑去,耽误不少加工的时间。
2. 改善建议。
咱可以做一个专门的刀具架,像图书馆的书架那样,给每个刀具都安排个小格子,在格子上标明刀具的型号、规格啥的。
这样一眼就能找到想要的刀具,多方便呐。
再搞个简单的电子管理系统,在电脑或者手机上就能申请领取刀具,仓库那边收到申请,直接把刀具准备好,咱过去拿就行,就跟点外卖似的,省了不少事儿。
3. 预期效果。
这样一来,每天找刀具的时间至少能节省个20 30分钟呢。
刀具管理更有条理,也不容易丢刀具了,那可是能给公司省下不少买新刀具的钱,咱加工的效率也能提高不少,说不定产量能多增加个百分之几呢。
二、CNC机床清洁与保养的改善。
1. 现状。
咱这CNC机床可是咱干活儿的宝贝,但现在清洁保养的工作做得不咋地。
机床里面的切屑和油污经常积累得厚厚的,就像给机床穿了一层脏兮兮的铠甲。
这不仅影响机床的美观,更重要的是对机床的精度和寿命有影响。
每次保养的时候,都是随便擦一擦,有些死角根本就清理不到。
2. 改善建议。
咱可以设计一种专门清洁CNC机床的工具,比如说那种带伸缩功能的小刷子,就像变形金刚似的,可以伸到机床的各个角落。
再定期安排专人负责机床的深度保养,给这个专人配备一套专门的清洁保养工具包,里面有各种清洁液、抹布、小铲子啥的。
然后呢,在机床旁边贴个小日历,把保养的日期标得清清楚楚,就像给机床定个健康检查的日程表一样。
3. 预期效果。
机床干净了,精度就能保持得更好,加工出来的零件质量肯定杠杠的。
复杂型腔铝合金零件在数控机床中的加工
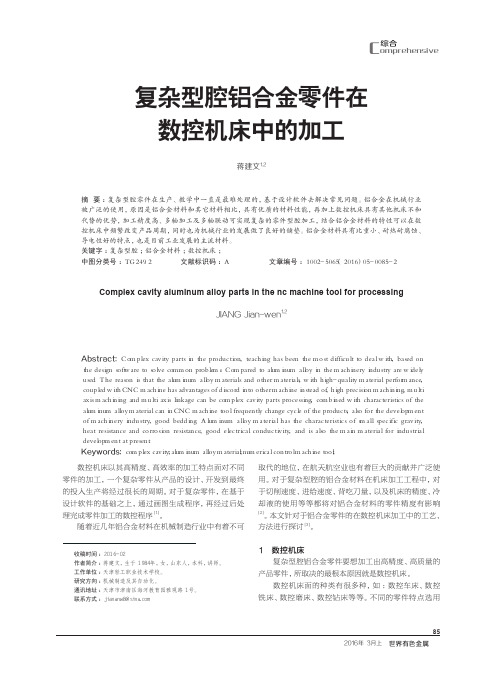
Abstract: Complex cavity parts in the production, teaching has been the most difficult to deal with, based on the design software to solve common problems. Compared to aluminum alloy in the machinery industry are widely used. The reason is that the aluminum alloy materials and other materials, with high-quality material performance, coupled with CNC machine has advantages of discord into other machine instead of, high precision machining, multi axis machining and multi axis linkage can be complex cavity parts processing, combined with characteristics of the aluminum alloy material can in CNC machine tool frequently change cycle of the products, also for the development of machinery industry, good bedding. Aluminum alloy material has the characteristics of small specific gravity, heat resistance and corrosion resistance, good electrical conductivity, and is also the main material for industrial development at present. Keywords: complex cavity;aluminum alloy material;numerical control machine tool;
CNC加工标准(草稿)

三CNC编程的依据1 CNC加工委托单(付图)注明2 模具材料、加工要求、加工顺序3 机床参数,刀具参数,切削数据4 EDM数据。
四CNC 编程流程1 认真分析模具的结构及产品,导出需加工的部件.2.导入加工部件。
3.①认真检查模型分中情况(可用模胚查看方法检查),需多面加工的考虑清楚加工面的顺序,工件的装夹方式(压板或底板),确定基准摆放方向,需要垫高加工的要在CNC加工程序单上注明,。
②认真检查模具的碰穿面,擦穿面,分型面,料位面,避空面,装配面,EDM面的位置,模型中所要加工的R角大小,尖角位置,需要做加工辅佐面的要清楚并先做好导入加工图型以便加工,认真留意加工委托单上的加工要求。
做到心中有数,用刀具大小,加工方式,余量控制心中有个大概的轮廓。
4首要加工模具R角位置,R角加工注意问题:①清楚材料高度,底部预留0.3—0。
5mm 余量。
②单边避空0.2mm。
③用大飞刀加工。
④使用等高加工方式.5一次粗加工.加工方式:①平行区域区域清除模型——相对简单模型适用.②偏置区域清除模型——常用开粗。
开粗余量控制侧壁0。
35-0。
5mm,底部0.15—0。
3mm.热处理材料总体;0.5mm。
6二次开粗加工。
加工方式:①偏置残留加工--建议使用:安全性高,加工均匀,残留计算准确。
②等高二次加工-—对于简单模型适用,加工均匀,加工时间短,计算时间快。
③平行开粗加工-—相对简单弧面模型,加工时间短,进给量可适当大,计算时间最快。
7曲面中光加工(大部分模具需中光)。
加工方式:①等高精加工——常用中光加工.②平行精加工——常用中光加工③三维偏置精加工等等。
.认真检测好开粗时的残留余量,部位。
适用合理的加工方式从而保证中光加工的均匀,余量的一致.曲面余量控制0.05-0。
12mm之间平面中光加工.加工方式①平行平坦面加工①偏置平坦面加工.中光平面时注意侧面的预留余量,底部余量0.05—0.08mm.8 曲面精光加工。
多腔缸体零件端面铣削加工的高精密夹具设计及其优化

Z nj n OU We —u ,L U G o l n HAO Ja -a ANG Ja —u , HANG Xi — n I u - a g ,Z i in c i,Y in g o Z n l g ,WAN o G Ke ( . c olo c a ia E gn eig h n h i io T n iest h n h i 0 2 0,C ia . x 1 S h o fMe h nc l n iern ,S a g a a o g Unv ri J y,S a g a 2 0 4 hn ;2 Wu i
B s Pei o ahn r C . t , ins x 2 4 6 , hn ) et rc i M c ie o ,Ld J guWu i 1 1 1 C ia sn y a
Absr c t a t:Th e mul p e c v t ng n y i e sa c m pl ae tu tr nd we k sif s . Fo usn t l - a iy e i e c l i nd rha o i t d sr cu e a a tfne s c c ig o h s r blm s,t spa e e e t i h- r c so o ai g a lm pig d sg o h r p e e’ n te ep o e hi p rpr s n s a h g p e ii n l c tn nd ca n e i n f rt e wo k i c
o tm ia in o he fx u e tu t r s u e o ee m i e t e fna sg o h hg p e ii xu e p i z t ft t r sr cu e i s d t d t r n h o i i lde i n ft e ih— r cson f tr . i Th e u t h w h tt e o tm ii g d sg x i t etrpe f r a c ha e o i i ld sg e r s ls s o t a p i z n e i n e hbisb te ro m n e t n t rg na e i n,be a e h h c us
CNC机床加工中的加工精度与加工质量控制

CNC机床加工中的加工精度与加工质量控制在现代制造业中,CNC机床是一种非常重要的工具。
它的高精度与高效率使其成为各个行业中的核心设备。
然而,CNC机床加工的加工精度与加工质量控制是一个至关重要的问题。
本文将探讨CNC机床加工中的加工精度控制方法以及对加工质量的影响。
一、加工精度的定义与影响因素在CNC机床加工过程中,加工精度是指零件加工后与设计要求之间的偏差。
加工精度是评价加工质量优劣的重要指标之一,其高低直接关系到零件的功能和性能。
加工精度的主要影响因素包括机床本身的精度、切削工具的质量、刀具刃磨技术、刀具路径规划、工艺参数的选择等等。
尤其是CNC机床本身的精度,对于零件的加工精度有着至关重要的影响。
二、加工精度控制的方法为了保证CNC机床加工过程中的加工精度,需要采取一系列的控制方法。
1. 选择合适的刀具与刀具路径规划在CNC机床加工中,选择合适的刀具是非常重要的。
合适的刀具能够提高加工效率,并且减小加工精度的误差。
同时,刀具路径的规划也非常关键,应尽量减小刀具在加工过程中的摆动,从而减小加工误差。
2. 优化工艺参数工艺参数的选择对于CNC机床加工的加工精度有着重要的影响。
优化工艺参数可以减小加工过程中的振动和变形,从而提高加工精度。
因此,合理设置切削速度、进给速度和切削液的使用量等参数十分必要。
3. 加强刀具管理与维护刀具的质量和磨损程度对加工精度有着重要影响。
定期对刀具进行检测和维护,及时更换磨损严重的刀具,可以有效地控制加工精度。
三、加工质量的控制在CNC机床加工中,加工精度的控制直接影响到最终的加工质量。
1. 减小加工误差加工误差是导致加工质量下降的主要原因之一。
通过优化加工工艺和完善工艺参数选择,可以减小加工误差,提高加工质量。
2. 提高表面质量表面质量是衡量加工质量的重要指标之一。
采用合适的刀具与加工工艺,控制切削过程中的振动和磨损,可以有效提高零件的表面质量。
3. 控制尺寸精度尺寸精度是CNC机床加工质量的重要参数。
CNC机床加工中的加工质量保证与控制

CNC机床加工中的加工质量保证与控制在现代制造业中,CNC(计算机数控)机床的应用已经成为普遍趋势。
CNC机床以其高精度、高效率的加工能力,为各行业的生产流程带来了重大改变。
然而,在CNC机床加工过程中,如何保证和控制加工质量成为一个重要的问题。
本文将会探讨CNC机床加工中的加工质量保证与控制,并提供一些建议和方法。
一、CNC机床加工质量的保证1.合理的加工方案设计在CNC机床加工过程中,一个合理的加工方案设计是保证加工质量的第一步。
合理的加工方案应包括对于零件的尺寸要求、材料特性、加工工艺等多个因素的综合考虑。
通过合理的设计,可以提前避免加工过程中可能出现的问题,从而保证加工质量的稳定性。
2.严格的设备维护与保养CNC机床作为一台高精密的加工设备,需要进行定期的维护与保养。
通过定期的设备检查、润滑以及部件更换,可以确保机床的运行状态良好,并减少因设备故障引起的加工质量问题。
同时,设备保养还能延长机床的使用寿命,提高生产效率。
3.严格的工艺控制CNC机床加工的每一个工序都需要严格遵循工艺规程。
工艺规程中应包括加工参数、刀具选用、切削液使用等详细要求。
只有遵循规程,才能保证零件的尺寸和表面质量符合要求。
同时,采用合适的工艺参数和刀具也能最大程度地提高加工效率和质量。
二、CNC机床加工质量的控制1.加工中的测量与检验CNC机床加工过程中,及时的测量与检验是保证加工质量的重要手段之一。
可以借助各种测量仪器和设备,对加工过程中的工件进行尺寸、形状、表面粗糙度等性能指标的检测。
通过及时的检验,可以及早发现加工中的问题,并采取相应措施进行调整或修正。
2.加工参数的优化与调整CNC机床加工中,各项加工参数的选择对于加工质量具有直接的影响。
通过不断地优化和调整加工参数,可以达到更好的加工效果和更高的加工质量。
例如,在铣削加工中,合理选择进给速度和切削速度,可以避免零件表面出现过大的切痕和热疲劳现象,保证加工表面质量的良好。
机械行业精密机械零件加工工艺改进方案
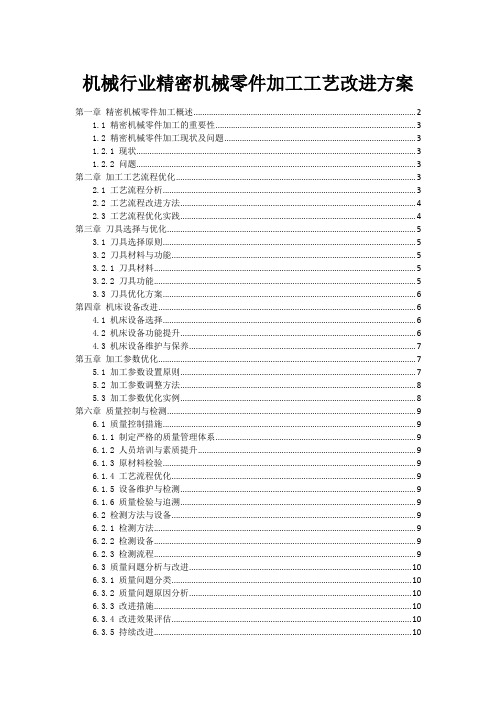
机械行业精密机械零件加工工艺改进方案第一章精密机械零件加工概述 (2)1.1 精密机械零件加工的重要性 (3)1.2 精密机械零件加工现状及问题 (3)1.2.1 现状 (3)1.2.2 问题 (3)第二章加工工艺流程优化 (3)2.1 工艺流程分析 (3)2.2 工艺流程改进方法 (4)2.3 工艺流程优化实践 (4)第三章刀具选择与优化 (5)3.1 刀具选择原则 (5)3.2 刀具材料与功能 (5)3.2.1 刀具材料 (5)3.2.2 刀具功能 (5)3.3 刀具优化方案 (6)第四章机床设备改进 (6)4.1 机床设备选择 (6)4.2 机床设备功能提升 (6)4.3 机床设备维护与保养 (7)第五章加工参数优化 (7)5.1 加工参数设置原则 (7)5.2 加工参数调整方法 (8)5.3 加工参数优化实例 (8)第六章质量控制与检测 (9)6.1 质量控制措施 (9)6.1.1 制定严格的质量管理体系 (9)6.1.2 人员培训与素质提升 (9)6.1.3 原材料检验 (9)6.1.4 工艺流程优化 (9)6.1.5 设备维护与检测 (9)6.1.6 质量检验与追溯 (9)6.2 检测方法与设备 (9)6.2.1 检测方法 (9)6.2.2 检测设备 (9)6.2.3 检测流程 (9)6.3 质量问题分析与改进 (10)6.3.1 质量问题分类 (10)6.3.2 质量问题原因分析 (10)6.3.3 改进措施 (10)6.3.4 改进效果评估 (10)6.3.5 持续改进 (10)第七章节能减排与环保 (10)7.1 节能减排措施 (10)7.1.1 提高能源利用效率 (10)7.1.2 优化加工工艺 (10)7.1.3 强化生产管理 (10)7.2 环保设备与应用 (11)7.2.1 环保型设备选型 (11)7.2.2 环保型设备应用 (11)7.3 环保工艺改进 (11)7.3.1 切削液替代技术 (11)7.3.2 废液处理与回收 (11)7.3.3 废气处理与排放 (11)第八章生产效率提升 (12)8.1 生产流程优化 (12)8.1.1 流程简化 (12)8.1.2 流程标准化 (12)8.1.3 流程监控与改进 (12)8.2 自动化技术应用 (12)8.2.1 技术应用 (12)8.2.2 信息化技术融合 (12)8.2.3 智能制造系统 (12)8.3 生产效率提升策略 (13)8.3.1 设备管理与维护 (13)8.3.2 人力资源管理 (13)8.3.3 质量管理 (13)8.3.4 生产计划与调度 (13)第九章人力资源与管理 (13)9.1 人力资源管理策略 (13)9.1.1 人才引进与选拔 (13)9.1.2 人才激励机制 (13)9.2 员工培训与技能提升 (14)9.2.1 培训体系的建立 (14)9.2.2 技能提升策略 (14)9.3 管理体系改进 (14)9.3.1 组织结构优化 (14)9.3.2 管理制度完善 (14)第十章创新与发展 (15)10.1 技术创新与应用 (15)10.2 市场需求分析 (15)10.3 行业发展趋势与展望 (15)第一章精密机械零件加工概述1.1 精密机械零件加工的重要性精密机械零件加工在现代制造业中具有举足轻重的地位。
某雷达精密异型薄壁腔体零件的加工

囵
件 。这 种 设计 结 构 紧 凑 ,体 积小 ,在雷 达 整机 中 占用 空 间少 。但是 ,加工 制 造难 度较 大
’ A
。
图 1
2 结 构 和 工 艺 分 析
从设 计 图上看 .设计 是将 一个 整体馈 源从 中心轴 线一分 为左 、右相 等 的两半 工 艺方 案 的选 择 和 分 析
对 图纸 和 加工工 艺进 行分 析 ,我们 认 为在进 行工 艺方案 设计 时 ,必须 首先 考虑工 厂现 状 ,制定一 套适 应可 行加 工方 案 ,同时 尽 可能地 消除焊 接对 馈源 内腔 质量 的影 响 ,找出解 决这 一 问题 的方法 。如果 这一 问题 解决 不好 ,完 全有可 能造 成产 品报废 ,带来损 失 。 首 先 ,从设 计方 案和工 艺 中可 以看 出要求 左 、右半 波导 采用精 密铸 造 。根据 工厂 现状 我们 采 用 机 械 加工 和 焊 接 来 达 到设 计 要 求 ,材料 采 用 铝 合 金 6 6 ( 0 3 旧牌 号 L 3 ) 『1 D 1 3, 该 材料 属 于可锻 铝 ,具 有 良好 的机 械性 能 ,冷 、热 加工 性能好 ,同时也 具有 良好 的焊接 性
述 ,解决 了机械 加 工和焊接 中影 响产品质 量的 主要 因素 。提 出了较好 的加工 方 案。 ’
关键词 :馈 源 精 密异 型 薄壁 腔体
精 密数 控铣
1 引 言
在某 型 雷 达 中 ,馈 源是 由喇 叭部分 、H面 弯 曲波 导部 分 组 成 的精 密 异 型薄 壁 腔体 零
为左 半波 导 和右 半波 导 ( 见图 1 。左 、右 半 波导 采用 焊 接组 合而 成 馈源 。 左 、右半 波 导 ) 是组成 馈源 的主要 构件 ,在 左半 波导和 右半波 导上 分别各 有一 半波导 腔体 和半 边 喇叭 ,半
- 1、下载文档前请自行甄别文档内容的完整性,平台不提供额外的编辑、内容补充、找答案等附加服务。
- 2、"仅部分预览"的文档,不可在线预览部分如存在完整性等问题,可反馈申请退款(可完整预览的文档不适用该条件!)。
- 3、如文档侵犯您的权益,请联系客服反馈,我们会尽快为您处理(人工客服工作时间:9:00-18:30)。
壳体腔体类零件C N C
精密加工
Document number【AA80KGB-AA98YT-AAT8CB-2A6UT-A18GG】
东莞市朝瑞自动化设备制造有限公司成立于2015-04-01,具体地址是在东莞市大朗镇新马莲骏马路68号B栋,自营外贸进出口权的英文名字为DSH GLOBAL PARTS MACHINING CO.,LTD。
朝瑞公司自成立以来,一直致力于专业为全球客户生产高精密模具和各种定制化的自动化设备及零部件加工产品。
朝瑞公司目前具体在以下几个方面能够为全球客户提供具有高品质,低成本,且按时保证交期的产品。
01:各种金属和非金属精密零部件的CNC原型打样,批量加工和OEM,CM组装。
02:生产线上用的专用自动化工装夹具设备的设计和制造。
03:汽车模具零配件的精密加工。
04:塑胶注塑模具的设计,制造和塑胶件的量产。
05:五金冲压模具的设计,制造和冲压件的量产。
06:铝,锌和镁精密铸造模具的设计,制造和压铸件的量产。
我们的客户遍及全球尤其欧美地区。
目前产品所涉及的行业也包括诸多领域,比如:智能机器人,通讯设备,汽车,履带滑板车,医疗设备,专用检测设备,打印机,航空航天设备和水下探测设备等。
我们有能力与客户一起从新产品的工程开发就开始参与,直到新产品进入正式大批量生产。
我们可以为客户改善加工工艺流程以便降低成本同时控制产品品质。
我们自己工厂有许多先进的CNC精密加工设备,我们有一个富有技术和管理经验的工程和品质
团队来保证我们的服务。
朝瑞公司期望能够在自动化设备和工装夹具模具的行业中,为客户提供全球化一流的精密零部件加工产品。
朝瑞模具公司总会不断的从客户的角度去思考和解决问题,不断的提升对客户的最佳服务意识,以实现客户以最低的成本,快速的采购到高品质的产品。
朝瑞公司一直希望能与客户建立长久的双赢合作关系,以根据客户的切实需求,协助客户研发和创新。
5、现场化的模具检测技术
精密模具的发展,对测量的要求越来越高。
精密的三坐标测量机,长期以来受环境的限制,很少在生产现场使用。
新一代三座标测量机基本上都具有温度补偿及采用抗振材料,改善防尘措施,提高环境适应性和使用可靠性,使其能方便地安装在车间使用,以实现测量现场化的特点。
6、镜面抛光的模具表面工程技术
模具抛光技术是模具表面工程中的重要组成部分,是模具制造过程中后处理的重要工艺。
目前,国内模具抛光至Ra0.05μm的抛光设备、磨具磨料及工艺,可以基本满足需要,而要抛至
Ra0.025μm的镜面抛光设备、磨具磨料及工艺尚处摸索阶段。
随着镜面注塑模具在生产中的大规模应用,模具抛光技术就成为模具生产的关键问题。
由于国内抛光工艺技术及材料等方面还存在一定问题,所以如傻瓜相机镜头注塑模、 CD、VCD光盘及工具透明度要求高的注塑模仍有很大一部分依赖进口。
罗百辉指出,模具表面抛光不单受抛光设备和工艺技术的影响,还受模具材料镜面度的影响,
这一点还没有引起足够的重视,也就是说,抛光本身受模具材料的制约。
例如,用45#碳素钢做注塑模时,抛光至Ra0.2μm时,肉眼可见明显的缺陷,继续抛下去只能增加光亮度,而粗糙度已无望改善,故目前国内在镜面模具生产中往往采用进口模具材料,如瑞典的一胜百136、日本大同的PD555等都能获得满意的镜面度。
镜面模具材料不单是化学成分问题,更主要的是冶炼时要求采用真空脱气、氩气保护铸锭、垂直连铸连轧、柔锻等一系列先进工艺,使镜面模具钢具内部缺陷少、杂质粒度细、弥散程度高、金属晶粒度细、均匀度好等一系列优点,以达到抛光至镜面的模具钢的要求。