有效提高湿摩擦色牢度的措施
常见色牢度问题及解决方案

常见色牢度问题及解决方案据统计,色牢度问题是所有染色疑问中被问及最多的问题之一。
染色牢度对染色、印花织物的质量要求很高,染色状态变异的性质或程度可用染色牢度来表示。
它与纱线结构、织物组织、印染方法、染料种类及外界作用力大小有关。
不同的染色牢度要求,会引起很大的成本差异和质量差异。
一、6种主要纺织牢度正常织物的染色牢度,一般要求达到3~4级才能符合穿着需要.以下内容概括了染整中6种主要的纺织牢度:1、日晒牢度日晒牢度是指有颜色织物受日光作用变色的程度。
其测试方法可采用日光照晒也可采用日光机照晒,将照晒后的试样褪色程度与标准色样进行对比,分为8级,8级最好,1级最差。
日晒牢度差的织物切忌阳光下长时间曝晒,宜于放在通风处阴干。
2、摩擦牢度摩擦牢度是指染色织物经过摩擦后掉色程度,可分为干态摩擦和湿态摩擦。
摩擦牢度以白布沾色程度作为评价原则,共分5级(1~5),数值越大,表示摩擦牢度越好。
摩擦牢度差的织物使用寿命受到限制。
3、洗涤牢度水洗或皂洗牢度是指染色织物经过洗涤液洗涤后色泽变化程度。
通常采用灰色分级样卡作为评定标准,即依靠原样和试样褪色后的色差来进行评判。
洗涤牢度分为5个等级,5级最好,1级最差。
洗涤牢度差的织物宜干洗,如若进行湿洗,则需加倍注意洗涤条件,如洗涤温度不能过高、时间不能过长等。
4、熨烫牢度熨烫牢度是指染色织物在熨烫时出现的变色或褪色程度。
这种变色、褪色程度是以熨斗同时对其它织物的沾色来评定的。
熨烫牢度分为1~5级,5级最好,1级最差。
测试不同织物的熨烫牢度时,应选择好试验用熨斗温度。
5、汗渍牢度汗渍牢度是指染色织物沾浸汗液后的掉色程度。
汗渍牢度由于人工配制的汗液成份不尽相同,因而一般除单独测定外,还与其它色牢度结合起来考核。
汗渍牢度分为1~5级,数值越大越好。
6、升华牢度升华牢度是指染色织物在存放中发生的升华现象的程度。
升华牢度用灰色分级样卡评定织物经干热压烫处理后的变色、褪色和白布沾色程度,共分5级,1级最差,5级最好。
影响湿摩擦牢度的有关问题及其提高措施
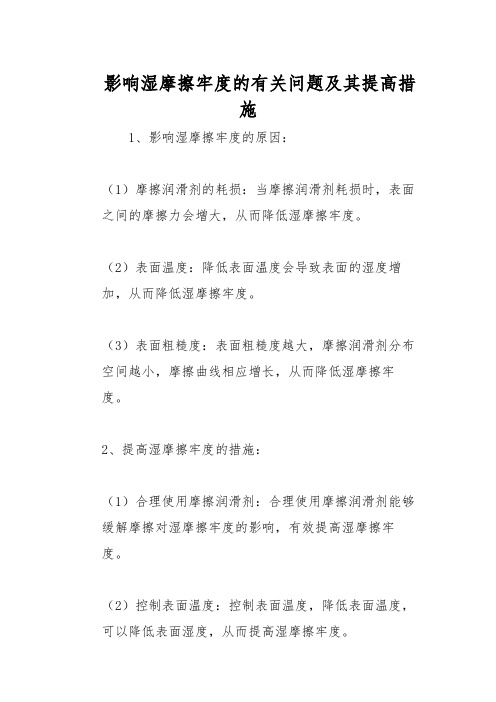
影响湿摩擦牢度的有关问题及其提高措
施
1、影响湿摩擦牢度的原因:
(1)摩擦润滑剂的耗损:当摩擦润滑剂耗损时,表面之间的摩擦力会增大,从而降低湿摩擦牢度。
(2)表面温度:降低表面温度会导致表面的湿度增加,从而降低湿摩擦牢度。
(3)表面粗糙度:表面粗糙度越大,摩擦润滑剂分布空间越小,摩擦曲线相应增长,从而降低湿摩擦牢度。
2、提高湿摩擦牢度的措施:
(1)合理使用摩擦润滑剂:合理使用摩擦润滑剂能够缓解摩擦对湿摩擦牢度的影响,有效提高湿摩擦牢度。
(2)控制表面温度:控制表面温度,降低表面温度,可以降低表面湿度,从而提高湿摩擦牢度。
(3)改善表面粗糙度:改善表面粗糙度,可以有效增加模具表面的摩擦润滑剂分布空间,从而改善湿摩擦牢度。
11招全方位提高织物高湿摩擦牢度?

11招全方位提高织物高湿摩擦牢度?纺织产品中,影响耐湿摩色牢度的主要因素有,织物的种类、织物组织结构;纺织物前处理,如退浆、煮炼、漂白、丝光等;纺织染料的选择,以及工艺、温度、时间等的控制是否严格,还有助剂的选择和使用是否正确;纺织物的后处理是否得当等等。
为了更好的提高织物湿摩擦牢度,小编建议大家可以从以下几方面入手。
针对这些影响耐湿摩擦色牢度的因素,我们应注意以下几点:1.根据纺织材料学的分析,一般化纤类织物比棉等天然织物的耐湿摩擦色牢度要好,稀薄织物比厚重织物要好。
所以在纺织物处理时,各道工序处理要匀透,以提高纤维的可吸性与染料的反应性或吸附固着性,使染料充分上染。
在染色过程中,要求控制严格,对助剂等须正确选择正确使用。
为提高纺织产品耐湿摩色牢度,在纺织物后处理中,可进行充分皂洗,如涤纶纤维用分散染料染色后高温定型导致染料泳移到纤维表面,引起摩擦牢度下降。
针对这种情况,加固色剂或平滑剂可在一定程度上提高耐摩擦色牢度。
2.选择染料时,选择具有良好提升性和匀染性的染料,良好的提升性和匀染性都有利于染料的渗透和扩散,可从一定程度上提高湿摩擦牢度。
染料应具有一定的水溶性和直接性,水溶性基团不能太多,否则会影响后面的湿摩擦牢度。
而直接性也应该选择以中等为最佳。
所选染料应具有的直接性不能太高,一般情况下应大于70%。
3.棉等天然织物耐湿摩擦色牢度相对较差,因此对棉坯布而言应选择纱支均匀、布面光洁的坯布。
若需要进行预处理应该选用高效前处理剂。
4.活性染料染色用水应尽量使用软水或去离子水,以此减少水中的钙镁等离子对染料的影响,从而提高纤维对染料的吸收性,使染料在纤维分子内固色更加稳定。
5.使用高效固色剂,所选固色剂应该是能在染料和纤维之间链接形成化合物,在与染料反应的时候,又可与纤维素纤维反应交联,使染料与纤维能够紧密牢固地联系在一起,加强染料与纤维的结合,防止染料从纤维上脱落或泳移到纤维表面,避免造成染色牢度下降。
提高纺织品色牢度的措施

提高纺织品色牢度的措施提高纺织品色牢度的主要措施有以下一些:1.前处理工艺(1)烧毛烧毛是烧去织物表面茸毛,以增加织物表而的光洁度和平滑度,减少摩擦系数,提高摩擦色牢度.(2)煮漂煮练要煮透,漂白的白度要达到要求,去除浆料和棉籽壳后,织物的吸水性提高,毛效达到8.lOcm/30s以上,可以提高染色时染料的透染性,匀染性,上染率和固色率,染料浮在织物表面的浮色越少,摩擦色牢度和水洗色牢度越好. (3)丝光丝光使织物表面更加平整,提高织物表面的光泽和滑爽度,提高摩擦色牢度和皂洗色牢度,丝光必须严格控制好碱浓度,光的效果.2.染色工艺(1)染料的选用达到充分丝摩擦色牢度提高0.5~1.0级.它是改进日晒色牢度的主要措施,其要点有:(1)染料的选择染料应选用扩散性好的染料,易扩散到纤维IAJ部,上色率和固色率高,配伍性好,易洗净和浮色少的染料.避免选用直接性高扩散性差的染料,造成表而浮色多,其水解染料不易洗除,使摩擦色牢度和皂洗色牢度下降.(2)染色工艺染色应采用浸染法染色,使织物有充分的时问与染料发生反应,达到染料与纤维充分上染和固着,具有较高的固色率,较好的而耐摩擦色牢度和皂洗色牢度.染色时,温度太高,时间太长,浴比太小及pH值太高,都将导致染料水解,染料浮色增加,导致摩擦色牢度和皂洗色牢度的下降,故而控制染色工艺是必需的.3.后处理(1)水洗皂洗处理处理是将染色后的织物内部和表而浮色染料,残余碱剂和电解质等杂质去除,使染色织物达到最佳麾擦色牢度和皂洗色牢度,日晒色牢度.后处理方法是通过水洗,皂洗和机械外力作用,去除染料浮色,其中皂洗所用助剂必须具有良好的渗透功能,而与染料亲和并形成胶束,降低染料和纤维的亲和力,形成内核为染料的胶束后稳定地分散在水中,可选用具有渗透和分散功能的阴离子型和非离子型表面活性剂复配而成,达不到彻底洗除浮色的效果,洗涤后期和洗后织物的pH 值应接近或保持中性,防止在洗涤过程中或洗后存放时染料发生断键,色牢度下降.后处理过程中的水质硬度高,将使浮色染料的水溶性基团形成难溶于水的色淀,严熏影响浮色染料的去除.(2)后整理在后整理上采用固色剂,以提高印染后的织物色牢度,专用固色剂可使活性染料深浓色渝因染料褪色的过程主要是由于染料的发色基团如偶氨键等发生了光致氧化反应或者光致还原反应,以及这两种反应同时作用所导致的,故要提高染色织物的日晒牢度,染料的选择是关键.应首先选用同晒牢度高的染料,在黄色色谱中,日晒牢度高的黄色染料多为吡唑啉酮和以吡啶酮为偶合组分或以2.氨基.3.6.8.萘三磺酸为熏氨组分的单偶氮染料,由于它们的偶氮基邻位都引入了吸电子基,使偶氮基上氦原子的电子云密度降低,不利于生成氧化偶氮化物,从而阻止或降低光氧化反应的发生,因此这些染料的日晒牢度较好,日晒色牢度都能达到5级以上,如C.I.活性黄2(K型,6.7级)等;蓝色色谱同晒牢度高的染料多以蒽醌型和酞菁型结构,如C.I.活性蓝2(6.7级)等;红色色谱活性染料的同晒牢度普遍较低,特别是浅色,只有一些偶氨基两个相邻位置含有配位能力的羟基与铜形成稳定的螫合环,可以提高日晒牢度,如C.I.活性红23(7级)等.(2)染料昀拼色在染色拼色时,选用日晒牢度水平相当的组分染料.拼色组分中含量相对较少的染料可选择同晒牢度等级较高的染料,从而保证织物色牢度的日晒等级.(3)固色剂固色剂对染料的同晒牢度有着紧密的关系,固色剂大致有三种:阳离子表而活性剂固色剂,非表面活性季铵盐型固色剂和反应性固色剂.大多数阳离子表而活性剂固色剂是季铵盐,锍盐或磷盐.此类固色剂与染料在纤维上生成色淀,虽水洗牢度很好,但往往会降低染料原有的日晒牢度,所以当日晒牢度要求高时,尽量避免选用这类固色剂.非表而活性季铵盐型固色剂,该固色剂既不属于合成树脂,本身又不具有表面活性,一般含有两个或多个季铵基团,此类固色剂和铜盐混合使用也能提高活性染料的日晒牢度,例如固色剂NFC是一种阳离子型多胺缩合体和特殊金属盐的混合物,应用时色变小,不影响染色的色光牢度,并有很好的皂洗牢度.反应型固色剂,活性染料染色以染料一纤维共价键结合,具有优良的湿处理牢度,但部分染料染色后会发生断键,水解,针对这种情况,反应型固色剂既具有与纤维结合的活性基团,又具有能与染料阴离子结合的阳离子基团,具有这种交联作用的固色剂,牢度更好.这类固色剂如LTG-8080,不影响色光,且同晒牢度佳,另外用在真丝织物上的LTF-S6F固色剂,提高皂洗,摩擦等牢度的同时不影响手感,色光和日晒牢度.其它的如上海大祥化学工业有限公司的固色剂3A粉,上海助剂厂的固色剂DS等,这类固色剂使用后,织物的色变小,只晒牢度不下降.。
一种提高毛用活性染料深色湿摩擦牢度的方法
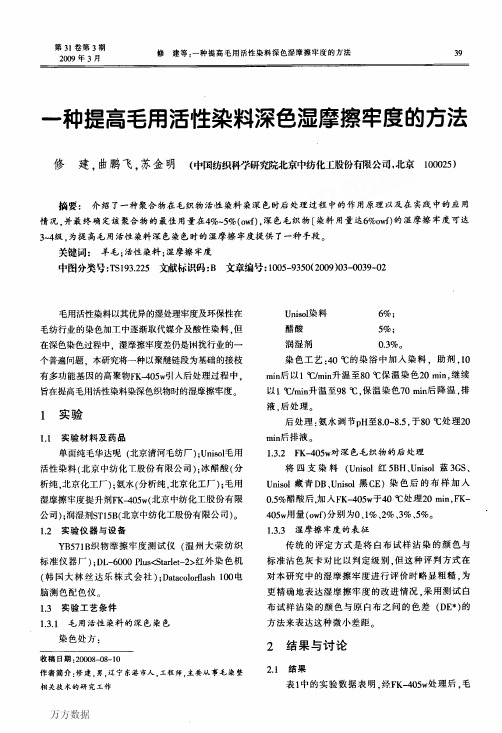
1, 低泡 泡沫太高會導致水洗效率下降,既浪費水資源, 淨洗也不徹底,嚴重會導致布面出現色斑。
2, 防沾色 無論是對於白地印花還是普通的染色紡品的皂 洗,都要求很好的防沾色,否則染料容易反沾汙 織物,導致牢度下降。 3, 抗鹽性能 活性染料染色後,皂洗工作液中含有大量無機 鹽,如果皂洗劑耐鹽性不夠,則會出現皂洗前後 的皂洗力不均一,色光、牢度等發生變化。
表面活性劑 馬丙共聚物 EDDHA-Na
防沾色性能比較,馬丙共聚物≈EDDHA-Na>表面 活性劑
4,抗鹽性能比較 通過電解質的電泳模擬皂洗工作液,電泳值
越高,耐電解質能力越好。
前言
活性染料印染色牢度不佳一般與印染後的清 洗不徹底有關,而消費者對活性染料印染物的色 牢度要求越來越高。因此皂洗劑的消耗量在整個 印染助劑所占的比例也越來越高,對於廣大印染 廠而言,每年都需要採購大量的皂洗劑,如何有 效的降低皂洗劑相關的採購成本,同時還能提高 皂洗效能,是降低生產成本的重要一環。
万方数据
Unisol染料 醋酸
6%: 5%;
润湿剂
O.3%。
染色工艺:40℃的染浴中加入染料,助剂,lO min后以l。C/min升温至80℃保温染色20 min,继续 以l。C/min升温至98 oC。保温染色70 rain后降温,排
液,后处理。
后处理:氨水调节pH至8.0~8.5,于80℃处理20 min后排液。 1.3.2 FK-一405w对深色毛织物的后处理
目前常用的皂洗劑
隨著科技的進步,特別是印染工作者不停的努 力,皂洗劑的經過幾代的發展和優勝劣汰,目前 常用的有三種: 1,表面活性劑類,多為脂肪醇醚類,如 AEO-9 等。
臺灣紡織研究期刊
活性染料湿摩擦牢度提升剂的制备原理及其应用技术

活性染料湿摩擦牢度提升剂的制备原理及其应用技术摘要:论述了活性染料染色存在织物湿摩擦牢度差的问题。
文中分析了湿摩擦牢度的测试方法,以及影响湿摩擦牢度的因素并提出了改进措施。
本文还列举了几种提升剂的制备及其应用技术。
关键词:活性染料湿摩擦牢度提升剂制备应用技术引言:活性染料深色染品的耐湿摩擦牢度差的问题,一直是长期困扰染整工作者的技术难题。
活性染料的耐湿摩擦牢度相对较差是由其自身的一些特性所决定。
例如染料自身的水溶性,在碱性条件下易水解而失去与纤维的反应性;与纤维分子反应形成的酯键或醚键易水解断键等。
因此,在生产实践中,分析湿摩擦牢度差的成因,加强各工序过程的控制和措施,弥补染料自身的缺陷,以提高产品的耐湿摩擦牢度,是染厂提高产品质量关键[1]。
活性染料具有色泽鲜艳、使用方便、色谱齐全、成本低廉等优点,取得了较快的发展,但还有很多处需要改进,如深浓色纺织品的摩擦牢度特别是湿牢度一直是困扰印染界的一大难题。
随着我国加入世贸组织,国际市场开放,关税壁垒已被打破,但技术壁垒即将成为我国出口贸易的主要障碍。
深浓色染色纺织品的耐湿摩擦牢度已成为外国所设置的纺织品贸易技术壁垒之一[2]。
本试验从活性染料的染色特性出发探讨了影响色牢度的原因及解决方法。
目录第一章活性染料的染色 (1)1.1染色理论 (1)1.1.1上染 (1)1.1.2 固着 (1)1.1.3后处理 (1)1.2 影响湿摩擦牢度的因素 (2)1.2.1染料的特性 (2)1.2.2 染色织物深度 (2)1.2.3织物的组织结构及其表面光洁度 (3)1.2.4 浮色 (3)1.2.5 水质 (4)1.3改进耐湿摩擦牢度的措施 (4)第二章湿摩擦牢度提升剂的制备 (5)2.1 湿摩擦牢度提升剂的分类及其作用机理 (5)2.1.1 吸附沉淀型湿摩擦牢度提升剂 (5)2.1.2交联型湿摩擦牢度提升剂 (5)2.1.3成膜覆盖隔离型湿摩擦牢度提升剂 (5)2.1.4固色剂型湿摩擦牢度提升剂 (5)2.1.5综合型湿摩擦牢度提升剂 (6)2.2提升剂的合成 (6)2.2.1阳离子型提升剂的制备 (6)2.2.2交联型提升剂的制备 (7)2.2.3聚氨酯型提升剂的制备 (8)2.2.4树脂类提升剂的制备 (9)第三章湿摩擦牢度提升剂性能的测试 (10)3.1固色处理和效果测试 (10)3.2湿摩擦牢度测试分析 (10)3.3 湿摩擦前后K/S 值的变化分析 (11)3.4 整理后织物色相的变化分析 (12)第四章提升剂应用性能的研究 (13)4.1整理剂对织物干、湿摩擦的提升性能 (13)4.2整理效果的耐洗性 (13)4.3整理剂对未染色织物的白度影响 (13)4.4对织物透气性和强力的影响 (13)4.5整理剂对织物风格的影响 (14)4.6整理前后织物日晒牢度的变化 (15)第五章展望 (15)参考文献 (16)第一章活性染料的染色1.1染色理论[3-6]1.1.1上染染料从染液内向纤维界面转移当靠近纤维到一定距离后染料分子迅速被纤维表面所吸附通过氢键范德华引力结合在纤维内外形成1个浓度差并向纤维内扩散直到纤维和溶液间的染料浓度达到平衡吸附量是固色的基础染料固着率与吸附量有很大关系因此应使染料尽量多地被吸附。
纺织产品如何使用湿摩擦牢度提升剂提升牢度

纺织产品如何使用湿摩擦牢度提升剂提升牢度纺织产品中影响耐湿摩擦牢度的因素有:织物的种类、织物组织结构;纺织物前处理,如退浆、煮练、漂白、丝光等;纺织染料的选择以及工艺、温度、时间等的控制是否严格,还有助剂的选择和使用是否正确;纺织品的后处理等。
针对这些影响耐湿摩擦色牢度的因素,我们应注意以下几点:1.根据纺织材料学的分析,一般化纤类的织物比棉织物等天然织物的耐摩擦色牢度要好,稀薄织物比厚重织物要好。
所以在纺织物处理时,各道工序处理要匀透,以提高纤维的可吸性与染料的反应性或吸附固着性,使染料充分上染。
在染色过程中,要求控制严格,对助剂等需正确选择正确使用。
为提高纺织产品耐湿摩擦牢度,在纺织品后处理中,可进行充分皂洗,如涤纶纤维用分散染料染色后高温定型导致染料泳移到纤维表面,引起摩擦牢度下降。
针对这种情况,加固色剂或平滑剂可在一定程度上提高耐摩擦色牢度。
2.选择染料时,选择具有良好提升性和匀染性的染料,良好的提升性和匀染性都有利于染料的渗透和扩散,可从一定程度上提高湿摩擦牢度。
染料应具有一定的水溶性和直接性,水溶性基团不能太多,否则会影响后面的湿摩擦牢度。
而直接性也应该选择中等为最佳。
所选染料应具有的直接性不能太高,一般情况下应大于70%。
3.棉等天然织物耐湿摩擦色牢度相对较差,因此对棉坯布而言应选择纱支均匀、布面光洁的坯布。
如果需要进行预处理应该选择高效前处理剂。
4.活性染料染色用水应尽量使用软水或去离子水,以此减少水中的钙镁离子对染料的影响,从而提高纤维对染料的吸收性,使染料在纤维分子内固色更加稳定。
5.使用高效固色剂,所选固色剂应该是能在纤维和染料之间链接形成化合物,在与染料反应的时候,又可与纤维素纤维反应交联,使染料与纤维能够紧密牢固的联系在一起,加强染料与纤维的结合,防止染料从纤维上脱落或泳移到纤维表面,避免造成染色牢度下降。
6.使用特种助剂,如增深剂等对染色织物进行整理,可减少染料用量而获得深浓色效应,同时提高湿摩擦色牢度。
技术│影响织物日晒牢度及深色湿摩擦牢度的因素及处理措施

技术│影响织物日晒牢度及深色湿摩擦牢度的因素及处理措施如何提高染色牢度,成为印染行业工程技术人员的研究课题。
特别是活性染料染浅色织物的日晒牢度、深浓色织物的湿摩擦牢度;分散染料的染后热迁移造成的湿处理牢度下降;以及高耐氯牢度、耐汗光牢度等,而影响色牢度的因素很多,提高色牢度的方法也有很多途径,如何通过在选择合适的染化料助剂,改进染整工艺,加强工序控制等方面,摸索了一些方法和措施,对染色牢度有一定的提高和改善,基本满足了市场需求。
活性染料浅色织物日晒牢度众所周知,染着在棉纤维上的活性染料,在日照下受到紫外线的攻击,染料结构中的发色团或助色团,会遭到不同程度的破坏,而导致色变或色浅,即产生日晒牢度问题。
国家标准对活性染料的耐光色牢度早已有规定,例如GB/T411-93棉印染布标准规定活性染料的染色布耐光牢度为4-5级,印花布耐光牢度为4级;GB/T5326精梳涤棉混纺印染布标准和FZ/T14007-1998棉涤混纺印染布标准均规定,分散/活性染色布耐光牢度为4级,印花布也是4级。
活性染料染浅色印染织物要达到这一标准是比较困难的。
染色母体结构与日晒牢度的关系活性染料的日晒牢度主要与染料的母体结构有关,活性染料母体结构的70-75%为偶氮型,其余为葸醌型、酞菁型和甲型。
偶氮型耐光牢度较差,蒽醌型、酞菁型和甲的耐光牢度较好。
黄色活性染料分子结构为偶氮型,母体发色体以吡唑啉酮和萘系三磺酸的日晒牢度最佳,蓝色谱的活性染料以蒽醌、酞菁、甲母体结构,日晒牢度优良,红色谱活性染料分子结构为偶氮型。
日晒牢度普遍较低,特别是浅色。
染色浓度与日晒牢度的关系染色试样的日晒牢度会随着染色浓度变化而不同,同一种染料在同一种纤维上染色的试样,它的日晒牢度随着染色浓度的增加而提高,主要是由于染料在纤维上的聚集体颗粒大小分布变化所引起的。
聚集体颗粒愈大,单位重量染料暴露于空气-水分等作用面积愈小,日晒牢度愈高。
染色浓度的增加会使纤维上的大颗粒聚集体的比例增加,日晒牢度也相应增加。
织物湿摩擦色牢度的影响因素浅析

织物湿摩擦色牢度的影响因素浅析在活性染料染色过程中,一部分染料直接与水发生水解反应,或者已与纤维键合的染料在一定条件下发生水解断键或氧化断键,这是纤维上浮色的两个主要来源。
这些浮色染料与纤维之间存在范德华力和氢键作用力,普通皂洗并不能将其去除干净,在外力摩擦下,织物上的浮色染料容易脱落,造成织物的摩擦色牢度变差,尤其是深色产品,往往达不到合格要求。
提高活性染料染色产品的摩擦色牢度,特别是湿摩擦色牢度,是一项亟待解决的技术难题。
1 摩擦沾色机理分析湿摩擦色牢度测试中,染料分子在外力摩擦作用下从织物上脱离,以水为媒介扩散到与之接触的标准白布上,扩散的动力来自于被测试织物与测试织物之间染料分子及其附着物的浓度梯度。
染色纺织品在与其他物体摩擦时染料脱落和沾色有两种方式:一种是纺织品上的染料脱落,沾染在摩擦物体表面;另一种是染色短纤维脱落,黏附在摩擦物体表面。
通常以前者为主。
2 影响染色织物湿摩擦色牢度的主要因素2.1 湿摩擦色牢度差的机理分析染色织物的湿摩擦色牢度差主要是由于织物表面浮色及纤维内部具有良好水溶性的染料发生扩散所造成的,本质上是由染料在纤维内部的扩散难易和染料与纤维之间直接性大小的矛盾决定的。
如果染料与纤维之间的直接性很大,则染料很容易上染纤维,与纤维大分子发生相互作用,牢固地键合在纤维大分子上,这有利于提高摩擦色牢度;但同时染料向纤维内部扩散的能阻也较大,染料分子不易向纤维内部扩散,难以染透整根纤维,大部分染料吸附在纤维表面,导致染色织物表面浮色较多,湿摩擦色牢度变差。
如果染料与纤维之间的直接性很小,则染料向纤维内部扩散的能阻较小,染料分子容易向纤维内部扩散,染透纤维,使染色织物表面浮色减少,湿摩擦色牢度提高;但另一方面,扩散进入纤维内部的染料也容易再扩散到纤维的表面,尤其是水溶性好的染料在湿摩擦时更容易扩散至纤维表面,导致纤维表面的浮色增多,导致湿摩擦色牢度降低。
扩散难易和直接性大小是矛盾的两个方面,二者相互影响,若要提高染色织物的湿摩擦色牢度,必须处理好这个矛盾。
干摩擦、湿摩擦牢度下降怎么解决

纺织产品中,影响耐摩擦色牢度的主要因素有:织物的种类、织物组织结构;纺织物前处理,如退浆、煮炼、漂白、丝光等;纺织染料的选择,以及工艺、温度、时间等的控制是否严格;还有助剂的选择和使用是否正确,纺织物的后处理等。
下面给大家介绍一下如何提高干湿摩擦牢度。
一、染料的选用活性染料的品种繁多,质量相差很大,选用符合染色质量标准的染料至关重要。
1、选用双活性基和多活性基的染料均三嗪类活性染料与纤维反应形成酯键,耐酸稳定性差,乙烯砜类染料与纤维反应以醚键结合,耐碱性差,双活性基团的染料耐酸耐碱稳定性提高。
2、选用直接性适宜的染料活性染料(如乙烯砜基活性染料)的直接性太高,则扩散性能差,染料易聚集在织物表面不易向纤维内部扩散和转移,易造成浮色多,难以洗净,但直接性也不能太低影响固色率,所以活性染料的直接性以中等为好,直接性的大小可由染料供应商提供的数据获得。
3、选用固色率高的染料固色率高的染料浮色少,固色率>80%,染后浮色量相对较少,有利于去除浮色;固色率<70%,(最终上染率—固色率)>15%的活性染料,其浮色很难清除,不适于染中深色。
4、选用提升力高的染料染色工艺设计,染料用量一般不宜超过染色饱和值的10%,过量的染料不能完全上染,固色不充分,未固色的染料附在被染物表面,影响被染物的湿摩擦牢度,染深色务必选用高吸尽率、高固色率和高提升力的染料,如双活性基和多活性基的活性染料。
二、选择纱支均匀、布面光洁的坯布,需要预处理时应该选用高效前处理剂处理。
三、染色用水应尽量使用软水或去离子水,可减少水中的钙、镁等离子对染色的影响。
四、柔软剂的选用目前市面上的柔软剂一般会让织物的干摩擦牢度和湿摩擦牢度下降半节左右,这在羊绒和羊毛面料上尤其明显。
如果染料选择得不好,织物很可能发生色牢度达不到要求的问题,而且难以通过后续工艺来解决。
我公司针对织物的色牢度问题开发的特色柔软剂EL-153拥有优异的蓬松、柔软、爽滑手感的同时能确保织物色牢度不下降,即使用在极易褪色的大红和翠蓝面料上也几乎不褪色。
染整生产中色牢度质量问题成因与措施
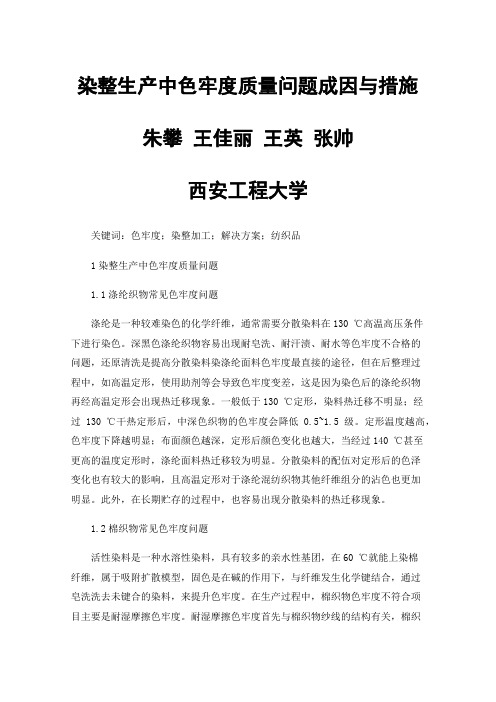
染整生产中色牢度质量问题成因与措施朱攀王佳丽王英张帅西安工程大学关键词:色牢度;染整加工;解决方案;纺织品1染整生产中色牢度质量问题1.1涤纶织物常见色牢度问题涤纶是一种较难染色的化学纤维,通常需要分散染料在130 ℃高温高压条件下进行染色。
深黑色涤纶织物容易出现耐皂洗、耐汗渍、耐水等色牢度不合格的问题,还原清洗是提高分散染料染涤纶面料色牢度最直接的途径,但在后整理过程中,如高温定形,使用助剂等会导致色牢度变差,这是因为染色后的涤纶织物再经高温定形会出现热迁移现象。
一般低于130 ℃定形,染料热迁移不明显;经过130 ℃干热定形后,中深色织物的色牢度会降低0.5~1.5 级。
定形温度越高,色牢度下降越明显;布面颜色越深,定形后颜色变化也越大,当经过140 ℃甚至更高的温度定形时,涤纶面料热迁移较为明显。
分散染料的配伍对定形后的色泽变化也有较大的影响,且高温定形对于涤纶混纺织物其他纤维组分的沾色也更加明显。
此外,在长期贮存的过程中,也容易出现分散染料的热迁移现象。
1.2棉织物常见色牢度问题活性染料是一种水溶性染料,具有较多的亲水性基团,在60 ℃就能上染棉纤维,属于吸附扩散模型,固色是在碱的作用下,与纤维发生化学键结合,通过皂洗洗去未键合的染料,来提升色牢度。
在生产过程中,棉织物色牢度不符合项目主要是耐湿摩擦色牢度。
耐湿摩擦色牢度首先与棉织物纱线的结构有关,棉织物如牛仔布等纱线较粗,表面摩擦阻力较大,在摩擦过程中易出现染料分子的脱落;其次在湿摩擦试验过程中,活性染料因具有较好的水溶性,使染料从纤维表面脱落而溶解在水中,造成湿摩擦色牢度变差。
活性染料染色织物的耐皂洗色牢度主要取决于未固着的染料,即水解染料和少量未反应染料数量。
提高活性染料染棉织物的耐湿摩擦色牢度,首先应选用色牢度较好的活性染料,染黑色时可选用两支黑色染料混拼,同时严格控制染色浓度,避免染料过饱和而产生较多浮色;其次,充分或多次皂洗也可将纤维表面浮色基本除净,后整理过程中适当添加柔软剂,以降低棉织物表面的摩擦阻力,提高耐摩擦色牢度。
湿摩擦

分散染料染涤纶的湿摩擦牢度是要比干摩牢度要好了
分散染料对涤纶的染色在一定条件下是一
个动态平衡过程,已染色物在一定的条件下其已经上染的染料会迁移到织物的表面来,如高温条件的后定型,特别是升华牢度差的蒽醌结构的分散染料更易(升华)迁移跑到织物表面来,并沾污机器;此外有些后整理的助剂,也会使已染色物中的染料部分溶解析出到织物的表面来,从而导致织物的干摩擦牢度下降程度大于湿摩擦牢度的结果。这和活性等其它染料对织物的摩擦牢度下降的原理是不同的。
不能主要依赖湿摩擦牢度提升剂,还要从选择染料与纤维键合的牢固程度,以及在后续的水洗、皂洗,最后不行才能使用湿摩擦牢度提升剂。现在,要选用阳离子型的,但是要控制布面和溶液的PH值,否则就会出现问题。厂家的话,可以选择广州庄杰化工的R24
1是从染料选择上要选用牢度好的染料,符合顾客要求,2是染色前处理要充分。3是我再说一下,在染色工艺上需要注意,两咱纤维的相互沾色的问题,在染色中要加入防沾色剂,这样可以减少沾色,便于后处理浮色的去除。4是后处理要充分,皂洗,还原清洗,热水洗要多次,在上油前要保证掉色达标,再上油固色,加牢度增进剂等,提高摩擦牢度。这里面的几个因素中,后三个因素可以在生产中好控制,关键是染料本身的问题,对湿摩擦牢度影响很大。所以选用合适的染料至关重要。谢谢!
本科有@:金陵科技学院 江苏技术师范学院 淮海工学院 徐州工程学院 淮阴工学院 三江学院
我最近刚好碰到并解决此问题,我采用科莱恩公司的 Appretan 96101 15g/l 浸轧 130度烘干2min, 干磨牢度明显提高!
专科有@:南京铁道职业技术学院 江苏经贸职业技术学院 镇江市高等专科学院 常州工程技术学院 无锡职业技术学院 无锡商业技术学院 苏州职业大学 苏州农业职业技术学院 南通职业大学 南通纺织职业技术学院 南通农业职业技术学院 扬州市职业大学 扬州市环境资源职业技术学院 泰州职业技术学院 江苏畜牧兽医职业技术学院 无锡工业职业技术学院 钟山职业技术学院
如何提高活性染料染色湿摩擦牢度

热水洗清 :
洗 水 温 度 的 影 响 增强染料从纤维扩散出来 减低染料的直接性 提高染料之溶解度 因表面张力的减弱,从而有更好的 吸湿性 更快把纤维中的染料及助剂清除
水洗工艺对浮色牢度的影响
以活性黑HWN(60℃加代用碱)为例:
冷洗
酸洗
皂洗
皂洗
冷洗
水洗工艺对浮色牢度的影响
以活维的形态结构
目前世界各国广泛栽培的棉花主要有陆地棉 又称细绒棉、海岛棉、亚洲棉又称中棉或粗绒 棉、非洲棉四种。它们的长、短、粗、细相差 很大,长度约为25--45 毫米,而宽度约为17-22 微米(沿长度方向粗细不均匀)。一般说, 较长的纤维,直径也较小,质量较高。
棉纤维的形态结构
角皮层:角皮层是棉纤维极薄的最外层。关 于它的组成尚未完全确定,大概是由油蜡和果 胶物质所组成。 初生胞壁:初生胞壁厚(约0.1—0.2µm )与 纤维的宽度(约20µm )相比是较薄的一层。初 生胞壁主要是纤维素的网状组织,但也发现有 一定量的杂质,如果胶,油蜡等存在。
冷洗
酸热洗
皂洗
热洗
冷洗
两种工艺对浮色牢度的影响对比
水洗工艺对浮色牢度的影响
以活性黑HWN(低温加代用碱)为例:
水洗
过酸
皂洗
热洗
水洗
水洗工艺对浮色牢度的影响 建议染色工艺:
如果用代用碱做固色剂,采用低温加碱法。
建议后处理工艺:
冷水洗2—3道→加酸70℃热洗1道→ 80--
98℃皂洗1道→ 70℃热洗1道→冷洗1道
皂洗工艺对染色质量的影响
皂 洗 温 度 的 影 响
高
扩散
中
低
0 20 40 60 80 100
亲和力
湿摩擦处理方法
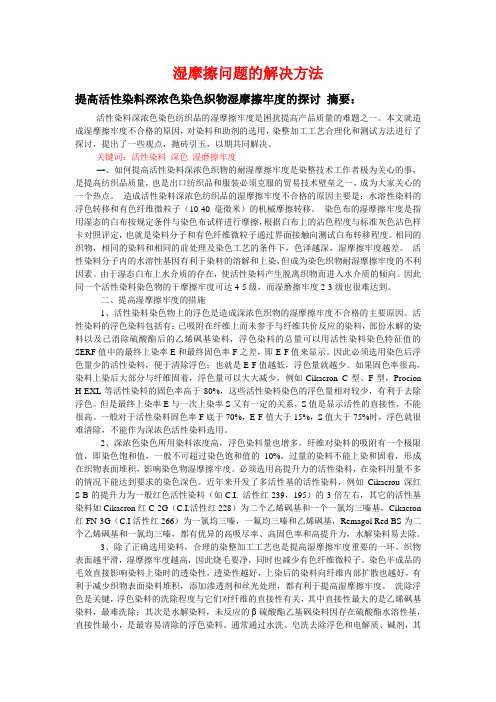
湿摩擦问题的解决方法提高活性染料深浓色染色织物湿摩擦牢度的探讨摘要:活性染料深浓色染色纺织品的湿摩擦牢度是困扰提高产品质量的难题之一。
本文就造成湿摩擦牢度不合格的原因,对染料和助剂的选用,染整加工工艺合理化和测试方法进行了探讨,提出了一些观点,抛砖引玉,以期共同解决。
关键词:活性染料深色湿磨擦牢度一、如何提高活性染料深浓色织物的耐湿摩擦牢度是染整技术工作者极为关心的事,是提高纺织品质量,也是出口纺织品和服装必须克服的贸易技术壁垒之一,成为大家关心的一个热点。
造成活性染料深浓色纺织品的湿摩擦牢度不合格的原因主要是:水溶性染料的浮色转移和有色纤维微粒子(10-40毫微米)的机械摩擦转移。
染色布的湿摩擦牢度是指用湿态的白布按规定条件与染色布试样进行摩擦,根据白布上的沾色程度与标准灰色沾色样卡对照评定,也就是染料分子和有色纤维微粒子通过界面接触向测试白布转移程度。
相同的织物,相同的染料和相同的前处理及染色工艺的条件下,色泽越深,湿摩擦牢度越差。
活性染料分子内的水溶性基因有利于染料的溶解和上染,但成为染色织物耐湿摩擦牢度的不利因素。
由于湿态白布上水介质的存在,使活性染料产生脱离织物而进入水介质的倾向。
因此同一个活性染料染色物的干摩擦牢度可达4-5级,而湿磨擦牢度2-3级也很难达到。
二、提高湿摩擦牢度的措施1、活性染料染色物上的浮色是造成深浓色织物的湿摩擦牢度不合格的主要原因。
活性染料的浮色染料包括有:已吸附在纤维上而未参予与纤维共价反应的染料,部份水解的染料以及已消除硫酸酯后的乙烯砜基染料,浮色染料的总量可以用活性染料染色特征值的SERF值中的最终上染率E和最终固色率F之差,即E-F值来显示。
因此必须选用染色后浮色量少的活性染料,便于清除浮色;也就是E-F值越低,浮色量就越少。
如果固色率很高,染料上染后大部分与纤维固着,浮色量可以大大减少,例如Cikacron C型、F型,Procion H-EXL等活性染料的固色率高于80%,这些活性染料染色的浮色量相对较少,有利于去除浮色。
提升纺织品摩擦色牢度方法

耐摩擦色牢度标准及试验方法
可看出,不同的检测标准对样布大小要求有差异。 客户在准备样布时,若被测试样是织物或地毯: 准备两组尺寸不小于50 mm× 140mm的试样,每组各两块。 (取样时,一块织物平行于经纱,另一块织物平行于纬纱。) 另外一种取样方法是试样的长度方向与织物的经纬向成一定的角度取样。
提升摩擦色牢度措施
1:选用染色后浮色量少的高提升力的活性染料, 便于清除浮色; 2:制定合理的染整加工工艺,以保证染料能充分与纤维结合,并充分渗入纤维内部,使其不会 聚集于纤维表面,染后要充分洗净浮色; 3:良好的烧毛工艺,添加渗透剂,丝光处理,都有利于湿摩擦牢度的提高; 4:加专用的平滑色交联剂可使染料与纤维结合更牢固,减少纺织品表面的摩擦力,同时使纤维 表面形成一个包覆染料的柔软薄膜,使其在摩擦时染料不易脱落,湿摩擦牢度一般可提高0.5~1.0 级。
评定结果:
1、评定分为5级,5级最好,1级最差;
2、评定时,在每个被评定的摩擦布背面放三层摩擦布;
3、去除摩擦Biblioteka 表面上多余的纤维;4、在适宜的光源下,用灰色样卡评定摩擦布的沾色级数; 评级时还需注意,美标的评级形式与国标和欧标不一样,举例如下:美标为3.5级,国标和欧标 应为3-4级。
织物的摩擦牢度取决什么因素?
织物的摩擦牢度取决于浮色的多少以及染料分子量的大小、染料与纤维的结合情况、染料渗透 的均匀度、染料在织物表面的粒子因素等。 如活性染料,染料与纤维是以共价键充分结合的,其摩擦牢度便高; 不溶性偶氮染料,当染色处理不好时,部分染料呈不溶状态,他们机械地附着在纤维表面,其 摩擦牢度低,如浮色去除不净,加上染料浓度一般偏大,使摩擦牢度降低; 特别是大多数染料与纤维的结合力在水分存在下更容易被破坏,故湿摩擦牢度比干摩擦牢度要 更低一些。
改善活性染料深色纯棉织物湿摩擦牢度的措施

万方数据
一73—
H蒜篙L一
_中曲高斯技术套^
物质与染料结合形成色淀沉积在织物表面,造成被染物手感粗糙. 增加了摩擦系数,使湿摩擦牢度降低。因此,在进行工艺设计时.必 须制定严格的用水标准,并加强检测与控制。
4.2优选染料 活性染料的品种繁多。质量相差很大,选用符合染色质量标准 的染料至关重要。 (1)选用双活性基和多活性基的染料。均三嗪类活性染料与纤维 反应形成酯键,耐酸稳定性差,乙烯砜类染料与纤维反应以醚键结 合耐碱性差。双活性基团的染料耐酸耐碱稳定性都较高。 (2)选用直接性适宜的染料。活性染料的直接性太高,如乙烯砜 基活性染料.则扩散性能差。染料易聚集在织物表面不易向纤维内 部扩散和转移,易造成浮色多难以洗净,但直接性太低,会影响固色 率。所以活性染料的直接性以中等为好。 (3)选用固色率高的染料。固色率高的染料浮色少。同色率大于 80%,染后浮色量相对较少,有利于去除浮色;固色率小于70%,最 终上染率与固色率之差大于15%的活性染料。其浮色很难清除。不 适于染中深色。 (4)选用提升力高的染料。染色工艺设计,染料用量一般不宜超 过染色饱和值的10%.过量的染料不能上染和固色.附在被染物表 面,会严重影响被染物的湿摩擦牢度。因此,染深色必须选用高吸尽 率、高固色率和高提升力的染料。 4.3优化染整工艺 选择使用染料,必须与采用合理的加工工艺相结合.而且染色工 艺的优化设计对染色的湿摩擦牢度起着决定性作用。制定合理的工 艺,以保证染料能充分与纤维结合,并充分渗入纤维内部,使其不会 聚集于纤维表面。 4.3.1加强织物的前处理 有效提高上染率是取得深色效果的手段之一.而上染率的提高 又和纤维对染料的亲和力、织物结构、表面情况等密切相关。前处理 越充分,织物润湿性越好,毛细管效应越大,越利用增加染料分子对 染物的扩散能力,提高上染率,减少染料在织物表面的聚集,减少色 淀的产生。 4.3.2合理设计染色工艺 从提高染色深度和染色牢度的角度.对染色工艺有三点基本要 求:第一,匀染透染;第二,充分固色;第三,彻底净洗。为此必须注意以 下各点: (1)根据染色半制品的毛效情况,加人适量的渗透剂和匀染剂.以 促进染料向纤维内部渗透扩散,使染料与纤维能充分接触充分键合。 (2)采用阶梯升温法染色,由低到高逐步升温.以保证染料均匀上 色。
- 1、下载文档前请自行甄别文档内容的完整性,平台不提供额外的编辑、内容补充、找答案等附加服务。
- 2、"仅部分预览"的文档,不可在线预览部分如存在完整性等问题,可反馈申请退款(可完整预览的文档不适用该条件!)。
- 3、如文档侵犯您的权益,请联系客服反馈,我们会尽快为您处理(人工客服工作时间:9:00-18:30)。
纺织产品中,影响耐湿摩色牢度的主要因素有,织物的种类、织物组织结构;纺织物前处理,如退浆、煮炼、漂白、丝光等;纺织染料的选择,以及工艺、温度、时间等的控制是否严格,还有助剂的选择和使用是否正确;纺织物的后处理等。
针对这些影响耐湿摩擦色牢度的因素,我们应注意以下几点:
根据纺织材料学的分析,一般化纤类织物比棉等天然织物的耐湿摩擦色牢度要好,稀薄织物比厚重织物要好。
所以在纺织物处理时,各道工序处理要匀透,以提高纤维的可吸性与染料的反应性或吸附固着性,使染料充分上染。
在染色过程中,要求控制严格,对助剂等须正确选择正确使用。
为提高纺织产品耐湿摩色牢度,在纺织物后处理中,可进行充分皂洗,如涤纶纤维用分散染料染色后高温定型导致染料泳移到纤维表面,引起摩擦牢度下降。
针对这种情况,加固色剂或平滑剂可在一定程度上提高耐摩擦色牢度。
选择染料时,选择具有良好提升性和匀染性的染料,良好的提升性和匀染性都有利于染料的渗透和扩散,可从一定程度上提高湿摩擦牢度。
染料应具有一定的水溶性和直接性,水溶性基团不能太多,否则会影响后面的湿摩擦牢度。
而直接性也应该选择以中等为最佳。
所选染料应具有的直接性不能太高,一般情况下应大于70%。
棉等天然织物耐湿摩擦色牢度相对较差,因此对棉坯布而言应选择纱支均匀、布面光洁的坯布。
若需要进行预处理应该选用高效前处理剂。
活性染料染色用水应尽量使用软水或去离子水,以此减少水中的钙镁等离子对染料的影响,从而提高纤维对染料的吸收性,使染料在纤维分子内固色更加稳定。
使用高效固色剂,所选固色剂应该是能在染料和纤维之间链接形成化合物,在与染料反应的时候,又可与纤维素纤维反应交联,使染料与纤维能够紧密牢固地联系在一起,加强染料与纤维的结合,防止染料从纤维上脱落或泳移到纤维表面,避免造成染色牢度下降。
使用特种助剂,如增深剂等对染色织物进行整理,可减少染料用量而获得深浓色效应,同时提高湿摩擦色牢度。
重视染后布面的pH值。
因为一般情况下深浓色棉织物染色工艺用碱量较高,然后加强水洗、皂洗与中和,织物上不能带碱,以免染料染后水解,造成湿摩擦牢度下降。
通常布面pH值控制在6.5—7.5,不能超过9或小于3。
从改进染后布面的特点出发,对织物进行整理,如生物酶抛光处理等,使得布面光洁度增加,摩擦力变小,从而提高其湿摩擦色牢度。
纤维上的浮色对耐湿摩擦色牢度极为不利,深浓色的活性染料染色织物,宜两次皂煮,但皂煮次数过多会破坏已上染的染料,从而发生断键现象,导致效果下降。
曾有试验,将染色织物用防沾污洗涤剂洗涤(用量2-3g/L,95℃处理10min),能使湿摩擦牢度达到3级。
在实际大生产时,常会发生许多状况,如蒸汽供压波动,使温度在规定时间内升不高;挡车操作失误或设备突然故障,而使预定程序偏离,发生色差后追加染化料,而使工艺变动等,从而导致色牢度差异(包括缸差)。
对于某些机械设备和染料品种、碱剂等化学药剂,在大生产中要使染色后的清洗十分彻底不太实际,所以应合理地选择。
由于活性染料染色后浮色是很难去除干净的,因此,在皂煮完后可用适当的剥色剂进行剥色处理,把浮色去除干净,使去掉浮色后的织物染料与纤维形成完整的一体,从而提高其湿摩擦色牢度。
针对活性染料与纤维形成的共价键在酸或碱的条件下可能会变得不稳定甚至断裂的情况,我们可以在其表面形成一层柔软、强韧、耐水的薄膜,以其拒水性和柔软的平滑性来改进湿摩擦牢度。
溶胶-凝胶法(Sol Gel method)是制备无机膜的一种重要方法,通过溶胶-凝胶技术在织物上形成组分不同的薄膜,可以提高织物的耐磨强度和拒水拒油性等,可以从一定程度上提高湿摩擦牢度。
但是,对其手感有一牢的影响。
有文献报道,日本一方社油脂公司开发的YKA2955和YKA2977,以4∶1组成的混合物用于活性染料染色物浸渍处理可在织物表面形成一层柔软强韧的薄膜,从而起到提高湿摩擦牢度的目的。
综上11点,均可有针对性地有效地提高纺织产品的耐湿摩擦色牢度。