颜色管理的标准化
车间颜色管理规范范例

车间颜色管理规范范例一、引言车间颜色管理规范是为了确保产品颜色的一致性和质量稳定性而制定的。
本文档旨在提供车间颜色管理的标准化流程和操作指导,以确保产品颜色的准确性和可重复性。
二、适用范围本规范适用于所有车间内进行颜色调配和管理的工作人员,包括颜色配方的制定、颜色样品的制备和颜色检测的操作。
三、术语定义1. 颜色配方:指定产品颜色的配方,包括颜色成分和比例。
2. 颜色样品:根据颜色配方制备的实际样品,用于颜色检测和比对。
3. 颜色检测:通过仪器或人工方法对颜色样品进行测量和比对,以确保其与标准颜色一致。
四、颜色配方制定1. 配方制定人员应具备一定的化学和色彩知识,能够准确理解客户的颜色要求。
2. 配方制定前,应了解产品的基础颜色和特殊要求,并与客户进行沟通和确认。
3. 配方制定应根据产品的成分和用途选择合适的颜色添加剂,并按照一定的比例进行配比。
4. 配方制定完成后,应进行内部审核和确认,并进行记录。
五、颜色样品制备1. 根据颜色配方,按照标准操作程序制备颜色样品。
2. 制备过程中应注意避免杂质的污染和颜色的偏差。
3. 制备完成后,应进行颜色检测和比对,确保样品与标准颜色一致。
4. 样品制备完成后,应进行标识和存储,方便后续的使用和追溯。
六、颜色检测1. 颜色检测应使用合适的仪器和方法,确保测量结果的准确性和可重复性。
2. 检测前,应对仪器进行校准,并确保其正常工作状态。
3. 检测时,应按照标准操作程序进行,避免操作人员的主观干扰。
4. 检测结果应与标准颜色进行比对,确保颜色的一致性。
5. 检测完成后,应进行记录和归档,方便后续的追溯和分析。
七、异常处理1. 如果颜色配方制定有误,应及时进行调整和修正,并重新制备颜色样品。
2. 如果颜色样品与标准颜色不一致,应进行原因分析,并采取相应的纠正措施。
3. 异常处理过程中,应进行记录和报告,并及时与相关部门进行沟通和协调。
八、培训和评估1. 车间颜色管理规范应纳入员工培训计划,确保所有相关人员掌握规范要求和操作流程。
材料颜色管理制度

材料颜色管理制度一、总则为规范材料颜色管理工作,提高标准化管理水平,特制定本制度。
本制度适用于所有涉及材料颜色管理的部门、单位以及相关人员。
凡发生争议、疑问、变更,由总经理办公室统一制定,执行。
二、管理范围本制度适用于公司所有生产、储存、管理、销售的材料颜色,包括但不限于原材料、成品、辅料等。
三、管理目标1、规范材料颜色的标准及认定程序。
2、加强对材料颜色管理的监督与管理。
3、促进材料颜色管理的标准化、规范化。
四、规范管理1、颜色标准及认定(1)颜色标准的制定应遵循国家相关标准和公司内部规定,并由专业人员负责认定。
(2)颜色认定程序应严谨、科学,确保认证结果的准确性和可靠性。
2、颜色监测(1)颜色监测应当进行定期检测,保证材料颜色符合相关标准。
(2)监测数据应及时记录、查验,确保实时监控。
3、颜色记录与报告(1)对颜色认定、监测的结果应当进行详细记录,包括但不限于颜色数值、监测时间、监测人员等。
(2)颜色报告应实事求是,充分体现监测结果,反映颜色情况。
4、颜色管理(1)对于不能满足颜色要求的材料,应当及时采取调整措施,确保符合标准要求。
(2)颜色管理包括但不限于发放使用颜色标准、监测仪器的定期维护与保养等。
五、管理责任1、总经理办公室负责制定和审批本制度,并进行监督与检查。
2、质量部门负责制定颜色标准,监测颜色情况,确保颜色管理的有效进行。
3、生产管理部门负责颜色的实际管理工作,包括颜色监测、报告、记录等。
4、相关人员负责严格遵守本制度的各项规定,保证材料颜色管理工作的顺利进行。
六、处罚机制对于违反本制度的相关人员,将依据公司相关处罚规定进行处罚。
严重违规者将依据公司相关规定给予相应的惩罚。
七、附则本制度经总经理办公室批准后执行,同时,对于本制度的解释权属于总经理办公室。
对于制度实施过程中出现的问题,可以随时向总经理办公室进行反映,总经理办公室将及时进行处理,并做好相应的改进工作。
在制度的制定过程中,我们废寝忘食,务求把制度系统化、科学化、可操作性高,我们也真诚的希望公司的每个员工都能严格遵守相关制度,按照制度的要求进行管理工作,为公司的发展添砖加瓦。
工业颜色标准
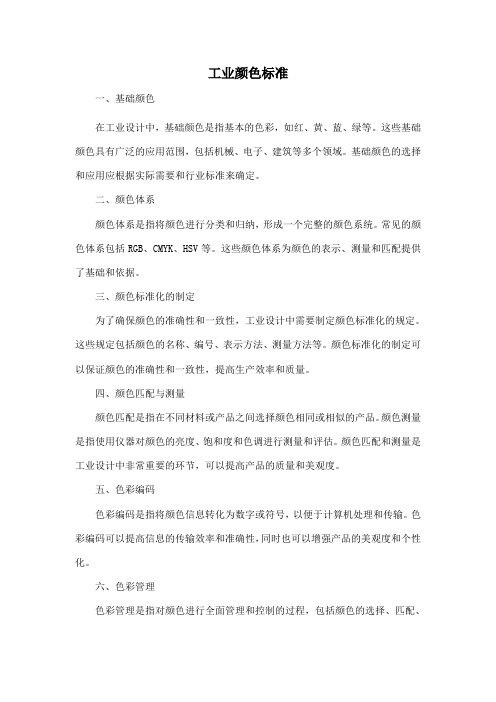
工业颜色标准一、基础颜色在工业设计中,基础颜色是指基本的色彩,如红、黄、蓝、绿等。
这些基础颜色具有广泛的应用范围,包括机械、电子、建筑等多个领域。
基础颜色的选择和应用应根据实际需要和行业标准来确定。
二、颜色体系颜色体系是指将颜色进行分类和归纳,形成一个完整的颜色系统。
常见的颜色体系包括RGB、CMYK、HSV等。
这些颜色体系为颜色的表示、测量和匹配提供了基础和依据。
三、颜色标准化的制定为了确保颜色的准确性和一致性,工业设计中需要制定颜色标准化的规定。
这些规定包括颜色的名称、编号、表示方法、测量方法等。
颜色标准化的制定可以保证颜色的准确性和一致性,提高生产效率和质量。
四、颜色匹配与测量颜色匹配是指在不同材料或产品之间选择颜色相同或相似的产品。
颜色测量是指使用仪器对颜色的亮度、饱和度和色调进行测量和评估。
颜色匹配和测量是工业设计中非常重要的环节,可以提高产品的质量和美观度。
五、色彩编码色彩编码是指将颜色信息转化为数字或符号,以便于计算机处理和传输。
色彩编码可以提高信息的传输效率和准确性,同时也可以增强产品的美观度和个性化。
六、色彩管理色彩管理是指对颜色进行全面管理和控制的过程,包括颜色的选择、匹配、测量、编码等方面。
色彩管理的目的是确保颜色的准确性和一致性,提高产品的质量和美观度。
七、色彩心理学在工业设计中的应用色彩心理学是指研究颜色对人类心理和行为的影响的学科。
在工业设计中,色彩心理学的应用可以帮助设计师更好地理解用户的需求和心理,从而设计出更符合用户需求的产品。
例如,不同的颜色可以引起不同的情绪和心理反应,如红色可以激发人们的热情和兴奋,蓝色可以给人带来平静和安宁的感觉。
因此,在工业设计中,应根据产品的特点和用户的需求来选择合适的颜色。
八、特殊工业环境下的颜色要求在不同的工业环境中,对颜色的要求也不尽相同。
例如,在航空航天领域中,为了确保飞行的安全和准确,需要使用特定的标志色和符号来进行标识;在化工行业中,为了确保生产过程的安全和稳定,需要使用特定的警示色和标志来进行标识。
车间颜色管理规范范例

车间颜色管理规范范例引言概述:车间颜色管理规范是生产车间中非常重要的一项工作,它直接关系到产品的质量和生产效率。
本文将介绍一套车间颜色管理规范范例,包括颜色选择、配色原则、颜色标准化、颜色维护和颜色检测等方面的内容。
一、颜色选择1.1 考虑产品特性:在选择车间颜色时,首先要考虑产品的特性。
不同的产品对颜色的要求不同,比如食品行业对颜色的要求可能更为严格,需要选择鲜艳、清晰的颜色;而电子产品可能更注重颜色的科技感,需要选择冷色调的颜色。
1.2 考虑环境因素:车间内的环境因素也会影响颜色的选择。
比如光线明亮的车间适合选择较浅的颜色,而光线较暗的车间则适合选择较亮的颜色,以提高可见度。
1.3 考虑品牌形象:车间颜色也要与品牌形象相符。
选择与品牌形象相符的颜色,能够加强品牌的识别度,并给人留下良好的印象。
二、配色原则2.1 色彩搭配:在车间中,颜色的搭配要符合一定的原则。
一般来说,可以采用相邻色、互补色、对比色等搭配方式。
相邻色搭配会给人以温和的感觉,互补色搭配会产生鲜明的对比效果,对比色搭配则能够突出重点。
2.2 色彩平衡:车间颜色的搭配要保持整体的平衡感。
不同区域的颜色应该相互协调,不要出现过于突兀或不协调的情况。
2.3 色彩适度:车间颜色的选择要适度,不宜过于鲜艳或过于暗淡。
过于鲜艳的颜色可能会刺激员工的眼睛,过于暗淡的颜色则可能会影响工作的积极性。
三、颜色标准化3.1 制定标准色板:车间颜色管理规范中应该包括制定标准色板的要求。
标准色板可以作为车间颜色的参考,使得不同车间的颜色保持一致。
3.2 规定颜色编号:为了方便管理,每种颜色都应该有一个独立的编号。
编号可以按照颜色的种类、用途等进行分类,方便查找和管理。
3.3 更新和维护:车间颜色标准应该定期进行更新和维护,以适应产品和市场的变化。
同时,对于已经使用的颜色,也要进行定期检查和修复,确保其符合标准。
四、颜色维护4.1 定期清洁:车间颜色的维护包括定期的清洁工作。
目视管理之颜色管理方法

目视管理之颜色管理方法引言在产品设计和开发过程中,颜色管理是一个至关重要的环节。
正确的颜色管理方法可以确保产品在不同平台和设备上保持一致的色彩表现,提高用户体验和产品质量。
本文将介绍几种常用的目视管理之颜色管理方法,并阐述其原理和适用场景。
什么是颜色管理颜色管理是指在不同设备上获取、生成、展示和打印色彩时保持一致的技术和管理方法。
通过颜色管理,可以确保产品在不同显示设备上呈现出一致的色彩效果,并消除因设备差异导致的色彩偏差。
目视管理之颜色管理方法色彩标准化色彩标准化是一种常见且简单的颜色管理方法。
它通过在设计和开发过程中使用标准化的颜色模型和色彩规范,确保产品在不同平台和设备上保持一致的色彩表现。
常见的色彩标准化方法包括使用标准的色彩空间(如sRGB、Adobe RGB等)、标准的色彩模型(如RGB、CMYK等)和标准的色彩规范(如Pantone色卡)。
色彩标准化方法适用于对色彩表现要求不高的应用场景,如网页设计、办公文档等。
它的优点是简单易行,不需要复杂的设备和软件支持。
然而,由于不同设备的色彩响应曲线和色彩空间差异,色彩标准化方法无法完全消除色彩偏差,只能保证相对一致性。
ICC颜色管理系统ICC(International Color Consortium)颜色管理系统是一种基于色彩配置文件(Color Profile)的颜色管理方法。
它通过使用设备特定的色彩配置文件,将色彩信息从一个设备转换为另一个设备的色彩表现,以确保色彩的一致性。
ICC颜色管理系统适用于对色彩表现要求较高的应用场景,如图像处理、印刷出版等。
它的优点是可以根据设备的色彩特性进行精确的色彩转换,有效消除色彩偏差。
然而,ICC颜色管理系统需要支持色彩管理的硬件和软件,在一些低成本设备上可能无法应用。
色彩校正色彩校正是一种通过调整显示设备的色彩设置来达到一致色彩表现的方法。
通过使用专业的色彩校正工具和仪器,对显示设备进行精确校准,可以减小不同设备之间的色彩差异,并实现一致的色彩效果。
车间颜色管理规范范例

车间颜色管理规范范例一、引言车间颜色管理规范旨在确保生产过程中颜色的准确性和一致性,以提高产品质量和客户满意度。
本文将详细介绍车间颜色管理的标准化流程和操作要求。
二、适用范围本规范适用于所有涉及颜色管理的车间,包括色母配方制备、颜色调配、颜色检测等环节。
三、定义1. 色差:样品与标准之间的颜色差异。
2. 色差公式:用于计算样品与标准之间色差的数学公式,如CIEDE2000、CIELAB等。
3. 标准色板:用于比较样品颜色的标准参照物,通常采用国际通用的PANTONE色卡。
四、色母配方制备1. 色母配方的编制应基于标准色板,并使用合适的色差公式进行计算,以确保配方的准确性和一致性。
2. 配方中使用的色母应严格按照规定的比例进行混合,避免误差的产生。
3. 配方制备过程中应注意避免色母的污染和交叉污染,使用专用工具和容器进行操作。
五、颜色调配1. 调配前,应检查所使用的色母和溶剂是否符合要求,避免使用已过期或质量不佳的材料。
2. 调配时应严格按照配方要求进行操作,避免误差的产生。
3. 调配完成后,应进行样品比对,确保调配的颜色与标准色板一致。
六、颜色检测1. 检测前,应校准和验证使用的色差仪或光谱仪,确保其准确性和稳定性。
2. 检测时应按照标准操作程序进行,避免操作人员的主观因素对结果产生影响。
3. 检测结果应与标准色板进行比对,记录并分析色差数据,及时调整和纠正不符合要求的样品。
七、记录与报告1. 所有配方、调配和检测过程应进行详细记录,包括配方编号、配方比例、调配日期、检测结果等信息。
2. 每次调配和检测的记录应归档保存,以便追溯和分析。
3. 定期生成颜色管理报告,包括配方准确率、调配一致性、检测稳定性等指标的统计和分析结果。
八、培训与评估1. 对车间操作人员进行颜色管理培训,包括色母配方制备、颜色调配和颜色检测等方面的知识和技能。
2. 定期对操作人员进行评估,确保其操作的准确性和一致性。
3. 针对评估结果进行反馈和改进,提供必要的培训和指导。
车间颜色管理规范范例
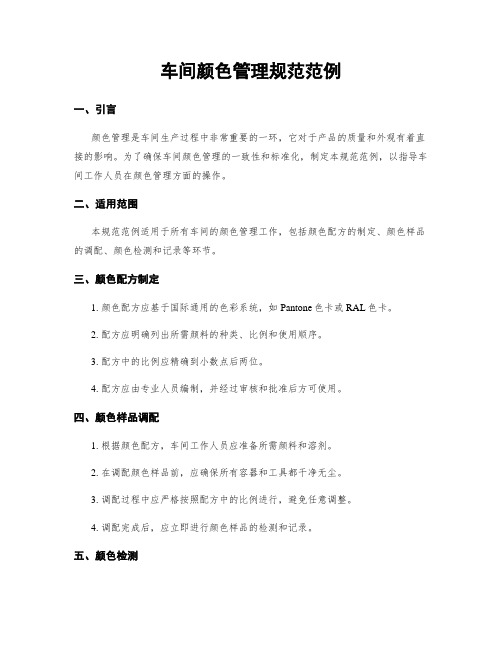
车间颜色管理规范范例一、引言颜色管理是车间生产过程中非常重要的一环,它对于产品的质量和外观有着直接的影响。
为了确保车间颜色管理的一致性和标准化,制定本规范范例,以指导车间工作人员在颜色管理方面的操作。
二、适用范围本规范范例适用于所有车间的颜色管理工作,包括颜色配方的制定、颜色样品的调配、颜色检测和记录等环节。
三、颜色配方制定1. 颜色配方应基于国际通用的色彩系统,如Pantone色卡或RAL色卡。
2. 配方应明确列出所需颜料的种类、比例和使用顺序。
3. 配方中的比例应精确到小数点后两位。
4. 配方应由专业人员编制,并经过审核和批准后方可使用。
四、颜色样品调配1. 根据颜色配方,车间工作人员应准备所需颜料和溶剂。
2. 在调配颜色样品前,应确保所有容器和工具都干净无尘。
3. 调配过程中应严格按照配方中的比例进行,避免任意调整。
4. 调配完成后,应立即进行颜色样品的检测和记录。
五、颜色检测1. 使用专业的颜色检测仪器对颜色样品进行检测。
2. 检测时应选择适当的光源和观察角度,确保结果准确可靠。
3. 检测结果应与颜色配方要求进行比对,确保符合要求的颜色样品能够通过检测。
六、颜色记录1. 每次调配和检测完成后,应将相关数据记录在颜色管理记录表中。
2. 记录表中应包括颜色配方、调配比例、检测结果等信息。
3. 记录应及时、准确地填写,确保数据的可追溯性和一致性。
七、颜色管理培训1. 车间应定期组织颜色管理培训,提高工作人员的专业知识和技能。
2. 培训内容应包括颜色配方制定、颜色样品调配、颜色检测等方面的知识。
3. 培训记录应保存并及时更新,以备查证。
八、颜色管理审查1. 定期对车间的颜色管理工作进行审查,确保规范的执行和效果的达标。
2. 审查结果应及时反馈给相关人员,并提出改进建议。
3. 审查记录应保存并定期归档,以备查阅。
九、附则1. 本规范范例的解释权归车间颜色管理部门所有。
2. 如有需要,可以根据实际情况对本规范范例进行修订和补充。
车间颜色管理规范范例
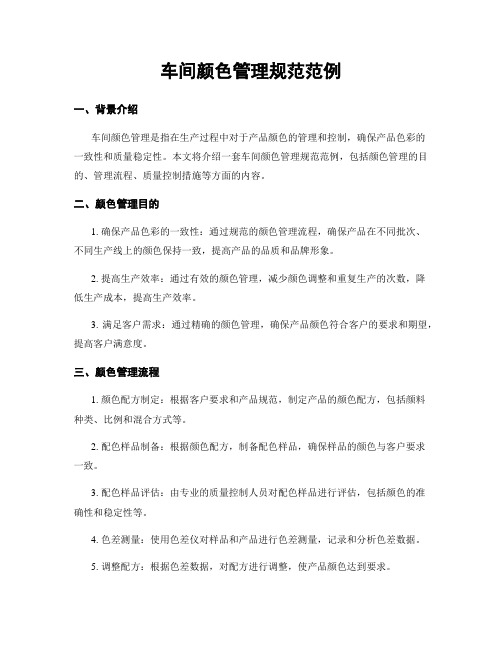
车间颜色管理规范范例一、背景介绍车间颜色管理是指在生产过程中对于产品颜色的管理和控制,确保产品色彩的一致性和质量稳定性。
本文将介绍一套车间颜色管理规范范例,包括颜色管理的目的、管理流程、质量控制措施等方面的内容。
二、颜色管理目的1. 确保产品色彩的一致性:通过规范的颜色管理流程,确保产品在不同批次、不同生产线上的颜色保持一致,提高产品的品质和品牌形象。
2. 提高生产效率:通过有效的颜色管理,减少颜色调整和重复生产的次数,降低生产成本,提高生产效率。
3. 满足客户需求:通过精确的颜色管理,确保产品颜色符合客户的要求和期望,提高客户满意度。
三、颜色管理流程1. 颜色配方制定:根据客户要求和产品规范,制定产品的颜色配方,包括颜料种类、比例和混合方式等。
2. 配色样品制备:根据颜色配方,制备配色样品,确保样品的颜色与客户要求一致。
3. 配色样品评估:由专业的质量控制人员对配色样品进行评估,包括颜色的准确性和稳定性等。
4. 色差测量:使用色差仪对样品和产品进行色差测量,记录和分析色差数据。
5. 调整配方:根据色差数据,对配方进行调整,使产品颜色达到要求。
6. 生产过程控制:在生产过程中,对颜色进行实时监控和调整,确保产品颜色的稳定性和一致性。
7. 产品检验:对生产出来的产品进行颜色检验,确保产品颜色符合要求。
8. 数据分析和改进:定期对颜色管理数据进行分析,找出问题和改进措施,不断提高颜色管理的效果和稳定性。
四、质量控制措施1. 质量培训:对车间员工进行颜色管理的培训,包括颜色配方制定、色差测量和调整配方等方面的知识和技能。
2. 设备维护:定期对色差仪和其他相关设备进行维护和校准,确保测量结果的准确性和可靠性。
3. 样品保存:对配色样品进行正确的保存和管理,避免样品受到污染和变质。
4. 数据记录和分析:对颜色管理的相关数据进行记录和分析,及时发现问题和改进措施。
5. 反馈和改进:对颜色管理的问题和改进意见进行及时反馈和处理,确保颜色管理的稳定性和持续改进。
颜色管理法
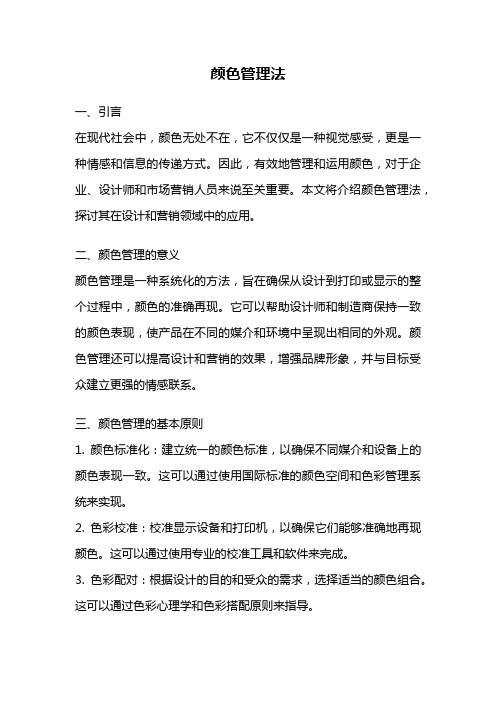
颜色管理法一、引言在现代社会中,颜色无处不在,它不仅仅是一种视觉感受,更是一种情感和信息的传递方式。
因此,有效地管理和运用颜色,对于企业、设计师和市场营销人员来说至关重要。
本文将介绍颜色管理法,探讨其在设计和营销领域中的应用。
二、颜色管理的意义颜色管理是一种系统化的方法,旨在确保从设计到打印或显示的整个过程中,颜色的准确再现。
它可以帮助设计师和制造商保持一致的颜色表现,使产品在不同的媒介和环境中呈现出相同的外观。
颜色管理还可以提高设计和营销的效果,增强品牌形象,并与目标受众建立更强的情感联系。
三、颜色管理的基本原则1. 颜色标准化:建立统一的颜色标准,以确保不同媒介和设备上的颜色表现一致。
这可以通过使用国际标准的颜色空间和色彩管理系统来实现。
2. 色彩校准:校准显示设备和打印机,以确保它们能够准确地再现颜色。
这可以通过使用专业的校准工具和软件来完成。
3. 色彩配对:根据设计的目的和受众的需求,选择适当的颜色组合。
这可以通过色彩心理学和色彩搭配原则来指导。
4. 色彩管理教育:培训设计师和印刷工人,使他们了解颜色管理的重要性,并掌握正确的颜色管理技术和工具。
5. 色彩监控:定期监控颜色的表现,及时发现和纠正问题。
这可以通过使用色彩测量仪和比对标准样品来实现。
四、颜色管理在设计中的应用1. 品牌形象设计:通过颜色的统一运用,塑造独特的品牌形象。
例如,可选择与品牌定位相符的主色调,并在不同的媒介上保持一致的表现。
2. 用户界面设计:根据用户的习惯和心理偏好,选择适合的界面颜色。
例如,对于手机应用程序,可以使用明亮和鲜艳的颜色来吸引用户的注意力。
3. 广告和宣传物料设计:通过色彩的巧妙运用,吸引目标受众的眼球。
例如,在户外广告中使用醒目的颜色,可以吸引更多的注意力。
4. 包装设计:通过颜色的选择和搭配,增强产品的吸引力和辨识度。
例如,食品包装常使用明亮的颜色,以增加食欲和诱惑力。
五、颜色管理在营销中的应用1. 广告策划:选取合适的颜色来传达产品的特点和品牌形象。
食品颜色管理制度

食品颜色管理制度一、前言食品颜色是指食品中由于色素及其他物质所形成的颜色,是食品的重要品质指标之一。
食品颜色的良好管理不仅可以提升食品的质量和口感,而且也是食品安全的一个重要方面。
为了确保食品颜色的质量和安全,制定一套科学的食品颜色管理制度显得尤为重要。
二、食品颜色管理的重要性食品颜色对于食品的质量和口感至关重要。
合适的食品颜色可以令食品更加诱人,增加消费者的食欲。
相反,若食品颜色不佳,则会减低食品的吸引力,影响销售和口碑评价。
此外,食品颜色也是食品新鲜度和成熟度的一种体现,某些食品的颜色也与其营养价值有关。
因此,对食品颜色进行管理尤为重要。
食品颜色管理不单单是对食品颜色本身的管理,还包括了对食品着色剂的管理。
着色剂通常包括天然色素和人工合成色素两种。
天然色素主要从天然植物、动物和微生物中提取,如胡萝卜素、花青素等;而人工合成色素则是利用化学合成的方式制得。
其中,人工合成色素较为廉价且色彩鲜艳,但也存在着潜在的安全隐患。
因此,对食品着色剂的选择和使用也需要加以管理。
三、食品颜色管理制度的建立为了保障食品颜色的质量和安全,制定一套完善的食品颜色管理制度显得尤为重要。
这一制度应包括以下几个方面的内容:1. 颜色管理的责任部门针对食品颜色的管理应设立专门负责的颜色管理部门或岗位,以便专人负责相关工作。
这包括对食品着色剂的选择、使用和质量控制等方面的管理工作。
2. 颜色管理的标准化制定相应的食品颜色标准,明确规定各类食品的颜色范围,并且制定相应的测试方法和仪器设备标准。
通过对食品颜色进行测试和验证,确保食品颜色符合相应的标准要求。
3. 内部质量控制建立相应的质量控制规程,确保在生产过程中对食品颜色的检测和控制。
这包括对食品原料、生产工艺、储存运输等各个环节的质量控制,保障食品颜色的稳定性和一致性。
4. 安全管理对食品着色剂的选择和使用做出相应的管理规定,避免使用有害的人工合成色素,尽量选用相对安全的天然色素,并严格遵守国家相关的法律法规,确保食品着色剂的安全。
食品行业色标管理制度

食品行业色标管理制度一、引言随着社会经济的快速发展和人们生活水平的提高,食品行业日益成为人们关注的焦点。
食品安全问题一直备受关注,而色标管理制度作为食品行业质量管理的重要组成部分,对确保食品安全具有重要意义。
本文将对食品行业色标管理制度进行深入探讨。
二、背景1.食品行业色标的概念和作用食品行业色标是指对食品在外观颜色上进行标准化的管理制度,通过对食品色彩的识别和分析,以及对食品颜色与质量关系的探究,确保食品在外观上的安全和符合消费者的需求。
食品行业色标管理制度旨在提高食品的安全性和质量,保障消费者的权益。
2.色标管理制度的重要性色标管理制度对食品行业具有重要意义。
首先,色标能够直观地反映食品的质量和新鲜程度,帮助消费者判断食品的好坏,增强消费者的信任感。
其次,色标管理制度可以规范食品行业的经营行为,提高食品从生产到销售环节中的安全管理水平,防止食品生产经营者出现色差过大、虚假标注等不良行为。
最后,色标管理制度有助于促进食品行业的发展和提升,通过统一的标准,规范市场秩序,提高食品的竞争力。
三、食品行业色标管理制度的要求1.色标标准化食品行业色标管理制度要求通过标准化的色标来指导食品生产和销售。
色标的制定需要考虑食品种类、工艺、保存期等因素,确保色标与食品的质量和安全密切相关。
同时,需要与国际标准接轨,提高食品行业在国际市场上的竞争力。
2.色标检测与监管为了确保色标的准确性和有效性,食品行业色标管理制度要求建立健全的色标检测和监管机制。
从生产、销售到消费环节,需要对食品色标进行全程监控,防止色差过大、虚假标注等不合格行为的出现。
同时,要加强对食品生产企业的监管,提高其色标管理的自律性和责任感。
3.色标宣传和教育食品行业色标管理制度要求加强对消费者的宣传和教育,提高公众对色标的认知和理解。
通过各种媒体途径,向广大消费者科普色标的作用和意义,让消费者能够更好地利用色标判断食品的质量和安全状况。
同时,要鼓励食品行业参与色标的宣传和教育,增强行业的社会责任感。
车间颜色管理规范范例

车间颜色管理规范范例一、引言车间颜色管理规范旨在确保生产车间的颜色管理达到标准化和规范化,以提高产品质量和生产效率。
本文将介绍车间颜色管理的基本原则、流程和标准,以及相关的培训和监督措施。
二、基本原则1. 一致性原则:车间内使用的颜色应与产品标准一致,确保产品质量的稳定性。
2. 规范化原则:车间内的颜色管理应符合国家和行业相关标准,遵循统一的规范和流程。
3. 可追溯性原则:车间内使用的颜色应具备可追溯性,方便问题溯源和质量追踪。
三、流程和标准1. 颜色配方管理a. 颜色配方应由专业的配色师制定,并经过审核和批准后方可使用。
b. 配方应包含颜色的具体成分、比例和混合方式,确保颜色的一致性。
c. 配方应定期进行复核和更新,以适应产品和市场的变化。
2. 颜色样板管理a. 车间应准备标准颜色样板,用于参考和比对。
b. 样板应定期进行检验和校准,确保其与产品标准一致。
c. 样板应储存于干燥、无尘、无异味的环境中,避免受到污染和损坏。
3. 颜色调配管理a. 调配颜色时,应使用准确的配方和工艺参数,确保颜色的准确性和稳定性。
b. 调配过程中应注意防止交叉污染和颜色偏差,确保调配的准确性。
c. 调配完成后,应进行颜色检验和比对,确保与产品标准一致。
4. 颜色使用管理a. 车间应按照产品要求使用正确的颜色,避免混用和错误使用。
b. 使用颜色时应注意使用顺序和操作规范,避免造成颜色污染和交叉污染。
c. 使用过程中如发现颜色异常或问题,应及时报告并采取相应的纠正措施。
四、培训和监督措施1. 培训a. 新进员工应接受颜色管理培训,了解基本原则、流程和标准。
b. 定期组织颜色管理培训,提高员工的专业技能和意识。
2. 监督a. 设立颜色管理监督岗位,负责监督车间内的颜色管理工作。
b. 定期进行颜色管理的内部审核和外部认证,确保符合相关标准和要求。
c. 建立问题反馈机制,及时处理和解决颜色管理中的问题和异常情况。
五、总结车间颜色管理规范是保证产品质量和生产效率的重要环节。
颜色管理的标准化
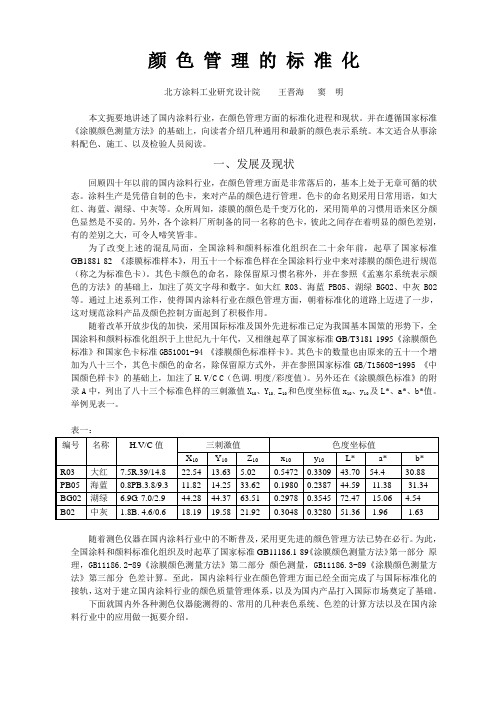
颜色管理的标准化北方涂料工业研究设计院王晋海窦明本文扼要地讲述了国内涂料行业,在颜色管理方面的标准化进程和现状。
并在遵循国家标准《涂膜颜色测量方法》的基础上,向读者介绍几种通用和最新的颜色表示系统。
本文适合从事涂料配色、施工、以及检验人员阅读。
一、发展及现状回顾四十年以前的国内涂料行业,在颜色管理方面是非常落后的,基本上处于无章可循的状态。
涂料生产是凭借自制的色卡,来对产品的颜色进行管理。
色卡的命名则采用日常用语,如大红、海蓝、湖绿、中灰等。
众所周知,漆膜的颜色是千变万化的,采用简单的习惯用语来区分颜色显然是不妥的。
另外,各个涂料厂所制备的同一名称的色卡,彼此之间存在着明显的颜色差别,有的差别之大,可令人啼笑皆非。
为了改变上述的混乱局面,全国涂料和颜料标准化组织在二十余年前,起草了国家标准GB1881-82 《漆膜标准样本》,用五十一个标准色样在全国涂料行业中来对漆膜的颜色进行规范(称之为标准色卡)。
其色卡颜色的命名,除保留原习惯名称外,并在参照《孟塞尔系统表示颜色的方法》的基础上,加注了英文字母和数字。
如大红R03、海蓝PB05、湖绿BG02、中灰B02等。
通过上述系列工作,使得国内涂料行业在颜色管理方面,朝着标准化的道路上迈进了一步,这对规范涂料产品及颜色控制方面起到了积极作用。
随着改革开放步伐的加快,采用国际标准及国外先进标准已定为我国基本国策的形势下,全国涂料和颜料标准化组织于上世纪九十年代,又相继起草了国家标准GB/T3181-1995《涂膜颜色标准》和国家色卡标准GB51001-94 《漆膜颜色标准样卡》。
其色卡的数量也由原来的五十一个增加为八十三个,其色卡颜色的命名,除保留原方式外,并在参照国家标准GB/T15608-1995 《中国颜色样卡》的基础上,加注了H.V/C C(色调.明度/彩度值)。
另外还在《涂膜颜色标准》的附录A中,列出了八十三个标准色样的三刺激值X10、Y10、Z10和色度坐标值x10、y10及L*、a*、b*值。
6S管理定置划线颜色及标准

汇报人:
确定颜色标准:根据 6S管理原则确定颜色 标准如红色代表危险、 黄色代表警告等。
制定颜色方案:根据颜 色标准制定颜色方案如 红色用于危险区域、黄 色用于警告区域等。
实施颜色划线:根据 颜色方案在定置划线 区域进行颜色划线如 红色用于危险区域、 黄色用于警告区域等。
定期检查和维护:定期 检查颜色划线是否清晰、 完整如有损坏及时进行 维护和更新。
颜色选择:根据不同区域和 功能选择合适的颜色
执行标准:制定执行标准确 保划线的准确性和一致性
检查与反馈:定期检查划线 的执行情况及时反馈和改进
制定标准:明确规定定置划线的 颜色和标准执行情况
添加标题
添加标题
添加标题
添加标题
培训员工:对员工进行定置划线 颜色和标准的培训
确定划线区域:根 据生产需要和现场 情况确定划线的区 域和位置。
划线设计:根据生 产流程和设备布局 设计划线的样式和 颜色。
划线实施:按照设 计要求使用划线工 具进行划线。
检查验收:划线完 成后进行现场检查 和验收确保划线符 合设计要求。
维护管理:定期对 划线进行维护和管 理确保划线的准确 性和清晰度。
保障安全生产:通过6S管理消除安全隐患保障安全生产降低事故发生率。
提高产品质量:通过6S管理提高产品质量降低不良品率提高客户满意度。
整理:区分必要和不必要 的物品将不必要的物品清 理掉
整顿:将必要的物品进行 分类、定位、标识方便查 找和使用
清扫:保持工作场所的清 洁防止灰尘、污垢等影响 产品质量
清洁:保持工作场所的整 洁防止灰尘、污垢等影响 产品质量
常见管理制度颜色

常见管理制度颜色1. 引言本规章制度旨在规范企业职能部门的管理,以保证工作效率和品质。
在企业的日常管理中,颜色是一种紧要的辅佑襄助工具,可以帮忙员工更好地进行沟通和协作。
本文将认真介绍常见管理制度中使用的颜色及其含义,以及相关的管理标准和考核标准。
2. 颜色及其含义2.1 红色•含义:红色在传统文化中常被视为警示色,暗示着不安全、紧急或禁止。
在管理制度中,红色通常用于表示紧急情况、行动禁止或存在的问题。
•管理标准:在收到红色指示或标记后,员工应立刻停止当前行为或操作,并向上级报告或寻求引导。
•考核标准:员工能够正确理解并遵守红色表示的紧急情况,并能够快速行动或报告。
2.2 黄色•含义:黄色通常被视为警戒色,用于提示员工注意。
在管理制度中,黄色通常用于表示注意事项、警告或潜在风险。
•管理标准:在收到黄色指示或标记后,员工应提高警觉,注意可能存在的风险并采取相应的措施,防备或解决问题。
•考核标准:员工能够正确理解并遵守黄色表示的注意事项或警告,并采取相应的防备措施。
2.3 绿色•含义:绿色通常被视为安全和正常运行的象征,用于表示工作正常进行、任务完成或通过审核。
•管理标准:在正常工作情况下,员工应保持绿色,工作顺利进行,任务定时完成,符合相关审核标准。
•考核标准:员工能够正确理解并遵守绿色表示的工作要求,并依照标准完成工作。
2.4 蓝色•含义:蓝色通常被视为信息,用于表示供应信息或需要关注的信息。
•管理标准:员工在收到蓝色指示或标记后,需要认真阅读相关信息,并依据需要采取相应的行动或做出回应。
•考核标准:员工能够正确理解并遵守蓝色表示的信息,依据需要采取相应的行动或做出回应。
3. 管理标准3.1 标准化使用颜色•全部管理制度中使用的颜色必需在内部统一,并依照相应的含义使用。
•颜色必需清楚可辨,避开使用过于相像的颜色。
•颜色使用必需符合相关企业的形象和风格要求。
3.2 清楚标识颜色含义•全部员工必需接受关于颜色含义的培训,了解各种颜色的含义和使用方式。
柔印的色彩管理和标准化

但是对柔印而言,印刷标准 化和色彩管理才刚刚起步。在柔
印行业,也有类似于胶印G7、 G M I这类的规范和认证体系,即 美国柔印协会(F T A)的F I R S T 规范体系和认证。目前该体系已 经取得一些品牌商的认可,如通 用磨坊(General Mills:哈根 达斯、湾仔码头、妙脆等),金 佰利(Kimberly Clarke: 舒洁 等)等。
点扩大状态的一致;时间是指在 不同时间印刷时都能达到一致的 效果。进行印刷机优化时,要考 虑多方面因素,如U V灯的强度、 干燥时间、放卷收卷张力、印刷 压力、套印精度等。此外还有作 业因数,如承印物的性能、油墨 性能、涂层、印版类型、胶带、网 纹辊、套筒等。F I R S T6.0认证中 推荐的印刷机优化测试图见图1。
莫春锦 郭 森
PRINTING FIELD 2019.10
柔印的色彩管理和标准化
近年来,包装印刷行业多品 种、小批量、高质量已成为一个 重要的发展趋势。为了应对这样 的市场趋势,印刷企业必须向标 准化和色彩管理转型,这样才能 既提高、稳定质量,又保持生产 效率。
在包装印刷行业,胶印工艺 的标准化和色彩管理发展得比较 早,也日趋成熟,已经发展出一 套完善的色彩管理体系,比如 F O G R A、G7、G M I等。很多胶印企 业已经采用这些体系并取得相关 认证。据不完全统计,全国有近 1 000家印刷厂已通过各类色彩管 理体系认证。
{经营管理}颜色管理的标准化
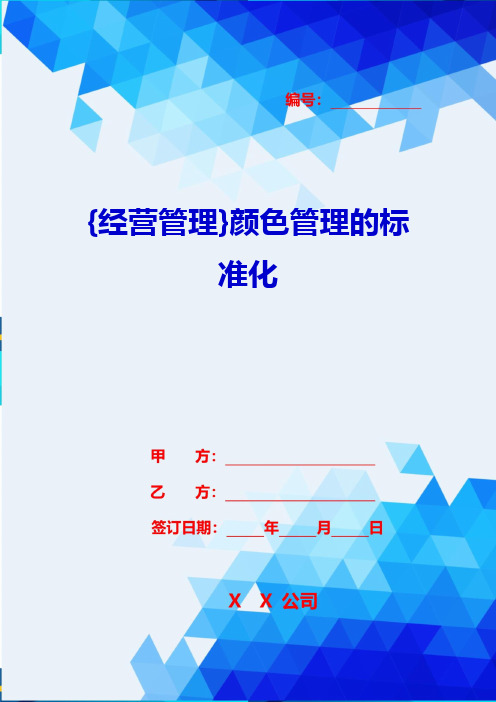
{经营管理}颜色管理的标准化颜色管理的标准化北方涂料工业研究设计院王晋海窦明本文扼要地讲述了国内涂料行业,在颜色管理方面的标准化进程和现状。
并在遵循国家标准《涂膜颜色测量方法》的基础上,向读者介绍几种通用和最新的颜色表示系统。
本文适合从事涂料配色、施工、以及检验人员阅读。
一、发展及现状回顾四十年以前的国内涂料行业,在颜色管理方面是非常落后的,基本上处于无章可循的状态。
涂料生产是凭借自制的色卡,来对产品的颜色进行管理。
色卡的命名则采用日常用语,如大红、海蓝、湖绿、中灰等。
众所周知,漆膜的颜色是千变万化的,采用简单的习惯用语来区分颜色显然是不妥的。
另外,各个涂料厂所制备的同一名称的色卡,彼此之间存在着明显的颜色差别,有的差别之大,可令人啼笑皆非。
为了改变上述的混乱局面,全国涂料和颜料标准化组织在二十余年前,起草了国家标准GB1881-82 《漆膜标准样本》,用五十一个标准色样在全国涂料行业中来对漆膜的颜色进行规范(称之为标准色卡)。
其色卡颜色的命名,除保留原习惯名称外,并在参照《孟塞尔系统表示颜色的方法》的基础上,加注了英文字母和数字。
如大红R03、海蓝PB05、湖绿BG02、中灰B02等。
通过上述系列工作,使得国内涂料行业在颜色管理方面,朝着标准化的道路上迈进了一步,这对规范涂料产品及颜色控制方面起到了积极作用。
随着改革开放步伐的加快,采用国际标准及国外先进标准已定为我国基本国策的形势下,全国涂料和颜料标准化组织于上世纪九十年代,又相继起草了国家标准GB/T3181-1995《涂膜颜色标准》和国家色卡标准GB51001-94 《漆膜颜色标准样卡》。
其色卡的数量也由原来的五十一个增加为八十三个,其色卡颜色的命名,除保留原方式外,并在参照国家标准GB/T15608-1995 《中国颜色样卡》的基础上,加注了H.V/C C(色调.明度/彩度值)。
另外还在《涂膜颜色标准》的附录A中,列出了八十三个标准色样的三刺激值X10、Y10、Z10和色度坐标值x10、y10及L*、a*、b*值。
常见管理制度:颜色管理

常见管理制度:颜色管理一、管理背景颜色是企业形象建设中不行或缺的一环,恰当的颜色运用和管理可以加强企业的品牌认知度和信任度。
为了规范和统一企业的颜色管理,特订立本制度。
二、适用范围本制度适用于公司全部内外部使用的颜色,包含但不限于标志、品牌文化宣传资料、产品包装等。
三、管理标准1.颜色标准–确定重要企业标志颜色和辅佑襄助颜色的名称、色号和使用范围。
–使用标准的Pantone色卡或CMYK/RGB数值,确保颜色的全都性和可再现性。
–确定颜色使用的背景和对比度要求,确保信息传递的清楚性和可读性。
2.颜色搭配–在设计企业文化宣传资料时,遵从统一的颜色搭配原则,确保视觉效果的统一和协调。
–通过颜色的明度、饱和度等参数的调整,实现不同场景下的最佳呈现效果。
–禁止随便更改、使用与标准不符的颜色。
3.颜色命名–为标志颜色和辅佑襄助颜色统一命名,以避开混淆和歧义。
–命名时要简洁明白,以便其他人易于理解和识别。
4.版面规范–为确保信息传递的清楚性和可读性,统一指定文字、图表、背景和边框的颜色使用规范。
–确保互动界面和产品包装的整体风格和颜色的协调性,彰显企业品牌形象。
四、考核标准1.严格遵从颜色管理制度,依照规定的颜色标准和搭配原则进行设计和制作。
2.遵从颜色命名规范,确保命名的准确性和便于他人理解和使用。
3.在设计企业文化宣传资料时,必需依照订立的版面规范进行操作,确保呈现效果的全都性。
4.审核人员将定期抽查和检查颜色使用情况,对不符合要求的进行矫正,并记录在案。
5.针对颜色管理制度的执行情况,定期进行绩效评估,评估内容包含但不限于符合度、标准化程度、操作规范等。
五、制度执行和维护1.颜色管理人员负责订立和更新颜色管理标准,并对相关人员进行培训,确保其理解和遵守制度。
2.颜色管理人员将订立一份颜色管理手册,认真介绍标准和操作流程,并通过内部平台进行发布和传阅。
3.工作人员在设计、制作和使用颜色时,应依照颜色管理手册的规定进行操作。
印刷色彩管理方法
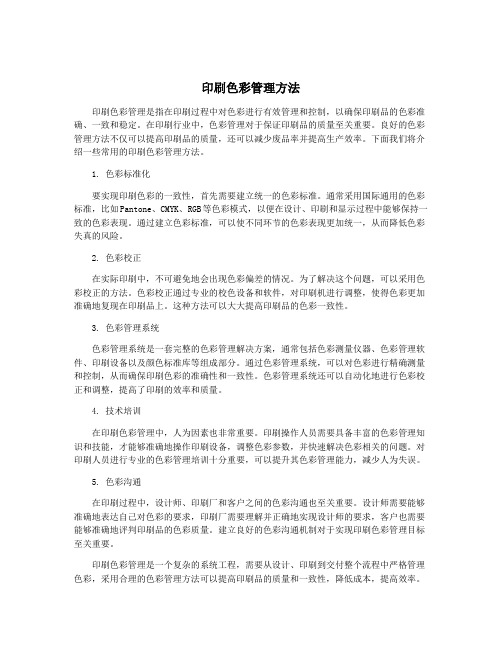
印刷色彩管理方法印刷色彩管理是指在印刷过程中对色彩进行有效管理和控制,以确保印刷品的色彩准确、一致和稳定。
在印刷行业中,色彩管理对于保证印刷品的质量至关重要。
良好的色彩管理方法不仅可以提高印刷品的质量,还可以减少废品率并提高生产效率。
下面我们将介绍一些常用的印刷色彩管理方法。
1. 色彩标准化要实现印刷色彩的一致性,首先需要建立统一的色彩标准。
通常采用国际通用的色彩标准,比如Pantone、CMYK、RGB等色彩模式,以便在设计、印刷和显示过程中能够保持一致的色彩表现。
通过建立色彩标准,可以使不同环节的色彩表现更加统一,从而降低色彩失真的风险。
2. 色彩校正在实际印刷中,不可避免地会出现色彩偏差的情况。
为了解决这个问题,可以采用色彩校正的方法。
色彩校正通过专业的校色设备和软件,对印刷机进行调整,使得色彩更加准确地复现在印刷品上。
这种方法可以大大提高印刷品的色彩一致性。
3. 色彩管理系统色彩管理系统是一套完整的色彩管理解决方案,通常包括色彩测量仪器、色彩管理软件、印刷设备以及颜色标准库等组成部分。
通过色彩管理系统,可以对色彩进行精确测量和控制,从而确保印刷色彩的准确性和一致性。
色彩管理系统还可以自动化地进行色彩校正和调整,提高了印刷的效率和质量。
4. 技术培训在印刷色彩管理中,人为因素也非常重要。
印刷操作人员需要具备丰富的色彩管理知识和技能,才能够准确地操作印刷设备,调整色彩参数,并快速解决色彩相关的问题。
对印刷人员进行专业的色彩管理培训十分重要,可以提升其色彩管理能力,减少人为失误。
5. 色彩沟通在印刷过程中,设计师、印刷厂和客户之间的色彩沟通也至关重要。
设计师需要能够准确地表达自己对色彩的要求,印刷厂需要理解并正确地实现设计师的要求,客户也需要能够准确地评判印刷品的色彩质量。
建立良好的色彩沟通机制对于实现印刷色彩管理目标至关重要。
印刷色彩管理是一个复杂的系统工程,需要从设计、印刷到交付整个流程中严格管理色彩,采用合理的色彩管理方法可以提高印刷品的质量和一致性,降低成本,提高效率。
车间颜色管理规范范例
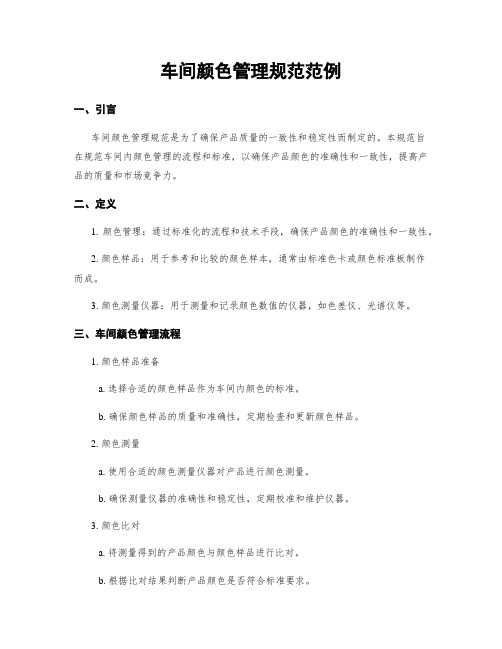
车间颜色管理规范范例一、引言车间颜色管理规范是为了确保产品质量的一致性和稳定性而制定的。
本规范旨在规范车间内颜色管理的流程和标准,以确保产品颜色的准确性和一致性,提高产品的质量和市场竞争力。
二、定义1. 颜色管理:通过标准化的流程和技术手段,确保产品颜色的准确性和一致性。
2. 颜色样品:用于参考和比较的颜色样本,通常由标准色卡或颜色标准板制作而成。
3. 颜色测量仪器:用于测量和记录颜色数值的仪器,如色差仪、光谱仪等。
三、车间颜色管理流程1. 颜色样品准备a. 选择合适的颜色样品作为车间内颜色的标准。
b. 确保颜色样品的质量和准确性,定期检查和更新颜色样品。
2. 颜色测量a. 使用合适的颜色测量仪器对产品进行颜色测量。
b. 确保测量仪器的准确性和稳定性,定期校准和维护仪器。
3. 颜色比对a. 将测量得到的产品颜色与颜色样品进行比对。
b. 根据比对结果判断产品颜色是否符合标准要求。
4. 调整和纠正a. 如果产品颜色与颜色样品不一致,进行适当的调整和纠正。
b. 调整和纠正过程中,记录和跟踪每一步的操作和结果。
5. 颜色管理记录a. 记录每次颜色测量和比对的结果。
b. 记录调整和纠正的过程和结果。
四、车间颜色管理标准1. 颜色一致性要求a. 产品颜色的一致性要求在一定的光源下和观察角度下保持稳定。
b. 产品颜色的一致性要求在不同的批次和生产线上保持一致。
2. 颜色容差要求a. 设置合理的颜色容差范围,允许产品颜色在一定范围内存在差异。
b. 颜色容差范围应根据产品的特性和市场需求进行确定。
3. 颜色管理人员要求a. 车间应指定专人负责颜色管理工作,确保颜色管理的专业性和连续性。
b. 颜色管理人员应具备相关的专业知识和技能,定期进行培训和考核。
五、颜色管理的效果评估1. 定期评估颜色管理的效果,检查产品颜色是否符合标准要求。
2. 根据评估结果,及时调整和改进颜色管理的流程和标准。
六、总结车间颜色管理规范是确保产品颜色准确性和一致性的重要手段,通过规范的流程和标准,可以提高产品的质量和市场竞争力。
- 1、下载文档前请自行甄别文档内容的完整性,平台不提供额外的编辑、内容补充、找答案等附加服务。
- 2、"仅部分预览"的文档,不可在线预览部分如存在完整性等问题,可反馈申请退款(可完整预览的文档不适用该条件!)。
- 3、如文档侵犯您的权益,请联系客服反馈,我们会尽快为您处理(人工客服工作时间:9:00-18:30)。
颜色管理的标准化北方涂料工业研究设计院王晋海窦明本文扼要地讲述了国内涂料行业,在颜色管理方面的标准化进程和现状。
并在遵循国家标准《涂膜颜色测量方法》的基础上,向读者介绍几种通用和最新的颜色表示系统。
本文适合从事涂料配色、施工、以及检验人员阅读。
一、发展及现状回顾四十年以前的国内涂料行业,在颜色管理方面是非常落后的,基本上处于无章可循的状态。
涂料生产是凭借自制的色卡,来对产品的颜色进行管理。
色卡的命名则采用日常用语,如大红、海蓝、湖绿、中灰等。
众所周知,漆膜的颜色是千变万化的,采用简单的习惯用语来区分颜色显然是不妥的。
另外,各个涂料厂所制备的同一名称的色卡,彼此之间存在着明显的颜色差别,有的差别之大,可令人啼笑皆非。
为了改变上述的混乱局面,全国涂料和颜料标准化组织在二十余年前,起草了国家标准GB1881-82 《漆膜标准样本》,用五十一个标准色样在全国涂料行业中来对漆膜的颜色进行规范(称之为标准色卡)。
其色卡颜色的命名,除保留原习惯名称外,并在参照《孟塞尔系统表示颜色的方法》的基础上,加注了英文字母和数字。
如大红R03、海蓝PB05、湖绿BG02、中灰B02等。
通过上述系列工作,使得国内涂料行业在颜色管理方面,朝着标准化的道路上迈进了一步,这对规范涂料产品及颜色控制方面起到了积极作用。
随着改革开放步伐的加快,采用国际标准及国外先进标准已定为我国基本国策的形势下,全国涂料和颜料标准化组织于上世纪九十年代,又相继起草了国家标准GB/T3181-1995《涂膜颜色标准》和国家色卡标准GB51001-94 《漆膜颜色标准样卡》。
其色卡的数量也由原来的五十一个增加为八十三个,其色卡颜色的命名,除保留原方式外,并在参照国家标准GB/T15608-1995 《中国颜色样卡》的基础上,加注了H.V/C C(色调.明度/彩度值)。
另外还在《涂膜颜色标准》的附录A中,列出了八十三个标准色样的三刺激值X10、Y10、Z10和色度坐标值x10、y10及L*、a*、b*值。
举例见表一。
表一:随着测色仪器在国内涂料行业中的不断普及,采用更先进的颜色管理方法已势在必行。
为此,全国涂料和颜料标准化组织及时起草了国家标准GB11186.1-89《涂膜颜色测量方法》第一部分原理,GB11186.2-89《涂膜颜色测量方法》第二部分颜色测量,GB11186.3-89《涂膜颜色测量方法》第三部分色差计算。
至此,国内涂料行业在颜色管理方面已经全面完成了与国际标准化的接轨,这对于建立国内涂料行业的颜色质量管理体系,以及为国内产品打入国际市场奠定了基础。
下面就国内外各种测色仪器能测得的、常用的几种表色系统、色差的计算方法以及在国内涂料行业中的应用做一扼要介绍。
二、H.V/C 表色系统为了便于了解颜色管理方面的基理,首先介绍色立体图(见图一)图一、颜色立体示意图色立体是利用三维坐标把颜色知觉的三个属性(色调、明度及彩度)完整的表示出来。
图中的每个具体空间位置均代表着一个特定颜色。
就颜色而言,它可分为非彩色和彩色两大类:非彩色是指白、黑及其中间不同程度的灰。
而彩色是指非色彩之外的一切颜色。
1、色调:又称色相,用H标号。
他表示红、橙、黄、绿、青、蓝、紫或相邻中间色的颜色特征。
在色立体图中用色调环来表述。
(见图二)图二、颜色色调环色调环中的红(R)、黄(Y)、绿(G)、蓝(B)、紫(P)五色为主色。
黄红(YR)、绿黄(GY)、蓝绿(BG)、紫蓝(PB)、红紫(RP)称为中间色。
色调按需要还可以进一步细分,本文不再详述。
在国家标准GB6749-86 《涂膜颜色表示方法》中,将漆膜颜色的有彩色按其色调分成十类,另加无彩色共十一类。
见表二表二:2、明度:与亮度成正比,用V标号。
他表示明暗程度,以理想白为10,理想黑为0。
0-10之间按视觉的等距离划分,从0至10分为11级。
(见图三左标尺)10/9/8/ C明7/度6/ /10V 5/4/3/2/1/0/黑图三、明度标尺与彩度标尺3、彩度:又称饱和度,用C标号。
它表示颜色的浓淡程度。
在相邻彩度之间按视觉的等距离划分为0-20。
(见图三右侧标尺)通过对颜色三个基本属性的认识,可以看到任何颜色都可以用H.V/C(彩色)或NV(非彩色)来加以表示。
以国家色卡标准GSB51001-94《漆膜颜色标准样卡》的八十三个样卡中的四个为例;见表四所示根据H.V/C值,可以对颜色进行分析、比较。
从而达到指导配色,控制产品的目的。
三、Y10x10y10 表色系统测色仪器所测得的颜色三刺激值是各种表色系统的计算基础。
针对国内涂料行业,我们首先介绍Y10 x10 y101964补充标准色度系统。
其条件是以观察视角为10 o ,在D65标准照明体下,被测物体的反射色。
Y10为亮度系数,x10 y是CIE 1964色度坐标图。
(见图四)图四、CIE 1964 补充色度系统色度图色度坐标由下式确定:x10 = X10/(X10+Y10+Z10) , y10 = Y10/(X10+Y10+Z10)图四中扇形曲线为光谱颜色轨迹,直线部分为绛紫轨迹。
所有颜色均处于由这两条轨迹所围成的马蹄形面积之中。
图中D65为CIE所推荐的标准照明体D65在色度图中的色度坐标(x10 = 0.3138、y10 = 0.3310)O点。
以标准中的湖绿色BG02(Y10=44.37,x10=0.2978,y10=0.3545)为例来说明图四的使用方法:1、主波长:在图中标出湖绿色的色度坐标点M。
连接OM作直线延长交于光谱轨迹与F。
F点位于498毫微米处,此波长即为湖绿色的主波长,它表示湖绿色在D65照明体下所呈现的颜色色调。
色调与波长之间的关系见表五:湖绿色的色调处于绿色范围内,并且主波长接近正绿色。
2、饱和度:在图四中,求OM与OF线段长度之比,即为湖绿色在此主波长下的饱和度。
OM = 4,OF = 50则OM/OF= 0.08。
饱和度表示颜色的浓淡程度,M点越靠近光谱轨迹,其饱和度越高,当M点落在光谱轨迹上时,其值为1。
(即为100%)当M点越靠近0点时颜色的饱和度越低。
湖绿色色样的饱和度是很低的,表示它的色感较弱。
3、亮度:Y10为亮度因数,其值越高越明亮。
湖绿色色样的Y10值为44.37,说明颜色比较明亮。
附:补色主波长:以标准中的玫瑰红色RP03 (Y10 = 13.02 x10 = 0.4151 y10 = 0.2701)为例,其色坐标点M’落在由光谱轨迹两端点与照明体D65的色度坐标点O所围成的三角区域内(见图四),连接OM’作直线延长交于绛紫轨迹与F”,可见它没有主波长,需用补色主波长来加以表示。
反向做OM’直线延长交于光谱轨迹与F’,F’点即为玫瑰红色的补色主波长,位于493毫微米处。
为了区别于主波长,规定在补色主波长前加以负号来表示,其饱和度用“OM’/OF””表示。
采用主波长(或补色主波长),饱和度,亮度因数来对颜色进行评定,比只用X10,Y10,Z10三刺激值来表示颜色其效果更为直观,也有利于对颜色的分析,因此Y10,x10,y10表色系统一直被广泛地加以应用。
四、L*、a*、b*表色系统在使用上述x10 y10色度图时,图中两个色度坐标点之间的相等距离,并不能代表相等的人眼感觉之差,既存在着不均匀性。
为此,CIE 1976年推荐了L*、a*、b*均匀色空间,简称CIELAB 色空间。
目前L*、a*、b*表色系统已得到广大使用者的认可。
国内涂料行业在国家标准《漆膜颜色测量》中也规定采用本系统。
本系统最大优点在于它的均匀性,更为接近人眼的感觉之差,所以有利于色差比较。
下面介绍L*、a*、b*色空间及色差⊿Eab*的计算:图五、L*、a*、b* 色空间图中的中央轴L*表示明度,与L*轴垂直的色空间予以刨切的截面用a*、b*标度。
a*、b*是以通过L*轴的中心来划分(+)侧和(-)侧。
利用测色仪器可以直接测得L*、a*、b*值。
由图五中可以看到L*值越大,其明度越高。
a*在(+)侧数值越大,则表示红色程度越高,在(-)测,则表示绿色程度,b*在(+)测数值越大,则表示黄色程度越高,在(-)侧,则表示蓝色程度越高。
在进行颜色比较时,其色差值按下式计算:⊿L* = L*T - L*R , ⊿a* = a*T - a*R , ⊿b* = b*T - b*R式中:L*T ,a*T ,b*T 为试样测量值L*R ,a*R ,b*R 为标准样测量值总色差值见下式:⊿Eab* = 〔(⊿L*)2 +(⊿a*)2+(⊿b*)2〕1/2色差对颜色管理来讲是非常重要的,色差值是指试样的颜色与标准样的颜色,在色度坐标中的几何距离之差,并用数据来加以表示。
其单位为NBS。
该数值与人眼感觉之间的相应关系如表六:至于色差规定为多少较为合适,需根据具体情况而定。
国内涂料行业控制产品的色差范围;除要考虑不同的产品的需要外,也可根据供需双方协商来加以确定。
五,L*,C*,H o表色系统L*,C*,H o表色系统与L*,a*,b*表色系统在色空间及色差Eab*计算方面都是统一的。
但在本系统中采用了明度L*(以直线表示),彩度C*和色调角H o(用极坐标表示)来表示颜色的色坐标。
它的定义方程见下式:L* = L*C* =〔(a*)2+(b*)2〕1/2H o = arctg (b*/a*)在进行颜色比较时总色差计算仍用下式计算:⊿E ab* = 〔(⊿L*)2 +(⊿a*)2+(⊿b*)2〕1/2明度差:⊿L* = L*T - L*R彩度差:⊿C ab* = C ab*T - C ab*R式中:L*T、C ab*T为试样测量值L*R、C ab*R为标样测量值当选用本表色系统计算色调差时,一般是不用色调角H o的,而用色调H*,其色调差⊿H*由下式确定:⊿H ab* = 〔(⊿E ab*)2– (⊿L*)2– (⊿C ab*)2〕1/2这样的规定是明度差,彩度差和色调差的平方和等于总色差的平方。
为此国内涂料行业在执行国家标准《涂膜颜色测量》—色差计算的试验报告中,明确规定要以以下形式表示试验结果:—色差⊿E ab*。
—有必要时也表示明度差⊿L*、彩度差⊿C ab*及色调差⊿H ab*。
六、Hunter L ,a ,b 表色系统亨特(Hunter)L,a,b表色系统是1966年被推荐的,由于在色差的表述上更为符合人的感觉之差,所以被广泛的予以采用,尤以美、日等几十个国家更为如此。
现介绍图六。
图六、Hunter (a , b) 管理图右侧标尺表示明度L,左图表示与L轴相垂直的颜色立体刨切的截面图。
L,a,b值由下式确定:L = 10 (Y10)1/2a = 17.2 (1.0547X10-Y10) / (Y10)1/2b = 6.75 (Y10-0.9318Z10) / (Y10)1/2色样的L值越大,其明度越高。