液膜分离的原理及应用
液膜分离的原理和方法

液膜分离的原理和方法液膜分离是一种利用液体膜将混合物分离的技术。
它的原理是在两个不相容的相之间形成一层液体膜,通过液膜的选择性渗透作用,将混合物中所需分离的成分从其他成分中分离出来。
液膜分离广泛应用于物质提纯、废水处理、溶剂回收等领域。
液膜分离的方法有多种,其中较常见的包括溶剂萃取、膜萃取和悬浮液膜分离。
首先是溶剂萃取法。
在液膜分离中,通常需要一种适用的溶剂作为液膜的载体。
溶剂萃取法主要通过液膜中溶剂与混合物中目标成分之间的物理或化学相互作用,达到选择性地分离目标成分的目的。
溶剂一般选择一种具有较高的选择性和相容性的有机物,例如水和石油醚、正庚烷等。
液膜中的溶剂可以通过高速旋转等方式形成一层薄膜,将目标成分从混合物中迁移至另一相中。
其次是膜萃取法。
膜萃取是利用特殊的膜材料,通过透过膜和保留膜两种作用,实现目标成分从混合物中分离的方法。
膜萃取既可以是液态膜,也可以是固态膜。
液态膜的膜材料可以是胶体粒子、微胶囊、液滴等,它们在溶剂中形成一个连续的相,从而实现液膜分离。
固态膜则是指通过多个过滤层、溶剂渗透层等构成的一种薄膜结构,具有选择性地渗透目标成分,实现分离。
膜萃取法具有操作简单、成本较低、效率高等优点,因此在化工、食品、制药等行业得到了广泛应用。
最后是悬浮液膜分离法。
悬浮液膜分离法是一种通过在两个不相容的相之间形成一层悬浮液膜,利用离心离子、电渗现象或受力作用引起的悬浮液层的流动,实现目标组分的分离。
该方法适用于固液、液液、气液等分离过程。
悬浮液膜分离法不需要添加溶剂,因此避免了溶剂萃取法中溶剂的回收问题,更符合环保要求。
总结起来,液膜分离是一种通过液体膜实现混合物分离的技术。
根据液体膜的不同形式,液膜分离的方法主要有溶剂萃取、膜萃取和悬浮液膜分离。
这些方法在应用中各有优缺点,但都具有高效、操作简单、分离效果好等特点,因此在化工、环保等领域得到了广泛应用。
膜分离技术的原理及优点
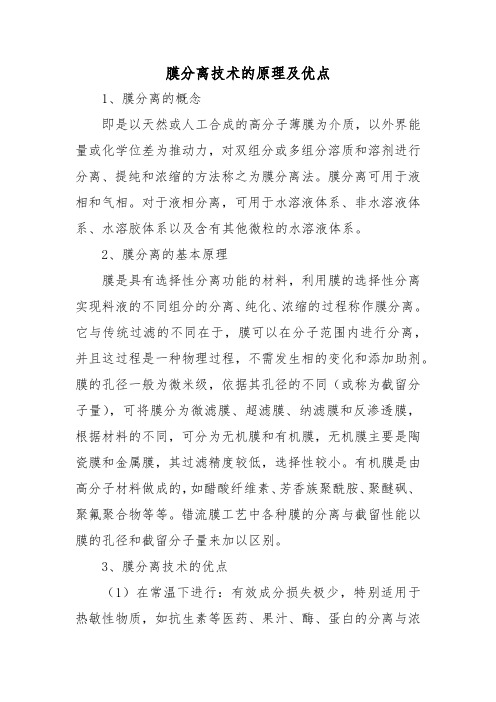
膜分离技术的原理及优点1、膜分离的概念即是以天然或人工合成的高分子薄膜为介质,以外界能量或化学位差为推动力,对双组分或多组分溶质和溶剂进行分离、提纯和浓缩的方法称之为膜分离法。
膜分离可用于液相和气相。
对于液相分离,可用于水溶液体系、非水溶液体系、水溶胶体系以及含有其他微粒的水溶液体系。
2、膜分离的基本原理膜是具有选择性分离功能的材料,利用膜的选择性分离实现料液的不同组分的分离、纯化、浓缩的过程称作膜分离。
它与传统过滤的不同在于,膜可以在分子范围内进行分离,并且这过程是一种物理过程,不需发生相的变化和添加助剂。
膜的孔径一般为微米级,依据其孔径的不同(或称为截留分子量),可将膜分为微滤膜、超滤膜、纳滤膜和反渗透膜,根据材料的不同,可分为无机膜和有机膜,无机膜主要是陶瓷膜和金属膜,其过滤精度较低,选择性较小。
有机膜是由高分子材料做成的,如醋酸纤维素、芳香族聚酰胺、聚醚砜、聚氟聚合物等等。
错流膜工艺中各种膜的分离与截留性能以膜的孔径和截留分子量来加以区别。
3、膜分离技术的优点(1)在常温下进行:有效成分损失极少,特别适用于热敏性物质,如抗生素等医药、果汁、酶、蛋白的分离与浓缩;(2)无相态变化:保持原有的风味,能耗极低,其费用约为蒸发浓缩或冷冻浓缩的31—81; (3)无化学变化:典型的物理分离过程,不用化学试剂和添加剂,产品不受污染;(4)选择性好:可在分子级内进行物质分离,具有普遍滤材无法取代的卓越性能;(5)适应性强:处理规模可大可小,可以连续也可以间隙进行,工艺简单,操作方便,易于自动化;(6)能耗低:只需电能驱动,能耗极低,其费用约为蒸发浓缩闹局世或冷冻浓缩的31—81。
4、膜分离技术的缺点(1)膜技术虽然浓缩成本低,但不能将产品浓缩成干物质;(2)膜技术虽然具有选择过滤性,但是同分异构体就无法实现分离。
5、膜分离技术的应用领域膜分离技术,是指在分子水平上不同粒径分子的混合物在通过半透膜时,实现选择性分离的技术。
液膜分离技术

液膜分离技术摘要:本文简要介绍了液膜分离技术的分类、传质机理、影响液膜稳定性因素、相关应用等,并对液膜分离技术的发展前景进行了展望。
关键词:液膜分离技术;乳化液膜;支撑液膜液膜分离技术(Liquid membrane permeation ,LMP)液膜分离技术(Liquid membrane permeation ,LMP)是以液膜为分离介质、以浓差为推动力的液-液萃取与反萃过程结合为一体的分离过程。
起分离作用的液膜通常为添加了表面活性剂的溶剂相,液膜两边的被萃相和反萃相通常都是可互溶相。
它是1968年由美国埃克森公司的美籍华人黎念之博士提出的。
液膜是一层很薄的液体,它阻隔在两个可互溶但组成不同的液相之间,一个液相中的待分离组分通过液膜的选择性渗透作用传递到另一个液相中,从而使物质达到分离提纯的目的。
液膜分离技术比固体膜分离技术具有高效、快速、选择性强和节能等优越性;比液液萃取具有萃取与反萃取同时进行,分离和浓缩因数高,萃取剂用量少和溶剂流失量少等特点。
该法的研制成功,不仅促进了环境分析、石油化工、医药、卫生等各不同领域分离问题的研究,也使分离科学上升到一个新水平。
1.液膜的分类1.1 根据组成分类按组成可分为:油包水型(膜相为油质而内外相都为水相)和水包油型(膜相为水质而内外相都为油相)两种。
1.2 根据机理分类按机理可分为:膜相中含载体和不含载体两类。
(1)膜相主要由载体和溶剂组成。
载体在膜相中通过萃取反应和反萃取反应,使溶质在液膜两侧不断传递,以达到脱除的效果。
(2)膜相中不含载体,则是利用溶质在膜相中的渗透速率的差别进行物质分离。
1.3 根据液膜构成和操作方式分类按组成和操作方式分为:乳化液膜(Emulsion liquid membrane)和支撑液膜(Supposed liquid membrane)两类。
(1) 乳化液膜(ELM)乳化液膜体系是一个三相系统,其中由两相构成的乳化液分散在另一连续相溶液中,这样形成的体系称为多重乳化液。
《液膜分离技术》PPT课件

(1)水处理:
①海水,苦咸水的淡化;
②纯水,超纯水的制备;
③工业废水的处理;
(2)元素的分离,富集;
(3)金属物质的分离,回收;
(4)气体分离
精选ppt
23
(1)、烃类混合物的分离
液膜分离技术已成功用于分离苯-正 乙烷、甲烷-庚烷、庚烷-己烯等混合物系。 如在分离芳烃与烷烃混合物时,芳烃易溶于 膜,烷烃难溶于膜,因而芳烃在膜内的浓度梯 度大,渗透速率高;烷烃在膜内的浓度梯度小, 渗透速率低,于是实现了混合烃的分离。
精选ppt
3
液膜分离的特点
• 优点:
(1)分离过程中没有相变化,不需要使液体沸 腾,也不需要使气体液化.因而是一种低能耗, 低成本的分离技术
(2)分离过程一般在常温下进行,因而对于需 避免高温分离,分级,浓缩与富集的物质,如 果汁,药品等,显示出其独特的优点.
(3)分离技术应用范围广,对无机物、有机物 及生物制品等均可适用;
• 由于将液膜含浸在多孔支撑
体上,支持液膜可以承受较
大的压力,且具有更高的选
择性。
精选ppt
膜厚为20~500μm,微 孔直径为0.1~5 μm。11
2.4.3 液膜的组成
膜溶剂 —膜相的基体物质
液
膜 的 组
表面活性剂
—是稳定油水分界 面的最重要的组分
成 流动载体 —对预提取的物质进 行选择性搬运迁移
(2)阳离子表面活性剂:各种胺盐,如季铵化物;
(3)非离子表面活性剂:烷基酚的聚乙烯醚衍生物、烷基硫
醇、醇类等。
精选ppt
14
(三)流动载体
1. 流动载体的作用:对预提取的物质进行选
择性搬运迁移,因此对选择性和膜的通量 起决定性作用。
膜分离技术在食品工业上的应用

膜分离技术在食品工业上的应用随着科技的不断发展,膜分离技术作为一种新型的分离技术,在食品工业中得到了广泛应用。
膜分离技术以其高效、节能、环保等特点,在食品加工过程中发挥着越来越重要的作用。
本文将详细介绍膜分离技术的原理、分类、特点,并探讨其在食品工业中的应用、存在的问题以及未来发展趋势。
膜分离技术是一种利用膜材料分离液体或气体混合物的新型分离技术。
其原理是利用膜材料的不同孔径和选择性能,将混合物中的不同组分进行分离、提纯和浓缩。
膜分离技术可分为微滤、超滤、纳滤、反渗透、电渗析等类别,具有高效、节能、环保、操作简便等特点。
在饮料加工过程中,膜分离技术主要用于果汁、酒类等液体的澄清和提纯。
通过超滤技术,可以有效地去除果汁中的果胶、蛋白质、细菌等杂质,提高果汁的澄清度和口感。
同时,在酒类加工中,膜分离技术可以去除酒中的甲醇、乙醛等有害物质,提高酒的质量和安全性。
在发酵工业中,膜分离技术主要应用于菌体分离、蛋白质分离和发酵液的澄清。
通过微滤或超滤技术,可以有效地将菌体和未发酵的溶液进行分离,得到高纯度的菌体蛋白质。
同时,膜分离技术还可以去除发酵液中的杂质,提高发酵产物的质量和产量。
在蒸馏工业中,膜分离技术主要应用于脱盐、脱氧、脱氨等操作。
通过反渗透技术,可以有效地去除溶液中的无机盐、有机物和微生物,得到高质量的蒸馏产品。
例如,在制糖工业中,反渗透技术可以去除糖汁中的盐分和色素,提高糖的纯度和白度。
膜污染是膜分离技术中普遍存在的问题。
由于原料液中的悬浮物、微生物和有机物等杂质会附着在膜表面,导致膜通量下降,甚至出现堵塞和破裂等问题。
为解决这一问题,可以采用预处理措施,如过滤、沉淀、离心等,以去除原料液中的杂质。
定期清洗和化学清洗也可以有效地减轻膜污染。
膜的寿命是影响膜分离技术成本的关键因素之一。
由于膜材料本身的质量和加工工艺的限制,膜的寿命存在一定的局限性。
为延长膜的寿命,可以选用高分子量、高稳定性、低污染的膜材料,优化膜组件的设计和加工工艺,避免极端操作条件等。
液膜分离技术介绍及其应用
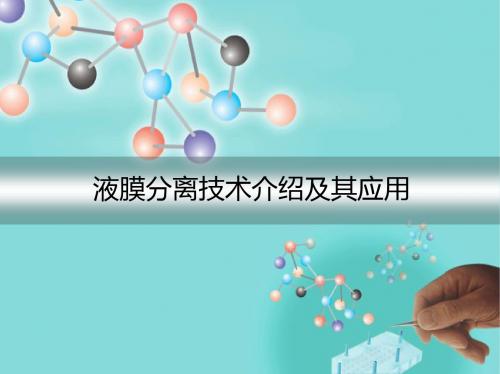
常见的乳状液膜可看成是“水/油/水:(W1/O/W2)或
“油/水/油”型(O1/W/O2)的双重乳状液高分散体系。
液膜的传递机理
可分为单纯迁移、反萃相化学反应促进迁移以及膜相 载体输送
①单纯迁移
又称物理渗透,根据料
液中各种溶质在膜相中
的溶解度(分配系数)和 扩散系数的不同进行萃 取分离。
传递机理
②反萃相化学反应促进迁移
传递机理
③ 膜相载体输送
在膜相中加入 Carrier , 它能选择性地与外相中的待 分离物质结合后透过膜相并
将它送入内水相。
二.乳状液膜分离过程
乳状液膜分离的典型工艺主要由液膜制备、混合分
离、沉降澄清和破乳等过程组成
• 乳化液膜的操作模式图
具体过程介绍
1. 乳状液膜的制备 通常采用搅拌、超声 波或其他机械分散等方式,使含有膜溶剂、 表面活性剂、流动载体以及膜增强剂的膜 相溶液与内相溶液进行混合. 2 .混合分离 使乳状液膜与待分离的料液 充分混合接触,形成W/O/W型或O/W/O型 多重乳状液分离系.
流动载体的研制与选择分离;
设备结构设计及工艺条件的优化; 开发经济实用的破乳技术等。
四.乳状液膜分离技术的应用
液膜分离萃取氨基酸
应用实例
液膜分离萃取抗生素
谢谢各位!
液膜分离技术介绍及其应用汇报Fra bibliotek容分离机理
分离过程
优点缺点 应用实例
液膜分离法, 是一种以液膜为分离介质、以浓度差为推动力的
膜分离操作
液膜 是悬浮在液体中很薄的一
层乳液微粒。它能把两个组成不 同而又互溶的溶液隔开,并通过 渗透现象起到分离的作用。
液膜通常是由溶剂、表面活性剂和添加剂制成
液膜分离法脱除废水中的污染物

液膜分离法脱除废水中的污染物一、实验目的(1)掌握液膜分离技术的操作过程。
(2)了解两种不同的液膜传质机理。
(3)用液膜分离技术脱除废水中的污染物。
二、实验原理液膜分离技术是近三十年来开发的技术,集萃取与反萃取于一个过程中,可以分离浓度比较低的液相体系。
此技术已在湿法冶金提取稀土金属、石油化工、生物制品,三废处理等领域得到应用。
液膜分离是将第三种液体展成膜状以分隔另外两相液体,由于液膜的选择性透过,故第一种液体(料液)中的某些成分透过液膜进入第二种液体(接受相),然后将三相各自分开,实现料液中组分的分离。
所谓液膜,即是分隔两液相的第三种液体,它与其余被分隔的两种液体必须完全不互溶或溶解度很小。
因此,根据被处理料液为水溶性或油溶性可分别选择油或水溶液作为液膜。
根据液膜的形状,可分为乳状液膜和支撑型液膜。
本实验采用乳状液膜法分离模拟水污染物-醋酸水溶液中的醋酸。
由于处理的是醋酸废水溶液体系,所以可选用与之不互溶的油性液膜,并选用NaOH 水溶液作为接受相。
先将液膜相与接受相(也称内相)在一定条件下乳化,使之成为稳定的油包水(W/O)型乳状液,然后将此乳状液分散于含醋酸的水溶液中(此处称作为外相)。
外相中醋酸以一定的方式透过液膜向内相迁移,并与内相NaOH反应生成NaAc而被保留在内相,然后乳液与外相分离,经过破乳,得到内相中高浓度的NaAc,而液膜则可以重复使用。
为了制备稳定的乳状液膜,需要在膜中加入乳化剂。
乳化剂的选择可以根据亲水亲油平衡值(HLB)来决定。
一般对于W/O型乳状液,选择HLB值为3-6的乳化剂。
有时,为了提高液膜强度,也可在膜相中加入一些膜增强剂(一般粘度较高的液体)。
溶质透过液膜的迁移过程,可以根据膜相中是否加入流动载体而分为促进迁移Ⅰ型或促进迁移Ⅱ型传质。
促进迁移I型传质,是利用液膜本身对溶质有一定的溶解度,选择性地传递溶质(见图11-1)。
促进迁移Ⅱ型传质,是在液膜中加入一定的流动载体(通常为溶质的萃取剂),选择性地与溶质在界面处形成络合物;然后此络合物在浓度梯度的作用下向内相扩散,至内相界面处被内相试剂解络(反萃),解离出溶质载体,溶质进入内相而载体则扩散至外相界面处再与溶质络合。
支撑液膜萃取

支撑液膜萃取支撑液膜萃取是一种常见的分离提纯技术,广泛应用于化工、制药、食品等领域。
本文将从液膜萃取的原理、应用及优势等方面进行介绍,以帮助读者更好地了解和应用这一技术。
一、液膜萃取的原理液膜萃取是一种利用液膜分离物质的技术。
在液体介质中,通过添加表面活性剂等物质,形成一层薄膜状的液体,与被提取物质接触。
被提取物质会从原料相中扩散到液膜相中,然后再通过萃取剂将目标物质从液膜中分离出来。
这种技术利用了液膜的选择性和传质性能,实现了物质的分离和纯化。
二、液膜萃取的应用1. 化工领域:液膜萃取技术广泛应用于化工工艺中的分离提纯过程。
例如,从废水中提取有机物,从溶液中分离金属离子等。
2. 制药领域:液膜萃取可以用于药物的纯化和分离。
通过调整液膜组成和条件,可以实现对目标药物的选择性吸附和传质。
3. 食品领域:液膜萃取可用于食品添加剂的提取和分离。
例如,从食品中提取香料、色素等物质。
三、液膜萃取的优势1. 高效:液膜萃取能够提供大表面积,加快物质传质速率,提高分离效率。
2. 选择性强:通过调整液膜组分和条件,可以实现对目标物质的选择性分离,减少副产物的生成。
3. 操作简便:液膜萃取过程相对简单,不需要高温高压条件,操作方便,降低了设备和能源成本。
4. 可持续发展:液膜萃取过程中所用的溶剂和表面活性剂可以回收利用,减少了对环境的污染。
支撑液膜萃取作为一种重要的分离提纯技术,在化工、制药、食品等领域有着广泛的应用前景。
通过调整液膜组分和条件,可以实现对目标物质的选择性分离和纯化,提高了分离效率和产品质量。
同时,液膜萃取具有操作简便、可持续发展等优势,为工业生产提供了一种高效、环保的分离技术。
相信随着科技的不断发展和改进,液膜萃取技术将在更多领域展现出其巨大的潜力和应用价值。
液膜分离法

液膜分离法
液膜分离法是一种利用液膜进行物质分离的工艺过程,其基本原理是利用不同组分在液膜中的溶解、扩散和迁移等特性来实现物质的分离。
液膜分离法主要包括乳化液膜、支撑液膜和流动载体等类型。
乳化液膜是一种将液体介质中的两种互不相溶的液体分别形成水包油型或油包水型乳液,通过控制乳液的粒径和稳定性,使乳液微滴在流动过程中通过液膜时实现物质的分离。
支撑液膜是将一种可渗透的液膜固定在多孔支撑板上,通过在液膜中添加不同性质的溶液,使不同组分在液膜中溶解、扩散和迁移,从而实现物质的分离。
流动载体则是一种将水溶液中的待分离物质通过化学反应转化为可以在有机相中溶解的物质,再通过液膜将其从有机相中提取出来的方法。
液膜分离法的优点包括选择性高、分离效果好、操作简单、能耗低等。
它可以用于分离各种不同的物质,如有机物、无机物、金属离子、蛋白质等,尤其适用于分离量大且对热敏感的物质。
然而,液膜分离法也存在一些局限性,如稳定性差、容易污染等。
因此,在实际应用中需要不断优化液膜分离工艺和材料,以提高其稳定性和分离效果。
以上信息仅供参考,如有需要,建议咨询化学专家或查阅相关文献资料。
液膜分离技术概述

液膜萃取技术分离氨基酸 液膜萃取技术在提取抗生素中的应用 利用液膜萃取技术提取生物碱
液膜分离技术的应用进展
支撑液膜:目前已用于气体分离、废水处 理、湿法冶金中重金属离子的回收浓缩、 生物产品的分离和固定酶等方面。(从含 铜废水中脱除和回收铜、用于 CO2、 NO、 CO、 H2S、 烯烃和氧气等气体分离) 乳状液膜:利用乳状液膜技术处理含锌废 水在国内外均有广泛研究,用乳状液膜技术 处理含镉废水取得了较好的结果 。
针对支撑液膜稳定性 ,进行了复合支撑液膜 的研究、 膜液改性 (膜载体固定化、 载体 化学接枝及溶剂功能一体化支撑膜 )、新型 SLM 组件的研究。 针对乳化液膜稳定性 ,进行了以下研究:合 成新型表面活性剂、 对乳化液膜流变性能 进行改性、 微乳化液膜 的制备。
液膜分离技术在医药工业中的应用
液膜分离技术ቤተ መጻሕፍቲ ባይዱ述
姓名:张洪勇 专业:生物化工
液膜分离技术概述
液膜分离技术分类 液膜分离技术的应用进展 影响液膜分离的因素 液膜分离技术在医药工业中的应用
液膜分离技术分类
液膜技术是 1968 年美国埃克森公司的 美籍华人黎念之博士提出的一种新型膜分 离方法。它是利用对混合物各组分渗透性 能的差异来实现分离、提纯或浓缩的分离 技术。 根据液膜构成和操作方式的不同, 可将 液膜分为支撑液膜 ( Supported liquid membrane) 和乳状液膜(Emulsion liquid membrane)。
影响液膜分离的因素
液相容易从支撑体的微孔中流失 膜内存在压差的影响 支撑膜孔被阻塞 剪切力诱导的乳化作用 渗透压的影响
支撑液膜
乳状液膜:它必须由制乳、提取与破乳 3 道 工序所组成, 而制乳与破乳往往是相互矛盾 的操作。由于夹带 (re-entrainment) 和渗 透压差 (osmotic pressure difference)引起 的液膜溶胀, 导致了内相中已浓缩溶质的稀 释、传质推动力的减小以及膜稳定性的下 降。
液膜分离技术

液膜分离技术液膜分离技术是一种快速,高效节能的新型分离方法。
目前,在广泛深入研究的基础上,液膜分离技术在湿法冶金,石油化工,环境保护,气体分离,有机物分离,生物制品分离与生物医学分离等领域中,显示出了广阔的应用前景。
一:液膜分离技术的特征液膜是用以分隔其互不相溶的液体的一个介质相,它是被分隔两相液体之间的“传质桥梁”。
与传统的溶剂萃取过程相比,液膜分离技术具有三个方面的特征。
1,传质推动力大,所需分离级数少。
2,试剂消耗量少,流动载体在膜的一侧与溶质结合,在膜的另一侧与将溶质释放,自身再生并可循环使用。
3,溶质可以“逆浓度梯度迁移”。
液膜分离技术按其构型和操作方式的不同,主要可以分为厚体载膜,乳状液膜和支撑液膜。
二:液膜分离机理及促进传递1,液膜分离机理的类型1)选择性渗透。
选择性渗透是指不同的物质依据他们在膜相的溶解度和渗透速率的不同进行分离。
2)渗透伴有化学反应。
渗透伴有化学反应的过程依据发生的反应类型不同,可以分为滴内反应和膜相反应两种。
3)萃取与吸附。
萃取与吸附机理是指料液中悬浮物为膜相吸附或者有机物为膜相萃取,从而达到分离的目的。
工业废水中有机物悬浮液滴或固体微粒的液膜分离属于这类机理。
2,液膜分离过程的传质推动力液膜分离过程实际上是特殊的萃取反萃耦合过程。
支撑液膜体系传质推动力主要来自料液相和反萃相的组成的差异,一般条件下,膜相的性质对传质推动力的影响比较小。
3,两种促进迁移1)促进迁移I。
I型促进迁移是指待分离溶质从料液相溶解于膜相并渗透扩散至膜相与接收相界面,与接收相内的化学试剂发生发硬,生成不溶于膜相的新的物质形态,无法透过膜相作逆向扩散。
2)促进迁移II。
II型迁移是指待分离溶质与膜相中的流动载体反应生成中间化合物,由流动载体负载着完成膜相的迁移。
a:反向迁移。
反向迁移是指载体与待分离溶质反应的络合物与供能溶质迁移方向相反的液膜过程。
b:同向迁移。
同向迁移是指载体与待分离溶质反应的络合物与供能溶质迁移方向相同的液膜过程。
第九章 液膜分离详解
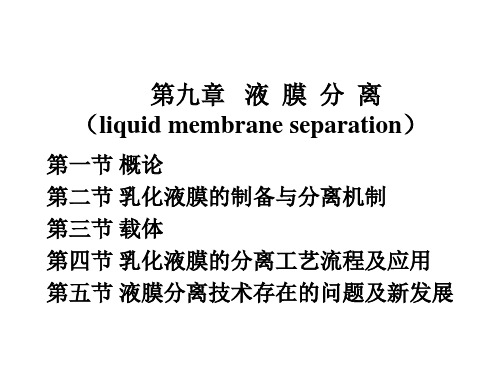
液膜模拟生物膜的结构,它利用选择 透过性原理,以膜两侧的溶质化学浓度差 为传质动力,将膜分离与溶剂萃取相结合, 使选择性渗透、膜相萃取和膜内相反萃取 三个传质环节同时完成,以使料液中待分 离溶质在膜内相富集浓缩,分离待分离物 质。
液膜分离涉及三种液体:通常将含有被 分离组分的料液作连续相,称为外相;接 受被分离组分的液体,称为内相;成膜的 液体处于两者之间,称为膜相。 在液膜分离过程中,被分离组分从外相 进入膜相,再转入内相,浓集于内相。
2、表面活性剂 它是液膜技术中稳定油水分界面的最重要 的组分,对液膜的稳定性、渗透速度、分离 效率和膜相与内水相分离后的循环使用有直 接关系。 3、流动载体 合适的载体是液膜分离技术的关键之一。 它能对欲提取的物质进行选择性运输,因此 对选择性和膜的通量(或分离速度)起决定 性作用。 起萃取剂作用。
4、膜增强剂 起增加膜的稳定性作用。 在液膜的分离操作时要求膜不过早破裂; 而在破乳工序中液膜层又容易破碎,以利 于膜相与内水相的分离。
三、液膜与生物膜的相似性 生物细胞膜主体是由类脂双分子层、蛋 白质构成的。 类脂分子的极性亲水端向外形成类脂双 分子层,非极性亲油尾端互相聚集。 膜中央近似液体,膜表面则近似晶体。 蛋白质分子以各种方式联结在膜上,这 些蛋白质有“识别”、“输送”物质的功 能,即能选择性地将一个物质分子或离子 从膜的一侧输送到膜的另一侧。
第一节 概述
膜是一种流动相内或两种流动相之间, 有一薄层凝聚相物质,可把流动相分割成 两部分,此一薄层物质即所谓的“薄膜”, 简称膜。 液体膜是膜技术的一个分支,是一种新 兴的节能型分离手段。
液体膜(简称液膜)是模仿生物膜的选 择性输送功能的一种人工膜。 液膜是一层很薄的液体,由悬浮在液体 中的一层很薄的乳液微粒构成。它阻隔在 两个可互溶但组成不同的液相之间,一个 液相中的待分离组分通过液膜的渗透作用 传递到另一个液相中,从而实现分离的目 的。
液膜分离技术

相的物质P,使渗透物C在内相中的浓度为零,从而保 持C在液膜内外两相有最大的浓度梯度,以促进C的传 递达到从料液相中分离C组分的目的。这种在滴内发 生化学反应而促进渗透物传递的机理也称为I型促进迁 移。 3)膜相化学反应(Ⅱ型促进迁移) 如图3-1(3)所示,在膜相中加入一种流动载体R1,料 液中的D组分在膜相/连续相的界面上与R1反应,生 成中间产物P1,P1在浓度差的作用下扩散至膜相的另 一侧,在膜相/内相界面上与内相试剂R2发生反应, 生成不溶于液膜的物质P2并使R1重新还原并释放至膜 相中,藉浓度梯度作用扩散返回至膜相/连续相界面 一侧。R1在整个传递过程中没有消耗仅起了载体的作 用。这种含流动载体的液膜在选择性、渗透性和定向 性二方面更类似于生物细胞膜的功能,它使分离和浓 缩两过程合二为一。这种迁移机理即为Ⅱ 型促进迁移, 也称为“离子泵”。
4)萃取和吸附
这种液膜分离过程具有萃取和吸附的性质,如图3-1(4) 所示。料液中的悬浮物为膜相吸附或有机物为膜相萃 取,从而实现分离的目的。
●
4. 液膜分离的操作过程
乳化液膜的操作过程与支撑液膜相比较为复杂,其流 程示意图如图3-14所示,主要步骤分为:乳化液膜制 备、混合分离、沉降澄清和破乳等工序。 (1)乳化液膜的制备 将含有膜溶剂、表面活性剂、流动载体以及其他膜 增强剂的膜相溶液同内相溶液进行混合,制得所需的 水包油(O/W)或油包水(W/O)型乳化液。通常,制得乳 液的稳定性与制乳过程的操作因素相关,主要包括: 表面活性剂的加入方式、制乳时的加料顺序、制乳搅 拌方式以及乳化器材质的润湿性能等。 (2)混合分离 这一阶段是使乳化液膜与料液进行混合接触,形成油 包水再水包油(O/W/O)型或水包油再油包水(W/O/W) 型多重乳化液,实现传质分离。在间歇式混合设备中,
液膜分离技术介绍及其应用

液膜分离技术介绍及其应用液膜分离技术是一种利用液膜技术来进行分离和提纯的方法。
液膜是指由适当的溶剂系统中的两相液体相互分离,通常是液滴悬浮在另一种液体中,形成的稳定界面。
液膜分离技术通过控制液膜的形成、分离和再生来实现分离和提纯的目的。
液滴生成是指通过喷雾、溶液分散或液滴生成器等方式将溶液转化为均匀大小的液滴。
液滴的大小和形状可以通过调节喷雾器、液滴生成器的参数来控制。
分离是指将生成的液滴传送到分离区域进行分离。
在分离区域,液滴与另一种液体相互接触,通过质量传递或化学反应将目标组分分离出来。
分离过程中,可以根据目标组分的性质调控分离液的成分、温度、pH值等条件来达到更好的分离效果。
再生是指将分离出的目标组分从液膜中还原出来。
再生的方法主要有两种:一种是通过改变分离液性质,使目标组分从分离液重新分离出来;另一种是通过添加剂或改变温度等方式改变液膜性质,从而实现目标组分的再生。
1.化学工程领域:液膜分离技术可以用于溶剂的回收和再利用。
例如,在有机合成过程中,可以通过液膜分离技术将溶剂从反应液中分离出来,然后再进行再利用,减少溶剂的使用量,降低成本。
2.环境保护领域:液膜分离技术可以用于处理水体中的有害物质,如重金属离子、有机污染物等。
通过调节液膜的成分和分离条件,可以将这些有害物质从水体中分离出来,达到净化水体的目的。
3.药物制造领域:液膜分离技术可以用于药物的提纯和纯化。
在药物制造过程中,通过液膜分离技术可以将目标药物从溶液中分离出来,去除杂质,提高药物的纯度和质量。
4.能源产业领域:液膜分离技术可以用于石油和天然气的脱硫、脱氮等工艺。
通过液膜分离技术,可以将有害气体和杂质从气体中分离出来,提高燃料的纯净度,减少环境污染。
总之,液膜分离技术作为一种高效、节能、环保的分离和提纯方法,具有广泛的应用前景。
随着技术的不断发展和改进,液膜分离技术将在各个领域中发挥越来越重要的作用。
液膜分离技术在医药化工中的应用

液膜分离技术在医药化工中的应用详细讲述了液膜的构成,液膜解析措施的原理以及特征,以及液膜分离技术在医药化工中的使用情况及其重要意义,同时对其发展展开详细论述。
标签:液膜分离;原理;医药化工;应用引言现在,在医药化工方面,药物的制造大多使用以往的吸附、沉积、液-液萃取法、微生物发酵、液-液有机溶剂萃取等很多方式,其操做程序非常复杂,使用的时间很长,制造程序中要使用很多原料,消耗的能源高,回收情况差,所以,改革药物的制造程序有着非常关键的作用,也是研发工作者日益关注的问题,伴随着液膜科技的发展,液膜技术在医药化工方面有着巨大的作用,文章就液膜解析措施在医药化工方面的使用以及前进展开了论述。
1 液膜液膜大多是膜溶剂、活性剂和介质构成。
液膜是由液体物料构成的膜,大多是漂浮在液体内的乳液颗粒经过化学反应构成的一种比较薄的薄层液体。
液膜是膜溶剂、介质、表面活性剂和稳定剂构成。
液膜离析技术也都称为液膜分离法,和固态液膜对比,拥有传递性能强、方便分离、消费低等优点,经过液膜萃取技术能够在最短时间内完成液体的分离以及浓缩。
1.1 液膜的分类液膜根据不一样的规范能够划分成几种不同的种类,例如,根据膜相的不同能过划分为水包油型和油包水型。
液膜种类重点根据其构造类型以及操做形式的不同,能够划分为支撑和乳状液膜。
这里,支撑油膜是隔离样式的液膜,关键是经过把媒介融解液滴到惰性多孔膜微孔,能够和别的颗粒分开。
乳状液膜液滴比较小同时贴近乳化状,平时使用的比较多。
根据媒介原理的不同,又可以划分为无介质和有介质两类。
这里,无介质运输是由液膜溶剂以及活性剂构成,有介质运输是膜溶剂、活性剂和掺入一定的介质构成。
现在,探索使用较为普遍的是有介质运输液膜。
1.2 液膜分离技术的优点液膜分离技术使用载体渗透性的不同开展液体解析,完成解析程序不用把液体溶液升温到达到沸点沸腾才能解析,更不用使液体达到气化状态,所以它的优势有:功效高;成本低;渗透能力强;易完成难度高的物质解析;操做浓度可大可小;操做技术简便,开支少。
液膜分离技术探讨

液膜分离技术探讨液膜分离技术(Membrane Liquid Separation Technology)又称为膜法分离技术,是一种基于半透膜原理的分离技术。
液膜分离技术广泛应用于各个行业,如环保、化工、食品、制药等领域。
其在分离材料、操作方式、分离过程中的能耗以及产物纯度等方面具有独特的优势。
液膜分离技术基于半透膜原理,即通过在分离系统中引入膜,利用膜的孔径大小和特定结构,实现对不同溶质、物质的选择性分离。
这种技术通过在分离系统中引入合适的膜,能够实现对流体、气体、固体等不同形态物质的高效分离和提纯。
与传统的分离技术相比,液膜分离技术具有结构简单、操作灵活、分离效率高、能耗低等优势。
液膜分离技术主要有三种操作方式,即扩散、渗透和电动力。
扩散是指通过半透膜间溶质的浓差差异实现分离。
渗透是指通过半透膜的选择性渗透性质实现分离。
电动力是指通过半透膜材料的电性特性实现分离。
这三种操作方式可以根据分离物质的特性和需求进行选择,提高分离效果和能量利用率。
液膜分离技术在分离过程中的能耗较低,主要是因为膜的效果提高了分离效果,减少了能耗的损失。
与传统的分离技术相比,液膜分离技术可以降低化学反应和物质转移的温度和压力要求,减少了热量和压力的消耗。
此外,由于膜材料的选择性,液膜分离技术可以在常温常压下进行,避免了能耗浪费。
液膜分离技术在产物纯度方面也具有一定的优势。
由于膜的选择性,可以实现对不同物质的高效分离和浓缩,从而提高产物的纯度。
此外,液膜分离技术可以实现对微小分子、粒径较小的悬浮物质的有效分离,提高了产物的质量。
虽然液膜分离技术具有许多优点,但在实际应用中还存在一些问题需要解决。
首先,膜的选择和设计是关键。
不同的分离物质和要求需要选择不同的膜材料和膜结构,因此需要对膜材料进行深入研究和优化。
其次,膜的寿命和稳定性是一个重要问题。
膜在使用过程中容易受到污染、损坏和老化等因素的影响,导致分离效果下降和寿命缩短。
- 1、下载文档前请自行甄别文档内容的完整性,平台不提供额外的编辑、内容补充、找答案等附加服务。
- 2、"仅部分预览"的文档,不可在线预览部分如存在完整性等问题,可反馈申请退款(可完整预览的文档不适用该条件!)。
- 3、如文档侵犯您的权益,请联系客服反馈,我们会尽快为您处理(人工客服工作时间:9:00-18:30)。
宁波大学硕士研究生2016/2017学年第1学期期末答题纸考试科目:生化分离技术课程编号:考卷类型:(A/B)姓名:学号:阅卷老师:成绩:液膜分离的原理及应用摘要:液膜模拟生物膜的结构,通常由膜溶剂、表面活性剂和流动载体组成。
它利用选择透过性原理,以膜两侧的溶质化学浓度差为传质动力,使料液中待分离溶质在膜内相富集浓缩,分离待分离物质。
关键字:液膜分离技术,乳化液膜,支撑液膜。
Principle and application of liquid membrane separationAbstract:Liquid membrane simulates the structure of a biofilm, usually consisting of a membrane solvent, a surfactant, and a mobile carrier. It uses the principle of selective permeability to the membrane on both sides of the solute chemical concentration difference for the mass transfer power,so that the liquid to be separated in the membrane solute enrichment enrichment, separation of the material to be separated.key words:liquid membrane separation technology, emulsion liquid membrane ,supported liquid membrane ,waste water treatment。
液膜分离是 60 年代中期诞生的一种新型的膜分离技术。
它具有膜分离的一般特点, 主要是依据膜对不同物质具有选择性渗透的性质来进行组分的分离。
自20世纪 60 年代美国林登埃克森研究与工程公司黎念之博士( N.N.Li)发明后[1]。
液膜通常由膜溶剂、表面活性剂、流动载体和膜增强添加剂组成[2]。
各国学者相继开展了大量的研究。
该技术在湿法冶金、金属离子回收、废水处理、生物制品分离与生物医药分离、化工分离等方面已显示出广泛的应用前景。
目前液膜技术处理农药厂废水已实现工业化, 在含锌废水处理中已进行了工业试验, 液膜技术分离宇宙飞船中 CO2 也已成功得到应用, 液膜分离技术正在得到迅速的发展。
生物学家们在液膜促进传递方面取得的成就引起了化学工程师们的注意. 60 年代中期 , Bloch 等[3]采用支撑液膜( supported liquid membrane) 研究了金属提取过程, Ward 与 Robb[4]研究了 CO2 与 O2 的液膜分离, 他们将支撑体液膜称为固定化液膜( immobilized liquid membrane). 黎念之( N .N . Li) 在用du Nuoy 环法测定含表面活性剂水溶液与油溶液之间的界面张力时 ,观察到了相当稳定的界面膜 ,由此开创了研究液体表面活性剂膜( liquid surfactant membrane) 或乳化液膜( emulsion liquid membrane)的历史[5]1液膜分离原理1.1液膜及其分类液膜是分隔两个液相的第三液相,它与被分隔液体的互溶度极小。
膜相液通常由膜溶剂、载体、表面活性剂、稳定剂所组成。
膜溶剂是膜相液的基体,占膜总量的90%以上,选择膜溶剂主要考虑膜的稳定性和对溶质的溶解性。
当原料液为水溶液时,用有机溶剂作液膜,当原料液为有机溶剂时,用水作液膜。
载体是运载溶质穿过液膜的物质,它能与被分离的溶质发生化学反应,它分为离子型和非离子型。
离子型载体通过离子交换方式与溶质离子结合,在膜中迁移;非离子型载体与原料液中的金属离子、阴离子形成络合物以中性盐的形式在液膜中迁移。
流动载体使指定的溶质或离子进行选择性迁移,决定分离的选择性和通量。
表面活性剂起乳化作用,它含有亲水基团和疏水基团,表面活性剂的分子定向排列在相界面上,用以增强液膜。
两种基团的相对含量用亲水亲油平衡值(HLB)表示,HLB 愈大,则表面活性剂的亲水性愈强,一般HLB为3-6的表面活性剂用于油膜,易形成油包水型乳液;HLB为8-15的表面活性剂用于水膜,易形成水包油型乳液。
表面活性剂是创造液膜固定油水分界面的最重要组分,它直接影响膜的稳定性、渗透速度、分离效率和膜的复用。
稳定剂可以提高膜相液的粘度,促进液膜的稳定性。
即要求液膜在分离操作过程中不过早破裂,以保证待分离溶质在内相中富集,而在破乳时又容易被破碎,便于内相与液膜的分离。
2液膜按其构型和操作方式的不同可分为乳状液膜和支撑液膜两类。
2.1 乳状液膜乳状液膜是以包裹层形式处于两液相之间。
被包裹的是内相,处于液膜外的称为外相。
内相液在乳液膜内分散成许多微液滴,悬浮在膜相液中构成乳状液。
微液滴直径为1-100μm,乳状液液滴直径为0.5-2mm。
当内相是水溶液,膜相是有机溶液时,称为油包水型(W/O)液滴,用于分离水溶液;当内相为有机溶液, 膜相为水时,称为水包油型(O/W)液滴,用于分离有机溶液。
乳状液膜形成的过程是:先将内相液分散到膜相液液中,形成乳状液膜。
在分离过程中,外相的分离组分通过膜传递到内相而达到分离目的。
乳状液膜的稳定性好,具有巨大的比表面积,大大提高萃取速度。
2.2支撑液膜支撑液膜是由溶解了载体的膜相液,在表面张力作用下,依靠聚合凝胶层中的化学反应或带电荷材料的静电作用,含浸在多孔支撑体的微孔内而制成,由于将液膜含浸在多孔支撑体上,可以承受较大的压力,且具有更高的选择性。
支撑液膜的性能与支撑体材质、厚度及微孔直径的大小关系极为密切。
通常孔径越小,液膜越稳定,但孔径过小将使空隙率下降,从而降低透过速度。
支撑液膜使用的寿命只有几个小时至几个月,不能满足工业化应用要求,需采取适当措施提高其稳定性。
长期以来,支撑液膜的稳定性问题一直未能很好解决.导致支撑液膜不稳定的因素如下:①膜液在料液相与接收相中的溶解损失(对液体分离) [5,6]与膜液的挥发损失(对气体分离)[7];②具有表面活性的载体分子提高了油-水两相的互溶性[8];③膜两侧压力差超过膜孔吸附膜液的毛细管力[9] .3、液膜分离的传质机理液膜分离过程可分为从原料液到膜相液和从膜相液到接受液两步萃取过程。
而萃取过程又可分为物理萃取和化学萃取。
因此,液膜分离的传质机理有四种类型。
3.1选择性渗透液膜不含载体。
这种液膜分离是靠待分离的不同组分在膜相液中的溶解度和扩散系数的不同导致透过膜的速度不同来实现分离的。
见图1。
原料液中的A、B组分,由于A易溶于膜,而B难溶于膜,因此,A透过膜的速率大于B,经过一定时间后,在接受液中的A的浓度大于B,原料液侧的B的浓度大于A,从而实现A、B的分离。
但当分离过程进行到液膜两侧被迁移的溶质浓度相等时,输送便自行停止,因此,它不能产生浓缩效果。
图表 1 选择性渗透3.2内相有化学反应液膜不含载体。
内相的接受液中含有试剂R,它能与原料液中迁移的溶质A发生不可逆的化学反应,并生成一种不能逆扩散透过膜的新产物P,从而使渗透物A在内相接受液中的浓度为零,直至R被反应完全为止,见图2。
因此,保持了A在内、外相中的最大浓度差,促进了A的传递;相反,由于B不能与R反应,即使它也能渗透进入内相,但很快达到了渗透停止的浓度,从而达到了A与B的分离目的。
图表2 内相有化学反应3.3偶合同向迁移膜相液中含有非离子型载体S,它与料液中的阴离子选择性络合的同时,又与阳离子络合成离子对而一起迁移,称为同向迁移,见图3。
载体S在外相界面上与原料中的阳离子M+和阴离子X-生成中性络合物MX·S。
此络合物不溶于外相而易溶于膜相,并以浓度差为推动力在膜内向内相界面扩散。
在内相界面上,由于内相液浓度低,络合物解络,释放出溶质离子M+和X-。
解络后的载体S留在膜相内,以扩散方式返回外相界面。
图表 3 偶合同向迁移3.4偶合逆向迁移它是指膜相液中含有离子型载体时溶质的迁移过程,见图4。
用酸性萃取剂HR作为金属离子M+的载体,在外相界面上发生M+与H+的交换,生成的MR进入膜相,并向外相界面扩散,而交换下来的M+进入内相。
由于M+在膜内溶解度极低,故不能返回。
整个传递过程的结果是M+从外相经膜进入内相,H+则从内相经膜进入外相,M+的迁移引起了H+的逆向迁移,所以称为逆向迁移。
图表 4 偶合逆向迁移4 液膜分离技术的特点4.1液膜分离技术的优点从本质上看,液膜分离技术兼有溶剂萃取和膜渗透两项技术的特点。
从工艺上看,它类似于溶剂萃取法。
它具有如下优点: ①液膜法中的提取和解吸是合并在一起同时完成的 ,大大提高了分离效率。
②降低了试剂消耗和成本。
③乳化液膜具有很大的表面积 ,具有很高的渗透性。
④能分离一般方法很难分离的一些物理、化学性质相似的碳氢化合物。
⑤操作浓度的区间大。
⑥工艺简单 ,操作方便 ,成本低。
4.2液膜分离技术的改进研究国内外研究者们一直在努力探索各种具有潜在工业应用意义的液膜分离技术 , 除了提高 E L M和S L M稳定性的研究之外,还不断探索新的液膜构型 ,以期在保持液膜分离特点的同时 ,克服液膜不稳定等缺点.目前 ,国内外研究者针对乳化液膜稳定性,进行了以下研究:合成新型表面活性剂、对乳化液膜流变性能进行改性微乳化液膜( Micro-Emulsion Liquid Membranes , MELM) 的制备[10]。
针对支撑液膜稳定性,进行了复合支撑液膜(Composite SupportedLiquid Membrane )的研究、膜液改性(膜载体固定化、载体化学接枝及溶剂功能一体化支撑膜)、聚液体支撑液膜及离子液体支撑液膜的研究[11]。
同时,进行了液膜新构型的研究,其中包括 : 流动液膜(包容液膜)、液体薄膜渗透萃取、静电式准液膜、内耦合萃反交替分离过程及支撑乳化液膜[12]。
通过各种改性研究 ,有效的改善了液膜的性质 ,从而使液膜的应用更为广泛。
参考文献:[1]Li N N. Separation hydrocarbons with liquid membrane: US, 3410794[P].1968- 11-12.[2] 张瑞华.液膜分离技术[M].南昌: 江西人民出版社, 1984:10- 12[3]Bloch R , Finkelstein A ,Kedem O , et al .Metal ion separation by dialysis through solvent membranes .Ⅰ & EC Process Design and Dev , 1967 , 6 :231 ~237[4] Ward Ⅲ W J .Robb W L . Carbon dioxide-oxygen separation : facilitated transport of carbon dioxide across a liquid film . Science , 1967 , 156 : 1481 ~1486[5] Li N N , Somerset N J . Separating hydrocarbons with liquid membrane . US Pat , 3419794 .1968[6]Danesi P R , Reichley -Yinger L , Rickert P G .Lifetime of supported liquid membranes :the influence of interfacial properties , chemical composition and w ater transport on the long -term stability of the membranes . J M embr Sci , 1987 , 31 ( 2 -3 ) : 117 ~145[7] Fabiani C , M erigiola M ,Seibona G , et al . Degradation of supported liquid membranes under an osmotic pressure gradient. J M embr Sci, 1987 , 30( 1) : 97 ~104[8] M atson S L , Lopez J , Quinn J A .Separation of gases with synthetic membrane .Chem Eng Sci , 1983 , 38 : 503 ~524[9] M ajumdar S , Sirkar K K , Sengupta A .Hollow –fiber contained liquid membrane .In :Ho W S , Sirkar K K ,eds .M embrane Handbook .New York :Chapman &Hall, 1992 .764 ~909[10]李成海, 龚福忠, 周立亚. W/O型微乳液膜的制备及提取稀土的研究[ J ] .化学通报, 2000, 2: 11 ~14.[11] Carlin RT . Supported ionic liquid membrane reactors : Energy saving with reduced materials Requirments [ A] . Green( or Greener ) Industroal Application so fIonic Liquids [ C ] .San Diego C A: U S A, 2001. 1 ~5.[12] Ho W S . Combined supported liquid membrane /strip dispersion process for the removal and recovery of metals [ P ] . US : 6350419, 2002 -02 -26.。