钻杆管体开裂失效原因分析
非开挖导向、定向钻杆的失效原因

非开挖导向、定向钻进用钻杆的失效原因及解决措施前言钻杆最可怕的失效形式是钻杆的断裂。
钻杆在导向、定向钻进铺管过程中一旦断裂,将会对工程造成严重影响,不仅是经济上的损失,而且影响工期,失去信誉,后果不堪设想。
因此,作为施工企业,一定要学会如何正确地选择和使用钻杆;而作为钻杆生产厂家,要知道非开挖工程对钻杆的特殊要求,生产出高强度、高弹性和高可靠性的钻杆。
笔者在1994年至1998年间曾带队做过多项导向钻进非开挖铺管工程,尽管当时的钻杆质量非常差,但在施工过程中从未遇到断钻杆事故。
后来,笔者从事非开挖工艺和钻具的研究、设计工作,此期间也是我国非开挖铺管技术迅猛发展的时期,时常有施工单位报告钻杆断裂事故,总觉得有些费解。
于是,笔者亲身在施工现场调查了多起事故原因,同时设计了多种结构形式的钻杆进行试验。
通过多年的事故分析和试验研究,总结出一些钻杆失效(主要是断裂)产生的原因:除钻杆自身质量问题外,施工中不当的操作是使钻杆失效的主要原因。
笔者撰写此文旨在避免施工企业重复走弯路,也算作为我国非开挖技术的发展做一点贡献。
一、钻杆主要失效形式及原因分析非开挖导向、定向钻进用钻杆往往在受到较大拉力和扭力作用的同时,还受到弯曲力的作用。
钻杆通过曲线段时,钻杆被迫弯曲,弧线内侧受压应力作用,弧线外侧受拉应力作用。
当钻杆在曲线段旋转时,杆体就受到拉压交变应力的作力,而钻孔曲率半径越小交变应力就越大。
研究表明这个交变应力达到一定值后,就极容易使钻杆产生疲劳裂纹。
钻杆刚开始产生的疲劳裂纹非常微小,肉眼很难发现,但疲劳裂纹发展速度极快,最后表现为突然的脆性断裂。
试验证明,钻杆受交变应力作用而疲劳断裂是非开挖钻杆断裂失效的主要原因。
很多钻杆在施工导向孔时发生断裂事故就佐证了这一结论。
目前我国的非开挖施工队伍有很多是经验丰富素质高的专业公司,但更多的是临时拼凑起来的没有任何施工经验和技术的队伍,他们往往连钻杆(或钻孔)的曲率半径都没听说过,让他们来指挥非开挖施工是造成钻杆断裂的人为方面的主要原因。
试分析钻杆管体横向开裂的原因和解决方法

学性能试验定义方法以及ASTM E23中对金属材料的缺口试验标准做了拉伸和冲击试验。
从实验结果得知,本次断裂的钻杆在力学性能上与API SPEC 5DP 中的钻杆规范完全相符。
3.3 金相最后笔者又对钻杆的开裂部位做取样进行了金相分析,从中得出管内存有许多裂纹,在裂纹的两侧部位没有发现氧化与脱碳现象。
4 分析结果本文以一宗钻杆开裂事故为研究对象,对开裂钻杆化学成分与力学性能进行了初步的检查,得出钻杆本身没有任何问题。
之所以出现了钻杆断裂,主要是因为钻杆的工作环境对钻杆造成了较为严重的腐蚀。
通过对钻杆端口纹路分析得知断口最初出现在外壁,且断口的扩展区有着明显的疲劳辉纹。
外壁、钻杆都有微裂纹、腐蚀凹坑,得出钻杆的外壁裂纹与开裂断口有相同的性质。
内壁扩展区疲劳辉纹是腐蚀疲劳。
在钻杆壁出现的腐蚀物为氧化腐蚀物,所以钻杆腐蚀为氧化腐蚀。
钻井液是钻井过程中必须用到的物品,其循环系统为半敞开系统。
钻井液在除砂器、离心泵、振动筛、储罐通过时都会与和大气接触[1]。
大气中的部分氧气会在此过程中渗入钻井液成为游离氧。
因溶解氧强去极化作用导致即便氧的质量分数非常低,同样也会导致钻杆出现腐蚀问题,甚至造成严重的损伤[2]。
5 应对钻杆开裂的手段腐蚀是钻杆开裂最主要的原因[3]。
因此钻杆保养工作首先要做的就是为钻杆和钻井液提供更安全的工作环境,减少甚至是消除溶解氧对钻杆的腐蚀。
笔者建议定期对钻井液做脱氧处理在钻井液当中添加一定的缓腐蚀剂,提高钻井液的酸碱值,使其pH 值保持在10以上。
此外还要大力推广内涂层钻杆应用,做好钻杆堆放期的维护工作,以免存放不当引发钻杆出现腐蚀坑。
钻杆存放前必须清理钻杆内外的钻井液,当清洁结束后才可以堆放钻杆。
6 结语本次开裂的钻杆失效机理是腐蚀性疲劳,原因是钻杆的内外壁氧化腐蚀进而出现了腐蚀坑。
在交变应力作用下,钻杆内的腐蚀坑出现了疲劳裂纹,在疲劳裂纹不断扩张的作用下,导致钻杆出现了横向开裂问题。
摩擦焊接钻杆焊缝断裂失效分析

摩擦焊接钻杆焊缝断裂失效分析运用金相显微镜、扫描电镜对摩擦焊接钻杆焊缝断裂失效进行了分析。
结果表明,碳化物分布不均匀导致调质处理后在钻杆接头中产生“带状组织”。
焊后不正确的热处理使焊缝组织中出现残存的条状分布的马氏体,此条状分布的马氏体使焊缝的强韧性下降,造成焊缝发生疲劳断裂失效。
改进热处理工艺后,消除了残存马氏体,提高了钻杆焊缝的强韧性,从而提高了钻杆的使用寿命。
石油钻杆是油田钻井机械的重要部件。
钻杆由钻杆接头和钻杆管体通过摩擦焊接而成,焊后进行正火或调质处理。
钻杆使用时承受很大的拉应力和扭矩,并经受强烈的震动和冲击。
合理的摩擦焊工艺和正确的焊后热处理可使焊缝力学性能满足行业标准[1]。
如果摩擦焊或焊后热处理工艺不当,钻杆使用时焊缝容易断裂,造成很大的经济损失。
现有现场使用断裂钻杆1根,需要进行失效分析,判定其失效原因,提出解决措施,以提高钻杆质量,避免断杆事故发生。
2 现场调研钻杆生产厂生产的钻杆采用的接头为外购件,材料为40CrMnMo钢,调质处理后硬度为285~319HB(30~35HRC)。
管体采用已使用过的钻杆切除已损坏的接头后的旧管体。
接头与管体采用摩擦压力25~30MPa和顶锻压力50~60MPa的摩擦焊进行焊接。
根据现场了解,摩擦焊工艺较稳定,一般情况下能保证焊接质量。
焊后钻杆经中频加热后冲去焊缝内翻边,然后用车床车去外翻边。
最终热处理工艺为:中频淬火+中频加热回火。
规定的淬火加热温度为920℃,回火温图2 钻杆接头母材的金相组织×400腐蚀剂:4%硝酸酒精根据化学成分分析结果可知,该接头的材料为40CrMnMo钢。
接头母材的金相显微组织为回火索氏体,晶粒度为7~8级,沿接头轴向呈带状分布,显微组织不均匀。
白色区间显微硬度为183~188HV,黑色区间显微硬度为216~223HV。
黑色区间内含有较多的白色碳化物颗粒,用HR-150型洛氏硬度计测定其洛氏硬度值为31~36HRC,平均值为34HRC。
关于R780钻杆断裂问题的分析研究

关于R780钻杆断裂问题的分析研究【摘要】本文主要研究定向钻机以及其钻杆断处的细节表象,对其展开细致的总体观察、机械能动性测试以及物理或者化学成分测定等。
在测试结束后研究其结果并进行总结后可知,R780钻杆断裂的主要原因为施工中受到扭转力过大从而致使其钻杆金属疲劳,进而断裂;而R780钻杆上出现裂缝的主要原因为该钻杆受力过大,同时制作钻杆的原材料的强度稍有不足。
【关键词】钻杆断裂;扭转应力;探究分析对于定向钻机而言,由于其采用非开挖技术,因此对城市的道路不会产生较大的损害,又因其工作效率较高、工作成本相对低廉,该定向钻机的用途非常广泛,例如城市供水系统建设、城市热能供应、城市天然气供应、挖掘安置石油管道和电力通讯设备的架设等方面。
然而由于地形、环境等方面的影响,定向钻机的钻杆很容易出现裂纹甚至断裂。
本文主要研究R780钻杆的断裂问题,通过从施工现场取样的断裂钻杆为例,以显微测定、钻杆原材料以及钻杆断裂面的成像等方式为主要检测手段,从根本上研究该钻杆的开裂原因。
一、对钻杆的理化测试(一)总体测定将于施工现场所取得的R780钻杆进行实验室测定可知其相关属性如下:钻杆的长度为300mm,其表面稍有生锈,其中断裂处外可见60mm左右的横向裂纹,如图1所示。
从该图中可知,钻杆壁的厚度正常,细致观察管壁内部可知,该断面与钻杆的轴线出现了倾斜,倾斜角度约为45°,该倾斜使得断裂部位出现双平台现象,断裂处氧化严重,但是通过技术检测,该部位依然显露出断裂纹,纹路较为清楚且指向均匀。
因此可知,该处是钻杆的断裂源头,其大小约为整个断裂口的30%。
(二)对钻杆进行成分测定以及机械测试机械测定主要是从钻杆的中部取样分析,分析所用的主要仪器如下。
(1)对样本进行化学分析的仪器为QFN750光谱仪;(2)对样本进行拉伸强度测试以GB/T228相关标准为理论基础,采用CMT系列微型测试仪;(3)以GBT229为主要测试标准,采用NCSI智能冲击实验仪器对样本的冲击性进行试验。
钻杆断裂原因分析及预防措施——以陆丰13-1油田LF13-1—10A井钻杆为例
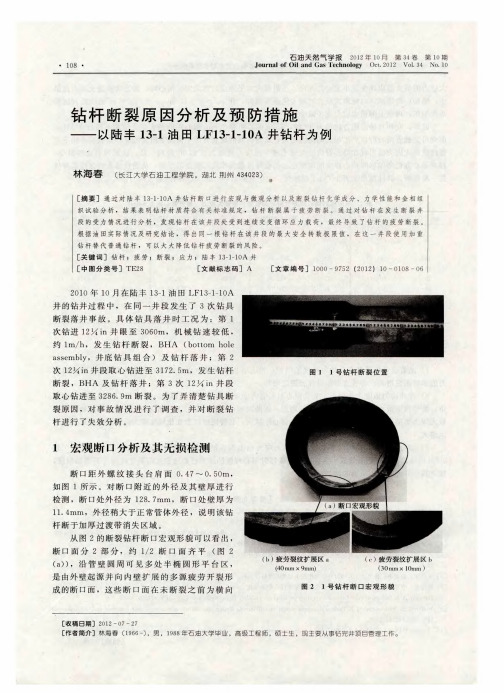
3 通过对 在 该井 中使 用 的钻具 组合 与井 眼实际 测量 轨迹 模 拟计算 发 现 ,在钻 杆易 发生 疲劳 的 7 7 ) 0 m
井段 附 近 。通 过将 普通 钻杆 更换 为 加重 钻杆 ,可 大大 延 长钻 具在 该井 段 的使用 寿命 『 。 3 ] 4 在复杂 井 况条 件下 使用 钻杆 应相 应地 增 加对 钻 杆 检验 的控 制标 准 ,通 过 缩 短 检验 周 期 、增 加 监 )
[ ] 李 鹤 林 .石 油 钻 柱 失 效 分 析 及 预 防 [ 3 M] .北 京 :石 油 工 业 出版 社 ,2 0 . 08
[ 辑] 萧 编
雨
弯 曲 应 力 ,并 长 时 间 承 受 循 环 应 力 而 导 致 钻 杆 发 生 纯 疲 劳 失 效 。
3 钻杆 在使 用过 程 中 ,由于钻 速 非常低 ,进尺 缓 慢 。 曾遇起 下 钻 遇 阻严 重 ,采取 了划 眼 和倒 划 眼 ) 的方 式通 过 ,顶 驱憋停 次 数较 多 ,这都 使得 钻杆 在 取心 过程 中承 受较 大 的拉伸 和扭 转载 荷 ,长期 遭受 多
7 建
Байду номын сангаас
议
1 在该井 造 斜点 之上 同一 位置 附 近连续 发 生钻 杆 断 裂失 效 ,说 明造 斜 点 以下 附近 位 置 井 眼可 能 存 ) 在更 大 的异 常 ,钻杆 在该 处弯 曲可 能 比现有 数 据反 映 的情况 更严 重 。 因此 建议 对造 斜 点上下 位 置进行 更 精确 的测 井 。 2 该次 钻杆 断裂 位置 位 于造斜 井段 , 由于在施 工 过程 中为 利 于早 点 偏 离 老井 眼 侧钻 出去 ,导 致 狗 ) 腿度 超过 设计 值 ,建议 在 施工 中对 于井 眼轨 迹较 复杂 的 井根据 实 际测 量轨 迹进 行钻 柱侧 向力 计算 ,并 做 相关 提示 ,以降低 由于井 眼全 角变 化率 较大 、井 段钻 杆 长期 承受 交变 应力 而导 致 的钻杆 疲劳 失效 事故 的
旋挖钻机钻杆管体开裂原因分析与解决方案

旋挖钻机钻杆管体开裂原因分析与解决方案作者:杨宏伟乔居斌来源:《海峡科技与产业》2016年第10期摘要:针对旋挖钻机钻杆使用过程中出现的管体开裂情况,综合考虑旋挖钻机作业时运行情况及钻杆材质、制造工艺等情况,查明开裂原因,并提出解决方案。
该方案切实可行,可大幅减少钻杆管体开裂情况,对提高钻杆使用寿命及施工效率具有重要意义。
关键词:旋挖钻机;钻杆;管体开裂旋挖钻机是目前基础施工中常见的钻孔灌注施工机械,图1为北京市三一重机有限公司生产的SR280R旋挖钻机,各主要部件如图1所示。
钻杆是旋挖钻机的工作装置,上端与随动架相连,下端与钻斗相连,将钻机输出的动力传递给钻斗,是钻机最重要的部件之一,提高钻杆的可靠性对提升钻机施工效率及施工质量具有重要意义[1-4]。
本文对钻杆中相对典型的管体开裂故障进行分析,并提出解决方案。
1 钻杆管体开裂情况管体开裂主要发生在机锁式钻杆的第一节第一组加压台与斜键间,既影响施工进度,也给客户造成经济损失,是钻杆作业过程中常见的及影响最大的故障之一。
图2是一起φ508-4×15m机锁杆管体开裂故障,该钻杆配备于SR280R入岩钻机,孔径1.5m,孔深27m,在使用500小时左右时第一节钻杆断裂,其余三节杆沉在孔中提不上来,严重影响施工进度。
2 钻杆管体开裂原因分析通过深入工地实地调研,并结合以往机锁式钻杆管体开裂的情况,分析总结原因如下:作用过程中强力加压,致主机前履带上翘,桅杆后仰,钻杆长时间在弯曲条件下作业,受弯矩折断。
模拟钻杆作业时各节杆的伸出顺序及状态,分析各状态时钻杆的受力情况,如图3至图5所示。
(1)如图3所示,使用第一节钻杆钻进时,各节钻杆重合在一起,抗弯性能比较强,桅杆后仰不会导致钻杆断裂。
(2)如图4所示,使用第二节钻杆最下面一组加压台钻进时,二、三、四节杆重合在一起,二杆顶端位于第一节杆中间一组传扭段。
当主机前履带翘起桅杆后仰时,第一节杆受动力头向后的力F1,其余各节杆保持竖直,对第一节杆产生力F2,两者形成力矩M,使第一节杆后仰距离x,将一杆最上端加压台与斜键间的管体扳断。
BRM-4型钻机钻杆发生断裂原因的分析及防止

设计制造
死 。这种地层往往接近终孔段 , 孔深且垂直度难以 保证 , 多呈波浪形或 “S ”形 , 而且常常因配重不 够 , 减压钻进操作难以得到保证 。钻杆在此种工况 下受力极其复杂 , 主要承受如图 2 所示的不对称交 变扭矩和轴向拉力或压力 ( 往往下部钻杆承受压 力 , 上部钻杆承受拉力 ) , 另因晃动和孔斜等引起 的侧向力作用 。由于交变扭矩比稳定扭矩对钻杆疲 劳强度的影响更大 , 所以有必要分别对钻杆在承受 非对称交变扭矩作用时的强度和承受最大冲击扭矩 作用时的静强度进行校核 , 计算如下 。 a1 钻杆在承受非对称扭矩作用下的强度计算 对钻杆疲劳强度影响最大的是变化的扭矩对钻 杆产生的交变剪应力 。为方便计算 , 暂对轴向力和 侧向力忽略不计 , 将钻杆近似看成是中心圆管受非 对称稳定交变扭矩作用 , 在钻杆中心管壁产生稳定 的非对称循环简单剪应力 , 如图 3 。 τ m= 剪应力幅 τ max - τ min = 2712MPa 2 45 号钢的剪切屈服极限 τ s = 180MPa , 对称循 环下剪应力极限 τ- 1 = 120MPa , 材料系数 ψ τ= 0, 钻杆外形系数 K τ 取 115 , 钻杆尺寸系数 ε τ 取 016 , 钻杆表面系数 β取 0165 。 τ α= 综合剪应力集中系数
017 × 7184 = 55kN・ m。
4 钻杆发生断裂损坏的原因及防止措施
通过上述计算 , 可以得出 : ① 一般工况下 , 钻 杆的抗拉强度安全系数为 414 , 这通常是钻杆强度 的设计依据 ; ② 在复杂工况下 , 遇到最大过载冲击 时钻杆的抗拉强度安全系数为 214 , 抗剪强度安全 系数为 2115 , 钻杆的强度是足够的 ; ③钻杆在承 受交变扭矩和频繁过载扭矩冲击作用下 , 按交变应 力计算 , 抗疲劳剪切安全系数仅为 1115 , 这正是 钻杆发生断裂损伤的根本原因 ; ④ 钻杆内应力非常 复杂 , 容易在钻杆法兰盘根部 、钻杆传扭筋与中心 管和法兰之间的焊缝热影响区等外形过渡处产生应 力集中 , 当峰值应力频繁作用在这些应力集中区 , 就造成了这些部位发生疲劳断裂 。钻杆的结构形式 也导致应力集中产生 , 这在其它型号的转盘式钻杆
钻具断裂的失效分析及预防

2017年09月钻具断裂的失效分析及预防张孝兵海照新陈保民(川庆钻探工程公司长庆钻井总公司,陕西西安710018)摘要:油气田勘探开发过程中钻具受力状态十分复杂,所以其失效形式也多种多样。
如过量变形、断裂、表面磨损等。
发生井下钻具断裂事故,处理费用数额大,更甚者会发生打捞失败而弃井。
通过多年井下钻具断裂事故的处理经验、案例分析及试验研究总结出,大多数的钻杆断裂事故都是由于疲劳而引起的。
关键词:失效;疲劳;过量变形;钻具断裂1钻具断裂事故发生的一般规律在钻井实践中观察到的大量钻杆断裂现象可概括为:①钻杆大多数的断裂事故发生于旋转钻进过程中或在钻进后立即提离井底的时候;②大多数断裂发生在据钻杆接头1.2米的范围内;③管体的疲劳和腐蚀疲劳断裂均发生在内加厚过渡区消失处;④在有腐蚀性的洗井液中将引起管体或接头严重坑蚀,从断裂面上看到的这些裂纹是从内表面的腐蚀斑点开始的;⑤上提遇卡而拔断钻杆,断裂位置通常发生在已经产生疲劳裂纹,但尚未发展成为断裂的部位;⑥钻杆接头螺纹的疲劳断裂多发生于内螺纹接头大端第一和第二螺纹牙根部或外螺纹接头大端第一和第二螺纹牙根部。
2钻具断裂事故中钻具的失效形式2.1钻杆管体的疲劳和腐蚀疲劳断裂钻杆发生疲劳和腐蚀疲劳断裂破坏的主要原因是由于钻杆在弯曲井眼中旋转时发生周期性交变旋转弯曲应力以及井下腐蚀介质共同作用所致。
影响钻杆疲劳和腐蚀疲劳断裂的主要因素:①钻杆材料的抗拉强度和疲劳极限的影响;②钻杆材料冲击韧性的影响;③钻杆表面质量的影响;④腐蚀环境的影响;⑤拉伸和弯曲的组合影响;⑥累计疲劳。
2.2钻杆内加厚过渡区刺穿失效事故在钻杆管端镦粗加厚工艺控制过程中,由于内加厚过渡区太短,在钻杆使用中,在该区产生严重的应力集中,进而导致腐蚀集中并形成较深的腐蚀坑。
在旋转钻井过程中,钻杆受到旋转弯曲交变载荷的作用,在腐蚀坑底产生疲劳裂纹,最终导致钻杆刺穿或断裂,这属于钻杆的腐蚀疲劳断裂。
2.3内涂层钻杆加厚过渡区刺穿失效事故(内刺穿)由于钻杆(内涂层)内加厚过渡区的形状不良,在钻杆使用时导致局部涂层脱落并产生集中腐蚀(涂层脱落处的腐蚀速率要远远高于正常的腐蚀速率),很快会产生较深的腐蚀坑。
钻杆:钻杆断裂的常见原因

钻杆:钻杆断裂的常见原因在钻井过程中,钻杆是连接钻头和钻机的重要部件。
钻杆的质量和牢固程度直接关系到钻井进度和效率。
然而,钻杆断裂是钻井作业中常见的问题,不仅会导致钻井中断,还可能造成意外事故。
本文将会介绍钻杆断裂的常见原因,以帮助读者更好地理解及预防此类问题的发生。
1. 材料问题钻杆通常由不锈钢、铁合金等优质材料所制成。
如果钻杆的材质不符合标准或者材料质量出现问题,那么钻杆就很容易出现裂纹或者断裂。
此外,由于钻杆通常处于悬挂状态,在运输、搬运和落地的过程中,如果受到撞击或者挤压等机械损伤,也会加速钻杆的疲劳破裂。
2. 钻杆疲劳通过连续地旋转和振动,钻杆会发生疲劳和龟裂现象。
尤其是在长时间的高强度钻井作业中,疲劳程度会更严重。
当钻杆内部的应力超过其承受能力时,就会出现疲劳破裂,导致钻杆断裂。
3. 断节区域设计问题钻井作业中,需要用到焊接的钻杆,若连接设计不合理或者焊接质量差,断节区域很容易出现龟裂、缺陷等缺陷,在钻井时候断裂导致难以控制、拆除。
断节区域的设计不当,比如装配了不适合的连接器,也会导致钻杆断裂。
4. 钻井参数设置问题在钻井过程中,如果钻杆没有合理的被加压或拉扯,可能会导致钻杆的轻微变形与内部的应力分布不均,从而导致疲劳破裂。
同时,如果钻井参数设置不合理,比如设置的钻头转速过快或钻压过大等等,也会导致钻杆断裂。
5. 操作方法问题如果钻杆的把持、转动或装卸不当,都会导致钻杆的损坏。
特别是在斜井或水平井中,如果钻杆撞到井筒边缘或者在管柱中折断,都属于操作不当导致的破裂。
6. 比例失衡在钻井施工中,如果使用过大的钻头,或者井深和钻头尺寸比例过于失衡,也会导致钻井作业中钻杆断裂。
比例失衡出现的最常见情况就是井深过大而使用过小的钻头,这会导致钻杆的剧烈振荡,从而导致钻杆的疲劳破裂。
总的来看,钻杆断裂往往是由材料问题、疲劳、断节区域设计问题、钻井参数设置问题、操作方法问题和比例失衡等多种因素共同作用导致的。
煤田勘探中钻杆断裂原因分析与预防措施的探讨

减小钻杆 弯曲挠度和弯 曲应力, 增 加半波 长度, 降低钻杆断裂频率 : ( 4 )针对不同岩性、 钻孔深度和钻孔直径 的要求, 合理选用钻进 参数, 防止钻 杆过载 ; ( 5 )钻 杆 要 分 级 使 用 , 不 能 新 旧混 用 。钻 杆 断 裂 总 是 在 钻 杆 最 薄弱的部位发生。因此, 钻杆连接时要尽量做到等强度, 按钻杆新 旧 程度分级, 统一调配 使用 , 不能新旧混 用。 ( 6 )钻杆在 使用时不应猛 敲、猛打,在每 回次时应对钻杆加强 检验,查找有裂 缝等不 良现象的钻杆 ,并用 新钻杆 替换 。 ( 7 )在遇到溶洞或地层坍 塌时,应及时有效地处理,防止钻杆 弯曲应力增大,增大钻杆折断的系数。 8 结 语 在勘探 区其余钻孔 的施 工中,根据地层特 点有 效地 采取 了预防 措施,舍弃 了使用时 间过长 的钻杆 ,新增 了质量 要求合格 的钻 杆, 严格按照 《 岩心钻探规程 》进行施 工,合理选择钻进参数 ,在 遇到 问题时及时有效地处理 ,使得这些钻孔较之前施 工的钻孔减少 了钻 杆断裂的发生 ,从而降低 了钻探成本,钻孔质量得到很 大的提 高。
[ 2 】 郑林. 钻杆加工工 艺探讨Ⅲ. 机械 工程师 ,2 0 0 9 . 【 3 】 刘鸿文. 材料力 学[ M] . 高等教 育出版社 ,1 9 9 7 . 作者简介 : 赵得全 ( 1 9 6 6 . 8 一 ),男 ( 汉族 ),重庆 人,毕业于陕西煤炭工业 学校 ,煤炭钻探专业 ,高级工程师 ,从事钻探现场技术管理工作 。
能够基本满足客流量相对较大 区段 的需求 , 而对于客流较小 的区段 , 做到有 限度 得维持运 营。同时采用该行车组织方法,也可 以现场抢 修人 员有足 够的时间和空间去进去抢修作业 ,从而可 以尽早得处理 完故障,恢 复正常行车 。 4 结 语 我国城市轨道交通建设 已经进入 了一个快速 的发展 阶段 ,地铁 作为人们出行交通工具中的一种 ,客流不断增长 的情况下 ,地铁设 备难免发生故障。为 了提高轨道交通运营时正线 出现道岔故障 时的 应急处理效率,对于 出现道岔故障时在行车安全风险可控范 围内, 最大的提升行车组织效率, 把设备故障对运 营服务 的影响 降至最低 。 参考文献 : …毛 保华.城市轨道 交通运营管理【 M】 . 北京 :人 民交通 出版社, 2 0 0 6 . 【 2 】 何 宗华, 汪松 滋, 何其 光. 城 市轨 道 交通运营组 织【 M】 . 北 京: 中国建筑
煤矿用钻杆断裂原因及解决措施浅析

煤矿用钻杆断裂原因及解决措施浅析【摘要】安全一直是煤矿井下施工的重中之重,在煤矿井下瓦斯抽采、煤矿探放水钻孔等施工过程中,钻杆是钻孔装备的重要组成部分,钻杆在钻进过程中的受力状态复杂,实际工况要求钻杆具备良好的性能。
在实际的煤矿施工中如果钻杆断裂,必定会对造成安全事故,本文分析了煤矿钻孔用钻杆材质、加工工艺与质量、现场使用时钻进工艺等产生钻杆断裂的原因,并提出了如何提高并稳定钻杆质量、减少防止钻杆施工过程中发生断裂事故的措施。
【关键词】钻杆煤矿坑道钻机钻杆断裂原因分析解决措施在煤矿井下瓦斯抽采、探放水的钻孔施工中,经常使用煤矿坑道钻机,钻杆作为钻机的重要组成部分,在钻孔施工现场大量使用。
实际钻进过程中,钻杆处于孔内复杂的工作状态,通常承受拉、压、弯、剪扭、液力、振动等交变载荷,并伴随着液体的冲刷,钻进时经常出现钻杆断裂现象。
钻杆断裂不仅影响正常生产,而且还因打捞困难使事故恶化,造成人力、财力的损失,给煤矿的施工安全带来很大影响。
因此,正确客观分析钻杆的断裂原因,提前采取有效预防措施,提高控制钻杆质量,降低钻孔事故率,有重要的意义。
1 煤矿勘探用全液压动力头式钻机介绍分体式全液压动力头式煤矿坑道钻机现已成为国内普遍生产的一种矿用回转式钻机。
在煤矿井下钻孔施工中被广泛应用,其结构分主机、泵站、操纵台三大部分,适用于回转和冲击回转给进,主要用于煤矿瓦斯抽采、煤矿井下探放水、探地质构造、探煤层厚度、煤层注浆注水及管棚等各类工程钻孔的施工。
其解体性好,搬迁方便,机械式拧卸钻具,卡盘、夹持器与油缸之间,回转器与夹持器之间可联动操作,自动化程度高,工作效率高,操作简便,工人劳动强度小;采用双泵系统,回转参数与给进参数独立调节,提高了钻机对各种不同钻机工艺的适应能力,用支撑油缸调整机身倾角方便省力,回转器采用通孔结构,钻杆长度不受给进行程的限制,操作台集中操作,人员可远离孔口,有利于人身安全。
2 煤矿用钻杆介绍在煤矿瓦斯抽放、对煤层注水等钻孔施工过程中,钻杆是必不可少的设备,作为钻机的配套设备,钻杆质量的好坏就直接影响施工的安全与进度,然而由于煤矿中钻杆需要承受的压力、材质、以及加工工艺的不同,使得钻杆存在一些质量的问题,这必将影响煤矿施工的进度。
钻杆管体开裂失效原因分析

Ab s t r a c t : Se ve r a l be nd i ng a n d f r a c t u r e a c c i d e nt o f d r i l l pi p e t o o k pl a c e i n o ne o i l f i e l d.At t he s a me t i m e, c r a c k W3 S f ou nd i n t he o t he r dr i l l pi p e du r i ng i ns p e c t i o n .I n o r de r t o kn o w t he c a u s e o f c r a c k o f d r i l l pi p e, a n i nv e s t i g a t i o n o n t he a c c i d e nt wa s i n t r o du c e d . Two c r a c ki n g p i pe s a mpl e s we r e a na l y z e d.Fr a c t ur e mo r pho l o gy, g e o me t r i c p a r a me t e r s , ph ys i c a l a nd c he mi c a l pr o pe r t i e s, mi —
钻杆 开裂机 理 为腐蚀 疲 劳, 建议加 强钻 杆 管理 , 采 用 内涂 层钻杆 。
关键 词 : 钻杆; 开裂 ; 腐 蚀 疲 劳 中 图分 类 号 : TE 9 2 1 . 1 文献标 识码 : A d o i : l 0 . 3 9 6 9 / j . i s s n . i 0 0 1 — 3 4 8 2 . 2 0 1 6 . O 1 . 0 0 8
47-钻杆接头断裂失效原因分析与预防

D r i l l P i e S u b F r a c t u r e R e a s o n A n a l s i s a n d P r e v e n t i o n p y
, , , , KONG X u e L I U J i n s a n MA R e n YU X i a o e i YU X i a o l o n u n i -y - -q -w - g
b 微观形貌图像2处能谱
a 微观形貌图像1处能谱
c 断口微观形貌图像 图 2 断 裂 接 头 断 口处 E D S能 谱 分 析
·4 2·
0 1 2年8月 石 油 矿 场 机 械 2
[ ]
2. 4 金相组 织 2-4 《 石油 钻 杆 接 头 》 中要求强度( 屈服强度 5 2 9 0—2 0 0 0 、 ) , 为8 抗拉强度为9 导致钻杆接头 2 7 MP a 6 5 MP a 断裂。 在断裂钻杆接头断口 处 取 样, 然后经过1 0 0# 、 2 0 0# 、 4 0 0# 、 6 0 0# 、 8 0 0# 、 1 0 0 0# 砂 纸 打 磨 后 在 抛 光机上抛光, 用 4% 的 硝酸酒 精 腐 蚀 , 在蔡式显微镜 ) 。 下 观察 其 金 相 组 织 和 夹 杂 物 ( 如图 3 由图 3 可 知, 断裂钻杆接头的金相组织为回火 索氏体+铁素体+ 上 贝 氏 体 混 合 组 织; 内部夹杂物 / 有 2 类, 分别为 C 1. 5和 D 1. 5。 根 据 国 标 G B T 《 钢 中 非 金属 夹 杂 物 测 定 标准 评 级 图 显 1 0 5 6 1—2 0 0 5 , 微 检 验法 》 非 金属 夹 杂 物 为 硅 酸盐 类 和环 状 氧 化 物 类, 级 别i =1. 5。
地质钻杆镦头过程中裂纹的成因及解决对策

地质钻杆镦头过程中裂纹的成因及解决对策摘要:地质钻杆是采用地质合金钢管,经摩擦焊接工艺设计和生产出的地质钻探工具,其在地质勘探中发挥着重要的作用。
为了保证钻杆的强度,一般在对其进行加工时,都会在两头进行镦头加厚处理,但是在镦头过程中,许多钻杆出现了裂纹,影响了其使用性能和安全。
文章结合相应的方法,对地质钻杆镦头过程中裂纹产生的原因进行了分析,并提出了合理有效的解决对策。
关键词:地质钻杆;镦头;裂纹成因;解决对策随着社会经济的发展,地质勘探工作发挥着越来越重要的作用,对于地质勘探的设备和器具也提出了更高的要求。
作为地质勘探中应用十分广泛的地质钻杆,其质量也受到了相关人员的充分重视。
钻杆在钻柱系统中起着传递动力、输送泥浆的作用,因此必须具备良好的抗冲击性能和抗扭性能,一旦钻杆出现故障,必然会影响地质勘察工作的有效进行,甚至造成巨大的经济损失和人员伤亡。
因此,做好地质钻杆的裂纹分析,确保钻杆的质量,是十分重要的。
1 地质钻杆裂纹的产生在对地质钻杆进行生产时,首先要结合地质勘探的实际需求以及客户的而要求,截取适当长度的无缝钢管,形成基础杆体,然后,采用中频炉,对钢管的两端进行加热,并利用镦压机,结合热挤压的方法,将一些钢材添加到钢管两端,对其镦头进行加厚处理。
这样可以为钻杆两头后续螺纹的加工提供良好的基础条件。
但是在对钻杆进行镦头加厚处理后,后续加工过程中去除表面的氧化层,发现钻杆存在裂纹现象,而且裂纹集中分布在钻杆的变径处,大体上成轴向分布,严重影响了钻杆的强度和使用安全,需要引起相关技术人员的重视,对裂纹产生的原因进行分析,并对其进行解决。
2 地质钻杆裂纹产生的原因分析2.1 分析方法①要针对发生裂纹的钻杆进行相应的化学成分检验。
在实验室环境下,取钻杆样品,利用ARL 23460直读光谱仪,对钻杆的材质进行分析,其分析结果见表1。
从表中可以看出,该钻杆管材的材质和材料成分可以满足相应的标准和规范,并不存在问题,因此裂纹并不是由于钢管材质较差引起的。
钻杆断裂常见的原因

钻杆断裂常见的原因,详见如下几点
钻杆是一种尾部带有缧纹的钢管,用于连接钻机地表设备和位于钻井底端钻磨设备或底孔装置。
钻杆的用途是将钻探泥浆运送到钻头,并与钻头一起提高、降低或旋转底孔装置。
钻杆在转动过程中,必须能够承受较大的扭矩、扭曲、弯曲和振动。
在钻探过程中,钻杆可以多次使用。
关于钻杆断裂常见的原因,详见如下几点:
1、非开挖钻杆使用时间太长,表面损伤较多,接近或超出疲劳寿命。
及时更换新钻杆。
2、钻杆杆体材质、厚度不符合就技术规范要求。
3、扩孔或长距离打导向孔时,钻头突然碰到硬物产生强大的冲击力。
造成扭矩突然增大,引起非开挖钻杆折断或扭断。
操作手在操作非开挖钻机时应合理控制旋转速度和推进力,避免该类情况发生,钻进,加压,以适宜的旋转速度正转钻进。
4、施工孔的曲率半径超过钻杆的最小曲率半径的参数控制施工孔的最小曲率半径。
5、钻杆杆体表面划伤严重避免使用有伤痕的钻杆。
6、钻机的扭矩大于钻杆倾角承受的扭矩。
为钻机配置合适的钻杆。
7、对孔位。
不形成对钻杆的操作,但要注意不要""别""钻杆。
8、放钻。
在钻杆和钻具重力作用下,克服孔壁磨擦力和泥浆浮力,实现钻杆伸展的过程叫放钻。
9、正确的放钻顺序为:外杆下放到位,相邻内杆才开始从外杆内伸出,由外到内,逐个完成。
煤矿用钻杆发生断裂的原因分析及预防措施

煤矿用钻杆发生断裂的原因分析及预防措施文章主要从金相组织角度出发,对我司外销产品进行成分化验、力学性能检测、金相分析等检测方法,最终确定带状组织在成品钢管热处理时如果消除不完全,就会导致钢管在不同方向上承受力的程度不同,即力学性能在不同方向上呈现异性,从而降低了钻杆的强度,导致过早的出现断裂。
标签:钻杆;断裂;带状组织1 前言我司供某机电公司的φ42×5mm规格、45钢钻杆用无缝钢管在组装焊接成钻杆后发往煤矿后在使用过程中钢管的中间部位发生断裂。
钢管焊接的单元长度为590mm,钻杆的总长度在150-200米间。
2 断口分析从整个断裂面观察,断口形貌粗糙,整个断面呈现由上部至周围放射性的河流花样,且断面处钢管呈现椭圆形,管材外壁有氧化脱皮现象,属于典型的塑性断裂,且裂纹源应位于钢管的上部。
3 化学成分检测在距断裂面10mm处取样进行化学成份检测,结果为碳:0.45%;硅:0.22%;硫:0.011%;磷:0.009%;锰:0.59%含量均符合GB/T 8162-2008中45钢碳:0.42-0.50%;硅:0.17-0.37%;硫:≤0.015%;磷:≤0.025;锰:0.50-0.80%的标准要求。
4 力学性能检测距断裂面20mm至260mm处,在断裂钢管上截取拉伸试样,结果为屈服强度(Rel):400MPa、380MPa;抗拉强度(Rm):640MPa、650MPa;断后伸长率(A):21%、22%。
均符合GB/T 8162-2008中45钢屈服强度≥335MPa,抗拉强度≥590MPa,断后伸长率≥14%,的标准要求。
5 非金属夹杂物检测在距断裂面10mm处取样进行非金属夹杂物检测,结果为硫化物类夹杂0.5级、氧化铝类夹杂1.5级、硫酸盐类夹杂0.5级、球状氧化物类夹杂2.0级、单颗粒球状类夹杂1.0级。
按GB8162-2008结构用无缝钢管标准要求,无需对钢管材质进行非金属夹杂物的检测,本文进行该项检测的目的是确定非金属夹杂物因素对钢管断裂所带来的影响程度的大小。
钻杆失效原因分析

钻杆失效原因分析2008年09月28日星期日钻杆失效原因分析在钻井过程中,钻杆在任何部位失效都会造成严重的后果,甚至使井报废。
我国各油田每年发生钻杆事故约五六百起,经济损失巨大,每年进口各种规格的钻杆就要耗用数亿元人民币的外汇。
随着浅层资源的不断枯竭,今后越来越多的钻深井、超深井,钻杆的安全可靠性就成为一个十分突出的问题。
钻杆失效一般表现为本体断裂和刺漏,钻杆螺纹处失效等。
原因大致是由以下一些因素引起的:钻进时钻杆的基本力学工况,钻具的组合及钻井工艺,井径规则性,偏磨,螺纹密封脂,钻井液,钻杆结构和材料,地层因素,井内腐蚀介质等,以上因素交互作用的结果导致钻杆失效。
钻杆的基本力学工况钻杆在内外充满钻井液的狭长井眼里工作,通常承受压、弯、扭、液力等载荷。
如果钻杆所受应力小于每平方米206.8牛顿时,钻杆虽经过无数次的弯曲,也不会产生疲劳裂纹。
钻井时钻杆承受弯曲、扭转和拉伸应力组成的复合应力很大,特别是在大位移定向井及水平井中扭矩极大,钻杆在远远小于100万次弯曲次数时便产生疲劳微裂纹;微裂纹产生后便不断扩大延伸,此时如果具有腐蚀作用的高压钻井液进入微裂纹中,就会加速裂纹扩展,最终导致钻井液刺穿钻杆的失效事故。
刺穿发展的结果,使钻杆有效断面不断缩小,刺孔加裂纹的总长度超过其临界裂纹尺寸时,即发生断裂。
除旋转向下的运动,同时还有钻杆的各种振动和涡动。
钻具组合及钻井工艺钻杆作为一个旋转的细长弹性杆件,有其固有振动频率,钻具的组合决定了此固有频率。
钻杆旋转时还会产生纵向、横向和扭转3种形式的振动,当它们的频率与固有频率相吻合时则产生共振。
共振的结果会在原来钻杆疲劳应力的基础上附加一个额外的疲劳应力,加速钻杆的失效。
采用长效螺杆钻杆替代转盘钻定向井、水平井的钻井工艺可以减少钻杆的旋转弯曲疲劳程度。
如牙轮钻头轴产生的纵向振动频率与钻头-钻柱系统的固有自振频率相同时会出现共振,使钻头的振幅增大,产生极大的冲击载荷,加剧钻杆疲劳。
钻具失效原因分析1

【技术论坛】钻具失效分析及预防钻井过程中,钻具除了受到拉力外,还要受到交替变化的弯曲应力,由于地层变化、转盘旋转等引起的横向振动和扭转振动的周期变化的干扰力,接触的介质是具有一定腐蚀性的钻井液,这些因素加速了钻具的失效。
钻具失效除了造成钻具损失外,打捞作业和停止钻进损失更大,甚至会造成进尺报废。
人们着手分析钻具失效问题,加强对钻具的使用、检测与管理,以减轻这一问题的影响。
钻杆失效类型主要有过量变形、刺穿或断裂及表面损伤。
过量变形是由于工作应力超过材料屈服极限引起;刺穿或断裂在钻柱失效事故中所占的比例较大,主要由于应力腐蚀、疲劳和腐蚀疲劳等原因造成。
表面损伤主要有腐蚀、磨损和机械损伤。
经中石油管材研究中心调查发现,70%的事故是由钻杆内加厚过渡区部位刺穿或断裂引起的。
从表面看,钻杆内加厚过渡区部位的失效有3种表现形式,即裂纹、刺穿和断裂,但实质上都是同一种失效。
钻杆被刺穿是因为泥浆在高压作用下穿过裂纹的缝隙,由于泥浆穿过这种缝隙时的高速流动,进一步扩大了该裂纹,并使之变成孔洞。
因此,刺穿的先决条件是已存在裂纹,多处刺穿孔洞连成一片,大幅度降低了钻杆的承载能力而导致断裂。
钻杆外壁的腐蚀较轻并且均匀,而钻杆内壁表面的腐蚀很不均匀,内加厚过渡区与管体交界处的腐蚀较严重,有许多点蚀坑,而裂纹正起源于这些点蚀坑底部。
有内涂层的钻具内壁腐蚀会减轻很多,但内加厚过渡区与管体交界处的内涂层易被冲蚀。
钻杆内壁的腐蚀以点蚀为主,钻杆出井时其内壁不可避免地残留有泥浆或井下腐蚀介质,如果在存放前未及时冲洗,会使钻杆内涂层剥落的部位产生点蚀,因腐蚀环境是开路系统,能充分吸收空气中的氧气而使腐蚀加速。
在以后的钻井过程中,在点蚀坑底部这个应力集中的地方产生初始裂纹。
钻杆管体腐蚀疲劳裂纹均起源于内壁的点蚀坑,其破坏过程:点蚀坑产生——裂纹萌生——扩展——刺穿。
应力腐蚀破裂是金属在拉应力(外加应力或残留应力)和腐蚀介质的共同作用下引起的一种破坏形式(如氢脆)。
- 1、下载文档前请自行甄别文档内容的完整性,平台不提供额外的编辑、内容补充、找答案等附加服务。
- 2、"仅部分预览"的文档,不可在线预览部分如存在完整性等问题,可反馈申请退款(可完整预览的文档不适用该条件!)。
- 3、如文档侵犯您的权益,请联系客服反馈,我们会尽快为您处理(人工客服工作时间:9:00-18:30)。
关键 词 : 钻杆; 开裂 ; 腐 蚀 疲 劳 中 图分 类 号 : TE 9 2 1 . 1 文献标 识码 : A d o i : l 0 . 3 9 6 9 / j . i s s n . i 0 0 1 — 3 4 8 2 . 2 0 1 6 . O 1 . 0 0 8
位置位 于钻 杆端 部 2 3 0  ̄4 0 0 0 mm 处 , 同 时在 施 工
过 程 中检 查 发 现 1 O支 钻 杆 存 在 裂 纹 。设 计 井 深
2 4 2 0 m, 井段 7 0 0  ̄2 4 2 0 m 为高分 子聚 合 物泥 浆 , 主要 性能 指标 为 : 密度 1 . 0 5 ~1 . 1 2 g / c m。 , 漏 斗 黏
Ab s t r a c t : Se ve r a l be nd i ng a n d f r a c t u r e a c c i d e nt o f d r i l l pi p e t o o k pl a c e i n o ne o i l f i e l d.At t he s a me t i m e, c r a c k W3 S f ou nd i n t he o t he r dr i l l pi p e du r i ng i ns p e c t i o n .I n o r de r t o kn o w t he c a u s e o f c r a c k o f d r i l l pi p e, a n i nv e s t i g a t i o n o n t he a c c i d e nt wa s i n t r o du c e d . Two c r a c ki n g p i pe s a mpl e s we r e a na l y z e d.Fr a c t ur e mo r pho l o gy, g e o me t r i c p a r a me t e r s , ph ys i c a l a nd c he mi c a l pr o pe r t i e s, mi —
某 井施 工 中 , 从井 深 2 0 5 5 ~2 4 0 0 m 作业 中连 续发生 o 1 2 7 . O 0 mm 钻 杆 断 裂 事 故 6次 , 钻 杆 断 裂
度 1 7 ~2 1 S , P H值 7 ~9 , 含砂量小于 1 , 固 相 含
量 7 ~1 O , 失水量 1 0 ~1 5 mL / 3 0 mi n 。断 裂 开
COm 。
2 0 1 6年 第 4 5 卷 第 l期 第 3 6页 文章编 号 : 1 O O 1 — 3 4 8 2 ( 2 0 1 6 ) O 1 — 0 0 3 6 - 0 5
0I L FI ELD
石 油 矿 场 机 械 E QUI P ME NT
水 平井 求产 螺杆 泵排 液 杆 柱 力 学分 析 及 防偏 磨 技 术
ma i n c au s e ቤተ መጻሕፍቲ ባይዱ f c r a c k i ng i s c o r r os i o n f a t i g ue .I n o r de r t o p r e v e nt t he r e c u r r e nc e of t he a c c i de nt i n
t he f u t u r e, i t wa s s u g ge s t e d t h a t i nt e r n a l c o a t i n g d r i l l p i pe s ha l l be us e d i n t hi s a r e a . Ke y wo r d s: d r i l l i ng pi p e; c r a c ki ng; c o r r os i o n f a t i gu e
2 0 1 6年 第 4 5卷
石 油 矿 场 机 械
OI L FI E LD E QUI P ME NT 2 0 1 6, 4 5 ( 1 ) : 3 2 — 3 6
第 1期 第 3 2页
文章编 号 : 1 0 0 1 — 3 4 8 2 ( 2 0 1 6 ) O 1 — 0 0 3 2 — 0 5
(1 . Xi ’ an Se r v St r e s s Engi ne e r i n g Te c h no l o gy Se r vi c e Co., Lt d., Xi ’ a n 71 0 07 5, Ch i na;
2. X i di an Un i v e r s i t y, Xi an 71 0 07 5, Chi na;
-
4 -”- 4 -・ . -1 -一—卜 ”- 4-“- 1 -” -4 - “- - 卜 ”- 4--— + -” —卜 一- 卜 “— - 卜 ”— 卜”- - 卜 “— +- ”- - 卜
大, 促进 疲劳腐 蚀 O 的形成 和扩 展 , 更 容 易 产生 应
力集 中开裂 。
[ 2 ] 张毅 , 赵鹏. O 1 2 7 I T I I  ̄×9 . 9 mm I E U S - I 3 5 钻 杆 腐 蚀 失 效分析[ J ] .钢管 , 2 0 0 3 ( 4 ) : 1 0 — 1 6 . E 3 1 吕拴 录 , 骆发前 , 周杰 , 等 钻 杆 接 头 纵 向裂 纹 原 因 分
钻 杆 管体 开裂 失 效原 因分 析
姬 丙 寅 , 史 学芳 。 , 史 交 齐 , 任 锐 。 , 李 敏。 , 梁 裕 如
( 1 . 西安三维应力工程技术有限公司 , 西安 7 1 0 0 7 5 ; 2 . 西 安 电子 科 技 大 学 , 西安 8 4 1 6 0 0 ; 3 . 胜 利 油 田高 原 石 油 装 备 有 限 责 任 公 司 , 山东 东 营 2 5 7 0 9 1 ; 4 . 陕西延长石油( 集 团) 有 限 责 任公 司 研 究 院 , 西安 7 1 0 0 7 5 )
摘要 : 某 井施 工 中, 连 续发 生钻杆 断裂 事故 , 检 查发 现 其他 钻 杆也 存 在 裂 纹。对 钻杆 开裂 事故 进 行
了深入调 查研 究 , 分析 了开裂钻杆‘ 样品, 对 断 口形 貌 、 几何 参 数 、 理化性能、 金 相 组 织和 腐 蚀产 物 能
谱 分析 等进 行 了试验 分析 。结果表 明 : 钻 杆 的 理化 性 能均 满足 AP I S P E C 5 D P要 求及 用 户要 求 ,
王金东 , 张 帆, 高一 淇 , 丛 蕊
( 东北石油大学 机械科学与工程学院 , 黑龙江 大庆 1 6 3 3 1 8 )
摘要 : 在 油 田水 平井 求产过 程 中, 螺杆 泵排液 杆柱 因受其 运动特 性及 井 内环境 的影响极 易发 生偏磨
现 象 。为 有效预 防 因螺杆 泵杆柱偏 磨 引起 的井 下事故 和 经济损 失 , 对 水 平 井求 产过 程 中的螺杆 泵
裂形 貌 如 图 1 , 断裂 钻 杆 的 断 口位 置 和 开裂 钻 杆 的
裂 纹位 置与管 体轴 向垂 直 , 断裂 或 裂 纹 在管 体 位 置 呈 分散分 布 。
收 稿 日期 : 2 0 1 5 — 0 7 — 1 9
作者简介 : 姬丙 寅 ( 1 9 8 3 一 ) , 男, 河 南 许 昌人 , 工程师 , 硕士, 主 要从事 油井 管评 价试 验研 究 , E - ma i l : j i b i n g y i n 2 0 0 5 @1 2 6
c r o s t r u c t ur e a n d c or r o s i on pr o du c t s we r e a na l y z e d . The t e s t r e s u l t s s ho w t ha t , t he p hy s i c o c he mi — c a l pr o p e r t i e s o f c a s i n g c o u pl i n g me t e d A PI S PEC 5 DP r e q ui r e me nt s a nd u s e r r e qu i r e me n t s .Th e
起失效 发生 。
Fr a c t u r e An a l y s i s o f Dr i l l i n g Pi p e
J I Bi n g y i n , SHI Xu e f a n g , S HI J i a o q i , REN Ru i 。 , LI Mi n g 。 , L I ANG Yu r u
析[ J ] .机 械 工程 材 料 , 2 0 0 6 ( 4 ) ; 9 5 — 9 7 .
综上所述 , 实 际使用 中由于存在严 重的腐蚀介
质, 在 停止钻 井作 业 期 间这 些 腐 蚀物 质 继 续 残 留 附
着于钻 杆 内壁处 , 并 与外 露 于 空 气介 质 共 同作用 产 生严重 的钻 杆腐蚀 , 钻杆 的腐 蚀面 不断扩 大 , 在后期 的作业 中由于应 力集 中的存 在 , 腐 蚀坑 开裂扩 展 , 引
3 .S h e n gl i Oi l f i e l d Hi g h l a n d Pe t r o l e u m Eq u i p me n t Co . 。 Lt d ., Do n g y i n g 2 5 7 0 9 1 , Ch i n a 4 .Re s e a r c h I n s t i t u t e o f Y a n c h a n g Pe t r o l e u m ( Gr o u p)Co . , Lt d. , Xi ’ a n 7 1 0 0 7 5, C h i n a )
排 液杆柱 进行 了力学分析 。根据 力 学分析 建立 了排 液杆 柱有 限 元 分析模 型 , 提 出 了螺 杆 泵杆 柱 防