公司生产车间工艺布局优化方案
工艺布局规划实施方案

工艺布局规划实施方案一、前言工艺布局规划是指根据生产工艺流程和生产设备的布局要求,合理规划车间内各种生产设备、工作台、通道、材料存储区等的位置,以实现生产流程的顺畅、生产效率的提高和生产安全的保障。
本文将就工艺布局规划的实施方案进行详细阐述。
二、工艺布局规划的目标1. 提高生产效率:通过合理的工艺布局规划,减少生产过程中的物料搬运、人员走动等不必要的时间浪费,提高生产效率。
2. 优化生产流程:通过工艺布局规划,使生产流程更加合理、紧凑,减少生产过程中的交叉干扰,提高生产质量。
3. 提高生产安全:合理的工艺布局规划可以减少设备之间的干扰,减少事故发生的可能性,提高生产安全性。
4. 提高车间利用率:通过合理的工艺布局规划,最大限度地提高车间空间的利用率,减少不必要的空间浪费。
三、工艺布局规划的实施步骤1. 调研分析:首先需要对生产工艺流程进行调研分析,了解各个生产环节的工艺要求、设备需求、人员流动等情况。
2. 制定布局方案:在调研分析的基础上,制定初步的工艺布局方案,包括设备的摆放位置、工作台的设置、通道的规划等。
3. 评审修改:将初步的布局方案提交给相关部门进行评审,根据评审意见进行修改和完善。
4. 实施调整:根据最终确定的工艺布局方案,进行实施调整,包括设备的搬迁、工作台的设置、通道的划定等。
5. 完善改进:在实施调整后,需要对工艺布局方案进行完善改进,包括人员的培训、设备的维护等。
四、工艺布局规划的实施要点1. 合理规划通道:通道的设置要合理,保证设备之间、工作台之间的通道畅通无阻,方便物料的运输和人员的流动。
2. 设备布局紧凑:设备的布局要紧凑,减少设备之间的距离,方便生产过程中的物料传递和操作。
3. 安全考虑:在工艺布局规划中要充分考虑安全因素,避免设备之间的干扰,设置安全通道和安全防护设施。
4. 灵活调整:工艺布局规划要考虑到生产过程中可能的调整和改进,保证布局方案的灵活性和可调性。
五、工艺布局规划的实施效果1. 生产效率提高:通过工艺布局规划的实施,生产效率得到显著提高,生产过程更加顺畅。
工艺布局优化可行性分析

工艺布局优化可行性分析引言工艺布局是企业生产过程中非常重要的组成部分,对产品质量、生产效率和成本控制起着关键作用。
因此,对工艺布局进行优化是提高企业竞争力的关键环节。
本文将从可行性的角度出发,对工艺布局优化进行分析和探讨。
优化目标工艺布局优化的目标是使生产设施的布置尽可能合理,以提高生产效率和质量。
具体而言,优化工艺布局应追求以下目标:1. 减少物料和人员的运输距离,提高物流效率。
2. 缩短生产周期,提高交付速度。
3. 最大限度地利用生产空间,提高生产效率。
4. 减少资源浪费,降低生产成本。
5. 改善工作环境,提高员工满意度和生产效率。
可行性分析在进行工艺布局优化前,需要进行可行性分析,评估各项改变的可行性和可能的成本效益。
1. 数据收集首先,需要收集与工艺布局相关的数据,包括生产设施的平面布置图、物料流程图、生产数据等。
这些数据将用于分析和优化工艺布局。
2. 现状评估对现有工艺布局进行评估,分析其存在的问题和改进空间。
这包括但不限于物料流程瓶颈、生产设施利用率、人员工作效率等方面的评估。
3. 优化方案制定根据现状评估的结果,制定合理的优化方案。
优化方案应考虑到物料流程的最优化、设备布局的合理性、人员工作效率的提高等因素。
4. 评估可行性对于制定的优化方案,进行可行性评估。
这包括技术可行性、经济可行性和操作可行性的评估。
- 技术可行性评估:评估优化方案是否符合现有技术水平,是否能够实施和操作。
- 经济可行性评估:评估优化方案的经济效益,包括成本节约、生产效率提升等。
- 操作可行性评估:评估优化方案的操作难度和员工适应性,包括对现有员工技能的要求和培训成本。
5. 风险评估对于优化方案可能面临的风险进行评估,包括技术风险、经济风险和人力资源风险等。
风险评估将帮助企业更好地了解潜在的风险和挑战,并制定相应的风险应对策略。
6. 方案实施最后,根据可行性评估和风险评估的结果,选择最佳的优化方案,并进行实施。
公司生产车间布局优化实施方案
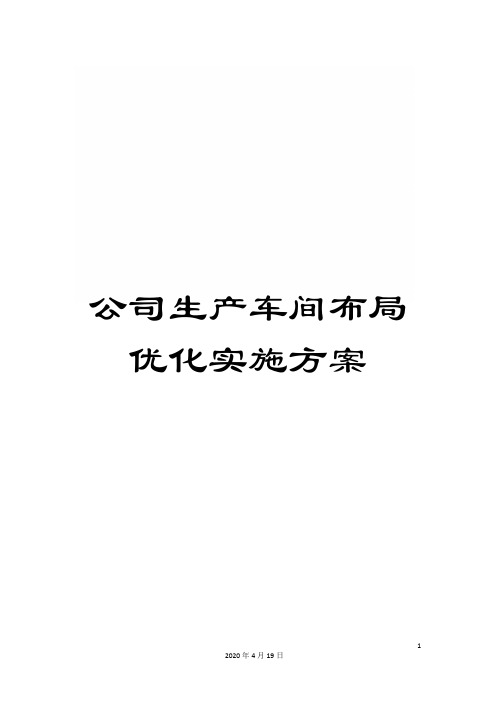
公司生产车间布局优化实施方案公司生产资源配置调整方案随着公司两大战略的实施,公司的装备、产品的质量与车间的布局,已远远满足不了公司发展的需要,为改变现状,经公司研究决定:购置生产装备、调整现有的生产布局。
布局调整后,新的人力资源整合如下:胶业公司更名为胶业营销公司,营销总经理:李永亭分厂厂长:唐正茂副厂长兼生产部部长:史胜武橡胶生产车间主任:王振华为保证上述任务顺利及时完成,特成立领导小组,具体组成如下:组长:张总(张云龙)副组长:韩总(韩卿旺)组员:唐正茂、刘洪强、张永杰、徐明文、赵雷、张仁君、史胜武具体方案为:1.购置生产装备,具体明细见下表:2.生产布局调整,2.1分厂西侧两跨车间为铆焊装配车间,北侧南跨车间为原材料存放、下料区域,北侧北跨车间为机加工车间。
现胶业公司轨道西侧整体搬迁到分厂;2.2 对湿法橡胶车间加东西隔断,电力车间整体搬迁至隔断北侧;2.3 木工房周边的设备搬迁到现胶业车间北侧指定区域;2.4 胶业车间腾出的区域:2.4.1 南侧自东到西依次为型材及下料区;2.4.2 中间自东到西依次为板材及下料区;2.4.3北侧自东到西依次为机加工半成品库、小件发货区;2.5 老药厂折掉,改造为喷砂、喷漆车间;2.6 装配车间与胶业车间中间的露天场地现有材料及设备分类整理清空转运至分厂后,安装大型起重设备(原起重设备保留);2.6.1 轨道以东,存放大型管材型材,轨道以西,为成品存放区;2.6.2 出厂时需要安装的衬板存放在原地,出厂时不需要装的衬板,存放在分厂;2.6.3 现车间内物流办公室腾出给仓库做办公室,物流办公室搬迁至木工房小房间内;2.7 现有的机加工车间主通道以西为大型铸件毛坯、半成品及成品存放区;2.8 六米五立车对面(通道以东)安装大型卷板机;2.9 筒体机床东面,安装自动焊机,原有的自动焊机调整至分厂;3.负责人、具体负责内容及时限要求见下表:负责人、实施内容及日期安排文档仅供参考,不当之处,请联系改正。
车间改造方案
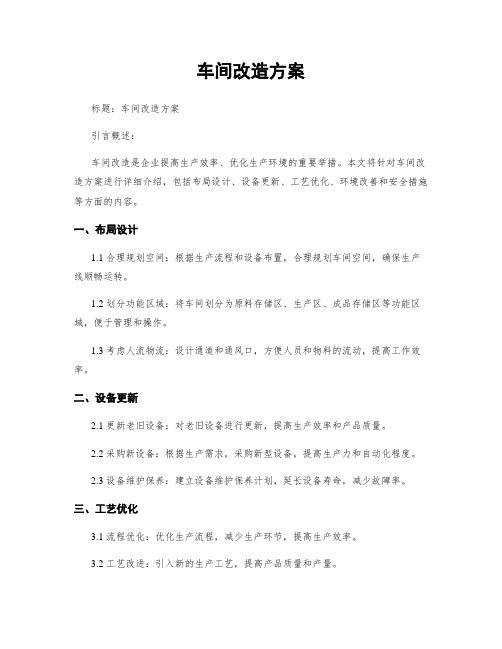
车间改造方案标题:车间改造方案引言概述:车间改造是企业提高生产效率、优化生产环境的重要举措。
本文将针对车间改造方案进行详细介绍,包括布局设计、设备更新、工艺优化、环境改善和安全措施等方面的内容。
一、布局设计1.1 合理规划空间:根据生产流程和设备布置,合理规划车间空间,确保生产线顺畅运转。
1.2 划分功能区域:将车间划分为原料存储区、生产区、成品存储区等功能区域,便于管理和操作。
1.3 考虑人流物流:设计通道和通风口,方便人员和物料的流动,提高工作效率。
二、设备更新2.1 更新老旧设备:对老旧设备进行更新,提高生产效率和产品质量。
2.2 采购新设备:根据生产需求,采购新型设备,提高生产力和自动化程度。
2.3 设备维护保养:建立设备维护保养计划,延长设备寿命,减少故障率。
三、工艺优化3.1 流程优化:优化生产流程,减少生产环节,提高生产效率。
3.2 工艺改进:引入新的生产工艺,提高产品质量和产量。
3.3 质量控制:建立完善的质量控制体系,确保产品符合标准。
四、环境改善4.1 空气净化:安装空气净化设备,减少粉尘和异味,改善工作环境。
4.2 采光通风:增加车间采光和通风设施,提高员工工作舒适度。
4.3 噪音控制:采取措施减少生产噪音,保护员工听力健康。
五、安全措施5.1 安全培训:定期进行安全培训,提高员工安全意识和应急处理能力。
5.2 安全防护:安装安全防护设施,保障员工人身安全。
5.3 安全检查:定期进行安全检查,发现隐患及时整改,确保生产安全。
结论:车间改造是企业提高生产效率、优化生产环境的重要手段。
通过合理的布局设计、设备更新、工艺优化、环境改善和安全措施,可以提高生产效率,改善工作环境,保障员工安全,实现企业可持续发展。
企业应根据实际情况,制定适合自身的车间改造方案,不断改进和完善。
公司生产车间工艺布局优化方案

【最新资料,Word版,可自由编辑!】目录摘要.................................................................................................. 错误!未定义书签。
Abstract ........................................................................................... 错误!未定义书签。
第一章绪论. (4)1.1 研究的背景及意义 (4)1.2 国内外研究综述 (5)1.2.1 国外研究现状 (5)1.2.2 国内研究现状 (6)1.3 研究内容及研究思路 (7)1.4 文章拟创新点 (8)第二章相关理论概述 (9)2.1 生产物流及优化 (9)2.1.1 生产物流的概念 (10)2.1.2 生产物流的基本特征 (10)2.1.3 影响生产物流的主要因素 (12)2.2 生产车间工艺布局的内容及要求 (12)2.2.1 生产车间工艺布局的内容 (12)2.2.2 车间设备配置的要求 (16)2.2.3 生产现场管理的要求 (18)2.2.4 生产日常管理的要求 (19)第三章 XX公司生产车间工艺布局现状分析 (22)3.1 XX公司车间简介 (22)3.2 XX公司车间制造流程 (22)3.3 XX公司车间生产工艺布局存在的问题及原因 (23)第四章 XX公司生产车间工艺布局优化研究 (26)4.1 车间工艺布局总体要求 (26)4.2 车间生产流程优化研究 (27)4.3 车间上设施布局优化研究 (29)4.4 车间搬运系统优化研究 (29)第五章方案评价 (34)5.1 目标函数模型 (34)5.2 评价结果 (35)5.2.1 XX分厂现有场地 (35)5.2.2 主厂房新的工艺布局一(现有DJ和SJ兼顾) (36)5.2.3 主厂房新的工艺布局二(全SJ) (38)5.2.4 车间工艺布局的比较与优化 (40)第六章结论与建议 (44)6.1 研究结论 (44)6.2 建议 (45)6.2.1 做好工艺布局的总体设计 (45)6.2.2 工艺布局的程序 (46)参考文献 ........................................................................................... 错误!未定义书签。
车间布局优化方案
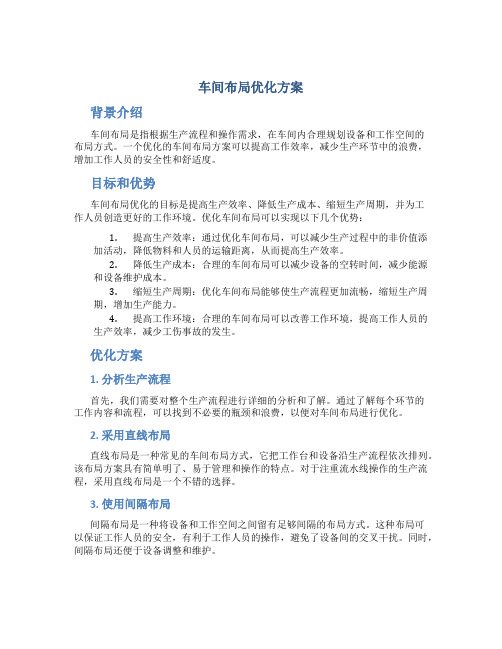
车间布局优化方案背景介绍车间布局是指根据生产流程和操作需求,在车间内合理规划设备和工作空间的布局方式。
一个优化的车间布局方案可以提高工作效率,减少生产环节中的浪费,增加工作人员的安全性和舒适度。
目标和优势车间布局优化的目标是提高生产效率、降低生产成本、缩短生产周期,并为工作人员创造更好的工作环境。
优化车间布局可以实现以下几个优势:1.提高生产效率:通过优化车间布局,可以减少生产过程中的非价值添加活动,降低物料和人员的运输距离,从而提高生产效率。
2.降低生产成本:合理的车间布局可以减少设备的空转时间,减少能源和设备维护成本。
3.缩短生产周期:优化车间布局能够使生产流程更加流畅,缩短生产周期,增加生产能力。
4.提高工作环境:合理的车间布局可以改善工作环境,提高工作人员的生产效率,减少工伤事故的发生。
优化方案1. 分析生产流程首先,我们需要对整个生产流程进行详细的分析和了解。
通过了解每个环节的工作内容和流程,可以找到不必要的瓶颈和浪费,以便对车间布局进行优化。
2. 采用直线布局直线布局是一种常见的车间布局方式,它把工作台和设备沿生产流程依次排列。
该布局方案具有简单明了、易于管理和操作的特点。
对于注重流水线操作的生产流程,采用直线布局是一个不错的选择。
3. 使用间隔布局间隔布局是一种将设备和工作空间之间留有足够间隔的布局方式。
这种布局可以保证工作人员的安全,有利于工作人员的操作,避免了设备间的交叉干扰。
同时,间隔布局还便于设备调整和维护。
4. 考虑人员流动在优化车间布局时,不仅要考虑设备和工作台之间的布局,还要考虑工作人员的流动。
要保证工作人员可以便捷地到达各个设备和工作台,避免拥挤和阻塞现象的发生。
5. 设置合理的储存区域储存区域在车间布局中起到重要的作用。
合理的储存区域可以使物料和工作台之间的距离最小化,提高物料的供应效率。
同时,储存区域还要设置标签和编号,以便工作人员可以快速找到所需物料。
6. 利用技术手段辅助布局现代技术手段可以提供车间布局分析和仿真的能力,通过计算机模拟,可以预测不同车间布局方式下的生产效果。
车间布局优化设计方案
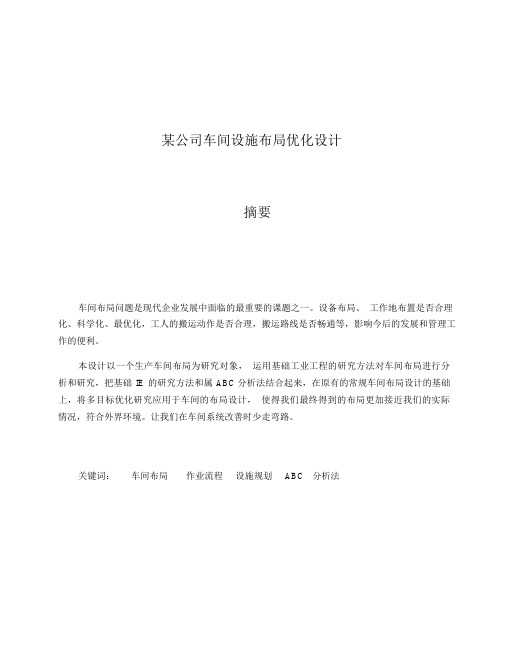
某公司车间设施布局优化设计摘要车间布局问题是现代企业发展中面临的最重要的课题之一。
设备布局、工作地布置是否合理化、科学化、最优化,工人的搬运动作是否合理,搬运路线是否畅通等,影响今后的发展和管理工作的便利。
本设计以一个生产车间布局为研究对象,运用基础工业工程的研究方法对车间布局进行分析和研究,把基础 IE 的研究方法和属 ABC分析法结合起来,在原有的常规车间布局设计的基础上,将多目标优化研究应用于车间的布局设计,使得我们最终得到的布局更加接近我们的实际情况,符合外界环境。
让我们在车间系统改善时少走弯路。
关键词:车间布局作业流程设施规划ABC分析法Workshop Optimization Design of Multi-Layers FactoryAbstractPlant layout problem is the development of a modern enterprise facing one of the most important issues. Equipment layout, and layout work is to rationalize the scientific and the most optimized, workers handling the action is reasonable, such as handling the flow line, the impact of future development and management of facilities.This thesis regards lighting company as the research object, use the research approach of basic industrial engineering to analyze and improve the shop floor ebasic SFL theory and multi-target model knowledge to design our new layout and act as one evaluation system. Let our work is more efficient and avoid any mistakes This thesis combines research approach of basic IE with an attribute hierarchicalmodel, And set up one kind of evaluation system for small companies. Practice has proved that the method that this paper adopts is effective and of good popularization meanings.Key words:Shop floor Layout ;Production procedure; Attribute hierarchical;ABC storage method目录摘要 (I)Abstract .............................................................................................................................................................................................................................................................................. I I第一章绪论 (1)1.1 设施布局的概念 (1)1.2 布局问题概述 (1)1.3 我国车间布局的发展现状 (2)第二章设计背景 (4)2.1 公司概况 (4)2.2 车间布局目前存在的问题分析 (5)第三章陶瓷车间总体规划 (6)3.1 企业生产系统布局的目标 (6)3.2 总体优化的目标 (7)3.2.1 设施规划的目标 (8)3.2.2 流程设计的目标 (8)3.3 改进前的总体布局 (9)3.4 总体布局优化 (10)第四章车间设施布局优化和设计 (15)4.1 车间储存区的优化设计 (15)4.1.1 基于 ABC 法库存分类管理 (15)4.1.2 陶瓷储存区优化的可行性分析 (21)4.2 生产区的物流路线分析 (21)4.2.1 原有方案分析 (21)4.2.2 作业改进 (25)4.3 确定优化方案 (28)4.4.1 原有方案分析 (28)4.4.2 确定优化方案 (30)4.5“ 5S管”理 (32)第五章方案评价 (35)结束语 (36)参考文献 (37)致谢 (38)附录 (38)附图(一)陶瓷车间改进前总体布局图 (38)附图(二)陶瓷车间改进后总体布局图 (38)附图(三)陶瓷车间改进前后物流路线图 (38)附图(四)陶瓷车间改进前后工艺流程图 (38)南京工业大学本科生毕业设计(论文)第一章绪论1.1 设施布局的概念所谓设施布局,是指在选定的设施区域内,合理安排组织内部各生产作业单元和辅助设施的相对位置和面积、设备的布置,使之构成一个符合企业生产经营要求的有机整体。
优化车间生产布局

优化车间生产布局车间生产布局对于企业的生产效率和成本控制具有重要影响。
一个合理优化的车间生产布局可以提高生产效率,减少物料和人力资源的浪费,降低生产成本,提高产品质量。
本文将从优化车间生产布局的重要性、优化方法和案例分析等方面进行探讨。
一、优化车间生产布局的重要性车间生产布局直接关系到企业的生产效率和产品质量,因此优化车间生产布局具有重要的意义。
1. 提高生产效率:合理的车间生产布局可以减少物料和人力资源的运输距离,缩短生产周期,提高生产效率。
2. 降低生产成本:通过优化车间生产布局,可以减少物料和半成品的库存,降低仓储成本;同时,减少运输距离和时间,降低物流成本。
3. 提高产品质量:优化车间生产布局可以避免不同生产环节的交叉干扰,减少错误和误操作,提高产品的质量和一致性。
二、优化车间生产布局的方法1. 综合评估现有布局:首先,需要对现有布局进行综合评估,分析存在的问题和瓶颈,了解各个生产环节的联系与依赖。
2. 制定优化方案:基于对现有布局的评估,制定相应的优化方案。
优化方案应该充分考虑生产流程、设备配置和人员安排等因素,力求简化流程、减少运输距离和提升效率。
3. 合理配置设备和工作站:根据优化方案,合理配置设备和工作站,确保各个环节之间的衔接流畅,避免资源浪费和交叉干扰。
4. 设计合理的物料流动路径:优化车间生产布局还需要设计合理的物料流动路径,尽量减少物料搬运和运输时间,提高物料运输效率。
5. 优化人员安排:合理的人员安排有助于提高生产效率和产品质量。
通过培训和合理的人员调度,确保员工在合适的岗位上发挥最大作用。
三、案例分析某汽车制造企业的车间生产布局存在问题,导致生产效率低下,成本高昂。
通过优化车间生产布局,取得了显著的效果。
1. 综合评估现有布局:通过对现有布局进行评估,发现生产车间之间距离过远,导致物料运输时间长,工作人员通勤时间长,严重影响生产效率。
2. 建立新的优化方案:建立新的优化方案,将生产车间重新划分,并合理布局设备和工作站,缩短物料运输距离和通勤时间。
车间布局规划方案
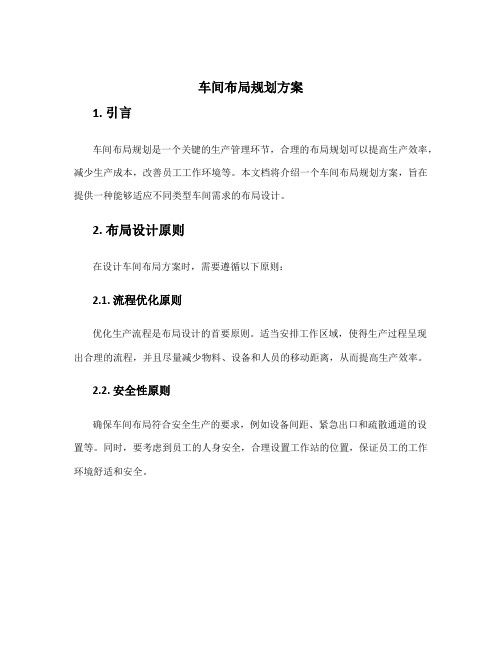
车间布局规划方案1. 引言车间布局规划是一个关键的生产管理环节,合理的布局规划可以提高生产效率,减少生产成本,改善员工工作环境等。
本文档将介绍一个车间布局规划方案,旨在提供一种能够适应不同类型车间需求的布局设计。
2. 布局设计原则在设计车间布局方案时,需要遵循以下原则:2.1. 流程优化原则优化生产流程是布局设计的首要原则。
适当安排工作区域,使得生产过程呈现出合理的流程,并且尽量减少物料、设备和人员的移动距离,从而提高生产效率。
2.2. 安全性原则确保车间布局符合安全生产的要求,例如设备间距、紧急出口和疏散通道的设置等。
同时,要考虑到员工的人身安全,合理设置工作站的位置,保证员工的工作环境舒适和安全。
2.3. 灵活性原则考虑到生产线的变动性,布局设计应具有一定的灵活性,能够适应不同产品或生产线的需要。
可以采用模块化的设计理念,通过调整或移动工作台、设备和物料仓库等,来满足不同工艺的生产需求。
3. 车间布局方案本方案将车间布局划分为五大区域:接收区、加工区、装配区、质检区和仓储区。
各区域的布局和功能如下:3.1. 接收区接收区位于车间入口附近,用于接收原材料和零部件。
该区域应设置货物检验台,用于对接收的物料进行检验和质量评估。
同时,可设置一些原材料暂存货架,方便后续的加工和仓储作业。
3.2. 加工区加工区是整个车间布局的核心区域,包含主要的生产设备和工作台。
加工区应根据生产流程的需求,合理安排设备的摆放顺序和工作台的位置,以最大限度地提高生产效率。
同时,要考虑设备之间的通道宽度和安全距离,确保员工和设备的安全。
3.3. 装配区装配区是用于对加工完成的零部件进行组装和调试的区域。
该区域应设置装配台和调试设备,方便员工进行组装过程中的操作和调试工作。
同样,要注意工作台的高度和人机工程学的原则,以提供一个舒适和安全的工作环境。
3.4. 质检区质检区应位于装配区的附近,用于对装配完成的产品进行质量检测和评估。
生产车间工艺优化流程图

生产车间工艺优化流程图第1章工艺优化概述 (3)1.1 工艺优化的重要性 (3)1.2 工艺优化的方法与步骤 (3)第2章车间布局优化 (4)2.1 车间布局现状分析 (4)2.1.1 车间空间布局 (4)2.1.2 生产线布局 (4)2.1.3 物流运输 (4)2.1.4 安全环保 (4)2.2 布局优化原则与目标 (4)2.2.1 优化原则 (5)2.2.2 优化目标 (5)2.3 布局优化方案设计 (5)2.3.1 生产线布局优化 (5)2.3.2 物流运输优化 (5)2.3.3 安全环保优化 (5)2.3.4 空间布局优化 (5)第3章生产流程优化 (5)3.1 生产流程现状分析 (6)3.1.1 生产流程概述 (6)3.1.2 现状问题分析 (6)3.2 流程优化方法与工具 (6)3.2.1 优化方法 (6)3.2.2 优化工具 (6)3.3 流程优化实施与监控 (6)3.3.1 实施步骤 (6)3.3.2 监控措施 (7)第4章作业标准化 (7)4.1 作业标准化概述 (7)4.2 作业标准制定与修订 (7)4.2.1 作业标准的制定 (7)4.2.2 作业标准的修订 (8)4.3 作业标准实施与监督 (8)4.3.1 作业标准实施 (8)4.3.2 作业标准监督 (8)第五章设备管理与优化 (8)5.1 设备管理现状分析 (8)5.1.1 设备配置与功能 (8)5.1.2 设备使用与管理 (8)5.1.3 设备故障与维修 (9)5.2 设备优化策略与措施 (9)5.2.2 设备更新与改造 (9)5.2.3 人员培训与管理 (9)5.2.4 设备维护与保养 (9)5.3 设备维护与保养 (9)5.3.1 定期检查与保养 (9)5.3.2 预防性维修 (9)5.3.3 优化维修流程 (9)5.3.4 建立设备档案 (9)5.3.5 加强设备信息化管理 (9)第6章人力资源管理优化 (9)6.1 人力资源管理现状分析 (10)6.2 人员配置与培训 (10)6.2.1 人员配置优化 (10)6.2.2 培训机制优化 (10)6.3 绩效考核与激励 (10)6.3.1 绩效考核优化 (10)6.3.2 激励机制优化 (10)第7章质量管理优化 (10)7.1 质量管理现状分析 (10)7.1.1 生产流程概述 (10)7.1.2 质量问题识别 (11)7.2 质量控制策略与措施 (11)7.2.1 原材料质量控制 (11)7.2.2 设备管理与维护 (11)7.2.3 人员培训与管理 (11)7.2.4 检验与质量控制 (11)7.2.5 环境保护与产品安全 (11)7.3 质量改进案例分析 (12)7.3.1 原材料质量改进 (12)7.3.2 设备管理改进 (12)7.3.3 人员培训与管理改进 (12)7.3.4 检验与质量控制改进 (12)7.3.5 环境保护与产品安全改进 (12)第8章物料管理优化 (12)8.1 物料管理现状分析 (12)8.2 物料采购与库存管理 (12)8.3 物料配送与回收 (13)第9章能源管理优化 (13)9.1 能源管理现状分析 (13)9.2 节能措施与设备改造 (13)9.3 能源监测与数据分析 (14)第10章环境与职业健康安全管理 (14)10.1 环境与职业健康安全管理现状分析 (14)10.1.2 职业健康安全现状 (14)10.2 环境与职业健康管理体系构建 (14)10.2.1 环境管理体系构建 (14)10.2.2 职业健康安全管理体系构建 (15)10.3 环境与职业健康安全监控与持续改进 (15)10.3.1 环境监控 (15)10.3.2 职业健康安全监控 (15)10.3.3 持续改进 (15)第1章工艺优化概述1.1 工艺优化的重要性工艺优化作为提高生产效率、降低成本、提升产品质量的重要手段,在现代制造业中发挥着越来越重要的作用。
生产车间改善方案实例
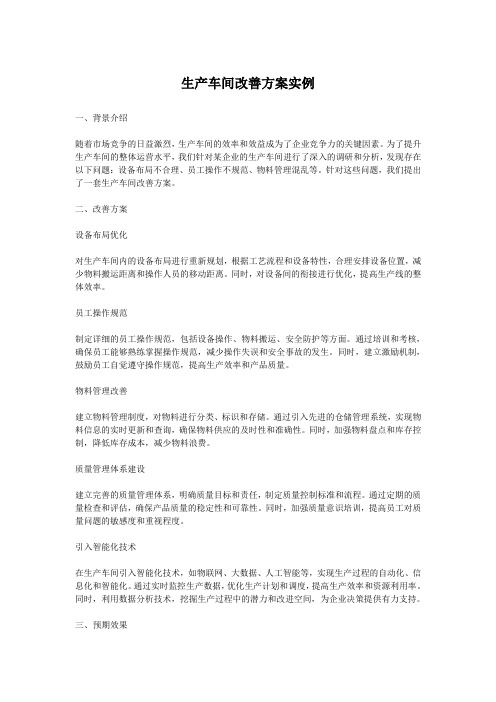
生产车间改善方案实例一、背景介绍随着市场竞争的日益激烈,生产车间的效率和效益成为了企业竞争力的关键因素。
为了提升生产车间的整体运营水平,我们针对某企业的生产车间进行了深入的调研和分析,发现存在以下问题:设备布局不合理、员工操作不规范、物料管理混乱等。
针对这些问题,我们提出了一套生产车间改善方案。
二、改善方案设备布局优化对生产车间内的设备布局进行重新规划,根据工艺流程和设备特性,合理安排设备位置,减少物料搬运距离和操作人员的移动距离。
同时,对设备间的衔接进行优化,提高生产线的整体效率。
员工操作规范制定详细的员工操作规范,包括设备操作、物料搬运、安全防护等方面。
通过培训和考核,确保员工能够熟练掌握操作规范,减少操作失误和安全事故的发生。
同时,建立激励机制,鼓励员工自觉遵守操作规范,提高生产效率和产品质量。
物料管理改善建立物料管理制度,对物料进行分类、标识和存储。
通过引入先进的仓储管理系统,实现物料信息的实时更新和查询,确保物料供应的及时性和准确性。
同时,加强物料盘点和库存控制,降低库存成本,减少物料浪费。
质量管理体系建设建立完善的质量管理体系,明确质量目标和责任,制定质量控制标准和流程。
通过定期的质量检查和评估,确保产品质量的稳定性和可靠性。
同时,加强质量意识培训,提高员工对质量问题的敏感度和重视程度。
引入智能化技术在生产车间引入智能化技术,如物联网、大数据、人工智能等,实现生产过程的自动化、信息化和智能化。
通过实时监控生产数据,优化生产计划和调度,提高生产效率和资源利用率。
同时,利用数据分析技术,挖掘生产过程中的潜力和改进空间,为企业决策提供有力支持。
三、预期效果通过以上改善措施的实施,预期生产车间将实现以下效果:生产效率提升:设备布局优化和员工操作规范将减少生产过程中的浪费和延误,提高生产效率。
产品质量提高:质量管理体系建设和员工质量意识培训将提升产品质量的稳定性和可靠性。
成本降低:物料管理改善和智能化技术的引入将降低库存成本和减少物料浪费,提高资源利用率。
生产车间布局规划

效率。
优化生产流程
02
按照生产流程来合理布局生产线,减少生产环节,提高生产效
率。
提高生产设备的利用率
03
通过提高生产设备的利用率,减少闲置设备带来的浪费,提高
生产效率。
降低成本
减少生产场地面积
合理规划生产车间的布局,提高场地的利用率,减少场地租金和运维成本。
节约运输成本
合理安排货物的存放和运输,减少运输距离和次数,从而降低运输成本。
03
布局规划方案
总体规划方案
1
考虑到生产流程和工艺要求,确定车间的总体 平面布局和功能区域划分。
2
根据生产设备的特性和工艺要求,设计设备布 局和相互之间的流水作业线。
3
安排生产员工的作业流程和安全通道,确保作 业效率和安全疏散。
设备布局规划
01
根据生产工艺和流程,合理安排设备的布局,提高生产效率。
03
物料搬运频率
分析物料搬运频率是否合理,过高的搬运频率会增加生产成本。
员工工作环境分析
1
工作环境舒适性
分析员工工作环境是否舒适,是否存在噪音、 污染等问题影响员工身心健康。
2
工作空间安全性
评估工作空间是否具有安全性,是否存在安全 隐患和职业病危害因素。
3
工作效率评估
分析员工工作效率是否符合预期,是否存在工 作负荷不足或过重的情况。
责任人分工
施工负责人
负责项目的施工组织与现场管理。
采购负责人
负责设备与材料的采购与供应。
项目负责人
负责整个项目的组织、协调与监督。
技术负责人
负责技术方案的制定与实施。
安全负责人
负责项目安全管理和风险控制。
优化生产布局提高生产效率

优化生产布局提高生产效率在现代工业生产中,优化生产布局是提高生产效率的重要手段之一。
通过科学合理地规划和调整生产区域的布局,可以最大程度地提高生产效率,减少资源浪费,提高产品质量。
本文将从生产布局的优化原则、实施步骤以及案例分析等方面,探讨优化生产布局的方法和效果。
一、优化生产布局的原则优化生产布局需要遵循以下几个原则:1. 设备排布合理:根据生产工艺流程和设备功能,合理安排设备的布局,使得生产线条流畅、无冗余距离,减少物料搬运和操作时间,提高生产效率。
2. 人员配备合理:根据生产区域的特点和生产工艺的需要,合理配置人员,并确保他们能够顺利地进行生产操作,避免出现人员交叉、资源浪费等问题,提高生产效率。
3. 物料流动便捷:合理规划物料的流动路线,保证物料可以方便地从供应区域到达生产线,并及时供应给生产设备使用,避免因物料不足或物料流动不畅导致的生产中断和效率低下。
4. 安全环保考虑:在优化生产布局的过程中,要注重安全生产和环境保护。
合理布置设备和人员的位置,确保生产过程中的安全,并采取相应的环境保护措施,减少对环境的污染。
二、优化生产布局的实施步骤优化生产布局的实施需要经过以下几个步骤:1. 评估现状:首先对当前的生产布局进行评估,了解目前存在的问题和瓶颈,确定需要改进的方向和重点。
2. 制定规划:根据评估结果,制定优化生产布局的规划方案。
考虑生产需求、设备配置、人员配备等因素,制定详细的布局方案。
3. 实施变更:根据规划方案,逐步实施生产布局的变更。
需要注意的是,在变更的过程中要注意协调各方利益,避免产生冲突。
4. 持续改进:优化生产布局是一个持续改进的过程。
定期评估生产效果,收集反馈意见,对布局进行优化和调整,不断提高生产效率和产品质量。
三、案例分析:某汽车组装车间的生产布局优化某汽车组装车间是一家汽车制造厂的核心生产区域,为了提高生产效率,他们对生产布局进行了优化。
首先,他们根据生产工艺流程,合理安排了设备的位置和工作区域的划分。
车间规划方案
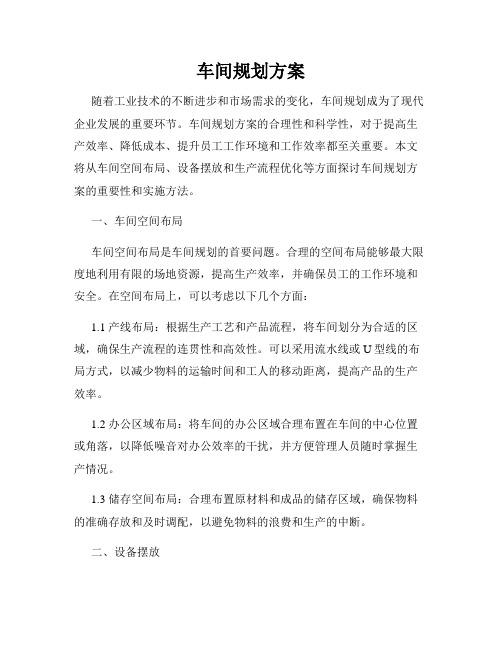
车间规划方案随着工业技术的不断进步和市场需求的变化,车间规划成为了现代企业发展的重要环节。
车间规划方案的合理性和科学性,对于提高生产效率、降低成本、提升员工工作环境和工作效率都至关重要。
本文将从车间空间布局、设备摆放和生产流程优化等方面探讨车间规划方案的重要性和实施方法。
一、车间空间布局车间空间布局是车间规划的首要问题。
合理的空间布局能够最大限度地利用有限的场地资源,提高生产效率,并确保员工的工作环境和安全。
在空间布局上,可以考虑以下几个方面:1.1 产线布局:根据生产工艺和产品流程,将车间划分为合适的区域,确保生产流程的连贯性和高效性。
可以采用流水线或U型线的布局方式,以减少物料的运输时间和工人的移动距离,提高产品的生产效率。
1.2 办公区域布局:将车间的办公区域合理布置在车间的中心位置或角落,以降低噪音对办公效率的干扰,并方便管理人员随时掌握生产情况。
1.3 储存空间布局:合理布置原材料和成品的储存区域,确保物料的准确存放和及时调配,以避免物料的浪费和生产的中断。
二、设备摆放设备摆放是车间规划的关键环节。
合理的设备摆放可以极大地提高生产效率和操作的便利性,避免生产过程中的瓶颈和事故发生。
在设备摆放上,需要考虑以下几个方面:2.1 设备类型选择:根据生产需求和工艺特点,选择适合的设备类型和性能,确保设备在使用中的稳定性和效率。
可以借助专业技术人员的意见和市场调研,选择最合适的设备供应商。
2.2 设备布局:根据设备的运作流程和工作间的尺寸,将设备合理布置在车间的合适位置。
保证设备之间的相互配合和操作工人的安全,尽可能减少生产过程中的物料转运和人员移动。
2.3 设备维护和保养:建立设备的维护保养计划和制度,定期对设备进行检修和保养,确保设备的长期稳定运行,减少设备故障对生产的影响。
三、生产流程优化生产流程优化是车间规划中的核心内容。
通过对生产流程进行优化,可以提高生产效率、降低成本,并减少浪费和错误的发生。
组装车间工艺优化设计报告

组装车间工艺优化设计报告引言组装车间是生产企业重要的一环,负责将不同零部件按照一定的工艺流程组装成最终产品。
优化组装车间的工艺设计可以提高生产效率、降低生产成本,并提高产品质量。
本报告旨在对组装车间工艺进行优化设计,以满足生产需求。
优化目标1. 提高生产效率:通过优化工艺流程和操作方式,减少组装过程中的非价值添加时间,提高车间的生产效率。
2. 降低生产成本:通过合理规划工艺流程,降低零部件的运输成本和装配成本,减少生产线的待机时间。
3. 提高产品质量:通过优化工艺流程和工艺参数,降低装配过程中的误差和缺陷率,提高产品的质量稳定性和一致性。
优化方案工艺流程优化1. 定制化布局:根据产品的特点和装配工艺特点,定制化设计生产线布局,降低物料和人员的运输距离,减少时间浪费。
2. 合理规划流程:优化零部件装配顺序,使得零部件的装配路径更加合理、简明,减少组装过程中的不必要步骤,提高生产效率。
3. 打破瓶颈环节:对于生产线上的瓶颈环节,采取相应措施进行优化,例如增加设备、调整工艺参数等,以提高该环节的生产效率。
操作方式优化1. 标准化操作:建立操作规范和标准化作业指导书,明确每个操作的执行步骤、要求和注意事项,减少由于操作不一致带来的不良品产生。
2. 人机协同:引入自动化设备,实现人机协同作业,人工和机器相互配合,提高生产效率和质量稳定性。
3. 培训和考核:提供员工培训,提高员工对工艺的理解和操作技能,确保每个员工能够按照工艺要求操作,减少错误和浪费。
工艺参数优化1. 工艺优化试验:通过实验和统计分析,确定优化的工艺参数,例如装配顺序、装配速度、紧固力等,以提高产品装配的质量。
2. 装配工具优化:选择合适的装配工具和夹具,确保装配过程的稳定性和一致性,减少装配误差和缺陷率。
3. 数据分析与反馈:对装配过程中的数据进行实时监控和收集,通过数据分析找出装配问题的根源,并及时采取措施纠正,避免问题再次发生。
结论通过对组装车间工艺的优化设计,可以提高生产效率、降低生产成本,并提高产品质量稳定性。
车间改善方案1篇

车间改善方案1篇车间改善方案一、引言车间是企业生产的重要场所,通过不断改善车间工作环境、提高生产效率,企业可以提升工人的工作积极性和生产质量,从而实现经济效益最大化。
本文将从六个方面展开叙述车间改善方案,包括车间布局优化、工作流程改进、设备升级、技能培训、员工参与和绩效评估等。
二、车间布局优化车间布局是车间工作效率的重要因素。
首先,要合理划分车间的不同区域,将原材料、半成品和成品分开存放,便于工人操作和管理。
其次,根据工序的先后顺序,将设备和工作台安排在合适的位置,减少物料和人员的移动距离,节省时间和能源。
此外,根据作业的相似性和频度,将相对应的工序安排在一起,提高生产效率。
三、工作流程改进针对车间的工作流程,可以通过以下几个方面进行改进。
首先,进行工序分析,找出生产中的瓶颈环节,采取相应的措施加以改善,提高生产效率。
其次,进行作业标准化,制定明确的工作规范和操作流程,减少人为因素对产品质量的影响。
此外,可以采用先进的生产管理方法,如精益生产、六西格玛等,优化工作流程,提高生产效率和品质。
四、设备升级现代化的设备是提升车间生产效率的重要保障。
首先,要对现有设备进行全面的检修和维护,确保其正常运行。
其次,根据生产需求,适时进行设备的更新和升级,引进高效能、智能化的新设备,提高生产效率和产品质量。
此外,可以考虑引入自动化生产线,减少人工操作,提高生产效率和安全性。
五、技能培训工人的技能水平直接影响到车间的生产效率和质量。
为此,企业应加强对工人的技能培训。
首先,要制定完善的培训计划,包括对新员工的基础培训和对老员工的进修培训。
培训内容可以包括工作安全、设备操作、工艺技术等方面的知识和技能。
其次,可以邀请专业人士进行内部培训或外部培训,提高工人的专业素质和技能水平。
此外,还可以建立技能评定和晋升制度,激励工人不断学习和提高。
六、员工参与员工是车间改善的主体,他们的参与和反馈对于改善方案的实施至关重要。
首先,要建立员工参与机制,如员工代表会议、意见箱等,鼓励工人积极参与车间工作和管理,提出改进建议和反馈意见。
生产工艺流程优化的方案
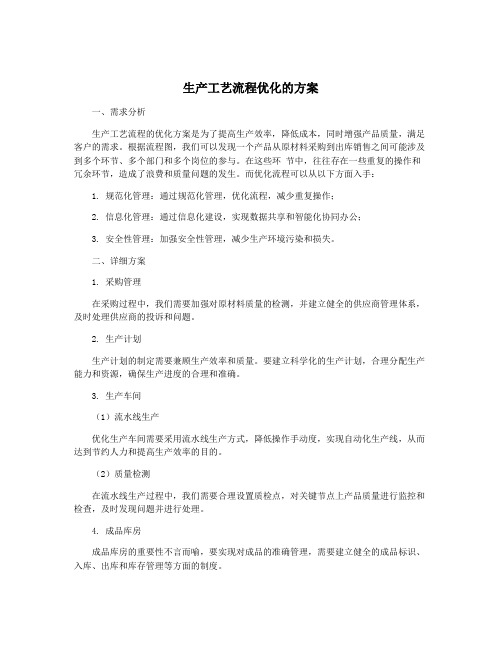
生产工艺流程优化的方案一、需求分析生产工艺流程的优化方案是为了提高生产效率,降低成本,同时增强产品质量,满足客户的需求。
根据流程图,我们可以发现一个产品从原材料采购到出库销售之间可能涉及到多个环节、多个部门和多个岗位的参与。
在这些环节中,往往存在一些重复的操作和冗余环节,造成了浪费和质量问题的发生。
而优化流程可以从以下方面入手:1. 规范化管理:通过规范化管理,优化流程,减少重复操作;2. 信息化管理:通过信息化建设,实现数据共享和智能化协同办公;3. 安全性管理:加强安全性管理,减少生产环境污染和损失。
二、详细方案1. 采购管理在采购过程中,我们需要加强对原材料质量的检测,并建立健全的供应商管理体系,及时处理供应商的投诉和问题。
2. 生产计划生产计划的制定需要兼顾生产效率和质量。
要建立科学化的生产计划,合理分配生产能力和资源,确保生产进度的合理和准确。
3. 生产车间(1)流水线生产优化生产车间需要采用流水线生产方式,降低操作手动度,实现自动化生产线,从而达到节约人力和提高生产效率的目的。
(2)质量检测在流水线生产过程中,我们需要合理设置质检点,对关键节点上产品质量进行监控和检查,及时发现问题并进行处理。
4. 成品库房成品库房的重要性不言而喻,要实现对成品的准确管理,需要建立健全的成品标识、入库、出库和库存管理等方面的制度。
5. 物流管理物流管理包括运输和配送,我们需要完善该方面的管理,加强物流跟踪,确保物流运输的安全和及时。
6. 信息化建设信息化建设可以实现数据共享和智能化协同办公。
通过建立ERP管理系统、设备检测系统、产品追溯系统等、辅助信息管理系统等工具,实现生产全面管理。
7. 安全性管理加强安全性管理可以有效地减少环境污染和损失。
我们可以采取以下措施:(1)制定紧急预案,应对突发情况,及时处理损失和问题;(2)制定安全操作规程,引导员工重复操作和降低工伤事故发生率。
生产工艺流程的优化方案是一项复杂的系统工程,需要涉及到多个部门以及多个环节。
解决车间问题的方案
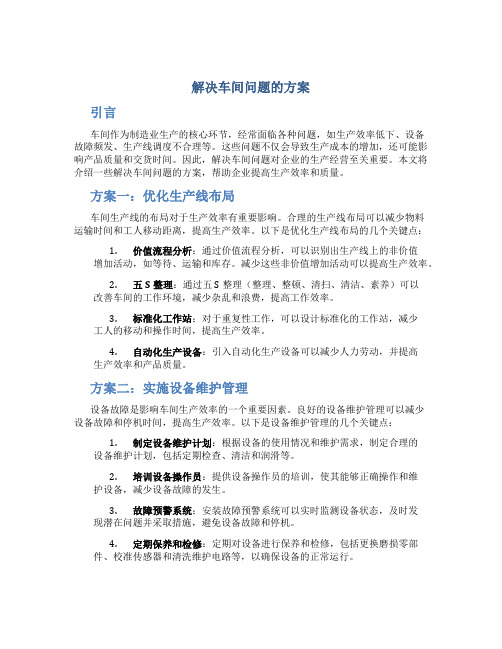
解决车间问题的方案引言车间作为制造业生产的核心环节,经常面临各种问题,如生产效率低下、设备故障频发、生产线调度不合理等。
这些问题不仅会导致生产成本的增加,还可能影响产品质量和交货时间。
因此,解决车间问题对企业的生产经营至关重要。
本文将介绍一些解决车间问题的方案,帮助企业提高生产效率和质量。
方案一:优化生产线布局车间生产线的布局对于生产效率有重要影响。
合理的生产线布局可以减少物料运输时间和工人移动距离,提高生产效率。
以下是优化生产线布局的几个关键点:1.价值流程分析:通过价值流程分析,可以识别出生产线上的非价值增加活动,如等待、运输和库存。
减少这些非价值增加活动可以提高生产效率。
2.五S整理:通过五S整理(整理、整顿、清扫、清洁、素养)可以改善车间的工作环境,减少杂乱和浪费,提高工作效率。
3.标准化工作站:对于重复性工作,可以设计标准化的工作站,减少工人的移动和操作时间,提高生产效率。
4.自动化生产设备:引入自动化生产设备可以减少人力劳动,并提高生产效率和产品质量。
方案二:实施设备维护管理设备故障是影响车间生产效率的一个重要因素。
良好的设备维护管理可以减少设备故障和停机时间,提高生产效率。
以下是设备维护管理的几个关键点:1.制定设备维护计划:根据设备的使用情况和维护需求,制定合理的设备维护计划,包括定期检查、清洁和润滑等。
2.培训设备操作员:提供设备操作员的培训,使其能够正确操作和维护设备,减少设备故障的发生。
3.故障预警系统:安装故障预警系统可以实时监测设备状态,及时发现潜在问题并采取措施,避免设备故障和停机。
4.定期保养和检修:定期对设备进行保养和检修,包括更换磨损零部件、校准传感器和清洗维护电路等,以确保设备的正常运行。
方案三:优化生产调度生产调度是车间组织和协调生产活动的过程,合理的生产调度可以最大程度地提高生产效率和产品质量。
以下是优化生产调度的几个关键点:1.制定合理的生产计划:通过合理的生产计划,可以避免生产过剩或生产不足的情况,提高生产效率。
生产车间布局改进:有效空间利用的实践指南

生产车间布局改进:有效空间利用的实践指南在工业生产过程中,生产车间的布局对于提高生产效率和优化工作流程起着至关重要的作用。
合理利用空间资源,优化生产车间布局,可以有效提升生产效率,降低物料运输成本,并减少作业人员之间的碰撞与干扰。
本文将从合理划分不同区域、布局工作站、减少物料运输距离以及注意安全隐患四个方面,为您提供一些实用的改进车间布局的指南。
一、合理划分不同区域1. 设立原材料存放区:将原材料储存在专门的区域内,并根据不同种类进行分类和标识,方便快速取用,避免浪费时间和混淆物料。
2. 设置生产工作区:将生产工作区域划分为不同的区域,按照工作流程和作业要求进行布局,确保各个工序之间的连贯性和高效性,并根据需要设立临时存放货物的区域,避免物料相互干扰。
3. 划分成品储存区:将加工完成的成品进行分类储存,确保产品的质量和完整性,在需要时能够快速取得,并设置合适的标识和记录,方便管理和库存控制。
二、布局工作站1. 依据工作流程优化工作站布局:根据生产工艺流程的特点,合理布置工作站的位置,确保操作员能够方便地进行工作,在隔离风险区域和避免交叉污染的同时,最大程度减少物料和人员之间的移动。
2. 统一工作站布局和设备摆放方式:保持工作站的统一规格和设备的标准化摆放,以减少操作员的学习成本和熟悉时间,并提高工作效率和工作品质。
3. 考虑人机工程学因素:根据操作员的身高、工作姿势和力学原理等,合理设置工作站的高度、角度和工作间距,为操作员提供一个舒适、安全的工作环境,减少不必要的工作负担和体力消耗。
三、减少物料运输距离1. 在生产线布局中合理安排物料传输设备:采用输送带、托盘运输等设备来替代人工搬运,减少物料的运输时间和人力成本,提高物料传送的效率和准确性。
2. 缩短物料运输路径:通过调整车间内设备的位置、设立中转站和临时存放区,缩短物料运输的路径,降低非价值增加时间,提高物料运输的效率和响应速度。
3. 优化布局,减少物料运输距离:在进行车间布局时,要根据生产流程和物料传输需求,将相互依赖的工序和设备相近地布置在一起,减少物料的运输距离,并合理安排物料的存放位置,便于操作员的取用和归还。
钳工技术合理布局与优化工作环境
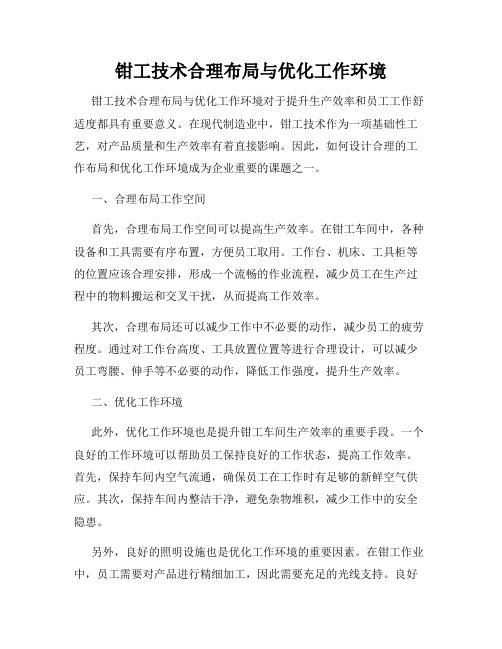
钳工技术合理布局与优化工作环境钳工技术合理布局与优化工作环境对于提升生产效率和员工工作舒适度都具有重要意义。
在现代制造业中,钳工技术作为一项基础性工艺,对产品质量和生产效率有着直接影响。
因此,如何设计合理的工作布局和优化工作环境成为企业重要的课题之一。
一、合理布局工作空间首先,合理布局工作空间可以提高生产效率。
在钳工车间中,各种设备和工具需要有序布置,方便员工取用。
工作台、机床、工具柜等的位置应该合理安排,形成一个流畅的作业流程,减少员工在生产过程中的物料搬运和交叉干扰,从而提高工作效率。
其次,合理布局还可以减少工作中不必要的动作,减少员工的疲劳程度。
通过对工作台高度、工具放置位置等进行合理设计,可以减少员工弯腰、伸手等不必要的动作,降低工作强度,提升生产效率。
二、优化工作环境此外,优化工作环境也是提升钳工车间生产效率的重要手段。
一个良好的工作环境可以帮助员工保持良好的工作状态,提高工作效率。
首先,保持车间内空气流通,确保员工在工作时有足够的新鲜空气供应。
其次,保持车间内整洁干净,避免杂物堆积,减少工作中的安全隐患。
另外,良好的照明设施也是优化工作环境的重要因素。
在钳工作业中,员工需要对产品进行精细加工,因此需要充足的光线支持。
良好的照明不仅可以帮助员工提高工作精度,还可以减少眼睛疲劳,保护员工的视力健康。
三、科技手段助力优化在现代制造业中,随着科技的不断发展,越来越多的企业开始引入智能设备来优化工作环境。
例如,智能机床可以提高生产效率,减少员工劳动强度;智能照明系统可以根据员工的工作需求调节光线亮度,提升工作效率。
除此之外,企业还可以通过引入智能物流系统,优化原材料的进出货流程,提高生产效率。
智能监控系统可以帮助企业实时监测生产情况,及时发现问题并进行处理,保障生产线的稳定运行。
综上所述,钳工技术合理布局与优化工作环境对于提升生产效率和员工工作舒适度至关重要。
通过合理布局工作空间、优化工作环境和引入科技手段,企业可以有效提高钳工车间的生产效率,提升产品质量,实现可持续发展。
- 1、下载文档前请自行甄别文档内容的完整性,平台不提供额外的编辑、内容补充、找答案等附加服务。
- 2、"仅部分预览"的文档,不可在线预览部分如存在完整性等问题,可反馈申请退款(可完整预览的文档不适用该条件!)。
- 3、如文档侵犯您的权益,请联系客服反馈,我们会尽快为您处理(人工客服工作时间:9:00-18:30)。
【最新资料,Word版,可自由编辑!】目录摘要.................................................................................................. 错误!未定义书签。
Abstract ........................................................................................... 错误!未定义书签。
第一章绪论. (4)1.1 研究的背景及意义 (4)1.2 国内外研究综述 (5)1.2.1 国外研究现状 (5)1.2.2 国内研究现状 (6)1.3 研究内容及研究思路 (7)1.4 文章拟创新点 (8)第二章相关理论概述 (9)2.1 生产物流及优化 (9)2.1.1 生产物流的概念 (10)2.1.2 生产物流的基本特征 (10)2.1.3 影响生产物流的主要因素 (12)2.2 生产车间工艺布局的内容及要求 (12)2.2.1 生产车间工艺布局的内容 (12)2.2.2 车间设备配置的要求 (16)2.2.3 生产现场管理的要求 (18)2.2.4 生产日常管理的要求 (19)第三章 XX公司生产车间工艺布局现状分析 (22)3.1 XX公司车间简介 (22)3.2 XX公司车间制造流程 (22)3.3 XX公司车间生产工艺布局存在的问题及原因 (23)第四章 XX公司生产车间工艺布局优化研究 (26)4.1 车间工艺布局总体要求 (26)4.2 车间生产流程优化研究 (27)4.3 车间上设施布局优化研究 (29)4.4 车间搬运系统优化研究 (29)第五章方案评价 (34)5.1 目标函数模型 (34)5.2 评价结果 (35)5.2.1 XX分厂现有场地 (35)5.2.2 主厂房新的工艺布局一(现有DJ和SJ兼顾) (36)5.2.3 主厂房新的工艺布局二(全SJ) (38)5.2.4 车间工艺布局的比较与优化 (40)第六章结论与建议 (44)6.1 研究结论 (44)6.2 建议 (45)6.2.1 做好工艺布局的总体设计 (45)6.2.2 工艺布局的程序 (46)参考文献 ........................................................................................... 错误!未定义书签。
第一章绪论1.1 研究的背景及意义工艺布局合理与否,是生产效益好坏的关键性问题。
建造一个理想的生产车问,就必须认真的研究工艺布局,使其操作方便、生产顺利、节约经费、效果显著。
根据各地的建厂经验,电机线圈生产的前部分是顺序排列,最好采用立体布局。
而后部分是几道工序的同时操作,最好采用平面布局。
前部分的立体布局即把工艺的第一阶段排成一条立体线,自上而下地安排工艺流程。
制造方法是由各种各样的工序和工艺方法组成的[1]。
在制造企业的生产流程中,工艺工作贯穿于整个流程当中。
工艺设计处于产品设计和加工制造的中间环节,它是生产技术准备工作的第一步。
工艺设计工作不仅涉及到企业的生产类型、产品结构、工艺装备、生产技术水平等,甚至还要受到工艺人员实际经验和生产管理体制的制约,其中的任何一个因素发生变化,都可能导致工艺设计方案的变化[2]。
工艺设计产生的工艺总方案、工艺路线和工艺规程是进行工装制造和零件加工装配的主要依据,它对组织生产、保证产品质量、提高生产率、降低成本、缩短生产周期及改善劳动条件等都有直接的影响,是整个生产流程中的关键性工作[3]。
因此,对产品设计进行可制造性评价时,应同下面的制造方法的设计观点密切关联[4]。
针对生产计划中要生产的产品对工厂的具体设施进行管理,是确定该设计的可制造性的关键要素之一[5]。
工厂内材料和工艺方法的流程能够显著地影响工厂的效率,并最后影响到产品的可制造性。
现在有很多的先进方法可以在产品设计阶段改善产品的可制造性。
1.2 国内外研究综述1.2.1 国外研究现状随着市场的全球化,企业间竞争愈演愈烈,在工厂设计初期,加工设备的选型错误及布局的不合理往往导致后期生产成本上升,后期改正这些错误的代价巨大。
因此,在工厂设计前期,合理选择加工设备,精益规划设备布局,高效组织并协调各生产要素,是降低产品的制造成本、提高设备的使用效率和生产率的关键。
加工精度是指加工设备所能达到的尺寸精度、形状精度和位置精度,它受制于加工设备本身的几何精度、运动精度、刚度、抗震性、热稳定性、精度保持性和误差补偿策略等。
设备加工精度过高或过低都是不可取的,我们需要的是经济加工精度,即加工设备在其正常使用条件下能经济合理地达到的加工精度[6]。
在制造业中,工艺布局设计主要是确定工厂的生产部门、辅助服务部门和管理部门的位置[7]。
合理有效的工厂布置对提高企业的生产效益、降低成本起着重要的作用[8]。
最具代表性的工艺布局设计方法是R.缪瑟(R.Muther)提出的“系统布置设计”(SLP)法,该方法通过对企业内部供应链系统的物流分析,提出了作业单位相互关系密级表示法,使布置设计由定性阶段发展到定量阶段[9]。
在缪瑟提出的系统布置设计(SLP)中,把产品P,产量Q,生产路线R,辅助服务部门S及生产时间安排工作为给定的基本要素(原始资料)和布置设计工作的基本出发点[10]。
表面质量主要指被加工工件表面几何学特性及表面层物理品质。
表面粗糙度等除与加工设备本身有关外,还与影响切削稳定性的因素有关,如切削用量、切削液、工件材料、刀具(或磨具)的几何形状及材料特性等,若选择设备时仅注意设备本身而忽视上述因素将是片面的,其效果可能事倍功半[11]。
西泽和雷德列举了流程导向型布局方法的优点和缺点。
其优点有:这种布局方式的应变能力很强,因为工作可以在车间里任何一台机器上进行。
相对的,一个工作单元至少要包括所有必需的设备中的一台(且每种只有一台)。
在车间布局里,一台机器停止工作不会使生产中断,因为相同的其他机器也可以继续运转,而工作单元里一台机器停止工作,整个单元就要停止下来。
不过,根据约束理论,如果停工不是发生在瓶颈环节,问题就不会很大[12]。
1.2.2 国内研究现状一般意义上来说,布局设计就是将一些物体按一定的要求合理放置在一个空间内,它是一个涉及参数化设计、人工智能、图形学、信息处理、优化、仿真等技术的交叉学术领域,实践证明它还是一个复杂的组合优化问题。
它存在于现实生活中的许多行业和领域[13]:①航空航天工业中,航天器上各种仪器的布局摆放问题;②造船、汽车等交通工具内不同形状、大小的物体放置问题;③集成电路设计中,各种元件的合理布置问题;④建筑设计中,各房间的合理布置及厂房,设备等布局问题;⑤机械设计领域中,各种基于装配的机床布局设计问题[14]。
生产系统中的布局问题包括在整个工厂中车间的布置,车间中生产单元的布置,以及生产单元中每台设备的具体布置问题。
我们主要在车间的层次上进行设备布局问题的研究。
车间布局是指对车间各基本工段、辅助工段、生产服务部门、设施、设备、仓库、通道等在空间和平面上的相互位置的统筹安排。
车间布置旨在最有效地利用厂房空间,一方面,方便于工作操作,避免生产设备的过度拥挤;另一方面,注意厂房的通风和防火防爆,确保安全生产。
其具体内容包括:①在纵跨、横跨、高跨、露天跨建筑面积上的安排;②在厂房内空间分层的安排;③在多层建筑内的安排[15]。
通常车间设备布局是在产品的工艺设计和设备选型之后进行的,通过工艺选择和生产能力规划产生整个生产的工序和设备的具体规格,以及设备之间的物料传递关系,为布局设计提供原始数据[16]。
同时两者也是相互影响的,布局决策包括各部门内的生产单位和设备布置,这种布置影响到系统工作的流畅性,并进而影响到生产能力、成本和生产柔性。
布置决策受产品和服务设计决策的影响。
布局问题具有广泛的应用背景,布局结果的好坏对整个行业生产的合理性、经济性、安全性等都有重大的影响。
其主要研究制造系统中车间布局设计问题。
生产车间是制造系统的基本组成部分,直接承担着企业的加工、装配任务,是将原材料转化为产品的部门[17]。
所谓车间布置就是按照一定的原则,合理地确定车间内部各组成单位(工段和班组)及工作地,设备之间的相互位置,从而使它们成为一个有机整体,实现车间的具体功能和任务。
车间布置一般包括:基本生产部分、辅助生产部分、仓库部分、过道部分、车间管理部分、生活福利部分等[18]。
1.3 研究内容及研究思路本文的组织结构:第1章绪论部分,主要阐述本文研究的背景及意义,国内外研究综述,研究内容及研究思路以及文章拟创新点。
第2章相关理论概述。
分别对生产物流及优化和生产车间工艺布局的内容及要求进行论述。
第3章XX公司生产车间工艺布局现状分析,结合XX公司车间简介,XX公司车间制造流程。
根据生产实际提出XX公司车间生产工艺布局存在的问题及原因。
第4章XX公司生产车间工艺布局优化研究。
通过分析车间工艺布局总体要求,结合优化方案进行对比分析。
第5章方案评价。
运用相关的目标函数模型对优化方案进行评价,并给出最终的评价结果。
最后是结论部分。
图1.1 技术路线1.4 文章拟创新点生产车间是制造企业的主战场,产品质量、生产效益、成本损耗和员工士气与生产车间和一线干部的管理水平息息相关,并直接影响企业的经营绩效。
因此,掌握科学的管理知识,灵活地运用各种科学管理手段,对提高和稳定产品质量,降低成本很有裨益。
本文的创新点主要是结合XX公司车间生产工艺布局方案进行比较研究,并利用目标函数模型进行评估,从而选定最佳的布局方案。
第二章相关理论概述2.1 生产物流及优化一个制造企业的生产过程实质上是一个物流过程。
所谓生产计划,实际上是物料流动的计划。
计划的对象是物料,计划执行的结果也要通过对物料的监控来考核。
这也是生产物流管理通常被称为“物料管理”的原因。
生产计划的实施,必定伴随着物料数量、形态和存储位置的改变。
人和物料都必定存放在一定的空间位置上,这些存储位置就是对物料的监控点。
对计划执行情况的监控和对物料状况的反馈信息主要来自这些监控点[19]。
计算机终端或数据采集装置往往就设在这里。
生产物流管理强调对物料的存储、传送、数量和状态的变化等信息的管理。
2.1.1 生产物流的概念生产物流是指原材料、燃料或外购件投入生产后,经过下料、发料、运送到各个加工点规定的生产工艺过程进行加工和储存的全部生产过程。
因此,生产物流的形式和规模取决于生产的类型、规模、方式和生产的专业化与协作化水平。
生产物流区别于其他物流系统的最显著特点是它和企业生产密切联系在一起。