IE工程师年终工作总结
ie工程师年终工作总结6篇

ie工程师年终工作总结6篇ie工程师年终工作总结 (1)1、在工程项目中担任资料员及技术助理,工程于20xx年12月10日开工××年×月×日竣工,总工期×天,工程造价万,总面积约3500㎡。
此工程系市政加少量土建工程,因以前做过少量市政工程,所以本工程对我来说还算容易上手。
绿化工程是一个对时间季节性比较挑剔的项目,从本工程开工时间上来说对本工程的影响不大,相对来说还是有利的。
虽然冬期栽种的花草树木不易走根,但是相对夏天来说不会很容易干枯,只要把保温措施做好了成活率是相当高的。
在施工过程中我不断查阅相关专业资料,对我们栽种的各种花草树木的成长要求进行了解,把保护措施做到最好,使成活率得到保证。
在施工期间本人积极协调各单位之间的配合,在全项目部全体成员的密切配合下在施工期间未发生一起安全质量事故,在规定的工期内严格按照业主及施工图纸要求使工程顺利实现竣工验收。
在此工程中又让我学习到了绿化方面更加专业的知识,使自己的专业技术水平有了进步的提高。
2、×项目。
该工程总造价××元,约1,45公里,于××日开工,××日竣工,工期40天。
在该工程中我担任办公室内业资料管理及技术助理,因为以前少有接触公路工程,所以这次是我一个很好的学习机会。
在项目经理的领导下,全项目部成员积极协调配合齐心协力,严格按国家规范规程要求施工,按创精品工程细部做法要求,精心完成每一个分项工程,最终使工程顺利通过竣工验收,并得到建设单位、质检等部门的好评。
通过这个工程的学习,作为技术助理,在本次施工中,我掌握了工程技术人员的管理责任:一是合理安排进度计划、严格执行技术规范,确保工程质量,消灭质量事故,降低质量成本;二是根据设计要求与工程特点,运用自身技术优势,采用适用有效技术措施和合理方案,走经济和技术相结合的道路,为降低工程成本提高经济效益开拓途径;三是严格执行安全操作规程,减少一般事故,消灭重大人身伤亡事故和设备事故,降低事故成本。
it工程师年终工作总结范文5篇
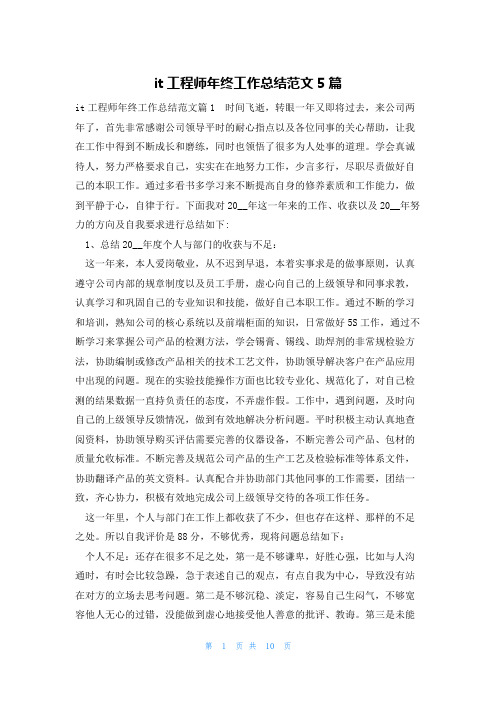
it工程师年终工作总结范文5篇it工程师年终工作总结范文篇1 时间飞逝,转眼一年又即将过去,来公司两年了,首先非常感谢公司领导平时的耐心指点以及各位同事的关心帮助,让我在工作中得到不断成长和磨练,同时也领悟了很多为人处事的道理。
学会真诚待人,努力严格要求自己,实实在在地努力工作,少言多行,尽职尽责做好自己的本职工作。
通过多看书多学习来不断提高自身的修养素质和工作能力,做到平静于心,自律于行。
下面我对20__年这一年来的工作、收获以及20__年努力的方向及自我要求进行总结如下:1、总结20__年度个人与部门的收获与不足:这一年来,本人爱岗敬业,从不迟到早退,本着实事求是的做事原则,认真遵守公司内部的规章制度以及员工手册,虚心向自己的上级领导和同事求教,认真学习和巩固自己的专业知识和技能,做好自己本职工作。
通过不断的学习和培训,熟知公司的核心系统以及前端柜面的知识,日常做好5S工作,通过不断学习来掌握公司产品的检测方法,学会锡膏、锡线、助焊剂的非常规检验方法,协助编制或修改产品相关的技术工艺文件,协助领导解决客户在产品应用中出现的问题。
现在的实验技能操作方面也比较专业化、规范化了,对自己检测的结果数据一直持负责任的态度,不弄虚作假。
工作中,遇到问题,及时向自己的上级领导反馈情况,做到有效地解决分析问题。
平时积极主动认真地查阅资料,协助领导购买评估需要完善的仪器设备,不断完善公司产品、包材的质量允收标准。
不断完善及规范公司产品的生产工艺及检验标准等体系文件,协助翻译产品的英文资料。
认真配合并协助部门其他同事的工作需要,团结一致,齐心协力,积极有效地完成公司上级领导交待的各项工作任务。
这一年里,个人与部门在工作上都收获了不少,但也存在这样、那样的不足之处。
所以自我评价是88分,不够优秀,现将问题总结如下:个人不足:还存在很多不足之处,第一是不够谦卑,好胜心强,比如与人沟通时,有时会比较急躁,急于表述自己的观点,有点自我为中心,导致没有站在对方的立场去思考问题。
ie工程师年终总结报告下年度计划

ie工程师年终总结报告下年度计划【标题】IE工程师年终总结报告及下年度计划【首段】尊敬的领导、全体同事:大家好!时光荏苒,转眼间又到了一年的尾声。
在此,我将以这份年终总结报告,回顾过去一年的工作,同时对下一年的计划进行规划和展望。
首先,我要感谢领导和团队的支持和帮助,使我得以在工作中不断成长和进步。
同时,我也要感谢与我并肩作战的同事们,是你们的团结和合作让整个团队取得了丰硕的成果。
【第一部分】年度工作回顾1. 参与项目工作在过去一年中,我主要负责了多个项目的开发与维护工作,包括ABC项目、DEF项目等。
在这些项目中,我参与了需求分析、技术方案设计、编码、测试等环节,并成功地完成了任务。
通过与团队的紧密合作,我们能够充分发挥各自的优势,解决了很多技术难题和工作中遇到的问题,有效提高了项目的整体进度和质量。
2. 技术能力提升作为一名IE工程师,技术能力的提升是我们保持竞争力的关键。
过去一年中,我不断加强自己的学习和训练,提高了自己在各个领域的技术水平。
我认真学习了新的开发工具、编程语言和框架,如Python、JavaScript、React等,通过实践应用,进一步提升了自己在前端开发、数据分析等方面的能力。
3. 团队合作与沟通在项目中,我与团队成员保持密切的合作与沟通。
与不同的同事合作,我学到了很多宝贵的经验和知识。
通过团队内部的交流与分享,我们能够快速解决问题,共同提升团队的整体实力。
我也积极参与团队的讨论和决策,为项目的发展和进展贡献自己的智慧和建议。
【第二部分】下年度工作计划1. 提升技术能力在下一年中,我将进一步提升自己的技术能力。
目前,前端开发和数据分析是行业的热点,我会继续学习和实践,在这两个方面取得更为深入的了解和能力。
同时,我也会关注最新的技术趋势和发展方向,不断学习新的知识和技能,以实现自身的职业成长和发展。
2. 加强项目管理与执行能力作为IE工程师,我们不仅仅需要具备技术能力,同时还需要具备一定的项目管理和执行能力。
2024年it工程师个人年终工作总结简洁版(3篇)

2024年it工程师个人年终工作总结简洁版时光荏苒,岁月如梭,转眼已经参加工作____年了,在这工作的____中,既有收获的踏实和欢欣,也有因不足带来的遗憾和愧疚。
在我工作的____年中,从____有限公司到____集团有限公司。
从铝业建设的行业转变为煤化工建设的行业中。
无疑对我来说是一个巨大的挑战,幸亏在领导和师傅的指导下,较好的融入了这种紧张和严谨的工作氛围中,较好地完成了领导安排各项工作,自身的业务素质和工作能力有了较大提高,对工作有了更多的自信。
过去的六年,我参与了许多设备现场安装及调试工作,从中受益匪浅,不仅学到了很多专业知识,对设备安装及调试有了更全面的理解和把握,而且培养了我作为机械工程师所应该具备的基本素质。
我认真工作,坚持自学,提高了理论水平。
具体总结如下:一、学习时段的工作成绩我是一名刚踏入社会的大学毕业生,____毕业于____高等专科学校房屋设备安装工程专业,作为一名新员工。
参加公司的培训工作。
了解了公司的基本情况,了解了自己在公司岗位工作的基本工作和任务。
作为一名新员工,我也积极地参加公司组织的其它培训,学到了许多以前没有接触到的知识和理念。
正式进入工作岗位后,起初,感到一切都很茫然,我虽然是学设备安装专业的,在学校只学习了一些理论知识,实践的机会很少,施工工地成了我学习和实践的好地方。
在工地后发现以前在学校学的理论知识太肤浅,工作起来非常困难,在工地我就向工人师傅虚心的请教,有不明白的地方我就问。
对这些设备图纸看起来都是很忙然,只有走上工作岗位后,才知道自己的学识很肤浅,要学习的东西很多,所以,我就虚心向师傅请教,多问,多看图纸,立足于岗位工作,从基本做起不怕不会,就怕不学,不问。
在____一年的学习期间,由于我勤奋好学,加上师傅的指导有方,很快,就对公司的建设有了基本的了解。
在这段时间里,我跟着师傅编制了青铜峡铝业工程建设的施工组织设计方案,细心研究施工图纸,提出施工时所需要的施工材料计划。
ie工程师年终总结报告

ie工程师年终总结报告ie工程师岗位职责篇一【生产车间布局规划】主导设计生产区域布局,协助拟定调整规划和搬迁计划,协助监督和协调实施进度。
主导提出新工厂的建设、装修要求,与厂房规划部门的同事配合完成新工厂的建设。
【新品量产前的工作】1、评估产品标准工时与产能、制造及人力成本和产线平衡率目标2、确定产品生产排线情况及人力配置,场地安排,提供参照排线表【量产后的生产现场工作】1、提供所有量产产品的计划工时定额及现行工时定额,更新工艺更改后的产品标准工时。
2、运用取消、合并、重排、简化等手法,对当前的制造流程及工艺进行优化和改善。
3、主导生产现场物流的优化,并进行小规模的布局变动改善4、负责生产车间可视化管理的规划设计5、生产班组绩效方案的推行与实施,监督和反馈绩效考核的结果知识:1、7年以上IE工作经验,有过2个以上汽车行业量产项目生产线布局开发经验,精通生产规划、节拍管理、产线优化工作;2、掌握方法研究和作业测定的基本方法,熟悉IE七大手法及其他工艺改善手法3、熟悉生产现场布置原则并掌握物流分析方法,熟练掌握AUTO CAD的用法;4、熟悉或掌握至少一项电机、变速器、减速器或控制器的装配工艺路线和关键工艺参数控制,;技能:1、熟练使用AUTO CAD、visfactory进行厂房布局设计;2、具备良好的工艺准备和实施控制能力;3、具备较好的分析问题和指导现场的能力;ie工程师岗位职责篇二1、负责微波/红外感应开关控制器产品的设计研发工作,有3年以上相关产品设计工作;2、能独立完成项目要求的总体设计(方案设计、器件选型、原理图设计、PCB设计、结构设计、产品调试测试等工作),并对设计质量负责;3、能独立完成编写各种技术文档;4、对开关电源生产加工各环节及工艺有较强的把控能力;5、工作责任感强,有较强的钻研精神和团队合作意识。
ie工程师岗位职责篇三职责:1、存储、服务器、云计算售后技术支持工程师;2、负责项目主机存储系统建设的实施方案设计、系统调试、系统测试;3、负责主流主机、存储、备份设备的安装调试;4、负责项目协调工作;5、负责存储、云计算项目的售后技术支持;6、负责设备的安装及调试。
2024年it工程师个人年终工作总结14篇
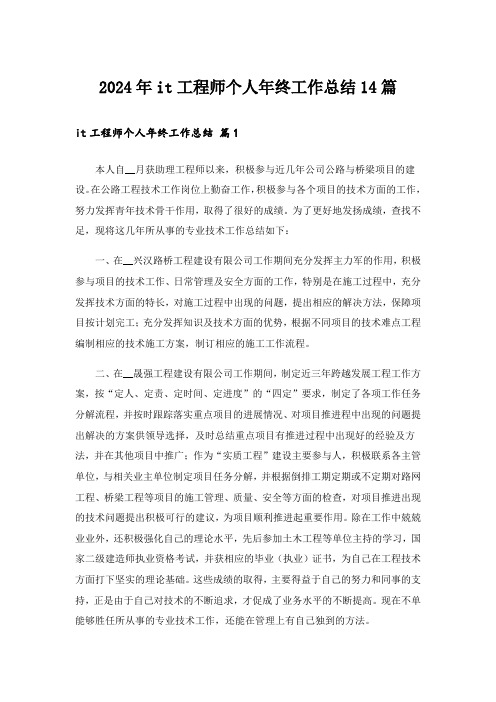
2024年it工程师个人年终工作总结14篇it工程师个人年终工作总结篇1本人自__月获助理工程师以来,积极参与近几年公司公路与桥梁项目的建设。
在公路工程技术工作岗位上勤奋工作,积极参与各个项目的技术方面的工作,努力发挥青年技术骨干作用,取得了很好的成绩。
为了更好地发扬成绩,查找不足,现将这几年所从事的专业技术工作总结如下:一、在__兴汉路桥工程建设有限公司工作期间充分发挥主力军的作用,积极参与项目的技术工作、日常管理及安全方面的工作,特别是在施工过程中,充分发挥技术方面的特长,对施工过程中出现的问题,提出相应的解决方法,保障项目按计划完工;充分发挥知识及技术方面的优势,根据不同项目的技术难点工程编制相应的技术施工方案,制订相应的施工工作流程。
二、在__晟强工程建设有限公司工作期间,制定近三年跨越发展工程工作方案,按“定人、定责、定时间、定进度”的“四定”要求,制定了各项工作任务分解流程,并按时跟踪落实重点项目的进展情况、对项目推进程中出现的问题提出解决的方案供领导选择,及时总结重点项目有推进过程中出现好的经验及方法,并在其他项目中推广;作为“实质工程”建设主要参与人,积极联系各主管单位,与相关业主单位制定项目任务分解,并根据倒排工期定期或不定期对路网工程、桥梁工程等项目的施工管理、质量、安全等方面的检查,对项目推进出现的技术问题提出积极可行的建议,为项目顺利推进起重要作用。
除在工作中兢兢业业外,还积极强化自己的理论水平,先后参加土木工程等单位主持的学习,国家二级建造师执业资格考试,并获相应的毕业(执业)证书,为自己在工程技术方面打下坚实的理论基础。
这些成绩的取得,主要得益于自己的努力和同事的支持,正是由于自己对技术的不断追求,才促成了业务水平的不断提高。
现在不单能够胜任所从事的专业技术工作,还能在管理上有自己独到的方法。
当然这些成绩的取得只能代表过去,面对新材料,新技术在公路工程行业不断应用的新局面,特别是现代融资方法、施工工艺不断更新的前提下,自己还有许多需要学习的地方。
ie工程师年终工作总结范文模板

ie工程师年终工作总结范文模板ie工程师年终工作总结总结在一个时期、一个年度、一个阶段对学习和工作生活等情况加以回顾和分析的一种书面材料,写总结有利于我们学习和工作能力的提高,因此我们需要回头归纳,写一份总结了。
总结怎么写才能发挥它的作用呢?下面是整理的ie工程师年终工作总结,仅供参考,希望能够帮助到大家。
ie工程师年终工作总结1自20xx年参加工作,到现在已经有一年多的时间了,在过去的日子里,本人主要负责核心技术领域,信息中心机房扩展设计与建设维护,报业信息系统建设与项目管理,网络与网络安全设计与研究完善,技术管理创新,以及协助推进报业集团信息生产一体化等工作。
严格履行个人岗位职责,认真学习,努力工作,较好地完成了本职工作和领导交给的各项任务.一、良好的思想政治表现我为人处事的原则是“认认真真学习,踏踏实实工作,堂堂正正做人,开开心心生活”,对自己,我严格要求,工作认真,待人诚恳,言行一致,表里如一。
做到遵纪守法,谦虚谨慎,作风正派,具有良好的思想素质和职业道德。
积极要求进步,团结友善,明礼诚信。
在先进性教育主题演讲比赛中获得过三等奖,“知荣明耻X社”演讲比赛中获得过三等奖,“我为报社改革发展献一策”活动中获得过三等奖。
连续四年被评为集团先进工作者,并获得过“市属机关优秀X 员”称号。
二、负重锻炼,鼓劲挖潜,较好地完成本职工作X集团正朝着规模化、多媒体化、多元化,网络化的方向快速发展,生产规模、管理理念、业务流程等都发生了很大的变化,在X 快速变革时期,记者编辑的数量增加,集团办公区域的扩大,并且在技术人员不足的环境条件下,集团采编流程,经营流程,网络安全,机房建设,信息化成本研究等方面的都进行了较大规模的设计建设与完善。
在信息建设的过程中,一方面在较少技术支持下独立研究项目的合理性,科学性,安全性,另一方面又要面对很多系统与网络核心维护,以及大量其他技术人员无法解决的问题。
在X集团这些日子里,较好的完成了集团领导下达的责任目标。
it工程师个人年终工作总结6篇
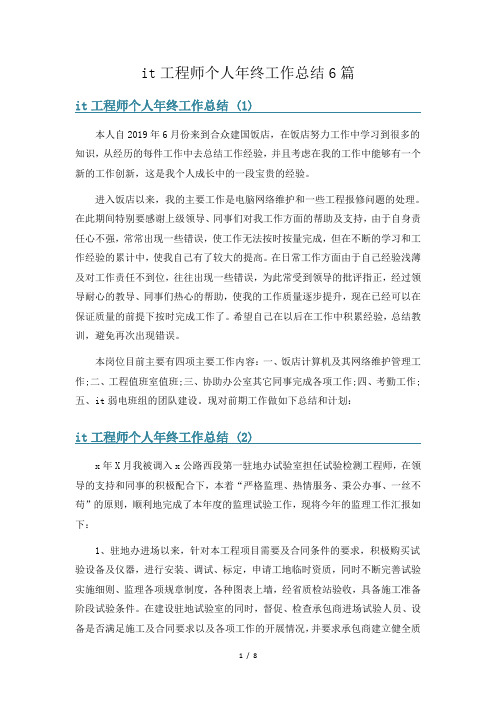
it工程师个人年终工作总结6篇it工程师个人年终工作总结 (1) 本人自2019年6月份来到合众建国饭店,在饭店努力工作中学习到很多的知识,从经历的每件工作中去总结工作经验,并且考虑在我的工作中能够有一个新的工作创新,这是我个人成长中的一段宝贵的经验。
进入饭店以来,我的主要工作是电脑网络维护和一些工程报修问题的处理。
在此期间特别要感谢上级领导、同事们对我工作方面的帮助及支持,由于自身责任心不强,常常出现一些错误,使工作无法按时按量完成,但在不断的学习和工作经验的累计中,使我自己有了较大的提高。
在日常工作方面由于自己经验浅薄及对工作责任不到位,往往出现一些错误,为此常受到领导的批评指正,经过领导耐心的教导、同事们热心的帮助,使我的工作质量逐步提升,现在已经可以在保证质量的前提下按时完成工作了。
希望自己在以后在工作中积累经验,总结教训,避免再次出现错误。
本岗位目前主要有四项主要工作内容:一、饭店计算机及其网络维护管理工作;二、工程值班室值班;三、协助办公室其它同事完成各项工作;四、考勤工作;五、it弱电班组的团队建设。
现对前期工作做如下总结和计划:it工程师个人年终工作总结 (2) x年X月我被调入x公路西段第一驻地办试验室担任试验检测工程师,在领导的支持和同事的积极配合下,本着“严格监理、热情服务、秉公办事、一丝不苟”的原则,顺利地完成了本年度的监理试验工作,现将今年的监理工作汇报如下:1、驻地办进场以来,针对本工程项目需要及合同条件的要求,积极购买试验设备及仪器,进行安装、调试、标定,申请工地临时资质,同时不断完善试验实施细则、监理各项规章制度,各种图表上墙,经省质检站验收,具备施工准备阶段试验条件。
在建设驻地试验室的同时,督促、检查承包商进场试验人员、设备是否满足施工及合同要求以及各项工作的开展情况,并要求承包商建立健全质量自检体系,为顺利开工奠定基础。
2、开工前,首先按照设计图纸及规范要求,对承包商提出的各种原材料、砼配合比、土及石灰土标准击实进行标准、验证试验,使各项指标均满足施工规范及设计图纸要求,为全面施工提供可靠、准确的试验依据。
ie工程师年终工作总结6篇

ie工程师年终工作总结6篇ie工程师年终工作总结 (1) 从八月份入职至今,已一年过去了,回顾自己这段时间在__单位所走过的路,所经历的事情,没有太多的感慨,没有太多的惊喜,却多了一份镇定,多了一份从容。
回想入职初,在__月份,从开始第一周熟悉工作环境,第二周便参与煤矿安全生产管理系统的相关文档设计工作,期间在项目组各位同事的指导、安排下,进行了系统的软件开发委托合同书及系统功能模块设计说明文档的编写,也借此过程学习煤矿生产业务。
在__月份,便正式参与了管理软件功能模块的设计工作,在张工的指导、讲解下初次尝试完成了管理软件的维护子系统的功能模块设计;在九月中旬跟随单位施工人员在_一号矿进行业务调研,从而在我们自己的管理系统中,取其长、补其短,也借此机会了解实际的.煤矿生产情况,加深对煤矿产业业务流程的理解;在九月底便根据张工的指导开始工程技术文档子系统的功能模块设计。
__月份,在张工张工的指导下,进行了物资管理子系统的功能模块设计,并就设计的正确性、合理性分别同张工张工及何工进行讨论;到十月中旬管理软件的各子系统功能模块基本全部设计完成;十月底,根据各子系统模块设计搜集系统数据,建立初步的数据字典及概念模型,为后期数据库设计做准备。
__月份的工作以整理系统业务关系与业务流为主,但由于业务关系图的表现形式不够合理,不足以清晰、明了得表现出各层次关系,导致工作多走了几个环节,好在张工张工及时发现问题,并多次向我指导、讲解,最终决定以列表结合流程图形式搜集、汇总系统所有子模块的业务动作、涉及人员及联系模块,为后面工作的展开提供依据。
__围绕两个工作展开,一是系统业务描述文档的设计编写,因为该文档是日后编程人员了解煤矿生产业务、系统功能及数据库设计的主要依据,张工张工也多次强调,文档的设计务必从读者角度考虑问题,因此最终设计由简单到复杂,由整体到具体,各层次尽量做到衔接紧密,易于理解;另一项工作是针对已完成的关系列表、系统功能模块设计的业务合理性、正确性和张工张工逐条讨论,并将设计中出现的问题逐条记录在问题跟踪文档中。
ie万能个人年终总结

ie万能个人年终总结在以"IE万能个人年终总结"为题目的内容中,我将按照个人年终总结的格式来书写。
请阅读以下内容:首先,我要感谢公司提供这个机会,让我能够写下自己的个人年终总结。
在过去的一年里,我作为一名IE(工业工程师)在公司的工作岗位上取得了一定的成绩,并积累了一些经验和教训。
以下是我个人年终总结的内容:一、工作成果及贡献在过去一年里,我在工作中付出了努力并取得了以下一些工作成果:1. 优化生产流程:通过分析和调整生产流程,我成功地提高了生产效率和产品质量,并降低了成本。
2. 成本控制:通过有效的物料管理和资源分配,我成功地控制了生产成本,并使公司在激烈的市场竞争中保持了竞争优势。
3. 团队协作:我与同事们建立了良好的合作关系,并积极参与团队项目,共同完成了一些重要的任务和项目。
二、职业发展与学习作为一名工程师,我深知职业发展与学习的重要性,并在过去的一年中注重提升自己的技能和知识:1. 学习新技术:我参加了多个培训课程和研讨会,学习了新的工程软件和技术应用,提高了自己的工程设计和分析能力。
2. 专业认证:为了提升自己的专业水平,我积极准备并顺利通过了IE领域的相关认证考试,如六西格玛、工业工程师等认证。
3. 实践经验:我积极参与公司内部的项目和任务,并通过实际操作和项目管理,不断丰富自己的经验和技能。
三、问题与改进在工作中,我也遇到了一些问题和挑战。
以下是我总结出的一些问题,并给出了相应的改进方案:1. 沟通不畅:由于工作中需要与多个部门和团队合作,我意识到沟通不畅可能会导致工作中的问题和误解。
因此,我决定加强与团队的沟通,提高信息交流的效率和准确性。
2. 时间管理:有时我会在时间管理方面存在一定的困难,导致工作进度出现滞后。
为了改进这个问题,我正在学习和应用时间管理技巧,并制定详细的工作计划和任务安排。
3. 自我反思与提升:我意识到在工作中出现的问题和挑战是自我提升的机会,因此我会持续进行自我反思,并积极寻找解决问题的方法和策略。
ie工程师年终工作总结
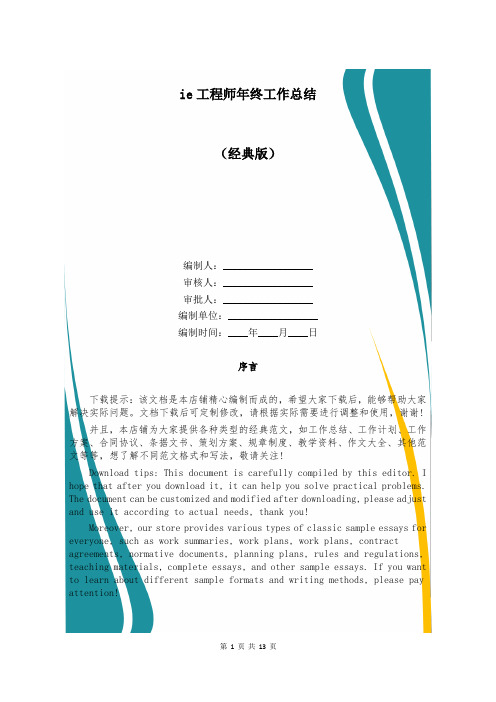
ie工程师年终工作总结(经典版)编制人:__________________审核人:__________________审批人:__________________编制单位:__________________编制时间:____年____月____日序言下载提示:该文档是本店铺精心编制而成的,希望大家下载后,能够帮助大家解决实际问题。
文档下载后可定制修改,请根据实际需要进行调整和使用,谢谢!并且,本店铺为大家提供各种类型的经典范文,如工作总结、工作计划、工作方案、合同协议、条据文书、策划方案、规章制度、教学资料、作文大全、其他范文等等,想了解不同范文格式和写法,敬请关注!Download tips: This document is carefully compiled by this editor. I hope that after you download it, it can help you solve practical problems. The document can be customized and modified after downloading, please adjust and use it according to actual needs, thank you!Moreover, our store provides various types of classic sample essays for everyone, such as work summaries, work plans, work plans, contract agreements, normative documents, planning plans, rules and regulations, teaching materials, complete essays, and other sample essays. If you want to learn about different sample formats and writing methods, please pay attention!ie工程师年终工作总结ie工程师年终工作总结总结是指社会团体、企业单位和个人对某一阶段的学习、工作或其完成情况加以回顾和分析,得出教训和一些规律性认识的一种书面材料,它能帮我们理顺知识结构,突出重点,突破难点,快快来写一份总结吧。
ie工程师年终工作总结6篇

ie工程师年终工作总结6篇ie工程师年终工作总结 (1) 进入公司工程管理部工作将近一年了,时光飞速而逝,而这期间的感受也像五味瓶—酸甜苦辣咸一应俱全,在公司领导强有力的领导及关心支持下,作为一个应届毕业生的我,学会了怎么与人共处,该如何做好工作;并让我很快完成了从学生到职员的转变,让我较快适应了公司的工作环境。
回首这一年的工作,内心充满着激动,也让我有着无限感慨。
新的一年工作伊始,很有必要认真总结去年的工作收获,以良好的姿态你去迎接全新的挑战,总结是工作的归类,是自我反省自我升华的过程,命运掌握在自己的手中,事业在于奋斗,逆流而上,生生不息,争取早日成为一名合格的土建工程师,为公司交一份满意的答卷,使自身价值得以体现。
现将20__年的工作情况作出如下总结:一、上年度工作情况1、熟悉了解公司各项规章我于20__年2月进入公司工程管理部,为更好更快的融入公司这个团队,为以后的工作打好铺垫,我加紧对公司各项规章制度的了解,熟悉公司的企业文化。
通过了解和熟悉,我为能进入公司这个团队而感到自豪,同时也能感觉到自身的压力。
在工作中我将以公司的各项规章制度为准则,严格要求自己,廉洁自律,在坚持原则的情况下敢于创新,更好更快的完成工作任务。
2、熟悉工程结构,现场情况作为工程管理部的一员,工作侧重点就是在工地。
初到工程部我首先对照相关设计图纸熟悉现场,详细了解现场平面布置情况、管理体系、施工情况、质量情况、进度计划及实际形象进度情况、特殊部位的特殊情况。
这一年中我主要负责天然气室内外工程、防盗门安装工程以及辅助管理14#楼主体工程。
在这近一年中,我学到了很多,经历了很多,认识到了自己的不足,也让自己成长了很多。
天然气室内外工程,室外工程已经全部按期完工,室内工程1#、2#、3#、5#、9#楼立管安装完成,4#、6#、7#、8#、10#、11#、12#、13#楼楼板开洞将于20__年1月10日前全部完成,剩余燃气工程将于20年3月15日前全部完成确保交房的顺利进行。
服装厂ie年底工作总结(3篇)

第1篇一、前言随着我国经济的快速发展,服装行业作为劳动密集型产业,在国内外市场占有重要地位。
作为服装厂的IE工程师,我深感责任重大。
在过去的一年里,我积极参与工厂的生产、管理、改进等工作,努力提高生产效率,降低生产成本,确保产品质量。
现将我本年度的工作进行总结,以便为今后的工作提供借鉴。
二、工作回顾1. 生产计划与调度(1)根据市场需求,制定合理的生产计划,确保各生产线有序进行。
(2)优化生产流程,提高生产效率,缩短生产周期。
(3)协调各部门,确保生产计划的顺利实施。
2. 设备管理(1)对生产设备进行定期检查、维护,确保设备正常运行。
(2)发现设备故障,及时上报,组织维修,降低设备停机时间。
(3)对设备操作人员进行培训,提高操作技能,确保生产安全。
3. 人员管理(1)根据生产需求,合理配置人力资源,提高员工工作效率。
(2)开展员工培训,提高员工技能水平,提升整体素质。
(3)关心员工生活,营造和谐的工作氛围。
4. 生产过程改进(1)对生产过程中的瓶颈环节进行分析,提出改进措施。
(2)实施改进措施,降低生产成本,提高生产效率。
(3)对改进效果进行跟踪评估,持续优化生产过程。
5. 质量管理(1)严格执行质量管理体系,确保产品质量符合标准。
(2)对不合格品进行统计分析,找出原因,制定整改措施。
(3)对生产过程进行监督,确保产品质量。
6. 节能减排(1)开展节能减排活动,提高员工节能意识。
(2)优化生产流程,降低能源消耗。
(3)推广节能设备,提高能源利用率。
三、工作亮点1. 优化生产流程,提高生产效率,缩短生产周期,降低生产成本。
2. 通过设备维护和培训,降低设备故障率,提高设备利用率。
3. 实施生产过程改进,提高产品质量,满足客户需求。
4. 落实节能减排措施,降低能源消耗,为环保事业贡献力量。
5. 营造和谐的工作氛围,提高员工满意度,增强团队凝聚力。
四、工作不足1. 对生产过程中存在的问题分析不够深入,改进措施不够具体。
IT工程师年终工作总结15篇

IT工程师年终工作总结IT工程师年终工作总结15篇总结在一个时期、一个年度、一个阶段对学习和工作生活等情况加以回顾和分析的一种书面材料,它可以促使我们思考,为此要我们写一份总结。
那么你知道总结如何写吗?下面是小编收集整理的IT工程师年终工作总结,欢迎大家借鉴与参考,希望对大家有所帮助。
IT工程师年终工作总结1时光荏苒,如今xx年的帷幕已经谢下,xx年的钟声已经敲响,在公司高层的正确领导下,我们佰腾科技又走过了一年。
而我也在自己的努力以及同事的帮助下完成了20xx年我所负责的工作,以下就是我对过去这一年的工作总结:一、测试工作及经验作为软件部测试组的一员,首先要做好的就是自己的本职工作,我在20xx年中所做的工作主要有:XXXX测试用例的编写,对系统的测试、跟踪;XXXX需求、高保图、界面和功能的测试;XXXX功能测试用例的编写,高保图、系统的测试;XXXX的静态页面测试和功能测试;XXXX的功能测试;XXXX第一、二、三迭代高保图测试,测试用例编写,静态页面和功能测试,并主持参与测试用例评审;XXXX平台高保图的测试和系统静态页面、功能的测试;XXXX的高保图测试和测试用例的编写;XXXX的静态页面和功能测试,参与测试用例的评审;XXXX的高保图测试、静态页面和功能测试;XXXX用户使用手册的编写;一年的工作,让我获得很多方面的经验:1.编写逻辑覆盖率全的测试用例甚为重要。
在理解需求的前提下编写测试用例,使得我掌握了多种测试用例编写方法,更让我对产品的需求有更加深入的理解,须知对需求是否理解透彻决定了能否有效、全面地对产品进行测试;2.要站在用户角度对系统进行测试。
从一些项目中出现的未能及时发现的bug中,我认识到用户体验的重要性,现在能够越来越多的从这方面来执行测试;3.对拿到手的项目有较清晰的思路,能够更加快速、准确地发现问题;4.越来越规范的工作流程的让我们的工作有条不紊的进行,让我深刻认识到工作的规范性是多么的重要,并且从中学习如何从文档和流程上规范工作。
ie个人年终工作总结

尊敬的领导,亲爱的同事们:随着岁月的流转,我们即将告别充满挑战与收获的一年。
在这一年中,我在公司领导的正确指引和同事们的无私帮助下,不断学习、进步,现将个人年终工作总结如下:一、工作回顾1. 熟练掌握IE工作流程和方法在过去的一年里,我积极参加公司组织的IE培训,认真学习IE理论知识,熟练掌握了IE工作流程和方法。
通过运用IE工具,提高了工作效率,降低了生产成本。
2. 优化生产流程,提高生产效率针对生产过程中存在的问题,我积极与生产部门沟通,分析原因,提出改进措施。
通过优化生产流程,减少了生产过程中的浪费,提高了生产效率。
3. 推进精益生产,降低生产成本为了进一步降低生产成本,我主动学习精益生产理念,将精益生产方法应用到实际工作中。
通过推行5S、看板管理等手段,提高了生产现场管理水平,降低了生产成本。
4. 加强团队协作,提高团队凝聚力在团队协作方面,我注重与同事沟通交流,关心团队成员的成长。
通过组织团队活动,增强了团队凝聚力,提高了团队整体战斗力。
5. 积极参加公司各项活动,展现个人风采在过去的一年里,我积极参加公司组织的各项活动,如篮球赛、知识竞赛等,充分展现了个人风采,为公司树立了良好的形象。
二、工作反思1. 专业能力有待提高尽管我在IE方面取得了一定的成绩,但与行业先进水平相比,我的专业能力仍有待提高。
在新的一年里,我将加强学习,不断提高自己的专业素养。
2. 沟通协调能力需加强在工作中,我发现自己在沟通协调方面还存在不足。
今后,我将努力提高沟通协调能力,更好地为团队和公司服务。
3. 工作态度需更加严谨在过去的一年里,我在工作中偶尔会出现马虎大意的情况。
新的一年,我将严格要求自己,对待工作更加严谨,确保工作质量。
三、展望未来新的一年,我将继续努力,以更加饱满的热情投入到工作中。
具体目标如下:1. 提升专业能力,成为行业精英2. 加强团队协作,提高团队凝聚力3. 优化生产流程,降低生产成本4. 丰富工作经验,为公司创造更多价值最后,感谢公司领导和同事们在过去一年里的关心与支持,让我在工作中不断成长。
ie工程师年终工作总结

ie工程师年终工作总结ie工程师年终工作总结总结是指社会团体、企业单位和个人在自身的某一时期、某一项目或某些工作告一段落或者全部完成后进行回顾检查、分析评价,从而肯定成绩,得到经验,找出差距,得出教训和一些规律性认识的一种书面材料,它可以提升我们发现问题的能力,让我们抽出时间写写总结吧。
我们该怎么去写总结呢?以下是小编帮大家整理的ie工程师年终工作总结,欢迎阅读与收藏。
ie工程师年终工作总结1时光荏苒,××年即将过去,回首过去的一年,内心不禁感慨万千……时间如梭,转眼间又将跨过一个年度之坎。
回首望,虽没有轰轰烈烈的战果,但也算经历了一段不平凡的考验和磨砺。
对于我们每一个追求进步的人来说,免不了会在年终岁未对自己进行一番盘点,也算是对自己的一种鞭策。
行政人事部是公司的关键部门之一,对内管理水平的要求应不断提升,对外要应对税务、工商、药监、社保等机关的各项检查。
行政人事部人员虽然少,但在这一年里任劳任怨,竭尽全力将各项工作顺利完成。
经过一年的磨练与洗礼,行政人事部的综合能力相比××年又迈进了一步。
回顾年,在公司领导的正确领导下,我们的工作着重于公司的经营方针、宗旨和效益目标上,紧紧围绕重点展开工作,紧跟公司各项工作部署。
在管理方面尽到了应尽的责任。
为了总经验,继续发扬成绩同时也克服存在的不足,现将××年的工作做如下简要工作总。
年行政人事部工作大体上可分为以下三个方面:一、人事管理方面根据部门人员的实际需要,有针对性、合理地招聘一批员工,以配备各岗位。
规范了各部门的人员档案并建立电子档案,严格审查全体员工档案,对资料不齐全的一律补齐。
配合采购和财务部门,严格把好促销员的进、出关。
有步骤的完善培训机制,不断的外派员工学习并要求知名公司来培训员工,同时加强内部的培训管理工作。
二、行政工作方面⒈办理好各门店的证照并如期进行年审工作。
⒉和相关职能机关如工商、税务、药监、社保、银行等做好沟通工作,以使公司对外工作更为通畅。
ie年终工作总结个人

一、前言时光荏苒,转眼间一年又即将过去。
在过去的一年里,我作为IE部门的一员,在公司的领导和同事们的支持下,认真履行职责,努力提升自身能力,为公司的发展贡献了自己的一份力量。
现将我在IE部门的年终工作总结如下:二、工作回顾1. 项目优化与改进在过去的一年里,我参与了多个项目的IE优化工作。
通过对生产流程的细致分析,我发现并解决了多个生产瓶颈问题,提高了生产效率。
具体包括:(1)优化生产流程,缩短生产周期,提高生产效率10%。
(2)针对关键工序进行设备改造,降低设备故障率,提高设备利用率。
(3)改进物料配送方式,减少物料浪费,降低成本。
2. 成本控制与降本增效在成本控制方面,我通过以下措施实现了降本增效:(1)优化采购流程,降低采购成本5%。
(2)通过数据分析,发现并消除生产过程中的浪费,降低生产成本3%。
(3)加强库存管理,降低库存成本2%。
3. 团队建设与个人成长(1)积极参与团队活动,与同事们建立了良好的沟通与合作关系。
(2)通过参加各类培训,不断提升自己的专业技能和综合素质。
(3)协助部门负责人进行团队建设,提高团队凝聚力。
三、工作亮点1. 创新思维在IE工作中,我始终保持创新思维,敢于尝试新方法、新技术,为公司的生产优化和成本控制提供了有力支持。
2. 团队协作我深知团队协作的重要性,在与同事们的共同努力下,成功完成了多项工作任务。
3. 持续改进在IE工作中,我始终坚持持续改进的理念,不断优化工作流程,提高工作效率。
四、不足与展望1. 不足之处(1)在数据分析方面,还需进一步提升自己的专业能力。
(2)在团队管理方面,还需加强沟通与协调能力。
2. 展望未来(1)在新的一年里,我将努力提升自己的专业能力,为公司创造更多价值。
(2)加强与同事们的沟通与协作,共同推动IE部门的发展。
(3)关注行业动态,紧跟技术发展趋势,为公司提供更具前瞻性的IE解决方案。
总之,过去的一年,我在IE部门的工作中取得了一定的成绩,但同时也认识到自己的不足。
ie工程年终个人工作总结
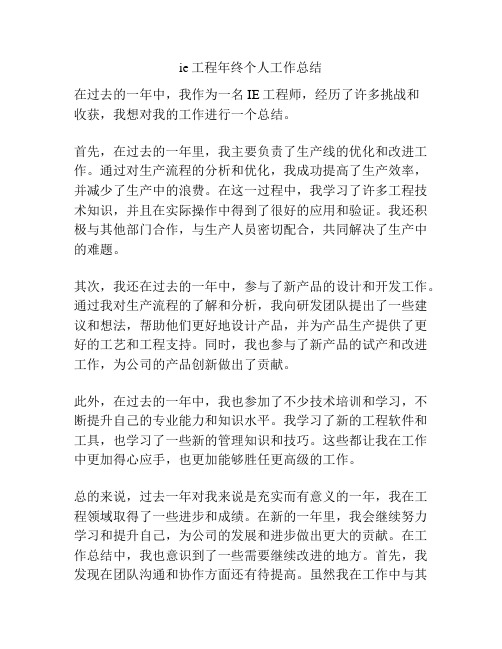
ie工程年终个人工作总结在过去的一年中,我作为一名IE工程师,经历了许多挑战和收获,我想对我的工作进行一个总结。
首先,在过去的一年里,我主要负责了生产线的优化和改进工作。
通过对生产流程的分析和优化,我成功提高了生产效率,并减少了生产中的浪费。
在这一过程中,我学习了许多工程技术知识,并且在实际操作中得到了很好的应用和验证。
我还积极与其他部门合作,与生产人员密切配合,共同解决了生产中的难题。
其次,我还在过去的一年中,参与了新产品的设计和开发工作。
通过我对生产流程的了解和分析,我向研发团队提出了一些建议和想法,帮助他们更好地设计产品,并为产品生产提供了更好的工艺和工程支持。
同时,我也参与了新产品的试产和改进工作,为公司的产品创新做出了贡献。
此外,在过去的一年中,我也参加了不少技术培训和学习,不断提升自己的专业能力和知识水平。
我学习了新的工程软件和工具,也学习了一些新的管理知识和技巧。
这些都让我在工作中更加得心应手,也更加能够胜任更高级的工作。
总的来说,过去一年对我来说是充实而有意义的一年,我在工程领域取得了一些进步和成绩。
在新的一年里,我会继续努力学习和提升自己,为公司的发展和进步做出更大的贡献。
在工作总结中,我也意识到了一些需要继续改进的地方。
首先,我发现在团队沟通和协作方面还有待提高。
虽然我在工作中与其他部门合作良好,但我意识到在一些工作中,我还需要更主动地去沟通和协调。
因此,我会在新的一年里加强与团队成员之间的沟通和协作,更好地融入团队,做好统筹规划,创造更加良好的工作氛围。
其次,我也意识到个人的技术提升不能停止,工程领域的知识更新迭代很快,我需要不断学习新的技术和知识,包括新的工程工具、新的工艺技术等。
我计划在新的一年里参加更多的技术培训和学习,不仅提升自己的技术水平,还能为公司的技术创新和进步做出更大的贡献。
另外,在工作总结中,我也要感谢公司和领导对我的支持和信任。
公司提供了良好的工作环境和机会,让我在工程领域得到了全面的提升和发展。
ie工程师年终工作总结(精选4篇)

ie工程师年终工作总结(精选4篇)ie工程师年终工作总结共四篇1(2364)字时光荏苒,不知不觉中,12个多月的时光匆匆溜走。
回顾以往,机电工作有收获也有不足,我们紧紧围绕安全生产方针,认真执行《煤矿安全规程》,以人为本,与时俱进,狠抓管理,基本实现了机电系统的安全、安装,稳定、经济、高效运行。
通过这以往的工作,大家积累了大量的工作经验,各方面都得到了较大的充实和提高。
现就机电工作情况作以总结汇报。
一、立足安全规程,强化机电安全质量标准化安全质量标准化是煤矿提高水平、建设安全生产长效机制的根本途径,只有安全质量标准化达到并保持一定的标准,使公司处于安全生产的良好状态,才能够适应和保障员工生命安全和煤炭工业现代化建设的需要。
从3月份开始,我们以条件最差的二采区集运巷为突破口,打造2210集运巷、二采区变电所、采区机电设备达标及电缆吊挂达标等工作,带动全矿各范围以此为基点,在全矿范围内掀起了新一轮大搞质量标准化建设的热潮。
通过达标评比,共评出“精品硐室”3处,“精品机房”2处。
二、机电工作完成情况1、以来,机电科紧紧围绕创建安全质量标准化“示范矿井”工作目标。
先后对二采区变电所进行了标准化硐室改造,实现了变电所内高低压设备布置精细化;高低压动力电缆及照明吊挂实现了“一线化”,重新更换新型塑料电缆钩共计3981组,铺设达标高低压电缆、信号电缆共计5971.5米。
实现井下电缆横竖一条线吊挂。
经过改造后,在井下机电硐室、大巷及采区电缆形成了新的亮点工程,提升了井下标准化水平。
2、由于受地质条件的制约,180万吨的产量使其采煤工作面综机设备的安装及工作面供电系统改造成为一项安全生产的重点工程。
全年安全顺利的完成了2213工作面、2200回采工作面、2110工作面、1203工作面、2212工作面5个工作面的综机设备安装、供水、压风系统的安装及供电系统改造;并安全顺利的完成2213工作面、2207工作面、2209工作面、2110工作面、2200回采工作面的撤面工作,实现了全年按面、撤面、供电的安全生产。
- 1、下载文档前请自行甄别文档内容的完整性,平台不提供额外的编辑、内容补充、找答案等附加服务。
- 2、"仅部分预览"的文档,不可在线预览部分如存在完整性等问题,可反馈申请退款(可完整预览的文档不适用该条件!)。
- 3、如文档侵犯您的权益,请联系客服反馈,我们会尽快为您处理(人工客服工作时间:9:00-18:30)。
2016年年度工作总结品质工程部—刘文东时间飞逝,转眼一年又即将过去,同时,也是自己加入公司整整一周年时间,审视自己一年来的工作,感触很多,在收获了很多宝贵的经验教训的,通过自身在工作中提升了自我,也同时发现了自我工作中的不足和待改善之处。
回顾过去的一年工作,现总结如下:一、关于产品标准工时长期以来,我司的工时管理执行的不是很理想,工时表格分散、过多,产品标准工时在制定后即无人维护,导致产品标准工时与实际相差过大。
且同一产品中同时存在多个不同版本的标准工时,导致生产效率统计混乱,标准工时无法起到应有的作用。
如下为几处典型的案例:1、产品工时分散、且同一产品的工时版本过多且不统一。
1.2、产品工时表格过多、分散,维护和产品统计困难,如下表所因表格过于分散,无法统计完全。
)评估,首要的一点是产品标准工时要符合生产的实际状况。
2、改善方案的制定及工时的评估、实施和制定产实际导入的跟进,改善了之前的产品工时报表分散、表格过多和重复发布工时的现象,在新导入的产品生产流程实施后,产品生产效率有显著的提升,且新发布的《产品标准工时明细汇总表》中产品标准工时能合理的反映出生产的实际状况。
2.2、改善后效果2.2.1、统一产品标准工时汇总表为改善我司长期以来产品工时报表过多、工时重复发布、工时版本过多和因产品工时表格过多而导致的工时维护困难的现象,依据公司产品ERP编码规则和产品工艺特性,制作了《产品标准工时明细汇总表》,即将产品标准工时依据ERP 编码汇总到统一的表格中,方便生产查询、工时维护和产品成本的核算产品汇总到一起,以方便统计和维护,如下以三代一体机AHE59产品装配工艺为便于后续对产品的工时的维护。
2.2.2、关于产品生产工艺的跟进、分析和标准工时的制定2.2.3、标准工时制定的合理性通过长期的数据收集、分析和整理并依据产品的生产状况和工艺变更,及时的维护产品标准工时。
现阶段制定的标准工时合理的体现了生产的实际生产状同时,针对产品因工艺变更等因素导致的影响产品工时的,为确保所制定的标准工时的科学、合理,同时也为了防止因疏忽而遗漏工序等原因而导致的工时错误,特与产品相关工程师讨论并制定出关于工时制定的标准作业流程。
具体流程如下所示:二、生产改善和效率提升方案的实施和导入1、AHE59平缝一体机HMI,JACK迅利Ⅱ-G改善。
通过对产品的的生产状况的跟进和评估,分析产品生产流程以及导入工装,在人员减少的情况下,生产产能和效率得到显著的提升。
具体改善措施如下所示:线外加工序列工序人数工时(s)1语音芯片烧写程序+将烧写完成的芯片周转入SMT贴片1 202 PCB板去工艺边+周转 1 9产品生产流程序列工序人数工时(s)1焊接插座(2PCS)+装焊按键(1PCS)2 482 点胶+装背光模块、LCD灯 1 203 焊接LCD镜片 1 214剪脚+烧写程序+烧写参数+贴贴纸1 13除注明外,工时全部不含宽放。
)产品生产流程问题点汇总和分析:(1)由上表分析,导致生产效率过低的因素在于工序2;(2)生产等待、堆积等浪费现象过多,生产效率低下,拉平衡率仅为78.33%;(3)现场搬运、周转等浪费现象过多;(4)如通过工装的导入,减少线外加工及其周转和搬运,同时通过ECRS原则对生产流程进行分析、评估和改善,进而提高生产效率。
改善方案:(1)导入工装,将原线外芯片烧写语音程序合并入流程中,取消线外周转、搬运工时;(2)流程及动素分析、调整生产流程,减少和消除生产瓶颈工序工时,提高生产效率;(3)人机结合分析,减少生产作业中的等待等浪费工时;(备注:上述表格为JACK迅利Ⅱ HMI非语音程序款和语音程序款改善,因两者之间总工时差异不大,为方便统计该流程为综合性流程。
)注明外,以此为标准。
)2、AHE59产品包装段改善由上流程分析可知,该工时的瓶颈工序为工序1,因而重点对该工序进行分析,通过改善工装、优化作业手法,进而改善或消除生产线瓶颈。
总工时(s ) 62机器效率 64.52% 人员作业效率35.48%通过如上分析,人员和机器的使用效率偏低,如能重复的利用人员和机器的操作等待时间,提高人机效率,进而提升产品的整体的生产效率改善实施:序列作业内容 分析 1 连接测试仪上线材入整机 1、 连接好测试仪线材入整机,测试仪开始测试时时,人员处于等等状态,等待时间约18s2、 如能合理的利用该等待浪费时间,进行有价值的增值动素,那么即提升产能2 开始进行T2测试3目检,取合格品入下一工序具体改善如下所示:1、 和工装工程师肖工和PE 工程师徐工共同讨论并改善T2测试仪测试工装,具体改善方案为由之前的1人操作1台测试仪改为目前1人操作2台测试仪,如下图所示,为改善前后效率改善前:(1人操作1台设备) 改善后:(1人操作2台设备)序列动素工时(s)总工时(s)分析1从周转车上取整机344序列3种整机进行功能测试时,作业人员可操作另一台机器中序列1、2和序列4的作业动素,减少等待浪费工时2连接整机入测试工装163整机测试40 4取机3序列工序人数工时(s)单机工时(s)1 T2测试2 44 222 简易缝纫机测试 2 52 263 整机外观检查 1 22 224装整机入外箱,摆板1 20 20如上表所示,改善后生产节拍时间由32s降低到26s改善前改善后生产总工时(s)192156生产产能(PCS/H)100120提高效率16.67%每台节约时间(s)36每台节约成本(元)0.33三、关于新产品的评估四、关于标准化的实施和导入长期以来,同一产品生产工时在不同的拉别生产,生产差异较大,且同一产品在同一线别不同的生产周期生产效率值浮动也较大,如下表位产品编码为分析:如下表所示,为生产1MUH07031时,包装段在不同时期投入的人员状况如上汇总统计表所示,主要的原因在于未导入标准化作业,在产品生产中,作业流程完全依据生产拉长的经验和主观意愿。
且因无标准化作业,作业人员在作业时,也是凭着自己的经验工作,导致好的作业方式、方法无人导入。
因为生产排拉的随意性导致的生产拉平衡率和错误的作业手法,导致生产效率浮动较大。
解决措施1、制定标准作业流程图,按标准作业流程指导生产排拉;2、动素分析,分析和设计产品最佳作业方式,以便提高工作效率;3、持续跟进生产进度,发现和评估生产过程中的瓶颈工序,分析并解决;4、与PE、品质和生产人员协商、沟通,共同评估和分析提高生产产能的方式和方法并导入标准中;五、关于内部培训为了更好的提高企业整体管理水平,满足企业战略需要,提升工程技术能力,同时针对我部门一半以上的员工的工作中涉及此类工作,为了提高我部相关技术人员的专业技能,以便于更好的提高工作效率,本年度我部开展了由我和设备工程师肖工共同主导的《IE专业技能内训》工作。
其中,如下内容为本人讲解课程在培训过程中,各参训人员认真听讲,以带着问题的心态参与培训,积极提问。
我部展开的内训工作的特点是:开阔思路,围绕实际,理论与实际相结合起来。
通过此次内训工作,使我部相关专业技术人员的专业技术水平和工作能力明显提高,并使其掌握了IE专业基础知识及IE的改善思路。
六、文件的审核和批准七、工作中遇到的问题1、产品机型过多,且因为ERP分类的原因,同一产品存在多个不同的ERP,导致在评估产品标准工时时对同一产品要重复、反复的统计计算;2、产品工艺变更过于频繁,特别是新产品,如套结机,工艺变更和测试反复更改,导致每一次生产该类机型时,原先评估的产品工时及生产作业流程也要跟着更改和重新评估;3、在需要评估产品工时及报价时,产品无生产且无法提供样机,导致很多产品仅能靠预估估算产品工时,因而导致与实际的生产数据有很大的差异;4、产品标准工时中的历史数据统计长期无专人维护,且很多产品工时仅仅只是在试产阶段评估后即无更新,导致产品标准工时与实际生产工时差异过大,需对所有的产品重新评估和重新制定标准作业流程及工时;5、产品评估时因无样机,因而无法对产品进行拆解、分析。
现阶段分析产品工时时仅仅只能在产品真正生产阶段方能接触产品,且也只能通过现场录像的方式对产品作业动素进行分析;以上问题点,会在今后的工作中加强与相关人员和各个部门的沟通和联系,通过与产品相关负责人的沟通和了解,确保产品所制定的产品生产数据的科学、合理,逐步的完善标准化。
八、来年工作计划不知不觉,一年时间结束了。
总结起来,在这一年中遇到过挫折,得到过收获,同时也让自己有所成长。
展望未来,在未来的一年时间中,结合工作的实际及应用,继续导入标准化、效率提升、现场改善和成本管控。
同时,紧跟新产品,对新产品工艺的评估和分析,逐步的导入和实现产品的效率的最大化。
同时,在即将到来的新的一年中,也要额外注意提升自我的专业技能,将自己的工作更好的,更高效的完成。